Torsion box alcove shelving - what size wood/mdf
Discussion
We're going to build some shelving in our alcoves. Looking to make torsion boxes which will be sandwiched between mdf and then painted. But struggling to decide what thickness timber to use for the boxes and the mdf top and bottom.
Span is about 115cm on side and about 145cm the other. Will be holding books so need to be reasonably sturdy
Any advice? I've seen lots of examples on line, but not many specify sizing used.
Span is about 115cm on side and about 145cm the other. Will be holding books so need to be reasonably sturdy
Any advice? I've seen lots of examples on line, but not many specify sizing used.
Doesn't matter much, the strength comes from the stiffness of the front strip you put on.
Mine used 2" x 1" for for the frames with 12 mm MDF because that's was the most sensible of the standard sizes timer yards hold. The MDF was the thinnest oak veneered I could find, there's not much to save by going thinner, but you could.
The fronts I used were roughly 2" x 2" ash, which give most of the strength to the shelf.
Mine used 2" x 1" for for the frames with 12 mm MDF because that's was the most sensible of the standard sizes timer yards hold. The MDF was the thinnest oak veneered I could find, there's not much to save by going thinner, but you could.
The fronts I used were roughly 2" x 2" ash, which give most of the strength to the shelf.
paulrockliffe said:
Doesn't matter much, the strength comes from the stiffness of the front strip you put on.
Mine used 2" x 1" for for the frames with 12 mm MDF because that's was the most sensible of the standard sizes timer yards hold. The MDF was the thinnest oak veneered I could find, there's not much to save by going thinner, but you could.
The fronts I used were roughly 2" x 2" ash, which give most of the strength to the shelf.
If the OP is effectively manufacturing a sandwich panel (not really a torsion box, as there's no torsion involved: it's a simply supported beam in bending), then this isn't the case: the top and bottom skins do most of the work (top skin is in compression, bottom skin in tension; the separating strips are 'webs' on the neutral axis and are mainly there to stabilise the skins).Mine used 2" x 1" for for the frames with 12 mm MDF because that's was the most sensible of the standard sizes timer yards hold. The MDF was the thinnest oak veneered I could find, there's not much to save by going thinner, but you could.
The fronts I used were roughly 2" x 2" ash, which give most of the strength to the shelf.
If you do it properly, then the thickness of the MDF can be surprisingly small (though plywood would be better than MDF, as MDF is nothing special in tension and will 'creep' over time).
The more they are spaced apart, the stiffer the structure will be (you're placing the skins further from the neutral axis, so making them work harder), but beyond that, it's going to be a compromise between aesthetics, the spacing of the shelves, and the amount of weight you're putting on them.
wolfracesonic said:
I'd make the internal 'ribs' a minimum 50mm deep with the top and bottom skins out of 18mm ply...
Obviously thick ply will work (it will just be heavier), but if you want to go all Colin Chapman/Aero Engineer, much thinner ply, with deeper ribs (to give the same overall thickness) would be very nearly the same stiffness, but much lighter and cheaper... for example instead of 18+50+18 = 86mm, try 6+75+6 = 87mm. - and that would still be overkill. I'd suggest that 6+50+6 would be more than adequate for a bookshelf.By way of interesting comparison, aircraft floors are frequently made out of sandwich panels of 1" thickness honeycomb cores with 0.75mm thick GRP skins (more relevant than it sounds - plywood is surprisingly close to GRP in strength/stiffness), and the floor on a Marcos sports car was 2 x 3mm plywood skins with 1/2" (12mm) spacer ribs.
Sandwich panels can be phenomenally stiff, if you manufacture them correctly.

uluru said:
Perhaps it's too early in the morning for me, but how can a sandwich of 2 x 1 plus two layers of 12mm MDF be fronted by a 2 x 2 piece of wood?
It's a good question, I definitely ran the 2 x 1 through the thicknesser so the total thickness matched the fronts, and the the fronts are probably 2 1/2 or 2 1/4 too. Equus said:
paulrockliffe said:
Doesn't matter much, the strength comes from the stiffness of the front strip you put on.
Mine used 2" x 1" for for the frames with 12 mm MDF because that's was the most sensible of the standard sizes timer yards hold. The MDF was the thinnest oak veneered I could find, there's not much to save by going thinner, but you could.
The fronts I used were roughly 2" x 2" ash, which give most of the strength to the shelf.
If the OP is effectively manufacturing a sandwich panel (not really a torsion box, as there's no torsion involved: it's a simply supported beam in bending), then this isn't the case: the top and bottom skins do most of the work (top skin is in compression, bottom skin in tension; the separating strips are 'webs' on the neutral axis and are mainly there to stabilise the skins).Mine used 2" x 1" for for the frames with 12 mm MDF because that's was the most sensible of the standard sizes timer yards hold. The MDF was the thinnest oak veneered I could find, there's not much to save by going thinner, but you could.
The fronts I used were roughly 2" x 2" ash, which give most of the strength to the shelf.
If you do it properly, then the thickness of the MDF can be surprisingly small (though plywood would be better than MDF, as MDF is nothing special in tension and will 'creep' over time).
The more they are spaced apart, the stiffer the structure will be (you're placing the skins further from the neutral axis, so making them work harder), but beyond that, it's going to be a compromise between aesthetics, the spacing of the shelves, and the amount of weight you're putting on them.
The only reason to take a different approach is if you wanted to spend the absolute bare minimum on the job, and if that was the case you wouldn't be asking on here, you you'd be doing some maths.
paulrockliffe said:
That's all true, but rather than going for an aircraft grade structural design, most people just put a stiff front on to stop the panels drooping.
Oh, absolutely - but the OP was specifically asking about a 'torsion box' construction, not the usual simple plank with a leading edge stiffener.44 x 44 timber baten screwed to the wall full width of shelf along the back and two battens each end less 15mm of overall shelf depth .
Dependent on shelf depth but let's say up to 250mm.
Grap yourself a sheet of 12mm mdf and per shelf 2 x 44x44 mm timber the length of the finished shelves less 90mm.. Set the first piece of 44mm section 45 mm back ie inset from the back of the shelf your making and glue and screw from both sides through the mdf, Screw and glue the other 44x 44mm section of timber flush with the front of the Mdf. . Add a piece of 12mm mdf to the front of the shelf (height 68mm) to finish the front edge off. Sand and prime ready for install .
Slide the shelf over the battens already fixed to the wall, screw through mdf to attached to wall battens .... fill screw holes and paint.. it will easily take weight of books etc if battens are fixed correctly to the wall.
It doesn't have to 44 x 44mm timber , it could be 40 x 40 for example or 50 x 50. Just depends on what you can source .
Job done. Don't get lost in the science
Dependent on shelf depth but let's say up to 250mm.
Grap yourself a sheet of 12mm mdf and per shelf 2 x 44x44 mm timber the length of the finished shelves less 90mm.. Set the first piece of 44mm section 45 mm back ie inset from the back of the shelf your making and glue and screw from both sides through the mdf, Screw and glue the other 44x 44mm section of timber flush with the front of the Mdf. . Add a piece of 12mm mdf to the front of the shelf (height 68mm) to finish the front edge off. Sand and prime ready for install .
Slide the shelf over the battens already fixed to the wall, screw through mdf to attached to wall battens .... fill screw holes and paint.. it will easily take weight of books etc if battens are fixed correctly to the wall.
It doesn't have to 44 x 44mm timber , it could be 40 x 40 for example or 50 x 50. Just depends on what you can source .
Job done. Don't get lost in the science

Edited by Wozy68 on Sunday 26th November 22:03
I did this in our front room a few years ago. They are unbelievably strong, I can stand on the lower ones and I'm 88kg!
I used 44x44, which turned out to be about 38mm, for the framing and 6mm ply for the surfaces. I came up with the sizes by working out how many shelves I wanted and how thick they would need to be without looking weird.
I made a ladder type frame, screwed to the wall on 3 sides, then shaped the ply to fit and glued and clamped them all together.
For the front edge I used car body filler which I sanded to a smooth finish before painting.
If I was doing it again, I would maybe go for 9mm ply or use more intermediate spans. They are a little bit like a drum, the TV can make the shelf vibrate at a certain resonance.
There's a few pictures of mine below. The cat always has to have final sign off of any of my DIY projects.
Shelf1 by ph mc, on Flickr
Shelf3 by ph mc, on Flickr
Shelf2 by ph mc, on Flickr
Shelf4 by ph mc, on Flickr
edited for silly linking photos
I used 44x44, which turned out to be about 38mm, for the framing and 6mm ply for the surfaces. I came up with the sizes by working out how many shelves I wanted and how thick they would need to be without looking weird.
I made a ladder type frame, screwed to the wall on 3 sides, then shaped the ply to fit and glued and clamped them all together.
For the front edge I used car body filler which I sanded to a smooth finish before painting.
If I was doing it again, I would maybe go for 9mm ply or use more intermediate spans. They are a little bit like a drum, the TV can make the shelf vibrate at a certain resonance.
There's a few pictures of mine below. The cat always has to have final sign off of any of my DIY projects.
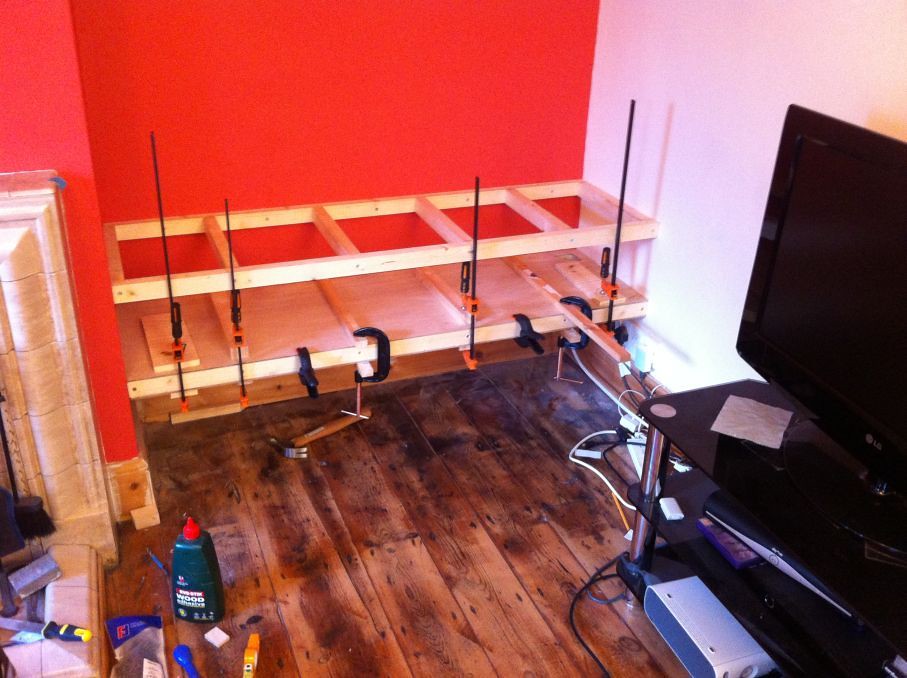
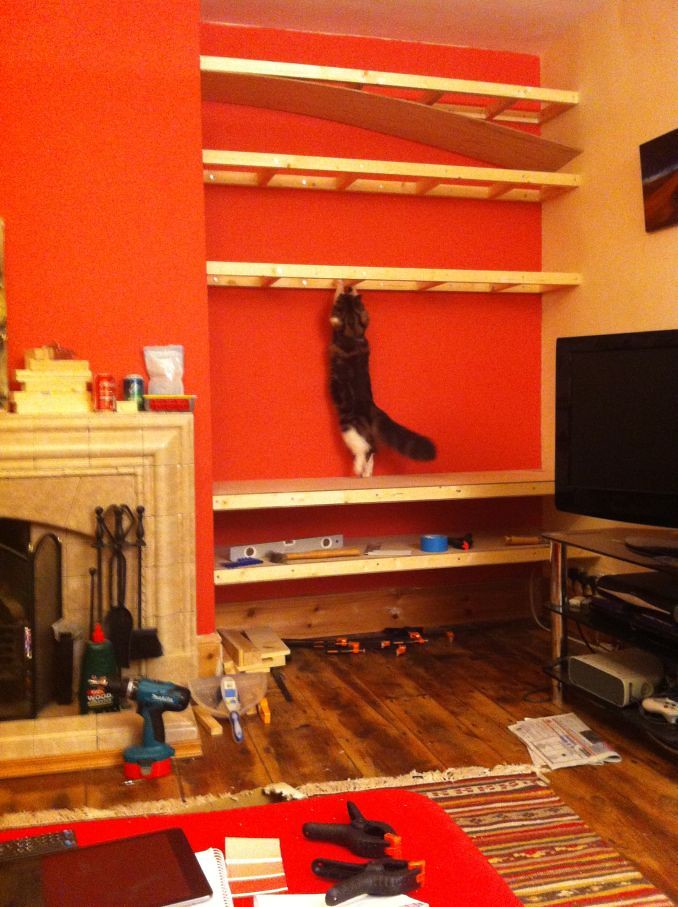
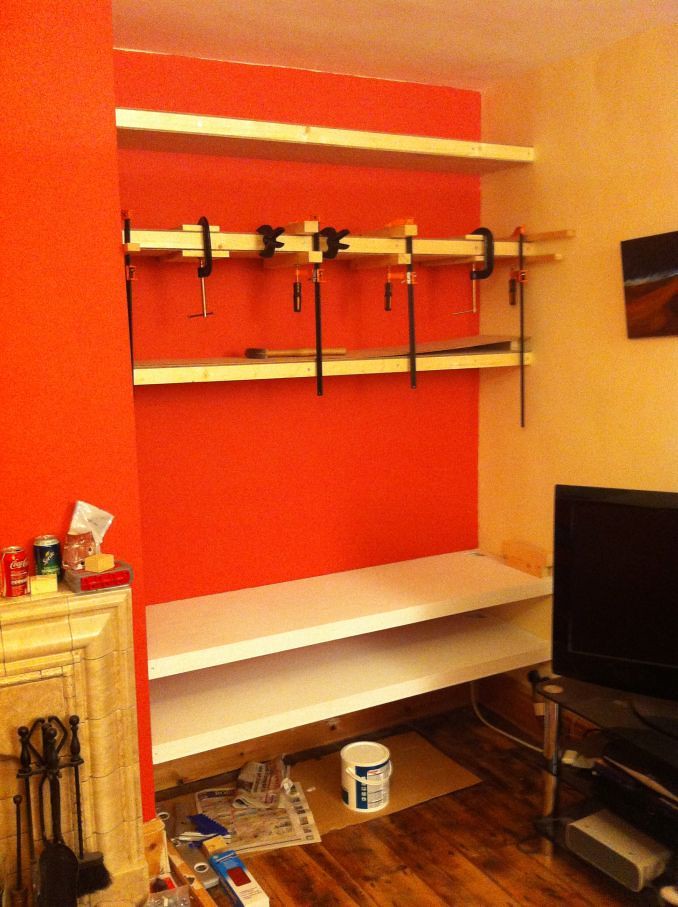
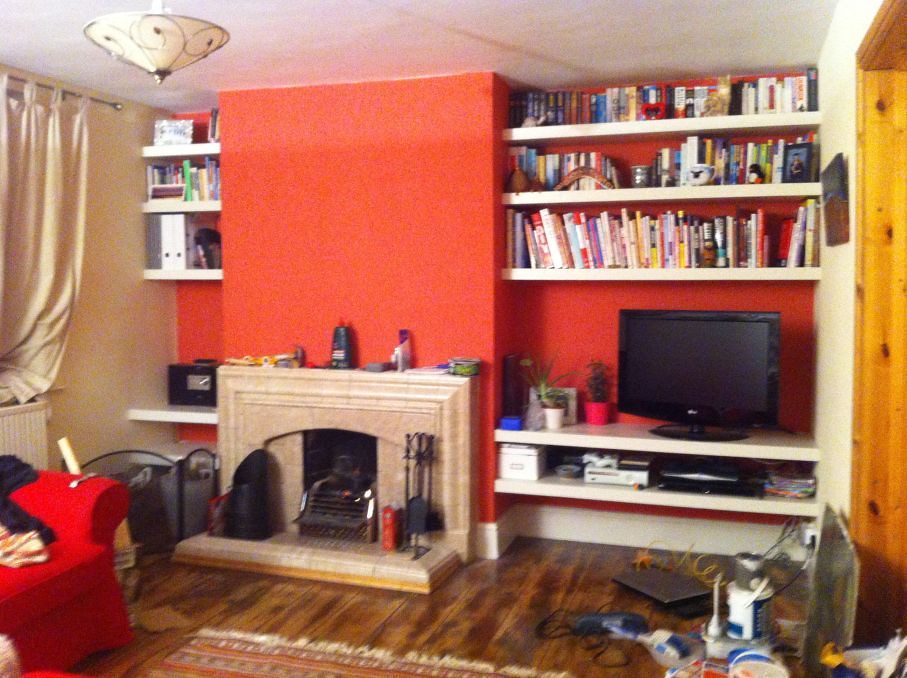
edited for silly linking photos
Edited by Pamoothican on Monday 27th November 13:48
On the advice of not getting bogged down with the science we ended up with 12mm mdf top and bottom - 12mm as slightly stiffer meant easier to cut down and mdf as easier to get a decent painted finish - and 34mm battens as the sandwich then ended up an what looked like the right sort of thickness. Glued and screwed then painted
Turned out ok, although took an age as wonky walls meant we had to template every shelf
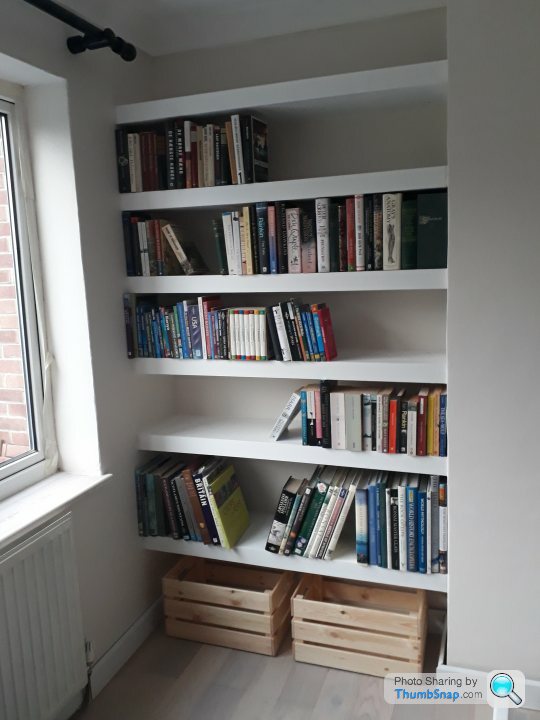
As well as the alcove shelves we have them extending round the corner, we were unsure prior to finishing whether we'd have to add additional support to the open end but they feel really solid without (the tv will be wall mounted above once we sort a bracket for the odd spacing on the tv - thanks sony)
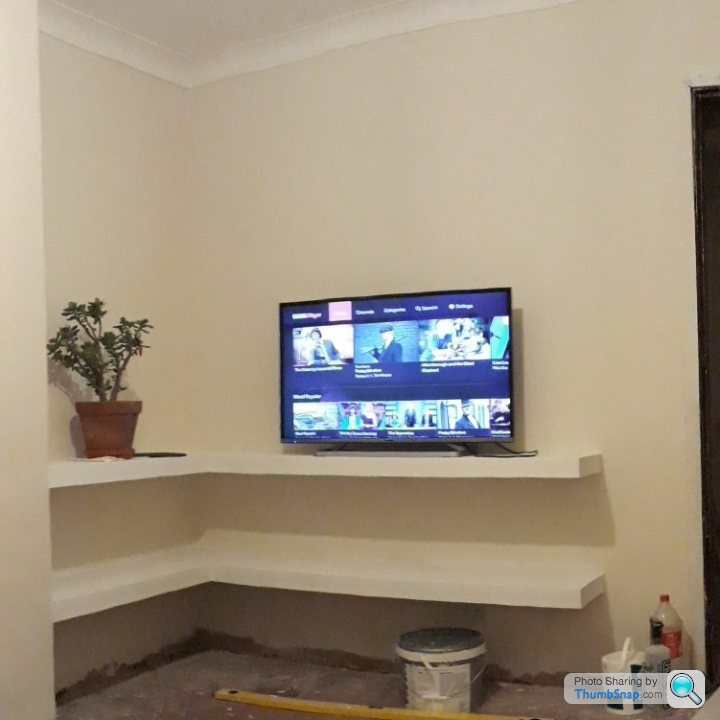
Turned out ok, although took an age as wonky walls meant we had to template every shelf
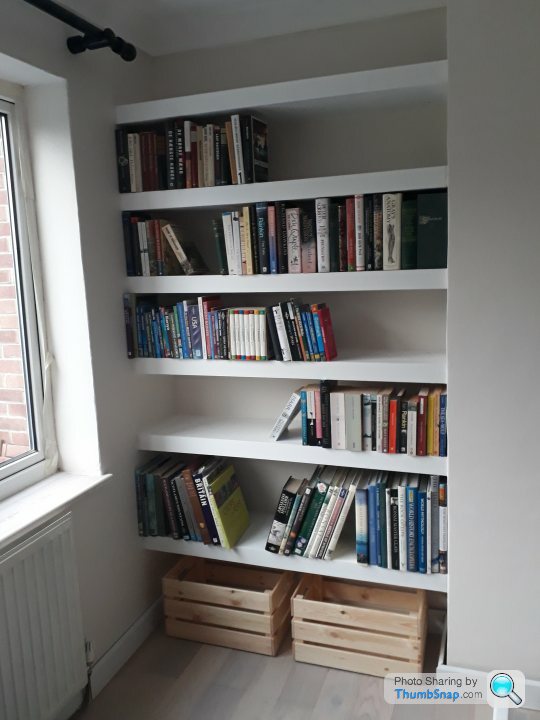
As well as the alcove shelves we have them extending round the corner, we were unsure prior to finishing whether we'd have to add additional support to the open end but they feel really solid without (the tv will be wall mounted above once we sort a bracket for the odd spacing on the tv - thanks sony)
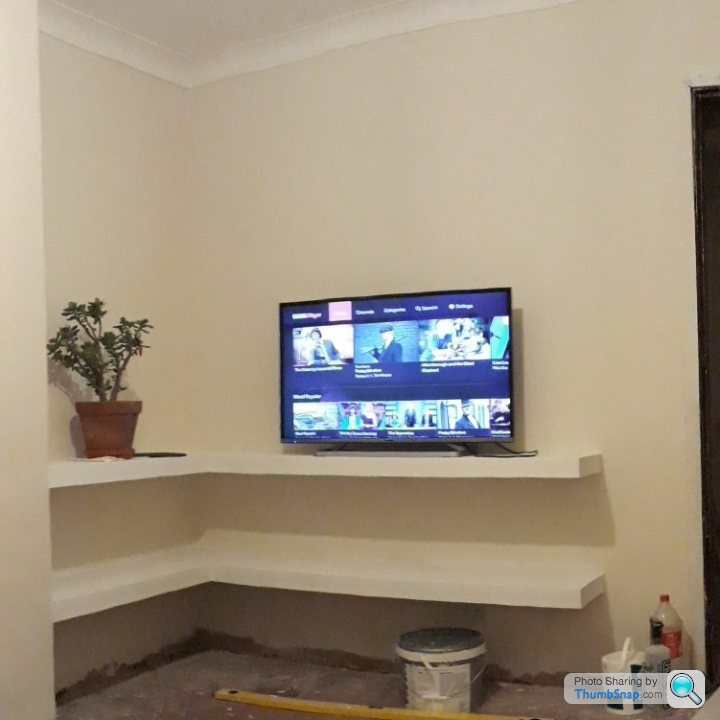
Gassing Station | Homes, Gardens and DIY | Top of Page | What's New | My Stuff