AWD Civic Coupe Turbo Build
Discussion
I also thought the civic had EBD.. my mistake!
If the actual connectors are the same, i would assume the wiring is the same. You can get the wiring for the EP3 online (helms manual).
My only worry is that if there is any internal biasing, similar to the EP3 ABS then it would be very difficult.. I couldnt even guess where the orifice was inside the ABS module.. This is why i thought it was too unsafe to carry on..
Not to mention a set of shelves collapsed in my garage and the ABS modultor CPU board was damaged. So essentially i have the EP3 module as a template only.. Ill have to buy another to do the job, and if the ATR does have increased functionality i would gladly use one!
If the actual connectors are the same, i would assume the wiring is the same. You can get the wiring for the EP3 online (helms manual).
My only worry is that if there is any internal biasing, similar to the EP3 ABS then it would be very difficult.. I couldnt even guess where the orifice was inside the ABS module.. This is why i thought it was too unsafe to carry on..
Not to mention a set of shelves collapsed in my garage and the ABS modultor CPU board was damaged. So essentially i have the EP3 module as a template only.. Ill have to buy another to do the job, and if the ATR does have increased functionality i would gladly use one!
interesting...
ill see what i can find.. i just found the EP3 does have EBD, so ill be fine using this system..
another thing i just found is that some VWs use a dual proportioning valve alongside the a diagonally isolated brake system. The 2 systems stay isolated but this valve (when the car dives under braking) biases pressure to the rear brakes.. If i pinch that system, with some modification and addition of some kind of adjuster, i see no reason why it cant be used to safey (and evenly) bias the output from the EP3 brake system...
ill see what i can find.. i just found the EP3 does have EBD, so ill be fine using this system..
another thing i just found is that some VWs use a dual proportioning valve alongside the a diagonally isolated brake system. The 2 systems stay isolated but this valve (when the car dives under braking) biases pressure to the rear brakes.. If i pinch that system, with some modification and addition of some kind of adjuster, i see no reason why it cant be used to safey (and evenly) bias the output from the EP3 brake system...
The firewall mounted one has long gone..
Im thinking, although the ABS controlls biasing, that is active. Whereas, those biasing valves are designed to increase pressure if the suspension height changes.
I found a forum where one has been successfully modified to assist the ABS in biasing the brakes. Plus my rear brakes are now over sized so will need reducing. I just need to make sure that the valve doesnt decrease the pressure below a usable limit..
Ill have to do some tests to see if it will all work..
Im thinking, although the ABS controlls biasing, that is active. Whereas, those biasing valves are designed to increase pressure if the suspension height changes.
I found a forum where one has been successfully modified to assist the ABS in biasing the brakes. Plus my rear brakes are now over sized so will need reducing. I just need to make sure that the valve doesnt decrease the pressure below a usable limit..
Ill have to do some tests to see if it will all work..
Im not sure.. The ABS system is reactive, so it will become active when the wheel starts to slip. My idea behind the additional manual valving, obviously controlled with a dial instead of their method, is that you can delay the onset of wheel slip by changing the basic level of bias.
The valve technology is archaic but it is still very well built, and is used still on some cars.. Plus i would buy the valve new...
The ABS system has built in bias on the rear outputs, in addition to the modulation it performs..
Im using a 1" integra Type R MC/Servo, with an Audi A4 electric vacuum pump (because of the anti lag). The front brakes are 315mm 4 piston wilwoods and the rears are 280mm with OEM calipers. But i obviously have the 4wd system and general weight distribution of the car changed.
What im simply trying to do is run additional restriction on the rear brakes, but this is based on the fact that my rear brakes are much bigger than the OEM ones, therefore i need to reduce the pressure anyway.
As i said, the valves can still be bought so i might do a bit more research, maybe register on the forum and speak to the chap that has done it already and then maybe bite the bullet and buy one to test..
The valve technology is archaic but it is still very well built, and is used still on some cars.. Plus i would buy the valve new...
The ABS system has built in bias on the rear outputs, in addition to the modulation it performs..
Im using a 1" integra Type R MC/Servo, with an Audi A4 electric vacuum pump (because of the anti lag). The front brakes are 315mm 4 piston wilwoods and the rears are 280mm with OEM calipers. But i obviously have the 4wd system and general weight distribution of the car changed.
What im simply trying to do is run additional restriction on the rear brakes, but this is based on the fact that my rear brakes are much bigger than the OEM ones, therefore i need to reduce the pressure anyway.
As i said, the valves can still be bought so i might do a bit more research, maybe register on the forum and speak to the chap that has done it already and then maybe bite the bullet and buy one to test..
Kozy said:
OK I get where you are coming from, but that is the purpose of EBD is it not? According to an SAE paper I purchased on the subject, the extra control logic over the general ABS protocol dictates the rear line pressure constantly according to the difference in the wheel accelerations between the front and rear axles, not just when the rear wheels begin to slip as with regular ABS. ABS might be reactive but EBD certainly sounds more active.
The idea is to overbrake the rear axle (as the ATR does) and afford full biasing duties to the modulator in the absence of any fixed mechanical valve, the modulator will assign correct pressure no matter what load, acceleration or road conditions prevail. With an underbraked rear axle you could have no rear pressure control at all and still be front biased up to around .6G, which obviously wastes potential.
I can send you the paper to have a read if it would be of interest?
I would love to have a read if you dont mind...The idea is to overbrake the rear axle (as the ATR does) and afford full biasing duties to the modulator in the absence of any fixed mechanical valve, the modulator will assign correct pressure no matter what load, acceleration or road conditions prevail. With an underbraked rear axle you could have no rear pressure control at all and still be front biased up to around .6G, which obviously wastes potential.
I can send you the paper to have a read if it would be of interest?
Edited by Kozy on Tuesday 21st February 15:53
What im thinking is that the abs sensors and therefore the abs can only detect wheel speed. They cant detect torque, so the abs and EBD will only take effect as the brakes start to lock up. My reason for additional bias strictly to balance the actual brake force.
ABS and EBD are designed to work when the wheel speeds themselves start to differ... Ill PM you my email address, thanks very much!
Little tiny update.
Ive been really busy building a project up for somebody. Unfortunately ive failed on the deadline which im a bit gutted about..
Last night, whilst eating my tea lol, i assembled my steering wheel controls (should have seen the looks the wife was giving me)..
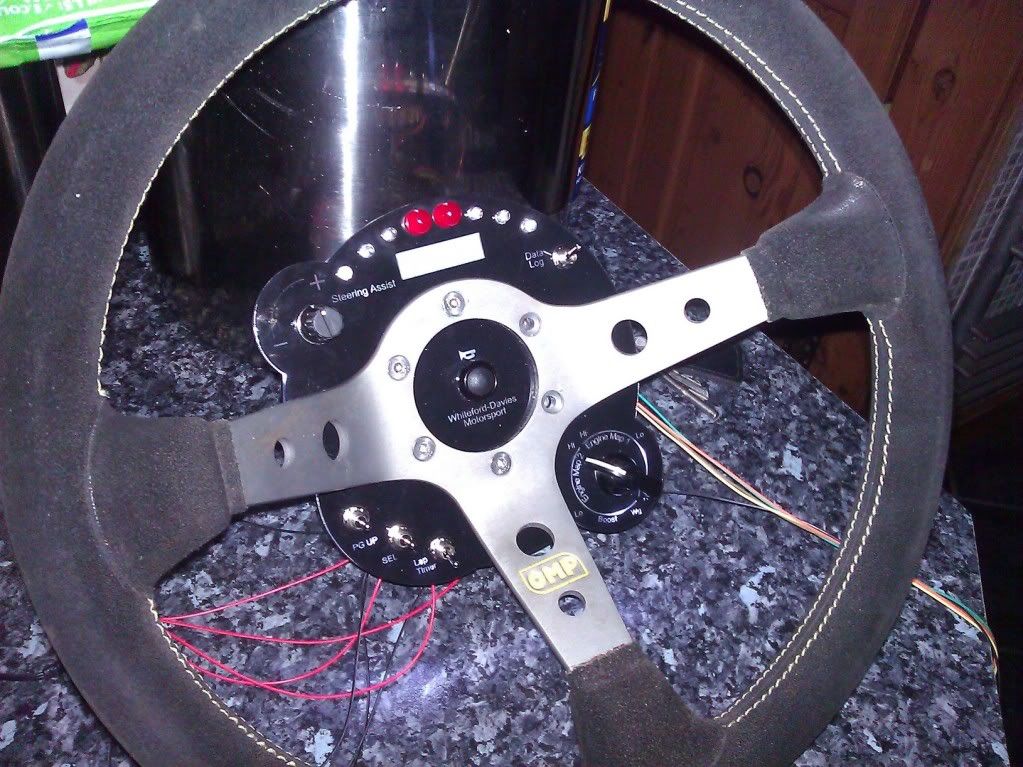
The white rectangle is actually the 4x 7 segment displays. For some reason its reflected perfectly white.. This is a multifunction screen which will show speed / current lap time / miles till empty .etc

Really sorry about the bad picture, the camera doesnt like dark and light in the same image..
Ive been really busy building a project up for somebody. Unfortunately ive failed on the deadline which im a bit gutted about..
Last night, whilst eating my tea lol, i assembled my steering wheel controls (should have seen the looks the wife was giving me)..
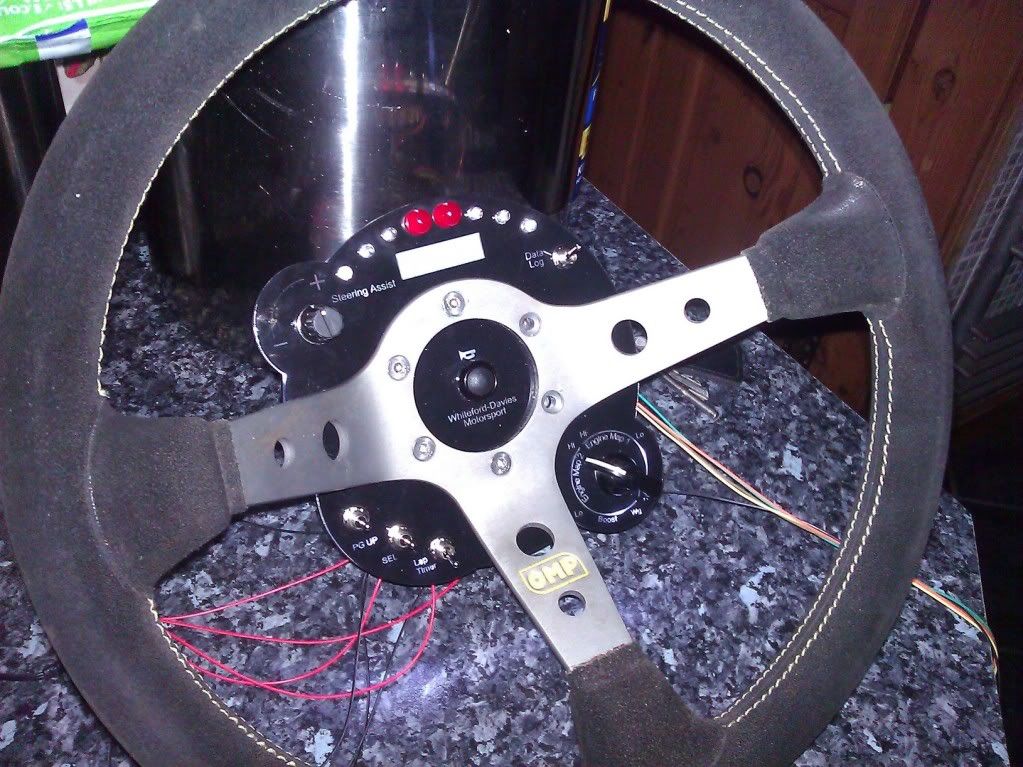
The white rectangle is actually the 4x 7 segment displays. For some reason its reflected perfectly white.. This is a multifunction screen which will show speed / current lap time / miles till empty .etc

Really sorry about the bad picture, the camera doesnt like dark and light in the same image..
Time for an update.. Its been a little while
Recently i have been very busy developing a new product. This is an extension of the coil on plug interface i have made which also allows the dizzy to be completely removed and replaced by the AEM EPM.
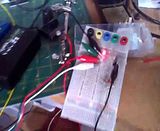
(leds represent spark outputs)

Showing emulated tachometer drive output

Okay my car.. Not a huge amount, apart from still waiting on parts to turn up. The passenger side rear wheel arch is now attached, and ive put a layer of fibreglass on the back to force it to retain the curve which the body has put on it. Ill be removing it and adding more reenforcement and using filler to make it smooth. Because of chassis flex, i wont be attempting to make them look permanent but they will look like perfect bolt ons. The drivers side was done tonight, under the watchful eyes of garrett..


Also had some time to suss out the rear diff control solution.. I stripped the diff down and removed all the hydraulics. Then i identified the 2 oil control orifices. I have drilled and tapped one for a blanking screw, the second i have drilled through to from outside and designed a plug i need to have turned. This will now allow me to supply oil externally..

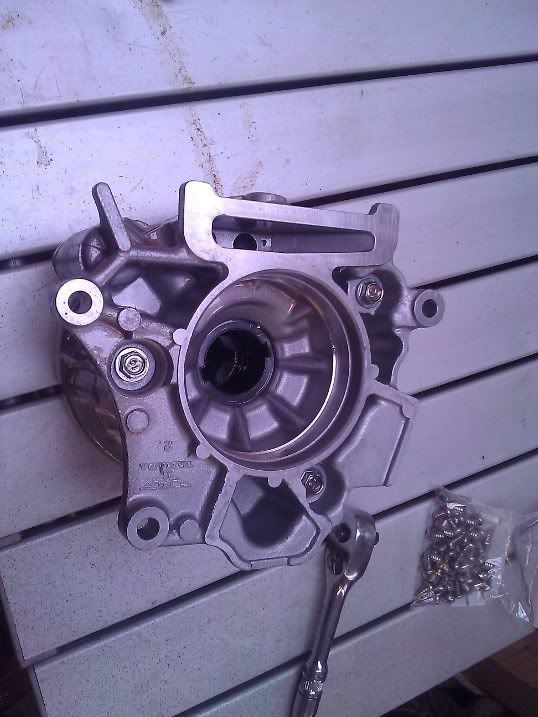

Recently i have been very busy developing a new product. This is an extension of the coil on plug interface i have made which also allows the dizzy to be completely removed and replaced by the AEM EPM.
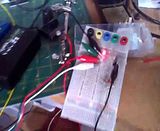
(leds represent spark outputs)

Showing emulated tachometer drive output

Okay my car.. Not a huge amount, apart from still waiting on parts to turn up. The passenger side rear wheel arch is now attached, and ive put a layer of fibreglass on the back to force it to retain the curve which the body has put on it. Ill be removing it and adding more reenforcement and using filler to make it smooth. Because of chassis flex, i wont be attempting to make them look permanent but they will look like perfect bolt ons. The drivers side was done tonight, under the watchful eyes of garrett..


Also had some time to suss out the rear diff control solution.. I stripped the diff down and removed all the hydraulics. Then i identified the 2 oil control orifices. I have drilled and tapped one for a blanking screw, the second i have drilled through to from outside and designed a plug i need to have turned. This will now allow me to supply oil externally..

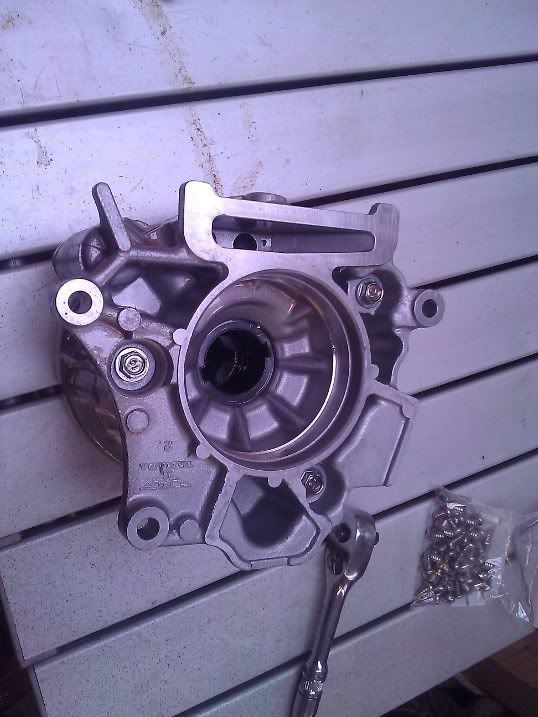

Lol thanks chaps..
Im looking forward to seeing the shakedown too.. There is most likely going to be alot of fault finding and debugging before it even hits the road..
No i dont have children at the moment, Im only 25 so i thought i may as well do this whilst i have the energy to do long days lol
most days im up at 5:15, gym, work for 7:00, till 17:00, work on my business / car stuff, wife time, bed, but sometimes ill be up till about 2:00 ish working on the computer for various things... Its working at the moment, but I honestly dont think i could manage it with children..
Im looking forward to seeing the shakedown too.. There is most likely going to be alot of fault finding and debugging before it even hits the road..
No i dont have children at the moment, Im only 25 so i thought i may as well do this whilst i have the energy to do long days lol
most days im up at 5:15, gym, work for 7:00, till 17:00, work on my business / car stuff, wife time, bed, but sometimes ill be up till about 2:00 ish working on the computer for various things... Its working at the moment, but I honestly dont think i could manage it with children..
Thats rather interesting information on the Moog valves.. wish i could afford it lol..
To be honest, its only a CRV rear diff anyway.. Im using a skyline R32 ATTESA unit to actuate it.. Need to make my own computer though. Plus as this is a much larger cylinder than the skyline, i need alot lower pressure..
Yes thats true, no kids and no sleep lol. BUt i have my chores to do, were decorating the house and landscaping the garden at the moment so im rather busy ha.
Ill get some more pictures of Garrett, i dont want to let it go to his head though..
To be honest, its only a CRV rear diff anyway.. Im using a skyline R32 ATTESA unit to actuate it.. Need to make my own computer though. Plus as this is a much larger cylinder than the skyline, i need alot lower pressure..
Yes thats true, no kids and no sleep lol. BUt i have my chores to do, were decorating the house and landscaping the garden at the moment so im rather busy ha.
Ill get some more pictures of Garrett, i dont want to let it go to his head though..
Thanks for the compliments chaps.. It really does mean a lot..
I know what you mean, but id still find it a little underhanded to taint a build thread with business stuff.. Plus i set the business up in order to fund the build, and thats it lol..
Its hopefully going to be a time attack car, but at least a trackday car.. Obviously the entrance fee for TA would probably require sponsorship.. And better tyres lol
I was offered a job by Williams F1.. But i unfortunately couldnt relocate so it wasnt affordable, im not dwelling on it and to be honest i hold on to it as it proves that i could have done it.. Id love at some point to do this sort of thing for a living but this is probably as close as im going to get lol
I know what you mean, but id still find it a little underhanded to taint a build thread with business stuff.. Plus i set the business up in order to fund the build, and thats it lol..
Its hopefully going to be a time attack car, but at least a trackday car.. Obviously the entrance fee for TA would probably require sponsorship.. And better tyres lol
I was offered a job by Williams F1.. But i unfortunately couldnt relocate so it wasnt affordable, im not dwelling on it and to be honest i hold on to it as it proves that i could have done it.. Id love at some point to do this sort of thing for a living but this is probably as close as im going to get lol
oooh ouch lol...
No not very many updates at the moment..
I bought this;
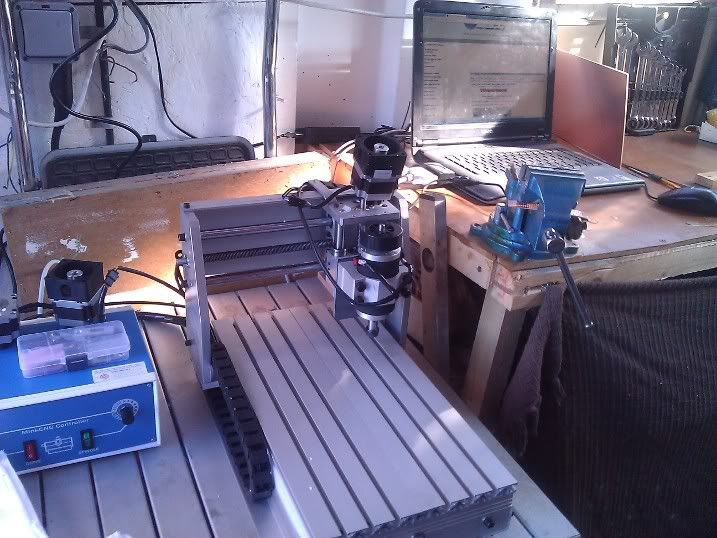
for my business, so im using it to make PCBs and small aluminium parts.. Not a bad little thing, its exceeded my expectations..
i finished the final DBW, i wasnt happy with some jitter it had so i redesigned it from scratch..
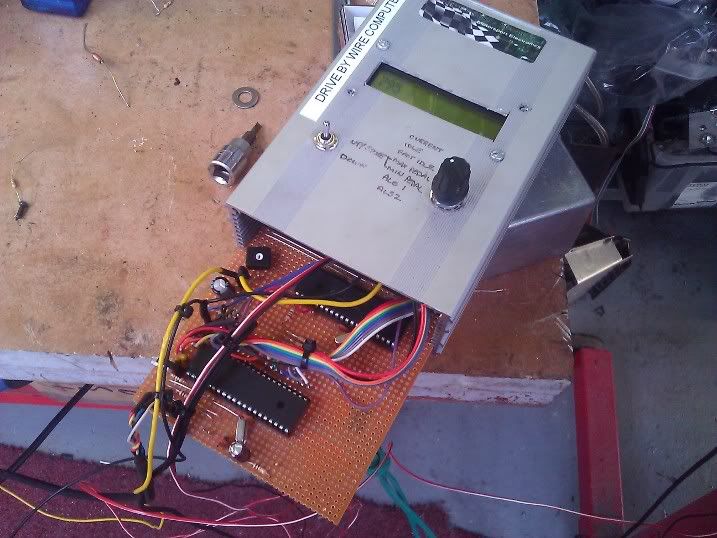

(connected to a function generator so it was opening and closing fully for 2 hours)
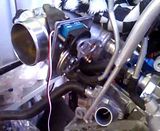
Ive figured out how to attach my arch flares properly, so they wont flex and yet remain separate. So i have ordered some extra wide ones, they should be here soon.
Thats it really
No not very many updates at the moment..
I bought this;
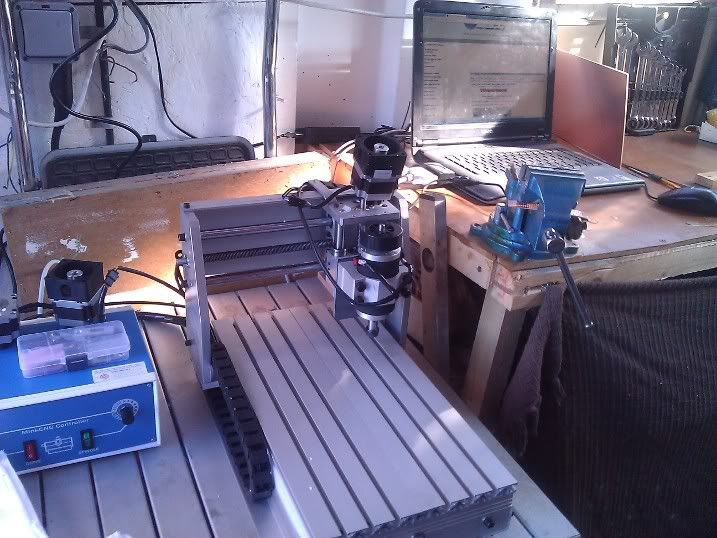
for my business, so im using it to make PCBs and small aluminium parts.. Not a bad little thing, its exceeded my expectations..
i finished the final DBW, i wasnt happy with some jitter it had so i redesigned it from scratch..
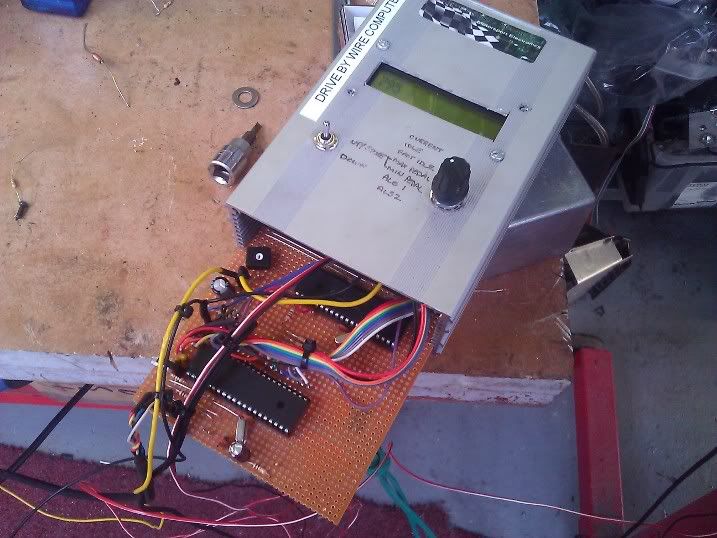

(connected to a function generator so it was opening and closing fully for 2 hours)
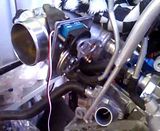
Ive figured out how to attach my arch flares properly, so they wont flex and yet remain separate. So i have ordered some extra wide ones, they should be here soon.
Thats it really
i couldnt agree more mate- and im always open to suggestions..
i have a few backups in the system..
1) youre correct, im using a high spec hobby servo. And youre correct, as standard there is no spring return, however the mechanism ive designed incorporates an idle return spring.
2) Estop, already covered. As the car uses electro-hydraulic power steering and electric vacuum brakes, i have a switch on the dash for shutting down the servo / engine. Flicking the switch terminates power to both the ecu and the drive by wire controller. The engine will obviously stop and the throttle will close on the spring.
3) i have provisioned- as i still have the old TPS, a crude feedback loop on the output micro. This chip drives the position of the servo, and is aware of its physical positioning. The TPS is to be wired in and provide a basic limiting system, if the throttle position is too different to the real position (obviously within a field of delay during the seek time) it reports an error and will disable the servo (so the spring will shut it).
This isnt installed yet, the software isnt ready. I dont want to overload the new system with safety protocols until i can ensure it works as standard on the engine. Once im happy, then i can develop it. But the hardware will all be ready.
As you say, im all for playing with this, but having been trained in the aerospace industry i cant help but have picked up a real safe working mentality. I wont do anything that puts passengers or other road users at risk. If there is a system im not sure about, i will either have a redundancy, shut off or at least a self check.
i have a few backups in the system..
1) youre correct, im using a high spec hobby servo. And youre correct, as standard there is no spring return, however the mechanism ive designed incorporates an idle return spring.
2) Estop, already covered. As the car uses electro-hydraulic power steering and electric vacuum brakes, i have a switch on the dash for shutting down the servo / engine. Flicking the switch terminates power to both the ecu and the drive by wire controller. The engine will obviously stop and the throttle will close on the spring.
3) i have provisioned- as i still have the old TPS, a crude feedback loop on the output micro. This chip drives the position of the servo, and is aware of its physical positioning. The TPS is to be wired in and provide a basic limiting system, if the throttle position is too different to the real position (obviously within a field of delay during the seek time) it reports an error and will disable the servo (so the spring will shut it).
This isnt installed yet, the software isnt ready. I dont want to overload the new system with safety protocols until i can ensure it works as standard on the engine. Once im happy, then i can develop it. But the hardware will all be ready.
As you say, im all for playing with this, but having been trained in the aerospace industry i cant help but have picked up a real safe working mentality. I wont do anything that puts passengers or other road users at risk. If there is a system im not sure about, i will either have a redundancy, shut off or at least a self check.
Thanks again chaps!
I have spent a week messing with this milling machine, there are a raft of issues with it (being from china). Noise issues, interface problems with a laptop (lower voltage parallel port) .etc
I have moved the VFD (spindle PSU) externally, its not in a case at the moment so its got a nice 230vAC going through it lol.. None of the wires are shielded so ive moved them out of the way until the new ones turn up.. This was causing errors like the z axis nudging slightly, it crashed the drill bit a couple of times (breaking them) and other problems were x and y axis nudging also..
This is the final setup (at least until i can mount them in cases)

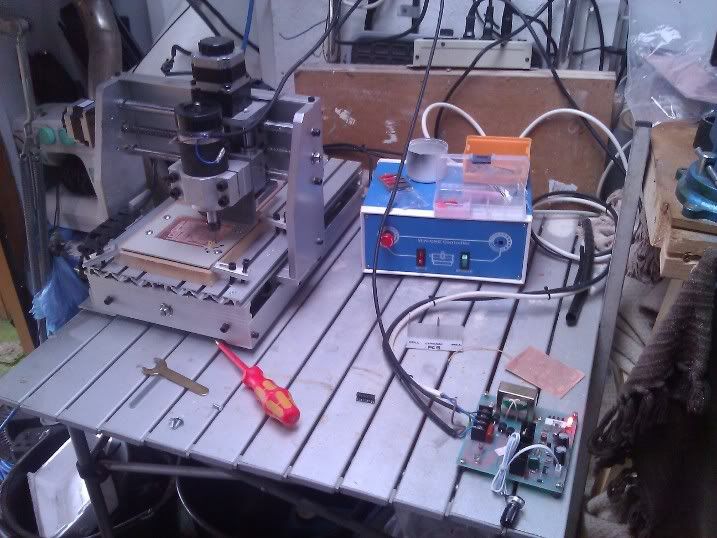
I have spent a week messing with this milling machine, there are a raft of issues with it (being from china). Noise issues, interface problems with a laptop (lower voltage parallel port) .etc
I have moved the VFD (spindle PSU) externally, its not in a case at the moment so its got a nice 230vAC going through it lol.. None of the wires are shielded so ive moved them out of the way until the new ones turn up.. This was causing errors like the z axis nudging slightly, it crashed the drill bit a couple of times (breaking them) and other problems were x and y axis nudging also..
This is the final setup (at least until i can mount them in cases)

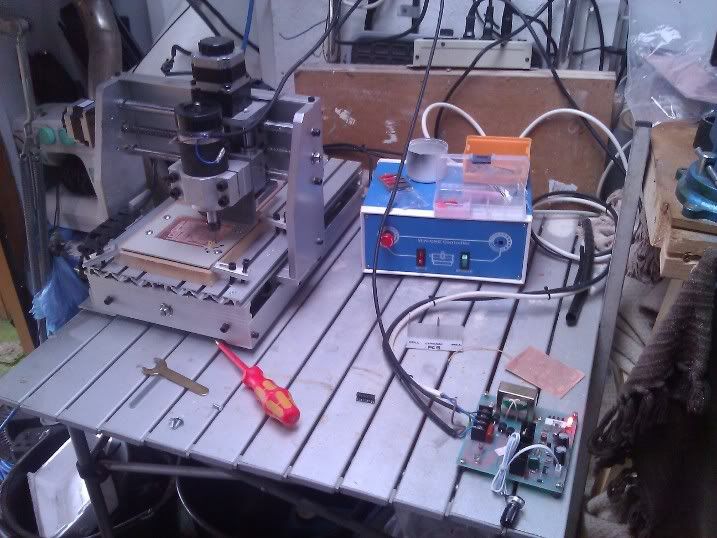
Gassing Station | Readers' Cars | Top of Page | What's New | My Stuff