Stuart 10V Vertical Steam Engine
Discussion
dr_gn said:
Why on earth are you using a round edge finder to try to find a datum on a round part?You have a perfectly straight vice jaw to use the edge finder on instead of hoping the edge finder is on centre with the round part.
Or just buy one of these...
https://www.machine-dro.co.uk/dial-co-axial-center...
Tango13 said:
dr_gn said:
Why on earth are you using a round edge finder to try to find a datum on a round part?You have a perfectly straight vice jaw to use the edge finder on instead of hoping the edge finder is on centre with the round part.
Or just buy one of these...
https://www.machine-dro.co.uk/dial-co-axial-center...
Takes far longer to describe than to do.
The moving vice jaw doesn’t necessarily move perfectly parallel to the fixed one when clamping a Non-parallel part, so I’d potentially be measuring a non-symmetrical taper and therefore getting a false centre.
Why on earth would I spend all that money on an elaborate tool when I can do the same thing perfectly well with what I’ve already got?
dr_gn said:
I don’t have to *hope* it’s in the centre at all, because it’s irrelevant: Lock the x-axis, touch on the curved surface, zero, lift and move to the opposite side in the y axis, lower and touch the other side. Divide the Y DRO reading by two and that’s precisely the y-axis centreline irrespective of if it’s on the tangent point or not. The y-axis is locked - it’s in the exact same position on the curve, but on the opposite side. Repeat in x, and there’s the exact centre, should I need it.
Takes far longer to describe than to do.
The moving vice jaw doesn’t necessarily move perfectly parallel to the fixed one when clamping a Non-parallel part, so I’d potentially be measuring a non-symmetrical taper and therefore getting a false centre.
Why on earth would I spend all that money on an elaborate tool when I can do the same thing perfectly well with what I’ve already got?
In 30+ years of precision engineering I have never seen anyone try to set a datum on a round part like that because if they did they would get laughed out of the factory!Takes far longer to describe than to do.
The moving vice jaw doesn’t necessarily move perfectly parallel to the fixed one when clamping a Non-parallel part, so I’d potentially be measuring a non-symmetrical taper and therefore getting a false centre.
Why on earth would I spend all that money on an elaborate tool when I can do the same thing perfectly well with what I’ve already got?
A moving jaw is irrelevant for setting a datum, set the datum off the fixed jaw and work back from that if you want to do it the hard way or just buy the correct tool for the job which will be quicker, easier and more accurate.
Tango13 said:
dr_gn said:
I don’t have to *hope* it’s in the centre at all, because it’s irrelevant: Lock the x-axis, touch on the curved surface, zero, lift and move to the opposite side in the y axis, lower and touch the other side. Divide the Y DRO reading by two and that’s precisely the y-axis centreline irrespective of if it’s on the tangent point or not. The y-axis is locked - it’s in the exact same position on the curve, but on the opposite side. Repeat in x, and there’s the exact centre, should I need it.
Takes far longer to describe than to do.
The moving vice jaw doesn’t necessarily move perfectly parallel to the fixed one when clamping a Non-parallel part, so I’d potentially be measuring a non-symmetrical taper and therefore getting a false centre.
Why on earth would I spend all that money on an elaborate tool when I can do the same thing perfectly well with what I’ve already got?
In 30+ years of precision engineering I have never seen anyone try to set a datum on a round part like that because if they did they would get laughed out of the factory!Takes far longer to describe than to do.
The moving vice jaw doesn’t necessarily move perfectly parallel to the fixed one when clamping a Non-parallel part, so I’d potentially be measuring a non-symmetrical taper and therefore getting a false centre.
Why on earth would I spend all that money on an elaborate tool when I can do the same thing perfectly well with what I’ve already got?
A moving jaw is irrelevant for setting a datum, set the datum off the fixed jaw and work back from that if you want to do it the hard way or just buy the correct tool for the job which will be quicker, easier and more accurate.
Why would I buy a device that may or may not be more accurate than what I’ve already got, when the parts I’m making are to completely un-toleranced drawings?
I somehow doubt that it would be quicker, since it only takes me about one minute to do currently. Even if it took a hour, so what? I’m not building this in a factory, and model engineering in a garage is very different from production engineering.
On to the cross head, which is supplied as a brass stamping. It’s got a spigot, which is handy for holding it for initial work. First job was to face the end:

Drill and tap for the piston rod:
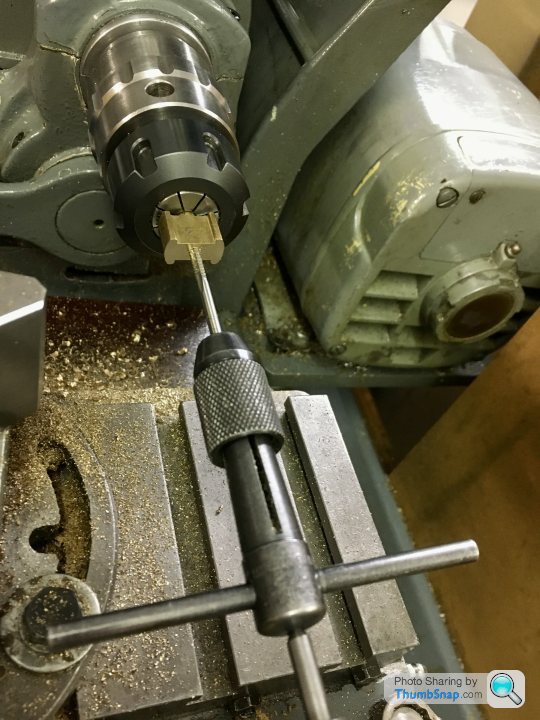
Then turn the O/D to within about 0.010” of finished:

Saw off the spigot:
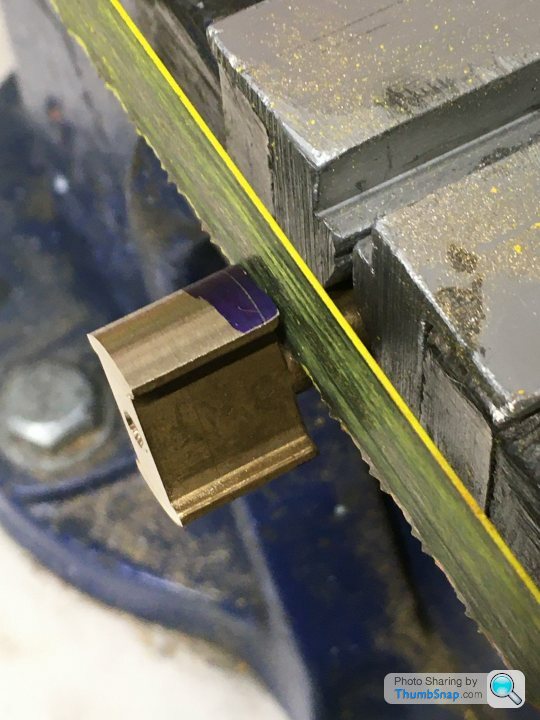
Tighten onto the piston rod, mark it so it can be tightened to the same position in future. Then mount in the collet chuck and incrementally turn to size for the standard bore. A good tip to easily get fractions of a thou feed is to turn the compound slide to a slight angle to the bed, such that any turn on the crank translates to a much smaller amount of feed into the work:
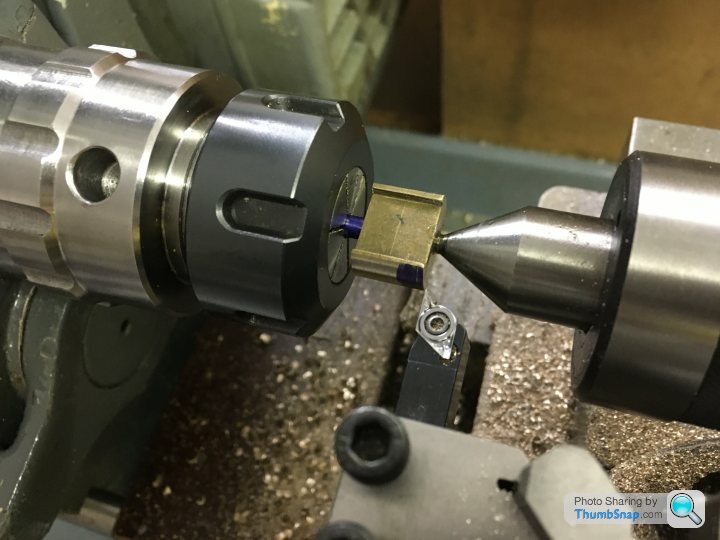
The final feature is the connecting rod hole. I was concerned that due to any errors in size accumulating from my own work, combined with the un-toleranced drawings, I might end up with the piston crashing into the cylinder caps. I decided to temporarily assemble the cylinder, measure it’s internal bore length, and calculate the clearances at each end based on the actual crank throw.
Measured the throw by using the z-dro on the mill:
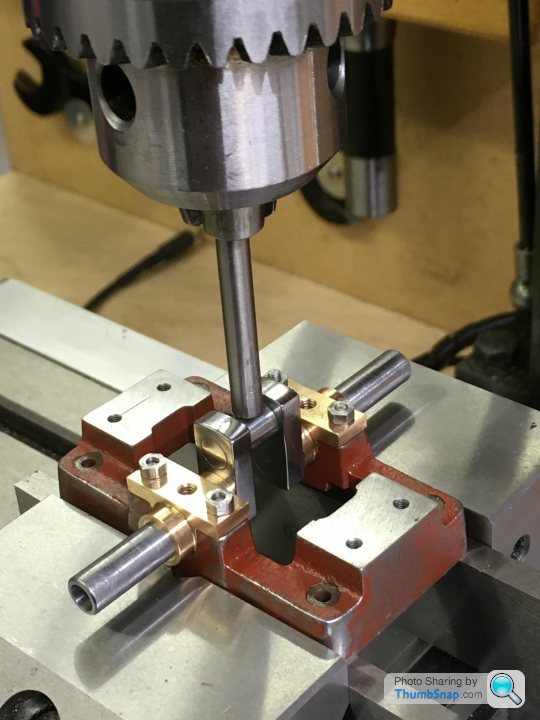
...and the bore length by measuring the piston displacement in a similar way:
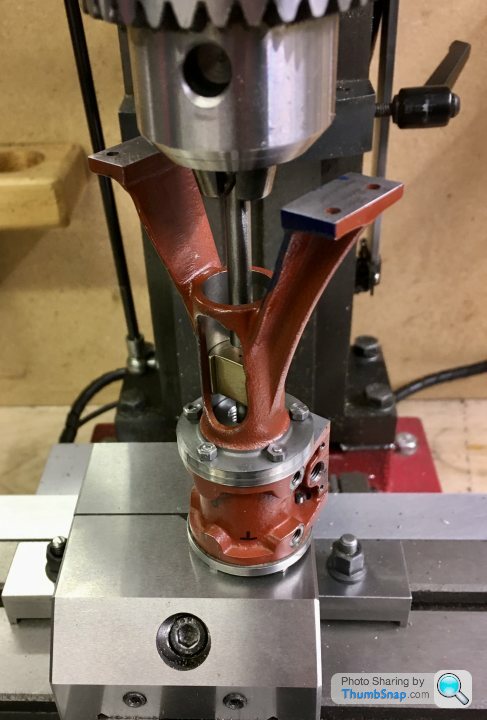
From these figures I calculated that I needed 0.7mm clearance at each end of the bore. I made a 0.7mm thick washer and put it in the bottom of the cylinder:
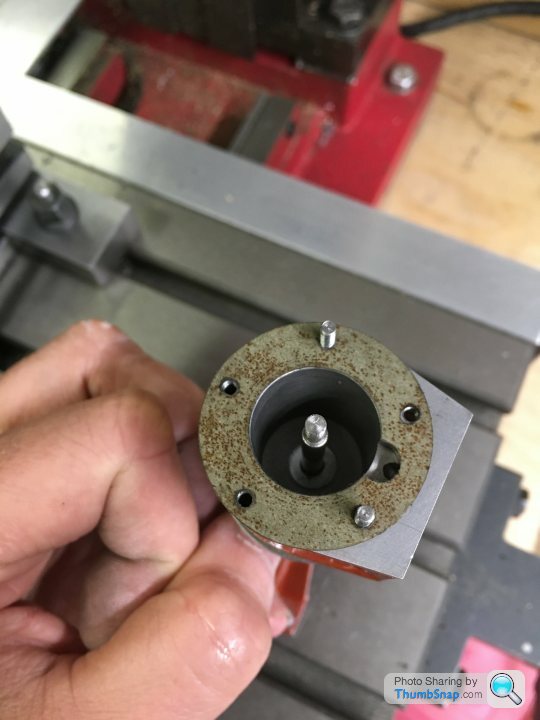
Then, with the crank at the bottom of its stroke, marked the hole position:
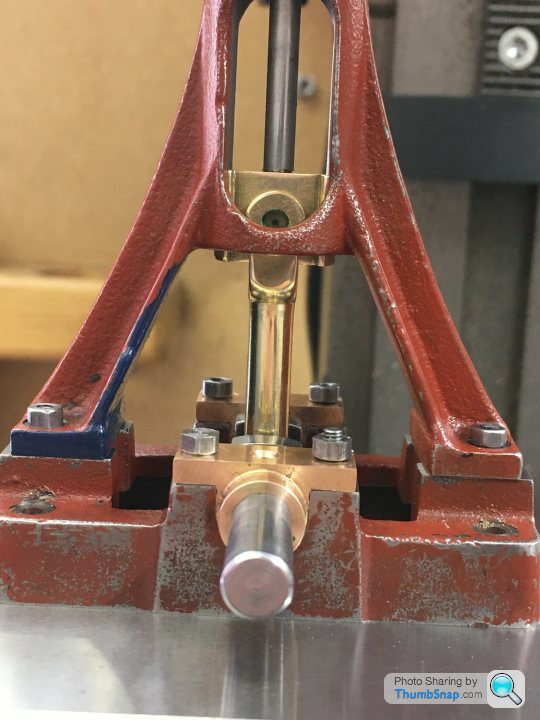
Double-checked at the top of the stroke, spot-on:
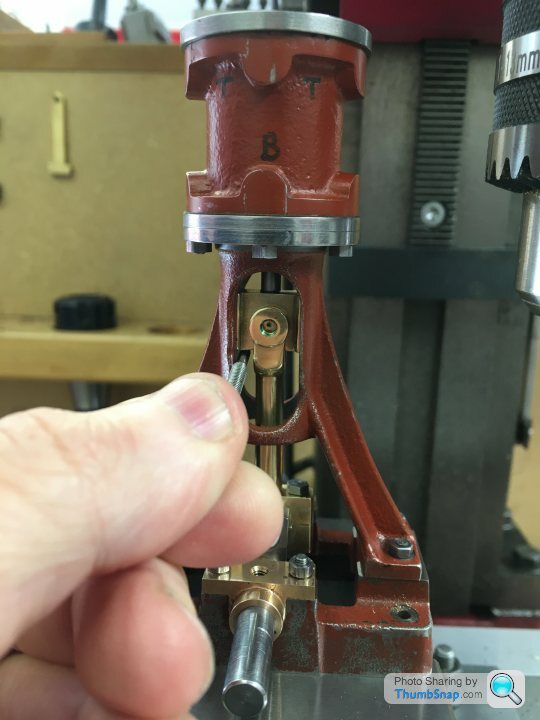
So then dis-assembled, and mounted in the mill vice. Double-checked it was level, then marked, drilled and reamed the pin hole:
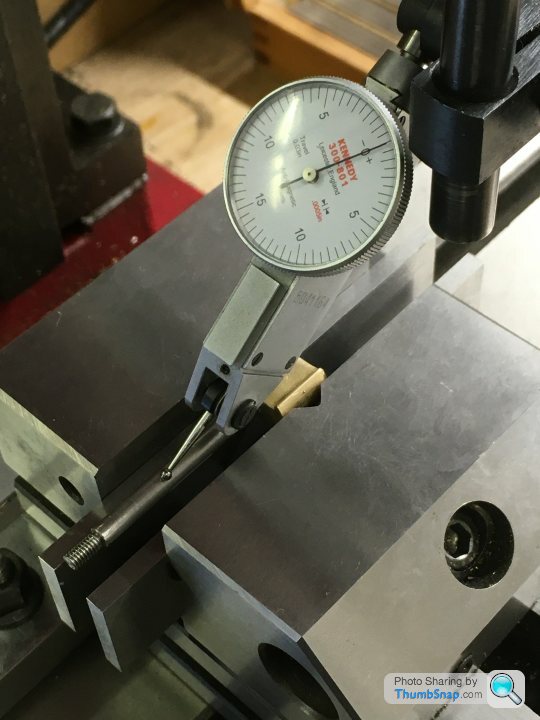
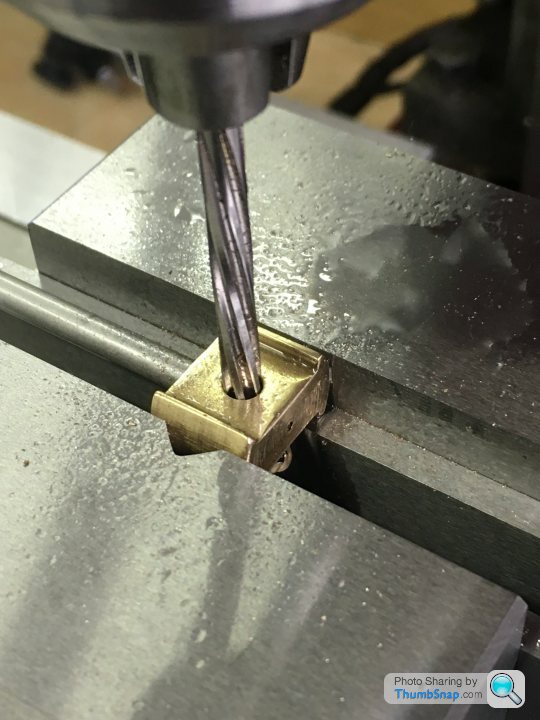
Next up is making the threaded pin. I think that’s the last bit of machining before test assembly.
Don’t want to speak too soon, but I expected this build to take me at least a year rather than 5 months!

Drill and tap for the piston rod:
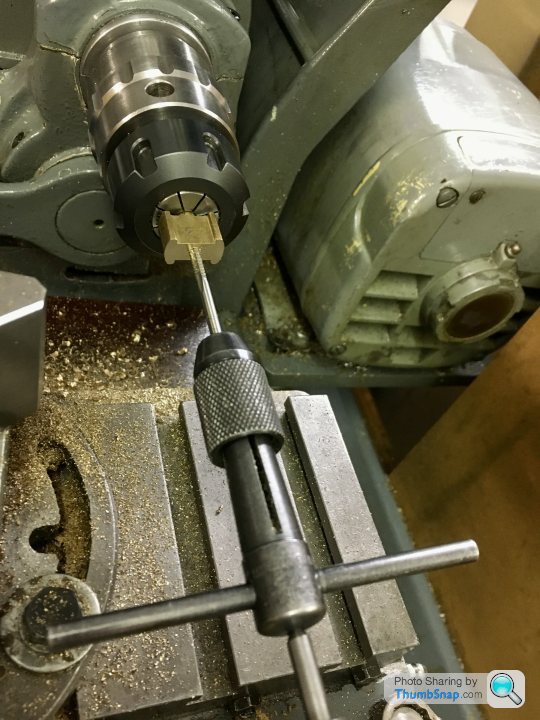
Then turn the O/D to within about 0.010” of finished:

Saw off the spigot:
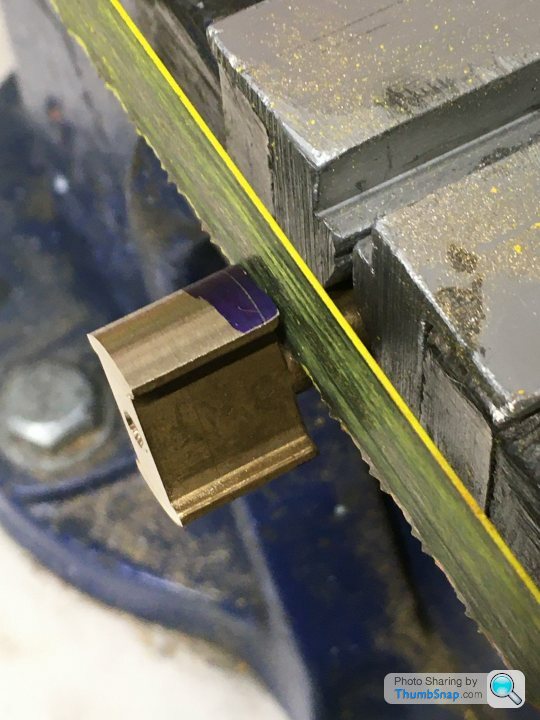
Tighten onto the piston rod, mark it so it can be tightened to the same position in future. Then mount in the collet chuck and incrementally turn to size for the standard bore. A good tip to easily get fractions of a thou feed is to turn the compound slide to a slight angle to the bed, such that any turn on the crank translates to a much smaller amount of feed into the work:
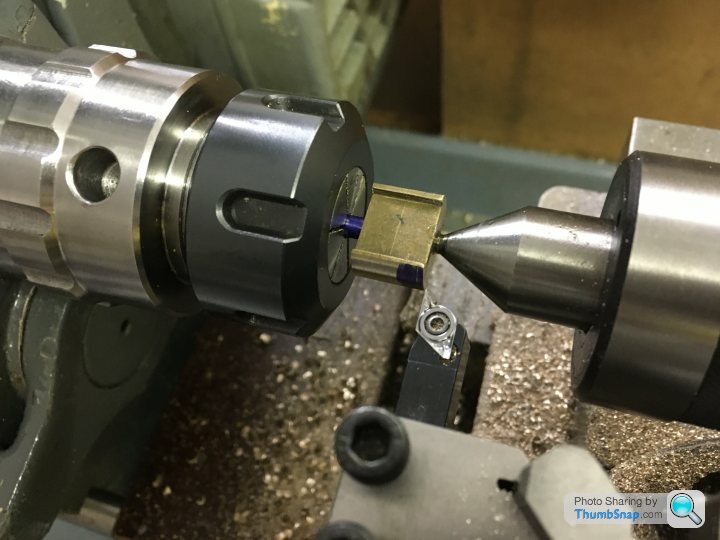
The final feature is the connecting rod hole. I was concerned that due to any errors in size accumulating from my own work, combined with the un-toleranced drawings, I might end up with the piston crashing into the cylinder caps. I decided to temporarily assemble the cylinder, measure it’s internal bore length, and calculate the clearances at each end based on the actual crank throw.
Measured the throw by using the z-dro on the mill:
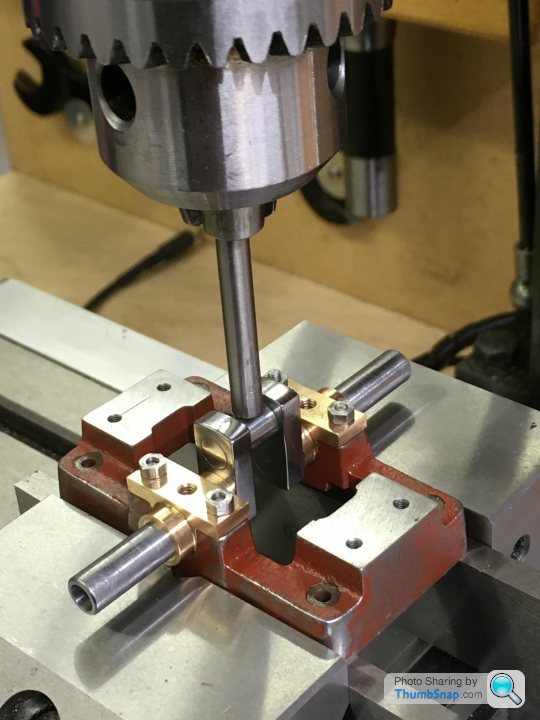
...and the bore length by measuring the piston displacement in a similar way:
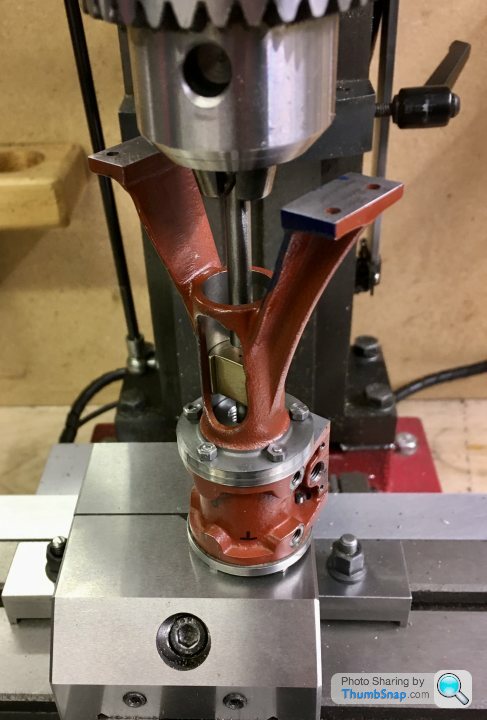
From these figures I calculated that I needed 0.7mm clearance at each end of the bore. I made a 0.7mm thick washer and put it in the bottom of the cylinder:
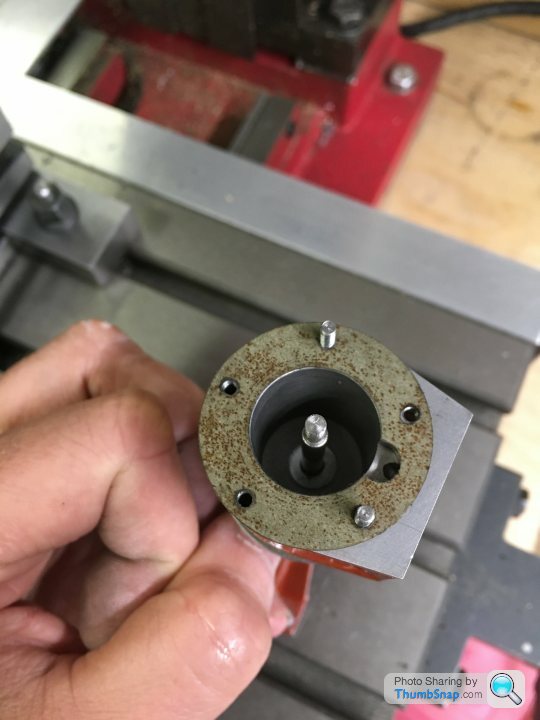
Then, with the crank at the bottom of its stroke, marked the hole position:
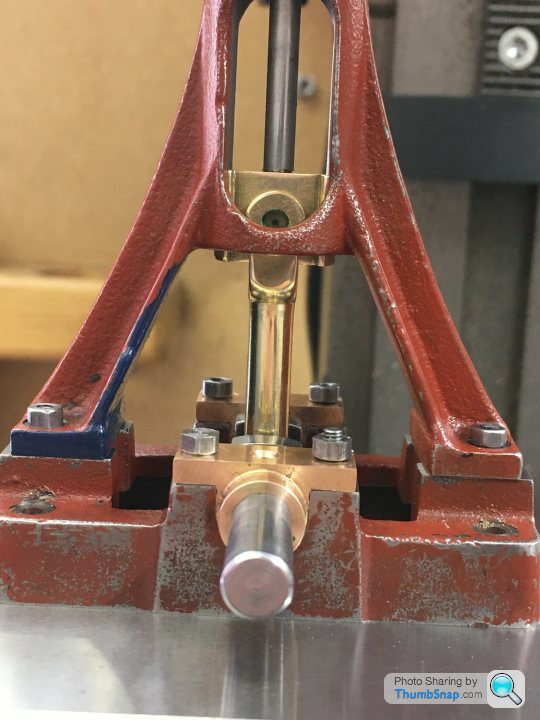
Double-checked at the top of the stroke, spot-on:
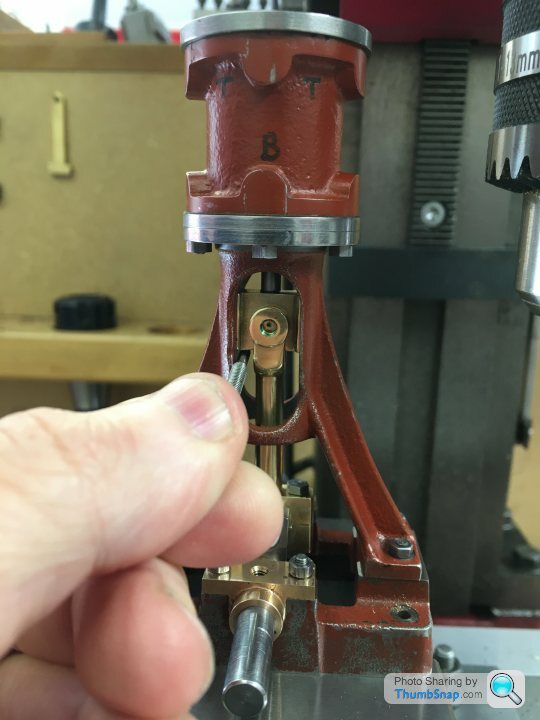
So then dis-assembled, and mounted in the mill vice. Double-checked it was level, then marked, drilled and reamed the pin hole:
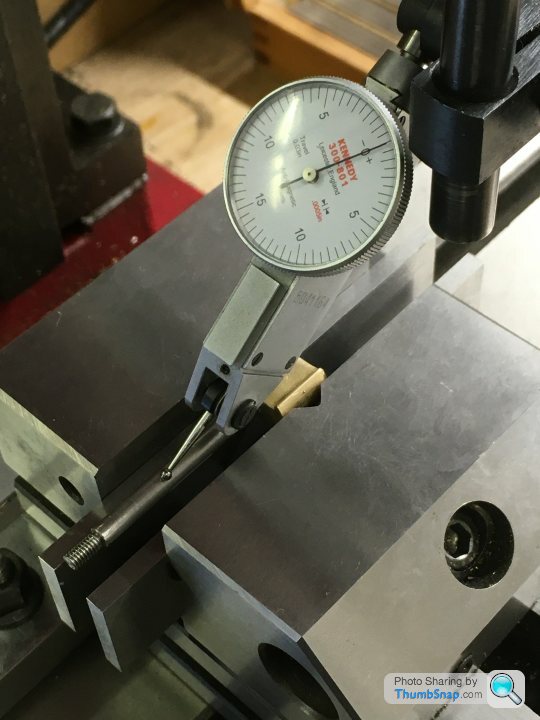
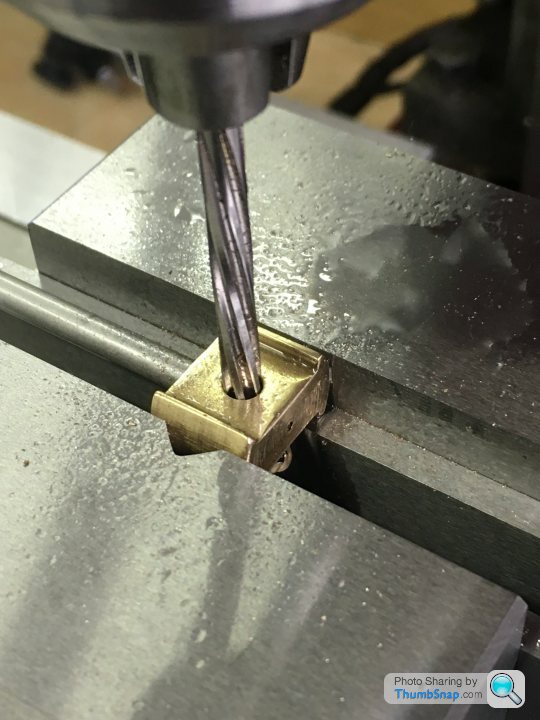
Next up is making the threaded pin. I think that’s the last bit of machining before test assembly.
Don’t want to speak too soon, but I expected this build to take me at least a year rather than 5 months!
For some reason I didn’t have enough rod left in the kit to make the pin - I think I made a mistake with the valve rod and had to scrap it. It was only a 15 minute job to turn one from an off-cut of steel though.
So here’s the first go at test assembly of all the mechanical parts:
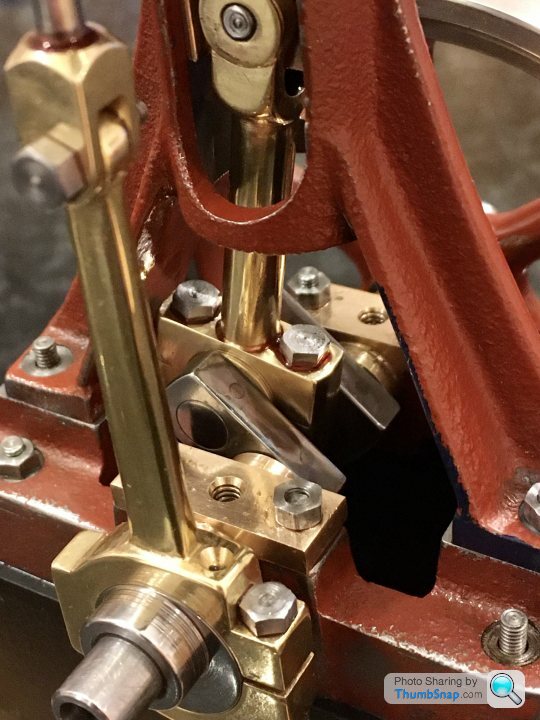
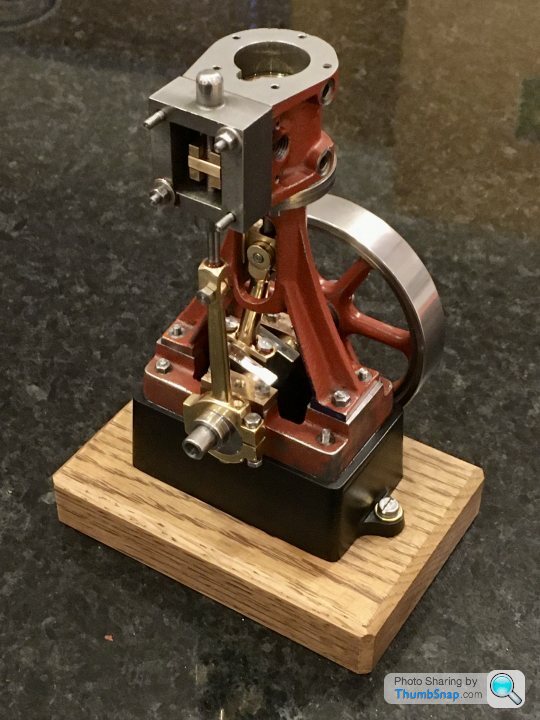
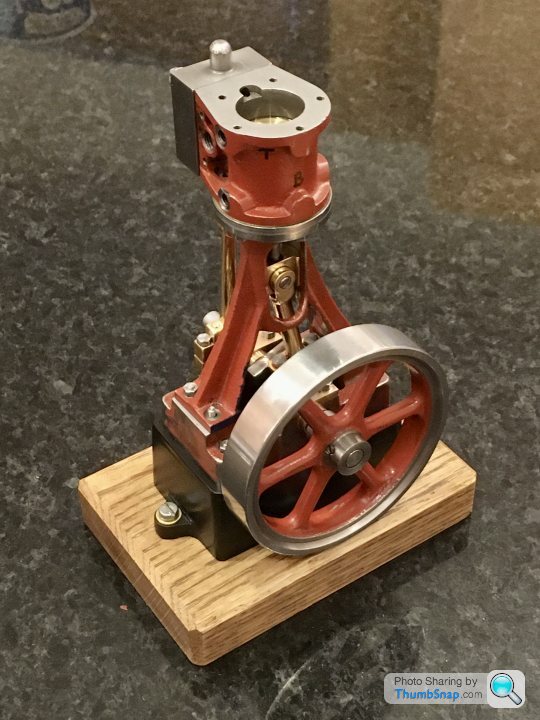
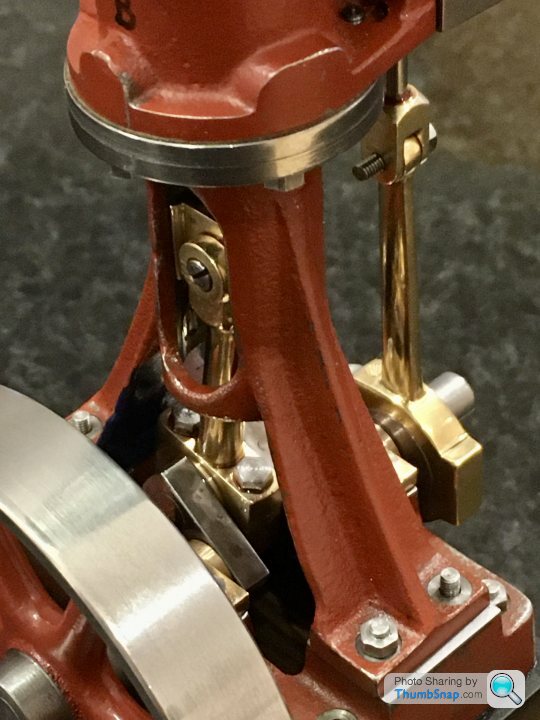
And a video clip of it moving, lubricated with some light oil. Valve and timing setup isn’t done yet, and there is no gland packing. There is one slightly tight spot towards the bottom of piston travel, but it’s getting more free as I fiddle with it:
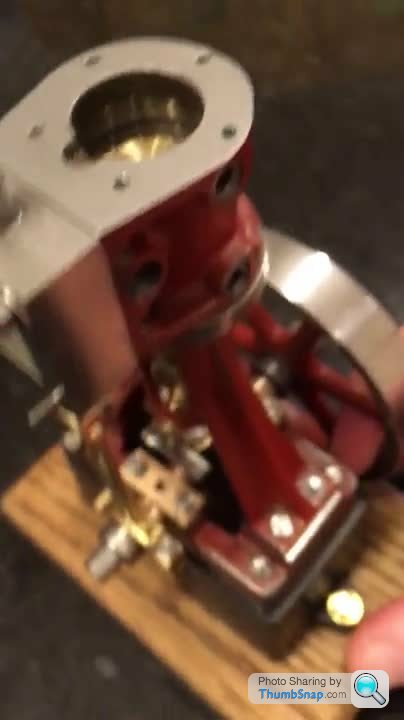
Next job is to make the inlet and exhaust fittings. I’ve got some hexagon bar on order, so they shouldn’t take long to make.
So here’s the first go at test assembly of all the mechanical parts:
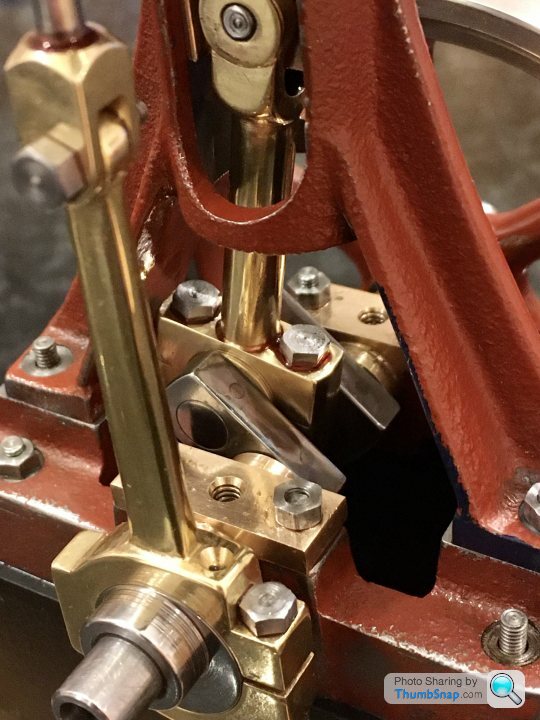
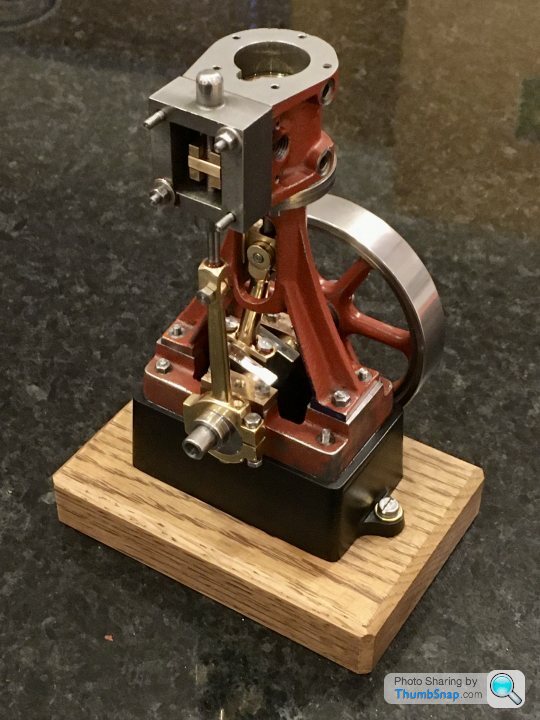
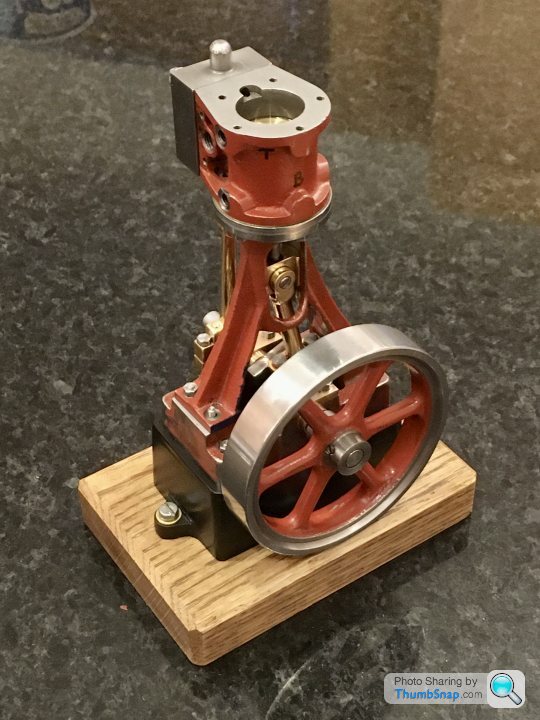
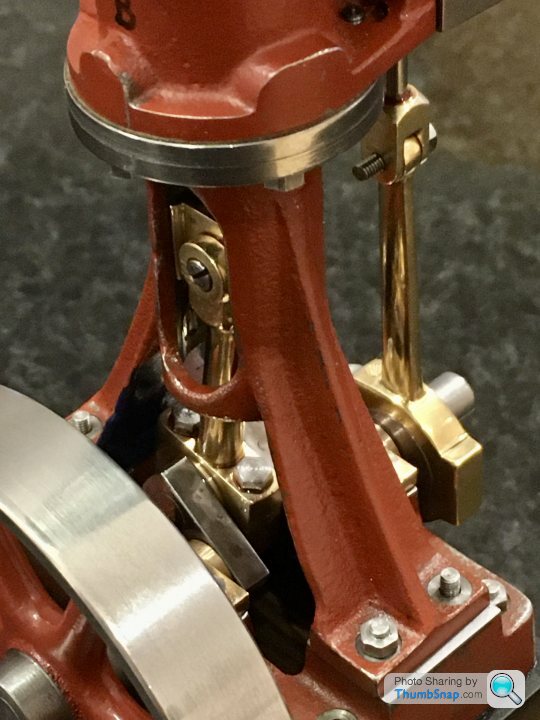
And a video clip of it moving, lubricated with some light oil. Valve and timing setup isn’t done yet, and there is no gland packing. There is one slightly tight spot towards the bottom of piston travel, but it’s getting more free as I fiddle with it:
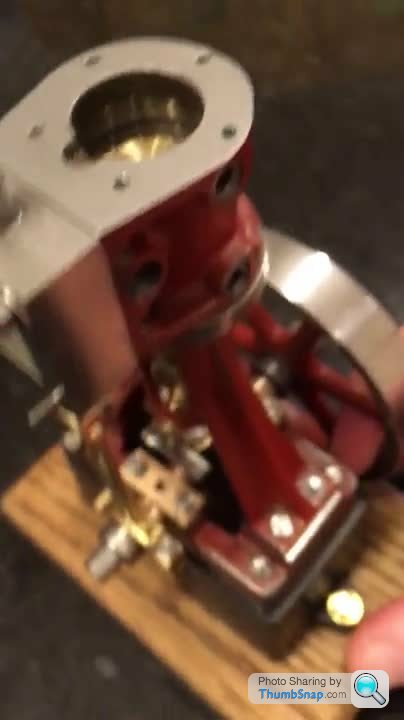
Next job is to make the inlet and exhaust fittings. I’ve got some hexagon bar on order, so they shouldn’t take long to make.
Made a start on painting the castings yesterday. Cleaned down with brake cleaner, and masked with Tamiya tape and Blu-Tack:
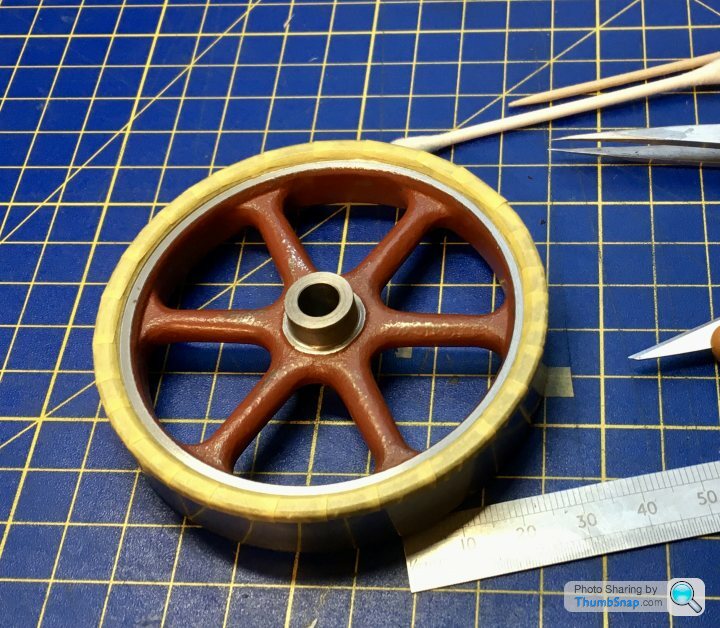
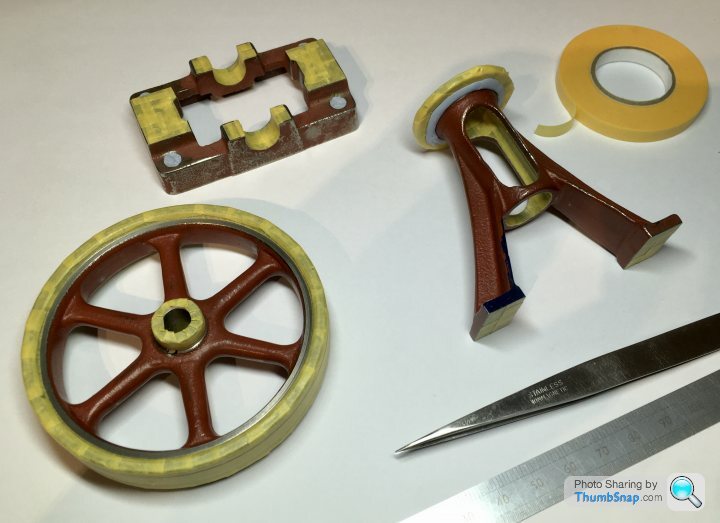
Primed with Tamiya fine surface primer and airbrushed with several thick coats of paint. After all the research I’ve done over the months, I’m fed up with the sight of green 10Vs, so decided on Dark Blue Meccano enamel that my dad bought decades ago, but never used. I think it will look great with polished silver and brass:
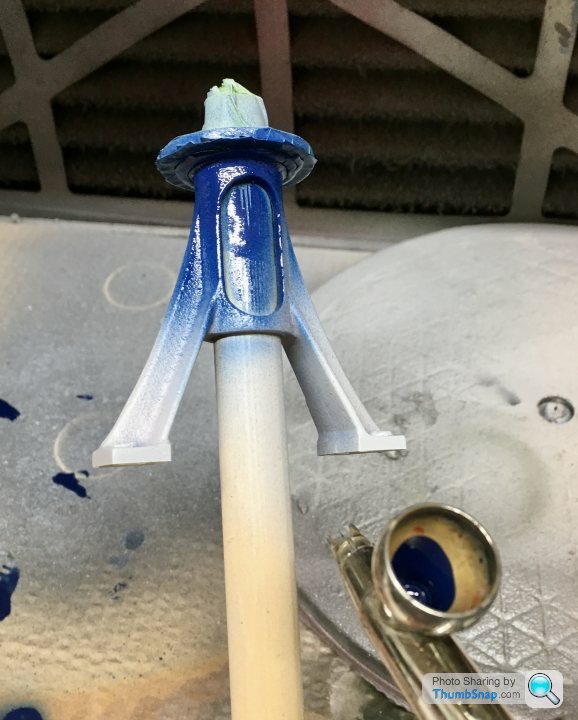
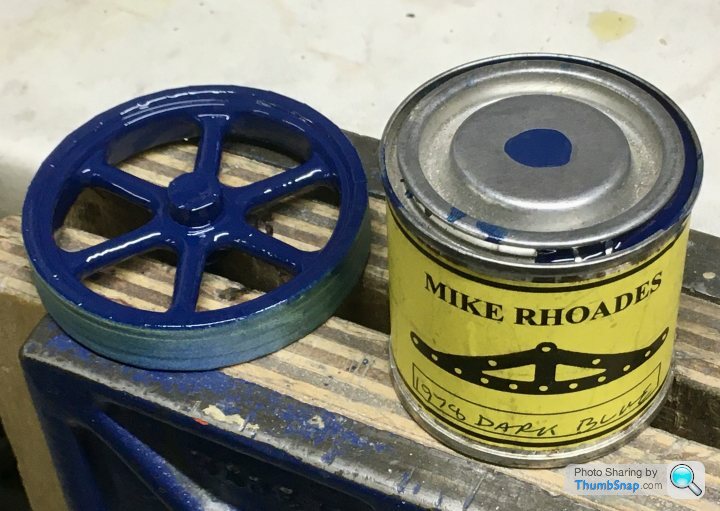
As expected, a few bits peeled off the smooth flywheel areas on removing the tape (should have removed it before the paint flashed off). Not a problem though because I’d always planned on a final corrective coat done in the lathe to get as concentric a demarcation as possible:
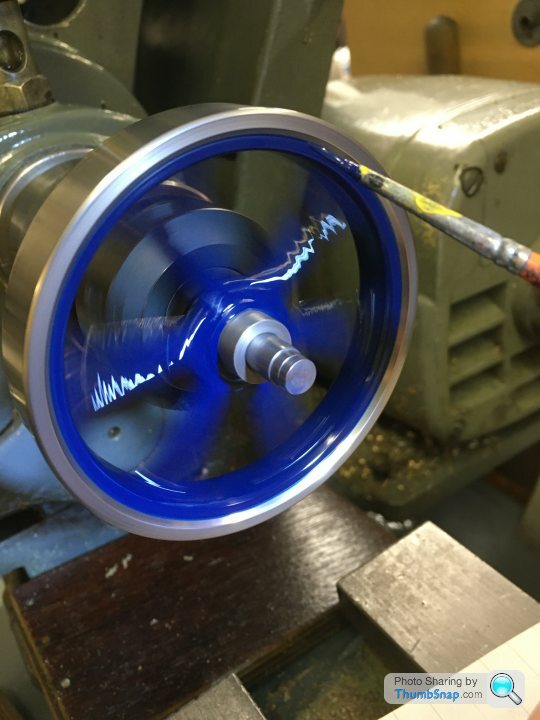
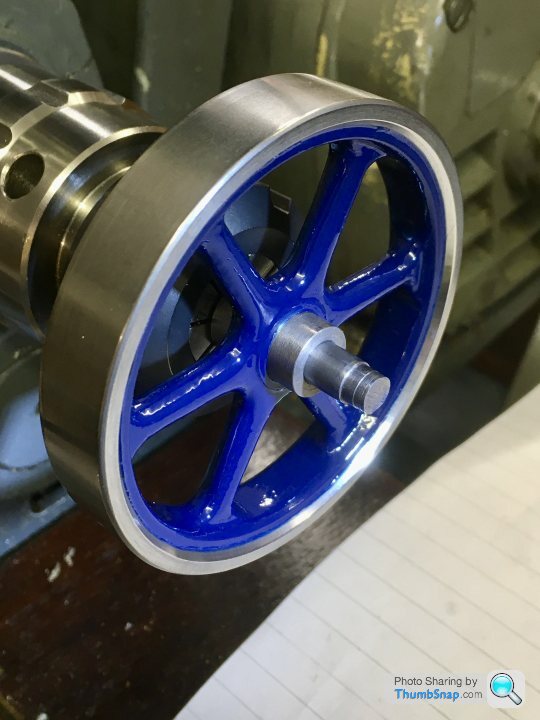
I often use this technique on scale models to get perfectly concentric painted bands on various things.
I thinned the paint a bit for the valve cover, and blobbed it into the cast recess, letting capillary action do the work:
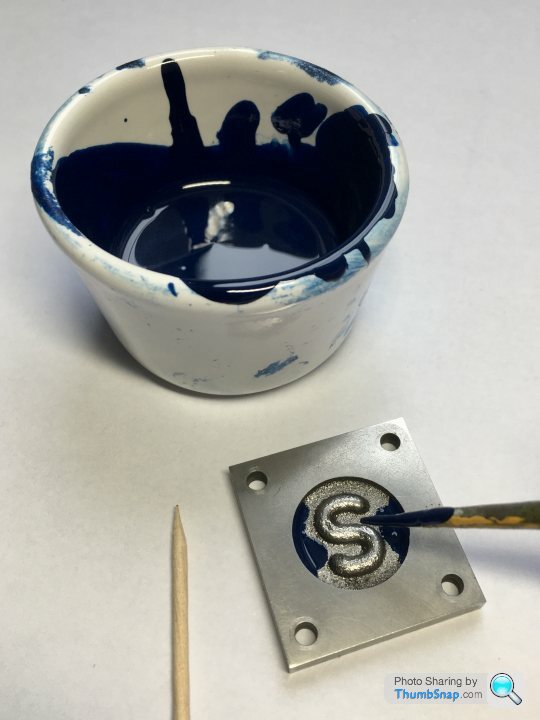
Then into the oven to bake out the solvents and harden the paint a bit:
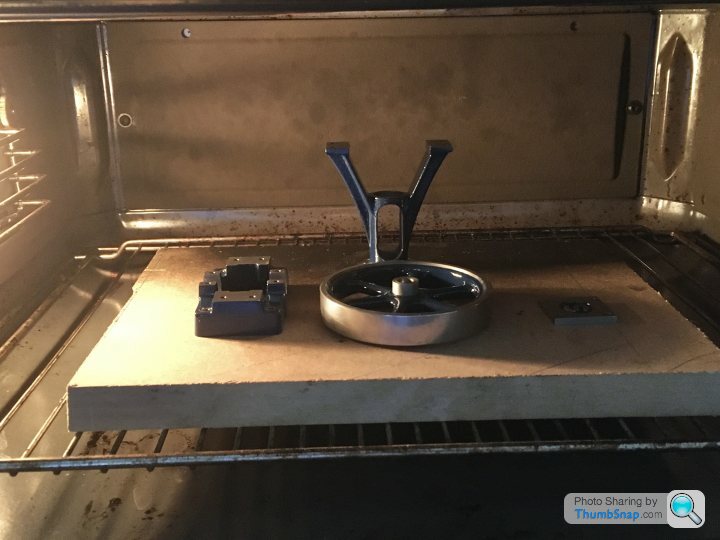
Pretty much done:
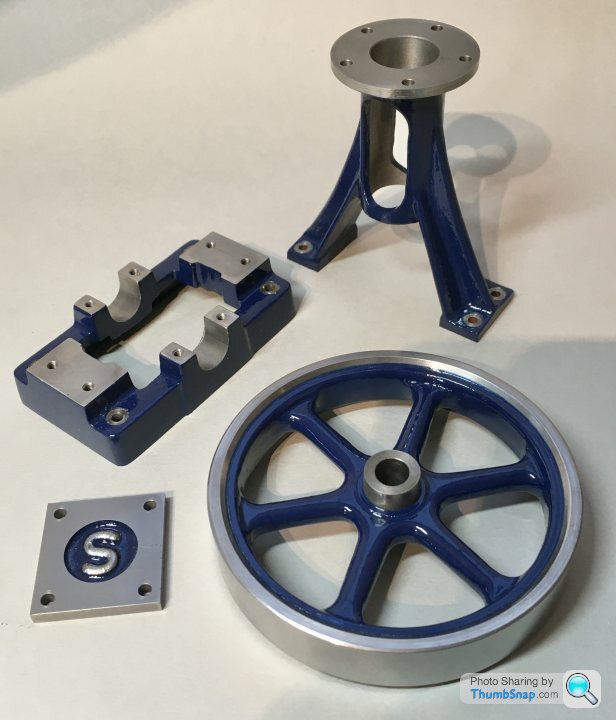
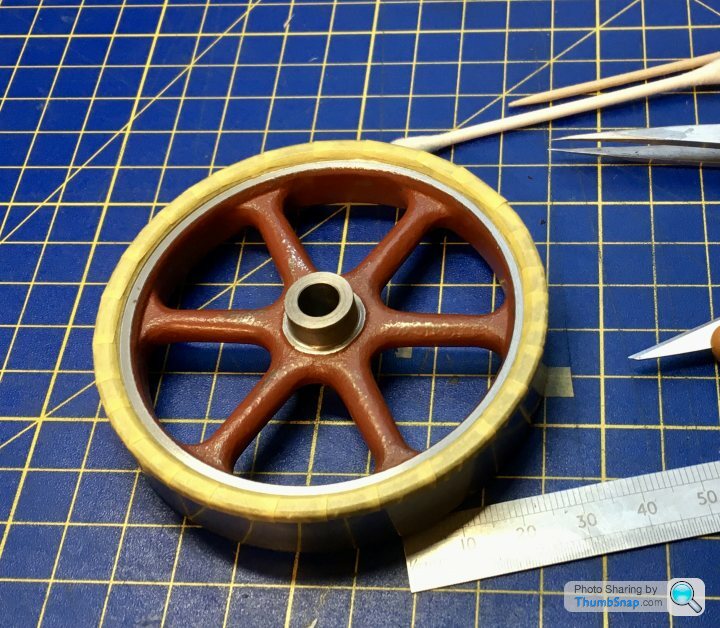
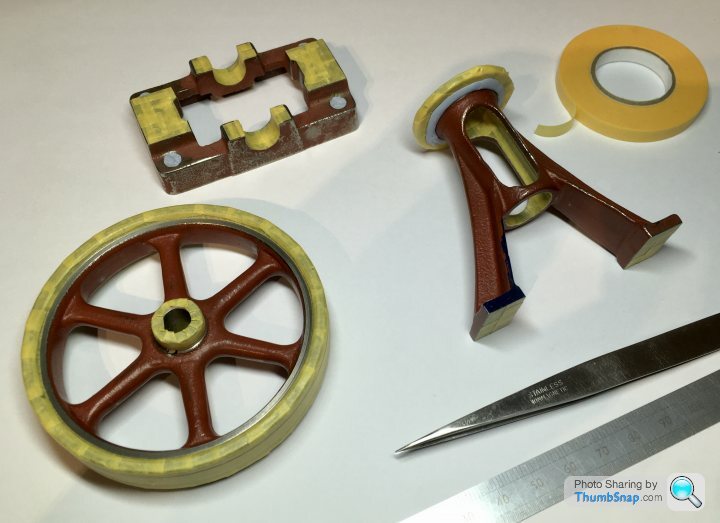
Primed with Tamiya fine surface primer and airbrushed with several thick coats of paint. After all the research I’ve done over the months, I’m fed up with the sight of green 10Vs, so decided on Dark Blue Meccano enamel that my dad bought decades ago, but never used. I think it will look great with polished silver and brass:
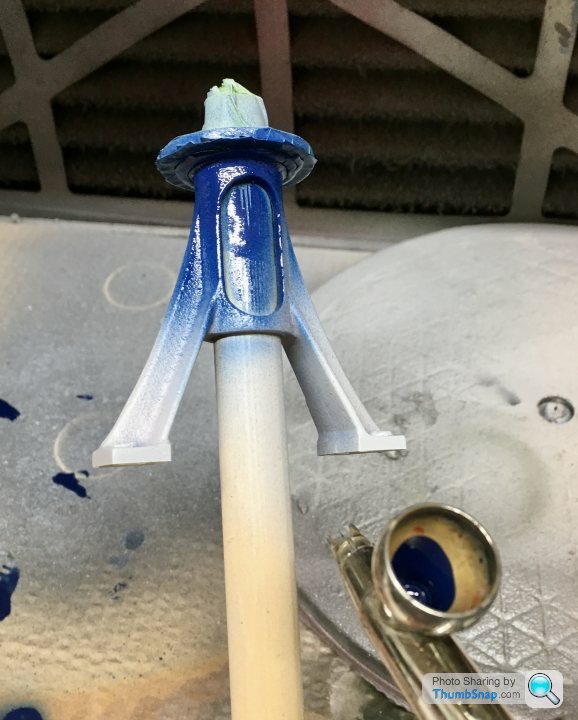
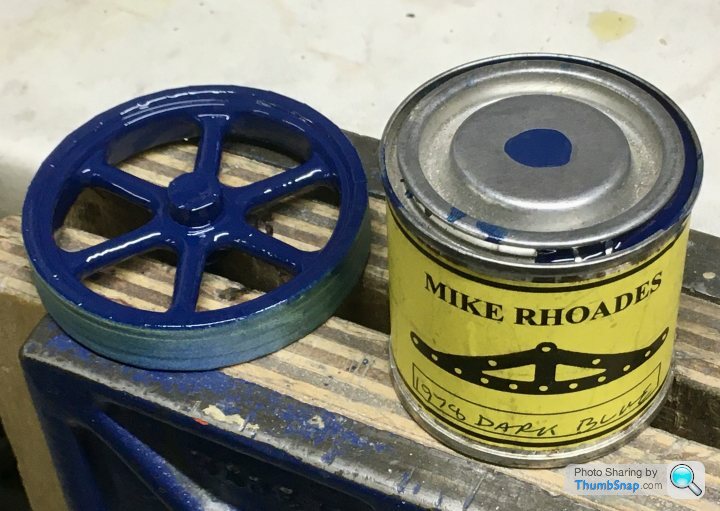
As expected, a few bits peeled off the smooth flywheel areas on removing the tape (should have removed it before the paint flashed off). Not a problem though because I’d always planned on a final corrective coat done in the lathe to get as concentric a demarcation as possible:
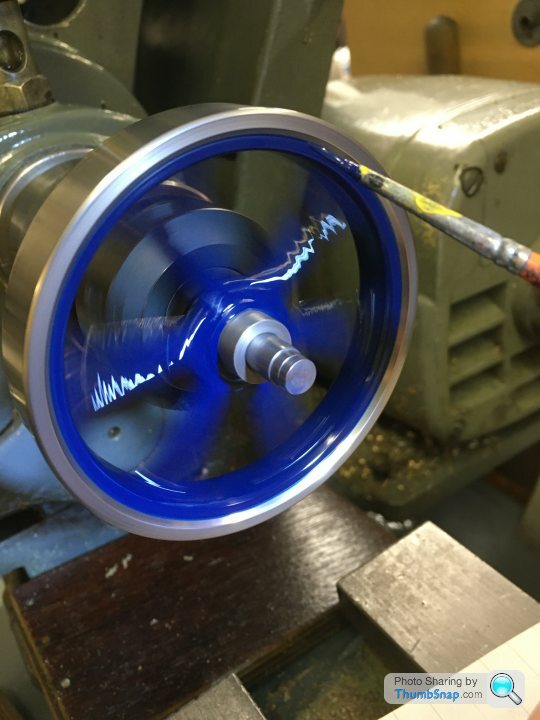
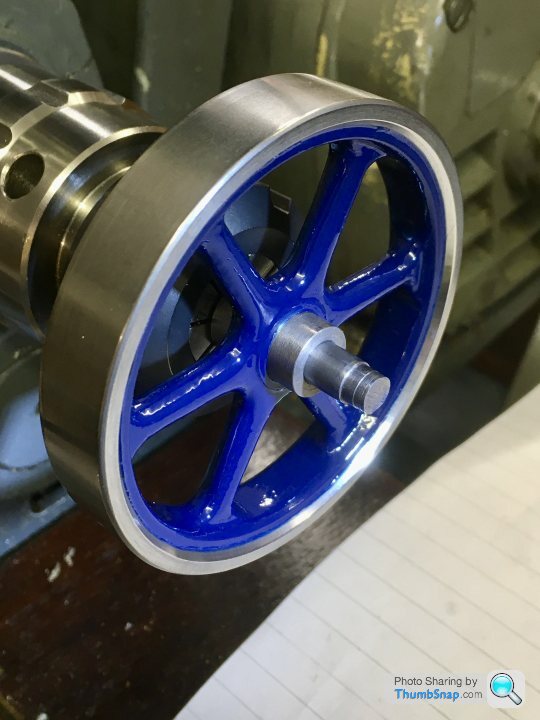
I often use this technique on scale models to get perfectly concentric painted bands on various things.
I thinned the paint a bit for the valve cover, and blobbed it into the cast recess, letting capillary action do the work:
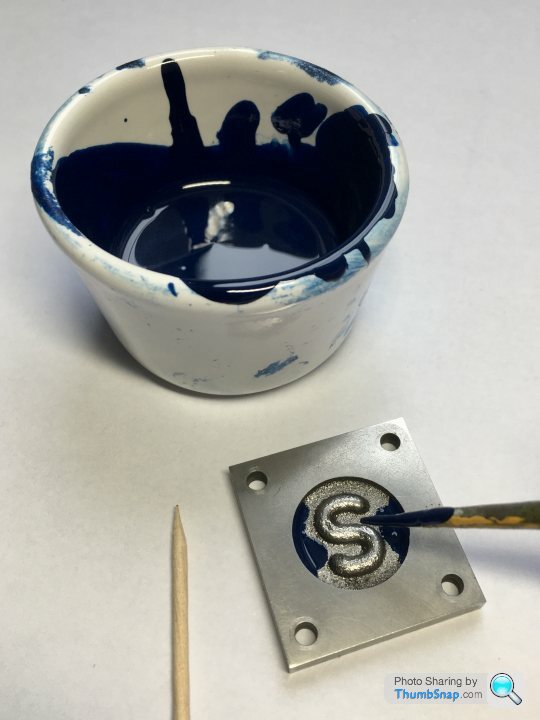
Then into the oven to bake out the solvents and harden the paint a bit:
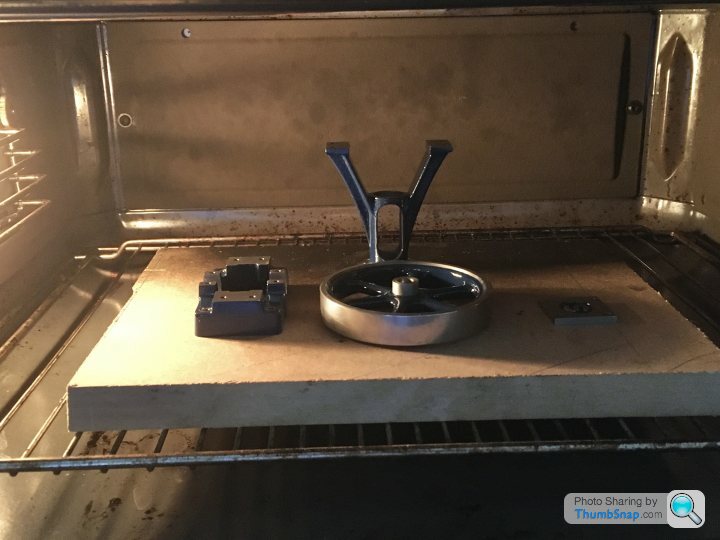
Pretty much done:
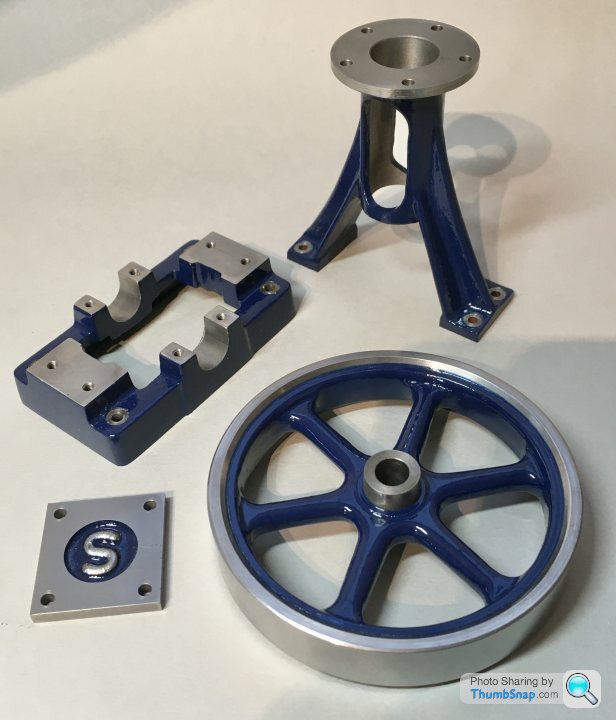
dhutch said:
Looks amazing, red is also nice, but definitely better than green.
Agreed - it has to be one of those three colours, or maybe black if you’re desperate. I had the dark blue paint sitting in a box so thought why not use it. I also like the Meccano connection somehow. The old 1930’s Meccano dark red would look nice too I think.Still waiting for a small step drill to arrive, to open up the jacket holes, and the hex bar to make the steam fittings.
Halmyre said:
Having followed this thread, I can understand why the unmachined Stuart kit is £96 and the machined kit is £466.
Actually £559.44 with VAT. Then postage on top.For the ready to run model it’s an eye-watering £803.76.
OK, it’s an ancient design, not really designed for commercial manufacture, but still, those prices are...interesting.
Gassing Station | Scale Models | Top of Page | What's New | My Stuff