Anyone interested in home-built sailing dinghies?
Discussion
I'm building a Campion Apple 16 at the moment, a 16ft sailing dinghy with an attractive classical gaff cutter rig. It's a simple stitch-and-glue design made from marine plywood using the same techniques as the famous Mirror Dinghy, but the Apple is a fairly pretty thing.

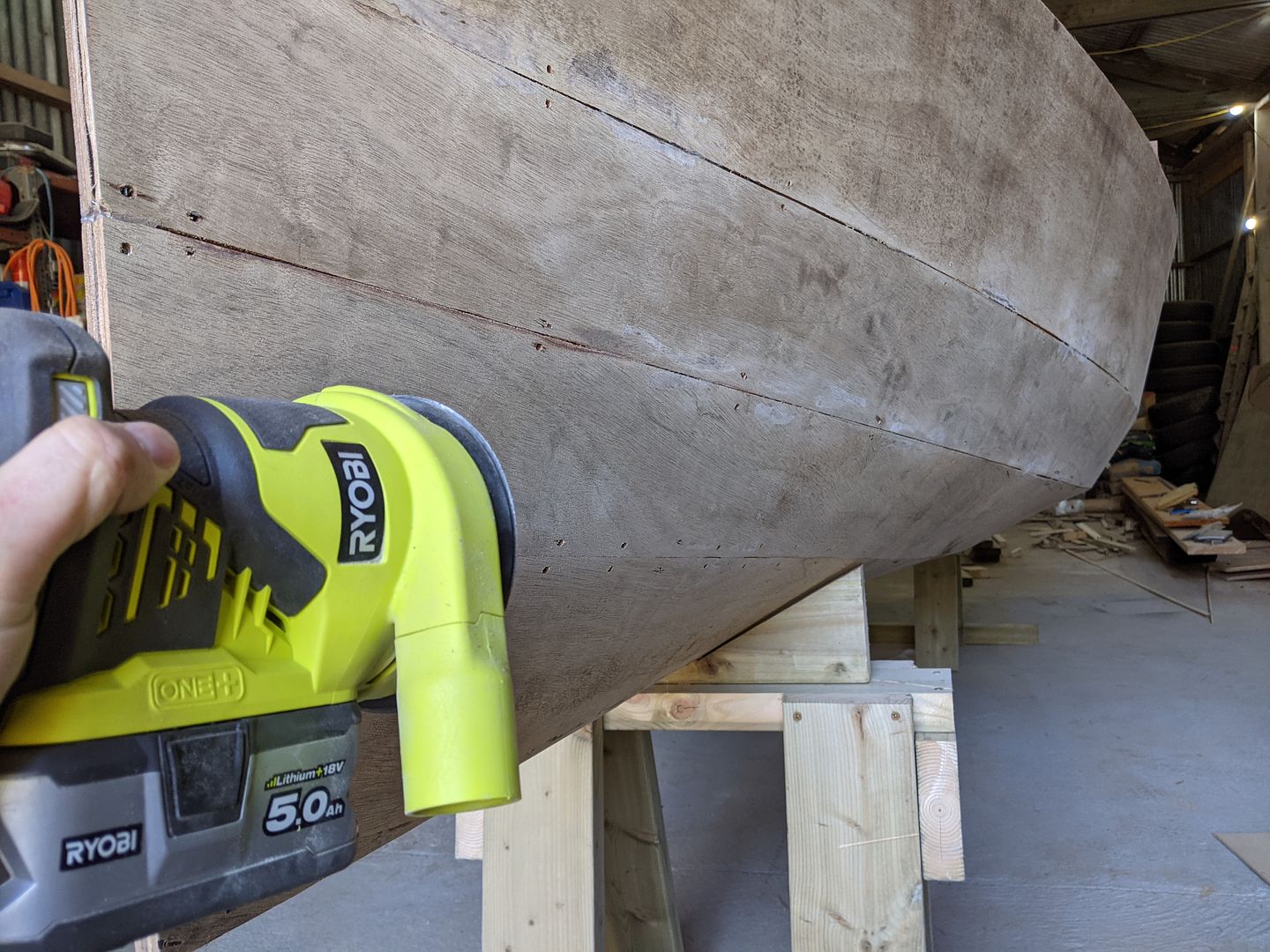
Any interest?

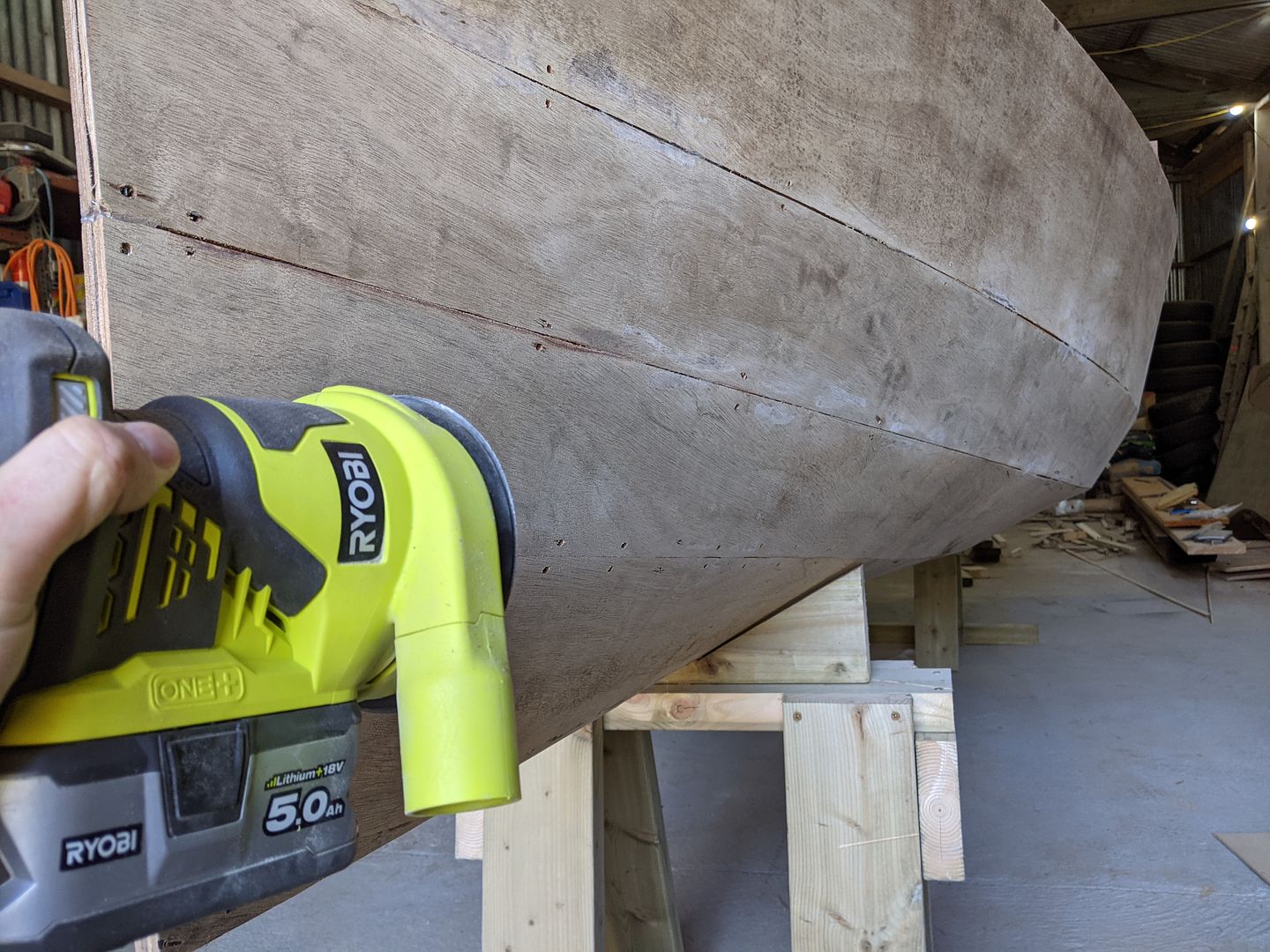
Any interest?
Edited by jamieduff1981 on Tuesday 31st May 19:55
Brilliant! Here goes then 
I've always liked things which go but usually motorised things. With boats my interests have either been WWI / WWII era warships mostly, or classic sailing vessels. Whilst I'd love a Riva Aquarama and a pair of Lamborghini V12s on song, for some reason I generally prefer sail to power boats.
I'm a bad sportsman. I expect to be able to win with no effort and if I can't just turn up and win, I won't take part. Watching racing yachts and stuff is cool, but I can't take part in that because I'm the worlds worst loser. So, cruising dinghy it is!
There are designs galore and of course lots you can buy already built. I wanted to build mine, but I try to be realistic now about how much free time I have and a limited attention span. I love watching good quality woodwork such as Sampson Boat Co on Youtube but practically speaking, I would never, ever finish a "proper" boat, which is compounded by the fact that suitable timber for boat building just doesn't really exist in Scotland and even in England you really have to have the right contacts and deep pockets. So, plywood boat it is. Trouble is, most of them are very functional but look more Land Rover Defender than Lamborghini Miura. The Campion Apple looked the part for me, and from doing further research its sailing qualities sounded about what I was looking for too. It's big enough for a weekend out with my wife and 2 daughters, but small enough to single-hand. With ballast it's quite well mannered and stable but is capable of around 7kt in a good breeze.
I bought the marine ply locally, and I have a stash of reclaimed Iroko school science lab benches which I wanted to use as much as is appropriate to save buying new hardwood.
I started with the rudder headstock. It is made from 2 cheeks, each one being 2 laminations of 9mm marine ply for 18mm total per side, spaced out by a block of Iroko. I taught my eldest daughter to use the power sander for this.
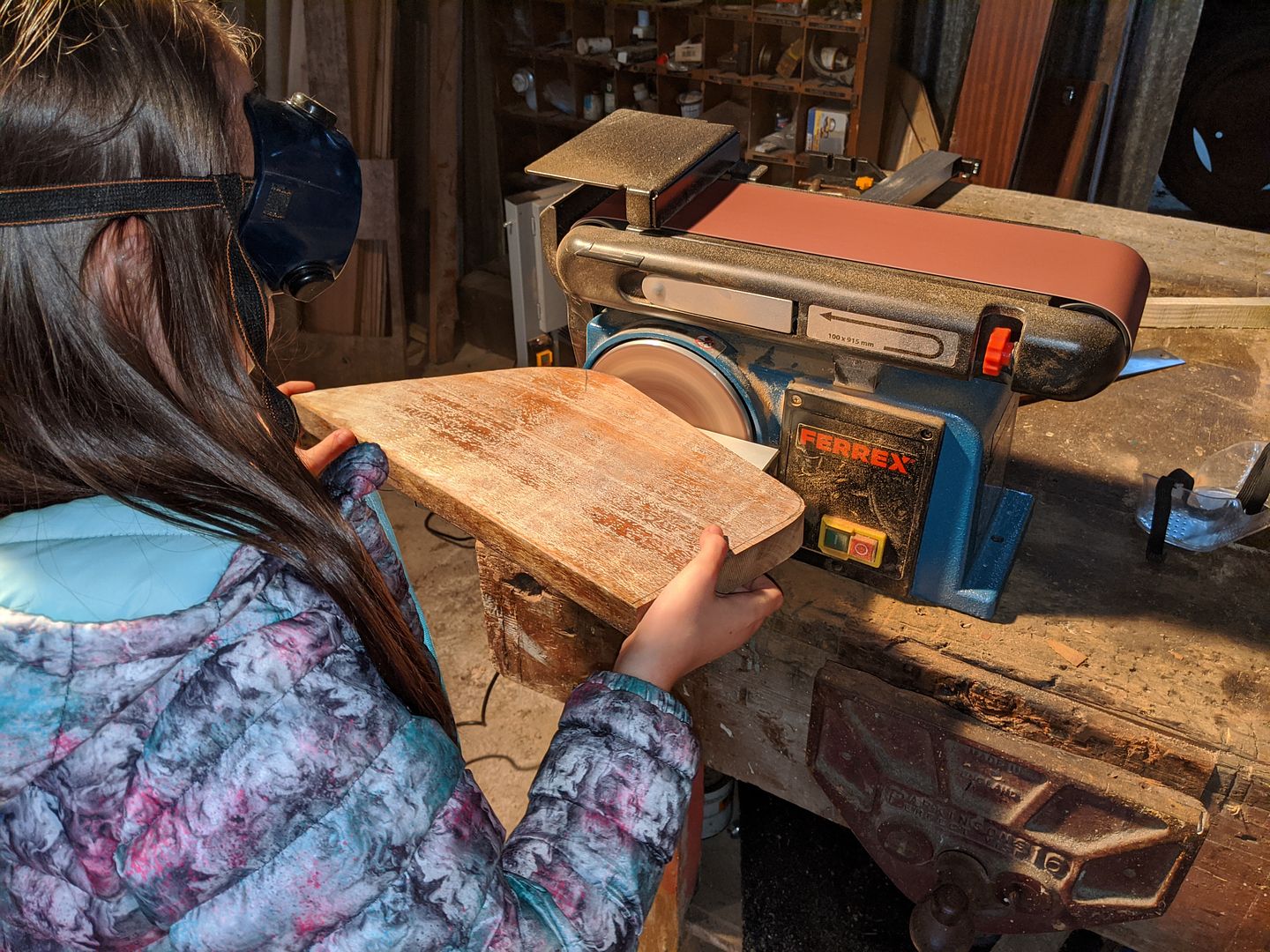
I'm using West Systems epoxy for the gluing. In the background I've started laminating rough cut strips for the rudder blade.
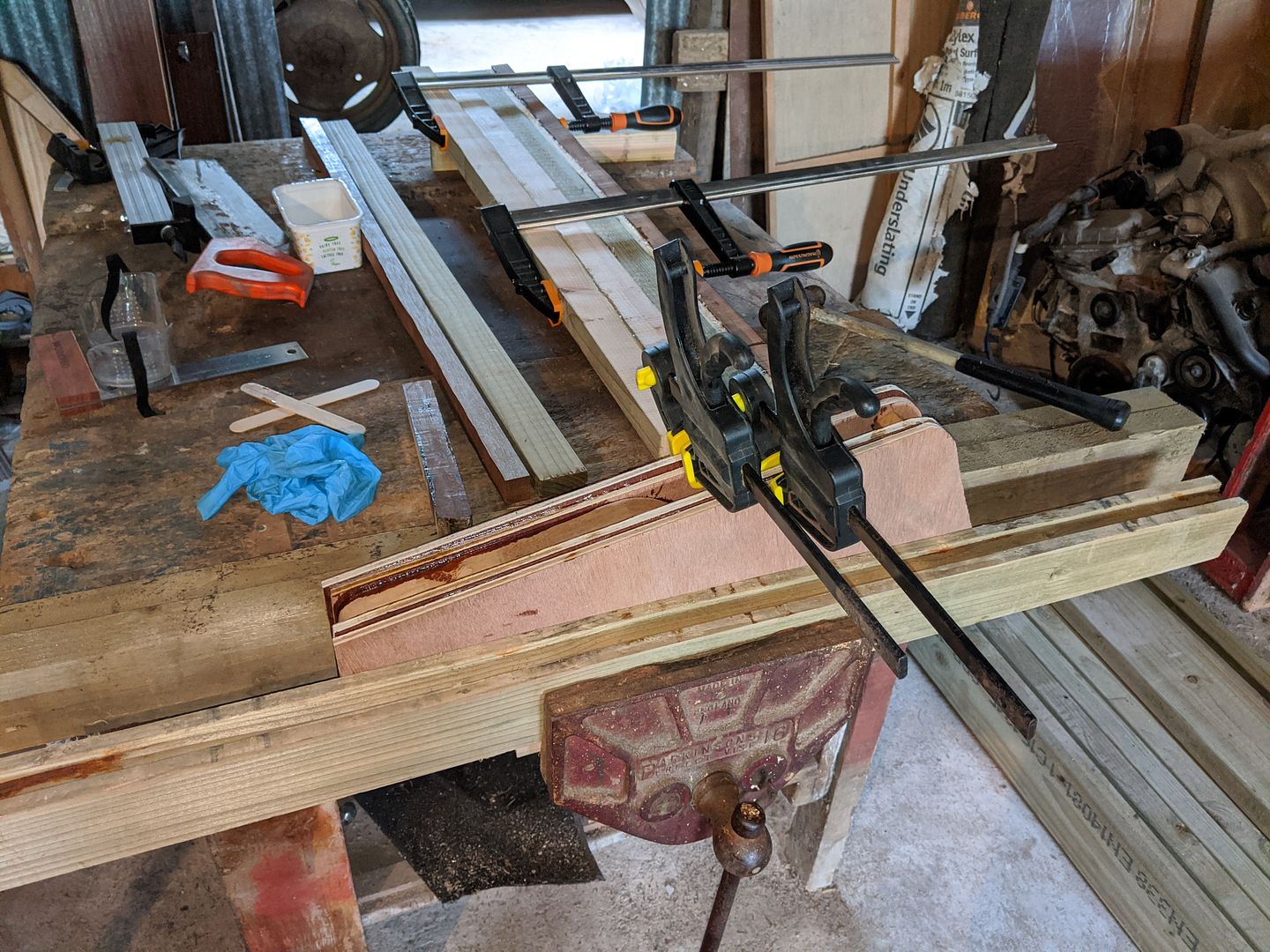
The blade is laminated from softwood strips with Iroko leading and trailing edges. I've upgraded from the plans slightly by fitting Oilite bronze bushes as bearings for the stainless steel through-bolt.

In the usual fashion this allows the blade to be pivoted back for shallow water.
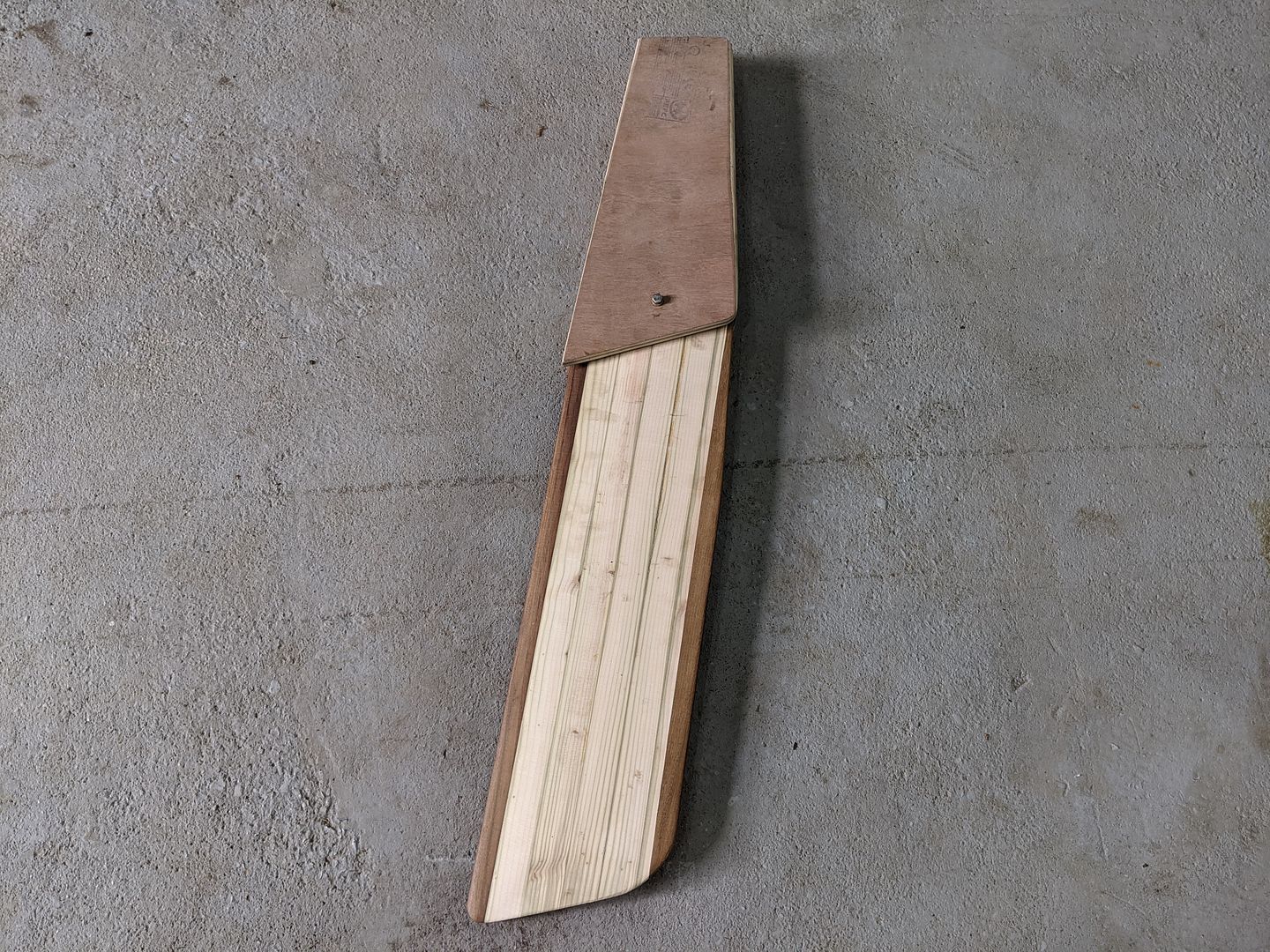
Thus:

The plans call for the blade to be fibreglassed with bidirectional glass cloth

And I started roughing out a tiller from Iroko which I will refine later.
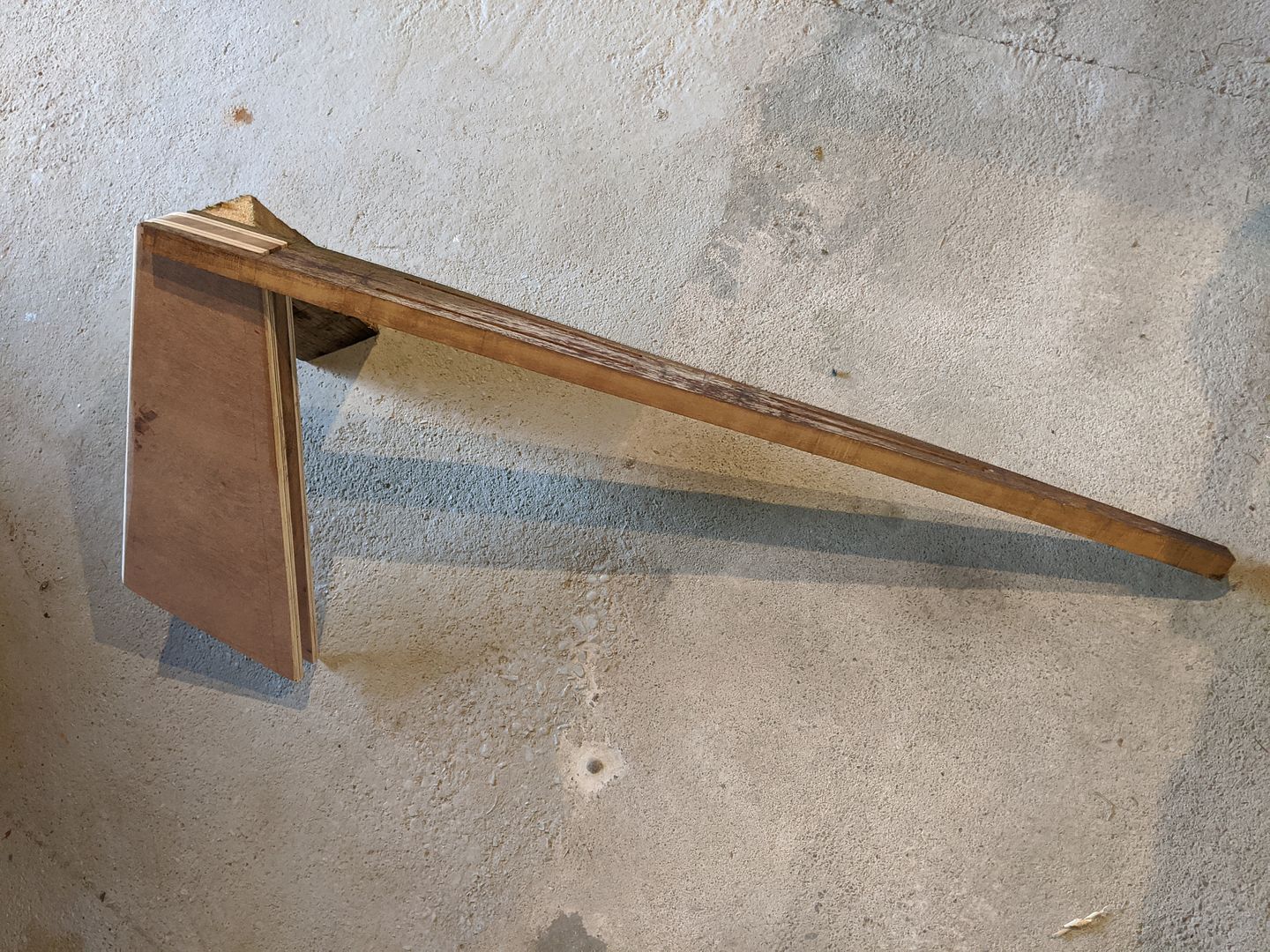

I've always liked things which go but usually motorised things. With boats my interests have either been WWI / WWII era warships mostly, or classic sailing vessels. Whilst I'd love a Riva Aquarama and a pair of Lamborghini V12s on song, for some reason I generally prefer sail to power boats.
I'm a bad sportsman. I expect to be able to win with no effort and if I can't just turn up and win, I won't take part. Watching racing yachts and stuff is cool, but I can't take part in that because I'm the worlds worst loser. So, cruising dinghy it is!
There are designs galore and of course lots you can buy already built. I wanted to build mine, but I try to be realistic now about how much free time I have and a limited attention span. I love watching good quality woodwork such as Sampson Boat Co on Youtube but practically speaking, I would never, ever finish a "proper" boat, which is compounded by the fact that suitable timber for boat building just doesn't really exist in Scotland and even in England you really have to have the right contacts and deep pockets. So, plywood boat it is. Trouble is, most of them are very functional but look more Land Rover Defender than Lamborghini Miura. The Campion Apple looked the part for me, and from doing further research its sailing qualities sounded about what I was looking for too. It's big enough for a weekend out with my wife and 2 daughters, but small enough to single-hand. With ballast it's quite well mannered and stable but is capable of around 7kt in a good breeze.
I bought the marine ply locally, and I have a stash of reclaimed Iroko school science lab benches which I wanted to use as much as is appropriate to save buying new hardwood.
I started with the rudder headstock. It is made from 2 cheeks, each one being 2 laminations of 9mm marine ply for 18mm total per side, spaced out by a block of Iroko. I taught my eldest daughter to use the power sander for this.
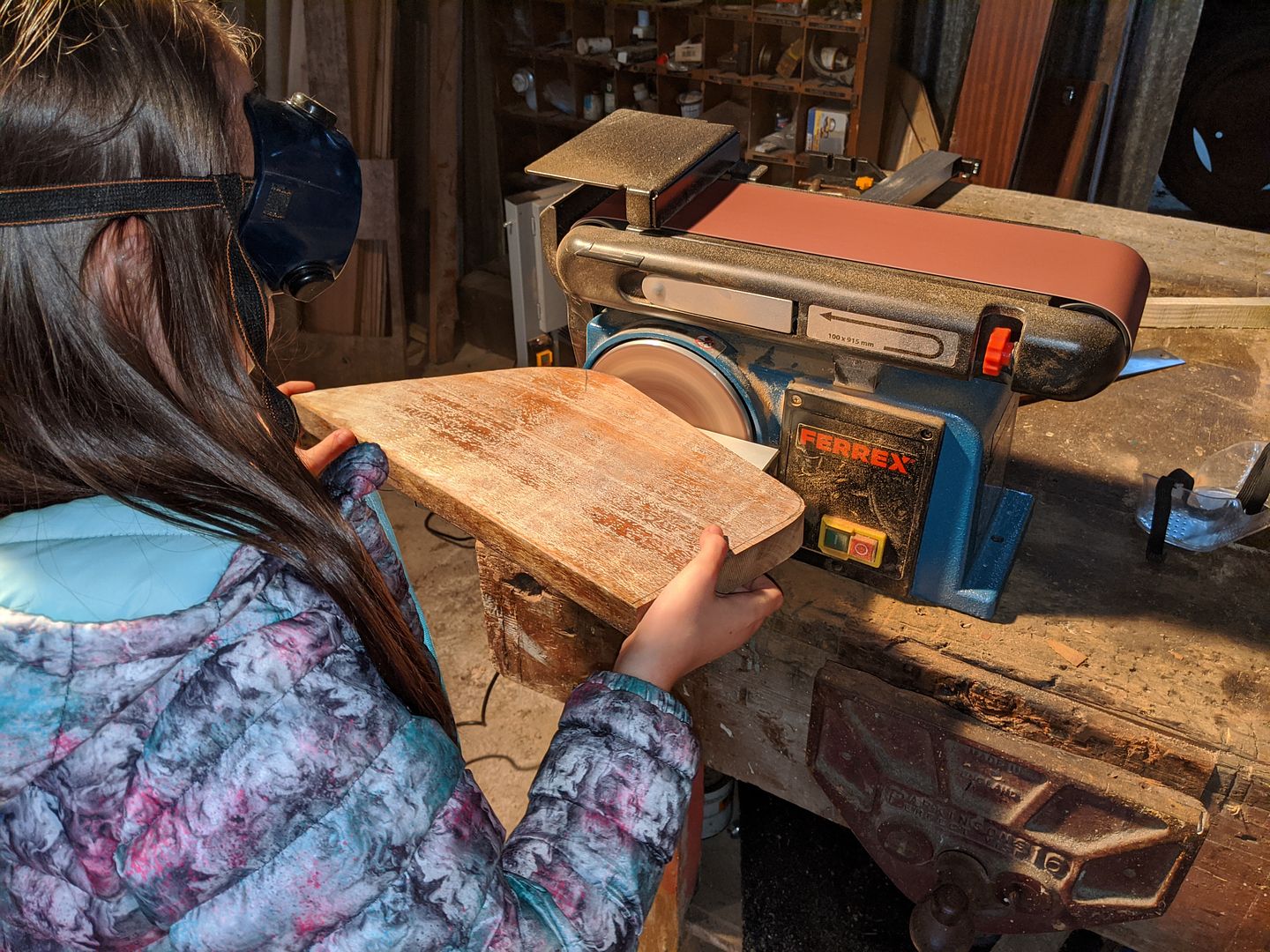
I'm using West Systems epoxy for the gluing. In the background I've started laminating rough cut strips for the rudder blade.
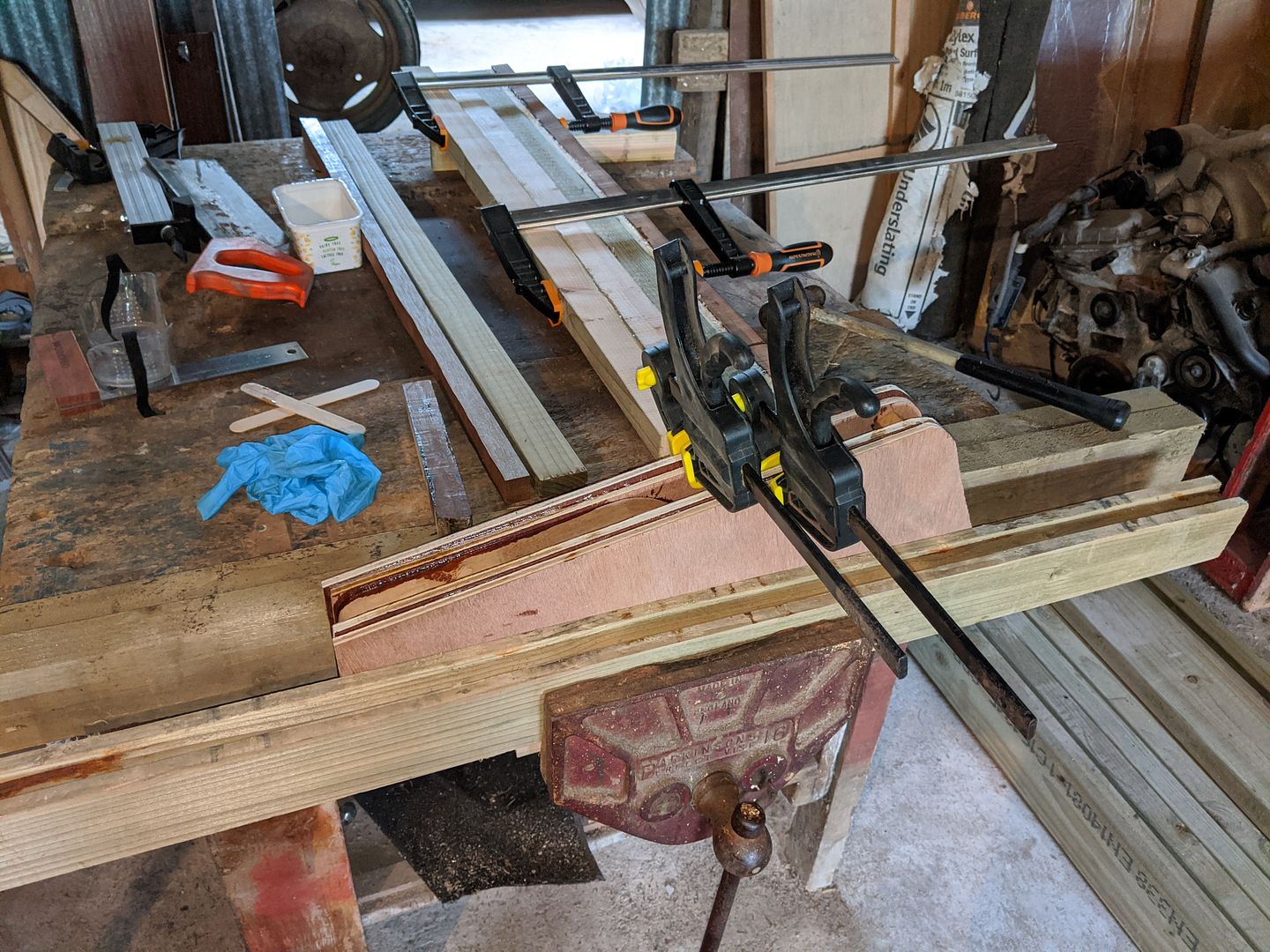
The blade is laminated from softwood strips with Iroko leading and trailing edges. I've upgraded from the plans slightly by fitting Oilite bronze bushes as bearings for the stainless steel through-bolt.

In the usual fashion this allows the blade to be pivoted back for shallow water.
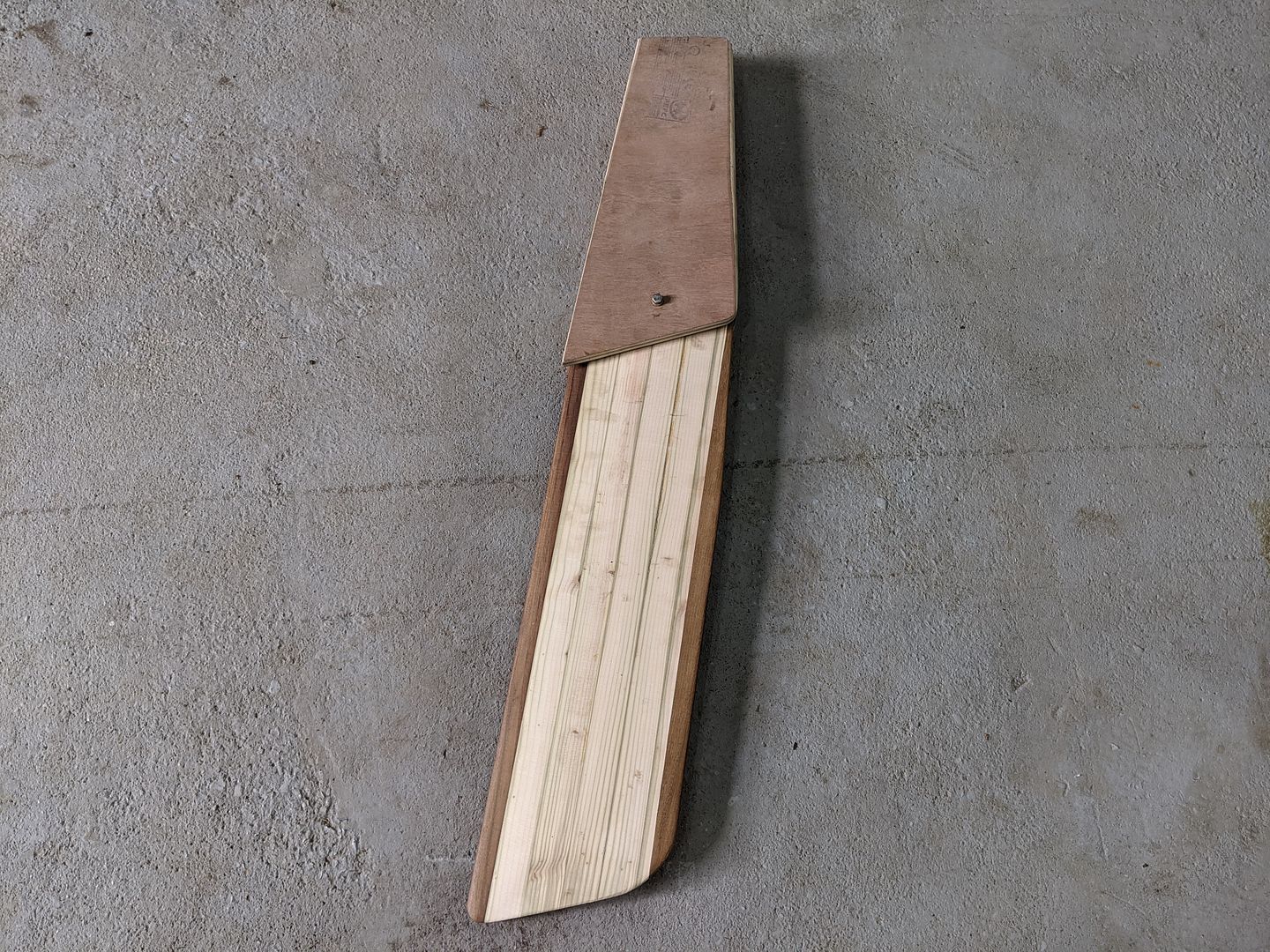
Thus:

The plans call for the blade to be fibreglassed with bidirectional glass cloth

And I started roughing out a tiller from Iroko which I will refine later.
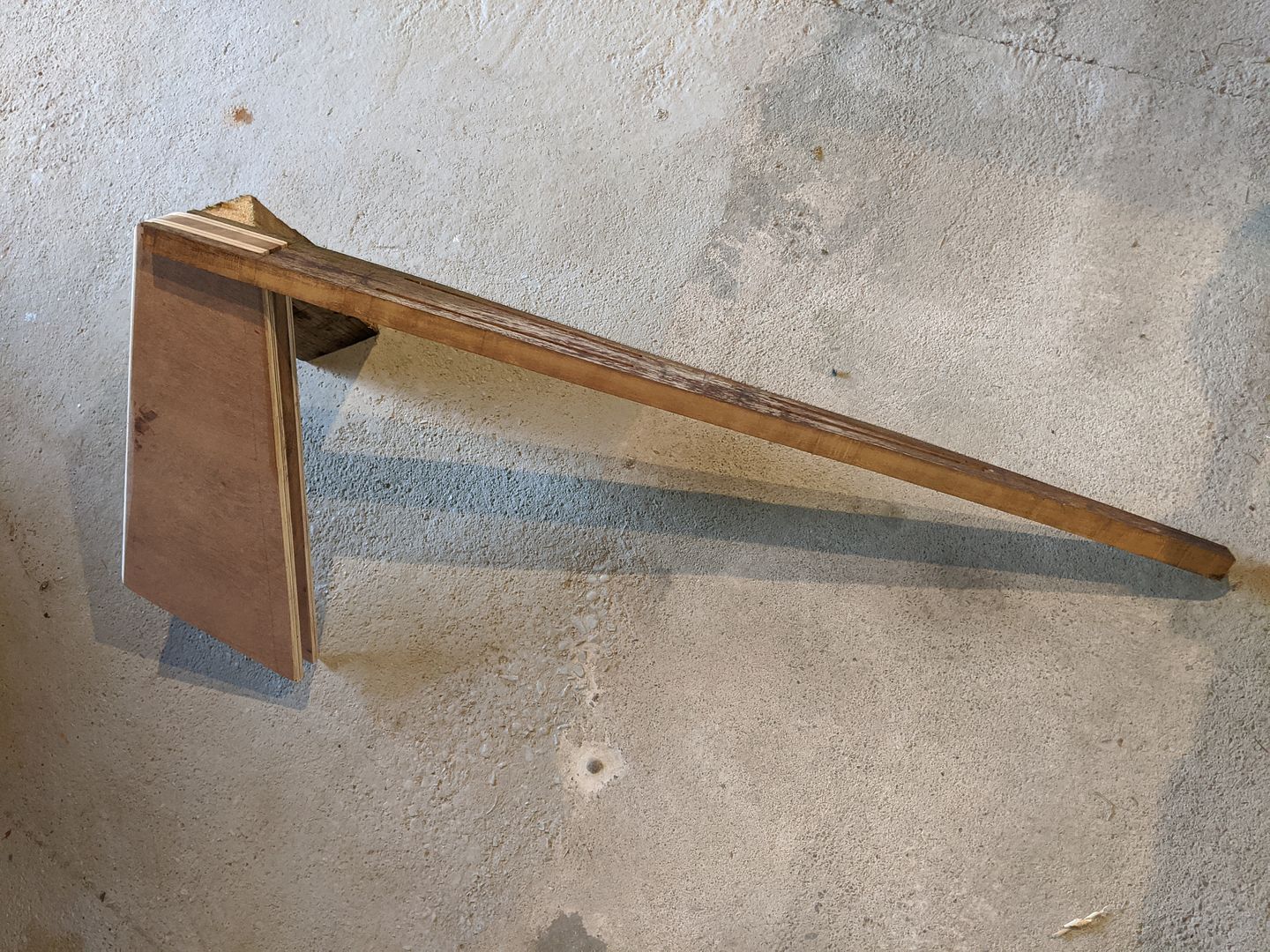
Edited by jamieduff1981 on Tuesday 31st May 20:02
The hull as you've seen is a multi-chine affair and the design uses 4 planks per side and a lower rubbing strip giving the visual impression of 5 per side. The designer, Mr Tom Dunderdale, has very cunningly nested the 2-dimensional shapes of the 4 planks such that each side fits into a single 16ft x 4ft board of 6mm marine ply.
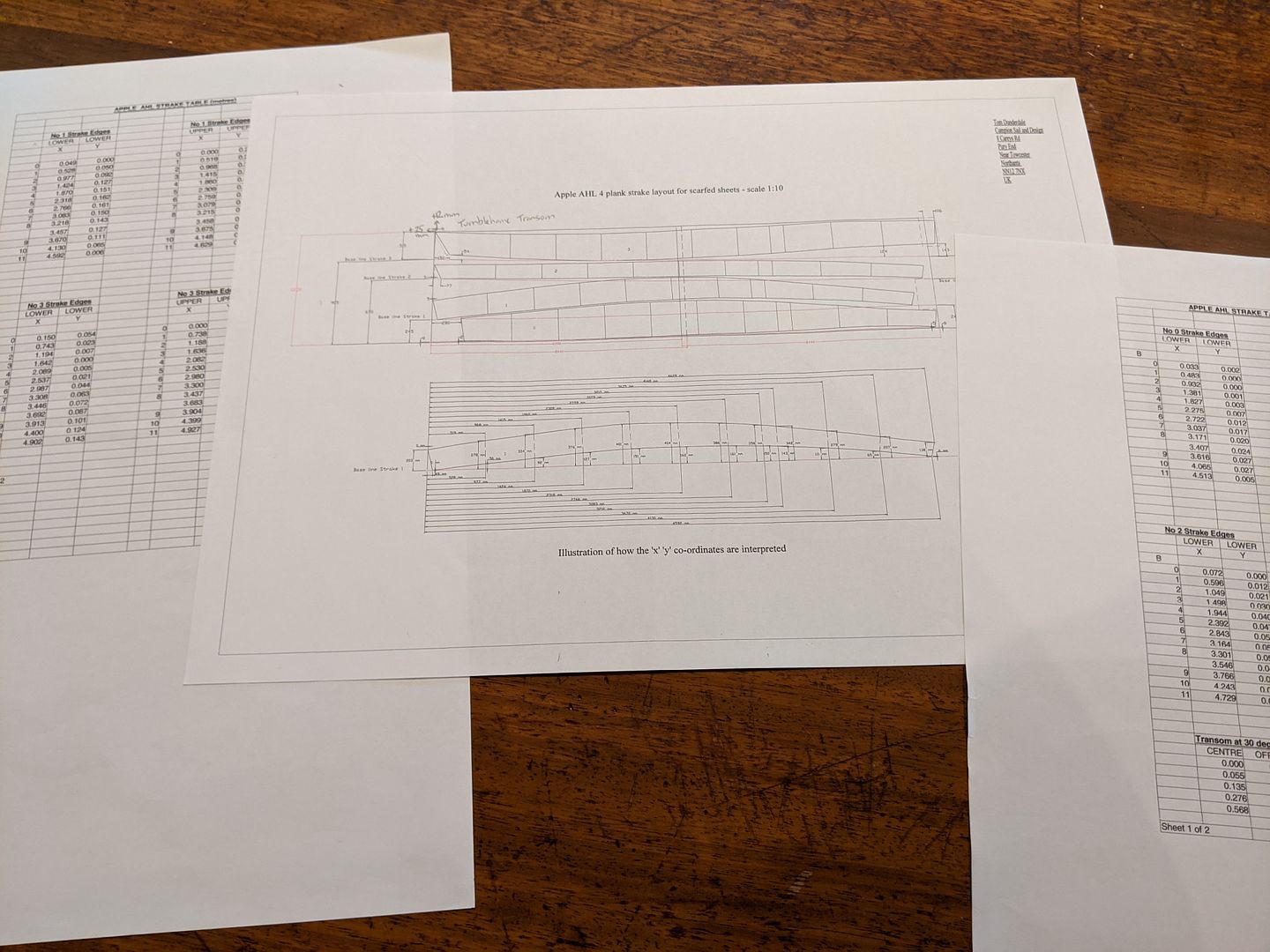
Of course, plywood boards come as 8ft x 4ft so the first job was to scarph them together. It is actually permissible in the plans to butt-join them and fibreglass tape the joint, but I preferred to scarph them.
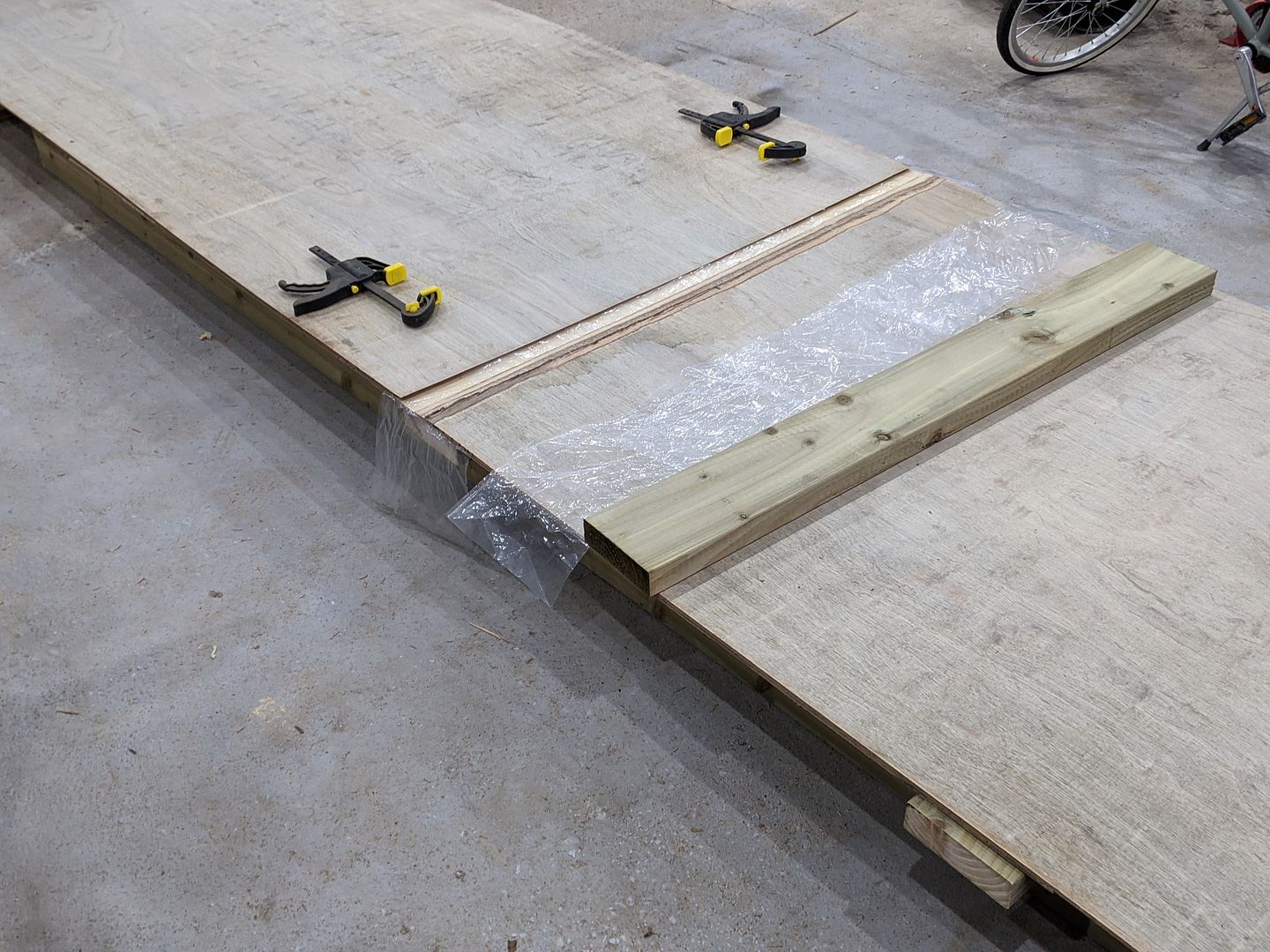
To lazy to make a scarphing jig, I just did it with the power planer and the results were useable but hardly great quality. To make up for lack of quality I thickened up the epoxy a touch with milled fibres.

I broke a plastic clamp whilst clamping the scarphs together for gluing and shortly after this photo went all-metal
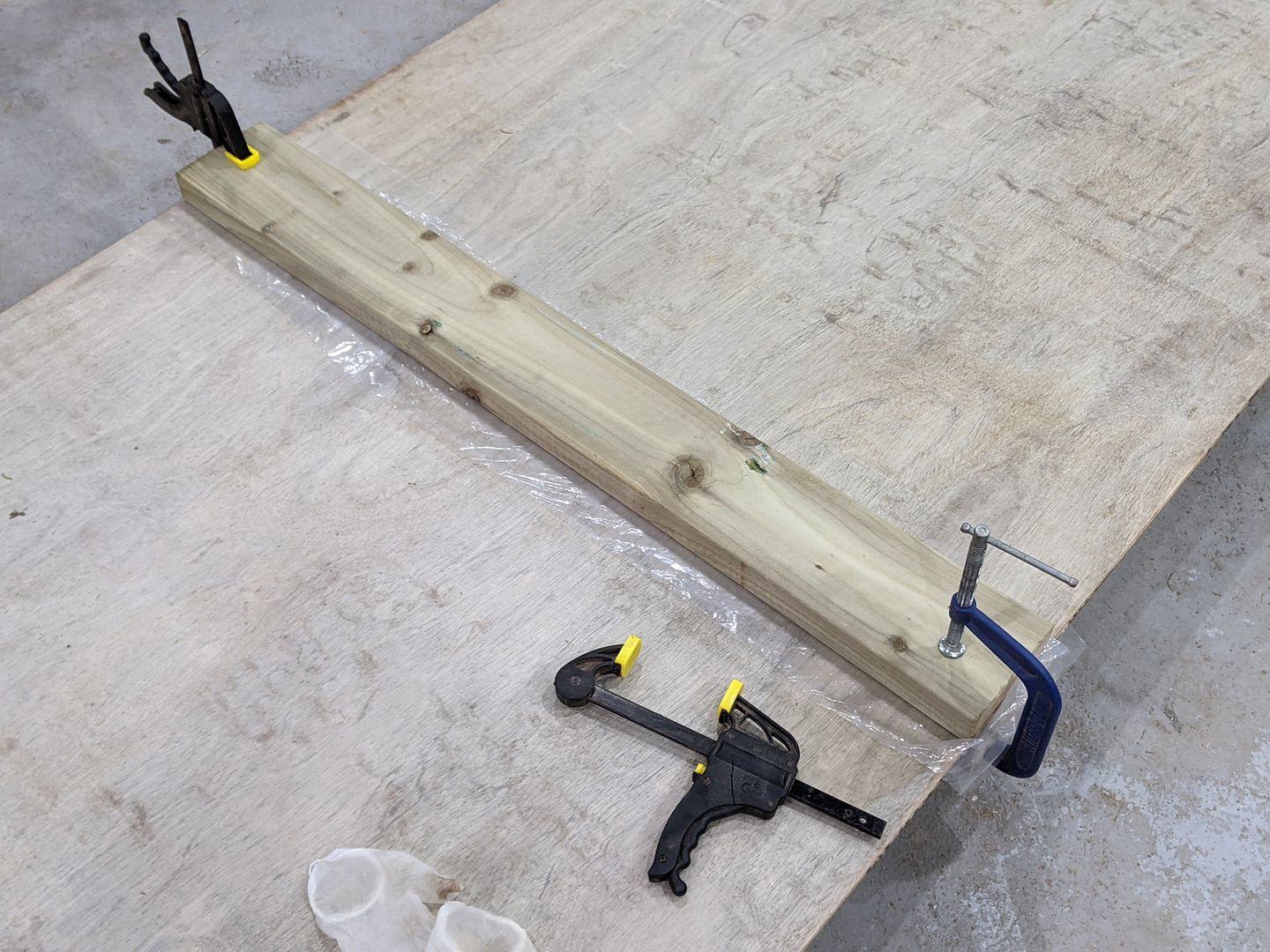
Obviously the polythene was to prevent me gluing the planks I used to distribute the clamping pressure across the whole joint to the joint itself...
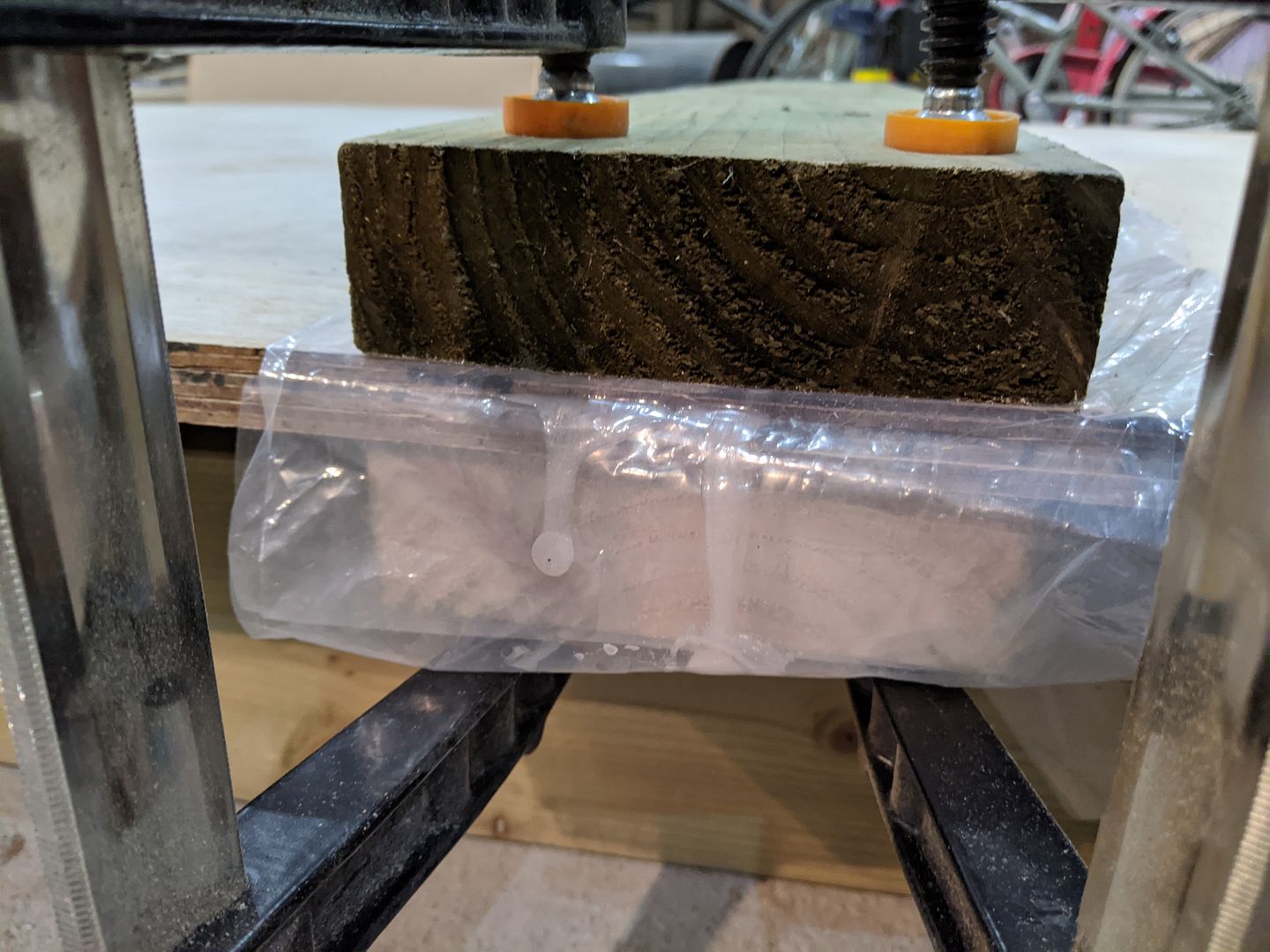
Each plank then needs its own datum measured and marked onto the resultant 16ft board, and a series of stations describing the upper and lower edges are lofted onto the plywood from a table of measurements
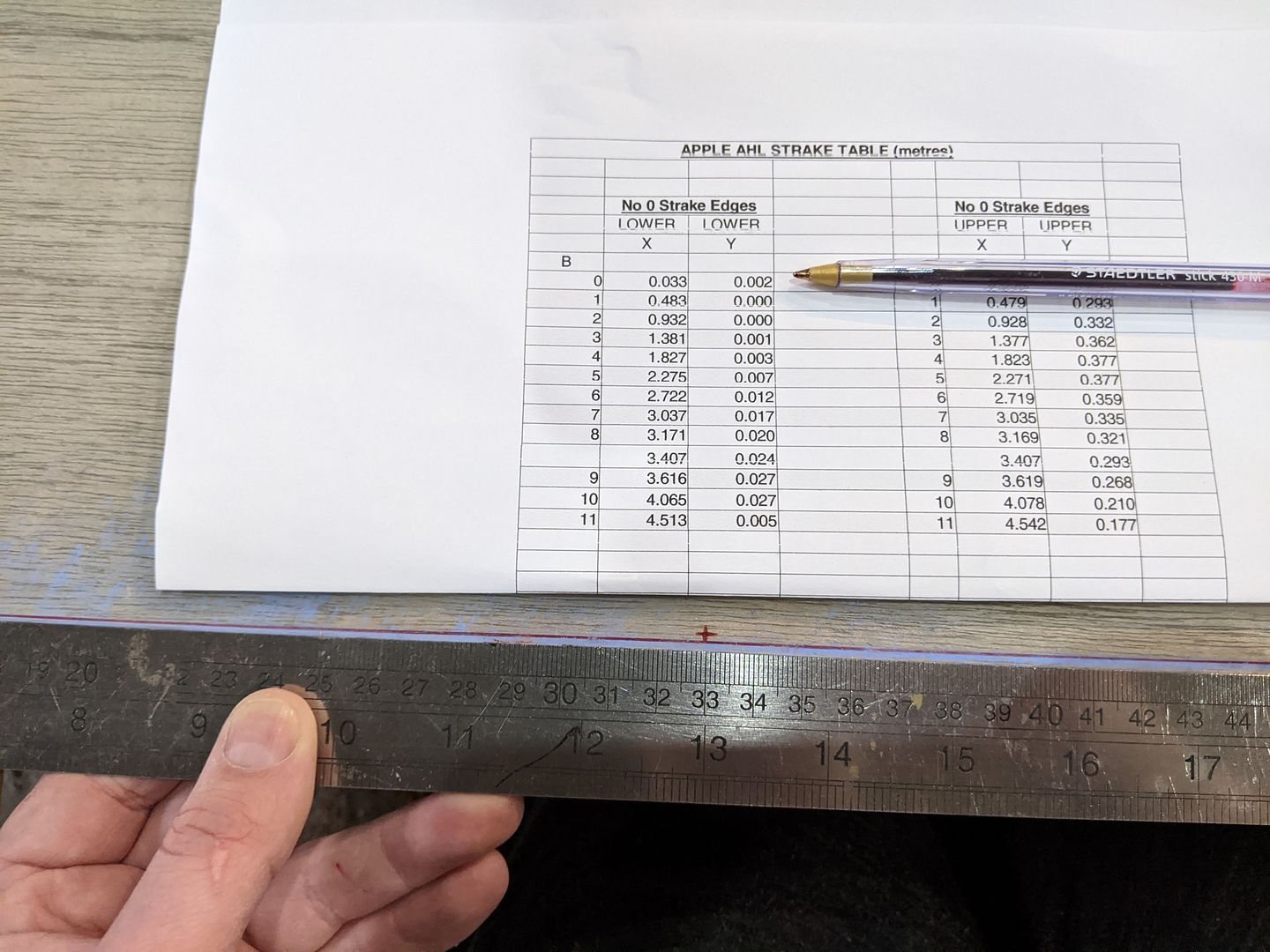
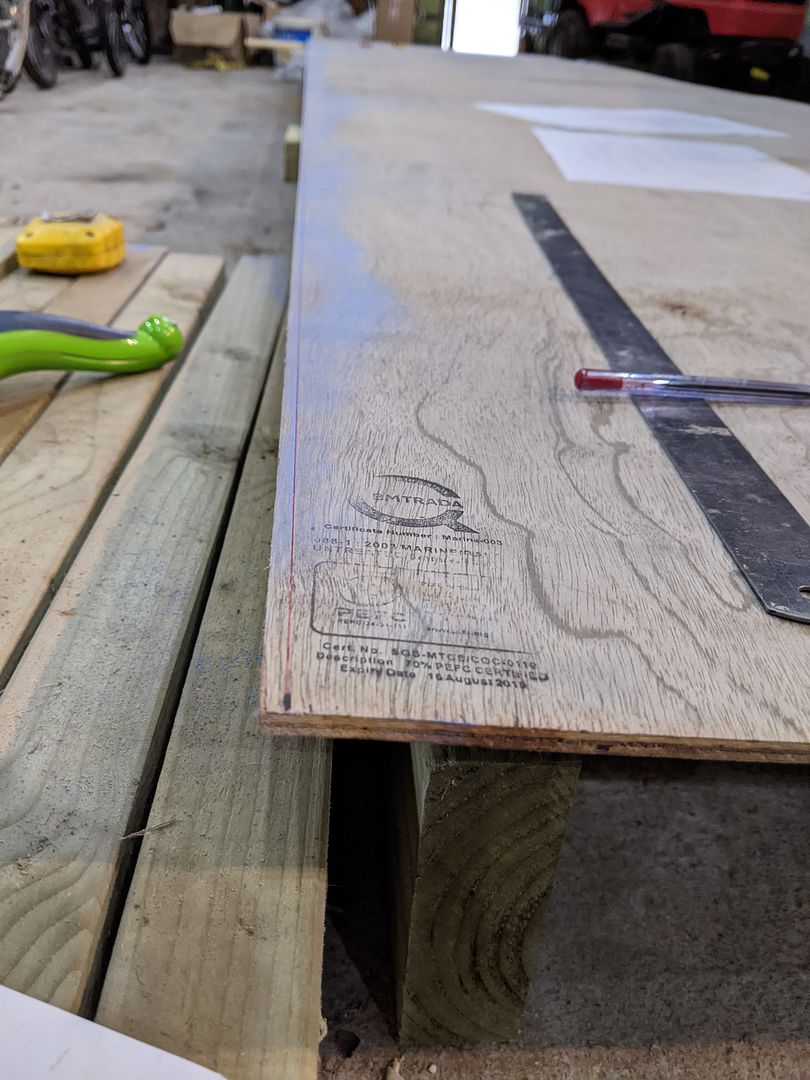
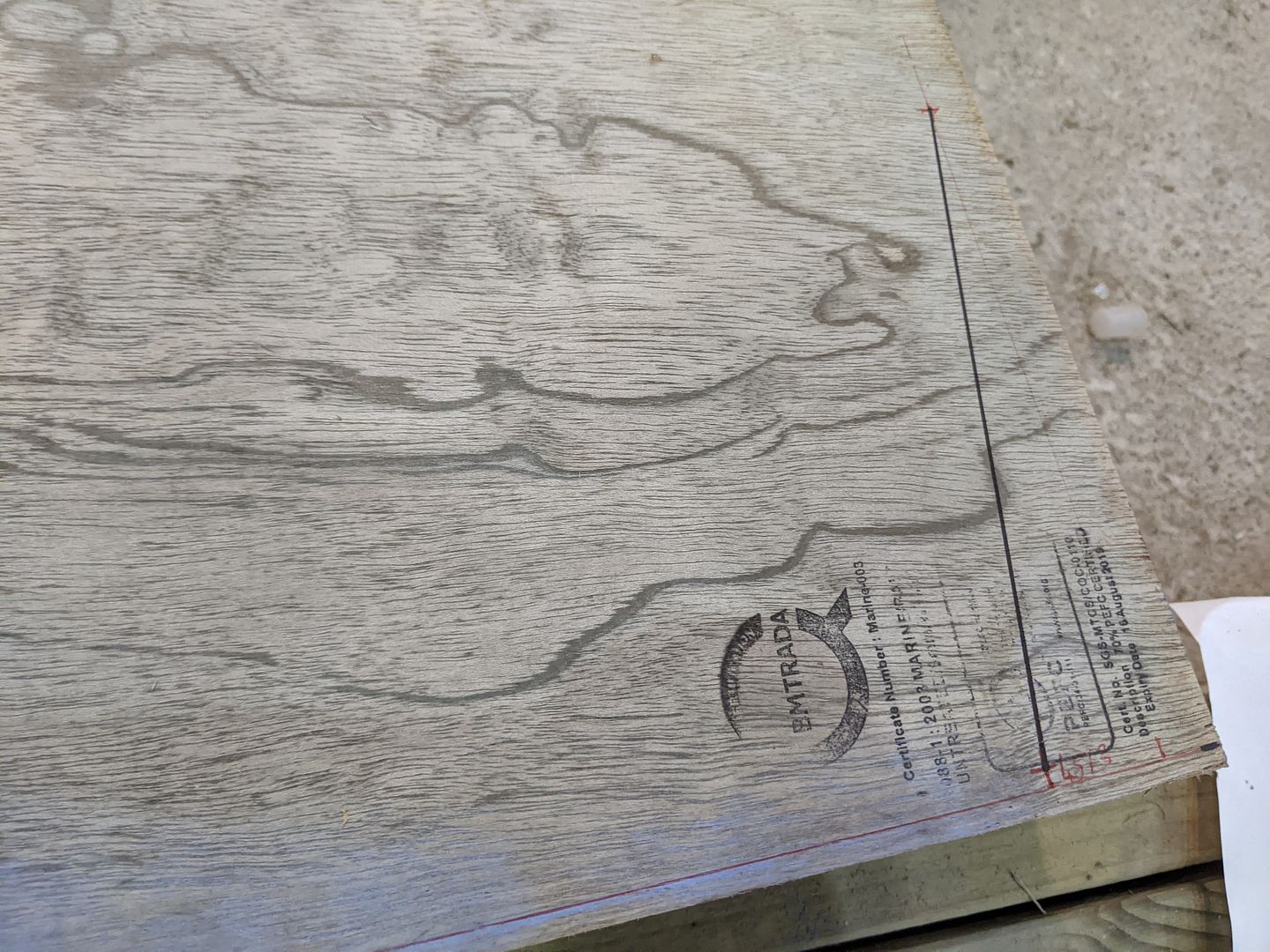
Once all the stations are marked, pins are tapped in to each and a long batton sprung to join the dots with a fair curve to trace out with a pen.

The uppermost plank does need an extra little bit scarphed on to make up the length, but the extra bit is cut from elsewhere on the board. Due to the nesting to get all planks from the one board, they're staggered slightly fore and aft to offset their deepest points.
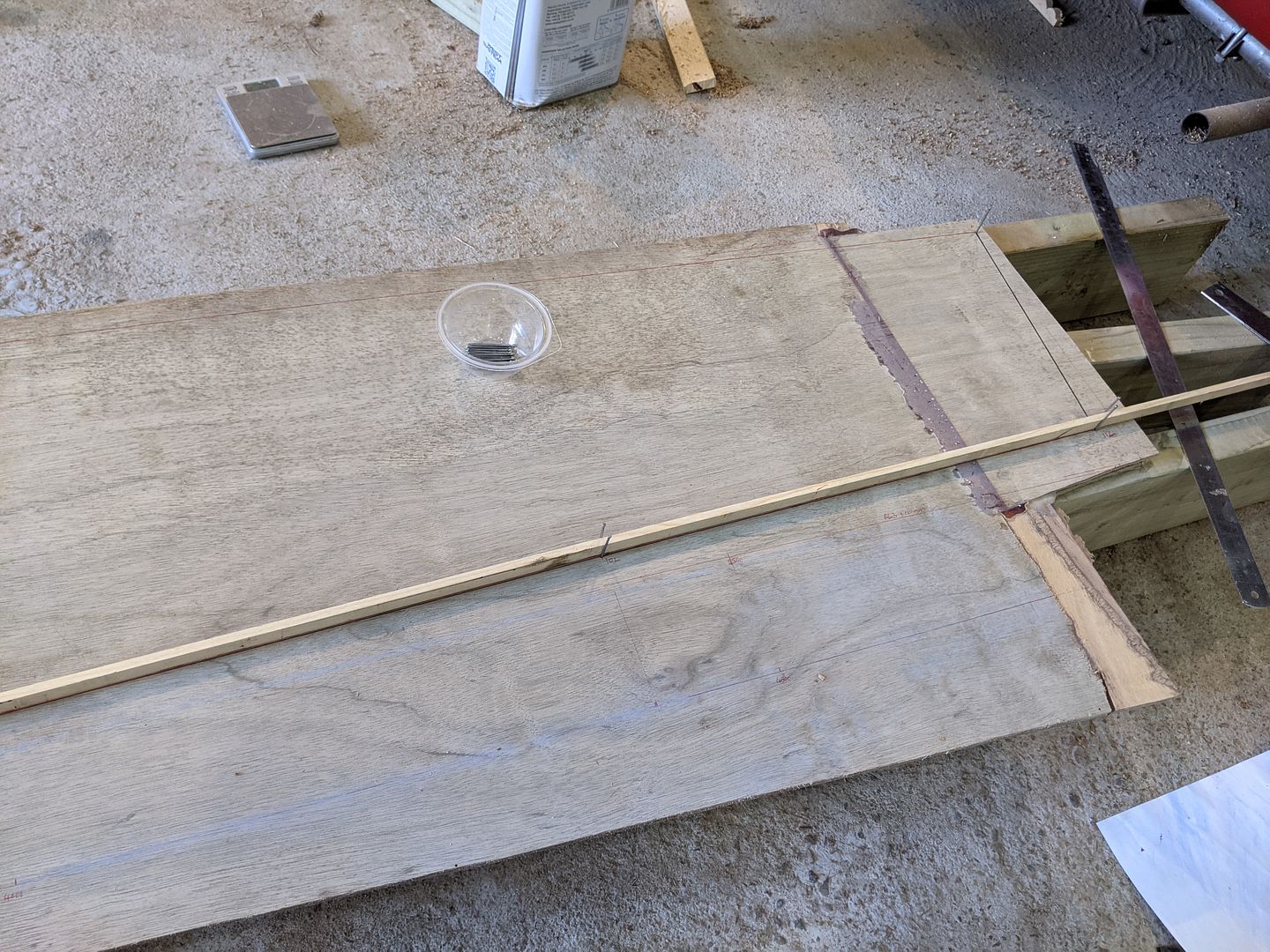
I only marked out the planks on one board, then clamped both boards together tightly, set the cut depth to 12mm on a circular saw with a fairly fine blade with lots of little teeth and cut them out together. Each pair of planks was then clamped together whilst I finished down to the lines.
Here we have a hull kit. Ok, not quite - there's no transom here and I hadn't yet cut out the internal frames. Actually on closer inspection, I'd rough cut the planks for this picture but evidently had had enough fun for one night - so they're still to be finally trimmed down to the lines.
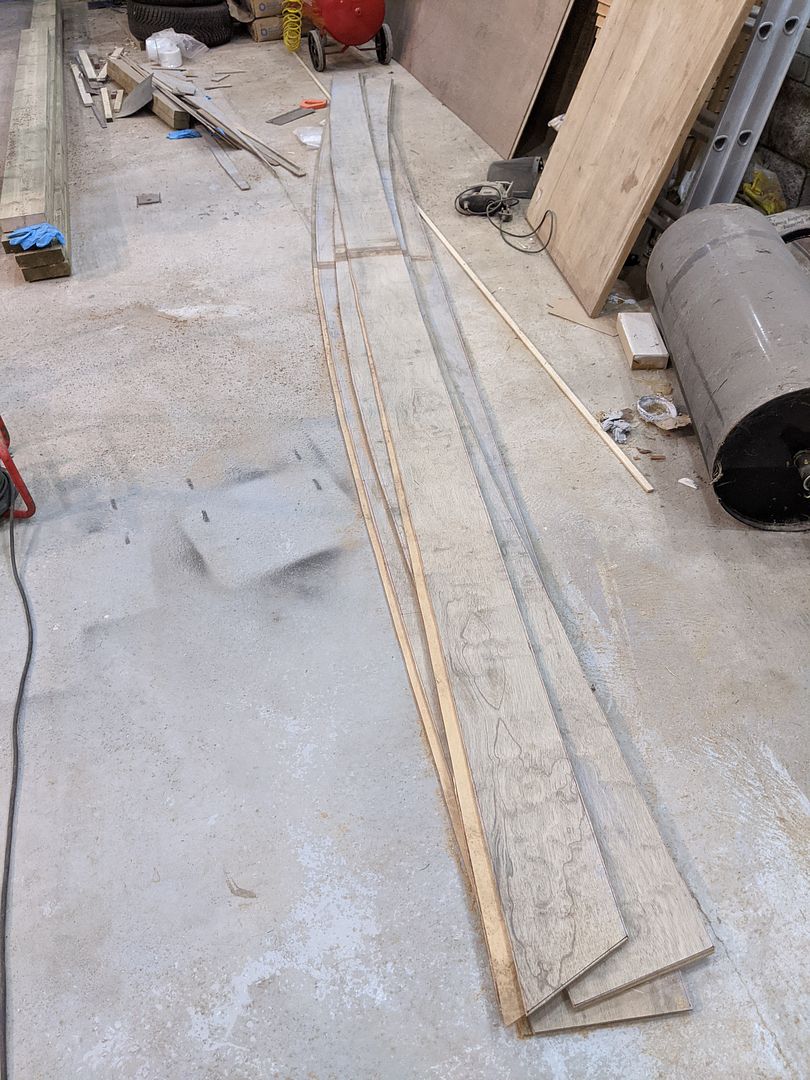
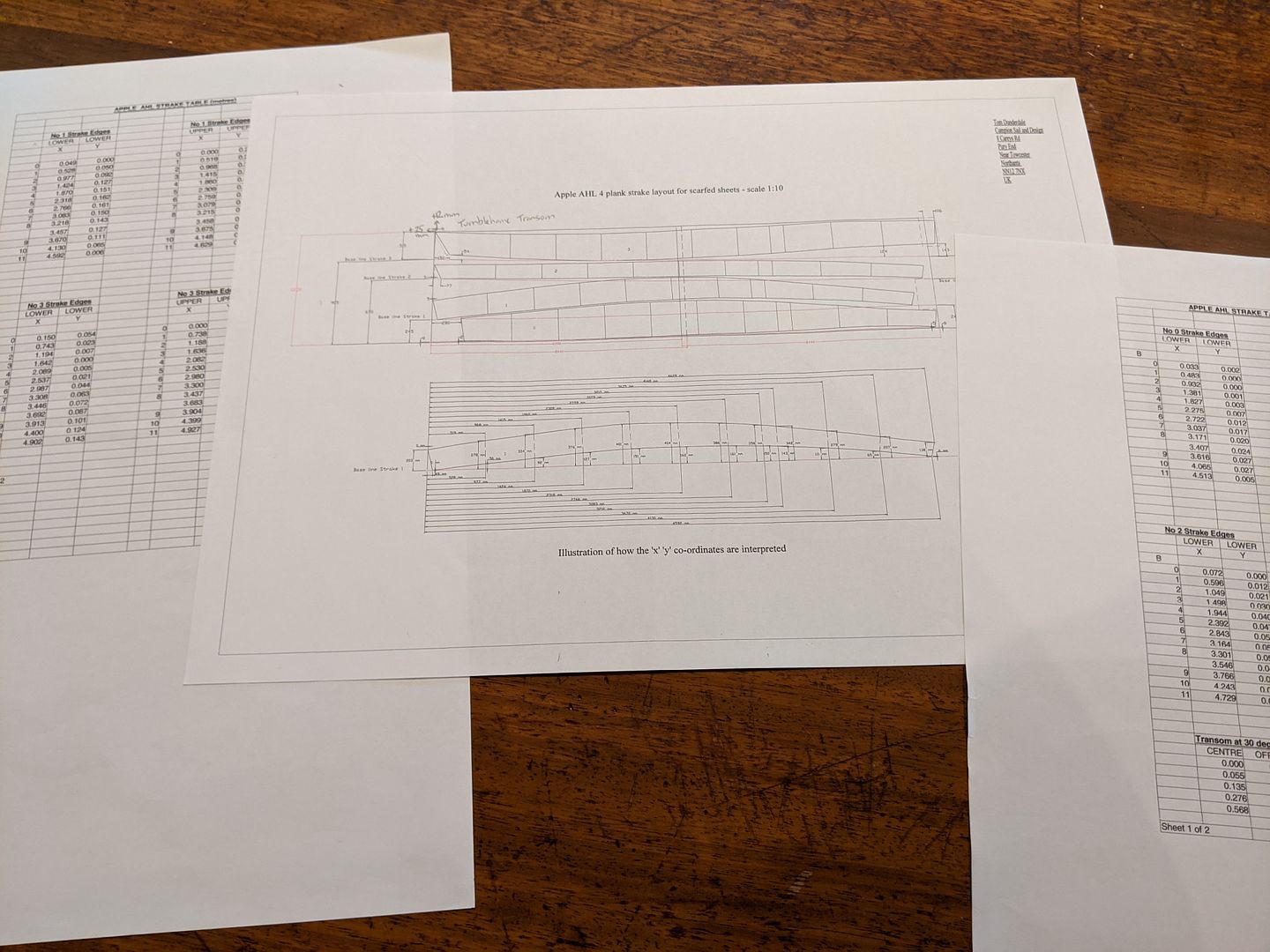
Of course, plywood boards come as 8ft x 4ft so the first job was to scarph them together. It is actually permissible in the plans to butt-join them and fibreglass tape the joint, but I preferred to scarph them.
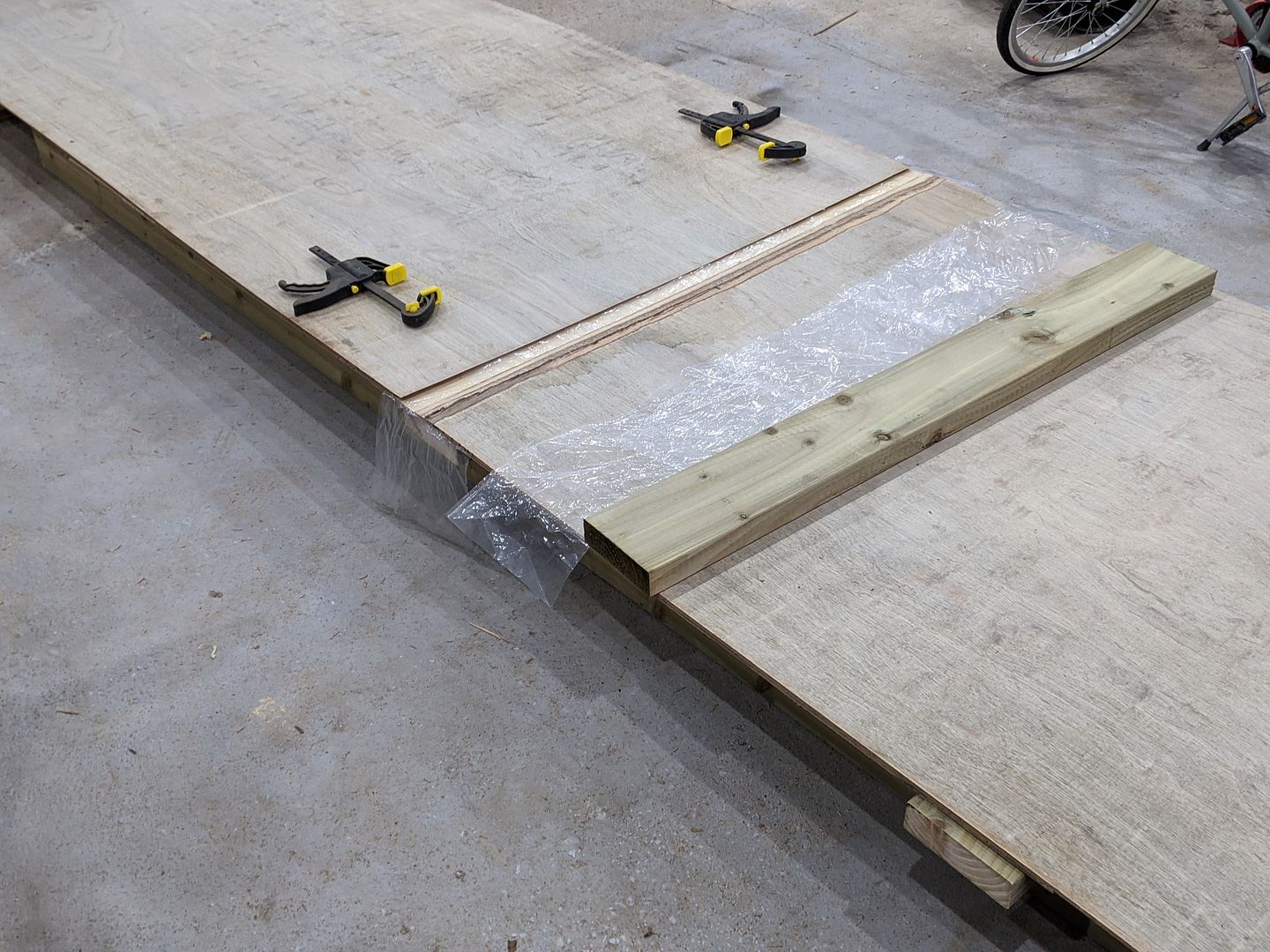
To lazy to make a scarphing jig, I just did it with the power planer and the results were useable but hardly great quality. To make up for lack of quality I thickened up the epoxy a touch with milled fibres.

I broke a plastic clamp whilst clamping the scarphs together for gluing and shortly after this photo went all-metal
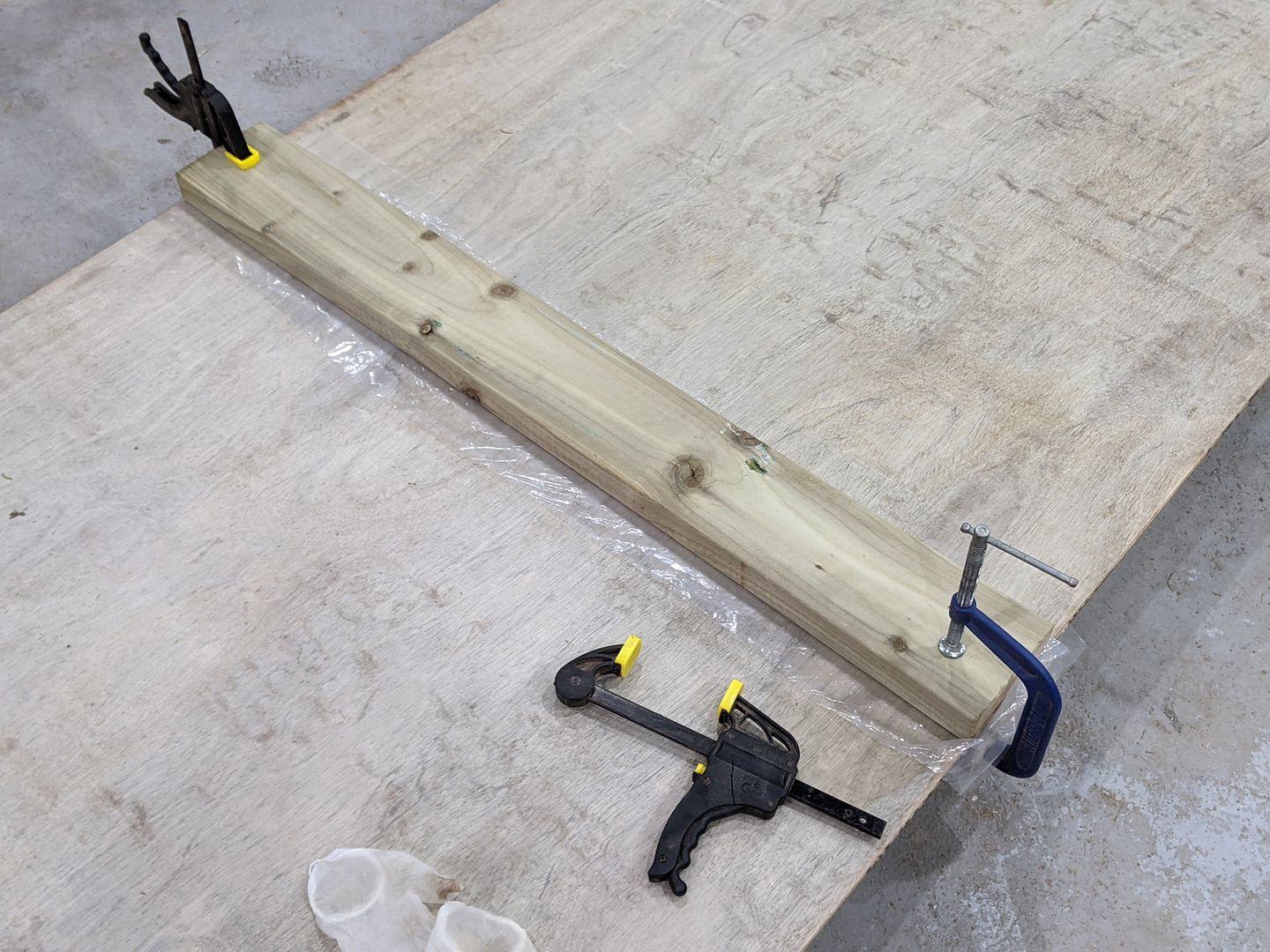
Obviously the polythene was to prevent me gluing the planks I used to distribute the clamping pressure across the whole joint to the joint itself...
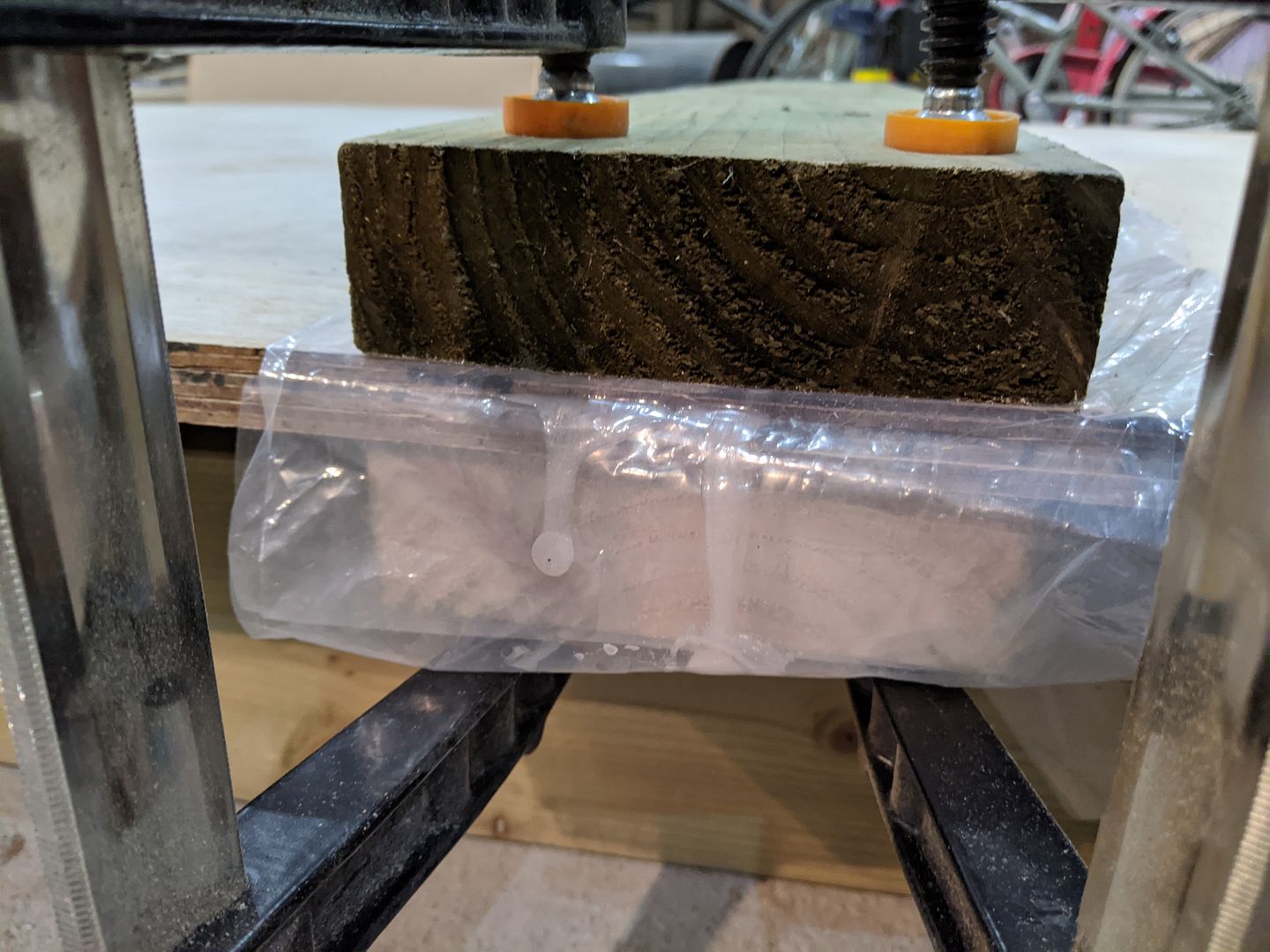
Each plank then needs its own datum measured and marked onto the resultant 16ft board, and a series of stations describing the upper and lower edges are lofted onto the plywood from a table of measurements
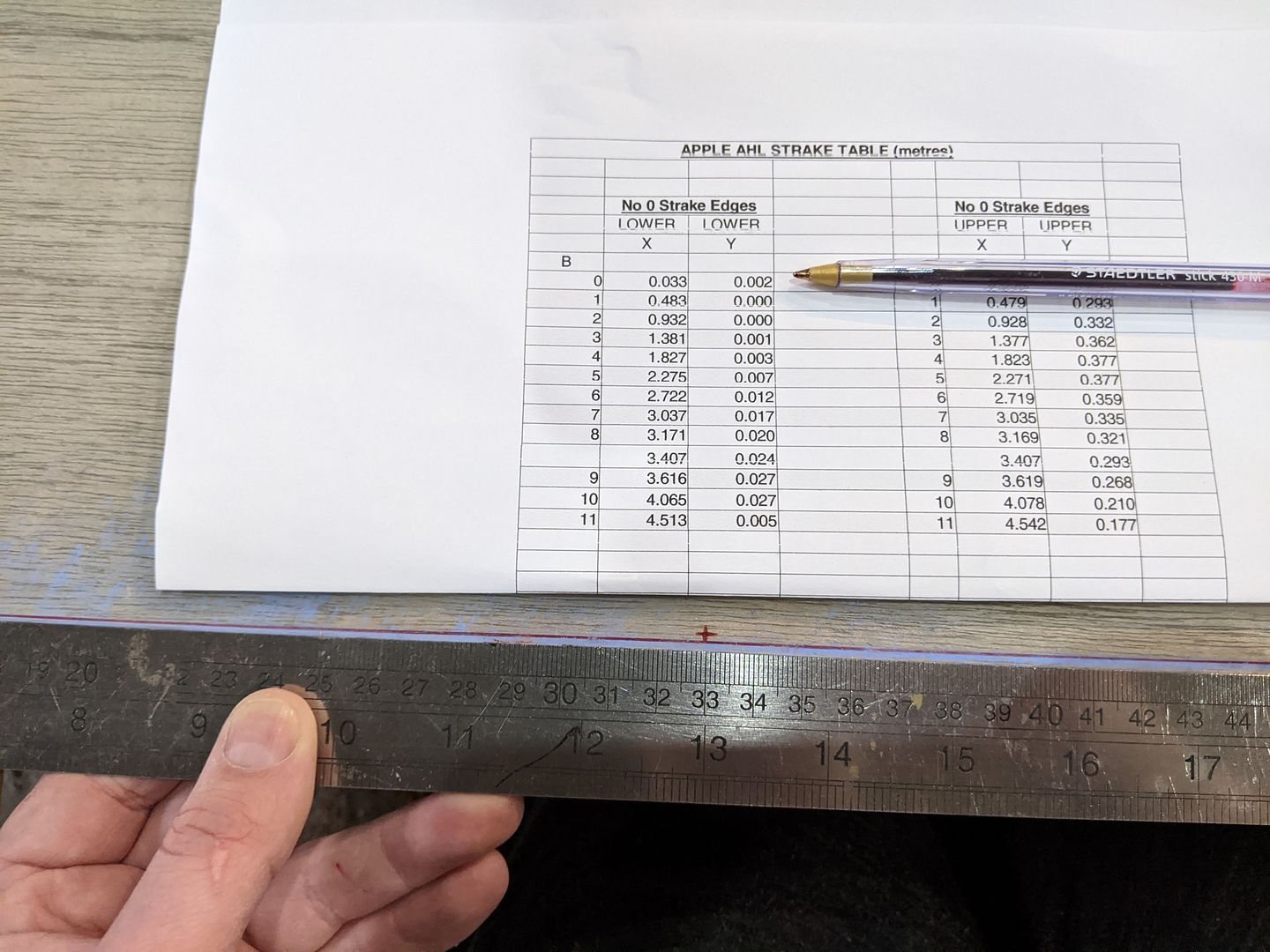
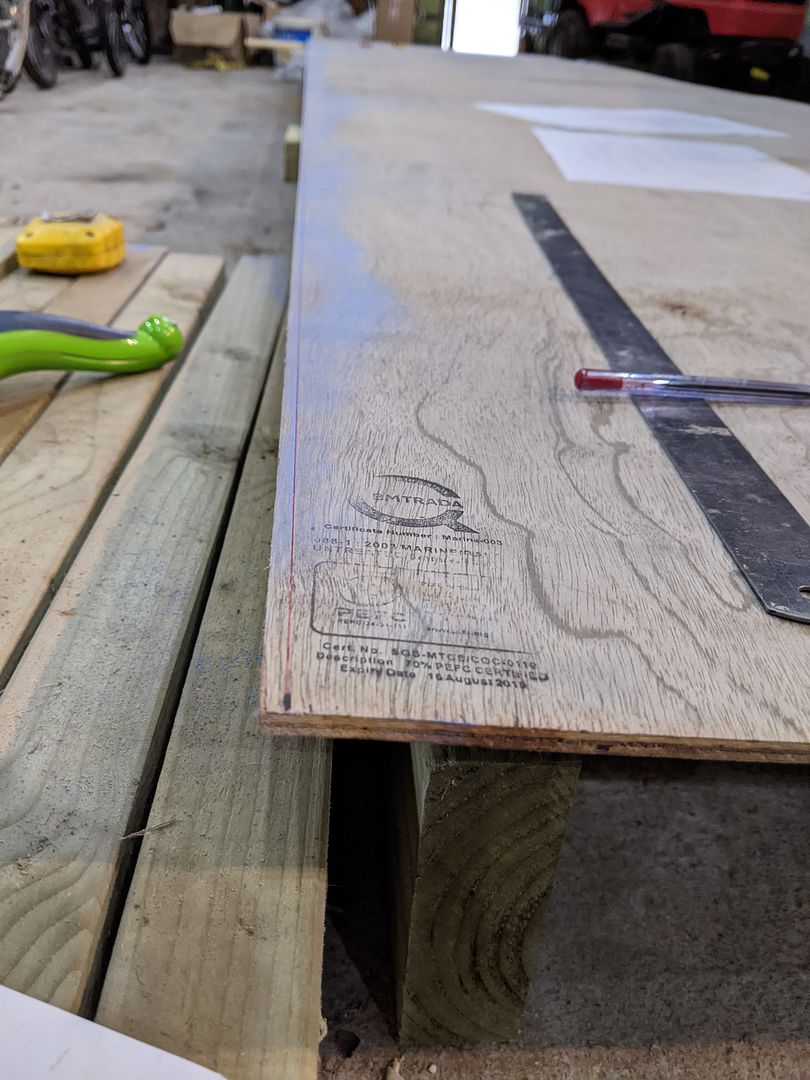
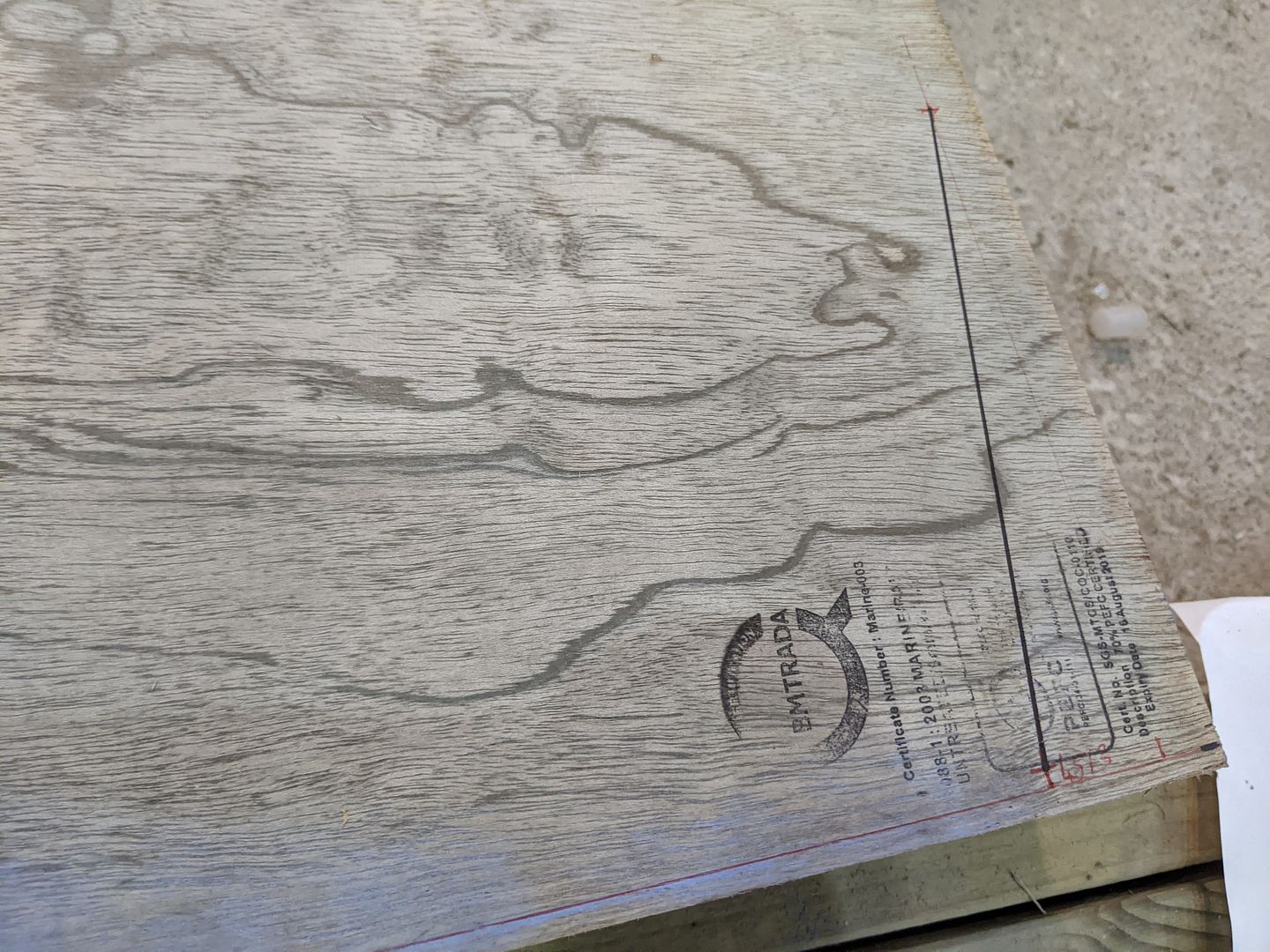
Once all the stations are marked, pins are tapped in to each and a long batton sprung to join the dots with a fair curve to trace out with a pen.

The uppermost plank does need an extra little bit scarphed on to make up the length, but the extra bit is cut from elsewhere on the board. Due to the nesting to get all planks from the one board, they're staggered slightly fore and aft to offset their deepest points.
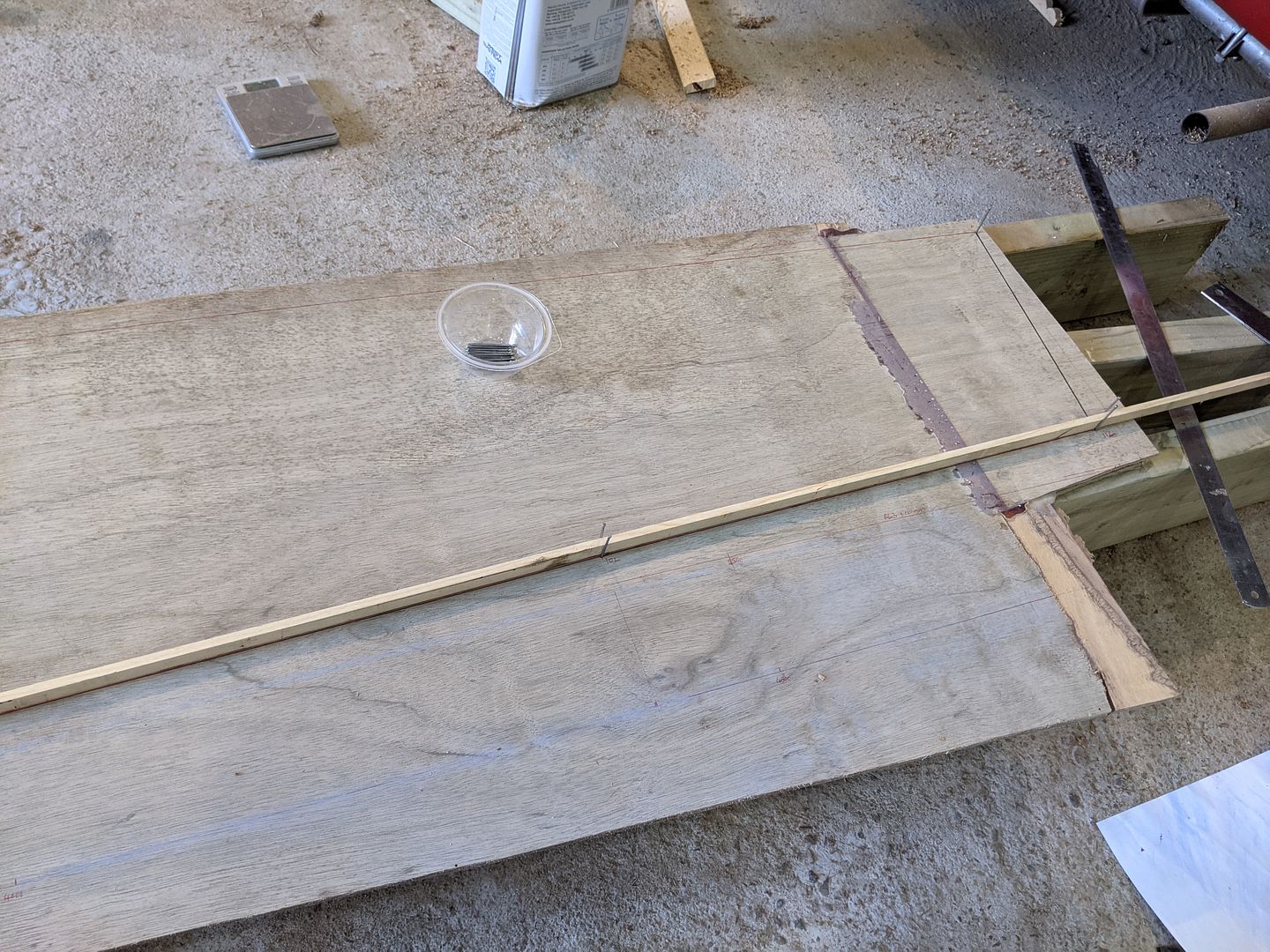
I only marked out the planks on one board, then clamped both boards together tightly, set the cut depth to 12mm on a circular saw with a fairly fine blade with lots of little teeth and cut them out together. Each pair of planks was then clamped together whilst I finished down to the lines.
Here we have a hull kit. Ok, not quite - there's no transom here and I hadn't yet cut out the internal frames. Actually on closer inspection, I'd rough cut the planks for this picture but evidently had had enough fun for one night - so they're still to be finally trimmed down to the lines.
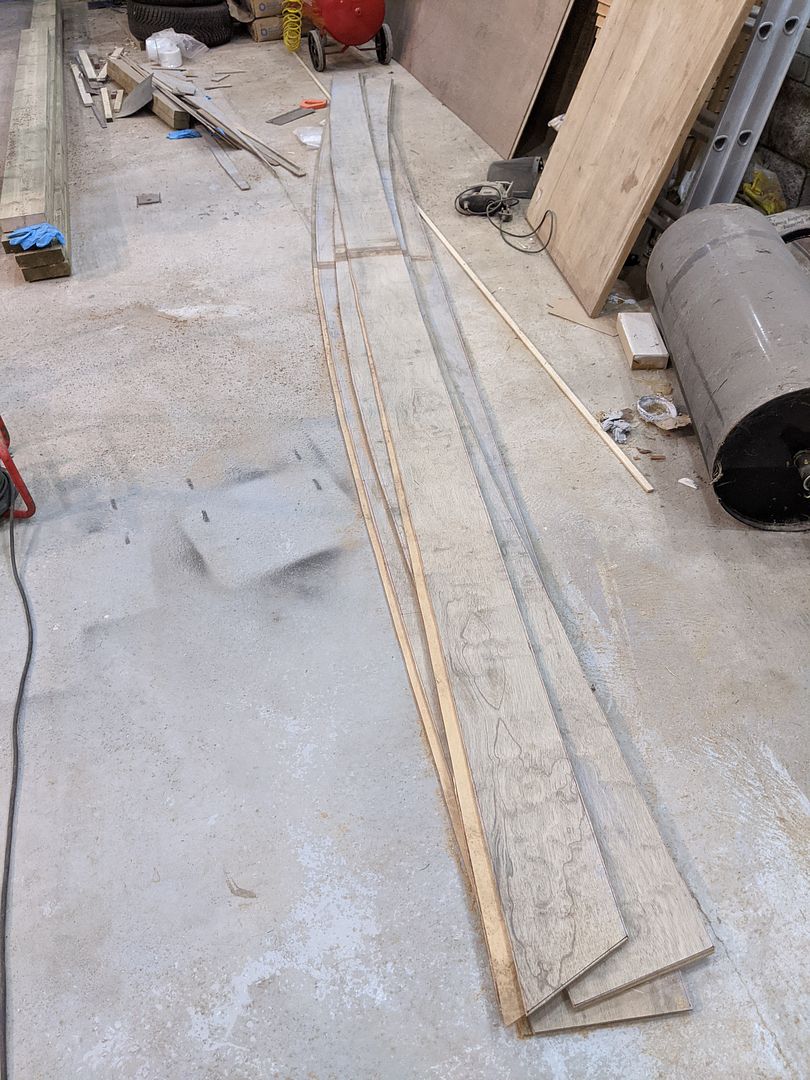
Edited by jamieduff1981 on Tuesday 31st May 20:56
Edited by jamieduff1981 on Wednesday 1st June 07:42
The bit I was most looking forward to was stitching the planks together of course. It all happened really fast although it quickly became a 2 person job from the 3rd plank onwards as it was quite unwieldy trying to support a 16ft long floppy plywood strip whilst carefully drilling two holes and tie-wrapping it to another.
The keel was easy. Not knowing what to expect, I used twice as many tie-wraps as turned out to be necessary. The top corner of the stem was bolted with penny washers as the twist here was substantial and the designer warned that a tie-wrap here would just fail and even bolts might pull through without big washers.
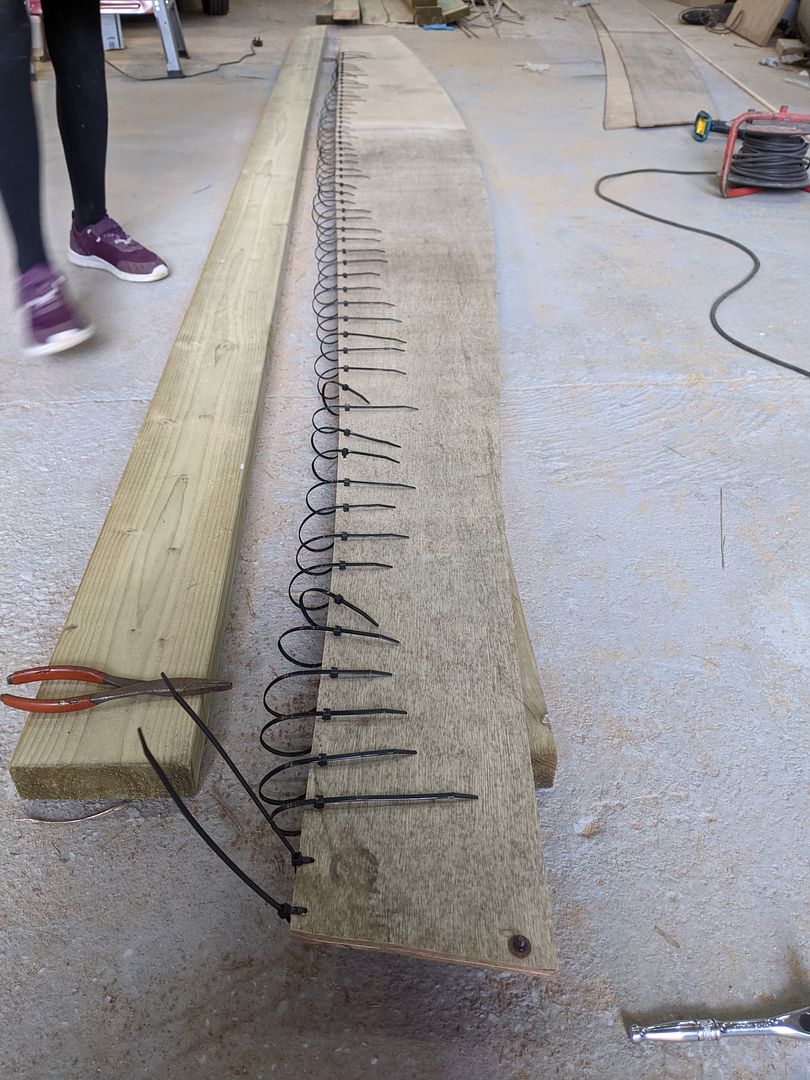
I was in no particular rush so I turned it upside down and left it overnight to start to relax into its new unnatural shape

Stitching on the second plank was easy enough on the floor, and I started jamming chunks of timber in the bow to prise the shape open.
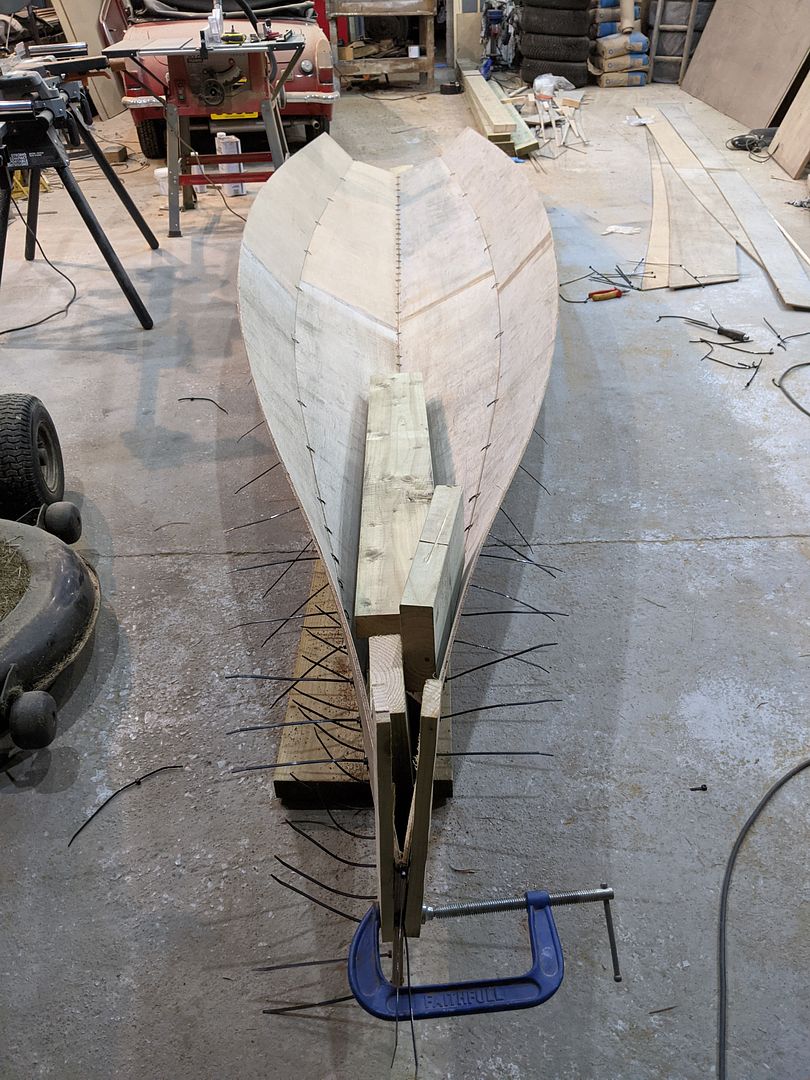
I was fearing that I'd fundamentally screwed up the lofting though as the planks just wouldn't close up at the bow.
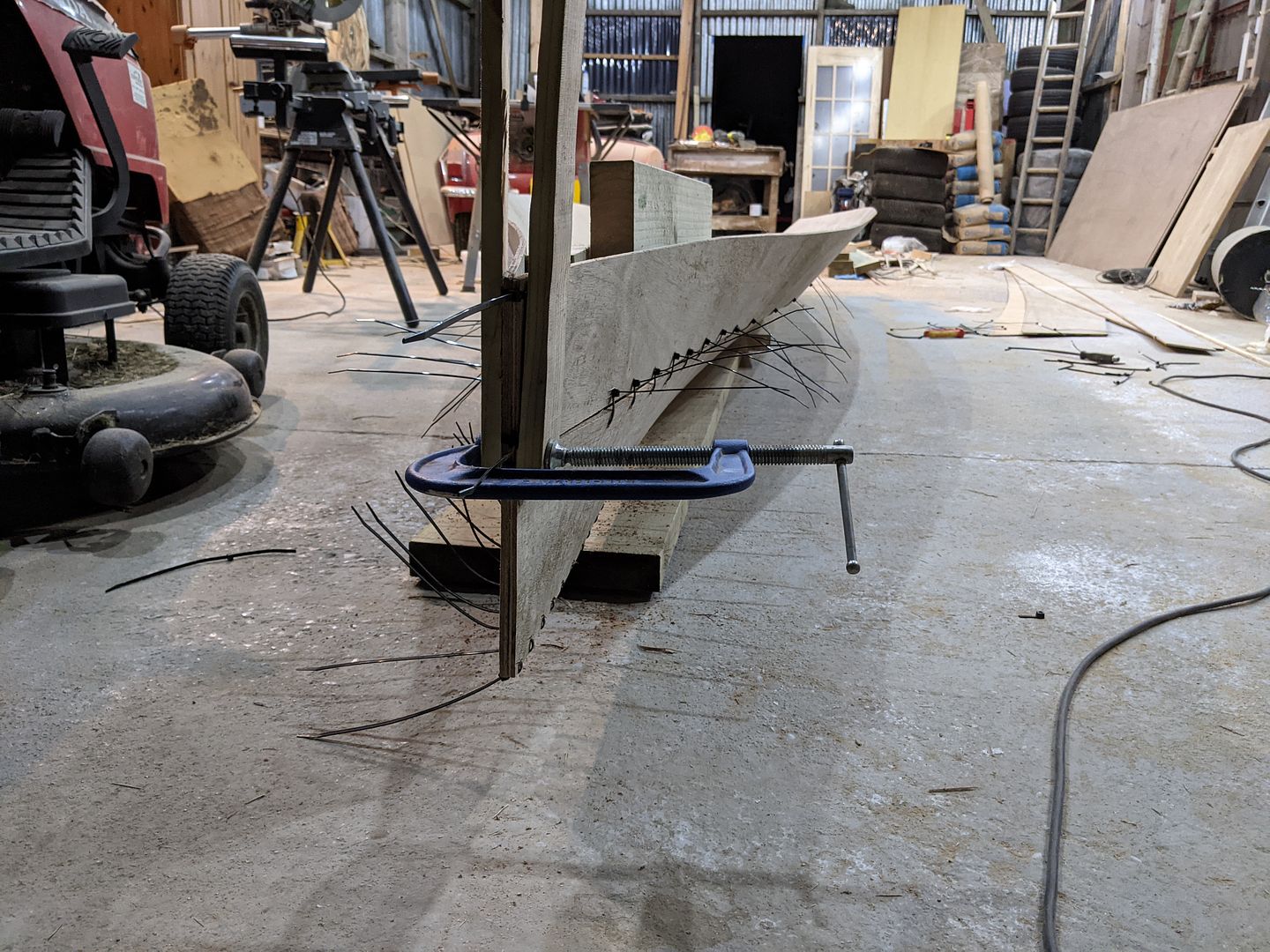
I realised that whilst the garage floor was flat, the keel wasn't supposed to be. Having the hull sat on the floor was effectively hogging the hull. I didn't know what this would mean, but nothing good, so it was time to knock up a couple of trestles and the family helped me lift the hull up onto them. As it by magic, all the tiewraps up front went slack and the gaps at the bow vanished. You'll notice I've added the transom and the biggest frame inside the hull - the one immediately forward of the mast.

The boat seemed to be in its most fragile state to date like this though. Without the final planks on, the hull kept trying to turn "inside out" over the aft trestle.
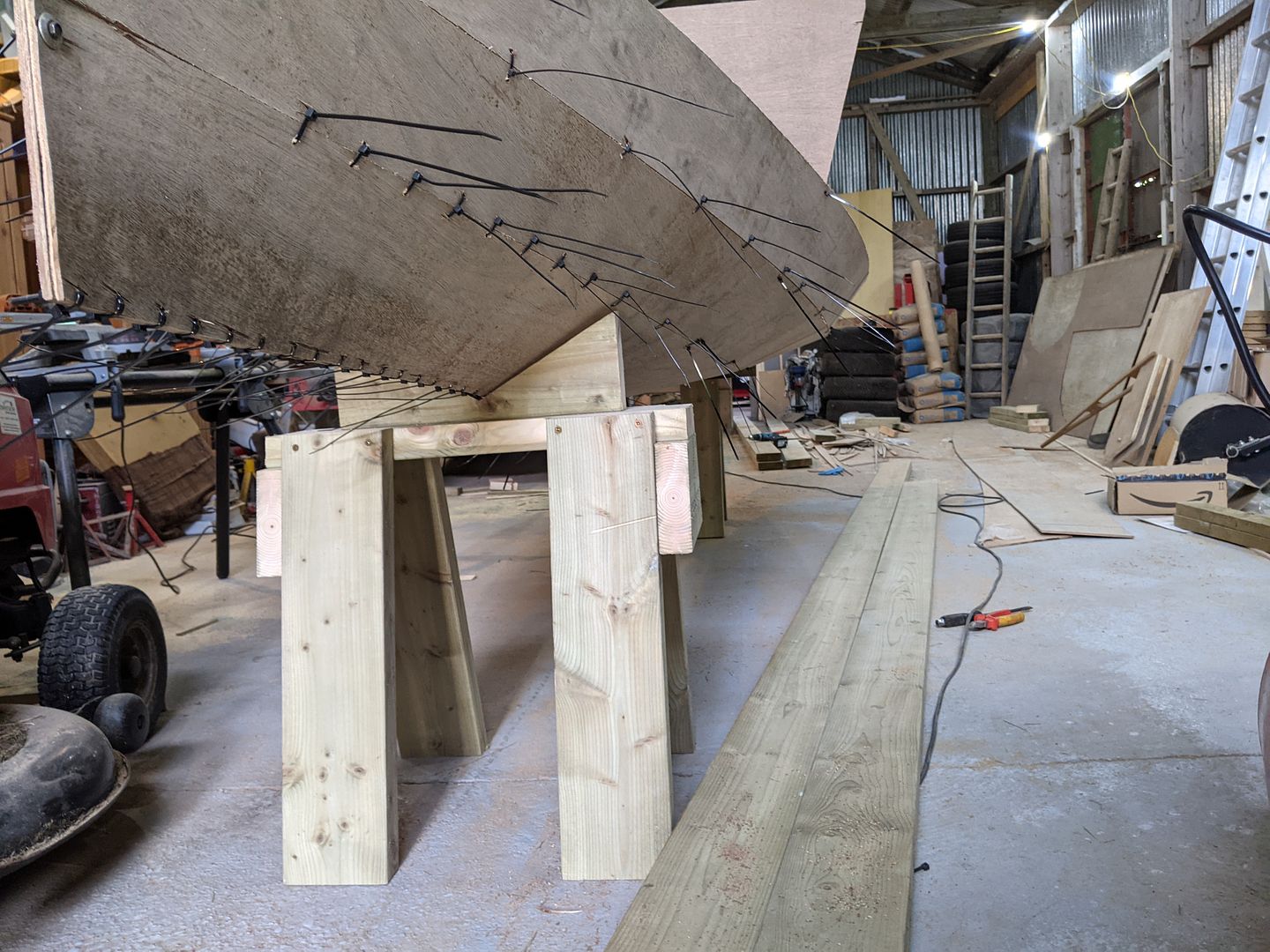
The keel was easy. Not knowing what to expect, I used twice as many tie-wraps as turned out to be necessary. The top corner of the stem was bolted with penny washers as the twist here was substantial and the designer warned that a tie-wrap here would just fail and even bolts might pull through without big washers.
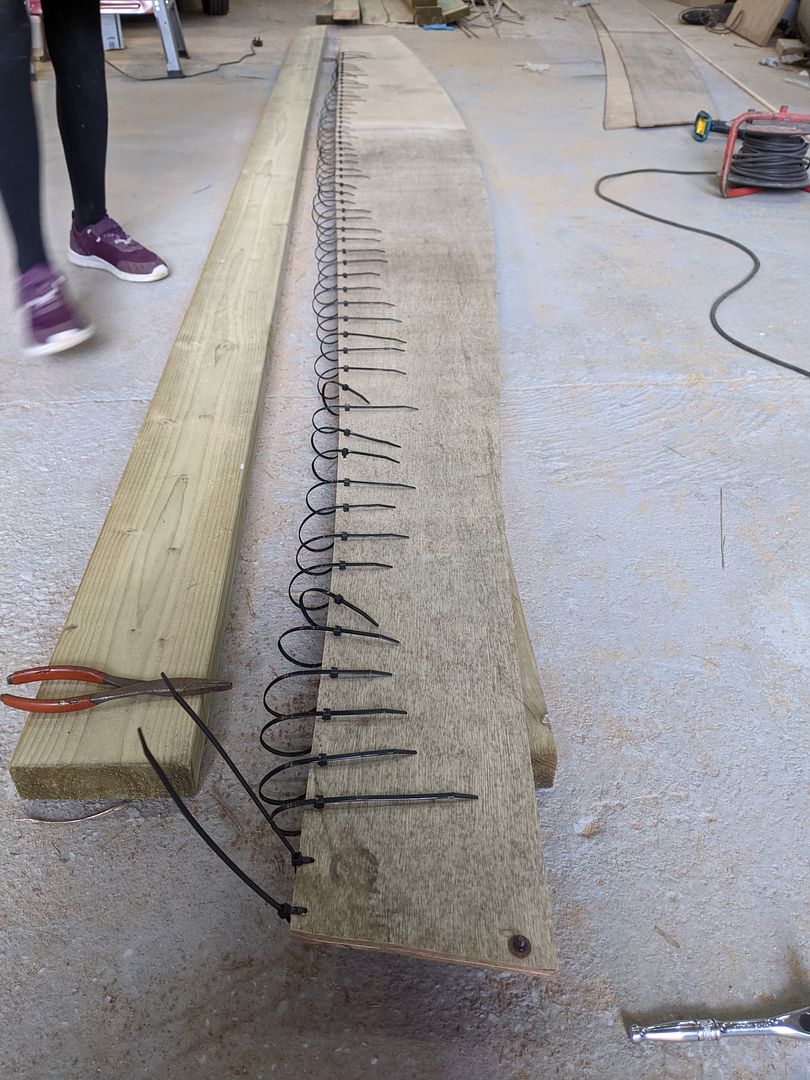
I was in no particular rush so I turned it upside down and left it overnight to start to relax into its new unnatural shape

Stitching on the second plank was easy enough on the floor, and I started jamming chunks of timber in the bow to prise the shape open.
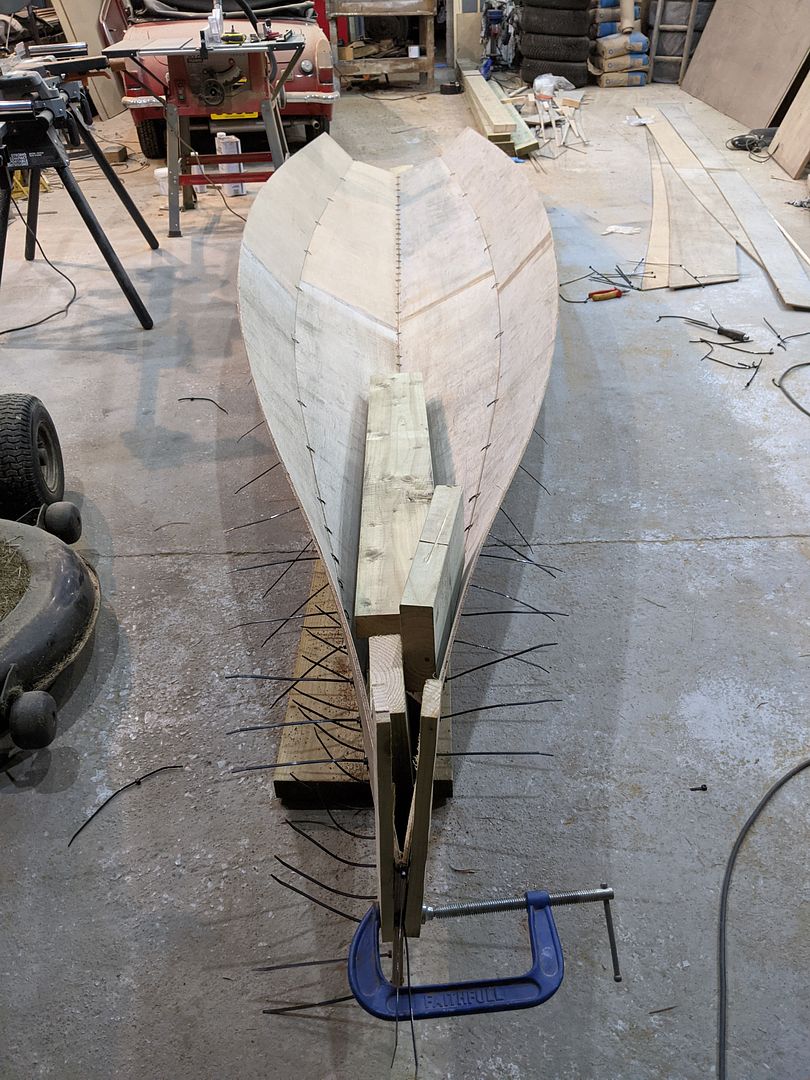
I was fearing that I'd fundamentally screwed up the lofting though as the planks just wouldn't close up at the bow.
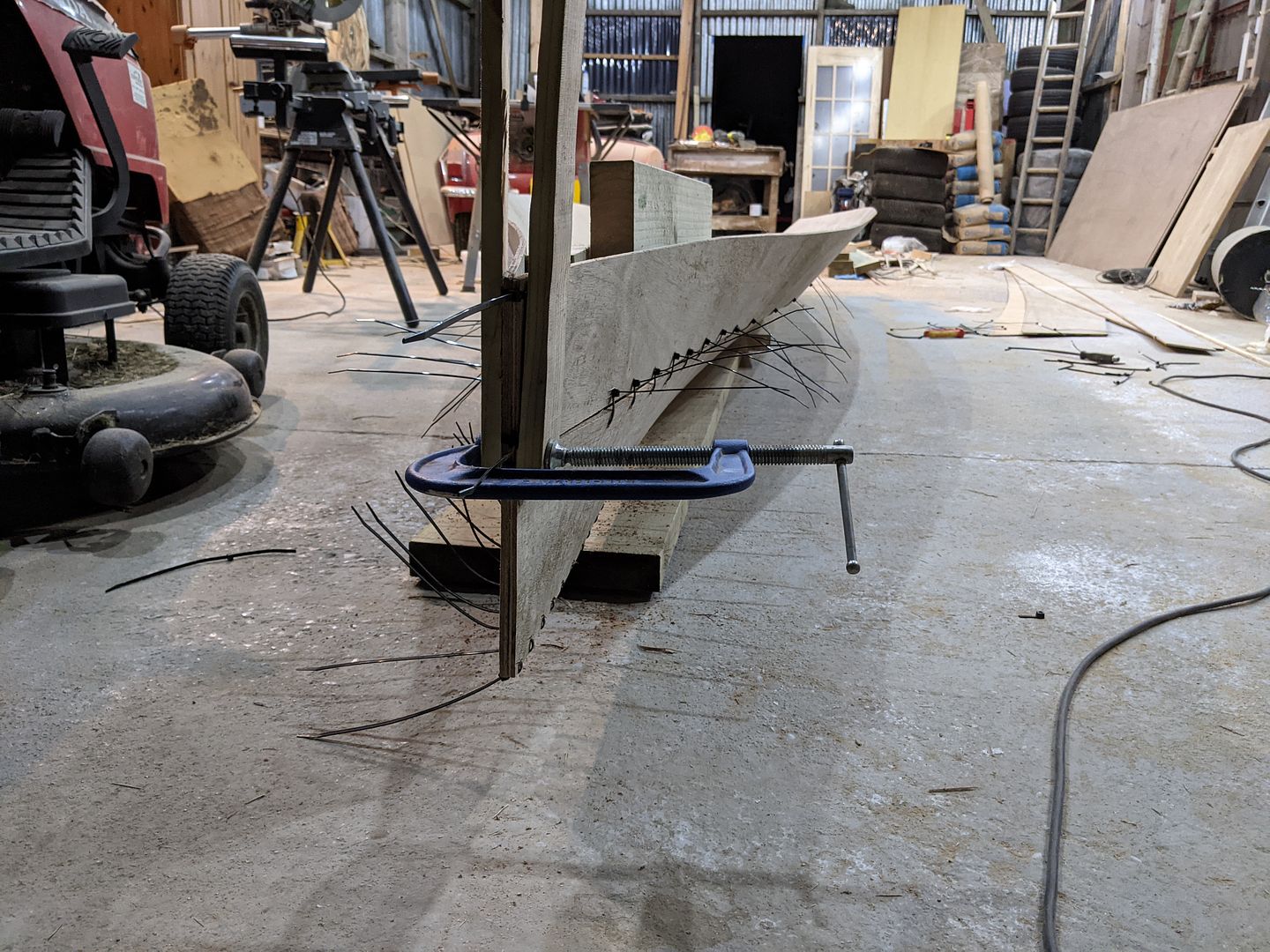
I realised that whilst the garage floor was flat, the keel wasn't supposed to be. Having the hull sat on the floor was effectively hogging the hull. I didn't know what this would mean, but nothing good, so it was time to knock up a couple of trestles and the family helped me lift the hull up onto them. As it by magic, all the tiewraps up front went slack and the gaps at the bow vanished. You'll notice I've added the transom and the biggest frame inside the hull - the one immediately forward of the mast.

The boat seemed to be in its most fragile state to date like this though. Without the final planks on, the hull kept trying to turn "inside out" over the aft trestle.
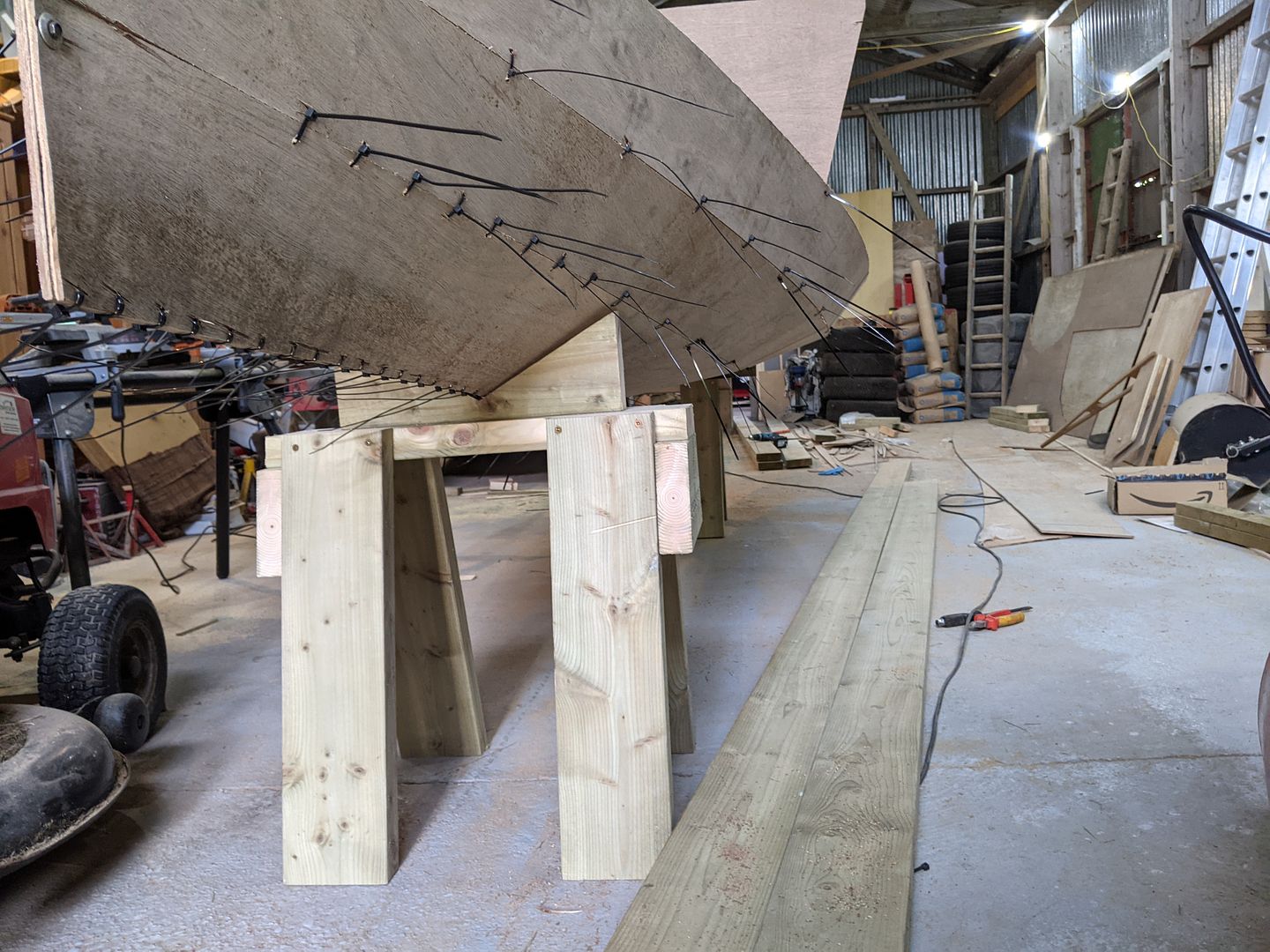
Edited by jamieduff1981 on Monday 4th October 13:41
Edited by jamieduff1981 on Friday 22 March 08:06
Edited by jamieduff1981 on Friday 22 March 08:07
Edited by jamieduff1981 on Friday 22 March 08:27
Hard-Drive said:
Yes! This is great. Let's have all the details! How long do you expect it to take...looks like you've done a lot of the work already!
I've done something similar although more of a major conversion/surgery job, rather than a new build, and it was on something a bit quicker! It started out as a very old £300 single wire, tin-rig Cherub, and ended up as a wider, longer, twin-wire big carbon rig boat that I won a National Championships with. There's nothing more satisfying than sailing something you've done a lot of design and building work on.
That's bloody brilliant, by the way.I've done something similar although more of a major conversion/surgery job, rather than a new build, and it was on something a bit quicker! It started out as a very old £300 single wire, tin-rig Cherub, and ended up as a wider, longer, twin-wire big carbon rig boat that I won a National Championships with. There's nothing more satisfying than sailing something you've done a lot of design and building work on.
I started half-baked around October last year, but bad weather / cold / damp / anti-epoxy conditions meant I didn't really start properly until February. I did nothing in May as I bought an XJ-S and have been trying to make sure that's up to the job of a trip to Orkney in August, but the time has come to crack on again with the boat. Hopefully late next summer??? Maybe?
Hi folks,
I'm glad this is vaguely interesting for some. I've got some more photos to upload to bring this up to date then we'll be real-time and I'll need to do some actual work to make actual progress again. I'm a bit frightened on the next thing I have to do and am therefore procrastinating
I'm glad this is vaguely interesting for some. I've got some more photos to upload to bring this up to date then we'll be real-time and I'll need to do some actual work to make actual progress again. I'm a bit frightened on the next thing I have to do and am therefore procrastinating

My daughters helped me hang the fourth planks one evening, which despite them being entirely typical in that they love playing with electronic tech, they enjoyed. This leads me to believe that as a generation of parents we can either be morons who berate the young for enjoying the technology we create, or we can create the opportunities for them to enjoy more physical stuff and be part of the solution rather than the problem.
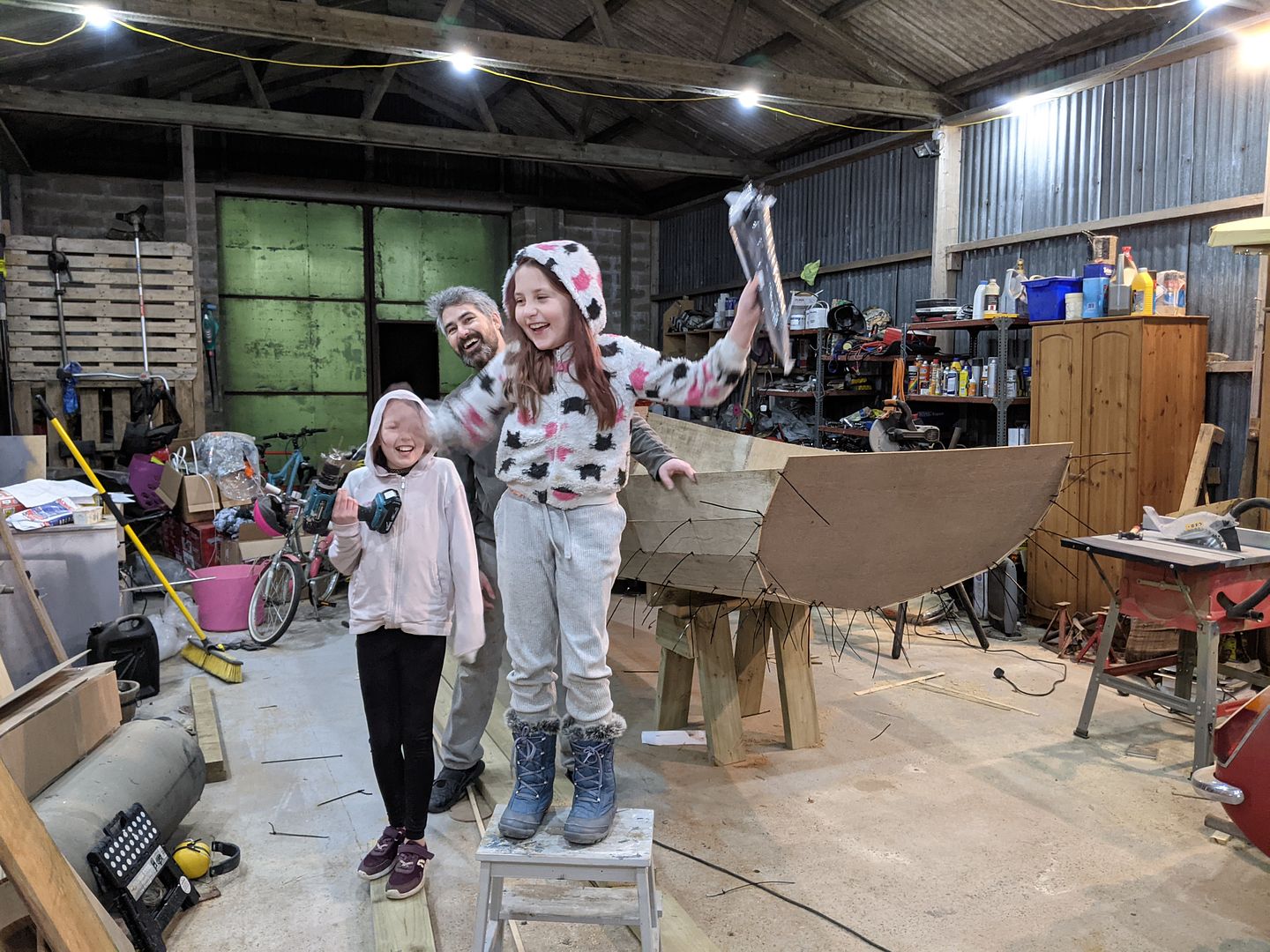
That really didn't stiffen up the boat as much as I thought it might though, so we lofted out and cut a couple more internal frames which helped-ish
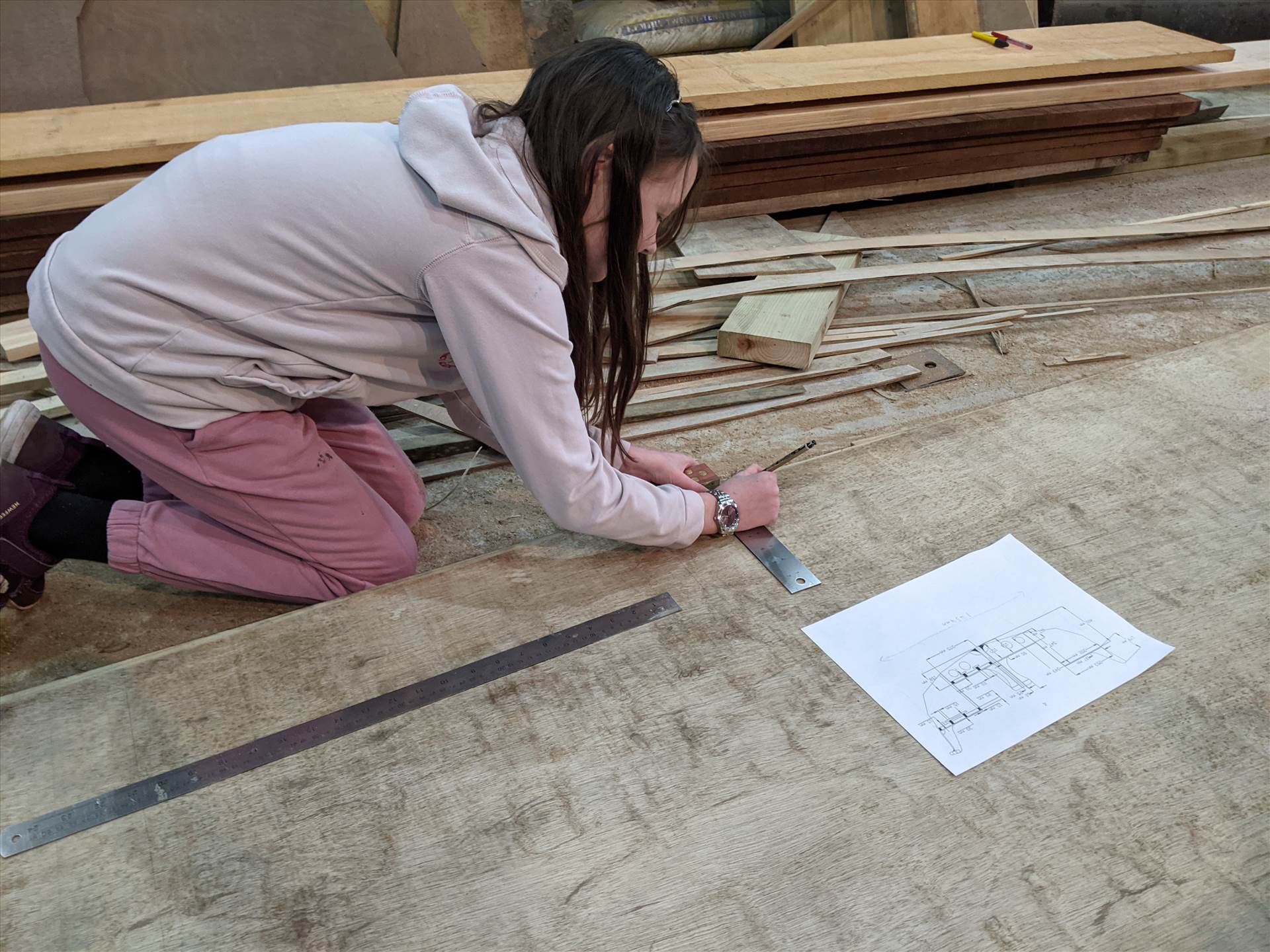
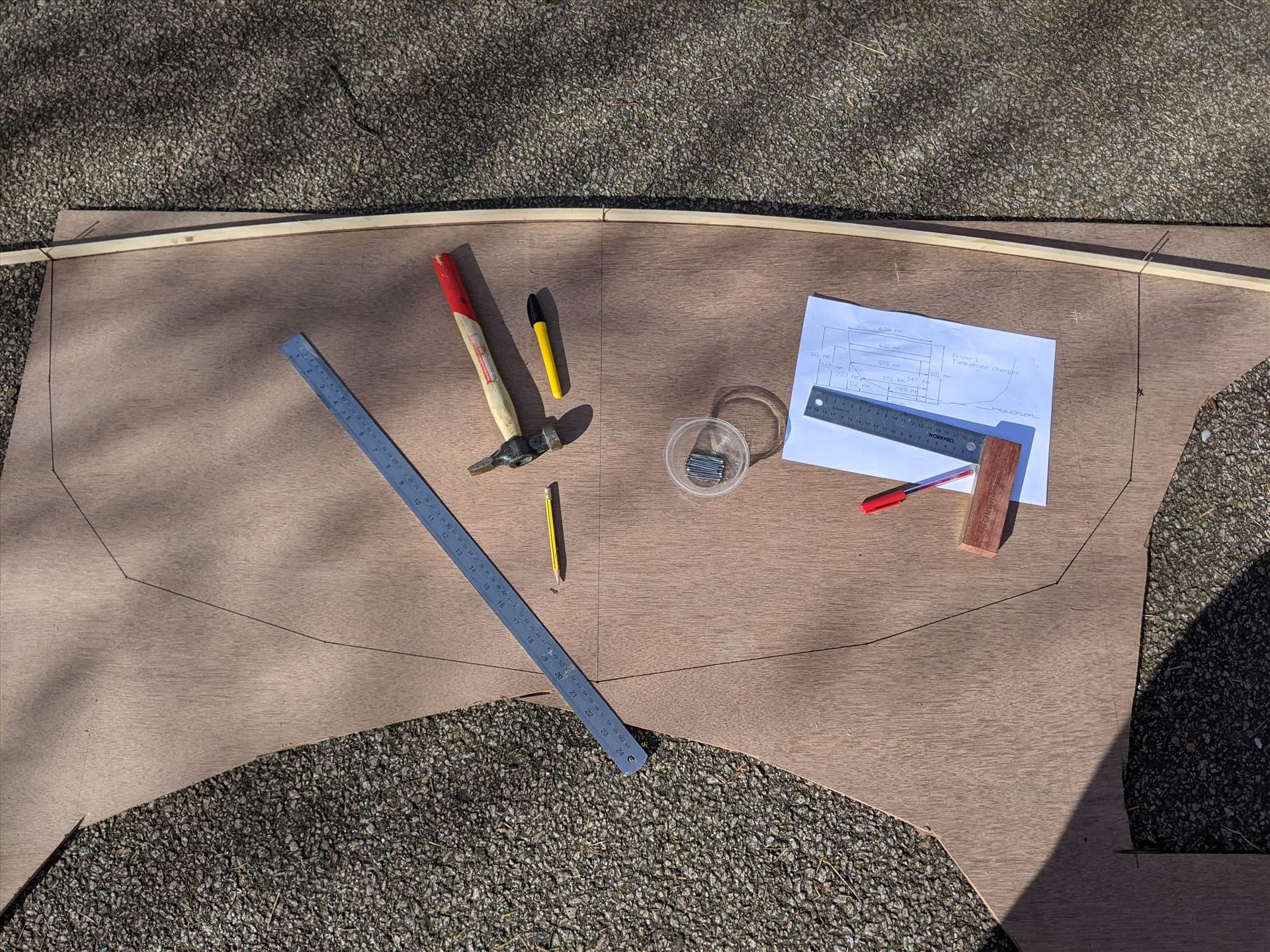
They were a struggle to fit though and the planks, especially aft, started trying to buck out and overlap. You might notice we marked the deck camber on but cut the frames out square. This was so I could easily spirit-level the frames to level them out down the hull's length to avoid locking any twist into the hull. We flipped the hull over and stood it on two of its frames.
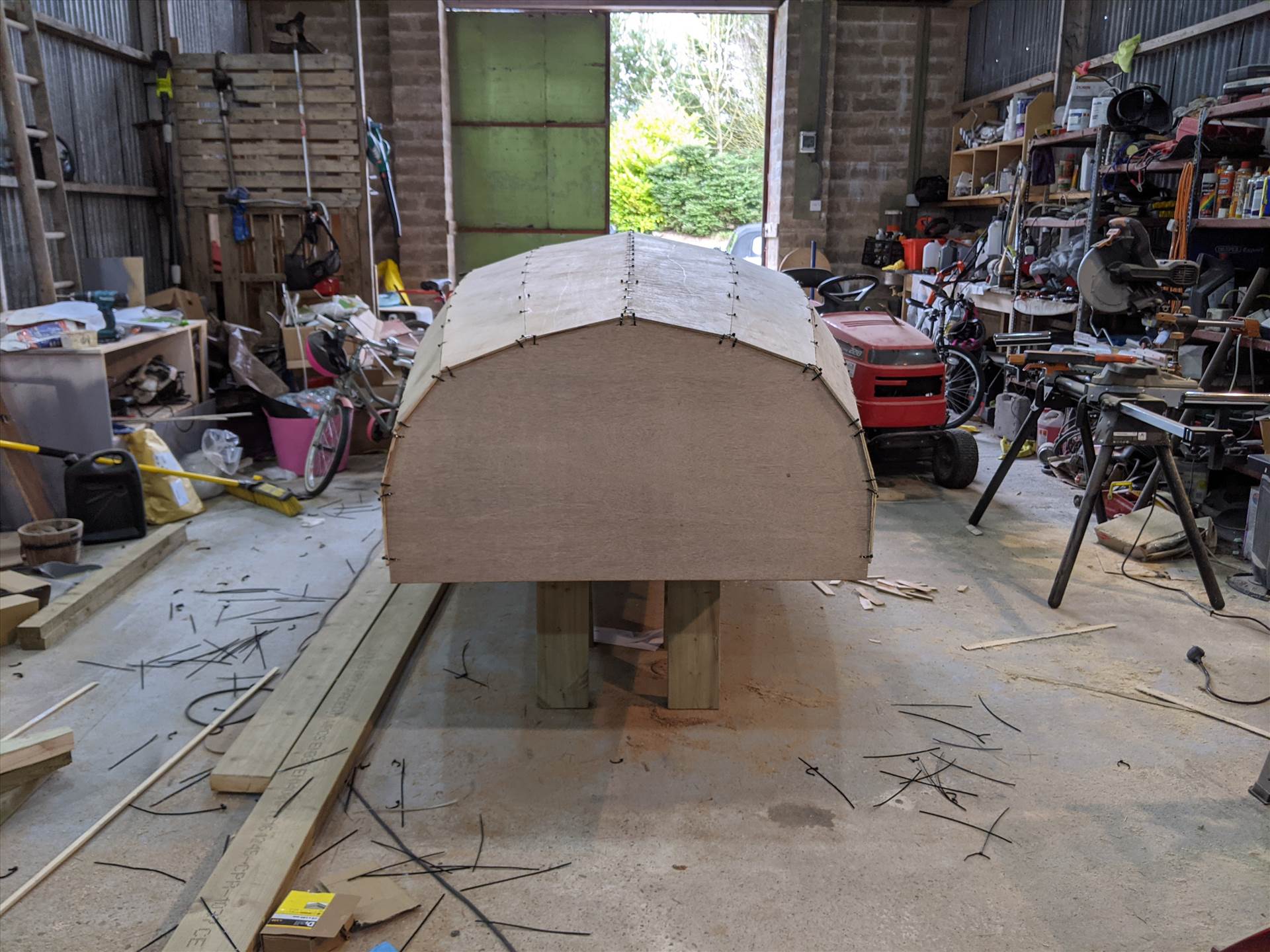
Once again, all the unhappy hull planks instantly and automatically sorted themselves out and the internal frames suddenly notched nicely into each chine.
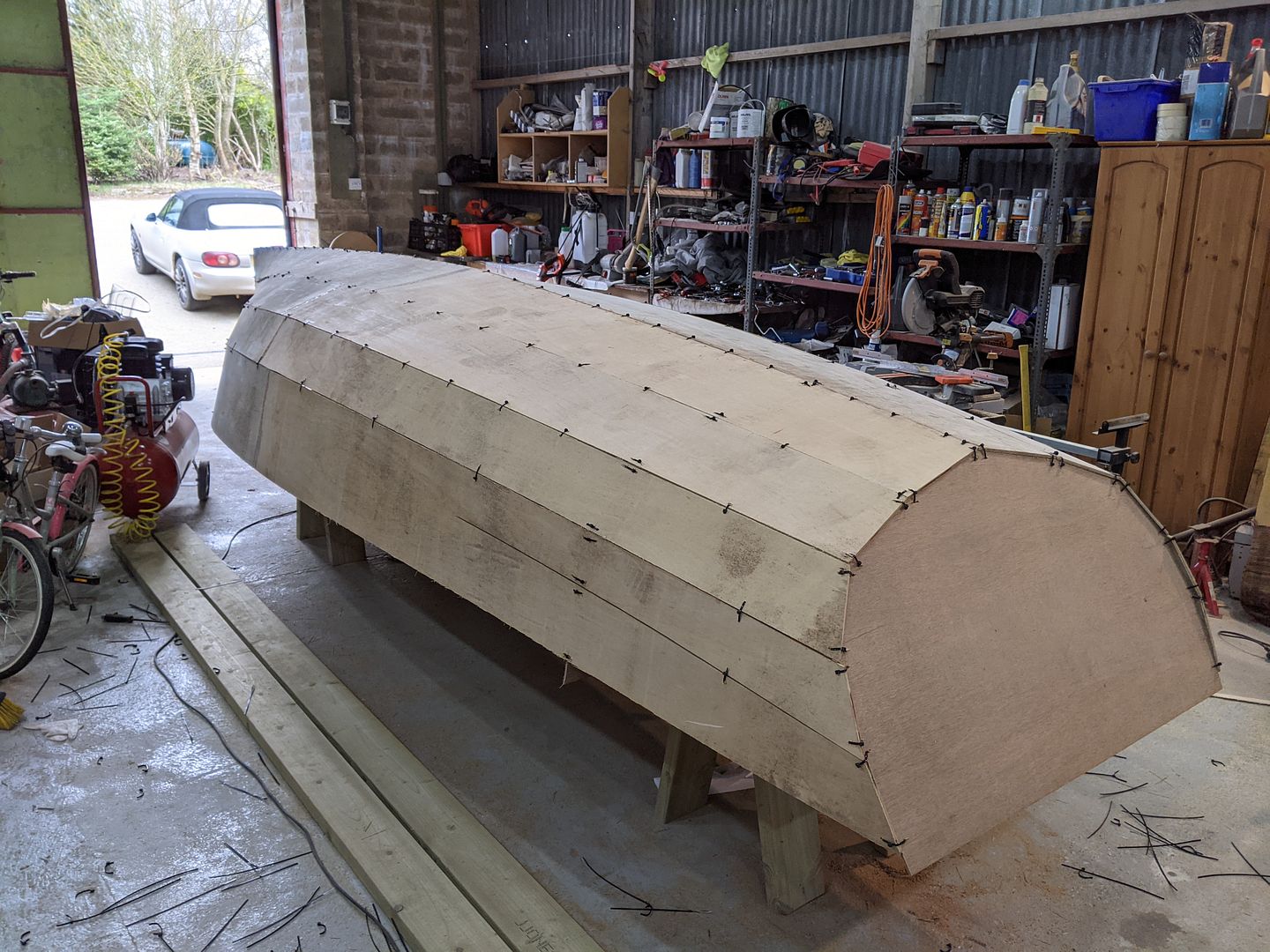
You may spot that the big wide upper plank has been slashed at the aft end. The plans give two options for the transom shape, either a straight one or a tumblehome version which is what I chose. I think it looks a bit nicer. As mentioned previously there's a lower rubbing strip below the gunwale half way down that big plank. Combined with the tumblehome transom it gives a very nice appearance and makes the hull look more shapely.
I don't think this looks at all bad for plywood sheets
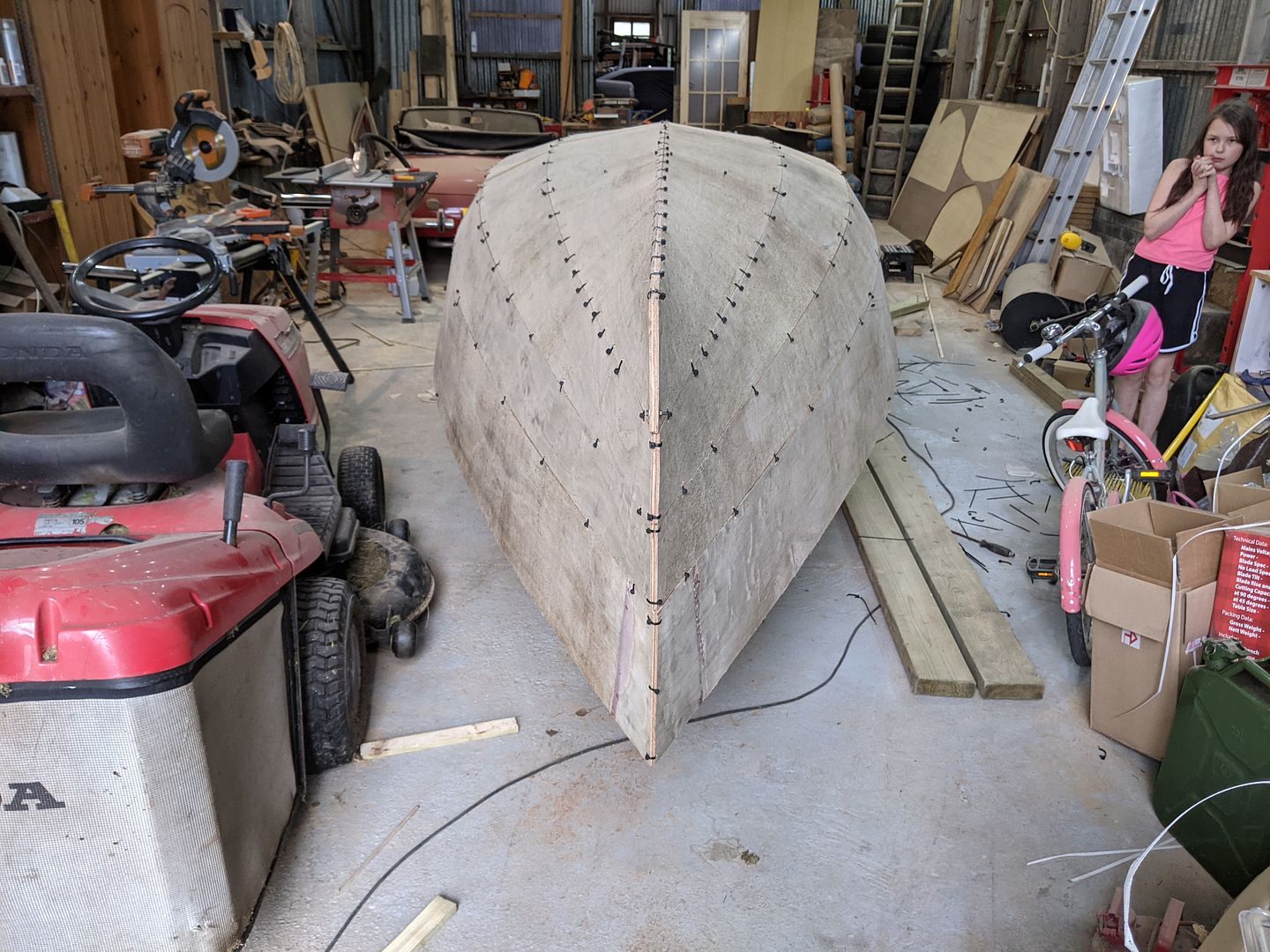
With the hull upside down, I spot glued in various places between the planks with dollops of 5 minute epoxy (which only takes 1 hour to harden - uh huh -that's how it's labelled and that's what the instructions say) to tack them together properly. Despite being mostly happy in its new shape, the planks would in places become slightly misaligned and I don't want wavy chines...
We flipped the boat back over again after this. 50mm wide fibreglass tape was cut into short lengths.
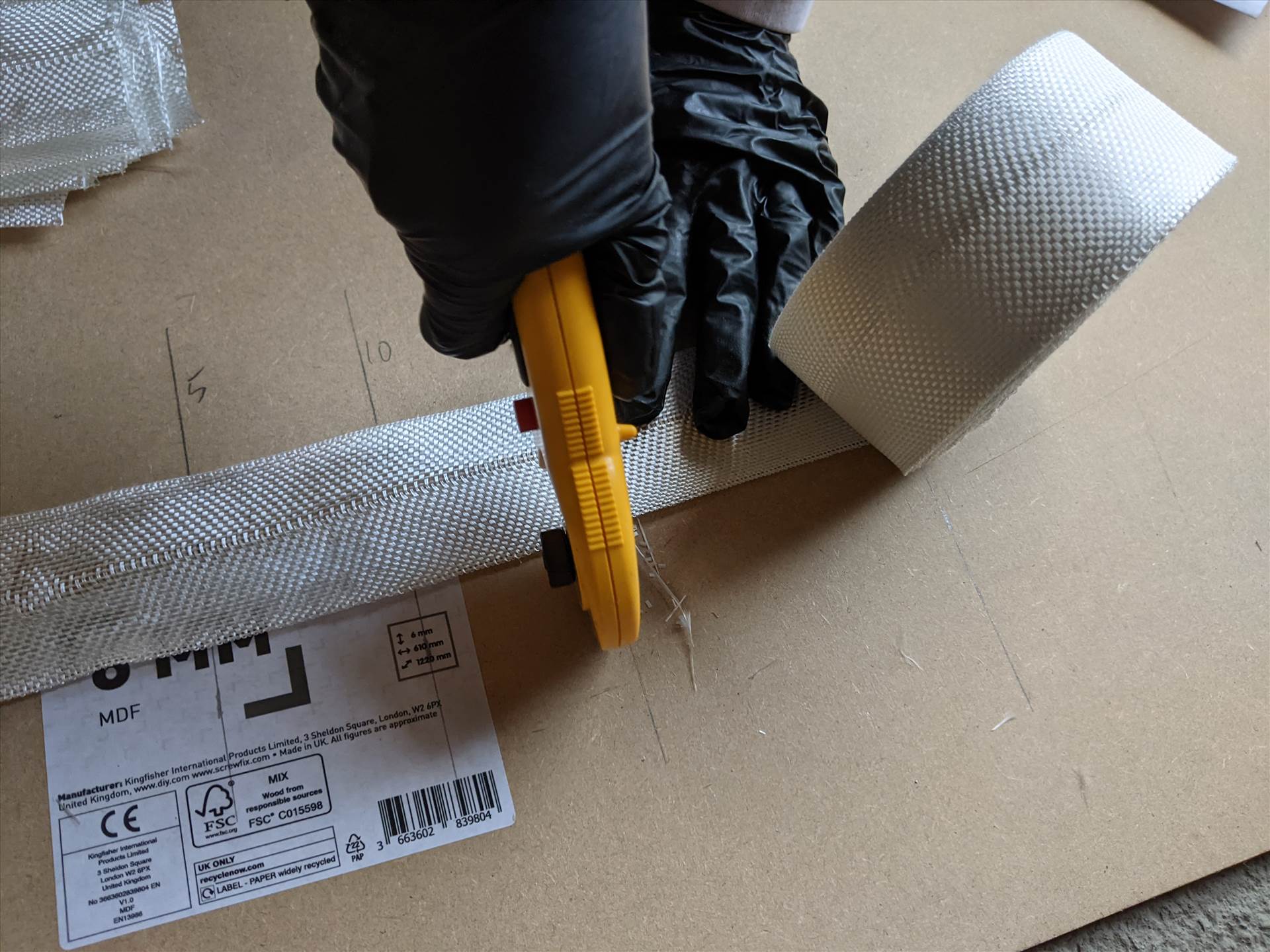
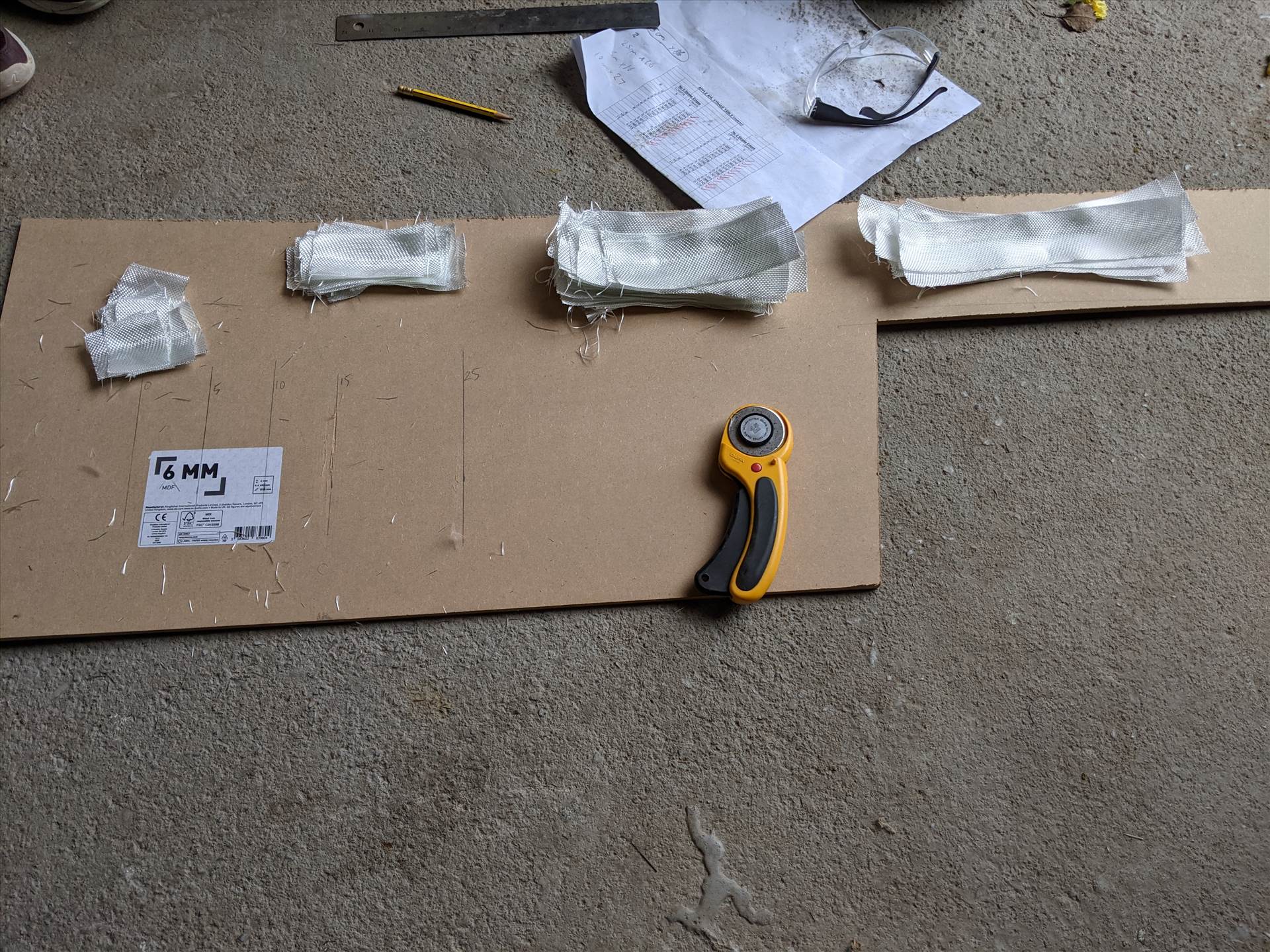
The boat has a 5ft beam so I couldn't actually reach the keel from outside, so I lifted my daughter in as she's much lighter than me and wouldn't collapse the somewhat precarious hull (although you'd think I'd lifted her into a minefield the way she gingerly shuffled about...) and she painted in the first row of fibreglass tapes between the tie-wraps.
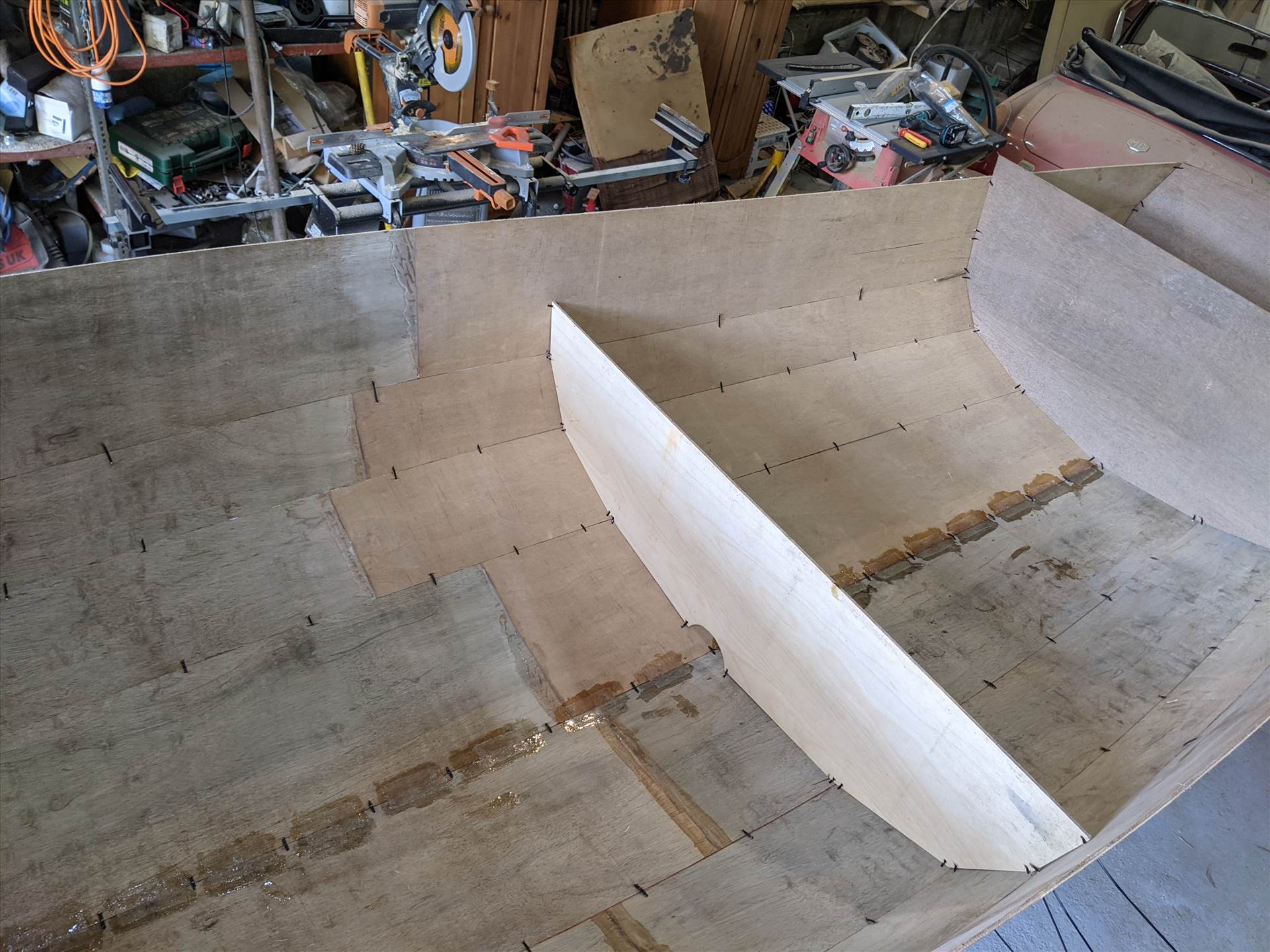
There were quite a lot to do. I used 200 grams of epoxy resin at a time. I found using more than that caused it to exotherm which is dangerous, useless, and a complete waste of money.
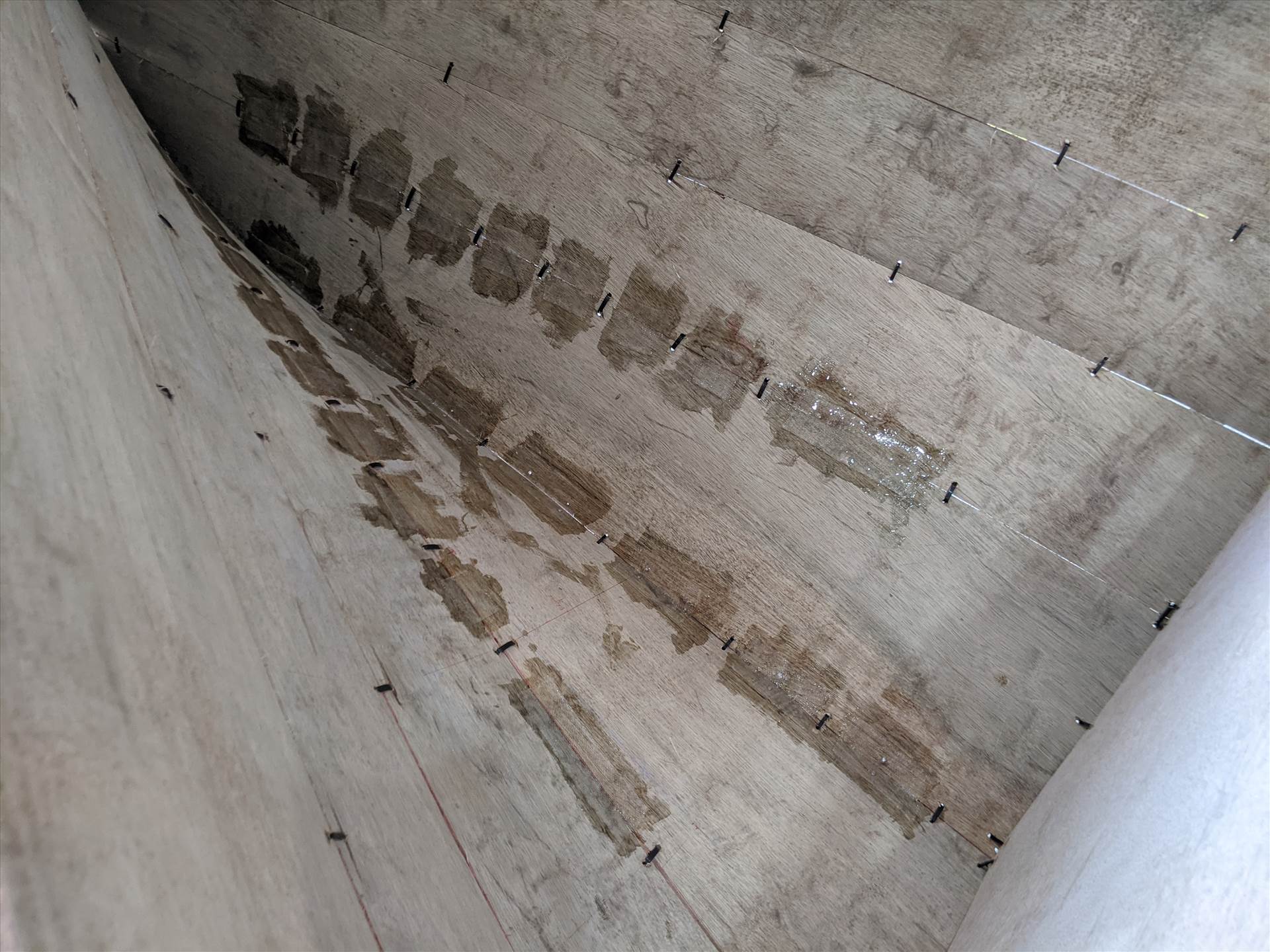
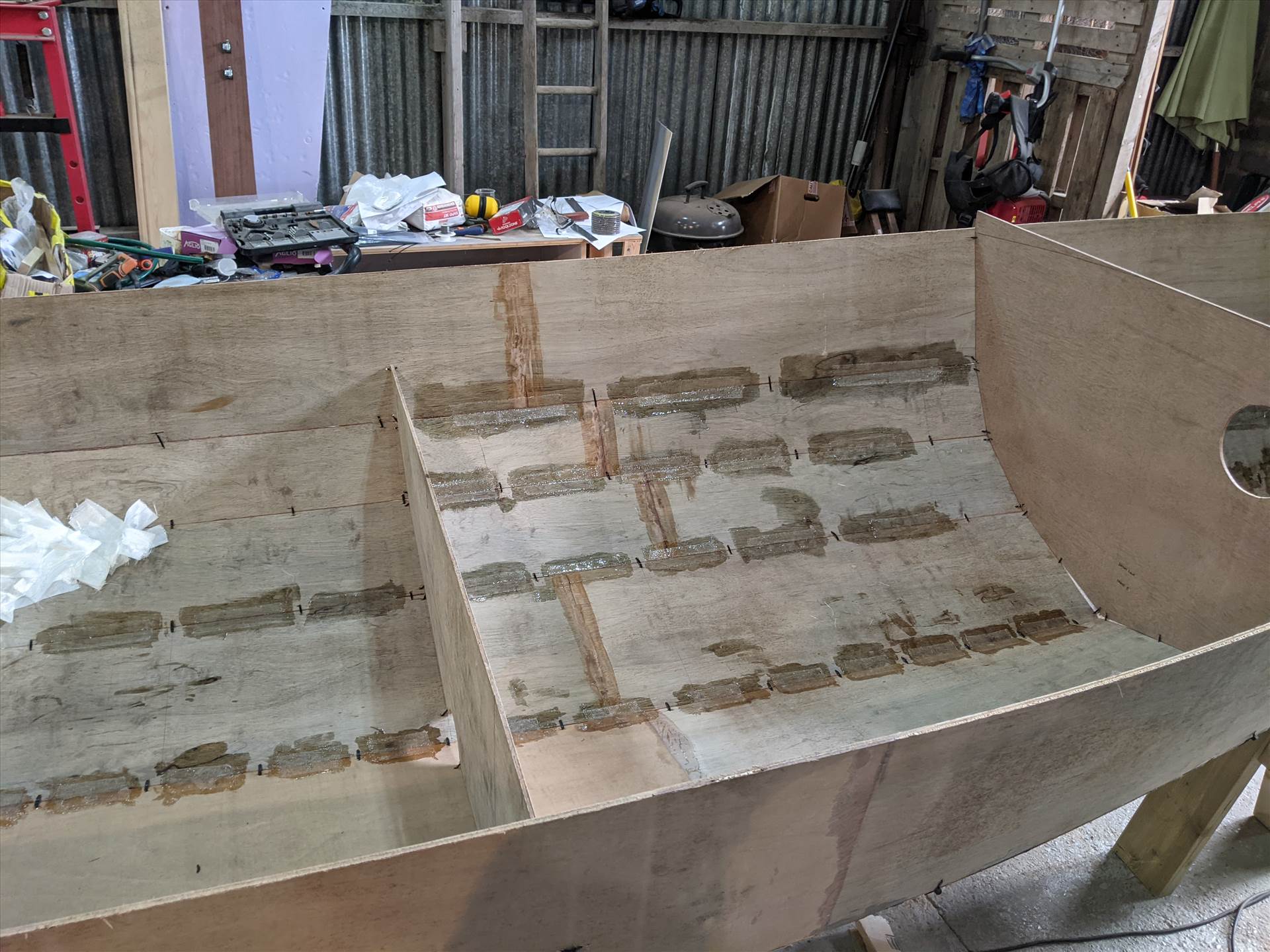
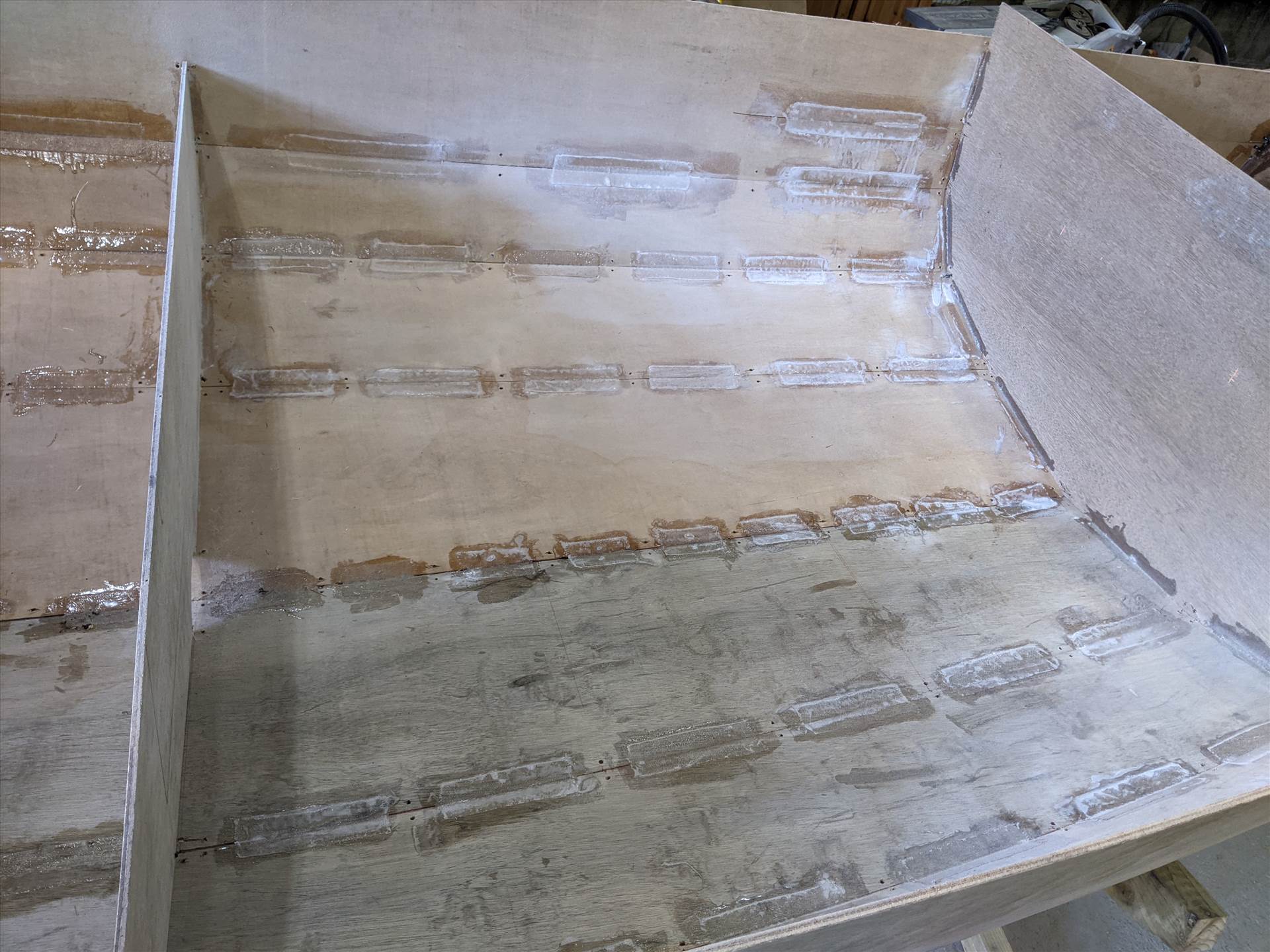
With all the joints now partially fibreglass taped, the boat is fairly rigid although with no gunwales on yet the shearline is still quite wobbly. The next thing to do was cut and remove all the tie-wraps which started out really satisfying but rapidly became quite tedious owing to the quantity used. Those gone, I got out the power sander and attacked all the seams from the outside to fair them off, then I knocked down the 50mm taped joints on the inside too.
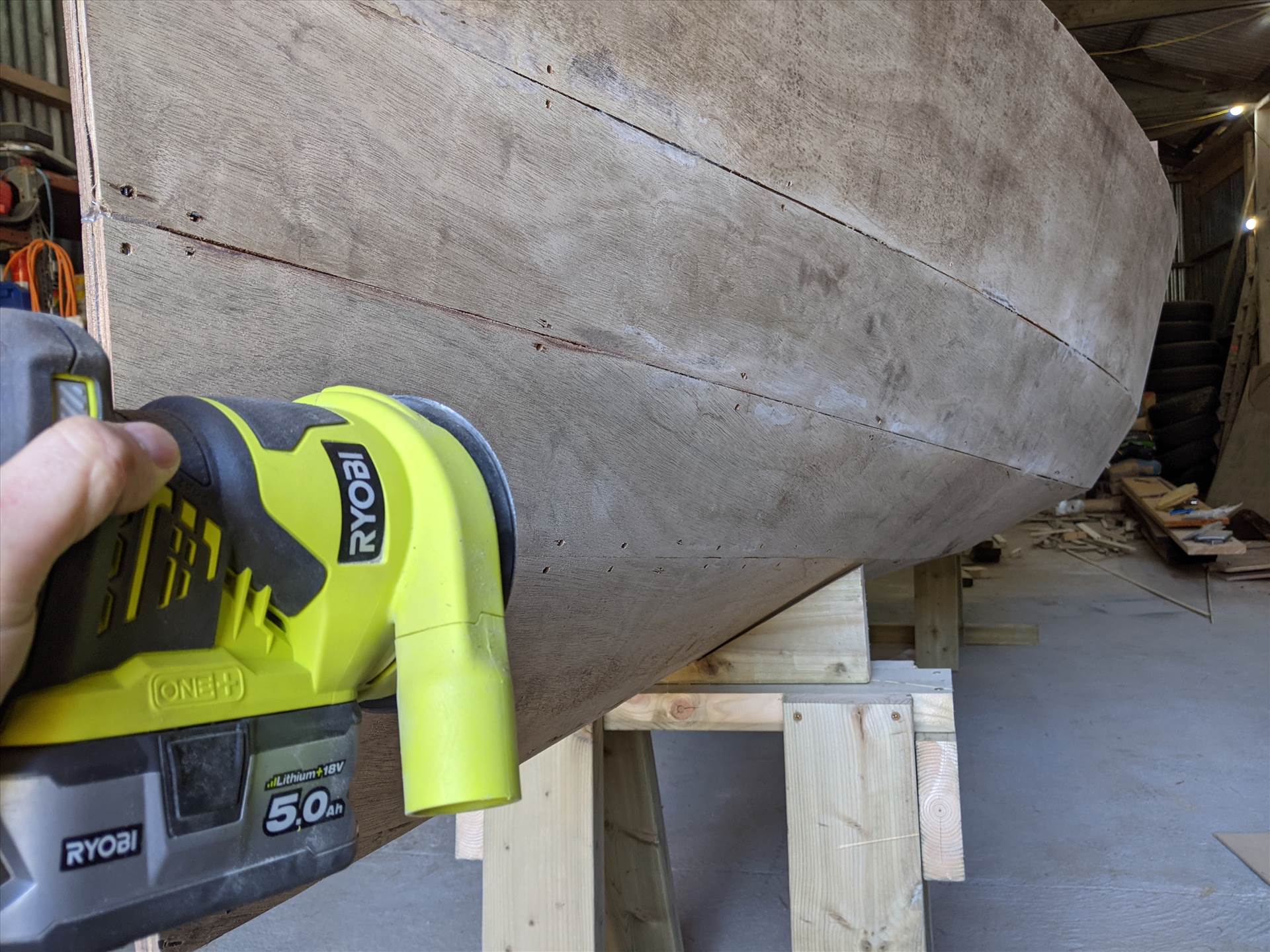
Each of the seams will be taped over continuously from stem to stern both inside and out in the near future.
Before doing that though, I want to fit the gunwales which will be Iroko but for this I bought some rough sawn board. I fully expect the gunwales will have something to say about the final shape of the boat as their fairly uniform stiffness will certainly try to apply some batton-effect to the top of the shear in plan-view. As I want to lock the boat together in its final shape rather than lock in extras stresses, I want to fit the gunwales before final taping of the seams.
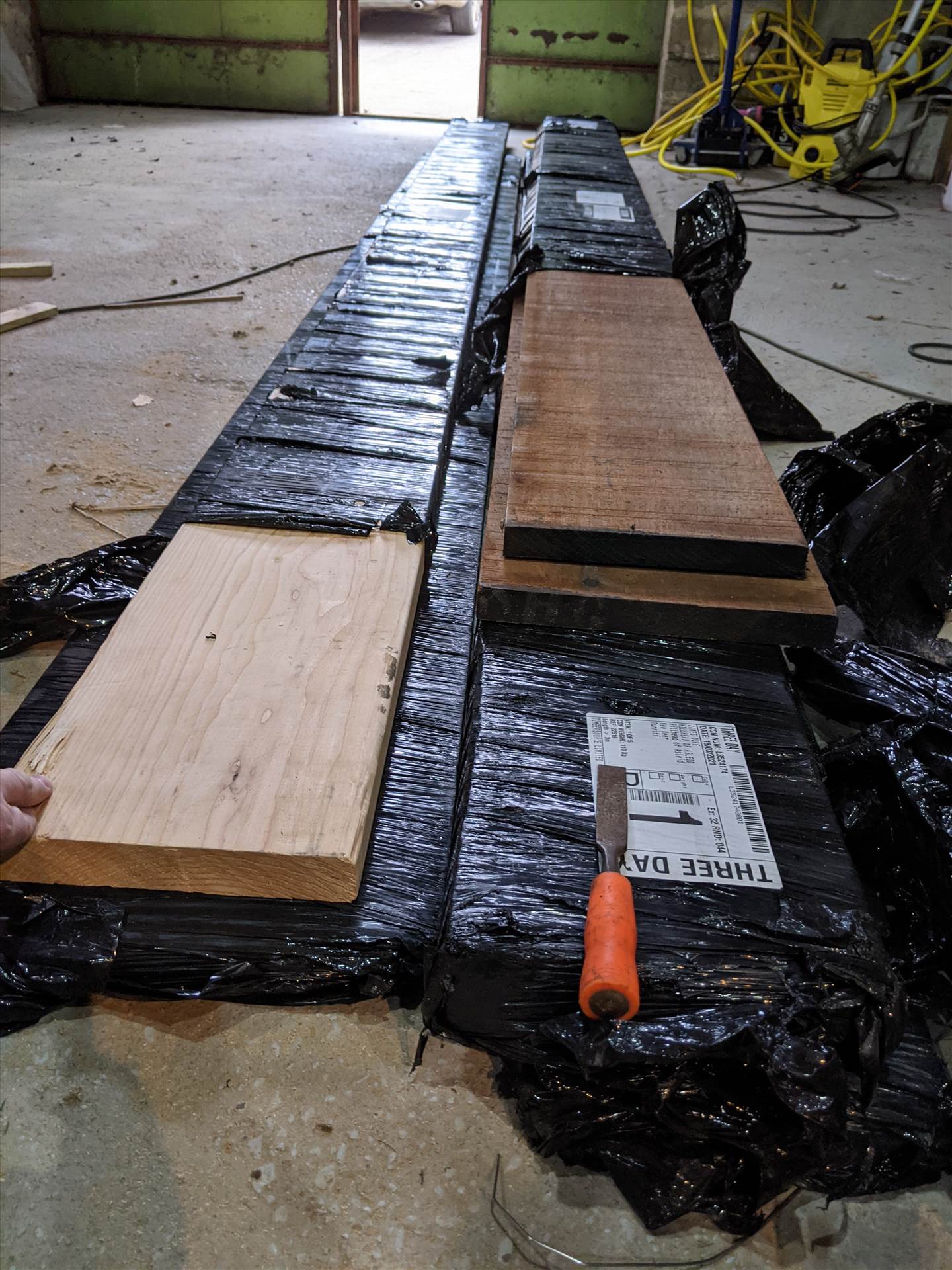
I bought some nice Douglas Fir boards at the same time which will become Melitele's (that's our boat's name, voted on by the family) mast, gaff, boom and bowsprit. Delivered, these boards cost me £500. As I need to rip these boards down, I'm a little nervous about screwing it up. There's no rational reason for this fear, but it's there and I've procrastinated a bit even buying a Jaguar V12 as something safer to play with. I want my sailing boat though so will crack on with this soon. Perhaps even tomorrow
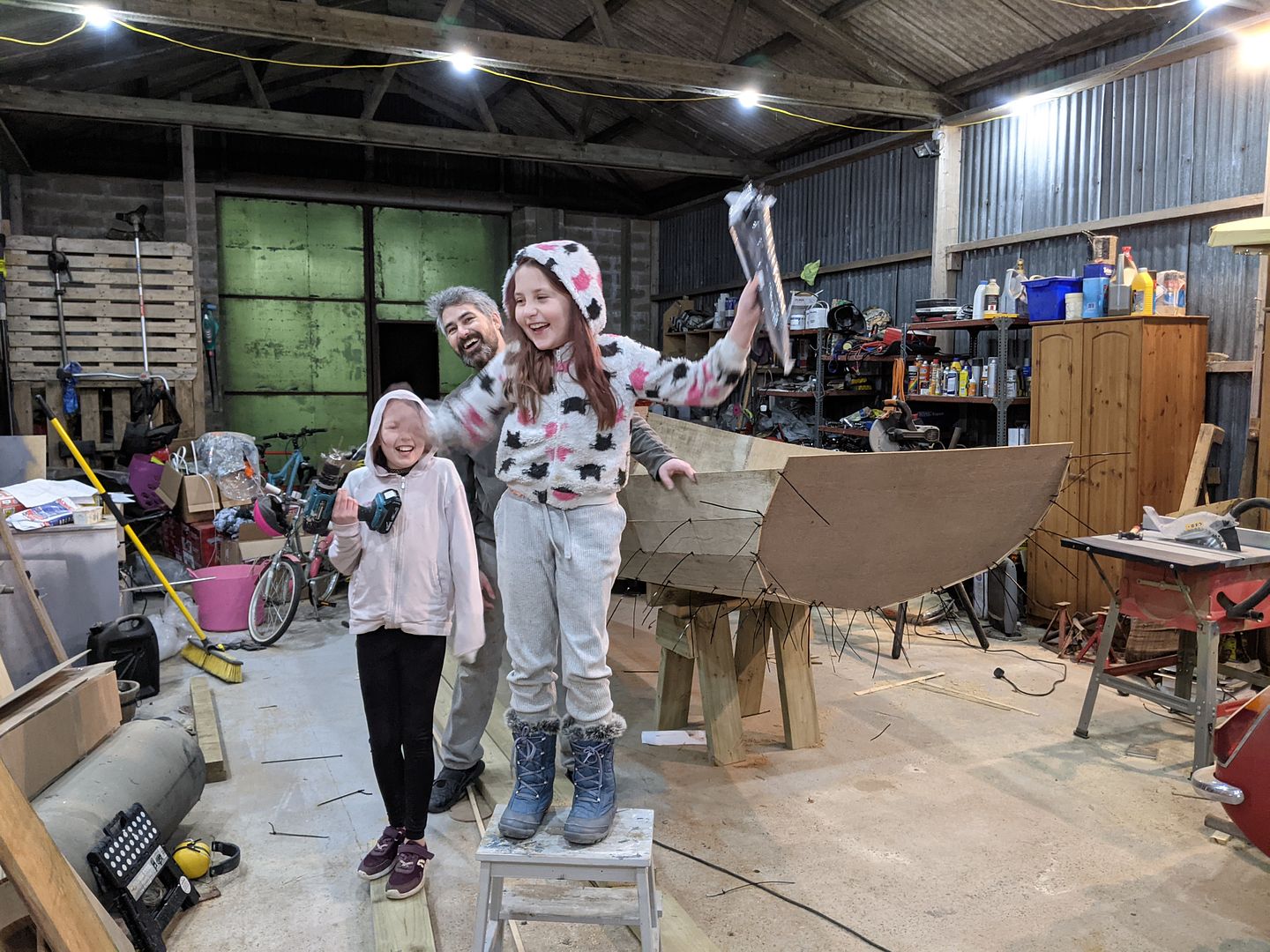
That really didn't stiffen up the boat as much as I thought it might though, so we lofted out and cut a couple more internal frames which helped-ish
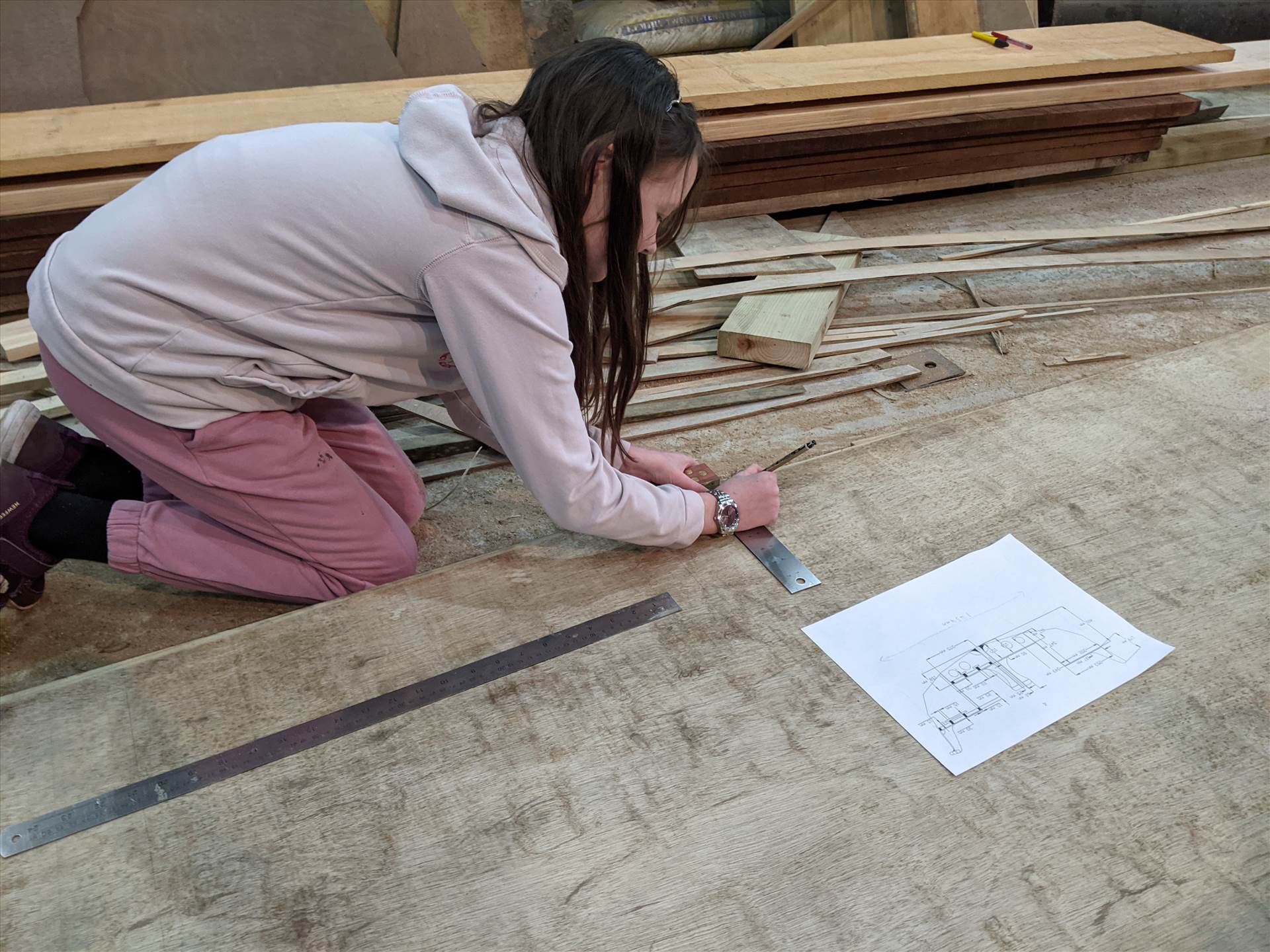
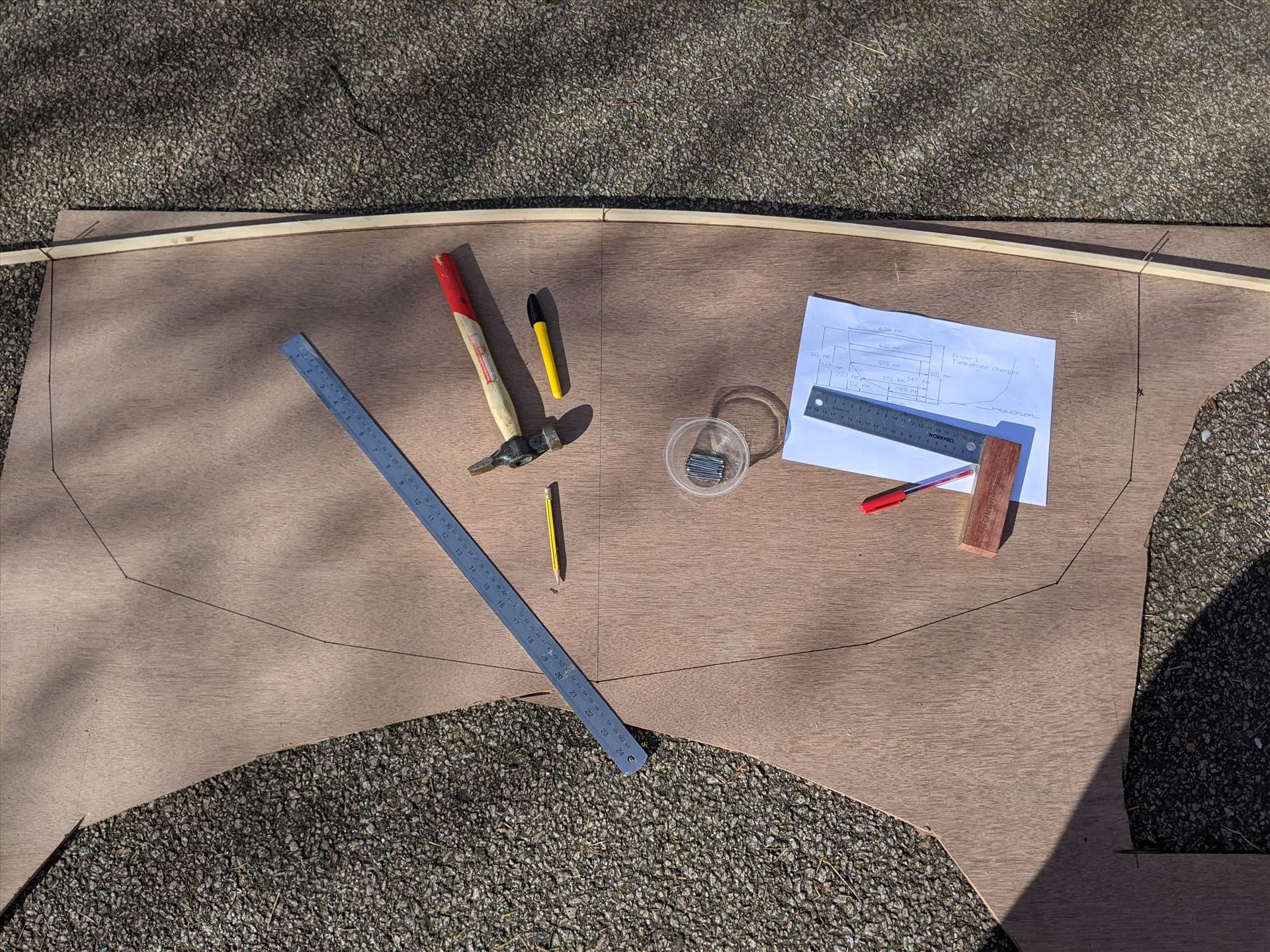
They were a struggle to fit though and the planks, especially aft, started trying to buck out and overlap. You might notice we marked the deck camber on but cut the frames out square. This was so I could easily spirit-level the frames to level them out down the hull's length to avoid locking any twist into the hull. We flipped the hull over and stood it on two of its frames.
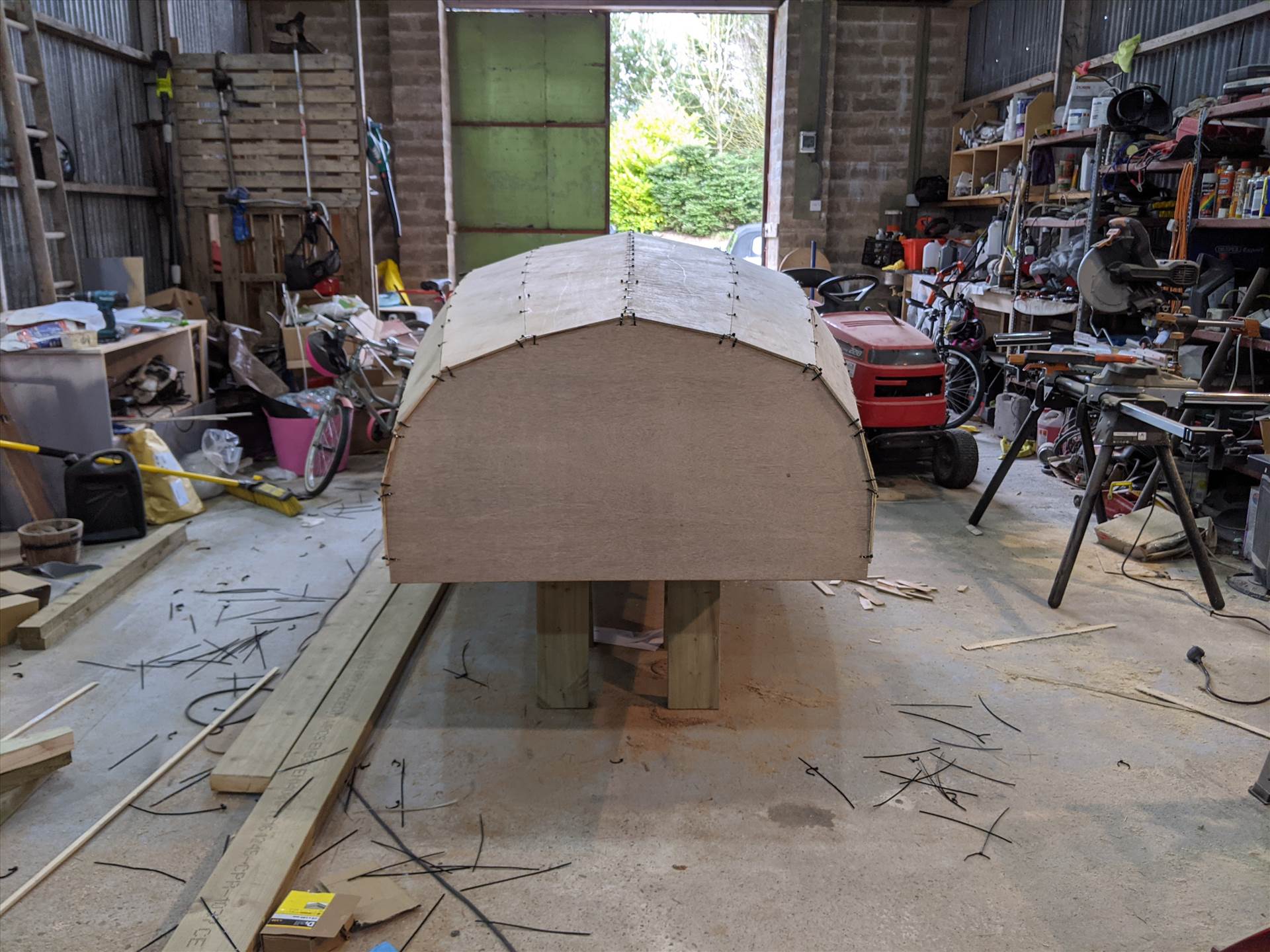
Once again, all the unhappy hull planks instantly and automatically sorted themselves out and the internal frames suddenly notched nicely into each chine.
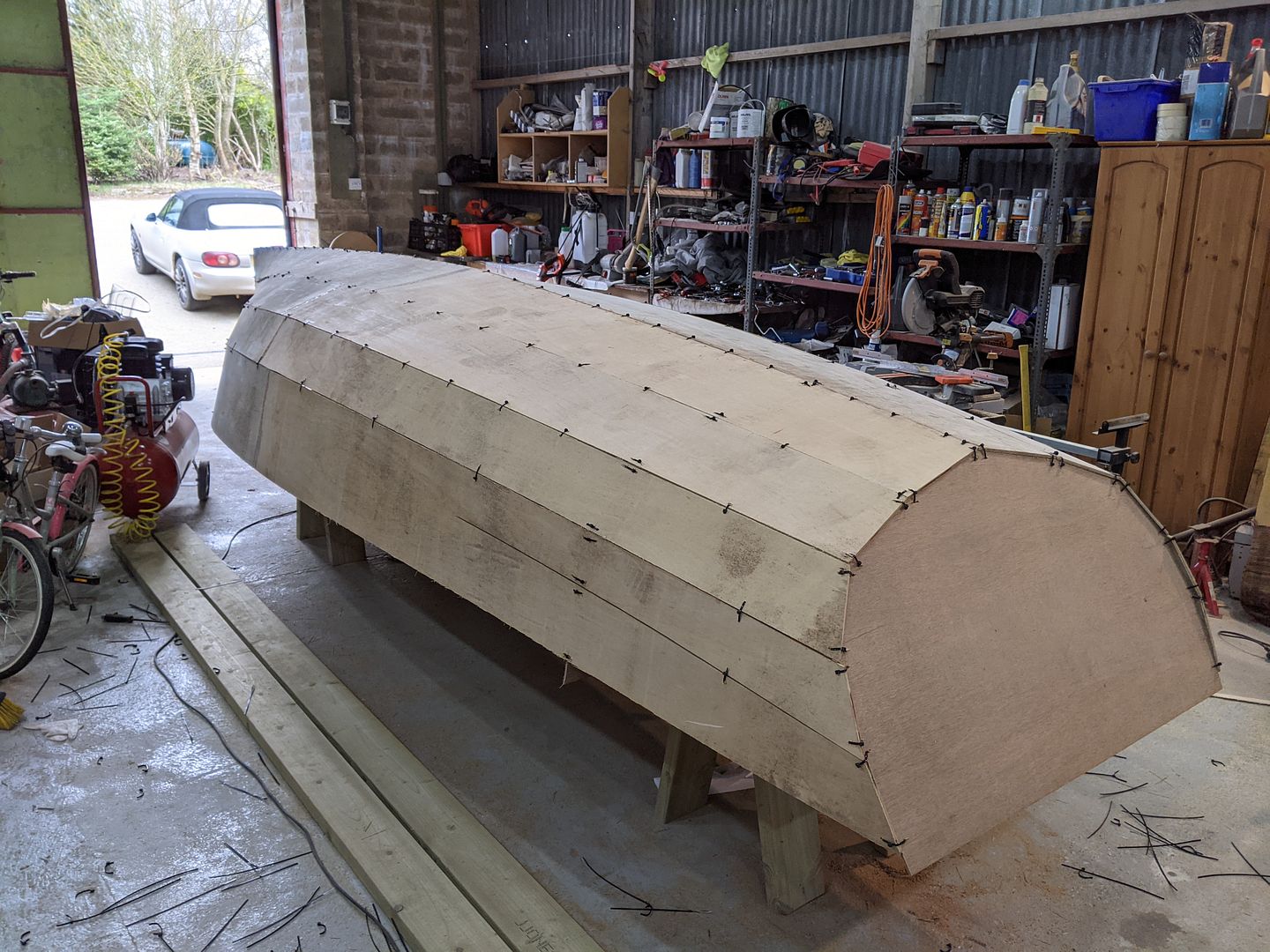
You may spot that the big wide upper plank has been slashed at the aft end. The plans give two options for the transom shape, either a straight one or a tumblehome version which is what I chose. I think it looks a bit nicer. As mentioned previously there's a lower rubbing strip below the gunwale half way down that big plank. Combined with the tumblehome transom it gives a very nice appearance and makes the hull look more shapely.
I don't think this looks at all bad for plywood sheets

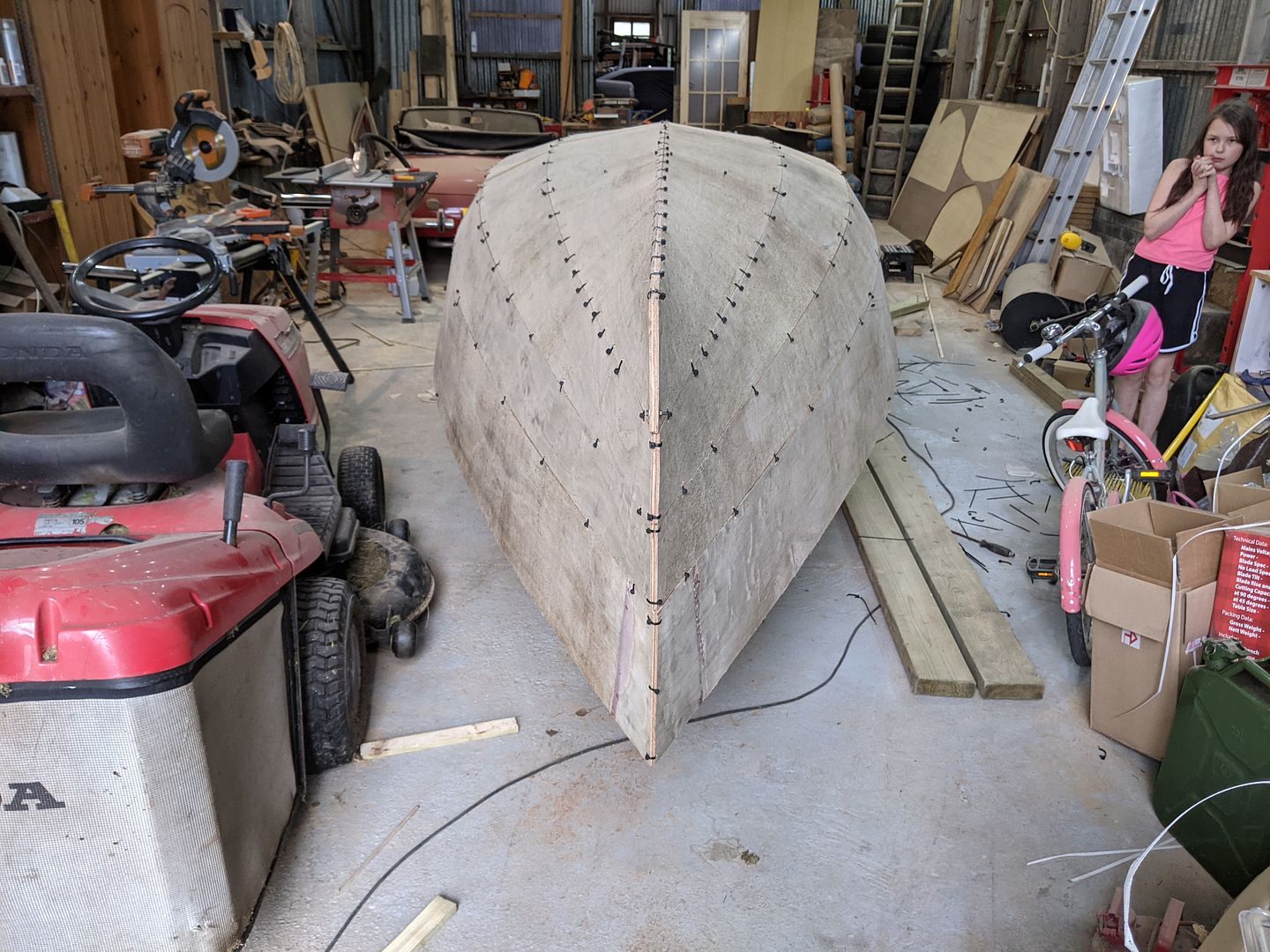
With the hull upside down, I spot glued in various places between the planks with dollops of 5 minute epoxy (which only takes 1 hour to harden - uh huh -that's how it's labelled and that's what the instructions say) to tack them together properly. Despite being mostly happy in its new shape, the planks would in places become slightly misaligned and I don't want wavy chines...
We flipped the boat back over again after this. 50mm wide fibreglass tape was cut into short lengths.
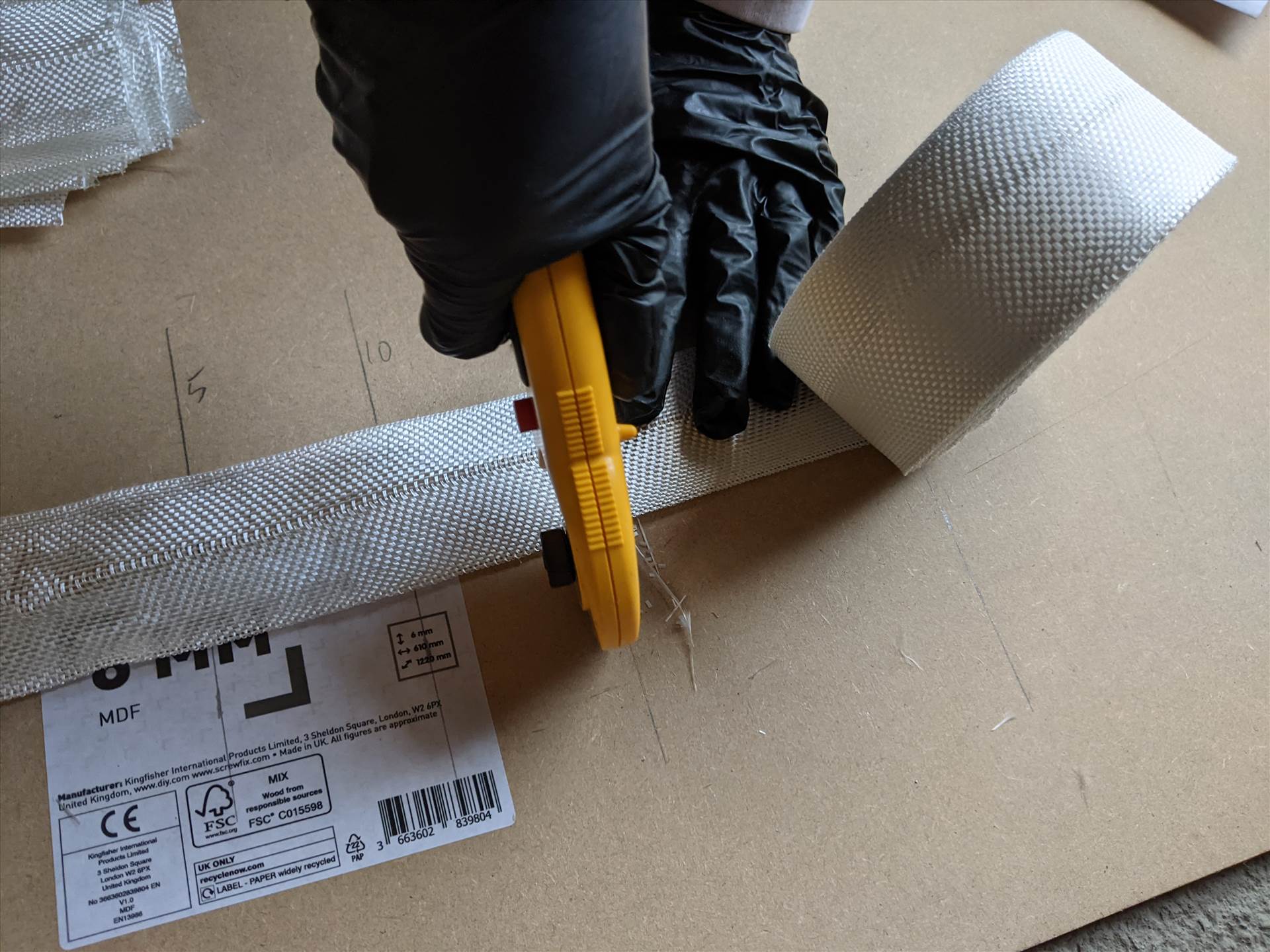
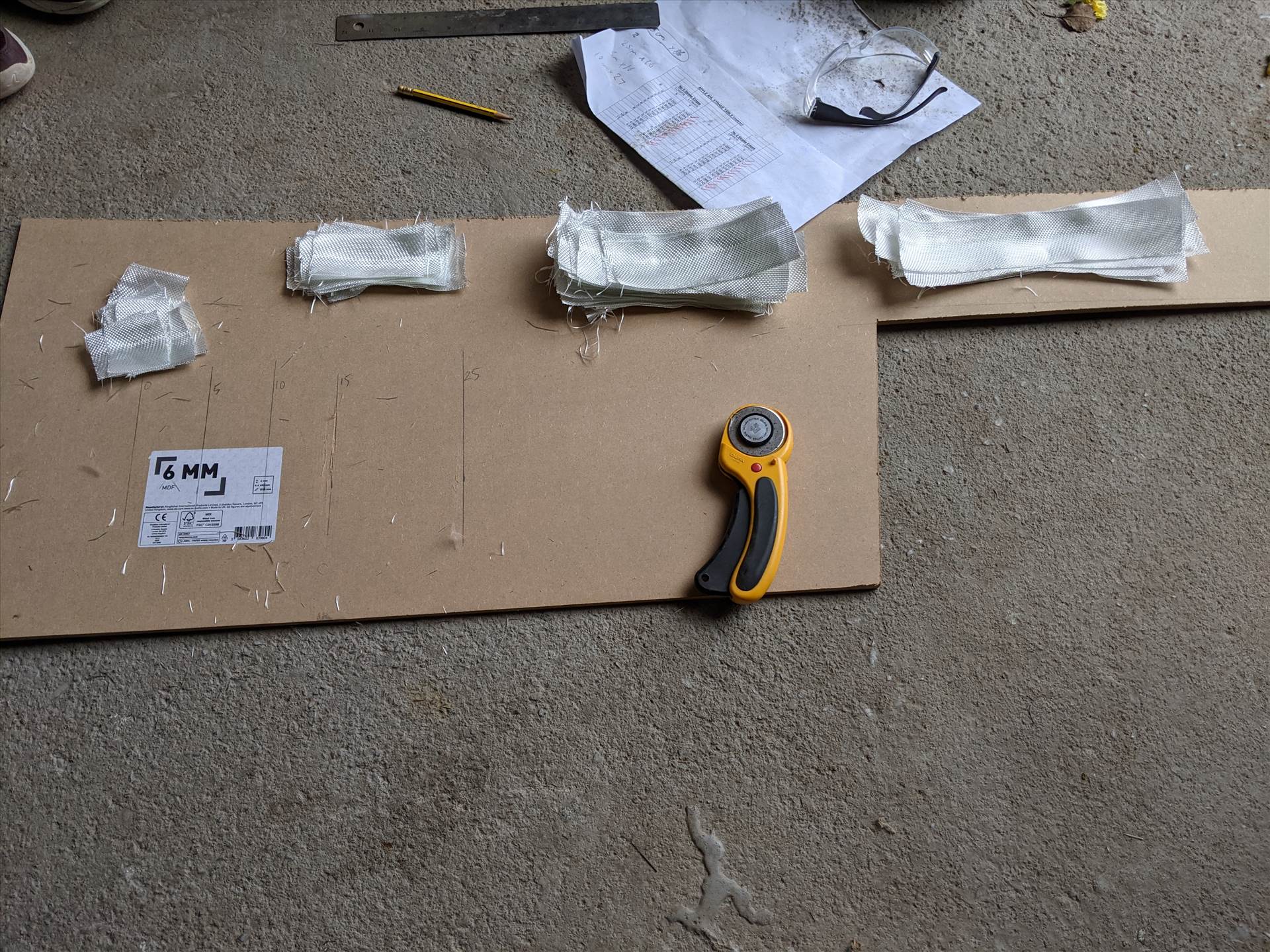
The boat has a 5ft beam so I couldn't actually reach the keel from outside, so I lifted my daughter in as she's much lighter than me and wouldn't collapse the somewhat precarious hull (although you'd think I'd lifted her into a minefield the way she gingerly shuffled about...) and she painted in the first row of fibreglass tapes between the tie-wraps.
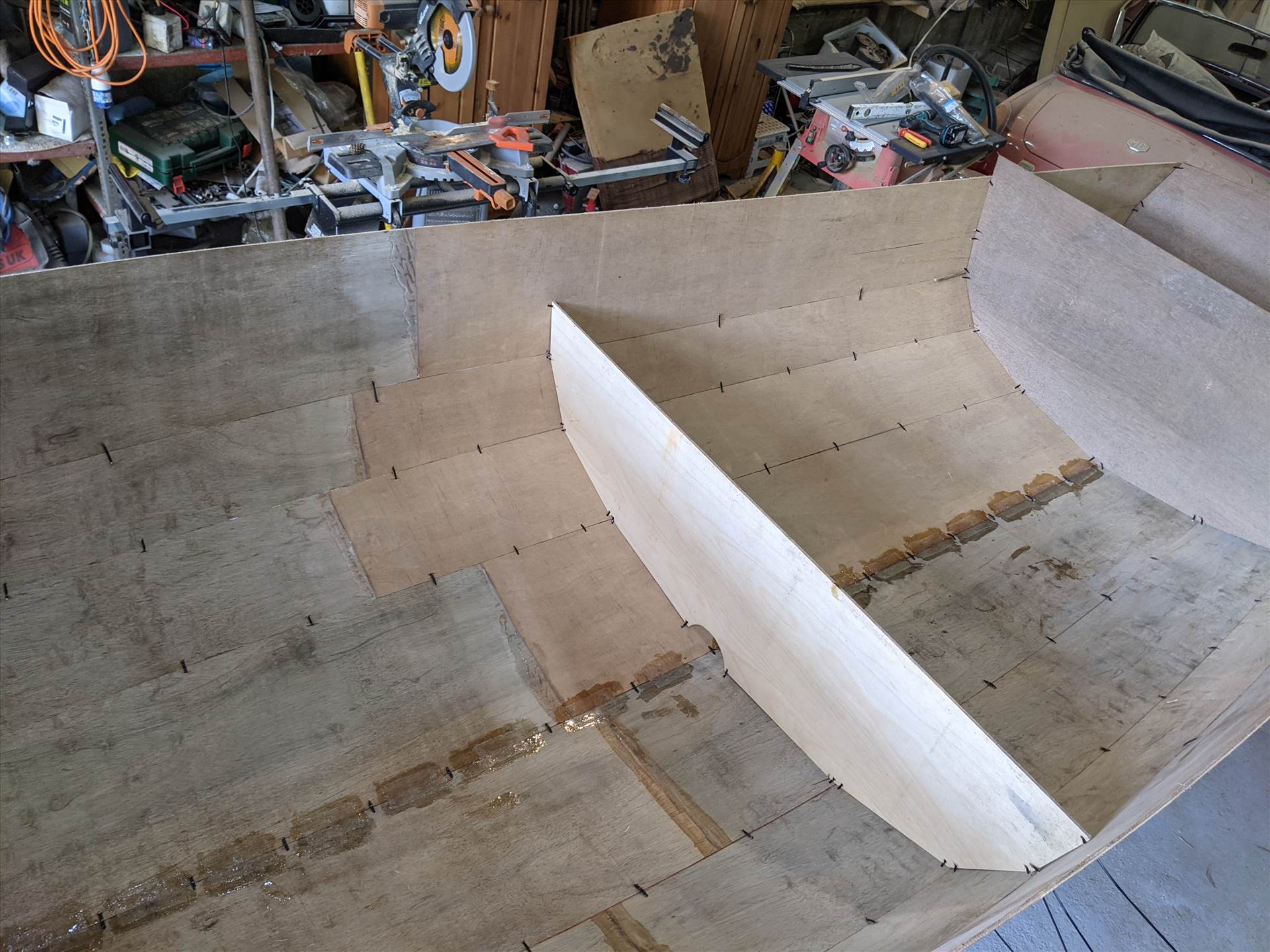
There were quite a lot to do. I used 200 grams of epoxy resin at a time. I found using more than that caused it to exotherm which is dangerous, useless, and a complete waste of money.
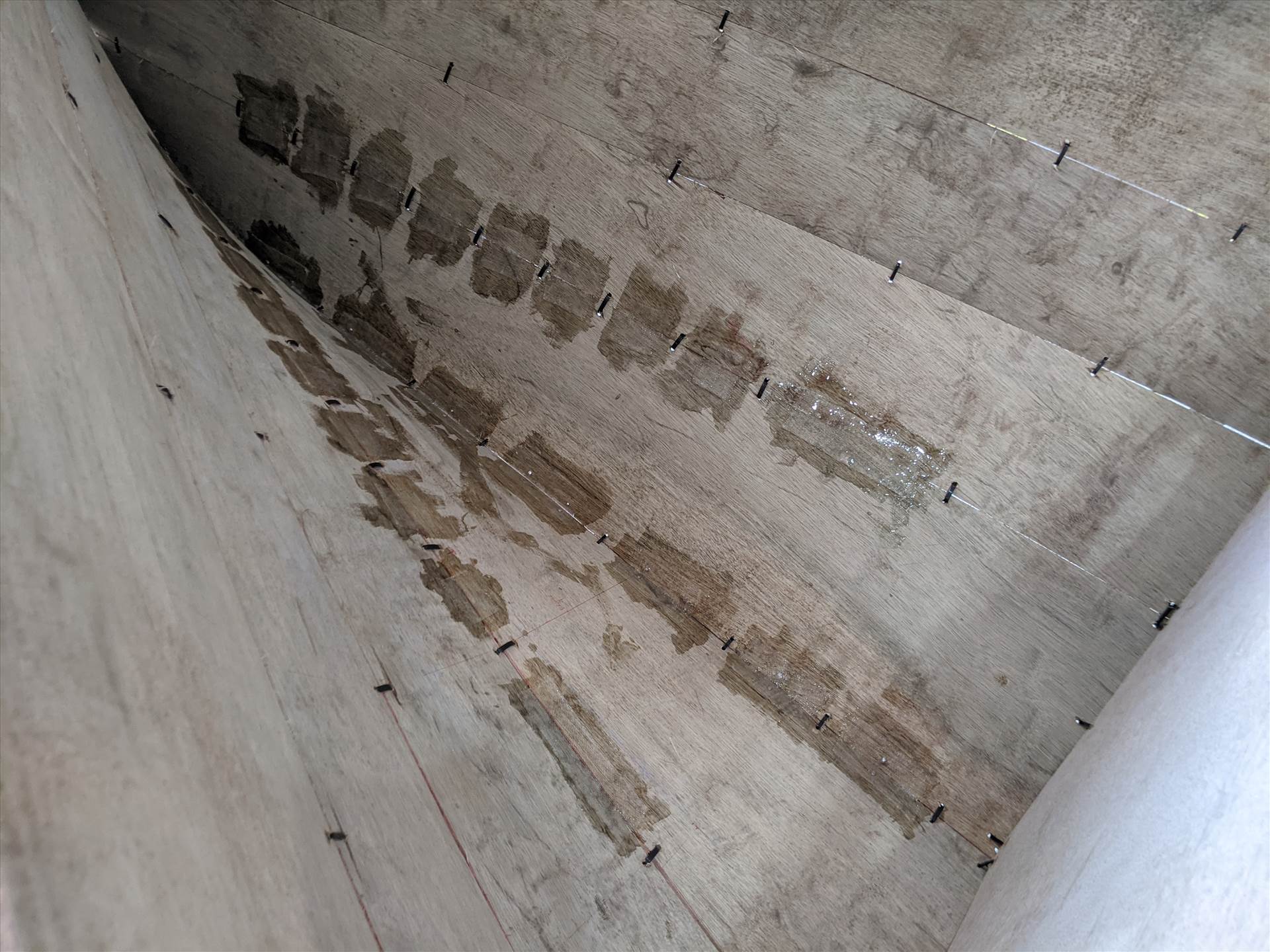
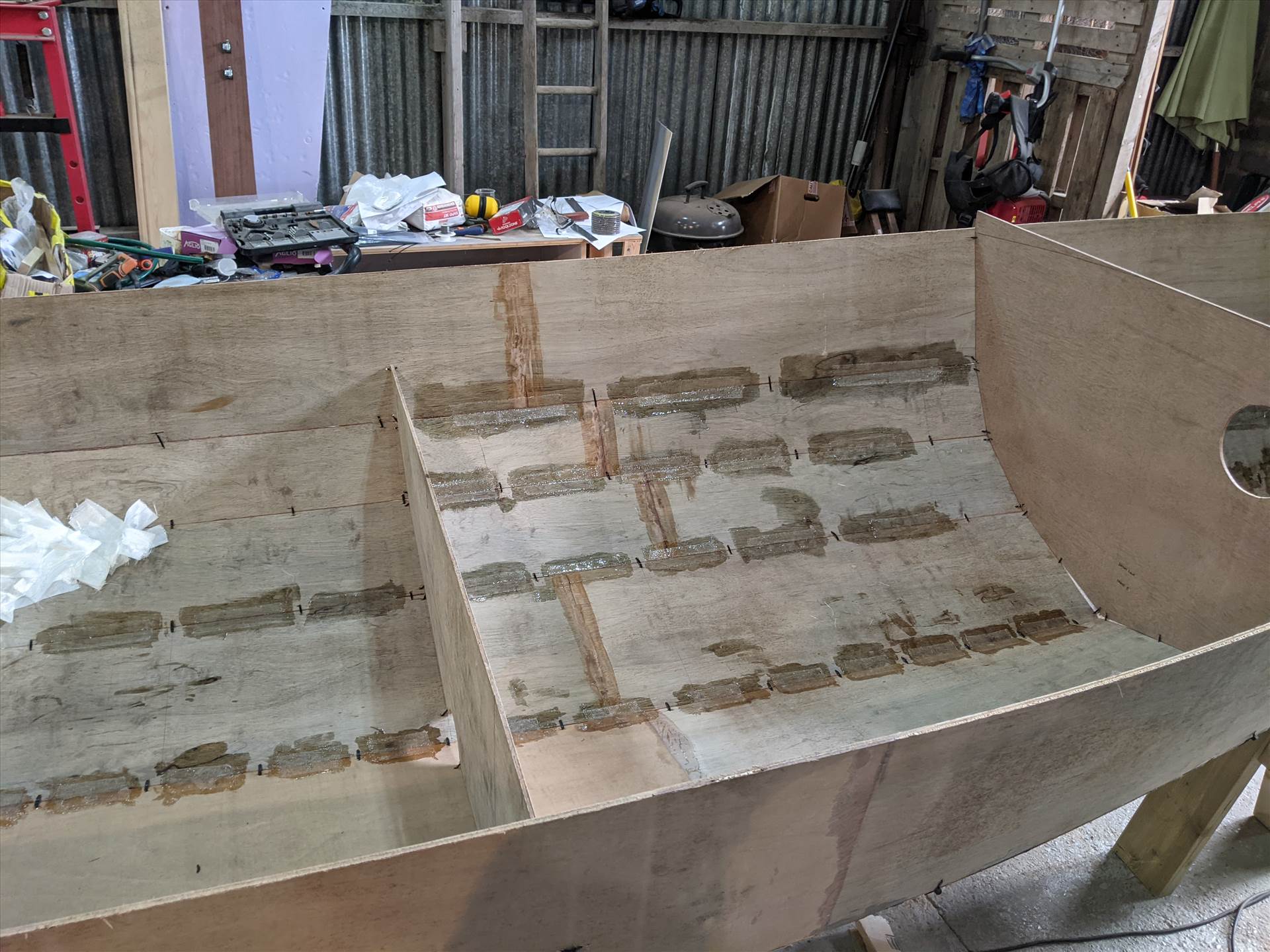
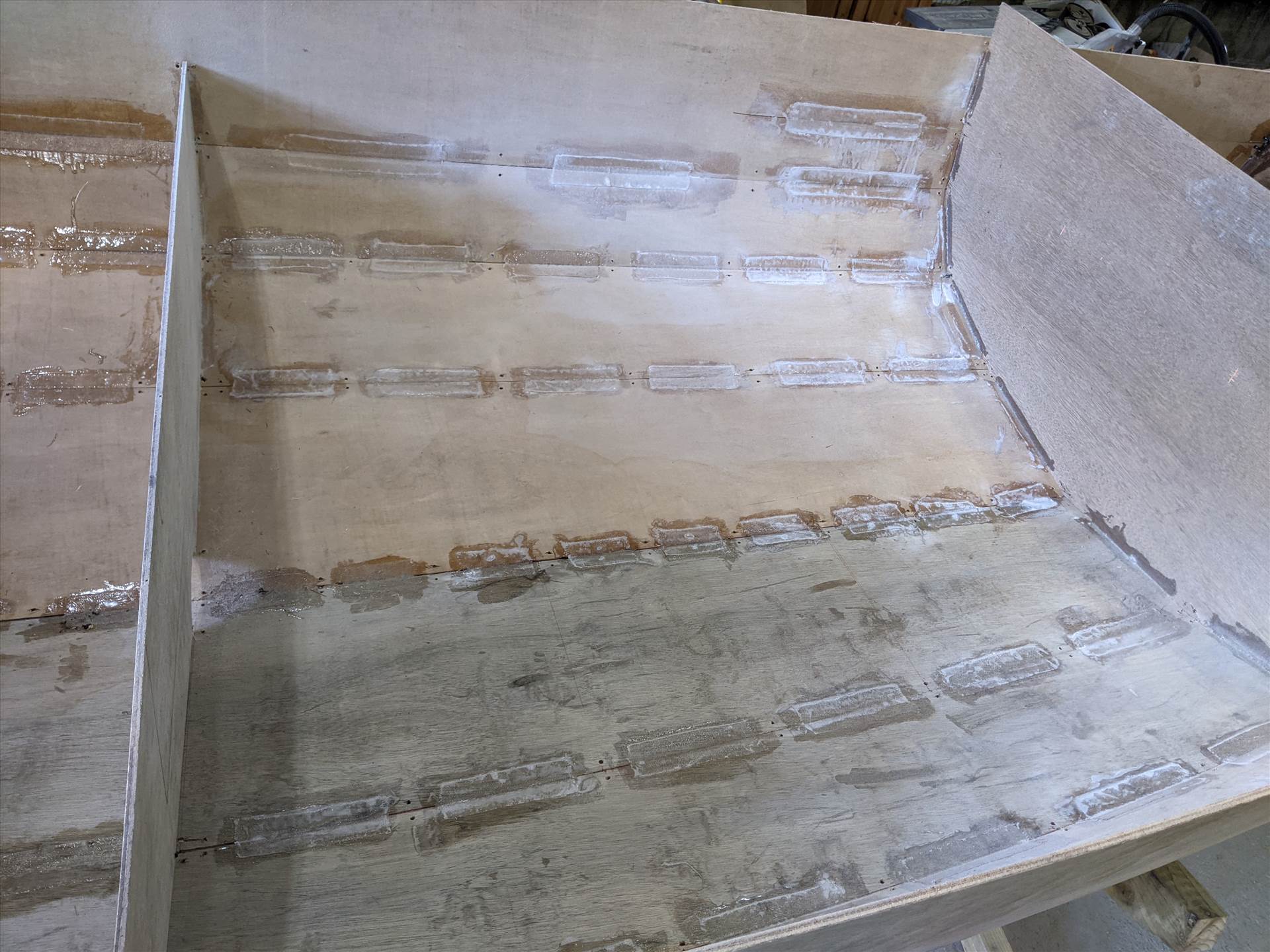
With all the joints now partially fibreglass taped, the boat is fairly rigid although with no gunwales on yet the shearline is still quite wobbly. The next thing to do was cut and remove all the tie-wraps which started out really satisfying but rapidly became quite tedious owing to the quantity used. Those gone, I got out the power sander and attacked all the seams from the outside to fair them off, then I knocked down the 50mm taped joints on the inside too.
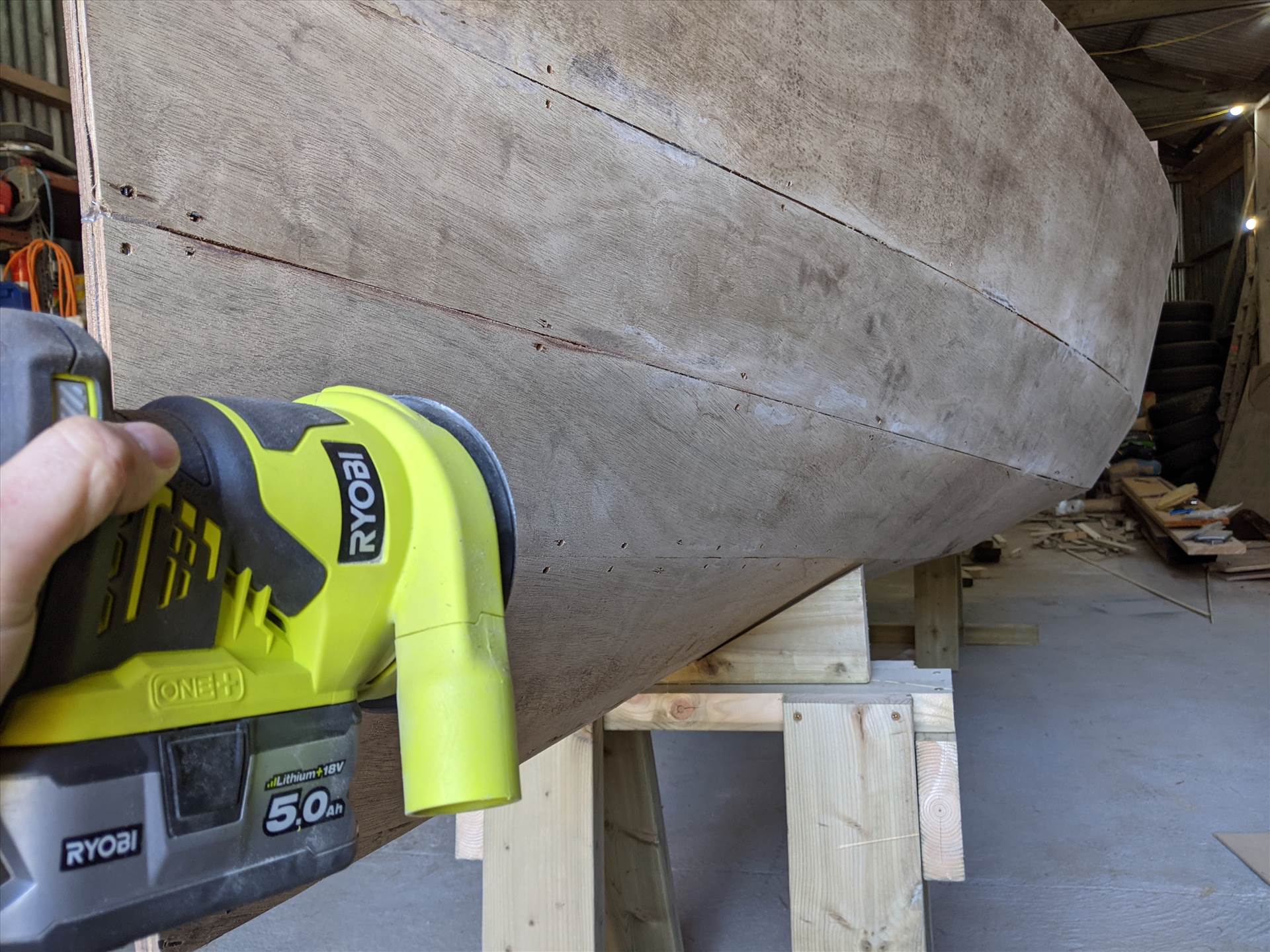
Each of the seams will be taped over continuously from stem to stern both inside and out in the near future.
Before doing that though, I want to fit the gunwales which will be Iroko but for this I bought some rough sawn board. I fully expect the gunwales will have something to say about the final shape of the boat as their fairly uniform stiffness will certainly try to apply some batton-effect to the top of the shear in plan-view. As I want to lock the boat together in its final shape rather than lock in extras stresses, I want to fit the gunwales before final taping of the seams.
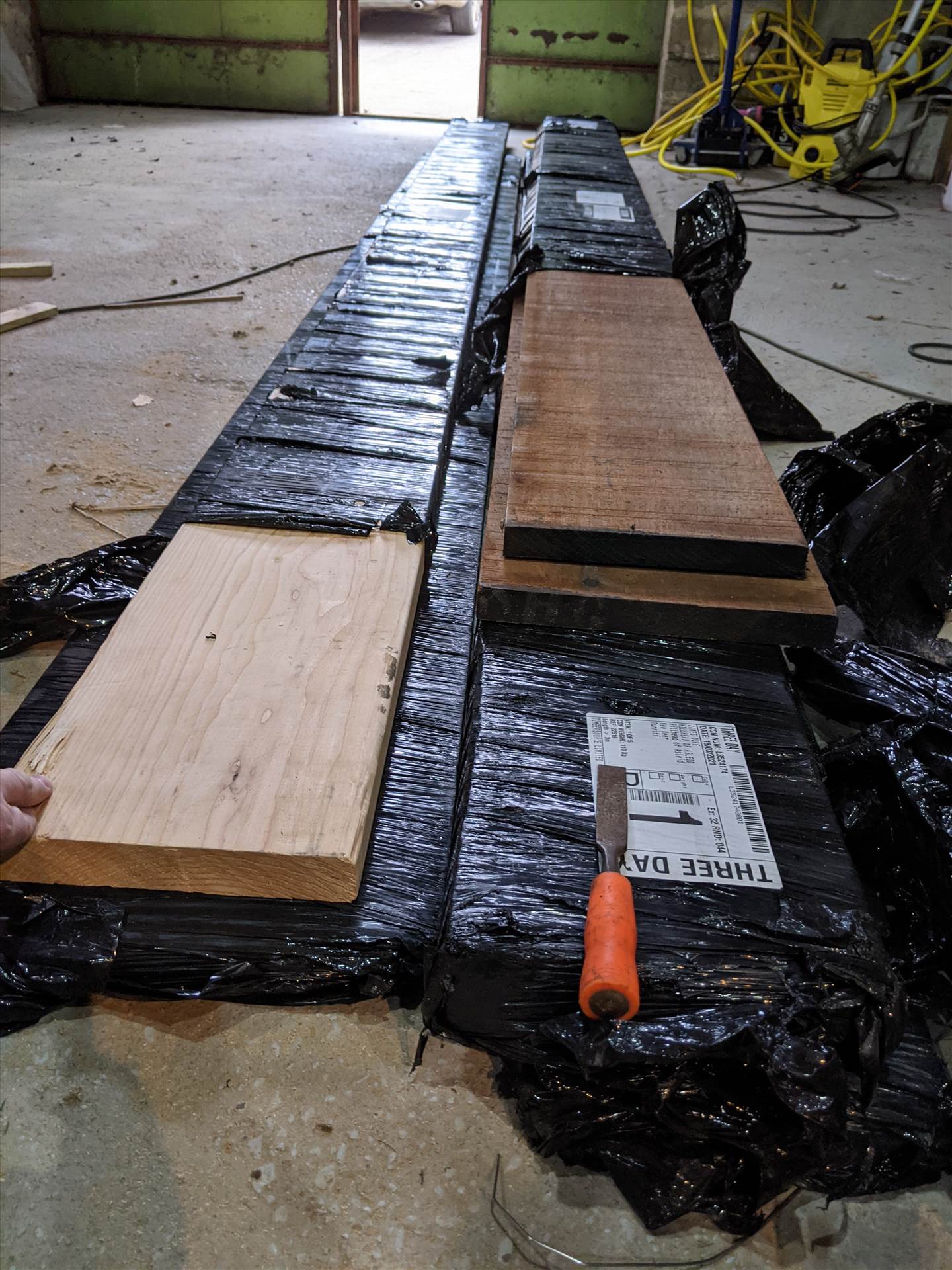
I bought some nice Douglas Fir boards at the same time which will become Melitele's (that's our boat's name, voted on by the family) mast, gaff, boom and bowsprit. Delivered, these boards cost me £500. As I need to rip these boards down, I'm a little nervous about screwing it up. There's no rational reason for this fear, but it's there and I've procrastinated a bit even buying a Jaguar V12 as something safer to play with. I want my sailing boat though so will crack on with this soon. Perhaps even tomorrow

Edited by jamieduff1981 on Friday 22 March 14:59
I sort of bought a car which kept me a bit busier than I had initially expected, but mostly that's an excuse and I was procrastinating as I was afraid of messing up that nice timber.
I don't really have any friends who are remotely interested in making things and whilst that blanket statement doesn't include my wife, she's not keen on lugging timber about.
My 11 and 9 year old daughters however have proven up for the task and having bought them each a new pair of kiddie-sized ear defenders they helped me plane and thickness down the first board with complete success. It was actually really rewarding seeing a beautiful piece of wood emerge from the tough sawn board. Silly, I know, but still really great.



This was thicknessed down to 20mm. The gunwales are made, according to the plans, from two laminations of 20mm x 20mm hardwood but I read on another forum a while ago that a builder had breakages bending the hardwood around the shear of the hull. To mitigate this, I decided to cut narrower strips i.e. 13.5mm and use three laminations instead. I expected mistakes and wastage but it actually went really well.
I was a little concerned about the shape of my bow which the plywood tried to straighten out.

To ensure the correct shape was locked in by the gunwales I cut temporary forms to clamp on the inside whilst gluing up the gunwales and tested it using scrap batons to check I achieved a nice fair curve. It worked.

There is a 20 x 20mm strip amongst these from which I'll cut the stem post and the hardwood keel strip back to the daggerboard opening (there's a wedge shaped skeg aft of the daggerboard opening which will need cut from another board later).


I don't really have any friends who are remotely interested in making things and whilst that blanket statement doesn't include my wife, she's not keen on lugging timber about.
My 11 and 9 year old daughters however have proven up for the task and having bought them each a new pair of kiddie-sized ear defenders they helped me plane and thickness down the first board with complete success. It was actually really rewarding seeing a beautiful piece of wood emerge from the tough sawn board. Silly, I know, but still really great.



This was thicknessed down to 20mm. The gunwales are made, according to the plans, from two laminations of 20mm x 20mm hardwood but I read on another forum a while ago that a builder had breakages bending the hardwood around the shear of the hull. To mitigate this, I decided to cut narrower strips i.e. 13.5mm and use three laminations instead. I expected mistakes and wastage but it actually went really well.
I was a little concerned about the shape of my bow which the plywood tried to straighten out.

To ensure the correct shape was locked in by the gunwales I cut temporary forms to clamp on the inside whilst gluing up the gunwales and tested it using scrap batons to check I achieved a nice fair curve. It worked.

There is a 20 x 20mm strip amongst these from which I'll cut the stem post and the hardwood keel strip back to the daggerboard opening (there's a wedge shaped skeg aft of the daggerboard opening which will need cut from another board later).


Boatbuoy said:
Great work Jamie, keep it up!
Thanks! I'm hoping I can finish work today with 2 ounces of energy left to mix up some epoxy and glue on the stem post. With that fitted first I can more neatly finish the stem end of each gunwale lamination. More clamps are on order and hopefully will be here tomorrow - fingers crossed...Hi,
In due course there will be a large breast hook from stem back through the first frame and terminating at the second frame immediately forward of the mast step which doubles as the mounting for the bow sprit. There is a 20mm square hardwood stem to be added, glassed and faired in on the outside of the hull for ding resistance. The design is actually half-decked bow and stern and the foredeck is to be glued to inner gunwales I still need to add, but the construction sequence tells me to add them after the outers.
Edited to add that I have still to go around all of the key joints and add a big radius fillet of epoxy and milled fibres - the bow will receive that on the inside. It's already glass taped on the inside.
The following are not my boat but show the same configuration that I'm building from the plans and, I admit, were my first inspiration for choosing the Campion Apple 16 from the beginning





In due course there will be a large breast hook from stem back through the first frame and terminating at the second frame immediately forward of the mast step which doubles as the mounting for the bow sprit. There is a 20mm square hardwood stem to be added, glassed and faired in on the outside of the hull for ding resistance. The design is actually half-decked bow and stern and the foredeck is to be glued to inner gunwales I still need to add, but the construction sequence tells me to add them after the outers.
Edited to add that I have still to go around all of the key joints and add a big radius fillet of epoxy and milled fibres - the bow will receive that on the inside. It's already glass taped on the inside.
The following are not my boat but show the same configuration that I'm building from the plans and, I admit, were my first inspiration for choosing the Campion Apple 16 from the beginning






Edited by jamieduff1981 on Monday 4th October 14:01
robm3 said:
My dad has a company doing these sorts of boats, his web design is hopeless though, he's been doing it since 1985 but his website says 25 years, then 30 years, but in reality it's 36... doh!
scruffie.com
That's cool. Based in Australia I assume from the phone number? Australians do seem to have quite a vibrant cruising sail boat community which is really great. I quite like the look of the Secret 33 yawl there. scruffie.com
Quite a tiny update but last night I got the stem cut and glued in place with 1 hour epoxy which is mixed 1:1 ratio. Someone has smashed my weighing scales so a replacement set has been ordered this morning. I can't / won't mix up the West Systems 105 without them but with the stem in place I can mark and cut the stem ends of the gunwales ready to glue in. Another bunch of clamps arrived this morning also.

This will be faired in later. The lower 2/3rds~ish needs sharpened slightly also (or else a constant small fountain of water will be squirted up over the foredeck, according to the designer, and we don't want that do we?)

This will be faired in later. The lower 2/3rds~ish needs sharpened slightly also (or else a constant small fountain of water will be squirted up over the foredeck, according to the designer, and we don't want that do we?)
I've peaked too soon today although maybe that's a good thing.
I remembered the chainplates which the gaff cutter version has. This detail is only on the gaff cutter versions of the drawings. The chainplates for the standing rigging pass through the gunwales so it's necessary to mark their positions and cut 4mm deep slots out of the gunwales before gluing to the hull. I'm sure if I missed this I could have drilled through and filed them out but I'm glad I didn't make life difficult for myself here. These were kerfed and chiselled out.

Like this:

Next I marked and cut the stem ends of the gunwales to neatly (a relative term wherever I'm involved...) fit the stem post. In retrospect I should have done this first then marked the slots for the chainplates afterwards as the latter is easier to get right than the former but I never was that bright...
Once the inner laminations were cut to fit I clamped up the next lamination dry to get that fettled also.

It's probably just because I'm messy but I burned through 4 or 5 pairs of rubber gloves gluing up the first set. Also, I've learned that when buying clamps one should forget the sets of 4, 6 or even 12 and just select "All" in the online shopping cart.

I assume it goes without saying but the joints in the laminations were staggered. Each strip is roughly 11ft long so they're approximately 2/3 : 1/3 of the length of the boat so the inner lamination has the joint down aft and the outer one is more forward.

Now I'm out of clamps so I'll stooge around and relax I think. Tomorrow morning I can do more.
I remembered the chainplates which the gaff cutter version has. This detail is only on the gaff cutter versions of the drawings. The chainplates for the standing rigging pass through the gunwales so it's necessary to mark their positions and cut 4mm deep slots out of the gunwales before gluing to the hull. I'm sure if I missed this I could have drilled through and filed them out but I'm glad I didn't make life difficult for myself here. These were kerfed and chiselled out.

Like this:

Next I marked and cut the stem ends of the gunwales to neatly (a relative term wherever I'm involved...) fit the stem post. In retrospect I should have done this first then marked the slots for the chainplates afterwards as the latter is easier to get right than the former but I never was that bright...
Once the inner laminations were cut to fit I clamped up the next lamination dry to get that fettled also.

It's probably just because I'm messy but I burned through 4 or 5 pairs of rubber gloves gluing up the first set. Also, I've learned that when buying clamps one should forget the sets of 4, 6 or even 12 and just select "All" in the online shopping cart.

I assume it goes without saying but the joints in the laminations were staggered. Each strip is roughly 11ft long so they're approximately 2/3 : 1/3 of the length of the boat so the inner lamination has the joint down aft and the outer one is more forward.

Now I'm out of clamps so I'll stooge around and relax I think. Tomorrow morning I can do more.
Maggas said:
Looked at the thread as mine Unc is doing something similar...and not to distract from the thread...but 'Jamie 1981' user....did you used to have a Ford Cougar and around 2002 attend Cougarfest near Northampton? If so I think you and a lady who went by 'Kilted Kougar' helped remove original Ford Badges from my Cougar and put Ford Owners clubs ones on! And you truly thrashed me in go karting as I weight about twice you. Went by the name "StockinTops" on FCOC.
Hi,Yes that was/is me. I'm surprised you remember me from that! I took Dawn with me because my wife was working that weekend and Dawn was skint so I drove her down and she kept me company so it worked out fine. I'd usually get handed a set of lowering springs to fit for someone in the campsite, and when I was in my 20s that didn't seem like a bad way to pass the time!
I still keep in touch with a few from that club but the car went many years ago.
As luck would have it, I still have photos from that particular year - it was 2006.

The guy on the left was named Larry but I haven't heard from him in about a decade - but I think he went overseas to work. He lived fairly close to me. The next guy is called Rod and I am still in touch with him. Then there's me but a darker, skinnier version. I'm still in touch with Matt who's second from the right and I'm still in touch with Dawn on the right.
Work has been rather busy lately, but I had Friday off (well, it was Schrodinger's Annual Leave really) and a productive Saturday and Sunday with my wife who, uncharacteristically, was feeling very industrious towards the dinghy.
We cleared out our downstairs garage, wired in a bigger heater with more clever thermostatic control, made a cradle with trolley wheels and moved Melitele out of the shed. As it happens, this is the first opportunity I've had to look at my boat from the side.


It just fits diagonally in the downstairs garage with room to squeeze around the stem, but with wheels it's easy to swing the doors open and move the boat to a better position to work on and then tuck it away warm for the epoxy to cure.

With Melitele out of the shed, I built racks to suspend the good timber off the floor for winter and cleared out space to get my old Jag X-Type in which needs a new sill. I was planning to scrap the car, but looking at what else is out there a new sill, a brake pipe and fixing an exhaust leak seams like very cheap 3.0 V6 AWD motoring for a while to come so there's a new sill on order and I've plenty welding consumables already. It'll make a good tow car for the boat.
Without a sill here already though, my wife was quite keen that we got some immediate benefit from the relocation works, the results of which are that by 9am on Sunday we completed all of the internal seam taping. This picture was from Saturday evening where we still had the last chine and the short slash on the top plank for the tumblehome transom to deal with.

We're going to flip the hull over and tackle the outsides of the seams next and will probably glass the exterior of the hull at that point. We could glass the interior now, but turning the hull over isn't really difficult and I would like the visual progress of the outside looking more matured.
We cleared out our downstairs garage, wired in a bigger heater with more clever thermostatic control, made a cradle with trolley wheels and moved Melitele out of the shed. As it happens, this is the first opportunity I've had to look at my boat from the side.


It just fits diagonally in the downstairs garage with room to squeeze around the stem, but with wheels it's easy to swing the doors open and move the boat to a better position to work on and then tuck it away warm for the epoxy to cure.

With Melitele out of the shed, I built racks to suspend the good timber off the floor for winter and cleared out space to get my old Jag X-Type in which needs a new sill. I was planning to scrap the car, but looking at what else is out there a new sill, a brake pipe and fixing an exhaust leak seams like very cheap 3.0 V6 AWD motoring for a while to come so there's a new sill on order and I've plenty welding consumables already. It'll make a good tow car for the boat.
Without a sill here already though, my wife was quite keen that we got some immediate benefit from the relocation works, the results of which are that by 9am on Sunday we completed all of the internal seam taping. This picture was from Saturday evening where we still had the last chine and the short slash on the top plank for the tumblehome transom to deal with.

We're going to flip the hull over and tackle the outsides of the seams next and will probably glass the exterior of the hull at that point. We could glass the interior now, but turning the hull over isn't really difficult and I would like the visual progress of the outside looking more matured.
I managed to capsize the boat alone yesterday, but I'll admit it was pretty awkward. The outside of the hull was then power sanded to remove any splinters or drips of epoxy through the tie-wrap holes. The stem post was shaped also.


That done, my wife laid out, marked and cut the fibreglass cloth ahead of time. We made up a filler paste from epoxy and milled fibres (heavier but a lot stronger than using microballoons) and filled all the seams and tiewrap holes.

Rather than let this cure and sand it back, we went straight ahead and glassed over it. The squeegee action to wet out the cloth takes care of any rough bits of filler while it's all still wet.

This was wet out in the usual way (at least it's usual for home built aircraft builders) - pour a little resin on then squeegee the bejesus out of it to see how far the resin will go whilst still wetting it out fully.

It still used loads of resin. It's a good thing I bought another 6kg pack of the stuff!



That done, my wife laid out, marked and cut the fibreglass cloth ahead of time. We made up a filler paste from epoxy and milled fibres (heavier but a lot stronger than using microballoons) and filled all the seams and tiewrap holes.

Rather than let this cure and sand it back, we went straight ahead and glassed over it. The squeegee action to wet out the cloth takes care of any rough bits of filler while it's all still wet.

This was wet out in the usual way (at least it's usual for home built aircraft builders) - pour a little resin on then squeegee the bejesus out of it to see how far the resin will go whilst still wetting it out fully.

It still used loads of resin. It's a good thing I bought another 6kg pack of the stuff!

I've been a victim of Village Photos falling off the edge of the world...
I have made up the dagger board case though and marked out the slot which needed to be cut out of the hull:

I hacked a hole in the bottom and the daggerboard case fits in it:

The rectangular case therefore pokes through the bottom of the hull at either end, so I traced it out with a Sharpie pen ...

It was trimmed accordingly and now fits nicely

Ready to mix up some thick epoxy with milled fibres and glue it in - but I think I'll make up the frames either side first and stick them in at the same time.

I have made up the dagger board case though and marked out the slot which needed to be cut out of the hull:

I hacked a hole in the bottom and the daggerboard case fits in it:

The rectangular case therefore pokes through the bottom of the hull at either end, so I traced it out with a Sharpie pen ...

It was trimmed accordingly and now fits nicely

Ready to mix up some thick epoxy with milled fibres and glue it in - but I think I'll make up the frames either side first and stick them in at the same time.

I need to rebuild many threads on many forums thanks to the Village Photos webhost disappearing and not renewing the security certificate.
In the mean time though, I've started adding the lower rubbing strips. These are temporarily screwed in place whilst the epoxy cures.

The screws are out now, actually, and I'm ready to glue the next lamination on, which will be screwed from the inside this time.
In the mean time though, I've started adding the lower rubbing strips. These are temporarily screwed in place whilst the epoxy cures.

The screws are out now, actually, and I'm ready to glue the next lamination on, which will be screwed from the inside this time.
Gassing Station | Boats, Planes & Trains | Top of Page | What's New | My Stuff