Clutch release bearing.
Discussion
Hi there. Should be simple. Clutch release arm sticks out of the side of the bell housing. The other end is on a ball mounting and held in by a spring clip. That has to be released. Bring the arm close to the front of the bell housing opening and tug it hard, it should release. Then slide it across slightly and the thrust release carrier should come free from the arm.
Hi Maffee,
Thanks for the reply. Kind of catch 22 Im afraid. The arm seen in the photos cannot be withdrawn out from under the clip because the main shaft is still in place. I cannot withdraw this, the bell housing is still bloted to it and one of four bolts securing it is obscured by the arm. You can kind of see this from the second picture, its the top right one. Does the bearing release from the arm while its all in place does anyone know?
Thanks for the reply. Kind of catch 22 Im afraid. The arm seen in the photos cannot be withdrawn out from under the clip because the main shaft is still in place. I cannot withdraw this, the bell housing is still bloted to it and one of four bolts securing it is obscured by the arm. You can kind of see this from the second picture, its the top right one. Does the bearing release from the arm while its all in place does anyone know?
Yes, the bearing does release and the arm can be removed while the bell housing is still attached to the gearbox, unless some one has modified it. The arm can be a little difficult to remove from its pivot but if you cant pull it out you should be able to gently lever it from the pivot and get it free. You can see from the pictures Maffe has put up how the bearing housing is just held to the arm by two tangs. Once the arm is freed you can get the bearing off the tangs. If yours is in any way different can you post photos please?
Mine, clutch slave rod still locates in outer hole.
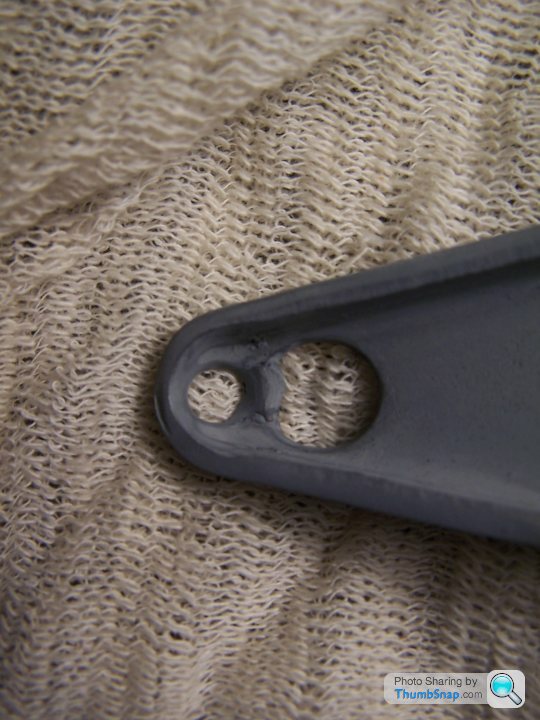
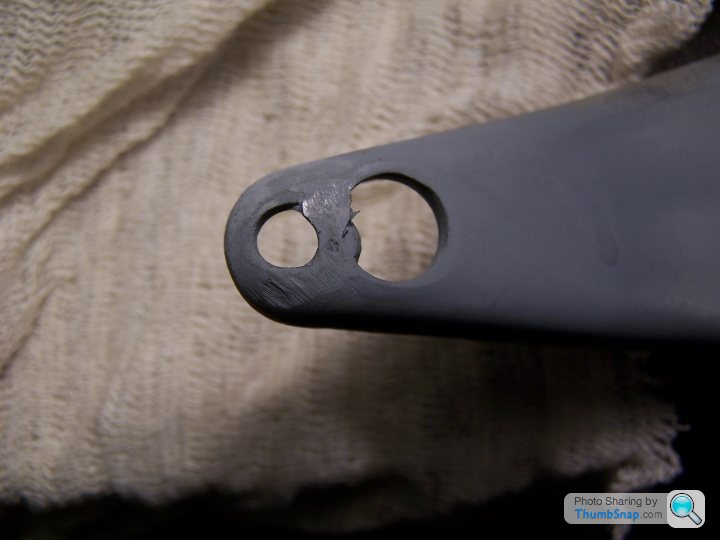
Keep weld heat right down, add weld but don't heat the clutch arm any more than absolutely necessary, it is a heat treated component.
The point where the rod locates needs to be as close to a ball and socket as you can get to allow the rod to move through enough angle easily and with the minimum wear. If the slot between the two holes is not filled you will get the usual ridges forming on the end piece on the rod and the wear will gradually get worse. Then I examined it carefully the end of the rod starts to jam in the hole and reduce the angle the rod can move and that seems likely to increase wear to one side of the slave cylinder as well.
It was of course designed for cable operation from the front and this TVR bodge wasn't the very best bit of engineering design!
Hmmm, socket looks rough on the photos, in fact it is dremel ground carefully to match the radius of the rod end.
The last two shots show how much the angle changes, and why we don't get even wear on the slave cylinder!
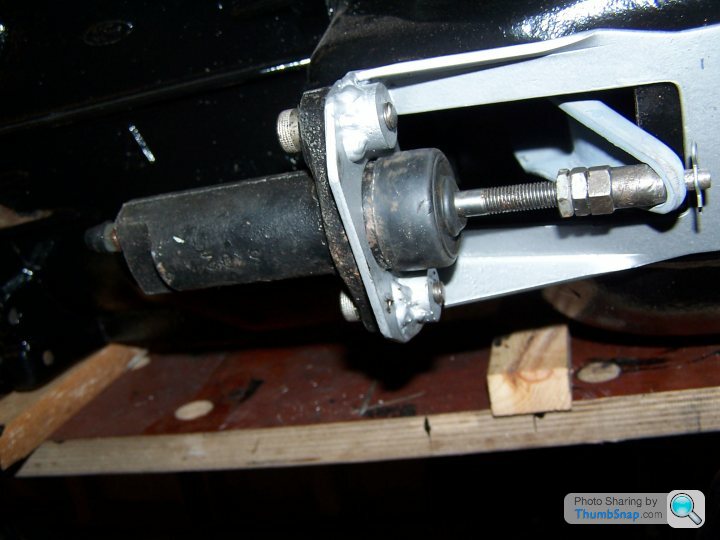
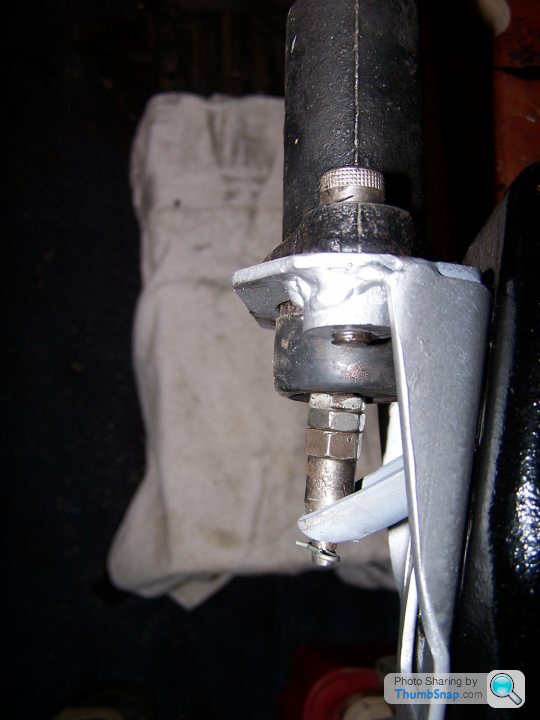
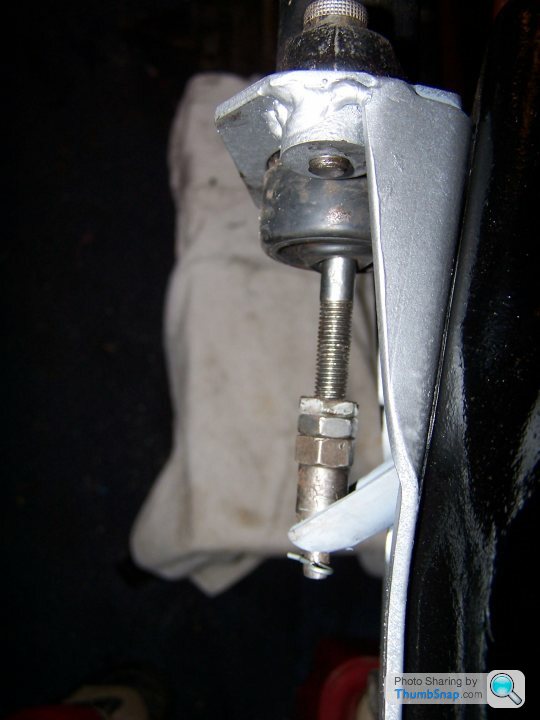
(Your slave cylinder will probably be held in by 2 nuts and bolts, I am slowly modifying the car for ease of maintenance and using allen screws where possible. Using allen screws in this instance saves the b....r of a job we had getting Willie Weirs out at the roadside! Philpott will notice, stainless Allen screws! I also have a tiny R pin in the end of the slave rod to be sure it cant come out!)
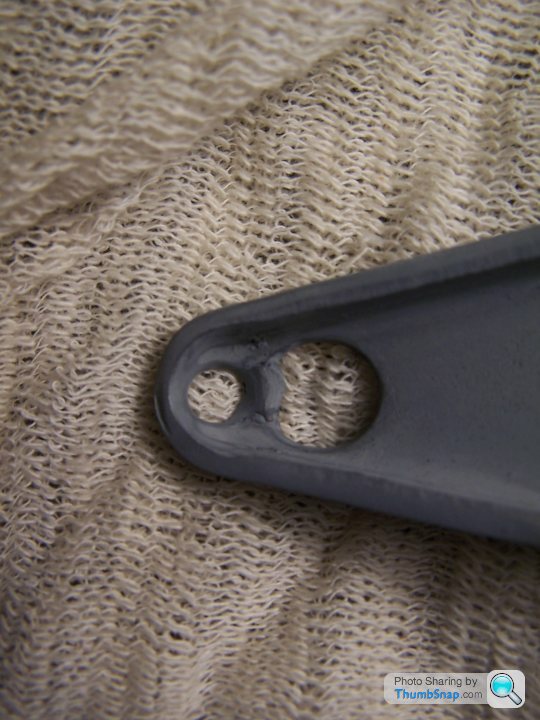
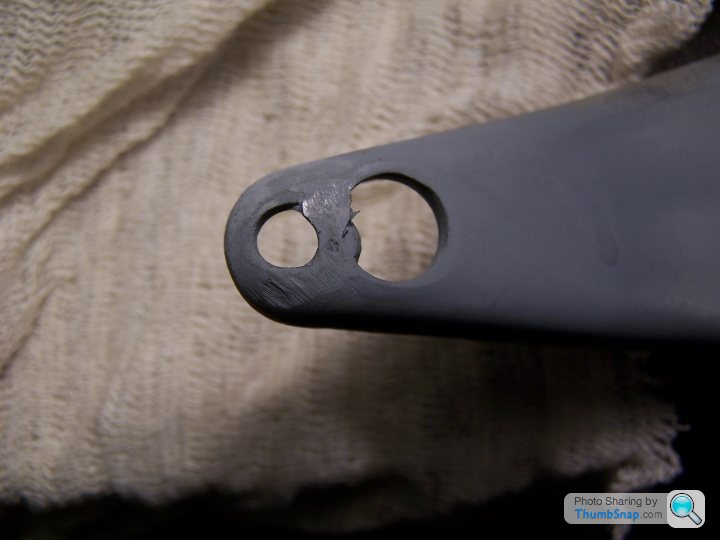
Keep weld heat right down, add weld but don't heat the clutch arm any more than absolutely necessary, it is a heat treated component.
The point where the rod locates needs to be as close to a ball and socket as you can get to allow the rod to move through enough angle easily and with the minimum wear. If the slot between the two holes is not filled you will get the usual ridges forming on the end piece on the rod and the wear will gradually get worse. Then I examined it carefully the end of the rod starts to jam in the hole and reduce the angle the rod can move and that seems likely to increase wear to one side of the slave cylinder as well.
It was of course designed for cable operation from the front and this TVR bodge wasn't the very best bit of engineering design!
Hmmm, socket looks rough on the photos, in fact it is dremel ground carefully to match the radius of the rod end.
The last two shots show how much the angle changes, and why we don't get even wear on the slave cylinder!
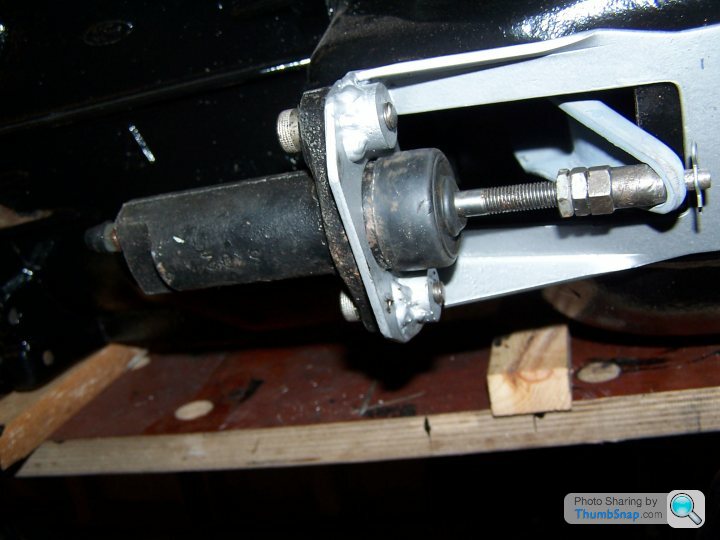
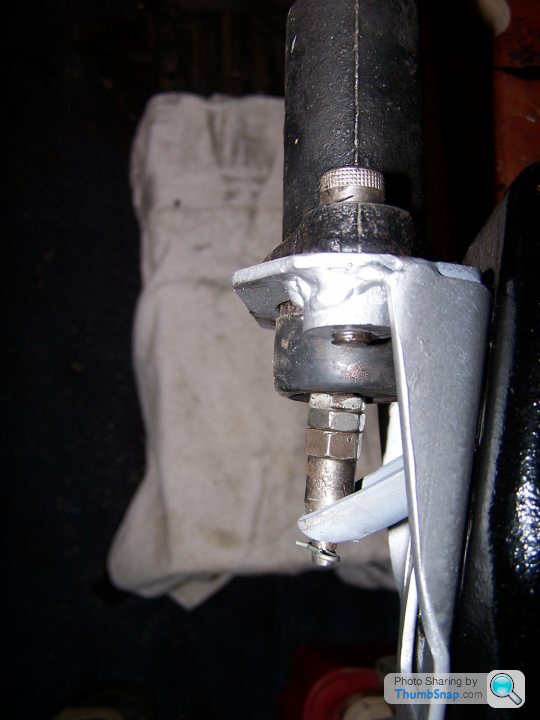
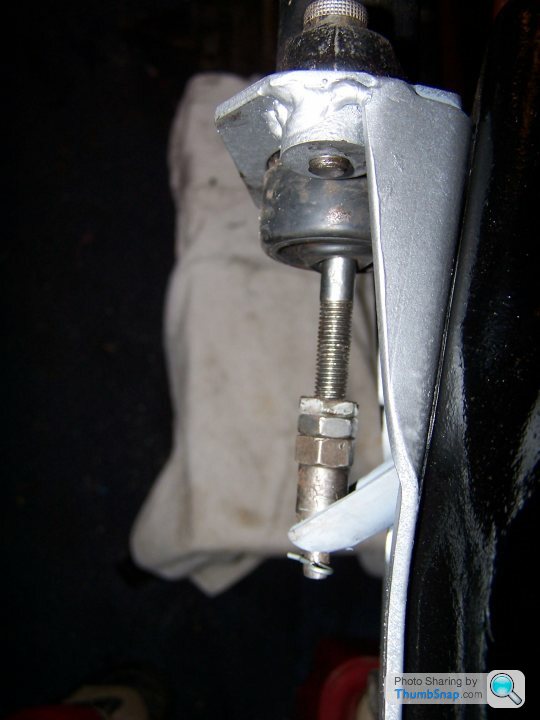
(Your slave cylinder will probably be held in by 2 nuts and bolts, I am slowly modifying the car for ease of maintenance and using allen screws where possible. Using allen screws in this instance saves the b....r of a job we had getting Willie Weirs out at the roadside! Philpott will notice, stainless Allen screws! I also have a tiny R pin in the end of the slave rod to be sure it cant come out!)
Edited by greymrj on Tuesday 17th April 10:34
theprof said:
Hi Maffee,
Thanks for the reply. Kind of catch 22 Im afraid. The arm seen in the photos cannot be withdrawn out from under the clip because the main shaft is still in place. I cannot withdraw this, the bell housing is still bloted to it and one of four bolts securing it is obscured by the arm. You can kind of see this from the second picture, its the top right one. Does the bearing release from the arm while its all in place does anyone know?
You can do this with the shaft in place ( Glen cool down), pull it strait out to the side so it loosens from the pin, then lift at an angle over the shaft no need to remove the housingThanks for the reply. Kind of catch 22 Im afraid. The arm seen in the photos cannot be withdrawn out from under the clip because the main shaft is still in place. I cannot withdraw this, the bell housing is still bloted to it and one of four bolts securing it is obscured by the arm. You can kind of see this from the second picture, its the top right one. Does the bearing release from the arm while its all in place does anyone know?
Thanks all for some interesting info. Ended up driving the pivot pin out from the other side of the bell housing with a pin punch. Was all very easy in the end and so would recomend this way to anyone else.
Now for the big question, with an overhall kit from about £150, has anyone split the box to repair seals and bearings before? If so so how much of a ball ache is it?
Now for the big question, with an overhall kit from about £150, has anyone split the box to repair seals and bearings before? If so so how much of a ball ache is it?
theprof said:
Now for the big question, with an overhall kit from about £150, has anyone split the box to repair seals and bearings before? If so so how much of a ball ache is it?
It's do able, had mine apart to fit a BGH Geartech "long first gear kit", but like any reasonably major job, it will depend on your skills, experience, facilities etc etc. No offence intended but if you got stuck at the first hurdle (removing the release bearing) may be a full gearbox strip is not too good an idea? 
Have you ever had a gearbox apart? Front and rear seals can be done without any stripping (and a lot less than £150).
Is there a known issue, does it need "overhauling" or are you thinking more on the line of preventative maintenance?
They are a pretty tough old box, would be my bet the vast majority of S's have never had a gearbox overhaul and are still going strong!
Edited by phillpot on Wednesday 18th April 21:05
Totally agree with Phillpot. If you haven't done a gearbox rebuild then don't do it without experienced help. One mistake and you may have a lot of little bits to try to put back together again.
First question, was the gearbox leaking, if so you are just doing the main seals which isnt a gearbox strip.
Second question, were gears difficult to change (but not noisy), if so was a it a clutch problem or a problem with the external part of the selectors. If so sort that, dont split the box.
Third question, was the box noisy or was the oil you took out dirty. If so it is a box overhaul. There are transmission specialists around who do this all the time. Inspection strip down costs about £150 (north west prices!) then it depends what needs doing.
As Phillpot says these are pretty basic and robust boxes, dont strip it unless you have good reason and certainly not without expertise.
Coming back to the initial problem. Do you know yet why you couldn't get the arm off the pivot pin? You certainly shouldn't have had to drive the pivot pin out. You will of course have to get the pin back and the arm will have to clip back on to it. Make absolutely sure that pin is tight when it goes back, if it comes loose you will be in serious trouble.
First question, was the gearbox leaking, if so you are just doing the main seals which isnt a gearbox strip.
Second question, were gears difficult to change (but not noisy), if so was a it a clutch problem or a problem with the external part of the selectors. If so sort that, dont split the box.
Third question, was the box noisy or was the oil you took out dirty. If so it is a box overhaul. There are transmission specialists around who do this all the time. Inspection strip down costs about £150 (north west prices!) then it depends what needs doing.
As Phillpot says these are pretty basic and robust boxes, dont strip it unless you have good reason and certainly not without expertise.
Coming back to the initial problem. Do you know yet why you couldn't get the arm off the pivot pin? You certainly shouldn't have had to drive the pivot pin out. You will of course have to get the pin back and the arm will have to clip back on to it. Make absolutely sure that pin is tight when it goes back, if it comes loose you will be in serious trouble.
Thanks agian to everyone offering help . It was never my intention to 'strip' the gearbox and break it down to its constituent parts, cos like every one else I am just mad amatuer! Stripping a box to all its bells and whistles is beyond my ability. The idea is to give the box a birthday. it leaks from the behind the clutch bearing tube so its either the seal or the gasket, probably both. So if i do that then why not attempt all the other gaskets and the seal at the other end. I suppose the question is if I do then how much of the box has to come apart to do it. The gearbox itself is sound otherwise, certainly no issue with selecting any gear or whining.
theprof said:
It was never my intention to 'strip' the gearbox and break it down to its constituent parts,
Could have fooled me................ 
theprof said:
Now for the big question, with an overhall kit from about £150, has anyone split the box to repair seals and bearings before? If so so how much of a ball ache is it?
Replace bearings requires full strip down!A Haynes manual for the V6 engined Ford Sierra's will show you all you need to know about changing gearbox oil seals (and more if you're feeling brave

Bit cheaper than £150 .... Type 9 gasket & seal kit
The two gaskets on the right will be "spare" as will the smallest oil seal and I wouldn't bother with the top cover gasket unless it's definitely leaking?

Edited by phillpot on Thursday 19th April 20:10
Gassing Station | S Series | Top of Page | What's New | My Stuff