SpaceX Tuesday...
Discussion
djdest said:
If you had no gimbals you wouldn't have a gyroscope!
You know what a gyroscope is made of?
Well, yes, traditional gyros use gimbals but I was inferring that mounting one inside another gimbal would kinda defeat the purpose. Not all gyroscopes use gimbals though, there are many solid state and optical types.You know what a gyroscope is made of?

I doubt it's the gyros that are the problem though, after all the rockets themselves obviously have extremely good gyros, as will pretty much every 'normal' payload.
I'd imagine having to design the spooks' extreme cutting edge instruments to absorb severe loads in one plane to survive launch is enough of a hassle without worrying bracing for shocks in other orientations.
loudlashadjuster said:
I'd imagine having to design the spooks' extreme cutting edge instruments to absorb severe loads in one plane to survive launch is enough of a hassle without worrying bracing for shocks in other orientations.
It could simply be that the payload is relatively long but thin, so horizontal integration would place unacceptable bending loads on it, especially at its attachment point to the launcherMartG said:
loudlashadjuster said:
I'd imagine having to design the spooks' extreme cutting edge instruments to absorb severe loads in one plane to survive launch is enough of a hassle without worrying bracing for shocks in other orientations.
It could simply be that the payload is relatively long but thin, so horizontal integration would place unacceptable bending loads on it, especially at its attachment point to the launchershalmaneser said:
MartG said:
loudlashadjuster said:
I'd imagine having to design the spooks' extreme cutting edge instruments to absorb severe loads in one plane to survive launch is enough of a hassle without worrying bracing for shocks in other orientations.
It could simply be that the payload is relatively long but thin, so horizontal integration would place unacceptable bending loads on it, especially at its attachment point to the launcherIf it is a structural issue then SpaceX could simply install temporary supports inside the fairing which are removed once it is vertical.
However if it is something else within the payload e.g. a sensitive optical system , then fitting the payload once the launcher is vertical at the pad would seem the simplest & cheapest way forward
However if it is something else within the payload e.g. a sensitive optical system , then fitting the payload once the launcher is vertical at the pad would seem the simplest & cheapest way forward
MartG said:
If it is a structural issue then SpaceX could simply install temporary supports inside the fairing which are removed once it is vertical.
However if it is something else within the payload e.g. a sensitive optical system , then fitting the payload once the launcher is vertical at the pad would seem the simplest & cheapest way forward
Doubt that would be either simple or cheap. The satellites are built and loaded in some degree of clean room conditions, can't imagine it would be trivial maintaining these transporting it to the pad, up a 70 m platform and into the vehicle.However if it is something else within the payload e.g. a sensitive optical system , then fitting the payload once the launcher is vertical at the pad would seem the simplest & cheapest way forward
loudlashadjuster said:
MartG said:
If it is a structural issue then SpaceX could simply install temporary supports inside the fairing which are removed once it is vertical.
However if it is something else within the payload e.g. a sensitive optical system , then fitting the payload once the launcher is vertical at the pad would seem the simplest & cheapest way forward
Doubt that would be either simple or cheap. The satellites are built and loaded in some degree of clean room conditions, can't imagine it would be trivial maintaining these transporting it to the pad, up a 70 m platform and into the vehicle.However if it is something else within the payload e.g. a sensitive optical system , then fitting the payload once the launcher is vertical at the pad would seem the simplest & cheapest way forward
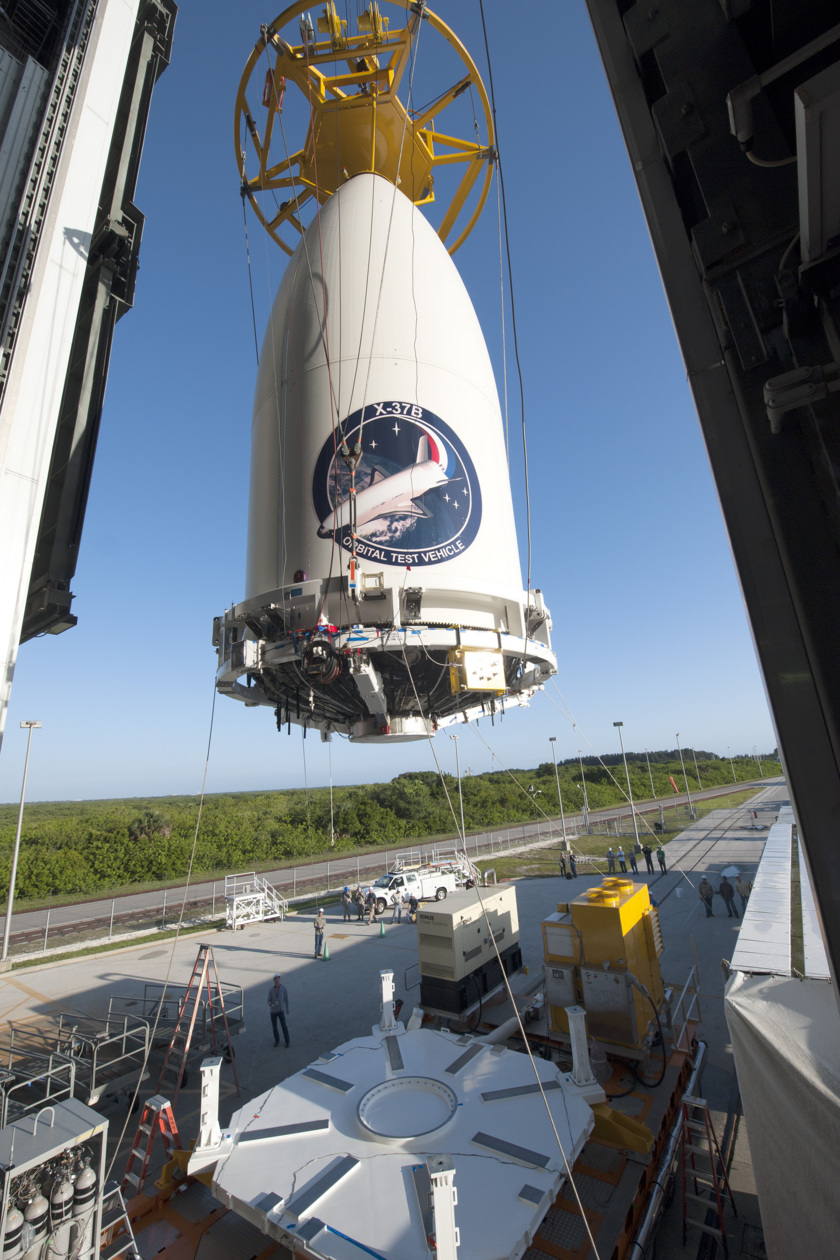
MartG said:
If it is a structural issue then SpaceX could simply install temporary supports inside the fairing which are removed once it is vertical.
However if it is something else within the payload e.g. a sensitive optical system , then fitting the payload once the launcher is vertical at the pad would seem the simplest & cheapest way forward
Optical system would be my guess as well, large complex mirrors and lenses, especially where NRO is concerned.However if it is something else within the payload e.g. a sensitive optical system , then fitting the payload once the launcher is vertical at the pad would seem the simplest & cheapest way forward
They had 3" resolution in the '60s, who knows what it is now.
annodomini2 said:
MartG said:
If it is a structural issue then SpaceX could simply install temporary supports inside the fairing which are removed once it is vertical.
However if it is something else within the payload e.g. a sensitive optical system , then fitting the payload once the launcher is vertical at the pad would seem the simplest & cheapest way forward
Optical system would be my guess as well, large complex mirrors and lenses, especially where NRO is concerned.However if it is something else within the payload e.g. a sensitive optical system , then fitting the payload once the launcher is vertical at the pad would seem the simplest & cheapest way forward
They had 3" resolution in the '60s, who knows what it is now.
You have to question what the NRO have in active service if those are already outmoded.
ETA, sounds like a made-up story. Read here. https://www.popsci.com/technology/article/2012-06/...
loudlashadjuster said:
MartG said:
If it is a structural issue then SpaceX could simply install temporary supports inside the fairing which are removed once it is vertical.
However if it is something else within the payload e.g. a sensitive optical system , then fitting the payload once the launcher is vertical at the pad would seem the simplest & cheapest way forward
Doubt that would be either simple or cheap. The satellites are built and loaded in some degree of clean room conditions, can't imagine it would be trivial maintaining these transporting it to the pad, up a 70 m platform and into the vehicle.However if it is something else within the payload e.g. a sensitive optical system , then fitting the payload once the launcher is vertical at the pad would seem the simplest & cheapest way forward
In the image below you can see that the structure has been swung back into the "stored" position in readiness for launch.

The next pictures shows the structure closed over the Shuttle. It was enormous.
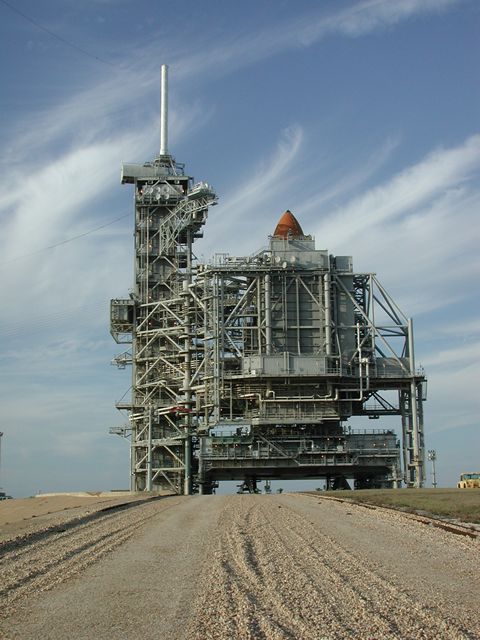
Trying again - live in about 35 mins https://www.youtube.com/watch?v=-p-PToD2URA
Eric Mc said:
Many payloads are loaded onto the rocket at the pad. For decades it has been possible to surround the top of a rocket in "clean room conditions". In fact, the huge "Payload Structure" that was part of Pads 39A and 329B during the Shuttle era were precisely that, clean rooms which allowed work to be carried out on Shuttle payloads whilst the vehicle was sitting on the pad.
In the image below you can see that the structure has been swung back into the "stored" position in readiness for launch.
The next pictures shows the structure closed over the Shuttle. It was enormous.
Yes, eminently possible, but I think those photos demonstrate it wouldn't be very cheap to adapt for Falcon (of one type, never mind two), nor would it seem to provide the lowest ongoing costs which is pretty much what SpaceX is all about.In the image below you can see that the structure has been swung back into the "stored" position in readiness for launch.
The next pictures shows the structure closed over the Shuttle. It was enormous.
Presumably the USAF money aimed at the use of the VAB?
loudlashadjuster said:
Yes, eminently possible, but I think those photos demonstrate it wouldn't be very cheap to adapt for Falcon (of one type, never mind two), nor would it seem to provide the lowest ongoing costs which is pretty much what SpaceX is all about.
Presumably the USAF money aimed at the use of the VAB?
The USAF had no involvement in the construction of the VAB nort have they any involvement with SLS either. They were obviously heavilly involved in the Shuttle programme (until the Challenger accident) so they probably had some requirements that need the VAB to be amended to suit their needs during the Shuttle programme.Presumably the USAF money aimed at the use of the VAB?
loudlashadjuster said:
Presumably the USAF money aimed at the use of the VAB?
SpaceX couldn't use Pad 39A for a vehicle erected in the VAB as their horizontal integration building blocks the old crawlerway between the pad and the VAB. LC40 is not accessible from the VAB.If they were to follow the NASA model of VAB and mobile launcher carrying a vertical launcher, all three current facilities ( 2 in Florida, one at Vandenberg ) would require a new VAB to be built, and a new mobile launcher to be developed and built - the one for 39A would need to be able to keep the payload vertical while ascending the slope to the pad.
Much simpler & cheaper to continue moving the launcher to the pad horizontally, then fitting the payload once the vehicle is vertical.
Atomic12C said:
Watched the launch earlier - near the end of second engine cut off there was a growing leak of gas/liquid near the base of the thruster cone where it attaches to stage 2. Anyone else expecting the screens to suddenly go blank?
I watched it too, but I thought that was just a boiloff valve.Gassing Station | Science! | Top of Page | What's New | My Stuff