Unusual job on the bench today
Discussion
ross-co said:
Thanks for the insight its something i have never really put much thought to, but now i have i find it fascinating, love the level of detail etc.
Is there a large chance when working with some materials of damage occurring, for instance when doing the "claws" and cutting and shaping in such close proximity to the stones do they get marked by processes being completed around them or are the tools designed to help avoid this?
Yup! Stones get broken, chipped, burnt and eroded, on a fairly frequent basis too....... although i try to keep it to a minimum. Some stones are more vulnerable to damage than others though. Here's a few common issues:Is there a large chance when working with some materials of damage occurring, for instance when doing the "claws" and cutting and shaping in such close proximity to the stones do they get marked by processes being completed around them or are the tools designed to help avoid this?
Diamonds: Although they are the hardest of the materials we know about they still do have their own risks. They are easily chipped, especially old-cuts, and any cut with sharp corners. Like any hard material they are very brittle if approached with the wrong tools at the wrong angle. Old-cut diamonds have a habit of chipping along the girdle, and sometimes flake off along the facets. Pear cuts and princess cuts usually fracture on the corners. Diamonds also burn. Direct heat will cause the surfaces of a diamond to burn and become cloudy, unless you use borax to protect them. This acts as a barrier that can be removed later. That said, at much higher temps diamonds will burn internally also so borax isnt a 100% protector, usually a problem when working with diamonds set in heavy platinum wedding bands as you cannot easily remove and reset them. Other than that diamonds are pretty hardy and don't cause too many issues.....unless they have been silicon filled at a lab and then all sorts of stuff can happen.
Emeralds, amethysts, aqua and other soft stones: Huge risk with these stones. They are very soft and brittle and any large internal flaws give cause for concern. Heat is a problem too and emeralds esecially will shatter at the slightest application of direct heat. Amethysts and aquas scratch easily and even heavy polishing can buff off the sharp edges of freshly cut facets leaving the stone dull with no sparkle. You can't use borax on these either as when warm it eats into the stone leaving it looking rough and worn. Best method with these items is to warn the customer of the risks and get them to authorise removing the stones prior to any further work being carried out. When larger (1ct plus) emeralds and cornflour-sapphires can be as pricey as diamonds it makes sense to play safe.
Dark sapphires and rubies: A fairly safe stone but still with risks as per diamonds. Big downside with these is that borax eats into the stone when hot so you need to be very carefull witn the amount of applied heat. Normally if the stones are allowed to cool naturally after heating they go back to original colour and structure, but every so often a lemon shows its face. Again, larger ones are flagged up put to the customer for authorisation ref removal prior to work being carried out. Nice rubies are more expensive than diamonds these days.
Opals, fire opals and pearls: Proper sods and need to be kept away from any abrasive tools, chemical and any heat. The only way to work with items containing these stones is to take them out. Simples!!
So, what do we do if we break or damage a stone: If it's small we just replace it. If its larger (0.5ct plus) we can have it repolished, recut where damaged or replaced depending on the severity. If it needs replacing then obviously the customer needs to be informed as many buyers these days have certificates for the stones they buy. Its a risky business at times but it's the game we play. Luckily for me the bigger stones tend to be more hardy and in better quality mounts than the smaller ones so work is easier to carry out safely. Biggest ive broken was a 6.6ct AAA Tanzanite but I know my father in law had a stinker with a 2ct silicon filled diamond back in the day. Nowt he could do about it, but you try reasoning with an angry customer!!
Celtic Dragon said:
Ecain, you are demonstrating some stunning work on this thread, please keep posting your work. Its great to see what a craftsman can do.
If you don't mind me asking, what tools do you use for the final fitting etc? You mention that claws etc are filed to shape. I dabble in making knife handles, (I can make blades, but now live in a flat so had to stop), and tried making the below. The plan was to have a Wolf paw print cut into the Mammoth Ivory but the attempt didn't quite quite turn out as I wanted due to my needle files not being fine enough.
The black is Water Buffalo horn, the white is Warthog ivory and the infill is Mammoth Ivory. The paw is copper dust encapsulated in clear resin.

All the blocks were cut, filed and glued by hand.
Hi mate. Interesting knife handle there. Maybe you should do a 'build thread' for one.If you don't mind me asking, what tools do you use for the final fitting etc? You mention that claws etc are filed to shape. I dabble in making knife handles, (I can make blades, but now live in a flat so had to stop), and tried making the below. The plan was to have a Wolf paw print cut into the Mammoth Ivory but the attempt didn't quite quite turn out as I wanted due to my needle files not being fine enough.
The black is Water Buffalo horn, the white is Warthog ivory and the infill is Mammoth Ivory. The paw is copper dust encapsulated in clear resin.

All the blocks were cut, filed and glued by hand.
Final finishing is dependent on what the job is:
For claw work the final shaping and filing is done with a grade 4 triangular needle file, scorpers and a fine bladed hacksaw. The file does the shaping, scorpers do the picking and the hacksaw takes away any slivers that the above wont shift. After that the claws are smoothed over with a graining tool (hollow ended tool), which also serves to ensure the claws are left flush with the stones.
For bigger jobs like shanks, signet ring finishing and sizing i use a medium half-round file to make the correct profile followed by 3 grades of emery paper to remove file marks and prepare for polishing.
There are loads of finishing attachments for the the pendant drill too. Everything from drill bits to silicon wheels and grinding tools. All of these play a part and the closer to the finished item you get the finer the tool you need.
Sorry for the delay / break in posts on this thread but ive been a bit manic of late.
Surgery to get rid of my bowel cancer was on May 15th (went really well), my son was born on May 21st (12 days overdue with wife have emergency delivery under general) and follow on chemo that started in June has left me a bit tired. Nevertheless i've been at work the whole time, making you guys the odd bit here and there.
Made this silver cross for a PHer to replace a base metal one they lost:
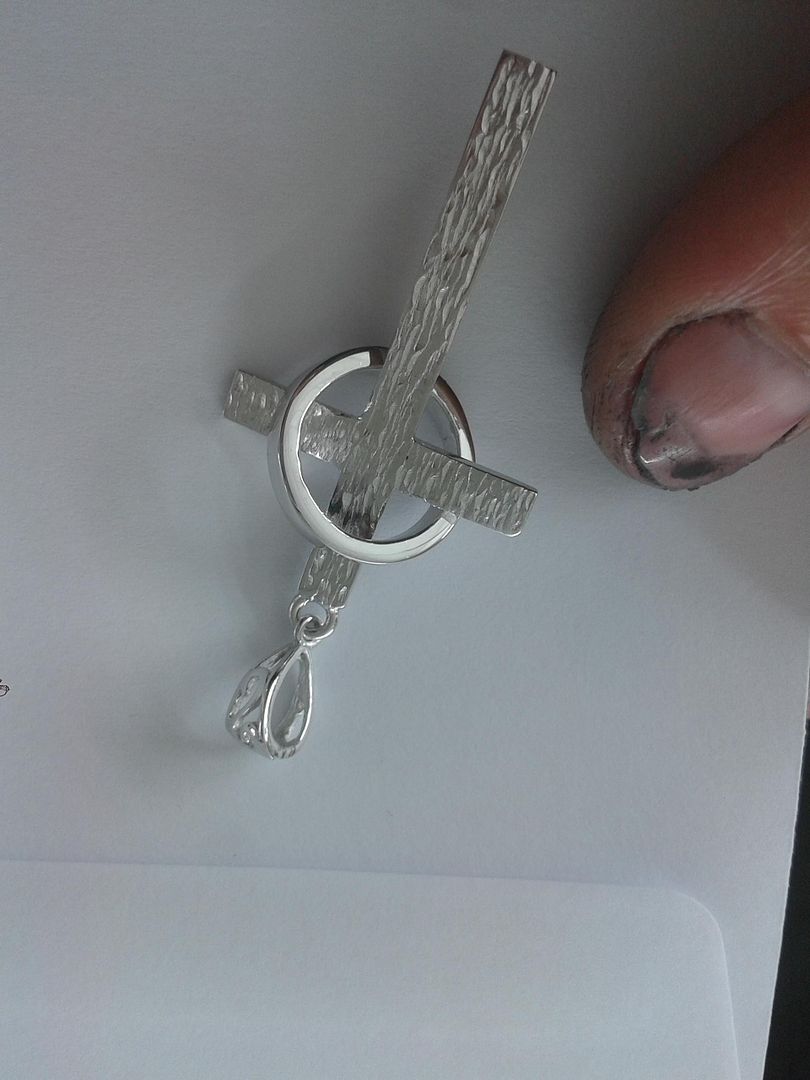
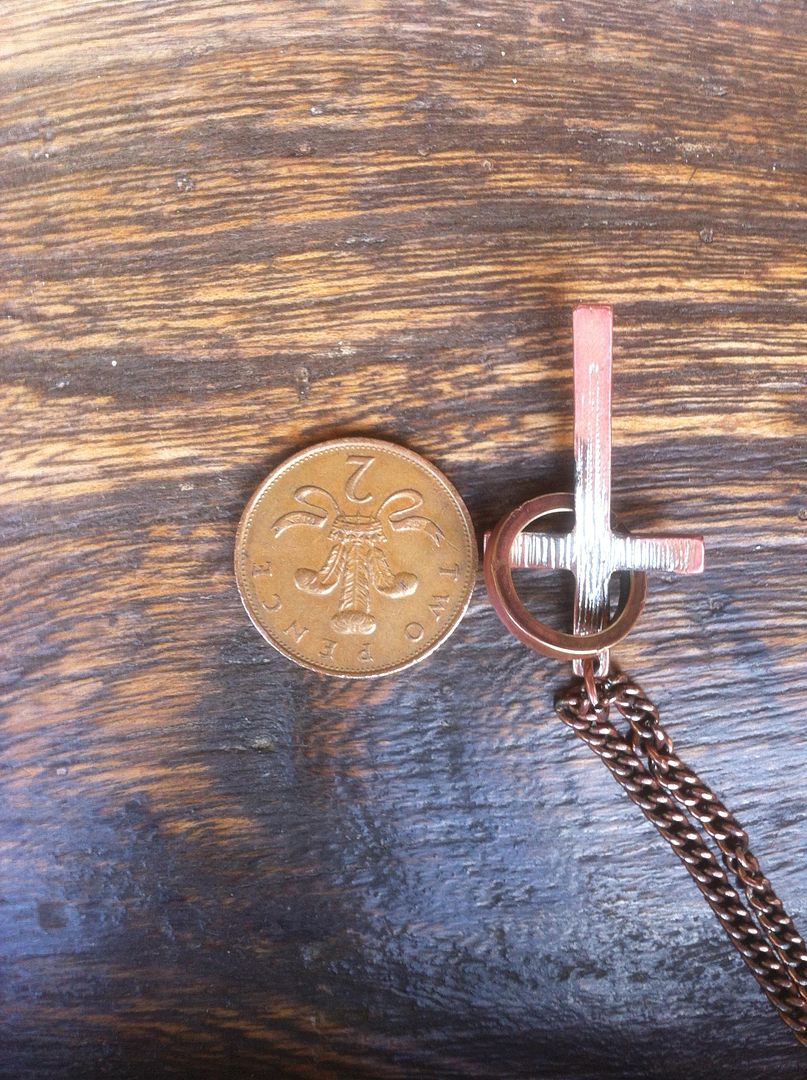
Servicing your watches still.
And currently i the middle of turning this 18ct white gold, 40 diamond bracelet
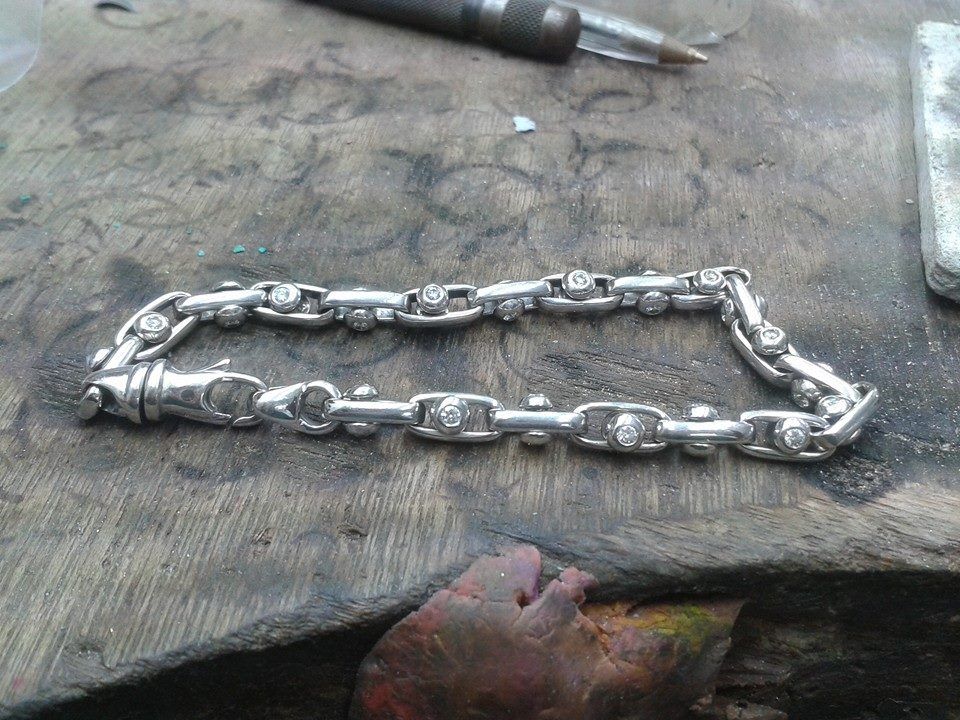
into a 40 diamond 18ct white gold ring:
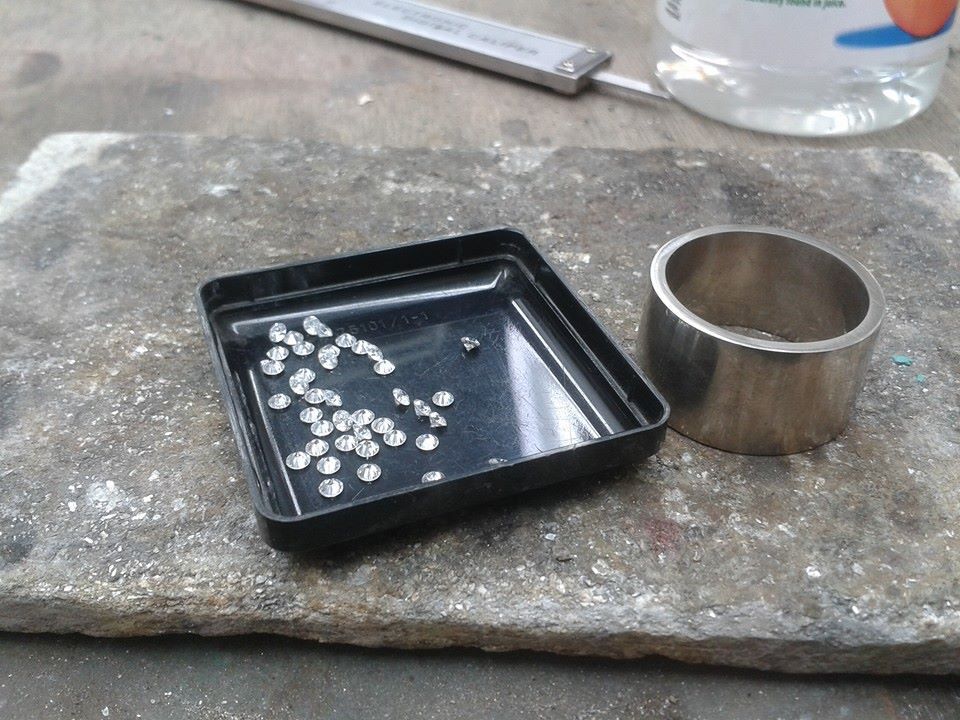
Finished article pics and more projects go follow.
Eddie
Surgery to get rid of my bowel cancer was on May 15th (went really well), my son was born on May 21st (12 days overdue with wife have emergency delivery under general) and follow on chemo that started in June has left me a bit tired. Nevertheless i've been at work the whole time, making you guys the odd bit here and there.
Made this silver cross for a PHer to replace a base metal one they lost:
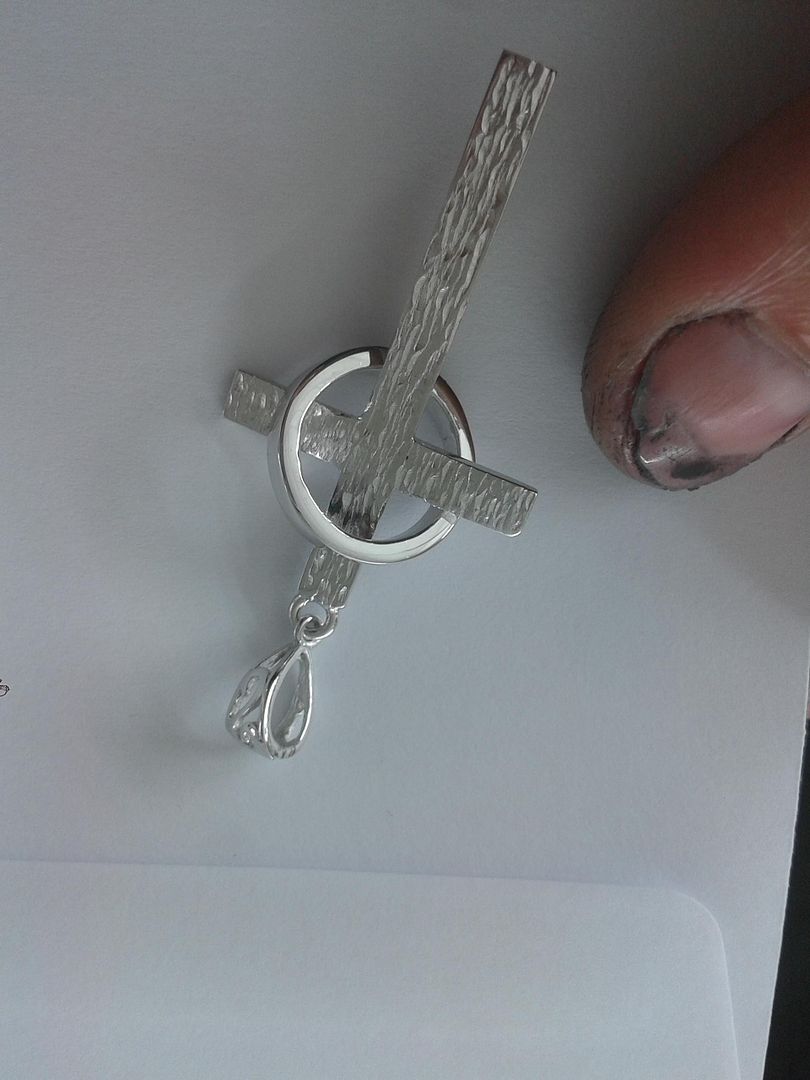
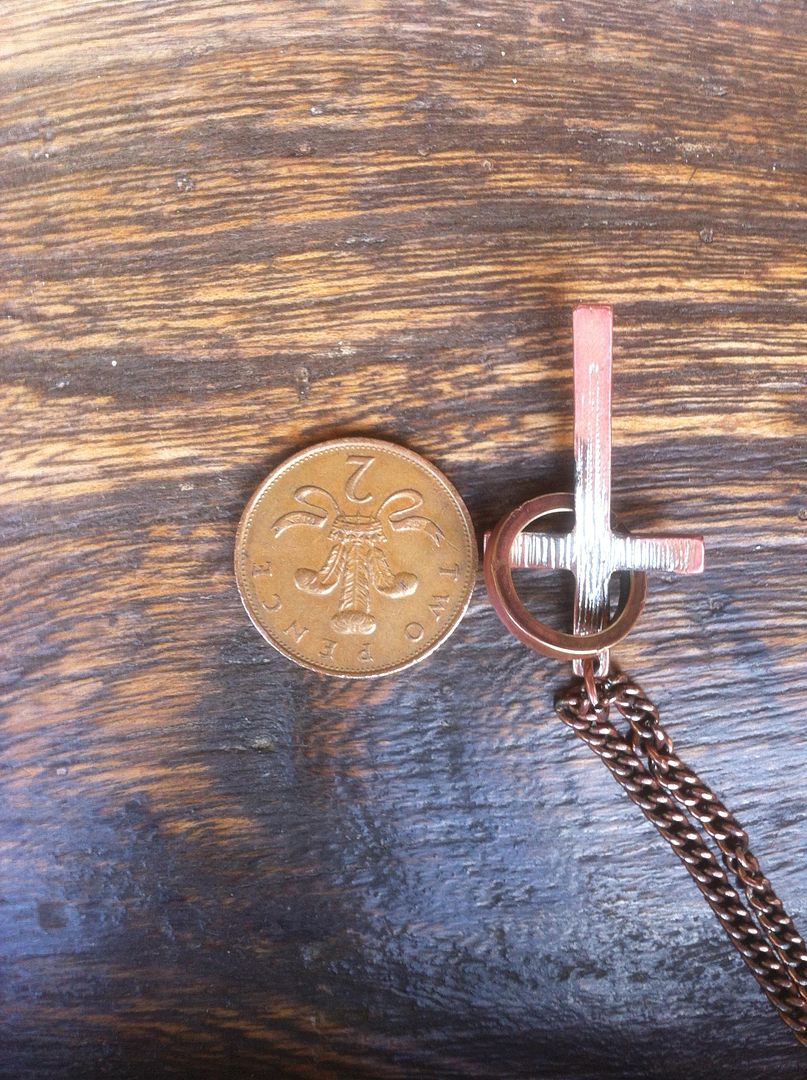
Servicing your watches still.
And currently i the middle of turning this 18ct white gold, 40 diamond bracelet
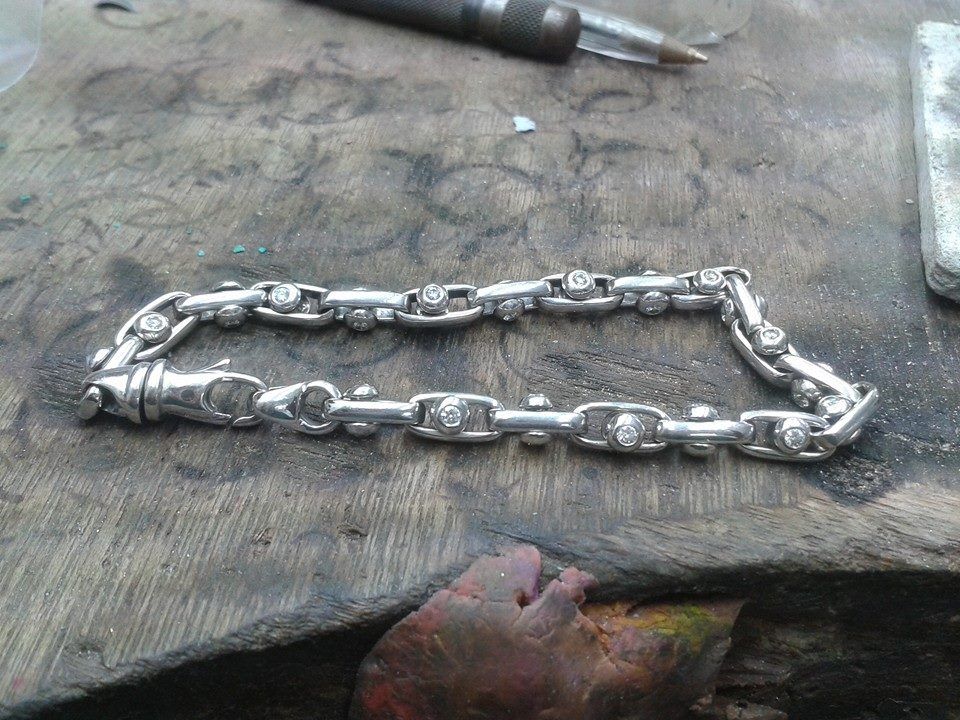
into a 40 diamond 18ct white gold ring:
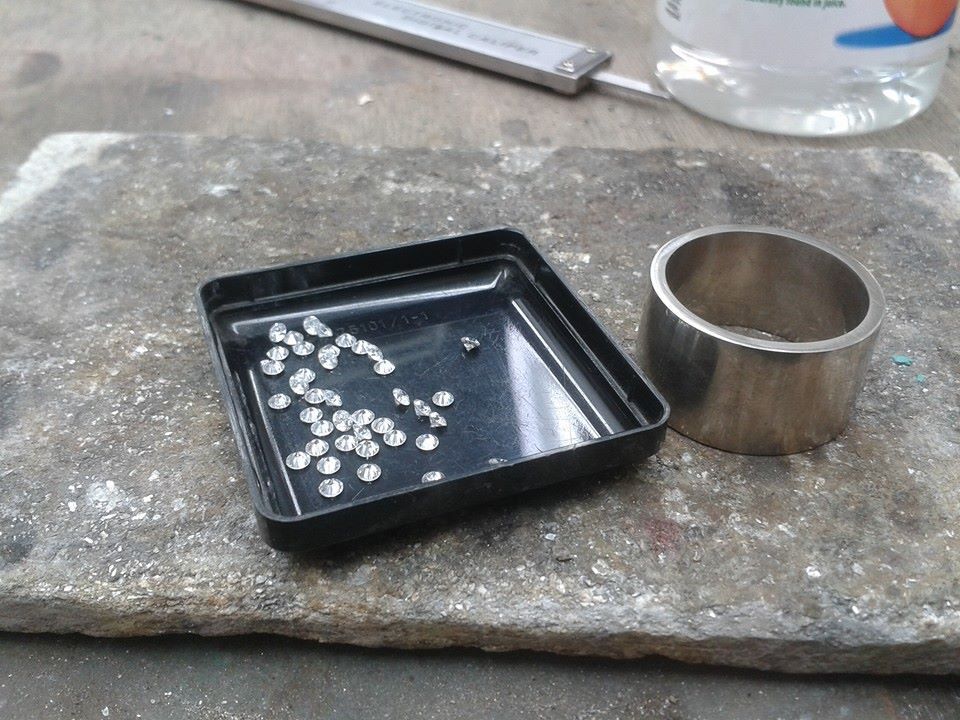
Finished article pics and more projects go follow.
Eddie
Thanks loads. My little man is my new inspiration. He's a bit of a miracle given the state i was in when we conceived so I need to look after him. 
I'm not 100% sure if i'll continue my work as a jeweller, the cancer thing has been a big wake up call. Got some decisions to make regarding the future of my business but the truth is that it was never how i imagined myself. I'm an outdoors kinda guy and i think in time i need to find a role where i can get back to what i enjoy and not just what i'm good at / been railroaded into. Jewellery repair / manufacture is a fantastic business and pays really well but id rather and average wage and fresh air any day of the week. You only live once and life is too short at the best of times.

I'm not 100% sure if i'll continue my work as a jeweller, the cancer thing has been a big wake up call. Got some decisions to make regarding the future of my business but the truth is that it was never how i imagined myself. I'm an outdoors kinda guy and i think in time i need to find a role where i can get back to what i enjoy and not just what i'm good at / been railroaded into. Jewellery repair / manufacture is a fantastic business and pays really well but id rather and average wage and fresh air any day of the week. You only live once and life is too short at the best of times.
buzzer said:
one of the best threads on PH. glad you are getting better and congratulations on the little one.
do what makes you happy!
Wouldn't go that far but thank you all the same.do what makes you happy!
Once I've got the all clear health wise later in the year I'll start looking more seriously at what im doing in life. Give me £1.5million and I know for sure what id do (buy a local trout fishery) but until that day........
ecain63 said:
Sorry for the delay / break in posts on this thread but ive been a bit manic of late.
Surgery to get rid of my bowel cancer was on May 15th (went really well), my son was born on May 21st (12 days overdue with wife have emergency delivery under general) and follow on chemo that started in June has left me a bit tired. Nevertheless i've been at work the whole time, making you guys the odd bit here and there.
Made this silver cross for a PHer to replace a base metal one they lost:
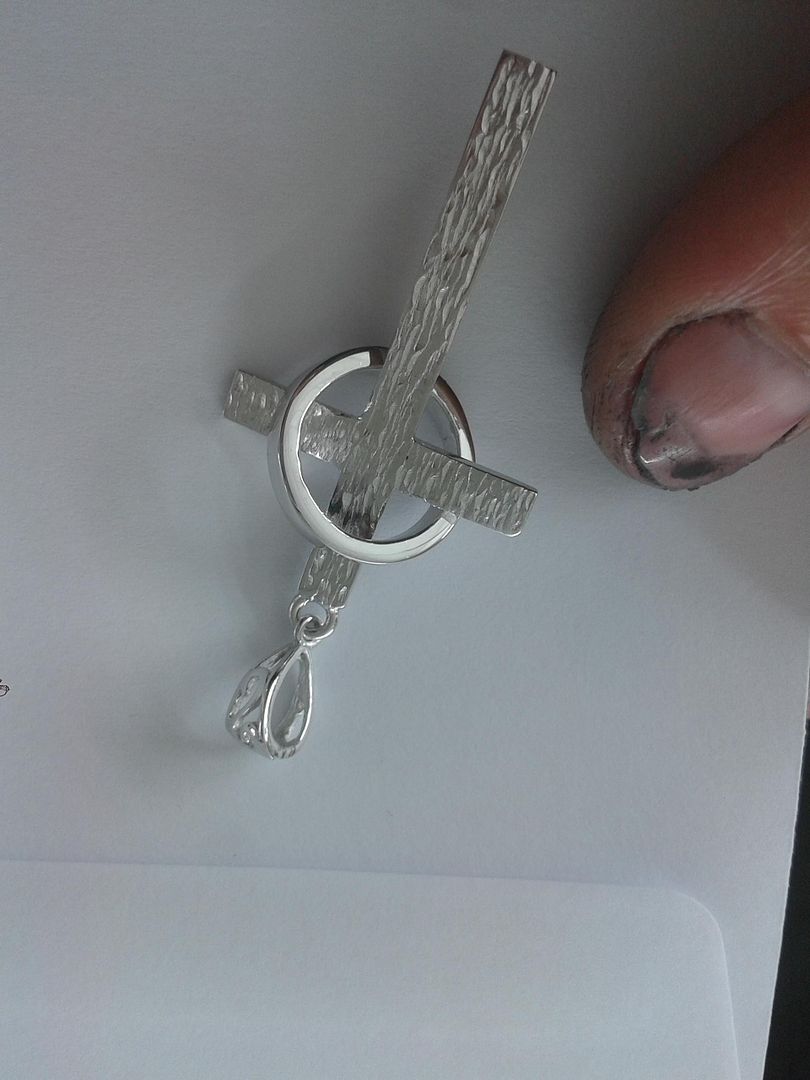
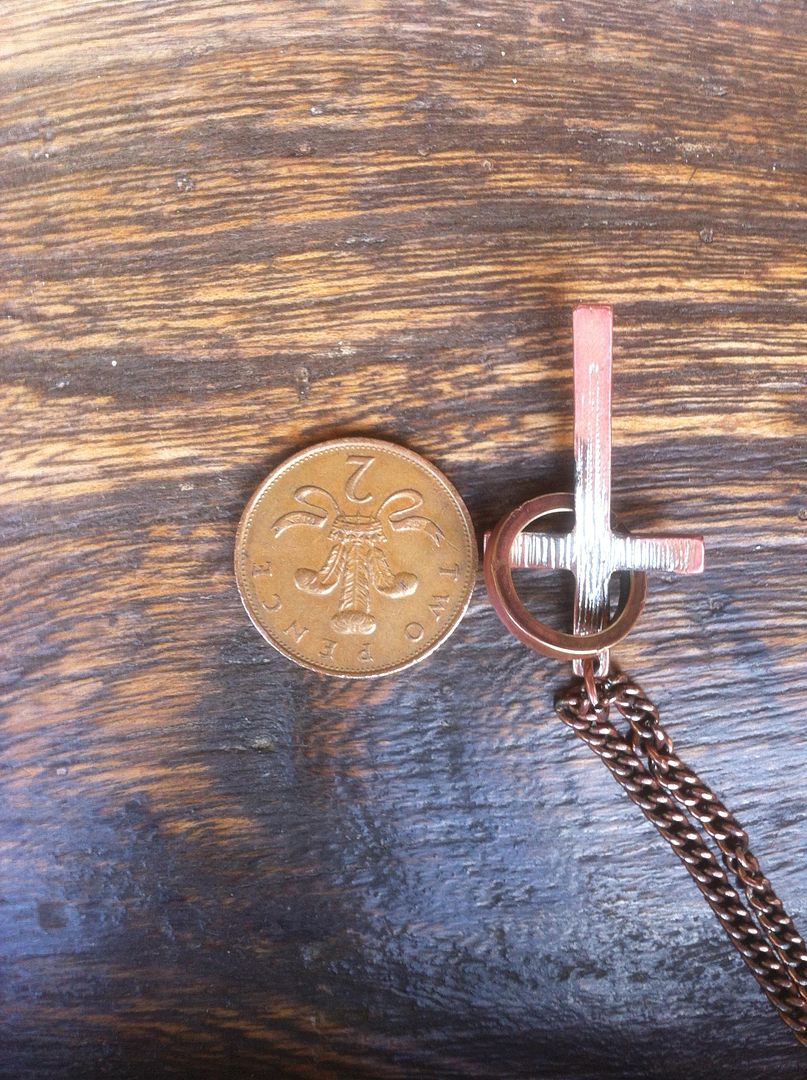
Servicing your watches still.
And currently i the middle of turning this 18ct white gold, 40 diamond bracelet
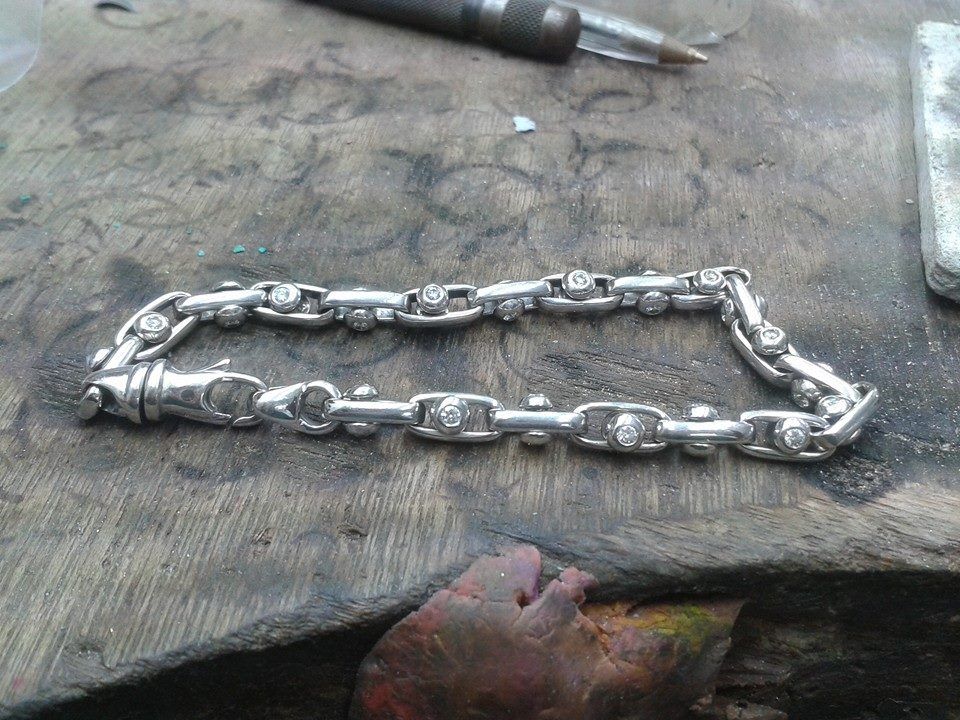
into a 40 diamond 18ct white gold ring:
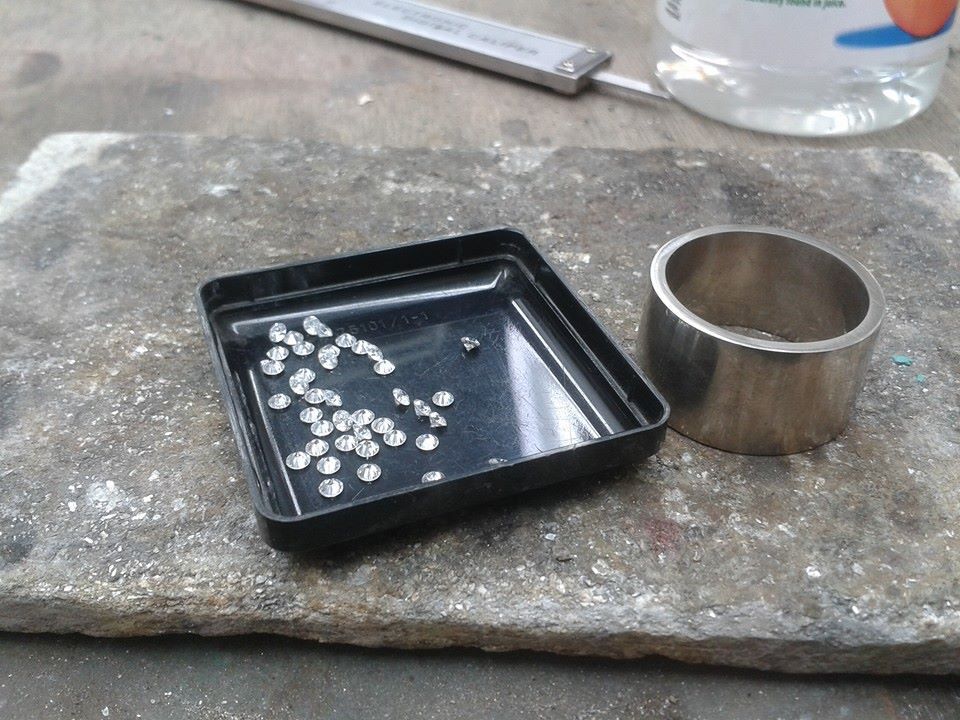
Finished article pics and more projects go follow.
Eddie
Sorry for the delay in updates again. Young child, holiday season, last rounds of chemo etc are all playing havoc with my evenings and spare time.Surgery to get rid of my bowel cancer was on May 15th (went really well), my son was born on May 21st (12 days overdue with wife have emergency delivery under general) and follow on chemo that started in June has left me a bit tired. Nevertheless i've been at work the whole time, making you guys the odd bit here and there.
Made this silver cross for a PHer to replace a base metal one they lost:
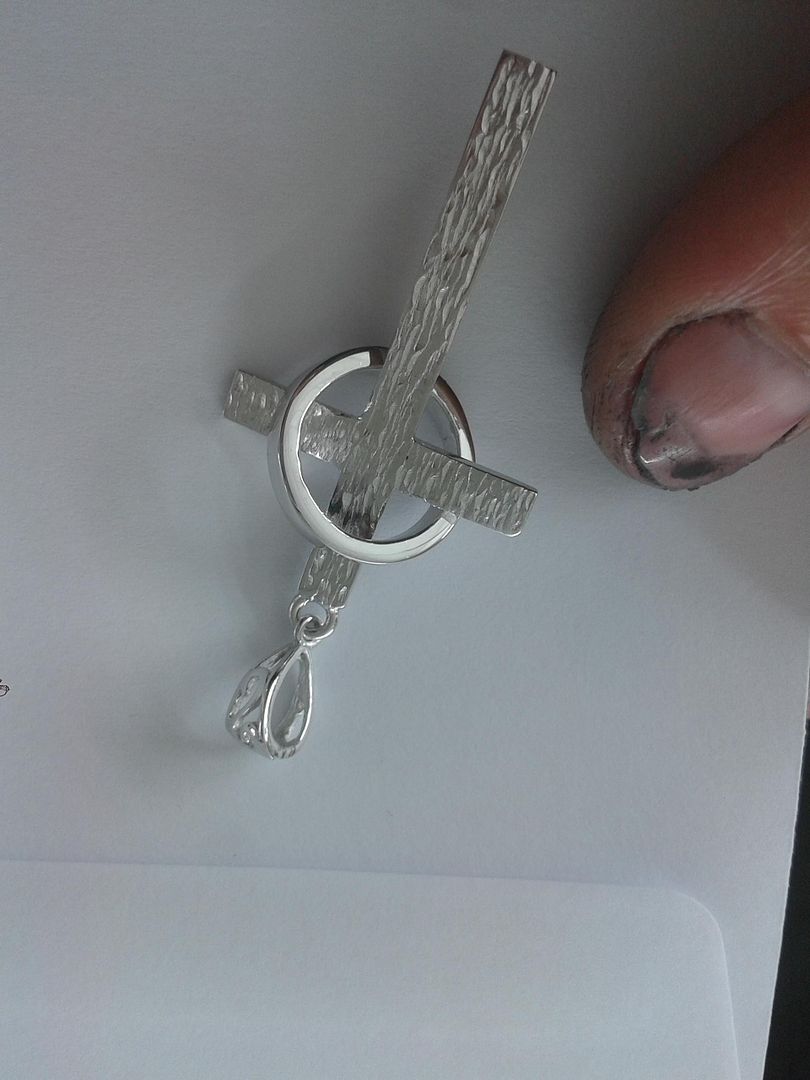
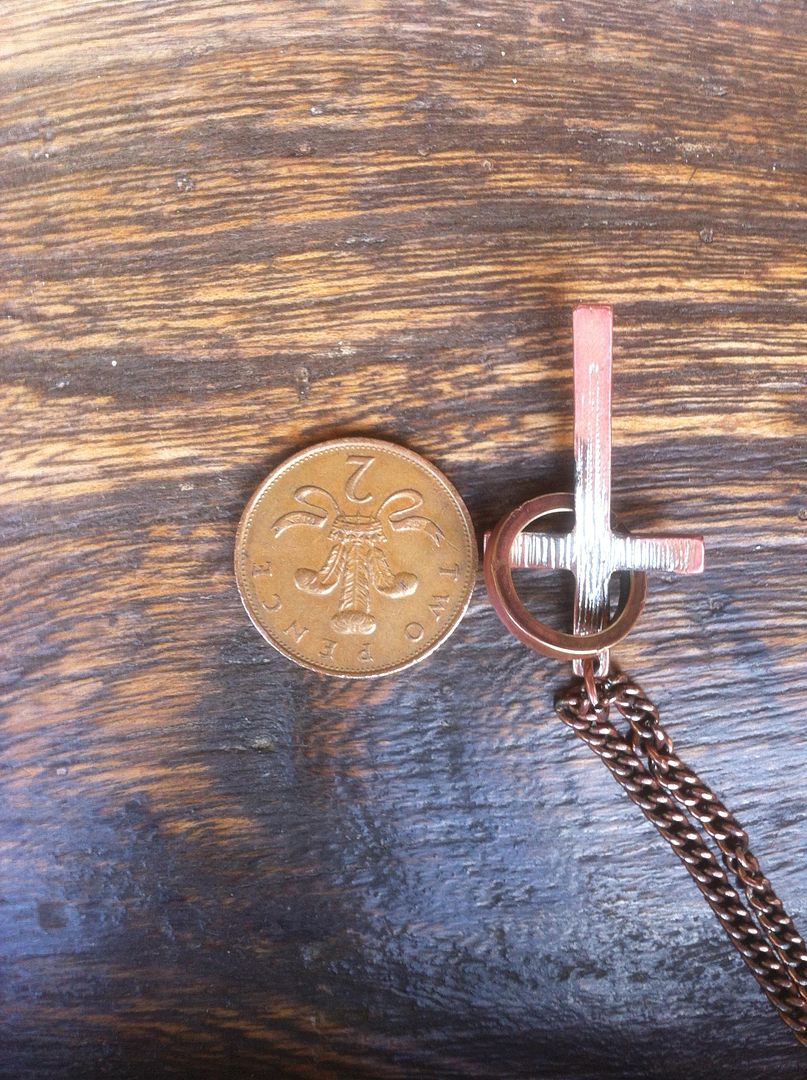
Servicing your watches still.
And currently i the middle of turning this 18ct white gold, 40 diamond bracelet
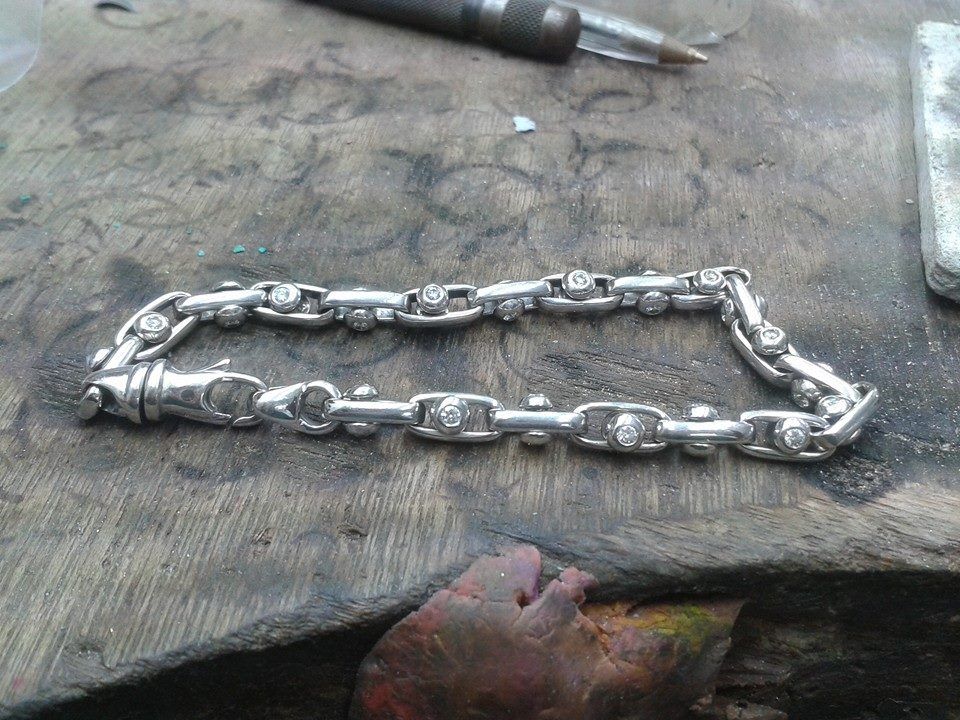
into a 40 diamond 18ct white gold ring:
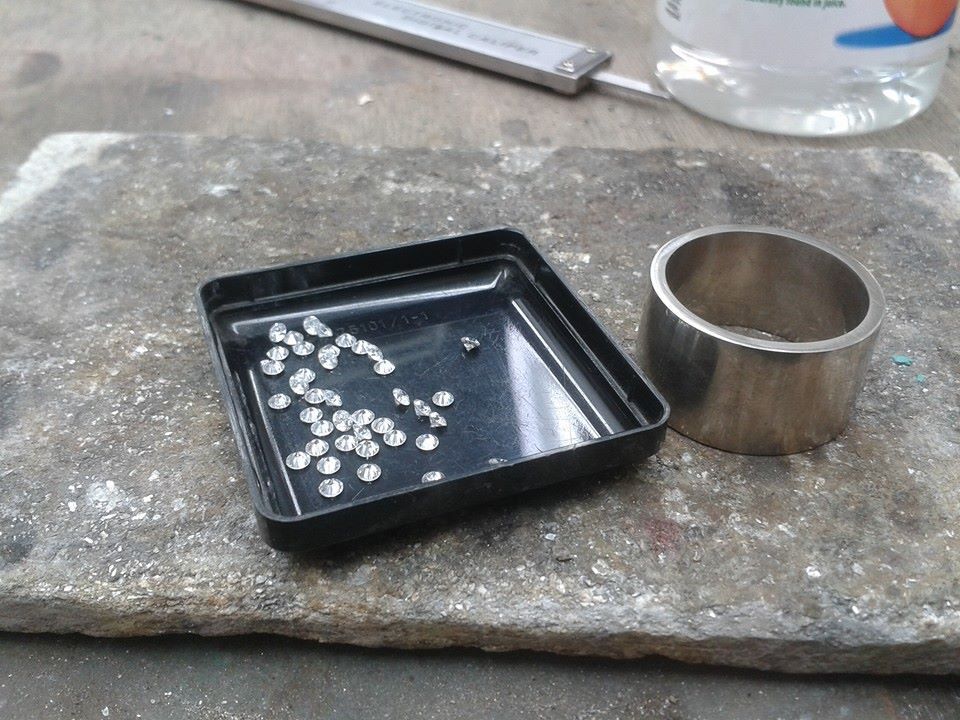
Finished article pics and more projects go follow.
Eddie
Here is the finished article that i made from the white gold and diamond bracelet:
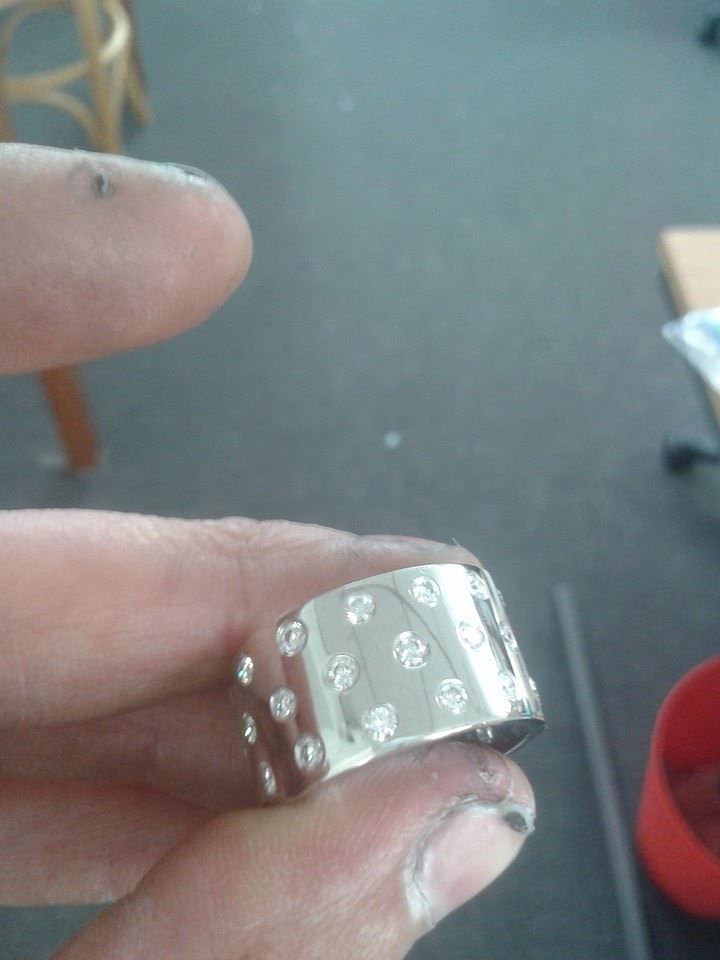
With the weather being so damned horrid today i went in to work early this morning to crack a big job that needs doing before the end of the month.
Take 1 x knackerd 8.6ct diamond and 18ct white gold tennis bracelet from Bonhams auction:

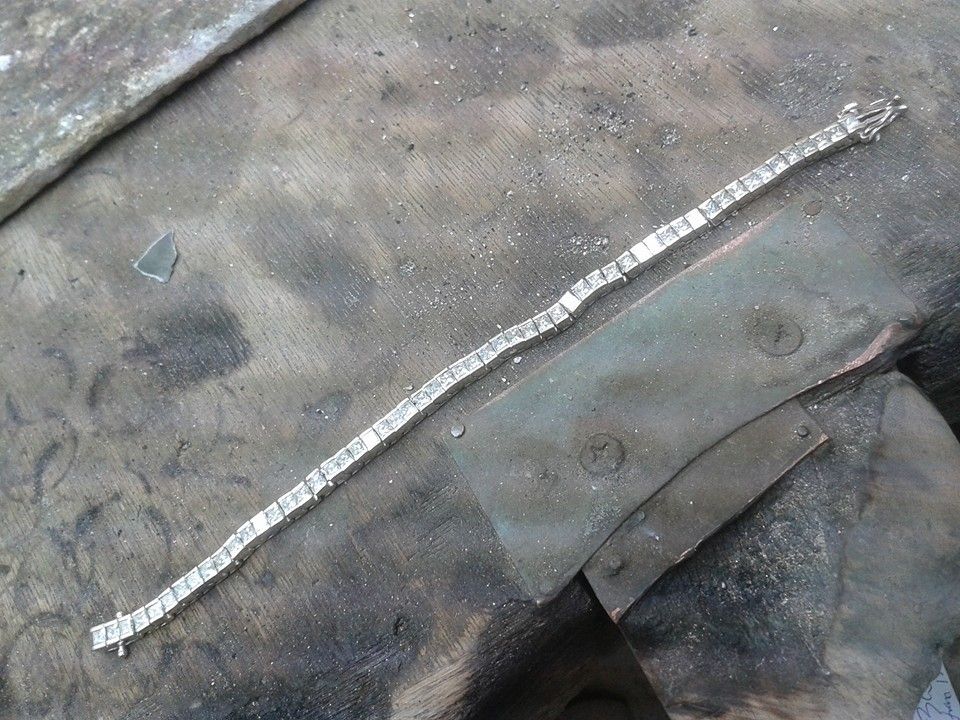
Spend 3 hours with a fine drill disassembling it: In that 3 hours i broke 7 x drill bits, drilled 2 fingers and strained my eyes to the point where i was almost blind.
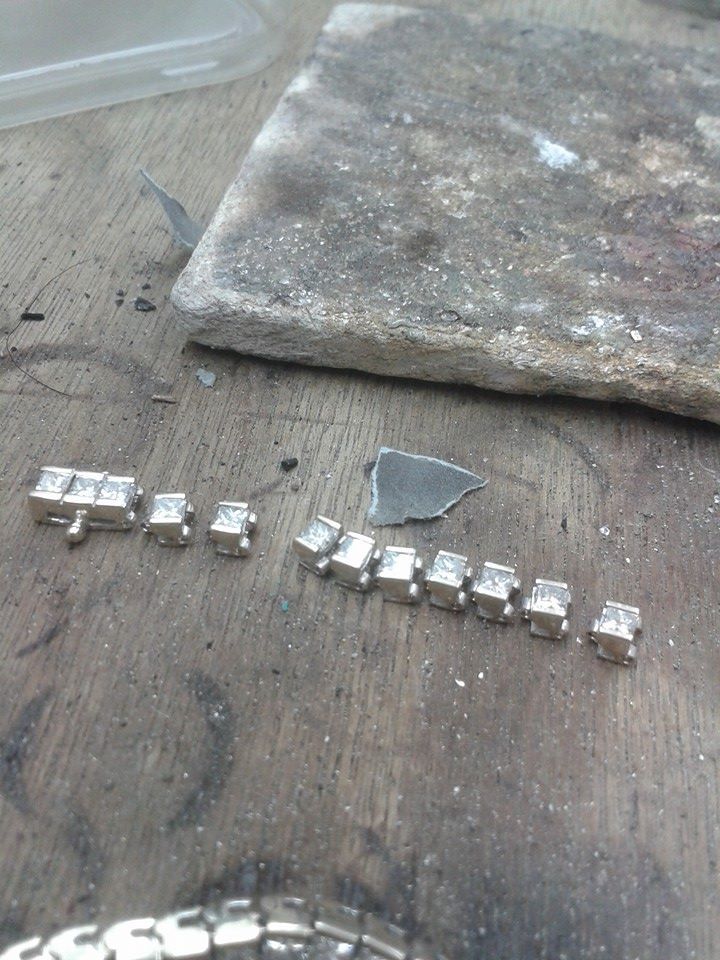
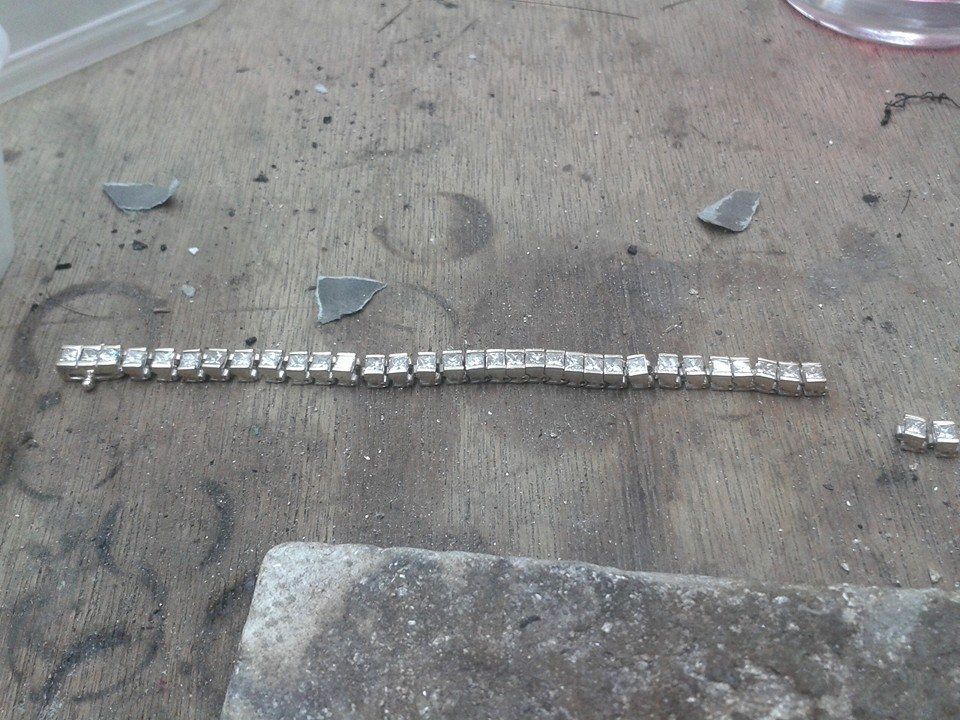
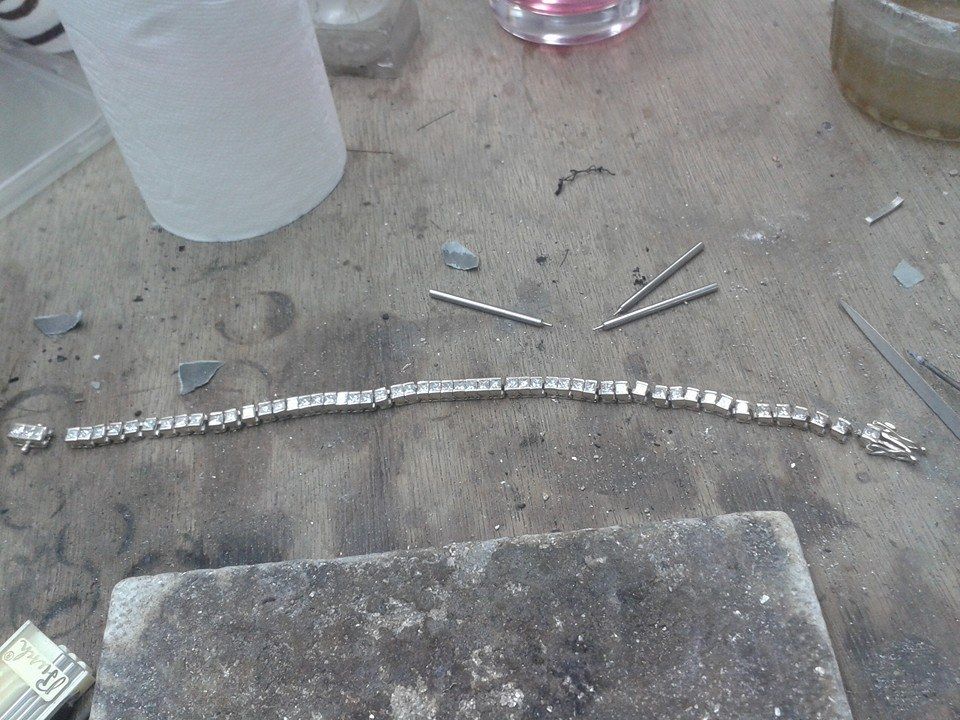
You can see how worn out the links are: There are 53 links!
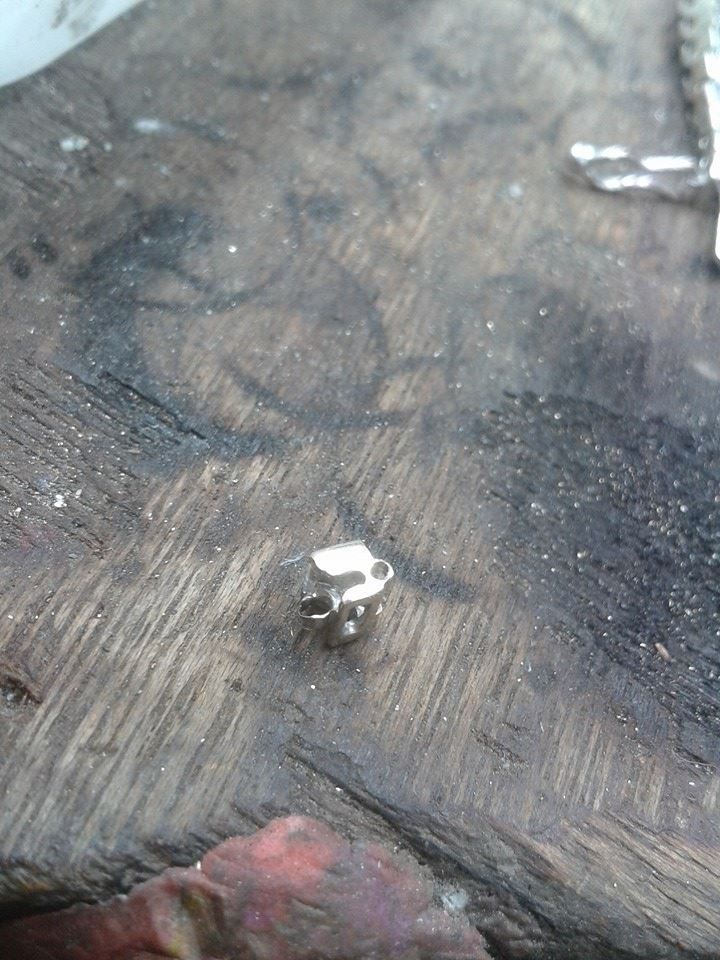
Take some (a lot really) 18ct wire and draw down to 0.7mm to use as hinge pins:
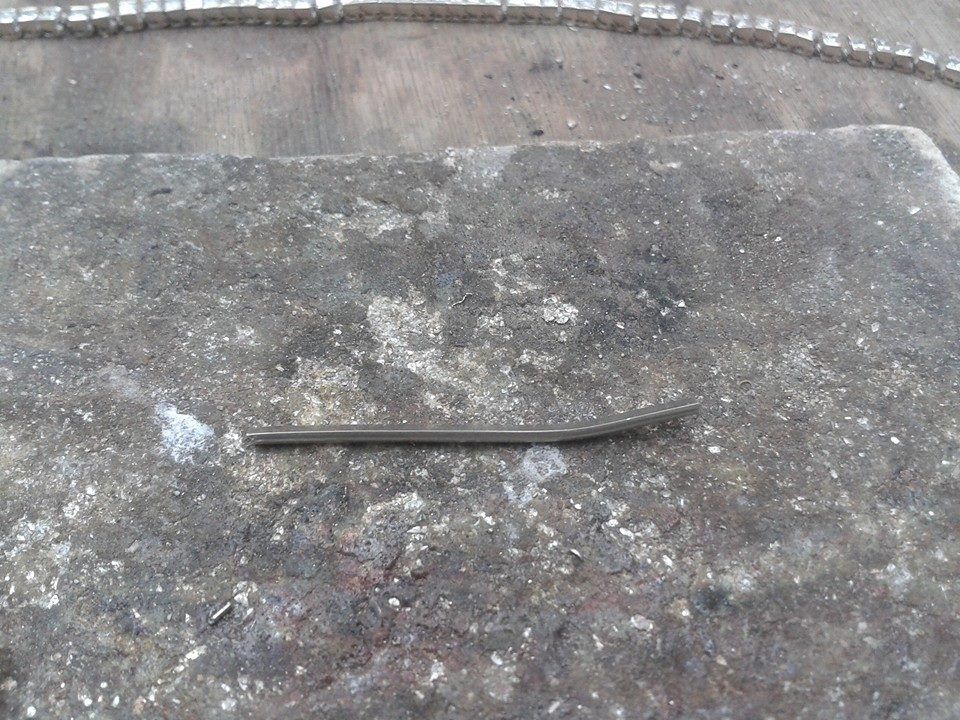
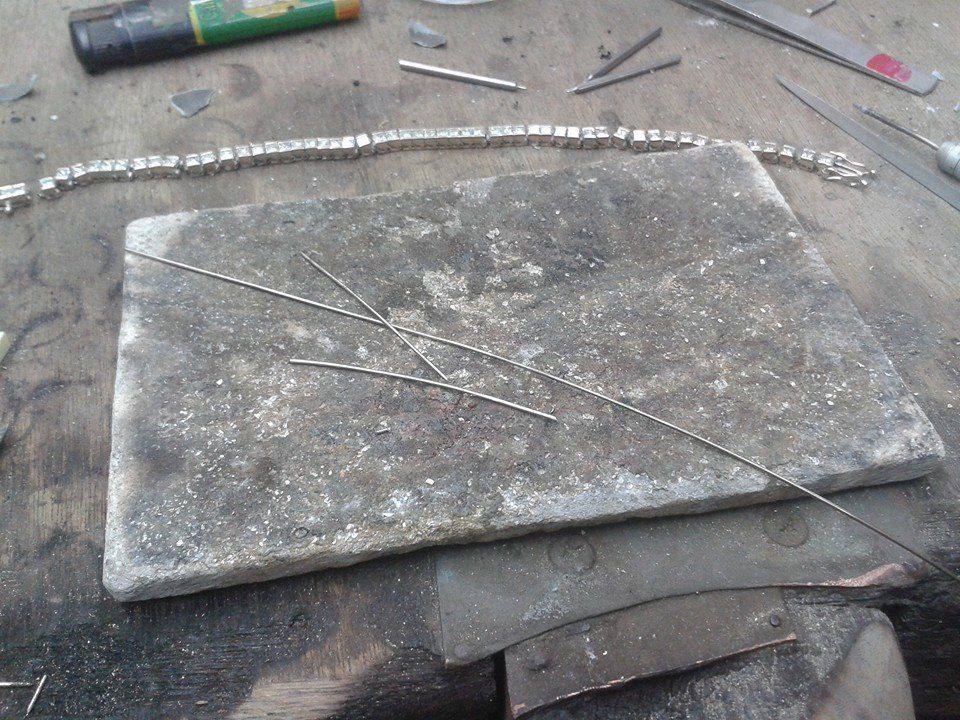
Then spend an eternity remaking the tubes for the pins to go through (apologies for crappy phone pic). 159 tubes all in!!!! My eyes need a service by now!
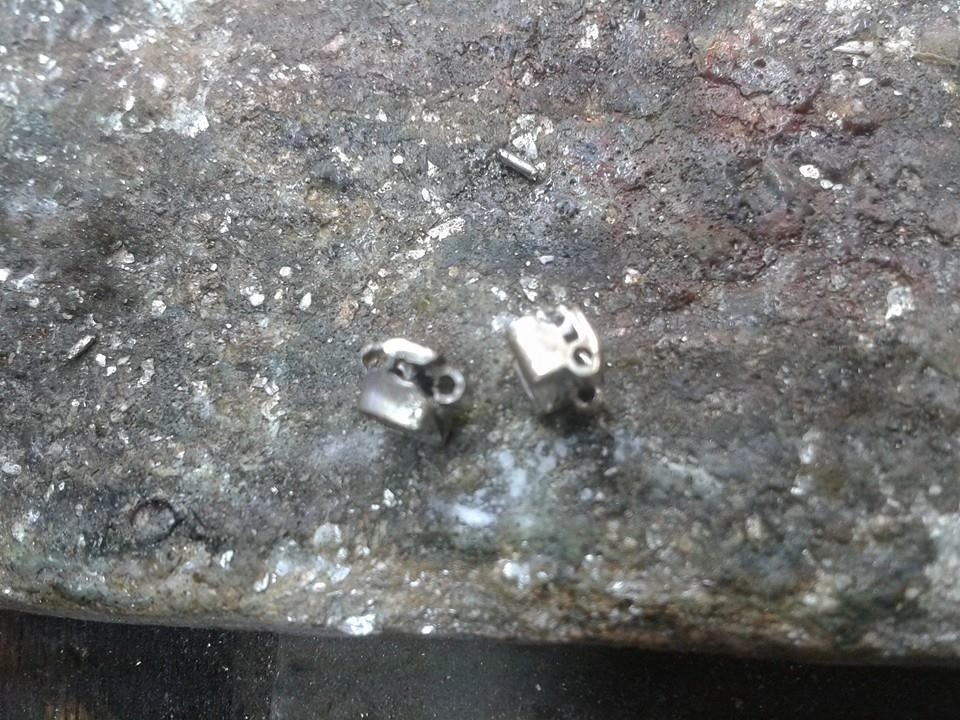
Once the tubes are all rebuilt, push wire through each and trim the excess:
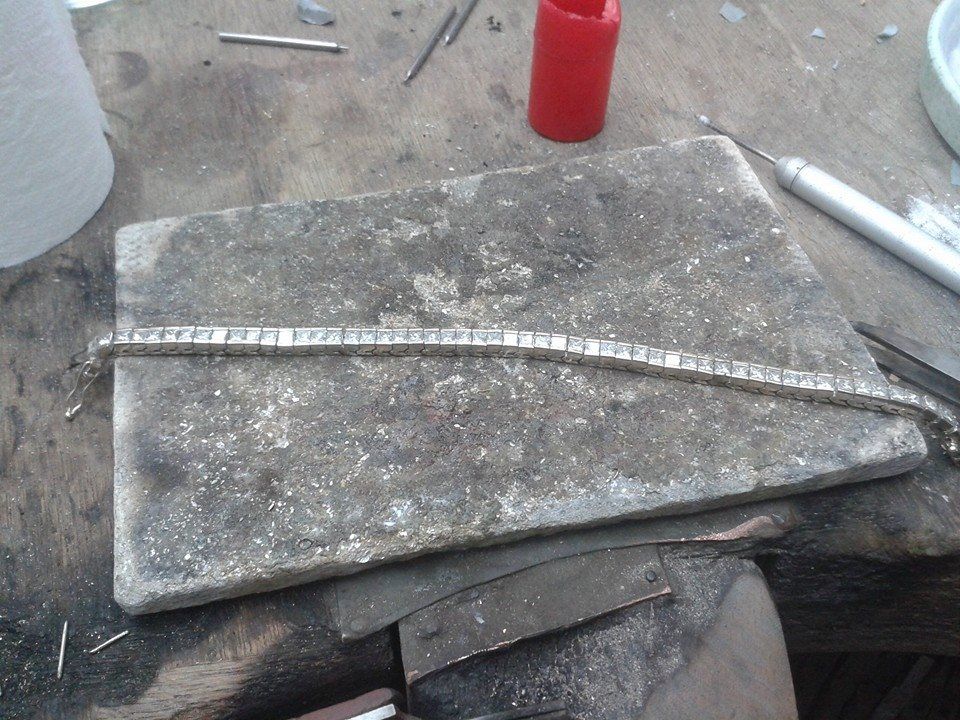
Each pin is then soldered at each end. Thats 106 solders! And then deep cleaned before being tidied up and adjusted ready for polishing:
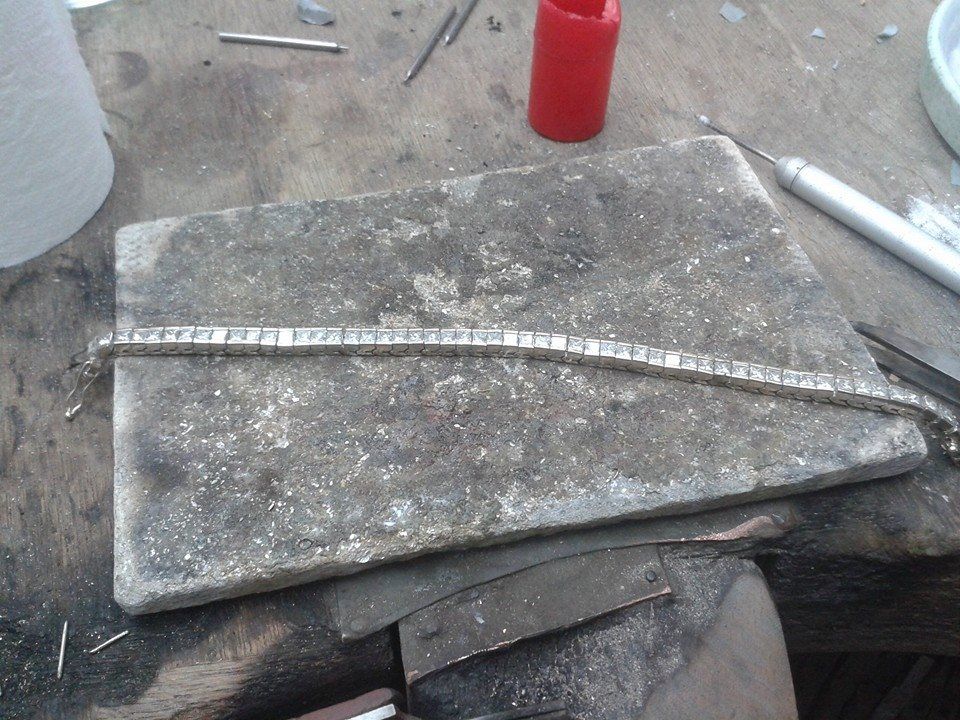
Ready for a polish and Rhodium plating:
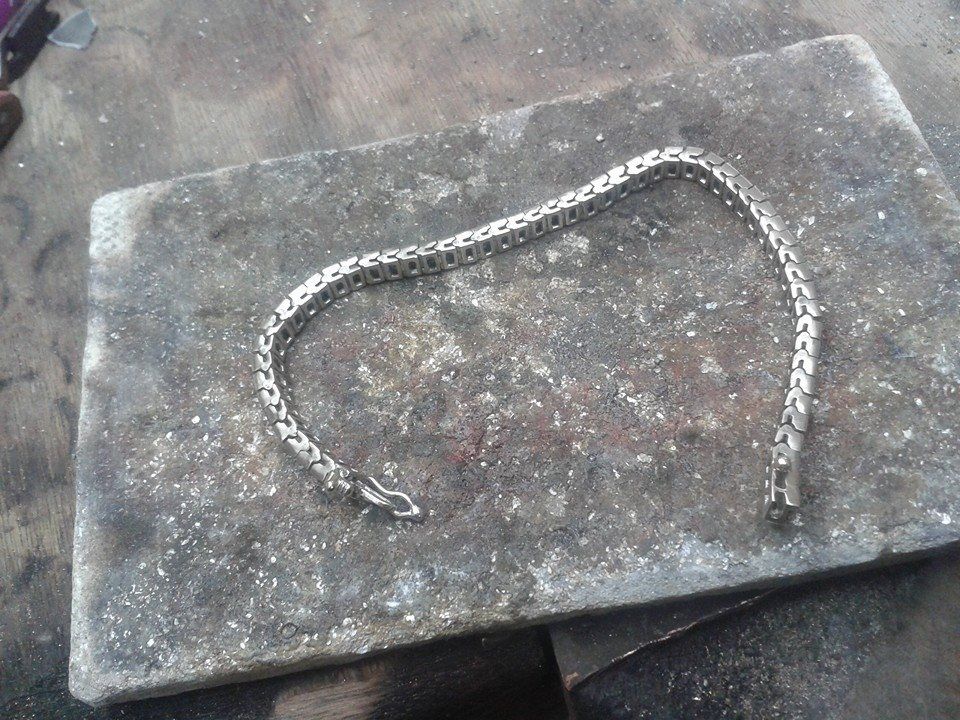
8 1/2 hours after i started it's all done. Home time!
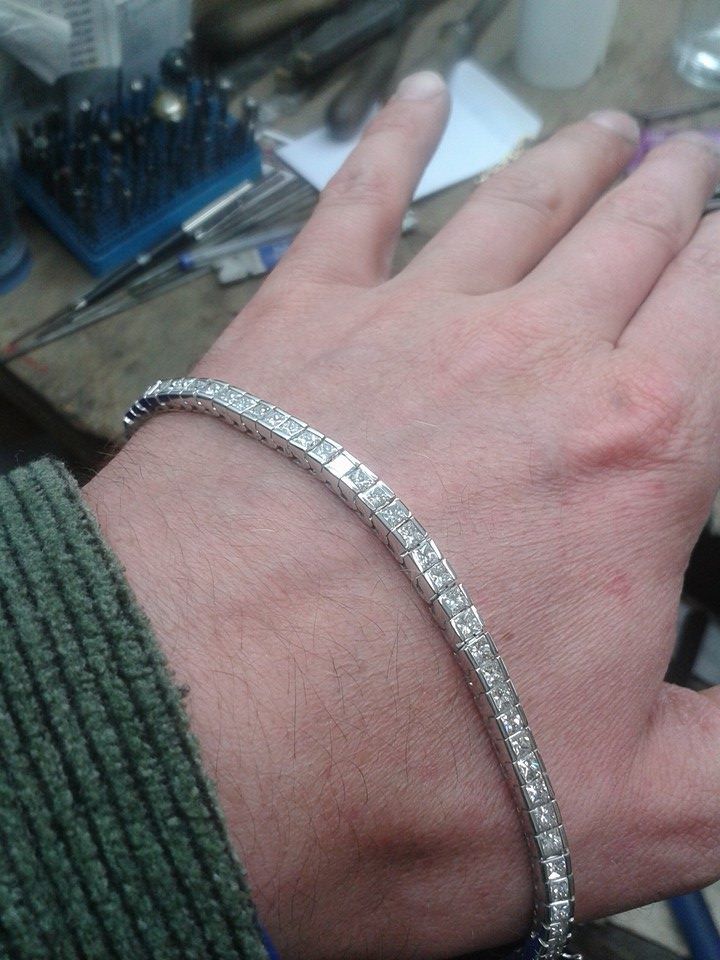
Chemo finishes for good on Sunday so hopefully i can start to get some more stuff up over the coming months.
Eddie
Not so much a 'build' thread today, but here are a couple of items i finished today.
1.0ct diamond, 10 stone 1/2 eternity for a lucky PHer.
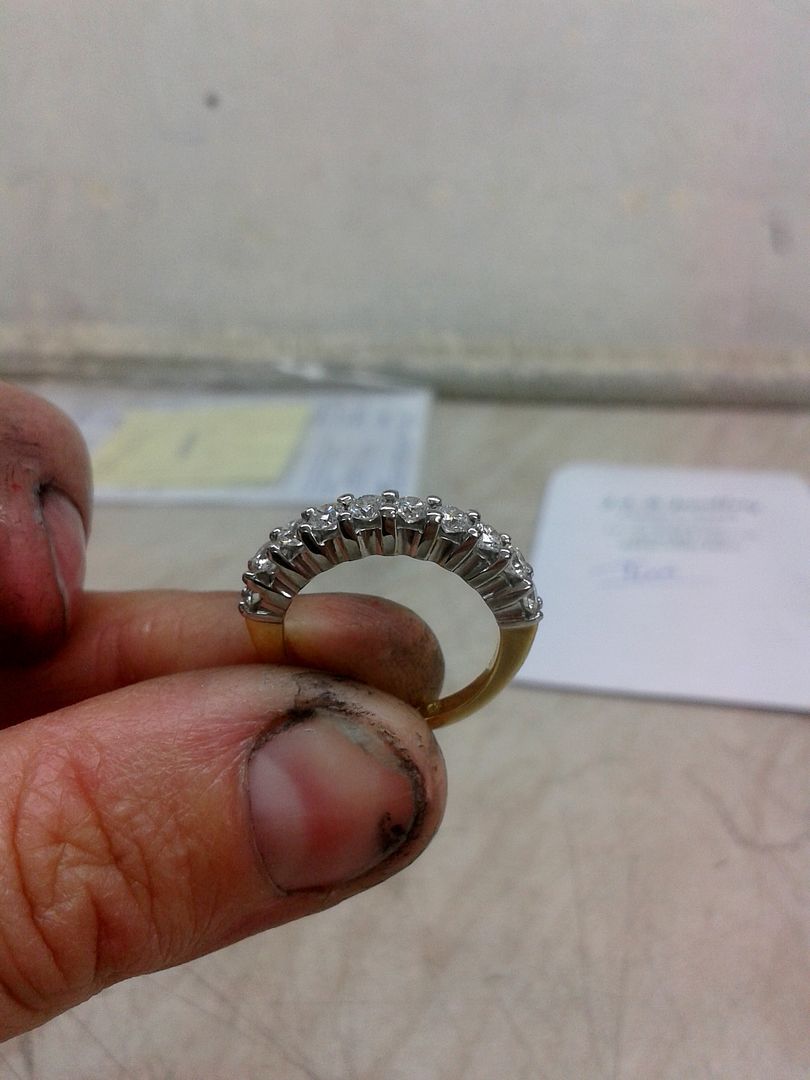
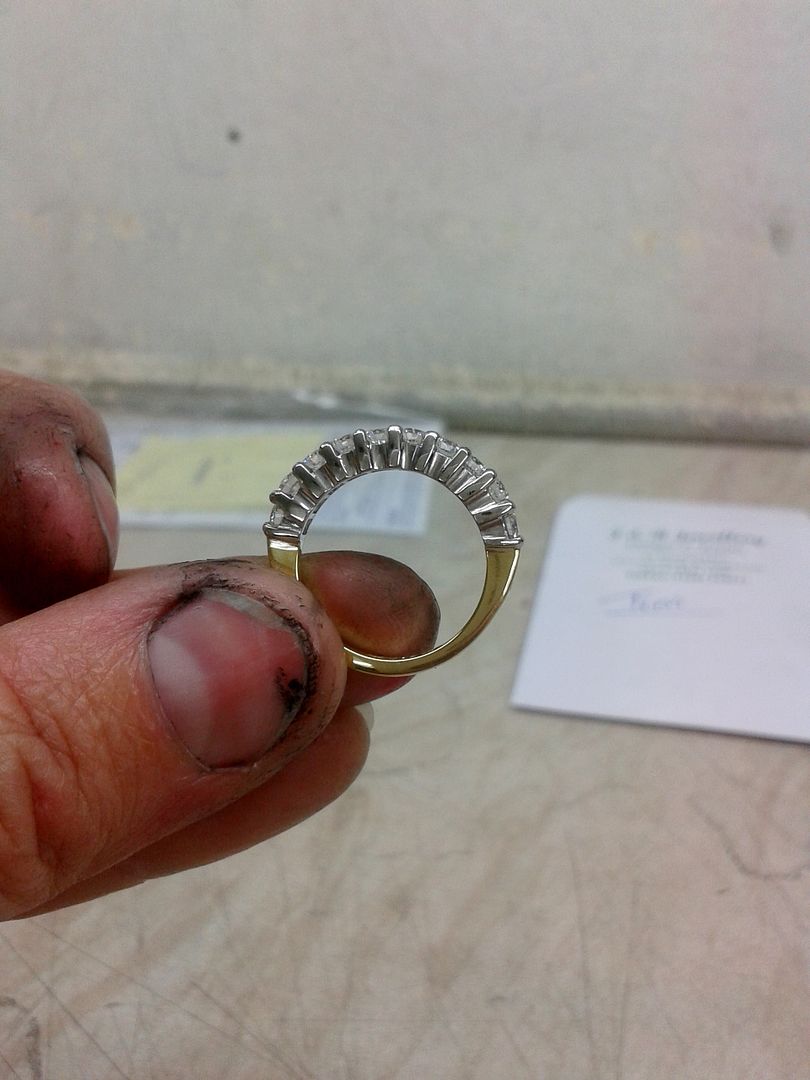
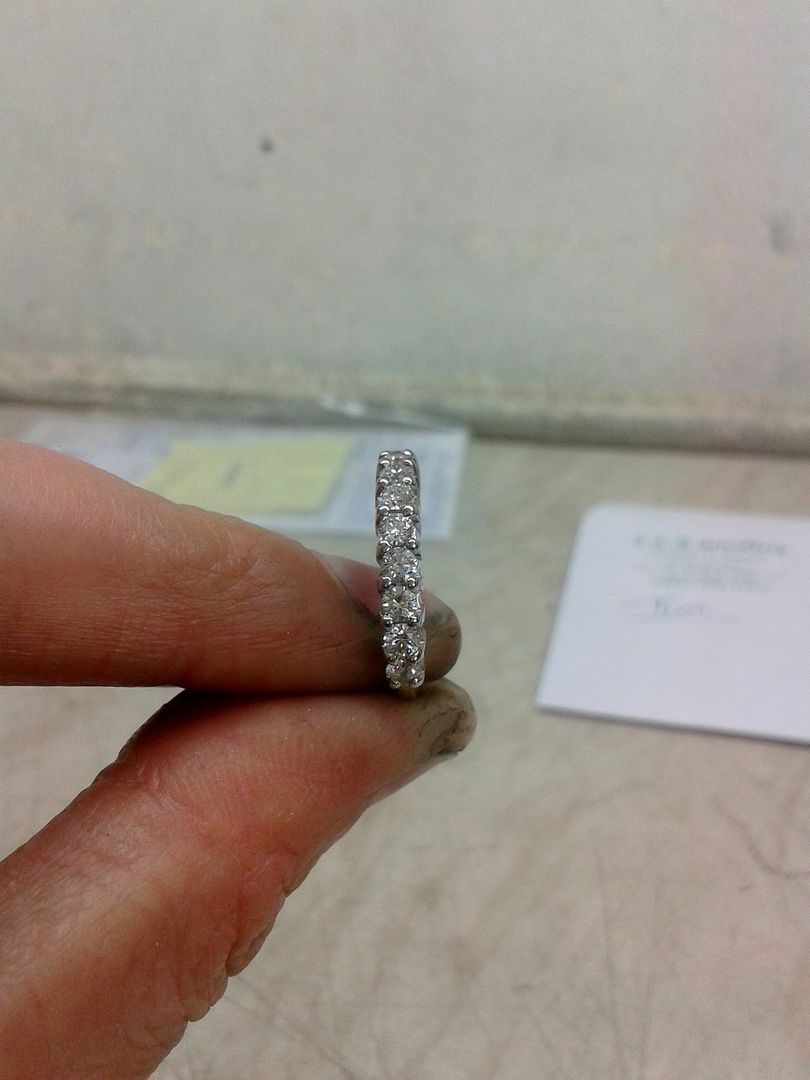
And a tiger / cat ring that i've made for my Ultimate Fighting Championship mate, to match his Bulldog, Wutang |Clan and Yankee Candle rings:
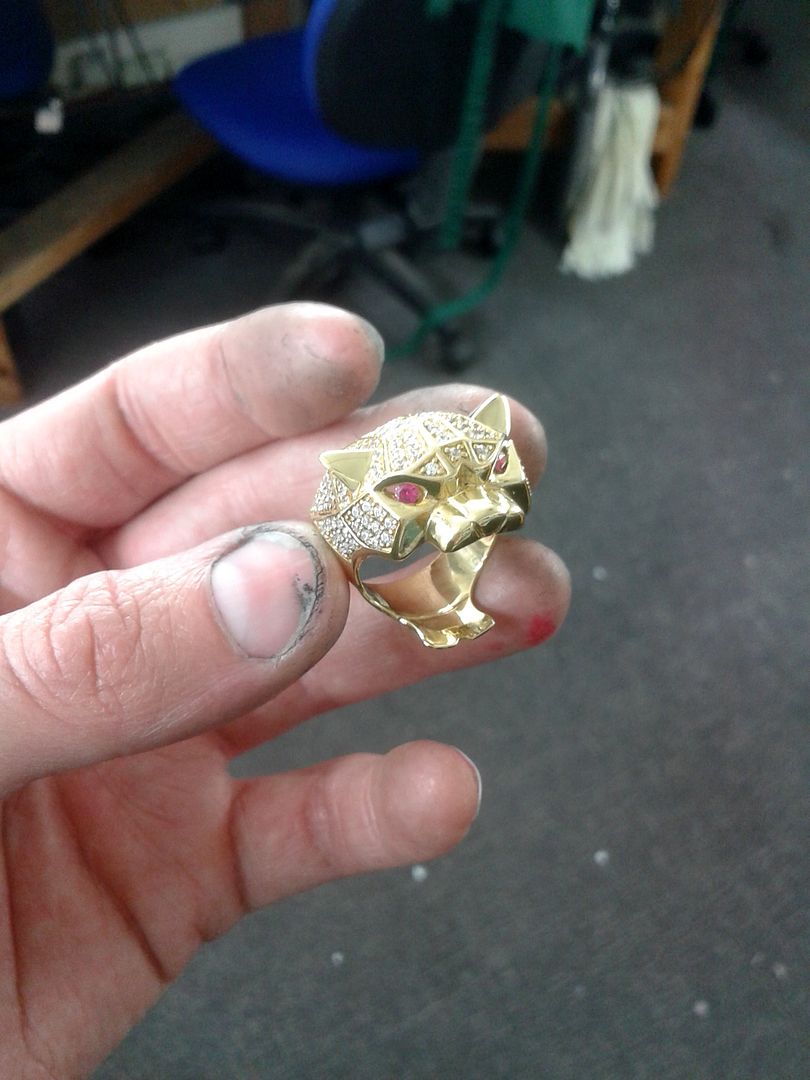
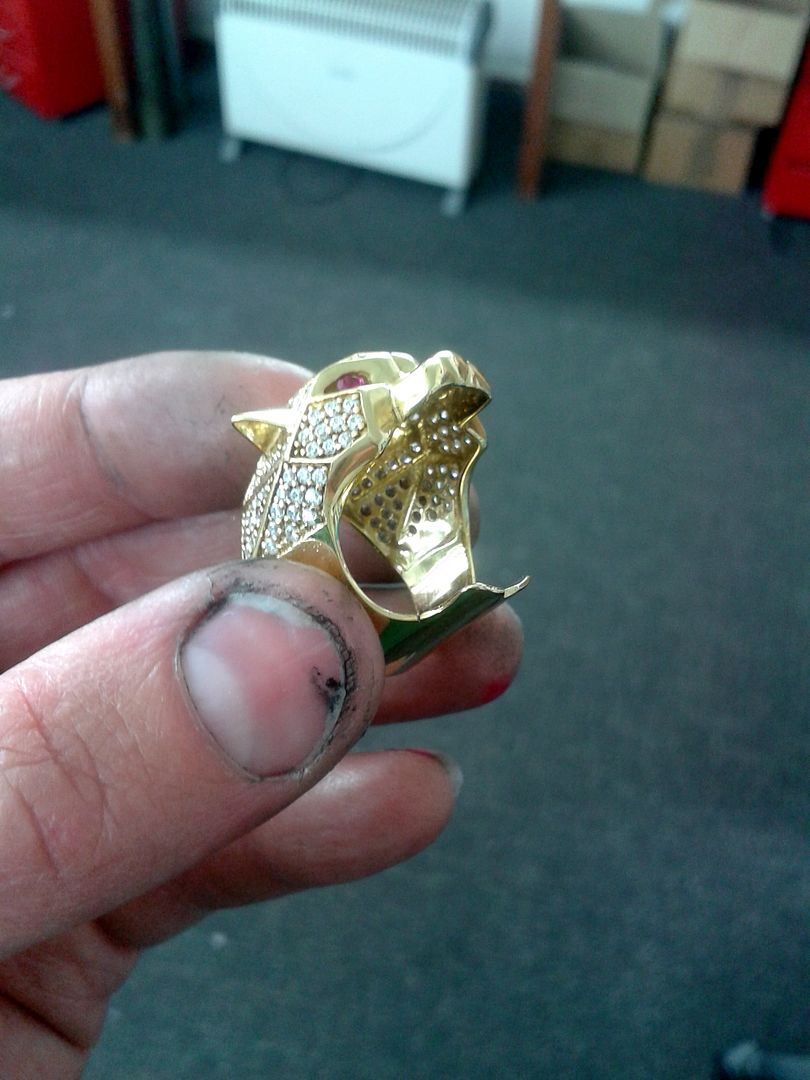
I will do another proper build thread some time soon, just need to figure out what to do.
Eddie
1.0ct diamond, 10 stone 1/2 eternity for a lucky PHer.
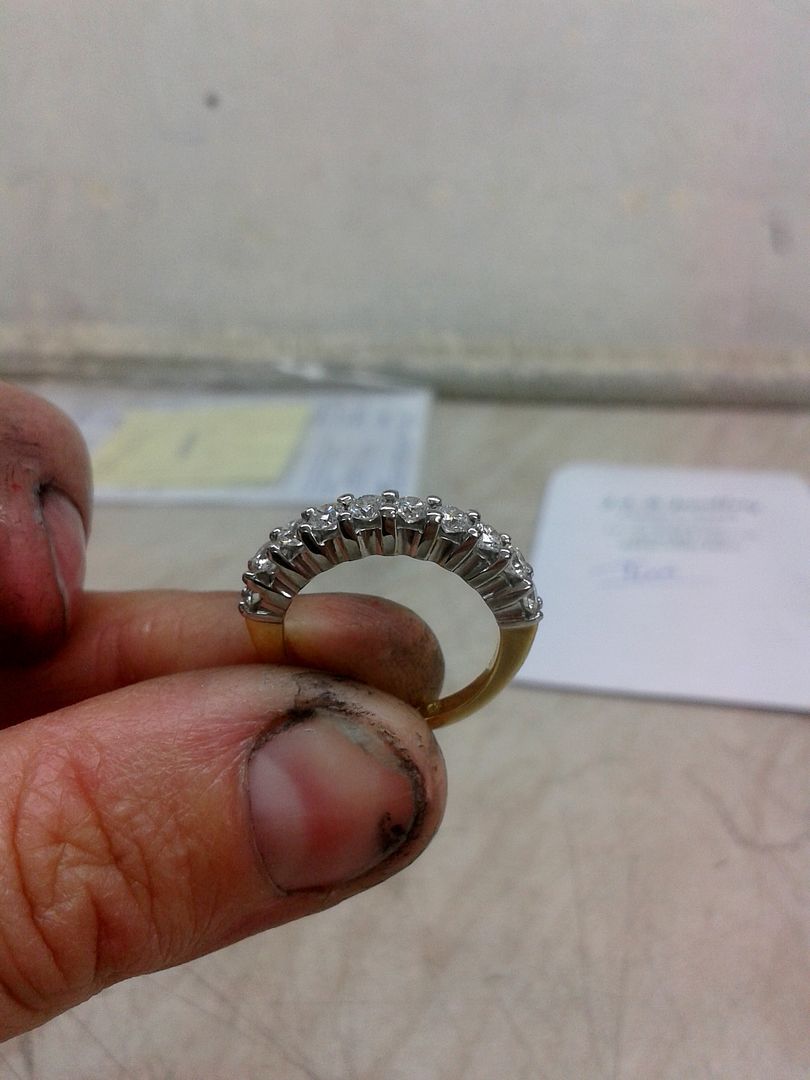
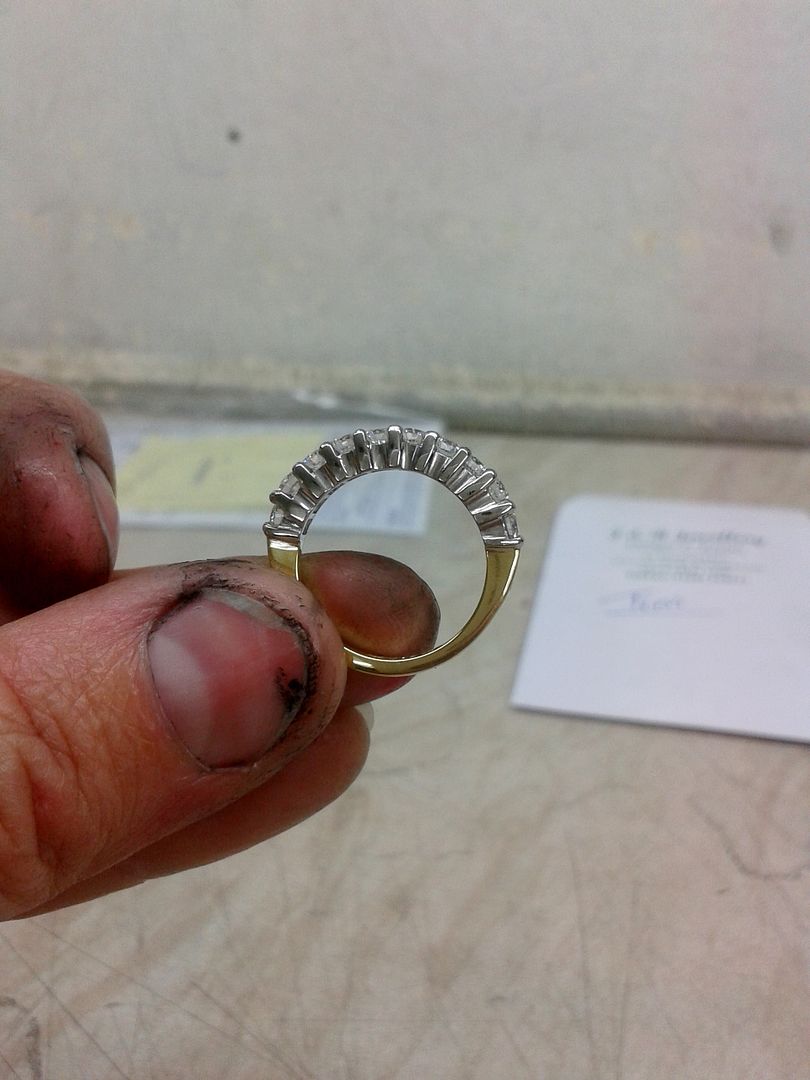
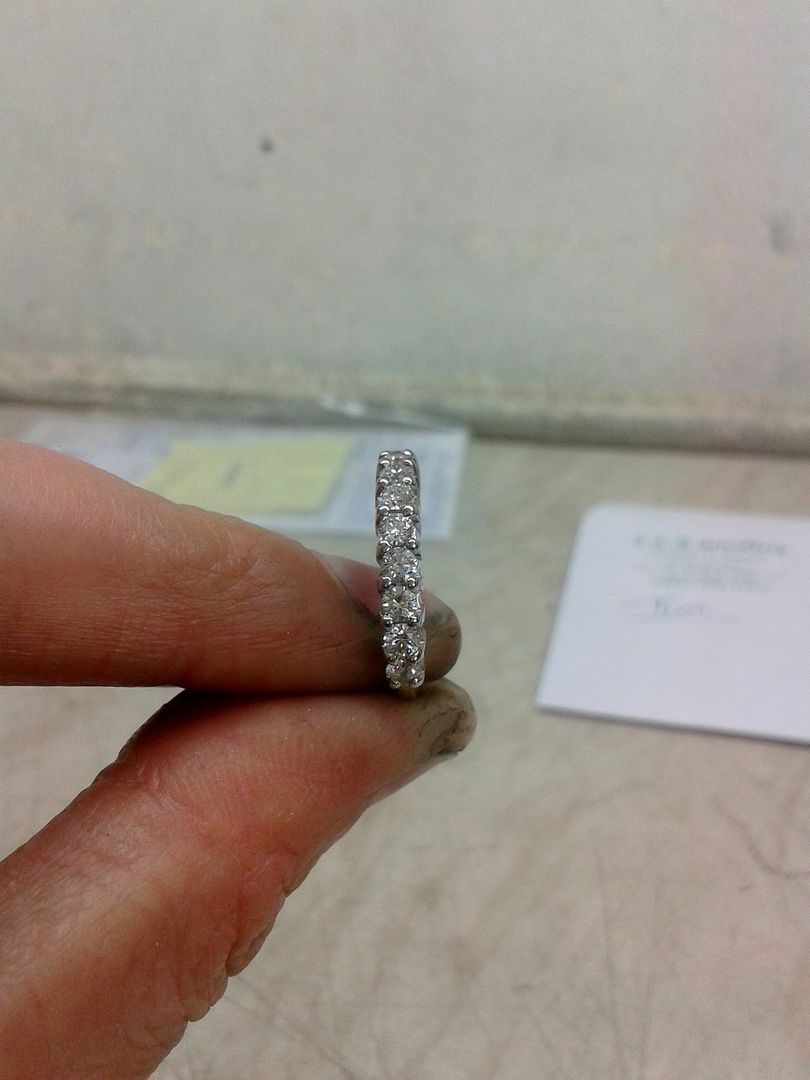
And a tiger / cat ring that i've made for my Ultimate Fighting Championship mate, to match his Bulldog, Wutang |Clan and Yankee Candle rings:
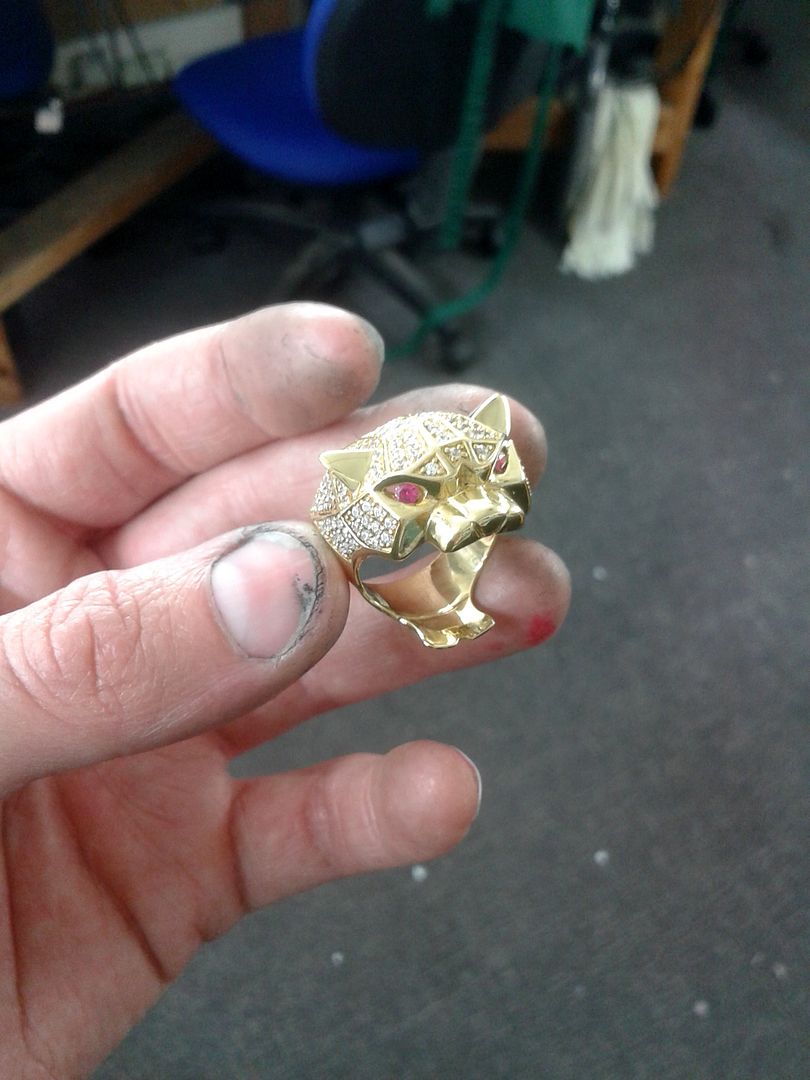
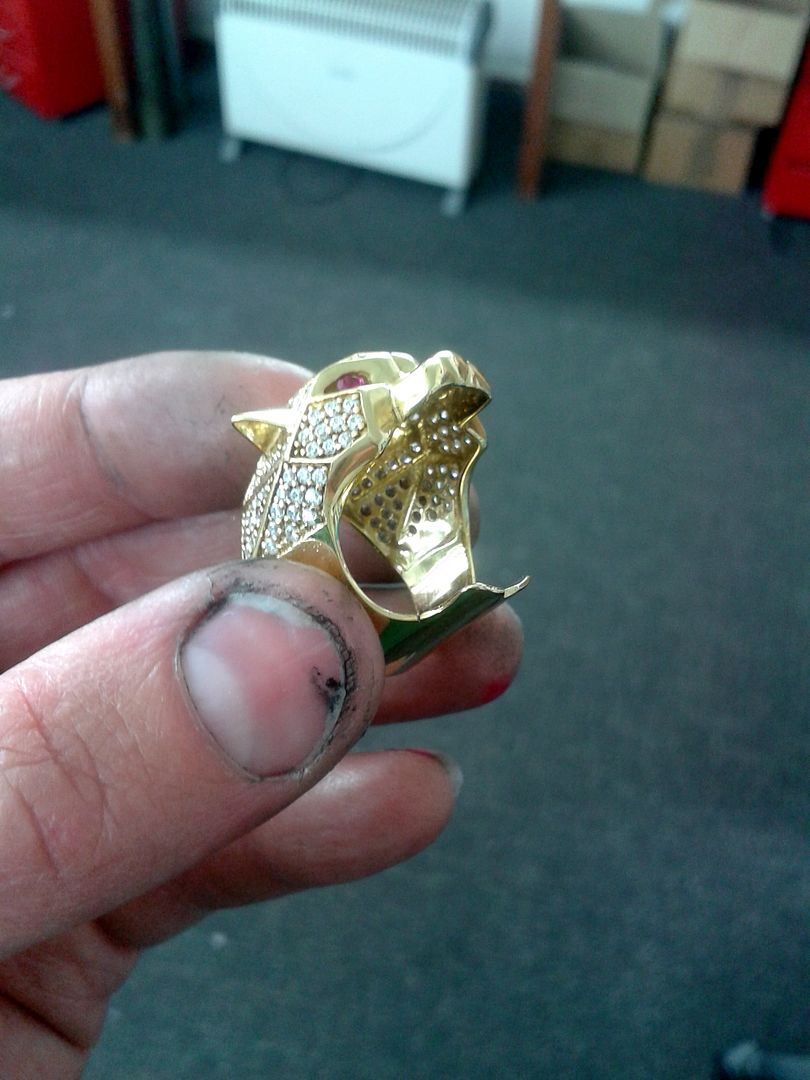
I will do another proper build thread some time soon, just need to figure out what to do.
Eddie
Todays build:
A bar of 18ct white gold and a sky blue topaz.
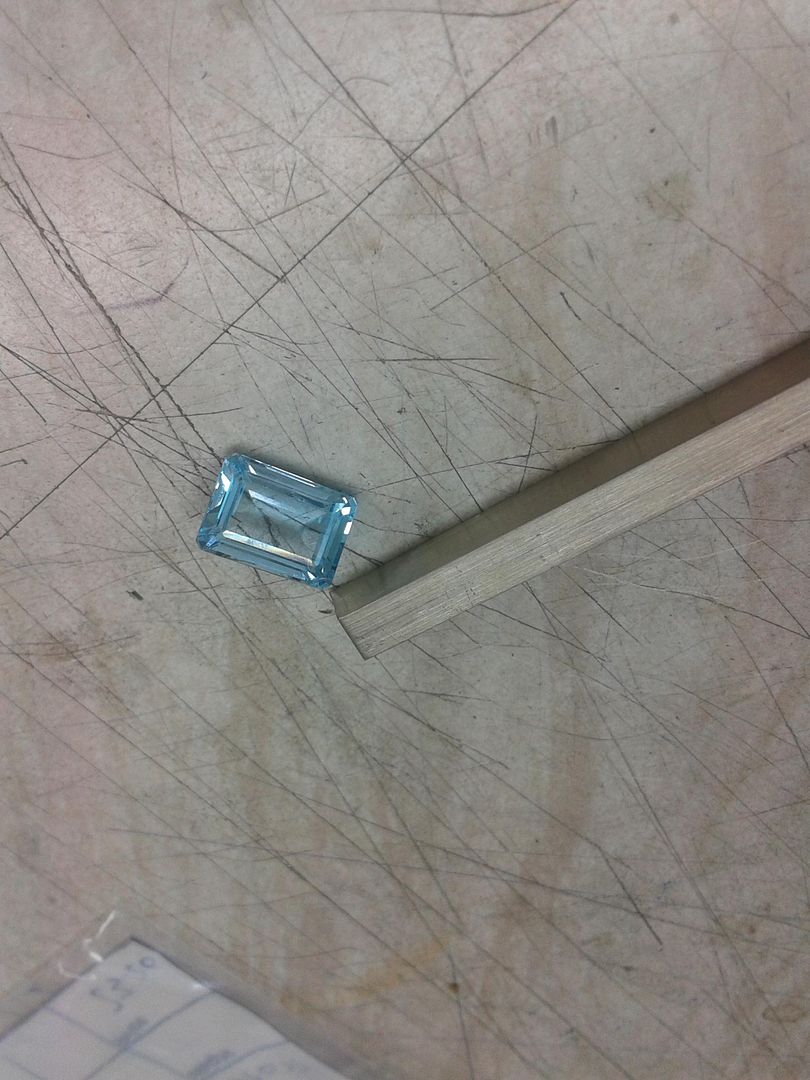
Made a setting:
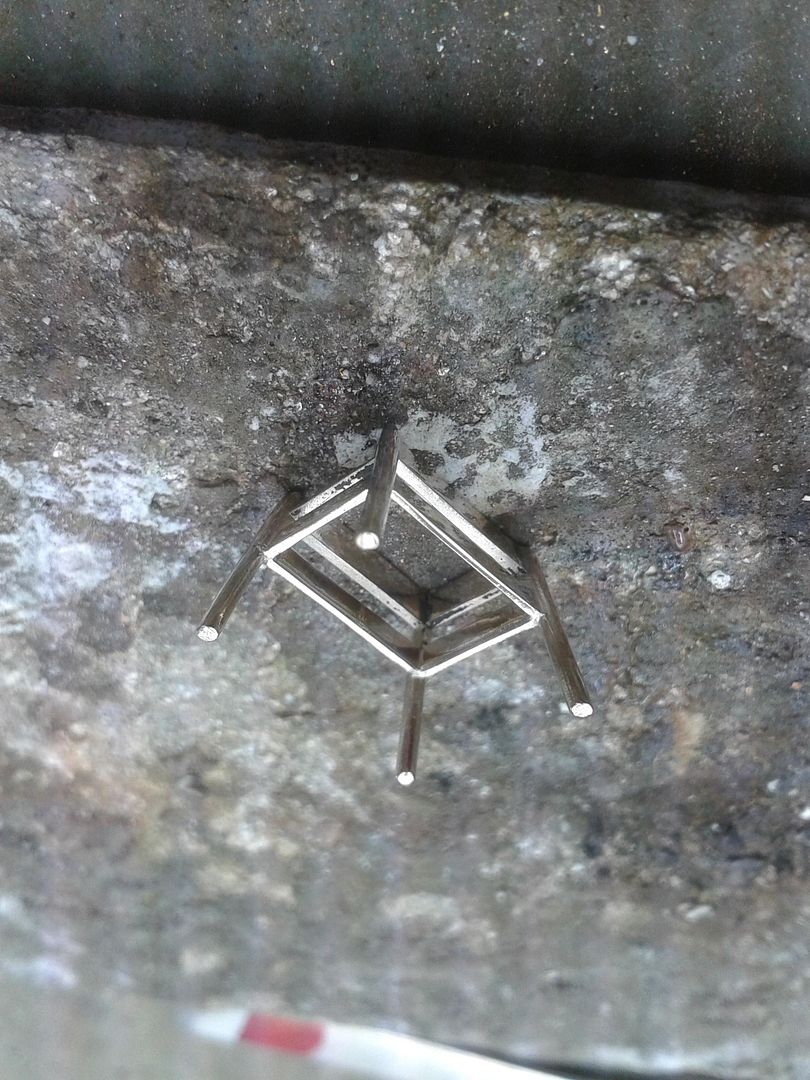
Then a split shank (in 2 peices because it's easier to build that way).
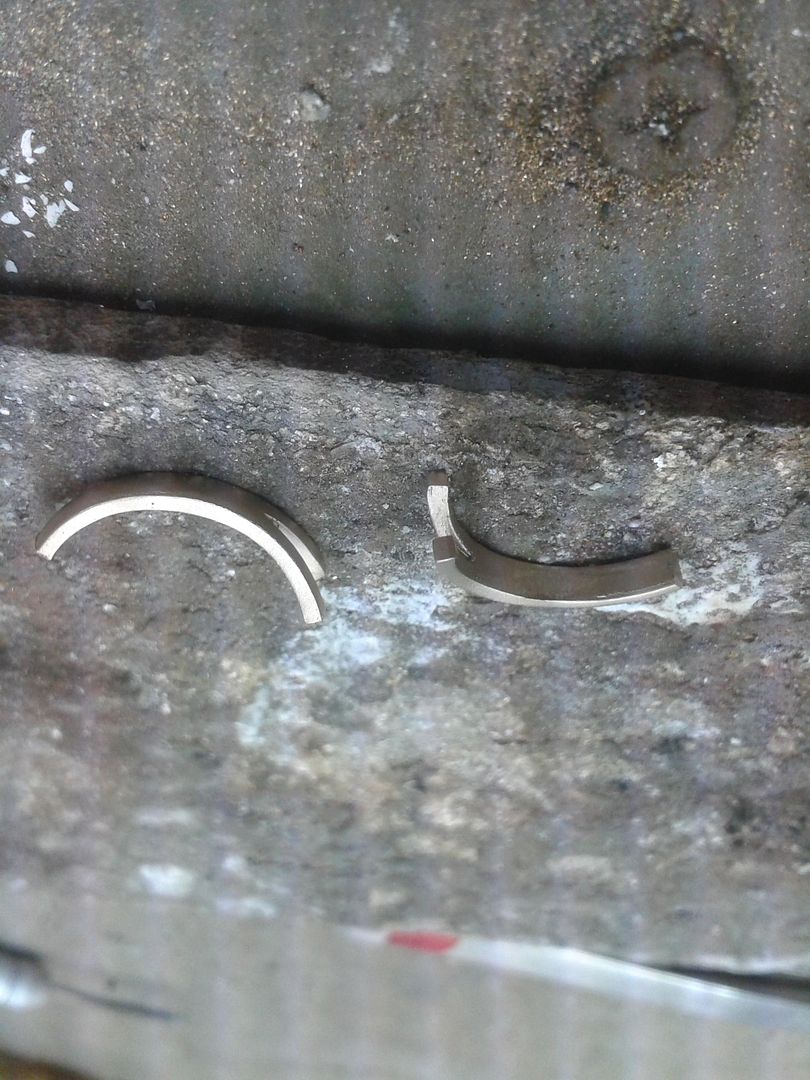
The two parts:
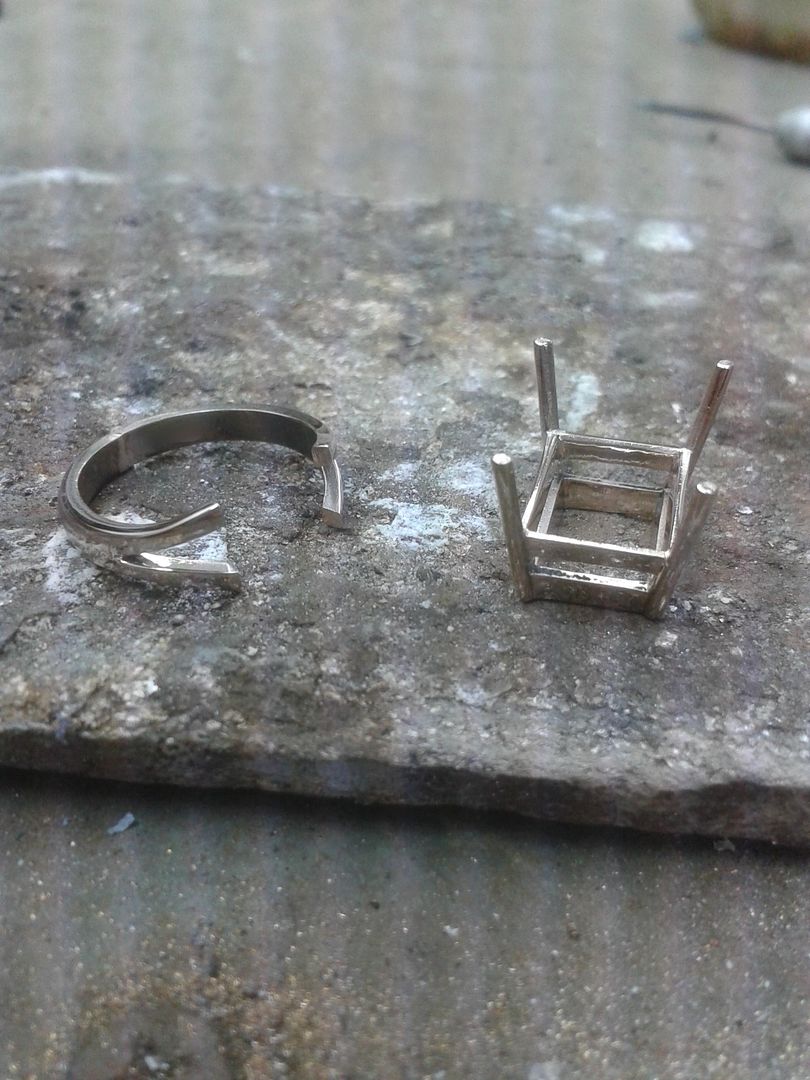
Soldered together:
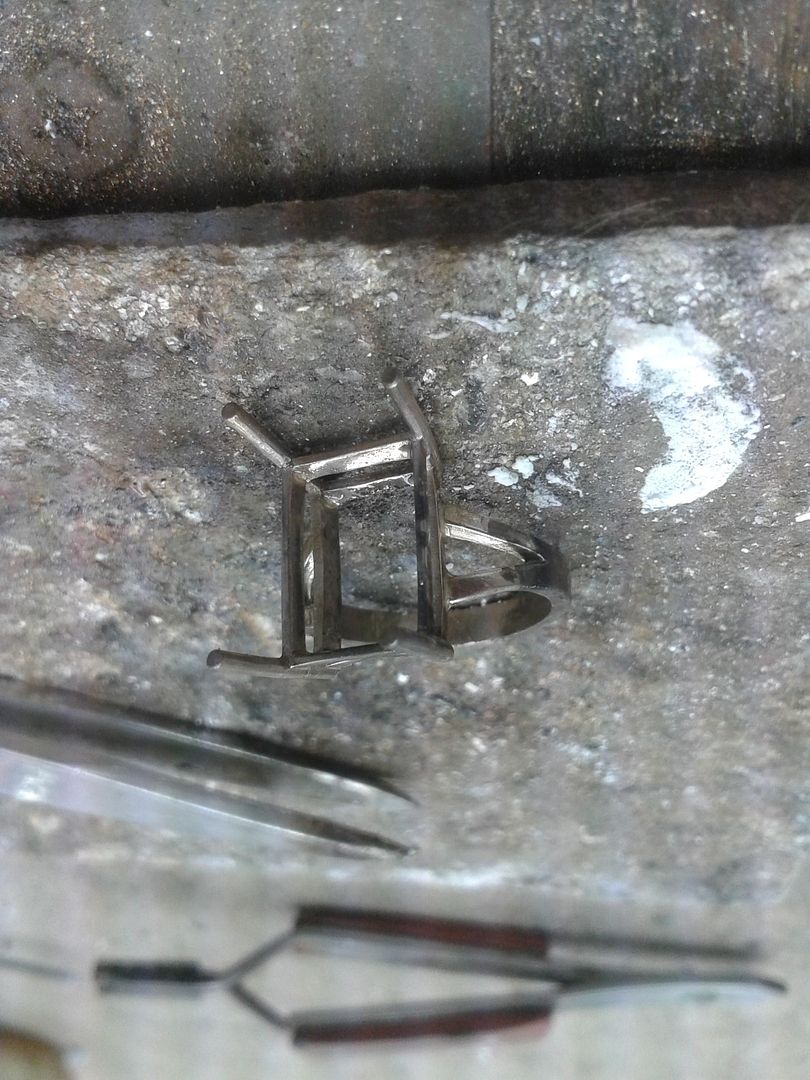
With the stone:
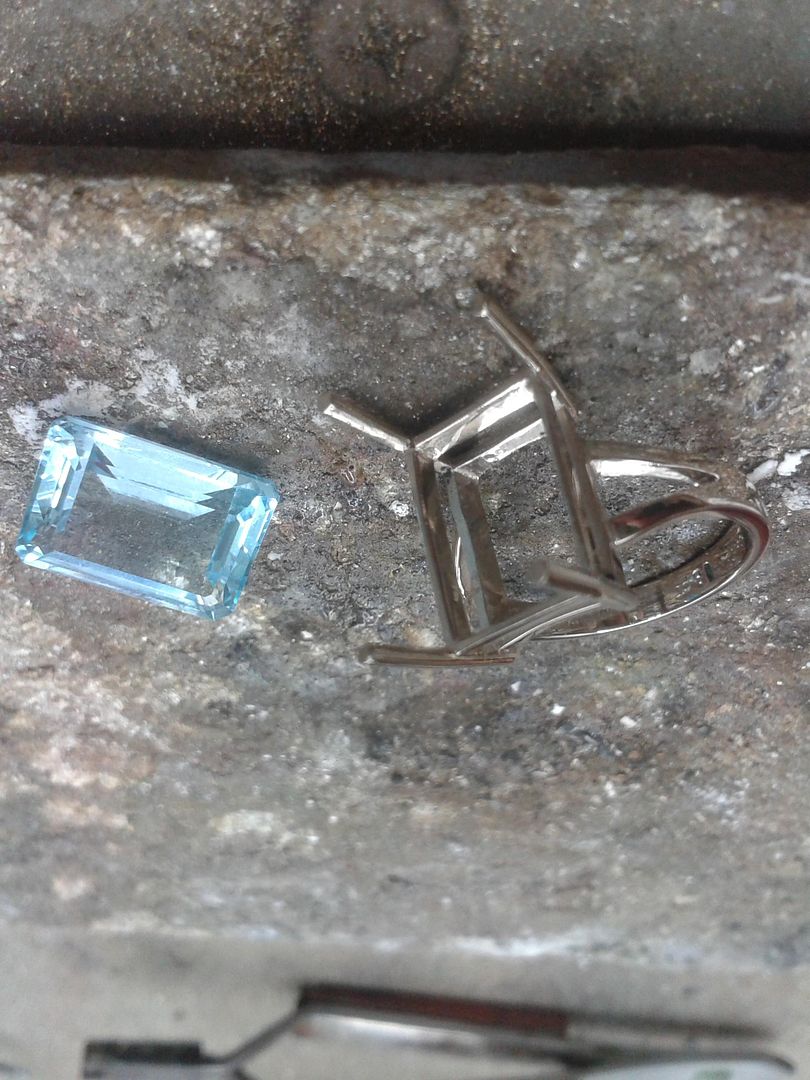
Stone set and ready for polishing and rhodium plating.
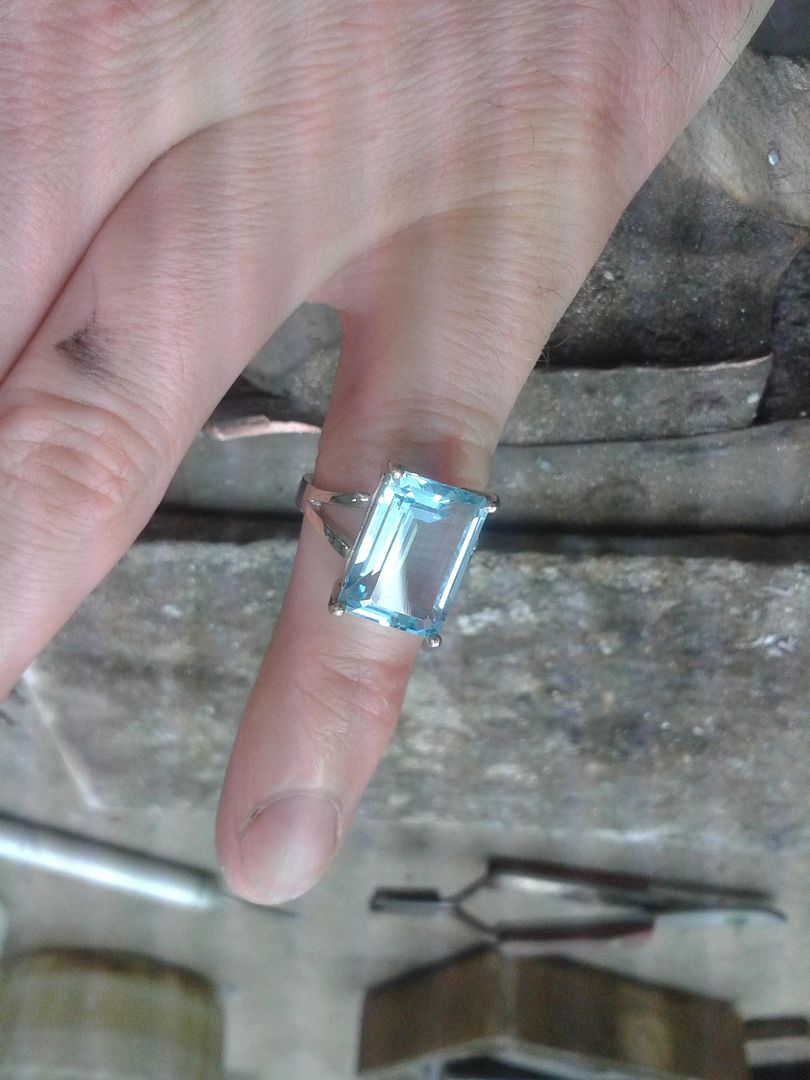
Done!
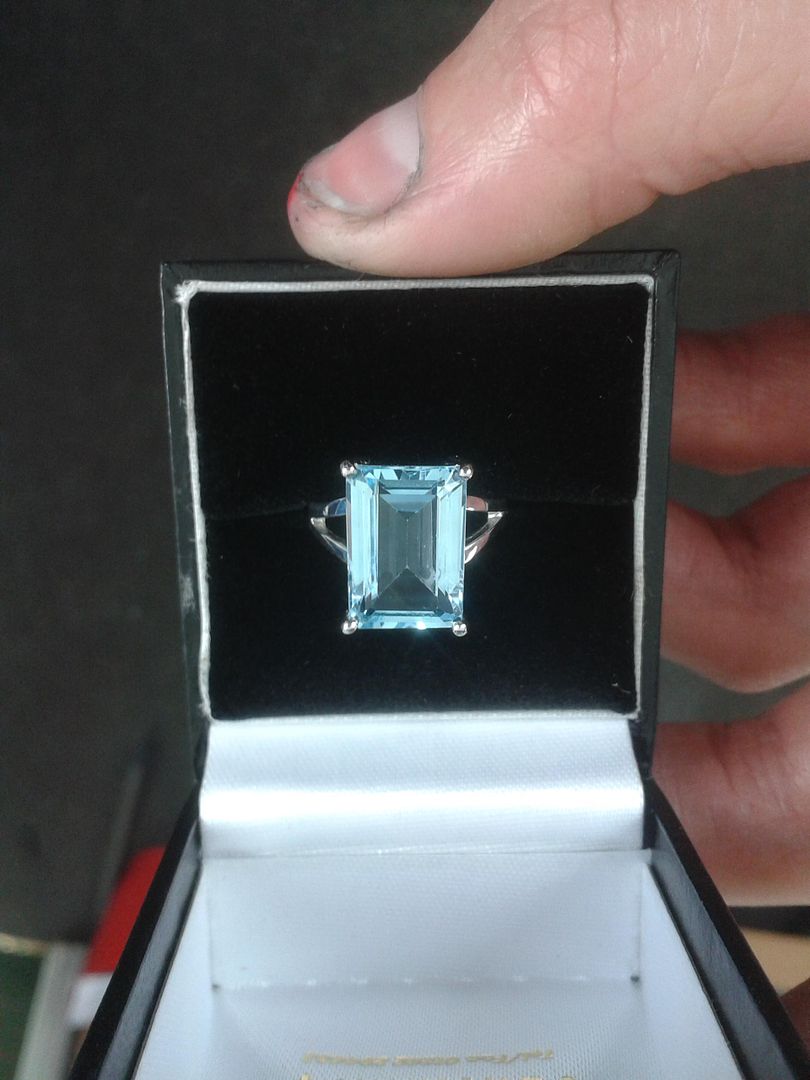
Eddie
A bar of 18ct white gold and a sky blue topaz.
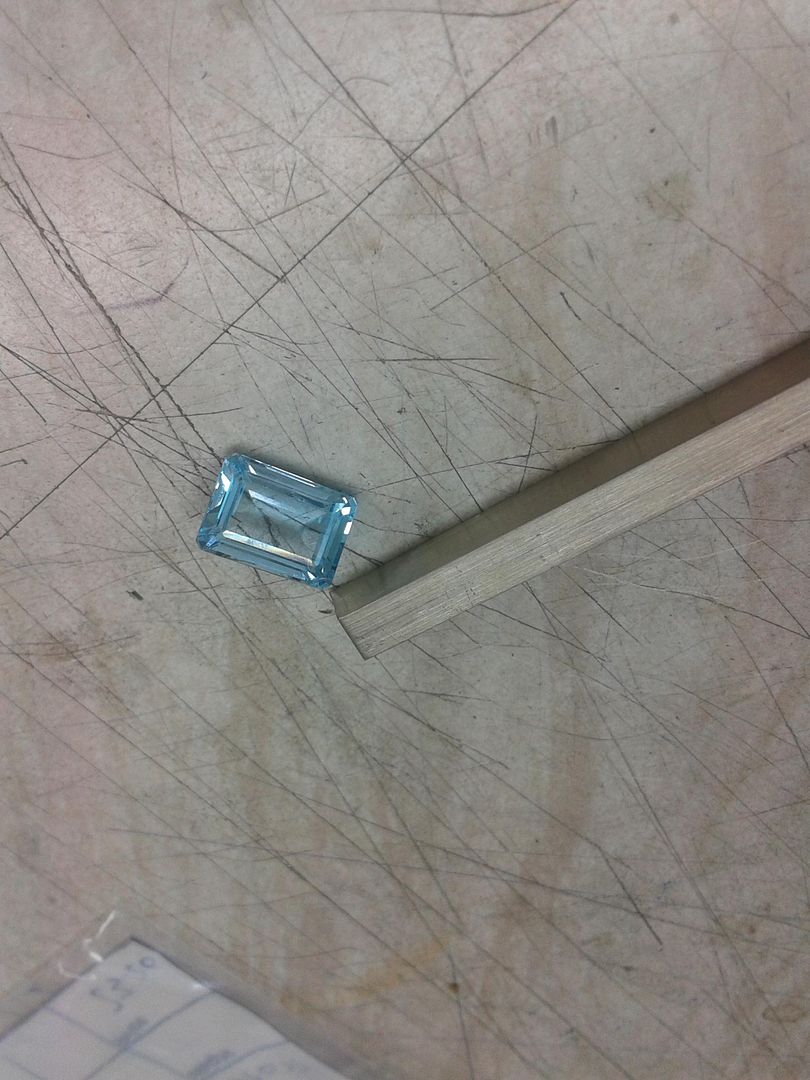
Made a setting:
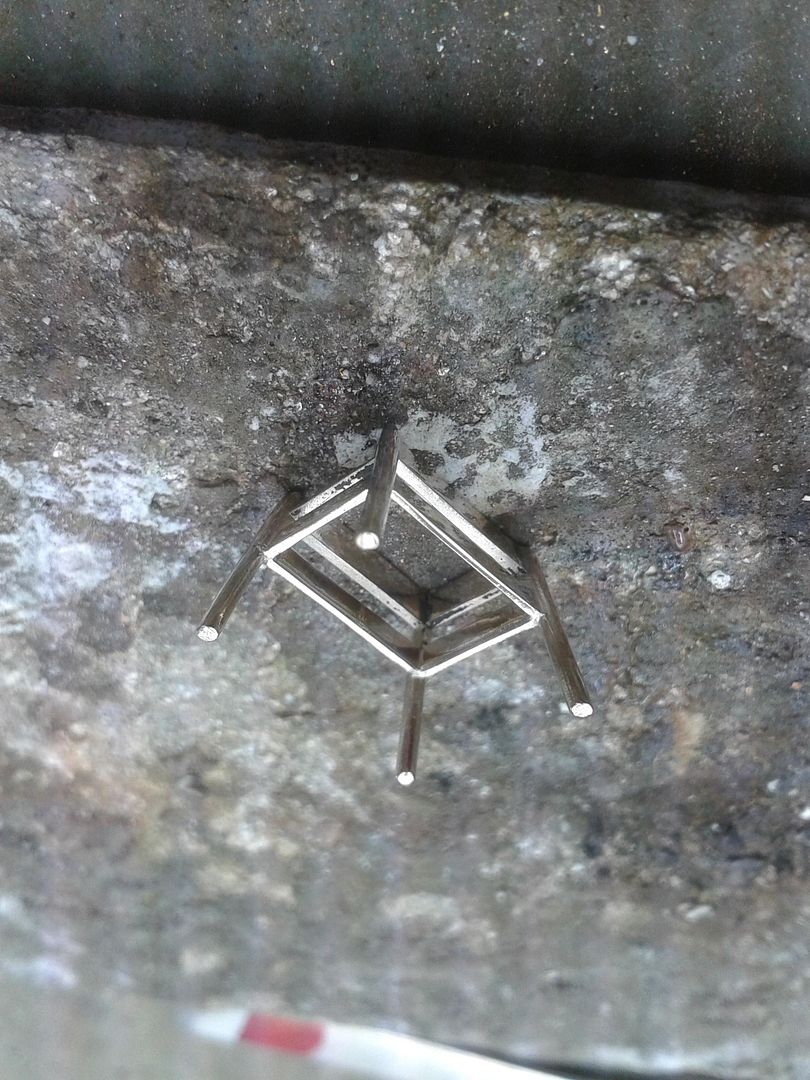
Then a split shank (in 2 peices because it's easier to build that way).
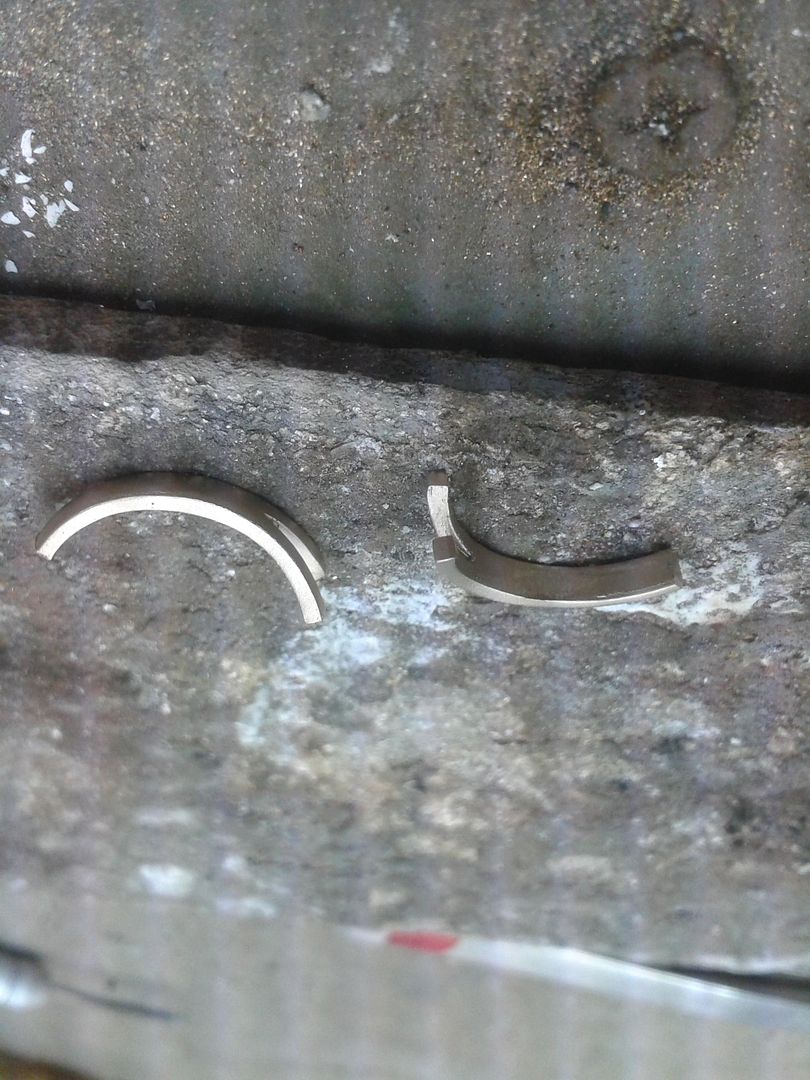
The two parts:
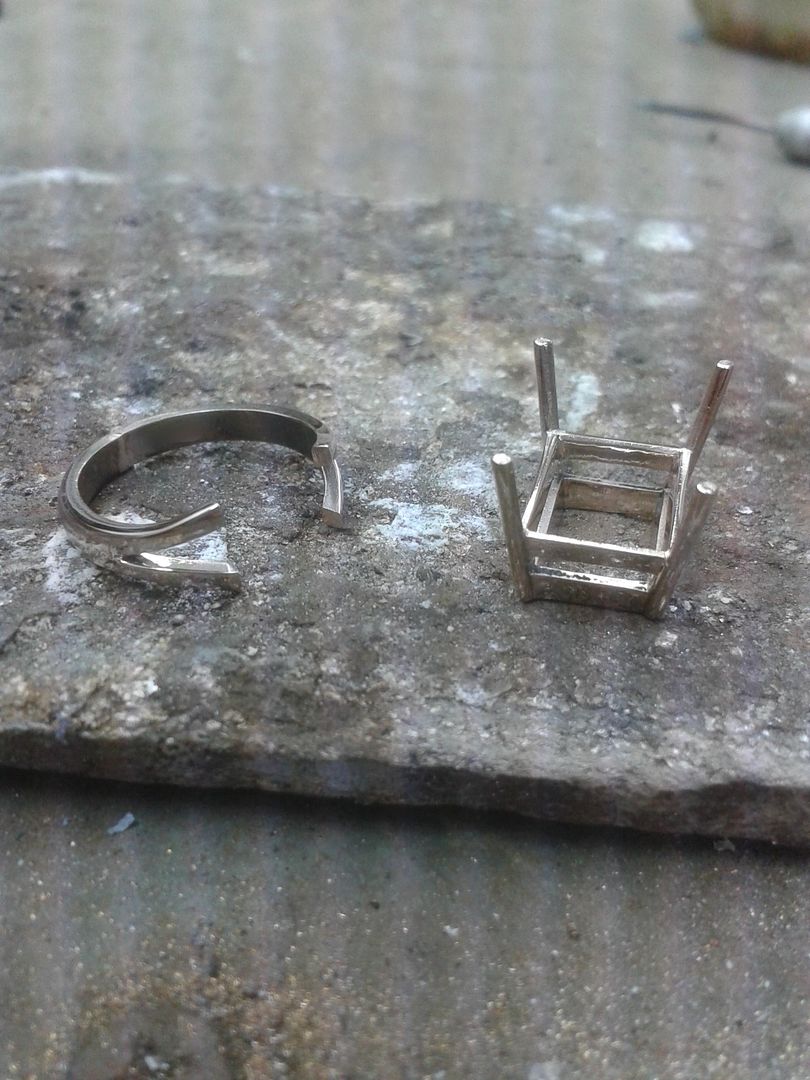
Soldered together:
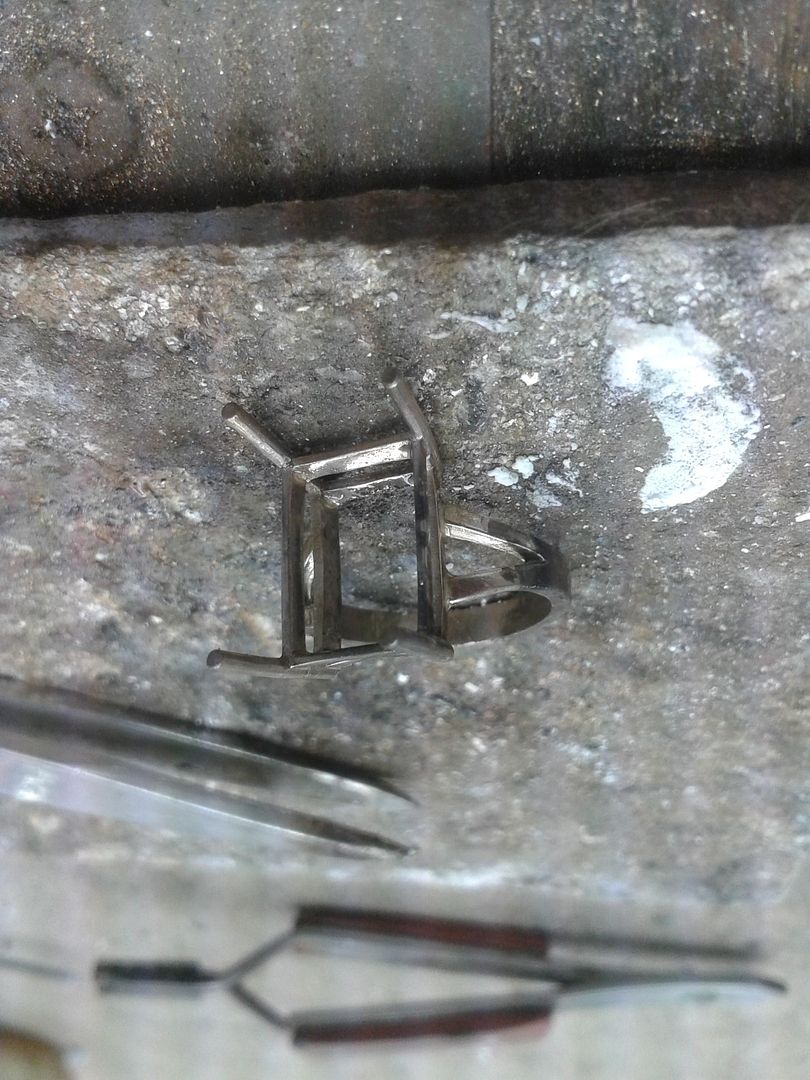
With the stone:
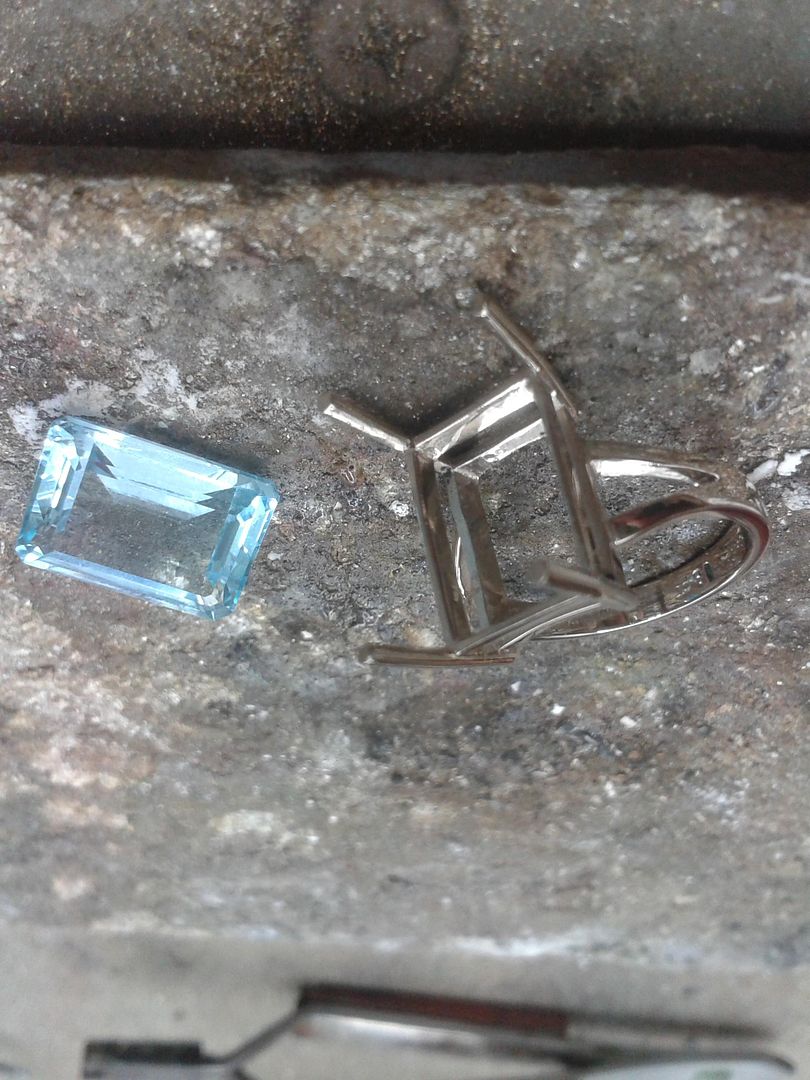
Stone set and ready for polishing and rhodium plating.
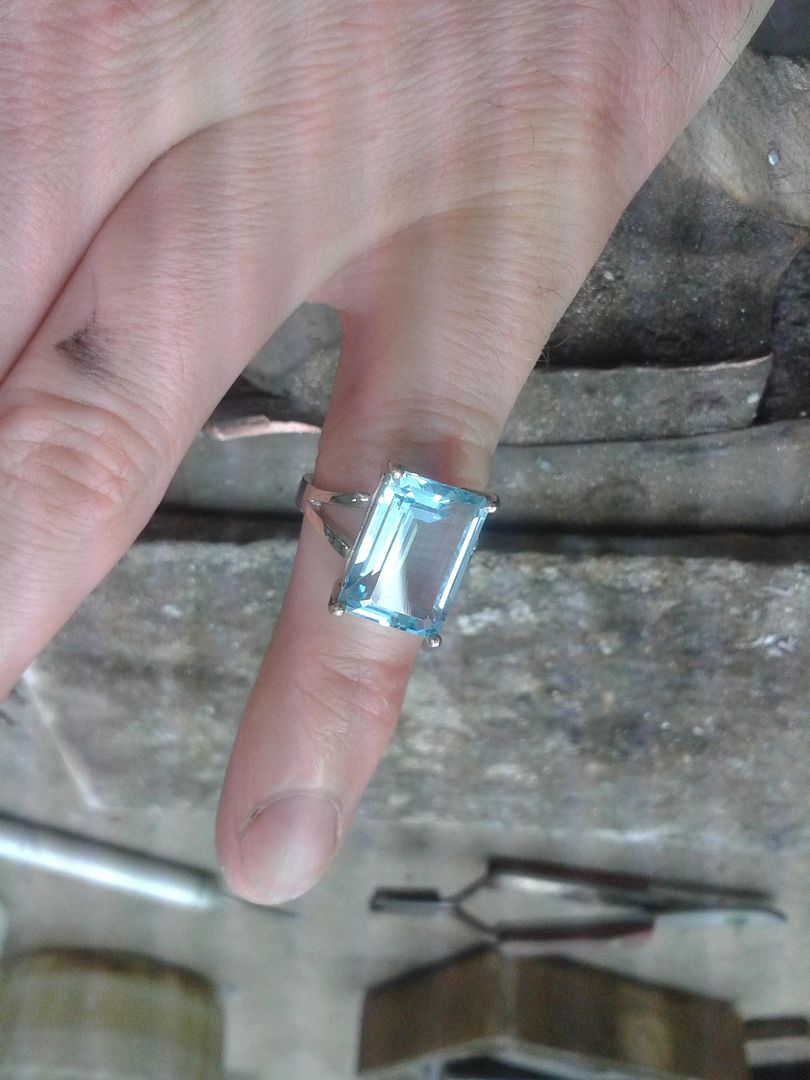
Done!
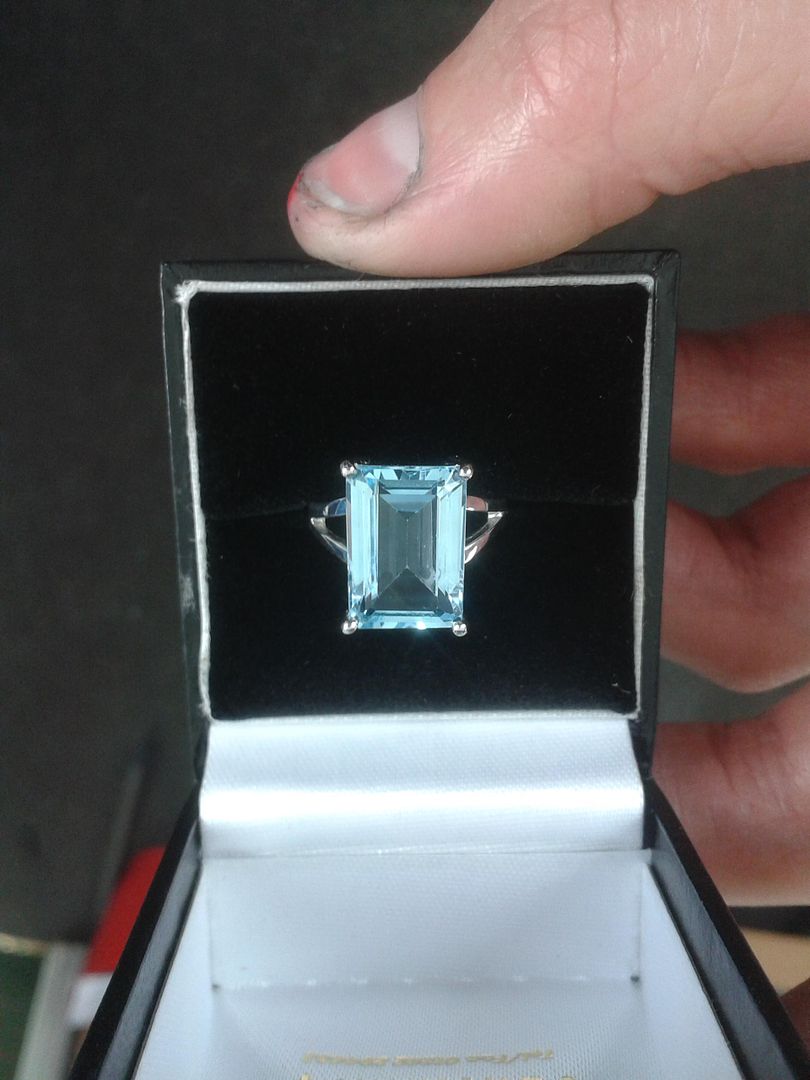
Eddie
Edited by ecain63 on Thursday 23 October 21:43
Depending on the metal and design the ring can either be compressed or cut and a piece removed. Good thing about compressing is that you avoid unnecessary joints and retain material weight. However, this can only be done for certain styles, heavier ones normally. Lighter weight rings can buckle. Cutting a piece out is the most risk free method but you do lose some material (negligible in the scheme of things, a size is roughly 1mm) and you will have a joint in the ring. If done correctly you wouldn't see this joint though and the correct solder ensures it's as strong or stronger than the rest of the ring. Helpful?
Eddie.
Eddie.
Race2the Redline said:
Eddie
Do you have a link to your website or contact details (I can't see anything on your profile) I want get my fathers St Christopher repaired and I'd like to send this and some future business your way as I'm sure many others would.
Regards
Hi mate,Do you have a link to your website or contact details (I can't see anything on your profile) I want get my fathers St Christopher repaired and I'd like to send this and some future business your way as I'm sure many others would.
Regards
This is my (fairly basic) website and fb page: More than happy to help.
https://www.google.co.uk/url?sa=t&rct=j&q=...
https://www.facebook.com/pages/JR-Jewellery/218680...
How do you mean 'thicker'? I assume you mean the shank (bit that goes from the sides under the finger).
A lot of people ask me to make the shank thicker but actually it's something that cannot be done without some horrendous joints and future complications. It's a lot of work for very little gain anyway. The way to make the shank thicker is actually by cutting the old shank off at the shoulders, where it is relatively unworn and then fitting a new shank to the correct spec. Much more effective job and minimal consideration needed when doing work further down the line. Send me a pm with some pics and i can give you some figures. I can keep the head unpolished if needs be too!
Eddie
A lot of people ask me to make the shank thicker but actually it's something that cannot be done without some horrendous joints and future complications. It's a lot of work for very little gain anyway. The way to make the shank thicker is actually by cutting the old shank off at the shoulders, where it is relatively unworn and then fitting a new shank to the correct spec. Much more effective job and minimal consideration needed when doing work further down the line. Send me a pm with some pics and i can give you some figures. I can keep the head unpolished if needs be too!
Eddie
buzzer said:
ecain63 said:
Fantastic.Can I come and sweep up in your workshop

Gassing Station | Watches | Top of Page | What's New | My Stuff