Knackered old Porsche with loads of natural light - Boxster!
Discussion
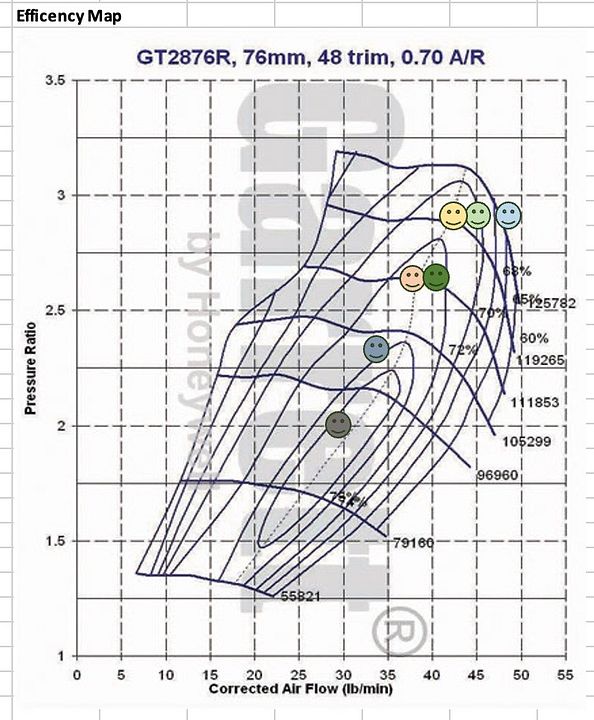
As thought it's a bit tight on that turbo for 500bhp but it'll do 475 just and is very happy at 400 - 425bhp so we'll put it in the good starting point box

I've about finished all the working out on this now, well as much as I'm going to do to sense check the basics so one the block is back from machining I'll get that into CAD and start building an engine. There's no rush on this project as it's purely an evenings and weekends job but lets see how much this escalates

Dr.Hellno said:
470 been done on standard cams; apparently that’s pretty much their limit. Over 100 been added with just better cams though.
I’m hoping for full escalation on this
To get that sort of gain they must have been reving to at least 8000RPM and have had a big enough turbo on there to deliver the additional airmass required for another 100bhp odd when they swapped cams.....it's never quite as simple as just swapping cam profiles I’m hoping for full escalation on this

The standard cams are all done by around 7200RPM but you can hang things in with a bit more boost (making up for the reducing valve open time with more air density) to 7500RPM which on a 76MM compressor wheel Garrett is 475bhp or so. You can make more than this with more boost but that needs a larger turbo and now you're not making that boost until later in the rev range with the same 7500RPM limit so the power band is ever shrinking (unless you're now getting into high flow low inertia turbo chargers, ALS etc.).... it's all a balancing act

As power = torque X rpm / 5252 the same torque at more RPM will always give more power hence why moving to a cam profile with lift optimised for higher RPM will make a big difference in power.
This works the other way too, for example the FIA F2 race cars (which were 1.8 20V powered) rev'd to 8500RPM with a GT30 derrived turbo and made 425bhp with another 50bhp or so more in push to pass but torque was always below 300ftlbs to keep the gearbox nice, light and reliable. They made this power using more revs rather than more torque.
Basically if you know the torque limit of the drivetrain (and you're not RPM limited in terms of input shaft speed) then this determines how high you're going to need to rev to make the target power and therefore what cams/turbo is required to achieve a good power band and response. As revs have far more impact on engine life than boost quite often to achieve the reliability target you end up boxed into a corner on how high you can rev it but that's all part of the game

P.S. The light green smiley face on the compressor map above is 475 bhp, at this we're still in a decent efficency island but right up there in compressor speed but it also brings us into another challenge, charge cooling.
At a pressure ratio of 2.9 or so and a 20 degree ambient we're going to be outputting air from the turbo at around 165 degrees C which means we need a really good charge cooling solution, we also need to minimise the pressure drop as much as possible to keep that boost pressure up post cooler. To do this I'm going to use a PWR barrel type charge cooler which is naturally very low pressure drop and with a decent diameter will give the cooling performance required achieving 85% efficency or so with a reasonably cool water loop (lets not dwell on that or we're now getting into deltas to ambient etc.
) which gives us a plenum intake temp of 42 degrees or so - pretty acceptable 
At a pressure ratio of 2.9 or so and a 20 degree ambient we're going to be outputting air from the turbo at around 165 degrees C which means we need a really good charge cooling solution, we also need to minimise the pressure drop as much as possible to keep that boost pressure up post cooler. To do this I'm going to use a PWR barrel type charge cooler which is naturally very low pressure drop and with a decent diameter will give the cooling performance required achieving 85% efficency or so with a reasonably cool water loop (lets not dwell on that or we're now getting into deltas to ambient etc.


Dr.Hellno said:
Been to see these guys today and what a helpful and genuinely nice lot they are! We had a great chat and they introduced me to an ECU option that I wasn't aware of. Lovely location overlooking the airfield too and a mega dyno!
Dr.Hellno said:
Nice!
I guess you’re referring to Ignitron!? Mine runs on an Emerald but may swap over at some point.
Look forward to updates!
Yes, I'm hugely impressed with it. Having spent the early part of my career on "proper" pro-motorsport engine control I never thought I'd see the day where an aftermarket ECU came close to OE engine control in some areas but aside from catalyst control and a few other emissions strategies this really is pretty close. It's leagues ahead of the various basic ECUs that have been common for the last couple of decades like Emerald, Omex, DTA etc. and features some really impressive stuff like weight of air calibration, MAF signal filtering, real proper knock control with adaption of windowing etc., boost control with proper configurable PIDs and none linear P support, anti-stall throttle and a full OBD2 integration (even though it's obviously not homologated). I guess you’re referring to Ignitron!? Mine runs on an Emerald but may swap over at some point.
Look forward to updates!
Okay we live in a world now where you can buy a Motec that has Simulink integration and write all that yourself but the Ignitron box is less than a Matlab licence alone

ATM said:
So let's pretend I understood none of your previous post. Although that's not true because I understand loads, obviously. Can one of these modern aftermarket ECU solve my problem of fitting a modern pork engine in a 986. Like a 981 engine maybe even with the - controversial - PDK box?
Yes and No, the ECU we're talking about here that I may end up using has been designed to directly replace the Bosch ME 7.5 controller and a lot of the strategies etc. are heavily inspired by the function of ME7.5 as a result. However it's still a unit designed to run port injectors, single cam VVT etc. etc. so of little use if you want to fit something from a 981 with a PDK box. For that you're going to need something with a bit more IO, which supports direct injection, multi cam VVT and of course the PDK box. Luckily for you Syvecs (which is a distant relation to Life Racing which in turn is a relation to Pectel/Cosworth) do a plug and play for the 981 and PDK box support:
https://www.syvecs.com/product/porsche-cayman-987-...
If you took the engine, box, looms etc. from a 981 then with some dedicated work you get these powered up and working in the 986 - the nice thing about an aftermarket ECU is that there is no immobilisers etc. to mess with and the ECU is easily communicated with so it's entirely possible to achieve these sorts of engine transplants. The big fly in the ointment though is calibration - OEMs spend millions on ECU calibration and it's the reason why road cars drive like they do now, you can absolutely get close to this on an aftermarket (especially in terms of actual driveability, engine performance etc.) but you just won't have covered all the edge cases that an OEM will have done so you'll have to accept these edge cases won't be perfect in the end car.
.... but the short answer is yes there's a box of sparks that'll run a 981 motor and PDK gearbox

richhead said:
I worked as a contractor with the old f2 palmer cars for a few years, one of the great engine heros of motorsport imo,
I could not agree more! I worked on the tail end of Mountune / MSVRs 20V engine program for a different applicaiton where with minimal component changes the same engines which had done three seasons of F2 were making nearly 600bhp! It was a fantastic engine package..... as was the whole car, I don't think anything quicker has been run for those sort of costs a mile before or after 
The engine spec for this project is heavily inspired by the F2 spec as a result of just how reliable they were at those power figures. The only difference is I've gone for a cast exhaust manifold and sacrified some weight and response for durability.
So last bits and bobs validating this idea done today, thermals will be the limiting factor as first thought but the green light is well and truly lit and project "Booster" is on 
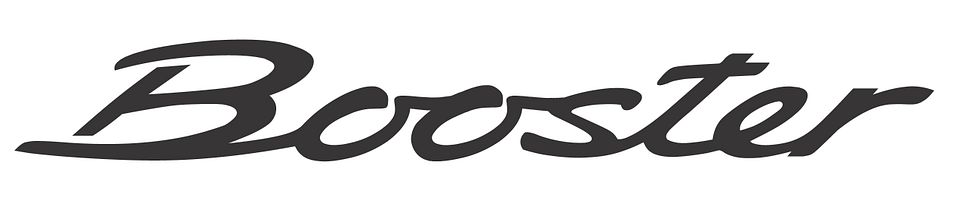
Time scales will be fairly slow on this due to lots of other stuff going on at the moment but roughly:
- CAD Complete M9.5
- Engine build complete M10
- Outsource Manufacture complete M11
- Build it over Xmas break
- Map it January and start the process of integration, emissions etc. etc.
Engine out During December means the Boxster will stay on the road until then and if I've got all the CAD correct it should all bolt in without too much of a drama....... let's check back on that statement during December

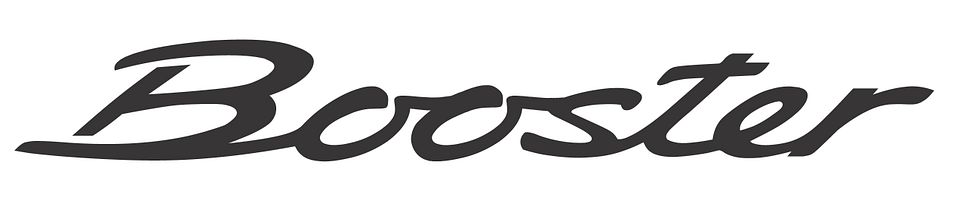
Time scales will be fairly slow on this due to lots of other stuff going on at the moment but roughly:
- CAD Complete M9.5
- Engine build complete M10
- Outsource Manufacture complete M11
- Build it over Xmas break
- Map it January and start the process of integration, emissions etc. etc.

Engine out During December means the Boxster will stay on the road until then and if I've got all the CAD correct it should all bolt in without too much of a drama....... let's check back on that statement during December

Edited by poppopbangbang on Monday 4th September 00:27
eltax91 said:
"Progress will be slow" and "done over xmas". Oxymoron. 
I started the strip and rebuild of a Range Rover. Had it 2 months now. The interior's out.... that's it.
Done is a strong word! 
I started the strip and rebuild of a Range Rover. Had it 2 months now. The interior's out.... that's it.


Good news is the CAD is coming together reasonably well with most of the large bits now in there so I can start looking at how to nicely do a front mount etc.
It's all a space claim at the moment using the dirtiest 3D scan ever (of actually the wrong engine) but it fits, two piece billet front engine mount that picks up on the original threaded holes in the block that carried the original upper mount in a Golf and translates that to pick up the standard Boxster front mount.
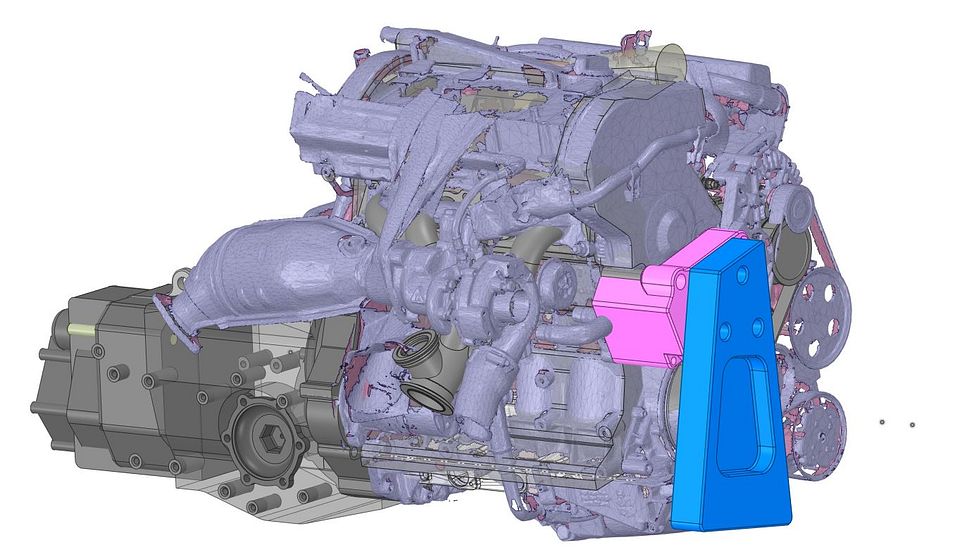
Waiting on a Boxster mount now so I can draw that up and once that's done I'll put some actual effort into making the mount nicer and somewhat lighter
As always it's critical to avoid falling foul of the DVLA "Radically Modified Vehicles" rules so this has to go in with zero modification to the monocoque i.e no brackets welded on, no holes drilled etc. etc.
Waiting on a Boxster mount now so I can draw that up and once that's done I'll put some actual effort into making the mount nicer and somewhat lighter

As always it's critical to avoid falling foul of the DVLA "Radically Modified Vehicles" rules so this has to go in with zero modification to the monocoque i.e no brackets welded on, no holes drilled etc. etc.
gofasterrosssco said:
Apologies in advance for the tangential query on a product you are just getting familiar with, but do you think a engine of a similar generation running an ME7.1 could be made to work (e.g. with 8-cyl, and 40v..)? I guess this may not have sufficient I/O..
My other (unrelated) car operates a modified OEM ECU that allows a similar (but less comprehensive) range of configuration. For me it just allows update mapping files dependent on pulley size (SC), and I think its certainly a more attractive set up then a full replacement unit.
Not enough coil drivers on this one to run that and the software doesn't appear to have 8 cylinder support (max 6 for VR6/R32). My other (unrelated) car operates a modified OEM ECU that allows a similar (but less comprehensive) range of configuration. For me it just allows update mapping files dependent on pulley size (SC), and I think its certainly a more attractive set up then a full replacement unit.
Regardless it's not just the hardware, that's the easy bit, it's the calibration of the ECU which is the complex and costly part of the job. Yes you can get a WOT power run in a day on a rolling road but all the subtleties of cold start, catalyst control, knock control etc. are significant work to get to an acceptable standard. In nearly all applications you're better off running an OE ECU with an OE based calibration if at all possible unless there is a hugely well developed option to replace it as the standard of aftermarket plug and play calibrations etc. can vary greatly even if the hardware physically plugs and goes.
CAD is going pretty well, all the big bits fit and of course as we know if it fits on CAD it'll definitely fit on the car 
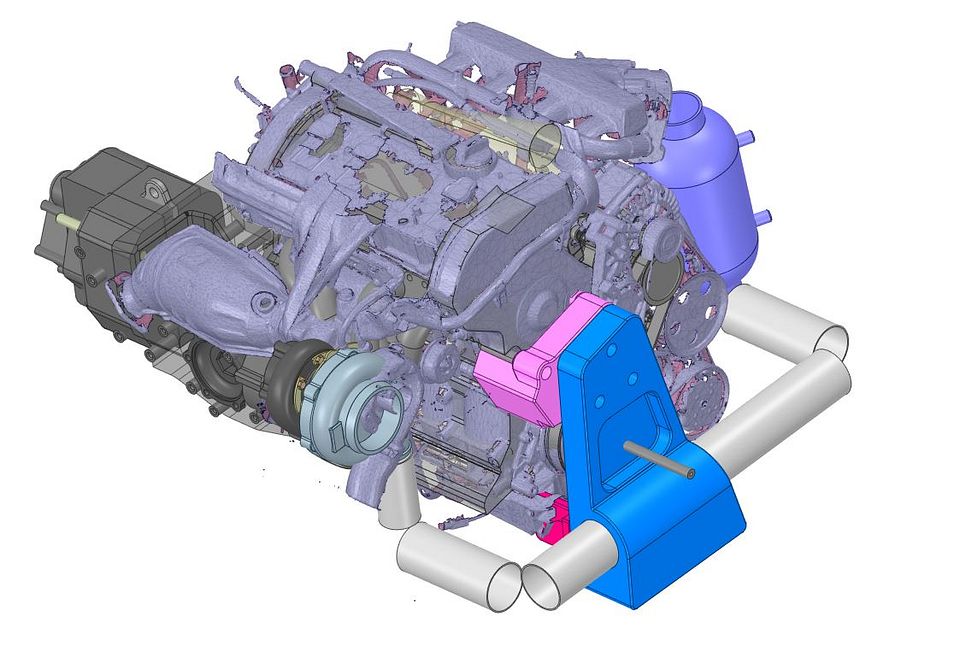
Lots of FEA to do on the front mount to get some weight out but it's looking the part now, it was rude not to run the boost transfer pipe through the engine mount really when it packages so well like that and I need the extra reach to pickup the standard front mounting point anyway. I added a small anti deflection mount on the lower mount inline with the load path to the original engine mount as the A4 sump has bosses here that carried the original anti-deflection mount on the OE installation so pretty certain the sump won't mind a bit of load going in here. The vertical of the front mount is so stiff at the moment it doesn't need it but best to give some options to reduce the mass in the front mount!
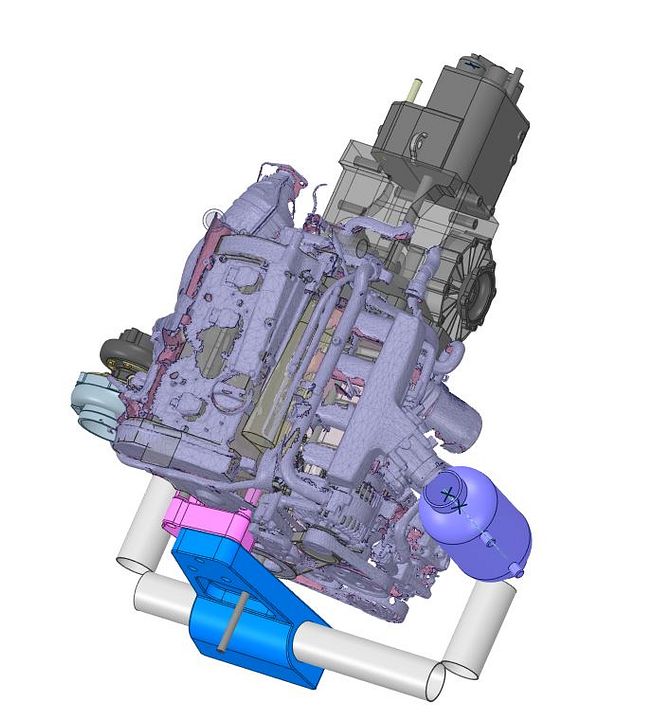
The turbo fits in a really nice position with lots of room for downpipe, CAT and a decent sized air filter in the side intake vent.
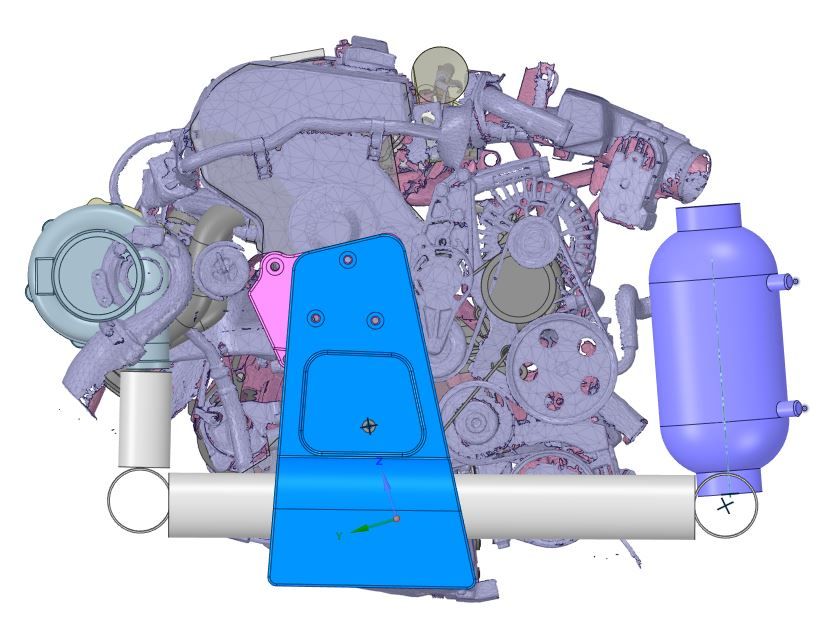
And the air delivery path is pretty short, I need to do some maths and see how small I can make them (they're all 3" at the moment so the mount FEA is done worst case) to get the volume down without impairing flow. Also some working out on which bends can be hard piped and just how much can be made as one piece as I want the minimum joins possible in this as there is nothing worse than a joiner buried in the bottom of the car as it's always that one which'll make a bid for freedom and a load of silicone and 27 hose clips just looks a mess. At the moment I think I can get this done with four joiners but might be able to get it down to three with a transfer pipe that loads into the car already in the engine mount.
Charge cooler packages nicely too, a PWR 6" X 6" one made the most packaging sense directly under the intake manifold, the big diameter and short length will help pressure drop but still provides plenty of cooling capacity but over 400 beans will likely need WI for sustained use unless the charge cooler rad works really, really well. I'll mount this to the engine with a couple of weld on mounts on the charge cooler so that way the entire system is retained on and moves with the engine which will help durability no end.
Onto exhaust packaging next, I really want to retain the standard Boxster silencer as 1) It's really well engineered onto the car in terms of mounts and packaging, 2) it's super quite so track legal and 3) there are a load of aftermarket exhausts that are a direct fit if greater flow is required. The problem with this idea is that they all have two entrances to the silencer box due to the pair of heads on the original flat six. There is just enough room to squeeze a transfer pipe of a Y pipe setup under the gearbox but now we're in to how bad would that be for the gearbox oil temps! Time to work that out as adding some gearbox cooling because you're cooking the gearbox with the exhaust seems a little counter productive.
Finally the rest of the engine build bits are currently waiting for UK Customs to pull their finger out and issue a duty invoice but they should be here by the end of next week with a bit of luck and then we can get into building a motor up.
This quick project has turned into a bit of a job now...... it better be bloomin quick once done

Lots of FEA to do on the front mount to get some weight out but it's looking the part now, it was rude not to run the boost transfer pipe through the engine mount really when it packages so well like that and I need the extra reach to pickup the standard front mounting point anyway. I added a small anti deflection mount on the lower mount inline with the load path to the original engine mount as the A4 sump has bosses here that carried the original anti-deflection mount on the OE installation so pretty certain the sump won't mind a bit of load going in here. The vertical of the front mount is so stiff at the moment it doesn't need it but best to give some options to reduce the mass in the front mount!
The turbo fits in a really nice position with lots of room for downpipe, CAT and a decent sized air filter in the side intake vent.
And the air delivery path is pretty short, I need to do some maths and see how small I can make them (they're all 3" at the moment so the mount FEA is done worst case) to get the volume down without impairing flow. Also some working out on which bends can be hard piped and just how much can be made as one piece as I want the minimum joins possible in this as there is nothing worse than a joiner buried in the bottom of the car as it's always that one which'll make a bid for freedom and a load of silicone and 27 hose clips just looks a mess. At the moment I think I can get this done with four joiners but might be able to get it down to three with a transfer pipe that loads into the car already in the engine mount.
Charge cooler packages nicely too, a PWR 6" X 6" one made the most packaging sense directly under the intake manifold, the big diameter and short length will help pressure drop but still provides plenty of cooling capacity but over 400 beans will likely need WI for sustained use unless the charge cooler rad works really, really well. I'll mount this to the engine with a couple of weld on mounts on the charge cooler so that way the entire system is retained on and moves with the engine which will help durability no end.
Onto exhaust packaging next, I really want to retain the standard Boxster silencer as 1) It's really well engineered onto the car in terms of mounts and packaging, 2) it's super quite so track legal and 3) there are a load of aftermarket exhausts that are a direct fit if greater flow is required. The problem with this idea is that they all have two entrances to the silencer box due to the pair of heads on the original flat six. There is just enough room to squeeze a transfer pipe of a Y pipe setup under the gearbox but now we're in to how bad would that be for the gearbox oil temps! Time to work that out as adding some gearbox cooling because you're cooking the gearbox with the exhaust seems a little counter productive.
Finally the rest of the engine build bits are currently waiting for UK Customs to pull their finger out and issue a duty invoice but they should be here by the end of next week with a bit of luck and then we can get into building a motor up.
This quick project has turned into a bit of a job now...... it better be bloomin quick once done

Luther Blissett said:
Why use a GT2876R? It's a 20 year old design at this point. I'm sure you can find much better these days.
Because 1) I have one, 2) I have an accurate simulation model of the 76mm compressor on the front of it and 3) It's almost what was run on the F2 cars so I have bags of real world data. Turbo's are easy to change at a later date if required but the wins available by going into something with solid data cannot be underestimated.
Magnum 475 said:
Beautifully done but very big - you have to give it to the Boxster platform though, there isn't much that won't fit in the back! I did toy with the idea of a big naturally aspirated motor but I have that in the 996 with the 3.7 and given I don't have a turbo car in the fleet and have a lot of boosted applications in my past the idea of building what is essentially the F2 motor for the back of it appealed greatly. ATM said:
Pop
Slightly off topic but 986 related - I promise. I'm trying to use a 986 16 inch rear on my 3.2S and it doesn't fit. Same problem I had with the 996 if you remember. Fouls on the toe arm. So I'm wandering if there are any non OEM type arms which might have a lower profile ball joint link or mounting. Can you think of any please?
That's tight! Something with a rose joint as the outer link will likely be your best bet as the joint body is pretty skinning in Z and you've got plenty of room for the fastener: Slightly off topic but 986 related - I promise. I'm trying to use a 986 16 inch rear on my 3.2S and it doesn't fit. Same problem I had with the 996 if you remember. Fouls on the toe arm. So I'm wandering if there are any non OEM type arms which might have a lower profile ball joint link or mounting. Can you think of any please?
https://suspensionsecrets.co.uk/product/suspension...
You could modify the stake collar to bring the joint up close to the upright (as there is very little misalighnment to compensate for there) but in doing so you will also be impacting the bump steer.... how much is calculatable once you know the reduction but it'll be pretty small given the short distance we're talking about here.
As a package check I'd probably order a cheap joint from McGill and mock it up with a bolt and washers to look at the maximum packaging height available - remember wheels move about on the hubs so a fag paper/blonde one is not going to be sufficent clearance as it's good practice to allow for an amount of wheel bearing failure/aging etc.
Bit of an update on the "Booster". CAD is done as far as it's getting done at this point, I need to get the car up in the air to confirm some overall lengths but it's all in a form where this can be accounted for in a few minutes in CAD so happy to say that'll do for now:
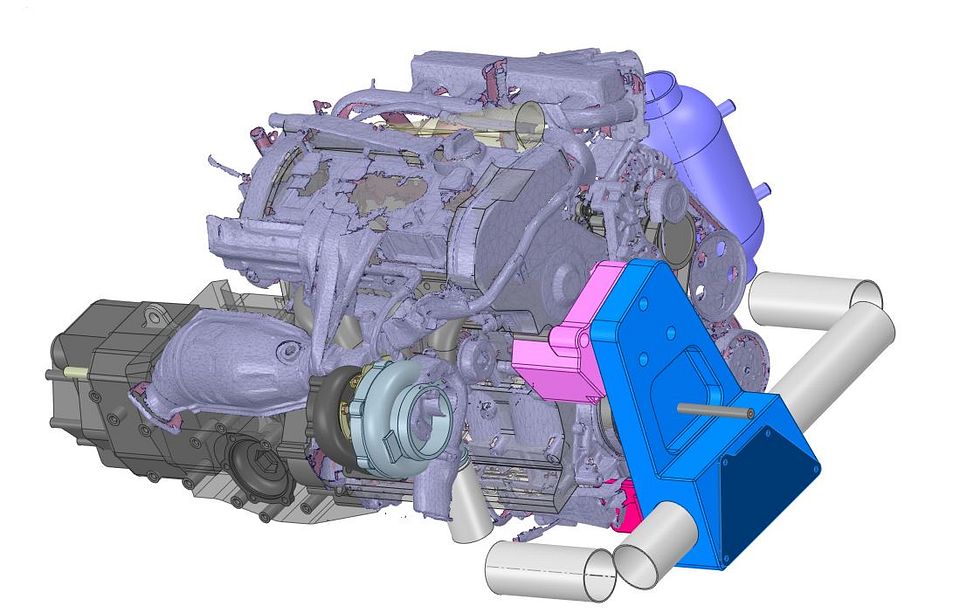
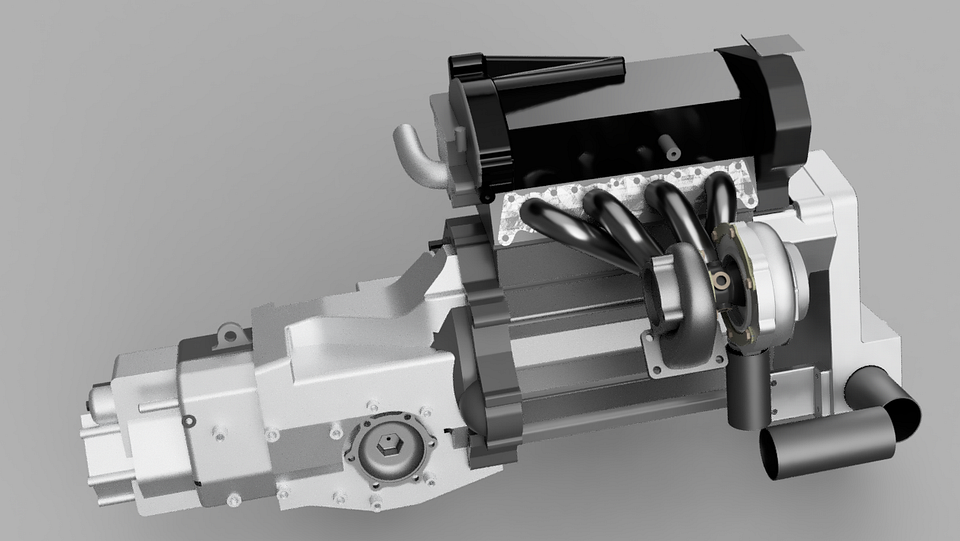

One of the last jobs to do before it goes out for machining will be a bit of prettying up but we'll get round to that once the overall package length is 100% known
Looking good to kick engine build off at the end of this month too with a fairly vast array of bits turning up including a load of plumbing and general bits and bobs as well as all the major bits. Very much looking forward to putting it together now!
Still to do is:
- Measure up and design the exhaust Y pipe.
- Measure up and design the downpipe.
- Finish working out which wires will need to go where, although I've hashed out all the loom drawings from the ME7.5 Golf and the Boxster so that's not too much of a job.
- Make a test rig up to work out where the standard Boxster oil level sensor needs to go to get an accurate oil level on the dash.
- Decide how much of the standard fillers/dip stick I'm going to use and how best to plumb those.
Still it's getting there at a reasonable pace
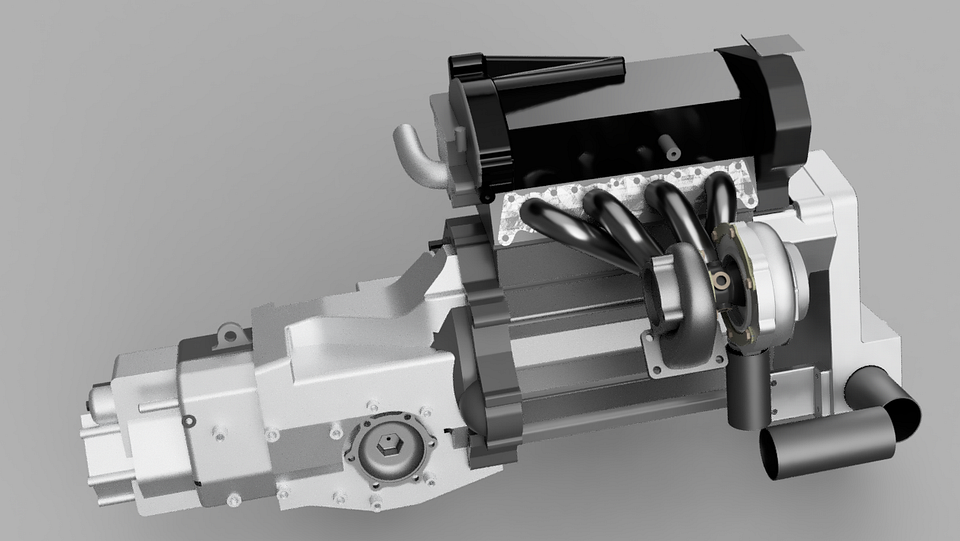

One of the last jobs to do before it goes out for machining will be a bit of prettying up but we'll get round to that once the overall package length is 100% known

Looking good to kick engine build off at the end of this month too with a fairly vast array of bits turning up including a load of plumbing and general bits and bobs as well as all the major bits. Very much looking forward to putting it together now!
Still to do is:
- Measure up and design the exhaust Y pipe.
- Measure up and design the downpipe.
- Finish working out which wires will need to go where, although I've hashed out all the loom drawings from the ME7.5 Golf and the Boxster so that's not too much of a job.
- Make a test rig up to work out where the standard Boxster oil level sensor needs to go to get an accurate oil level on the dash.
- Decide how much of the standard fillers/dip stick I'm going to use and how best to plumb those.
Still it's getting there at a reasonable pace

gofasterrosssco said:
Haha Quite! Could you please advise the length of your 1.8T engine (bell housing flange to end of crank pulley)? You seem to have a decent amount of space between the engine and bulkhead.
Definitely end of pulley on the 1.8T or to the mounting face of the front engine mount? The latter would give you the total available length with the box in the standard position as the bulkhead is pretty much inline with that. Let me know and I'll get the measuring tape out. Some of what you see on the CAD is space claim waiting to be finalised so it's not quite that much but it's pretty significant!
I've seen yours and I like it a lot! When I was deciding what motor to go for on this project I re-read your thread. Top job doesn't quite do it justice!
. I was told "it ends up at an angle" but of course that can only happen if the front engine mount height is incorrect - either way it all fits on CAD and there's plenty of sump clearance so we'll see when it's in the car.
..... K20 swaps are what Elise were built for after all 
) so should PNP. I am going to retain the original cable pedal and just mount the DBW pedal sensor in place of the 90 degree drive for the original throttle cable.
How has yours been with regards bay thermals? The surface temps are going to be pretty high on mine around the exhaust manifold, turbine housing, downpipe and cat - certainly WAY more than would ever have been tested originally in that area on account of how much more energy is kicking around on that side (370kW minus turbine vs 75kW originally
) so I'm super keen to try and get ahead of that issue. I'm hoping that given the significant increase in free space around that area it'll be pretty easy to get away with although free flow into the bay will be somewhat restricted as the air intake is on one side and the other side is being used to feed the charge cooler heat exchanger with the outflow into the bay so whilst the deltas will still be good vs the manifold surface temps it'll have an impact on flow.... still finding this out is all part of the fun right 
Escy said:
Is all your CAD done with the gearbox in the original position or are you lowering it? The 1.8t's I've seen in a Boxster have problems with the height. I've seen lots of people start these swaps (mainly in the US), not sure I've seen a completed car though.
There's a couple of AEB ones in the US but very few 06A based ones if any. I've heard this height thing from someone else but don't really understand it as the crank centreline is the crank centre line, that's the only bit between engines that doesn't change 
Escy said:
There is a guy in America (or maybe Canada) that is developing a K20 swap for a Cayman (he's on YouTube), he ended up going transverse mounted. It seems wrong but it made a lot of sense when you saw it from a packaging point of view.
I think this is a case of so concerned if he could he didn't stop to think if he should 

Escy said:
I ran a Boxster 5 speed (with a Kaaz diff in it) at 400ft/lbs with no issues.
Officially it's 420NM and I'm trying to stick to the OEM ratings for everything on this (hence an RS4 clutch etc.). I can make the power required inside of that rating albeit over the RPM limit for the box slightly when on the PTP but they're a tough old gearbox for sure! Escy said:
Some things that might be useful information. The later 986 (and 987) 5 speed gearbox has output flanges with larger bolts (up from M8 to M10) with larger driveshafts.
Weirdly they're rated at the same torque though despite being heavier! It could have been a metallurgy change for cost down though or just no requirement to durability at anything higher but I can't find any info on that or who drew them originally or an actual reason for the change. The 996 was the same with gen 2 cars going to thicker rear shafts but again they were rated at the same torque. Escy said:
The stock Boxster DBW pedal worked fine with the Audi ME7 ECU when I tried.
I've found it's the same Bosch pedal sensor on the 9X6 as on the S4 and a few other Audis (and 3.5L Formula Renault 
Escy said:
The 987 engine cover is made from aluminium rather than composite like on the 986, it's lighter and has more engine clearance so a worthwhile swap.
That's very useful, it needs +12MM at the rear to clear the rocker cover and that's an easier mod on an ally one! Thank you, very handy to know! How has yours been with regards bay thermals? The surface temps are going to be pretty high on mine around the exhaust manifold, turbine housing, downpipe and cat - certainly WAY more than would ever have been tested originally in that area on account of how much more energy is kicking around on that side (370kW minus turbine vs 75kW originally


Edited by poppopbangbang on Tuesday 19th September 23:47
Gassing Station | Readers' Cars | Top of Page | What's New | My Stuff