Building "Thor"
Discussion
These are the half shafts...
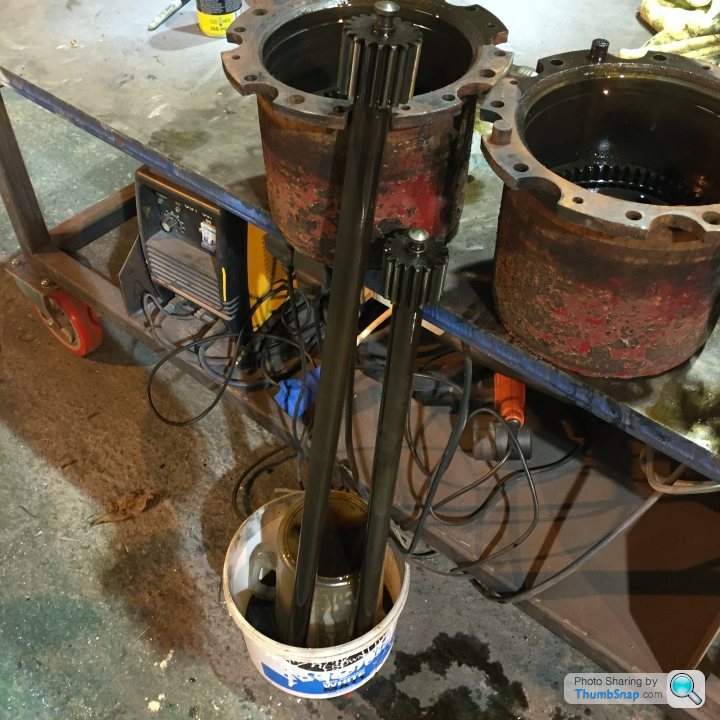
Remember that these parts are from a lorry built to carry 16 tonnes and weigh well over 20 tonnes.
The bearings are around 5" diameter and 2" deep. Even with the 'car' weighing around 6 tonnes it will just spin the rear wheels and smoke the tyres. I suspect I will only lock the second axle if I get stuck. But at least the torque will be split between the two.
It is difficult to get a feel for how substantial everything is from the photos.
Paul
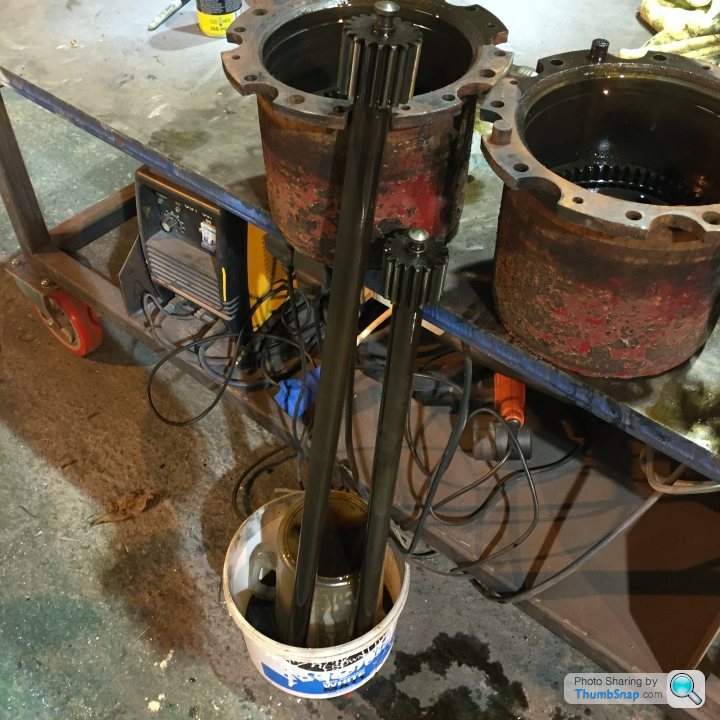
Remember that these parts are from a lorry built to carry 16 tonnes and weigh well over 20 tonnes.
The bearings are around 5" diameter and 2" deep. Even with the 'car' weighing around 6 tonnes it will just spin the rear wheels and smoke the tyres. I suspect I will only lock the second axle if I get stuck. But at least the torque will be split between the two.
It is difficult to get a feel for how substantial everything is from the photos.
Paul
Hugo a Gogo said:
is the engine all whitworth too I suppose?
I'm certain it would be. Probably all handmade[1] (and beautifully so) bolts, nuts etc. Although I suppose there is more of a chance of milspec stuff being stamped the old stuff like that is conspicuous by the absence of any markings on them. [1] By machine obviously, but none of this automated cranking out of masses of nuts/screws etc.
I dunno
Whitworth was invented to allow standardised industrialised construction
I imagine UK industry banged out millions of standard nuts and screws in those days
just reading up on it, wikipedia says they changed the size of the nuts and screw heads of BSW to match BSF in WW2, to save metal
I never did fully understand the sizes on my whitworth tool set! (working on old buses - stuff like Gardner engined Bristol Lodekkas would be the oldest)
Whitworth was invented to allow standardised industrialised construction
I imagine UK industry banged out millions of standard nuts and screws in those days
just reading up on it, wikipedia says they changed the size of the nuts and screw heads of BSW to match BSF in WW2, to save metal
I never did fully understand the sizes on my whitworth tool set! (working on old buses - stuff like Gardner engined Bristol Lodekkas would be the oldest)
No wheels on my chassis!
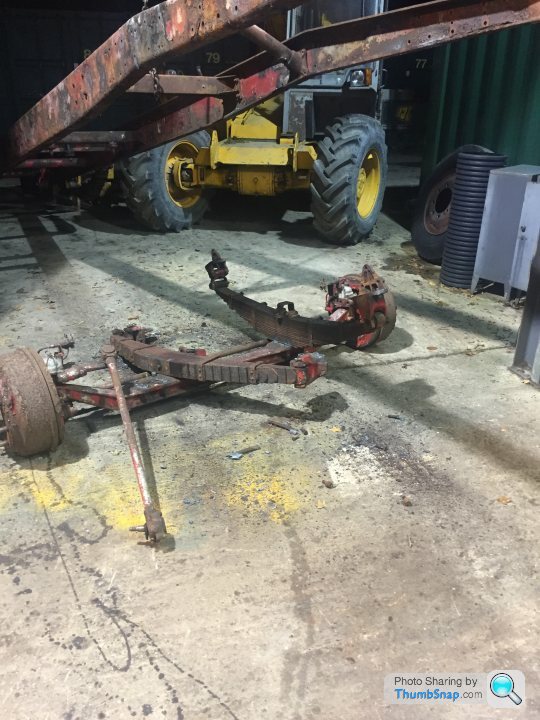
The workshop is a little emptier as I have stashed the bits away. They will come back out for cleaning/blasting and painting or refurbishment.
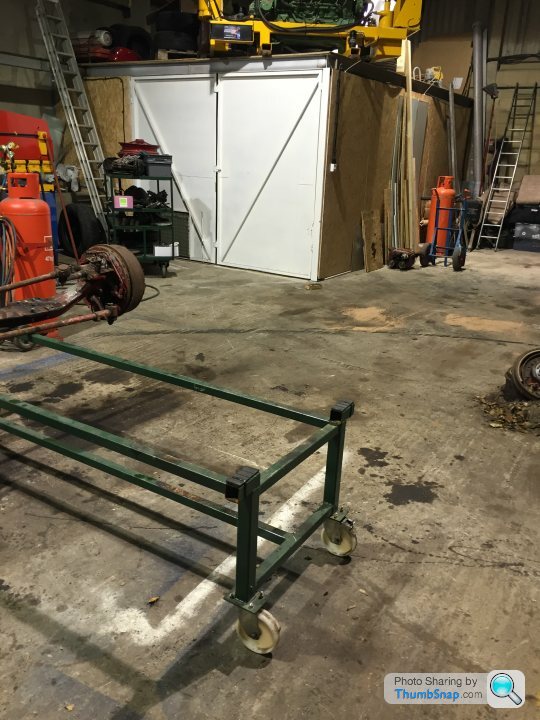
There will be a slow down on progress for a few days due to other commitments.
Some things that have become known now are.
Due to not using the reduction gears in the hubs the axles will need to be turned over to get wheel rotation correct.
This will necessitate the middle axle being the permanent driven one with the rear switchable.
It will not need a gizmo to increase engine speed, just a connection adaptor between engine and transmission.
Some interesting calculated stats are:-
300rpm in 1st = 8.18mph
750rpm in 2nd = 34 mph
500rpm in 3rd(top) = 33mph
1000rpm in 3rd = 67.6mph
1500rpm in 3rd = 101.4mph
2000rpm in 3rd = 135.2mph
2500rpm in 3rd = 169mph
Obviously the 2 fastest of those speeds are likely to be totally academic. But it will do over 100mph in second, which is nice!
I am not building a speed machine, this is about the theatre and challenging myself to build it.
The good thing is that I will not be artificially reducing the power/torque. The mass of gears and thick oil will do that for me!
Tyres are not going to be truck super singles as they are only rated to 75mph so I will be looking to our American cousins for suitable rubber to give the same rolling circumference.
It also maintains the aesthetics in my opinion.
Paul
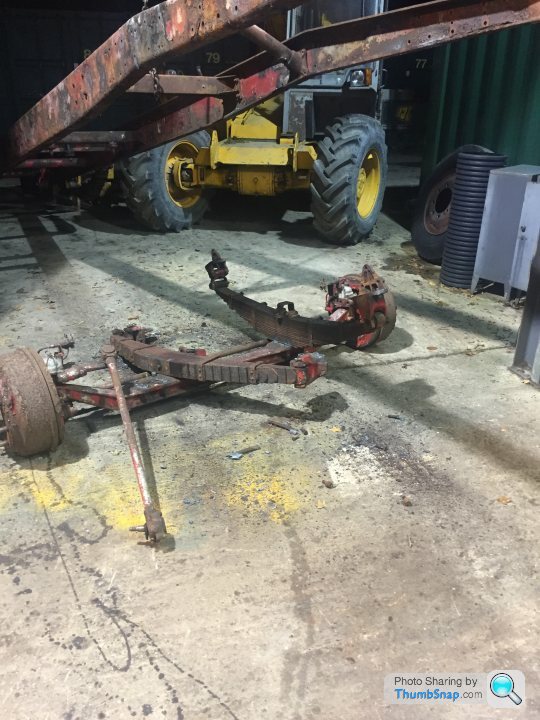
The workshop is a little emptier as I have stashed the bits away. They will come back out for cleaning/blasting and painting or refurbishment.
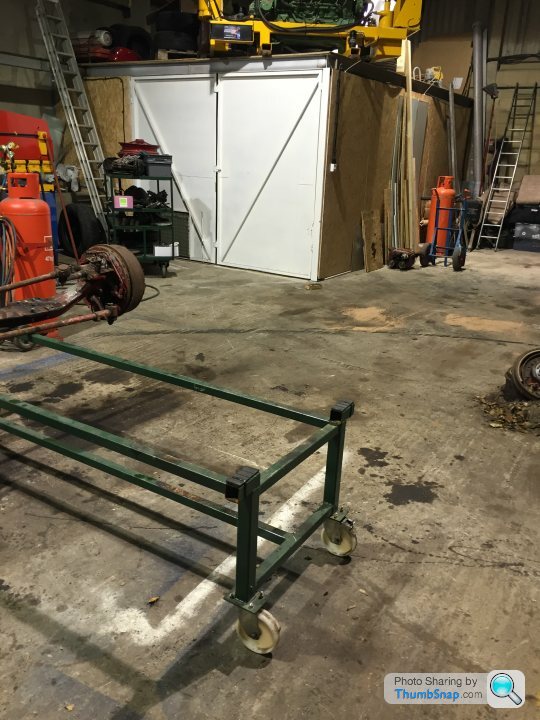
There will be a slow down on progress for a few days due to other commitments.
Some things that have become known now are.
Due to not using the reduction gears in the hubs the axles will need to be turned over to get wheel rotation correct.
This will necessitate the middle axle being the permanent driven one with the rear switchable.
It will not need a gizmo to increase engine speed, just a connection adaptor between engine and transmission.
Some interesting calculated stats are:-
300rpm in 1st = 8.18mph
750rpm in 2nd = 34 mph
500rpm in 3rd(top) = 33mph
1000rpm in 3rd = 67.6mph
1500rpm in 3rd = 101.4mph
2000rpm in 3rd = 135.2mph
2500rpm in 3rd = 169mph
Obviously the 2 fastest of those speeds are likely to be totally academic. But it will do over 100mph in second, which is nice!
I am not building a speed machine, this is about the theatre and challenging myself to build it.
The good thing is that I will not be artificially reducing the power/torque. The mass of gears and thick oil will do that for me!
Tyres are not going to be truck super singles as they are only rated to 75mph so I will be looking to our American cousins for suitable rubber to give the same rolling circumference.
It also maintains the aesthetics in my opinion.
Paul
Steve_D said:
After all that work you could have gone down to your local steel merchants and bought a couple of lengths of 'U' section and bolted them together with some cross members.
Just a thought.
Possibly. Although it wouldn't be a heavily modified truck chassis then and might fall foul of some DVLA regulation or somesuch. Although, having said that, I think this is going to be an "Agricultural Vehicle" so maybe it would be exempt from that. Just a thought.
Steve_D said:
After all that work you could have gone down to your local steel merchants and bought a couple of lengths of 'U' section and bolted them together with some cross members.
Just a thought.
Steve
But this way he is using the original chassis and axles, so much more a modified vehicle, as opposed to a "new build".Just a thought.
Steve
No new pictures to show but a brief update of progress.
The chassis is now completely stripped down to it's component parts ready for rust removal, blasting and a coat of primer.
I still have a little work to do on the axles, removing the remaining bearings and stub axle, prior to blasting and primer.
I have stripped down a scrap (read - parts donor) engine removing magnetos and plug leads, water pump and pipes, carbs and cooling system. With the starter still connected I took the engine, my auto gearbox, flex plate and a few other odds and ends to Charlie Broomfield so that he can manufacture the gearbox mounting plate, engine/gearbox coupling and bearings.
The starter allows the engine to be hand cranked to check for clearances of the output drive.
So some progress even though no updates. I may get a bit more done over Christmas but as the chassis blasting will be done outside, the weather needs to dry up a bit.
As everywhere seems to shut down for 2 weeks over the holiday period work on my business move and expansion will be on hold so I may do a bit more on the engine intake manifold.
I will take a few pictures as things move forward.
Paul
The chassis is now completely stripped down to it's component parts ready for rust removal, blasting and a coat of primer.
I still have a little work to do on the axles, removing the remaining bearings and stub axle, prior to blasting and primer.
I have stripped down a scrap (read - parts donor) engine removing magnetos and plug leads, water pump and pipes, carbs and cooling system. With the starter still connected I took the engine, my auto gearbox, flex plate and a few other odds and ends to Charlie Broomfield so that he can manufacture the gearbox mounting plate, engine/gearbox coupling and bearings.
The starter allows the engine to be hand cranked to check for clearances of the output drive.
So some progress even though no updates. I may get a bit more done over Christmas but as the chassis blasting will be done outside, the weather needs to dry up a bit.
As everywhere seems to shut down for 2 weeks over the holiday period work on my business move and expansion will be on hold so I may do a bit more on the engine intake manifold.
I will take a few pictures as things move forward.
Paul
Hi Storer, did you ever consider a manual box? These torque figures from your v12 can't be that uncommon in modern diesel truck engines? I'm guessing you must have done, just wondering what the downsides were?
Really happy to see progress on this, these. Interesting build threads like this are the best part of ph
Really happy to see progress on this, these. Interesting build threads like this are the best part of ph
Lefty said:
Hi Storer, did you ever consider a manual box? These torque figures from your v12 can't be that uncommon in modern diesel truck engines? I'm guessing you must have done, just wondering what the downsides were?
Really happy to see progress on this, these. Interesting build threads like this are the best part of ph
Briefly considered a manual but the thought of the heavy engineering required to get one to work was quickly dismissed. Most of the Meteor builds use an auto. They do make life easier.Really happy to see progress on this, these. Interesting build threads like this are the best part of ph
The Meteor engine has nowhere to mount a gearbox to or a plate on the end of the crank to bolt a flywheel onto.
The crank has a female spline which is inside the crank case, which takes a male 'floating' spline that then protrudes. This male spline is normally direct coupled to the Centurion gearbox/clutch pack.
If the auto box struggles at 300/350rpm then 500rpm is a possibility so we have some flexibility.
Paul
Gassing Station | Readers' Cars | Top of Page | What's New | My Stuff