KIT CAR DEVELOPMENT COSTS?
Discussion
There is a very interesting thread re car body buck building without cnc here
http://www.locostbuilders.co.uk/viewthread.php?tid...
Clearly this is a quality item. It shows full detail from when he started in 2006 up to date.
I guess he is at an advantage as it is a replica so he knows what to expect. Taking a 2D sketch or an idea firmly pictured in your mind and spending massive time creating a buck is a brave move.
That is where clay or cladding timber frame come in. At least they are cheap and can be altered and you get a real sense of proportions before it is anywhere near finished. When it starts to drift from your dream you can reach for the large hammer or pat your self on your back once you have an early warning or confidence boost as the case may be.
A full body for a car can take months and months only to provide disappointment, again perhaps a good case for getting the pro's involved but the sense of personal achievement would then be considerably reduced.
http://www.locostbuilders.co.uk/viewthread.php?tid...
Clearly this is a quality item. It shows full detail from when he started in 2006 up to date.
I guess he is at an advantage as it is a replica so he knows what to expect. Taking a 2D sketch or an idea firmly pictured in your mind and spending massive time creating a buck is a brave move.
That is where clay or cladding timber frame come in. At least they are cheap and can be altered and you get a real sense of proportions before it is anywhere near finished. When it starts to drift from your dream you can reach for the large hammer or pat your self on your back once you have an early warning or confidence boost as the case may be.
A full body for a car can take months and months only to provide disappointment, again perhaps a good case for getting the pro's involved but the sense of personal achievement would then be considerably reduced.
Stuart Mills said:
There is a very interesting thread re car body buck building without cnc here
http://www.locostbuilders.co.uk/viewthread.php?tid...
Clearly this is a quality item. It shows full detail from when he started in 2006 up to date.
I guess he is at an advantage as it is a replica so he knows what to expect. Taking a 2D sketch or an idea firmly pictured in your mind and spending massive time creating a buck is a brave move.
That is where clay or cladding timber frame come in. At least they are cheap and can be altered and you get a real sense of proportions before it is anywhere near finished. When it starts to drift from your dream you can reach for the large hammer or pat your self on your back once you have an early warning or confidence boost as the case may be.
A full body for a car can take months and months only to provide disappointment, again perhaps a good case for getting the pro's involved but the sense of personal achievement would then be considerably reduced.
Great thread. That really highlights the effort required to manufacture a body by hand to a high standard.http://www.locostbuilders.co.uk/viewthread.php?tid...
Clearly this is a quality item. It shows full detail from when he started in 2006 up to date.
I guess he is at an advantage as it is a replica so he knows what to expect. Taking a 2D sketch or an idea firmly pictured in your mind and spending massive time creating a buck is a brave move.
That is where clay or cladding timber frame come in. At least they are cheap and can be altered and you get a real sense of proportions before it is anywhere near finished. When it starts to drift from your dream you can reach for the large hammer or pat your self on your back once you have an early warning or confidence boost as the case may be.
A full body for a car can take months and months only to provide disappointment, again perhaps a good case for getting the pro's involved but the sense of personal achievement would then be considerably reduced.
Not surprisingly given his experience Stuart Mills is on the money again with his comments and an excellent thread for us to research.
I have built and bodied various specials over the years.
My bodies are little more than variations on the sheet alloy approach which means that complex double curves and sexy profiles are out on my attempts.
My reason for seeking a complex distinctive new Kit Car shape is that I am convinced there are individuals about who can and should create a really different aerodynamic shape which could then be made within the UK in volume for builders.
Clearly the likes of Stuart Mills could achieve this.
Indeed he does with his own excellent distintive, individual and very good, products. The MEV X5 and his other designs on the MX5 based cars are certainly the kits that I would look at currently.
The single donor with fully independent suspension, superb twin cam engine, perfect ride height and all in one package is my reason for thinking this is an excellent result. Virtually every instrument and mechanical part is available with one purchase of an MX5, of which there are plenty around at sub £700.
That is the kit to beat currently IMO.
Forty ++ years of kit building have made me appreciate just how of a much of a saving of time an effort a one donor kit of this quality means. I would expect a reduction of at least half in the build time over a Bitsa like my Robin hood with Alfa Romeo 2 litre engine box and Ford everything else.
A right pig to source.
It has taken me over a year to finish it.
If I had known about the MEV kits when I started the RH I would have got one from the start and had a lot more time in the sun in Italy.
But then as my OH says I am nuts. Sadly all my friends agree. And my enemies!!
Never mind the RH will be on the road shortly (Ish!!!!!!!)
I have built and bodied various specials over the years.
My bodies are little more than variations on the sheet alloy approach which means that complex double curves and sexy profiles are out on my attempts.
My reason for seeking a complex distinctive new Kit Car shape is that I am convinced there are individuals about who can and should create a really different aerodynamic shape which could then be made within the UK in volume for builders.
Clearly the likes of Stuart Mills could achieve this.
Indeed he does with his own excellent distintive, individual and very good, products. The MEV X5 and his other designs on the MX5 based cars are certainly the kits that I would look at currently.
The single donor with fully independent suspension, superb twin cam engine, perfect ride height and all in one package is my reason for thinking this is an excellent result. Virtually every instrument and mechanical part is available with one purchase of an MX5, of which there are plenty around at sub £700.
That is the kit to beat currently IMO.
Forty ++ years of kit building have made me appreciate just how of a much of a saving of time an effort a one donor kit of this quality means. I would expect a reduction of at least half in the build time over a Bitsa like my Robin hood with Alfa Romeo 2 litre engine box and Ford everything else.
A right pig to source.
It has taken me over a year to finish it.
If I had known about the MEV kits when I started the RH I would have got one from the start and had a lot more time in the sun in Italy.
But then as my OH says I am nuts. Sadly all my friends agree. And my enemies!!
Never mind the RH will be on the road shortly (Ish!!!!!!!)
Thank you for your kind words Steffan.
Here is a link of interest.
http://www.youtube.com/watch?v=rBTaIck42GM&fea...
Anyone guess what this would cost?
I don't know the answers BTW so it would be very interesting to hear opinions or fact from those in the know.
Drawing of initial concept sketch say £?
Fully dimensioned/scaled working drawings say £?
CAD conversion for machine prog say £?
CNC polystyrene or polyurethane block milling say £?
Form returns for opening sections (boot/bonnet/doors)£?
Interior pattern forming for inner wheel arches/dash ect say £?
Finish in resin say £?
Take moulds in GRP with bolt on relief splits say £?
The above all assumes a reverse engineering approach to chassis/function/fit.
Here is a link of interest.
http://www.youtube.com/watch?v=rBTaIck42GM&fea...
Anyone guess what this would cost?
I don't know the answers BTW so it would be very interesting to hear opinions or fact from those in the know.
Drawing of initial concept sketch say £?
Fully dimensioned/scaled working drawings say £?
CAD conversion for machine prog say £?
CNC polystyrene or polyurethane block milling say £?
Form returns for opening sections (boot/bonnet/doors)£?
Interior pattern forming for inner wheel arches/dash ect say £?
Finish in resin say £?
Take moulds in GRP with bolt on relief splits say £?
The above all assumes a reverse engineering approach to chassis/function/fit.
Stuart Mills said:
Thank you for your kind words Steffan.
Here is a link of interest.
http://www.youtube.com/watch?v=rBTaIck42GM&fea...
Anyone guess what this would cost?
I don't know the answers BTW so it would be very interesting to hear opinions or fact from those in the know.
Drawing of initial concept sketch say £?
Fully dimensioned/scaled working drawings say £?
CAD conversion for machine prog say £?
CNC polystyrene or polyurethane block milling say £?
Form returns for opening sections (boot/bonnet/doors)£?
Interior pattern forming for inner wheel arches/dash ect say £?
Finish in resin say £?
Take moulds in GRP with bolt on relief splits say £?
The above all assumes a reverse engineering approach to chassis/function/fit.
We need a CAD expert in this type of engineering to tell us the reality.Here is a link of interest.
http://www.youtube.com/watch?v=rBTaIck42GM&fea...
Anyone guess what this would cost?
I don't know the answers BTW so it would be very interesting to hear opinions or fact from those in the know.
Drawing of initial concept sketch say £?
Fully dimensioned/scaled working drawings say £?
CAD conversion for machine prog say £?
CNC polystyrene or polyurethane block milling say £?
Form returns for opening sections (boot/bonnet/doors)£?
Interior pattern forming for inner wheel arches/dash ect say £?
Finish in resin say £?
Take moulds in GRP with bolt on relief splits say £?
The above all assumes a reverse engineering approach to chassis/function/fit.
I would think that the costs would be totally prohibitive for Kit Car use.
Taking a general stab at possible figures I guess (yes guess!!)
Drawing of initial concept sketch possibly £5000 to £15,000
Fully dimensioned/scaled working drawings possibly £10,000
CAD conversion for machine prog possibly £5000
CNC polystyrene or polyurethane block milling possibly £20,000
Form returns for opening sections (boot/bonnet/doors)possibly £10,000
Interior pattern forming for inner wheel arches/dash ect possibly £10,000
Finish in resin possibly £10,000
Take moulds in GRP with bolt on relief splits possibly £25,000
These figures add up to the order of something over £100K.
Could be totally wrong and wildly out but it is at least a stab at a suggestion.
No more.
It depends largely on the cutting cost and running cost of the big cutter which I have had to guess.
My only direct manufacturing experience has been in Zund work on lighting assemblies and much smaller CAD based cutting programs on plastic components.
I have a complete cost analysis of a Kit Car project built in the UK over the last two years producing a very distinctive shape and car which a client of mine has been developing.
That would give a pretty precise figure for a real time project.
This has cost more than my analysis above.
I will ask the question whether my client wants any of this project known.
I cannot identify anything until then.
CAD-reader software imports and reads DXF files with Siemens ShopMill software.
If you are going to machine an entire car to mould from, would it not pay to machine the moulds from silver steel(hardenable) or similar?
Large production runs would be easier and better quality than a gel/grp mould.
1point7bar said:
CAD-reader software imports and reads DXF files with Siemens ShopMill software.
If you are going to machine an entire car to mould from, would it not pay to machine the moulds from silver steel(hardenable) or similar?
Large production runs would be easier and better quality than a gel/grp mould.
You may well be right but what would the costs be for that kind of cutting power. You are sculpturing a seriously big piece of metal. And the handling capacity of a machine required to be capable of managing a blank that size.If you are going to machine an entire car to mould from, would it not pay to machine the moulds from silver steel(hardenable) or similar?
Large production runs would be easier and better quality than a gel/grp mould.
We are talking kit cars here a production run of hundreds of bodies would be an outstanding success. In fact probably the market leader!
I would think this a prohibitively expensive option.
But I watch with interest.
Large tooling is made of smaller precision ground blocks that bolt to a backing plate. You are not going to press these sections so the tooling could be quite light in comparison.
CNC routines start with a plastic workpiece to check for tool crashes.
Machines large enough to do a car in one piece are rare and unnecessary.
CNC routines start with a plastic workpiece to check for tool crashes.
Machines large enough to do a car in one piece are rare and unnecessary.
Edited by 1point7bar on Wednesday 14th March 19:40
1point7bar said:
Large tooling is made of smaller precision ground blocks that bolt to a backing plate. You are not going to press these sections so the tooling could be quite light in comparison.
CNC routines start with a plastic workpiece to check for tool crashes.
Machines large enough to do a car in one piece are rare and unnecessary.
Interesting approach. What would it cost?CNC routines start with a plastic workpiece to check for tool crashes.
Machines large enough to do a car in one piece are rare and unnecessary.
Edited by 1point7bar on Wednesday 14th March 19:40
Stuart Mills said:
Thank you for your kind words Steffan.
Here is a link of interest.
http://www.youtube.com/watch?v=rBTaIck42GM&fea...
Anyone guess what this would cost?
I don't know the answers BTW so it would be very interesting to hear opinions or fact from those in the know.
.....
The above all assumes a reverse engineering approach to chassis/function/fit.
This is the Olme Spyder - do you know the story behind this? Long story short: bloke in Sweden builds car, effectively gets it IVA'ed without body. Masters students at Umeå design & build body for him. I don't know, but would guess all at minimal if any cost to the bloke (at least for design, CAD & buck): good project & publicity for UniversityHere is a link of interest.
http://www.youtube.com/watch?v=rBTaIck42GM&fea...
Anyone guess what this would cost?
I don't know the answers BTW so it would be very interesting to hear opinions or fact from those in the know.
.....
The above all assumes a reverse engineering approach to chassis/function/fit.
slight longer version here: http://www.cardesignnews.com/site/home/rss_display...
gallery from one if the students: http://www.coroflot.com/thepureautostudio/OLME-Spy...
composite image from gallery:

Kinda have mixed feelings about this one; the chassis isn't the greatest - rear deck area problem in particular (compare to rear deck height of, say, a Sonic...

Transport Design courses have sprung up like mushrooms over the last 20 years and Umeå in Sweden & Pforzheim in Germany, & IED in Italy seem to be particularly well equipped. There are now about half a dozen courses in the UK but I don't know if any have this kind of kit. Even if you can find a partner, get the brief and everything else right, student quality can vary considerably between years; IED have exhibited at Geneva for some years now, below is '08 project (top) vs. 2012. I know which I prefer...

Very interesting: the pace of change in Car design and prototype build has clearly been changing! Ain't technology wonderful!
However it seems probable to me that the raw cost of each of the three cars shown would move all these project well outside the Kit car enthusiasts price range.
Kit car manufacture in the UK is a relatively low volume business. Kit Car sales are very price sensitive.
Without revealing manufacturers secrets I think we can confirm that very few kit car manufacturers assemble more than a car a week and generally significantly less (see Raven and Pinch Kit Car Manufacture in UK).
Westfield and a few others may exceed that number but the majority of manufacturers must look for a return on a very low volume of kit sales.
I simply cannot see the economics working for this type of complex product.
But it is certainly very interesting to see how the boundaries are being pushed out in car design. Very interesting indeed.
Now what we have to do is harness that design capacity to actually designing and producing a prototype Kit car which could be produced at a volume and price the UK Kit Car enthusiasts could afford.
That really is a challenge!
On we go!
However it seems probable to me that the raw cost of each of the three cars shown would move all these project well outside the Kit car enthusiasts price range.
Kit car manufacture in the UK is a relatively low volume business. Kit Car sales are very price sensitive.
Without revealing manufacturers secrets I think we can confirm that very few kit car manufacturers assemble more than a car a week and generally significantly less (see Raven and Pinch Kit Car Manufacture in UK).
Westfield and a few others may exceed that number but the majority of manufacturers must look for a return on a very low volume of kit sales.
I simply cannot see the economics working for this type of complex product.
But it is certainly very interesting to see how the boundaries are being pushed out in car design. Very interesting indeed.
Now what we have to do is harness that design capacity to actually designing and producing a prototype Kit car which could be produced at a volume and price the UK Kit Car enthusiasts could afford.
That really is a challenge!
On we go!
1point7bar said:
Large tooling is made of smaller precision ground blocks that bolt to a backing plate. You are not going to press these sections so the tooling could be quite light in comparison.
CNC routines start with a plastic workpiece to check for tool crashes.
Machines large enough to do a car in one piece are rare and unnecessary.
Steel tooling, even if split into smaller blocks would be uneconomical and unnecessary. The material would be expensive, take longer to machine and be way overkill for composite parts.CNC routines start with a plastic workpiece to check for tool crashes.
Machines large enough to do a car in one piece are rare and unnecessary.
Edited by 1point7bar on Wednesday 14th March 19:40
Larger tools of as few pieces of possible from a suitable tooling board is the way to go. The type of board used would depend on what route you want to go for the moulds, ie wet lay or pre-preg. The denser and more durable the board, the more expensive the pattern (through material cost and increased machining time)
1point7bar said:
Design priorities:-
1 Looks do the selling.
2 Priced so it can be bought.
3 Performance beats the competition.
4 Function daily drive or race car.
Right order?
A perfectly reasonable list of design priorities.1 Looks do the selling.
2 Priced so it can be bought.
3 Performance beats the competition.
4 Function daily drive or race car.
Right order?
My interest, being an Accountant, is what is the cost budget for the first prototype car when produced at low volume for sale? And how can I set out a framework that will encourage discussion.
On the basis that the selling price must be more than the cost of the kit let us start here.
In the days of old when I were a lad (actually a very old lad) Ron Champion produced a book which suggested a Kit Car could be built at a reasonable cost by the average handyman mechanic and that a kit car could be built and on the road for a very reasonable £250.
Interest was rapidly fueled and another book came out from Haynes which added growth to the low cost idea (Locost!) suggesting a Kit Car could be built for a very reasonable budget which was considerably more germane IMO. Certainly I was unconvinced that £250 was sufficient.
Clearly the cost base has changed since then and we need to include the cost of IVA which in itself allowing for one failure (common) and transport costs, devours alone, £1,000 in itself.
Stuart Mills offers the advice on his website that the MEV X5 cars can be built BY the FACTORY with the donor provided by the buyer, at an all up cost of £5000 including paint.
The kit is available at an all in price of £2500 and donor cars are about to my knowledge for sub £700 in decent mechanical order.
We therefore have a genuine example of a Kit Car that can be on the road for £6000 or maybe a bit less. Remarkable value which is why I recommend that Kit Car. It is stunning value for money.
Going back to our example how do we assess the price at which a new kit car could be marketed successfully?
IMO the Kit Car enthusiasts needs all of the priorities that 1point7bar has listed. Very probably in the order suggested.
Starting with the first priority: Looks, I think this is absolutely crucial.
If a new design can be produced which incorporates` the flowing lines and aerodynamic qualities of some of the models paraded earlier on this topic I think a reasonable price would be assured. I believe that the right shape based on the right one donor vehicle could nudge double figures as a finished IVA'd car and still sell in volume.
But the shape has to be a real attention grabber.
I am very hopeful of Italo on this with the CKC ideas coming along.
Given all this, the a sales price well above the cost pricing of the Kit car made to sell in volume and cover costs MUST become possible. If the MEV X5 can be on the road for £6000 built and painted then we must be able to source a body shape in glassfibre and the essential underpinnings needed for the Kit for around that figure.
Thus would allow a greater return per car reflecting the complexity of the svelte enclosed (but roadster) shape. We` would be planning a significant return to tooling and laying costs and mould costs from the sale of every kit.
Labour costs could then be applied to the assembly process. I believe we have sufficient margin in the figures to make this viable and still reach an affordable price.
Now we turn to performance beating the competition.
Down to donor selection IMO. With the number of high power Japanese cars reaching structural failure in everyday motoring there is an ample supply of potential donors. I leave that to the designers but we need a one donor design that gives excellent and immediate performance.
Functionality will depend on the buyers requirements. By holding weight to a minimum and using well developed multivalve engines and very light bodywork replacing the old steel tub I see no reason why this should not be available as the buyer wishes it to be from the start.
Low frontal area, low drag, low weight and high power means, performance. Low ride height, low centre of gravity, low roll centre means, more performance.
So there I think is a discussion document for consideration.
The figures can be developed the ideas can be certainly challenged.
I may be totally wrong. I an interested in reading the views of other enthusiasts.
But I do think there is mileage in this approach. I certainly hope so.
Steffan said:
...the raw cost of each of the three cars shown would move all these project well outside the Kit car enthusiasts price range
If that referred to my post, just like to clarify: the IED pics only used as example of variable quality - that's the best angle of this years (red one) - not a suggestion of what should be made (though I think stripped out spyder version of the '08 project would sell like hot cakes). As for the Olme roadster, I don't see that it'd be expensive (simple body, no doors, etc.), it just isn't good enough.I'm not proposing that approaching an academic institution is a viable strategy, but it'd be more likely to succeed if it was something 'relevant' like an EV or hybrid - you could claim a raw two seater was 'challenging preconceptions about whether an environmentally responsible vehicle can be run'. If also compatible with ICE version that everyone actually buys, so much the better....
Strangely enough, the situation generally reminds me of starter homes. There's a clear demand, get the product right and price is less of an issue (though there is clearly a ceiling) and satisfying it could be a successful enterprise. The catch is that if you're truly capable (in terms of initial investment, time to profitability, etc) of doing that, chances are it's a small additional step on to a different, wealthier, demographic - so why wouldn't you? Someone was recently asking if the BAC Mono was being offered as a kit, and my first thought was why: if you're charging £74k for a turn key, offering as a kit is surely going to undermine your position - and given the price, how much would such a kit cost anyway??
Stuart Mills said:
There is a very interesting thread re car body buck building without cnc here
http://www.locostbuilders.co.uk/viewthread.php?tid...
....when he started in 2006 up to date.
....Taking a 2D sketch or an idea firmly pictured in your mind and spending massive time creating a buck is a brave move...
...perhaps a good case for getting the pro's involved but the sense of personal achievement would then be considerably reduced.
I've been following Fred's thread for a while; the quality looks astounding but as you say he's 6 years in - fine for a personal project, but a not a business one.http://www.locostbuilders.co.uk/viewthread.php?tid...
....when he started in 2006 up to date.
....Taking a 2D sketch or an idea firmly pictured in your mind and spending massive time creating a buck is a brave move...
...perhaps a good case for getting the pro's involved but the sense of personal achievement would then be considerably reduced.
You are allowed to add steps inbetween paper & buck you know...

Quarter or third scale models are still used in the mainstream industry, IIRC Fred's project actually used a model (not even especially large scale, 1:18th) as a datum; but any kind of model will help. If drawing's not a strong point, making a sketch model might actually be easier than making a sketch: bit of styrofoam, sanding paper & stanley knife from B&Q and you're away. Progress onto a decent scale - say 1:10th, based around some appropriately sized blocks of wood for oily bits and you might have something that can be cut into sections for use as basis of buck.
As far as authorship goes, a professional can be brought in for specific parts as necessary - didn't gtrclive bring in clay modellers for some of the trickier bits around the headlights, etc. on his project? Though in the case of designers, I would say that you need to be a good client to get best results: you need to be able to accept change (which may come in the form of criticism), but also remember they're there to satisfy your needs not their ego.
Jumping all the way back to the OP, I meant to ask about the Rocket & Sonic7. Obviously they're different chassis, but isn't there a lot of commonality? I don't think I've ever asked you if there was a grand plan but could it be that developing an exo first, with reductions in time & cost gets you up & running so that full body model could be developed, carrying over as much as possible (suspension, uprights, etc.) minimising on costs and inventory, etc. improves overall chances of success? In fact, IIRC that's why I signed up the PH in the first place - to me, the next step in that progression seemed to be a fully enclosed body based on the Sonic chassis.
seansverige said:
Jumping all the way back to the OP, I meant to ask about the Rocket & Sonic7. Obviously they're different chassis, but isn't there a lot of commonality? I don't think I've ever asked you if there was a grand plan but could it be that developing an exo first, with reductions in time & cost gets you up & running so that full body model could be developed, carrying over as much as possible (suspension, uprights, etc.) minimising on costs and inventory, etc. improves overall chances of success? In fact, IIRC that's why I signed up the PH in the first place - to me, the next step in that progression seemed to be a fully enclosed body based on the Sonic chassis.
Correct Sean, the Rocket came first and I used a Rocket chassis to form the original pattern (buck) for the Sonic7, suspension/track/wheel base/engine and driver position all remained the same but a totally different car was the result. Have to say this saved an awful lot of time but my flex ply pattern required considerable input from my old school mate who is a pattern maker. He spent months on it!He ensured symmetry and applied very slight compound curves to all surfaces, he made the front grille and made the boot and bonnet shut returns. He also made the fiddly bits like the gutter around the bonnet and boot openings. The pattern was still attached to the chassis at the time so we knew exactly where the internal components had to clear and that enabled us to get it tight and right.
The whole pattern was then coated several times then sanded and eventually polished to provide a perfect finish like glass.
The Sonic7 chassis is stiff and light, I agree, a good base for a Coupe but I designed a completely new chassis for the MEV Superlight as there are always compromises if you try to use a chassis designed for a different body. The Superlight offers 12 variations on the same chassis which is stiff but weighs only 68 kgs which is good considering it is wide enough to support a full body.
Stuart Mills said:
seansverige said:
Jumping all the way back to the OP, I meant to ask about the Rocket & Sonic7. Obviously they're different chassis, but isn't there a lot of commonality? I don't think I've ever asked you if there was a grand plan but could it be that developing an exo first, with reductions in time & cost gets you up & running so that full body model could be developed, carrying over as much as possible (suspension, uprights, etc.) minimising on costs and inventory, etc. improves overall chances of success? In fact, IIRC that's why I signed up the PH in the first place - to me, the next step in that progression seemed to be a fully enclosed body based on the Sonic chassis.
Correct Sean, the Rocket came first and I used a Rocket chassis to form the original pattern (buck) for the Sonic7, suspension/track/wheel base/engine and driver position all remained the same but a totally different car was the result. Have to say this saved an awful lot of time but my flex ply pattern required considerable input from my old school mate who is a pattern maker. He spent months on it!He ensured symmetry and applied very slight compound curves to all surfaces, he made the front grille and made the boot and bonnet shut returns. He also made the fiddly bits like the gutter around the bonnet and boot openings. The pattern was still attached to the chassis at the time so we knew exactly where the internal components had to clear and that enabled us to get it tight and right.
The whole pattern was then coated several times then sanded and eventually polished to provide a perfect finish like glass.
The Sonic7 chassis is stiff and light, I agree, a good base for a Coupe but I designed a completely new chassis for the MEV Superlight as there are always compromises if you try to use a chassis designed for a different body. The Superlight offers 12 variations on the same chassis which is stiff but weighs only 68 kgs which is good considering it is wide enough to support a full body.
i2 variations on the same chassis is an excellent result and clearly underlines the inherent strength and accessibility of that chassis design. Sounds like something of a record to me!
68KG is an excellent weight for a wide body chassis capability as well.
Your pattern maker is obviously a multi talented guy.
I cannot successfully produce double curves on a Kit car body despite 40 years of trying. I obviously need some lessons.
And getting both halves of a body shape to be truly symmetrical is another challenge that is beyond my abilities. I can get one half right but two halves never quite work for me.
That is why I am so hopeful that a really new and different Kit Car design will stimulate the kind of flurry there was when Ron Champion and Haynes made their marks years ago.
Come on Italo!! Onward and upward hopefully.
Cars with doors and screens are always going to cost far more to design/tool up for. The trick here is to use an off the shelf unit. The Smart roadster screen is 48" at the widest point and 29" at the highest and is therefore a potential kit car unit, not cheap though at £128 plus VAT. Expect to pay £60 trade for say a MK1 Escort screen forinstance. Yes there is big profit in car glass.
Bespoke tooling is around £3k plus pattern and silk screen for printing of black surround. Size makes little difference but the more it curves the more it costs. The MEV Sonic 7 screen is bespoke. Tooling was £2800. Most people agree however that the Sonic7 looks better with a fly screen due to the relatively wide shoulders on the car. The problem here is that as the screen is a slow sell then it will take forever if ever to get the £3k back.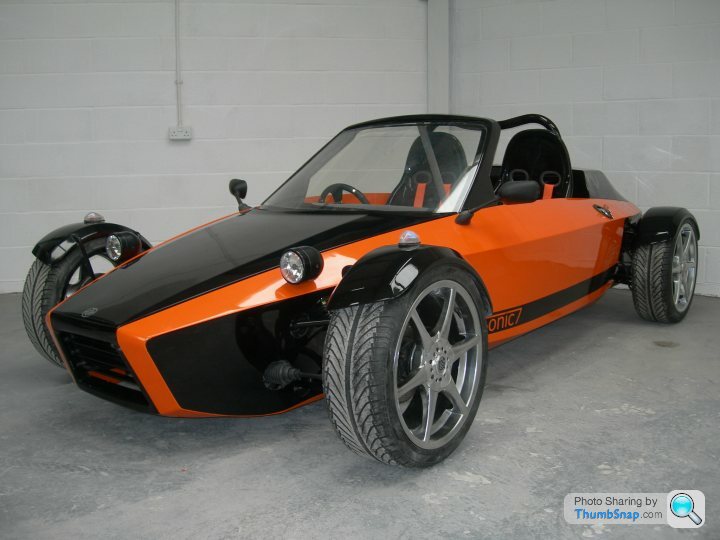
Bespoke tooling is around £3k plus pattern and silk screen for printing of black surround. Size makes little difference but the more it curves the more it costs. The MEV Sonic 7 screen is bespoke. Tooling was £2800. Most people agree however that the Sonic7 looks better with a fly screen due to the relatively wide shoulders on the car. The problem here is that as the screen is a slow sell then it will take forever if ever to get the £3k back.
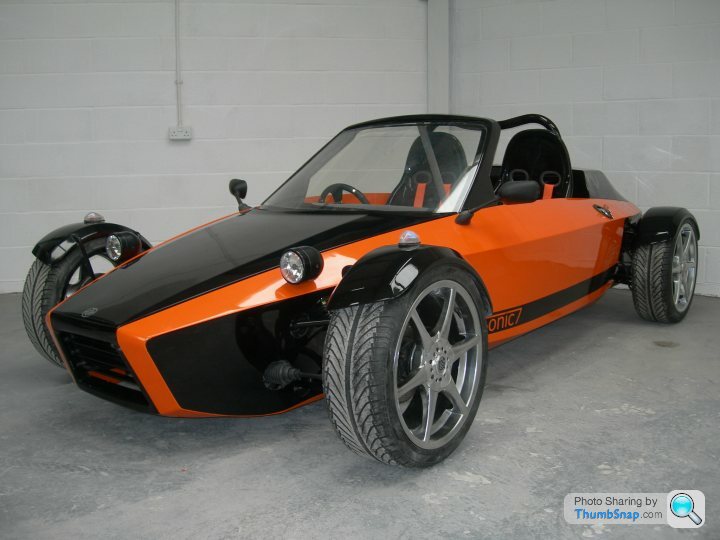
Gassing Station | Kit Cars | Top of Page | What's New | My Stuff