What Engine for 500BHP
Discussion
Evoluzione said:
+1 for trying Cometic, I stopped using Spesso after failures - one leaked water before the engine had even been started and the dealer wasn't interested in the slightest. I use nothing but Cometic MLS now on performance stuff and never had an issue.
You will need to consider stronger studs (unless you already have them?) I've got the details of a manufacturer of studs and MLS gaskets (somewhere), if you need some leads drop me a PM and I'll hunt them out.
Sounds like Cometic do decent gaskets, so I will see what they have to say.You will need to consider stronger studs (unless you already have them?) I've got the details of a manufacturer of studs and MLS gaskets (somewhere), if you need some leads drop me a PM and I'll hunt them out.
As for the studs - buying studs is the easy part, the problem is actually removing the old ones. they are screwed into an insert in the alloy block & normally are "stuck" in the insert so removing them also removes the insert & chews up the block, it can be done, but its not easy... any there is a big chance of wrecking the block....
neiljohnson said:
I know of a focus Rs that runs haltech with knock control I'm not sure if its a standard feature though
Haltech as far as I know only has knock control for car specific Pro ecu's. Its not mentioned for my Sport 2000 which is the top ECU.Logging wise I can choose only 8 channels for onboard logging, I would need to plug in the laptop to log all the channels, but it can be done. Of course i wasnt logging when I had the failiure....
OK Took the heads off today, Cylinder 4 has a blown the gasket...
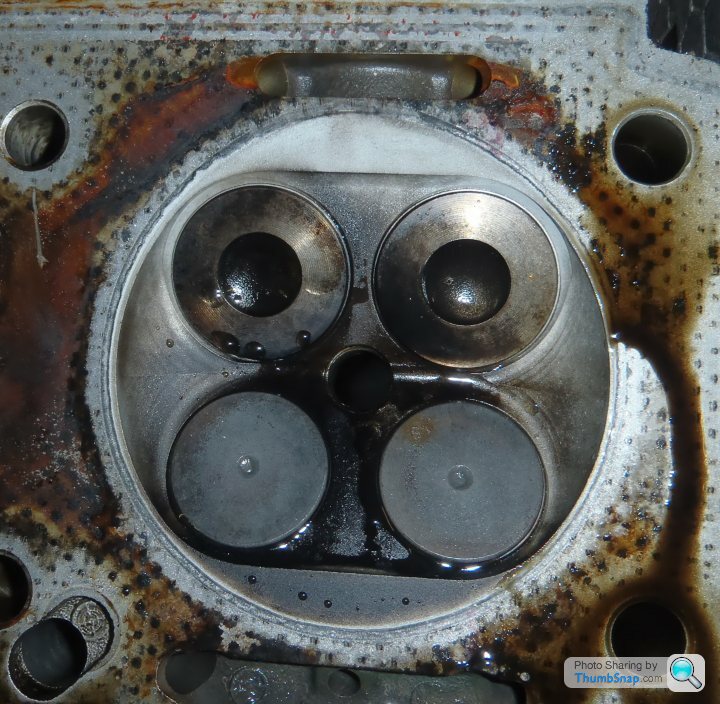
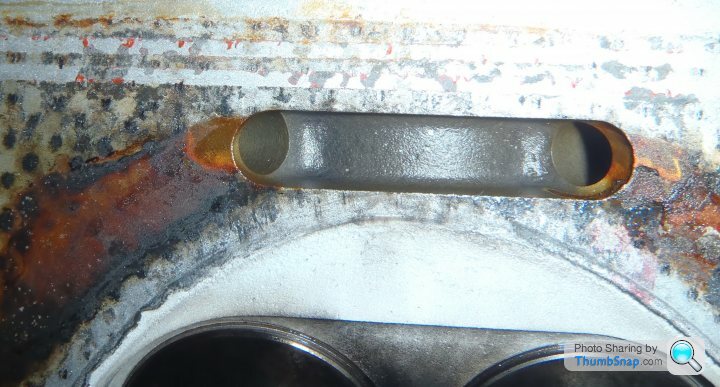
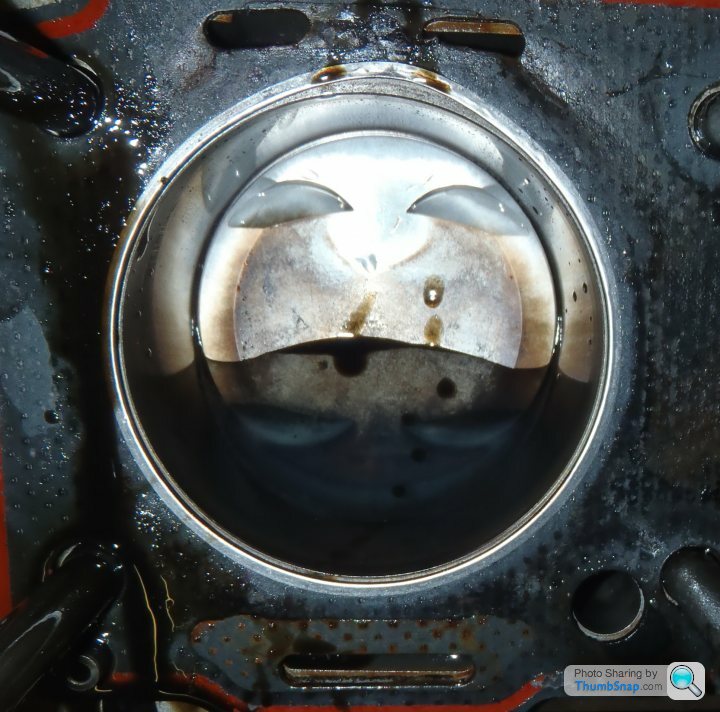
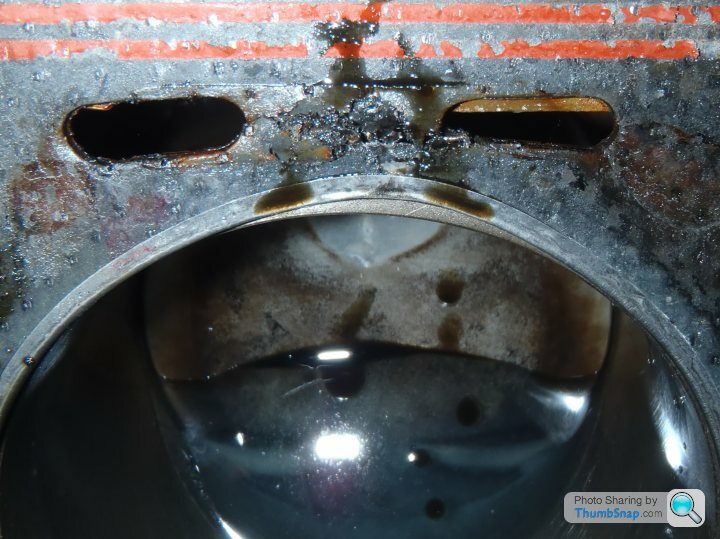

That is by far the worst one. Looking at the other cylinders, most are showing very clean piston crowns and heads between the Inlet valves and the cylinder wall. My guess would be that this is caused by detonation burning off all the carbon, not sure as I don't have any experience of this phenomenon....
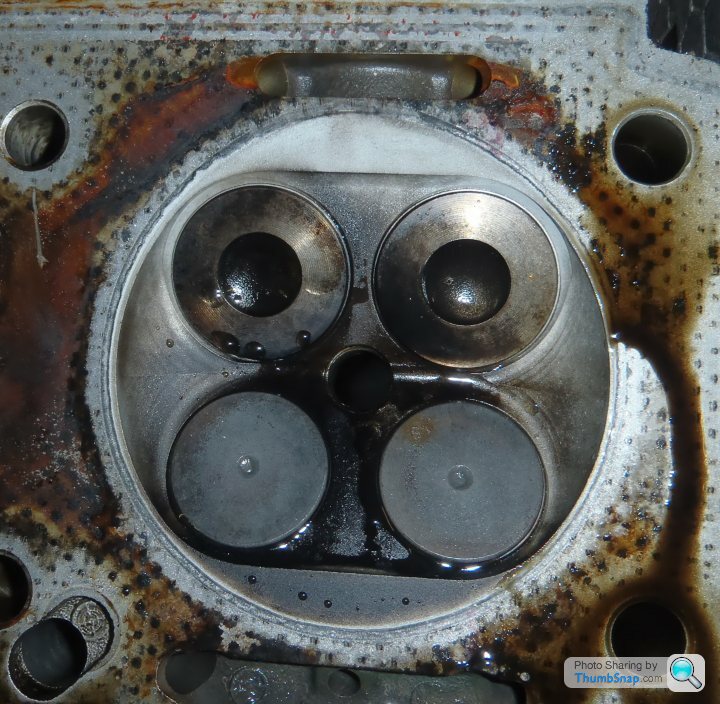
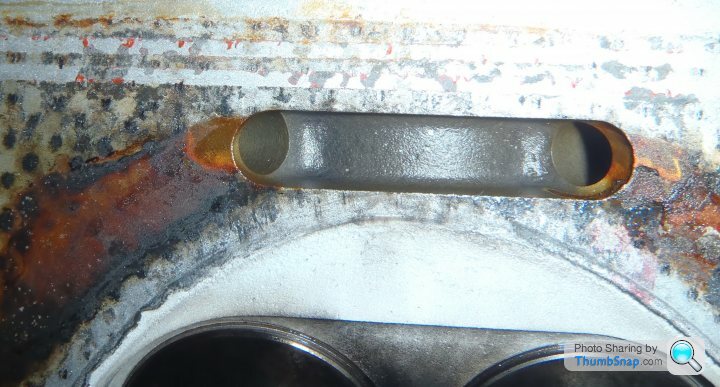
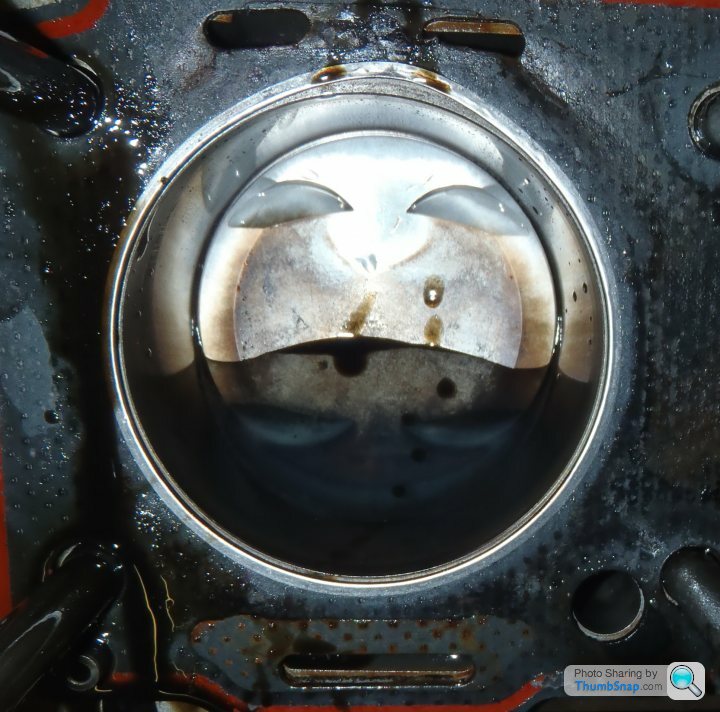
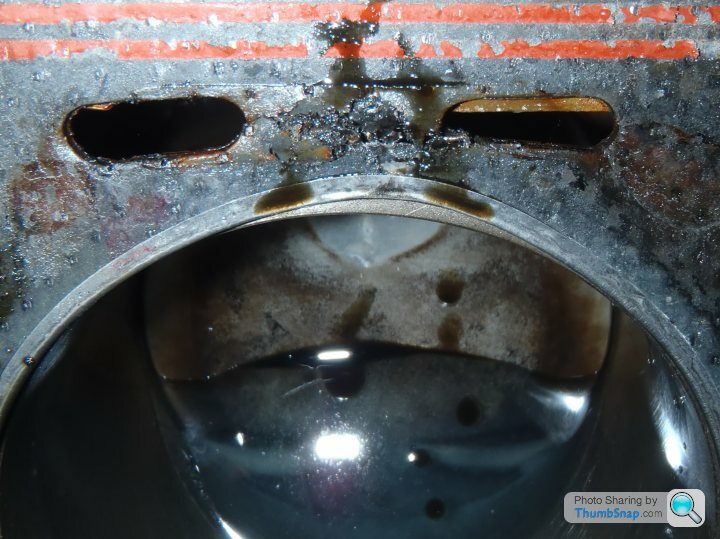

That is by far the worst one. Looking at the other cylinders, most are showing very clean piston crowns and heads between the Inlet valves and the cylinder wall. My guess would be that this is caused by detonation burning off all the carbon, not sure as I don't have any experience of this phenomenon....
Wow, not really much support behind the fire ring in that (critical) location is there!
(right at the back of the squish zone, where cylinder pressure and especially knocking pressure can get "focused" by the converging geometery. Looking at the head, the water way break through is very likely to give a poor clamp load, and hardly any "back up" capability. I'd say, looking at the those pics there is no sign of excessive det, and the gasket failure is simply a peak pressure overload one. (Pmax, not PKmax)
I think you're going to have to approach one of the custom gasket firms and get something specific designed to suit that situation. You may also wish to consider getting the heads welded to remove the "weak" spot too.......
(right at the back of the squish zone, where cylinder pressure and especially knocking pressure can get "focused" by the converging geometery. Looking at the head, the water way break through is very likely to give a poor clamp load, and hardly any "back up" capability. I'd say, looking at the those pics there is no sign of excessive det, and the gasket failure is simply a peak pressure overload one. (Pmax, not PKmax)
I think you're going to have to approach one of the custom gasket firms and get something specific designed to suit that situation. You may also wish to consider getting the heads welded to remove the "weak" spot too.......
Thanks for the comments/ suggestions & help! - it does look like a serious weak spot, all the cylinders are looking the same with the gasket pushed out in the same spot, to varying extents... e.g. cylinder 2.
As for it not being the best design for boost, I guess I cant really blame alfa for that, as it was never designed as a boosted engine....
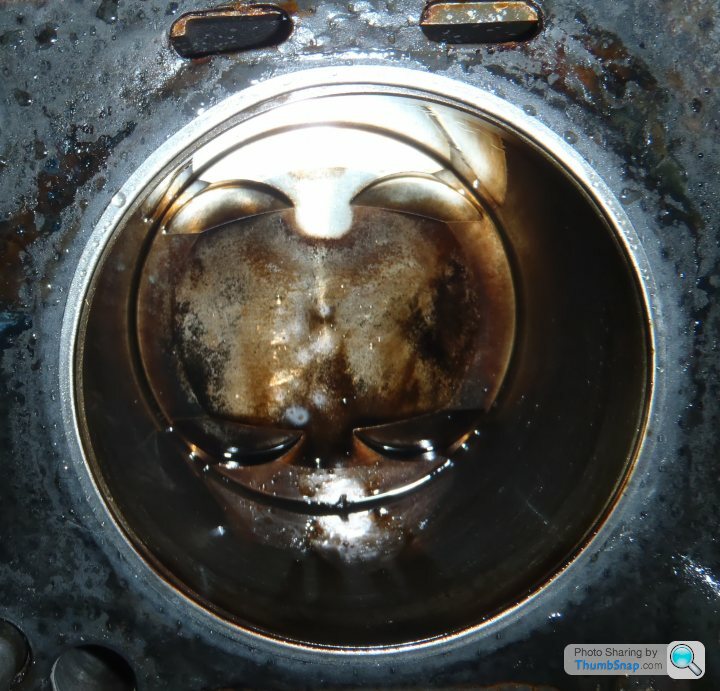
by welding I assume you mean in the area indicated below (excuse the photo shop painting) I have never had any welding done on heads before - is it specialist, or can any decent ally welder do it?? I would guess it needs a specialist...
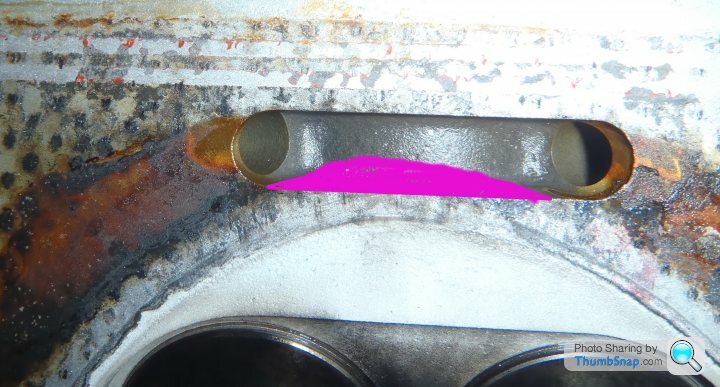
Looking on the exhaust side there is more material there, so less of a problem..
I Guess(as I dont know) that it could have been a slowly failing gasket, that started to leak slightly that caused some detonation.... or am I way off there...
Definitely I will talk to some of the custom gasket guys & show them the photos and see what they suggest.. It will be a while before I do the rebuild, so plenty of time to investigate......
As for it not being the best design for boost, I guess I cant really blame alfa for that, as it was never designed as a boosted engine....
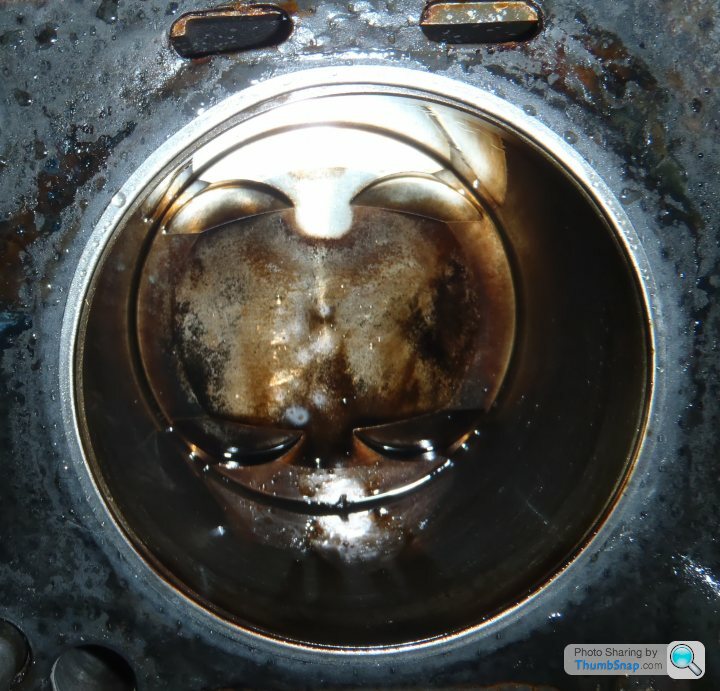
by welding I assume you mean in the area indicated below (excuse the photo shop painting) I have never had any welding done on heads before - is it specialist, or can any decent ally welder do it?? I would guess it needs a specialist...
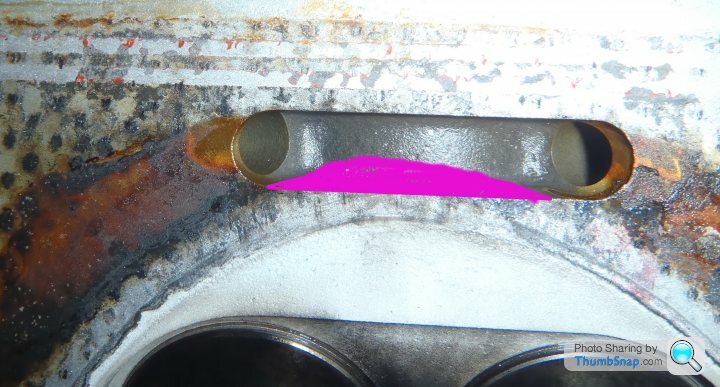
Looking on the exhaust side there is more material there, so less of a problem..
I Guess(as I dont know) that it could have been a slowly failing gasket, that started to leak slightly that caused some detonation.... or am I way off there...
Definitely I will talk to some of the custom gasket guys & show them the photos and see what they suggest.. It will be a while before I do the rebuild, so plenty of time to investigate......
I'd completely "fill in" the deck of the head, then just re-drill holes for the coolant passages. it's the inlet side, so you've got less heat to worry about (the exhaust side actually looks pretty decent with a cooling port up the middle of the bifurication bridge).
If all the cylinders look the same, and show no "pockmarking" or other signs of det(measure your top ring gaps / lands and check for any deformation), it's a clear indication that your current gasket simply cannot cope with the maximum cylinder pressure at it's current clamp load. Std fibre gaskets have little or no "lateral" stiffness, and if the pressure loads over come the clamp load, the low friction co-efficient between the stainless fire ring and the liner/head pretty much mean it's going to just move backwards. A MLS or similar gasket will be a lot more tolerant to that sort of loading.
It's worth trying to get some info on your studs, if they are simply too elastic, then any headlift is going to end badly as you are totally relying on the vertical clamp load to secure the fire ring in that area. What head tightening strategy have you employed? (Having a spare block / head to test tighten studs to destruction (whilst measuring elongation if possible) can be an enlightening experience, not to mention a lot of fun as, when you finally fail the fastener, you tend to go flying off across the workshop with a torque wrench in your hand..........)
I suspect the detonation was a symptom of the gasket failure, rather than vise versa.
Welding heads is a bit of an art, needs a good welder, a large oven, and really a post weld bulk material heat treatment afterwards to normalise the material properties again.
If all the cylinders look the same, and show no "pockmarking" or other signs of det(measure your top ring gaps / lands and check for any deformation), it's a clear indication that your current gasket simply cannot cope with the maximum cylinder pressure at it's current clamp load. Std fibre gaskets have little or no "lateral" stiffness, and if the pressure loads over come the clamp load, the low friction co-efficient between the stainless fire ring and the liner/head pretty much mean it's going to just move backwards. A MLS or similar gasket will be a lot more tolerant to that sort of loading.
It's worth trying to get some info on your studs, if they are simply too elastic, then any headlift is going to end badly as you are totally relying on the vertical clamp load to secure the fire ring in that area. What head tightening strategy have you employed? (Having a spare block / head to test tighten studs to destruction (whilst measuring elongation if possible) can be an enlightening experience, not to mention a lot of fun as, when you finally fail the fastener, you tend to go flying off across the workshop with a torque wrench in your hand..........)
I suspect the detonation was a symptom of the gasket failure, rather than vise versa.
Welding heads is a bit of an art, needs a good welder, a large oven, and really a post weld bulk material heat treatment afterwards to normalise the material properties again.
stevieturbo said:
perfectly flat and
Agreed!stevieturbo said:
mirror finish.
Disagreed! With your existing fibre gasket/stainless fire ring, you want the higher co-efficient of friction you can get to prevent lateral movement. A pretty 'rough' finish on the head would help that.Of course, a move to MLS or similar will require a different finish RA.
BTW, there is some chance that the original engine actually has a higher Pmax, than your turbo version (depending on the ignition angle you are running), but the shorter, sharper pressure curve of the NA engine might just act for too short a time period to overcome the cylinder head inertia and result in lifting. Your long fat turbo pressure characteristic may have enough time to cause clamp load reduction, even with a lower Pmax value
BTW part 2: I can't quite tell from the pics, but it looks like there might be some signs of fretting/polishing where the fire ring sits on the head surface(on the intake side, middle of squish zone periphery)? If so, this could indicate that the gasket has been undergoing flexure on every high load firing event, eventually resulting in sag and eventual catastrophic failure.
the main thing with welding that will be getting it really clean. my old man would of bead blasted the head and then run a burr around the area to dig down to good clean metal.
once its welded, the whole thing will need a skim to get it perfect again.
not a particulary difficult job for an experienced head guy who can weld.
Ask around a few specialists.
once its welded, the whole thing will need a skim to get it perfect again.
not a particulary difficult job for an experienced head guy who can weld.
Ask around a few specialists.
I would agree with max ,
fill the whole bathtub shape ..then redrill the holes at either end ,then skim it flat with the lightest of skims .
it looks a lot like a lack of clamping ,so as said look to find some better head bolts/studs.
looking at the chamber coloration , it doesn't look like detonation to me ,just too much pressure in normal combustion for the design and amount of head face before the waterway.
piston and bore look fine.
I like the rigidity of the mls for this.my 500cc twin Honda runs a mls ,with a homemade thicker centre section ,it runs at 270bhp/litre power level with pk power at 9k rpm ,and reasonable cylinder pressure at 80 lbs/ft at 8k, this has been completely reliable for 10 years of 15 psi ,this is relevant because it also has liners like yours unsupported at the top and using a mls has been successful.
regards
robert
fill the whole bathtub shape ..then redrill the holes at either end ,then skim it flat with the lightest of skims .
it looks a lot like a lack of clamping ,so as said look to find some better head bolts/studs.
looking at the chamber coloration , it doesn't look like detonation to me ,just too much pressure in normal combustion for the design and amount of head face before the waterway.
piston and bore look fine.
I like the rigidity of the mls for this.my 500cc twin Honda runs a mls ,with a homemade thicker centre section ,it runs at 270bhp/litre power level with pk power at 9k rpm ,and reasonable cylinder pressure at 80 lbs/ft at 8k, this has been completely reliable for 10 years of 15 psi ,this is relevant because it also has liners like yours unsupported at the top and using a mls has been successful.
regards
robert
Update... I have just put my ring compressor on the head and drawn in where the gasket was or should be if it was round and 93mm. as shown in the photos below, this gives the same width to the space between the cylinder and cooling bore as on the exhaust size which is aprox 6.8-7.0mm the liners are 8mm wall thickness.
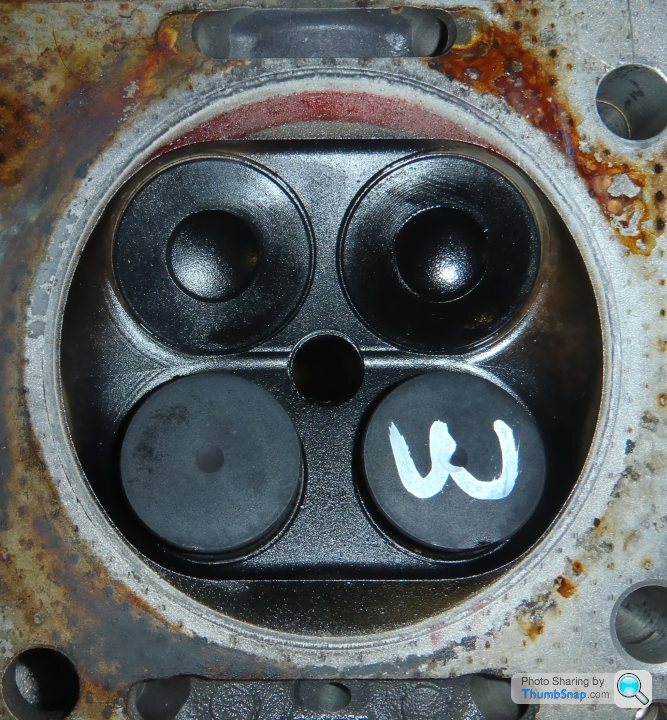
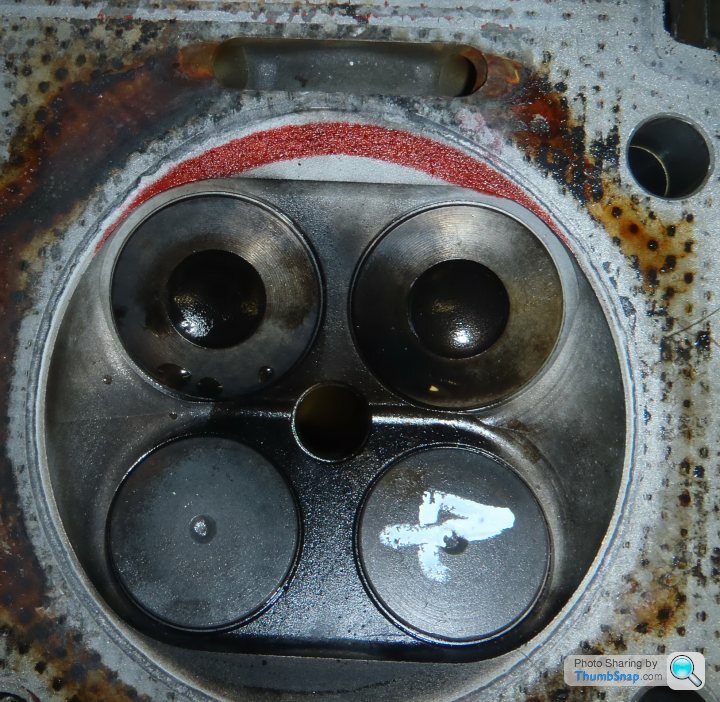
So as suggested it looks more and more like poor clamping load on the inlet side, I guess it is lower this side as it runs cooler? It was asked above about the tightening - as per alfa a small torque + an angle tightened once and then left alone.
One thought re the MLS gasket - I have a slight groove machined in the liner top, would this cause any problems with a MLS gasket, as they need a really good finish on the mating surface..
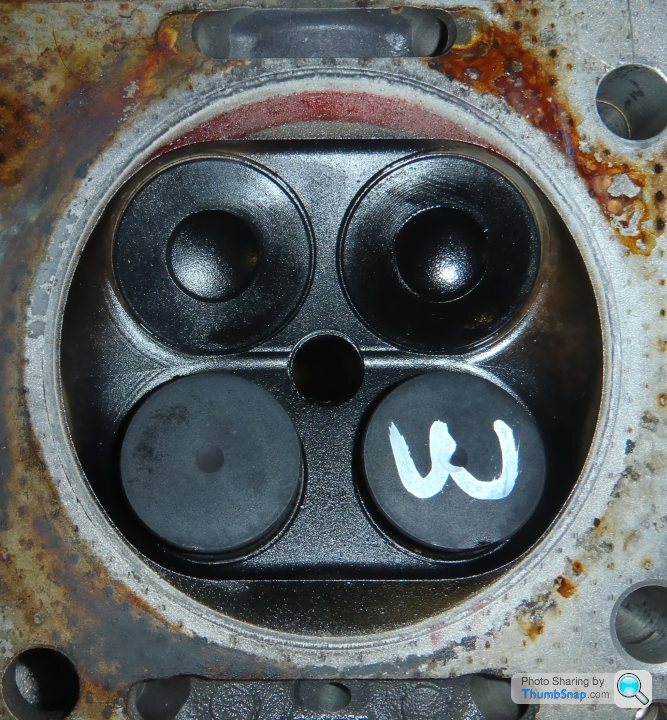
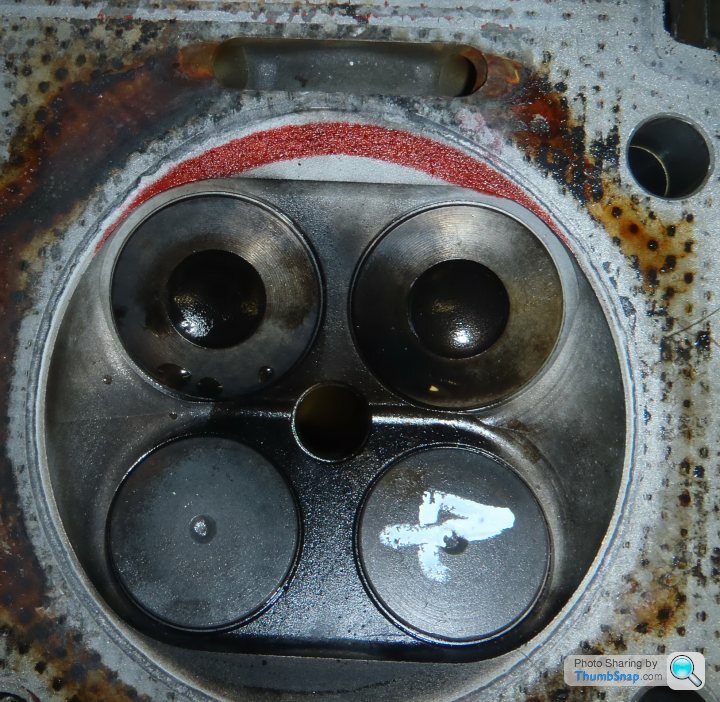
So as suggested it looks more and more like poor clamping load on the inlet side, I guess it is lower this side as it runs cooler? It was asked above about the tightening - as per alfa a small torque + an angle tightened once and then left alone.
One thought re the MLS gasket - I have a slight groove machined in the liner top, would this cause any problems with a MLS gasket, as they need a really good finish on the mating surface..
turbonutter said:
It was asked above about the tightening - as per alfa a small torque + an angle tightened once and then left alone.
Suggesting that the studs are torqued to yield. In which case, any increase in pressure loading leads to a direct head lift........... I'd want to get some measurements from the current studs to see where they sit before i spent any cash on new gaskets / head mods etc.........Gassing Station | Engines & Drivetrain | Top of Page | What's New | My Stuff