Bloodhound LSR Thread As Requested...
Discussion
AW111 said:
Plus a mustachioed man in a black trilby skulking about stealing secrets / sabotaging the project.
re brakes - what sort of decelleration is required for Bloodhound? I assume you have a couple of km to slow down in.
Total energy dissipation remains huge, of course, but I'm interested in the power required
About 3g from 1000mph initially.re brakes - what sort of decelleration is required for Bloodhound? I assume you have a couple of km to slow down in.
Total energy dissipation remains huge, of course, but I'm interested in the power required

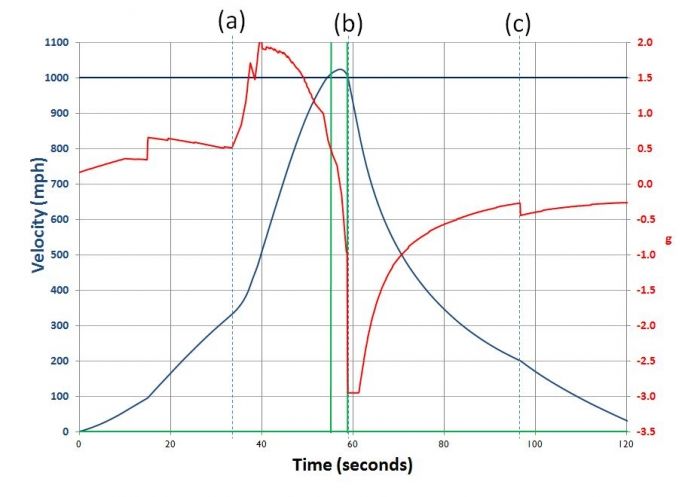
BLOODHOUND SSC accelerates from rest using the EJ-200 jet engine, taking it up to just over 300mph.
At that point (a) the rocket will be ignited, so that it and the jet are operating simultaneously, thereby increasing the acceleration to around 2g.
Having reached maximum speed (1,050mph), the rocket thrust will be stopped, the jet engine throttled back and airbrakes begin to deploy (point b). The car will decelerate at nearly 3g.
When the vehicle slows to subsonic speeds the aerodynamic drag will reduce dramatically, slowing the deceleration of the vehicle. An additional deceleration peak is shown on the curves (point c) at 200 mph when the hydraulically operated disc brakes can be used.
shirt said:
they've done development work for renault's past f1 efforts as well as WRC and the engine in the veyron. the jcb dieselmax previously discussed was theirs, and their bread and butter is engine and gearbox development for automotive OEM's, military projects etc.
for us they managed to wring 15% more power and 8% better fuel efficiency out of a 20 year old design which is bloody good going for a 6 tonne 1000hp diesel!
if i had an engine project with very specific requirements [including packaging] they would be my first choice.
Did you work on Dieselmax?for us they managed to wring 15% more power and 8% better fuel efficiency out of a 20 year old design which is bloody good going for a 6 tonne 1000hp diesel!
if i had an engine project with very specific requirements [including packaging] they would be my first choice.
Silent1 said:
But i think my point still stands that F1 brakes have to do lots of applications per lap whereas eurofighter brakes go from cold to full application and then they're used very little after that, so the total energy they dissipate per 'lap' must be greater for a formula 1 car and as such would possibly be slightly more effective?
Which is precisely what we are doing.CraigyMc said:
On the positive side, bloodhound doesn't weigh as much as the Typhoon - perhaps half as much - and only applies the carbon brakes at about 200mph max. The rest of the "slow down from 1000mph" is aerodynamic.
About 7800kg fully fuelled, about 6400kg at the end of a run (assuming nothing has fallen off)!New BBC update too.
Featuring quite a lot of the parts I designed (fin, upper chassis)
Proud moment.
http://www.bbc.co.uk/news/science-environment-2592...
Featuring quite a lot of the parts I designed (fin, upper chassis)
Proud moment.
http://www.bbc.co.uk/news/science-environment-2592...
All parts have been designed with FOS of a minimum equivalent to that of a commercial airliner, where we have cases that we are unsure about loads etc we have added margins as appropriate.
Things such as suspension parts we have carried out fatigue & also load testing to validate or assumptions, thus far we've proven pretty good.
Things such as suspension parts we have carried out fatigue & also load testing to validate or assumptions, thus far we've proven pretty good.
Some more pornography for you.
AMAD mounting plate, this is the part that mounts the EJ200 AMAD gearbox into the car.
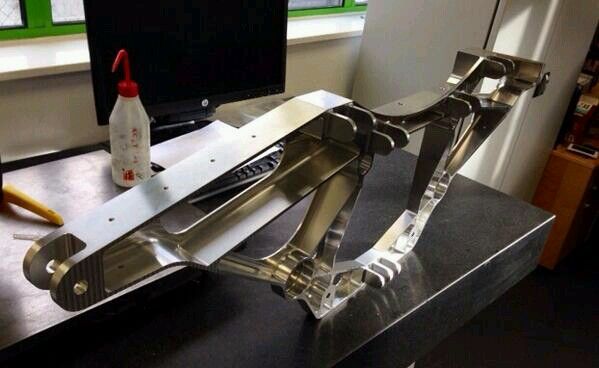
Fin shear plate, 2m long. It's the interface between the upper chassis & the tail fin, will be anodised & primed to aid bonding, started as an 800kg billet, part weight is 7.8kg!!!!
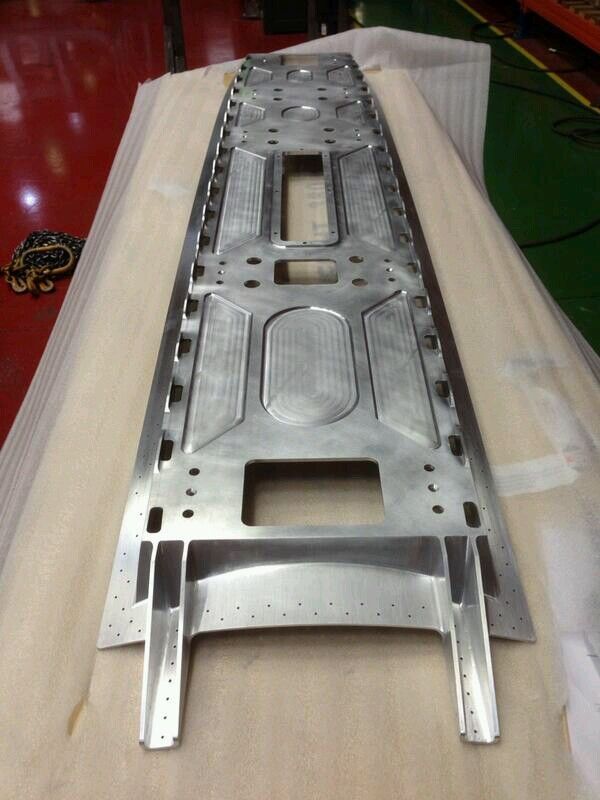
AMAD mounting plate, this is the part that mounts the EJ200 AMAD gearbox into the car.
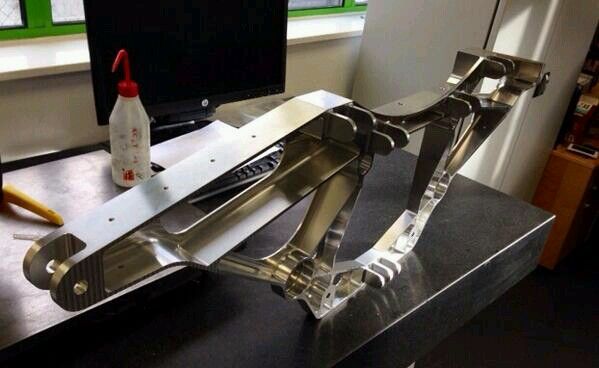
Fin shear plate, 2m long. It's the interface between the upper chassis & the tail fin, will be anodised & primed to aid bonding, started as an 800kg billet, part weight is 7.8kg!!!!

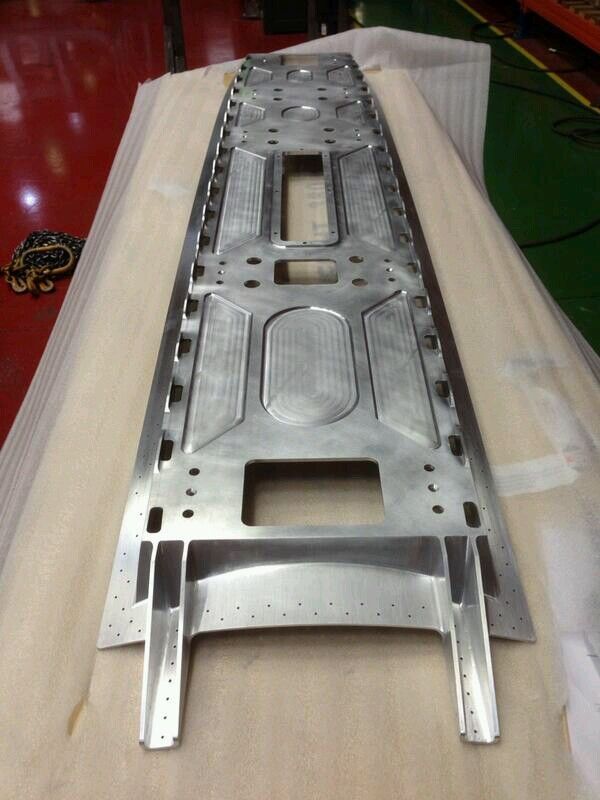
Edited by IN51GHT on Friday 7th February 06:40
Gassing Station | General Gassing | Top of Page | What's New | My Stuff