KIT CAR DEVELOPMENT COSTS?
Discussion
Russ Bost said:
During the last 10 years I can think of about 5 or 6 manufacturers that have actually produced something new & interesting within the kitcar market & at least 3 of those have posted on here, all the rest keep on producing the same old thing, occasionaly adding a very slight new twist to a dreadfully jaded old product.
I truly wish it were not the case, but the kitcar market has already contracted massively in the last couple of years & will continue to do so unless we as manufacturers come up with some genuinely new & exciting products, the kitcar market will look very different in another 5 years I think you'll find
As may on/off interest in Kit cars goes back to the very early 1980's I feel I can comment. The kit car industry is always changing. I see the current boom of Sevens like that of the beach buggy in the 60's, a pasting fad. The real problem is and has been since the 80's reaching customers buyers.I truly wish it were not the case, but the kitcar market has already contracted massively in the last couple of years & will continue to do so unless we as manufacturers come up with some genuinely new & exciting products, the kitcar market will look very different in another 5 years I think you'll find

A few weeks a go I meet a group of young (19-23) drive. All had hotted up small hatch backs, mostly done by themselfs. A couple had totally rebuild their cars and upgraded them at the same time. Most had spend 4 or 5 thousand on modifying they cars. Just to be different. I had a few copies of CKC in my car and showed these to them. They show a lot of interest, but pointed out they could not afford two cars, as most of the kit car could never replace a their cars day to day. This is why the market is contracting. All that's needed are a bit of weather protection and better marketing to drivers like this.
One of them put forwards the idea of a coupe Seven! A two seater with a bit of space for bags. A Seven GTI, as they put it.
To get this thread back on track we now have:
£2k to have it drawn in CAD to scale .
£5k to an engineer to design chassis/suspension geometry.
£5k to a fabricator to provide jigs for chassis/suspension.
£10k for CNC buck and molds
(most people would do at least one of those themselves)
0.5k for set of wheels/tyres/brakes
0.5k seats/instruments/trim
1k for specialists for ecu complications from a donor etc
1k engine and gearbox
1k for the first chassis produced plus any mods required.
1k labour for prototype assembly.
1k for IVA, registration fee, road tax and insurance.
On the road for 31k or less if you do some of the chassis and body tasks yourself
10k for desk/PC/van/office carpet/racks/tools/chair/coffee machine etc.
10k for start up stock of lights/suspension/chassis/ball joints, etc
In business for 31+21=52K
5k to exhibit at 5 shows inc fuel/hotel/food.
2k for company set up/accountant/bank chargers/product liability insurance.
1k for 4 adverts in magazines.
5k for small unit rent/rates/heating/electric/telephone.
recurring costs are 14K
2k gross profit per kit sold.
10k directors salary whilst building up trade.
so that's a first year loss of 8K profit - 10K salary - 14K costs = 16K down
2k gross profit per kit sold.
50K income
14K recurring costs
30k directors salary
6K to pay off initial debts and reinvest
Is this feasible?, even if you get to this by year two you won't have covered the first year debt until the end of year four.
- Bodywork and chassis design
£2k to have it drawn in CAD to scale .
£5k to an engineer to design chassis/suspension geometry.
£5k to a fabricator to provide jigs for chassis/suspension.
£10k for CNC buck and molds
(most people would do at least one of those themselves)
- Other parts needed
0.5k for set of wheels/tyres/brakes
0.5k seats/instruments/trim
1k for specialists for ecu complications from a donor etc
1k engine and gearbox
- Assemble first car
1k for the first chassis produced plus any mods required.
1k labour for prototype assembly.
1k for IVA, registration fee, road tax and insurance.
On the road for 31k or less if you do some of the chassis and body tasks yourself
- Start the business (non recurring)
10k for desk/PC/van/office carpet/racks/tools/chair/coffee machine etc.
10k for start up stock of lights/suspension/chassis/ball joints, etc
In business for 31+21=52K
- Start the business (recurring)
5k to exhibit at 5 shows inc fuel/hotel/food.
2k for company set up/accountant/bank chargers/product liability insurance.
1k for 4 adverts in magazines.
5k for small unit rent/rates/heating/electric/telephone.
recurring costs are 14K
- ...and then
2k gross profit per kit sold.
10k directors salary whilst building up trade.
so that's a first year loss of 8K profit - 10K salary - 14K costs = 16K down
- ...and hopefully
2k gross profit per kit sold.
50K income
14K recurring costs
30k directors salary
6K to pay off initial debts and reinvest
Is this feasible?, even if you get to this by year two you won't have covered the first year debt until the end of year four.
KDIcarmad said:
As may on/off interest in Kit cars goes back to the very early 1980's I feel I can comment. The kit car industry is always changing. I see the current boom of Sevens like that of the beach buggy in the 60's, a pasting fad. The real problem is and has been since the 80's reaching customers buyers.
A few weeks a go I meet a group of young (19-23) drive. All had hotted up small hatch backs, mostly done by themselfs. A couple had totally rebuild their cars and upgraded them at the same time. Most had spend 4 or 5 thousand on modifying they cars. Just to be different. I had a few copies of CKC in my car and showed these to them. They show a lot of interest, but pointed out they could not afford two cars, as most of the kit car could never replace a their cars day to day. This is why the market is contracting. All that's needed are a bit of weather protection and better marketing to drivers like this.
One of them put forwards the idea of a coupe Seven! A two seater with a bit of space for bags. A Seven GTI, as they put it.
The idea of a Seven with everyday usability does keep popping up in these discussions - it's something that might even interest me. Something that goes like a Seven but has decent weather protection and maybe a bit of a boot. But the extra weight of the doors, roof and boot, it's bound to blunt the performance a bit, and then it starts to sound like an MX5, albeit a modified one. (Sylva/SSC Stylus anyone?)A few weeks a go I meet a group of young (19-23) drive. All had hotted up small hatch backs, mostly done by themselfs. A couple had totally rebuild their cars and upgraded them at the same time. Most had spend 4 or 5 thousand on modifying they cars. Just to be different. I had a few copies of CKC in my car and showed these to them. They show a lot of interest, but pointed out they could not afford two cars, as most of the kit car could never replace a their cars day to day. This is why the market is contracting. All that's needed are a bit of weather protection and better marketing to drivers like this.
One of them put forwards the idea of a coupe Seven! A two seater with a bit of space for bags. A Seven GTI, as they put it.
So there's the challenge, can the industry come up with an everyday car that keeps enough Seven style performance and looks good & different enough and still make it cheap enough to make sense to the lads who warm up their hatches?
Current market suggests not ...
Frankthered said:
The idea of a Seven with everyday usability does keep popping up in these discussions - it's something that might even interest me. Something that goes like a Seven but has decent weather protection and maybe a bit of a boot. But the extra weight of the doors, roof and boot, it's bound to blunt the performance a bit, and then it starts to sound like an MX5, albeit a modified one. (Sylva/SSC Stylus anyone?)
So there's the challenge, can the industry come up with an everyday car that keeps enough Seven style performance and looks good & different enough and still make it cheap enough to make sense to the lads who warm up their hatches?
Current market suggests not ...
Well there have been four seater kits, Quantum sold a fairly successfull one based on the fiesta.So there's the challenge, can the industry come up with an everyday car that keeps enough Seven style performance and looks good & different enough and still make it cheap enough to make sense to the lads who warm up their hatches?
Current market suggests not ...
Since you mentioned Caterham, how about something like this:
It's a Caterham 21 with extra length and height to make a 2+2. Spyder make replacement chassis for the Lotus Elan Plus2 and Excel, either of which could fit and provide proven handling and driveline options.
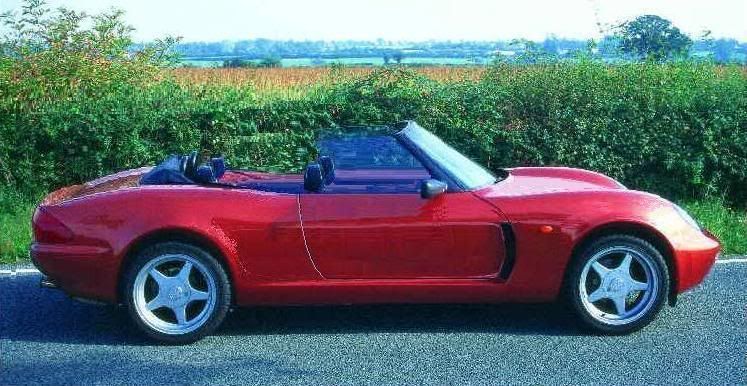
Keep it simple and you have a very focused 2+2 for those who can't justify a car without the extra practicality. It would still see off most production cars and there are plenty of V6s around that might fit without increasing the weight too much.
Frankthered said:
The idea of a Seven with everyday usability does keep popping up in these discussions - it's something that might even interest me. Something that goes like a Seven but has decent weather protection and maybe a bit of a boot. But the extra weight of the doors, roof and boot, it's bound to blunt the performance a bit, and then it starts to sound like an MX5, albeit a modified one. (Sylva/SSC Stylus anyone?)
So there's the challenge, can the industry come up with an everyday car that keeps enough Seven style performance and looks good & different enough and still make it cheap enough to make sense to the lads who warm up their hatches?
Current market suggests not ...
I have always had a hankering for the CC Cyclone, the styling was a bit odd in places as was its donor, however it really could have been the natural development of the LSIS market, it had a proper roof, a heater that actually worked and whilst not as easy to get out of as a normal car it didn't require the owner to be a contortionist when the weather was inclement. It really was a LSIS you could use every day, its just a shame that a divorce got in the way and it met its demise.So there's the challenge, can the industry come up with an everyday car that keeps enough Seven style performance and looks good & different enough and still make it cheap enough to make sense to the lads who warm up their hatches?
Current market suggests not ...
Frankthered said:
The idea of a Seven with everyday usability does keep popping up in these discussions - it's something that might even interest me. Something that goes like a Seven but has decent weather protection and maybe a bit of a boot. But the extra weight of the doors, roof and boot, it's bound to blunt the performance a bit, and then it starts to sound like an MX5, albeit a modified one. (Sylva/SSC Stylus anyone?)
So there's the challenge, can the industry come up with an everyday car that keeps enough Seven style performance and looks good & different enough and still make it cheap enough to make sense to the lads who warm up their hatches?
Current market suggests not ...
How this a for more usable Sevenish car...So there's the challenge, can the industry come up with an everyday car that keeps enough Seven style performance and looks good & different enough and still make it cheap enough to make sense to the lads who warm up their hatches?
Current market suggests not ...


The Maxton rollerskate from 1992-3, sold in USA. Total of around 50 sold. Very much the car you want. I think the back looks better than the blue car.
Also like the CC Cyclone, wonder what happend to the molds and jigs!
Edited by KDIcarmad on Tuesday 6th March 18:52
Anything with complex curves like that would be expensive to produce. A set of patterns may cost £10k for a pro to do it and moulds for those shapes could be expensive, A, because they are large and B, because those shapes would require several release splits in the moulds. Then the parts you cast will need all the split lines sanding and polishing out. No problem, all can be done but again it is all down to how much of the work Fred can do then hopefully his mate Salesmen Sam will be able to get a few sold.
So could it stack up? A relatively high set up cost using pros all round can be justified if a better product is produced that could sell in the sort of numbers that will ammortise the set up costs in a reasonable time frame. A calc required from Business brain Bob!
Just noticed the flat screen, now that would save a lot of money.
So could it stack up? A relatively high set up cost using pros all round can be justified if a better product is produced that could sell in the sort of numbers that will ammortise the set up costs in a reasonable time frame. A calc required from Business brain Bob!
Just noticed the flat screen, now that would save a lot of money.
Edited by Stuart Mills on Tuesday 6th March 20:33
Coming in a bit late on this topic, we have played this game from several angles. We have done it with real car firms, car firms that hope to be and kit car firms. Cost is dependent on what you want the end result to be. Spend money on design, engineering and tooling and you save on build cost. Having done the sums, to produce a decent kit car allow 100k for engineering and tooling and 100k to run it for a year (shows, stock, labour). Then it is up to you how you recover 200k in one year - 100x2k or 2x100k.
The reality is most people get conspicuously good value if they buy a good second hand car. Doors that fit and work are one of the biggest challenges you can set yourself. So the kit car has to deliver something amazing in looks or performance.
Good luck with the thread. We do it for a job.
The reality is most people get conspicuously good value if they buy a good second hand car. Doors that fit and work are one of the biggest challenges you can set yourself. So the kit car has to deliver something amazing in looks or performance.
Good luck with the thread. We do it for a job.
As I said on another thread this Maxton looks very much like a MK1 Sprite to me. The bulbous lamps and frontal shape is uncannily similar
I cannot see this as progress. The Mk 1 Austin Healey Sprite was designed` over 50 years ago. Wonderful cars I owned several. Then.
I expect I am wrong in my views.
I have not seen the actual car but it is certainly reminiscent of the Mk1 Sprite and I would hope we are able to find a more svelte bodyshape.
I like the Sprite but it is hardly avante garde sports car design?
I cannot see this as progress. The Mk 1 Austin Healey Sprite was designed` over 50 years ago. Wonderful cars I owned several. Then.
I expect I am wrong in my views.
I have not seen the actual car but it is certainly reminiscent of the Mk1 Sprite and I would hope we are able to find a more svelte bodyshape.
I like the Sprite but it is hardly avante garde sports car design?
I have heard 100k mentioned in the past as a ball park figure but again if Jack of all trades were a good sales man then it could be considerably less, but then the end result could be a considerably less desirable car.
Coming back to the KDIcarmad post though, here another potential angle emerges.
Take an old kit, convert it to modern running gear, cut chunks out of the grp and reshape to sharpen the lines and introduce modern lights in the correct IVA positions. Then tidy it all up. Get a pro paint job done, show it, get some orders having quoted a 3 months lead time, take moulds of it, deliver.
When I made the Sonic7 pattern I used a Rocket chassis and wrapped flex ply around to achieve the curves. I was aiming at a bodied Rocket and so the wheel base/engine position etc remained the same. I then used jelutong to form the awkward sections. I am not a fan of the laser cut foam approach, you finish up with a large bill and a massive task of finishing the surface to a suitable standard.
Coming back to the KDIcarmad post though, here another potential angle emerges.
Take an old kit, convert it to modern running gear, cut chunks out of the grp and reshape to sharpen the lines and introduce modern lights in the correct IVA positions. Then tidy it all up. Get a pro paint job done, show it, get some orders having quoted a 3 months lead time, take moulds of it, deliver.
When I made the Sonic7 pattern I used a Rocket chassis and wrapped flex ply around to achieve the curves. I was aiming at a bodied Rocket and so the wheel base/engine position etc remained the same. I then used jelutong to form the awkward sections. I am not a fan of the laser cut foam approach, you finish up with a large bill and a massive task of finishing the surface to a suitable standard.
You have to look at the labour intensive methods from the past. We used wood and clay and took time. That method still holds true today, and if you are a serial developer you can re-use wood, styrofoam block and clay! We recently estimated laser scan a model, smooth the surfaces and then CNC cut body moulds at 60k. You should be able to build a buck, style and splash off it for half that.......but it will be unbalanced and will not be mirror finish. You then have to spend time on each body finishing it.
Why do the people who engineer vehicles not do their own cars? Because they know how difficult it is.
Why do the people who engineer vehicles not do their own cars? Because they know how difficult it is.
Doors are expensive and difficult to get right. BUT
Beauford, uses doors from a Mini.
MEV Superlight uses lightened MX5 doors with a GRP cap.
Didn't Ginetta use a Fiesta door?
The problem is finding one of a suitable height. It is amazing how 20mm difference between a saloon and a sports car door change the whole balance.
Beauford, uses doors from a Mini.
MEV Superlight uses lightened MX5 doors with a GRP cap.
Didn't Ginetta use a Fiesta door?
The problem is finding one of a suitable height. It is amazing how 20mm difference between a saloon and a sports car door change the whole balance.
John@arden said:
You have to look at the labour intensive methods from the past. We used wood and clay and took time. That method still holds true today, and if you are a serial developer you can re-use wood, styrofoam block and clay! We recently estimated laser scan a model, smooth the surfaces and then CNC cut body moulds at 60k. You should be able to build a buck, style and splash off it for half that.......but it will be unbalanced and will not be mirror finish. You then have to spend time on each body finishing it.
Why do the people who engineer vehicles not do their own cars? Because they know how difficult it is.
Spot on. Your figures sound about right to me.Why do the people who engineer vehicles not do their own cars? Because they know how difficult it is.
2k to cad a body sounds very low, you're unlikely to get anything other than a basic styling surface of a simple design for that.
egomeister said:
John@arden said:
You have to look at the labour intensive methods from the past. We used wood and clay and took time. That method still holds true today, and if you are a serial developer you can re-use wood, styrofoam block and clay! We recently estimated laser scan a model, smooth the surfaces and then CNC cut body moulds at 60k. You should be able to build a buck, style and splash off it for half that.......but it will be unbalanced and will not be mirror finish. You then have to spend time on each body finishing it.
Why do the people who engineer vehicles not do their own cars? Because they know how difficult it is.
Spot on. Your figures sound about right to me.Why do the people who engineer vehicles not do their own cars? Because they know how difficult it is.
2k to cad a body sounds very low, you're unlikely to get anything other than a basic styling surface of a simple design for that.
What is the most effective way to a buck?
- CNC foam or resin
- hand formed filler/clay
- commision an ally body and take molds from that
- some combination of the above, i.e. rough cut CNC with tricky areas CNC'd to a better finish, the rest hand finished
cymtriks said:
So the earlier figures of 2K for a CAD model and 10K for a hard foam CNC buck were way out?
What is the most effective way to a buck?
How much of someones time is 2k going to buy you, week and a half perhaps? You're not going to get much of a body in that time - maybe a simple surface with some basic engineering for lights etc. You could possibly do a low density buck for taking grp moulds from for 10k, but a car is a big lump of material... cost would be very dependant upon shape and complexity.What is the most effective way to a buck?
- CNC foam or resin
- hand formed filler/clay
- commision an ally body and take molds from that
- some combination of the above, i.e. rough cut CNC with tricky areas CNC'd to a better finish, the rest hand finished
John's suggestion of 60k for a body sounds reasonable. For that, you should get a decent styling surface and then body engineering of your panels, so things like your closures and seals work properly and fit nicely. I should think you'd also be cutting patternwork for your part rather than a one piece body, meaning you get straight into moulding components rather than working out how you car going to split the car up.
I would always see the CAD and CNC route as the most effective, partially because thats what I do every day and partially because I've had the headaches when working on a project that was all done by hand. The main issue is see for the kit car industry is that there is not the capital available to go down this route in most cases, hence having to resort to the blood sweat and tears of doing everything manually.
What is it that drives the cost of a CNC buck?
Is it the size of machine, in which cast a mold made up of sections created by a smaller machine would be a cheaper route?
Is it the surface finish required in wich case there might be a compromise surface finish which would be dimensionally accurate but would require hand finishing?
How much of the 60K quoted is creating the styling on CAD and how much is doing the CNC?
At these prices the cost of getting started is going to be too great for any new companies to consider.
Is it the size of machine, in which cast a mold made up of sections created by a smaller machine would be a cheaper route?
Is it the surface finish required in wich case there might be a compromise surface finish which would be dimensionally accurate but would require hand finishing?
How much of the 60K quoted is creating the styling on CAD and how much is doing the CNC?
At these prices the cost of getting started is going to be too great for any new companies to consider.
i asked a couple of kit car firms about the costs of a one off kit, it seamed to me it was a completely closed shop
i asked who to go to for the laminatling as most sub this out, no one would tell me
i was thinking of doing a one off kit for myself using a doner car for everything, just a body conversion really, i ve seen one i like.
heres a link i posted on dnas web site
http://www.dnaoc.co.uk/index.php/topic,3028.0.html
i asked who to go to for the laminatling as most sub this out, no one would tell me
i was thinking of doing a one off kit for myself using a doner car for everything, just a body conversion really, i ve seen one i like.
heres a link i posted on dnas web site
http://www.dnaoc.co.uk/index.php/topic,3028.0.html
cymtriks said:
What is it that drives the cost of a CNC buck?
Is it the size of machine, in which cast a mold made up of sections created by a smaller machine would be a cheaper route?
Is it the surface finish required in wich case there might be a compromise surface finish which would be dimensionally accurate but would require hand finishing?
How much of the 60K quoted is creating the styling on CAD and how much is doing the CNC?
At these prices the cost of getting started is going to be too great for any new companies to consider.
The main areas of cost are volume of material used and complexity of shape to be machined. Small details mean smaller cutters and longer machining time - the ideal shape would be a nice open sweeping surface allowing easy access with a large cutter.Is it the size of machine, in which cast a mold made up of sections created by a smaller machine would be a cheaper route?
Is it the surface finish required in wich case there might be a compromise surface finish which would be dimensionally accurate but would require hand finishing?
How much of the 60K quoted is creating the styling on CAD and how much is doing the CNC?
At these prices the cost of getting started is going to be too great for any new companies to consider.
Size if machine is less critical, but if you can do it in fewer pieces there is less setting up and re-assembly to do and therefore less cost everything else being equal. If you are cutting engineered panel patterns then these would be smaller than a full car anyway, and much more likely to fit on a machine in one - perhaps another benefit of upfront investment in design.
You could make savings by hand finishing yourself, but the more work done on machine the better the final product will be. It's also very easy to damage a pattern by over zealous sanding, leaving dips in the surface!
I'd say the split between design and tooling would be about 50/50 on the 60k quote, but perhaps John can provide a bit more insight into that? Certainly you could spend whatever you liked on design, depending on just how good you want your final product to be. They are scary numbers for a kit car builder for sure, which is why you rarely see kit cars done in this way. Ultimately if the kit car industry wants to have products that can compete as an alternative to mainstream built cars, it has to find a way to raise the quality of its products - a tricky investment to make with no guarantee of the sale to pay back that investment.
Gassing Station | Kit Cars | Top of Page | What's New | My Stuff