An interesting time to be a car fan?
Discussion
benny.c said:
I had an extended drive of my brother-in-law’s e-tron 55 the other day. I know it’s an SUV and not meant to be that exciting but by Christ it’s dull. Our crappy school run up! is ten times more entertaining to drive. Ditto the Hemi Grand Cherokee I had and even the tractor of a Wrangler I currently drive daily. I think I’m a dinosaur.
They gave me an e-tron as a loaner when the Taycan went in for software updates. Let’s just say I’m glad it was only for the day. Edited by benny.c on Monday 20th June 21:57

TheDeuce said:
2 years and 20k. You definitely need a test drive because I don't think there's any other way of convincing a car person that a two plus tonne SUV can actually behave in a fun and sporty manner. It would fail quickly on a track but on the open road... It's insane how hard you can push it without it feeling flawed by size/weight. I'll probably get flamed on here for saying that...
You'd need a full day with it ideally. My first hour or so testing it I actually wasn't impressed because part of my head simply refused to accept such a car could be acceptable
ETA: it's obviously not on Taycan level but if you appreciate practicality and luxury along with sportiness, hard to beat.
That sounds great, plenty of time to get to know it then You'd need a full day with it ideally. My first hour or so testing it I actually wasn't impressed because part of my head simply refused to accept such a car could be acceptable

ETA: it's obviously not on Taycan level but if you appreciate practicality and luxury along with sportiness, hard to beat.
Edited by TheDeuce on Tuesday 21st June 19:07

I've been watching quite a few reviews on it, they all seem very good! My brother's friend has one, they love it, saying it's not just a good electric car, bit a great car full stop.
Max_Torque said:
Just for reference valve springs hardly consume any power or create any parasitic drag because the energy used to compress the spring on the camshaft opening ramp is mostly returned on the closing ramp, where the spring actually pushes the cam around rather than vise versa! Hysteric losses are there, but for metal valve springs they are only a few percent at max. Yes, there are frictional loses, but for modern cam geometries these are also fairly small.
I'd like to test that to see just how much torque is required. If what you're saying is true, it should be possible to turn a camshaft by hand using the camshaft pulley. I've never tried it, and I may be wrong, but I imagine it could not be done.jamesbilluk said:
TheDeuce said:
2 years and 20k. You definitely need a test drive because I don't think there's any other way of convincing a car person that a two plus tonne SUV can actually behave in a fun and sporty manner. It would fail quickly on a track but on the open road... It's insane how hard you can push it without it feeling flawed by size/weight. I'll probably get flamed on here for saying that...
You'd need a full day with it ideally. My first hour or so testing it I actually wasn't impressed because part of my head simply refused to accept such a car could be acceptable
ETA: it's obviously not on Taycan level but if you appreciate practicality and luxury along with sportiness, hard to beat.
That sounds great, plenty of time to get to know it then You'd need a full day with it ideally. My first hour or so testing it I actually wasn't impressed because part of my head simply refused to accept such a car could be acceptable

ETA: it's obviously not on Taycan level but if you appreciate practicality and luxury along with sportiness, hard to beat.
Edited by TheDeuce on Tuesday 21st June 19:07

I've been watching quite a few reviews on it, they all seem very good! My brother's friend has one, they love it, saying it's not just a good electric car, bit a great car full stop.
Also as a ground up EV, and this is where I get back on topic, they were able to throw out the rule book in terms of car layout. Hence the wheels pushed right into each corner, the stubby bonnet, the batteries mounted as low as possible and a flat rear floor. At present a lot of EVs are either adapted ICE platforms or new platforms designed to accommodate electric AND ice powertrains. You can imagine the compromises.
I expect many more ground up EV platforms over the next few years - there has to be, the lifespan of being able to sell ICE cars is now close to being within the development time of a new platform.
gmaz said:
I'd like to test that to see just how much torque is required. If what you're saying is true, it should be possible to turn a camshaft by hand using the camshaft pulley. I've never tried it, and I may be wrong, but I imagine it could not be done.
what? Think about it :-)Have you noticed when you change a cambelt that the cam wants to "jump" into another position when you take the belt off? because when free'd from the crank it will jump around and spin until the net clockwise and net counter clockwise forces are balanced. If you were strong enough to turn the cam by hand, you would indeed feel the load go up as the spring is compressed and then the cam will jump out of your hand and spin round as the spring pushes the cam round on the closing ramp
This causes what we call camtrain torsion vibration and is a major issue in cam drive design, however as mentioned the forces sum to very nearly zero so the overall power losses are small.
Max_Torque said:
gmaz said:
I'd like to test that to see just how much torque is required. If what you're saying is true, it should be possible to turn a camshaft by hand using the camshaft pulley. I've never tried it, and I may be wrong, but I imagine it could not be done.
what? Think about it :-)Have you noticed when you change a cambelt that the cam wants to "jump" into another position when you take the belt off? because when free'd from the crank it will jump around and spin until the net clockwise and net counter clockwise forces are balanced. If you were strong enough to turn the cam by hand, you would indeed feel the load go up as the spring is compressed and then the cam will jump out of your hand and spin round as the spring pushes the cam round on the closing ramp
This causes what we call camtrain torsion vibration and is a major issue in cam drive design, however as mentioned the forces sum to very nearly zero so the overall power losses are small.
It's not a big win for ICE efficiency but its valid

Max_Torque said:
what? Think about it :-)
Have you noticed when you change a cambelt that the cam wants to "jump" into another position when you take the belt off? because when free'd from the crank it will jump around and spin until the net clockwise and net counter clockwise forces are balanced. If you were strong enough to turn the cam by hand, you would indeed feel the load go up as the spring is compressed and then the cam will jump out of your hand and spin round as the spring pushes the cam round on the closing ramp
This causes what we call camtrain torsion vibration and is a major issue in cam drive design, however as mentioned the forces sum to very nearly zero so the overall power losses are small.
I freely admit I've never done a cambelt change, so I'll defer to your knowledge on that one.Have you noticed when you change a cambelt that the cam wants to "jump" into another position when you take the belt off? because when free'd from the crank it will jump around and spin until the net clockwise and net counter clockwise forces are balanced. If you were strong enough to turn the cam by hand, you would indeed feel the load go up as the spring is compressed and then the cam will jump out of your hand and spin round as the spring pushes the cam round on the closing ramp
This causes what we call camtrain torsion vibration and is a major issue in cam drive design, however as mentioned the forces sum to very nearly zero so the overall power losses are small.
I'll have to get the cambelt off the wife's Yaris and move the camshaft back and forth with a torque wrench to check

This is obviously not a static situation either but I don't think it's clear that despite all that ICE complexity you guys are talking about that they don't last longer than EVs. ICE is at least well proven at this point and well capable of going for a very long time so not all these moving parts actual matter a whole lot when they're known quantity with a massive service industry to keep them running. There is much less to service in an EV of course but batteries are not just for Christmas and I don't know if the motors necessarily last forever either along with the inverters.
TheDeuce said:
He's right. Friction aside the energy used to compress a spring is reclaimed when it exerts the same energy against the element that compressed it in the first place.
It's not a big win for ICE efficiency but its valid
You may reclaim a lot of the energy when you turn the camshaft slowly, but, at high RPM the springs are struggling to return the valves to their seats, traditionally springs are sized to just eliminate 'valve float' at max revs. So at cruising revs, maybe 2/3 of the energy might be recovered?It's not a big win for ICE efficiency but its valid

Personally the only cams and belts I touch are Ducati Desmo engines, which only have baby springs to back up the closing cams.
Even so, the effort to turn the cams seems significant in terms of the effort to turn the crank, but I'd not guess at any numbers.
The torque to generate 50psi with the oil pump probably matters too?
gmaz said:
Max_Torque said:
what? Think about it :-)
Have you noticed when you change a cambelt that the cam wants to "jump" into another position when you take the belt off? because when free'd from the crank it will jump around and spin until the net clockwise and net counter clockwise forces are balanced. If you were strong enough to turn the cam by hand, you would indeed feel the load go up as the spring is compressed and then the cam will jump out of your hand and spin round as the spring pushes the cam round on the closing ramp
This causes what we call camtrain torsion vibration and is a major issue in cam drive design, however as mentioned the forces sum to very nearly zero so the overall power losses are small.
I freely admit I've never done a cambelt change, so I'll defer to your knowledge on that one.Have you noticed when you change a cambelt that the cam wants to "jump" into another position when you take the belt off? because when free'd from the crank it will jump around and spin until the net clockwise and net counter clockwise forces are balanced. If you were strong enough to turn the cam by hand, you would indeed feel the load go up as the spring is compressed and then the cam will jump out of your hand and spin round as the spring pushes the cam round on the closing ramp
This causes what we call camtrain torsion vibration and is a major issue in cam drive design, however as mentioned the forces sum to very nearly zero so the overall power losses are small.
I'll have to get the cambelt off the wife's Yaris and move the camshaft back and forth with a torque wrench to check

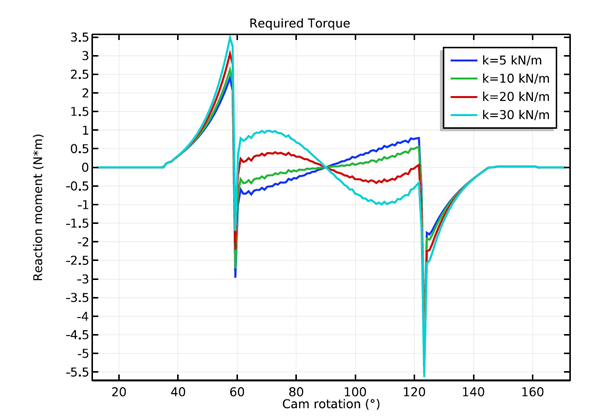
note the near net zero average torque! On the opening the cam puts energy into the spring as it compresses it, on the closing the spring releases that same energy back into the cam. The only loses are hysteretics in the material of the spring, which for steel springs are pretty small. Most of the actual loss in the valve train is frictional between the valves and guides and cam lobes and lifters, and also in the drive arrangement (ie belt / chain and bearings)
Max_Torque said:
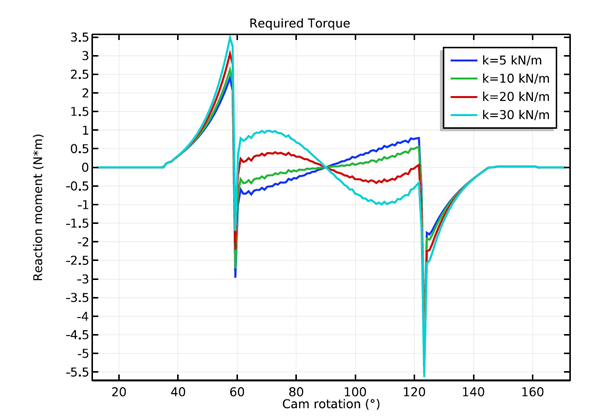
note the near net zero average torque! On the opening the cam puts energy into the spring as it compresses it, on the closing the spring releases that same energy back into the cam. The only loses are hysteretics in the material of the spring, which for steel springs are pretty small. Most of the actual loss in the valve train is frictional between the valves and guides and cam lobes and lifters, and also in the drive arrangement (ie belt / chain and bearings)
At high RPM, the closing of the valve will take all the spring's force to accelerate the valve and other bits, and the opening force will be roughly doubled as the came has to accelerate the hardware as well as compress the spring.
At moderate RPM, some of the energy will be recovered.
But putting any numbers to this seems quite hard, I recall a long and mildly futile debate about exactly what the loads on a Ducati timing belt would be.
Car timing belts are rated to carry quite a lot of power, and I don't believe car makers over-size things all that much.
There's also a more general point, energy going into (and back out of) reciprocating bits means the engine tends not to want to run at a constant angular speed. So we have DMFs and cush drives and other lossy stuff to blur the issues.
Lots of detail to look at, for the people chasing the last fraction of a % of efficiency..
OutInTheShed said:
TheDeuce said:
He's right. Friction aside the energy used to compress a spring is reclaimed when it exerts the same energy against the element that compressed it in the first place.
It's not a big win for ICE efficiency but its valid
You may reclaim a lot of the energy when you turn the camshaft slowly, but, at high RPM the springs are struggling to return the valves to their seats, traditionally springs are sized to just eliminate 'valve float' at max revs. So at cruising revs, maybe 2/3 of the energy might be recovered?It's not a big win for ICE efficiency but its valid

Personally the only cams and belts I touch are Ducati Desmo engines, which only have baby springs to back up the closing cams.
Even so, the effort to turn the cams seems significant in terms of the effort to turn the crank, but I'd not guess at any numbers.
The torque to generate 50psi with the oil pump probably matters too?
It's a spring.. other than friction you pretty much get out what you put into it overall!
The effort to turn the cams is significant because your arm can't reclaim the energy as it lurches forward after each quarter turn or whatever, and put that same energy into the next part turn. And the tolarances do mean that friction is a constant factor.
Yes the various ancillaries attached to any ICE all steal energy - and there's a fair few, which is one of the reasons they're not all that efficient. Hundreds of moving parts are never going to be efficient, every single one generates heat, noise, vibration. It's all wasted energy. A hermetically sealed electric motor straight through to an also sealed reduction box on to the axle is undeniably a better way to power the machine - if the challenge is to design the machine in the most efficient and logical manner.
TheDeuce said:
If a spring fails to fully return and doesn't feed that energy back into the cam, then roughly the same amount of energy lost is also saved the next time the cam compresses a not fully decompressed spring.
....r.
No, that's wrong, the spring has inertia and will be travelling towards the cam when the cam comes around again, increasing the force on the cam. If the spring hasn't caught up with the cam by then. Which it likely will have because the cam is maybe 120 degrees of opening and 240 degrees of base circle?....r.
I think there was an era of 2V pushrod engines where the valves were launched away from the cams at high RPM and a lot of 'lash' could actually be a good thing, up the point where it all got messy and expensive. Valve opening periods (angles) were less at lower RPM when the valves followed the cam profile closely, resulting in more low down grunt. There must be an art to getting that right!
I'm told that several manufacturers are working on less wasteful oil pumps.
Thinner oil to reduce viscous loss is a big thing.
Electric water pumps...
BorkBorkBork said:
The batteries were garbage because no one put any serious R&D $ into it. If just a fraction of the R&D budgets of the top manufacturers had gone into battery tech, like it is now, I suspect ICE would have died decades ago.
Sony's development of the lithium ion battery was a game changer indeed but quite along time ago now and design has changed that much since.Maybe solid state batteries will be another leap we will see. Batteries a much harder nut to crack than say Mores law for semiconductors where performance doubles every two years by just making the devices ever smaller to get more on the same chip for the same cost. Similarly the rapid progress in flat panel displays over the last 20 years.
granada203028 said:
Sony's development of the lithium ion battery was a game changer indeed but quite along time ago now and design has changed that much since.
Maybe solid state batteries will be another leap we will see. Batteries a much harder nut to crack than say Mores law for semiconductors where performance doubles every two years by just making the devices ever smaller to get more on the same chip for the same cost. Similarly the rapid progress in flat panel displays over the last 20 years.
Actually, vast amounts of research have gone into batteries and fuel cells over more than a century.Maybe solid state batteries will be another leap we will see. Batteries a much harder nut to crack than say Mores law for semiconductors where performance doubles every two years by just making the devices ever smaller to get more on the same chip for the same cost. Similarly the rapid progress in flat panel displays over the last 20 years.
OutInTheShed said:
TheDeuce said:
If a spring fails to fully return and doesn't feed that energy back into the cam, then roughly the same amount of energy lost is also saved the next time the cam compresses a not fully decompressed spring.
....r.
No, that's wrong, the spring has inertia and will be travelling towards the cam when the cam comes around again, increasing the force on the cam. If the spring hasn't caught up with the cam by then. Which it likely will have because the cam is maybe 120 degrees of opening and 240 degrees of base circle?....r.
I think there was an era of 2V pushrod engines where the valves were launched away from the cams at high RPM and a lot of 'lash' could actually be a good thing, up the point where it all got messy and expensive. Valve opening periods (angles) were less at lower RPM when the valves followed the cam profile closely, resulting in more low down grunt. There must be an art to getting that right!
I'm told that several manufacturers are working on less wasteful oil pumps.
Thinner oil to reduce viscous loss is a big thing.
Electric water pumps...
As for lower viscosity oil, that's all well and good. As is bio and synthetic fuel. But these things were explored to extend the life of ICE and they all make substantial improvements. But as I said, none of it can approach the efficiency of the simplified electric drivetrain and with the impending ICE bans, most such initiatives are losing momentum. You simply cannot have the complexity of all those moving parts and expect to compete on efficiency terms - you can make them 'more' efficient but never 'as' efficient as a machine that doesn't have the complexity in the first place.
OutInTheShed said:
granada203028 said:
Sony's development of the lithium ion battery was a game changer indeed but quite along time ago now and design has changed that much since.
Maybe solid state batteries will be another leap we will see. Batteries a much harder nut to crack than say Mores law for semiconductors where performance doubles every two years by just making the devices ever smaller to get more on the same chip for the same cost. Similarly the rapid progress in flat panel displays over the last 20 years.
Actually, vast amounts of research have gone into batteries and fuel cells over more than a century.Maybe solid state batteries will be another leap we will see. Batteries a much harder nut to crack than say Mores law for semiconductors where performance doubles every two years by just making the devices ever smaller to get more on the same chip for the same cost. Similarly the rapid progress in flat panel displays over the last 20 years.
Whoever eventually cracks the problem takes the entire world forward a leap and will make an unbelievable amount of money.
TheDeuce said:
More so than ever right now. For over a decade investment in firms developing solid state cells (the next thing after li-ion, no practical charge rate cap or number of cycles, no fire risk and a starting point of 2x energy density) but in recent years the investment has run into well over $100bn easily. The rate of investment at this point is suggestive that a commercial product isn't judged to be too far away and that there is subsequently a race on to get the first mass producible example proven and protected.
Whoever eventually cracks the problem takes the entire world forward a leap and will make an unbelievable amount of money.
I thought Toyota were pretty close?Whoever eventually cracks the problem takes the entire world forward a leap and will make an unbelievable amount of money.
quick Google...
https://uk.motor1.com/news/559246/toyota-solidstat...
Thought I read something about it. The tech will be expensive come 2025 though. Yup they go on to say as much in the article. I think the Prestige manufacturers will be able to make a case as they'll be able to double the battery cost and it will be part of the marketing. Lower weight or Double the range, pick your poison.
GT9 said:
LasseV said:
There are two interesting looking car coming, Hopium Machina and Hyundai Ioniq 6. Both looks very nice with futuristic streamliner lines.
The Machina is a lovely looking thing, but geez why would you go with Hopium for a hydrogen fuel cell car brand.Hopium in English is a combination of hope and opium, to describe the irrational addiction to hope when there is none...
ETA: There is also the open goal that was missed to use Protium instead.
Edited by GT9 on Sunday 19th June 21:20
Biggest problem of Hyundai's Ioniq 6 is that it is battery electric vehicle. Inferior grand tourer because of that.
Gassing Station | EV and Alternative Fuels | Top of Page | What's New | My Stuff