Stereo Lithography
Discussion
AFAIK, SLS and SLA models are not durable enough for production parts. I've had some made before, but only to use as visual aids, or for packaging or a quick look-see. First part was a heater blower wheel - it lasted about an hour (early lay-up style). They do still tend to be a bit fragile IMHO. And expensive. But quick turn around direct from CAD model.
Jordan use SLS to produce components that are used on their cars and these stay on for up to 3 races, so presumably would be fairly durable for low stress components in a road car ?
Any chance someone could explain how this actually works ? (pref. in English for the hard of thinking
)
Any chance someone could explain how this actually works ? (pref. in English for the hard of thinking

mrsd said:From my knowledge, it is generally a medium in a workspace, which is then partially (a layer or slice of the geometry) hardened by a 2D-moving "tool". After one layer is hardened, the next one builds up on that by
[url]Any chance someone could explain how this actually works ? (pref. in English for the hard of thinking )
a) moving the tool one unit upwards or
b) moving the workpiece one unit downwards
(A unit is a layer thickness, which is less than 0.1mm.)
The layers stick firmly together.
I've had an eye on two processes:
one has a laser, which hardenes resin; the workspace is filled with liquid resin, and a table is moving the hardened geometry downwards in a hutch. After hardening, the workpiece is fished out of the bath and will be dried. IIRC the original Stereo Lithography.
The other process uses a standard HP printer head, which prints water, or even colored water on clay powder.
A brush brushes dry powder in layer-height over the entire workpiece, and the printer prints one slice on that, and hardens the geometry. The operator has to dig out the part when the process is finished.
Additives could make the material harder, or more elastic.
Additions and corrections welcome to the above

mrsd said:
Any chance someone could explain how this actually works ? (pref. in English for the hard of thinking )
There are a few different processes, Bodo has explained the SLA system (liquid resin) and 3D printing systems. A couple of others are Selective Laser Sintering and Fused Deposition Modelling.
The main thing with all these processes is that they are additive processes, whereas traditional machining is a subtractive process.
SLS usues powder, which is "sintered" (melted to the point of fusing) by a laser in a 2D slice, then another layer of powder is added and rolled smooth. This can manufacture parts in various nylons, a rubber type material and even metals. Note that as it is made up of fused powder it is porous until infiltrated with another material.
This is what the jordan nose cone uses.
FDM lays down a thin bead of hot material (normally nylon) in a 2D pattern which adheres to the material below it (so build too fast and it'll sag to a sloppy mess!) Kind of like modelling with a toothpaste tube ! I think Dyson have a few of these.
Most of these processes can run almost completely unattended 24hrs a day.
I also seem to remember that some bits were tested and approved for use by NASA a couple of years ago.
SLA parts have been around the longest and use a liquid photopolymer (liquid that sets under a laser), these were very brittle, but have improved. My choice for real parts is still SLS.
Time to hang up the anorak for the day.

Bodo said:
one has a laser, which hardenes resin; the workspace is filled with liquid resin, and a table is moving the hardened geometry downwards in a hutch. After hardening, the workpiece is fished out of the bath and will be dried. IIRC the original Stereo Lithography.
Workspace ? Hutch

Am I corrected in envisioning a 'goldfish bowl' of resin with a platform in it, onto which the laser 'paints' a layer of the part which then hardens, then the table moves down a few thou, then another layer is 'painted' and so on ??? (this is what a site on SLA seemed to show...)
mrsd said:I tried hardest to use English, but since I only learnt that language a few years ago, I'm not very good in explaining state-of-the-art technologies. sorry
Workspace ? Hutch ![]()
Am I corrected in envisioning a 'goldfish bowl' of resin with a platform in it, onto which the laser 'paints' a layer of the part which then hardens, then the table moves down a few thou, then another layer is 'painted' and so on ??? (this is what a site on SLA seemed to show...)

Anyway, I've discovered a workaround for my deficit in expression:
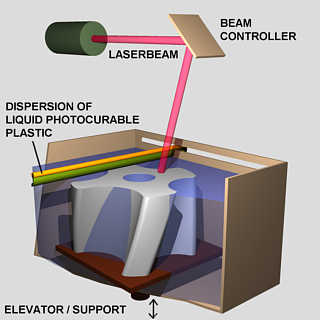
The light brown box is what I meant with hutch, and the platform is the darkbrown support

Wow! I think the quick answer for Mrsd was 'yes'.
Fairly big parts are possible, but not complete car body size in one shot.
The technique certainly has its uses, but mainly for large volume manufacture where the cost can be spread out. It's also reliant upon good quality CAD system output, so no good for Wind tunnel models unless that's where you're designing the bodywork. Producing stylish bodywork is an art and CAD systems don't do art
(BMW Z4
) Leave it to PW, his best ferret and a drum of filler.
>> Edited by rat on Thursday 19th June 17:59
Fairly big parts are possible, but not complete car body size in one shot.
The technique certainly has its uses, but mainly for large volume manufacture where the cost can be spread out. It's also reliant upon good quality CAD system output, so no good for Wind tunnel models unless that's where you're designing the bodywork. Producing stylish bodywork is an art and CAD systems don't do art


>> Edited by rat on Thursday 19th June 17:59
Have to add a part made by 3d-printing...
... and a link with a small sales presentation of a printer's function from the manufacturer:
www.zcorp.com/products/demo.asp?ID=1

... and a link with a small sales presentation of a printer's function from the manufacturer:
www.zcorp.com/products/demo.asp?ID=1
mrsd said:It were exactly the words 'hutch' and 'workspace', I had problems with (language that is); it would be coincidence if they are engineer-ish
Thankyou Nothing wrong with your English Bodo, I think it was just that I don't speak engineer

Anyway, good to get some feedback, when I have problems to express myself; I've no idea, how many disaccords and misunderstandings I've left on Gassing Station due to my humble knowledge of communication in foreign languages, and the lack of feedback/correction.

So thank you for reasking this and the other case.




Ian
rat said:
It's also reliant upon good quality CAD system output, so no good for Wind tunnel models unless that's where you're designing the bodywork. Producing stylish bodywork is an art and CAD systems don't do art![]()
I think most major manufacturers have "Class A" surfacing facilities used for car body design. Though sometimes they make a clay mock up then scan and reverse engineer that back into CAD to create the tooling. Also a lot of CFD (Computational Fluid Dynamics) work is carried out on the shape before it gets as far as a wind tunnel.
No RP system I know of could produce surface finishes suitable for wind tunnel testing straight off the machine. It would need finishing/polishing first. I'm sure I've seen RP models in reduced size wind tunnel tests at some race teams but I wouldn't swear to it(might have been Arrows anyway so I guess that wouldn't count any more!)
And CAD can do art for art's sake [url] www.bathsheba.com/sculpture/antipot/ [/url]
There's a whole industry creating CAD/RP art, gives the artist freedom to create work that would be almost impossibe to sculpt/cast.
Gassing Station | General TVR Stuff & Gossip | Top of Page | What's New | My Stuff