325TI - Project Mpact
Discussion
Onto the rear arches, i used to have 19x9.5 et45 on the rear and i had a couple of mm clearance between the tyre and the wheel arch...... it used to rub slightly with a bit of 'spirited driving'. I wanted to roll them slightly just to gain a bit more clearance but seeing as the car was immaculate i didn't dare touch them.
A few years later with stone chips and bubbles appearing now was the perfect time to find a bit more clearance.
The inside lip of the rear wheel arches are a common place for mud to build up and prone to rusting through, with a twisted wire wheel on a grinder and various wire wheels on a drill the inside of the arch lip was taken back to bare metal. To my surprise it was absolutely spotless, not a sign of rust.
Because of the angle and lighting i couldn't get a photo of this.
The under side of the wheel arches were also ground back to bare metal using a power file to remove any rust and bubbling.
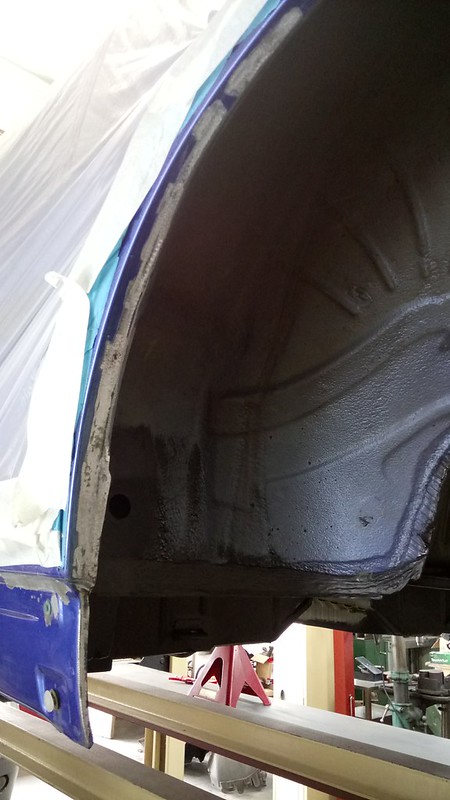
Back in 2012-2013 i built a MK1 Caddy, i made a 'quick' arch roller, it took longer to find it than it would make a new one! As it was made to suit a 4x100 stud pattern i needed to re-drill it to 5x120 to match the bmw stud pattern.
To use the arch roller i had to reinstall the rear axle carrier/arms/hubs etc.... bit of a pain it the ass.
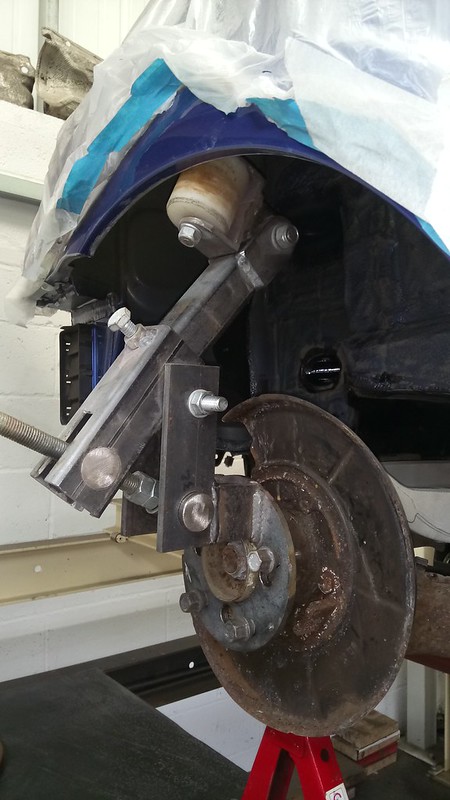
Being very careful the arches were rolled, i only wanted to roll the edges slightly and not 'pull' the arches out or distort the shape of the rear quarters. After a lot of faffing 6mm each side has been gained, it may not seem much but it will certainly stop any rubbing!
A few years later with stone chips and bubbles appearing now was the perfect time to find a bit more clearance.
The inside lip of the rear wheel arches are a common place for mud to build up and prone to rusting through, with a twisted wire wheel on a grinder and various wire wheels on a drill the inside of the arch lip was taken back to bare metal. To my surprise it was absolutely spotless, not a sign of rust.
Because of the angle and lighting i couldn't get a photo of this.
The under side of the wheel arches were also ground back to bare metal using a power file to remove any rust and bubbling.
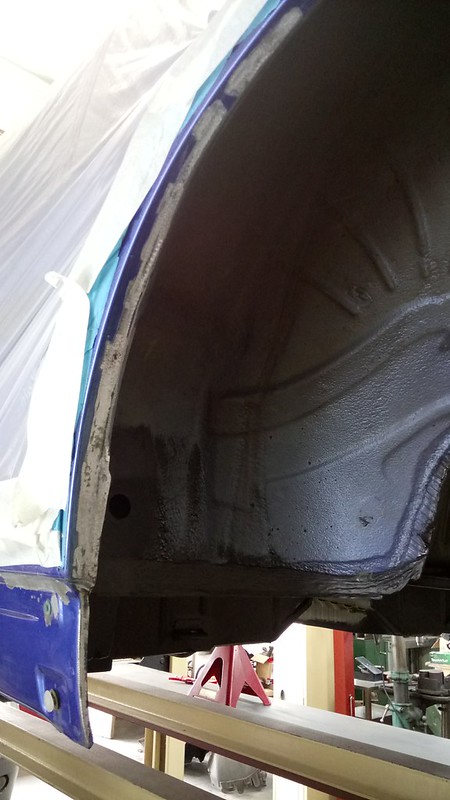
Back in 2012-2013 i built a MK1 Caddy, i made a 'quick' arch roller, it took longer to find it than it would make a new one! As it was made to suit a 4x100 stud pattern i needed to re-drill it to 5x120 to match the bmw stud pattern.
To use the arch roller i had to reinstall the rear axle carrier/arms/hubs etc.... bit of a pain it the ass.
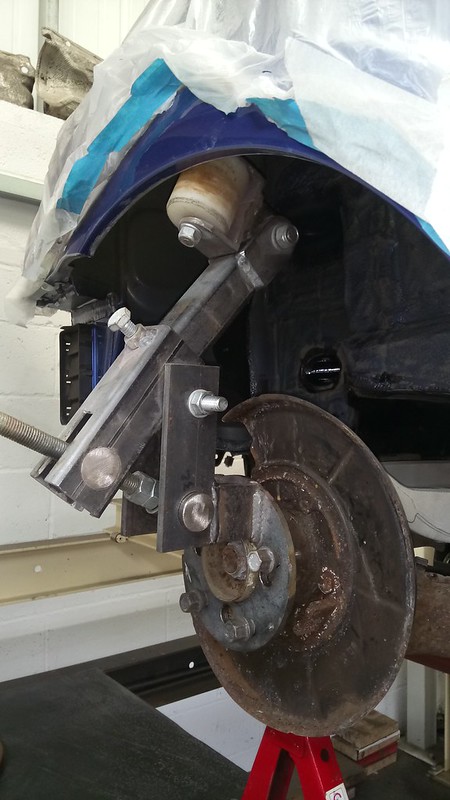
Being very careful the arches were rolled, i only wanted to roll the edges slightly and not 'pull' the arches out or distort the shape of the rear quarters. After a lot of faffing 6mm each side has been gained, it may not seem much but it will certainly stop any rubbing!
Fast Bug said:
amc_adam said:
therusterman said:
Was that the world's most over engineered dust pan I see?!
Haha, yes that is a stainless dust pan 

Great work though, I wish I had half your skill set!

Thank you, i think it's having lot's of patience rather than skill!
e30m3Mark said:
Any idea how light you'll be able to get it?
Gonna be a cracker of a car when finished.
Depends how much more dirt i find in the car to remove, can't possibly be any more hidden anywhere!Gonna be a cracker of a car when finished.

I do hope so, it's certainly turned out to be more than the engine swap it started off as!
Andrew Kettle said:
Apparently, the compact suffers less with rust in the arches than any other E46 variant, something to do with them being manufactured in a different factory (in Mexico IIRC), which used a different corrosion protection process.
Well i never knew that, learn something new every day!RoverP6B said:
AWG said:
amc_adam said:
therusterman said:
Was that the world's most over engineered dust pan I see?!
Haha, yes that is a stainless dust pan 

Dust pan aside, Back onto the compact build.
While i was inside the passenger rear arch curiosity got the better of me, i noticed a tiny split in the factory seam sealer about 5mm long. Not wanting to leave it i grabbed a screw driver and gently opened it up, the little 5mm split turned out to be a large blister and the factory sealer/paint had lifted allowing moisture to get under.
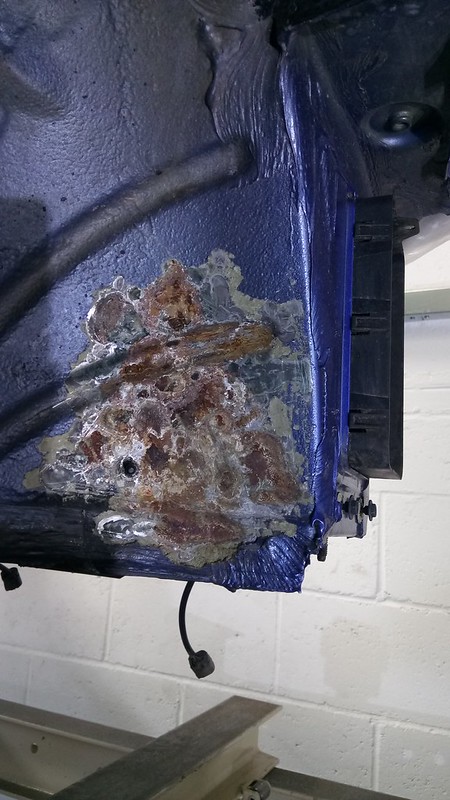
Cleaned up the corrosion
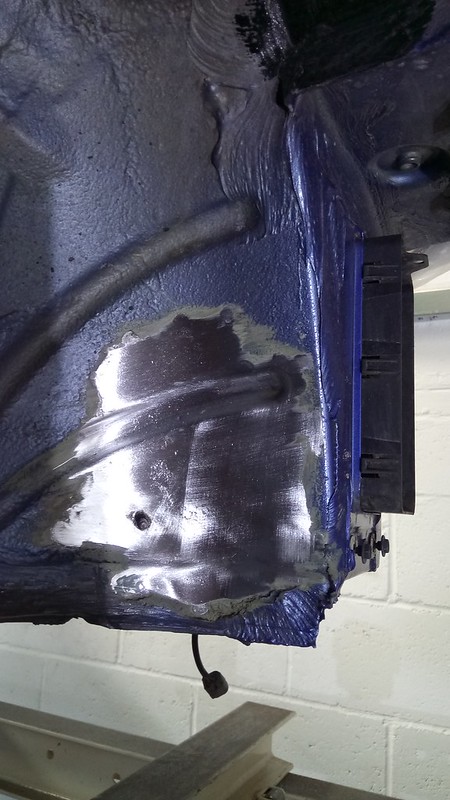
Treated with POR15
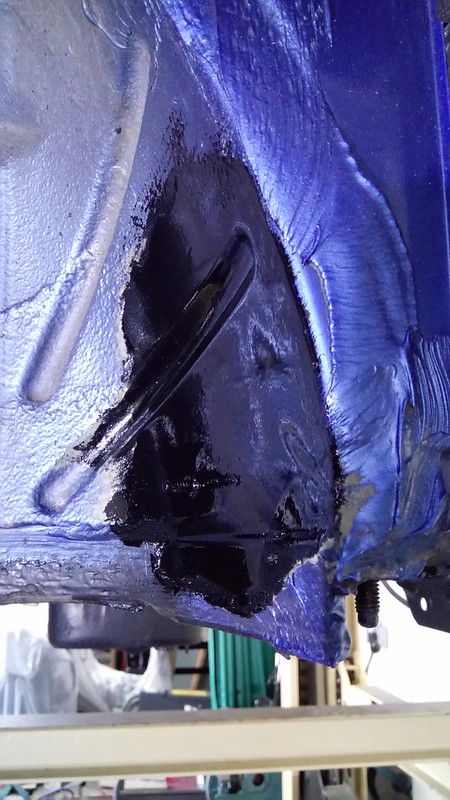
While i was inside the passenger rear arch curiosity got the better of me, i noticed a tiny split in the factory seam sealer about 5mm long. Not wanting to leave it i grabbed a screw driver and gently opened it up, the little 5mm split turned out to be a large blister and the factory sealer/paint had lifted allowing moisture to get under.
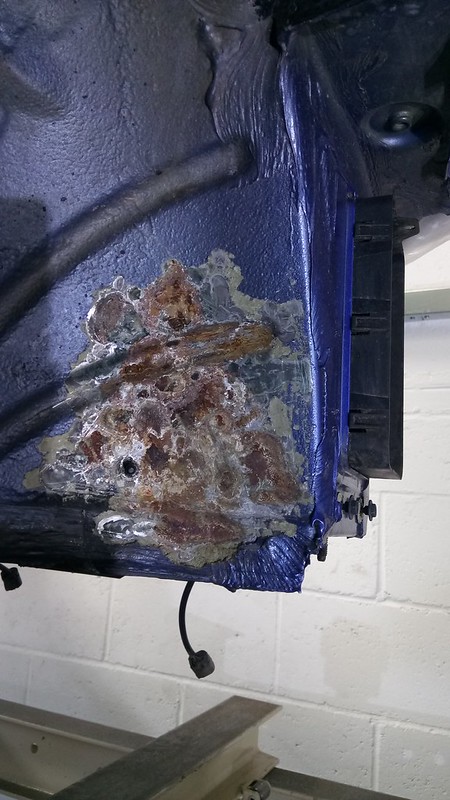
Cleaned up the corrosion
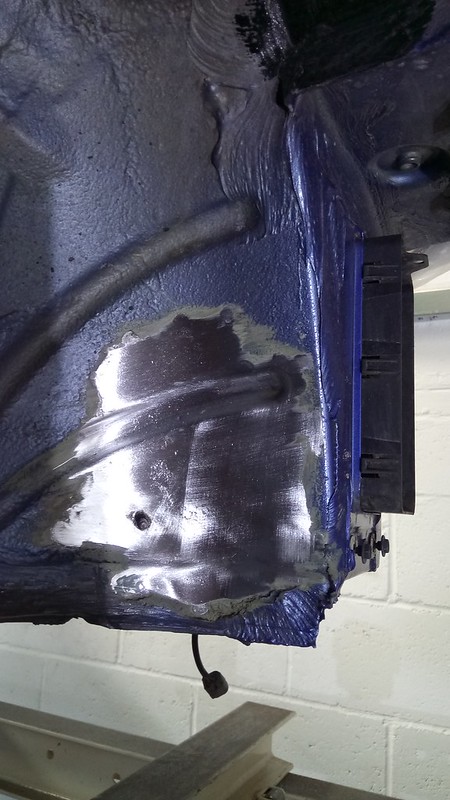
Treated with POR15
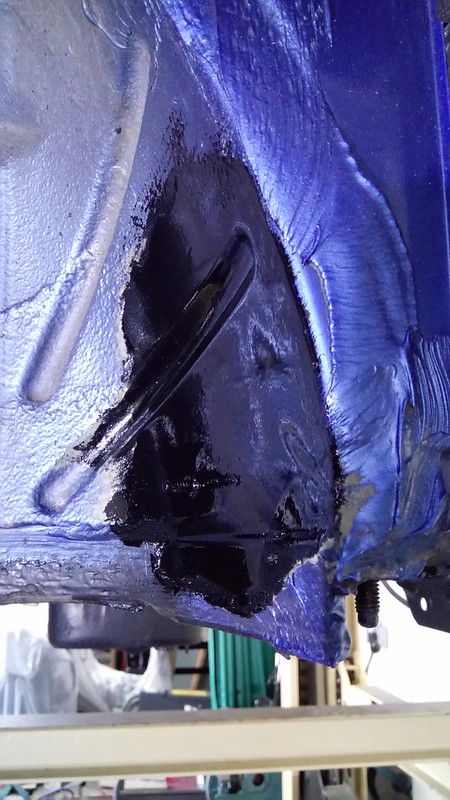
All the jacking points had a little tidy up too, where the plastic jacking point pushes into the sill some paint had rubbed off so they all got cleaned up and rust protected.
The passenger side rear jacking point/floor was the area that the 'BMW Specialist' had damaged previously, the sill/floor seam overlap had split and let moisture ingress inside.I didn't want to just leave it, so out came the grinder.....
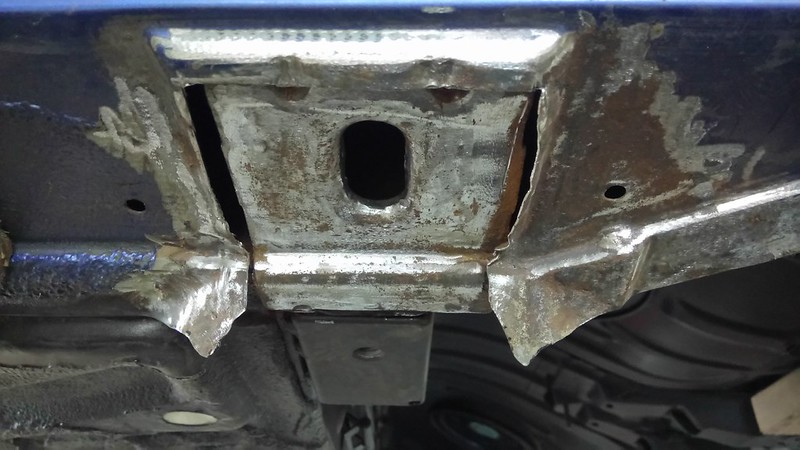
I did eventually cut out more so i could clean up inside the sill and jacking point, but i didn't photo this.... wasn't actually that bad inside. Before it was welded i rust treated everything with POR15 leaving any areas that were to be welded, these i sprayed with a weld through primer.
With it fully TIG welded and cleaned you wouldn't even know it had been opened up.
After many hours researching on how to get the OEM finish of the factory seam sealer i ordered a spray seam seal gun. With some spray seam sealer that i was advised to use by the local body shop just round the corner.
The seam sealer comes in a cartridge that screws onto the spray gun, my first attempt at setting it up while pointing it at a board i pulled the trigger and almost emptied the entire cartridge in one go
Jacking point looking much better and seam sealed,
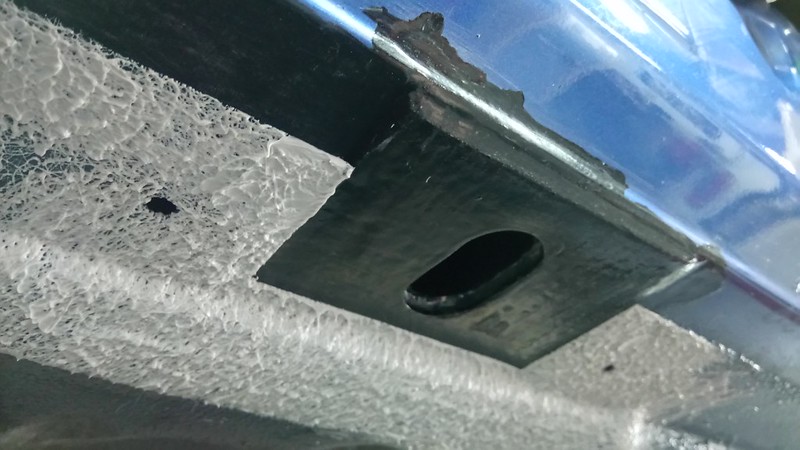
The passenger side rear jacking point/floor was the area that the 'BMW Specialist' had damaged previously, the sill/floor seam overlap had split and let moisture ingress inside.I didn't want to just leave it, so out came the grinder.....
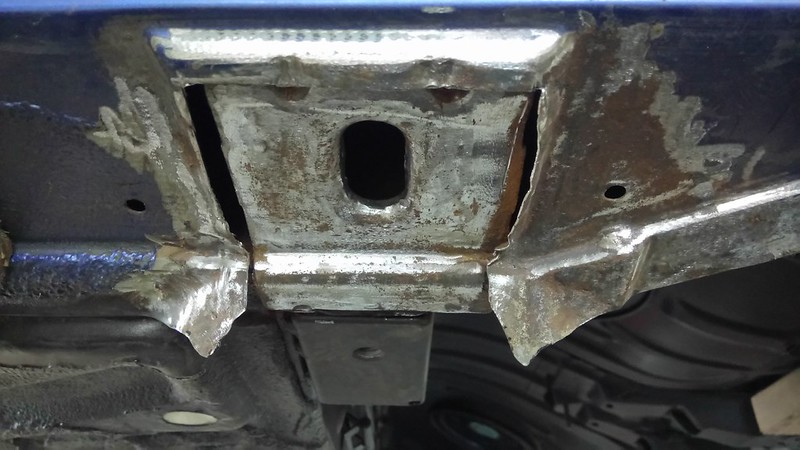
I did eventually cut out more so i could clean up inside the sill and jacking point, but i didn't photo this.... wasn't actually that bad inside. Before it was welded i rust treated everything with POR15 leaving any areas that were to be welded, these i sprayed with a weld through primer.
With it fully TIG welded and cleaned you wouldn't even know it had been opened up.
After many hours researching on how to get the OEM finish of the factory seam sealer i ordered a spray seam seal gun. With some spray seam sealer that i was advised to use by the local body shop just round the corner.
The seam sealer comes in a cartridge that screws onto the spray gun, my first attempt at setting it up while pointing it at a board i pulled the trigger and almost emptied the entire cartridge in one go

Jacking point looking much better and seam sealed,
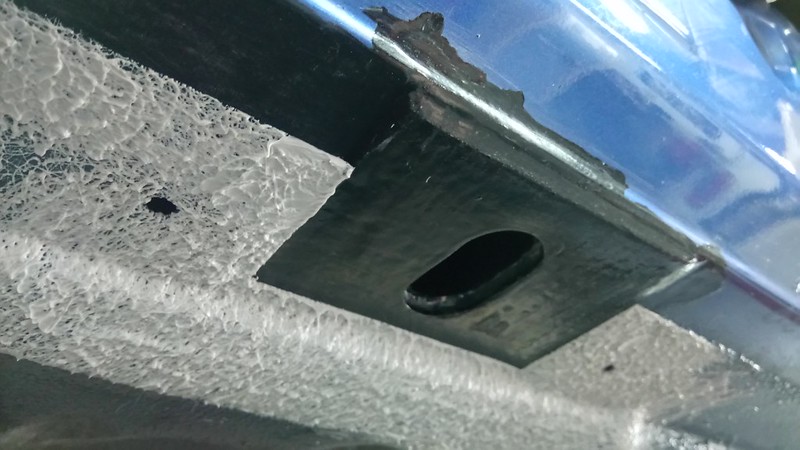
The entire under side, front and back wheel arches, floor pan and boot floor of the car was 'keyed' with scotch bight pads and sand paper to give a rough finish so that when the time comes to paint the under side it has something to stick to.
Any Factory seam seal i had previously removed from either corrosion, the reinforcement plates or just from curiosity was reapplied. I tried to do it in such a way that it would look factory as possible. I masked areas off to build it up in places, then removed the masking tape and blew over everything to blend it in, very time consuming on something that will go unnoticed.
Here you can see the mounts that i previously fitted (and forgot to photo) for where the M3 V-brace bolts onto,
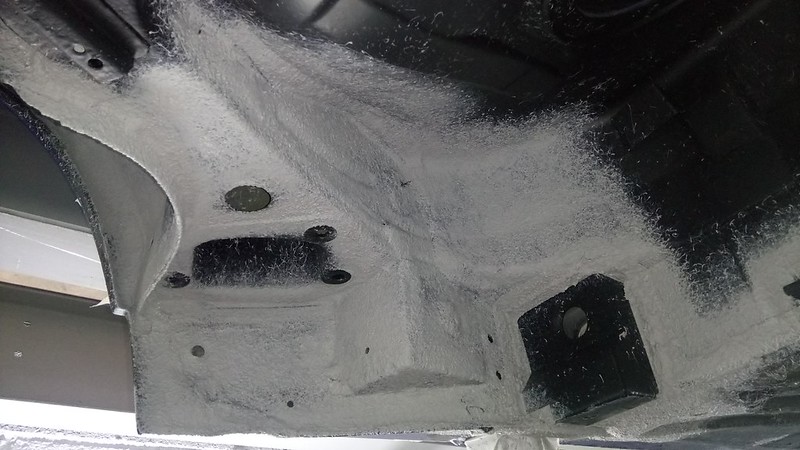
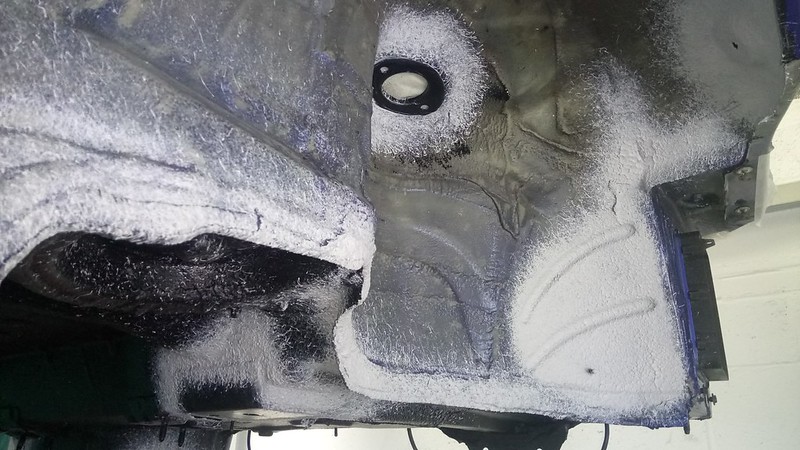
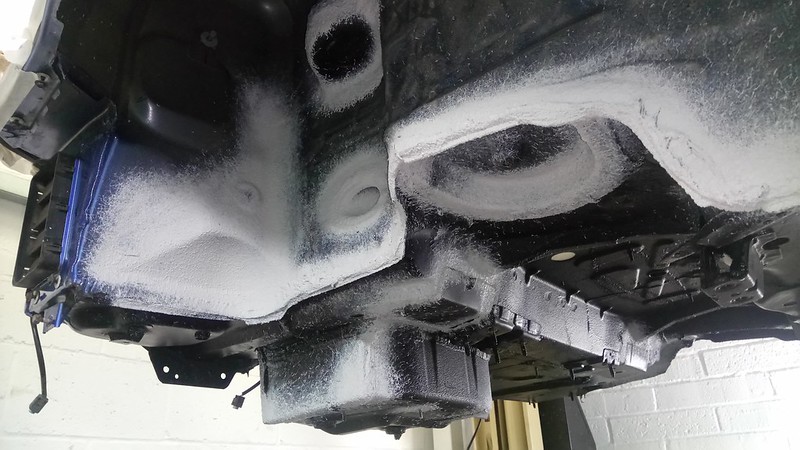
Where i had removed all the factory seam sealer from inside the rear arch lips before rolling them, i reapplied it....but instead of just spraying it over them i filled the entire lip up. So now there is nowhere for mud to build up or water to sit, after it had slightly cured i sprayed over them to blend it in.
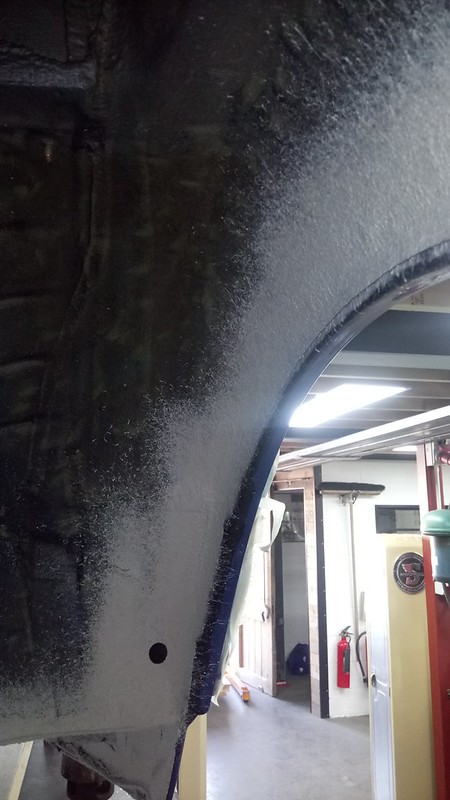
Any Factory seam seal i had previously removed from either corrosion, the reinforcement plates or just from curiosity was reapplied. I tried to do it in such a way that it would look factory as possible. I masked areas off to build it up in places, then removed the masking tape and blew over everything to blend it in, very time consuming on something that will go unnoticed.
Here you can see the mounts that i previously fitted (and forgot to photo) for where the M3 V-brace bolts onto,
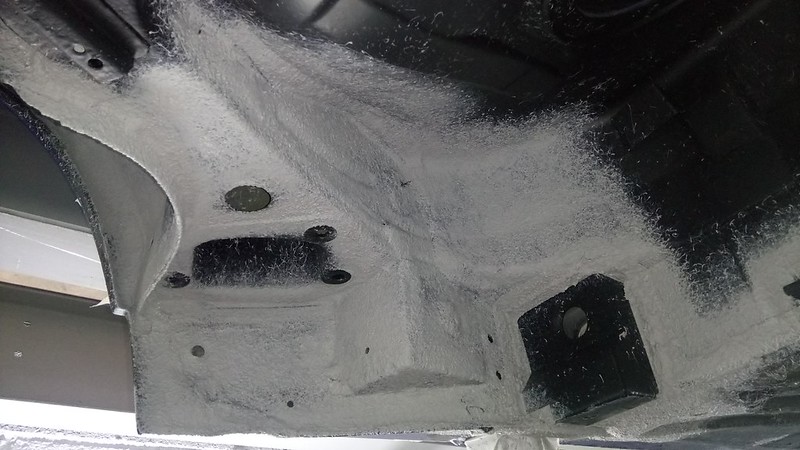
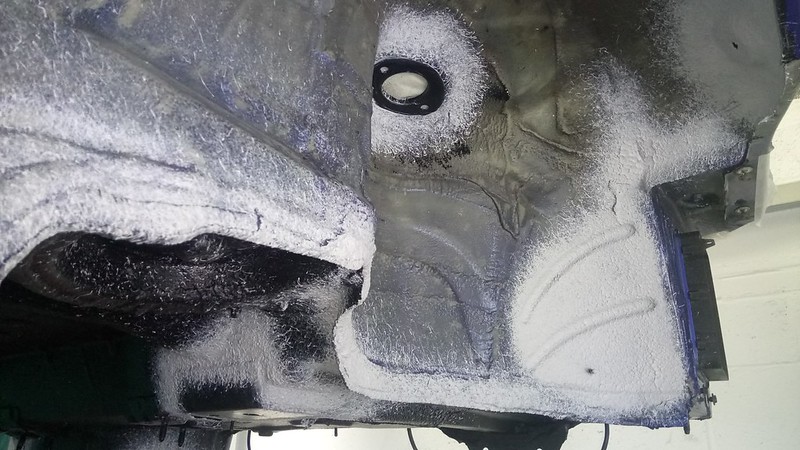
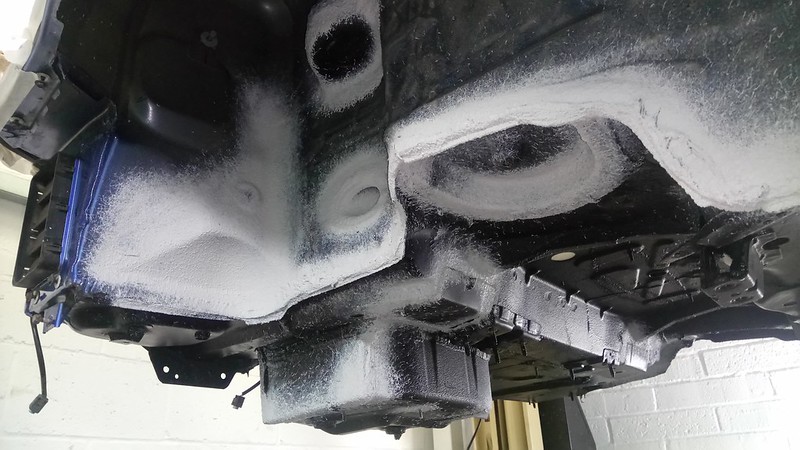
Where i had removed all the factory seam sealer from inside the rear arch lips before rolling them, i reapplied it....but instead of just spraying it over them i filled the entire lip up. So now there is nowhere for mud to build up or water to sit, after it had slightly cured i sprayed over them to blend it in.
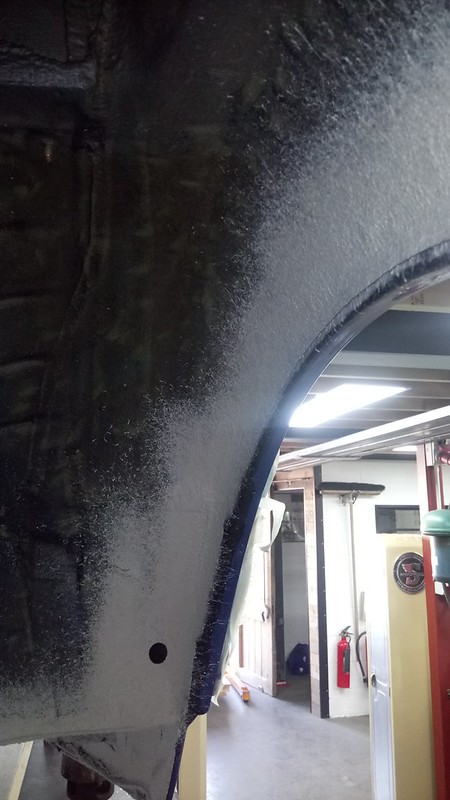
Quhet said:
The detail in this is brilliant. One of my favourite RR threads along with that bloody 500bhp fiesta that has gone too quiet.....
Thanks, think i need to start putting a stop watch next to each item that gets made like on Project Binky 
I don't think I've seen the fiesta thread? sounds interesting!
So........ to the next point / step / part of the never ending build!
Now after a lot of head scratching and Emailing various companies trying to track down the original colour code for the Factory OEM 'E-coat' used, with no reply's from anyone (maybe a trade secrete to those who know it).
With a RAL chart and the eyes of the girlfriend (i'm colour deficient, i'd choose totally wrong colour
) she matched it to the existing 'E-coat' Green of the untouched transmission tunnel. This took a couple of attempts to get right as the first colour ended up being Beige, nothing like the RAL code that was chosen.
I could of gone with colour coding the underside the same colour as the top (Estoril Blue) but for me that wasn't how it came from the Factory. The only reason the inner arches are colour coded from Factory is from the over spray from it being built on the production line.
With the entire under side (minus transmission tunnel) and all four wheel arches cleaned and degreased, every inch was prept and keyed using various abrasives.
Turned the ramp into a spray booth,
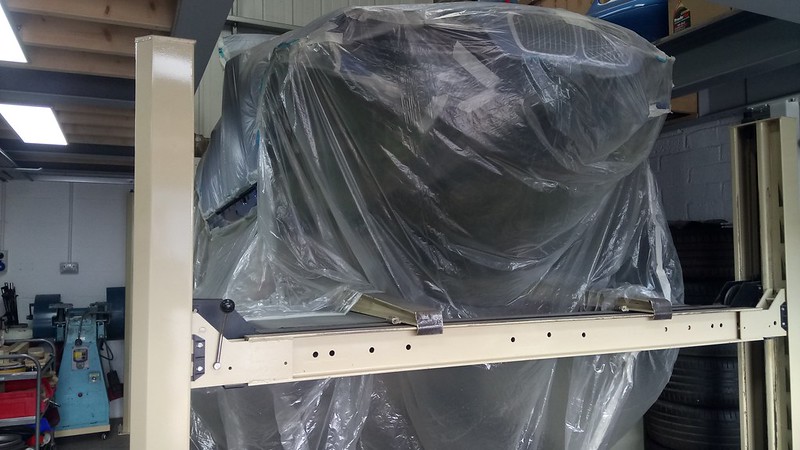
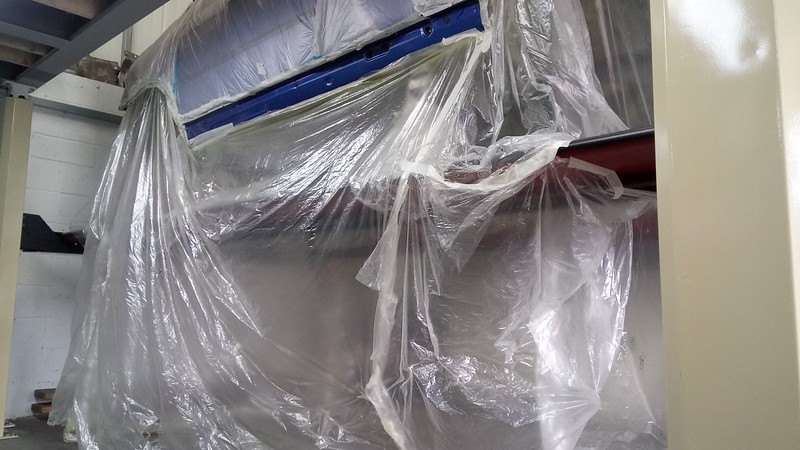
For the underside coating i used Upol Rapter, this is tintable. Quite simple to use, it comes in 1 liter bottles which screw directly onto a Schutz Gun. All that has to be done is pour some hardener to one mark on the bottle and then add the colour to the next mark...shake and squirt.
It took a bit of fiddling about with air pressures to get the finish i was after but it came out well!
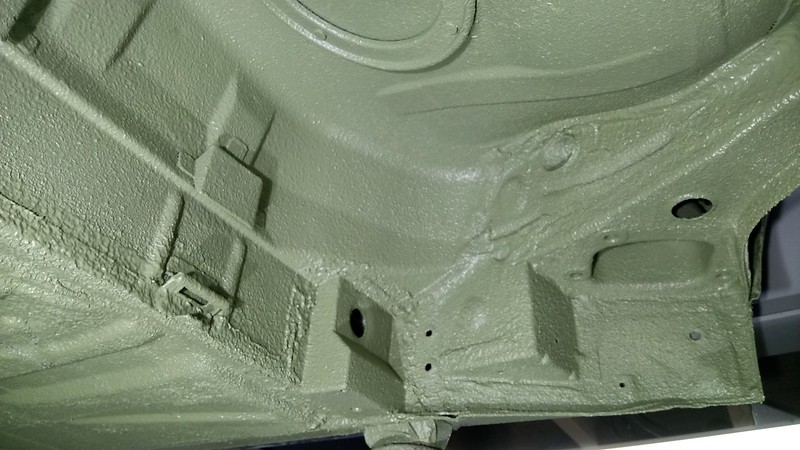
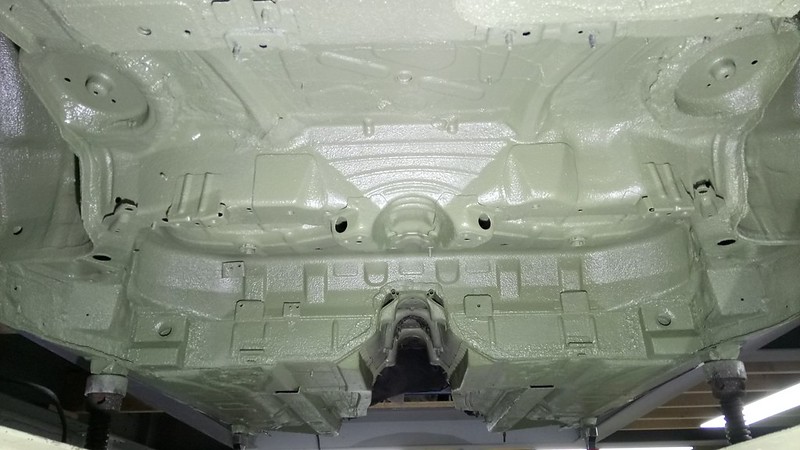
It was quite satisfying to get it to this stage, could almost start putting it back together!
Now after a lot of head scratching and Emailing various companies trying to track down the original colour code for the Factory OEM 'E-coat' used, with no reply's from anyone (maybe a trade secrete to those who know it).
With a RAL chart and the eyes of the girlfriend (i'm colour deficient, i'd choose totally wrong colour

I could of gone with colour coding the underside the same colour as the top (Estoril Blue) but for me that wasn't how it came from the Factory. The only reason the inner arches are colour coded from Factory is from the over spray from it being built on the production line.
With the entire under side (minus transmission tunnel) and all four wheel arches cleaned and degreased, every inch was prept and keyed using various abrasives.
Turned the ramp into a spray booth,
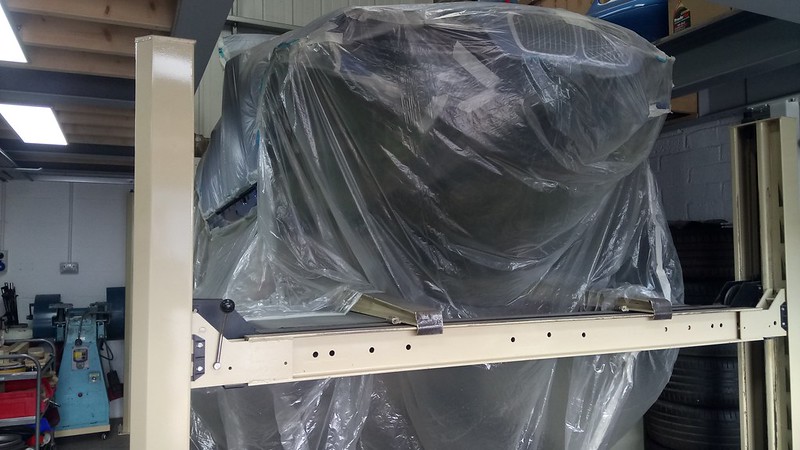
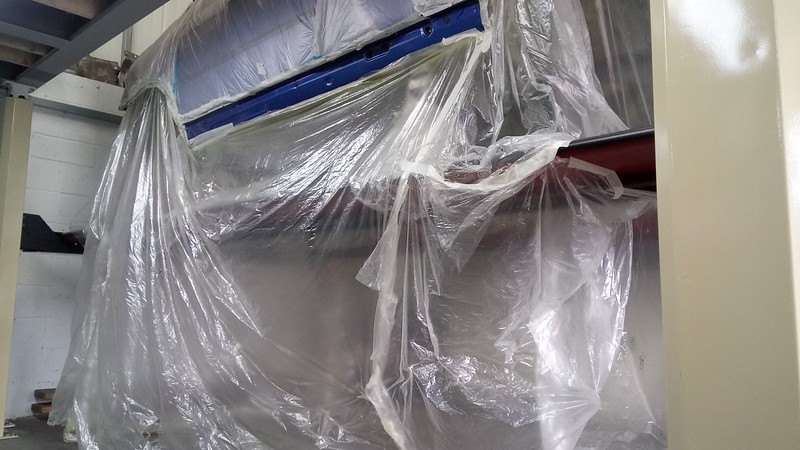
For the underside coating i used Upol Rapter, this is tintable. Quite simple to use, it comes in 1 liter bottles which screw directly onto a Schutz Gun. All that has to be done is pour some hardener to one mark on the bottle and then add the colour to the next mark...shake and squirt.
It took a bit of fiddling about with air pressures to get the finish i was after but it came out well!
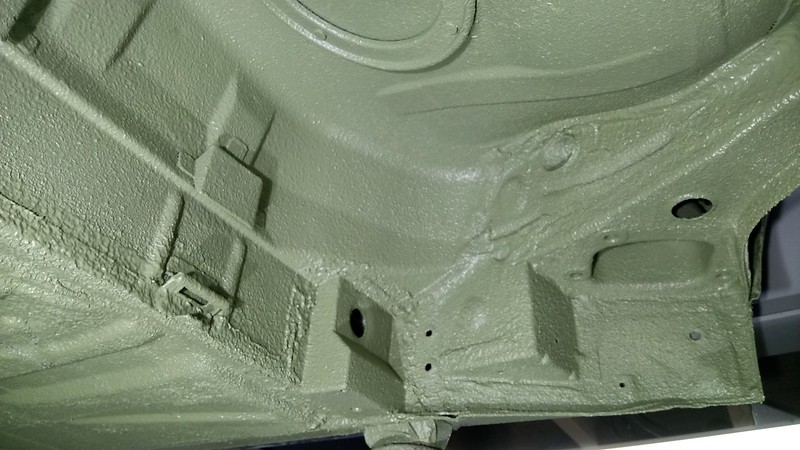
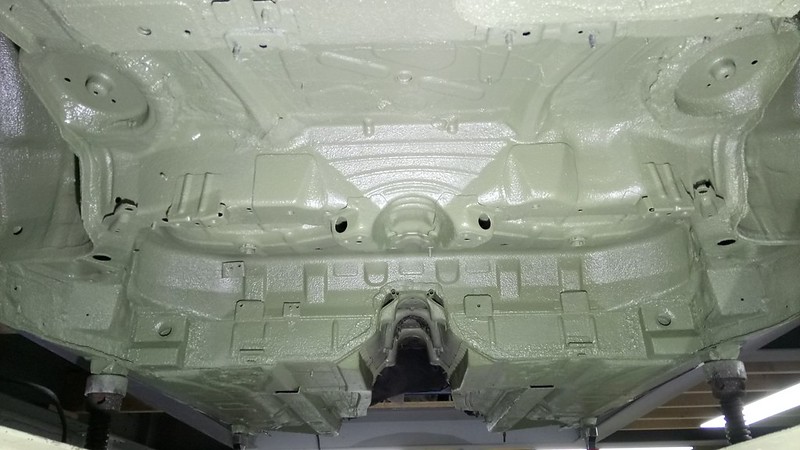
It was quite satisfying to get it to this stage, could almost start putting it back together!
eezeh said:
E91M3 said:
That would be a 316/318 as only the 325's had the battery in the rear.Looks like its coming along nicely, will be brand new by the time you've finished with it


As Eezeh said, 316/318 had there battery under the bonnet for some reason.
With the underside of the vehicle coated, i needed to cavity wax anything that had been exposed to heat from welding or just areas that needed attention, i used an Innotec cavity wax that is temperature stable (doesn't go all runny when it gets hot).
First i started from the inside of the vehicle, spraying into the cavities. I done this until i could see it running out of the bottom of the vehicle, then put the rubber bungs in and sprayed up from the underside making sure each part was coated nicely.
A couple of cans later and i'm confident I've covered/filled areas that needed it. As its transparent and inside cavities i couldn't photo this!
Back onto the rear arches, previously i showed the arches had gotten a bit tatty which was an excuse to grind back any corrosion and roll them. With all that done (previously pictured) it was back on to sort the paint out.
I'm by no means a sprayer/bodyworker but i have a rough idea what too do-ish.
The arches were back to bare metal, i then POR15 treated anything that needed it, that was then keyed. With everything masked off i Zinc primed them. Once that had dried 1/2 days it was flattened off, tack ragged and the blown in with some Estoril Blue i had mixed previously, then lacquered.
Both arches came out surprisingly well, colour is a good match too.
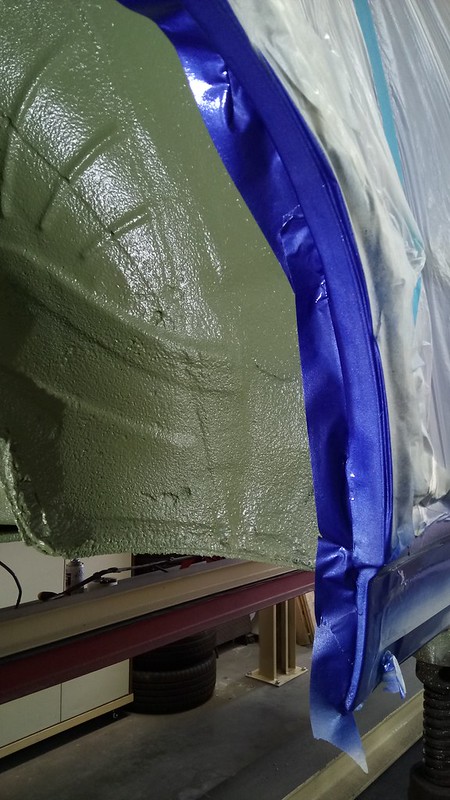
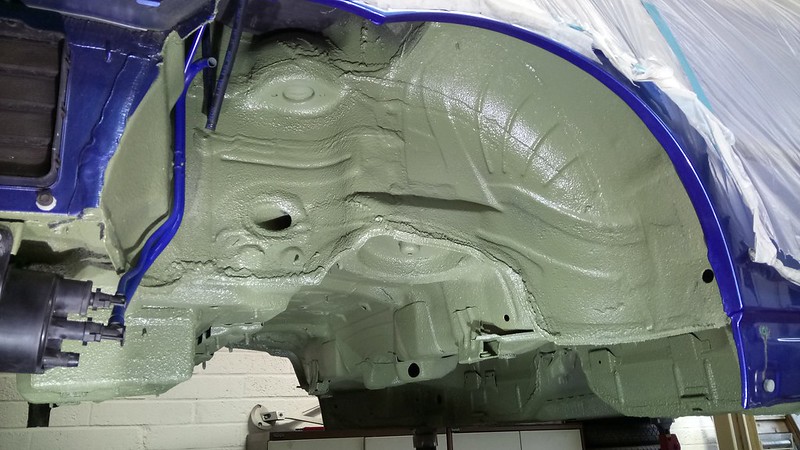
First i started from the inside of the vehicle, spraying into the cavities. I done this until i could see it running out of the bottom of the vehicle, then put the rubber bungs in and sprayed up from the underside making sure each part was coated nicely.
A couple of cans later and i'm confident I've covered/filled areas that needed it. As its transparent and inside cavities i couldn't photo this!
Back onto the rear arches, previously i showed the arches had gotten a bit tatty which was an excuse to grind back any corrosion and roll them. With all that done (previously pictured) it was back on to sort the paint out.
I'm by no means a sprayer/bodyworker but i have a rough idea what too do-ish.
The arches were back to bare metal, i then POR15 treated anything that needed it, that was then keyed. With everything masked off i Zinc primed them. Once that had dried 1/2 days it was flattened off, tack ragged and the blown in with some Estoril Blue i had mixed previously, then lacquered.
Both arches came out surprisingly well, colour is a good match too.
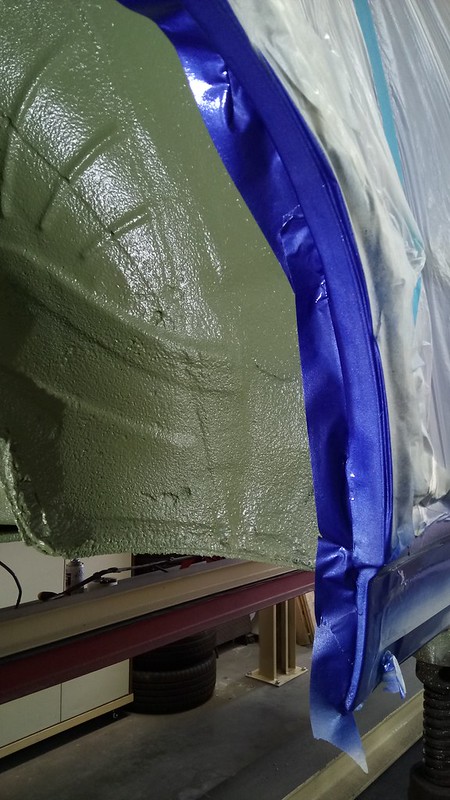
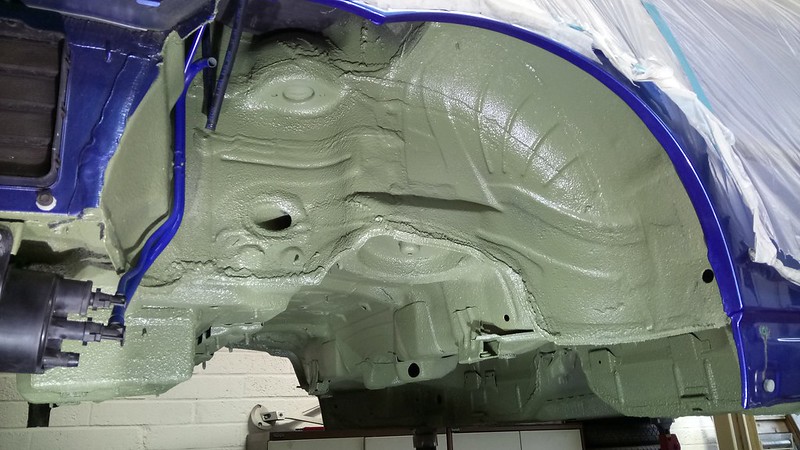
Few more bits (rear bumper shocks/mounts, subframe disc things, a few bolts and brake pipe clips) blasted and treated with the POR15, one can seems to be lasting for ever!

Next i needed to make some longer subrfame bolts as they now need to protrude through to the inside of the vehicle. These are made from high tensile threaded bar with a stainless spacer which was drilled and tapped to replicate the original part.



Next i needed to make some longer subrfame bolts as they now need to protrude through to the inside of the vehicle. These are made from high tensile threaded bar with a stainless spacer which was drilled and tapped to replicate the original part.


Brake hard lines, the rears had been changed two years previous for an M.O.T. Unfortunately the BMW 'specialist' (as mentioned previously in the thread) who done the work had made a right hash job of it and i think i would have preferred to keep the corroded ones!
So after a lot of head scratching and research, rather than going for the OEM steel lines from BMW or using copper a friend brought to my attention 'Kunifer' a copper/Nickel mix. Unlike steel it doesn't rust and unlike copper it doesn't age harden (become brittle).
I've never had to make brake lines myself, so was a quick learning curve...... but still pretty easy. After a couple of test pieces just to see how malleable it is and how tight it could be bent without kinking i managed to make these up,

They don't look much in the above photo but using the M3 donor vehicle i manged to replicate every angle and curve so they follow the exact line of the original items.
The front half of the brake lines were untouched and original, so i managed to save these and with some sand paper i took them back to bare metal.
With some black paint (POR15,again) i repainted them and the new 'Kunifer' lines.



So after a lot of head scratching and research, rather than going for the OEM steel lines from BMW or using copper a friend brought to my attention 'Kunifer' a copper/Nickel mix. Unlike steel it doesn't rust and unlike copper it doesn't age harden (become brittle).
I've never had to make brake lines myself, so was a quick learning curve...... but still pretty easy. After a couple of test pieces just to see how malleable it is and how tight it could be bent without kinking i managed to make these up,

They don't look much in the above photo but using the M3 donor vehicle i manged to replicate every angle and curve so they follow the exact line of the original items.
The front half of the brake lines were untouched and original, so i managed to save these and with some sand paper i took them back to bare metal.
With some black paint (POR15,again) i repainted them and the new 'Kunifer' lines.



Gassing Station | Readers' Cars | Top of Page | What's New | My Stuff