Stainless outriggers
Discussion
Well, I've pulled my finger our at last and put the last nut and bolt on, to complete the second side stainless outrigger upgrade.
This one was a little trickier than the first one as the fuel pipes fun along the outrigger, so have to be moved out of the way before and replaced after.
However it was all done with the body on, so minimal hassle and disturbance.
Also attached are a few pics of the view of the fist one I did (nearside) that is still shinney after a couple of years on the car. And, more to the point, still firmly attached!
I have painted over the welds with silver hammerite because they tend to rust with the type of welding wire I was recommended.
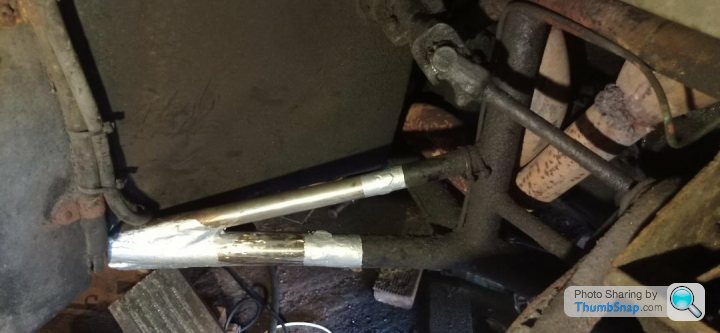
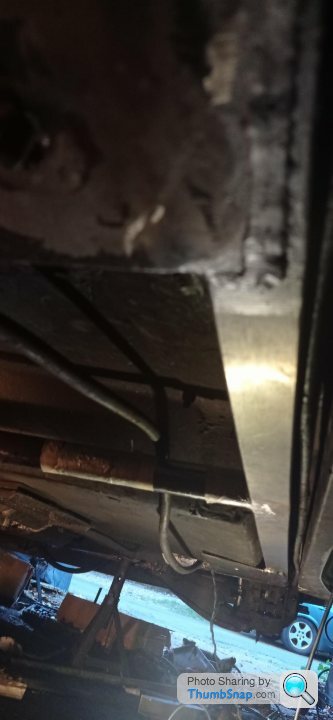
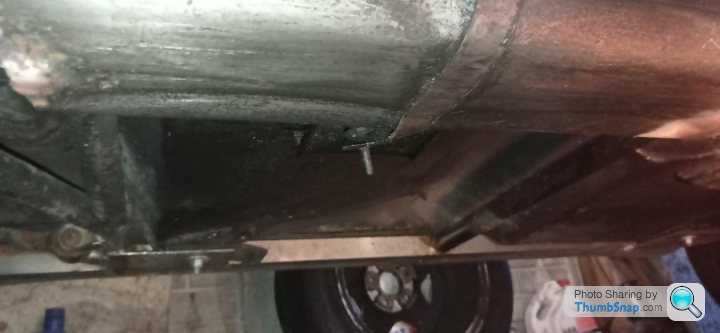
This one was a little trickier than the first one as the fuel pipes fun along the outrigger, so have to be moved out of the way before and replaced after.
However it was all done with the body on, so minimal hassle and disturbance.
Also attached are a few pics of the view of the fist one I did (nearside) that is still shinney after a couple of years on the car. And, more to the point, still firmly attached!
I have painted over the welds with silver hammerite because they tend to rust with the type of welding wire I was recommended.
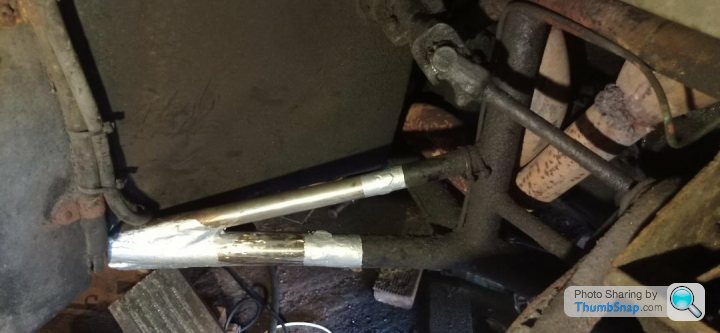
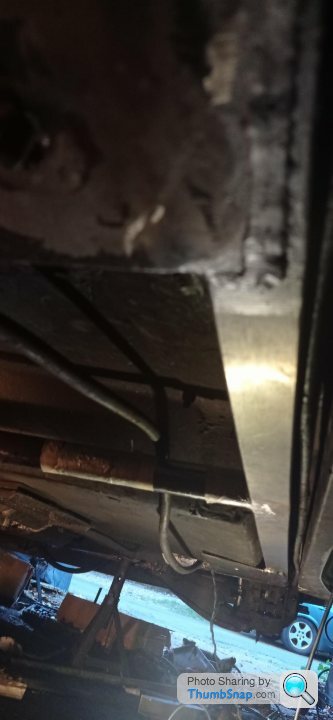
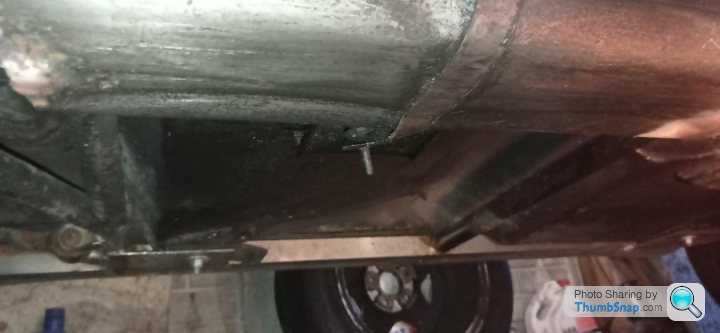
complete non-sense, imo.
not quite so corrosion-resistant "stainless steels", such as CrMn 45-12, for example, can be welded halfway permanently on a normal steel tube.
If you join a stainless steel with a "rusting" steel, such as structural steels, this is called a black and white joint. This weld seam should be welded with a high-alloy filler metal. After completion of the weld, the seam will of course slowly rust, even with stainless steel, because the mild steel melt naturally runs into the stainless steel during welding.
Due to the different colouring in the microsection, joint welds between unalloyed steels and stainless materials are referred to as black-white joints. The greatest challenge is to avoid martensite formation and the associated susceptibility to cracking. The following measures must be taken to achieve this:
Welding without filler metal is generally not permitted
Unalloyed filler metals lead to a fully martensitic structure and are therefore unusable.
By using over-alloyed filler metals such as 1.4370 or, even better, 1.4332, an almost martensite-free microstructure can be achieved.
not quite so corrosion-resistant "stainless steels", such as CrMn 45-12, for example, can be welded halfway permanently on a normal steel tube.
If you join a stainless steel with a "rusting" steel, such as structural steels, this is called a black and white joint. This weld seam should be welded with a high-alloy filler metal. After completion of the weld, the seam will of course slowly rust, even with stainless steel, because the mild steel melt naturally runs into the stainless steel during welding.
Due to the different colouring in the microsection, joint welds between unalloyed steels and stainless materials are referred to as black-white joints. The greatest challenge is to avoid martensite formation and the associated susceptibility to cracking. The following measures must be taken to achieve this:
Welding without filler metal is generally not permitted
Unalloyed filler metals lead to a fully martensitic structure and are therefore unusable.
By using over-alloyed filler metals such as 1.4370 or, even better, 1.4332, an almost martensite-free microstructure can be achieved.
Well, like I said, the other side has been on there for 3 years and doing well. No signs of any joints cracking.
For the joints I was recommended to use 309L which, as you know, has a composition of 24% chromium and 13% nickel with a maximum carbon content of 0.03%, and is formulated for this very purpose.
Of course, there's more to it than that, and my method was to totally overengineer the join areas, where the metal is 3.6mm-4.0mm thick (where the usual tube thickness is 2mm). But, to the naked eye, it looks like a straight join.
For the joints I was recommended to use 309L which, as you know, has a composition of 24% chromium and 13% nickel with a maximum carbon content of 0.03%, and is formulated for this very purpose.
Of course, there's more to it than that, and my method was to totally overengineer the join areas, where the metal is 3.6mm-4.0mm thick (where the usual tube thickness is 2mm). But, to the naked eye, it looks like a straight join.
Gassing Station | Wedges | Top of Page | What's New | My Stuff