Saturn V anecdote
Discussion
From Bill Sawchuck:

The day Frank Borman learned he was an honorary member of Led Zeppelin.
This is Colonel Frank Borman, commander of Apollo 8, the first manned mission to travel from the earth to moon which took place in December 1968. He is holding my personal copy of the album Led Zeppelin II which I purchased, at the age of 10, upon its initial release in 1969. The Grammy-nominated cover art for the album was designed by David Juniper who was a friend of Led Zeppelin’s guitarist Jimmy Page. Although Borman is depicted on the album cover, David Juniper, when re-telling the story behind the artwork over the years, had always recounted that it was Neil Armstrong’s likeness that was used.
Several years ago, I made a small inquiry about the album to members of the space collector community on the website collectSPACE. In 2013, after a lively discussion, it was determined that Juniper had in fact mistakenly recounted which astronaut had appeared on the album’s cover. In fact, the actual portrait of Borman that was used by Juniper was determined, thus negating Juniper’s claims that it was Neil Armstrong.
As It turns out, this was an easy mistake to make, given that the album cover was designed in early 1969, just prior to the time that Neil Armstrong became a household name when selected by NASA to go to the moon on the Apollo 11 mission. When the cover art was originally constructed, it was, in fact, Borman who was the astronaut who was most prominently in the news at the time. However, at the time of the album’s release in late 1969, with the broader media coverage given to the Apollo 11 mission and moon landing, Neil Armstrong naturally overshadowed all other astronauts including Borman.
Several months after I had learned that it was Borman on the cover, I took the initiative of having him sign my album. I provided him with a detailed letter and graphic describing the story behind the artwork. As it turned out, until the time of the signing, Borman was completely unaware that he was on the cover of this iconic album!
And the rest is history.


The day Frank Borman learned he was an honorary member of Led Zeppelin.
This is Colonel Frank Borman, commander of Apollo 8, the first manned mission to travel from the earth to moon which took place in December 1968. He is holding my personal copy of the album Led Zeppelin II which I purchased, at the age of 10, upon its initial release in 1969. The Grammy-nominated cover art for the album was designed by David Juniper who was a friend of Led Zeppelin’s guitarist Jimmy Page. Although Borman is depicted on the album cover, David Juniper, when re-telling the story behind the artwork over the years, had always recounted that it was Neil Armstrong’s likeness that was used.
Several years ago, I made a small inquiry about the album to members of the space collector community on the website collectSPACE. In 2013, after a lively discussion, it was determined that Juniper had in fact mistakenly recounted which astronaut had appeared on the album’s cover. In fact, the actual portrait of Borman that was used by Juniper was determined, thus negating Juniper’s claims that it was Neil Armstrong.
As It turns out, this was an easy mistake to make, given that the album cover was designed in early 1969, just prior to the time that Neil Armstrong became a household name when selected by NASA to go to the moon on the Apollo 11 mission. When the cover art was originally constructed, it was, in fact, Borman who was the astronaut who was most prominently in the news at the time. However, at the time of the album’s release in late 1969, with the broader media coverage given to the Apollo 11 mission and moon landing, Neil Armstrong naturally overshadowed all other astronauts including Borman.
Several months after I had learned that it was Borman on the cover, I took the initiative of having him sign my album. I provided him with a detailed letter and graphic describing the story behind the artwork. As it turned out, until the time of the signing, Borman was completely unaware that he was on the cover of this iconic album!
And the rest is history.

From Stephen Coester:
"A tale about the first LH2 load into the new Pad B storage tank at the beginning of the Apollo program before Apollo 10.
We were experts from loading hundreds of liquid hydrogen tankers on Pad A so I wasn't concerned about this hazardous but routine operation. I was the engineer in charge of this initial fill. We cleared the area of nonessential personnel, blocked off the pad perimeter road, stationed the fire trucks and did all of our preparations.
The first wave of five tankers were backed up to the LH2 fill manifold, the manual valves opened and the tankers pressurized to initiate flow. I relaxed once flow began knowing we had dozens more to offload to chill down the warm new 850000 gallon tank and get it filled at 7-10 thousand gallons per tanker.
Suddenly I heard a crack and looked up from my procedure which was resting on the LH2 fill manifold. As I stared, the pipe started bending against its supports and all of a sudden the bellows in the manifold started breaking and liquid air began venting out of the vacuum jacketed outer pipe. I immediately yelled for the tanker operators to vent their tanks and for my mechanics to close the fill manifold valves and open the vent valves.
Whew! We were now safe, but what the hell had happened?
It turned out that for unknown reasons the designers didn't make the fill manifold the same as on Pad A. Normally the inner pipe would be made of Invar, a metal that wouldn't shrink when subjected to the -423 degree LH2 temperature. Instead they built it using 316 stainless steel which shrinks two inches for every forty feet of length. And theyused the same bellows in the outer vacuum jacket pipe as on Pad A. So when the pipe got hit with that super cold temperature it contracted and the bellows couldn't handle all that shrinkage. First the pipe bent like a snake and then the bellows cracked. Quite impressive and a bit scarey.
Fortunately the inner pipe didn't break and no hydrogen escaped. The system now couldn't support filling the storage tank so it was delayed for a month or so while the fill manifold was torn apart and beefier bellows installed. Finally we got the tank filled with LH2 in time to support Apollo 10....and as far as I know that same repaired fill manifold supported all subsequent Skylab, Soyuz and Shuttle missions on LC-39B."

Postscript - "When they took the fill manifold apart they found a partially eaten sandwich in the annulus between the pipes. No wonder we sometimes had trouble maintaining the extreme vacuum in there."
"A tale about the first LH2 load into the new Pad B storage tank at the beginning of the Apollo program before Apollo 10.
We were experts from loading hundreds of liquid hydrogen tankers on Pad A so I wasn't concerned about this hazardous but routine operation. I was the engineer in charge of this initial fill. We cleared the area of nonessential personnel, blocked off the pad perimeter road, stationed the fire trucks and did all of our preparations.
The first wave of five tankers were backed up to the LH2 fill manifold, the manual valves opened and the tankers pressurized to initiate flow. I relaxed once flow began knowing we had dozens more to offload to chill down the warm new 850000 gallon tank and get it filled at 7-10 thousand gallons per tanker.
Suddenly I heard a crack and looked up from my procedure which was resting on the LH2 fill manifold. As I stared, the pipe started bending against its supports and all of a sudden the bellows in the manifold started breaking and liquid air began venting out of the vacuum jacketed outer pipe. I immediately yelled for the tanker operators to vent their tanks and for my mechanics to close the fill manifold valves and open the vent valves.
Whew! We were now safe, but what the hell had happened?
It turned out that for unknown reasons the designers didn't make the fill manifold the same as on Pad A. Normally the inner pipe would be made of Invar, a metal that wouldn't shrink when subjected to the -423 degree LH2 temperature. Instead they built it using 316 stainless steel which shrinks two inches for every forty feet of length. And theyused the same bellows in the outer vacuum jacket pipe as on Pad A. So when the pipe got hit with that super cold temperature it contracted and the bellows couldn't handle all that shrinkage. First the pipe bent like a snake and then the bellows cracked. Quite impressive and a bit scarey.
Fortunately the inner pipe didn't break and no hydrogen escaped. The system now couldn't support filling the storage tank so it was delayed for a month or so while the fill manifold was torn apart and beefier bellows installed. Finally we got the tank filled with LH2 in time to support Apollo 10....and as far as I know that same repaired fill manifold supported all subsequent Skylab, Soyuz and Shuttle missions on LC-39B."

Postscript - "When they took the fill manifold apart they found a partially eaten sandwich in the annulus between the pipes. No wonder we sometimes had trouble maintaining the extreme vacuum in there."
Edited by MartG on Saturday 2nd June 17:16
Stephen has uploaded more stories here http://www.usna63.org/classmates/roster/cur-bio/31...
More from Stephen Coester
Saturn V LC-39 LH2 Adventures in vacuum pumping.
When I came to the LH2 engineering group in 1966, it was virtually brand new and they hadn't had to do much maintenance on the vacuum jacketed 10" LH2 transfer lines. Each forty foot long pipe section had a televac vacuum gauge and the mechanics had a fairly large box to read the vacuum level in each line.
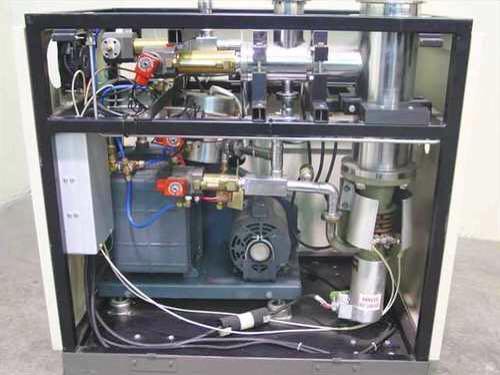
There were about forty line sections across the pad and twenty on each LUT. It was soon discovered that the lines weren't as maintenance free as they were supposed to be. In the event that the lines needed evacuating we had been supplied with a couple of Varian diffusion pumps. These were large similar to the first photo and had very small casters on the base and a trailer tow bar. They weren't very stable when towing across railroad tracks or across the field and were known to tip over. The pumps had an eight inch flange on top and we had these huge 8" vacuum flex hose to connect to the vacuum port on the transfer line which was only two inches. And worse they operated off of 480 volts and there wasn't any 480 running across the field so that had to be installed. Now 480 volts is really dangerous and for some reason the facility electrical guys could never get all the outlets phased the same. And phasing was critical because wrong phasing could make the vacuum pump run backwards and spew pump oil out instead of sucking in. Well first I determined that those huge flex hoses weren't going to work so I reduced the pump flange down from 8" to 1" and substituted tygon tubing for the big unwieldy hoses. The mechanics made up some pigtails to correct the phasing problem and were supposed to momentarily start the pump, verify correct rotation and if wrong use the right pigtail. One mechanic didn't check and while pumping one of the lines beneath the LH 2 disconnect tower filled the annulus with pump oil. This destroys the vacuum and the ability to maintain a vacuum. We pumped for days with no positive effect and then I came up with the brilliant idea to heat the line to boil out the oil. I searched around and found that North American the S-II contractor had some flexible heat blankets and were willing to lend them to me. We applied the blankets but could not get the temperature I wanted so I had the mechanics wrap the blankets with fiberglass insulation. This worked great and we got the temperature up and were making headway when I noticed smoke. We tore off the insulation and the blankets were burned to a crisp. The North American guys weren't real pleased with me. I called my logistics people and they said not to worry they would buy some new ones.
I mentioned the danger of 480 volts. We were pumping a line on the LUT which is all metal. We were investigating a leak in the line and had a mass spectrometer working with us. The Bendix mass spec operator was leaning on his machine and touched our vacuum pump. Next thing we knew he was flung about ten feet and was unconscious. He was seriously injured and I'm not sure if he ever returned to work. I never fully understood the chain of events but our electrical people made serious grounding mods to our machines.
Over time we determined that these big diffusion pumps weren't needed for the level of vacuum required in our transfer lines. The diffusion pumps could evacuate to about a ten thousandth of a micron while we were satisfied with 100 microns. I convinced our design group to use a simple mechanical pump like in the second photo. It was light and ran off of 110 volts which solved a lot of our problems.
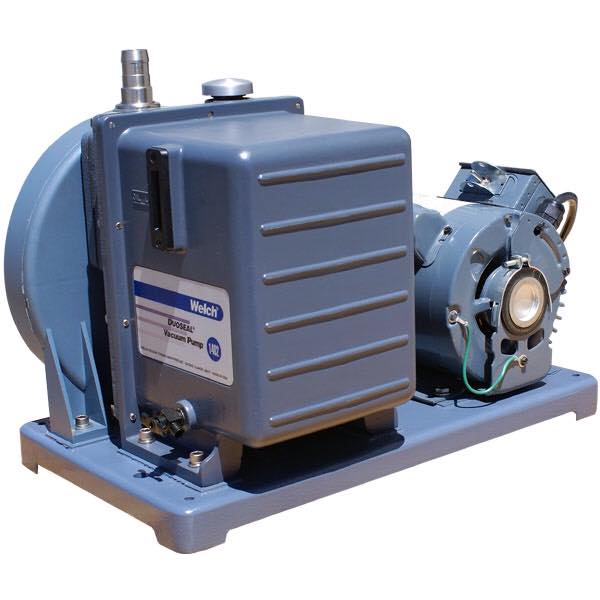
For those who aren't familiar a micron, is an SI derived unit of length equaling 1×10−6 metre (SI standard prefix "micro-" = 10−6); that is, one millionth of a metre (or one thousandth of a millimetre, 0.001 mm, or about 0.000039 inch). When used in vacuum it refers to the pressure exerted by that height of mercury. One atmosphere is 760000 microns.
Over the program we made many modifications to the transfer lines themselves replacing the vacuum gauges, completely changing the pumping port and other improvements.
Saturn V LC-39 LH2 Adventures in vacuum pumping.
When I came to the LH2 engineering group in 1966, it was virtually brand new and they hadn't had to do much maintenance on the vacuum jacketed 10" LH2 transfer lines. Each forty foot long pipe section had a televac vacuum gauge and the mechanics had a fairly large box to read the vacuum level in each line.
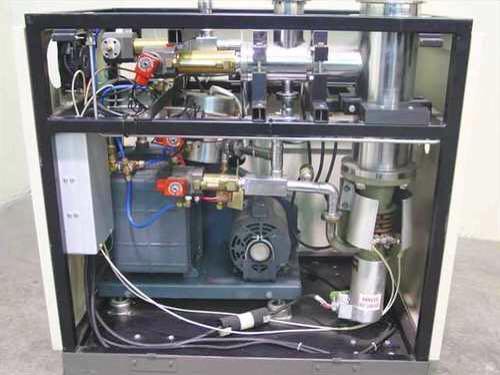
There were about forty line sections across the pad and twenty on each LUT. It was soon discovered that the lines weren't as maintenance free as they were supposed to be. In the event that the lines needed evacuating we had been supplied with a couple of Varian diffusion pumps. These were large similar to the first photo and had very small casters on the base and a trailer tow bar. They weren't very stable when towing across railroad tracks or across the field and were known to tip over. The pumps had an eight inch flange on top and we had these huge 8" vacuum flex hose to connect to the vacuum port on the transfer line which was only two inches. And worse they operated off of 480 volts and there wasn't any 480 running across the field so that had to be installed. Now 480 volts is really dangerous and for some reason the facility electrical guys could never get all the outlets phased the same. And phasing was critical because wrong phasing could make the vacuum pump run backwards and spew pump oil out instead of sucking in. Well first I determined that those huge flex hoses weren't going to work so I reduced the pump flange down from 8" to 1" and substituted tygon tubing for the big unwieldy hoses. The mechanics made up some pigtails to correct the phasing problem and were supposed to momentarily start the pump, verify correct rotation and if wrong use the right pigtail. One mechanic didn't check and while pumping one of the lines beneath the LH 2 disconnect tower filled the annulus with pump oil. This destroys the vacuum and the ability to maintain a vacuum. We pumped for days with no positive effect and then I came up with the brilliant idea to heat the line to boil out the oil. I searched around and found that North American the S-II contractor had some flexible heat blankets and were willing to lend them to me. We applied the blankets but could not get the temperature I wanted so I had the mechanics wrap the blankets with fiberglass insulation. This worked great and we got the temperature up and were making headway when I noticed smoke. We tore off the insulation and the blankets were burned to a crisp. The North American guys weren't real pleased with me. I called my logistics people and they said not to worry they would buy some new ones.
I mentioned the danger of 480 volts. We were pumping a line on the LUT which is all metal. We were investigating a leak in the line and had a mass spectrometer working with us. The Bendix mass spec operator was leaning on his machine and touched our vacuum pump. Next thing we knew he was flung about ten feet and was unconscious. He was seriously injured and I'm not sure if he ever returned to work. I never fully understood the chain of events but our electrical people made serious grounding mods to our machines.
Over time we determined that these big diffusion pumps weren't needed for the level of vacuum required in our transfer lines. The diffusion pumps could evacuate to about a ten thousandth of a micron while we were satisfied with 100 microns. I convinced our design group to use a simple mechanical pump like in the second photo. It was light and ran off of 110 volts which solved a lot of our problems.
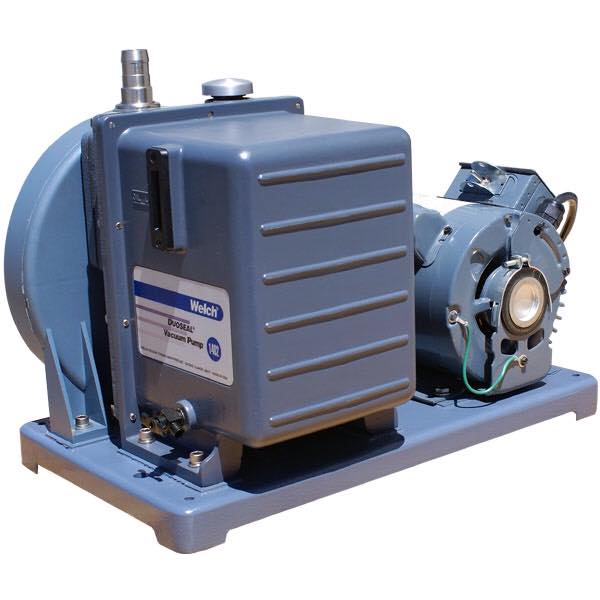
For those who aren't familiar a micron, is an SI derived unit of length equaling 1×10−6 metre (SI standard prefix "micro-" = 10−6); that is, one millionth of a metre (or one thousandth of a millimetre, 0.001 mm, or about 0.000039 inch). When used in vacuum it refers to the pressure exerted by that height of mercury. One atmosphere is 760000 microns.
Over the program we made many modifications to the transfer lines themselves replacing the vacuum gauges, completely changing the pumping port and other improvements.
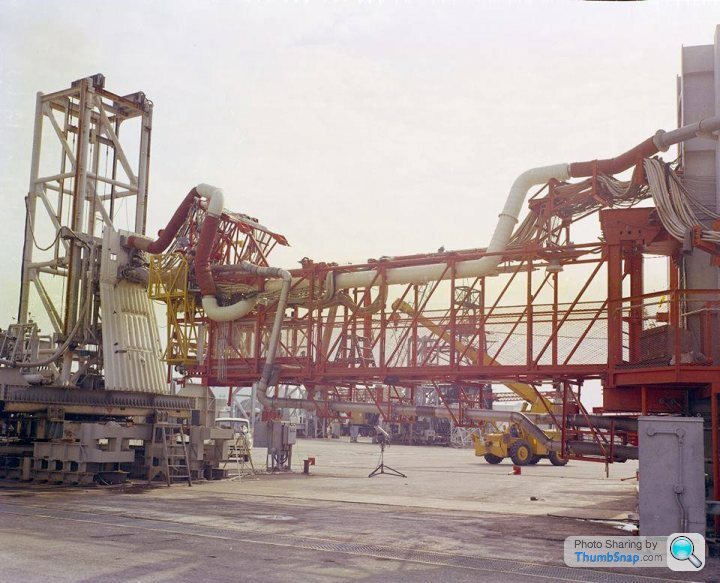
The Random Motion/Lift-Off Simulator (aka the "Arm Farm") at Marshall Space Flight Center.
July 28, 1967
The Marshall Space Flight Center (MSFC) played a crucial role in the development of the huge Saturn rockets that delivered humans to the moon in the 1960s. Many unique facilities existed at MSFC for the development and testing of the Saturn rockets. Affectionately nicknamed “The Arm Farm”, the Random Motion/ Lift-Off Simulator was one of those unique facilities. This facility was developed to test the swingarm mechanisms that were used to hold the rocket in position until lift-off. The Arm Farm provided the capability of testing the detachment and reconnection of various arms under brutally realistic conditions. The 18-acre facility consisted of more than a half dozen arm test positions and one position for testing access arms used by the Apollo astronauts. Each test position had two elements: a vehicle simulator for duplicating motions during countdown and launch; and a section duplicating the launch tower. The vehicle simulator duplicated the portion of the vehicle skin that contained the umbilical connections and personnel access hatches. Driven by a hydraulic servo system, the vehicle simulator produced relative motion between the vehicle and tower. On the Arm Farm, extreme environmental conditions (such as a launch scrub during an approaching Florida thunderstorm) could be simulated. The dramatic scenes that the Marshall engineers and technicians created at the Arm Farm permitted the gathering of crucial technical and engineering data to ensure a successful real time launch from the Kennedy Space Center.
We came close to having a major fire/catastrophe during the Apollo program. The 850,000 gallon liquid hydrogen tank is continuously boiling off the -423F liquid and it must be vented to prevent over pressurizing the tank. The primary vent path was out to the burn pond on Apollo or the flare stack on Space Shuttle. During non operational periods the tank was continuously vented out a pipe at the top of the tank. There were two 12 inch manual valves to direct the flow one way or the other and one was always open and the other closed depending on whether we were in a loading operation or in a standby condition. The valves were chained and locked to prevent unauthorized changing.
We detected internal leakage through one of the valves and it was decided it needed to be changed out. This was a problem because draining the tank was a big deal and there wasn't enough helium in the free world to purge and inert the tank.
I was charged with figuring out how to accomplish the valve changeout without draining and purging the tank. I came up with a plastic containment with gloves like in a hazardous biological lab that would fit around the valve and could be purged with helium. Also I had made a guillotine like device that could be slid in between the valve and the upstream piping to seal off the tank while the valve was being removed. The valve was huge and required a crane to lift it? Sounded good in theory.
Then I arranged for anti-static mats to be placed under the valve and large fans were set up to blow any escaped hydrogen away. We opened the vent valve going to the burn pond to get the tank pressure as close to zero as possible.
We got all this set up and the mechanics started removing the valve flange bolts inside my super containment box. As soon as the seal was broken the box immediately filled with explosive hydrogen gas and visibility was reduced to zero. They ripped off the box and managed to get my guillotine seal in place but not before we had a huge cloud of vapor surrounding us all. The defective valve was then lifted by the crane and removed. Then they had no choice but to lift the replacement valve into place, remove the temporary seal and bolt the new valve in place, once again in a billowing cloud of hydrogen vapor.
Somehow nothing ignited and the valve installation was successfully accomplished. Another of my not so shining moments as I was directing the operation and being sure we were all going up in flames.
Steven Coester
We detected internal leakage through one of the valves and it was decided it needed to be changed out. This was a problem because draining the tank was a big deal and there wasn't enough helium in the free world to purge and inert the tank.
I was charged with figuring out how to accomplish the valve changeout without draining and purging the tank. I came up with a plastic containment with gloves like in a hazardous biological lab that would fit around the valve and could be purged with helium. Also I had made a guillotine like device that could be slid in between the valve and the upstream piping to seal off the tank while the valve was being removed. The valve was huge and required a crane to lift it? Sounded good in theory.
Then I arranged for anti-static mats to be placed under the valve and large fans were set up to blow any escaped hydrogen away. We opened the vent valve going to the burn pond to get the tank pressure as close to zero as possible.
We got all this set up and the mechanics started removing the valve flange bolts inside my super containment box. As soon as the seal was broken the box immediately filled with explosive hydrogen gas and visibility was reduced to zero. They ripped off the box and managed to get my guillotine seal in place but not before we had a huge cloud of vapor surrounding us all. The defective valve was then lifted by the crane and removed. Then they had no choice but to lift the replacement valve into place, remove the temporary seal and bolt the new valve in place, once again in a billowing cloud of hydrogen vapor.
Somehow nothing ignited and the valve installation was successfully accomplished. Another of my not so shining moments as I was directing the operation and being sure we were all going up in flames.
Steven Coester
As NASA’s facilities and launch complexes were being constructed for the Saturn V, at Kennedy Space Center, one of the problems was how to get the Saturn V from the VAB to the launch pad. Studies were done transporting the Saturn V via barge down the many water canals or via rail. Barry Schlenk, a Bucyrus-Erie Company representative, contacted NASA’s Deputy Chief of the Future Launch Systems Study Office to discuss overhead cranes for use with the Titan missile. Schlenk happened to mention a steam shovel crawler as a possible alternative for moving the Saturn V. In 1962 Launch Operations officials visited Paradise, Kentucky to witness a Bucyrus-Erie 2,700 metric-ton crawler-shovel in action. The coal mining crawler-shovel was found to have a platform that could be leveled and stabilized on uneven terrain carrying immense weight.
Water transport was later found to be unreliable as transport via barge proved unstable not only in water, but with wind as a factor as well. Rail was deemed the worst for transport as curved rails would pose a problem carrying the immense rocket weight even with reinforcements and the rails would require a complex switching system. Even a combination of the two was ineffective. The crawler method was found to be the best as a crawler could be designed and built for the Saturn V, modeled after the coal mining crawler-shovel. The crawler method received a boost when the U.S. Army Corps of Engineers also conducted their own study and found the crawler was the best way to transport the rocket to the launch pad.
After the Apollo Program ended, the Crawler-Transporters had continued use in transporting the Space Shuttles to the launch pad and are currently being modified for use with the Orion Program.
( pic - A Bucyrus-Erie steam shovel crawler)
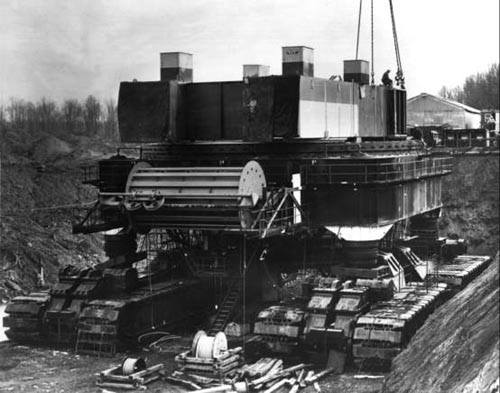
Water transport was later found to be unreliable as transport via barge proved unstable not only in water, but with wind as a factor as well. Rail was deemed the worst for transport as curved rails would pose a problem carrying the immense rocket weight even with reinforcements and the rails would require a complex switching system. Even a combination of the two was ineffective. The crawler method was found to be the best as a crawler could be designed and built for the Saturn V, modeled after the coal mining crawler-shovel. The crawler method received a boost when the U.S. Army Corps of Engineers also conducted their own study and found the crawler was the best way to transport the rocket to the launch pad.
After the Apollo Program ended, the Crawler-Transporters had continued use in transporting the Space Shuttles to the launch pad and are currently being modified for use with the Orion Program.
( pic - A Bucyrus-Erie steam shovel crawler)
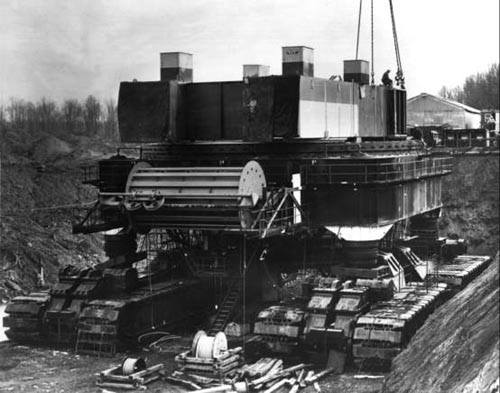
09/26/2002: A view of the camera mounted on the external tank of Space Shuttle Atlantis. The color video camera mounted to the top of Atlantis' external tank will provide a view of the front and belly of the orbiter and a portion of the solid rocket boosters (SRBs) and external tank during the launch of Atlantis on mission STS-112. It will offer the STS-112 team an opportunity to monitor the shuttle's performance from a new angle. The camera will be turned on fifteen minutes prior to launch and will show the orbiter and solid rocket boosters on the launch pad. The video will be downlinked from the external tank during flight to several NASA data-receiving sites and then relayed to the live television broadcast. The camera is expected to operate for about 15 minutes following liftoff. At liftoff, viewers will see the shuttle clearing the launch tower and, at two minutes after liftoff, see the right SRB separate from the external tank. When the external tank separates from Atlantis about eight minutes into the flight, the camera is expected to continue its live feed for about six more minutes although NASA may be unable to pick up the camera's signal because the tank may have moved out of range.
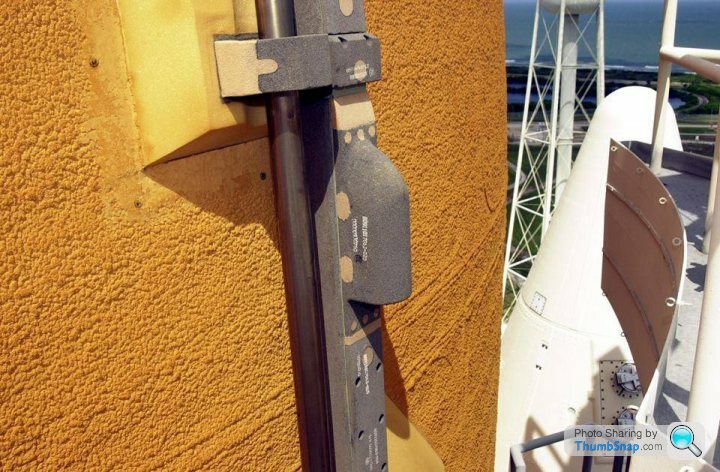
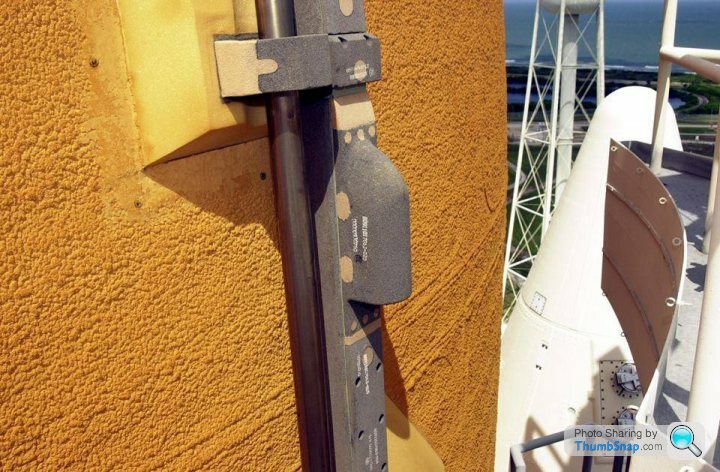
From J Harvey LeBlanc
"The day I scared the seagulls at Launch Pad 39----- During one of the early Saturn V CDDTs it was reported that a large amount of helium was being vented to the atmosphere from the LUT area. Post test inspection indicated that the helium was coming from the system I had designed for chilling the Thrust Chambers on the S-II Stage J-2 engines. I was directed to fly down to KSC to do some troubleshooting of my system ASAP. During my hardware and data review I found that the helium had come from a large relief valve (#3) which had opened and failed to reseat (See the very simplified schematic of the system). The system gets it helium supply from a 6,000 psi storage facility which has a total tank volume of 9,000 gallon. The helium pressure was reduced in my system by two series pressure regulators. The first (#1) drops the pressure from 6,000 psi to 3,200 psi and the second (#2) drops the pressure from 3,200 psi to 1,200 psi. In the event that regulator #2 failed open or partially open, relief valve #3 was set to relieve at approximately 1,440 psi to assure that the down stream systems were not pressurized to an unsafe level. The 1200 psi gas was normally routed through the S-II LH2 Heat Exchanger to chill the gas down to about -300 degrees before flowing through a shutoff valve (#5), then to the S-II Stage engines to chill-down the Thrust Chambers to the start requirements. Shutoff valve #5 was normally opened to start the flow then closed just prior to liftoff. My data review indicated that after the shutoff valve #5 was closed, the cold gas in the line between the Heat Exchanger and #5 valve started to warm up which of course caused the pressure to start increasing to the point that the big relief valve #3 opened then failed to close when the system pressure was back to 1,200 psi. This resulted in the continuous venting of about 3 million cubic feet of helium to the atmosphere around the LUT! The guys at KSC kidded me by saying all the seagulls in the area were screeching in high pitch voices!!!
It had been my experience that large 1 1/2” high pressure relief valves, like #3, were not always reliable on reseat pressures if they were caused to relieve by very slowly increasing the inlet pressure. Since this application had a very slow pressure rise due to thermal expansion, I eliminated the problem by adding a small 3/8” backpressure regulator (#4) in parallel to the big relief valve but set to relieve at about 50 psi lower. Slow thermal expansion would cause a slow rise in pressure which was relived by the new small backpressure regulator #4 and prevent the pressure from going high enough to cause the big relief valve #3 to open. In the event of a major failed open regulator #2, both #4 and then #3 would open to keep the system safe. We never had another problem with this system!
This is just a minor example of the type problems that a Pneumatic System Designer would face all the time!!!"
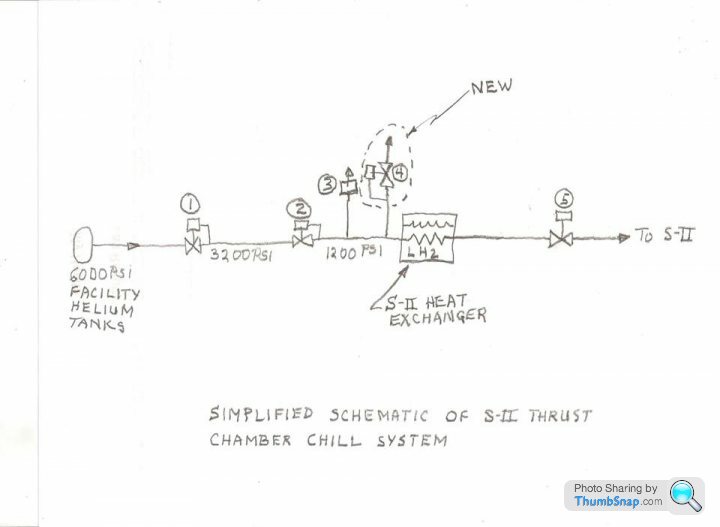
"The day I scared the seagulls at Launch Pad 39----- During one of the early Saturn V CDDTs it was reported that a large amount of helium was being vented to the atmosphere from the LUT area. Post test inspection indicated that the helium was coming from the system I had designed for chilling the Thrust Chambers on the S-II Stage J-2 engines. I was directed to fly down to KSC to do some troubleshooting of my system ASAP. During my hardware and data review I found that the helium had come from a large relief valve (#3) which had opened and failed to reseat (See the very simplified schematic of the system). The system gets it helium supply from a 6,000 psi storage facility which has a total tank volume of 9,000 gallon. The helium pressure was reduced in my system by two series pressure regulators. The first (#1) drops the pressure from 6,000 psi to 3,200 psi and the second (#2) drops the pressure from 3,200 psi to 1,200 psi. In the event that regulator #2 failed open or partially open, relief valve #3 was set to relieve at approximately 1,440 psi to assure that the down stream systems were not pressurized to an unsafe level. The 1200 psi gas was normally routed through the S-II LH2 Heat Exchanger to chill the gas down to about -300 degrees before flowing through a shutoff valve (#5), then to the S-II Stage engines to chill-down the Thrust Chambers to the start requirements. Shutoff valve #5 was normally opened to start the flow then closed just prior to liftoff. My data review indicated that after the shutoff valve #5 was closed, the cold gas in the line between the Heat Exchanger and #5 valve started to warm up which of course caused the pressure to start increasing to the point that the big relief valve #3 opened then failed to close when the system pressure was back to 1,200 psi. This resulted in the continuous venting of about 3 million cubic feet of helium to the atmosphere around the LUT! The guys at KSC kidded me by saying all the seagulls in the area were screeching in high pitch voices!!!
It had been my experience that large 1 1/2” high pressure relief valves, like #3, were not always reliable on reseat pressures if they were caused to relieve by very slowly increasing the inlet pressure. Since this application had a very slow pressure rise due to thermal expansion, I eliminated the problem by adding a small 3/8” backpressure regulator (#4) in parallel to the big relief valve but set to relieve at about 50 psi lower. Slow thermal expansion would cause a slow rise in pressure which was relived by the new small backpressure regulator #4 and prevent the pressure from going high enough to cause the big relief valve #3 to open. In the event of a major failed open regulator #2, both #4 and then #3 would open to keep the system safe. We never had another problem with this system!
This is just a minor example of the type problems that a Pneumatic System Designer would face all the time!!!"
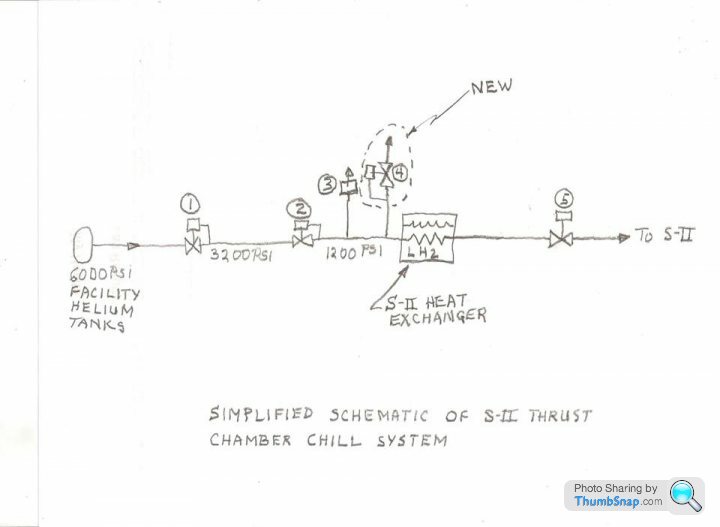
Even the smallest things can cause problems in space...
From NASA engineer Dave Parker
"Hubble Space Telescope Power Control Unit, PCU, Main Bus C fastener that loosened due to thermal cycling on orbit and required PCU EVA replacement on Servicing Mission 3B by astronaut John Grunsfeld. When the old PCU was returned, my NASA program manager permitted me to open up the PCU and determine all of the failures. Based on telemetry, we suspected that this Fastener was at fault, and we were right. The fastener was too short to fully engage the nutplate locking feature, and it had been reused several times as witnessed by scarring of the torque-set in the head and worn, reduced diameter of the threaded tip. After removing the conformal coating around the fastener head, the washer under the head was free spinning. The loose joint in this bus resulted in an impedance fault causing batteries five and six to under charge. Since we knew this bus joint was implicated based on telemetry, we reworked and improved this joint in the replacement PCU before the Servicing Mission."
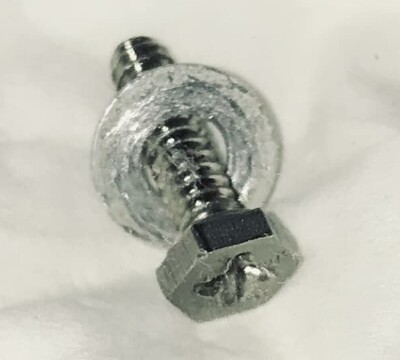

"This one fastener was holding together two lead-tin coated copper bus bars (PCU Main Bus C) carrying 1/3 of of all battery charge current for the Telescope. The loose joint prevented proper battery 5&6 charging. Battery 5&6 were chronically under-charged and reduced available battery capacity to support orbit night loads and potential safe mode events."
From NASA engineer Dave Parker
"Hubble Space Telescope Power Control Unit, PCU, Main Bus C fastener that loosened due to thermal cycling on orbit and required PCU EVA replacement on Servicing Mission 3B by astronaut John Grunsfeld. When the old PCU was returned, my NASA program manager permitted me to open up the PCU and determine all of the failures. Based on telemetry, we suspected that this Fastener was at fault, and we were right. The fastener was too short to fully engage the nutplate locking feature, and it had been reused several times as witnessed by scarring of the torque-set in the head and worn, reduced diameter of the threaded tip. After removing the conformal coating around the fastener head, the washer under the head was free spinning. The loose joint in this bus resulted in an impedance fault causing batteries five and six to under charge. Since we knew this bus joint was implicated based on telemetry, we reworked and improved this joint in the replacement PCU before the Servicing Mission."
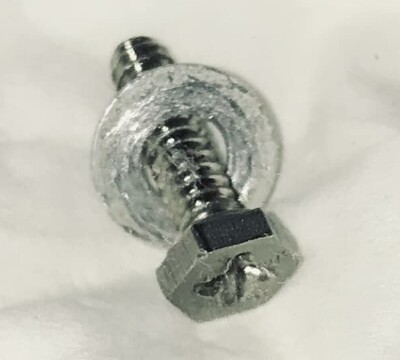

"This one fastener was holding together two lead-tin coated copper bus bars (PCU Main Bus C) carrying 1/3 of of all battery charge current for the Telescope. The loose joint prevented proper battery 5&6 charging. Battery 5&6 were chronically under-charged and reduced available battery capacity to support orbit night loads and potential safe mode events."
From Chuck Waller
"I mentioned I once had to go on the launcher while the Saturn V, I think AS501, was fully fueled. Not normal, crews were kept a long way from the pad until the flight crew with their support were sent out after fueling. There was a small leak at a 1" connection about 15 ft. back on the LOX fll line on the side of swing arm 4. I knew this connection was going to leak as it had during 500F tests and no changes had been made to fittin. While I was in the firing room during the LOX fill of the S-II, the small leak was displayed on one of the large video screen there. I then got a call on headset from launch director to explain. Told him it was a boss type 1" male fitting with a teflon "O" ring. He then requested I that go to pad to check it out. I knew I could not fix it, but only tighten it down until I had a metal to metal seal which would still leak. Nobody asked me if I could fix it,, just get out there. I was not part of the Red Crew which was trained for pad work after fueling so I was surprised and nervous. Two swing arm techs. and a QC guy were sent with me. We were suited up and had anti static straps belted to anke. My feelings when we got to pad were much like explained in J.H. Ward's book Rocket Ranch". He says when the Red Crew had to go out it was "memorable". As he said "The strange and unearthly noises that dammed rocket made:creaking, groaning -- loud ssssss and some time sounding like a group of screaming banshees" All of this at night with the bright white light from the search lights. We hurried up the launcher out on arm 4 tightened the fitting and then got the hell out of Dodge. As far as I know that fitting leaked on every Saturn V launch. It was only a small dribble and would evaporate as it fell from arm 4."
"I mentioned I once had to go on the launcher while the Saturn V, I think AS501, was fully fueled. Not normal, crews were kept a long way from the pad until the flight crew with their support were sent out after fueling. There was a small leak at a 1" connection about 15 ft. back on the LOX fll line on the side of swing arm 4. I knew this connection was going to leak as it had during 500F tests and no changes had been made to fittin. While I was in the firing room during the LOX fill of the S-II, the small leak was displayed on one of the large video screen there. I then got a call on headset from launch director to explain. Told him it was a boss type 1" male fitting with a teflon "O" ring. He then requested I that go to pad to check it out. I knew I could not fix it, but only tighten it down until I had a metal to metal seal which would still leak. Nobody asked me if I could fix it,, just get out there. I was not part of the Red Crew which was trained for pad work after fueling so I was surprised and nervous. Two swing arm techs. and a QC guy were sent with me. We were suited up and had anti static straps belted to anke. My feelings when we got to pad were much like explained in J.H. Ward's book Rocket Ranch". He says when the Red Crew had to go out it was "memorable". As he said "The strange and unearthly noises that dammed rocket made:creaking, groaning -- loud ssssss and some time sounding like a group of screaming banshees" All of this at night with the bright white light from the search lights. We hurried up the launcher out on arm 4 tightened the fitting and then got the hell out of Dodge. As far as I know that fitting leaked on every Saturn V launch. It was only a small dribble and would evaporate as it fell from arm 4."
Not Saturn related, but maybe a tenuous connection via reverse engineering of old technology...
When new nuclear warheads were required in the mid 90s, engineers realised there was no need to re invent the wheel, and set about making replacements based on the older ones, made back in the 70s. One small problem: A vital component, used to hold parts of the explosive shell in place, was no longer made, the very name was classified, as were it's components (it was apparently like an aerogel substance, that turned to plasma as part of the detonation cycle) and none of the manufacturing data had been kept, as it was so classified all the info was destroyed once they had finished making the required amounts. (And the original teams had long been retired and many had passed away)
But hey, it's the 90s, they can reverse engineer it from the existing material still in warheads, right?
Years later, way past the deadlines and horrifically over budget, they still hadn't been able to replicate it perfectly enough for it to do what it was supposed to do. It turns out modern manufacturing was the problem, as modern cleaning techniques on the manufacturing gear was eliminating a contaminant that had unkowingly been there back in the 70s, which when introduced in the manufacturing process added just the right thing to the gunk.
Once they figured that out, they added the contaminant as an ingredient and could then actually make something that had been originally made almost 30 years before. Sometimes modern gear and a couple decades of knowledge don't give the results you expect.
When new nuclear warheads were required in the mid 90s, engineers realised there was no need to re invent the wheel, and set about making replacements based on the older ones, made back in the 70s. One small problem: A vital component, used to hold parts of the explosive shell in place, was no longer made, the very name was classified, as were it's components (it was apparently like an aerogel substance, that turned to plasma as part of the detonation cycle) and none of the manufacturing data had been kept, as it was so classified all the info was destroyed once they had finished making the required amounts. (And the original teams had long been retired and many had passed away)
But hey, it's the 90s, they can reverse engineer it from the existing material still in warheads, right?
Years later, way past the deadlines and horrifically over budget, they still hadn't been able to replicate it perfectly enough for it to do what it was supposed to do. It turns out modern manufacturing was the problem, as modern cleaning techniques on the manufacturing gear was eliminating a contaminant that had unkowingly been there back in the 70s, which when introduced in the manufacturing process added just the right thing to the gunk.
Once they figured that out, they added the contaminant as an ingredient and could then actually make something that had been originally made almost 30 years before. Sometimes modern gear and a couple decades of knowledge don't give the results you expect.
From Stephen Coester...
This tale just shows how stupid I was in my twenties. The LUT was on the pad. We had some question about one of the expansion joints on the hydrogen lines. By myself I went up on the zero level, climbed over the hand rail, shinnied down the vertical LH2 lines and crawled across the horizontal lines to inspect the joint. No safety, no harness, just me sixty feet above the bottom of the flame trench. But I did accomplish my inspection. And I was afraid of heights.
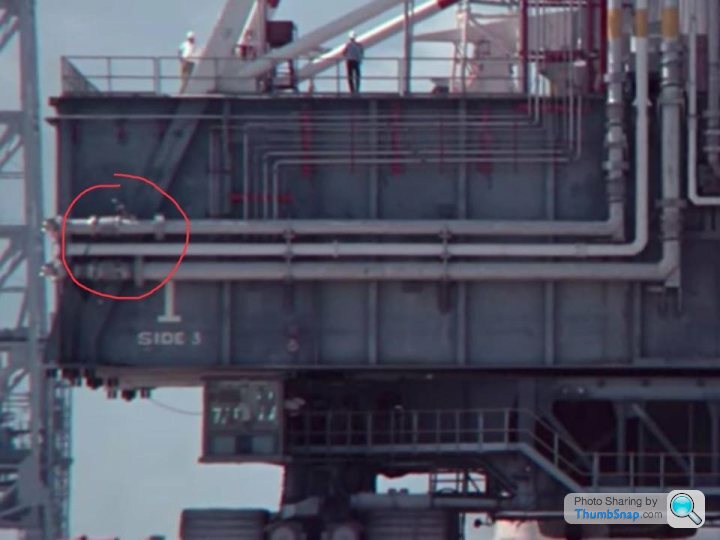
This tale just shows how stupid I was in my twenties. The LUT was on the pad. We had some question about one of the expansion joints on the hydrogen lines. By myself I went up on the zero level, climbed over the hand rail, shinnied down the vertical LH2 lines and crawled across the horizontal lines to inspect the joint. No safety, no harness, just me sixty feet above the bottom of the flame trench. But I did accomplish my inspection. And I was afraid of heights.
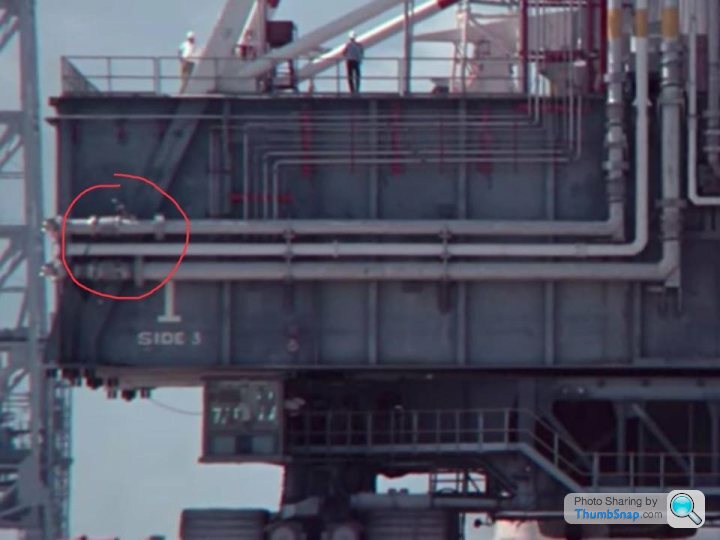
With TASS reporting the death of space pioneer Valery Bykovksy, something rather bizarre has happened. The original six Vostok cosmonauts have passed away in the exact order they flew in space. Only the sixth and last, Valentina Tereshkova, now remains...
Gagarin (1968), Titov (2000), Nikolayev (2004), Popovich (2009), Bykovksy (2019), Tereshkova (living)
Gagarin (1968), Titov (2000), Nikolayev (2004), Popovich (2009), Bykovksy (2019), Tereshkova (living)
Gassing Station | Science! | Top of Page | What's New | My Stuff