Stuart 10V Vertical Steam Engine
Discussion
Few loose ends to tidy up.
The holes positions for the cylinder cladding screws are such that the undersides are unsupported, making the cladding bow on tightening. I made some Milliput bosses, filed flush, then painted satin black:
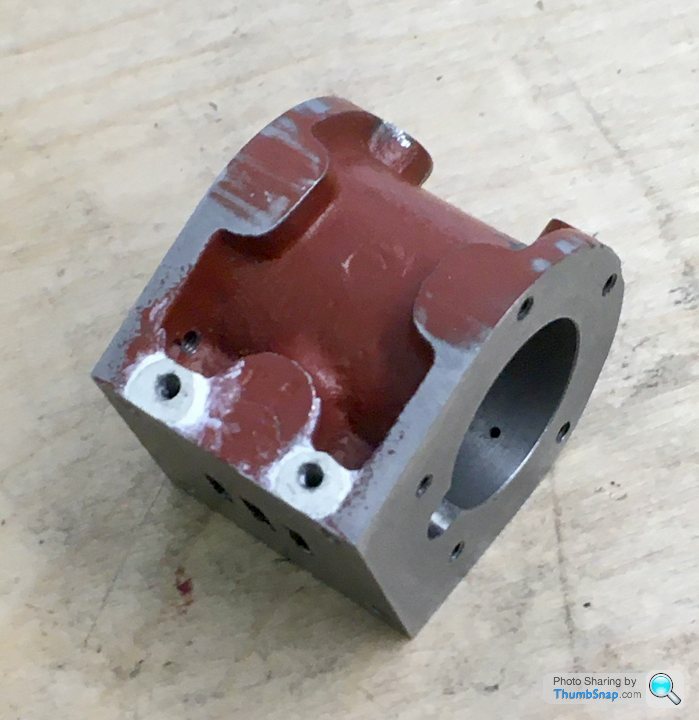
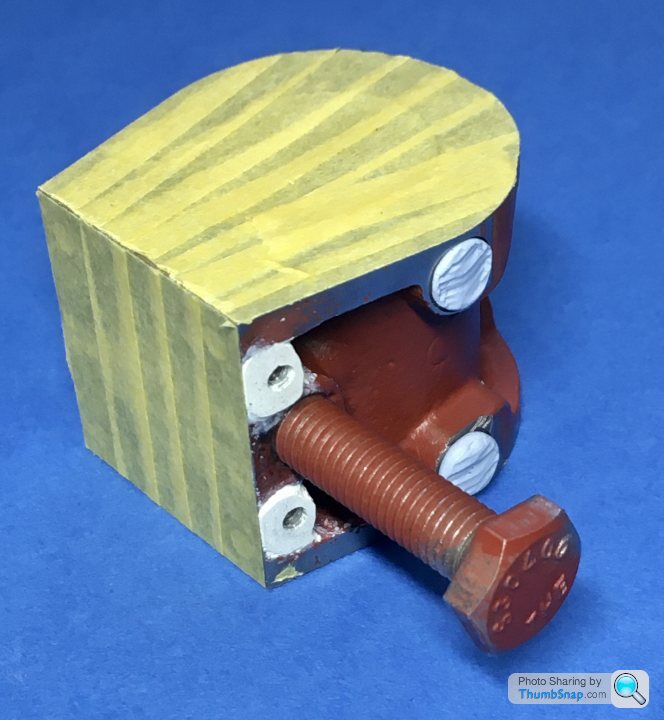
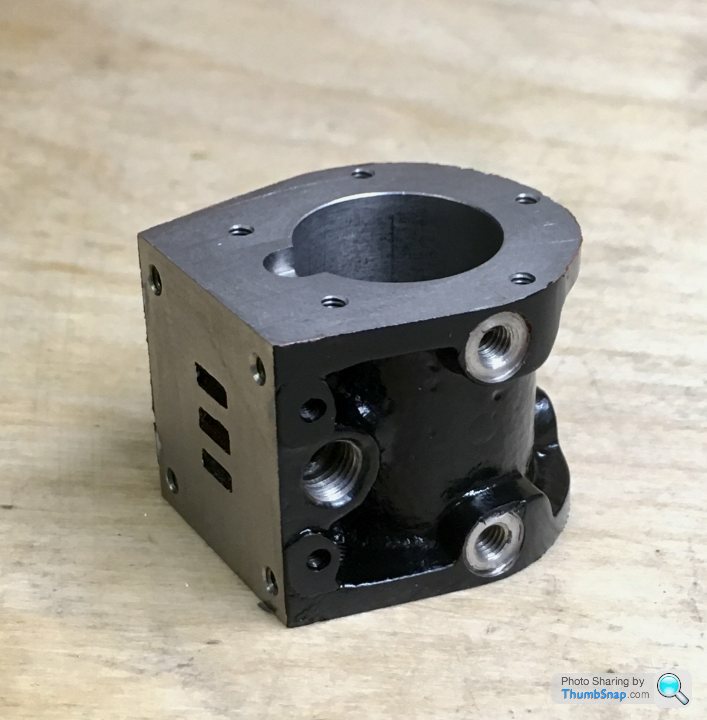
Then the 1/4” thread for the steam inlet union:
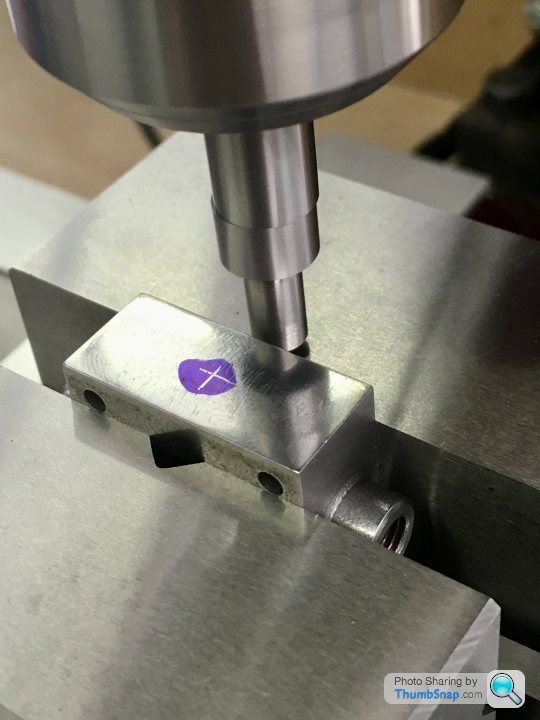
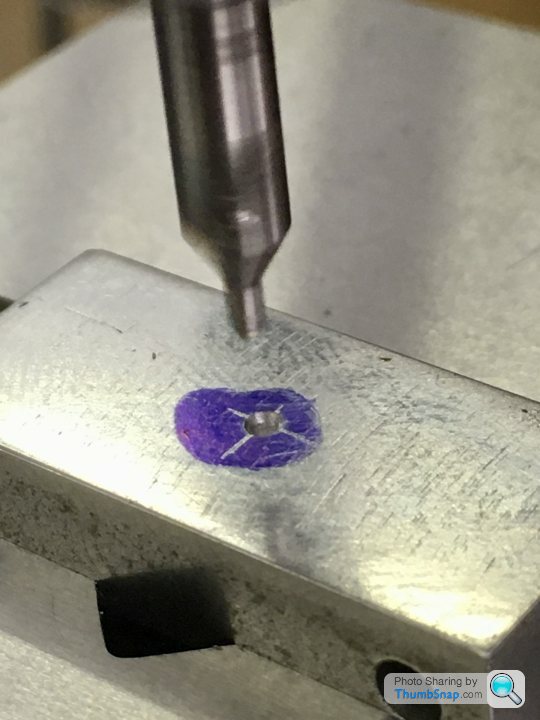
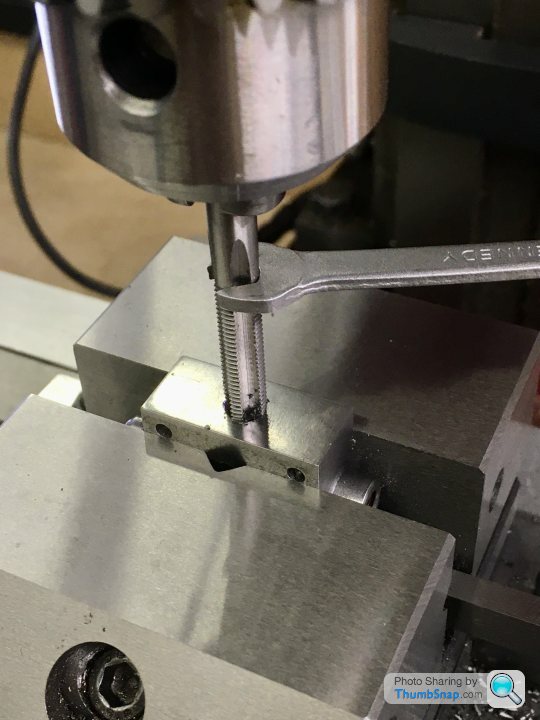
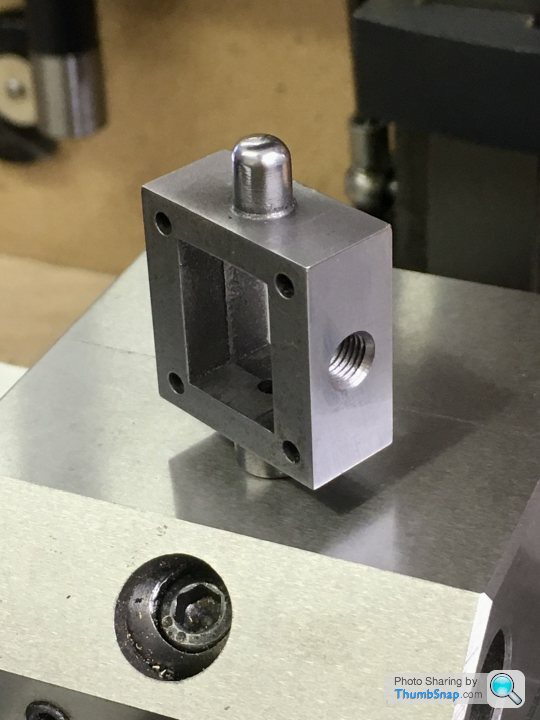
And made a sealing washer parted off from some old copper pipe. Needs annealing:
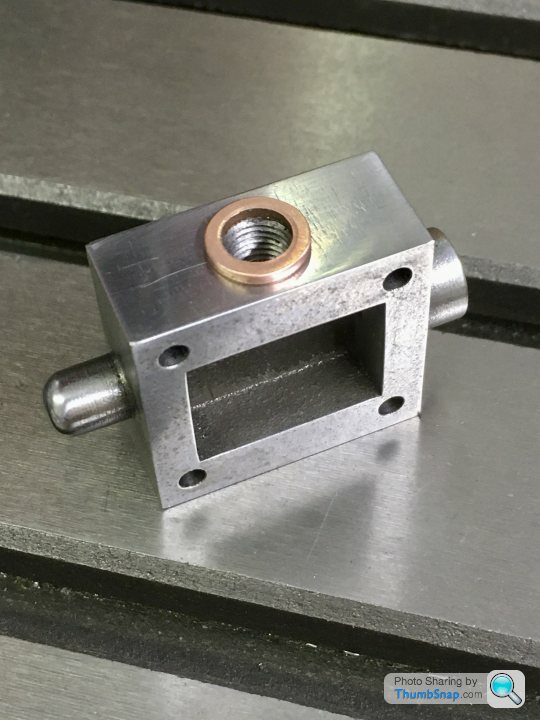
The holes positions for the cylinder cladding screws are such that the undersides are unsupported, making the cladding bow on tightening. I made some Milliput bosses, filed flush, then painted satin black:
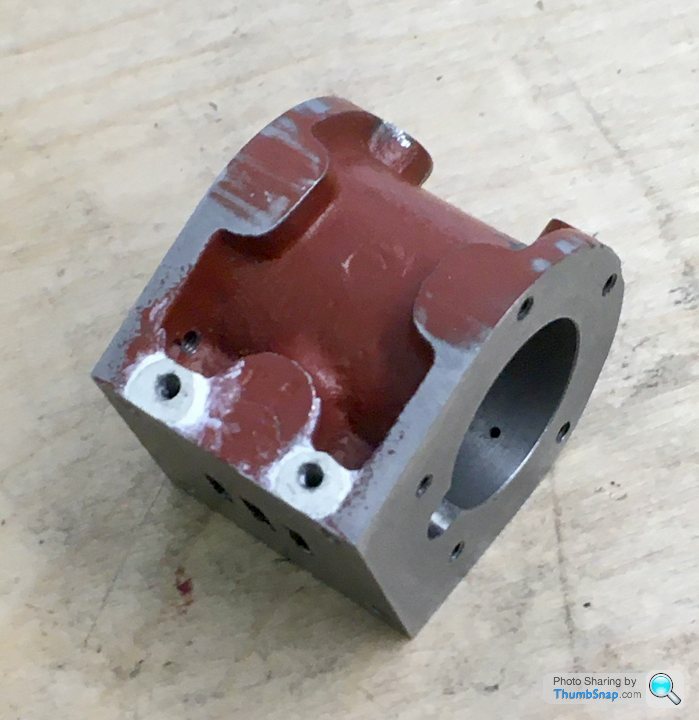
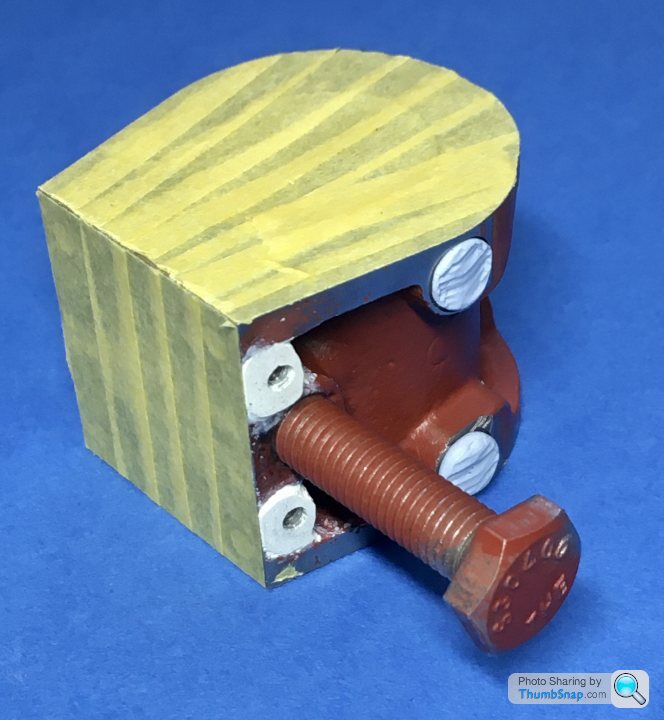
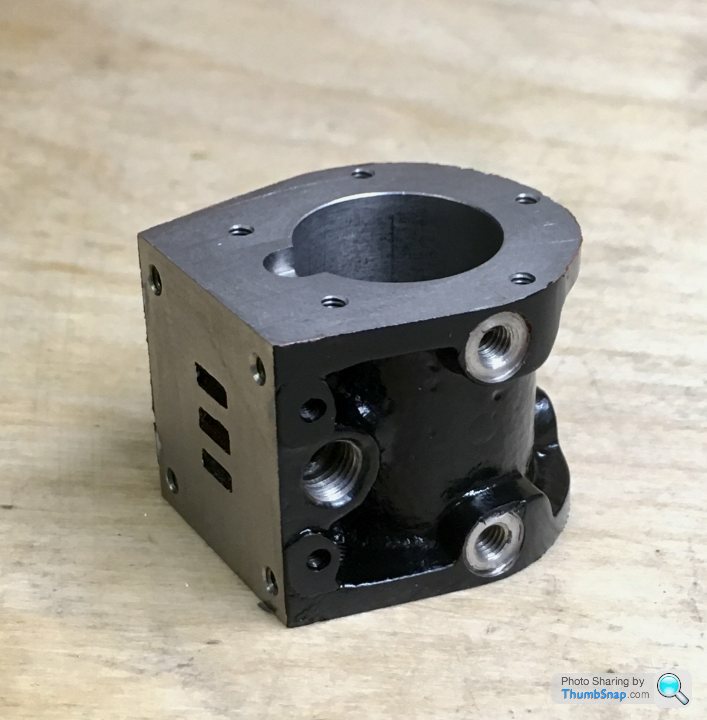
Then the 1/4” thread for the steam inlet union:
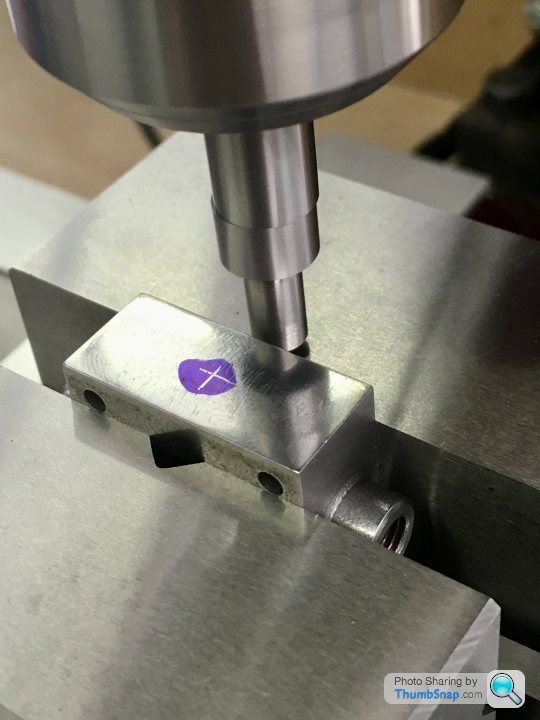
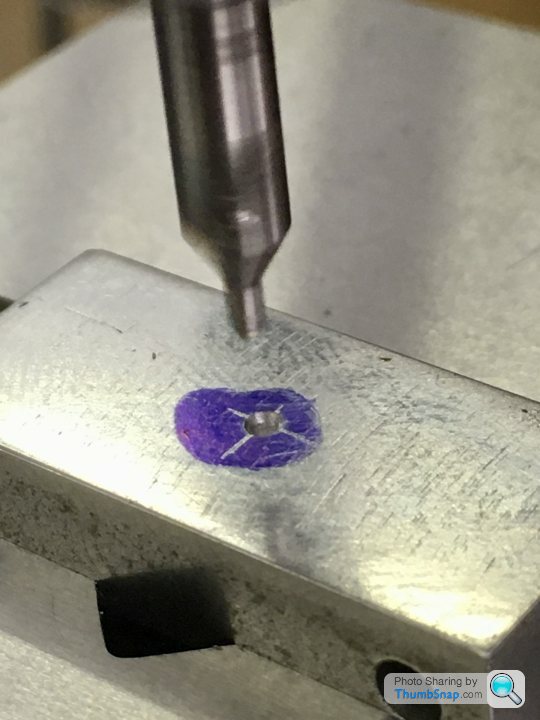
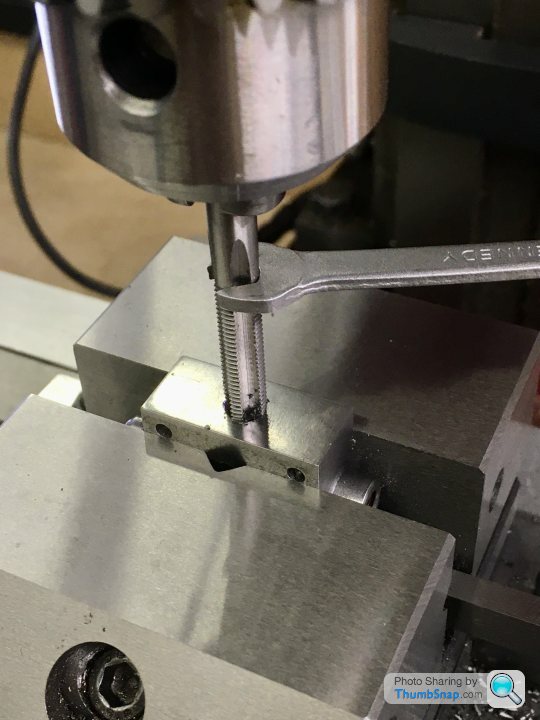
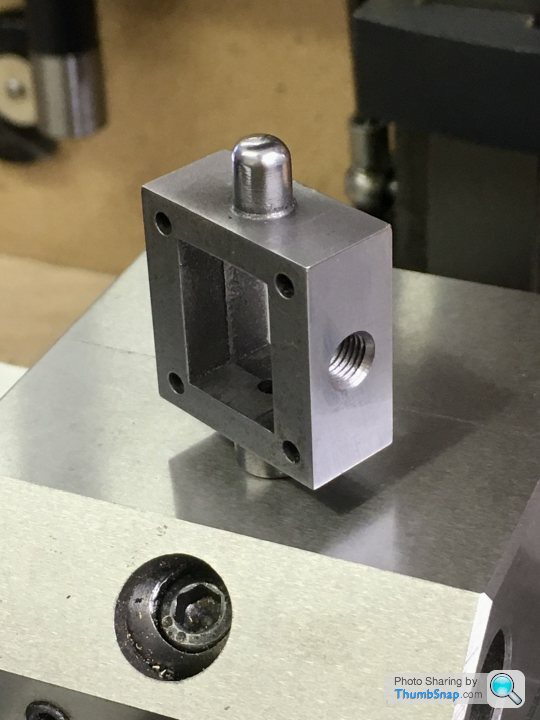
And made a sealing washer parted off from some old copper pipe. Needs annealing:
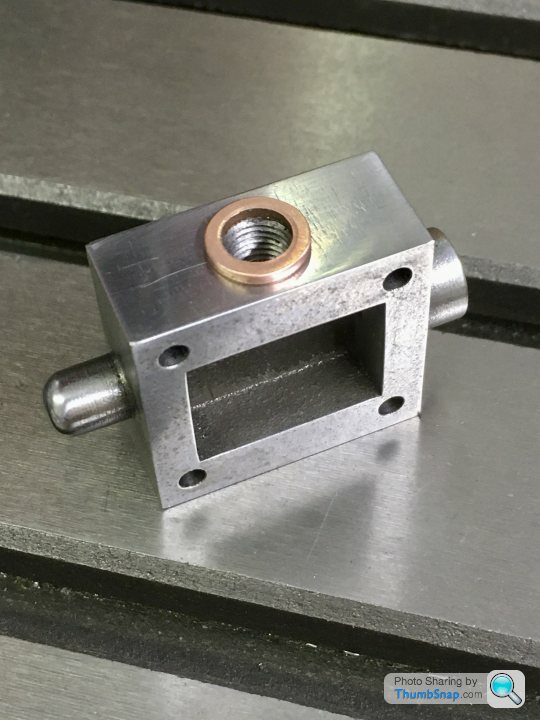
Edited by dr_gn on Friday 9th October 18:15
Every time I looked at the connecting rod:
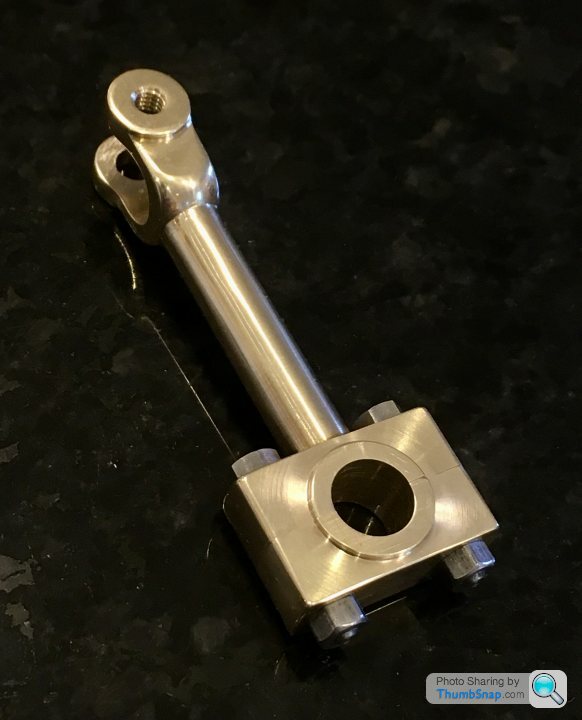
...I saw an Elephant’s leg.
By mistakenly sawing off the turning spigot, I gave myself a problem in how to hold it to subsequently taper-turn the shaft. The main bearing block is turned to a diameter, so I decided to try and make a split fixture for that end, and clamp an aluminium block in the little end for centre drilling:
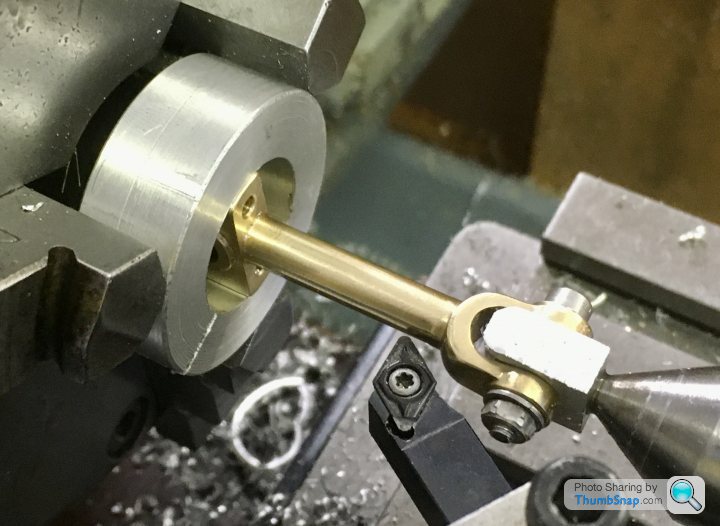
I drew it out on CAD, and settled on a 3 degree included angle taper. After setting the compound slide to 1 1/2 degrees, try as I might, I couldn’t get any of my turning tools to do it in one pass. I ended up doing half, then re-setting the tool and doing the rest. After a quick polish you can’t see the join. It now looks better:
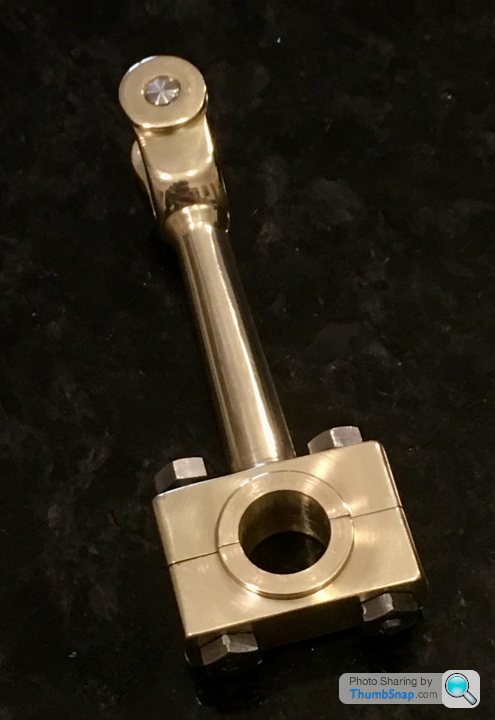
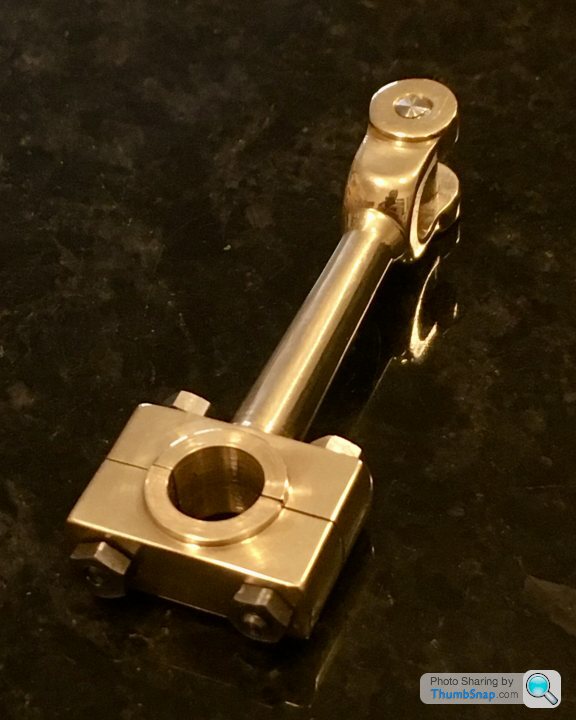
Also cleaned up all the Little end pin end, the stud ends and bolt heads - most of them had prominent pips:
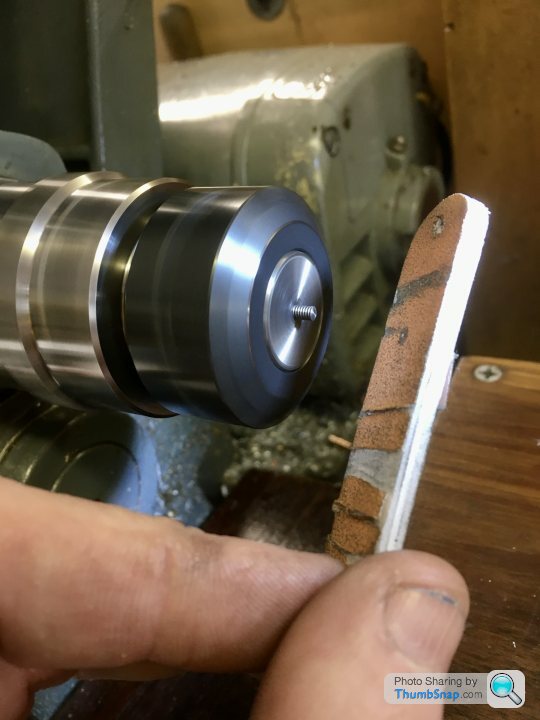
So now I’m waiting for some supplies to make the unions and open up the cladding holes, and it’ll be on to assembly and testing.
It’s worth noting that as I went through all the supplied fasteners, I found two of the nuts were half-nuts - probably for the eccentric clamp bolt. I’d already made my own half nuts by turning down some standard ones. I’ll just use the supplied ones for the big-end caps instead.
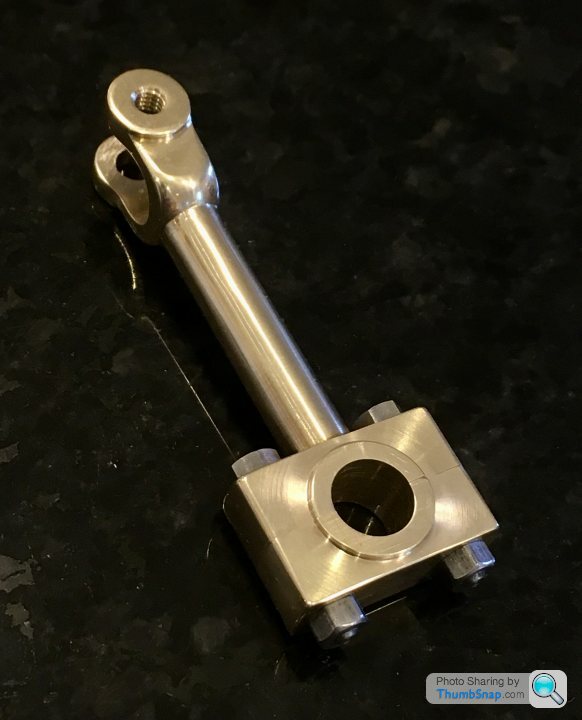
...I saw an Elephant’s leg.
By mistakenly sawing off the turning spigot, I gave myself a problem in how to hold it to subsequently taper-turn the shaft. The main bearing block is turned to a diameter, so I decided to try and make a split fixture for that end, and clamp an aluminium block in the little end for centre drilling:
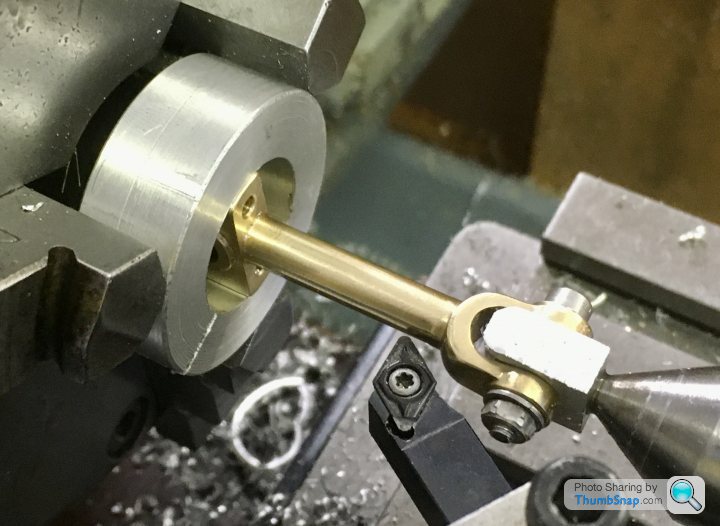
I drew it out on CAD, and settled on a 3 degree included angle taper. After setting the compound slide to 1 1/2 degrees, try as I might, I couldn’t get any of my turning tools to do it in one pass. I ended up doing half, then re-setting the tool and doing the rest. After a quick polish you can’t see the join. It now looks better:
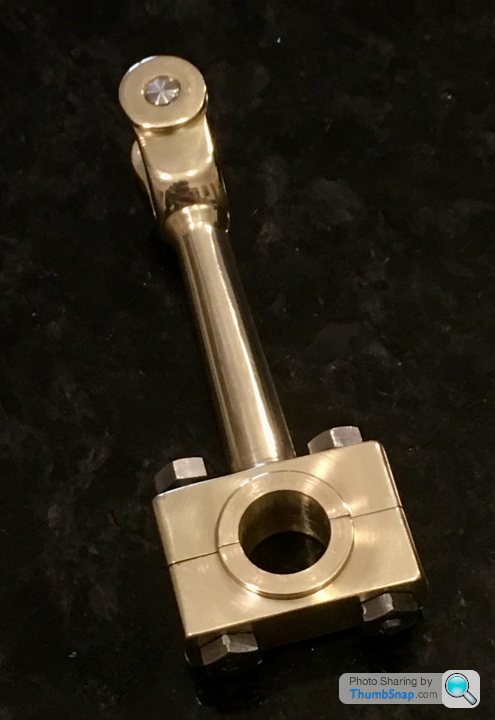
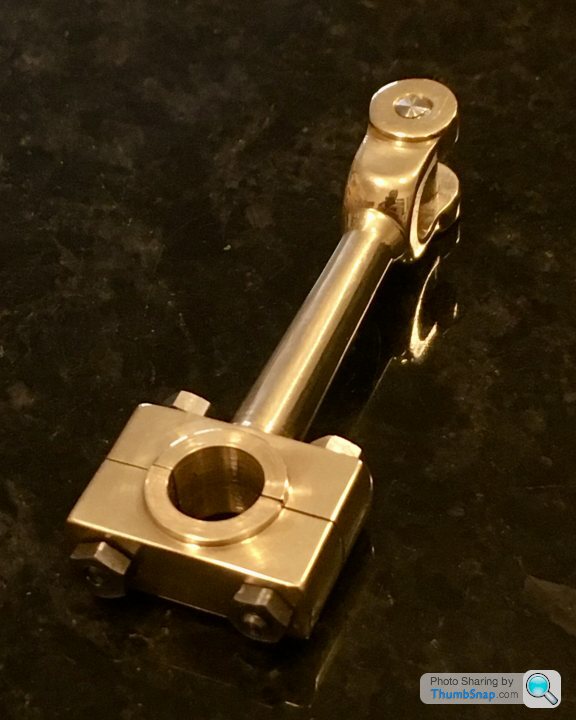
Also cleaned up all the Little end pin end, the stud ends and bolt heads - most of them had prominent pips:
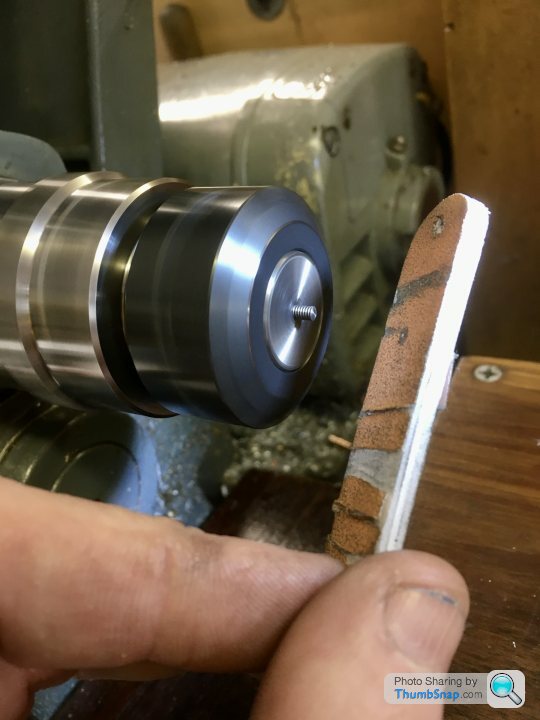
So now I’m waiting for some supplies to make the unions and open up the cladding holes, and it’ll be on to assembly and testing.
It’s worth noting that as I went through all the supplied fasteners, I found two of the nuts were half-nuts - probably for the eccentric clamp bolt. I’d already made my own half nuts by turning down some standard ones. I’ll just use the supplied ones for the big-end caps instead.
dr_gn said:
fourfoldroot said:
I’ve been looking at the Stuart models website to look for a next model; that looks like an S50, not a 10H.My second project was the S50 above,but was not really any harder than the 10V, possibly a bit easier.
I’m currently tackling a Sanderson beam engine. I can’t say I’m loving the castings. They are very poorly cast compared to Stuart and some of them are undersized. They are a very old set from ebay. I’m guessing the current offerings are much better.
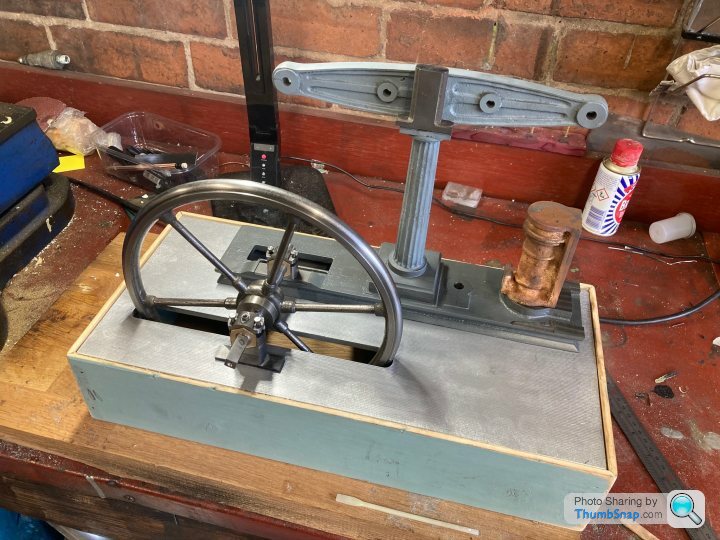
fourfoldroot said:
...I’m guessing the current offerings are much better.
I have no knowledge of the kit, or castings, but that appears a significant assumption to me!fourfoldroot said:
My second project was the S50 above,but was not really any harder than the 10V, possibly a bit easier.
I’m currently tackling a Sanderson beam engine.
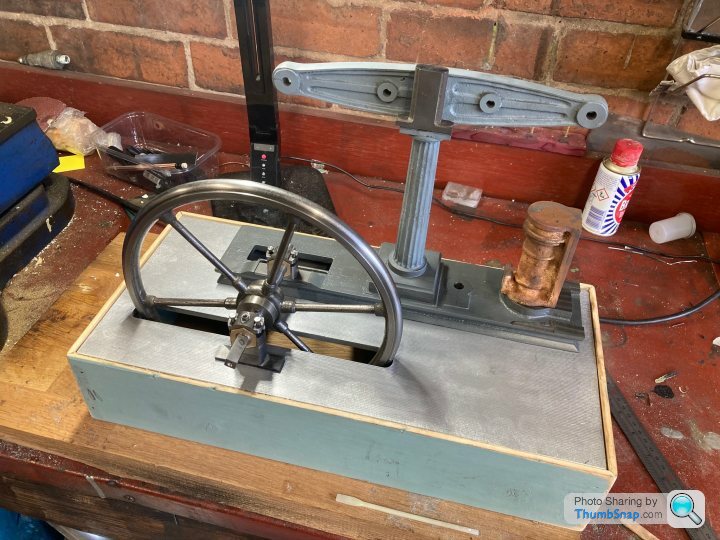
Very nice.I’m currently tackling a Sanderson beam engine.
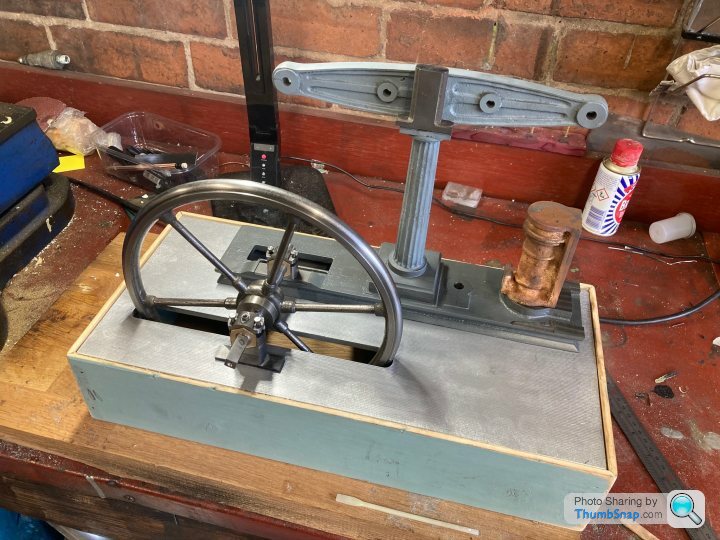
fourfoldroot said:
dr_gn said:
fourfoldroot said:
I’ve been looking at the Stuart models website to look for a next model; that looks like an S50, not a 10H.My second project was the S50 above,but was not really any harder than the 10V, possibly a bit easier.
I’m currently tackling a Sanderson beam engine. I can’t say I’m loving the castings. They are very poorly cast compared to Stuart and some of them are undersized. They are a very old set from ebay. I’m guessing the current offerings are much better.
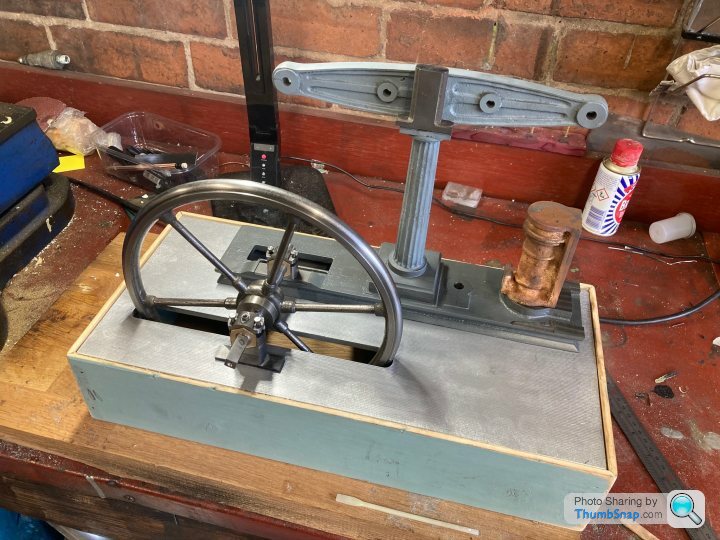
After asking the question on the ME forum "What's a good second model", I'm going with my desire to build a Stuart Twin Victoria. However, after getting some wisdom from the guys over there, I wont be spending £625 of the full kit, but only buying the drawings, and the main castings, which should come to less than £200. I'll be sourcing all the raw materials supplied in the kit from my local metals company, and all the ME fasteners online. The box beds are castings, but it's been suggested that these can easily be made from aluminium bar and JB weld, and will be indistinguishable form castings once shot blasted, painted and machined. The governor kit for it looks nice, so I'll get that too. So - a much more complex build, slightly different valve gear; a step on from the 10V, and a few new techniques too.
I also mentioned my ambition to one day build a traction engine. To my surprise everyone who commented urged me to start on this long-term project now. It's a bit daunting, but I'll be starting on the "Minnie" 1" scale traction engine next year. It's a model that was first outlined in Model Engineer magazine in 1969/70. I am currently compiling all the relevant issues. It's a popular design, and many of the parts such as wheel parts, gears and main castings are commercially available. The most expensive individual component will be the certified boiler, which I will order from a specialist. Apparently it's about a 1 year waiting list, so by that time so other parts should be done.
Start on both. The victoria will give you something to achieve a finished model and build up skills for machining the more complex parts of the Minnie. It will extend the period to build up castings from abandoned projects on ebay.
I was gifted an entire workshop, machines and materials by a lady after her husband died. He was the model engineer. She was a domestic science teacher. Feeling the need to join in she built a 2” Fowler B1 ploughing engine including boiler as her first project. It is one of the finest large models I have ever seen. She then assisted her husband with his projects and for herself built wooden boat kits.
I was gifted an entire workshop, machines and materials by a lady after her husband died. He was the model engineer. She was a domestic science teacher. Feeling the need to join in she built a 2” Fowler B1 ploughing engine including boiler as her first project. It is one of the finest large models I have ever seen. She then assisted her husband with his projects and for herself built wooden boat kits.
fourfoldroot said:
Start on both. The victoria will give you something to achieve a finished model and build up skills for machining the more complex parts of the Minnie. It will extend the period to build up castings from abandoned projects on ebay.
I was gifted an entire workshop, machines and materials by a lady after her husband died. He was the model engineer. She was a domestic science teacher. Feeling the need to join in she built a 2” Fowler B1 ploughing engine including boiler as her first project. It is one of the finest large models I have ever seen. She then assisted her husband with his projects and for herself built wooden boat kits.
Wow. That's some wife!I was gifted an entire workshop, machines and materials by a lady after her husband died. He was the model engineer. She was a domestic science teacher. Feeling the need to join in she built a 2” Fowler B1 ploughing engine including boiler as her first project. It is one of the finest large models I have ever seen. She then assisted her husband with his projects and for herself built wooden boat kits.
Yes - I've fallen into the "huge model" trap with the paper/card Bismarck. Previously I'd built 4 ships in 4 years, and had the satisfaction of completing them, but the Bismark is languishing on its shelf not even 1/10 complete after 14 months...
I’ve got a Wilesco valve that I might try to use on the 10V somehow:
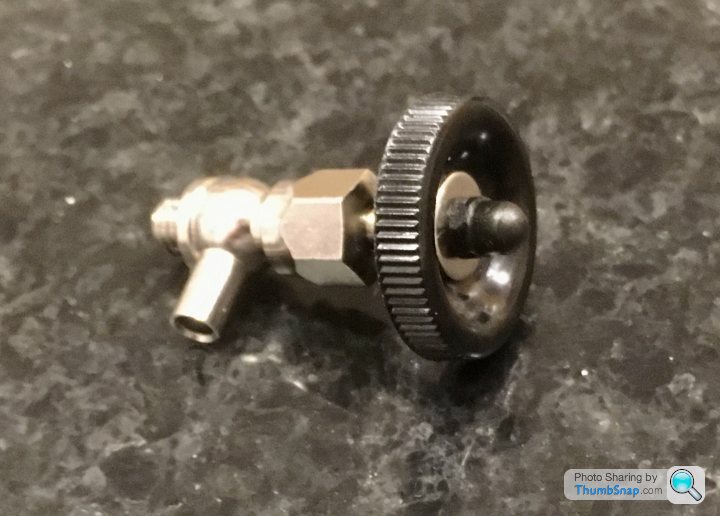
I suppose I’m scratching about looking for things to make until the step drill arrives and I can call it done, but anyway. The black plastic wheel looked a bit cheap, so I made a replacement out of scrap brass:
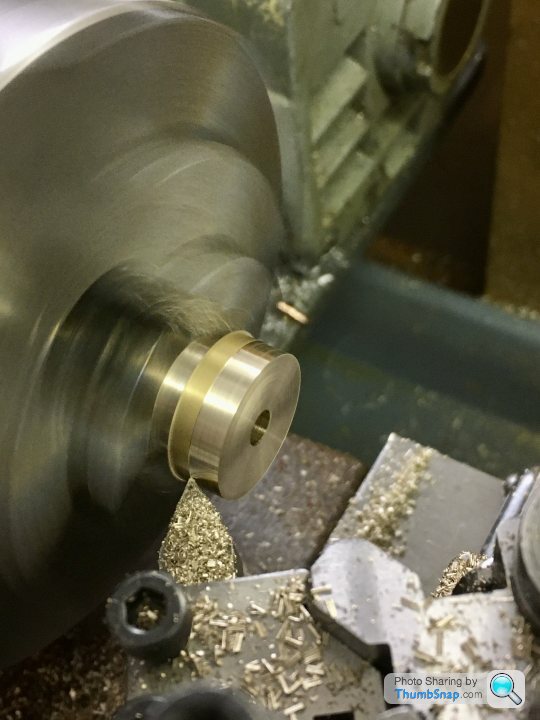
Bolted it to some brass hexagon bar and put in the vice, then got the centre using the edge finder:
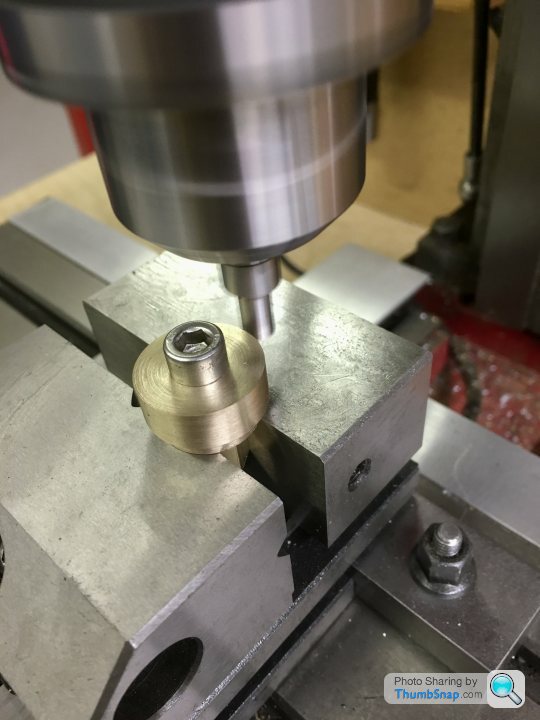
Then co-ordinate drilled the holes in the correct orientation for milling the edge detents using the hexagon bar as a 60 degree angle fixture:
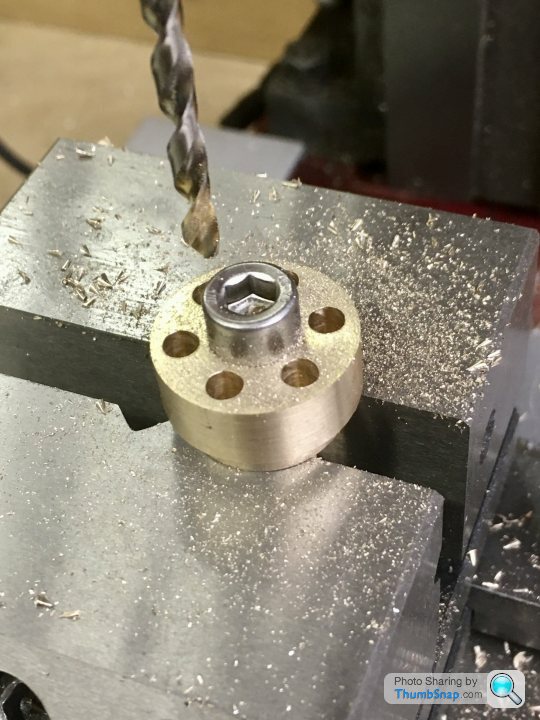
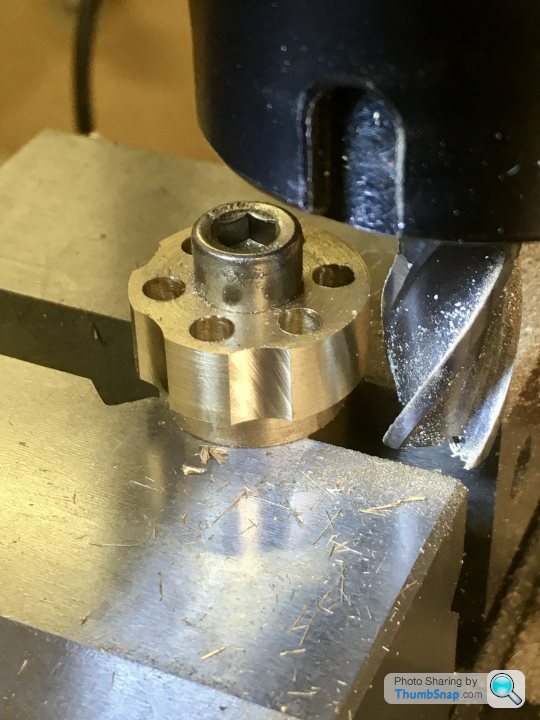
Then back in the lathe for parting off and profiling the faces:
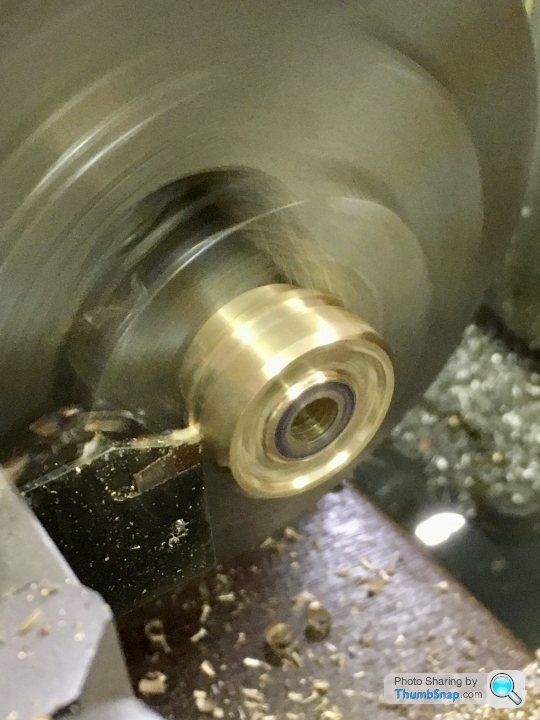
Used a square file to open up the central hole to suit the original slotted plate. I’d used a 4mm drill so the circumference quadrant points could be used a filing limit for the square edges:
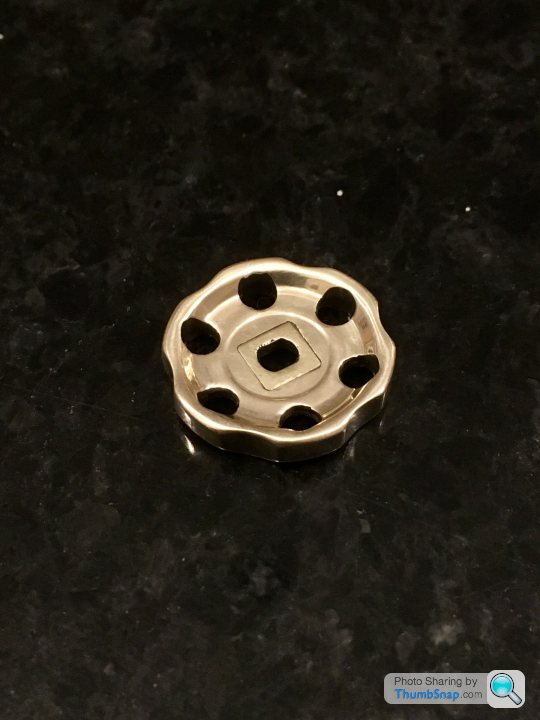
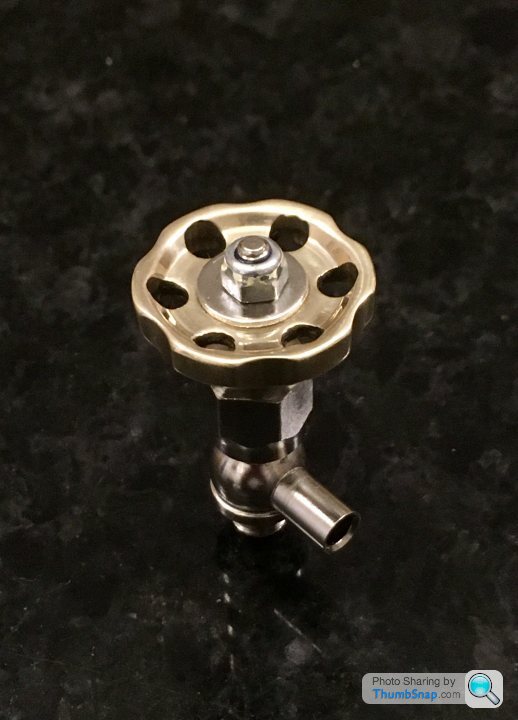
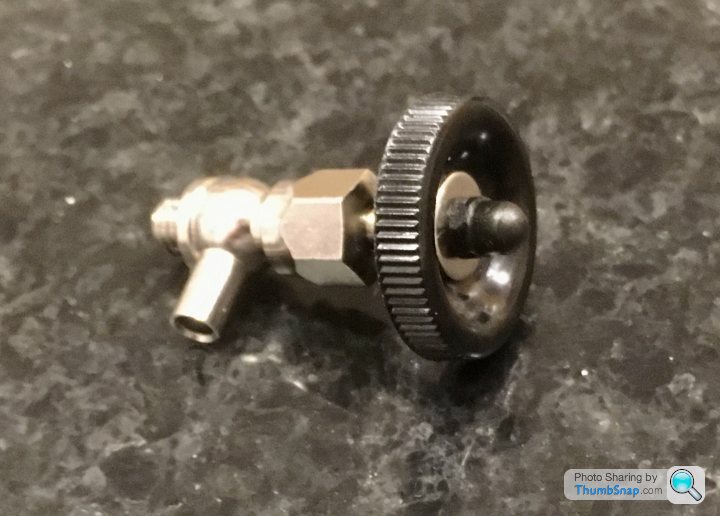
I suppose I’m scratching about looking for things to make until the step drill arrives and I can call it done, but anyway. The black plastic wheel looked a bit cheap, so I made a replacement out of scrap brass:
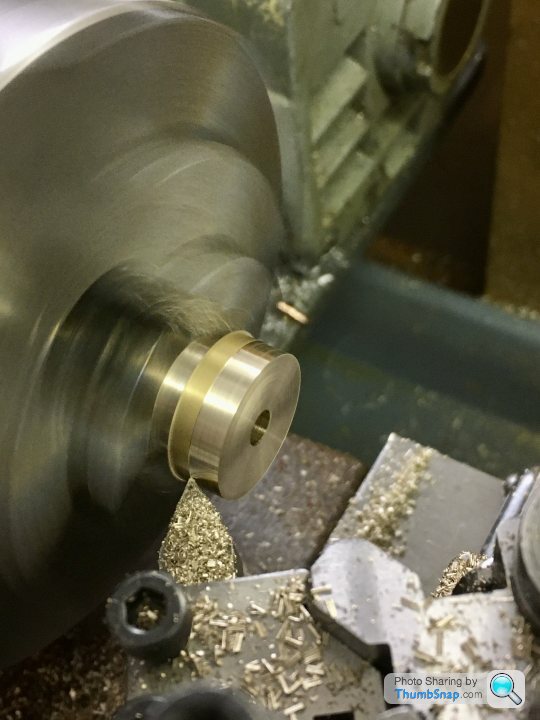
Bolted it to some brass hexagon bar and put in the vice, then got the centre using the edge finder:
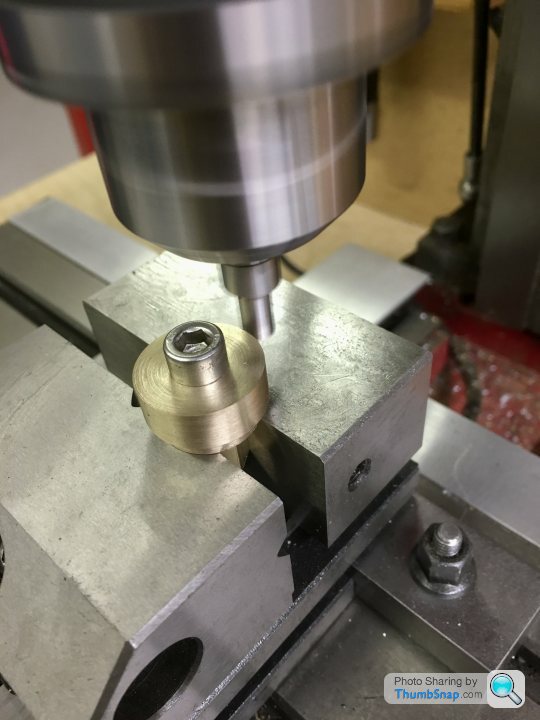
Then co-ordinate drilled the holes in the correct orientation for milling the edge detents using the hexagon bar as a 60 degree angle fixture:
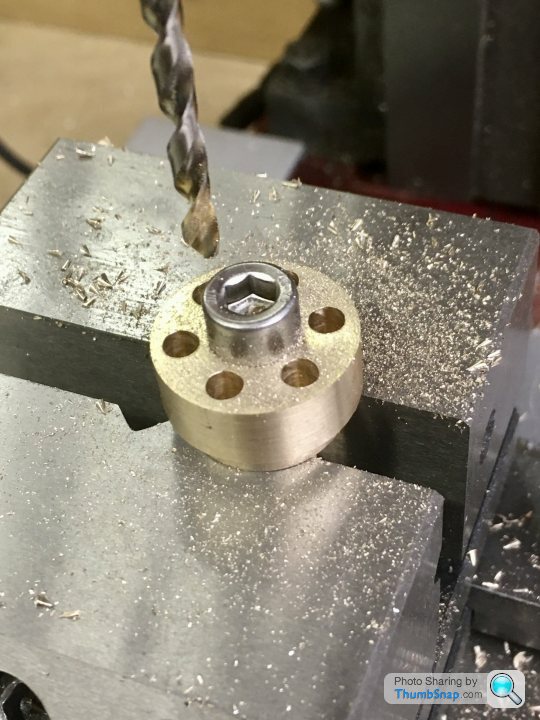
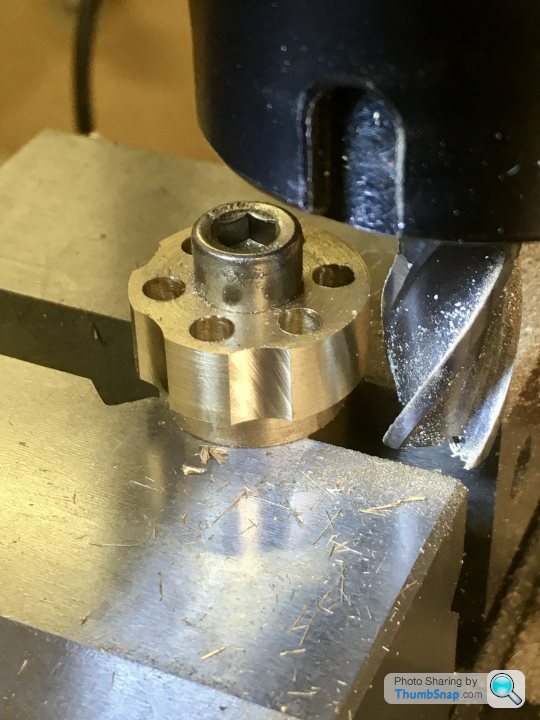
Then back in the lathe for parting off and profiling the faces:
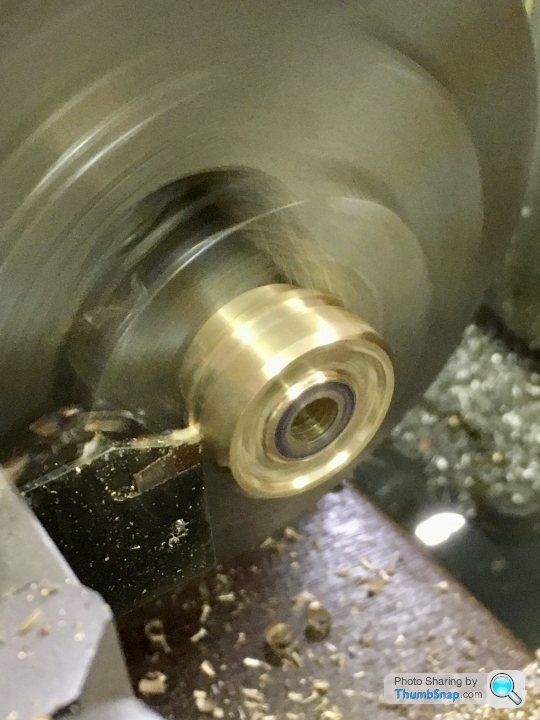
Used a square file to open up the central hole to suit the original slotted plate. I’d used a 4mm drill so the circumference quadrant points could be used a filing limit for the square edges:
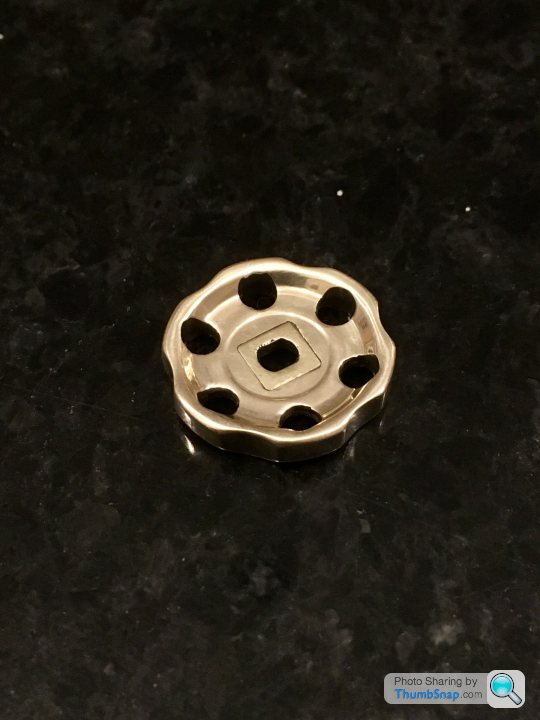
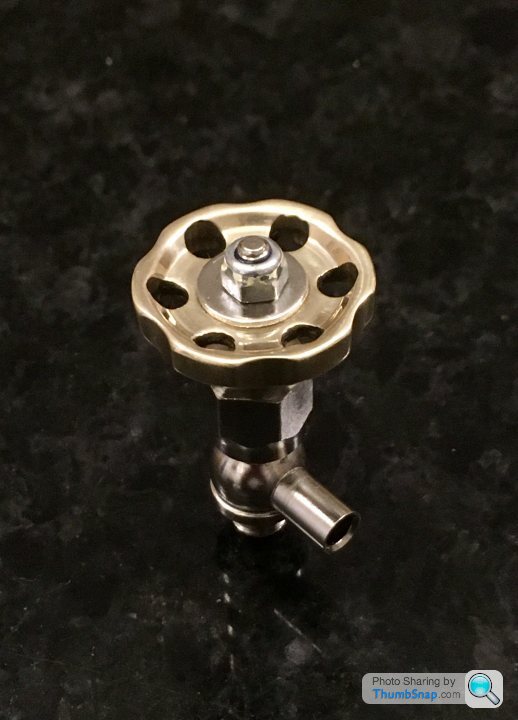
dhutch said:
I would love the build a traction engine, but would pick a larger scale. Either 4" or maybe 6" and then you could plod round the rally field on it!
Daniel
I hear what you’re saying, but for me at some point practicality has to prevail: Cost, weight and timescales are against me for a large model. The 1” was also designed specifically such that the largest turned parts (rear wheels) could be done on a small lathe like the ML7, so there is some reasoning behind the scale. Daniel
I’ve got a Wilesco Steam roller that I’m supposed to be making a bit more realistic with various parts. I’ll probably get that done before starting on the ‘proper’ one. All good fun.
dhutch said:
I also dont know, but I would expect the quality and finish of the commercially produced it item is sufficient and consistent, but more economically done than the example here.
I was given the pre-machined kit as a leaving present by my former employer. Following this thread, I do feel that kit is somewhat of a cheat 
Step drills arrived today:
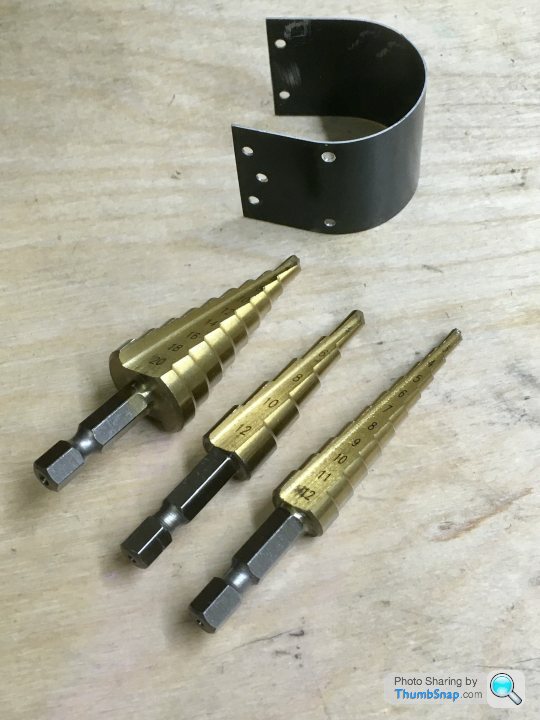
I used some parallels to extend the jaws upwards, and put masking tape on the surfaces to give some extra grip, then re-aligned the pilot holes:
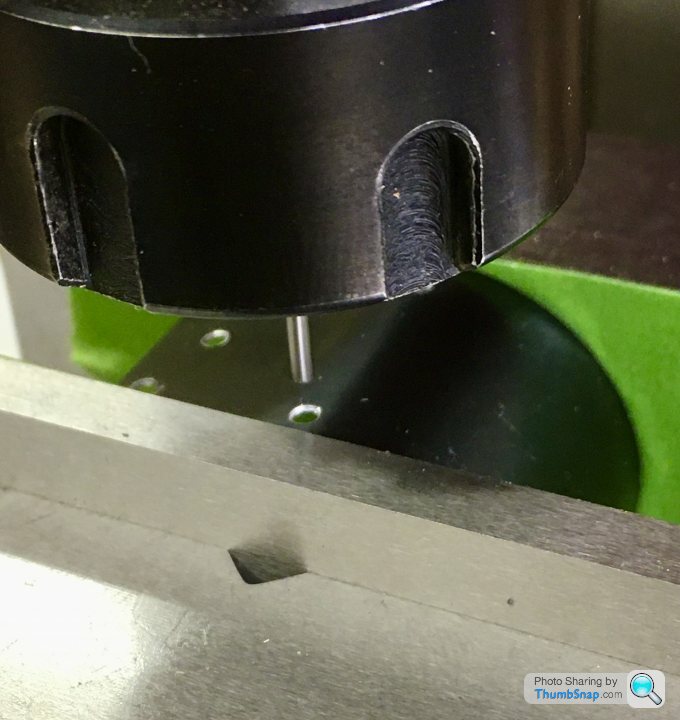
The drain cock holes were less than 1mm from the edge, but the drills worked really well:
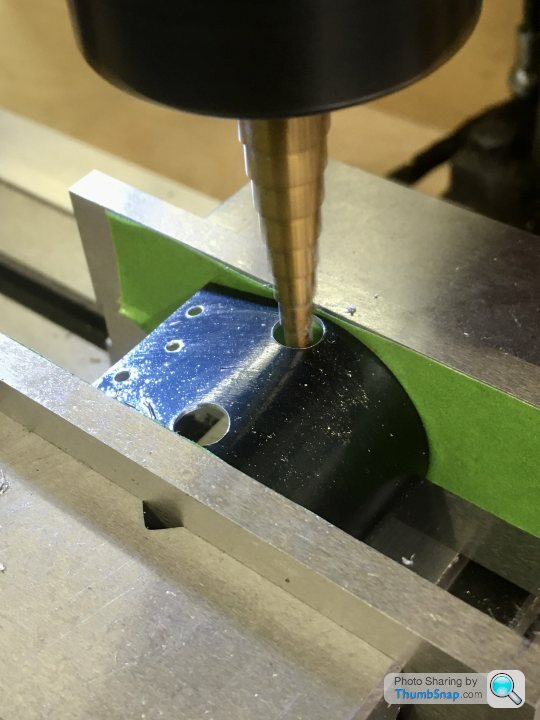
Exhaust hole wasn’t a problem:
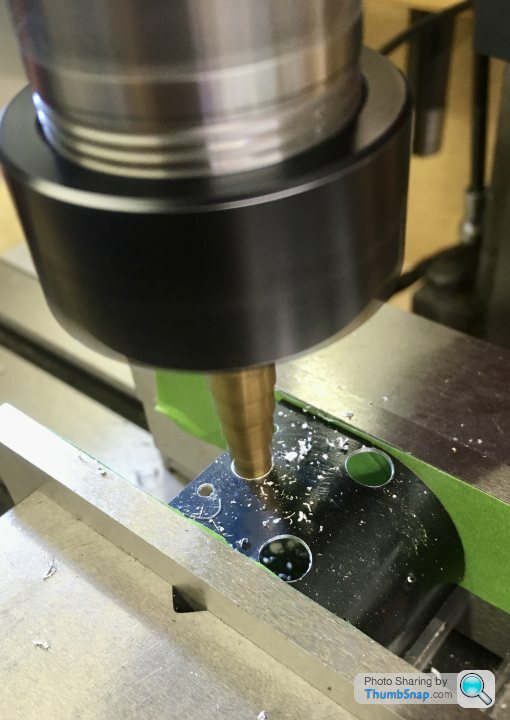
I ended up spraying it satin black, then cleaned up the edges with wet & dry:
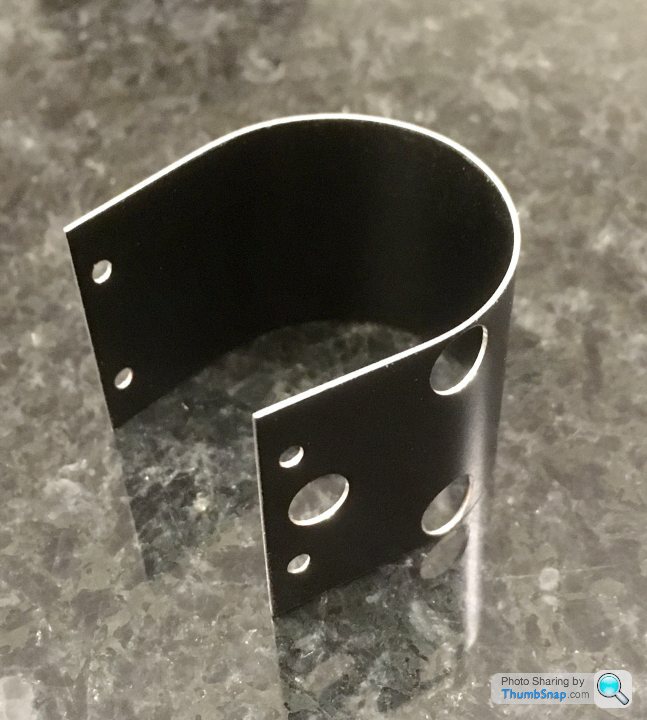
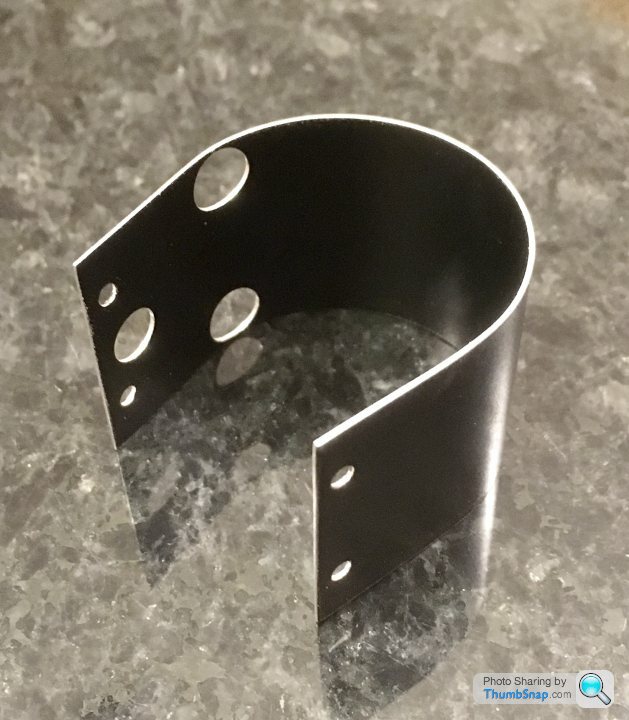
So final assembly and testing next.
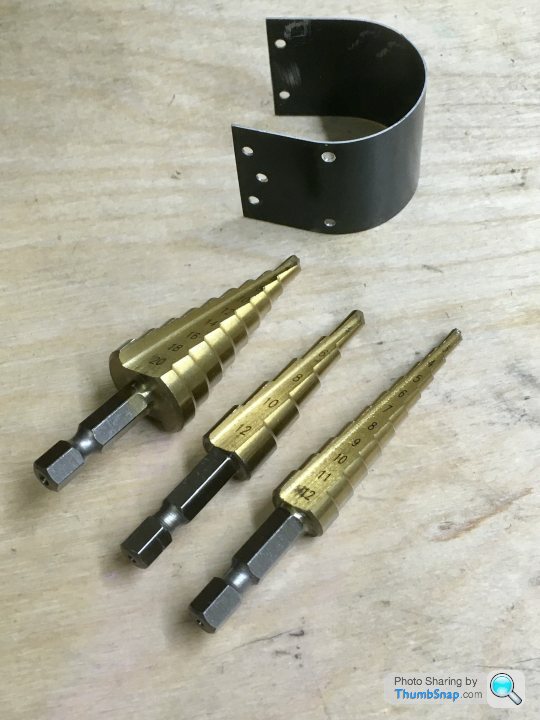
I used some parallels to extend the jaws upwards, and put masking tape on the surfaces to give some extra grip, then re-aligned the pilot holes:
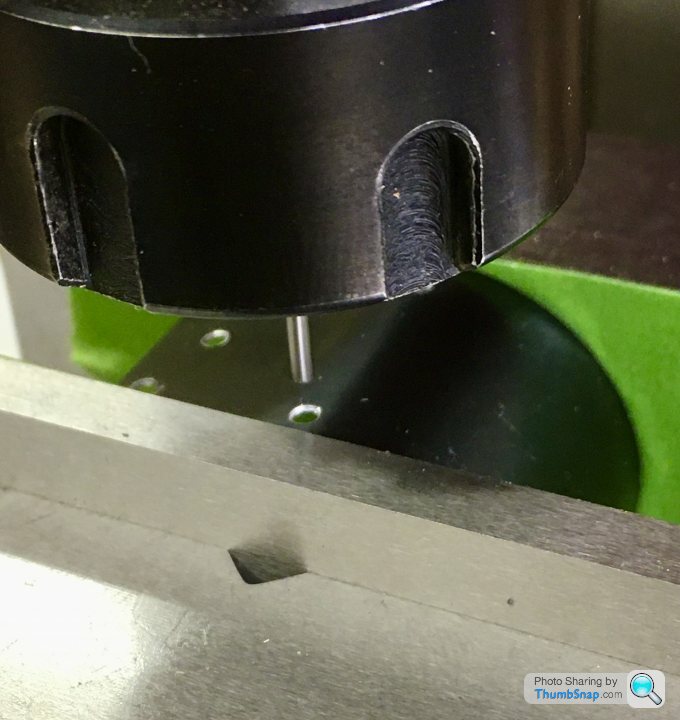
The drain cock holes were less than 1mm from the edge, but the drills worked really well:
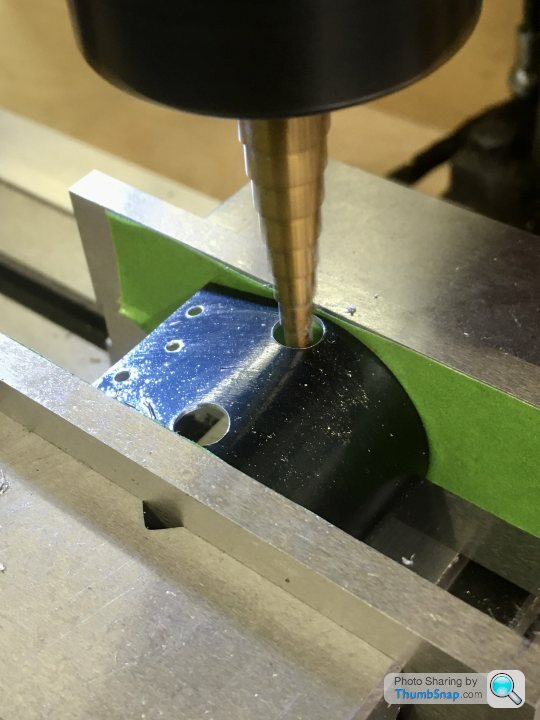
Exhaust hole wasn’t a problem:
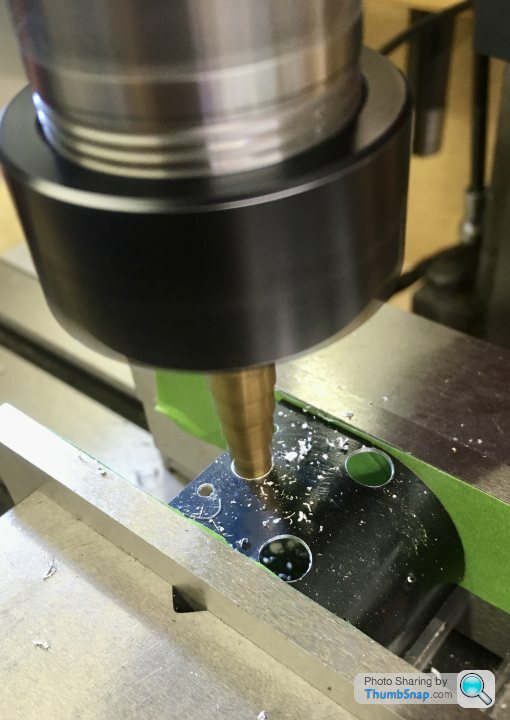
I ended up spraying it satin black, then cleaned up the edges with wet & dry:
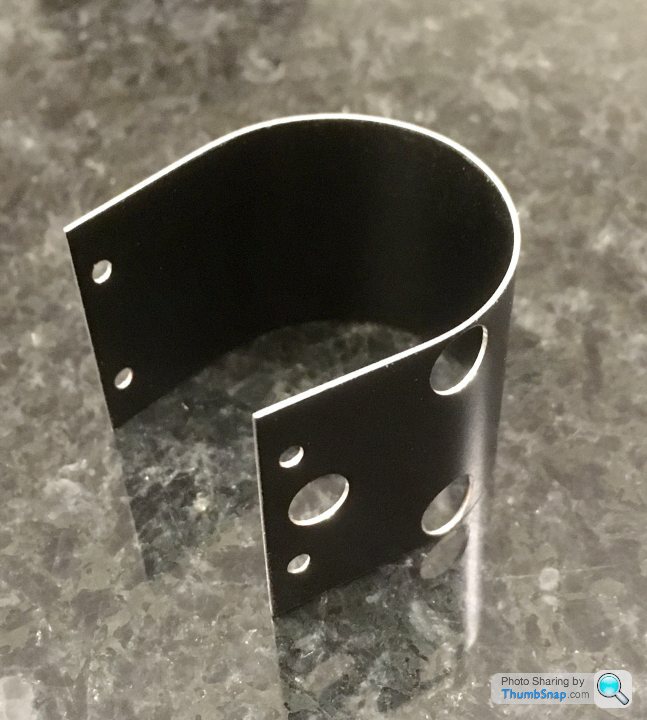
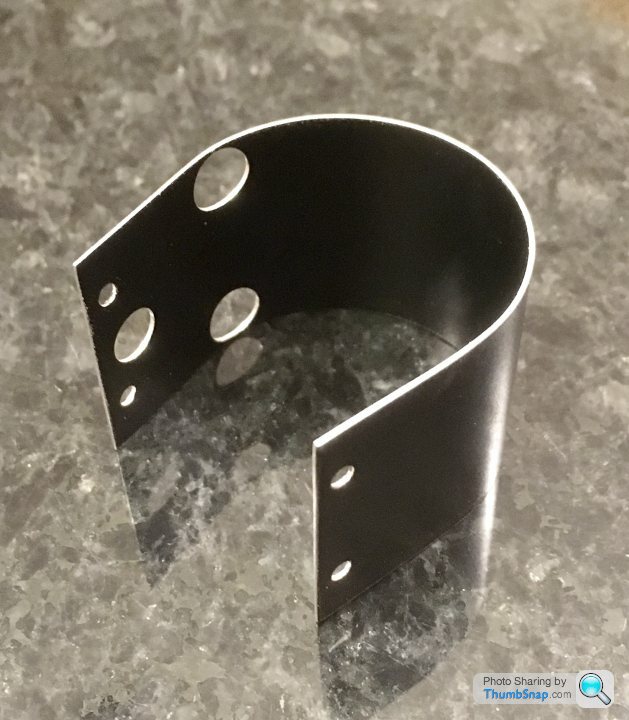
So final assembly and testing next.
dhutch said:
A work of art.
Thanks - must say I'm happy with that because I dodged a couple of bullets with the cheapo step drills and the holes ending up so close to the edge of the plate. I can't even rememebr if I accounted for the clearance holes when I machined the cylinder casting. Next time I'd make them 1mm further in board.Here’s a video of it running for the first time. Should work if you click on it:
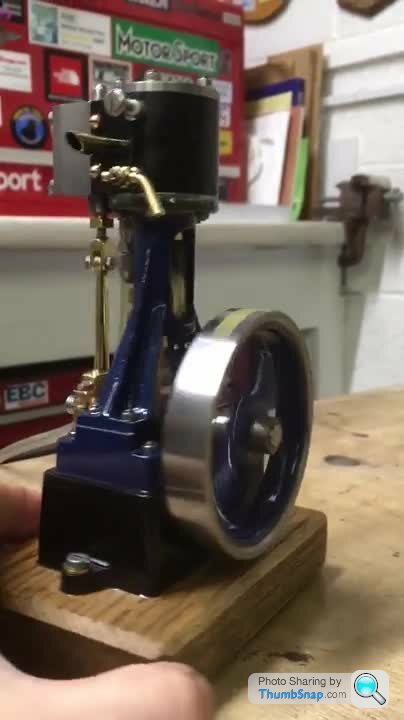
I sheared off the top drain cock on fitting - I didn’t realise how fragile they were (or it was already damaged).
I’ll link to my son’s YouTube channel with some better quality video at some point. In the meantime, thanks for looking, and thanks for the advice all. About five months of work - almost to the day. I’ve enjoyed every minute, and I’m very pleased with the result. Cheers!
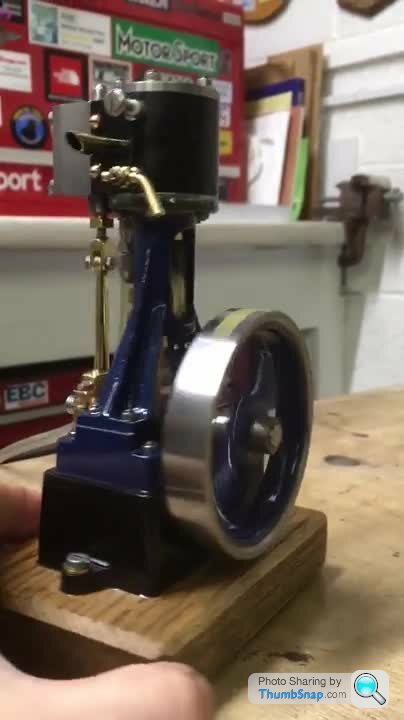
I sheared off the top drain cock on fitting - I didn’t realise how fragile they were (or it was already damaged).
I’ll link to my son’s YouTube channel with some better quality video at some point. In the meantime, thanks for looking, and thanks for the advice all. About five months of work - almost to the day. I’ve enjoyed every minute, and I’m very pleased with the result. Cheers!
Gassing Station | Scale Models | Top of Page | What's New | My Stuff