Bicycle tech for Caterham - UPDATE
Price and weight saving estimate released for the butted steel chassis
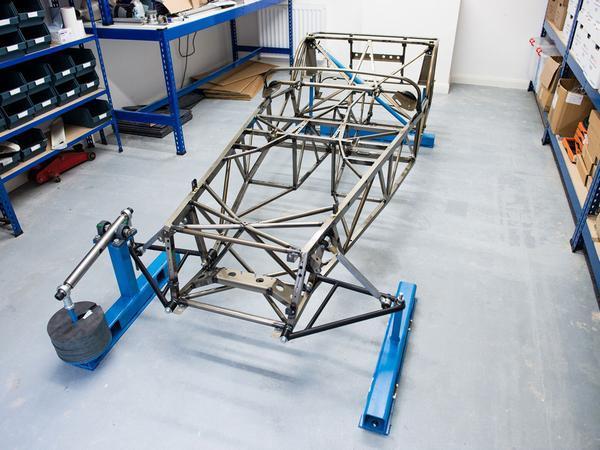
Now Caterham has announced further details on the project, with a prototype chassis produced through Simpact's Computer Aided Engineering expertise. The interesting news is that Caterham has claimed more than 10 per cent has been taken from the weight of a Seven chassis. Given how light it is already, that's quite some achievement.
As for cost, Caterham is predicting the butted tube chassis will cost between £1,000 and £2,000 as an option. But if you want the ultimate lightweight Caterham...
The prototype chassis will continue to be refined by Caterham in the coming months, with a view to creating a production version "in due course." We'll keep you posted!
October 26, 2015
As anyone from the more beardy end of the Pedal Powered forum will gladly tell you, butted steel tubing remains the purist's choice of material from which to build a bicycle. Modern-day MAMILs may dote over their flashy carbon fibre or titanium but the 'ping' and feel of high quality butted steel tubes retains a unique appeal and strong following. And in terms of stiffness and weight can actually compare well with more apparently space age materials too, providing an interesting contrast with Ariel's investigations into using titanium for building ultra lightweight (and expensive) Atom chassis.
For the uninitiated, butted tubing has thicker walls at the ends to support welded joins with staged thinning to potentially just fractions of a millimetre towards the centre to save weight. The length of the butts, the sophistication of the alloys used and thickness of the walls are all proprietory tech unique to each manufacturer but, at its best, it can be lighter, stiffer AND stronger than cheap, plain gauge piping, albeit at a cost.
Meaning if your business is building lightweight cars based on tubular steel frames the technology could well be of interest. Step up Caterham, which has announced a collaboration with iconic tubing manufacturer Reynolds and Simpact Engineering to investigate its application in the construction of chassis for its iconic Seven range.
"Our target is to end up with a chassis that delivers a 10 per cent mass saving in weight," says Reynolds Technology's Keith Noronha. "Our butted tubes have contributed to weight reduction in diverse applications from bicycle frames to NASA spacecraft projects. This project aims to prove that car designers can re-think how to use steel - a sustainable and recycleable material - whilst meeting challenging targets on stiffness and driveability. The Caterham Seven should be the first car to incorporate these innovative aspects."
To put the theory to the test Simpact Engineering will use its CAD expertise to 'build' a Seven chassis out of butted tubing and conduct virtual testing ahead of construction of a physical prototype from Reynolds tubing. Support for the project comes from the Niche Vehicle Network, funded by Innovate UK, the Office for Low Emissions Vehicles and the Department for Business Innovation and Skills to illustrate the wider applications of such technology for building simple, cost-effective and lightweight cars.
And if the way of doing that is building a lighter, faster Caterham with the zing of a classic, high-end steel racing bike at its core consider us sold on the idea!
[quote] I am suprised they weren't using butted tubes already, the bicycle industry has been using it on spokes and frames of various materials for a long time to save weigth where you don't need the material for strength.
Ps. I admit that my pie input leaves much to be desired too...
A 753r or 531c sticker on your dashboard would be quite cool.
Some of the alloys are also very corrosion resistant, which can only be good.
Also, the higher quality bike tubes are drawn, not seamed. That'd be nice in the car application, too.
Presumably, Reynolds will effectively manufacture tube "sets" with everything cut and contoured in the right place.
Caterham pop them in a jig, weld them up, clean, powder coat and away it goes.
A 753r or 531c sticker on your dashboard would be quite cool.
Some of the alloys are also very corrosion resistant, which can only be good.
Also, the higher quality bike tubes are drawn, not seamed. That'd be nice in the car application, too.
Presumably, Reynolds will effectively manufacture tube "sets" with everything cut and contoured in the right place.
Caterham pop them in a jig, weld them up, clean, powder coat and away it goes.
The tubeset is the only way with butted tubes - which may prevent the outcome being high end models only. Will be interesting to see the difference in BOM costs versus the reduced labour in measuring, cutting, prepping, etc.
One of my friends went all wobbly at the knees when he saw a carbon fibre framed bike ridden by another bloke in lycra - surely CF (not lycra) is the future as costs reduce...?
Or composites (a la new TVR) from Gordon Murray's iStream tech...
"Rather than stamped steel, iStream uses a tubular frame and a composite monocoque, promoting manufacturing efficiency and reducing weight."
- Incorrect. The specific stiffness of the steel doesn't change if you use 'posh' tubing instead of 'gas pipe'. What exotic tubes enable you to do is use thinner walled tubes but retain STRENGTH.
I believe Reynolds made exotic thin-gauge steel tubing for British helicopters in the late 1950s so they will have some experience of working with larger-diameter, thin- gauge tubing.
One of my friends went all wobbly at the knees when he saw a carbon fibre framed bike ridden by another bloke in lycra - surely CF (not lycra) is the future as costs reduce...?
Or composites (a la new TVR) from Gordon Murray's iStream tech...
"Rather than stamped steel, iStream uses a tubular frame and a composite monocoque, promoting manufacturing efficiency and reducing weight."


We need Brian.
Gassing Station | General Gassing | Top of Page | What's New | My Stuff