Stuart Twin Victoria (Princess Royal) Mill Engine
Discussion
Temporarily clamped the bosses to the castings, and drilled the 7BA clearance holes using the DROs:
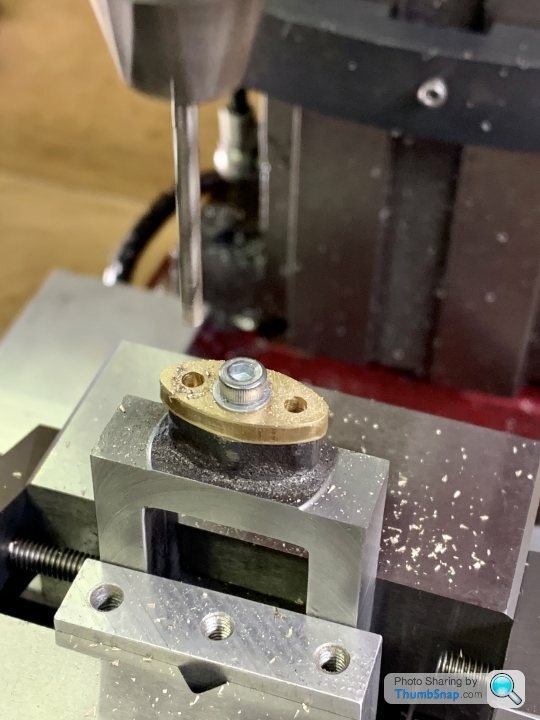
Then tapped the stud holes:
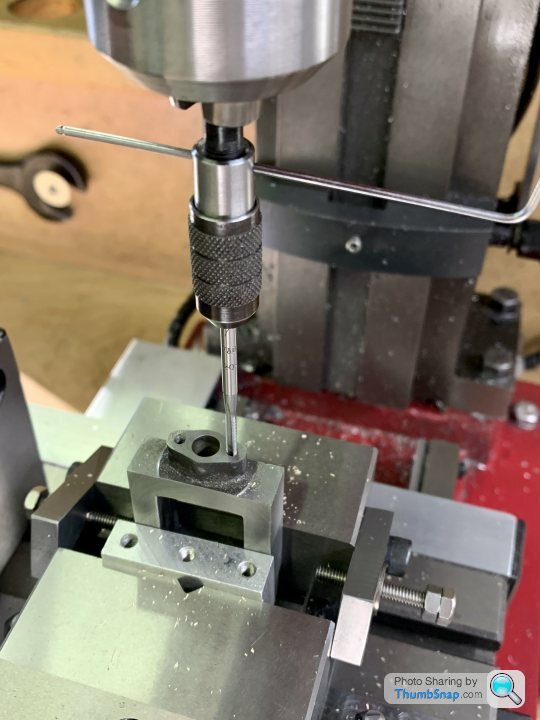
Then fixed them using 7BA csk screws ready for machining, and centered the vice on the R/T:
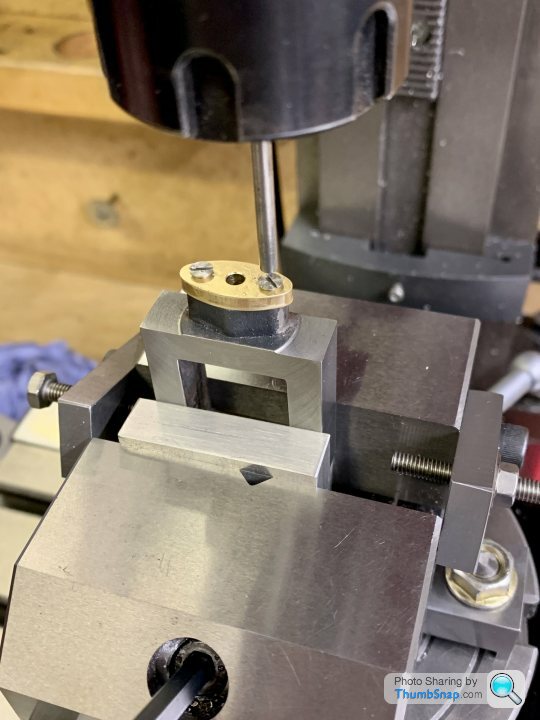
I’d previously made this adjustable fixture for the vice so I could slide the chest side to side to get the right offsets for centering on the rotary table for the mid and end radii:
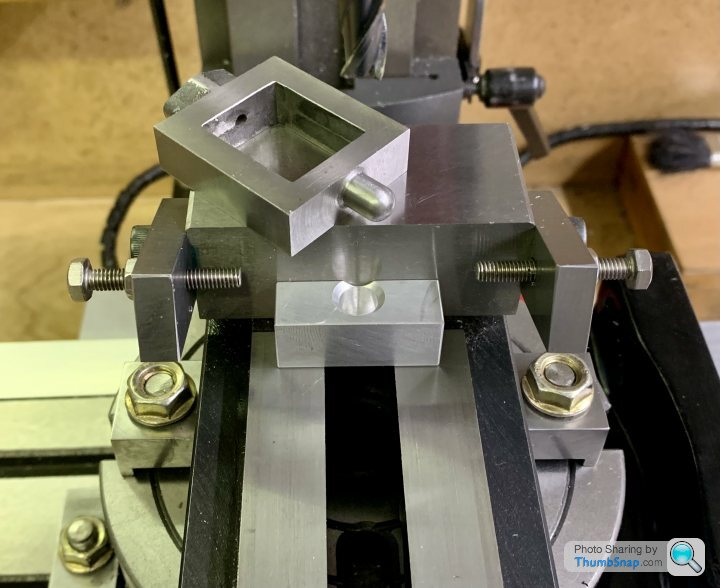
Then, after much adjustment, centering and angle calculation, made a start on milling the profile while periodically moving in x, then rotation in z, at gradually increasing depts of cut:
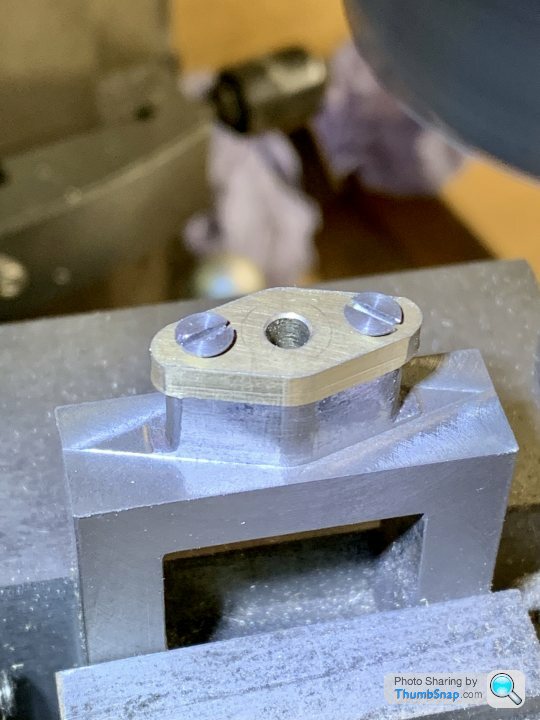
Then re-centered on each end, using the vice stops, and rotated the table to give the radii:
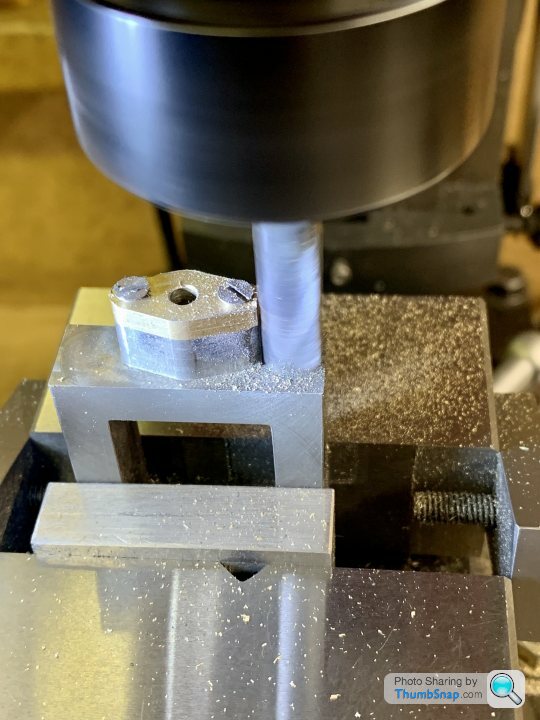
Turned out OK for a first attempt:
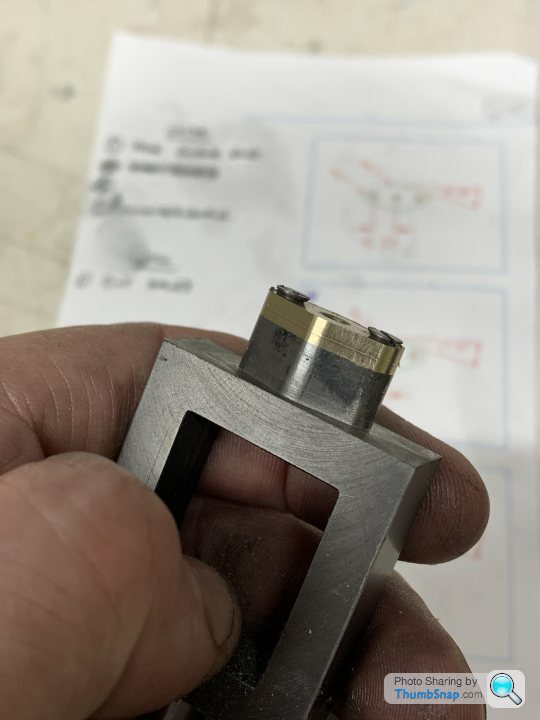
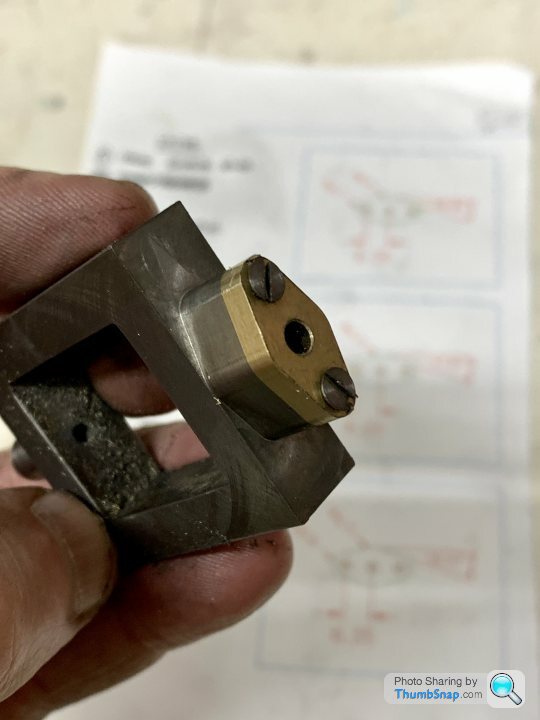
Before and after:

Needs some flatting of the machining marks. Not a big deal because they will be painted eventually:
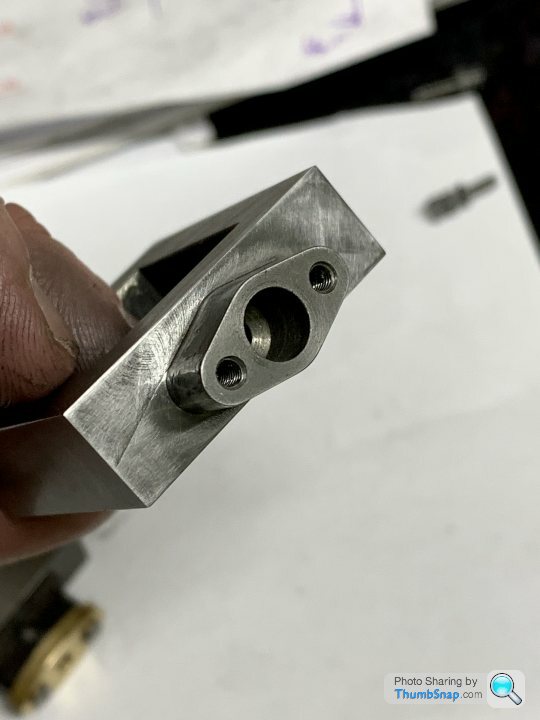
Now for the other one…
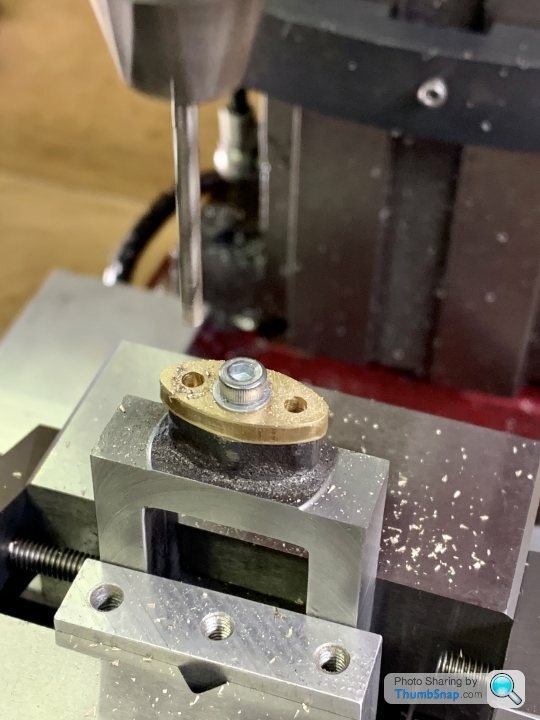
Then tapped the stud holes:
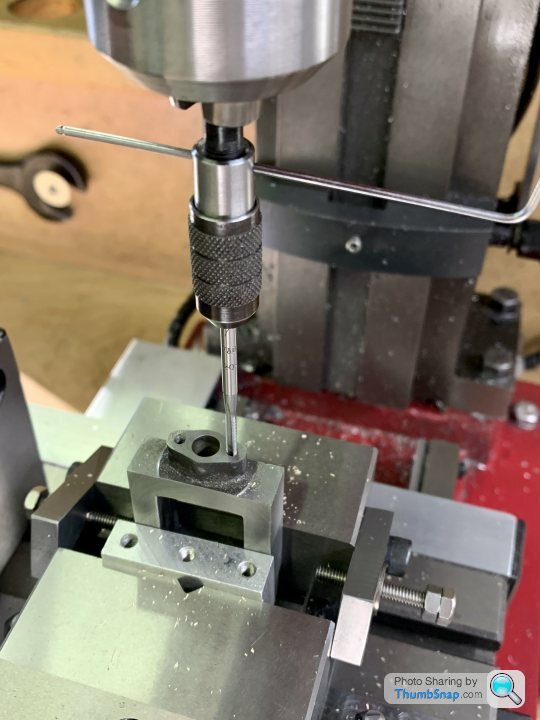
Then fixed them using 7BA csk screws ready for machining, and centered the vice on the R/T:
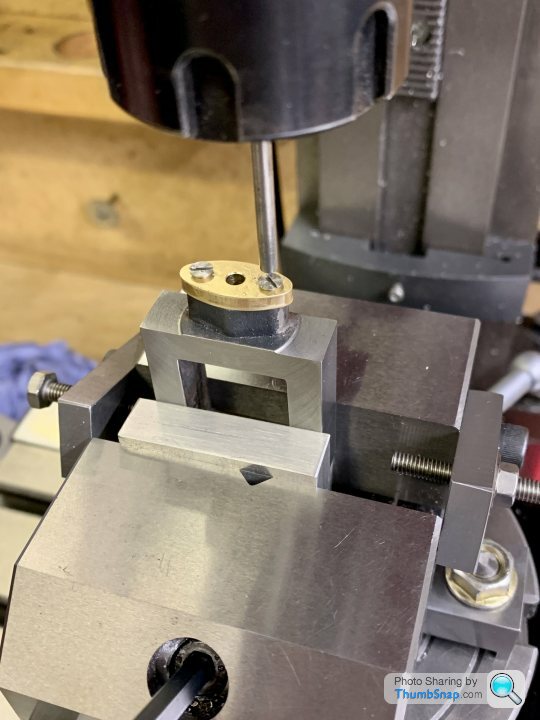
I’d previously made this adjustable fixture for the vice so I could slide the chest side to side to get the right offsets for centering on the rotary table for the mid and end radii:
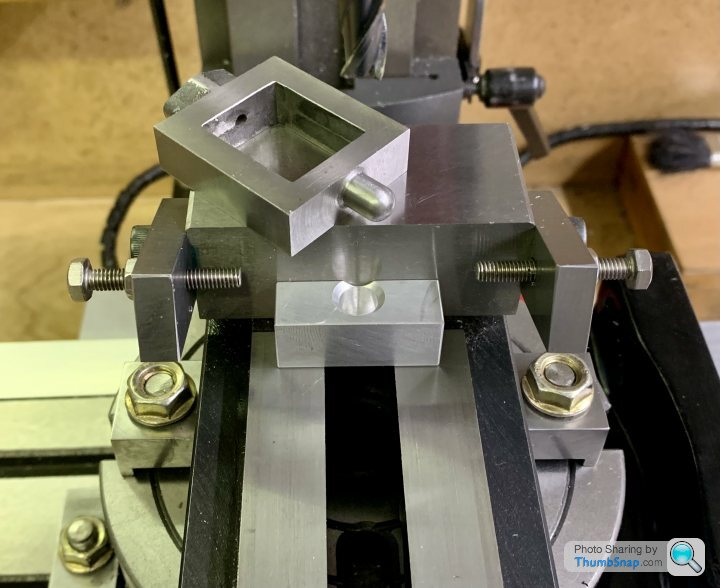
Then, after much adjustment, centering and angle calculation, made a start on milling the profile while periodically moving in x, then rotation in z, at gradually increasing depts of cut:
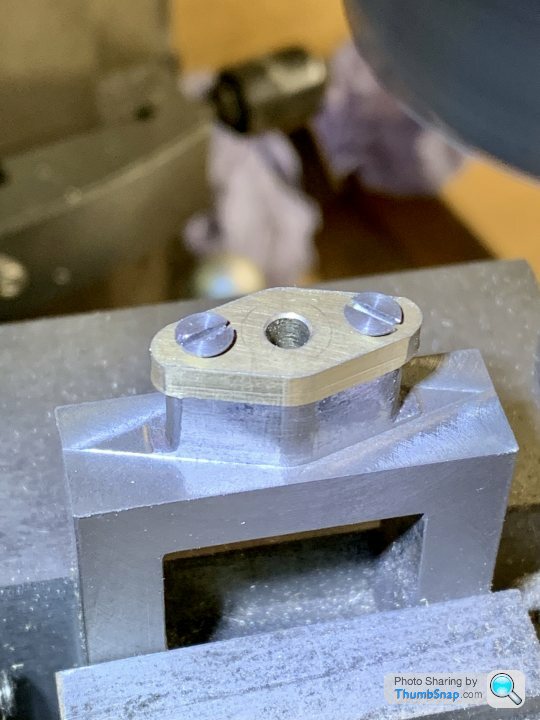
Then re-centered on each end, using the vice stops, and rotated the table to give the radii:
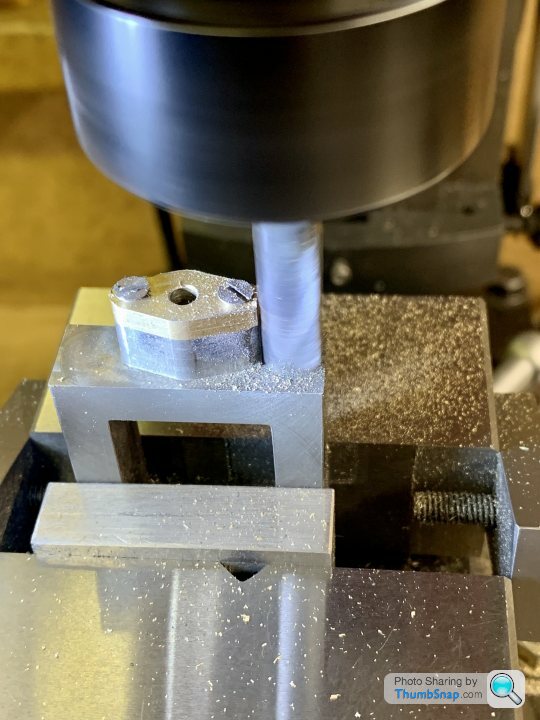
Turned out OK for a first attempt:
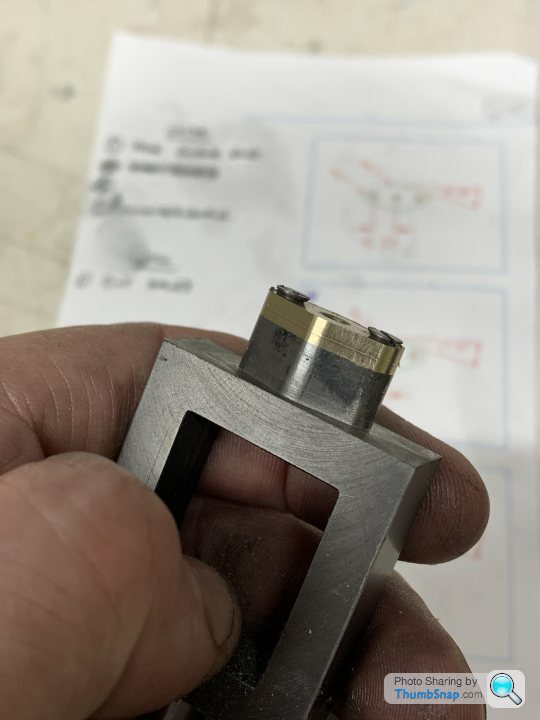
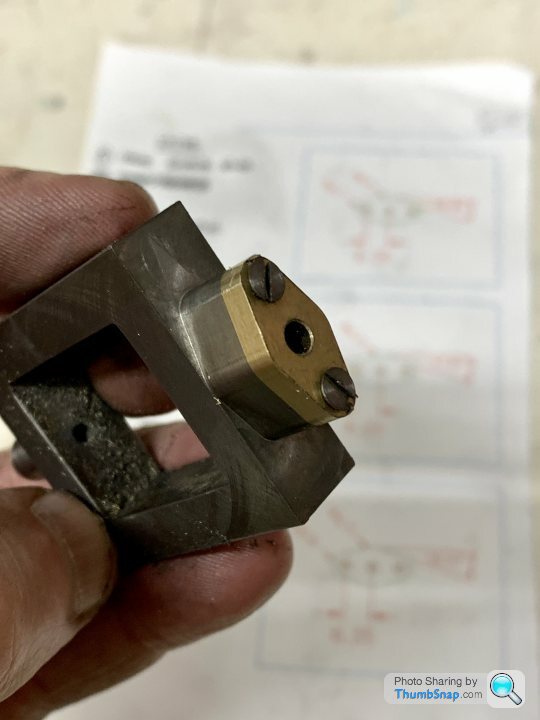
Before and after:

Needs some flatting of the machining marks. Not a big deal because they will be painted eventually:
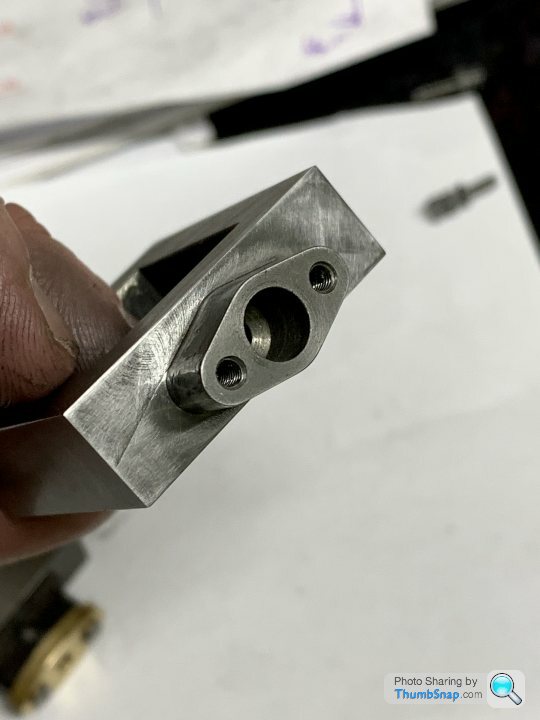
Now for the other one…
Got the other side done this morning:
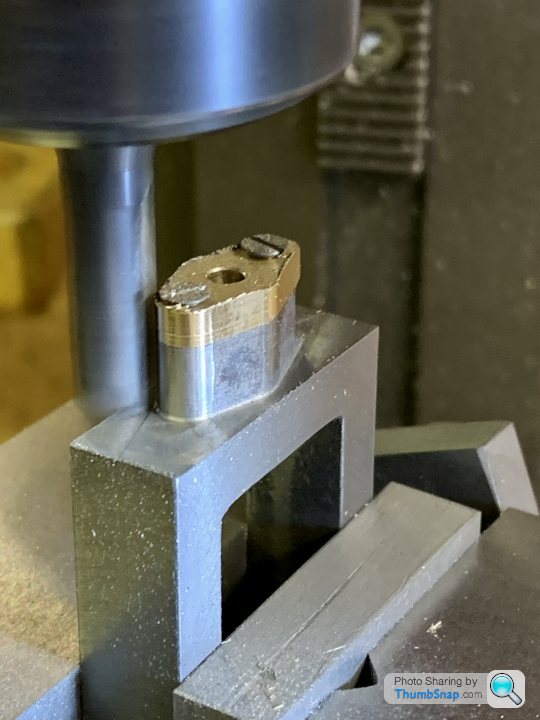
I was given a set of small files, so used them to get rid of the larger machining marks. I found using a flat one, bowed very slightly convex was good for dealing with the surfaces away from the edges:
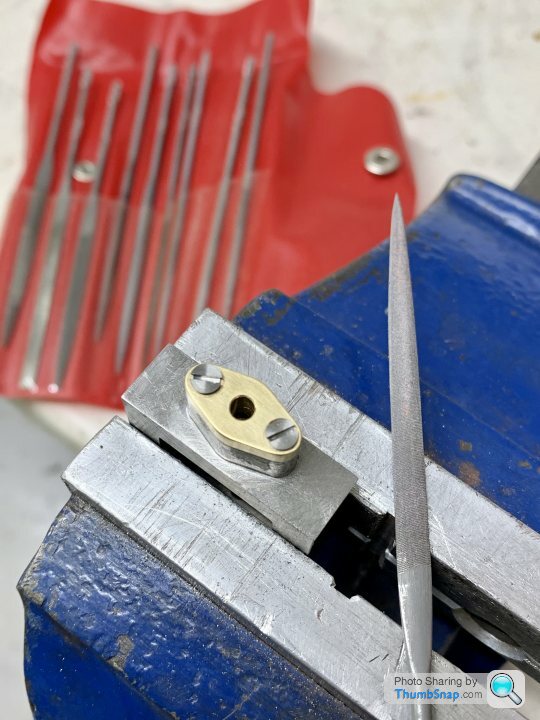
I do t have any Emery cloth, but used some #250 and #400 wet and dry lubricated with WD40. I would have gone further if they were to be left as bare metal, but I think as they are will give a good key for the primer:
This is the result:
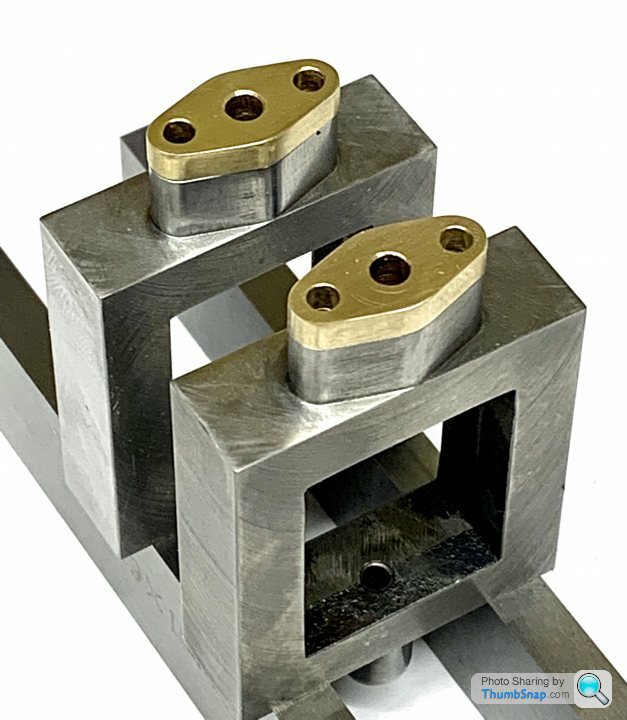
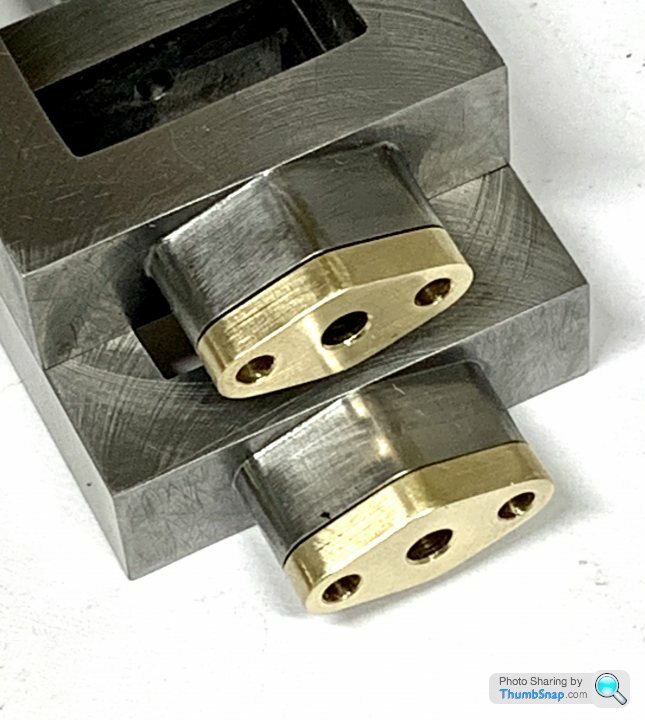
I aimed to remove the absolute minimum from the castings, and the result was that a few places were missed:
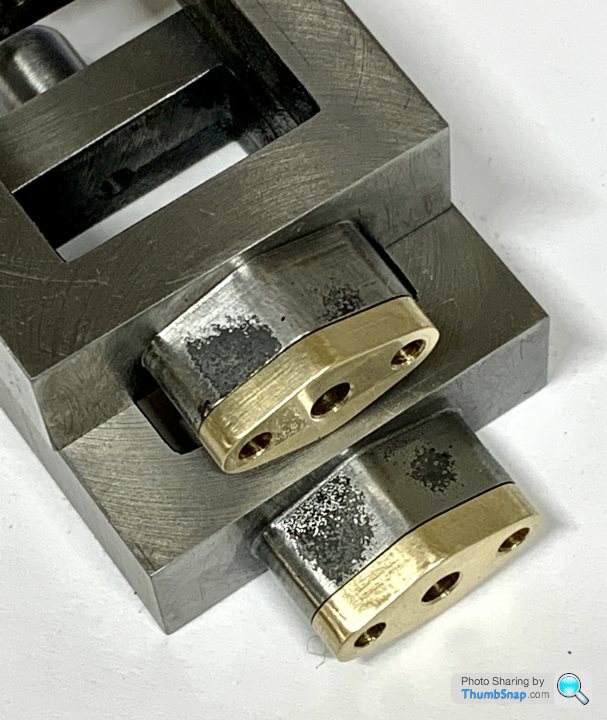
I opted to leave them because a) I think they are the undersides, and won’t be visible once assembled, and b) Once painted it won’t be obvious anyway.
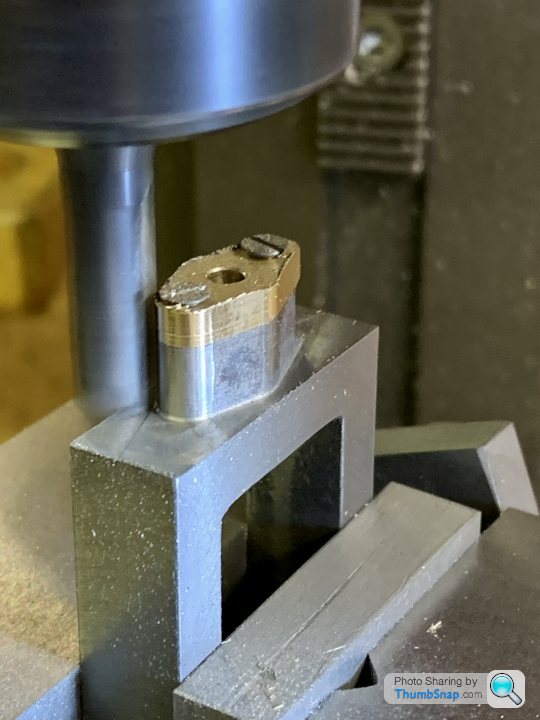
I was given a set of small files, so used them to get rid of the larger machining marks. I found using a flat one, bowed very slightly convex was good for dealing with the surfaces away from the edges:
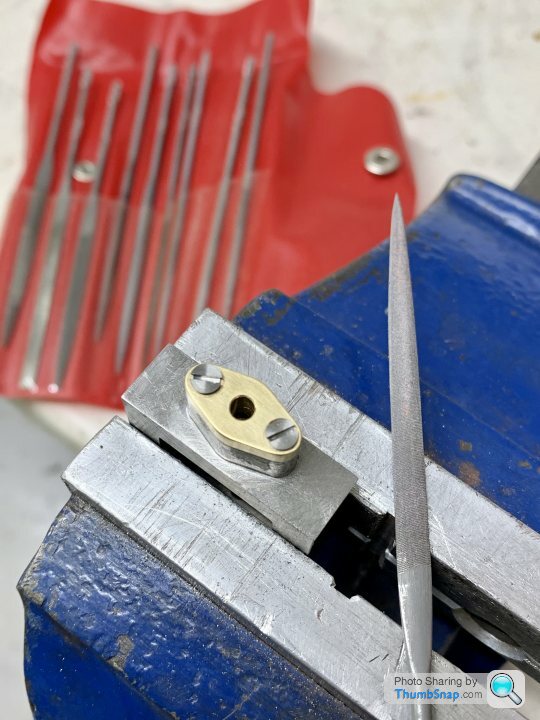
I do t have any Emery cloth, but used some #250 and #400 wet and dry lubricated with WD40. I would have gone further if they were to be left as bare metal, but I think as they are will give a good key for the primer:
This is the result:
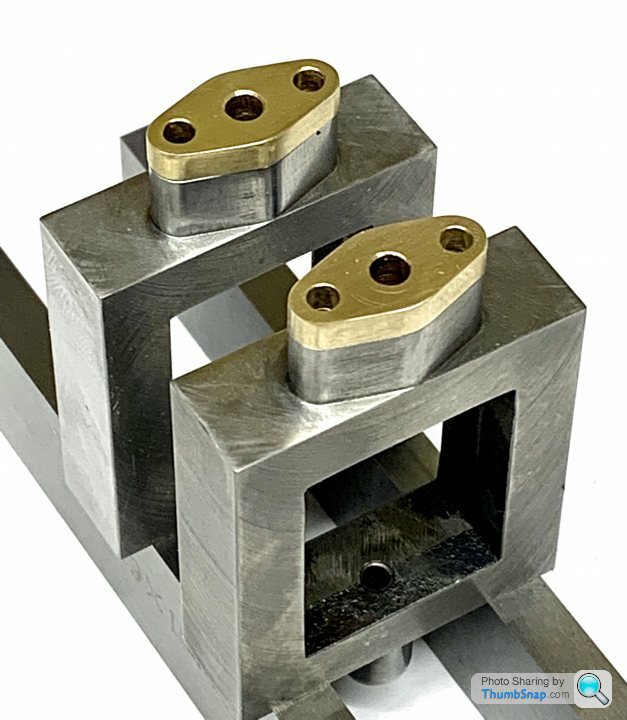
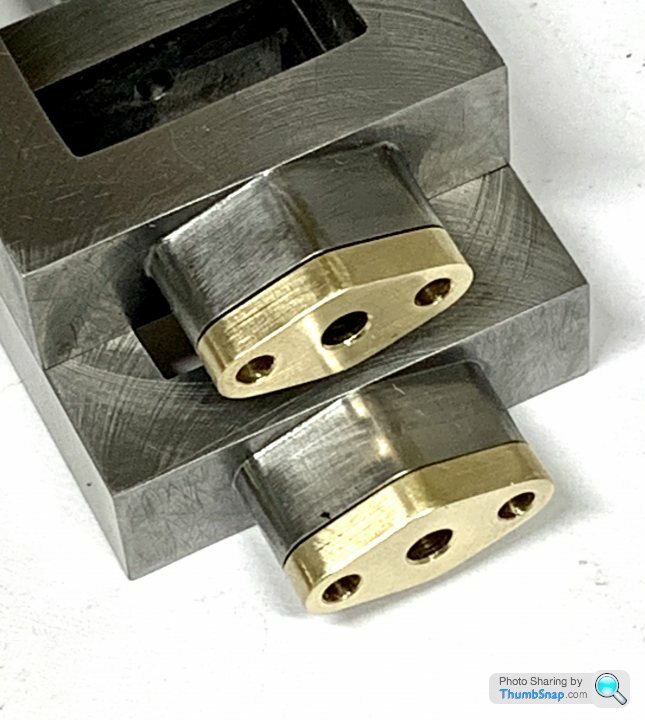
I aimed to remove the absolute minimum from the castings, and the result was that a few places were missed:
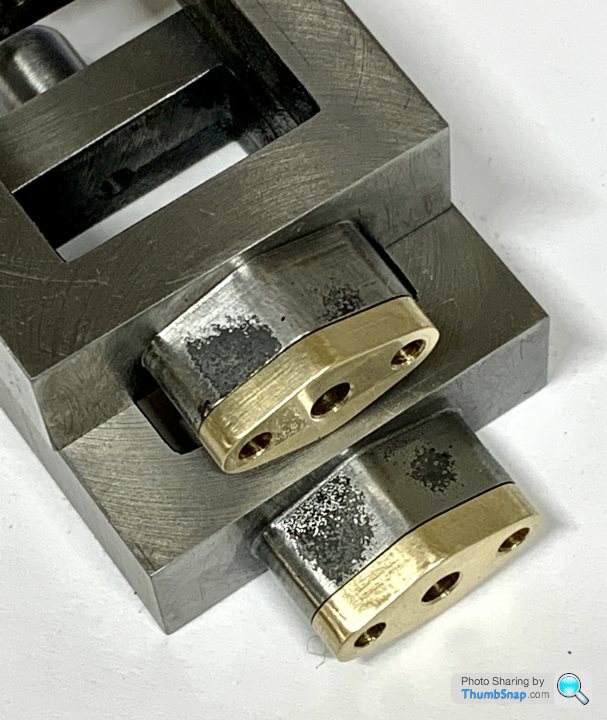
I opted to leave them because a) I think they are the undersides, and won’t be visible once assembled, and b) Once painted it won’t be obvious anyway.
anonymous said:
[redacted]
I’ve got to live long enough to finish it first…I bought some Traction engine castings recently. I’m the third owner; first owner died, second owner got too old to start the model. The certified boiler for that engine is made to order, and has a two year waiting list. People die before taking delivery, so sometimes they have one for immediate collection.
What a hobby.
I had a go at the cylinder covers this afternoon. I’ve read the article method loads of times, but still couldn’t make head or tail of the descriptions: It says machine the plain cover spigot first, to a good fit to the cylinder, the reason being that it centralises the packing…but there isn’t any packing on that cover.
It then says make the spigot on the gland cover ends (the ones with the packing) a slack fit. It also says to machine the spigot diameter after facing, to ensure concentricity. Surely concentricity doesn’t depend on the face being true, plus if it’s slack, why is it important?
I was left wondering why in those cases bother with either spigot at all since one has nothing to centre, and the other is a slack fit anyway.
In the end I just went with what seemed logical. I assume when the article was written, the covers didn’t come with cast tails on the back, so I used those to mount in the chuck. I first faced the gland bosses, centre drilled them as best I could on the mill after marking with the verniers, and set up true in the 4 jaw. Then turned the bolt faces and re-faced the gland bosses to the correct depths:
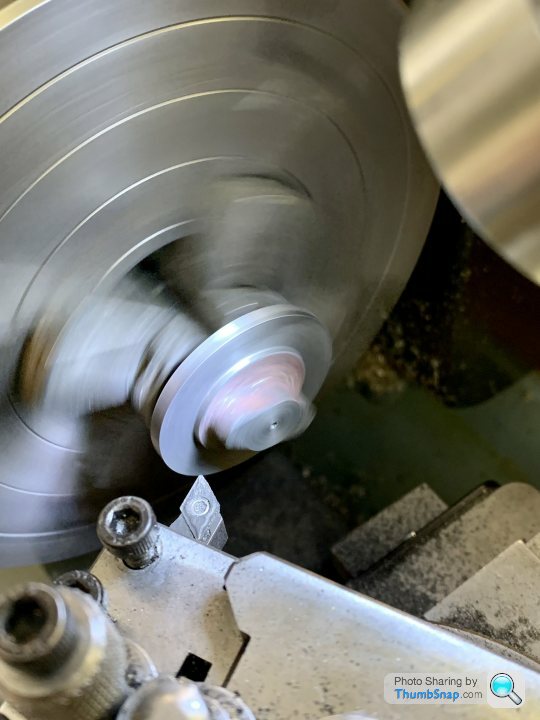
Then drilled the piston rod and packing holes:
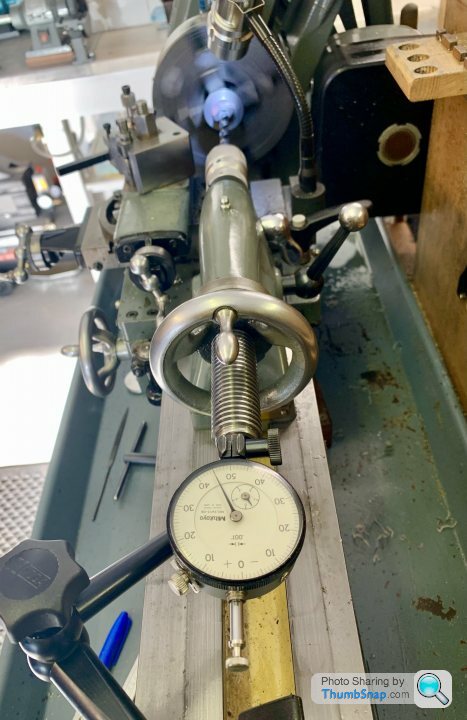
The 10V piston hole was reamed, but it says not to bother for this one. Which seems logical since it’s the piston and cross head that seem to define the rod position. Adding a third fit seems pointless, especially when the packing will centralise the rod. Anyway, that got me here:
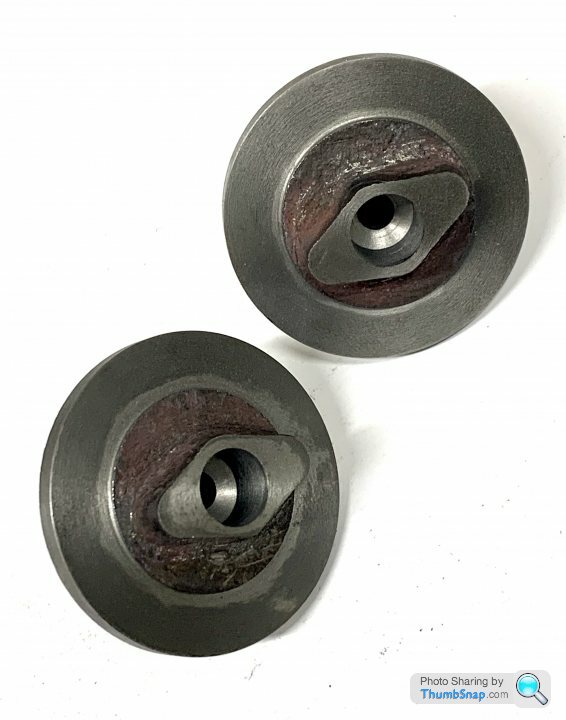
Then sawed off the tails:
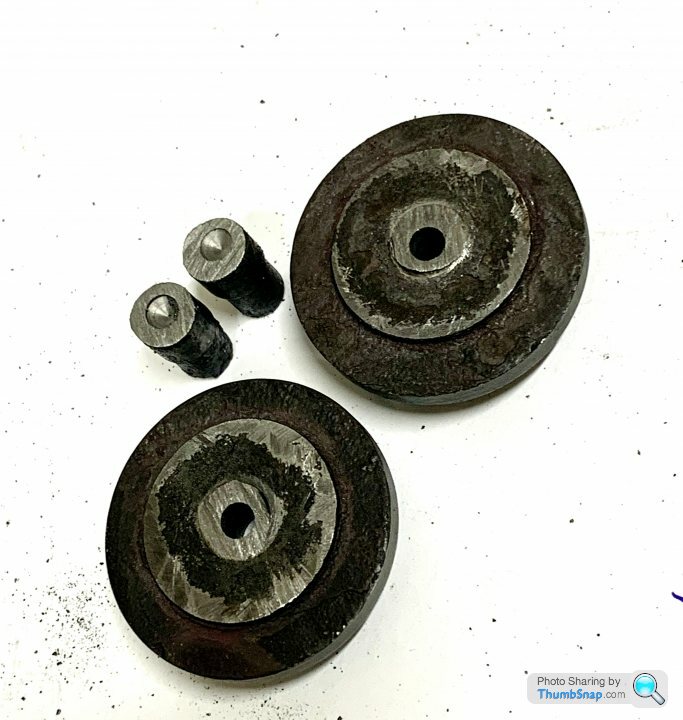
Made a mandrel as per the article:
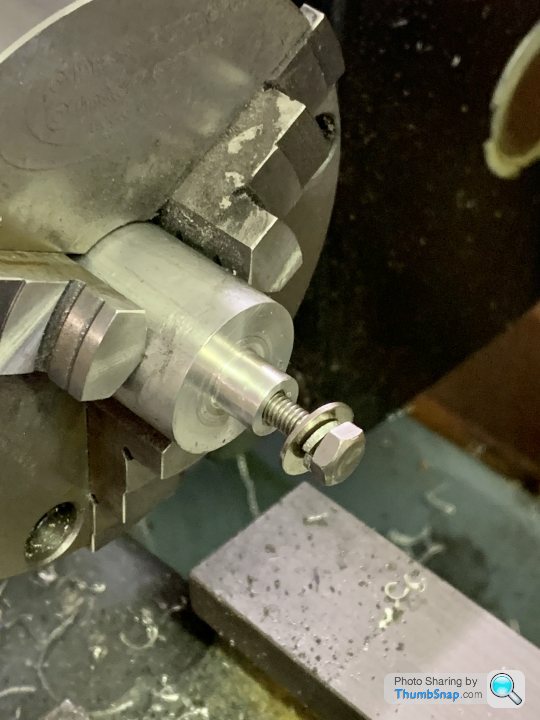
Set up with a dti (both were within 0.002” O/D and 0.001” on the face, so I thought that was ok:
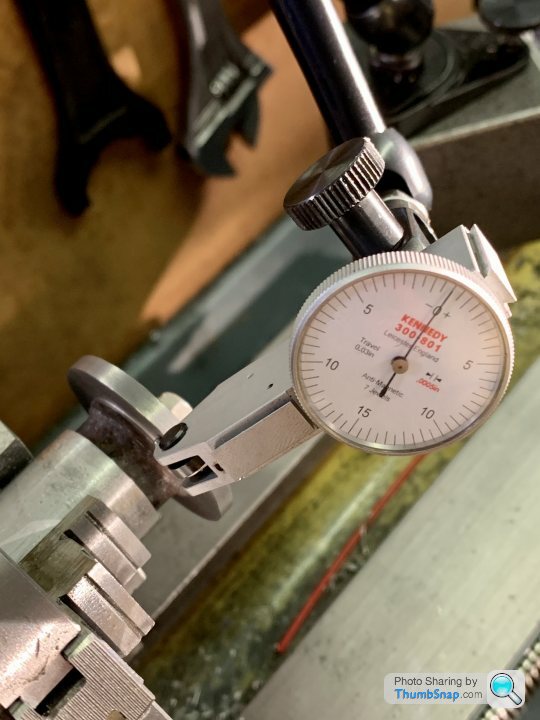
And turned the inside spigots and the flanges to thickness. I made the spigots a good fit to the cylinders. I can slacken them off if I need to I suppose:
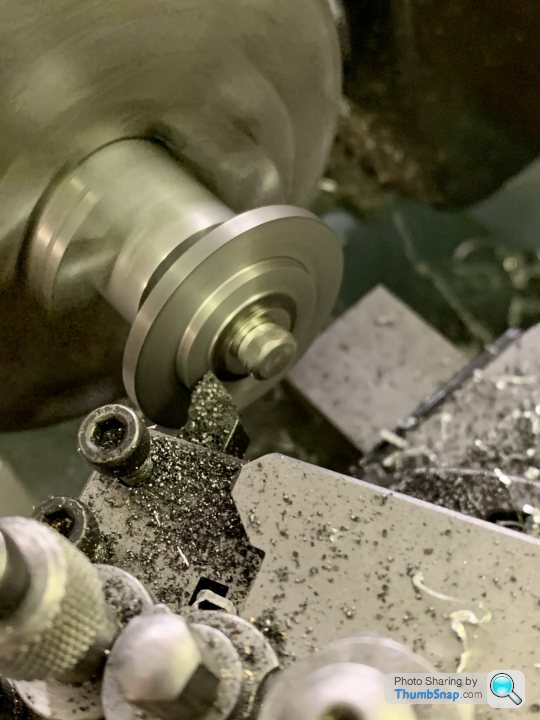
Then finished the spigot faces in the 3 jaw:
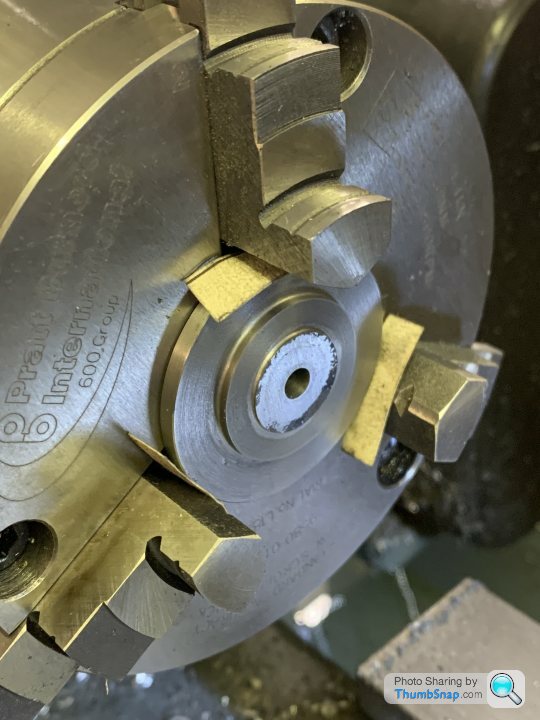
I guess there was better way to do it than this, but it seemed to work ok:
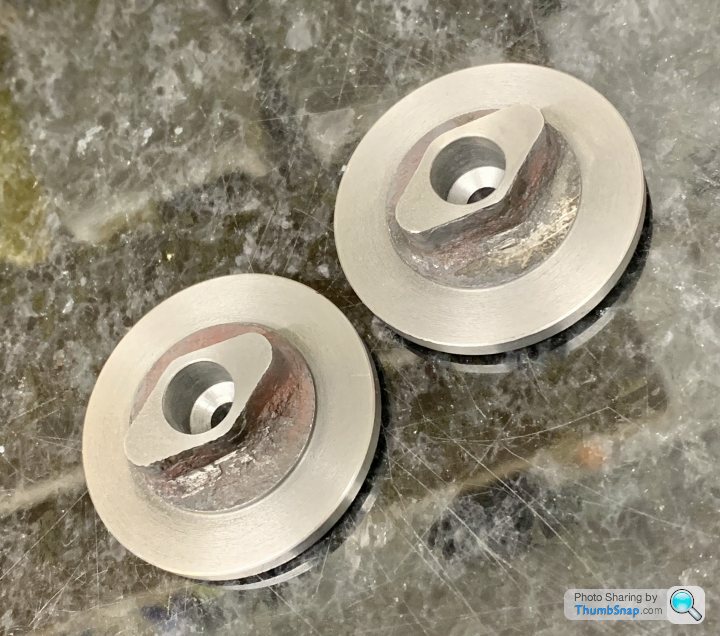
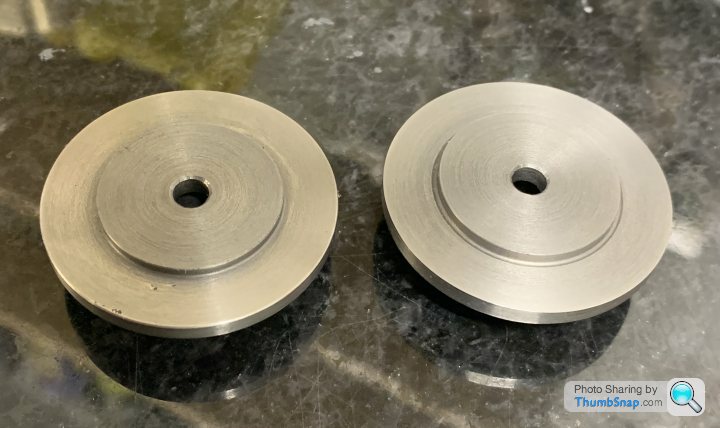
The castings where right on the edge of being big enough for the stated dimensions, in fact there are still a couple of pinholes on one of the gasket faces. The brass extrusion I bought was never going to be big enough to make the glands:
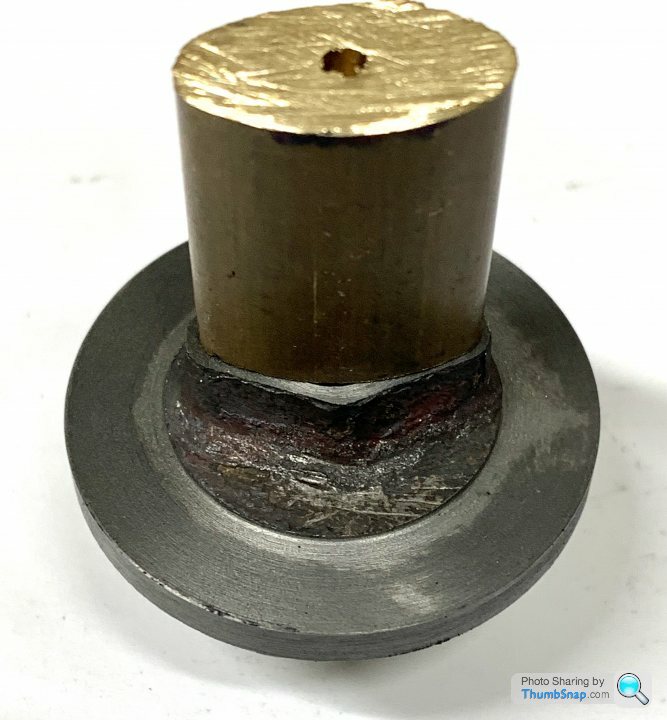
Got plenty spare…
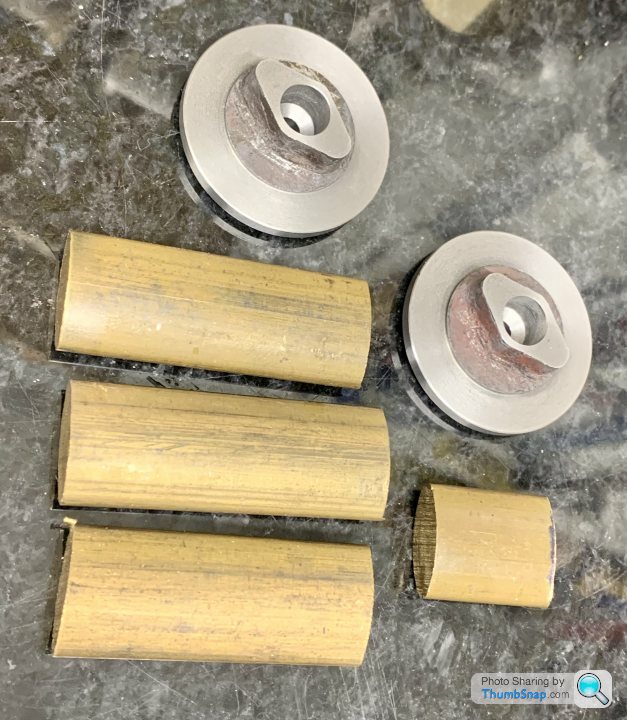
I’ve got some brass bar, so I’ll try to make them from that:
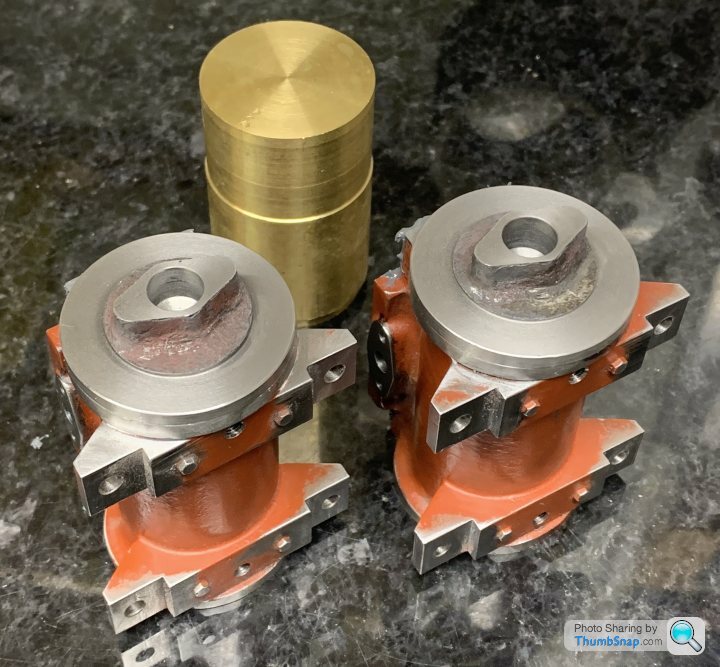
Lessons learned: I should have bored the packing holes rather than drilled them - my smallest boring bar will just fit. Oh well, I think they will be ok.
Next job is to make a mounting block for them for the R/T vice, and get them milled as per the valve blocks. I might put some JB Weld around the bosses - they look very close to being undersized despite everything being pretty central.
It then says make the spigot on the gland cover ends (the ones with the packing) a slack fit. It also says to machine the spigot diameter after facing, to ensure concentricity. Surely concentricity doesn’t depend on the face being true, plus if it’s slack, why is it important?
I was left wondering why in those cases bother with either spigot at all since one has nothing to centre, and the other is a slack fit anyway.
In the end I just went with what seemed logical. I assume when the article was written, the covers didn’t come with cast tails on the back, so I used those to mount in the chuck. I first faced the gland bosses, centre drilled them as best I could on the mill after marking with the verniers, and set up true in the 4 jaw. Then turned the bolt faces and re-faced the gland bosses to the correct depths:
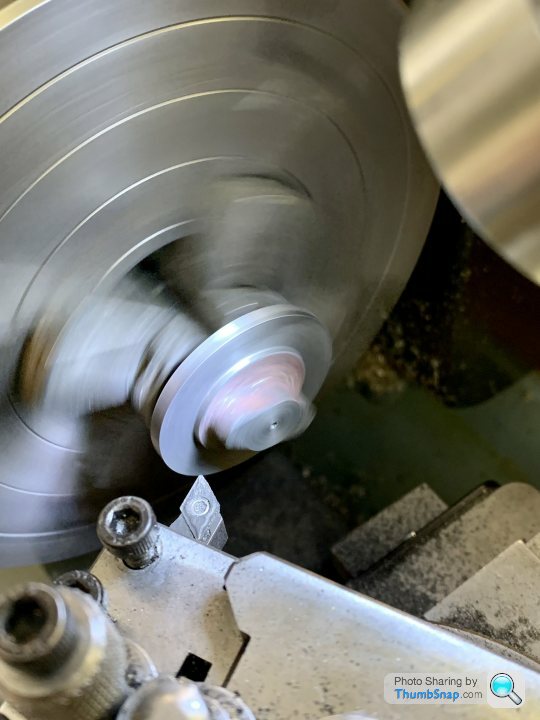
Then drilled the piston rod and packing holes:
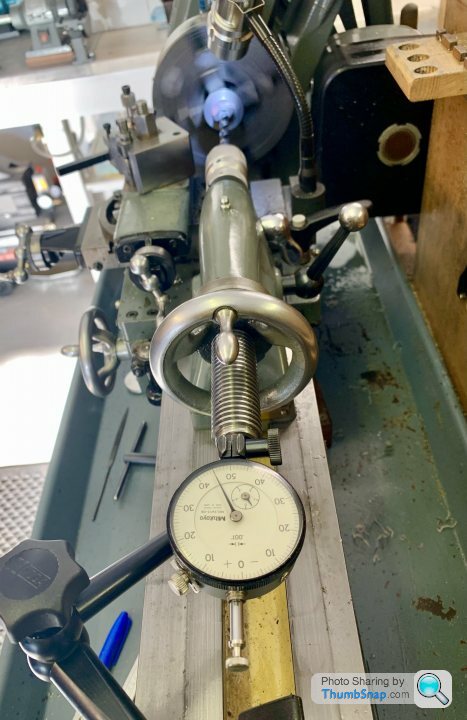
The 10V piston hole was reamed, but it says not to bother for this one. Which seems logical since it’s the piston and cross head that seem to define the rod position. Adding a third fit seems pointless, especially when the packing will centralise the rod. Anyway, that got me here:
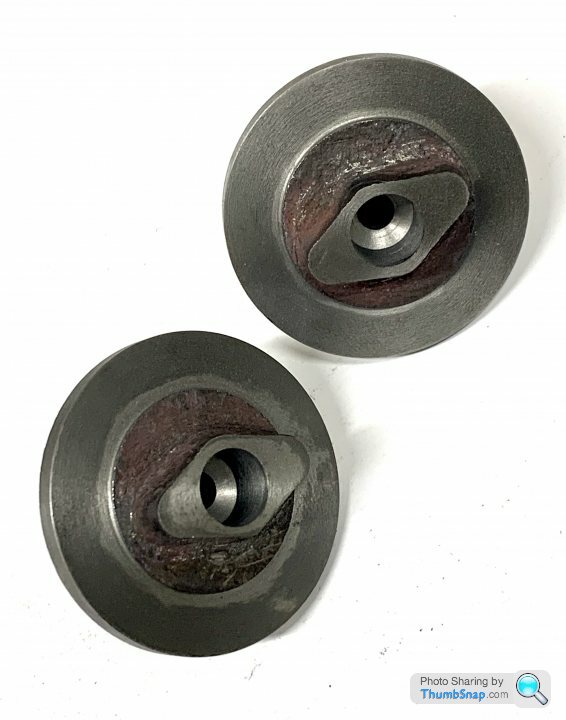
Then sawed off the tails:
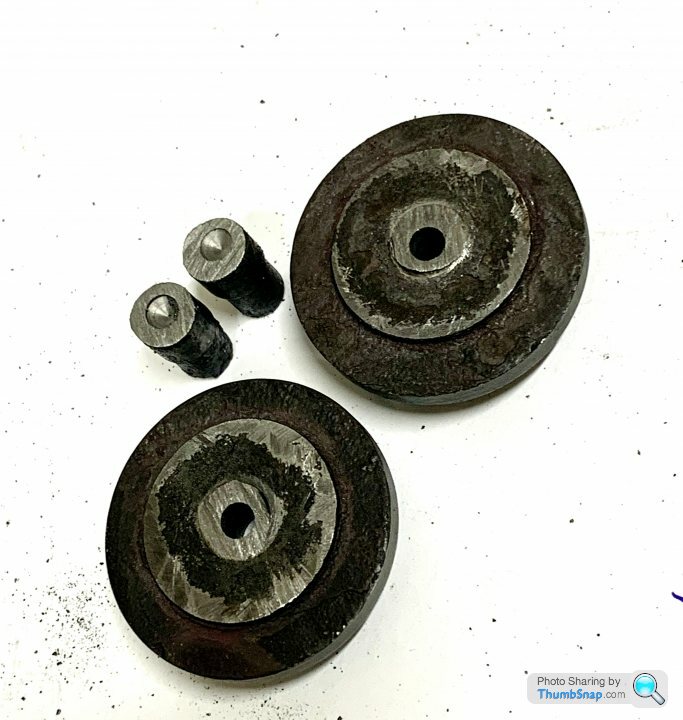
Made a mandrel as per the article:
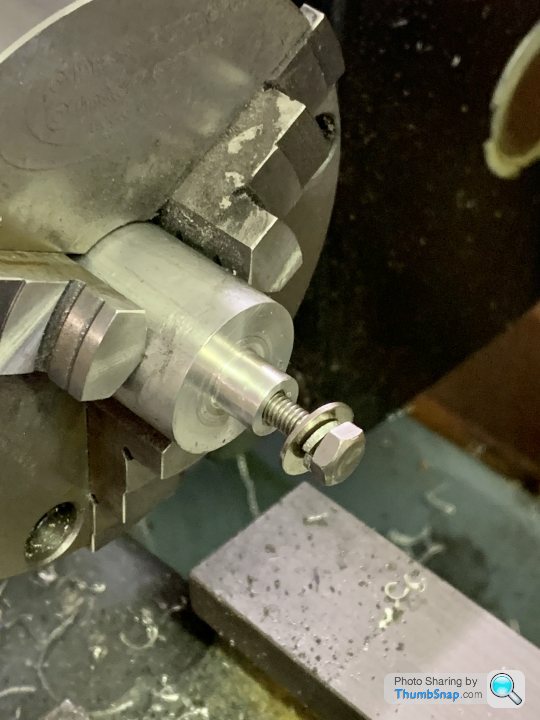
Set up with a dti (both were within 0.002” O/D and 0.001” on the face, so I thought that was ok:
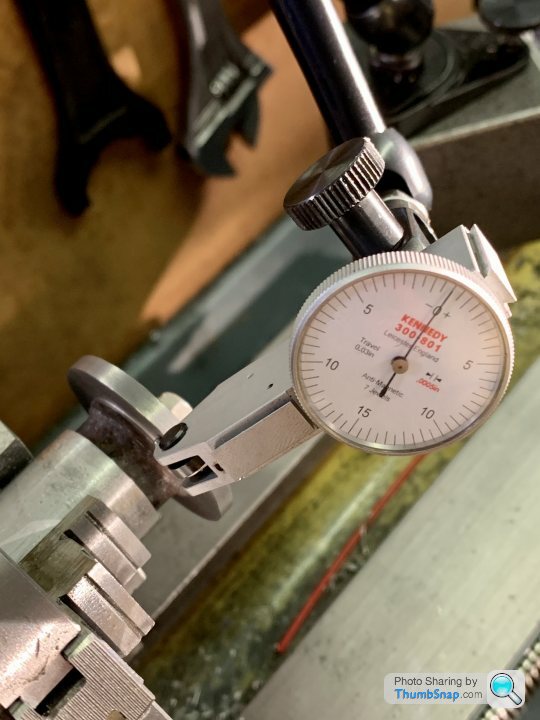
And turned the inside spigots and the flanges to thickness. I made the spigots a good fit to the cylinders. I can slacken them off if I need to I suppose:
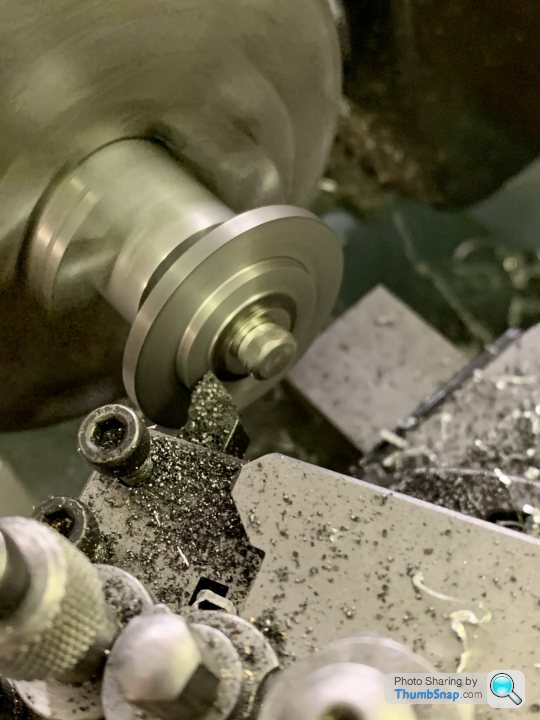
Then finished the spigot faces in the 3 jaw:
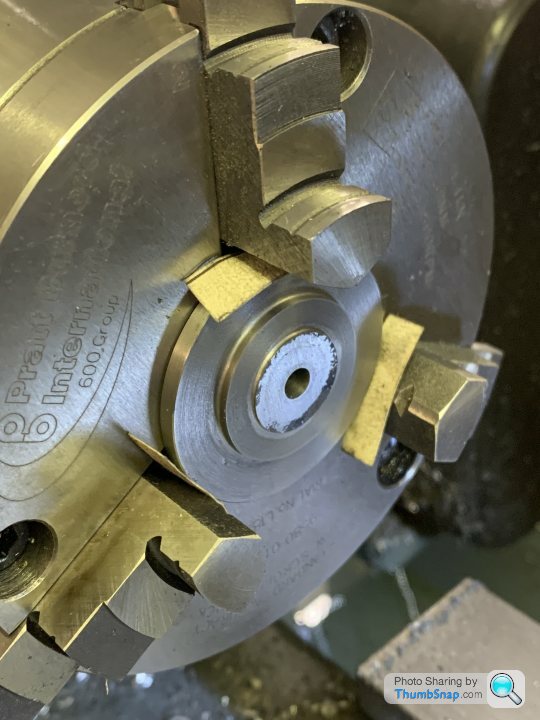
I guess there was better way to do it than this, but it seemed to work ok:
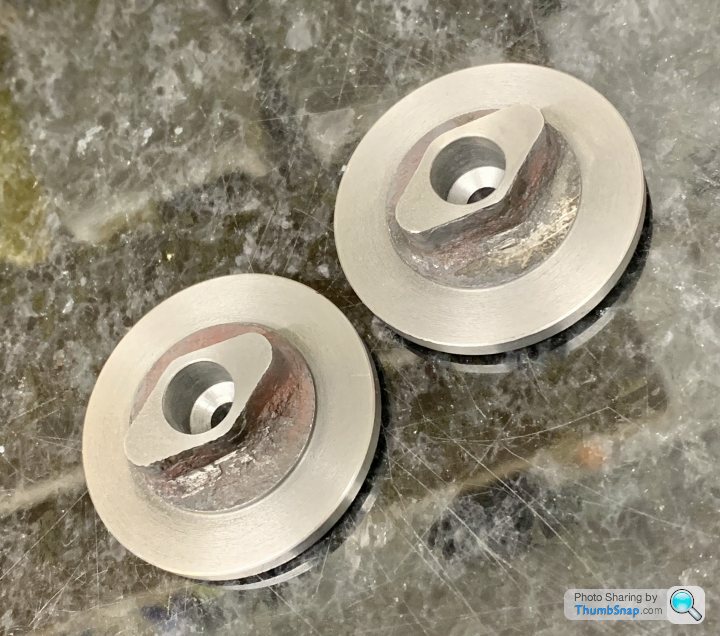
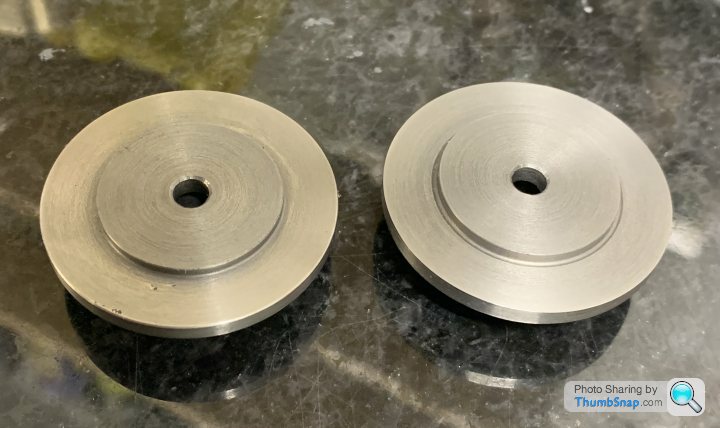
The castings where right on the edge of being big enough for the stated dimensions, in fact there are still a couple of pinholes on one of the gasket faces. The brass extrusion I bought was never going to be big enough to make the glands:
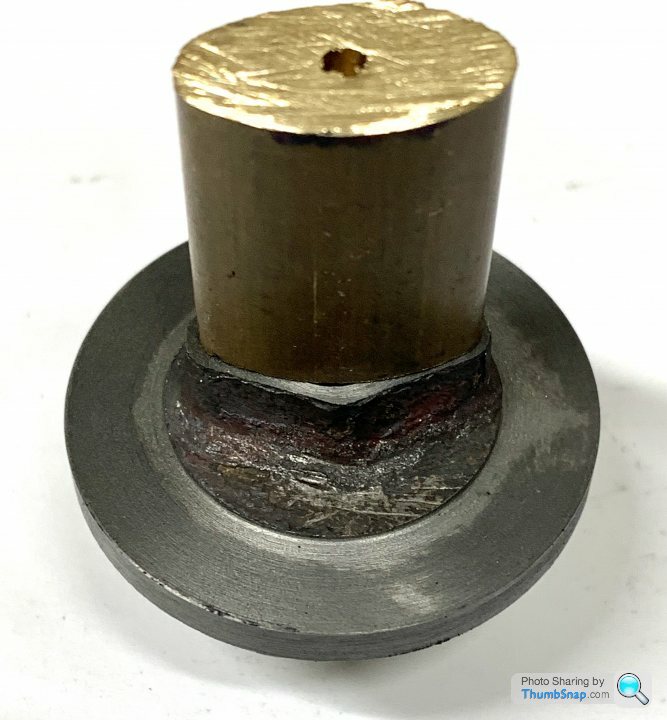
Got plenty spare…
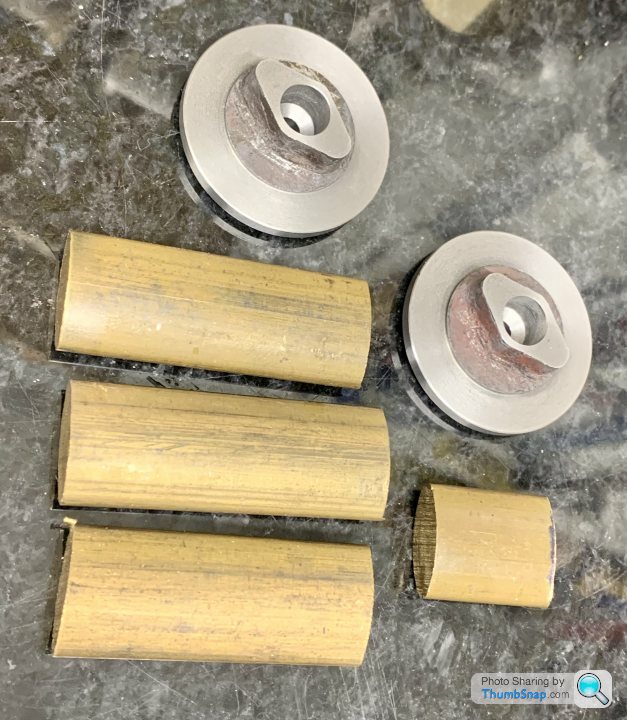
I’ve got some brass bar, so I’ll try to make them from that:
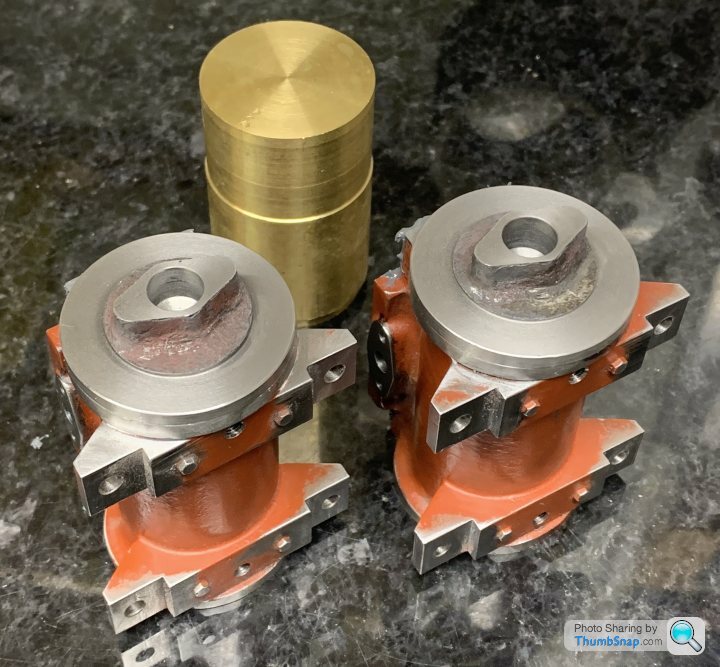
Lessons learned: I should have bored the packing holes rather than drilled them - my smallest boring bar will just fit. Oh well, I think they will be ok.
Next job is to make a mounting block for them for the R/T vice, and get them milled as per the valve blocks. I might put some JB Weld around the bosses - they look very close to being undersized despite everything being pretty central.
In other news, went to the Kelham Island museum this morning (it’s only 30 minutes from home). Parked next to a double flywheel similar to the one on the Twin Victoria. Never seen one before, it looks like it was part of some electrical machine judging by the circumferential details:
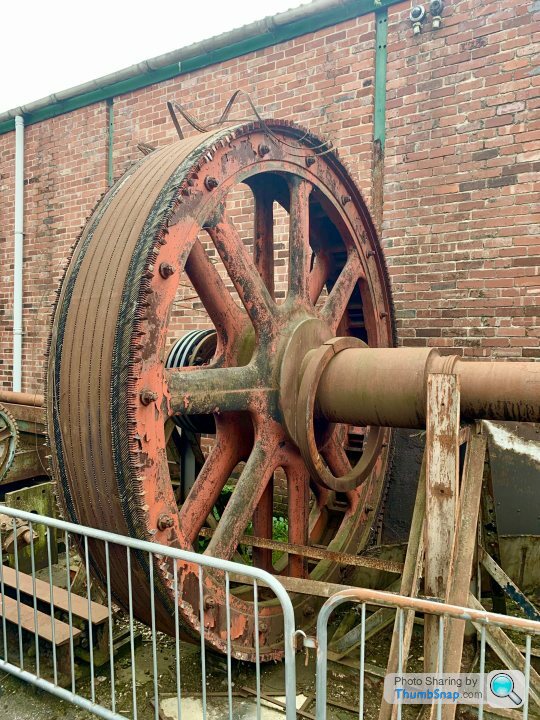
A few other engines:

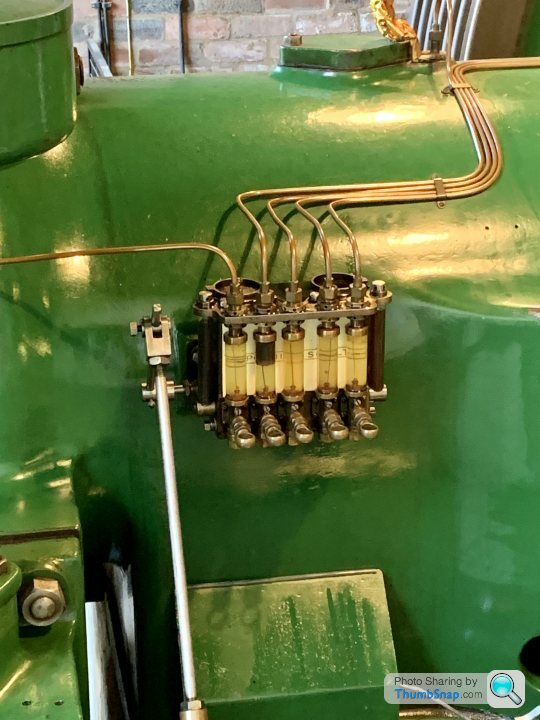
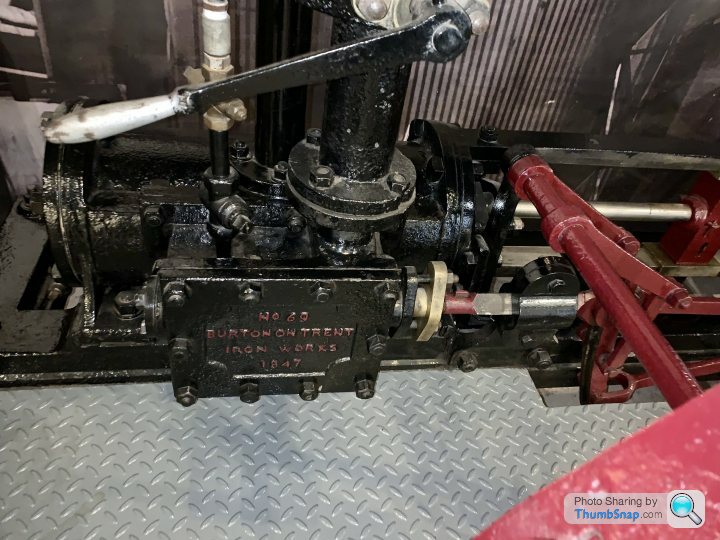
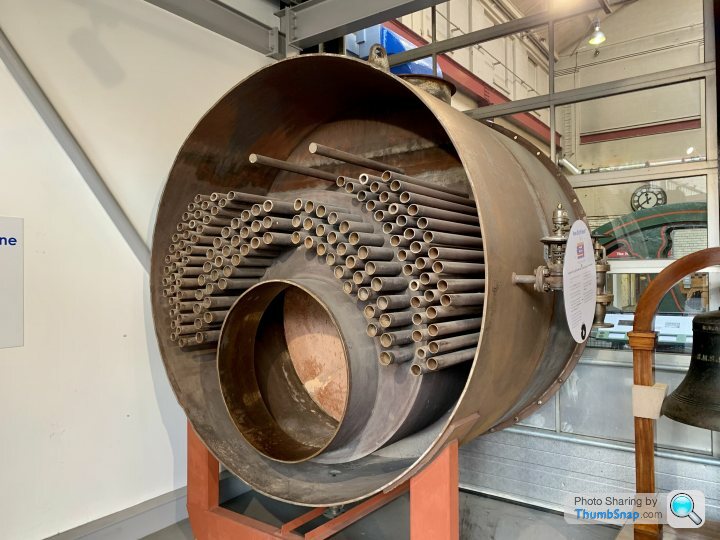
And things in glass cases (always good):
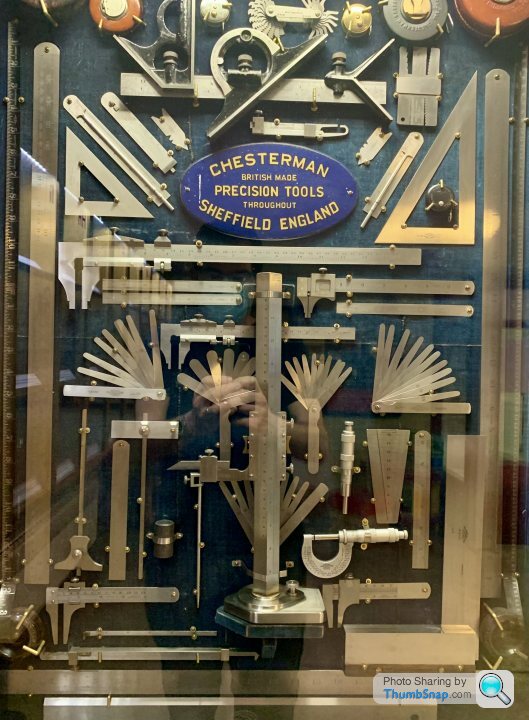
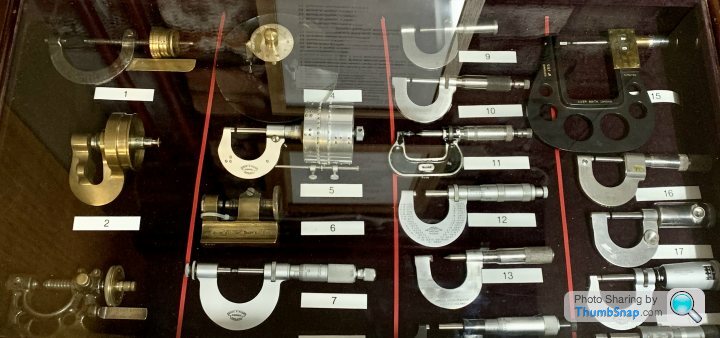
And of course the 12,000hp River Don engine:
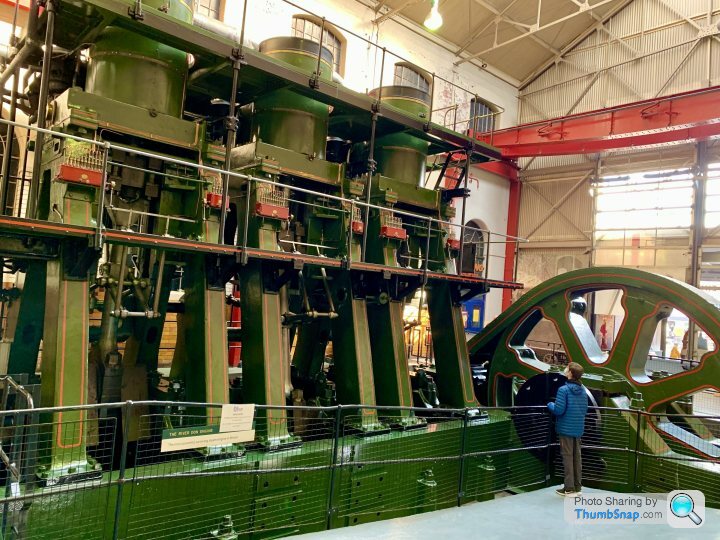
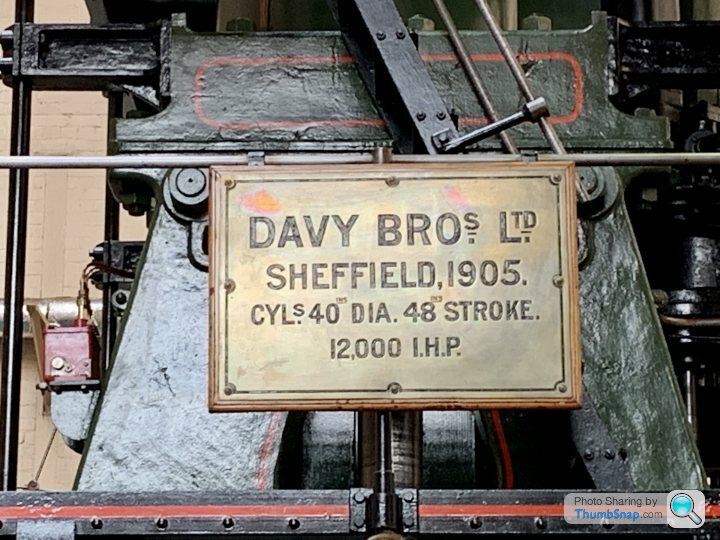
Bought myself a poster for the workshop:
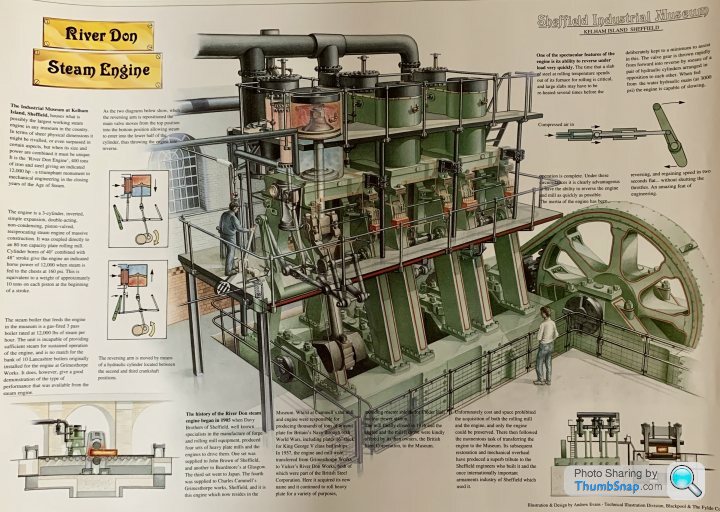
Unfortunately it wasn’t running today due to a boiler issue. I’m always amazed it can go from full forward speed to full reverse speed in 2 seconds, without shutting the throttles. It’s one of those things where you can feel the power just by standing near to it when it’s working. Same awesomeness as a Typhoon display, or being on the pit wall at Silverstone when the old 3.5 litre V10 F1 cars were current.
Other random stuff:
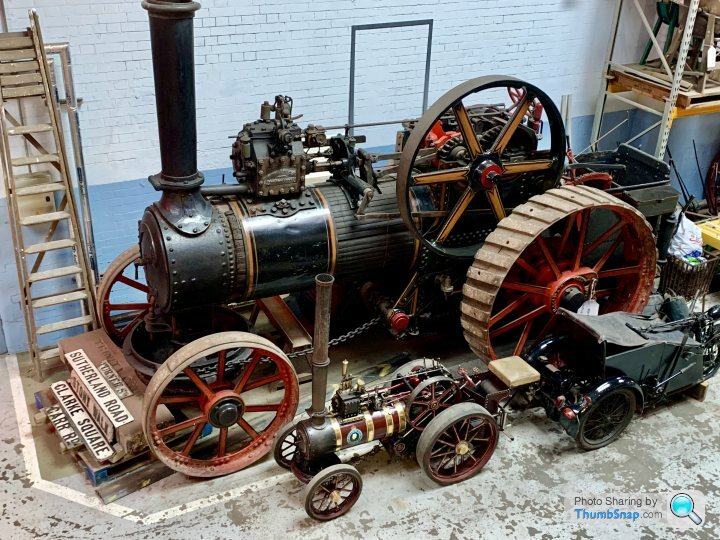
Sheffield Simplex:
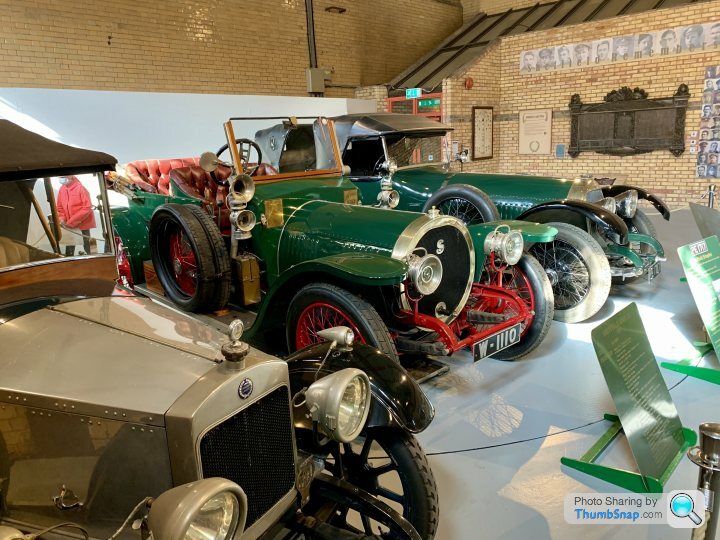
Cavity magnetron (with Sheffield made magnet!):
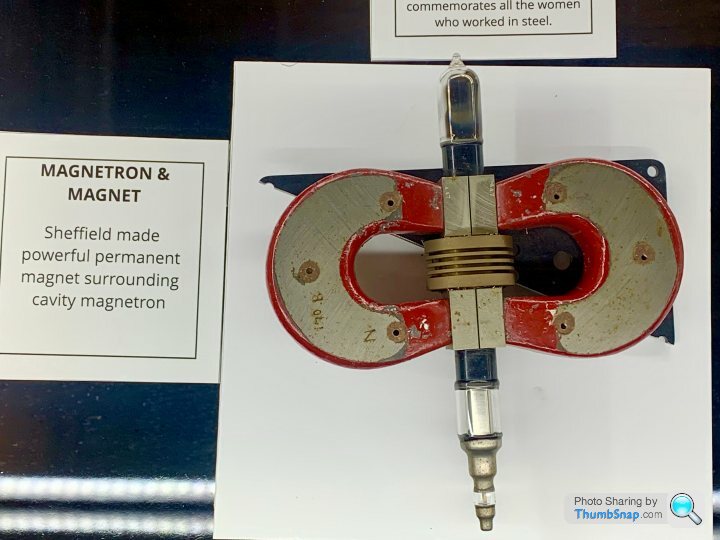
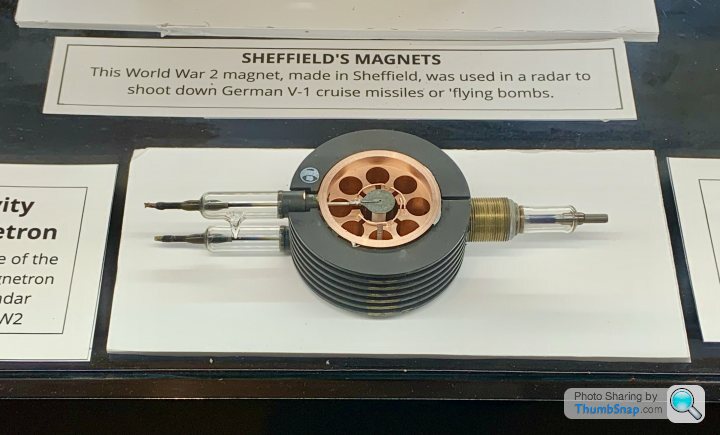
Anyway, a great museum, and it’s free (of course made a donation though).
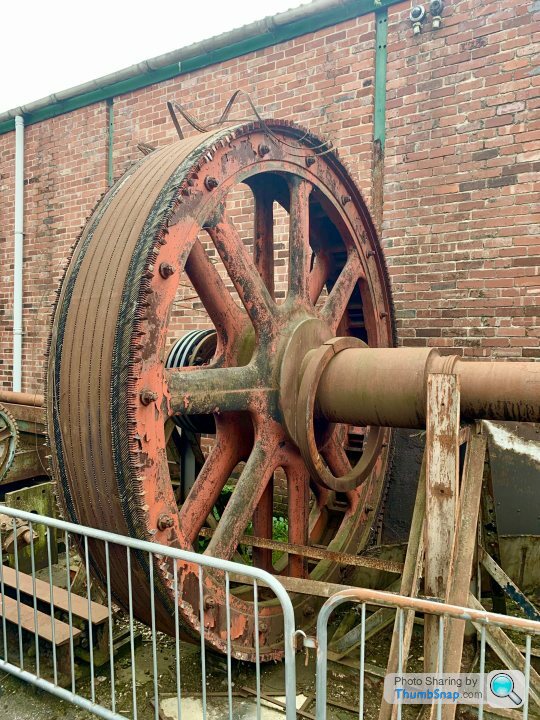
A few other engines:

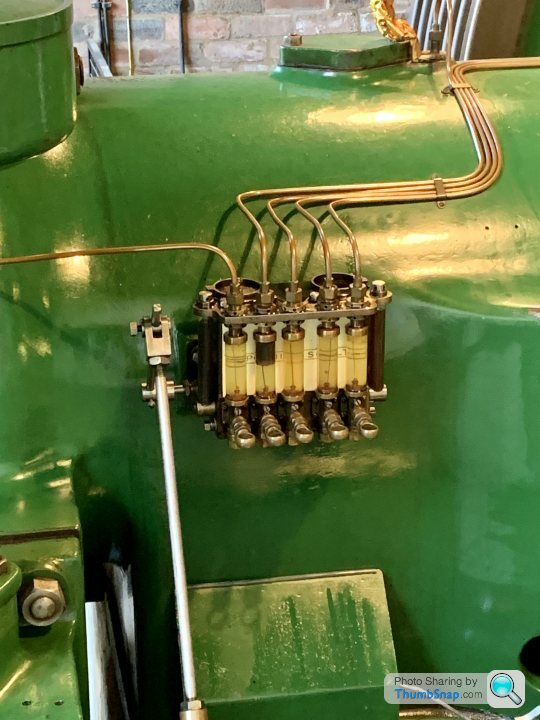
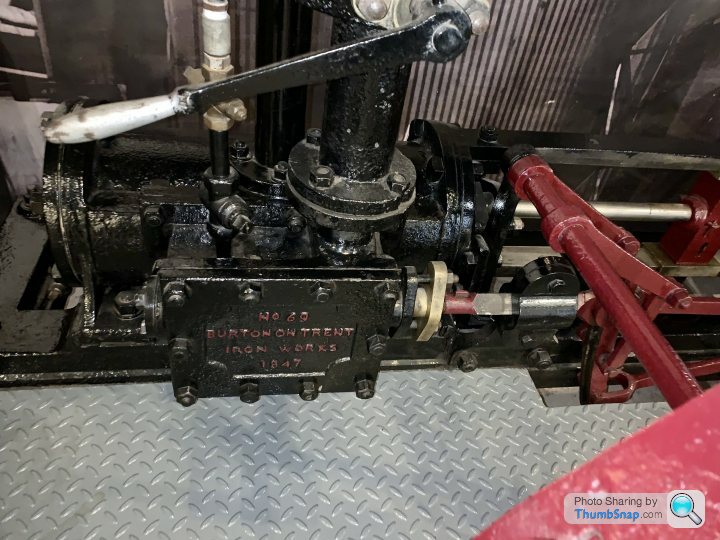
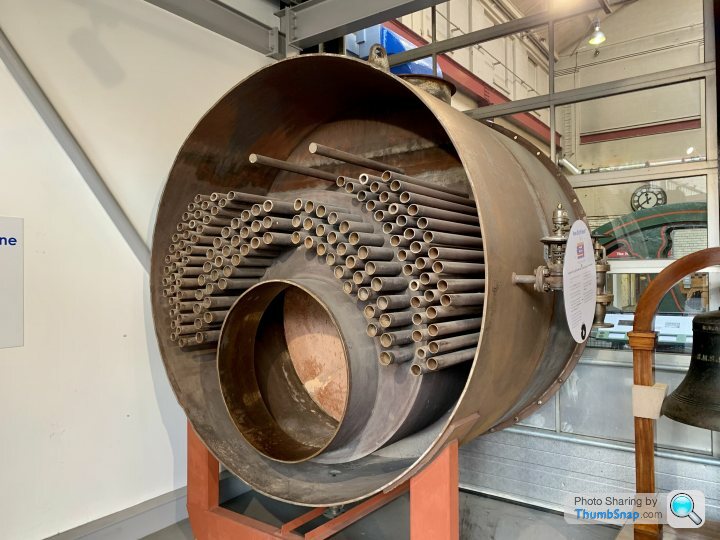
And things in glass cases (always good):
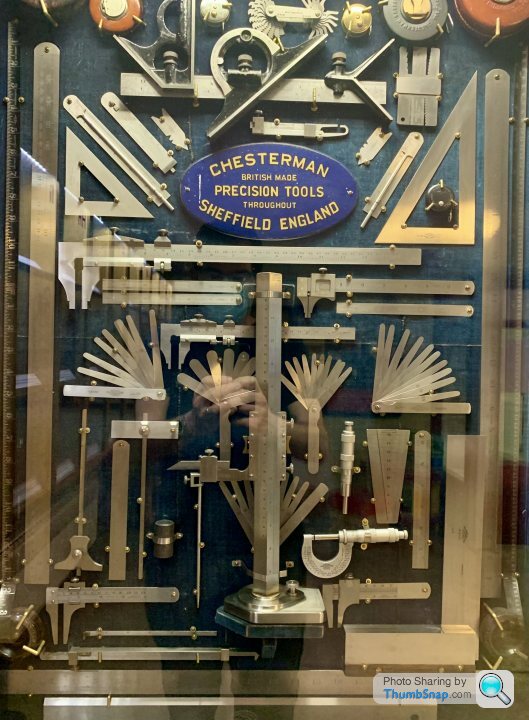
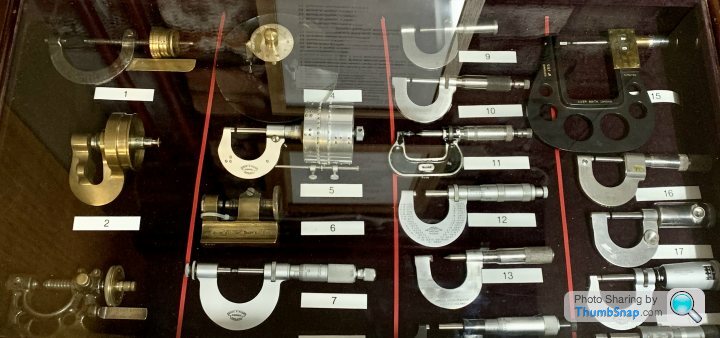
And of course the 12,000hp River Don engine:
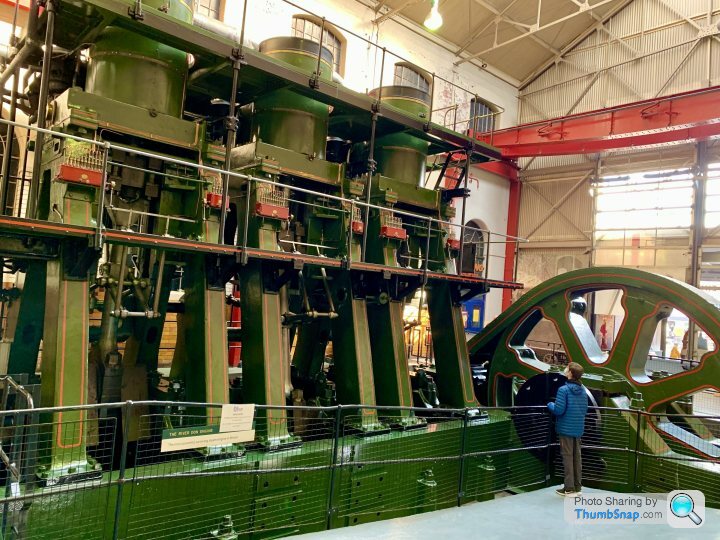
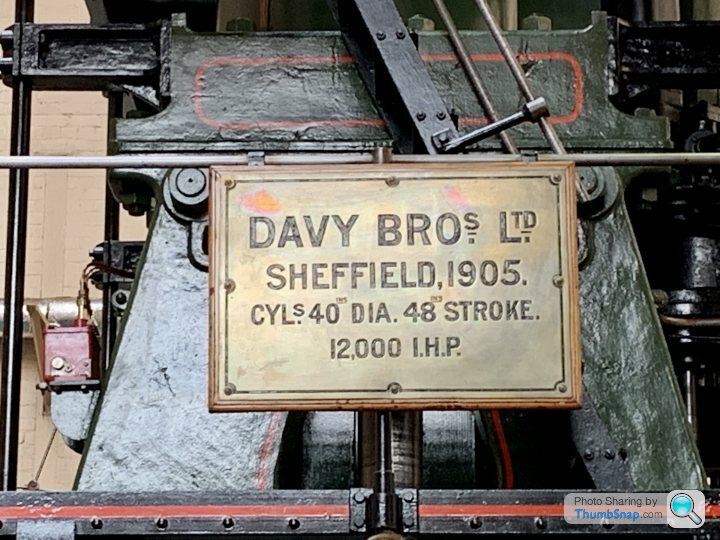
Bought myself a poster for the workshop:
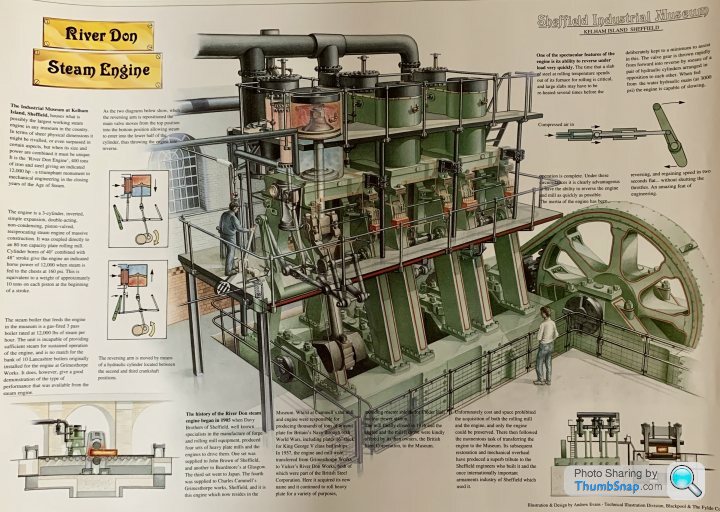
Unfortunately it wasn’t running today due to a boiler issue. I’m always amazed it can go from full forward speed to full reverse speed in 2 seconds, without shutting the throttles. It’s one of those things where you can feel the power just by standing near to it when it’s working. Same awesomeness as a Typhoon display, or being on the pit wall at Silverstone when the old 3.5 litre V10 F1 cars were current.
Other random stuff:
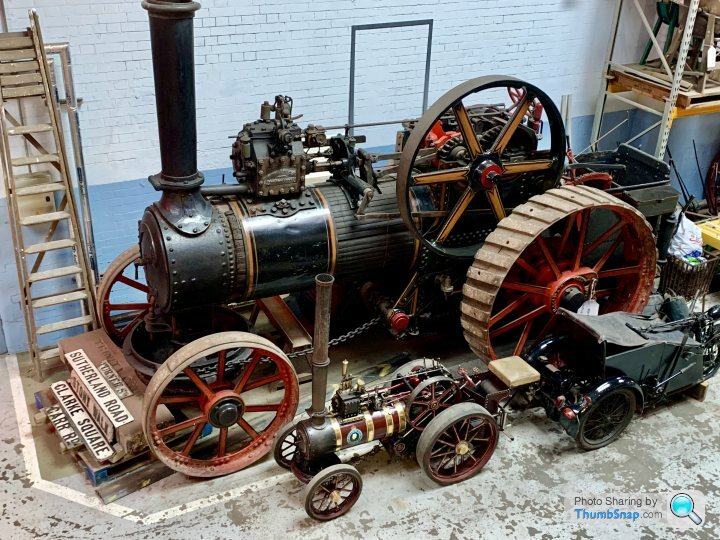
Sheffield Simplex:
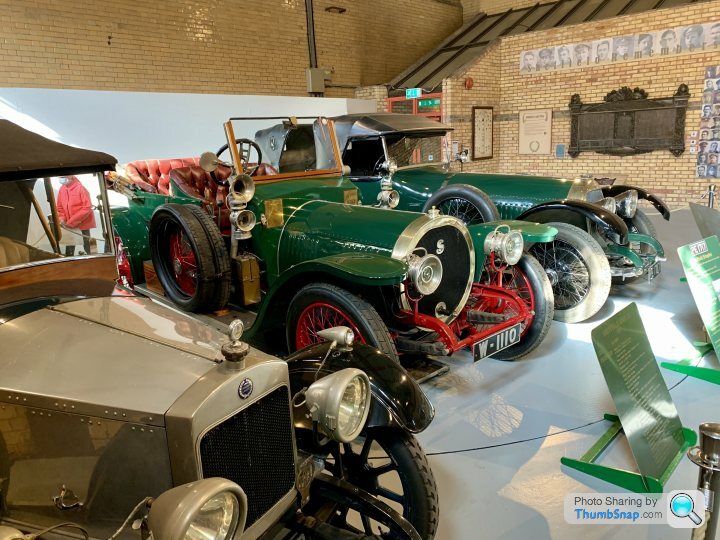
Cavity magnetron (with Sheffield made magnet!):
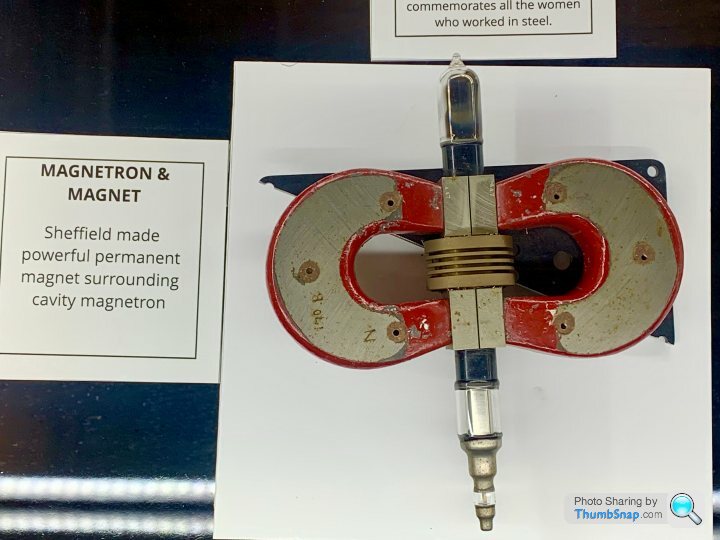
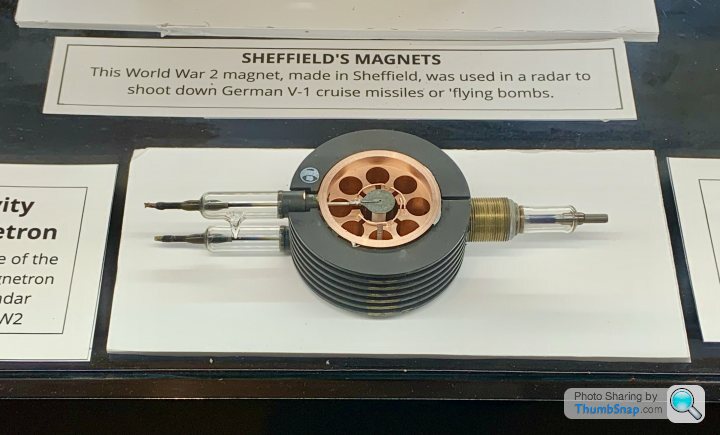
Anyway, a great museum, and it’s free (of course made a donation though).
dudleybloke said:
dr_gn said:
Are they the ones with an arm that rotates?
They have a reservoir Inline with the centre of rotation that looks like its defying gravity.Best example I've seen is on the huge mill engine at Trencherfield Mill in Wigan.
The back cylinder caps are domed, and this was a challenge. I took the advice I understood from the ME forums, and drew out the profile in CAD, then machined from a bar of cast iron:

I set the tool parallel to the bed:
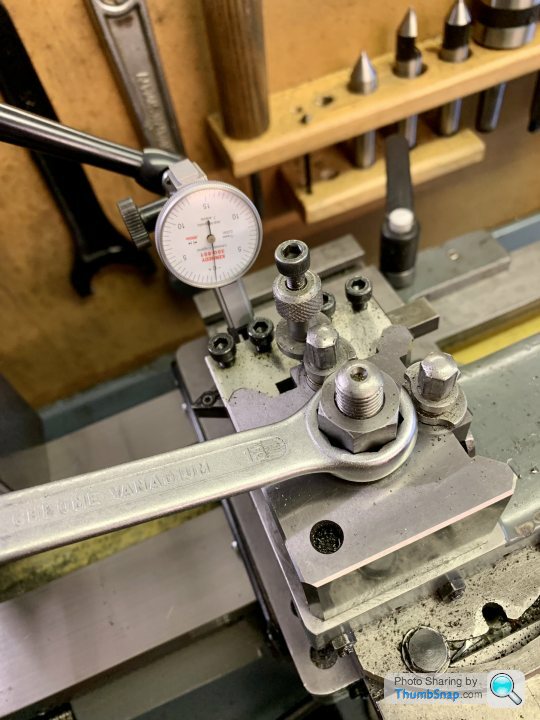
And using more CAD:

Roughed the domes out:
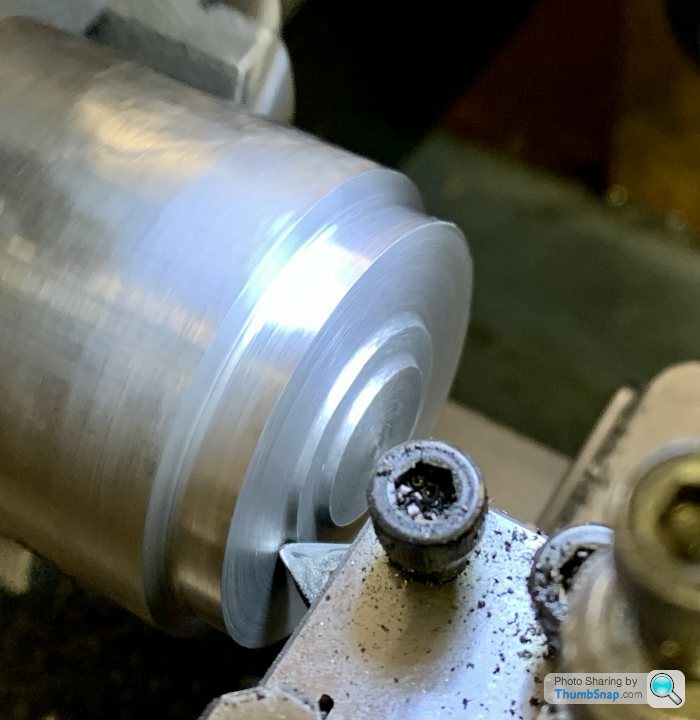
Then using co-ordinates, approximated the profile:
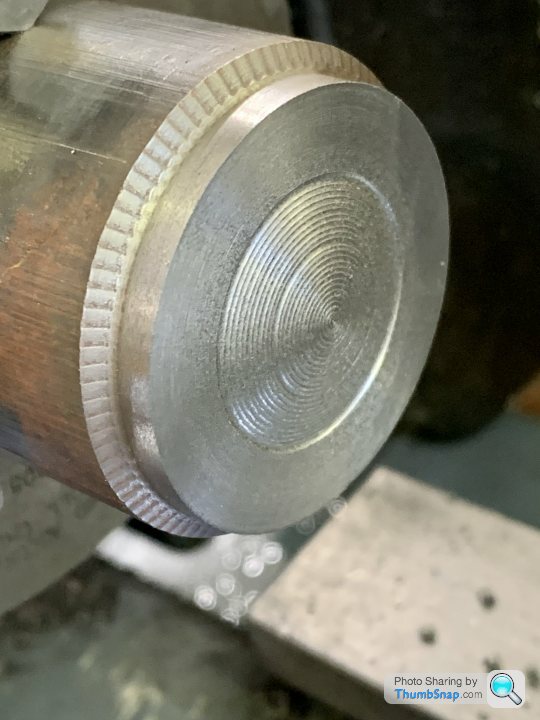
Then using a combination of a dremel, files and abrasive paper:

Smoothed to shape:
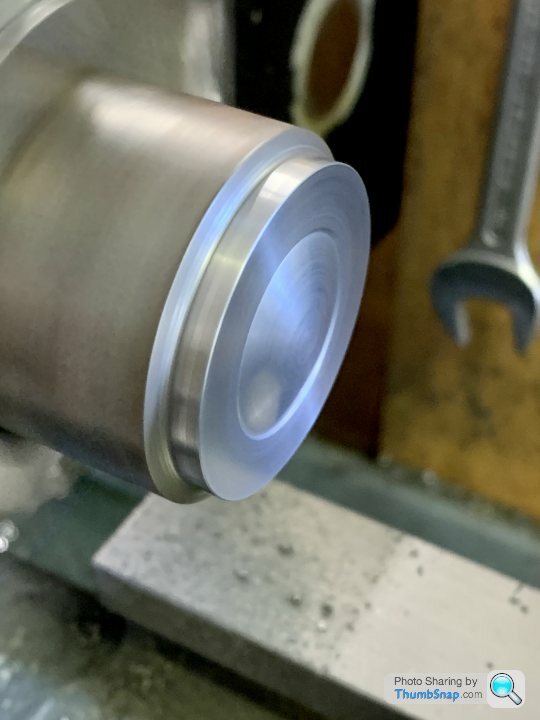
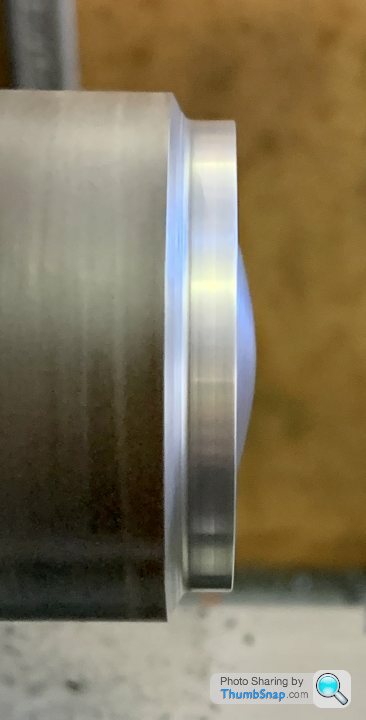
Parted off using the home made rear post from earlier this year (worked great):

Then made a spacer ring and reversed in the chuck to turn and mill the inside details:
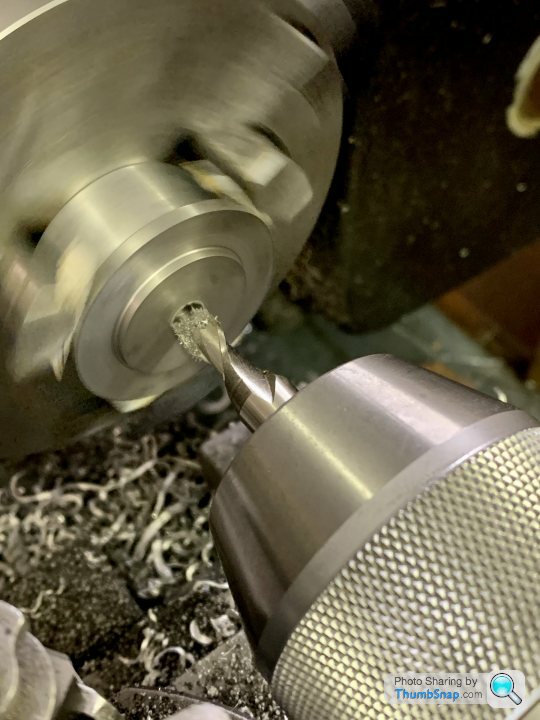
Took a few goes, but eventually I got a decent result:
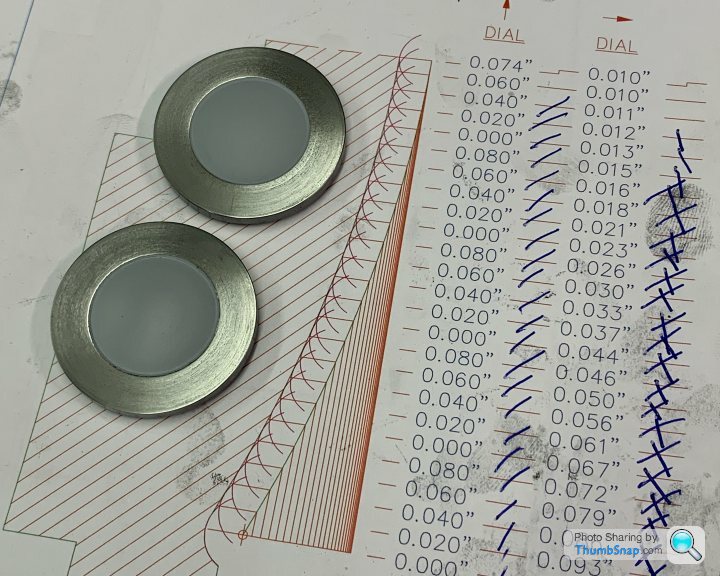
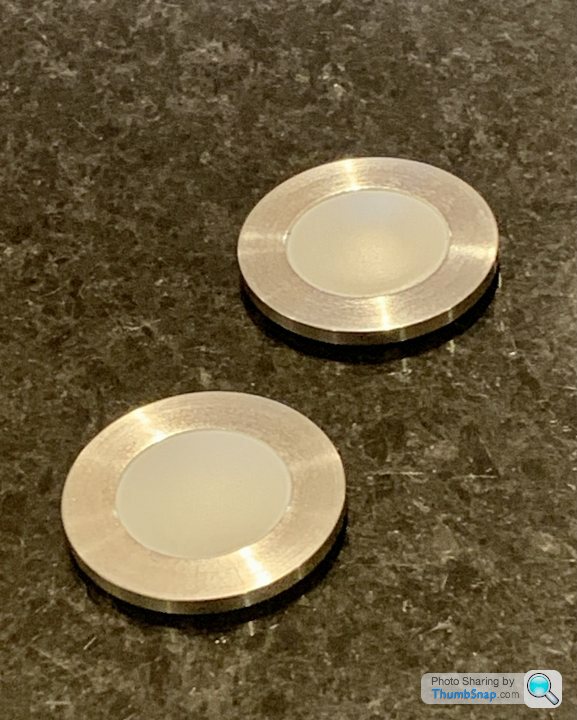
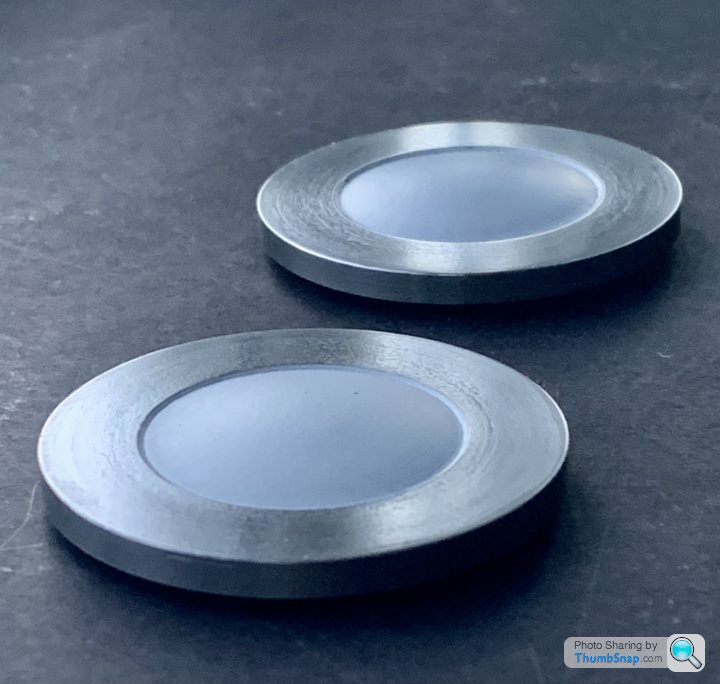
The domes are primed; they’ll be painted blue eventually.

I set the tool parallel to the bed:
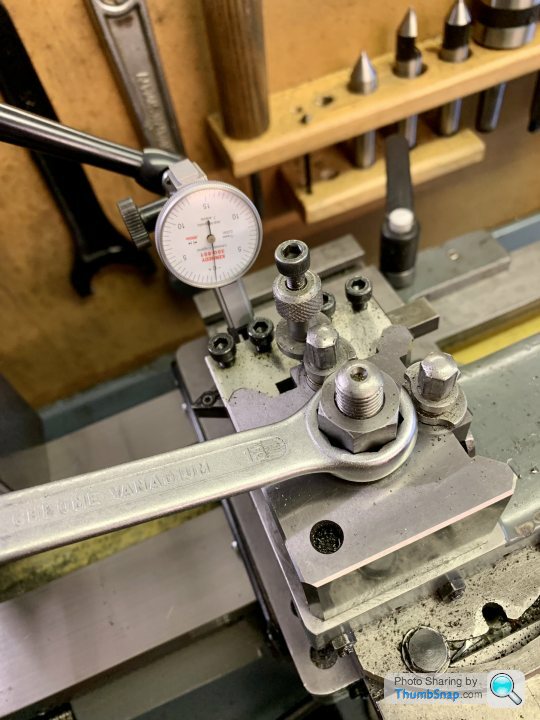
And using more CAD:

Roughed the domes out:
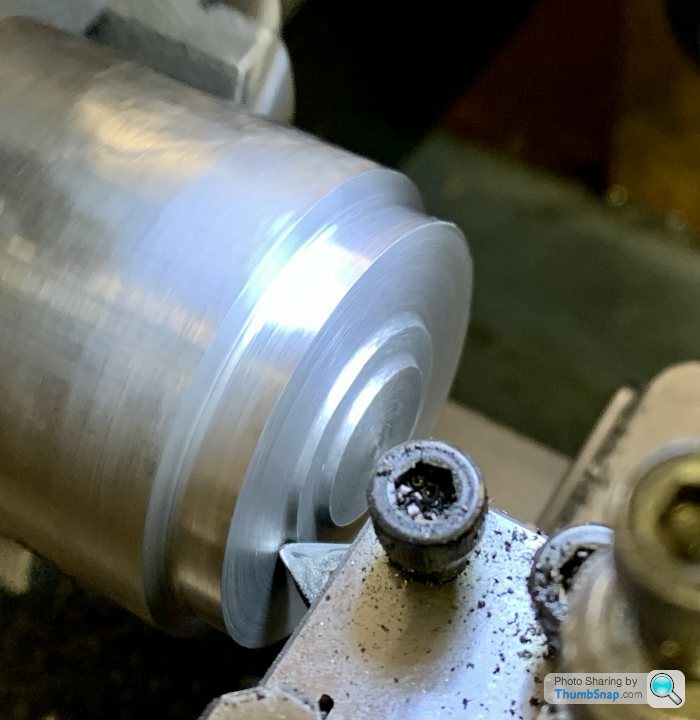
Then using co-ordinates, approximated the profile:
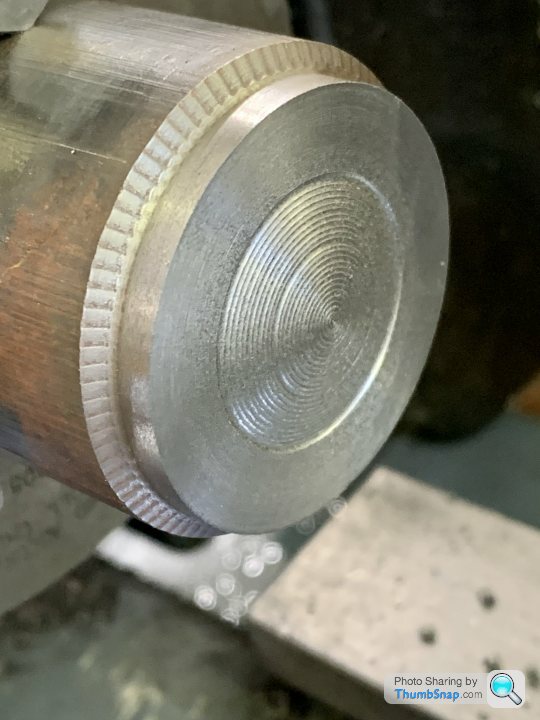
Then using a combination of a dremel, files and abrasive paper:

Smoothed to shape:
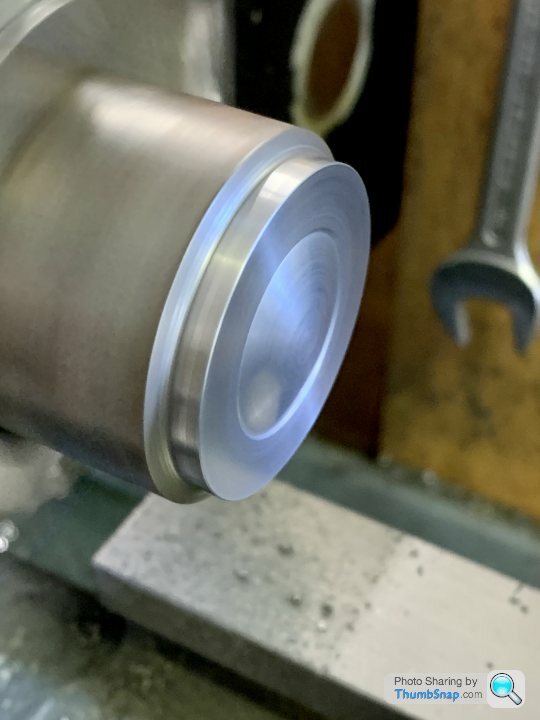
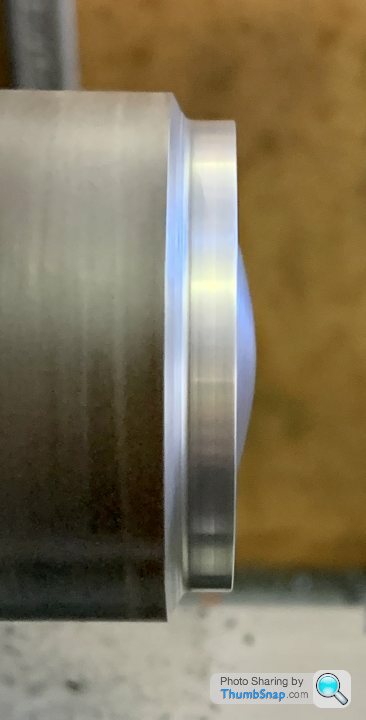
Parted off using the home made rear post from earlier this year (worked great):

Then made a spacer ring and reversed in the chuck to turn and mill the inside details:
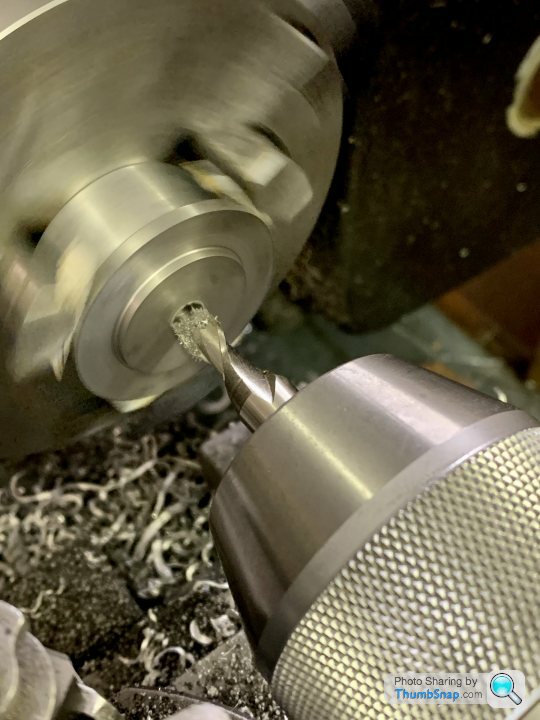
Took a few goes, but eventually I got a decent result:
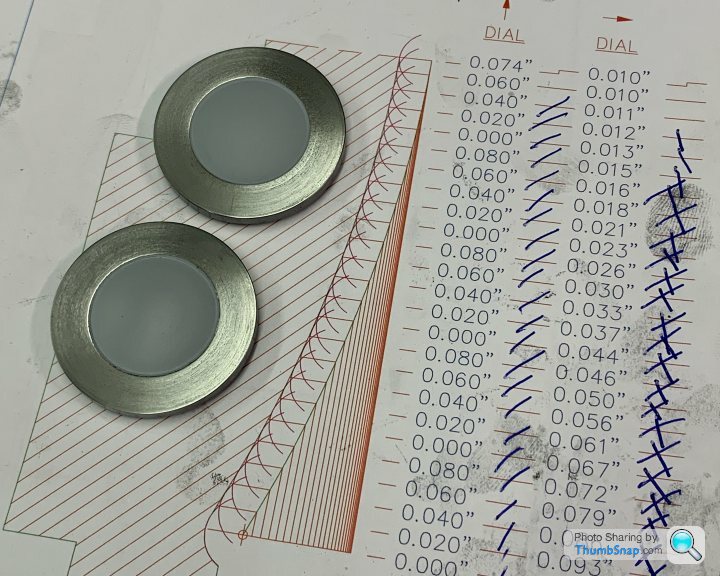
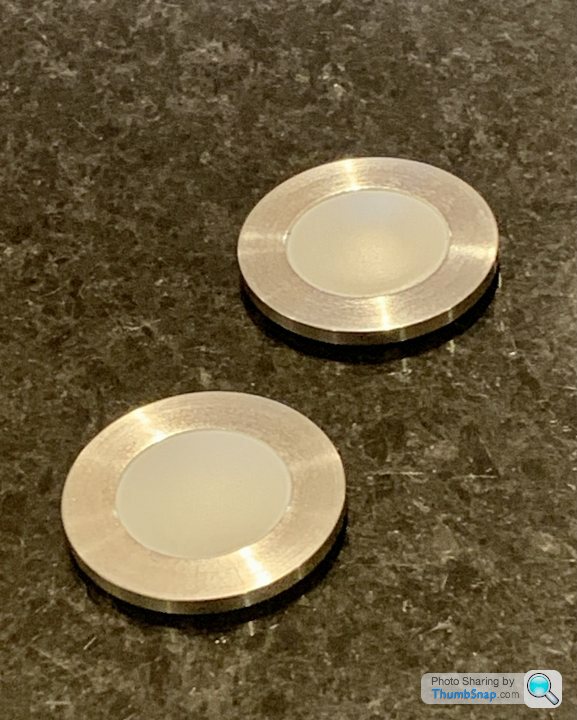
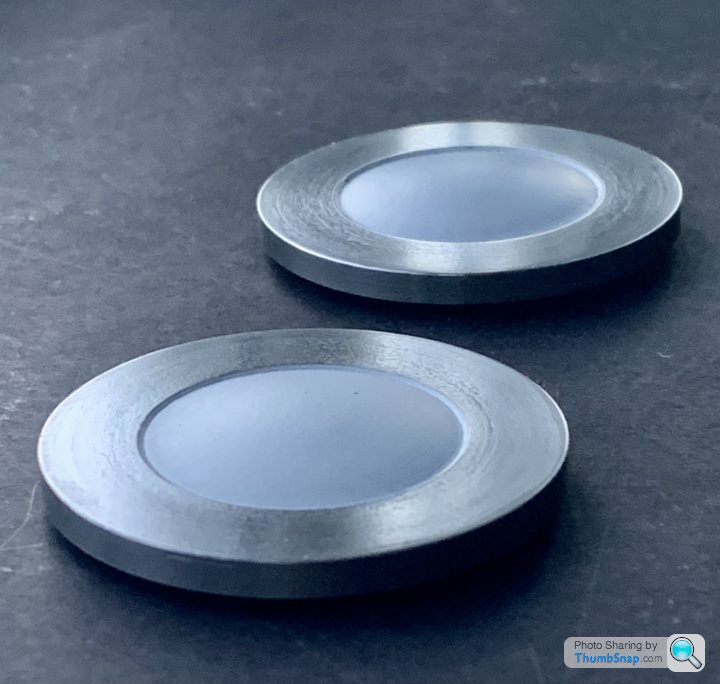
The domes are primed; they’ll be painted blue eventually.
It’s been a while since I did anything on this for one reason or another (mainly a broken foot, then Covid, combined with a freezing cold garage over the winter).
I did some work on the first cylinder back in November, but didn’t get around to posting: First marked it out ready for drilling the valve chest holes:
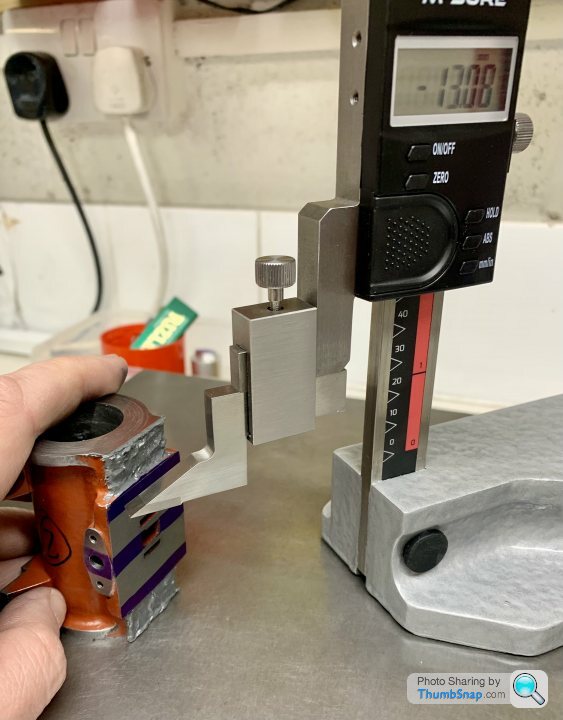
Then put it back on the mandrel for machining:
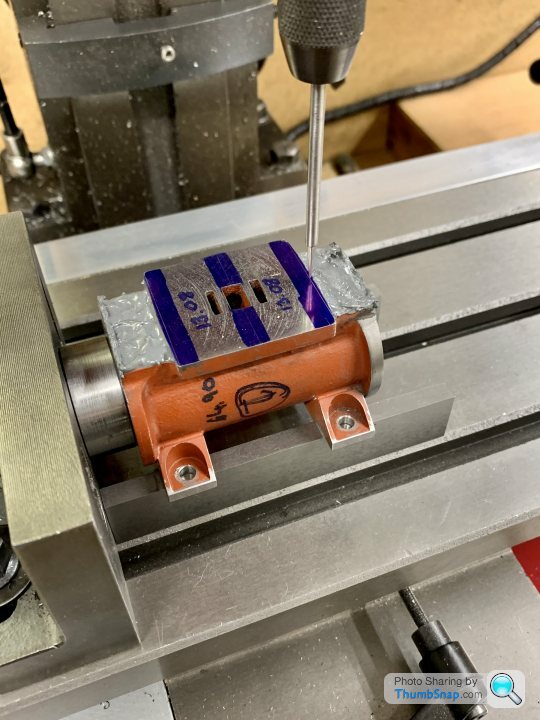
The cast flats either side of the valve faces were slightly too shallow to match the cylinder cap diameter, so I used JB Weld to add material, which was then milled back. The offset from each cylinder end also defined the edges of the valve face:
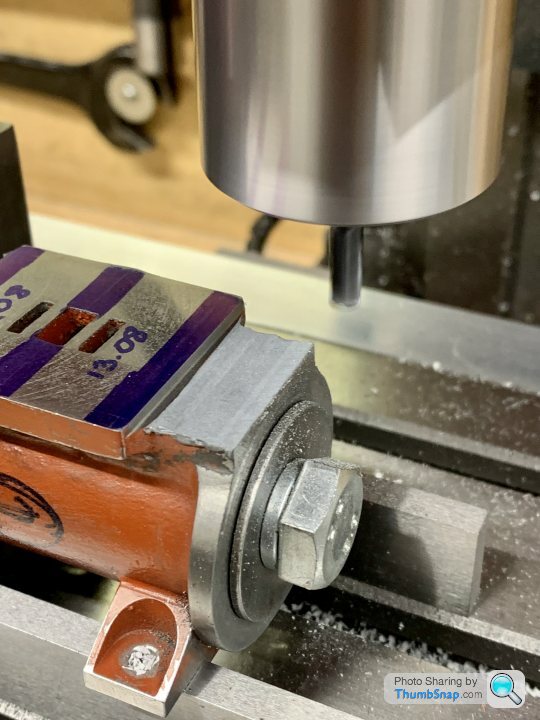
Then after finding the centre of the valve face, I offset the hole positions and drilled and tapped the 7BA holes:
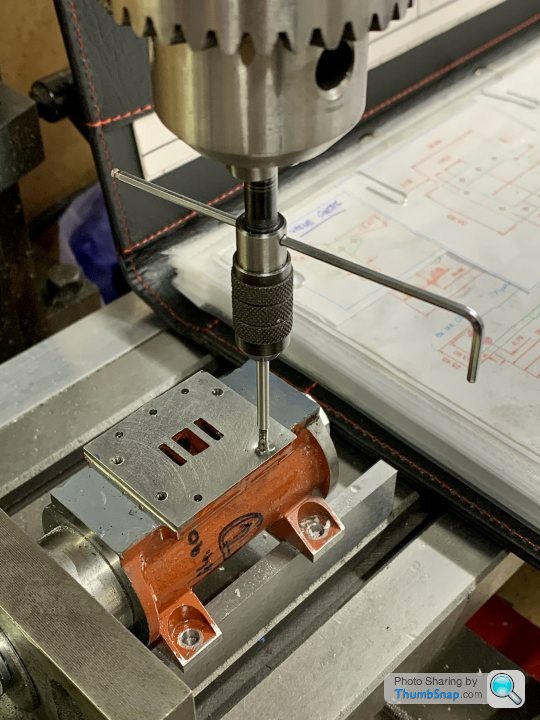
Then this evening (6 months later!) I repeated the process on the other cylinder. I think I mentioned previously that there’s a slight asymmetry on this one in terms of a difference in length from valve port centre to cylinder ends. I made it a best fit, and at the end of the day it’s only about 0.6 mm out, so not obvious to the eye when everything is assembled. In fact by the time the gaskets are fitted, and considering selective assembly of the cylinder caps, the overall cylinder assemblies will probably be pretty much identical:
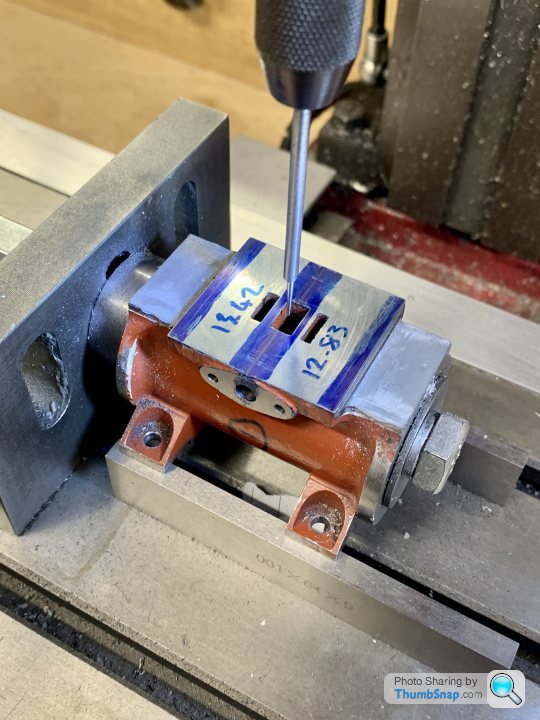
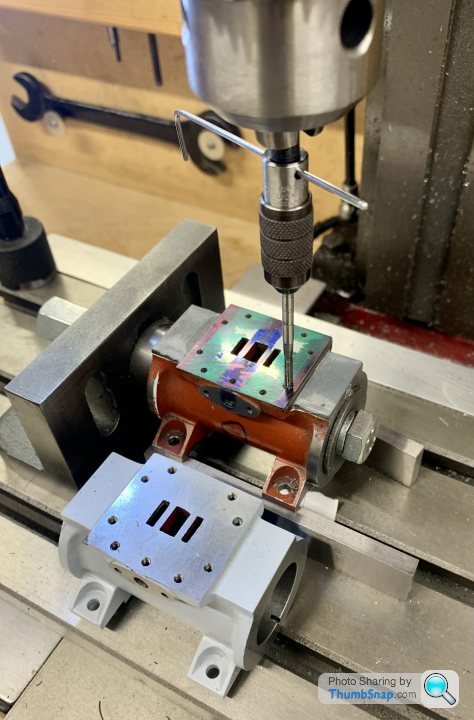
A quick check with the height gauge shows they’re pretty much spot-on identical in terms of valve face height:
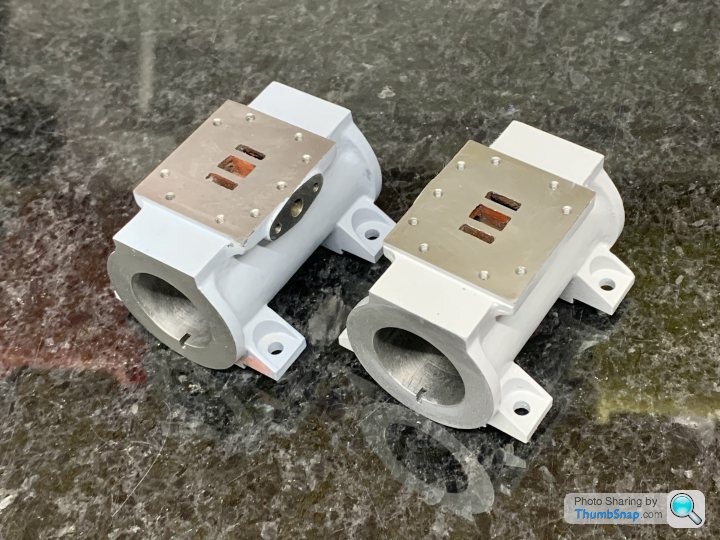
And the end cap diameters now match the flats, so there’s no unsightly step:
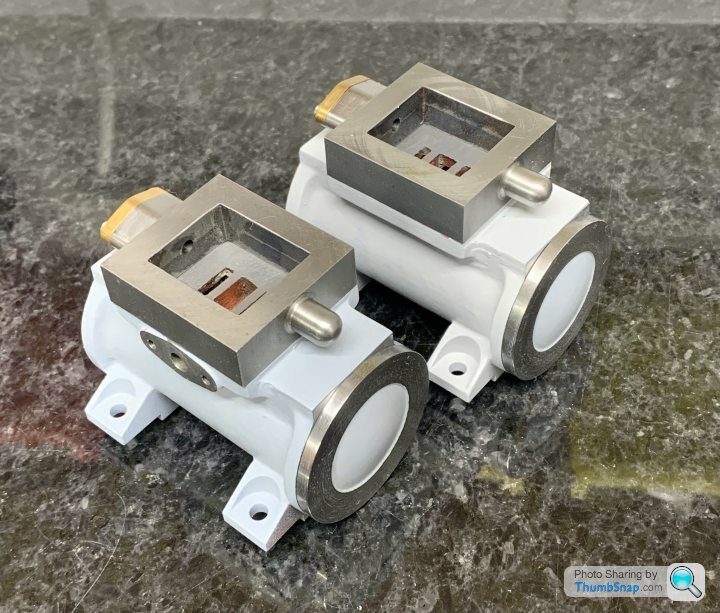
Again, a matter of 10ths of a mm, but for some reason the castings were just undersized.
Still some minor cosmetic filing and filling to do, but pretty much there:
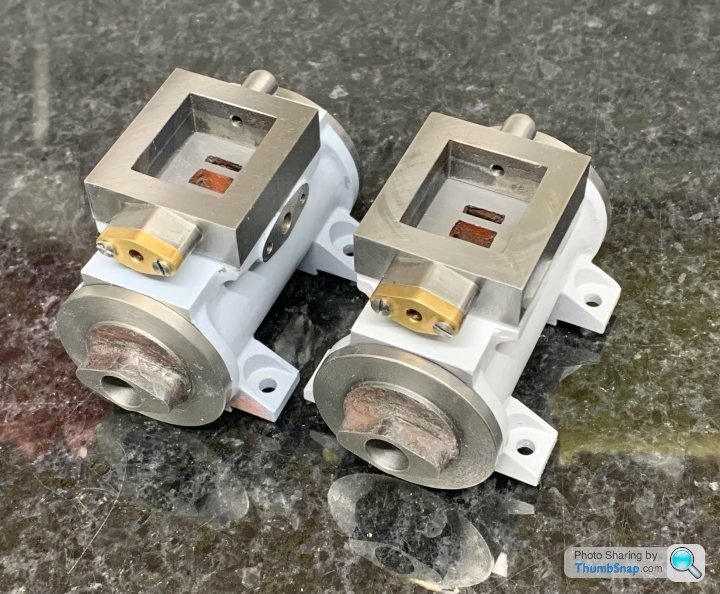
The bosses on the cylinder caps still need milling in the rotary table, but I think I’ll drill and tap the cylinder cap stud holes next, while the milling vice is set up square.
I did some work on the first cylinder back in November, but didn’t get around to posting: First marked it out ready for drilling the valve chest holes:
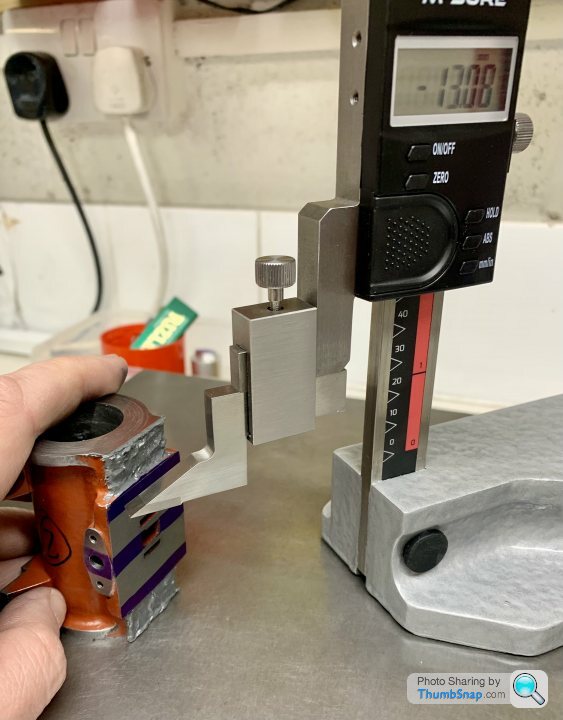
Then put it back on the mandrel for machining:
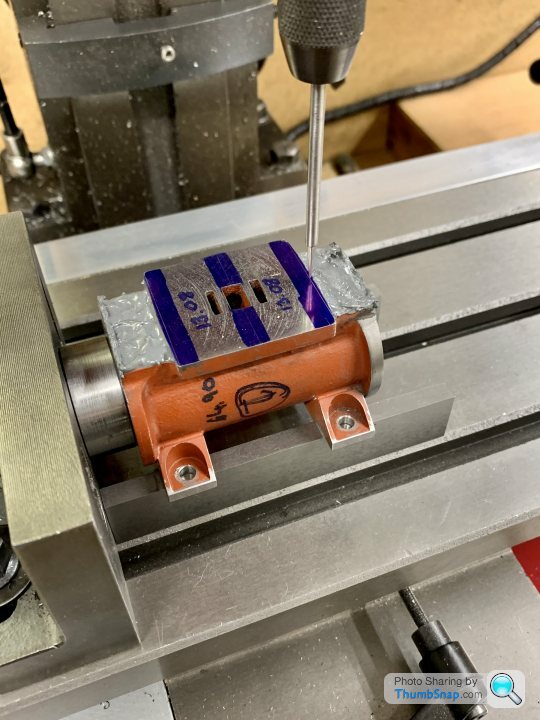
The cast flats either side of the valve faces were slightly too shallow to match the cylinder cap diameter, so I used JB Weld to add material, which was then milled back. The offset from each cylinder end also defined the edges of the valve face:
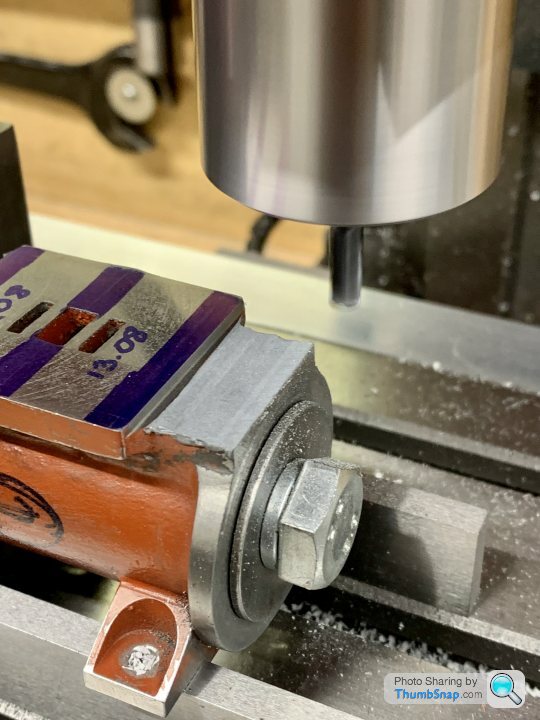
Then after finding the centre of the valve face, I offset the hole positions and drilled and tapped the 7BA holes:
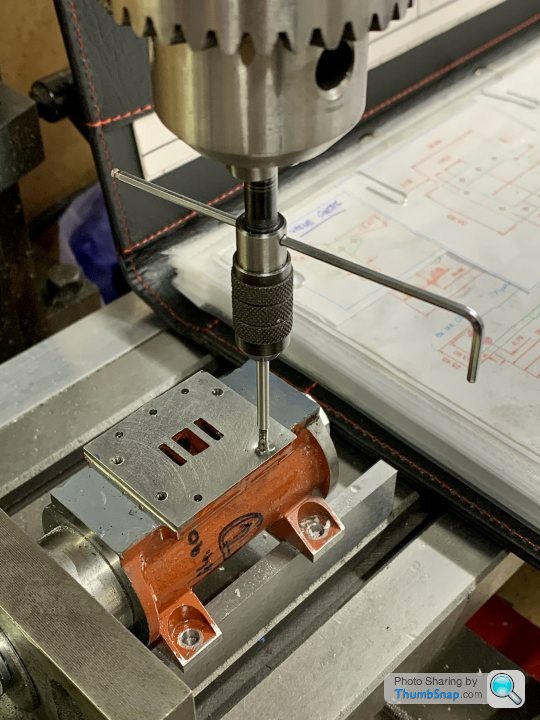
Then this evening (6 months later!) I repeated the process on the other cylinder. I think I mentioned previously that there’s a slight asymmetry on this one in terms of a difference in length from valve port centre to cylinder ends. I made it a best fit, and at the end of the day it’s only about 0.6 mm out, so not obvious to the eye when everything is assembled. In fact by the time the gaskets are fitted, and considering selective assembly of the cylinder caps, the overall cylinder assemblies will probably be pretty much identical:
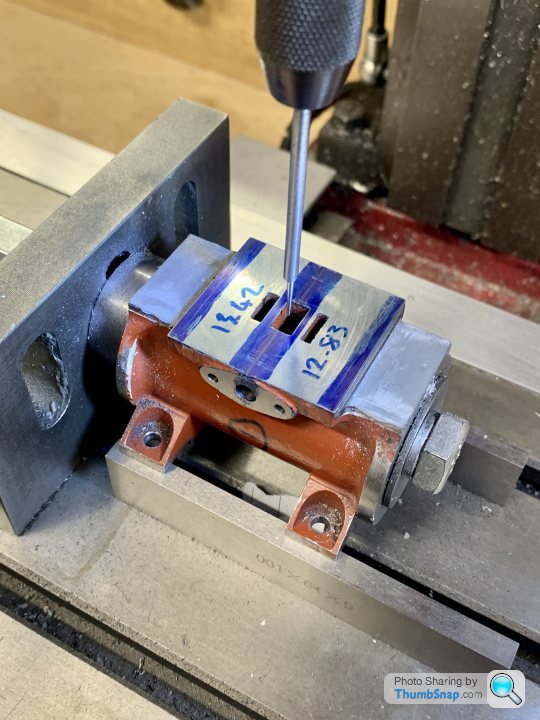
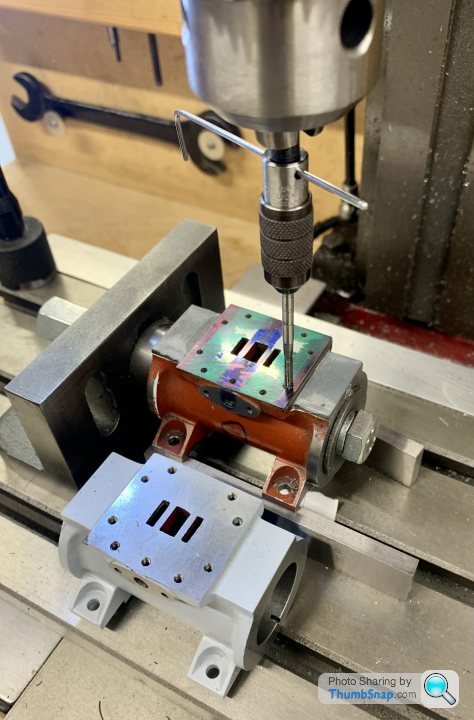
A quick check with the height gauge shows they’re pretty much spot-on identical in terms of valve face height:
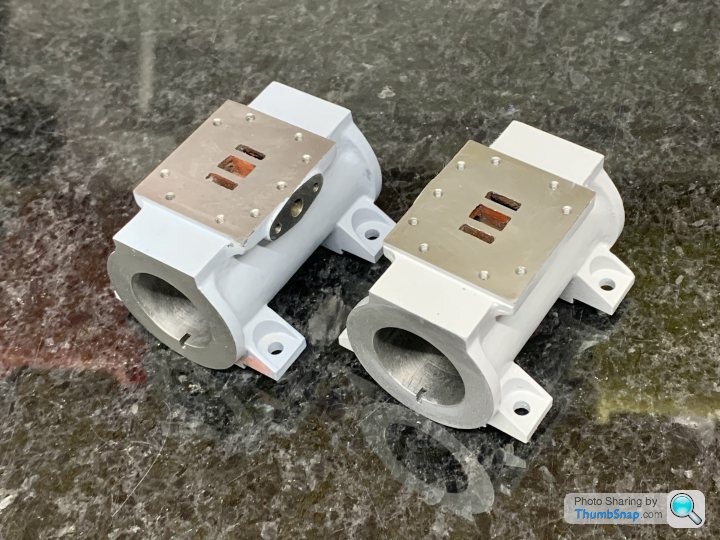
And the end cap diameters now match the flats, so there’s no unsightly step:
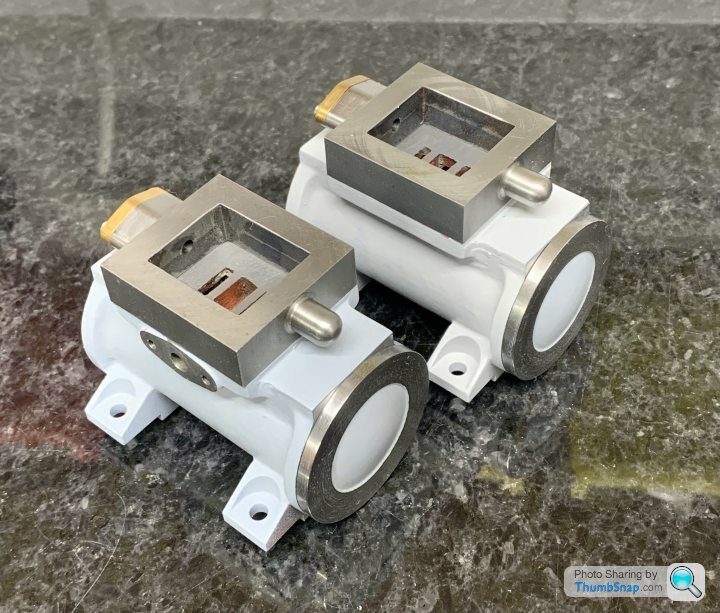
Again, a matter of 10ths of a mm, but for some reason the castings were just undersized.
Still some minor cosmetic filing and filling to do, but pretty much there:
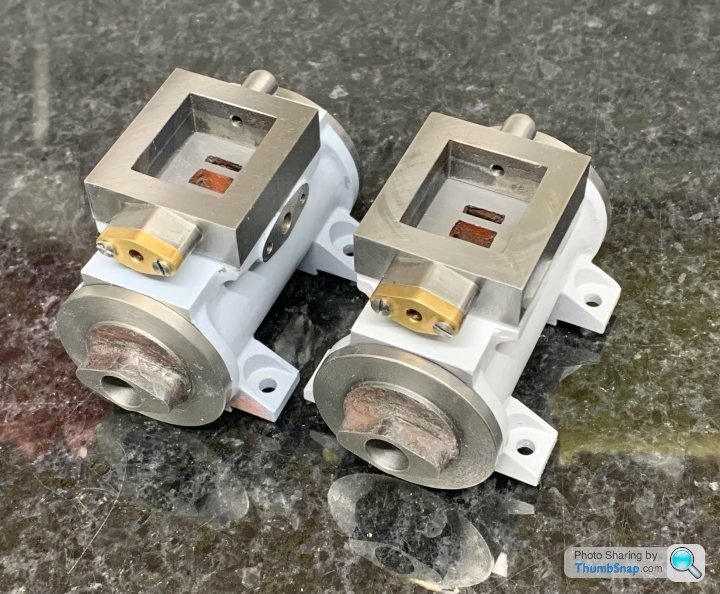
The bosses on the cylinder caps still need milling in the rotary table, but I think I’ll drill and tap the cylinder cap stud holes next, while the milling vice is set up square.
Cylinder cap stud holes today (all 40 of them!).
Checked the hole PCDs were right - I wanted the studs mid way between the cap o/ds and the central cast bits. This turned out to be slightly different from the plans. I got the co-ordinates from CAD, double-checked with the formula in my Zeus booklet:
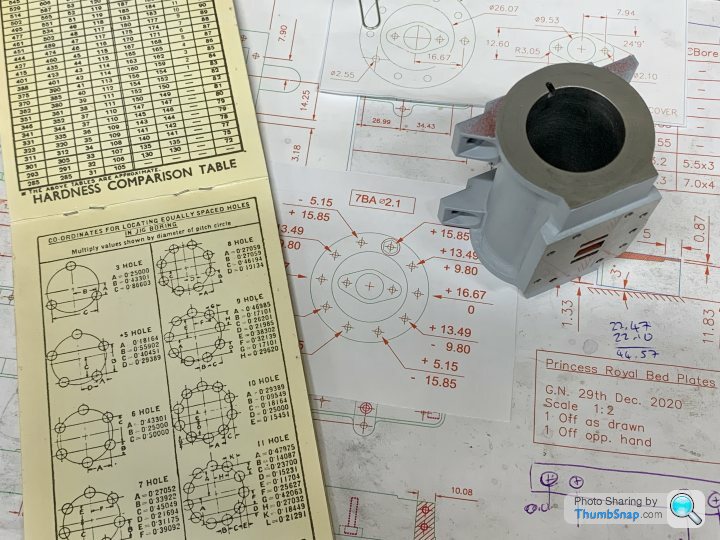
Then, in the vice, checked the face for flatness:

Got the centre of the face with the finder:
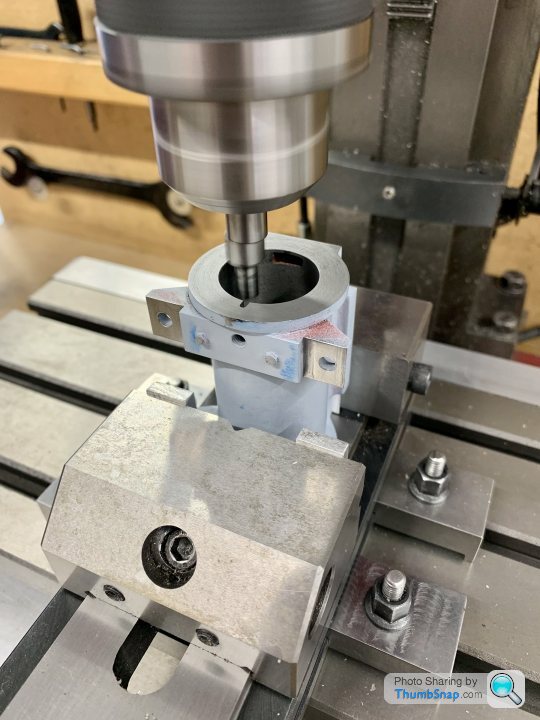
Double-checked the co-ordinates using a 7BA washer (looked OK):
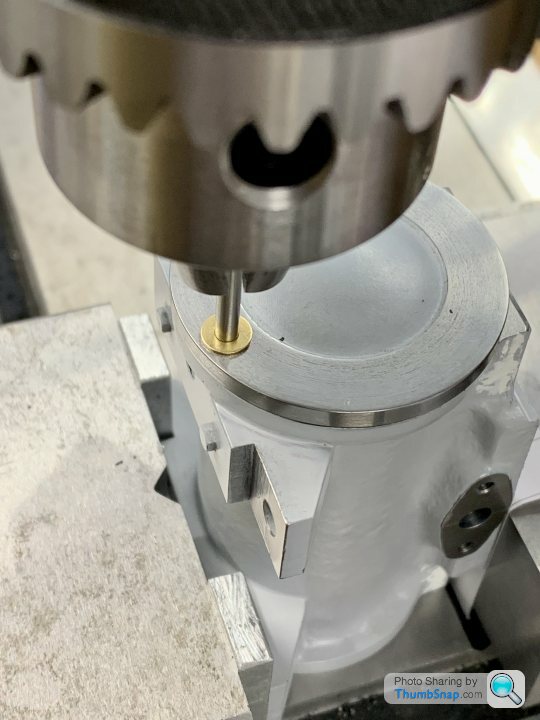
Then co-ordinate drilled the holes using the DRO. I went to 3mm deep, making sure I didn’t break through the flanges:
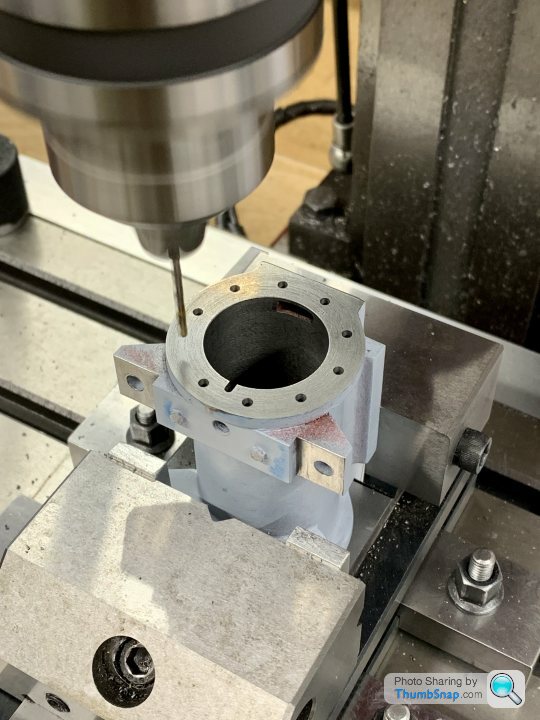
Tapped to 7BA using a plug tap:

Then went round each one by hand with a countersink to remove any burrs:
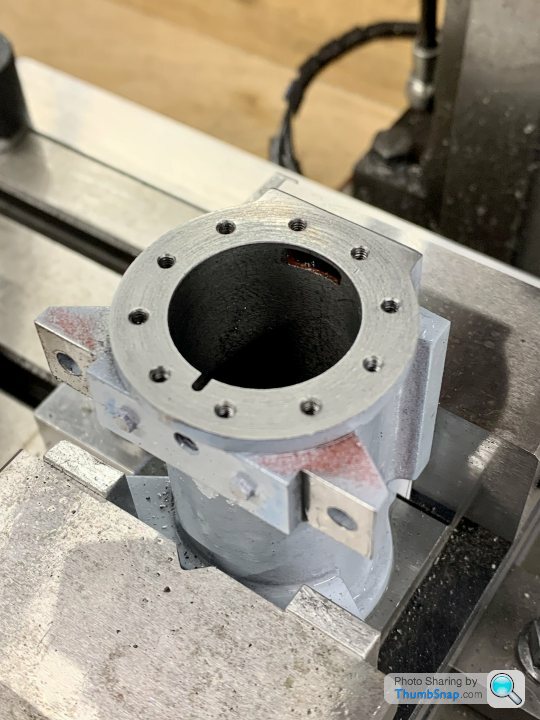
So a bit more progress:

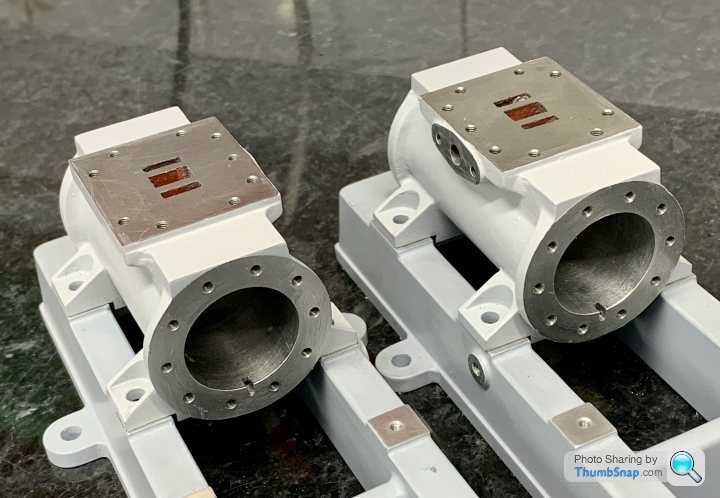
Next job I think I’ll drill the valve chests.
Checked the hole PCDs were right - I wanted the studs mid way between the cap o/ds and the central cast bits. This turned out to be slightly different from the plans. I got the co-ordinates from CAD, double-checked with the formula in my Zeus booklet:
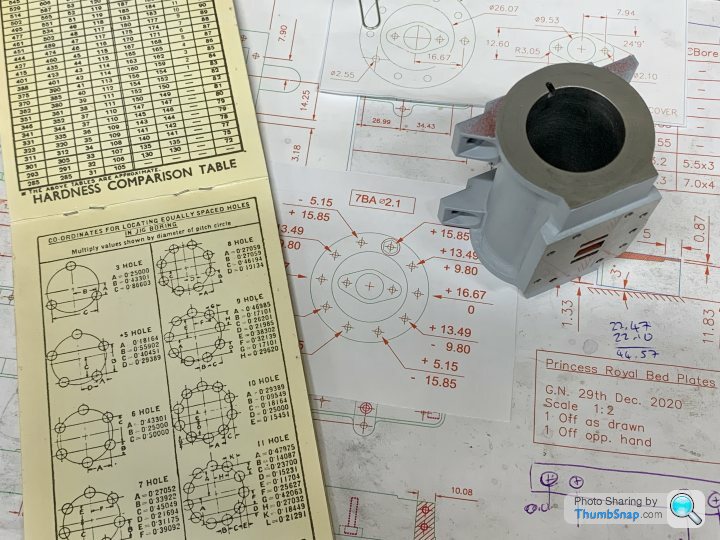
Then, in the vice, checked the face for flatness:

Got the centre of the face with the finder:
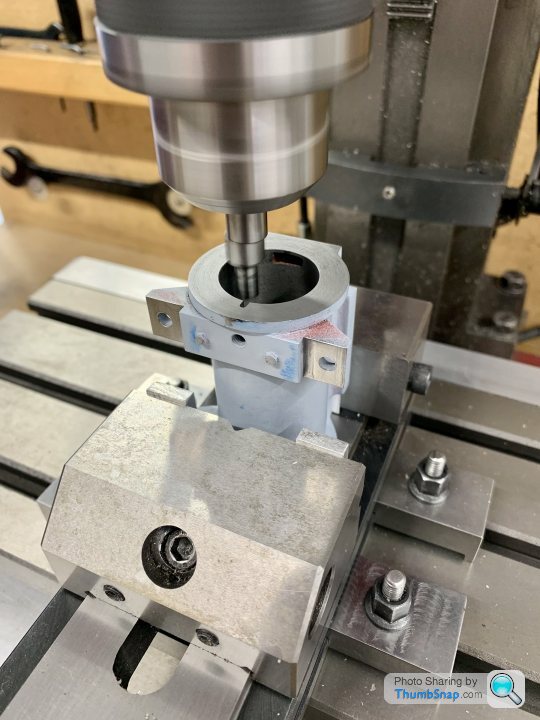
Double-checked the co-ordinates using a 7BA washer (looked OK):
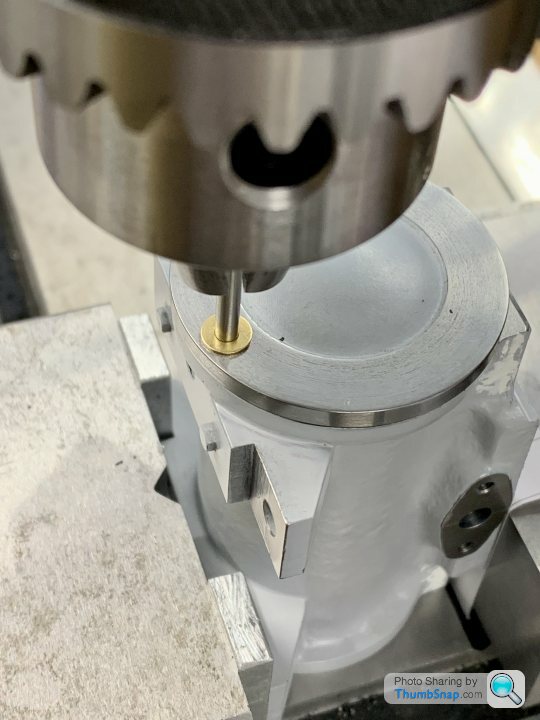
Then co-ordinate drilled the holes using the DRO. I went to 3mm deep, making sure I didn’t break through the flanges:
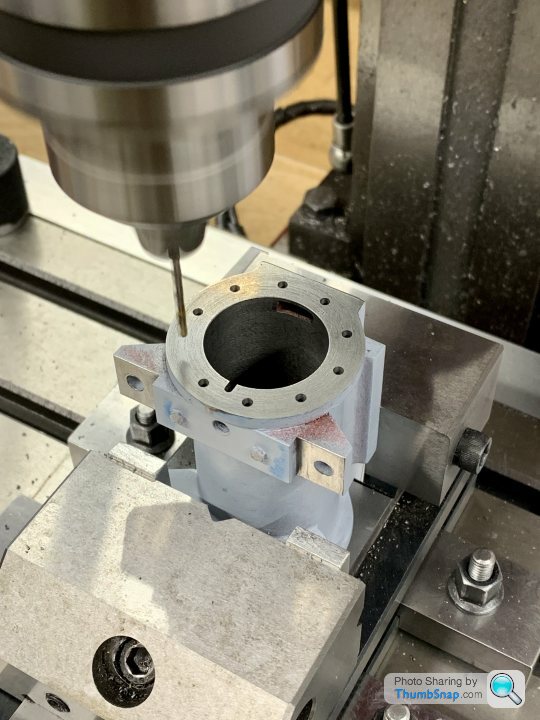
Tapped to 7BA using a plug tap:

Then went round each one by hand with a countersink to remove any burrs:
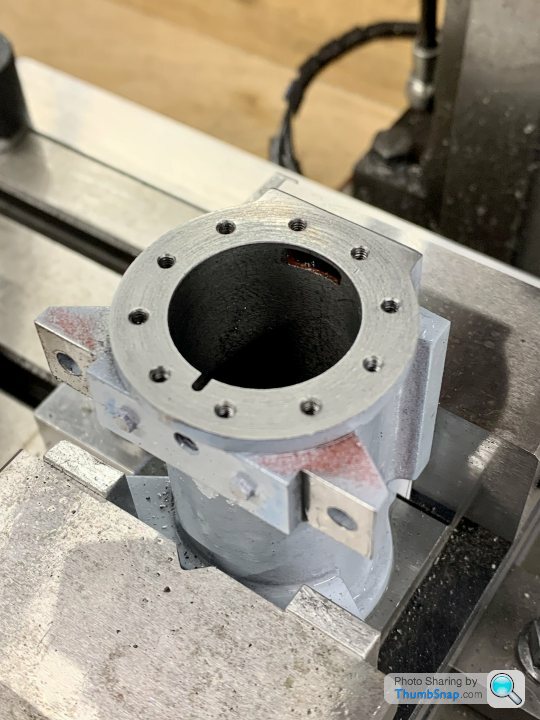
So a bit more progress:

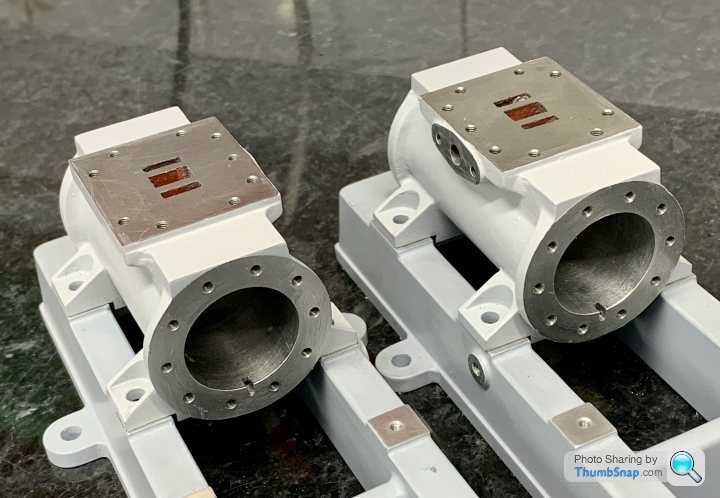
Next job I think I’ll drill the valve chests.
Spent some time today drilling the valve chests. They are handed, and have a top and a bottom, but still look very similar, so easy to make a mistake…
Started by putting them in the mill and checking they’re flat:
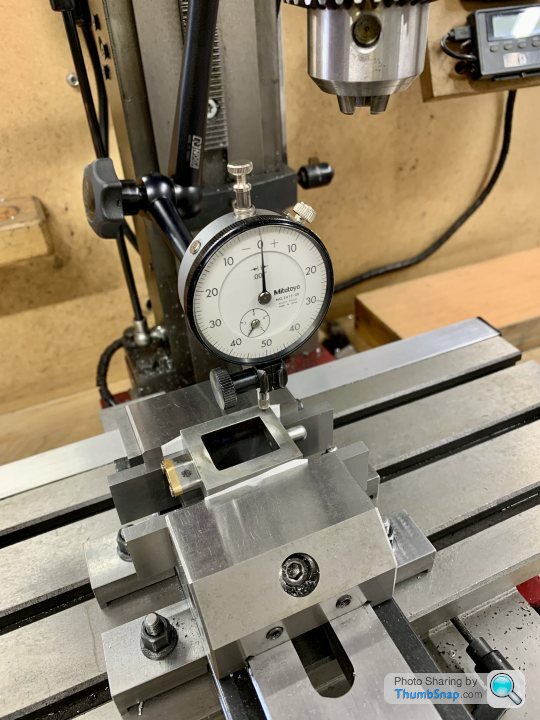
Then got the centre with the edge finder:
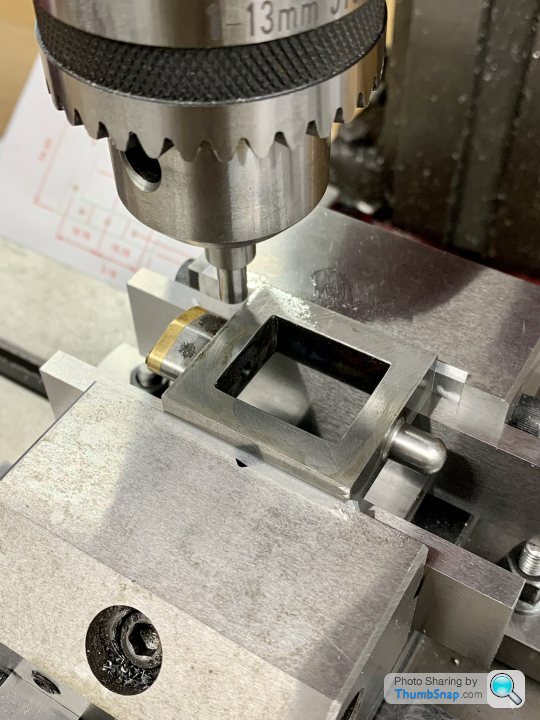
Then co-ordinate drilled with a centre drill. I skipped this step for the second one because the centre drill seemed to leave a central pip. I later realised I’d had this discussion before, and bought a stub drill (I think that’s what it’s called). I think Covid has a lot to answer for in terms of occasional brain fog:
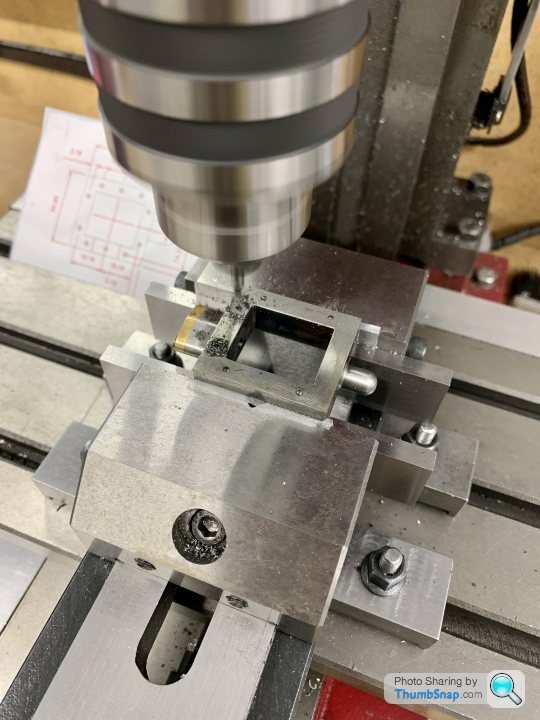
Through-drilled to 7BA clearance:
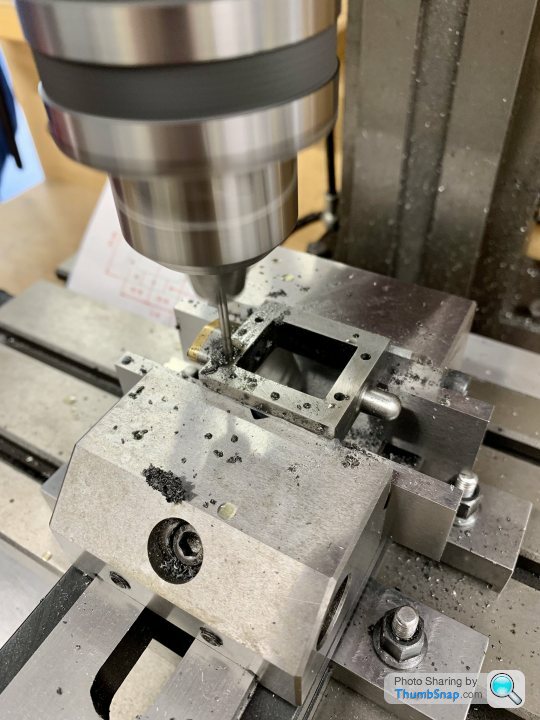
I thought the drill might wander on contact, hence why I initially used centre drilling, but in the event it was fine.
Then drilled and tapped one 7BA hole, over where the steam inlet will be:
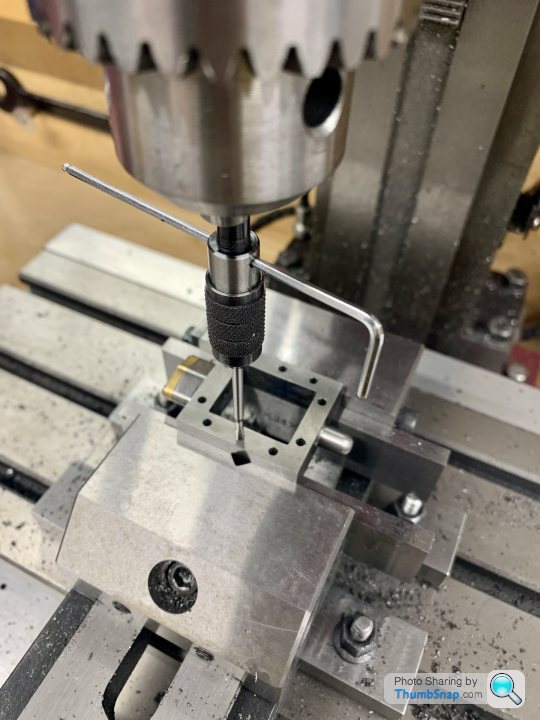
Finished by hand countersinking all the holes.
The drilled chests:
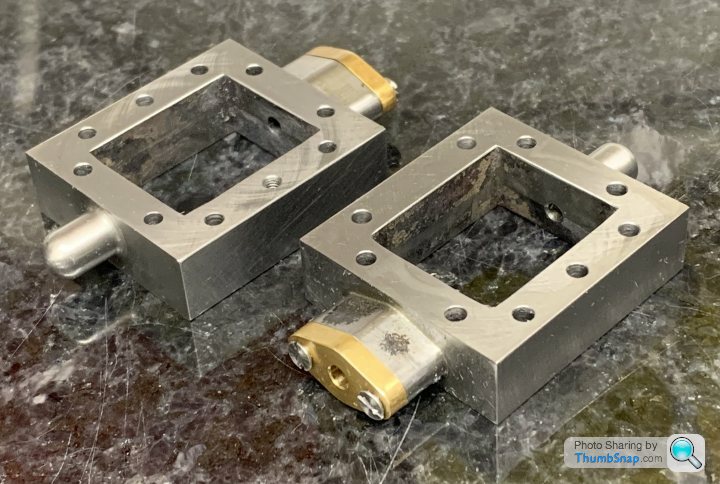
Test fitted to the cylinders using bolts:
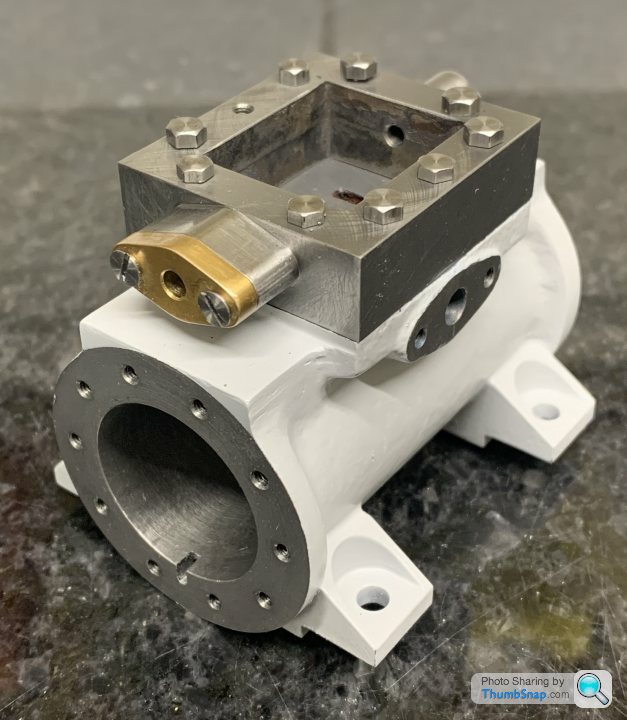

So far so good. The only thing left to do on the chests is to drill the steam inlet holes, and the mount holes for the inlet boxes.
Started by putting them in the mill and checking they’re flat:
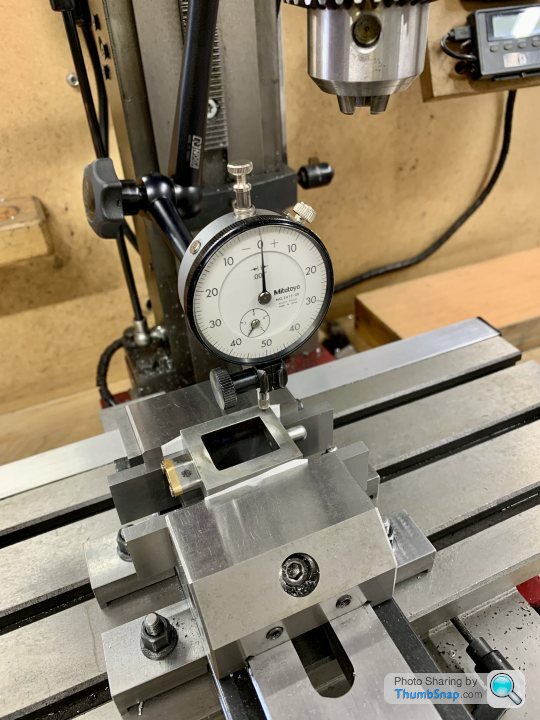
Then got the centre with the edge finder:
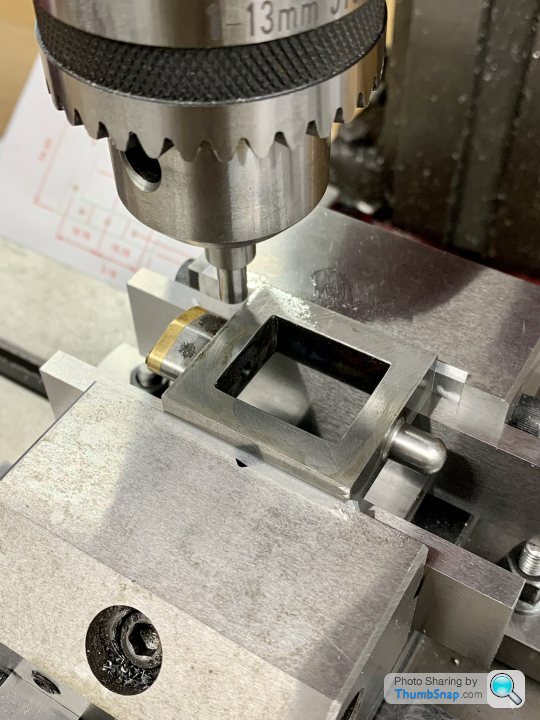
Then co-ordinate drilled with a centre drill. I skipped this step for the second one because the centre drill seemed to leave a central pip. I later realised I’d had this discussion before, and bought a stub drill (I think that’s what it’s called). I think Covid has a lot to answer for in terms of occasional brain fog:
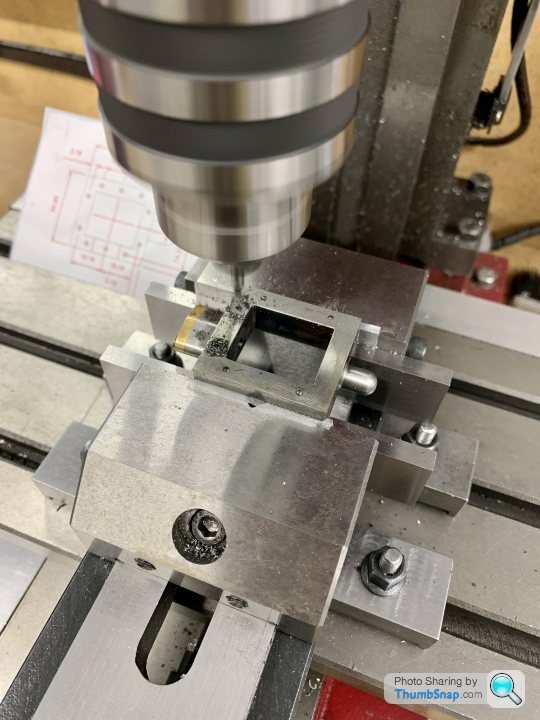
Through-drilled to 7BA clearance:
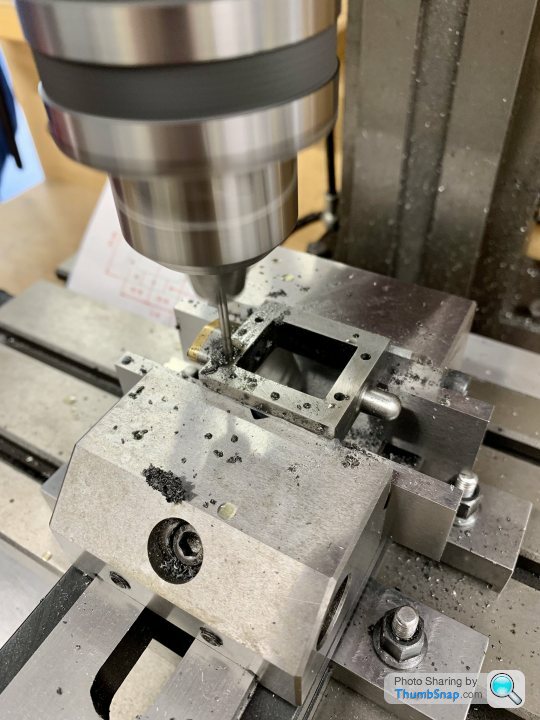
I thought the drill might wander on contact, hence why I initially used centre drilling, but in the event it was fine.
Then drilled and tapped one 7BA hole, over where the steam inlet will be:
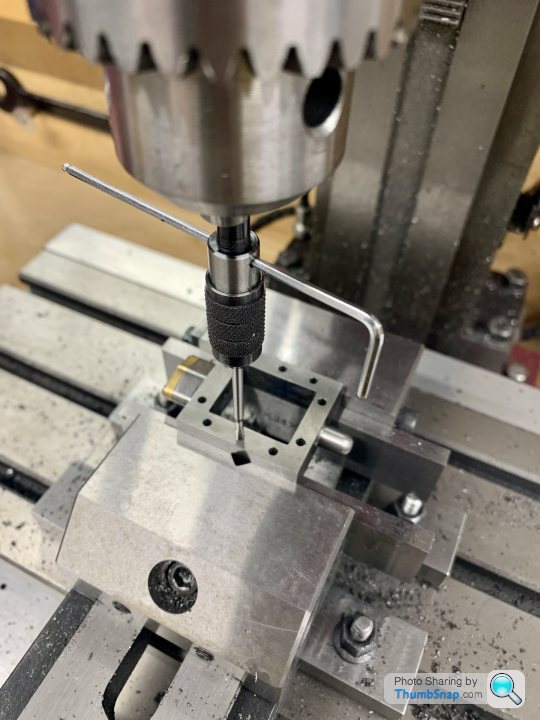
Finished by hand countersinking all the holes.
The drilled chests:
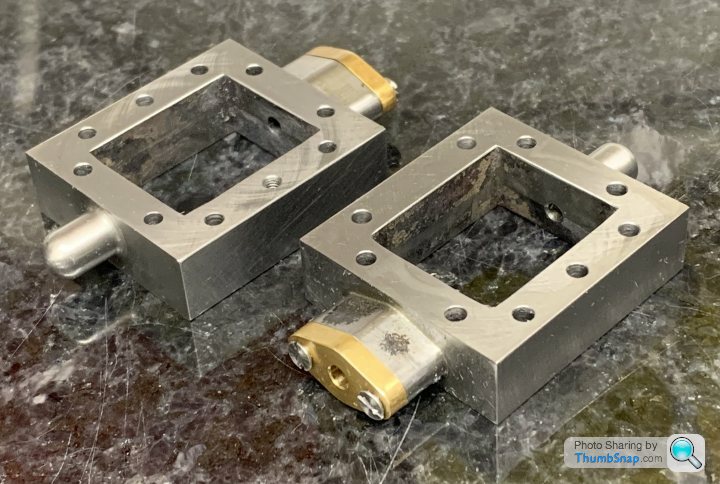
Test fitted to the cylinders using bolts:
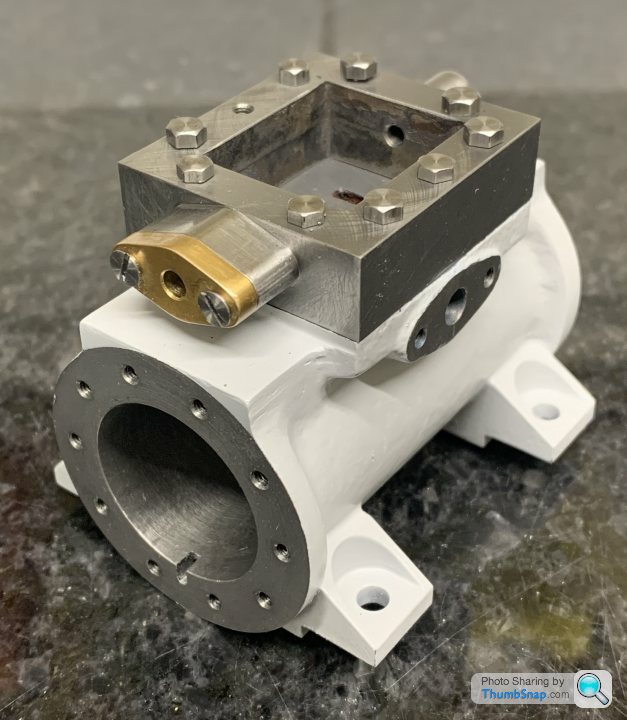

So far so good. The only thing left to do on the chests is to drill the steam inlet holes, and the mount holes for the inlet boxes.
Gassing Station | Scale Models | Top of Page | What's New | My Stuff