Heater stepper motor problem.
Discussion
The short version: https://youtu.be/RO6iuAUaCPs
The long version:
I rebuilt my Tuscan and in the course of rebuilding it, I had the heater ECU looked at because the temperature and blower control did not work. They came back from repair and apparently worked so I fitted them. A few months later the heater temperature stopped working so I bought a new one from TVR power. They said the motor mechanism was a new design/supplier and needed the arm on the stepper motor gearbox to be made shorter. TVR Power said to replace the steel connection arm between the stepper motor and the hot/cold flap with an aluminium arm which was shorter. The motor worked fine, but I did notice a horrible noise (buurrrrrrmmmm) at every ignition cycle.
A year later and the same thing again, no heat control. I removed the stepper motor again (which is a complete pain in the back) and the gearbox appeared to be slipping. It would push the flap upwards to a point and then drop. So that looked like the stepper motor's gearbox had failed. Back to TVR power and the diagnosis was "over rotation".
I had to buy a new one and had before fitting it properly I connected the wiring and took a look at the behaviour of the arm. The issue I found was that the stepper motor ECU moves the arm anticlockwise 90 degrees every ignition cycle, regardless of its previous/starting position. Therefore, if the flap was at the fully cold position, the motor would try and rotate 90 degrees anticlockwise. This obviously puts huge strain on the mechanism, and with the new motor/gearbox assembly (stepper motor), the bd is so strong it is stretching and bending the aluminium arm. I think the horrible noise I experienced before was the motor rotating but being unable to go beyond a certain point.
My car is a Jan 2000 Tuscan Mk1, and we all know they changed stuff as they went through production. Does anyone have a cut off switch to tell the stepper motor that the flap is fully down and in the fully cold position? From what I can work out, the ECU seems to trying to find a zero position.
I've read on PH about the cluster settings for the fine tuning of the flap position, but my cluster is an early one and I have no control over the flapper preset position. I have access to no settings at all besides the buzzer tone, brightness and some other variable. I've been trying to contact Paul Smith who did the original ECU repair but have had no luck yet. Can anyone else shed some light on why I'm having problems. Its seems that the stepper motor failing isn't uncommon. It sounds like a software issue to me. I've tried to make a cut off switch but that didn't work out.
Any thoughts, experience or advice is more than welcome. I'd love to drive my car this year!, but all the while the heater matrix is loose in the engine bay, I can't drive the car , which is really upsetting considering the weather we've had recently.
Cheers,
Martin
The long version:
I rebuilt my Tuscan and in the course of rebuilding it, I had the heater ECU looked at because the temperature and blower control did not work. They came back from repair and apparently worked so I fitted them. A few months later the heater temperature stopped working so I bought a new one from TVR power. They said the motor mechanism was a new design/supplier and needed the arm on the stepper motor gearbox to be made shorter. TVR Power said to replace the steel connection arm between the stepper motor and the hot/cold flap with an aluminium arm which was shorter. The motor worked fine, but I did notice a horrible noise (buurrrrrrmmmm) at every ignition cycle.
A year later and the same thing again, no heat control. I removed the stepper motor again (which is a complete pain in the back) and the gearbox appeared to be slipping. It would push the flap upwards to a point and then drop. So that looked like the stepper motor's gearbox had failed. Back to TVR power and the diagnosis was "over rotation".
I had to buy a new one and had before fitting it properly I connected the wiring and took a look at the behaviour of the arm. The issue I found was that the stepper motor ECU moves the arm anticlockwise 90 degrees every ignition cycle, regardless of its previous/starting position. Therefore, if the flap was at the fully cold position, the motor would try and rotate 90 degrees anticlockwise. This obviously puts huge strain on the mechanism, and with the new motor/gearbox assembly (stepper motor), the bd is so strong it is stretching and bending the aluminium arm. I think the horrible noise I experienced before was the motor rotating but being unable to go beyond a certain point.
My car is a Jan 2000 Tuscan Mk1, and we all know they changed stuff as they went through production. Does anyone have a cut off switch to tell the stepper motor that the flap is fully down and in the fully cold position? From what I can work out, the ECU seems to trying to find a zero position.
I've read on PH about the cluster settings for the fine tuning of the flap position, but my cluster is an early one and I have no control over the flapper preset position. I have access to no settings at all besides the buzzer tone, brightness and some other variable. I've been trying to contact Paul Smith who did the original ECU repair but have had no luck yet. Can anyone else shed some light on why I'm having problems. Its seems that the stepper motor failing isn't uncommon. It sounds like a software issue to me. I've tried to make a cut off switch but that didn't work out.
Any thoughts, experience or advice is more than welcome. I'd love to drive my car this year!, but all the while the heater matrix is loose in the engine bay, I can't drive the car , which is really upsetting considering the weather we've had recently.
Cheers,
Martin
On the mk 1, the 90 deg rotation at key on is normal. It's such a basic control system that it doesn't use limit switches or potentiometers to determine its position. It literally commands the flap motor to run for 10s (or whatever) to ensure it closes the flap is fully closed, regardless of motor stall or not.
It then goes from there with adjusting the position of the motor/flap based on how many cumulative seconds (+ and -) power has been applied to the motor since key on. That's how it works out its position.
It's a horribly crude system and would need a redesigned heater ECU logic and a stepper motor with a position potentiometer on it to sort.
It then goes from there with adjusting the position of the motor/flap based on how many cumulative seconds (+ and -) power has been applied to the motor since key on. That's how it works out its position.
It's a horribly crude system and would need a redesigned heater ECU logic and a stepper motor with a position potentiometer on it to sort.
dvs_dave said:
On the mk 1, the 90 deg rotation at key on is normal. It's such a basic control system that it doesn't use limit switches or potentiometers to determine its position. It literally commands the flap motor to run for 10s (or whatever) to ensure it closes the flap is fully closed, regardless of motor stall or not.
It then goes from there with adjusting the position of the motor/flap based on how many cumulative seconds (+ and -) power has been applied to the motor since key on. That's how it works out its position.
It's a horribly crude system and would need a redesigned heater ECU logic and a stepper motor with a position potentiometer on it to sort.
Wow, that is rather surprising! So the "system" relies on the motor being overpowered/blocked from rotating by the flap being fully closed and either the gearbox slipping or the motor's force being overcome. That surely will burn out the motor with time or strip the teeth on the gearbox.It then goes from there with adjusting the position of the motor/flap based on how many cumulative seconds (+ and -) power has been applied to the motor since key on. That's how it works out its position.
It's a horribly crude system and would need a redesigned heater ECU logic and a stepper motor with a position potentiometer on it to sort.
Having observed the motor the last time I installed it, the new aluminium arm, that TVR power provided with the new motor, bent the right angles at either end. The flap mounting bracket bent as well, which in combination with the bending arm meant that the motor arm managed to rotate into a position that is 180degrees out.
So basically, there are two options, reinforce the brackets and replace the Ali arm for a steel one, and keep the existing ecu logic, or redesign the ecu logic. I haven't got those electrical skills unfortunately. I will see if I can get that cut off switch working.
How do the later flaps work? Is it feasible to retrofit the newer system into my car?
Thanks for the input dvs_Dave.
When I did my motor setting up I had similar issues, in the end to get it to work correctly, I removed the arm, set the heater control to minimum and them switched the ignition on. The motor then cycles through full open to shut cycle and the stops. At this point connect the arm with the flap shut and fingers crossed it should work, we it did for me! Test before screwing back together :-)
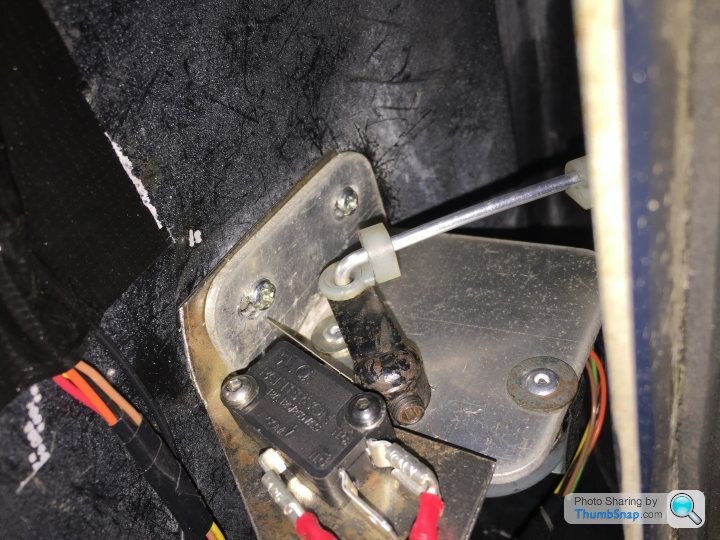
I think I've worked out a solution. Using one of the 12v wires, I used a micro switch to cut off power to the motor when in the fully cold position. This stops the motor over stressing the gearbox and flap/arm.
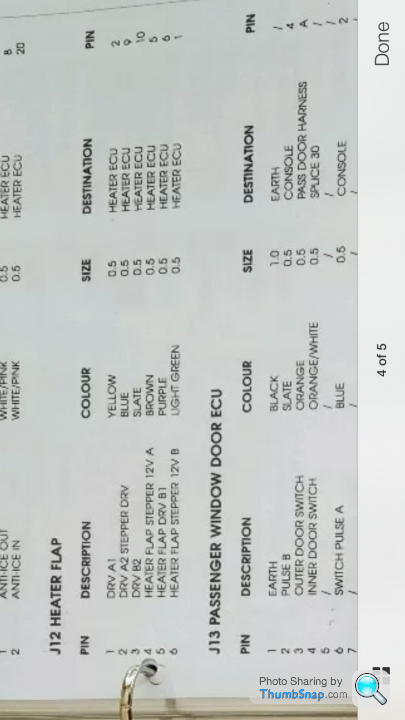
It's the light green wire that powers the hot to cold direction of the motor.
http://youtu.be/Upq-tmR0avU
http://youtu.be/UlT6sGvH55g
By the way, my Tuscan Mk2 has this microswitch mounted from factory already.
But the Switch gets in contact to the flap not to the actuating arm.
Due to this cars are 10 years and older the flap not closes airtight because the rubber glued on the flap to
ensure proper sealing was only laying around and not sealing anymore on my car.
Easy to test:When heater matrix is unmounted, switch on cold air and blower.
Then there should come no air on heater matrix side!
Also mounting a valve on water side is not a proper fix, when AC is on air is going along
the heater matrix side and air flow along aircon Matrix is low. so not enough cold air will
enter passenger cabin.
Took 6 hours to fix all properly, a lot of work, but now ice cold air, and proper working of flap
(3 green lights from cold flap is 20% open!)
All can be done without regassing aircon and without draining cooling water, but you get bloody fingers
to get the both heatexchangers out!
Uwe
But the Switch gets in contact to the flap not to the actuating arm.
Due to this cars are 10 years and older the flap not closes airtight because the rubber glued on the flap to
ensure proper sealing was only laying around and not sealing anymore on my car.
Easy to test:When heater matrix is unmounted, switch on cold air and blower.
Then there should come no air on heater matrix side!
Also mounting a valve on water side is not a proper fix, when AC is on air is going along
the heater matrix side and air flow along aircon Matrix is low. so not enough cold air will
enter passenger cabin.
Took 6 hours to fix all properly, a lot of work, but now ice cold air, and proper working of flap
(3 green lights from cold flap is 20% open!)
All can be done without regassing aircon and without draining cooling water, but you get bloody fingers
to get the both heatexchangers out!
Uwe
I’m trying to use this micro switch method on my mk1 Tuscan but can’t get it to work. The light green wire mentioned above is to a centre tap feed of the unipolar stepper motor which doesn’t switch off the motor if disconnected but reduces the torque to that phase of the motor.
I tried connecting the micro switch to one of the phase wires ( any of the four non centre taps) and when the micro switch is engaged the motor stops (stalls) but when the direction is reversed by the stepper motor ecu it doesn’t drive the motor off the micro switch. It seems to be a one-way trip. I’ve tried fiddling around with the position of the micro switch so that it only just engages in the cold position but no luck.
Am I doing something wrong?
Is there an alternative way to use the micro switch to temporarily cut power or stall the motor until the reverse direction signals come from the heater ecu?
I tried connecting the micro switch to one of the phase wires ( any of the four non centre taps) and when the micro switch is engaged the motor stops (stalls) but when the direction is reversed by the stepper motor ecu it doesn’t drive the motor off the micro switch. It seems to be a one-way trip. I’ve tried fiddling around with the position of the micro switch so that it only just engages in the cold position but no luck.
Am I doing something wrong?
Is there an alternative way to use the micro switch to temporarily cut power or stall the motor until the reverse direction signals come from the heater ecu?
Dalamar said:
I’m trying to use this micro switch method on my mk1 Tuscan but can’t get it to work. The light green wire mentioned above is to a centre tap feed of the unipolar stepper motor which doesn’t switch off the motor if disconnected but reduces the torque to that phase of the motor.
I tried connecting the micro switch to one of the phase wires ( any of the four non centre taps) and when the micro switch is engaged the motor stops (stalls) but when the direction is reversed by the stepper motor ecu it doesn’t drive the motor off the micro switch. It seems to be a one-way trip. I’ve tried fiddling around with the position of the micro switch so that it only just engages in the cold position but no luck.
Am I doing something wrong?
Is there an alternative way to use the micro switch to temporarily cut power or stall the motor until the reverse direction signals come from the heater ecu?
Hi Dalamar, I had completely forgotten I did this to my tuscan and I no longer have it. Sorry. Everything I did was in the post above. Maybe the wiring was changed later in production of the mk1?I tried connecting the micro switch to one of the phase wires ( any of the four non centre taps) and when the micro switch is engaged the motor stops (stalls) but when the direction is reversed by the stepper motor ecu it doesn’t drive the motor off the micro switch. It seems to be a one-way trip. I’ve tried fiddling around with the position of the micro switch so that it only just engages in the cold position but no luck.
Am I doing something wrong?
Is there an alternative way to use the micro switch to temporarily cut power or stall the motor until the reverse direction signals come from the heater ecu?
Martin
Hello Martin. Thanks for the quick reply and I think you’re right. My PCB is the very first design with the square stepper motor driver chip.
I think I’ll have to come up mechanical solution of some kind.
Thanks also for posting those YouTube videos. They helped me identify which gearbox ratio I needed to achieve the 90 degree rotation on ignition on or moving to max heat.
I think I’ll have to come up mechanical solution of some kind.
Thanks also for posting those YouTube videos. They helped me identify which gearbox ratio I needed to achieve the 90 degree rotation on ignition on or moving to max heat.
Dalamar said:
Hello Martin. Thanks for the quick reply and I think you’re right. My PCB is the very first design with the square stepper motor driver chip.
I think I’ll have to come up mechanical solution of some kind.
Thanks also for posting those YouTube videos. They helped me identify which gearbox ratio I needed to achieve the 90 degree rotation on ignition on or moving to max heat.
You're welcome. Hope you get it sorted soon.I think I’ll have to come up mechanical solution of some kind.
Thanks also for posting those YouTube videos. They helped me identify which gearbox ratio I needed to achieve the 90 degree rotation on ignition on or moving to max heat.
Gassing Station | Tuscan | Top of Page | What's New | My Stuff