KIT CAR DEVELOPMENT COSTS?
Discussion
It would be interesting to hear peoples views on a business plan for a kit car start up firm.
For a start lets say a 2 seat roadster was developed.
Please feel free to amend these figures, but for an opener;
1k to a stylist for an approved sketch.
£2k to have it drawn in CAD to scale .
£5k to an engineer to design chassis/suspension geometry.
£5k to a fabricator to provide jigs for chassis/suspension.
£10k to a pattern maker for the bucks of the various panels.
£10k to the laminater to produce moulds having prepped the bucks.
1k for specialists for ecu complications from a donor etc.
1k to engineer to design/turn hubs/uprights or other specialist parts.
1k for the first cast from the new moulds, plus any mods required.
1k for the first chassis produced plus any mods required.
1k for a decent donor.
1k for set of wheels/tyres/seats/instruments.
1k for exhaust/prop shaft etc.
1k labour for prototype assembly.
1k for IVA, registration fee, road tax and insurance.
1k for web site, leaflets, banners, letterheads, cards etc.
5k to exhibit at 5 shows inc fuel/hotel/food.
1k for a trailer to cart your show piece around.
2k for company set up/accountant/bank chargers/product liability insurance.
1k for 4 adverts in magazines.
4 kits sold in year one whilst establishing a name/reputation/brand.
2k gross profit per kit sold.
5k for small unit rent/rates/heating/electric/telephone.
10k directors salary whilst building up trade.
10k for desk/PC/van/office carpet/racks/tools/chair/coffee machine etc.
10k for start up stock of lights/suspension/chassis/ball joints, ect
WHAT HAVE I MISSED OUT?
Is this something you may help with Steffan?
For a start lets say a 2 seat roadster was developed.
Please feel free to amend these figures, but for an opener;
1k to a stylist for an approved sketch.
£2k to have it drawn in CAD to scale .
£5k to an engineer to design chassis/suspension geometry.
£5k to a fabricator to provide jigs for chassis/suspension.
£10k to a pattern maker for the bucks of the various panels.
£10k to the laminater to produce moulds having prepped the bucks.
1k for specialists for ecu complications from a donor etc.
1k to engineer to design/turn hubs/uprights or other specialist parts.
1k for the first cast from the new moulds, plus any mods required.
1k for the first chassis produced plus any mods required.
1k for a decent donor.
1k for set of wheels/tyres/seats/instruments.
1k for exhaust/prop shaft etc.
1k labour for prototype assembly.
1k for IVA, registration fee, road tax and insurance.
1k for web site, leaflets, banners, letterheads, cards etc.
5k to exhibit at 5 shows inc fuel/hotel/food.
1k for a trailer to cart your show piece around.
2k for company set up/accountant/bank chargers/product liability insurance.
1k for 4 adverts in magazines.
4 kits sold in year one whilst establishing a name/reputation/brand.
2k gross profit per kit sold.
5k for small unit rent/rates/heating/electric/telephone.
10k directors salary whilst building up trade.
10k for desk/PC/van/office carpet/racks/tools/chair/coffee machine etc.
10k for start up stock of lights/suspension/chassis/ball joints, ect
WHAT HAVE I MISSED OUT?
Is this something you may help with Steffan?
The numbers I put in are not facts and are intended as a start point only.
MEV development costs are kept much lower by keeping them in house and are done in my spare time, a mate does my website and another does my CAD.
If forinstance a team was set up comprising of say a welder a carpenter and a salesman then the figures change enormously.
So as I said, please feel free to amend the numbers, hypothetically build your own website, work from your home garage, spend say £300 on a mig set and a chop saw at Machine Mart, do not use a pro to style it, buy books on chassis design and GRP, estimate costs and sales and let us know what the return could be. Is 20k returned in a year possible?
You may show readers how low start up costs can be and encourage them to take the plunge.
MEV development costs are kept much lower by keeping them in house and are done in my spare time, a mate does my website and another does my CAD.
If forinstance a team was set up comprising of say a welder a carpenter and a salesman then the figures change enormously.
So as I said, please feel free to amend the numbers, hypothetically build your own website, work from your home garage, spend say £300 on a mig set and a chop saw at Machine Mart, do not use a pro to style it, buy books on chassis design and GRP, estimate costs and sales and let us know what the return could be. Is 20k returned in a year possible?
You may show readers how low start up costs can be and encourage them to take the plunge.
The figures I posted were to spark debate but the vast majority on here are not manufacturers, and can only guess true costs. The fact is that if fictitious Fred in his shed who was good at welding and woodwork had a go he may succeed. He could buy books re chassis design and grp, get a free website then exhibit his product in the show car parks were you get in free in a kit. A little sad if that is the only way to make it pay though. So your right, if Fred possessed some or all of the prerequisite skills then my figures are completely out.
Please feel free to post a more attractive set of figures based on more conservative estimates and increased sales income. The number of years it takes to see the initial investment returned is the bottom line.
What do we think would be a reasonable % return in other industries?
5 years = 20%, 2 years = 50%?
Please feel free to post a more attractive set of figures based on more conservative estimates and increased sales income. The number of years it takes to see the initial investment returned is the bottom line.
What do we think would be a reasonable % return in other industries?
5 years = 20%, 2 years = 50%?
1point7bar said:
There aren't lots of new exciting models to tempt trading up and used kit cars are
way to easy to keep alive(from a consumer product standpoint).
That's an interesting point, I wonder how many kit cars that made it on to the roads are still on the roads or could be put back on without too much trouble? That may suggest that the way to compete with all the second hand kits on sale is to ensure that new products are offered that are sufficiently different to those produced in large numbers in the past. Thankfully Exocet sells very well and allows us to earn a living and still reinvest in new products. At Stoneleigh Team MEV will launch 2 new kits that are not aimed at the Cobra or 7 market, they will be a bike engined exo car known as MEVABUSA and a restyled MEVX5. We will see if we can tempt customers to buy new instead of one of the second hand kits on sale.way to easy to keep alive(from a consumer product standpoint).
Thanks for your contribution Qdos, I love the bit about educashun!
You mention Project X. I hope that name does not stick as it is a film that is in the cinemas now isn't it?
One very important factor I keep forgetting to mention is how cheap British manufacturing costs have become compared to many countries.
I read about MNR, SDR, Westfield, GBS etc selling very well overseas. I too bang 10 MEV kits in a 20 foot container on a regular basis. RTR won't mind me telling you that they are filling a 40ft container right now and have the next one part full in terms of orders to produce.
Steffan, your dream will come true in the next few years I feel. British manufacturing will again be growing and exports will keep us on top. Nice.
So in terms of investment in the industry, if the export market is captured then the business plan starts to stack up even if Fred the shed or Jack of all trades struggle to sell home grown products. It makes a better case for using the pro's.
You mention Project X. I hope that name does not stick as it is a film that is in the cinemas now isn't it?
One very important factor I keep forgetting to mention is how cheap British manufacturing costs have become compared to many countries.
I read about MNR, SDR, Westfield, GBS etc selling very well overseas. I too bang 10 MEV kits in a 20 foot container on a regular basis. RTR won't mind me telling you that they are filling a 40ft container right now and have the next one part full in terms of orders to produce.
Steffan, your dream will come true in the next few years I feel. British manufacturing will again be growing and exports will keep us on top. Nice.
So in terms of investment in the industry, if the export market is captured then the business plan starts to stack up even if Fred the shed or Jack of all trades struggle to sell home grown products. It makes a better case for using the pro's.
Anything with complex curves like that would be expensive to produce. A set of patterns may cost £10k for a pro to do it and moulds for those shapes could be expensive, A, because they are large and B, because those shapes would require several release splits in the moulds. Then the parts you cast will need all the split lines sanding and polishing out. No problem, all can be done but again it is all down to how much of the work Fred can do then hopefully his mate Salesmen Sam will be able to get a few sold.
So could it stack up? A relatively high set up cost using pros all round can be justified if a better product is produced that could sell in the sort of numbers that will ammortise the set up costs in a reasonable time frame. A calc required from Business brain Bob!
Just noticed the flat screen, now that would save a lot of money.
So could it stack up? A relatively high set up cost using pros all round can be justified if a better product is produced that could sell in the sort of numbers that will ammortise the set up costs in a reasonable time frame. A calc required from Business brain Bob!
Just noticed the flat screen, now that would save a lot of money.
Edited by Stuart Mills on Tuesday 6th March 20:33
I have heard 100k mentioned in the past as a ball park figure but again if Jack of all trades were a good sales man then it could be considerably less, but then the end result could be a considerably less desirable car.
Coming back to the KDIcarmad post though, here another potential angle emerges.
Take an old kit, convert it to modern running gear, cut chunks out of the grp and reshape to sharpen the lines and introduce modern lights in the correct IVA positions. Then tidy it all up. Get a pro paint job done, show it, get some orders having quoted a 3 months lead time, take moulds of it, deliver.
When I made the Sonic7 pattern I used a Rocket chassis and wrapped flex ply around to achieve the curves. I was aiming at a bodied Rocket and so the wheel base/engine position etc remained the same. I then used jelutong to form the awkward sections. I am not a fan of the laser cut foam approach, you finish up with a large bill and a massive task of finishing the surface to a suitable standard.
Coming back to the KDIcarmad post though, here another potential angle emerges.
Take an old kit, convert it to modern running gear, cut chunks out of the grp and reshape to sharpen the lines and introduce modern lights in the correct IVA positions. Then tidy it all up. Get a pro paint job done, show it, get some orders having quoted a 3 months lead time, take moulds of it, deliver.
When I made the Sonic7 pattern I used a Rocket chassis and wrapped flex ply around to achieve the curves. I was aiming at a bodied Rocket and so the wheel base/engine position etc remained the same. I then used jelutong to form the awkward sections. I am not a fan of the laser cut foam approach, you finish up with a large bill and a massive task of finishing the surface to a suitable standard.
Doors are expensive and difficult to get right. BUT
Beauford, uses doors from a Mini.
MEV Superlight uses lightened MX5 doors with a GRP cap.
Didn't Ginetta use a Fiesta door?
The problem is finding one of a suitable height. It is amazing how 20mm difference between a saloon and a sports car door change the whole balance.
Beauford, uses doors from a Mini.
MEV Superlight uses lightened MX5 doors with a GRP cap.
Didn't Ginetta use a Fiesta door?
The problem is finding one of a suitable height. It is amazing how 20mm difference between a saloon and a sports car door change the whole balance.
There is a very interesting thread re car body buck building without cnc here
http://www.locostbuilders.co.uk/viewthread.php?tid...
Clearly this is a quality item. It shows full detail from when he started in 2006 up to date.
I guess he is at an advantage as it is a replica so he knows what to expect. Taking a 2D sketch or an idea firmly pictured in your mind and spending massive time creating a buck is a brave move.
That is where clay or cladding timber frame come in. At least they are cheap and can be altered and you get a real sense of proportions before it is anywhere near finished. When it starts to drift from your dream you can reach for the large hammer or pat your self on your back once you have an early warning or confidence boost as the case may be.
A full body for a car can take months and months only to provide disappointment, again perhaps a good case for getting the pro's involved but the sense of personal achievement would then be considerably reduced.
http://www.locostbuilders.co.uk/viewthread.php?tid...
Clearly this is a quality item. It shows full detail from when he started in 2006 up to date.
I guess he is at an advantage as it is a replica so he knows what to expect. Taking a 2D sketch or an idea firmly pictured in your mind and spending massive time creating a buck is a brave move.
That is where clay or cladding timber frame come in. At least they are cheap and can be altered and you get a real sense of proportions before it is anywhere near finished. When it starts to drift from your dream you can reach for the large hammer or pat your self on your back once you have an early warning or confidence boost as the case may be.
A full body for a car can take months and months only to provide disappointment, again perhaps a good case for getting the pro's involved but the sense of personal achievement would then be considerably reduced.
Thank you for your kind words Steffan.
Here is a link of interest.
http://www.youtube.com/watch?v=rBTaIck42GM&fea...
Anyone guess what this would cost?
I don't know the answers BTW so it would be very interesting to hear opinions or fact from those in the know.
Drawing of initial concept sketch say £?
Fully dimensioned/scaled working drawings say £?
CAD conversion for machine prog say £?
CNC polystyrene or polyurethane block milling say £?
Form returns for opening sections (boot/bonnet/doors)£?
Interior pattern forming for inner wheel arches/dash ect say £?
Finish in resin say £?
Take moulds in GRP with bolt on relief splits say £?
The above all assumes a reverse engineering approach to chassis/function/fit.
Here is a link of interest.
http://www.youtube.com/watch?v=rBTaIck42GM&fea...
Anyone guess what this would cost?
I don't know the answers BTW so it would be very interesting to hear opinions or fact from those in the know.
Drawing of initial concept sketch say £?
Fully dimensioned/scaled working drawings say £?
CAD conversion for machine prog say £?
CNC polystyrene or polyurethane block milling say £?
Form returns for opening sections (boot/bonnet/doors)£?
Interior pattern forming for inner wheel arches/dash ect say £?
Finish in resin say £?
Take moulds in GRP with bolt on relief splits say £?
The above all assumes a reverse engineering approach to chassis/function/fit.
seansverige said:
Jumping all the way back to the OP, I meant to ask about the Rocket & Sonic7. Obviously they're different chassis, but isn't there a lot of commonality? I don't think I've ever asked you if there was a grand plan but could it be that developing an exo first, with reductions in time & cost gets you up & running so that full body model could be developed, carrying over as much as possible (suspension, uprights, etc.) minimising on costs and inventory, etc. improves overall chances of success? In fact, IIRC that's why I signed up the PH in the first place - to me, the next step in that progression seemed to be a fully enclosed body based on the Sonic chassis.
Correct Sean, the Rocket came first and I used a Rocket chassis to form the original pattern (buck) for the Sonic7, suspension/track/wheel base/engine and driver position all remained the same but a totally different car was the result. Have to say this saved an awful lot of time but my flex ply pattern required considerable input from my old school mate who is a pattern maker. He spent months on it!He ensured symmetry and applied very slight compound curves to all surfaces, he made the front grille and made the boot and bonnet shut returns. He also made the fiddly bits like the gutter around the bonnet and boot openings. The pattern was still attached to the chassis at the time so we knew exactly where the internal components had to clear and that enabled us to get it tight and right.
The whole pattern was then coated several times then sanded and eventually polished to provide a perfect finish like glass.
The Sonic7 chassis is stiff and light, I agree, a good base for a Coupe but I designed a completely new chassis for the MEV Superlight as there are always compromises if you try to use a chassis designed for a different body. The Superlight offers 12 variations on the same chassis which is stiff but weighs only 68 kgs which is good considering it is wide enough to support a full body.
Cars with doors and screens are always going to cost far more to design/tool up for. The trick here is to use an off the shelf unit. The Smart roadster screen is 48" at the widest point and 29" at the highest and is therefore a potential kit car unit, not cheap though at £128 plus VAT. Expect to pay £60 trade for say a MK1 Escort screen forinstance. Yes there is big profit in car glass.
Bespoke tooling is around £3k plus pattern and silk screen for printing of black surround. Size makes little difference but the more it curves the more it costs. The MEV Sonic 7 screen is bespoke. Tooling was £2800. Most people agree however that the Sonic7 looks better with a fly screen due to the relatively wide shoulders on the car. The problem here is that as the screen is a slow sell then it will take forever if ever to get the £3k back.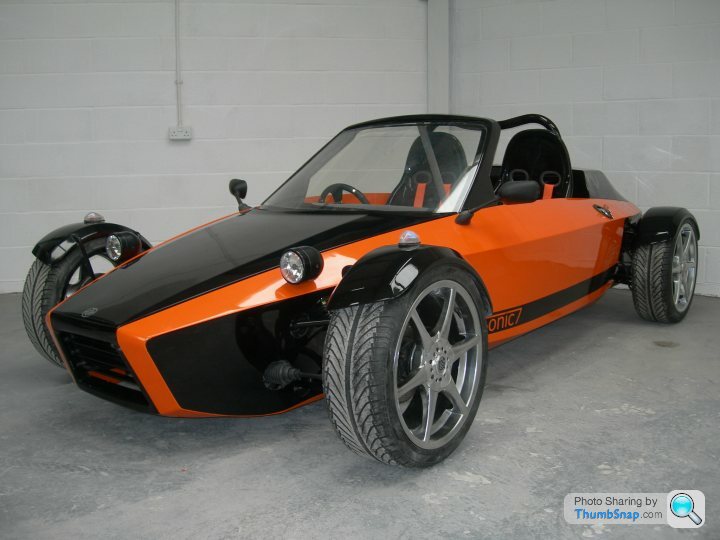
Bespoke tooling is around £3k plus pattern and silk screen for printing of black surround. Size makes little difference but the more it curves the more it costs. The MEV Sonic 7 screen is bespoke. Tooling was £2800. Most people agree however that the Sonic7 looks better with a fly screen due to the relatively wide shoulders on the car. The problem here is that as the screen is a slow sell then it will take forever if ever to get the £3k back.
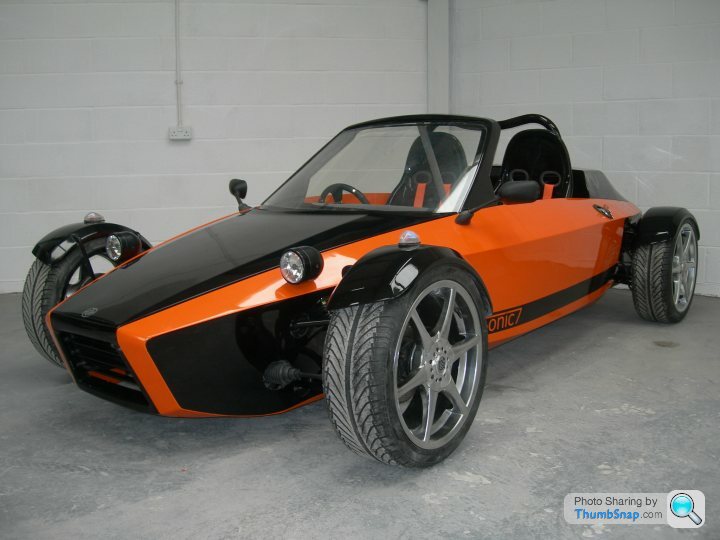
IVA test does not cover emergency egress Sean.
I would have thought the easiest and cheapest way to gain access to a water tight cabin is to climb over a relatively low side with a velcro a side flap that is zipped to the folding roof or hard top.
My Bond Bug has reasonable "doors" made from soft top material with a simple steel frame.
I would have thought the easiest and cheapest way to gain access to a water tight cabin is to climb over a relatively low side with a velcro a side flap that is zipped to the folding roof or hard top.
My Bond Bug has reasonable "doors" made from soft top material with a simple steel frame.

seansverige said:
Without wanting to sound like a snob, there'd be a different perception of quality with rigid panels and surely this is about broadening appeal; but I did have a think about it.
There's a whole aesthetic of high end technical outdoor clothing that could be exploited but I can't think of a single example where this has been done. Maybe if the fabric was in tension on a frame with a few curved spars (maybe even composite ones borrowed from dome tents) to give some form: think Velorex bonnet. Waterproof zips would obviate need for overlaps at joints which not only looks better but should reduce wind noise, drips etc.
Still think perspex (rigid) window with opening a must though...
Tensioned fabric sounds like a possibility, not too expensive either.There's a whole aesthetic of high end technical outdoor clothing that could be exploited but I can't think of a single example where this has been done. Maybe if the fabric was in tension on a frame with a few curved spars (maybe even composite ones borrowed from dome tents) to give some form: think Velorex bonnet. Waterproof zips would obviate need for overlaps at joints which not only looks better but should reduce wind noise, drips etc.
Still think perspex (rigid) window with opening a must though...
Remember the documentary when we were informed that Caterham spent 300k developing the 21 and Lotus spent 8M developing the Elise
http://domestic1.sjc.ox.ac.uk/~jn/caterham-bbc4-do...
Gassing Station | Kit Cars | Top of Page | What's New | My Stuff