Stuart 10V Vertical Steam Engine
Discussion
Yes, yours looks great.
The width of my valve chest was defined by the width of the cylinder port face (exactly 1" on the drawing, which mine is). The 1" dimension is in turn defined from the cylinder axis to valve face (that's also correct to within 0.011").
Then there is plus 0.5 mm per side to allow for flush fitting of the lagging.That figure is what the valve chest is machined to. The height of the valve chest is fine - the cover plate had plenty of excess on that, but the width was marginal to start with.
So long as the cover ends up central, the slight step around it doesn't bother me - in fact it breaks up the blocky look of the assembly a bit.
The width of my valve chest was defined by the width of the cylinder port face (exactly 1" on the drawing, which mine is). The 1" dimension is in turn defined from the cylinder axis to valve face (that's also correct to within 0.011").
Then there is plus 0.5 mm per side to allow for flush fitting of the lagging.That figure is what the valve chest is machined to. The height of the valve chest is fine - the cover plate had plenty of excess on that, but the width was marginal to start with.
So long as the cover ends up central, the slight step around it doesn't bother me - in fact it breaks up the blocky look of the assembly a bit.
So I made a start on the cylinder covers, firstly the top one, because It’s much less critical than the lower. The only feature that’s important is the spigot that fits into the cylinder.
I chucked the cast iron bar in the three jaw, faced and turned to size: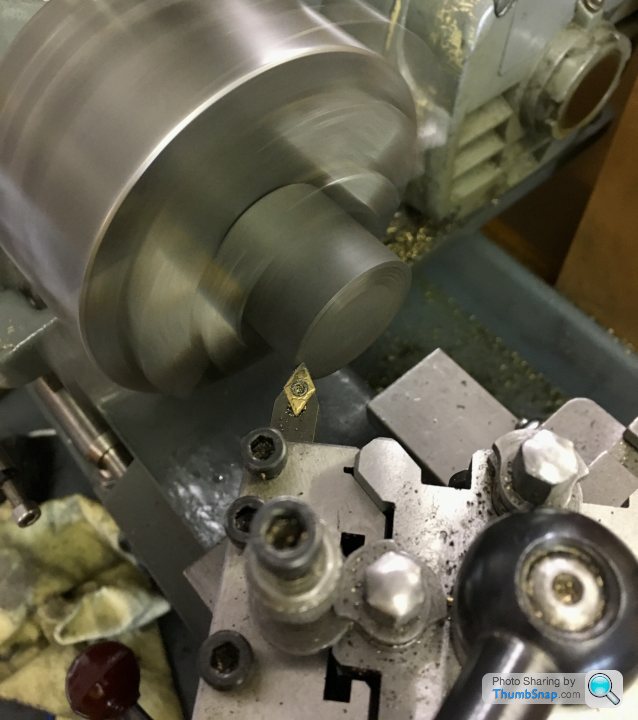
Then turned the inner spigot, to be a good fit in the bore diameter:
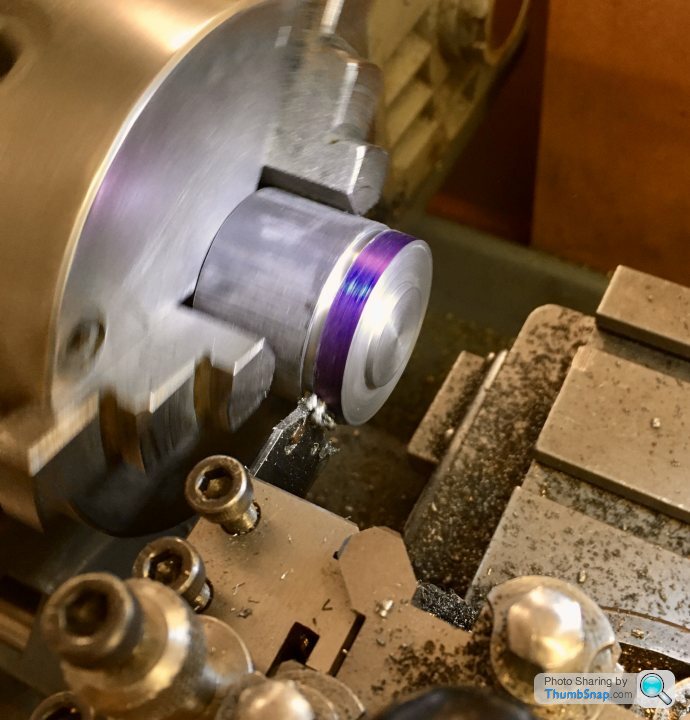
I started to part-off the job, with the intention of reversing it in the chuck and turning the top features. It seemed to be going well, so I decided to part it in two stages- the first to form the upper boss, then move the tool back and part off from the stock:
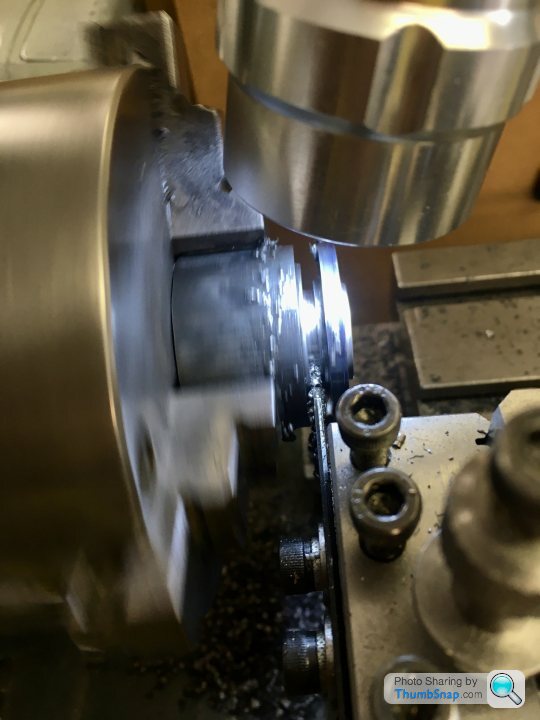
It actually worked pretty well, but some clean-up was required anyway, and due to this the top boss is a bit short (not that it matters). On balance I should have parted off, reversed and just turned the other side as normal. In the end my initial method could have worked, but as usual didn’t quite.
Anyway, it fits the cylinder, and it’s gasket, and it looks ok:
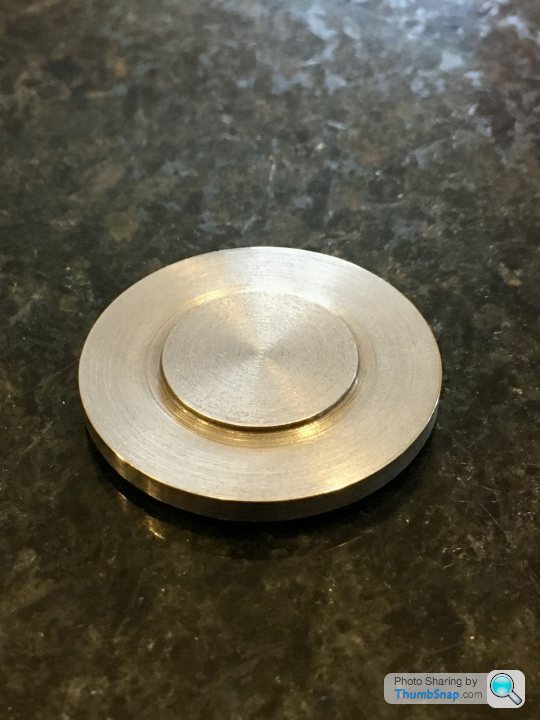
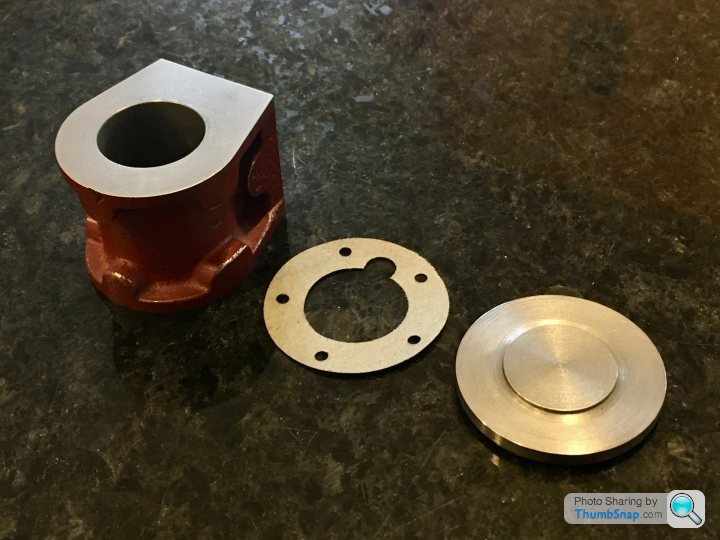
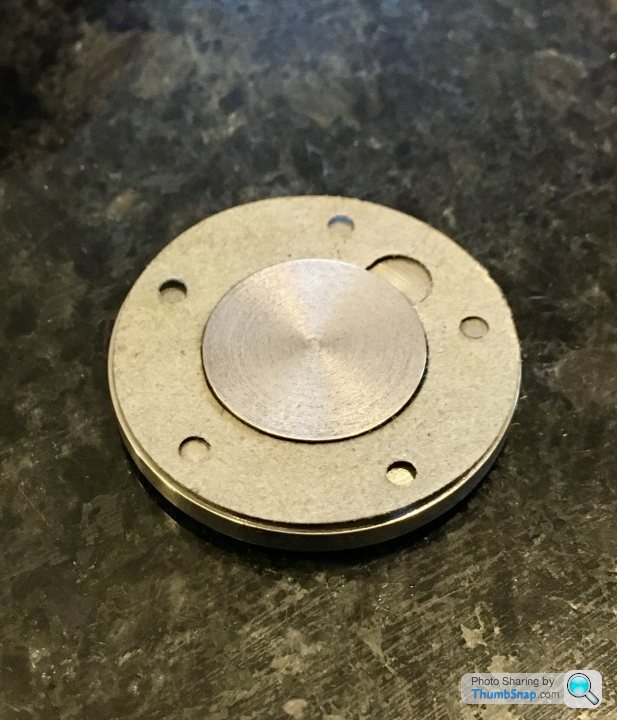
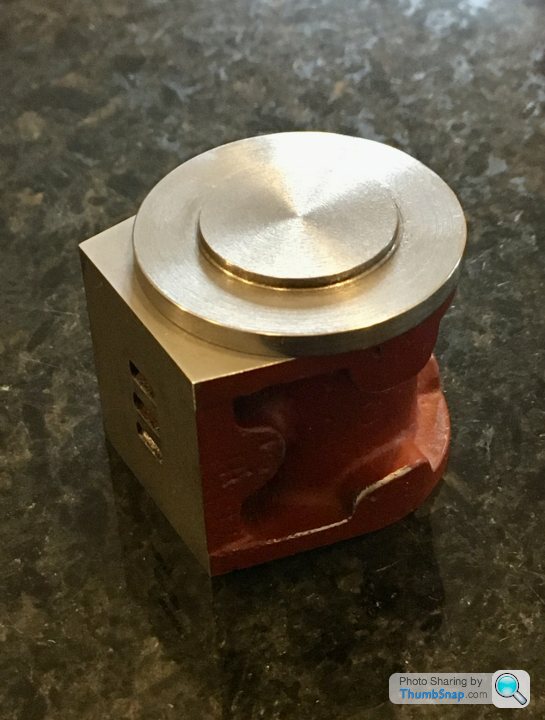
I was hoping the overhang would be concentric around the circular portion, so the lagging plate would be a flush fit. Unfortunately it’s not the case:
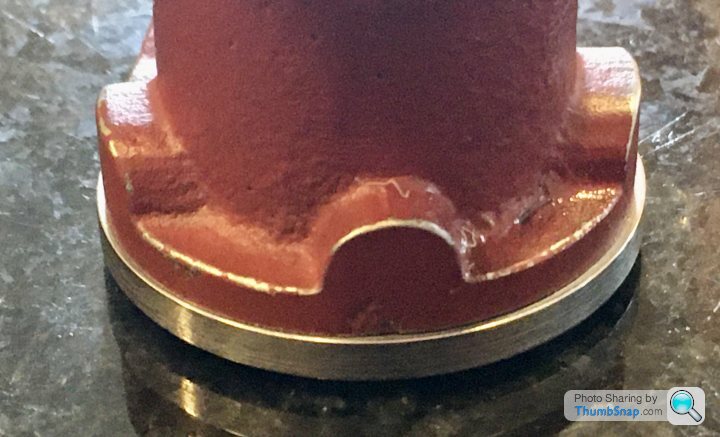
So some filing will be needed. Pretty sure I setup the casting pretty much as good as it could have been, so I wonder if the cast surface is slightly bulged? No big deal.
So next the lower cover. I still don’t really know how to reverse and hold it.
I chucked the cast iron bar in the three jaw, faced and turned to size:
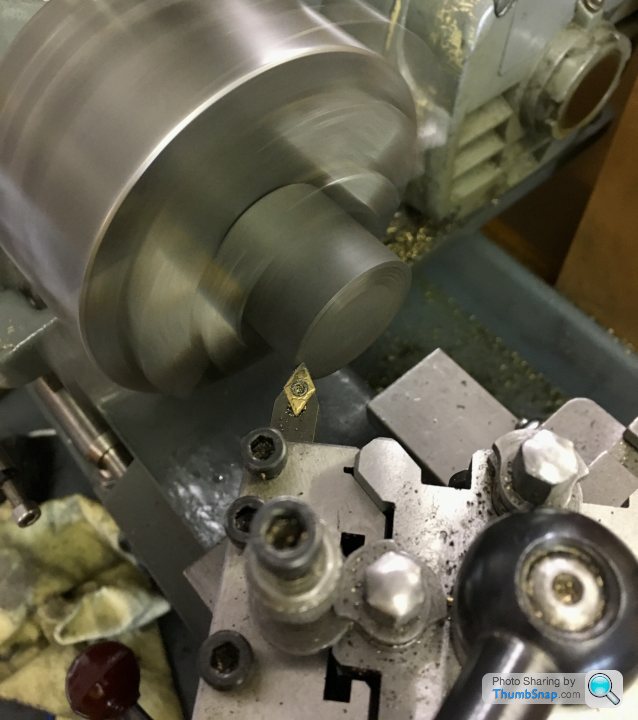
Then turned the inner spigot, to be a good fit in the bore diameter:
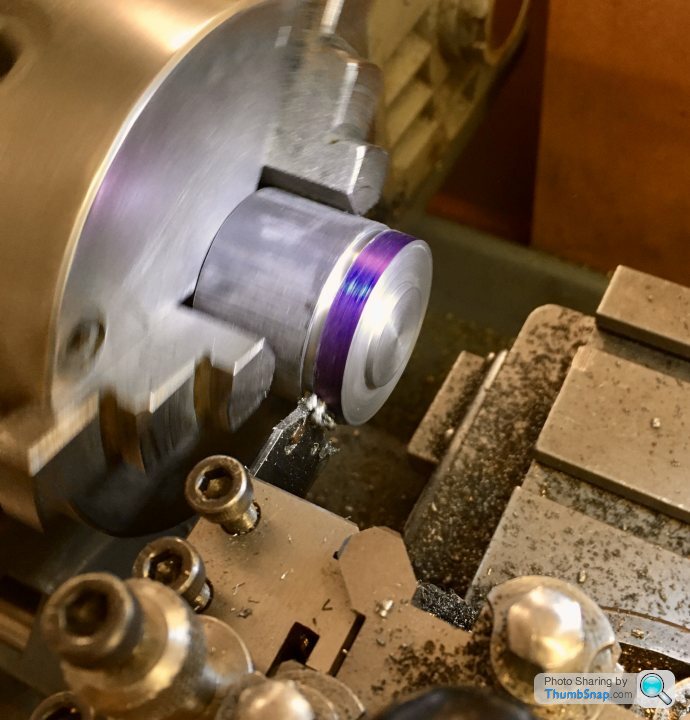
I started to part-off the job, with the intention of reversing it in the chuck and turning the top features. It seemed to be going well, so I decided to part it in two stages- the first to form the upper boss, then move the tool back and part off from the stock:
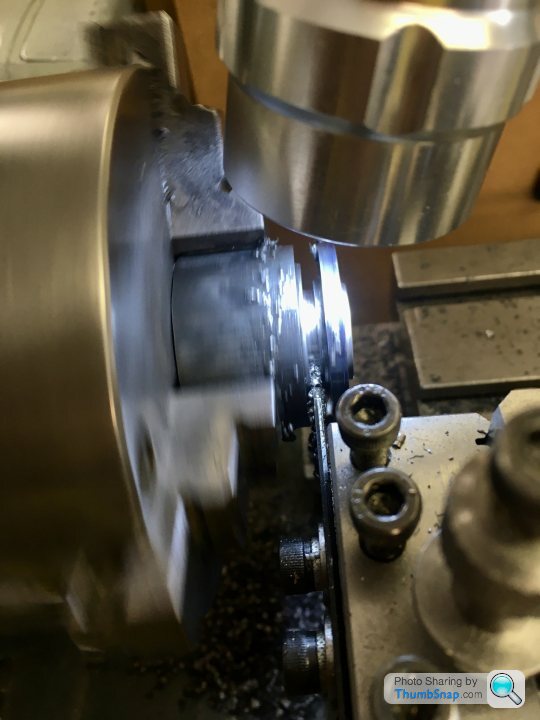
It actually worked pretty well, but some clean-up was required anyway, and due to this the top boss is a bit short (not that it matters). On balance I should have parted off, reversed and just turned the other side as normal. In the end my initial method could have worked, but as usual didn’t quite.
Anyway, it fits the cylinder, and it’s gasket, and it looks ok:
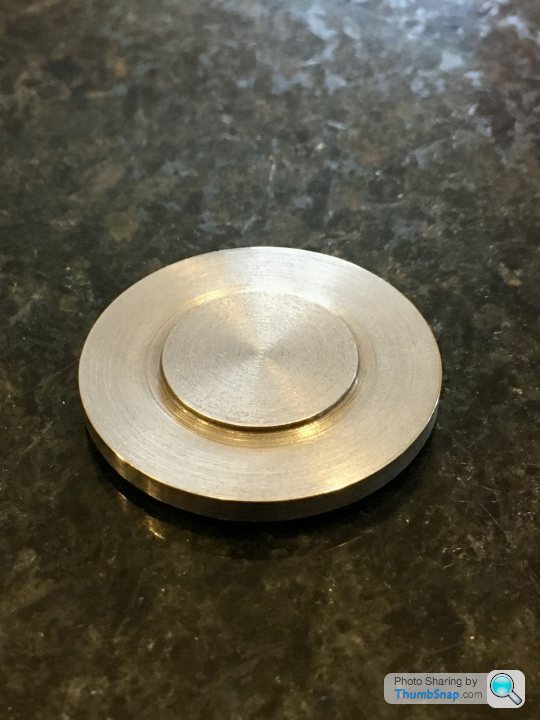
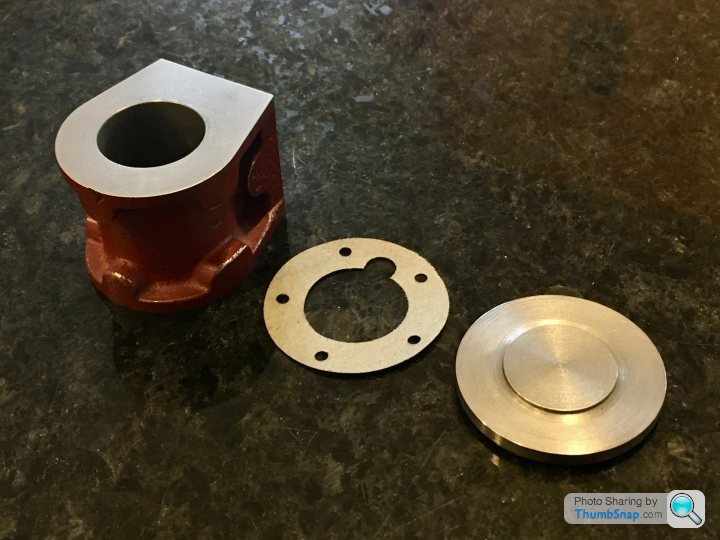
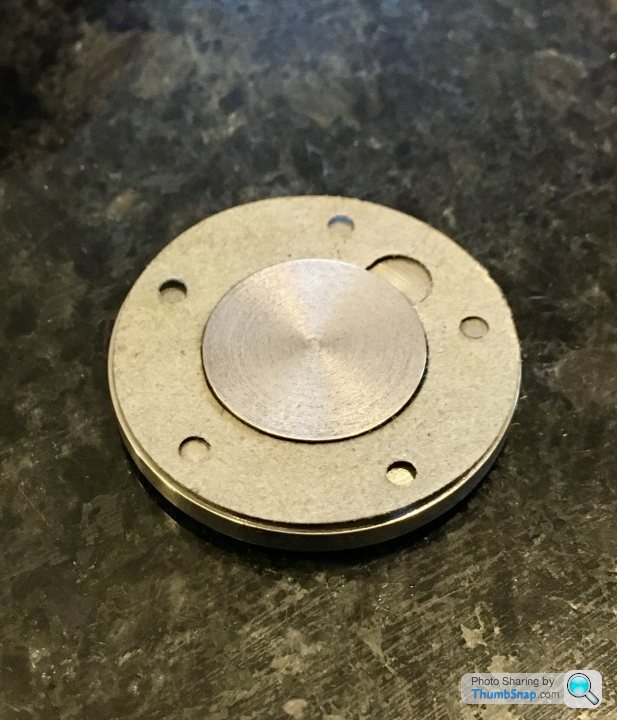
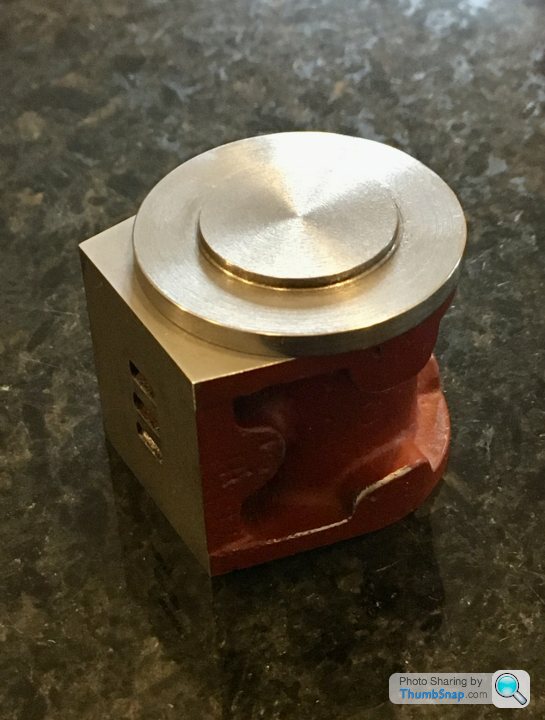
I was hoping the overhang would be concentric around the circular portion, so the lagging plate would be a flush fit. Unfortunately it’s not the case:
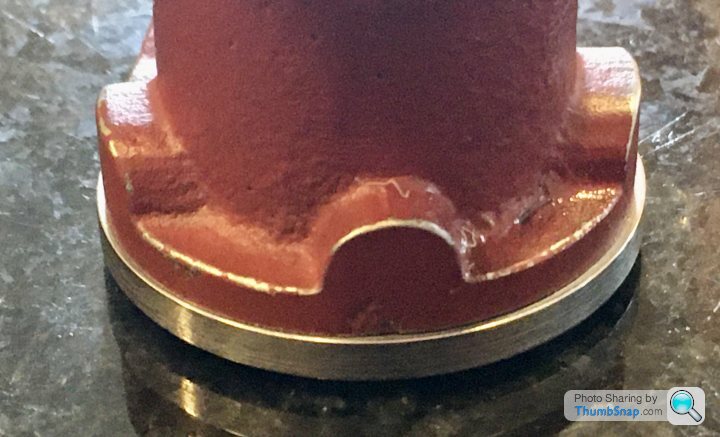
So some filing will be needed. Pretty sure I setup the casting pretty much as good as it could have been, so I wonder if the cast surface is slightly bulged? No big deal.
So next the lower cover. I still don’t really know how to reverse and hold it.
fourfoldroot said:
Knock up something like this. Turn it to spigot size,slit it, and when you put it back in 3 jaw you can do what you like with perimeter and other side. 
Someone on the ME forum just posted the exact same thing, but in CAD. 
I'll do it tomorrow.
Cheers!
ETA I'm scanning some of my old '70s & '80's F1 pictures in at the moment for the F1M forum. Many of them taken by my Dad with his trusty Olympus Trip 35.
fourfoldroot said:
Forgot to add, when you make split collet, centre punch it adjacent to jaw one on chuck, so when you put it back in it remains concentric. If it is good fit for spigot, you won’t be far out. I mark all mandrels so they go back in same position,even a good 3 jaw is a bit out.
Thanks, yes that was mentioned too. I can't use my three jaw for consistent work, so I'll have to be careful. Ill also have to remember to break the edges of the part so it fits snugly into the corners of the fixture.Nice collection of cameras by the way - you still use film? I've got my Dad's Olympus here in a drawer, still in its original zipped bag.
fourfoldroot said:
dr_gn said:
Thanks, yes that was mentioned too. I can't use my three jaw for consistent work, so I'll have to be careful. Ill also have to remember to break the edges of the part so it fits snugly into the corners of the fixture.
Nice collection of cameras by the way - you still use film? I've got my Dad's Olympus here in a drawer, still in its original zipped bag.
Oh yes. Digital for utility. Film for fun. The Trip 35 do not need a battery and if stored in the dark, the photocells round the lens do no degrade. They are a good little camera and have their own online fan clubs.Nice collection of cameras by the way - you still use film? I've got my Dad's Olympus here in a drawer, still in its original zipped bag.
So after some false starts, I finished the lower cover this evening.
Turned the inner spigot, drilled and reamed:
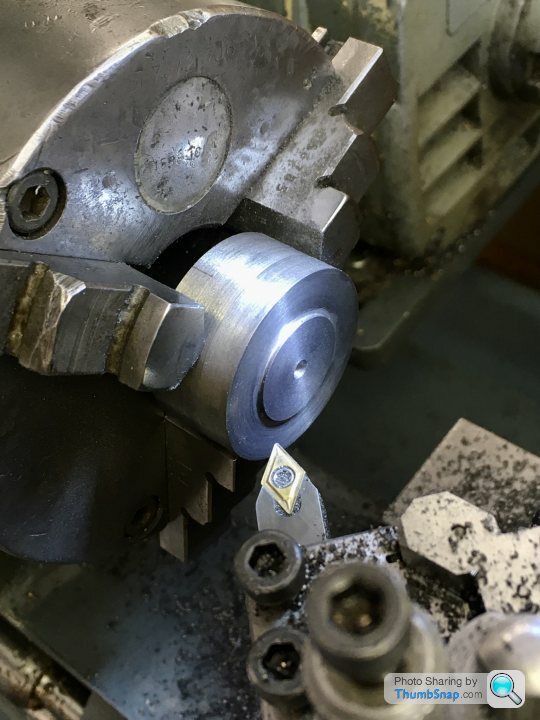
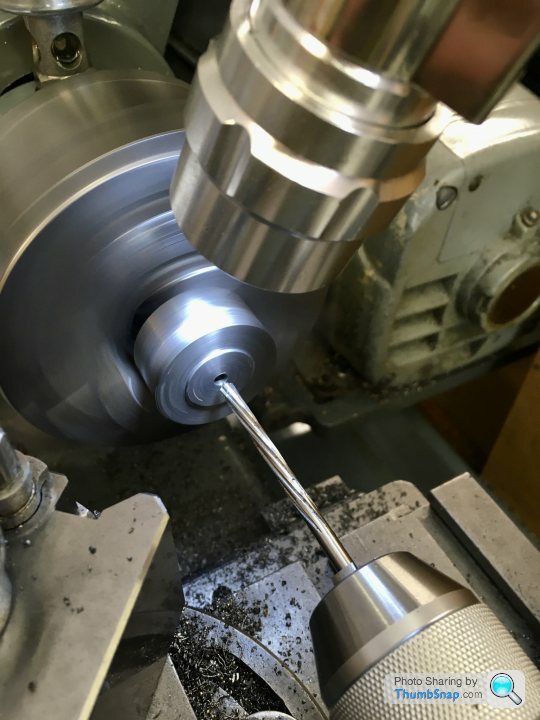
Close fit into the bore, all ok there:
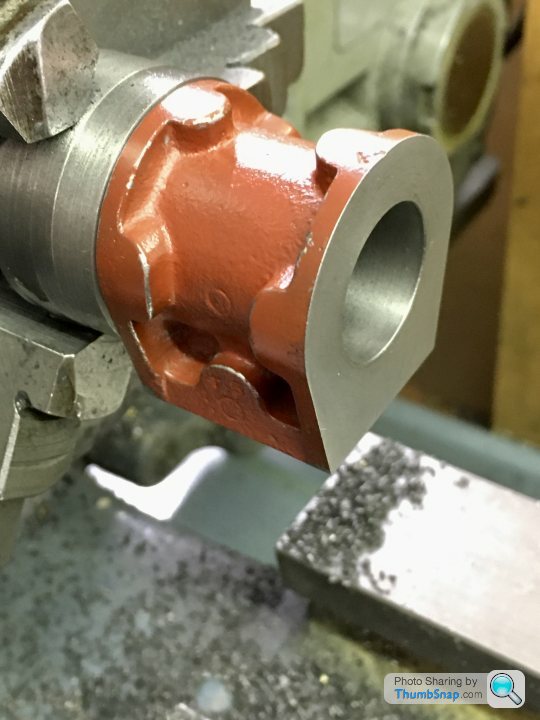
5/32” rod supplied was oversized, but I eventually got it to fit by some polishing in the chuck:
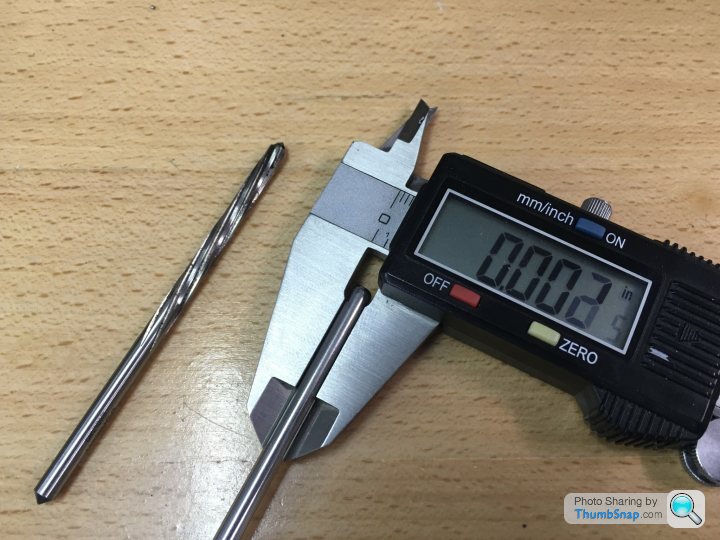
Then, after two failed attempts, made the split bush to hold the cover while machining the reverse side:
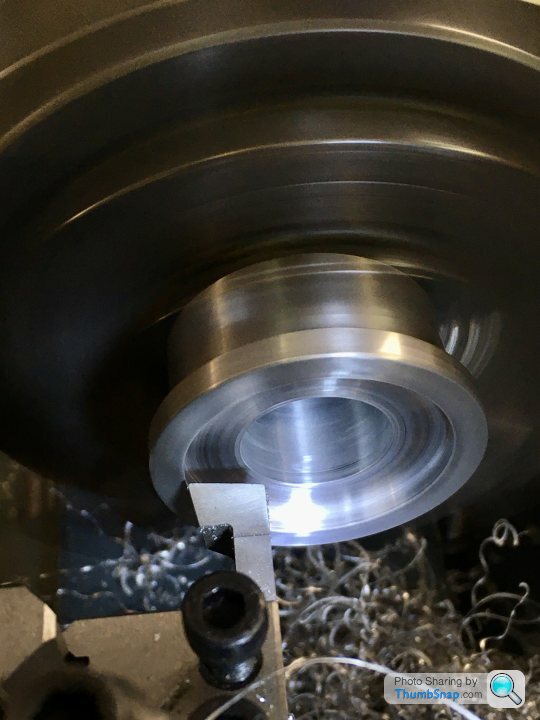
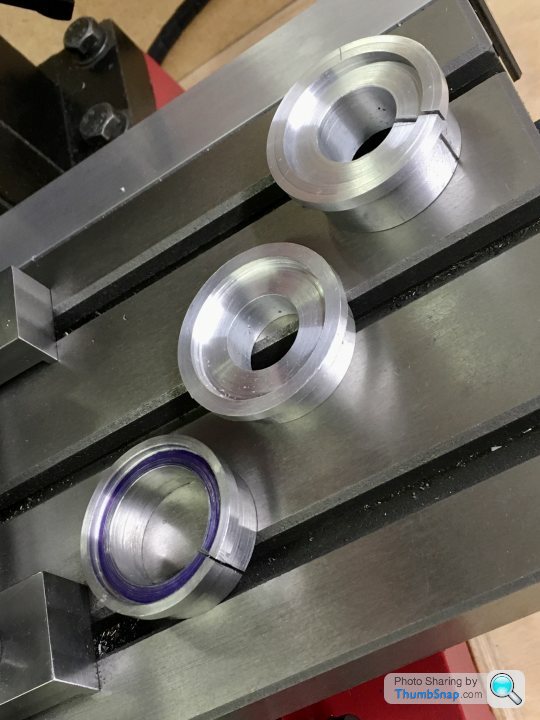
Matched to jaw #1, I checked runout of the coverWith a DTI. Virtually nothing this time, much less than 0.001”. I then pushed the rod into the hole and checked that:
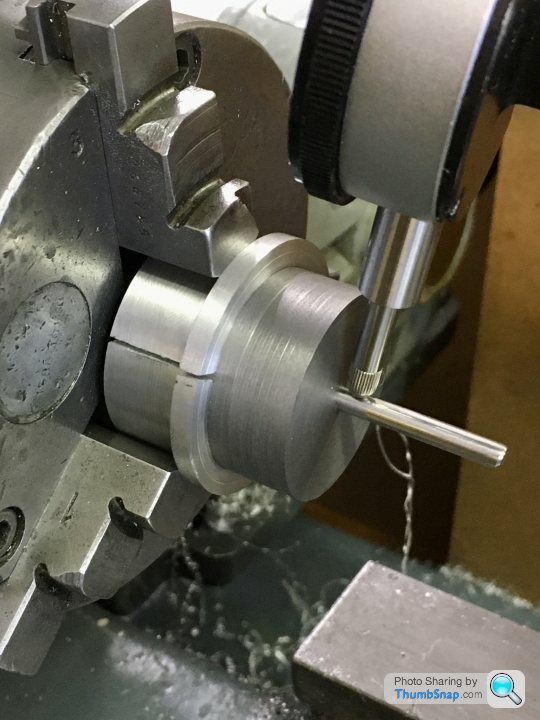
Quickly wished I hadn’t; 0.004” runout.
Anyway, I can’t keep re-doing this cover. It’s getting the better of me and I need to move on. It must have been the drill that wandered, despite me being very careful.
I made the recess the right depth for the cover, so it was a simple matter to turn down the boss:
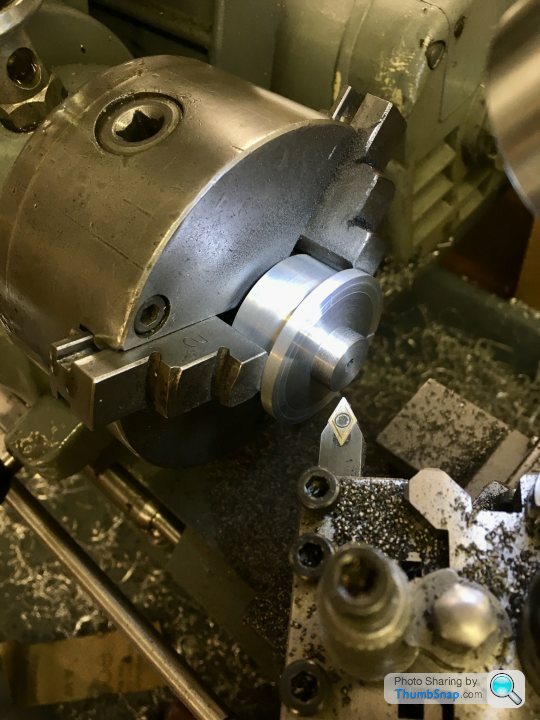
Close fit in the standard; ok:
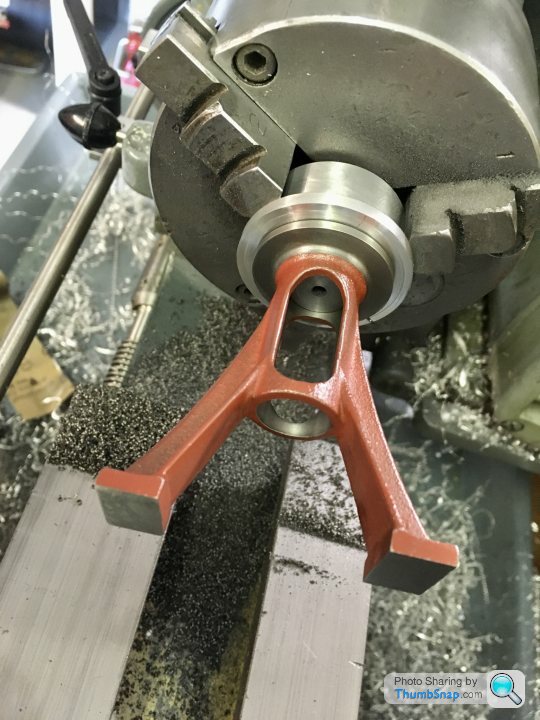
Drill & tap:
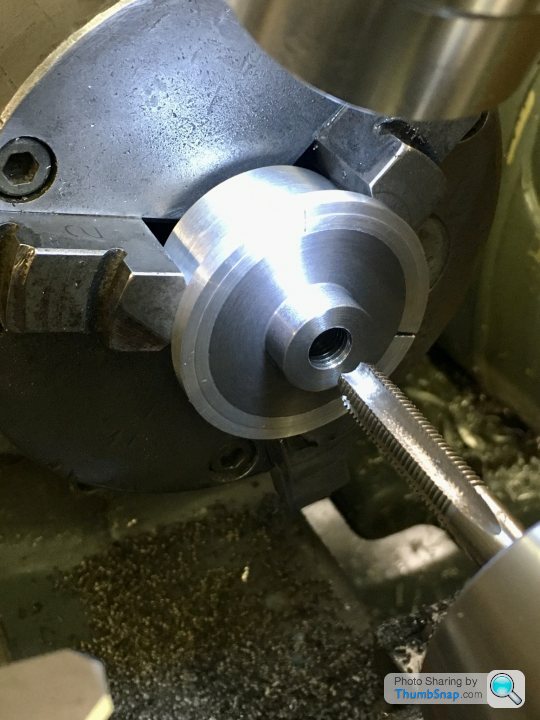
Finished:
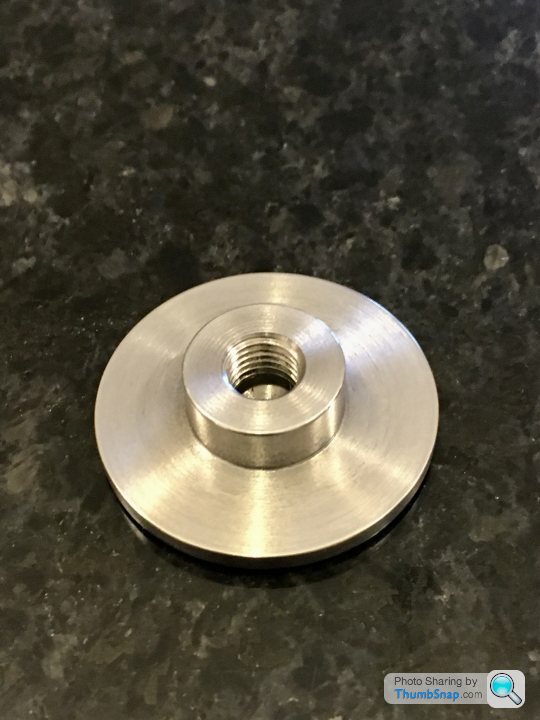
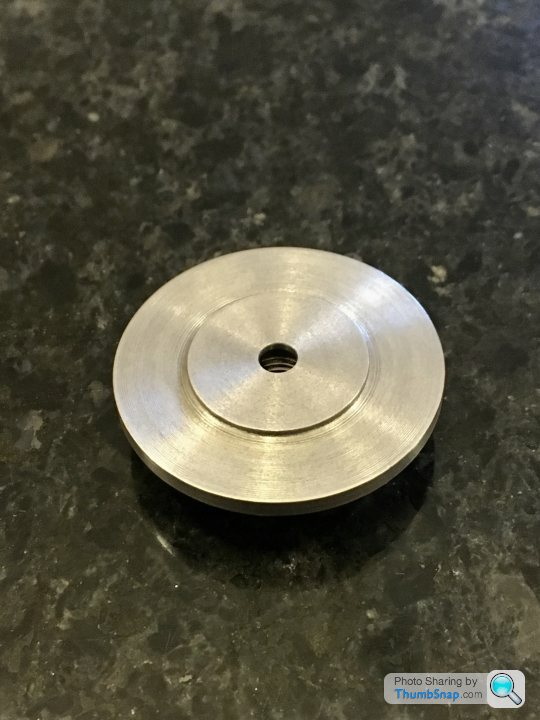

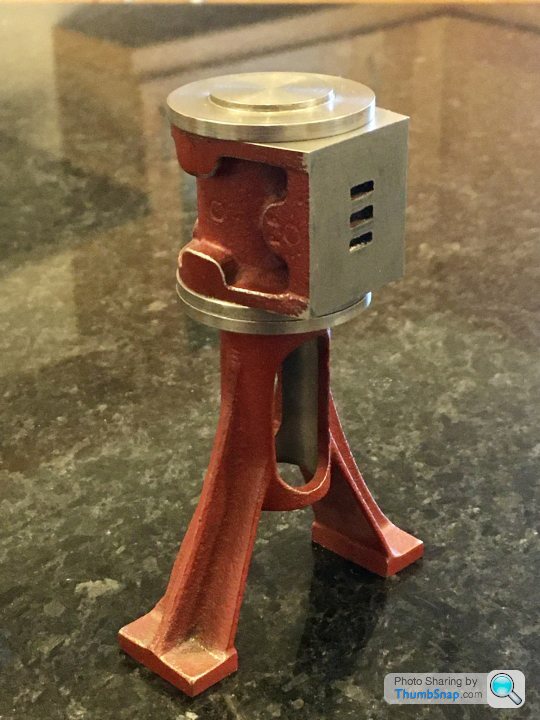
The standard diameter is a fraction more. I might turn it down to match - it should also reduce the depth of the edge flaw In the casting a bit.
The reamed hole is very shallow, significantly less than its diameter (as per the drawing). I’m wondering now if it was meant to be reamed at all. The drawing doesn’t say so, I just assumed it did. The packing nut also isn’t specified as a reamed hole. I think maybe they should be a close fit, but not to a ream tolerance. The combined length of the assembly, plus packing Would probably form a good enough sliding location. We will see how it assembles I guess.
Turned the inner spigot, drilled and reamed:
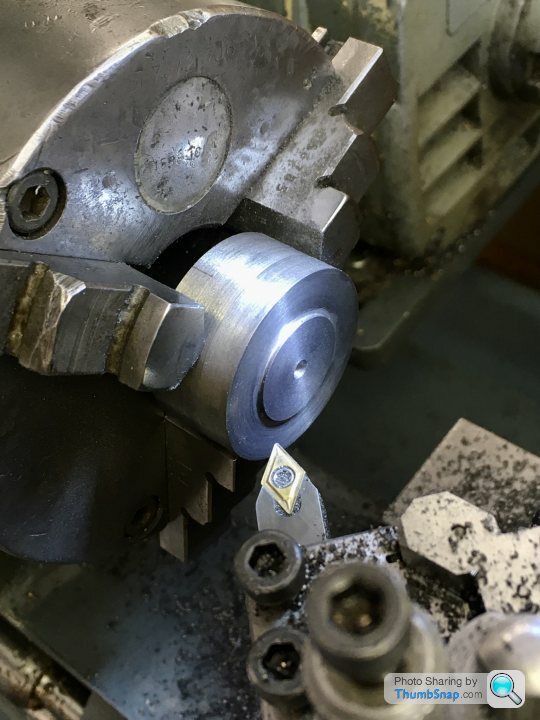
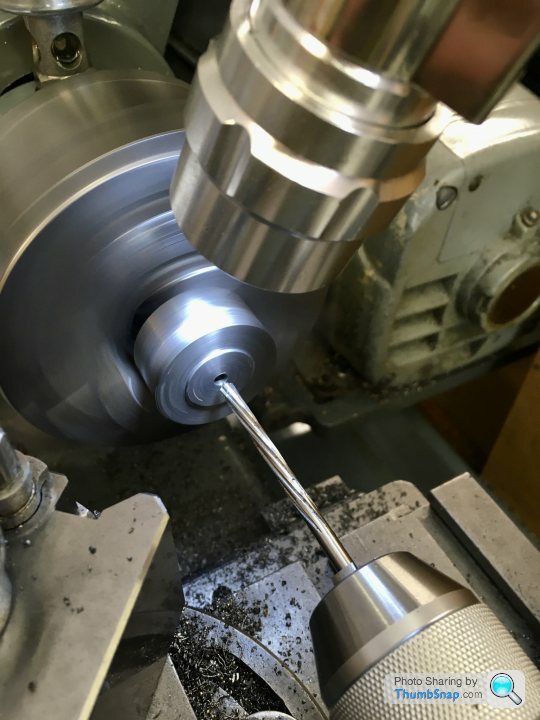
Close fit into the bore, all ok there:
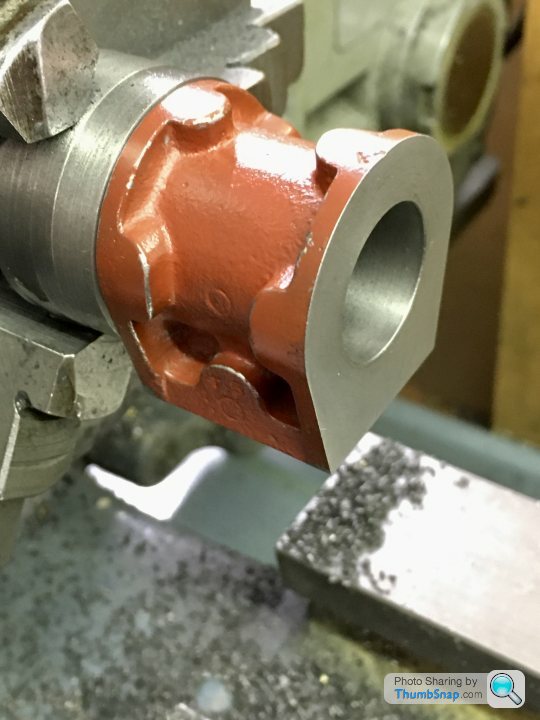
5/32” rod supplied was oversized, but I eventually got it to fit by some polishing in the chuck:
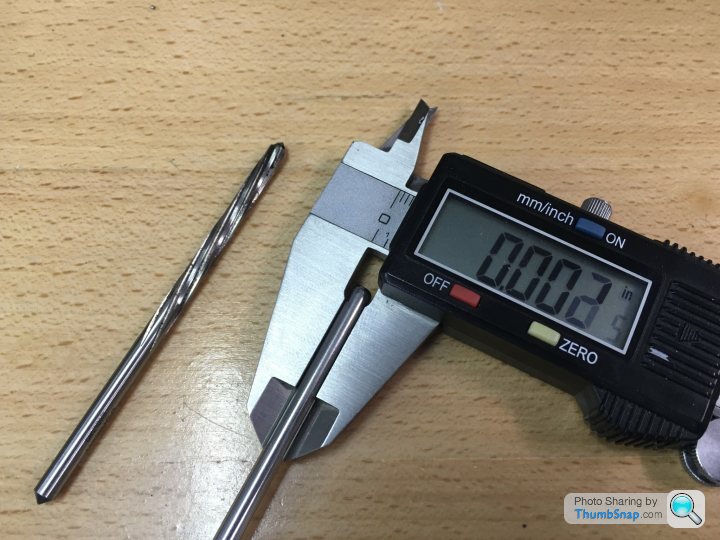
Then, after two failed attempts, made the split bush to hold the cover while machining the reverse side:
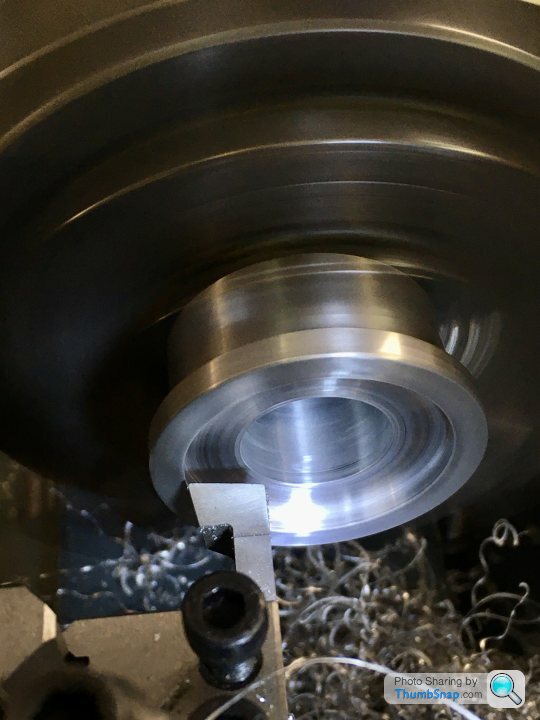
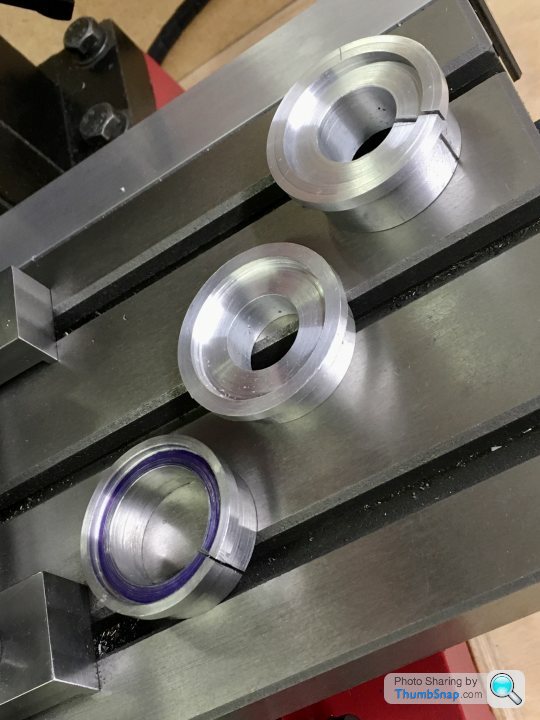
Matched to jaw #1, I checked runout of the coverWith a DTI. Virtually nothing this time, much less than 0.001”. I then pushed the rod into the hole and checked that:
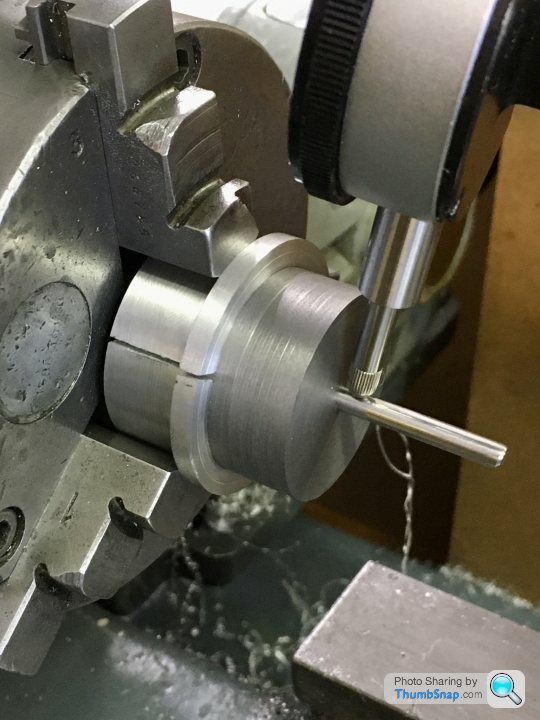
Quickly wished I hadn’t; 0.004” runout.
Anyway, I can’t keep re-doing this cover. It’s getting the better of me and I need to move on. It must have been the drill that wandered, despite me being very careful.
I made the recess the right depth for the cover, so it was a simple matter to turn down the boss:
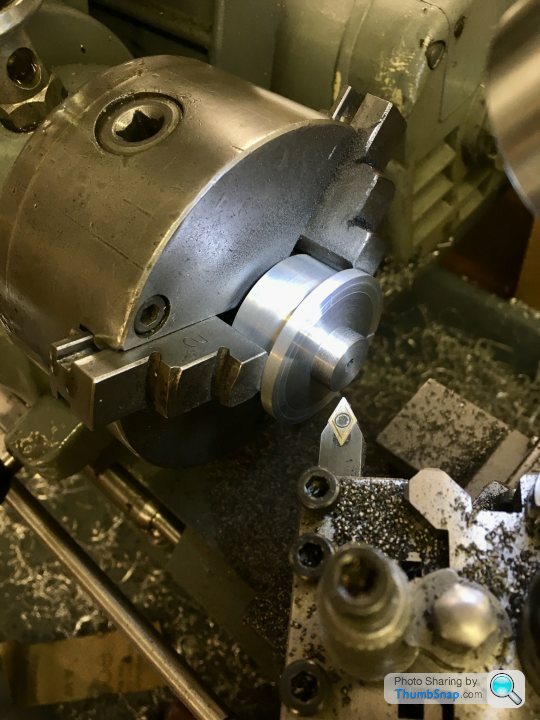
Close fit in the standard; ok:
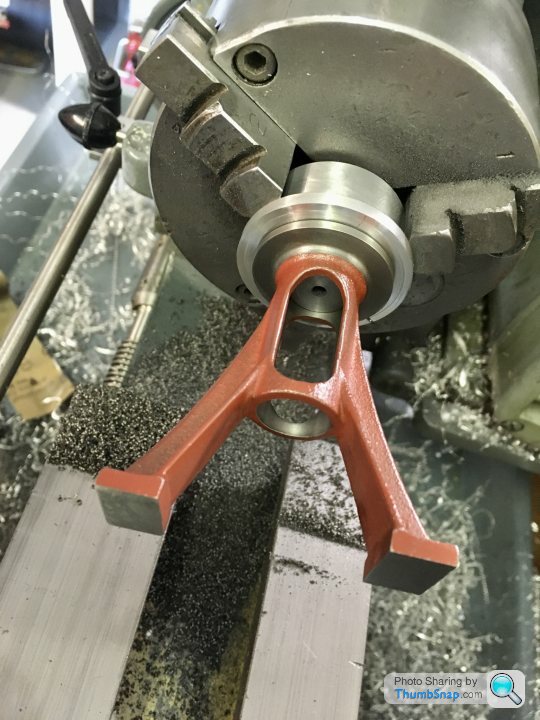
Drill & tap:
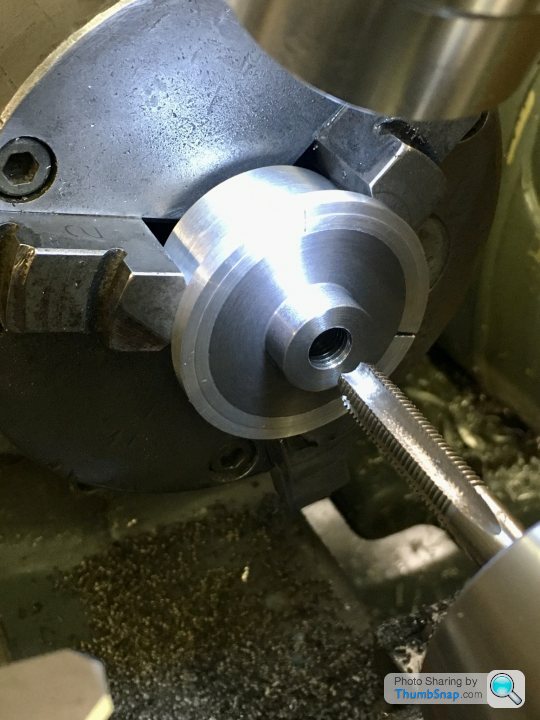
Finished:
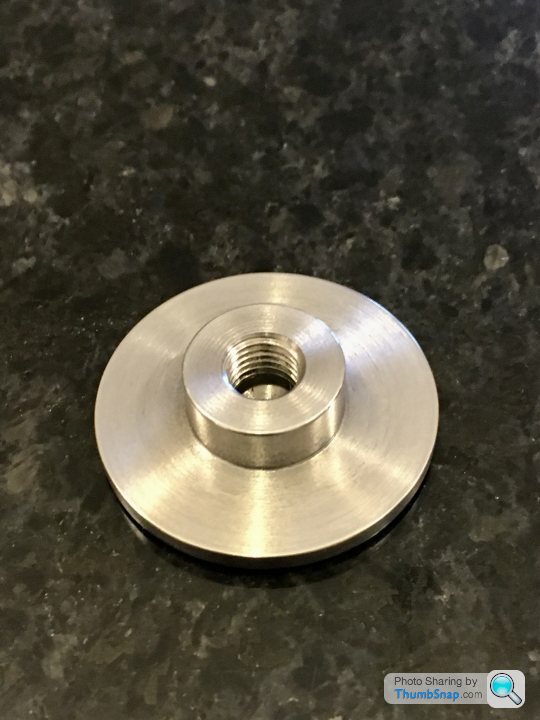
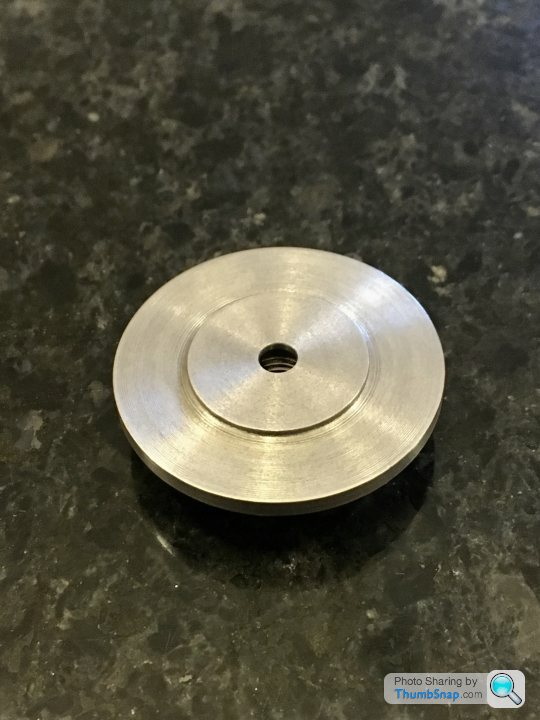

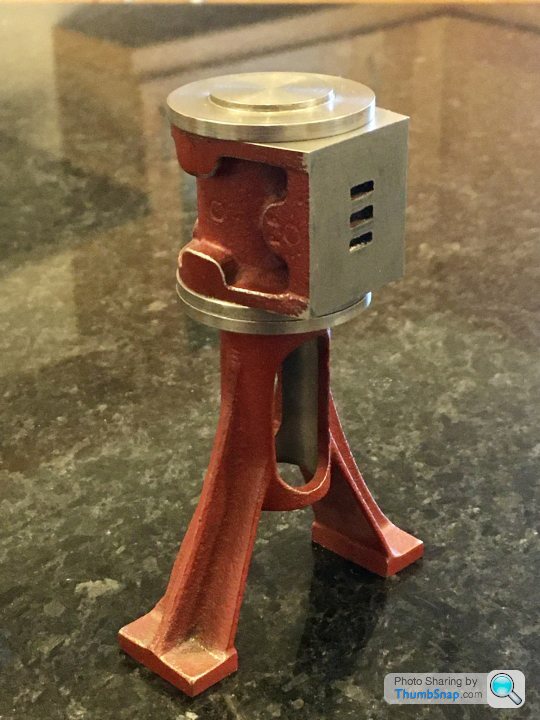
The standard diameter is a fraction more. I might turn it down to match - it should also reduce the depth of the edge flaw In the casting a bit.
The reamed hole is very shallow, significantly less than its diameter (as per the drawing). I’m wondering now if it was meant to be reamed at all. The drawing doesn’t say so, I just assumed it did. The packing nut also isn’t specified as a reamed hole. I think maybe they should be a close fit, but not to a ream tolerance. The combined length of the assembly, plus packing Would probably form a good enough sliding location. We will see how it assembles I guess.
I put the cover back in the fixture and put a finger gauge in what’s left on the reamed hole:
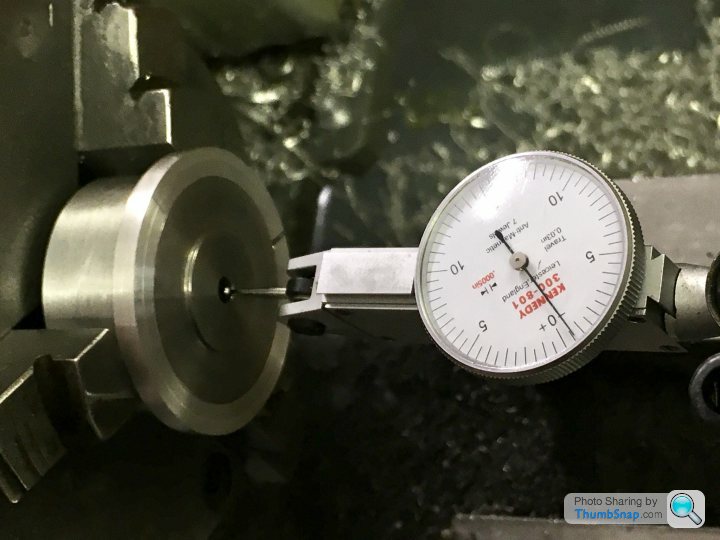
I’m getting a maximum reading of about 0.00075”. I suppose my previous reading could have been made worse by any clearance between the rod and hole, and error in the rod itself. Plus I guess a small inherent error with the split ring itself. Anyway, I don’t think I can get better than that.
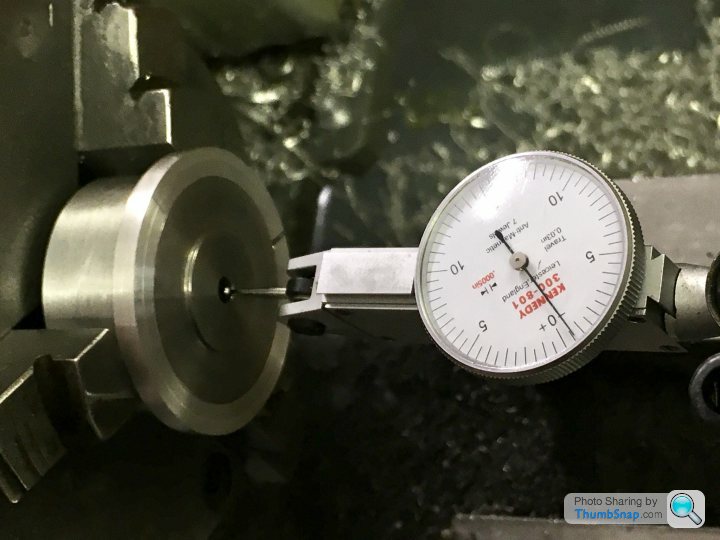
I’m getting a maximum reading of about 0.00075”. I suppose my previous reading could have been made worse by any clearance between the rod and hole, and error in the rod itself. Plus I guess a small inherent error with the split ring itself. Anyway, I don’t think I can get better than that.
Thanks both. Yes, it's all about experience; the drawings have the bare-bones dimensions, and it's up the builder to figure out what's important.
I mentioned over on the ME forum that I can't see why the cover hole is critical at all. The assembled piston, rod and crosshead take all axial and rotations normal to the axis' degrees of freedom out of the system when assembled in their bores, so adding a reamed hole in the middle just seems like an over constraint. I think it's just for the seal, which conforms to any runout anyway, and fills any slight fit errors.
Still, I must admit I'm glad that the runout is in fact less than 0.001" after all that. I was gutted when I saw 0.004" on the DTI.
It'll be interesting to see if it all slides freely without opening the cover hole up!
I mentioned over on the ME forum that I can't see why the cover hole is critical at all. The assembled piston, rod and crosshead take all axial and rotations normal to the axis' degrees of freedom out of the system when assembled in their bores, so adding a reamed hole in the middle just seems like an over constraint. I think it's just for the seal, which conforms to any runout anyway, and fills any slight fit errors.
Still, I must admit I'm glad that the runout is in fact less than 0.001" after all that. I was gutted when I saw 0.004" on the DTI.
It'll be interesting to see if it all slides freely without opening the cover hole up!
OK - the bore honing is for another day!
Today I co-ordinate drilled the covers, standard and cylinder block. Started by triple checking my calculations, then set the cylinder in the vice and finding the centre of the bore, which I set to be 0,0
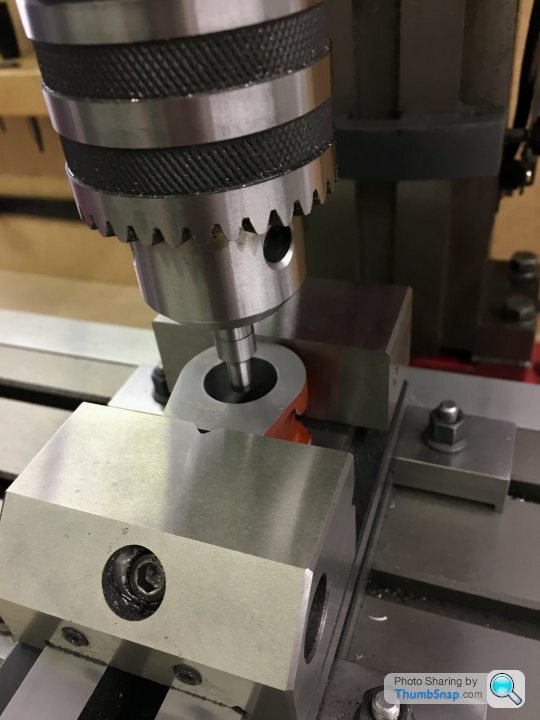
Dotted the co-ordinates as a sanity check:
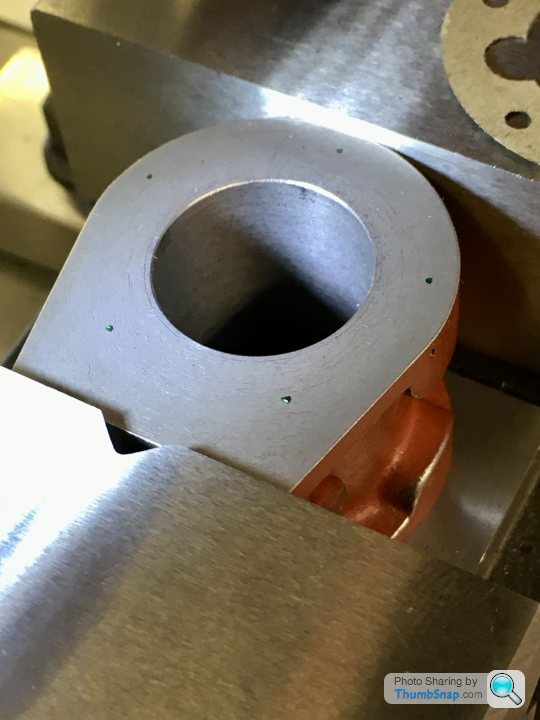
The gasket PCD was a bit small, but after checking yet again I could find nothing wrong with my calcs, so went ahead and drilled and tapped each of the 10 holes in turn:
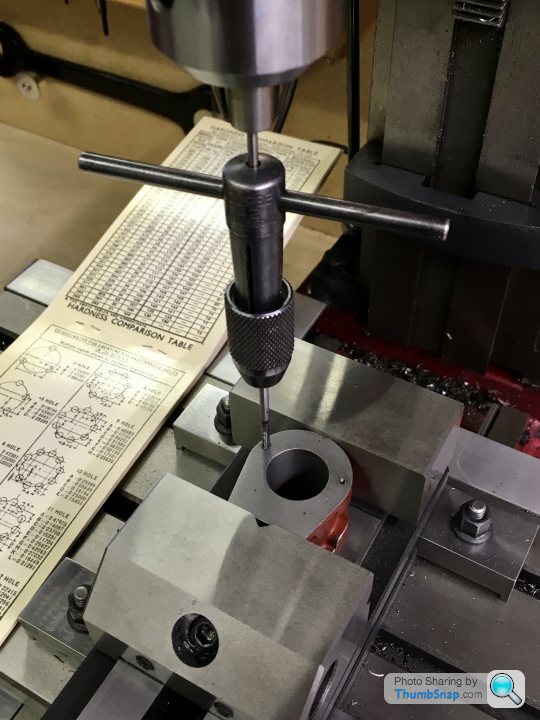
Then, on to the top cover. Used the inside of the vice jaws as the y-reference:
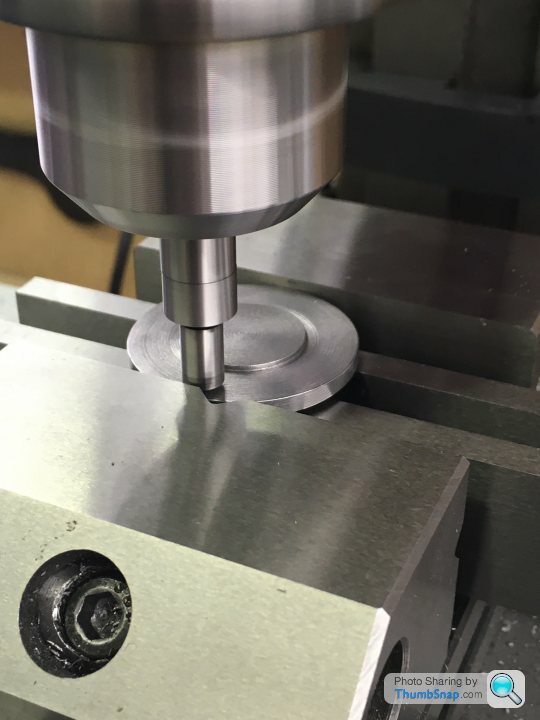
Clearance drilled:
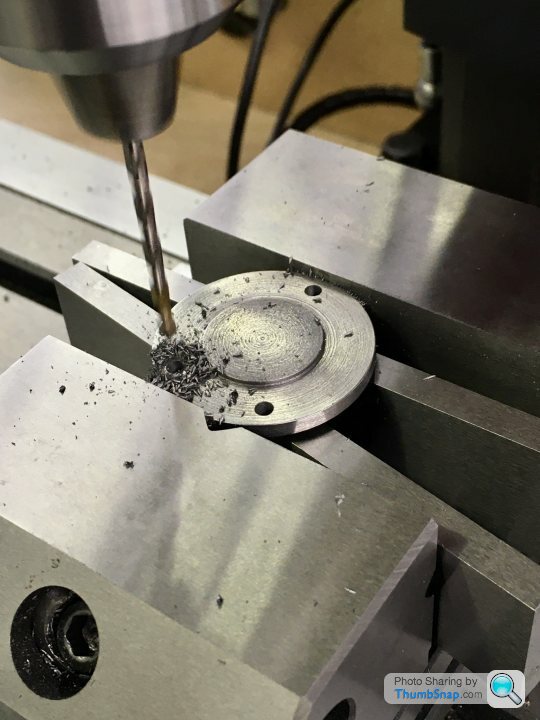
Same with the lower cover, but gripped by the lower boss:
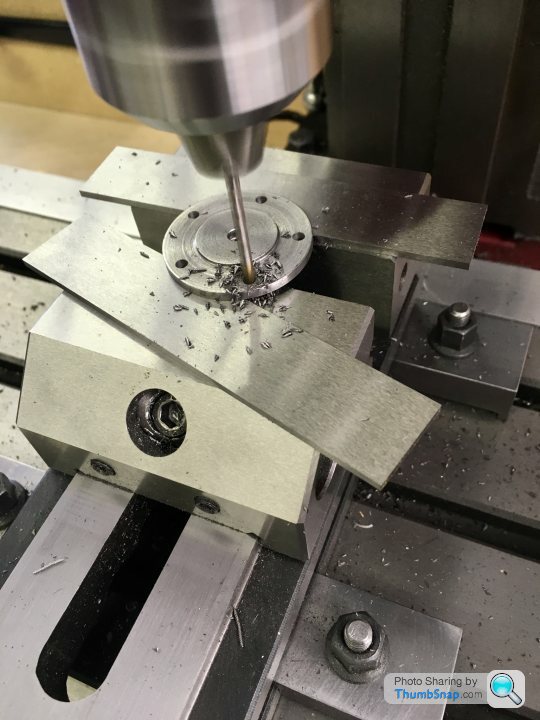
Then the standard - I put it in the vice using the feet edges as a reference for clocking the hole array:
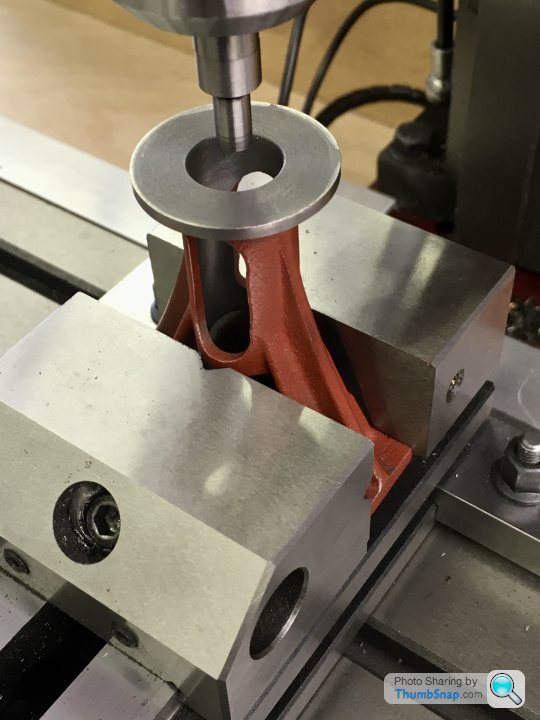
Clearance drilled :
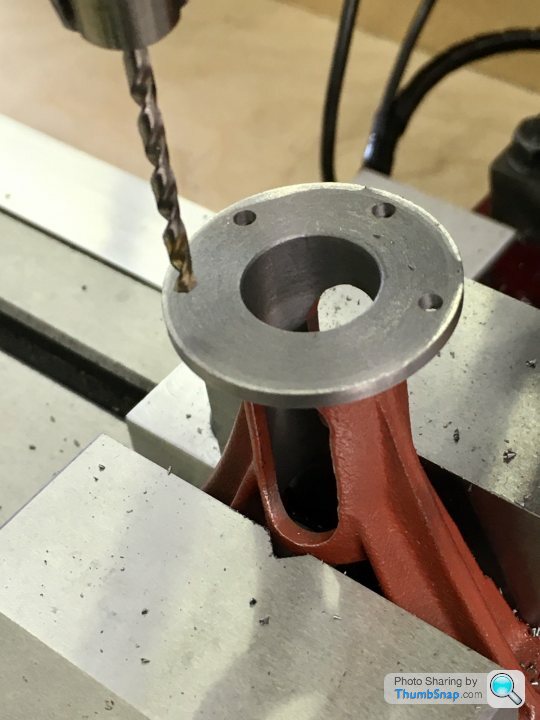
All de-burred:
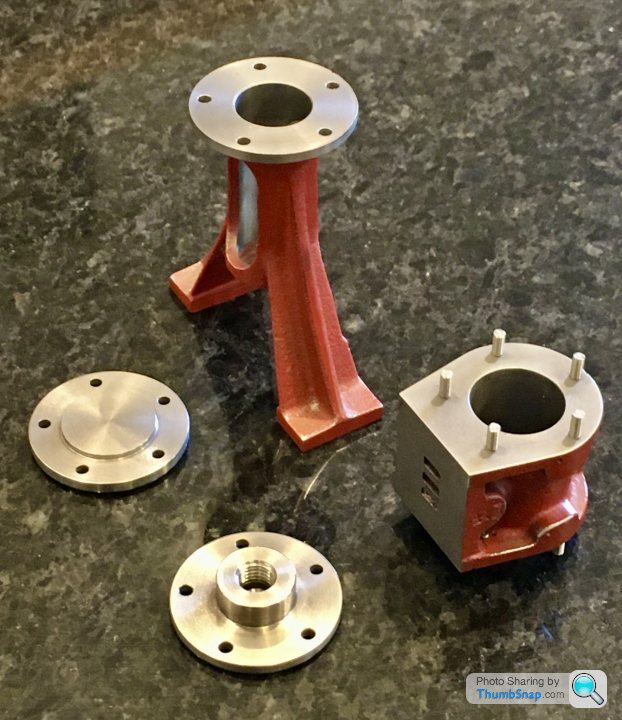
Studs test fitted, everything clicks into place, although the lower cover only fits in two orientations:
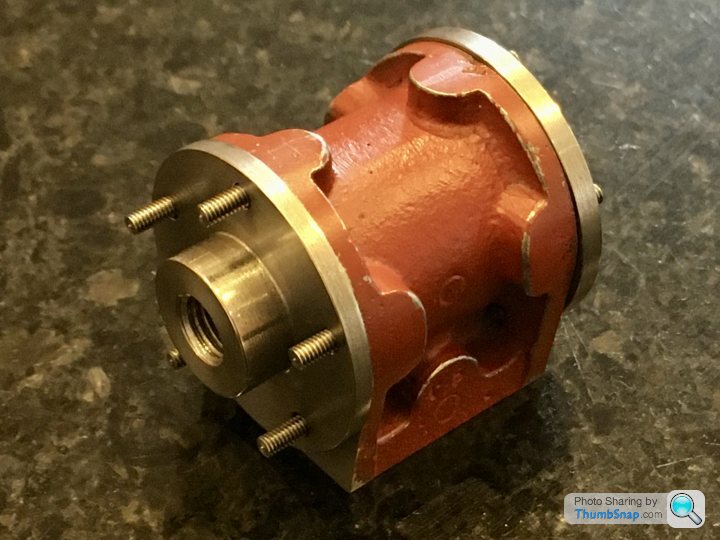
The gaskets have a bit of stretch, and do in fact fit ok:
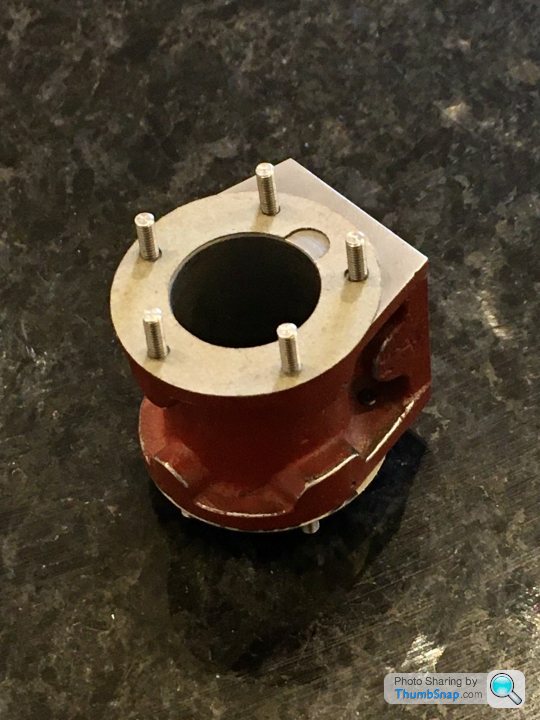
The lower nuts fit, but their corners *just* touch the machined radius unfortunately. I can correct it though:
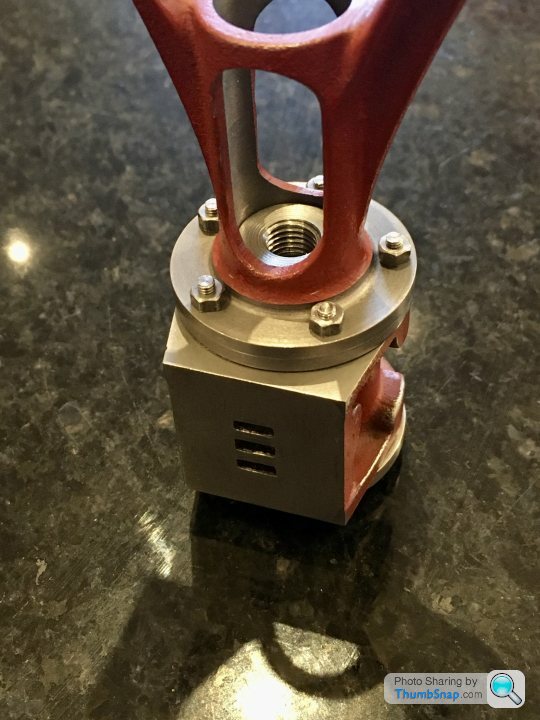
But all in all, happy with that.
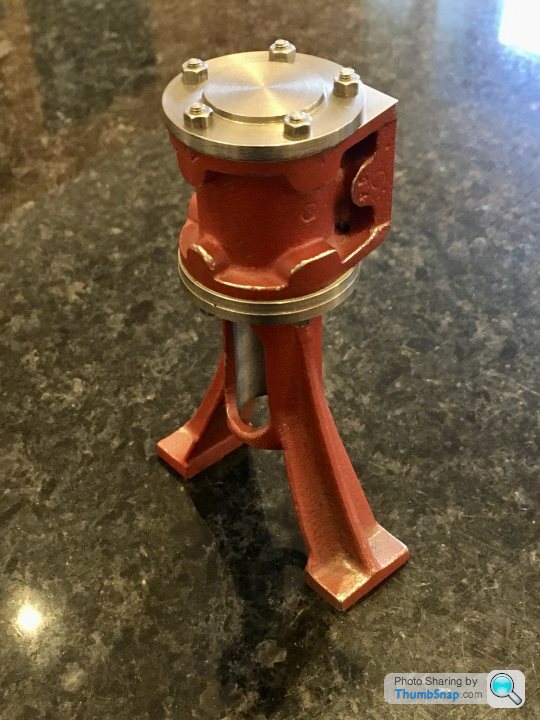
Today I co-ordinate drilled the covers, standard and cylinder block. Started by triple checking my calculations, then set the cylinder in the vice and finding the centre of the bore, which I set to be 0,0
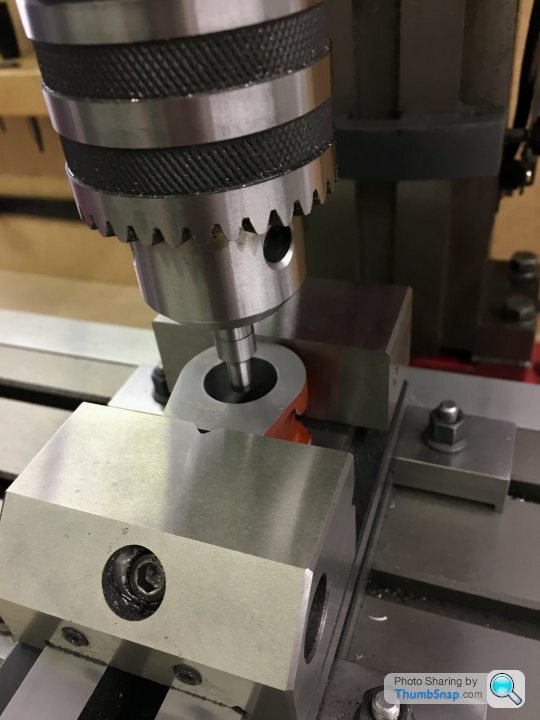
Dotted the co-ordinates as a sanity check:
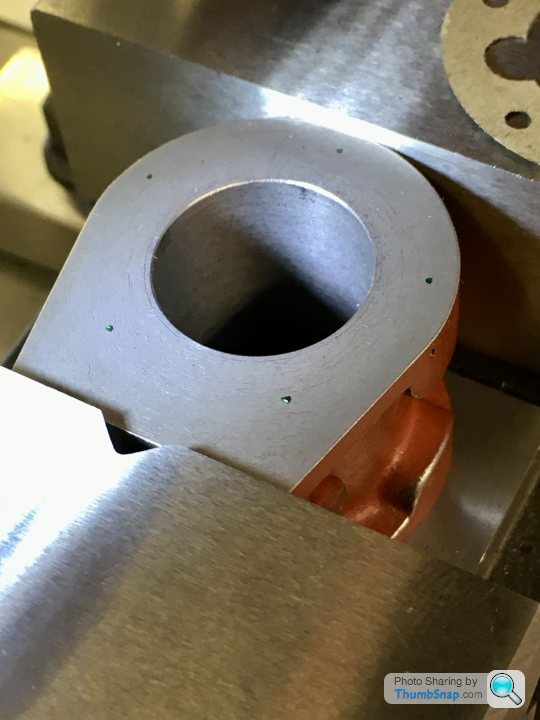
The gasket PCD was a bit small, but after checking yet again I could find nothing wrong with my calcs, so went ahead and drilled and tapped each of the 10 holes in turn:
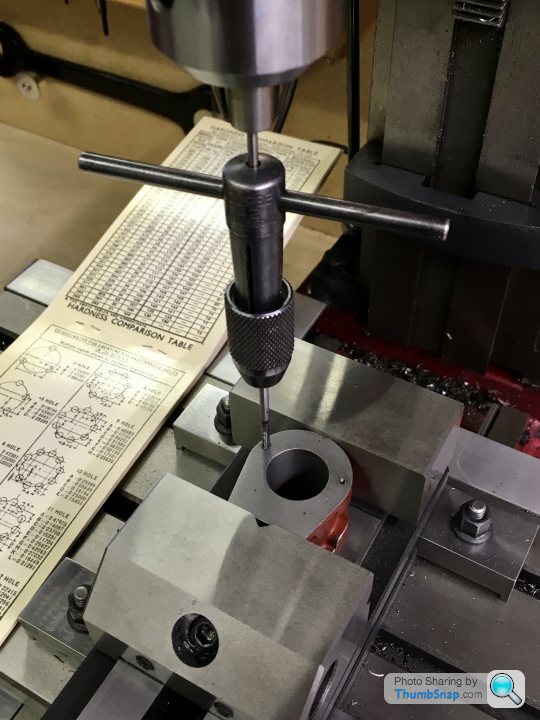
Then, on to the top cover. Used the inside of the vice jaws as the y-reference:
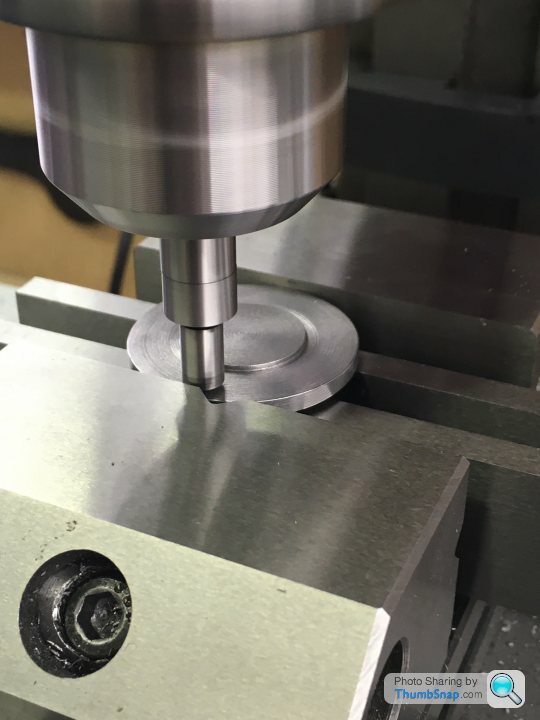
Clearance drilled:
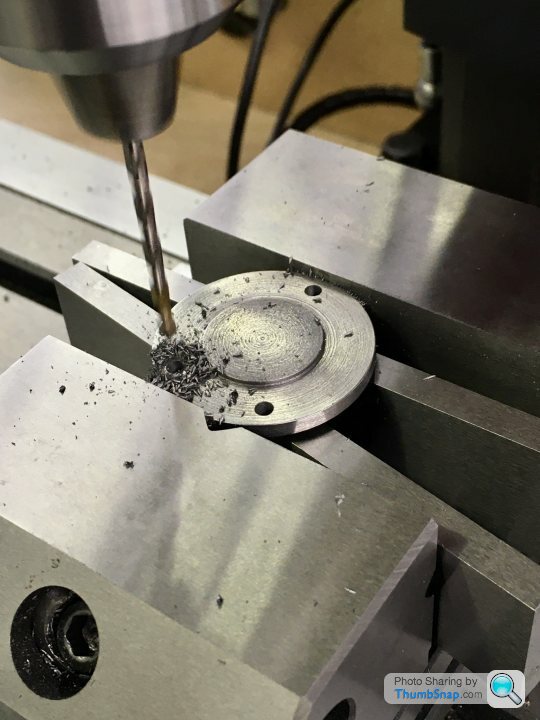
Same with the lower cover, but gripped by the lower boss:
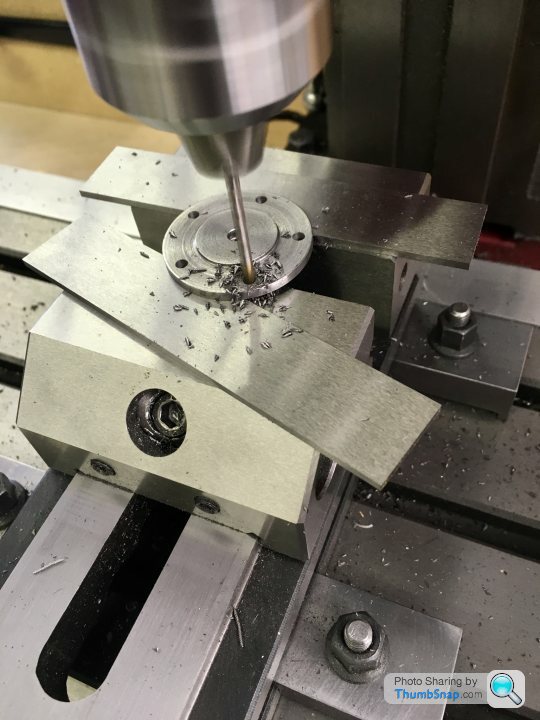
Then the standard - I put it in the vice using the feet edges as a reference for clocking the hole array:
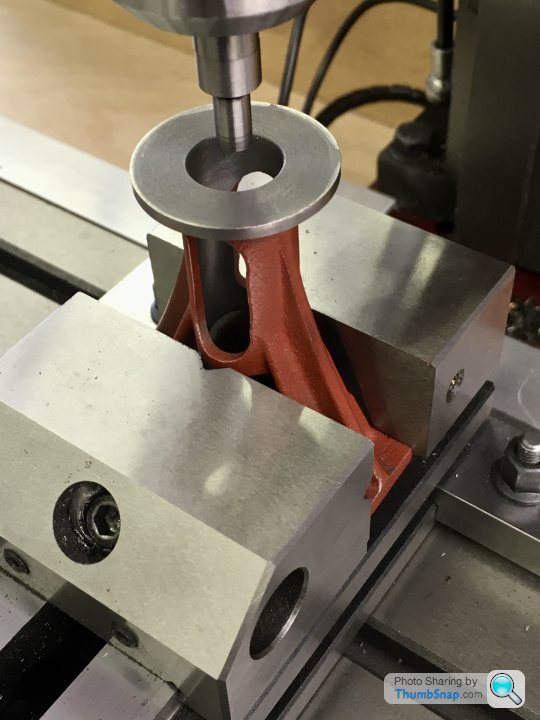
Clearance drilled :
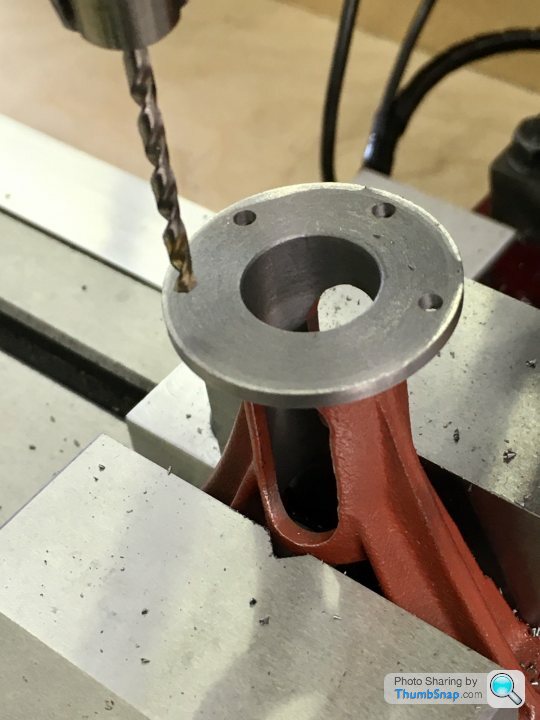
All de-burred:
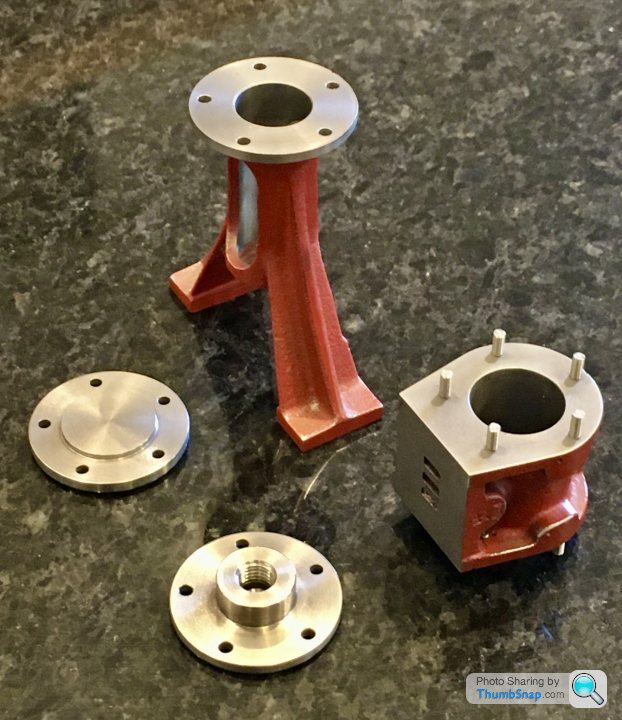
Studs test fitted, everything clicks into place, although the lower cover only fits in two orientations:
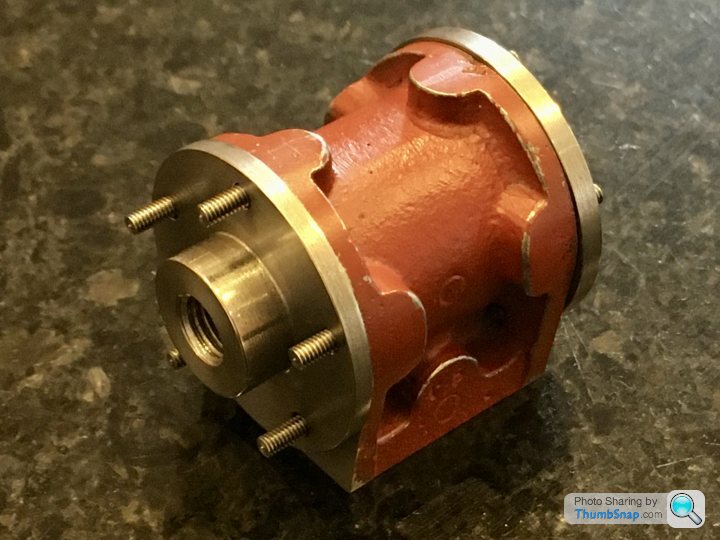
The gaskets have a bit of stretch, and do in fact fit ok:
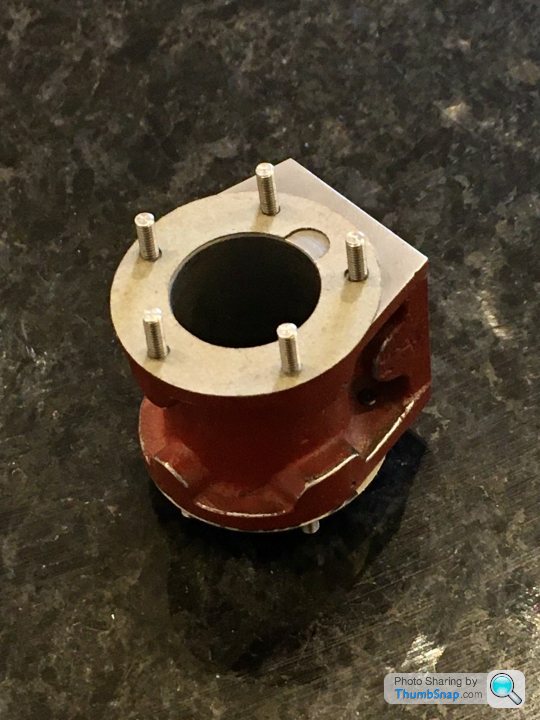
The lower nuts fit, but their corners *just* touch the machined radius unfortunately. I can correct it though:
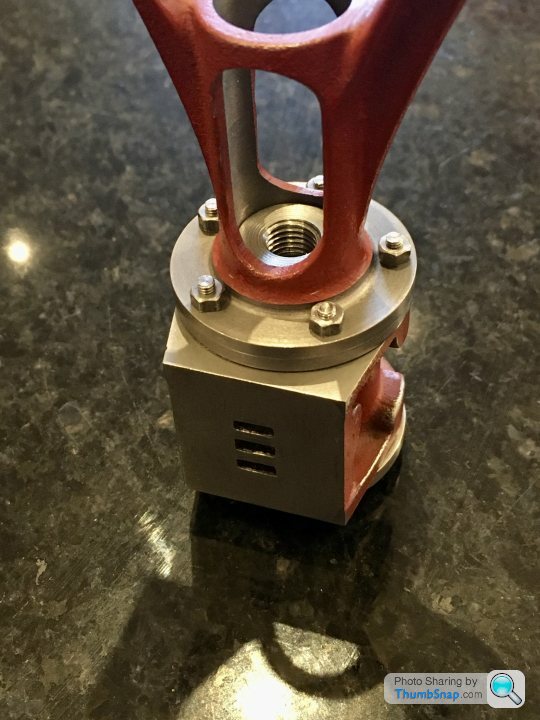
But all in all, happy with that.
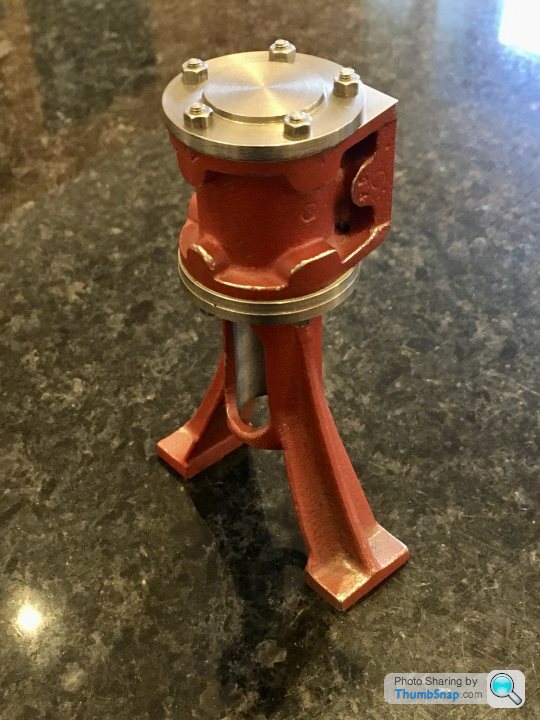
Thanks - yes I’ve come to regard those DROs as a basic human right. I can see why things aren’t consistent if they’ve been made on machines with hand wheels and backlash (like my lathe in fact). All the stuff that I’ve turned isn’t very consistent: I’ve got to re-visit the standard Upper diameter to get it to match the lower cover for example.
I think a lot of old machinery was the same in terms of assembly. In fact even today in aerospace applications things like replacement panels or bits of sub structure have to be fettled or drilled to suit other parts before they’ll fit.
I think a lot of old machinery was the same in terms of assembly. In fact even today in aerospace applications things like replacement panels or bits of sub structure have to be fettled or drilled to suit other parts before they’ll fit.
So on to the valve chest fitting. Began by clamping the cylinder in the vice using some parallels to get the top face flat:
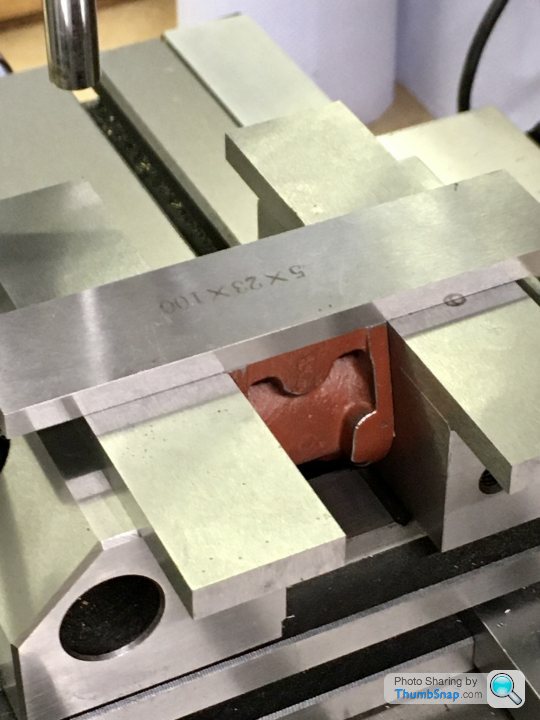
Checked for flatness:
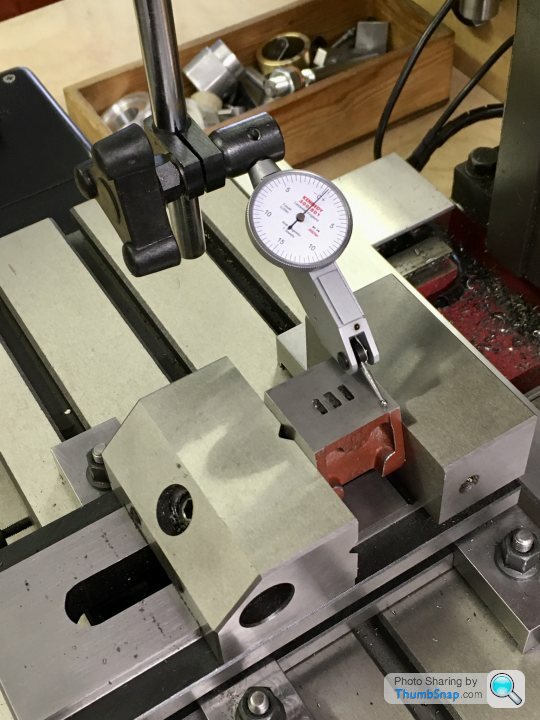
And got the centre using the edge finder:
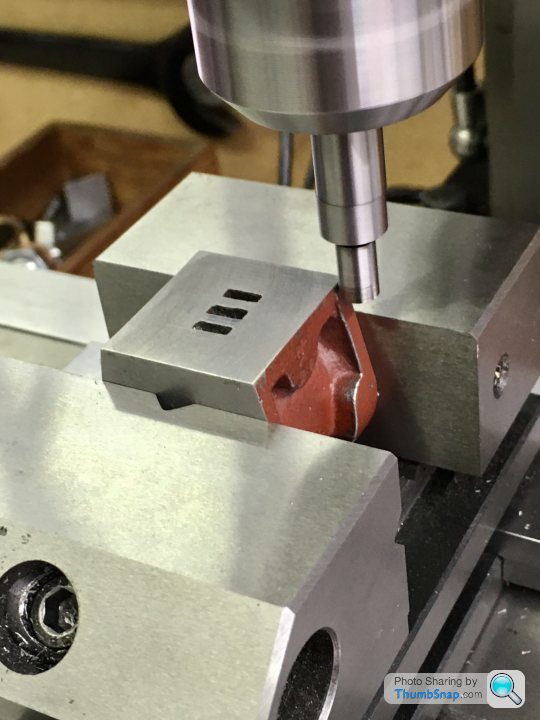
Then co-ordinate drilled and tapped in one setting using the DROs:
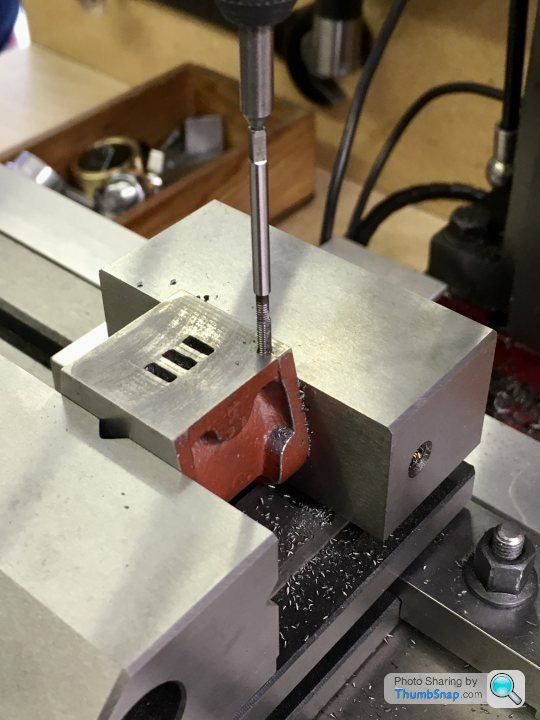
Same with the valve chest:
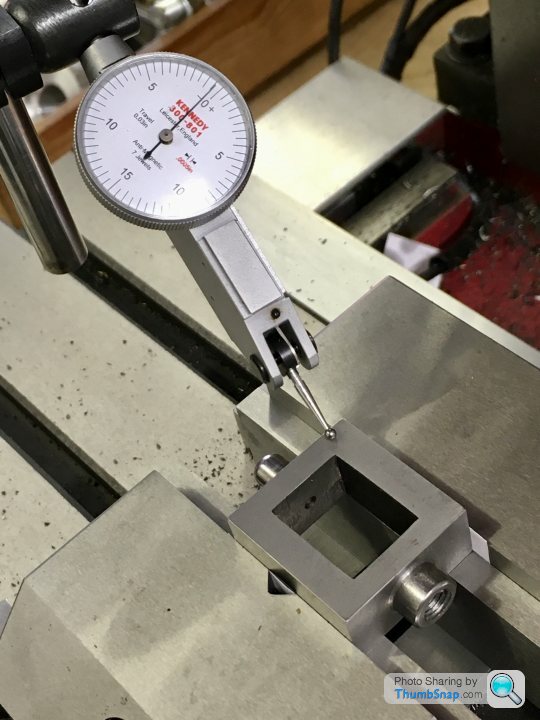
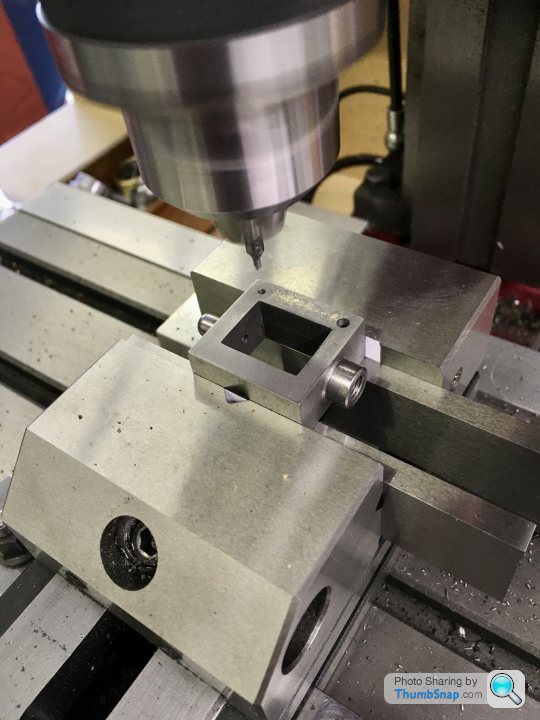
And the cover:
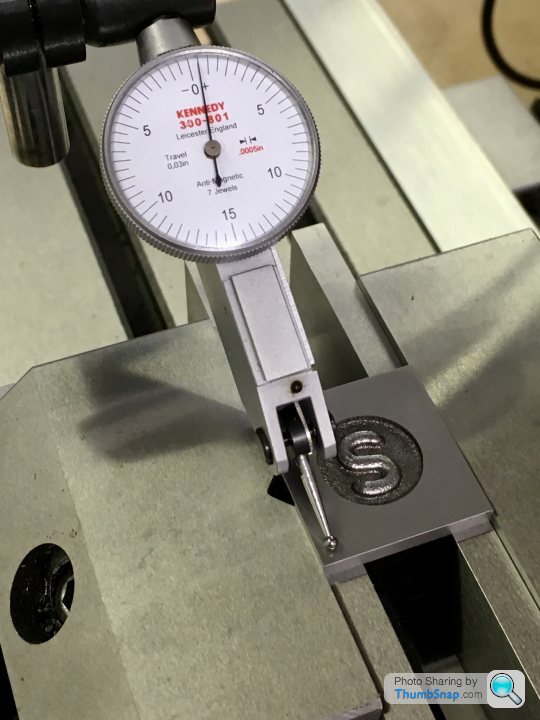
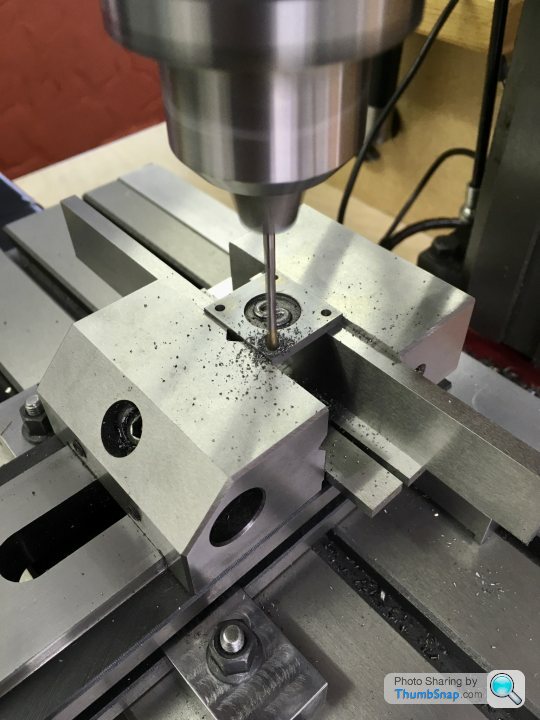
Fitted the studs temporarily:
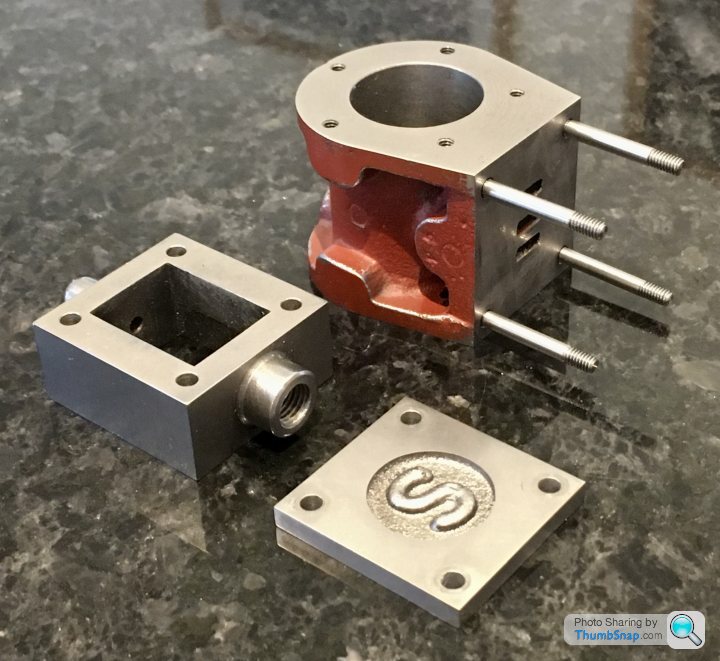
Gaskets fit, so must be about right:
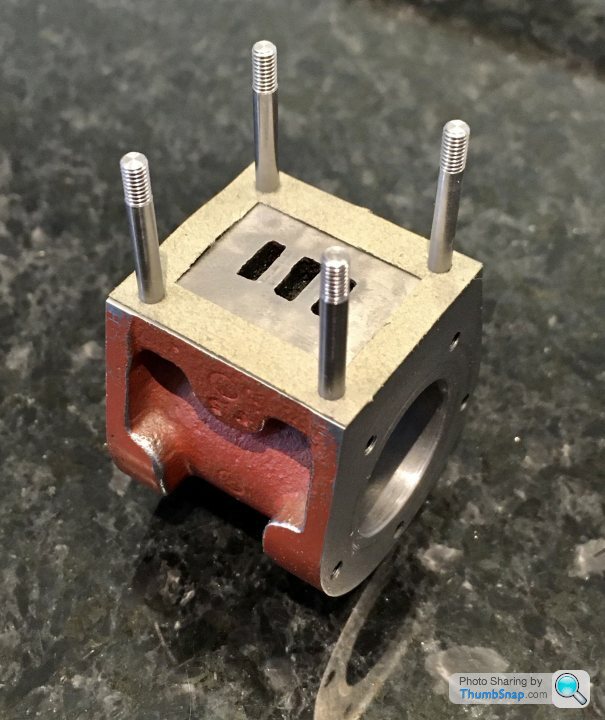
It all slides together nicely, and seems to be central:
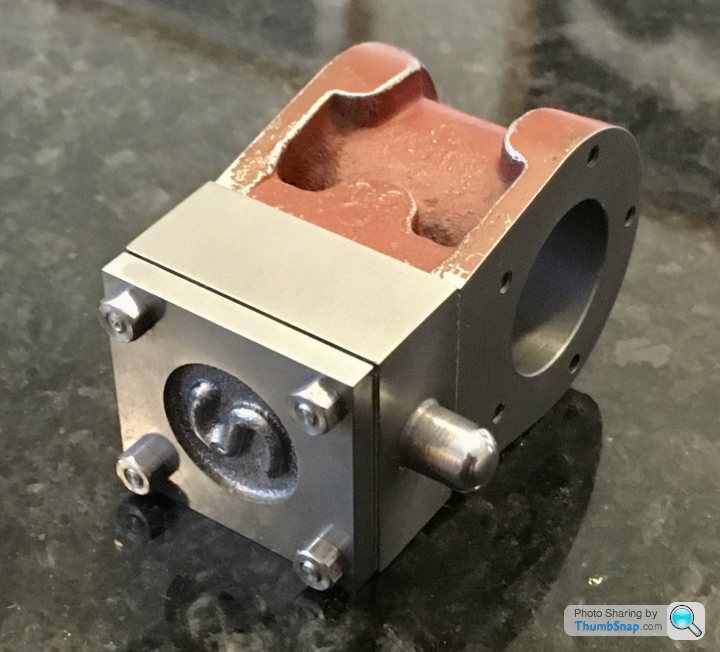
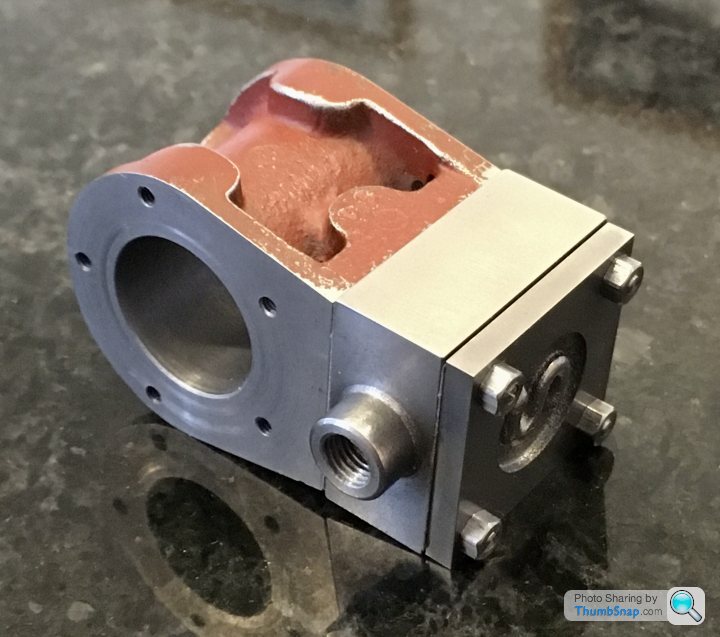
And the jacket is a flush fit too:
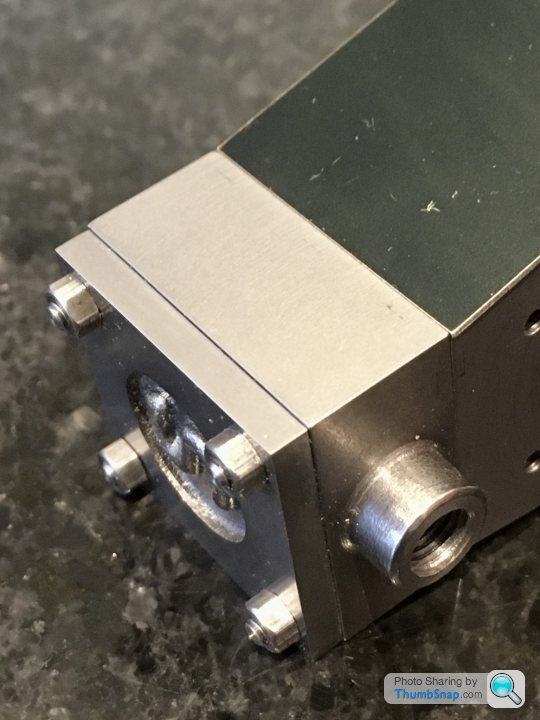
Next job will be fitting the main bearings and standard to the sole plate.
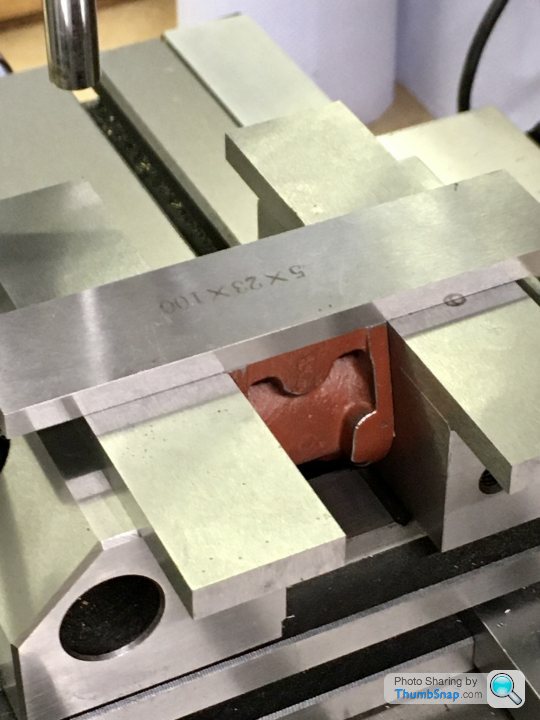
Checked for flatness:
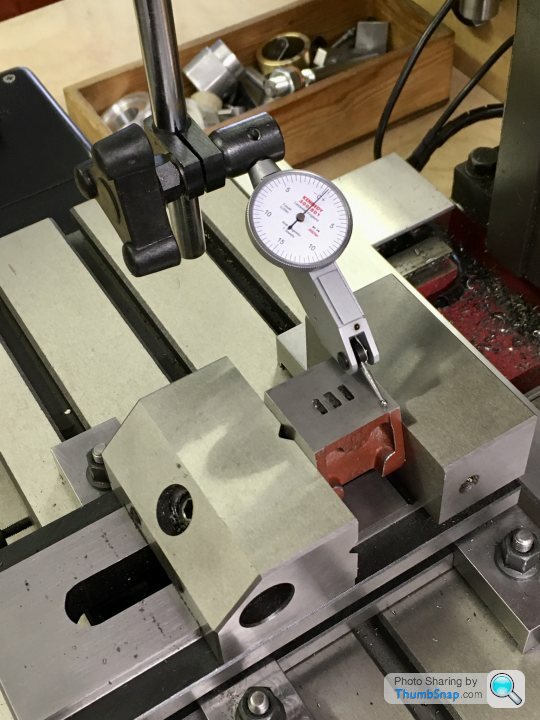
And got the centre using the edge finder:
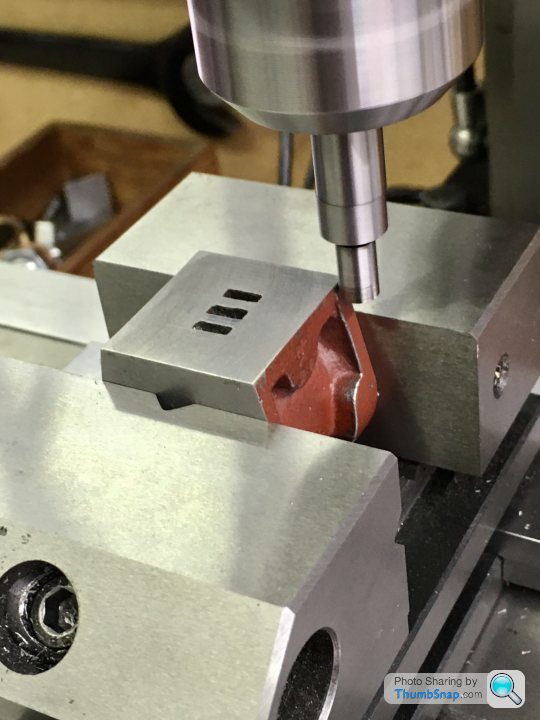
Then co-ordinate drilled and tapped in one setting using the DROs:
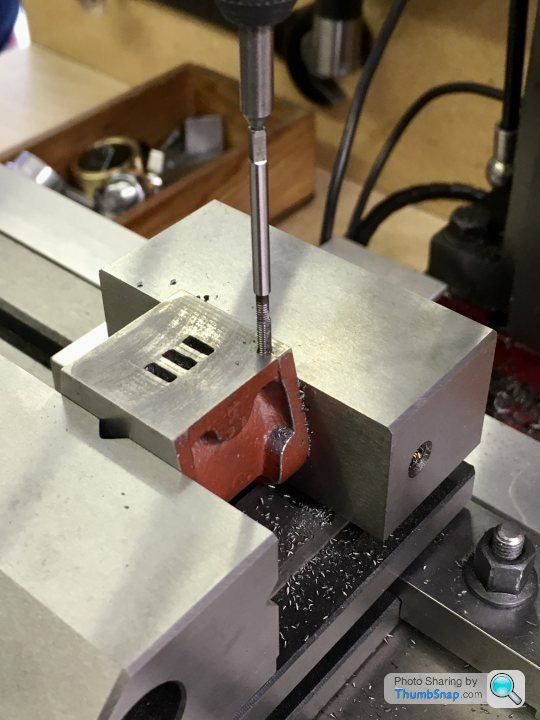
Same with the valve chest:
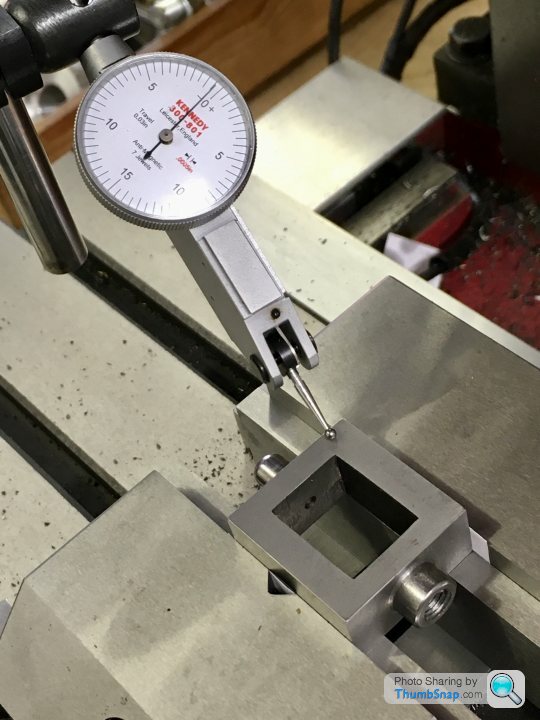
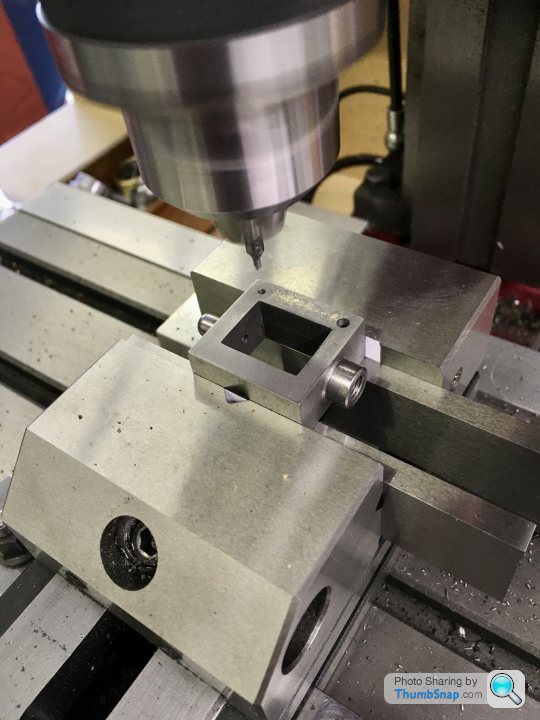
And the cover:
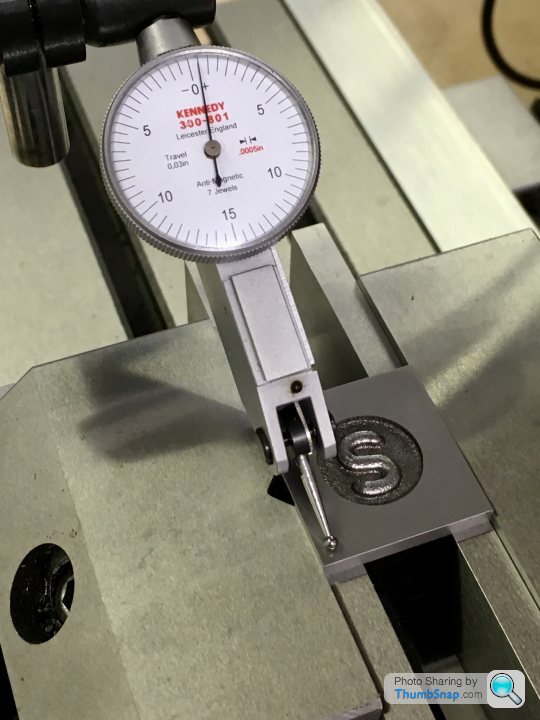
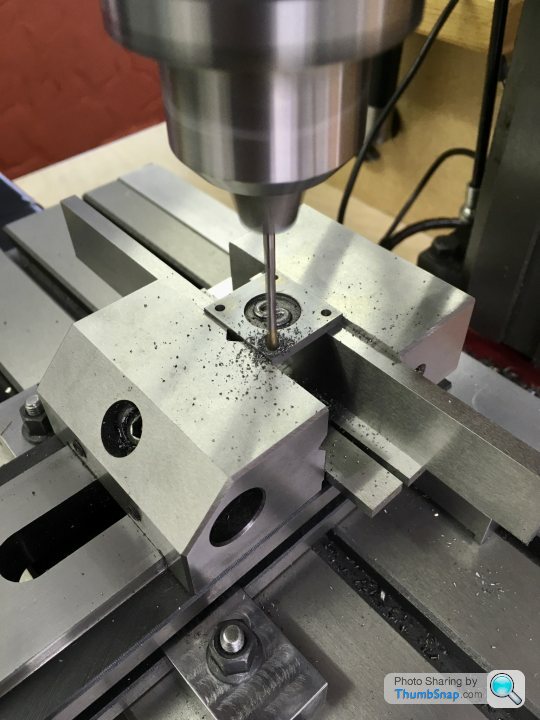
Fitted the studs temporarily:
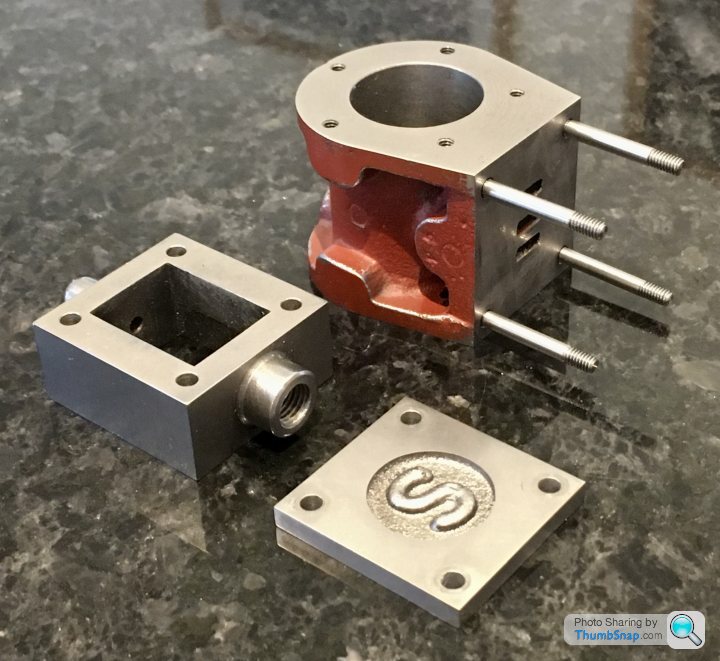
Gaskets fit, so must be about right:
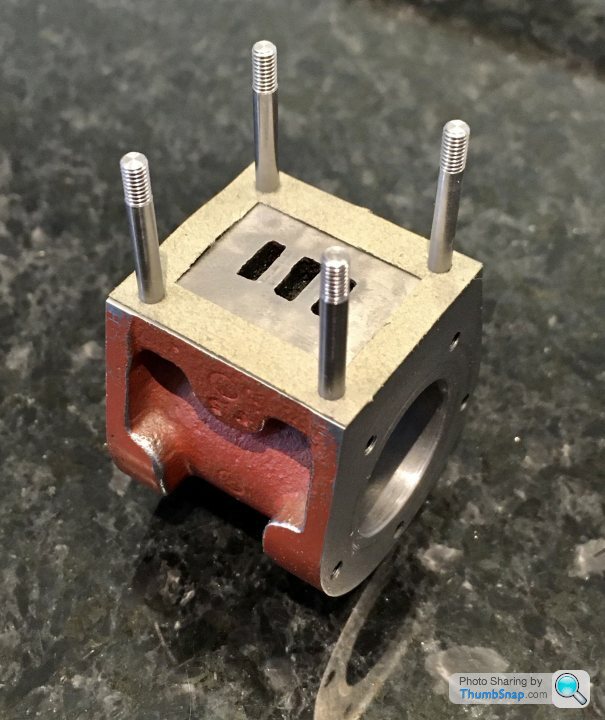
It all slides together nicely, and seems to be central:
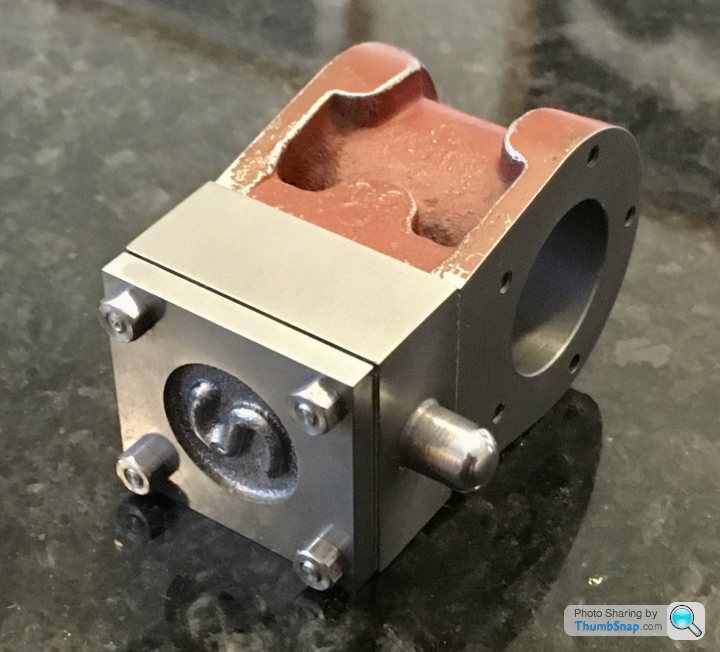
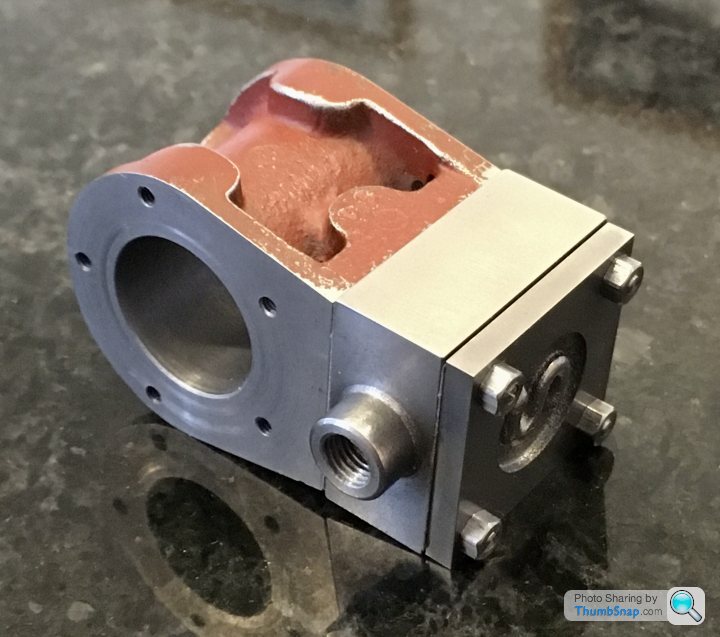
And the jacket is a flush fit too:
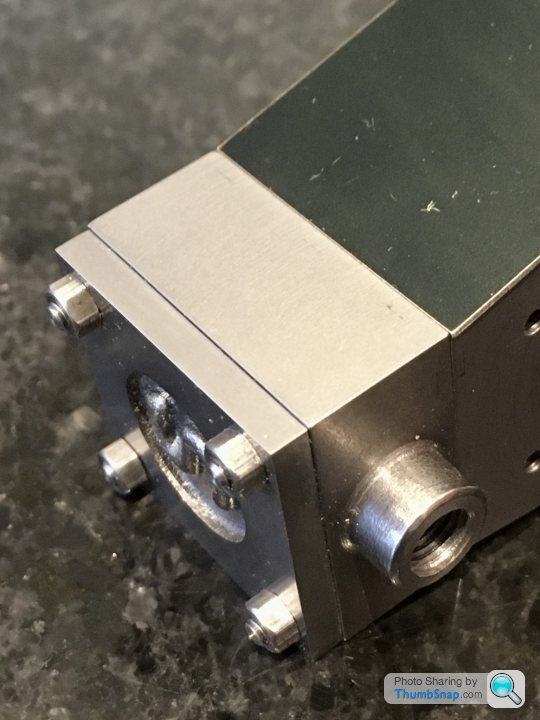
Next job will be fitting the main bearings and standard to the sole plate.
Got a bit sidetracked with this, but made another start, this time on the flywheel:
Expanded the 3-jaw Chuck to clamp the inside of the rim, and turned true:
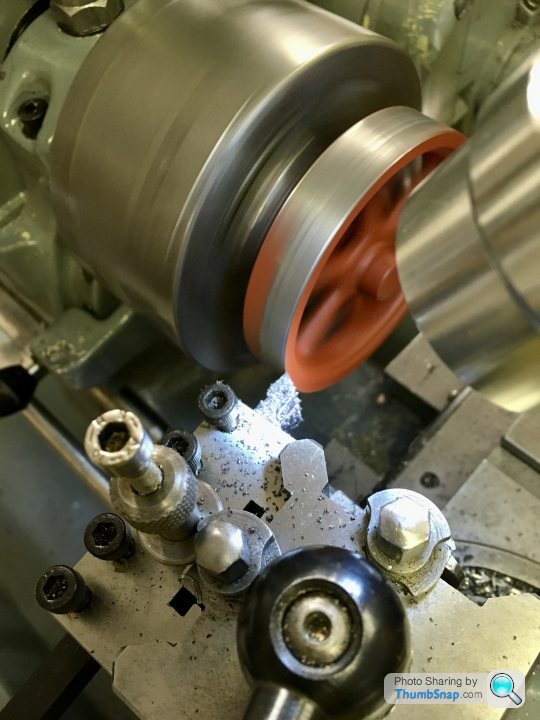
Drilled the bore:
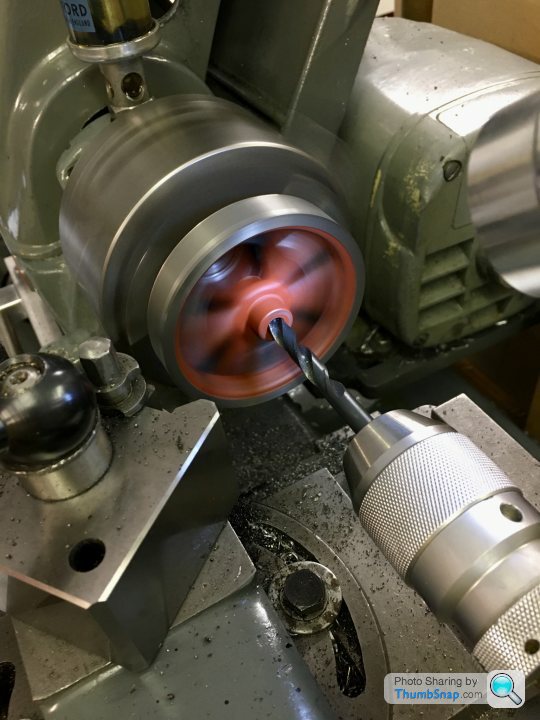
Reamed to suit the crankshaft:
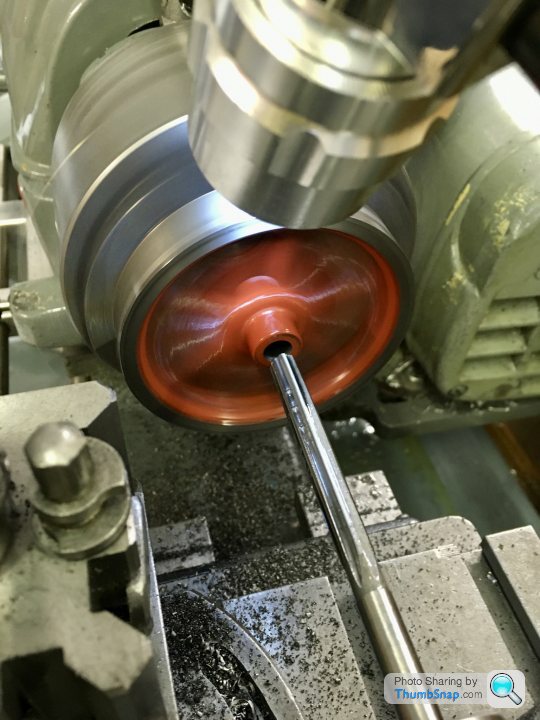
And machined the inside rim and boss, then reversed in the chuck and did the other side.
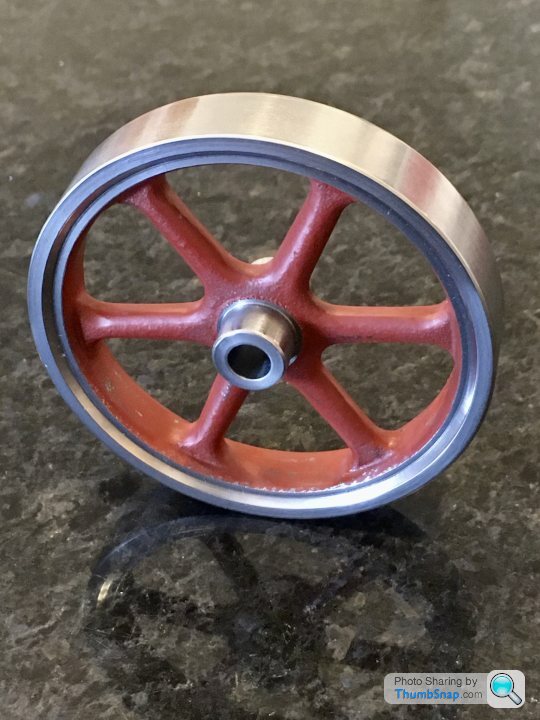
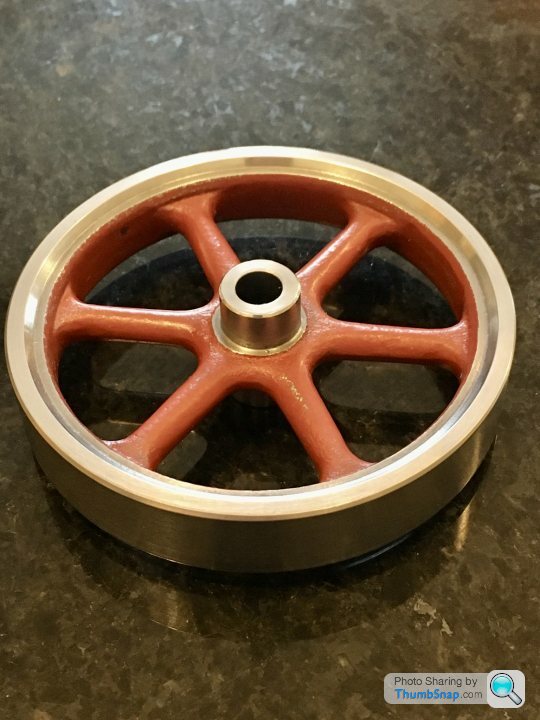
Fit on the shaft is fine, and the features turned on the initial setup are true, however the features on the reverse setup are noticeably off (when spun on the shaft). I might set it up again in the 4-jaw (on the o/d) and re-do the bits that are off.
Expanded the 3-jaw Chuck to clamp the inside of the rim, and turned true:
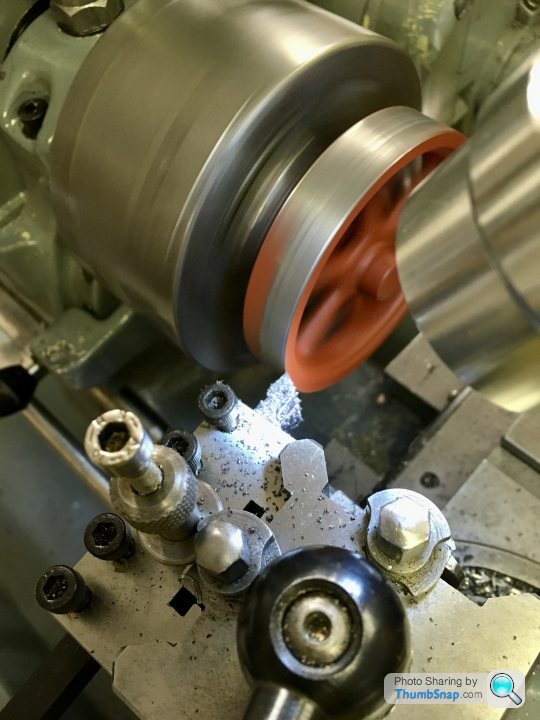
Drilled the bore:
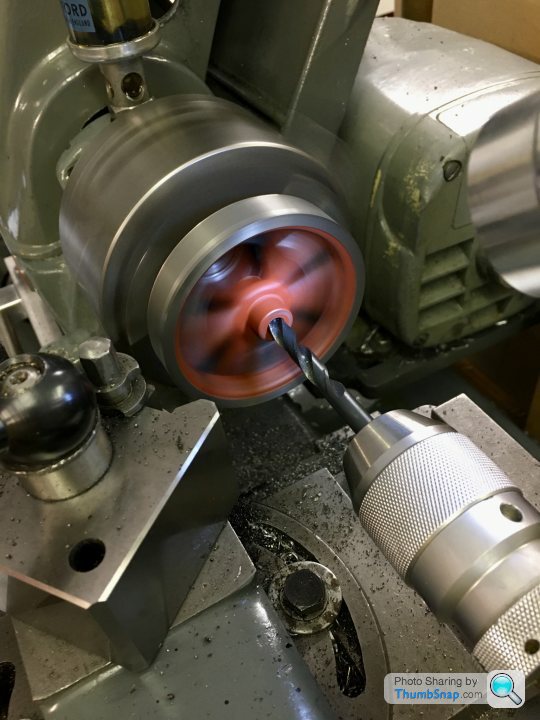
Reamed to suit the crankshaft:
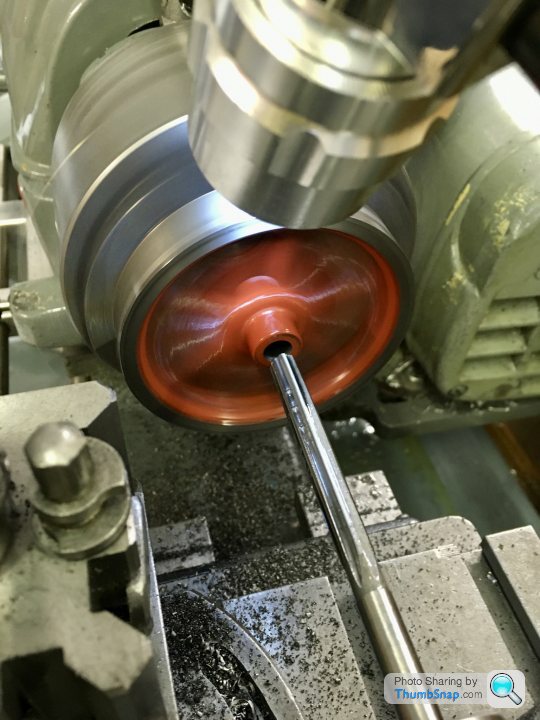
And machined the inside rim and boss, then reversed in the chuck and did the other side.
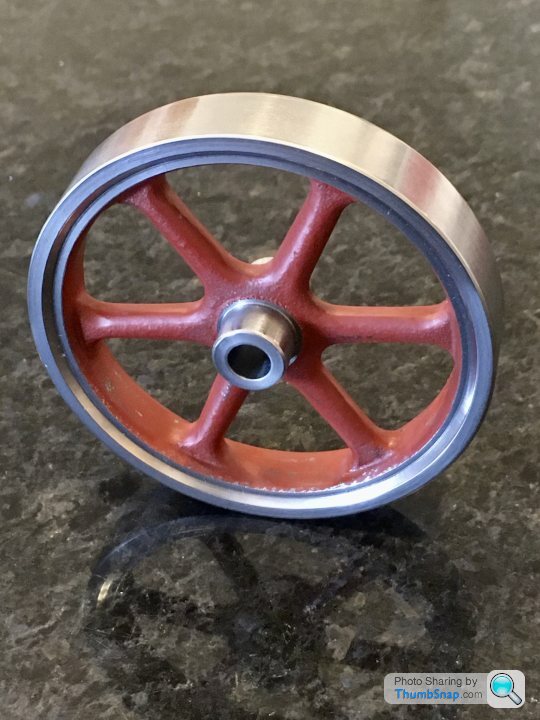
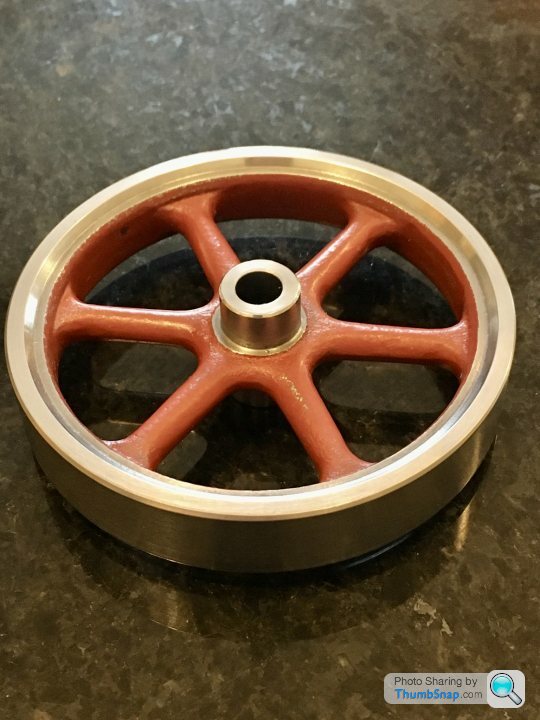
Fit on the shaft is fine, and the features turned on the initial setup are true, however the features on the reverse setup are noticeably off (when spun on the shaft). I might set it up again in the 4-jaw (on the o/d) and re-do the bits that are off.
Quick bit of turning to get back into it: The valve rod packing nut. It’s turned from some hexagonal bar:
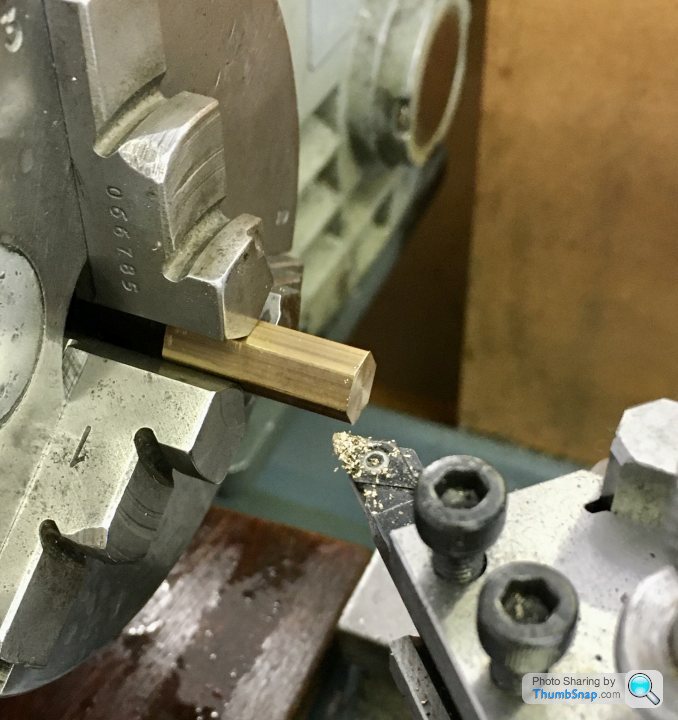
Then drilled and reamed to 1/8” to suit the valve rod.
Turned to 1/4” and chamfered to give a lead for the die:
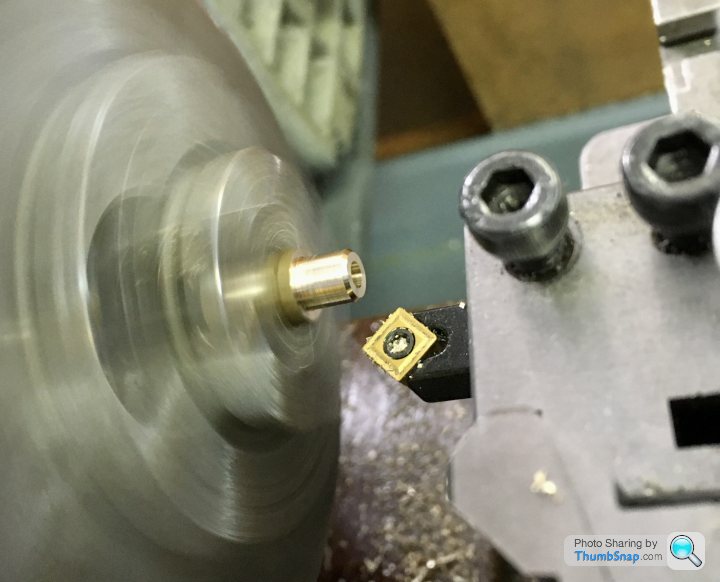
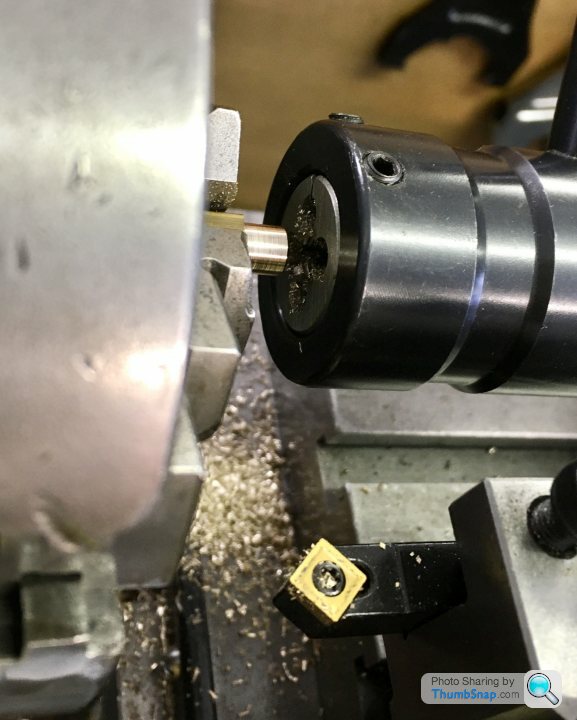
Then chamfered the flats and parted off:
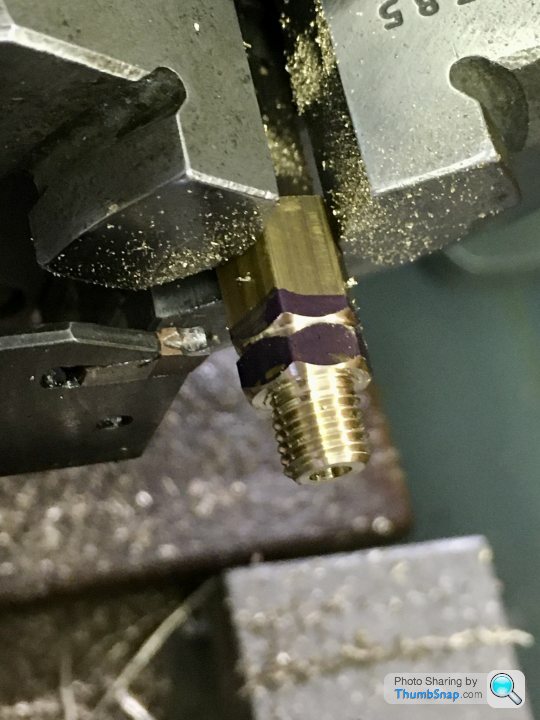
Seems to fit ok:
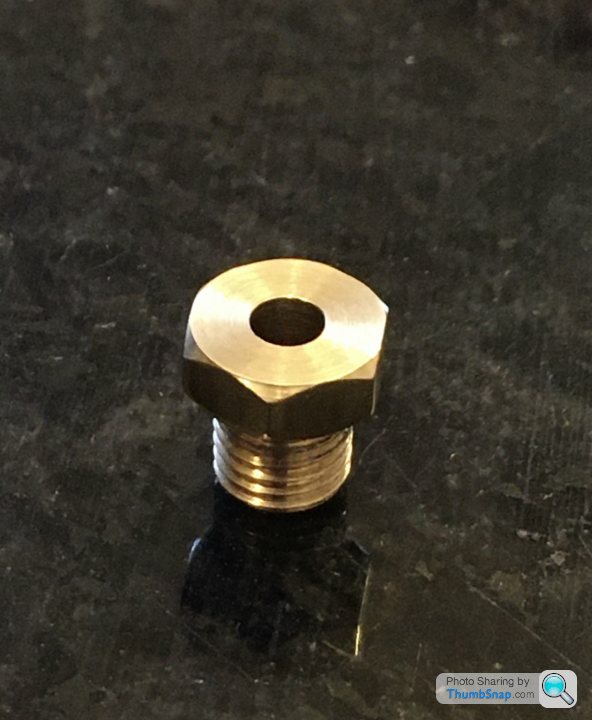
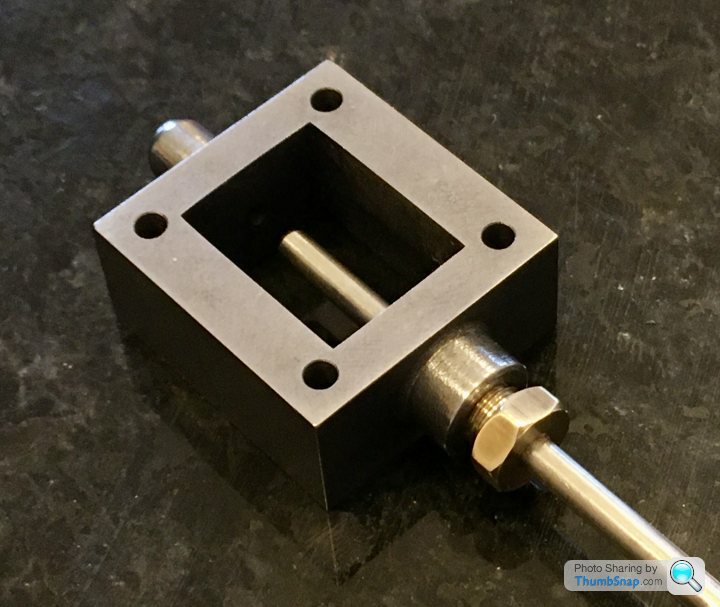
h
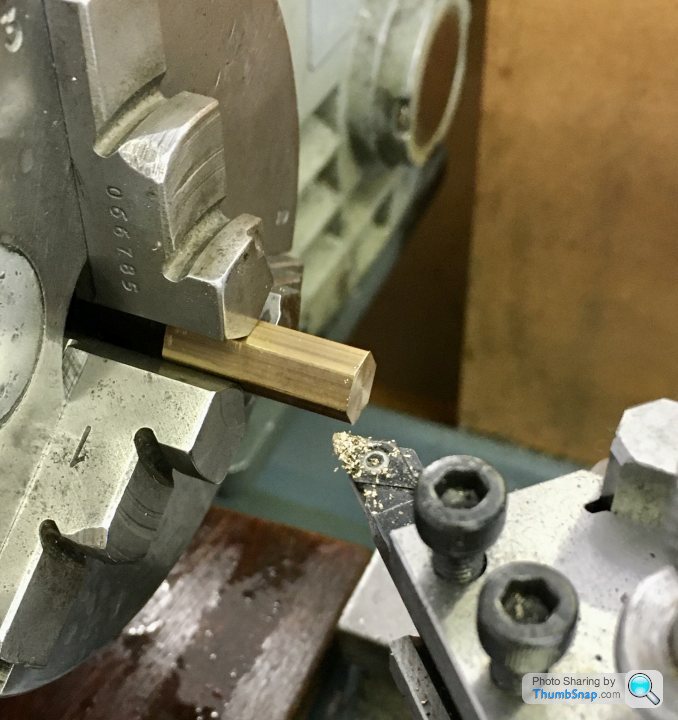
Then drilled and reamed to 1/8” to suit the valve rod.
Turned to 1/4” and chamfered to give a lead for the die:
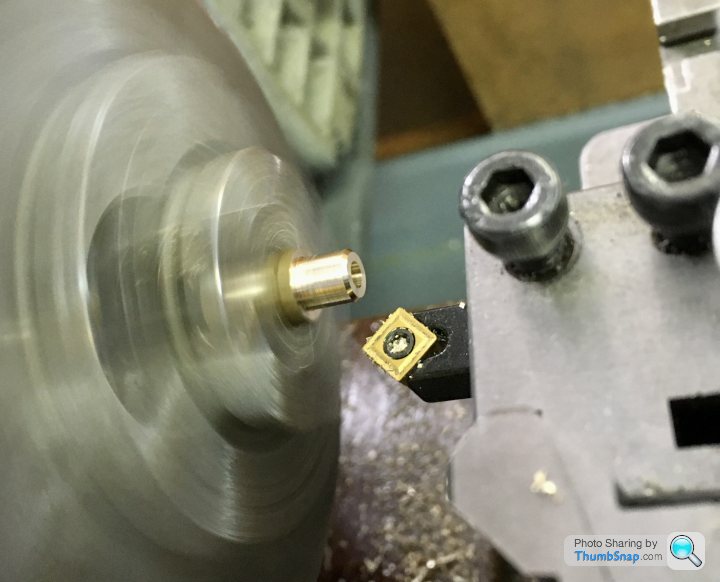
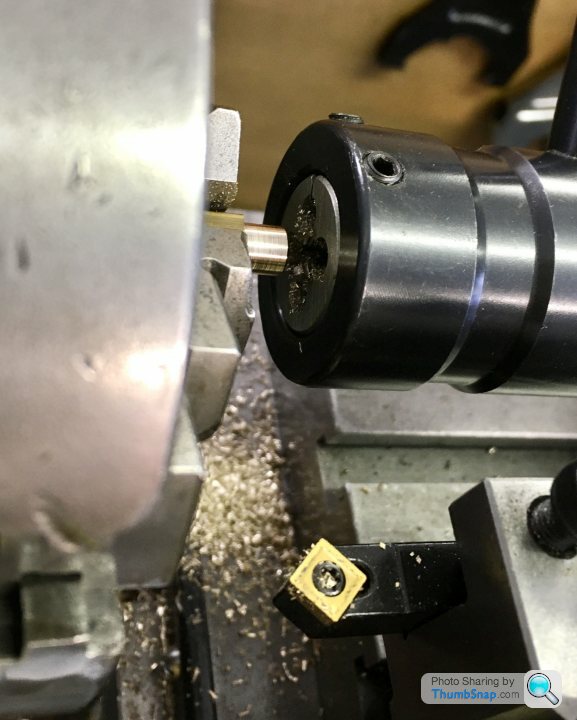
Then chamfered the flats and parted off:
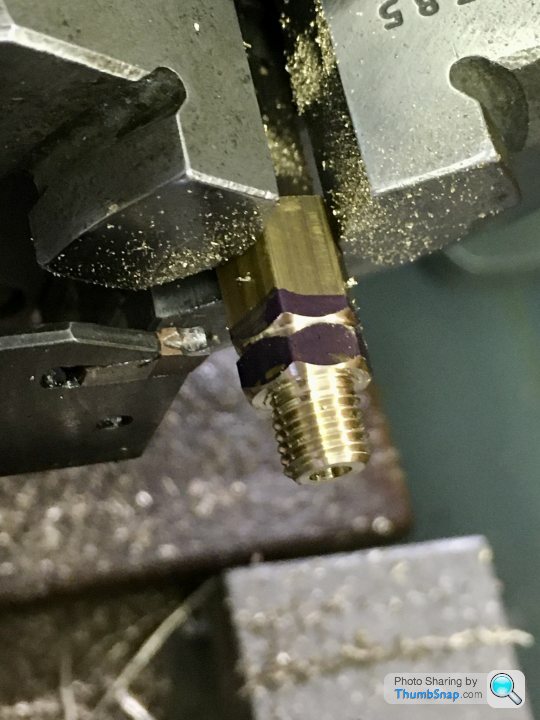
Seems to fit ok:
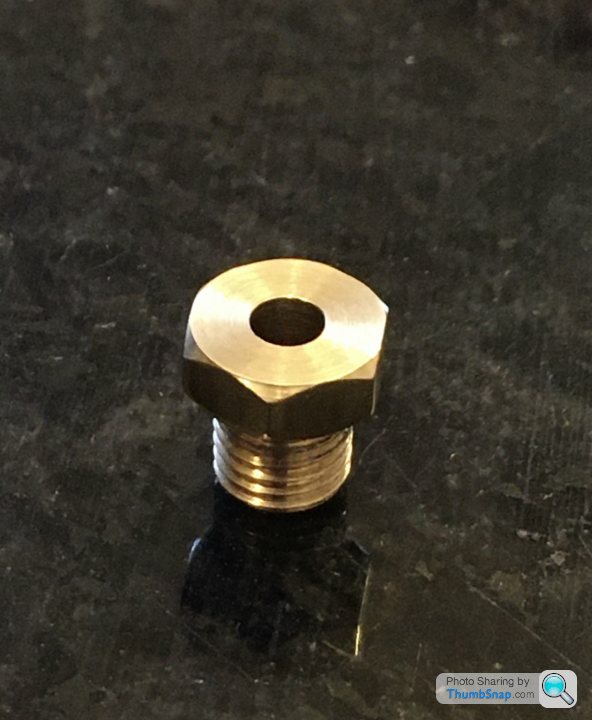
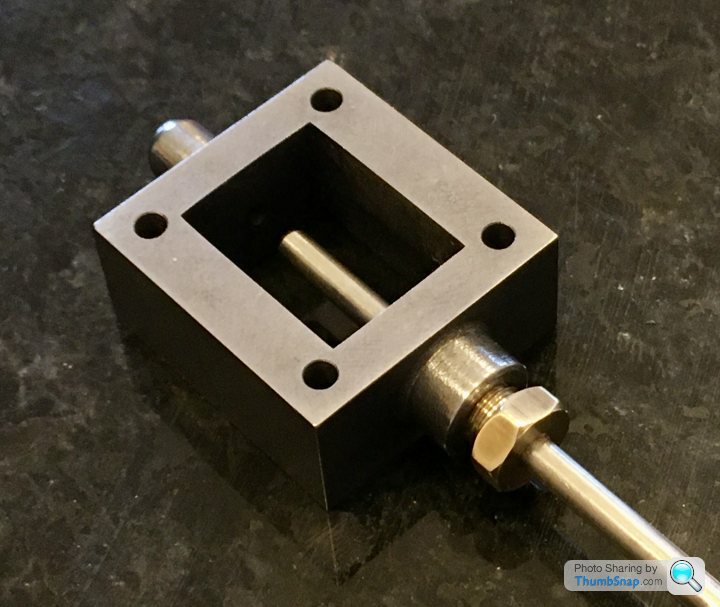
h
Edited by dr_gn on Sunday 19th July 19:21
The piston rod seal packing nut is a bit different from the valve rod nut; it’s larger, and has screwdriver cut-outs for tightening instead of flats due to it fitting within the standard. It’s turned from the same brass stock suppled for the piston:
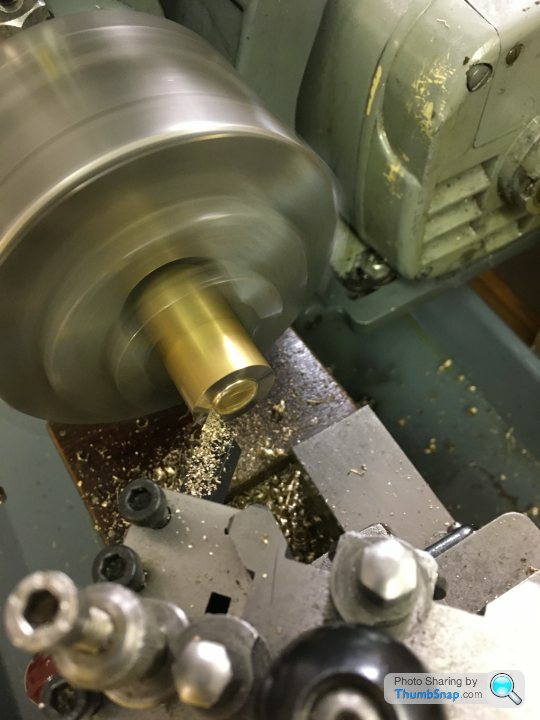
Drilled, reamed, threaded, then turned down to size before parting off:
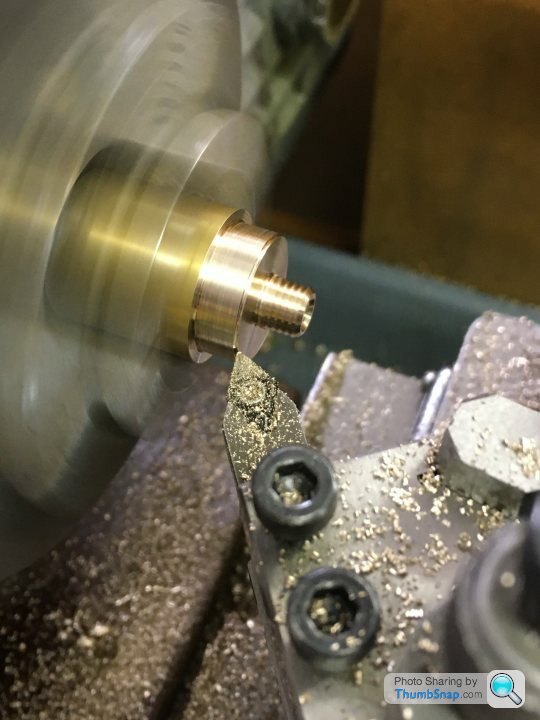
There are six undimensioned cut-outs in the O/D. I don’t have a rotary table, so I made a simple fixture out of the remaining hexaganol stock from the valve nut:
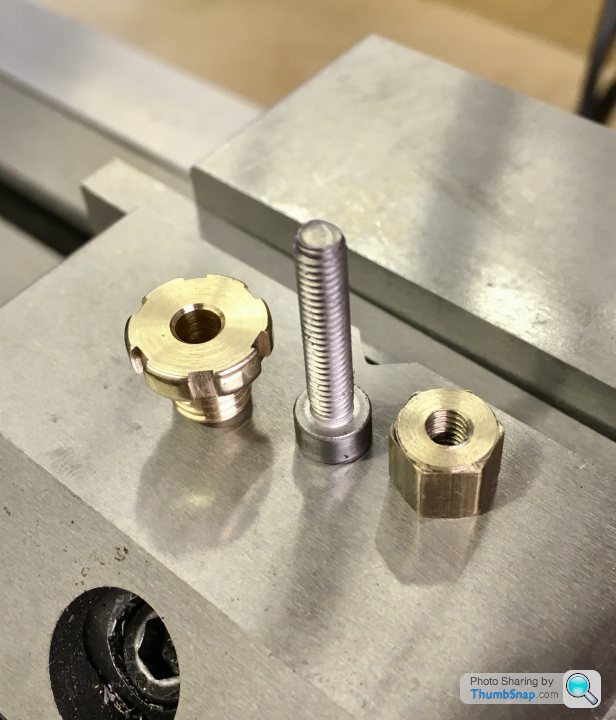
It’s just sits in the milling vice on a parallel, and the slots milled to 2mm and 0.85mm deep from touching on the diameter. Then move around one flat at a time:
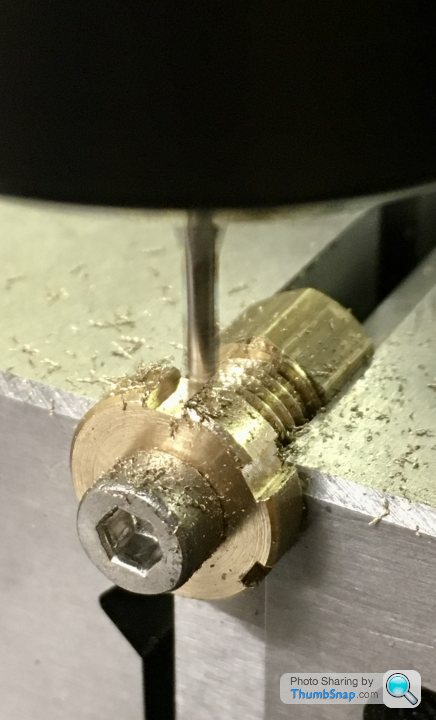
Worked OK:
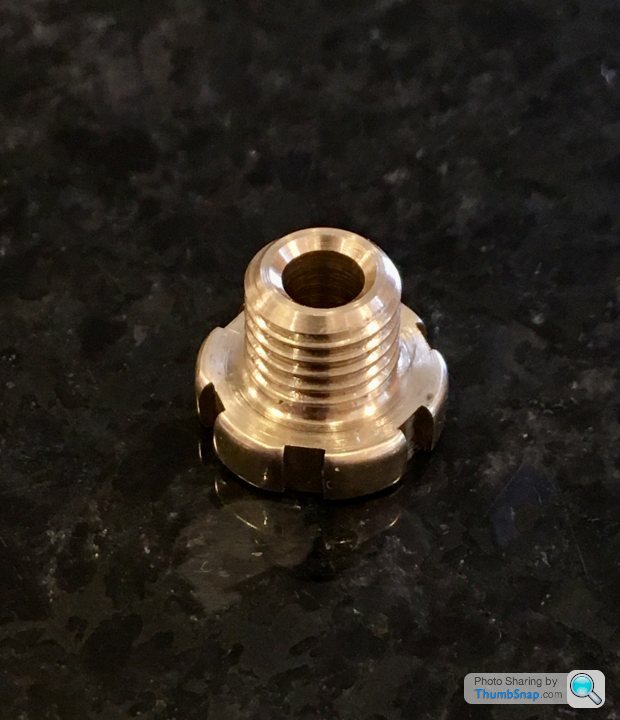
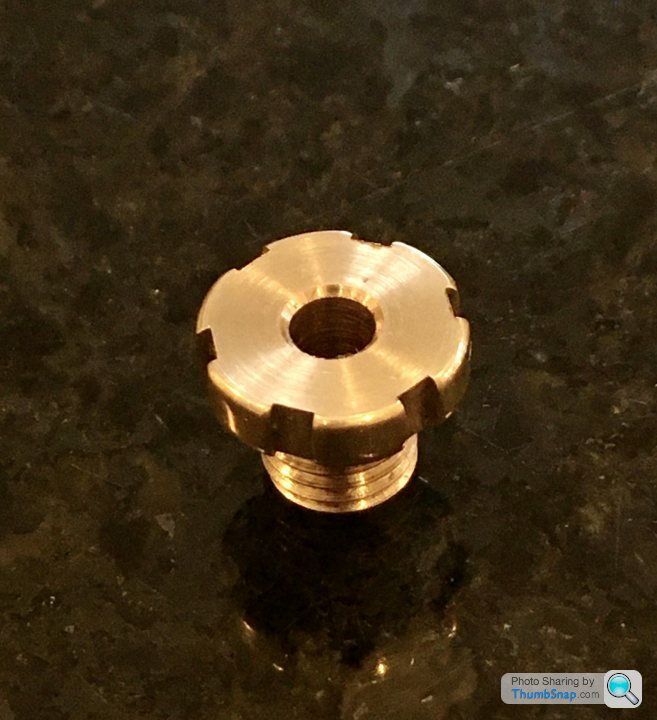
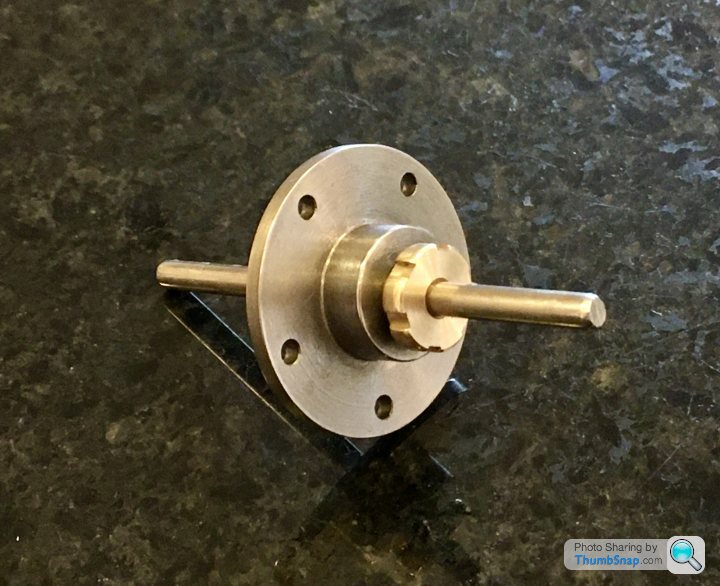
The threads are a bit sloppy in their holes, not sure why. I suppose I could use thread lock if they loosen.
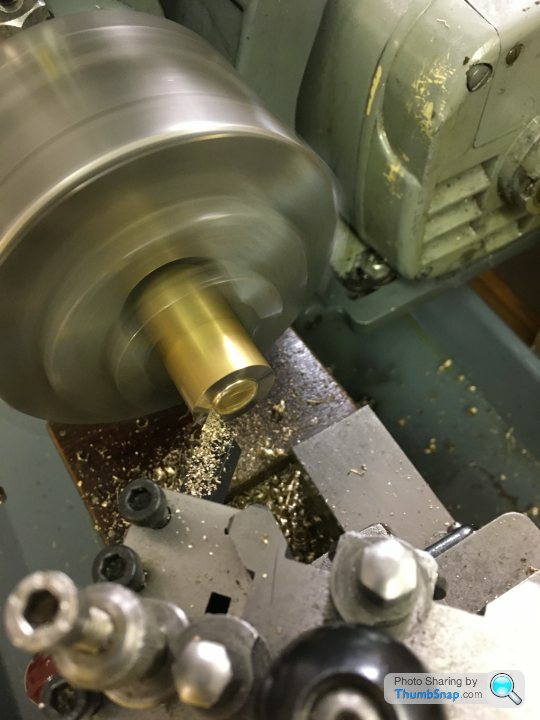
Drilled, reamed, threaded, then turned down to size before parting off:
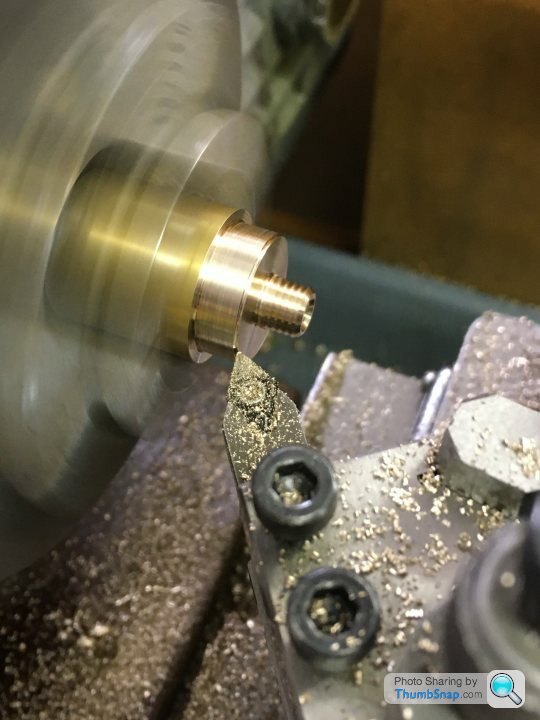
There are six undimensioned cut-outs in the O/D. I don’t have a rotary table, so I made a simple fixture out of the remaining hexaganol stock from the valve nut:
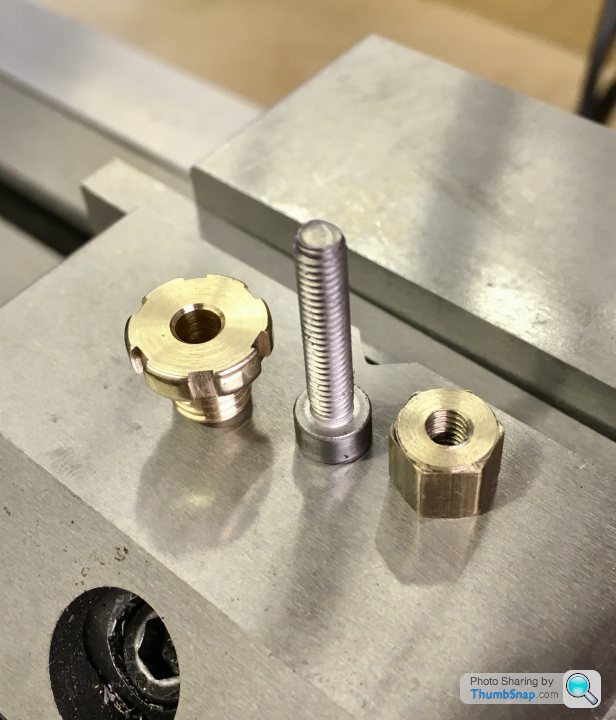
It’s just sits in the milling vice on a parallel, and the slots milled to 2mm and 0.85mm deep from touching on the diameter. Then move around one flat at a time:
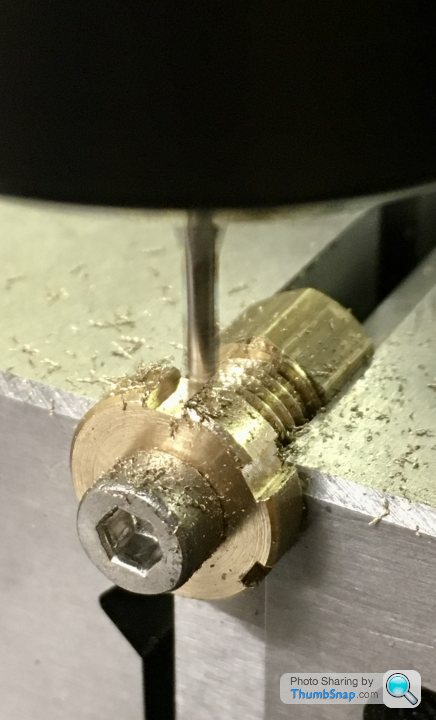
Worked OK:
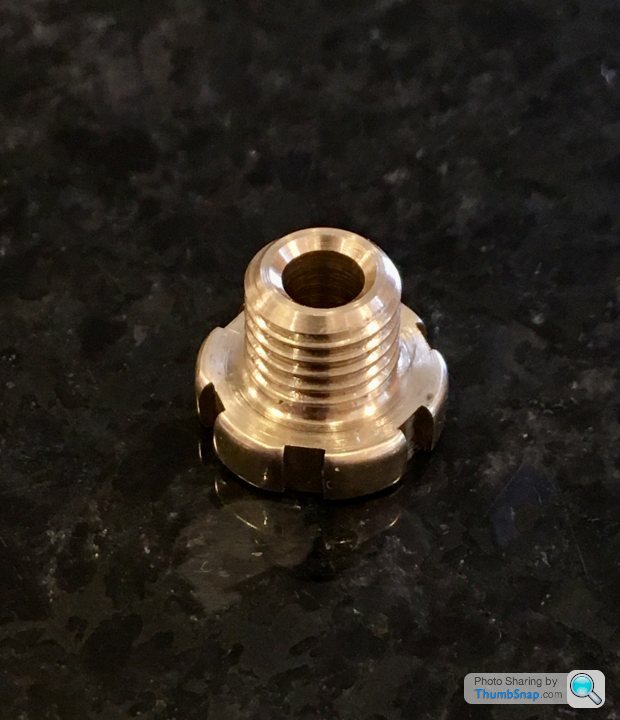
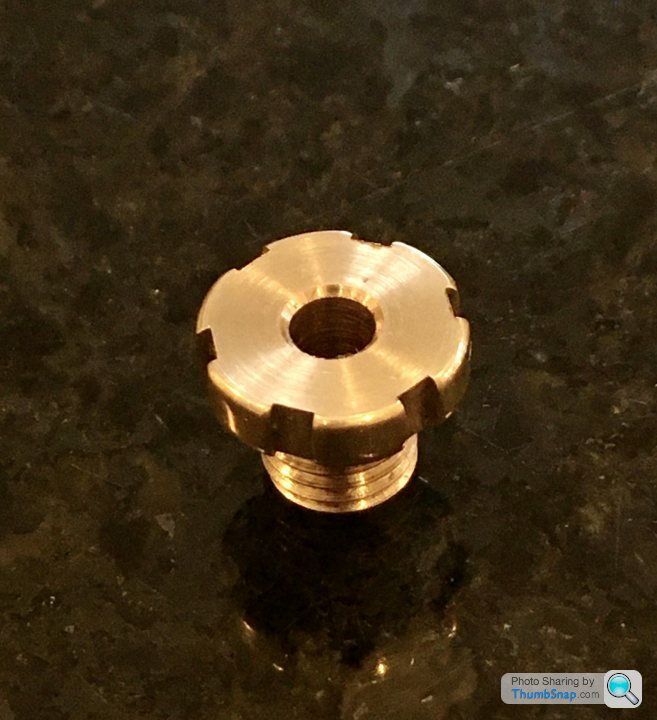
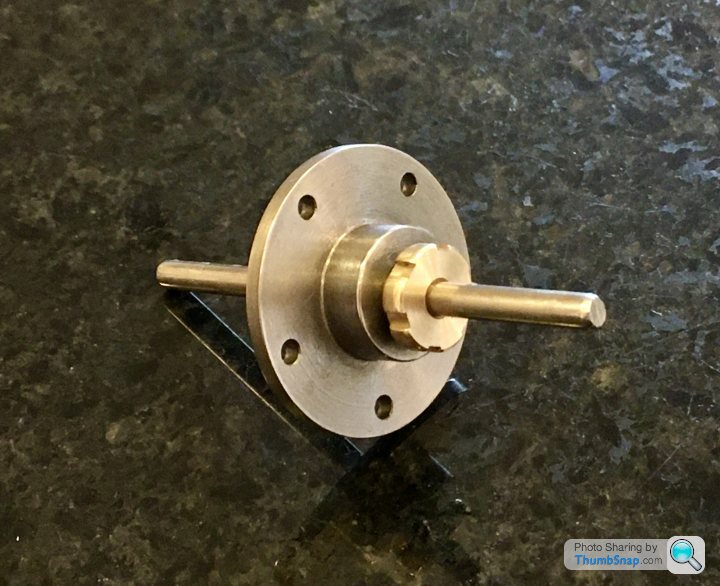
The threads are a bit sloppy in their holes, not sure why. I suppose I could use thread lock if they loosen.
So here - somewhat inevitably - is where it goes wrong...
The valve rod is stepped, and threaded. First of all I made a split bush to fit the 3-jaw chuck (4-jaw won’t close enough). I got it to within 0.0015” of true, centre drilled and turned the end to be a good fit in the valve chest top as per the image:
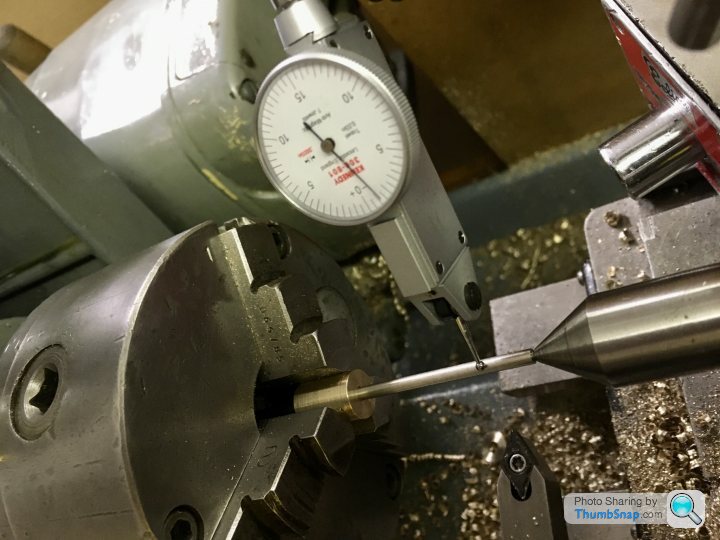
Not sure if this was the best method, but I didn’t get a particularly good finish on the end. Still, it fitted smoothly enough.
Then, the 5BA thread. The die wouldn’t go on the turned-down end. This is where my heart sank as I realised what I’d done. The hole in the top of the valve chest should be 3/32” (2.38mm), but for some reason I’d ended up with 2.75mm.
The root diameter of the 5BA tap is 2.49mm. so obviously it won’t go on.
M3 has a root diameter of 2.46mm (too small) and a slightly finer pitch Than 5BA. I had an old M3 die which did For whatever reason fit over the spigot, but the thread was all over the place. A new M3 die wouldn’t fit at all. The rod also got slightly bent during all this. It does fit, and it does slide in the chest, but it’s not right - too sloppy.
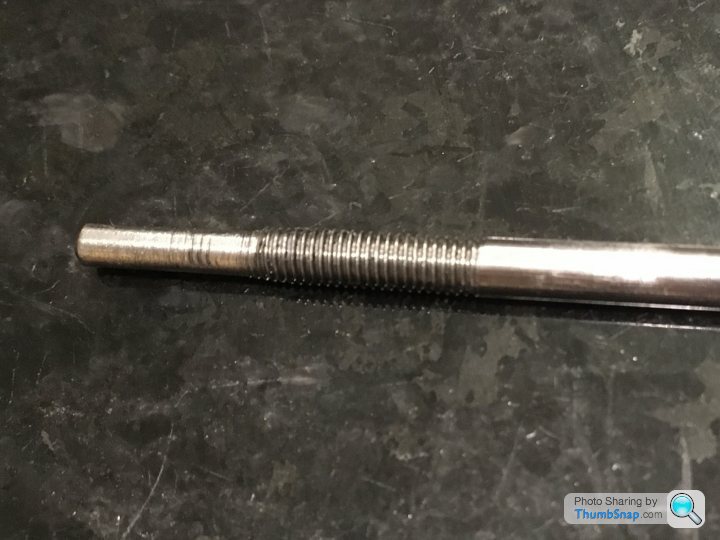
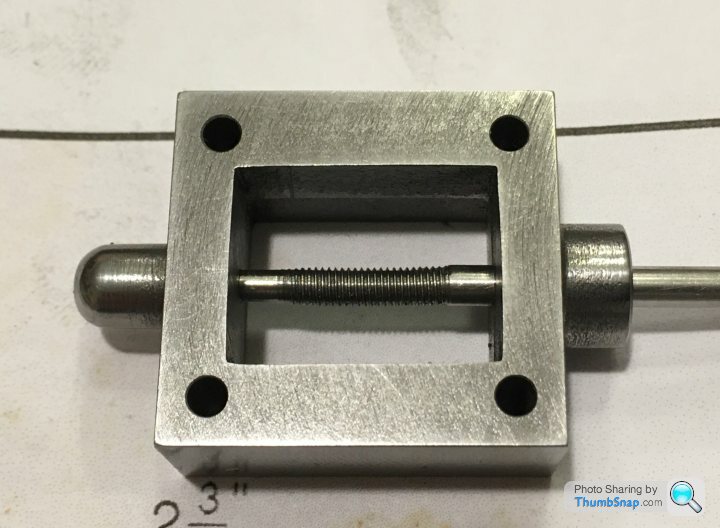
So...I don’t want to re-make another valve chest because it fits everything else perfectly. The only option I can see is to drill the top chest hole out to 1/8” (same as the reamed gland hole at the bottom), Loctite a brass plug into it and re-drill to 3/32”.
And of course re-make the rod.
The valve rod is stepped, and threaded. First of all I made a split bush to fit the 3-jaw chuck (4-jaw won’t close enough). I got it to within 0.0015” of true, centre drilled and turned the end to be a good fit in the valve chest top as per the image:
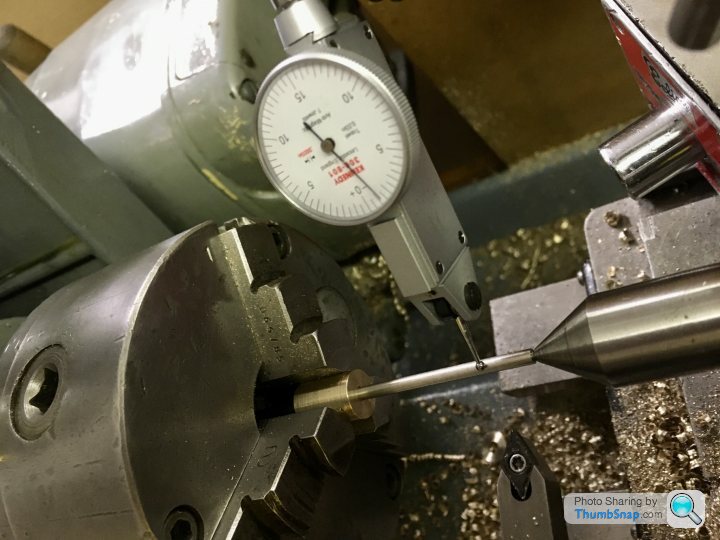
Not sure if this was the best method, but I didn’t get a particularly good finish on the end. Still, it fitted smoothly enough.
Then, the 5BA thread. The die wouldn’t go on the turned-down end. This is where my heart sank as I realised what I’d done. The hole in the top of the valve chest should be 3/32” (2.38mm), but for some reason I’d ended up with 2.75mm.
The root diameter of the 5BA tap is 2.49mm. so obviously it won’t go on.
M3 has a root diameter of 2.46mm (too small) and a slightly finer pitch Than 5BA. I had an old M3 die which did For whatever reason fit over the spigot, but the thread was all over the place. A new M3 die wouldn’t fit at all. The rod also got slightly bent during all this. It does fit, and it does slide in the chest, but it’s not right - too sloppy.
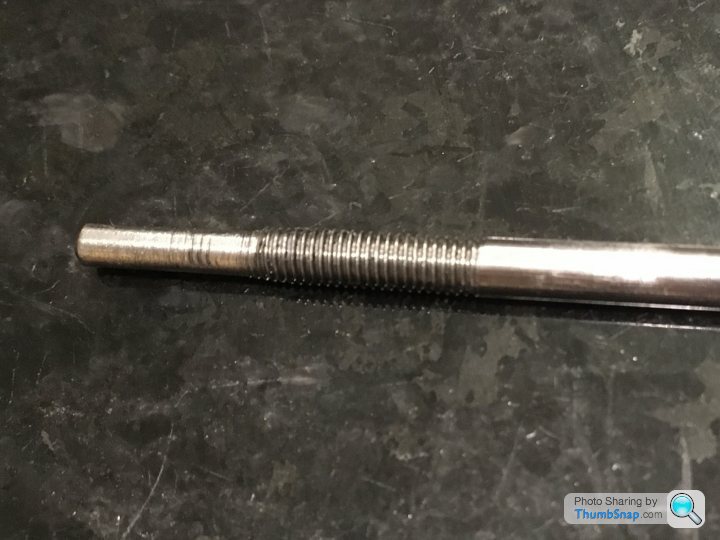
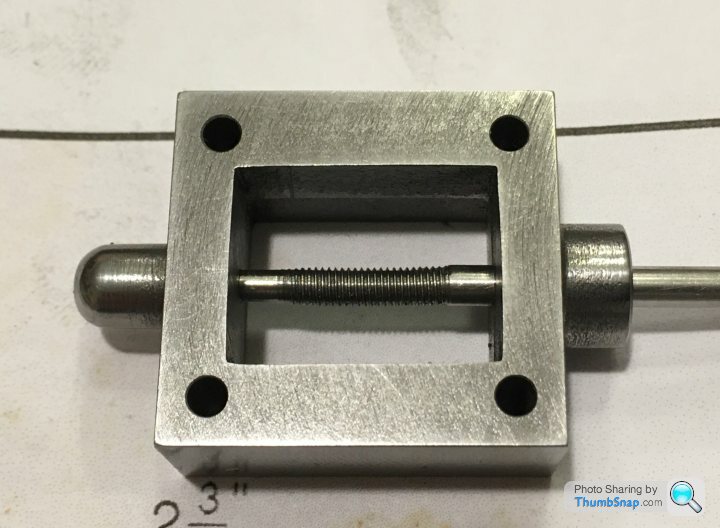
So...I don’t want to re-make another valve chest because it fits everything else perfectly. The only option I can see is to drill the top chest hole out to 1/8” (same as the reamed gland hole at the bottom), Loctite a brass plug into it and re-drill to 3/32”.
And of course re-make the rod.
Thanks, yep, I think that’s the answer. I’ve asked on the ME forum too, but there can’t be many options.
Not making excuses at all, but I think part of the issue was/is the drawings. They only have basic, un-toleranced dimensions, and the Stuart book I’ve got rounds imperial to metric, often to whole numbers. I’ve got into a habit of thinking “so long as that fits to that nicely, the absolute numbers don’t matter too much”. I totally missed the root diameter being critical.
I think I’ll clean the workshop up, get everything back in it’s place and try again. I was hoping not to have to buy any replacement parts, but I think the rod is too short now.
Not making excuses at all, but I think part of the issue was/is the drawings. They only have basic, un-toleranced dimensions, and the Stuart book I’ve got rounds imperial to metric, often to whole numbers. I’ve got into a habit of thinking “so long as that fits to that nicely, the absolute numbers don’t matter too much”. I totally missed the root diameter being critical.
I think I’ll clean the workshop up, get everything back in it’s place and try again. I was hoping not to have to buy any replacement parts, but I think the rod is too short now.
I've got some high strength retainer, so if it's a tight fit it won't go anywhere. Question is wall thickness and being able to drill it perfectly concentric.
The comment form the ME forum was to partially thread the spigot becasue it won't have any effect on the function of the part. I can't assemble it like that though...
The comment form the ME forum was to partially thread the spigot becasue it won't have any effect on the function of the part. I can't assemble it like that though...
So I tried to find a sleeve of about the right size, but no luck. I also considered making a Pre-drilled bush to press in, and drill to size when fitted, but a) A small enough drill was very flexible and b) The very thin wall might collapse on fitting.
Anyway I fitted a plain brass plug:
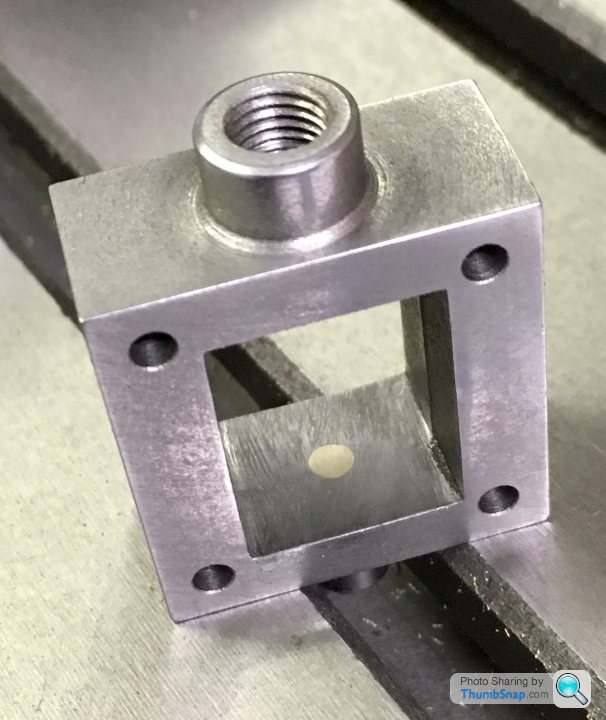
Set it up as best I could again in the 4-jaw chuck and re-drilled to a size that was a definite clearance fit in the 5BA die:
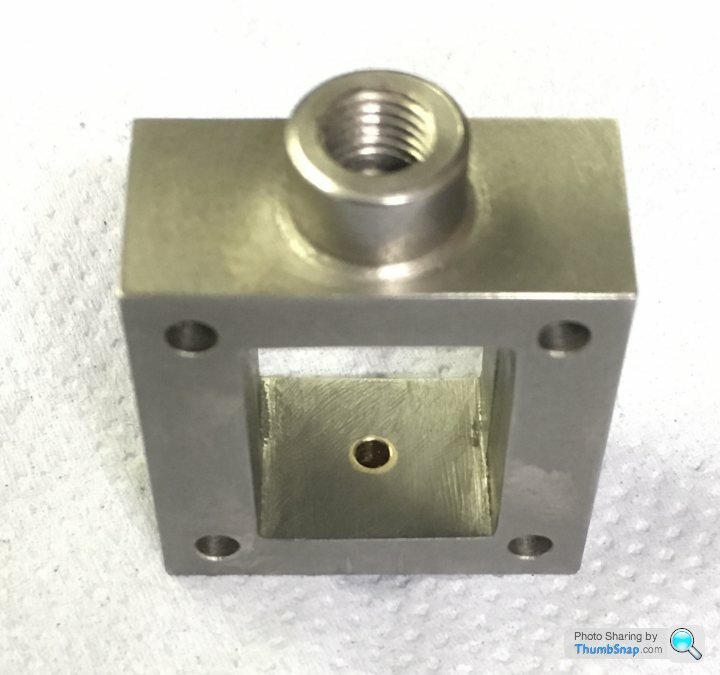
OK, ok it’s not drilled exactly centrally, but there we go. I guess there was no guarantee the initial hole was spot-on either.
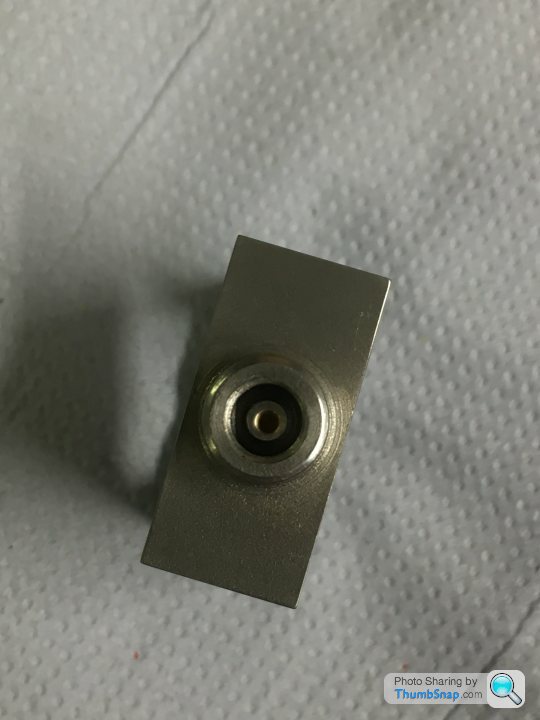
There is some float in the lower seal hole and nut, so I think the new valve rod (yet to re-make it) should be a good enough fit. If not I’ll drill out again and risk a pre-centred bush.
Anyway, lessons learned. Onwards...
Anyway I fitted a plain brass plug:
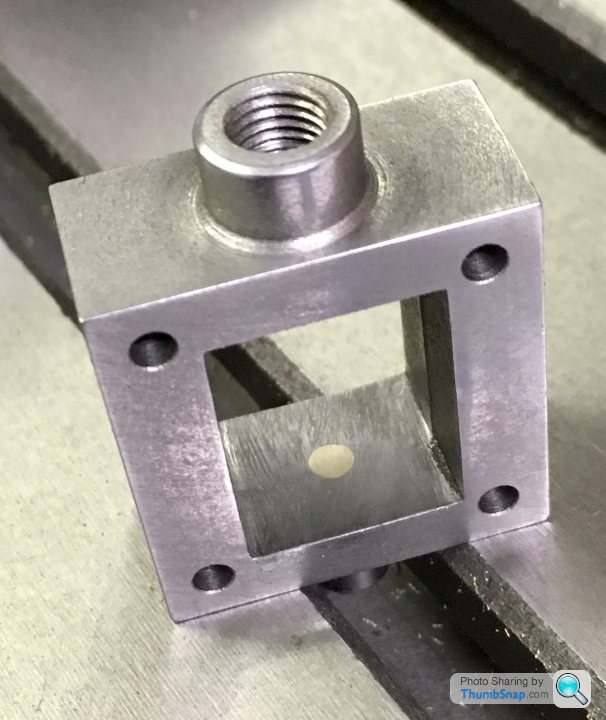
Set it up as best I could again in the 4-jaw chuck and re-drilled to a size that was a definite clearance fit in the 5BA die:
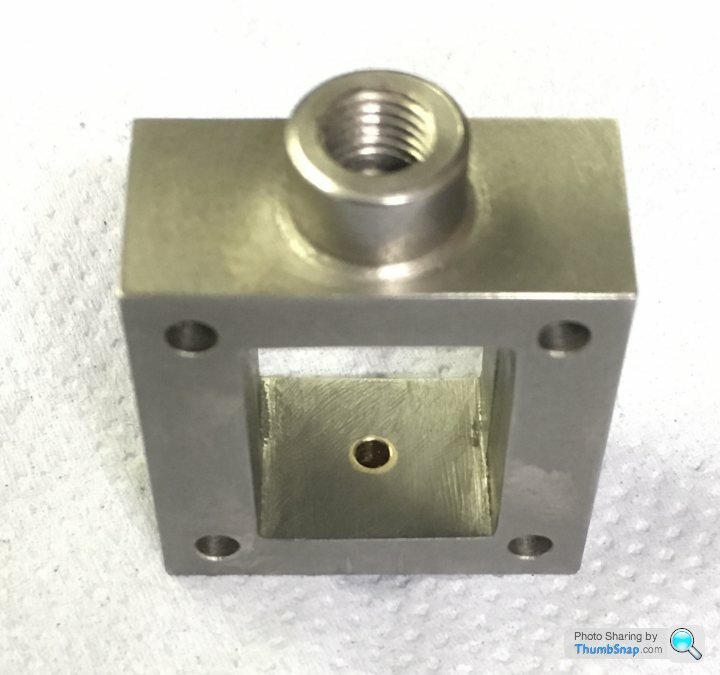
OK, ok it’s not drilled exactly centrally, but there we go. I guess there was no guarantee the initial hole was spot-on either.
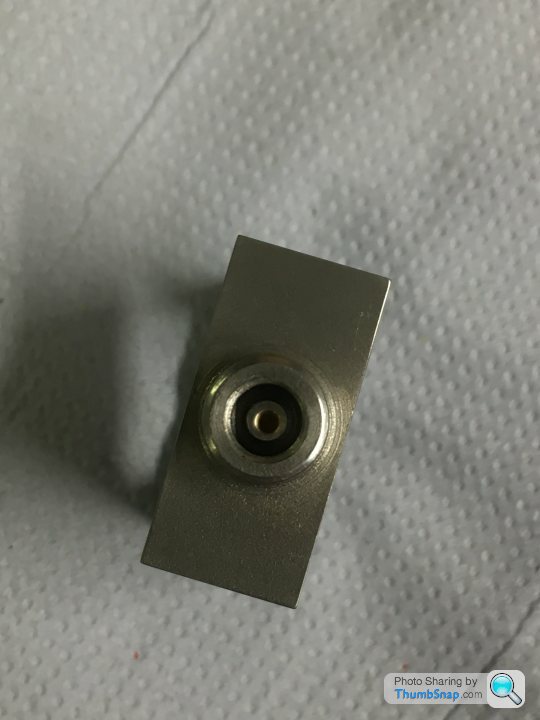
There is some float in the lower seal hole and nut, so I think the new valve rod (yet to re-make it) should be a good enough fit. If not I’ll drill out again and risk a pre-centred bush.
Anyway, lessons learned. Onwards...
Gassing Station | Scale Models | Top of Page | What's New | My Stuff