E36 Track Car - Replacement Engine Build(s)
Discussion
I wanted to change to E36 M3 3.2 rear arms, which use a much larger wheel bearing, to try and resolve the issues previous in this thread. The plan was to keep my subframe (so I stay with medium case sized differential) and use the trailing arms and brakes. I had everything blasted and powder coated in the same colour as before.
First up was 4 new Meyle ball joints in the trailing arms..
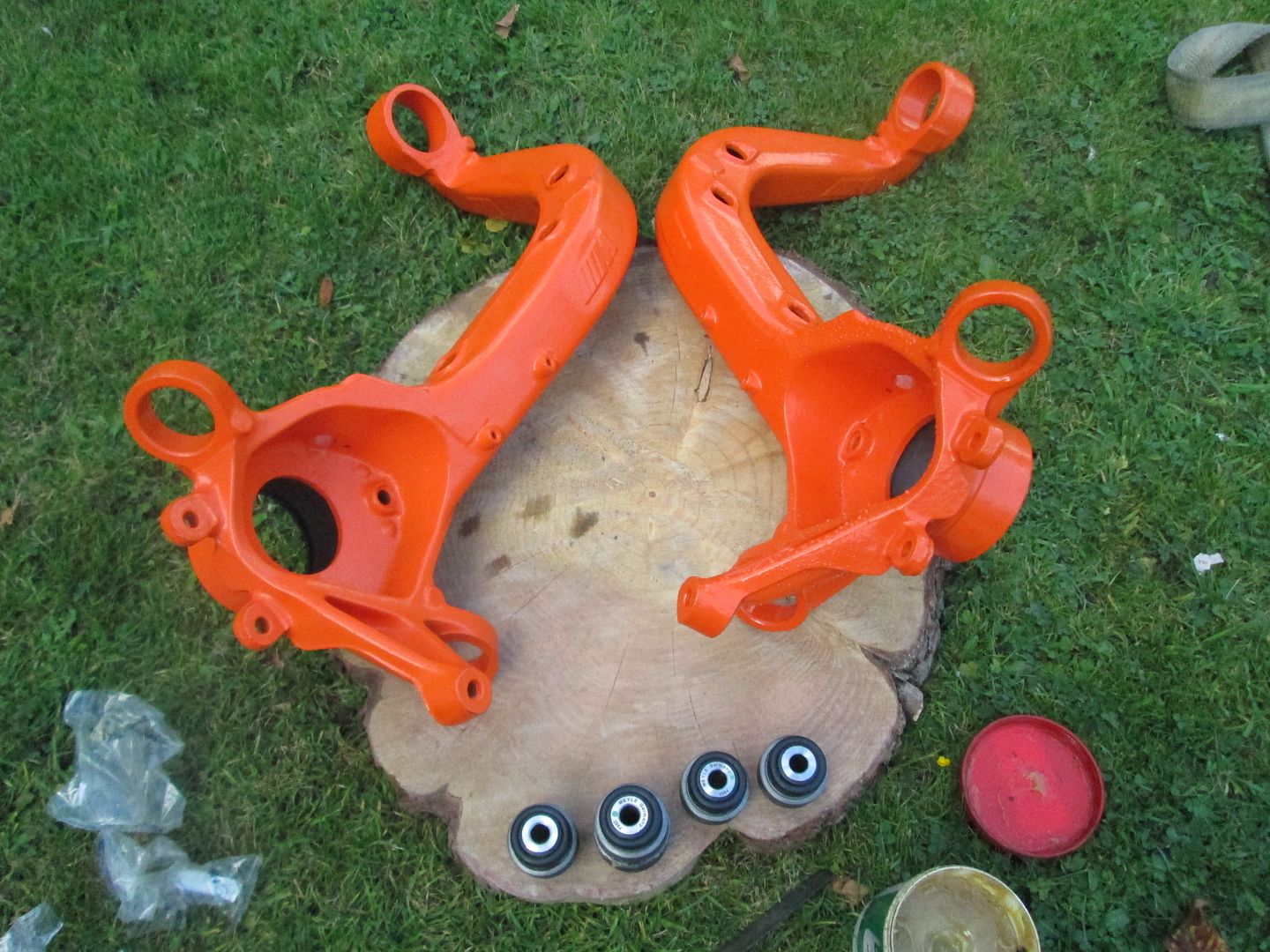
Then two new Meyle bearings. I also swapped my Powerflex Black Series trailing arm bushes to the new arms..
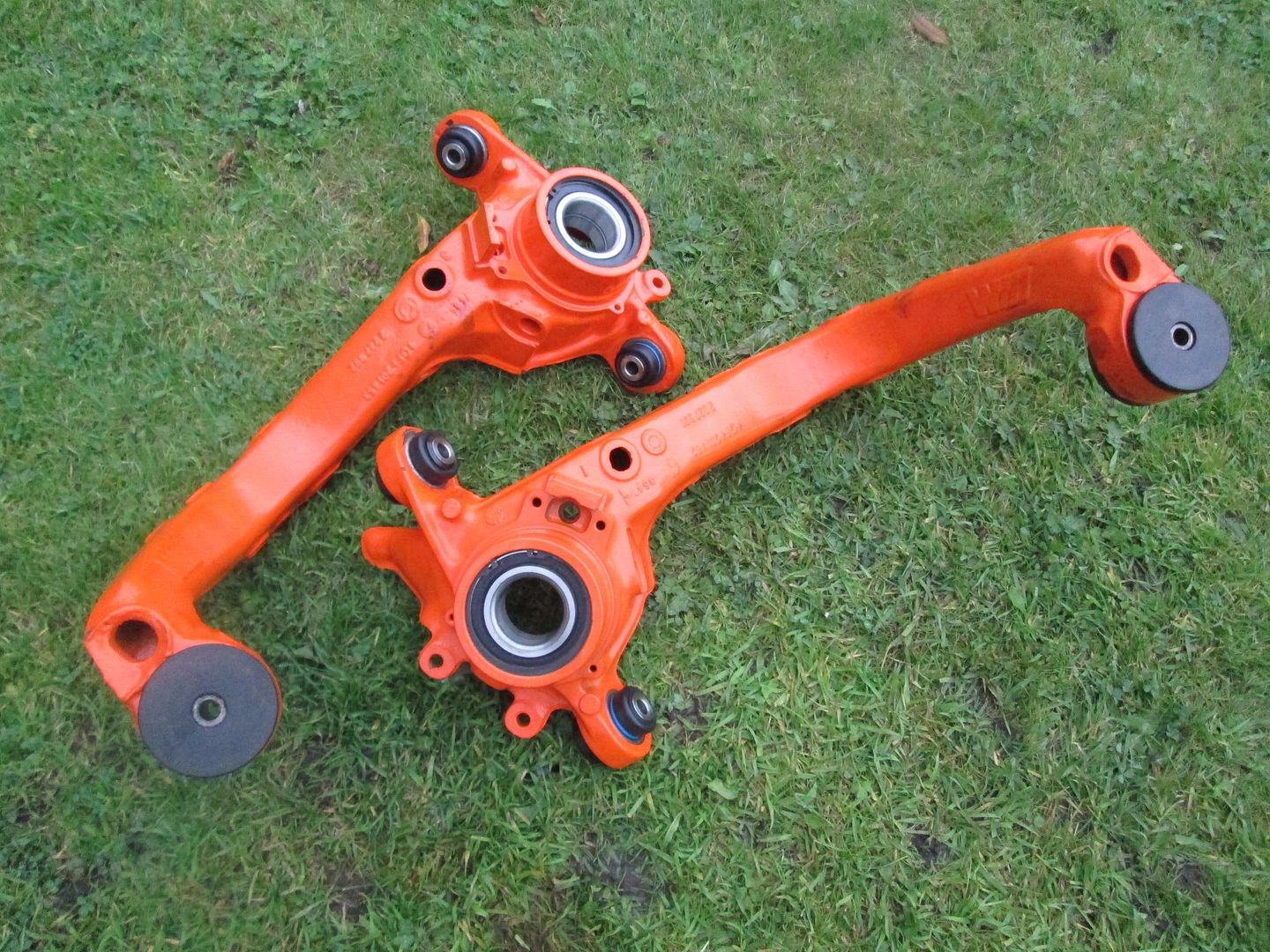
Stub axles were then pressed in and my studs swapped over, applied some Loctite 271 and torqued..
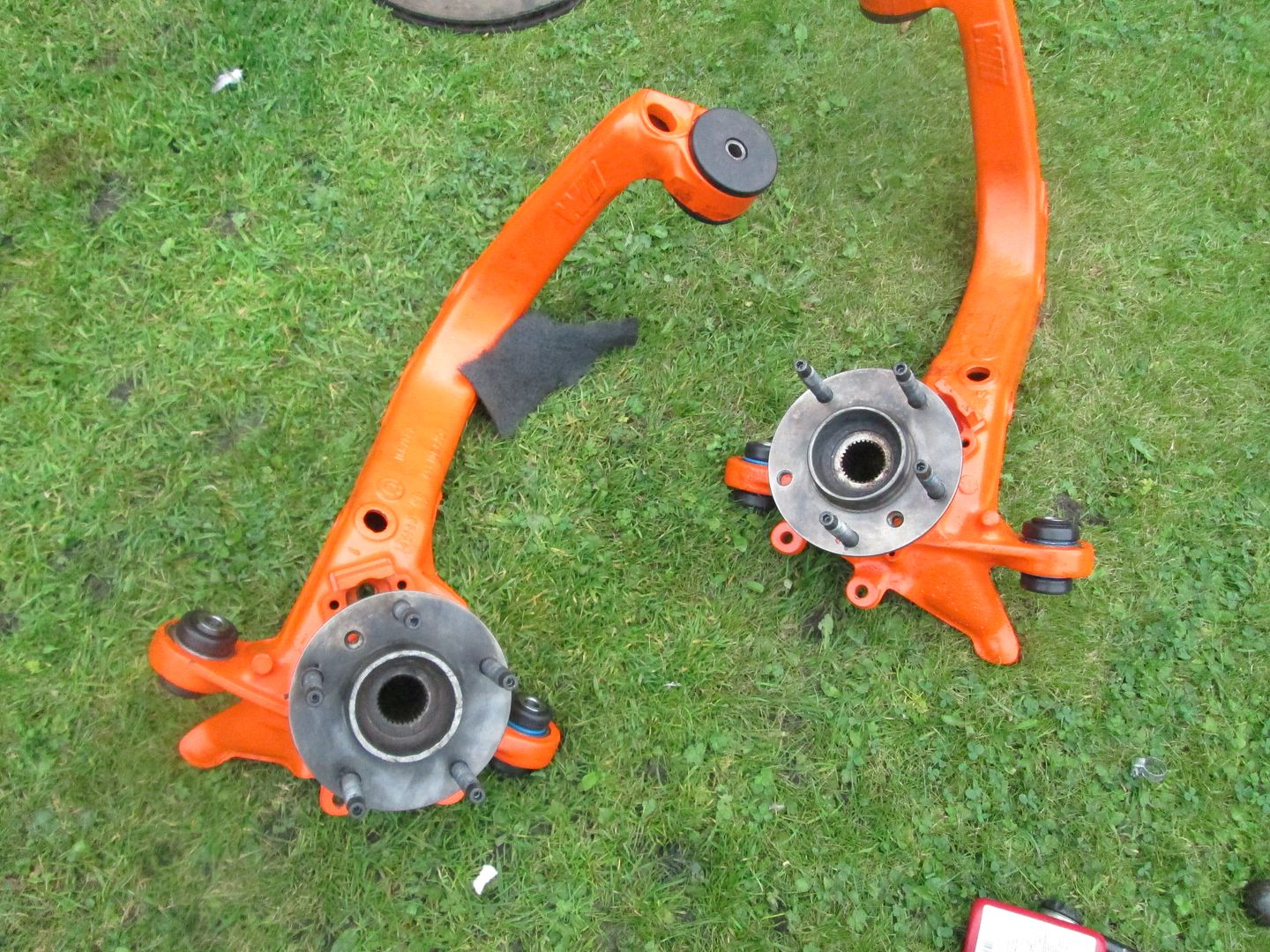
I stripped my adjustable camber arms down which were looking a bit well used (been on the car nearly 2 years). The standard rubber bushes were also showing signs of cracking, so they were stripped out.
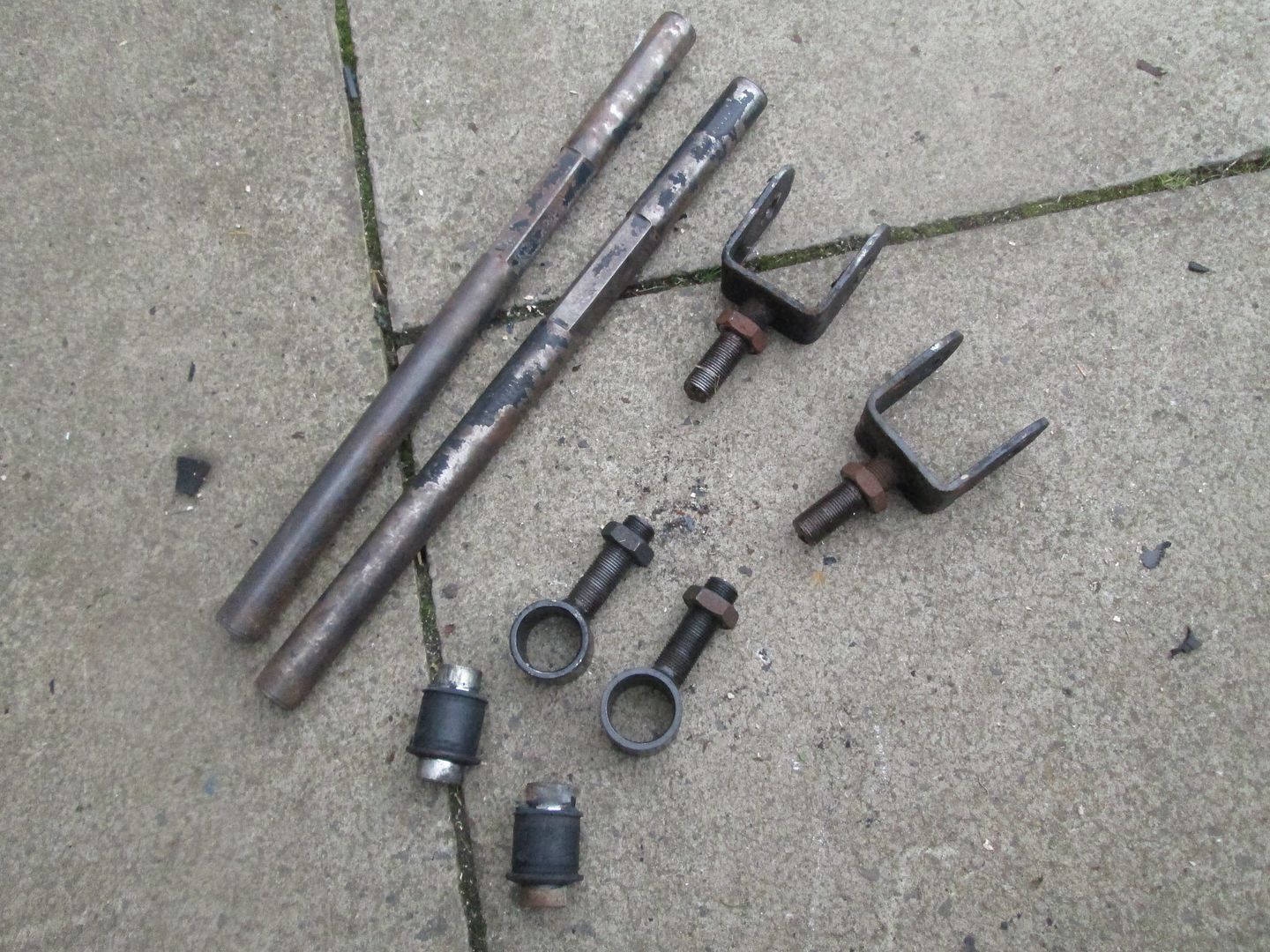
I managed to find some polybushes for the camber arms from a European supplier, as PowerFlex dont sell anything similar. They needed a bit of trimming to fit (outer diameter) as they are not meant for these exact camber arms - they work fine and fit well now..
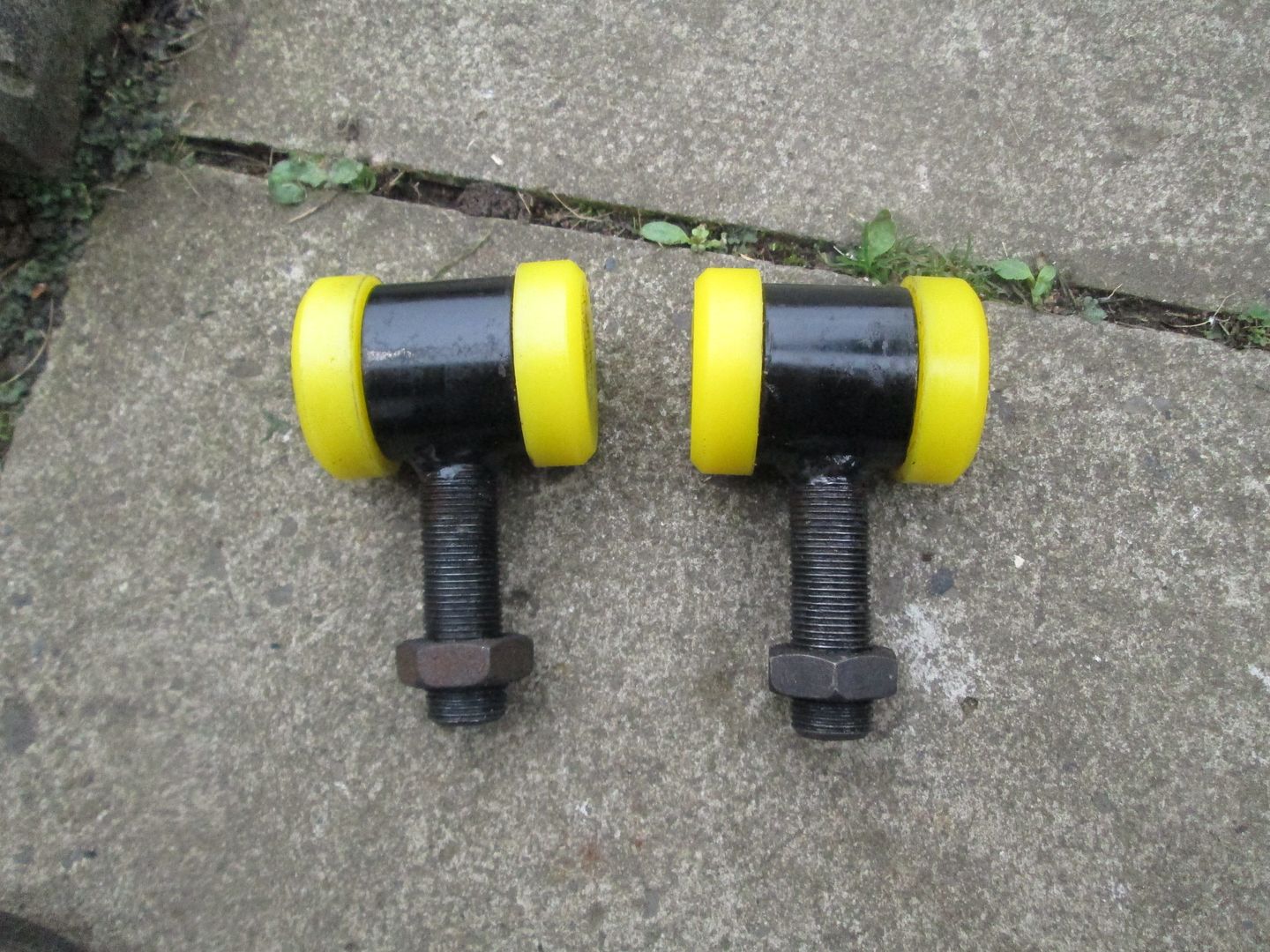
Then cleaned up, painted and assembled..
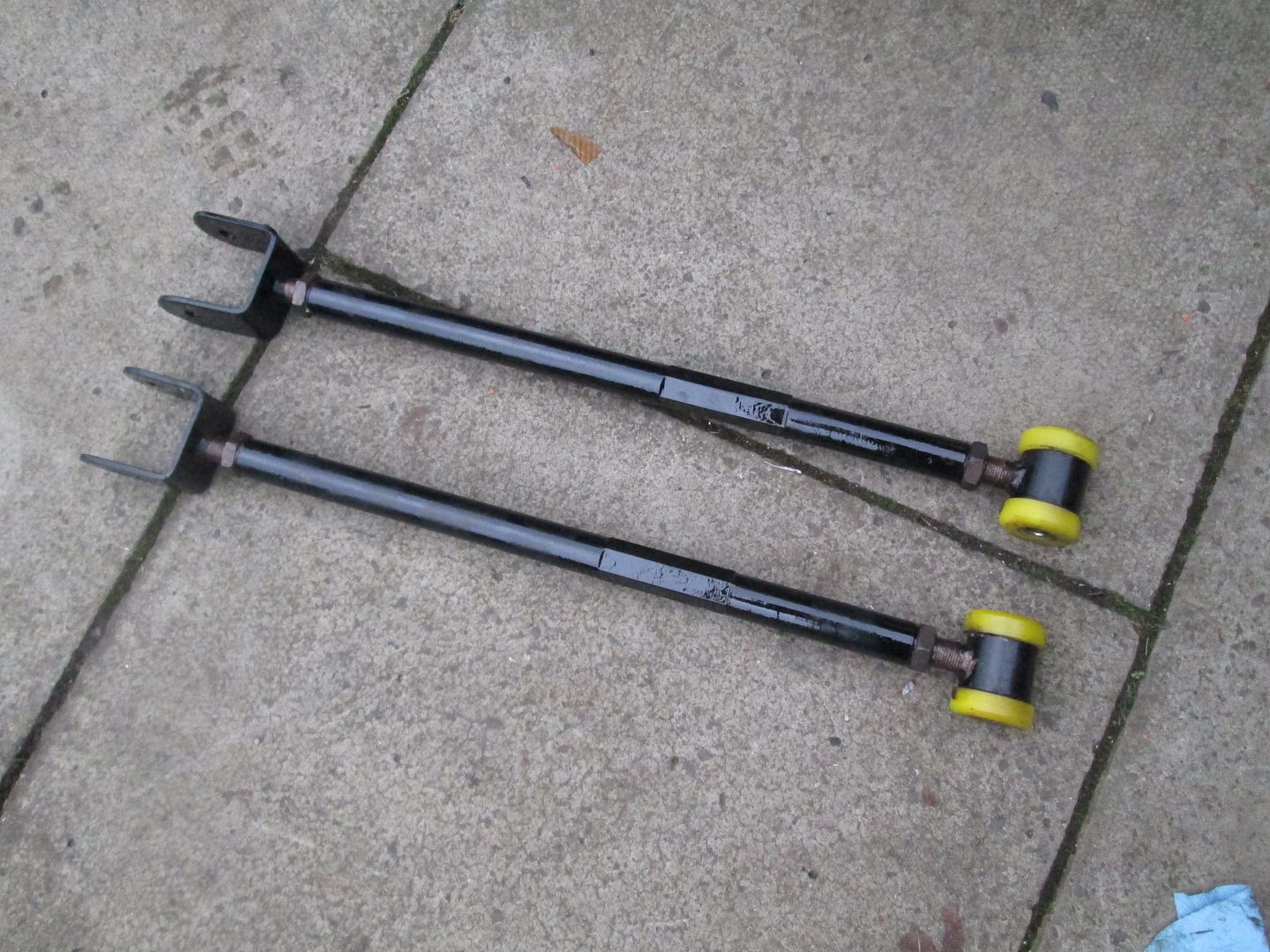
When the subframe was last built, I used a standard Lemforder bush on the upper inner control arm. The same supplier that stocks the above bush also have a polybush for this location, so it made sense to swap it also.
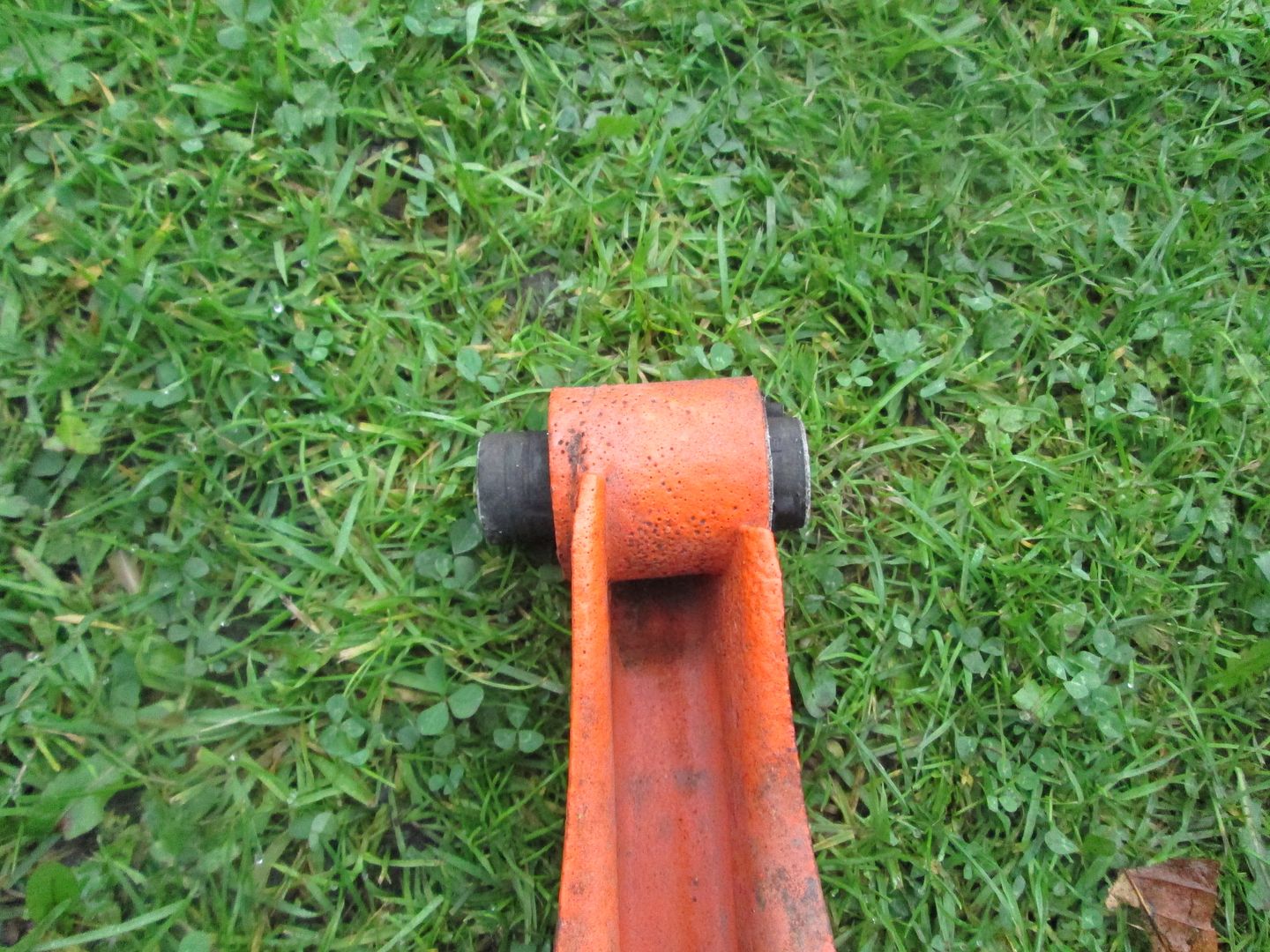
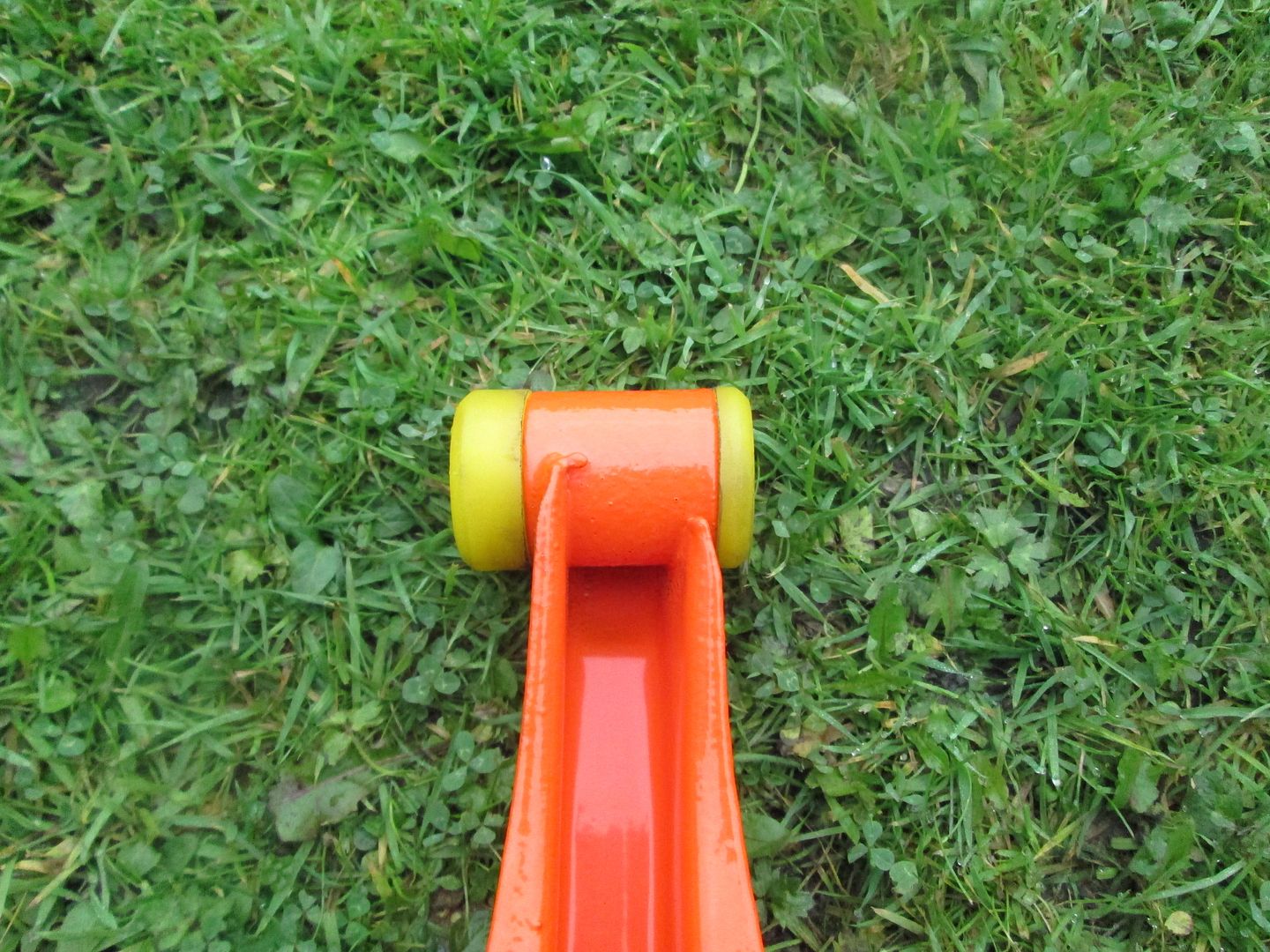

The above set of trailing and control arms were then bolted up to the car with the shock and spring, with new hardware. When the trailing arms were powder coated, the M3 3.2 rear calipers were also stripped and done. I then built them up with new seals and pistons.
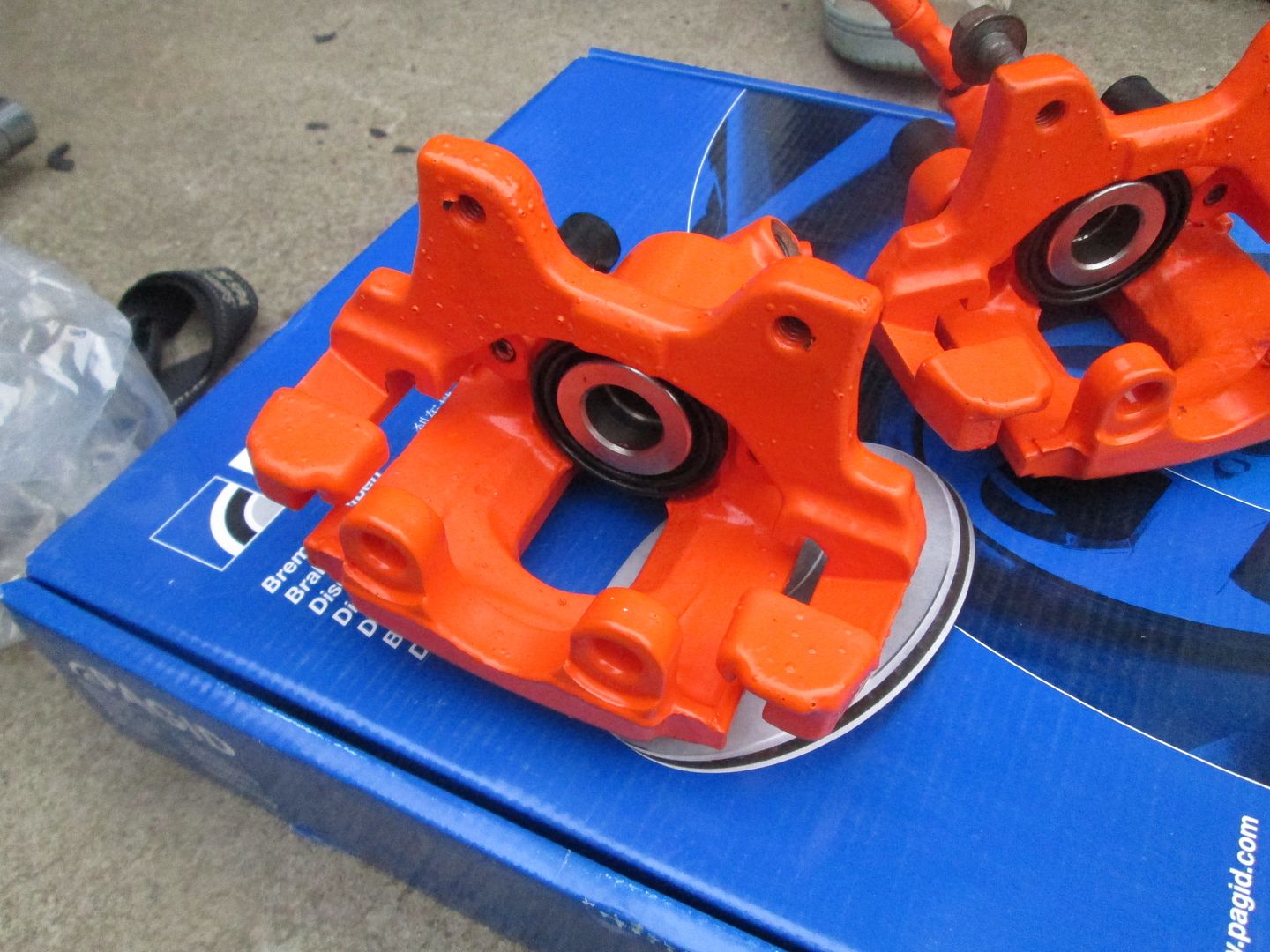
Got some CL RC5+ (to match the fronts), with new discs, and put them on the car..
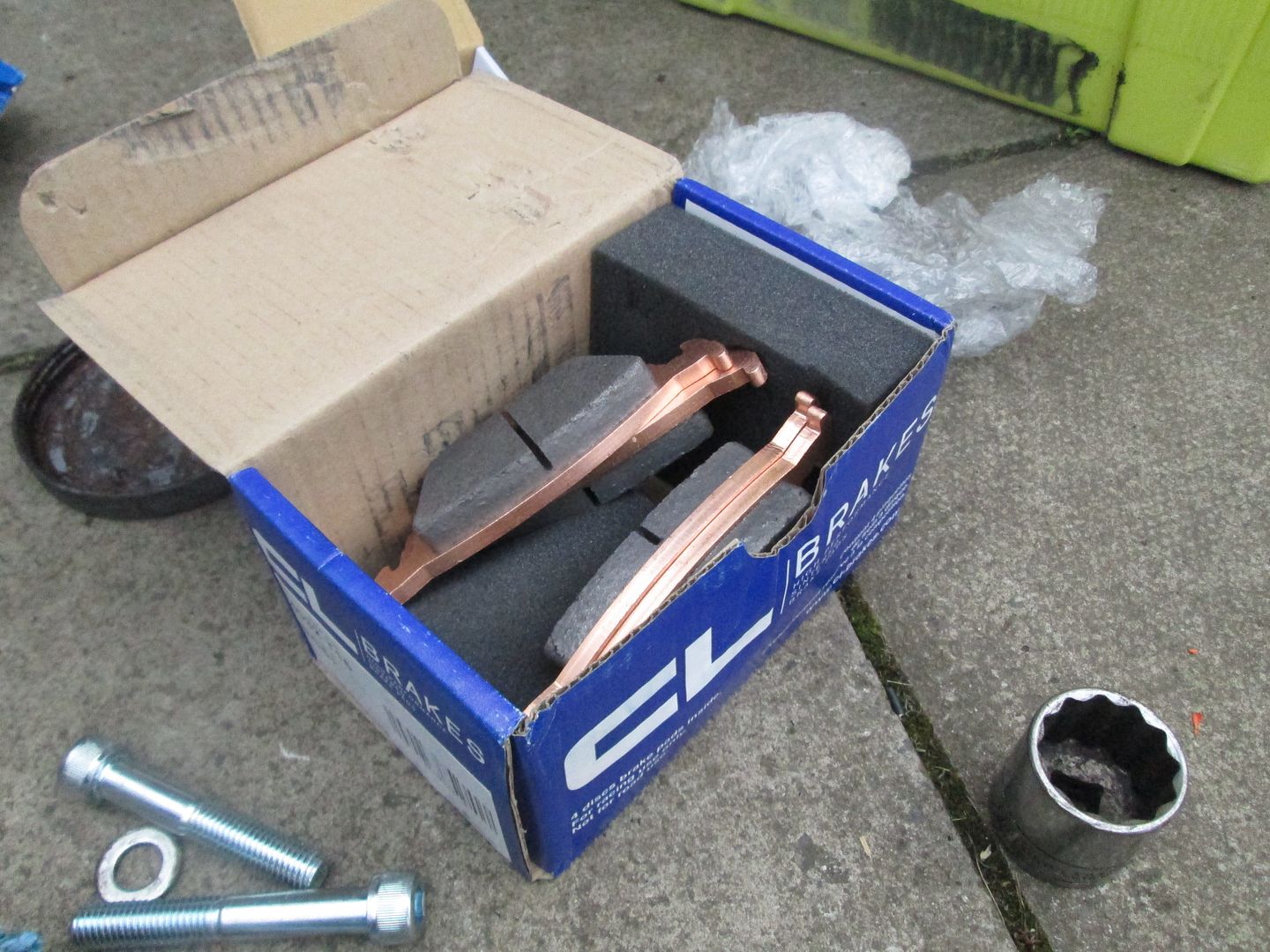
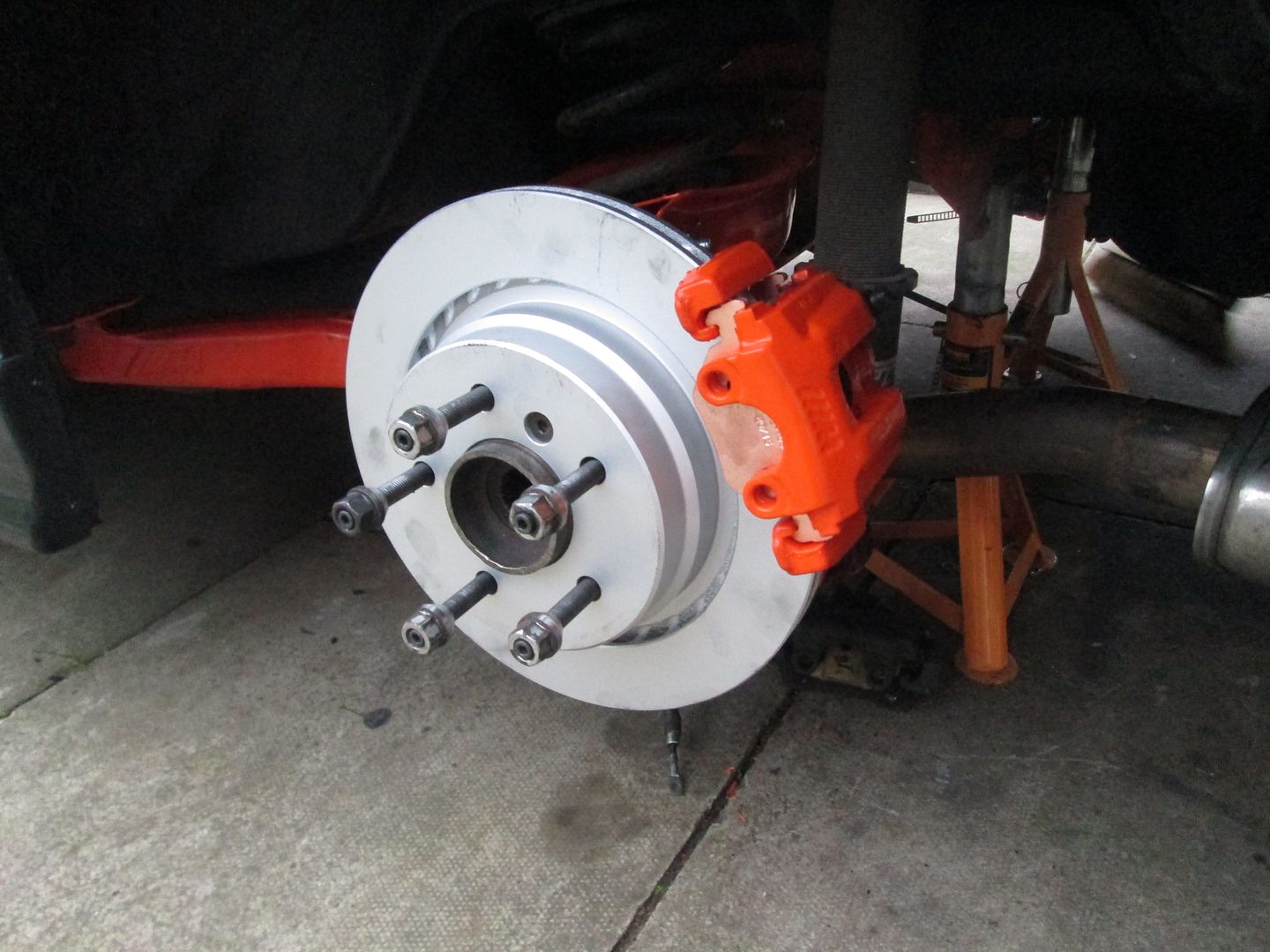
This has taken it from 276x19mm > 312x20mm.
There has been a massive amount of changes over the past month, with the above being just one. Days have been spent stripping l excess wiring out of the engine and interior looms, then rewrapping everything and generally tidying things up. This saved a good 4-5kg which I could not believe - there is so much rubbish in there. You always think these are going to be 'quick' jobs but they are so time consuming. The cooling fan has also been re-wired so the ECU controls the relay, rather than a radiator switch, and a manual override added.
With the rear end components replaced, I obviously needed to get the alignment done again. I decided to ditch the current 'normal' tyres I use for wet days (RainSport2) for a set of Michelin Pilot Sport 3's. Still using the Federal RS-R on my other set of wheels for dry days.
Once those were sorted, I had the alignment done. Previously, I ran:
Camber - 2.3deg Front, 1.8deg Rear
Toe - 0 Square Front, Total 20' Toe In Rear
I have now changed this, increased camber and a tad more rear toe:
Camber - 3.1deg Front, 2.4deg Rear
Toe - 0 Square Front, Total 30' Toe In Rear
The rear is now around the 'stock' M3 3.2 spec, alignment wise with camber and toe. I will have to see how it feels and go from there - the additional poly bushes on the rear arms are noticeably different.
Next up was a change in gearbox mounts - the standard ones do not last long and go soft over time. There are a number of companies selling poly mounts, but I wanted to avoid the 'bolt through the middle' style as no doubt it would just drastically increase noise and vibration. Quite a number of people use the RevShift mounts, which are made by a small company in the US. I ordered a pair and a couple of weeks later they dropped through the letterbox..
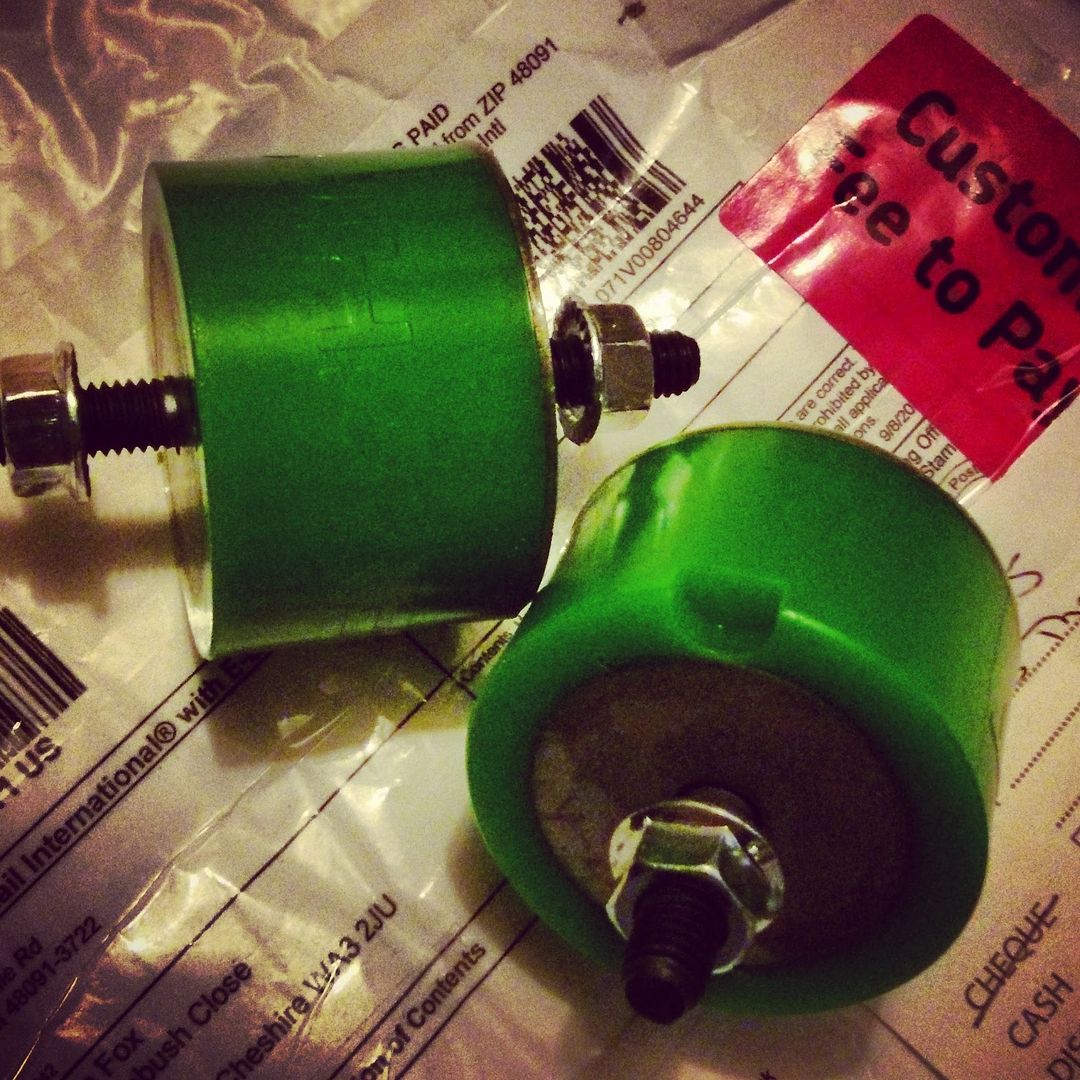
They were then fitted, and I also changed the gearbox oil at the same time. My gearbox has been noisy for some time, and the oil has already been changed (75w90) around 12 months ago. I suspected the level may have been low, or it just wasn't thick enough, even though its the recommended grade. Since using the single mass flywheel I have also had gearbox 'chatter/rattle' on idle, which goes once you are moving, but it was annoying. Many people have had success with mixing RedLine oils, but the two I needed are not really readily available. I went for the Lightweight Shockproof instead...

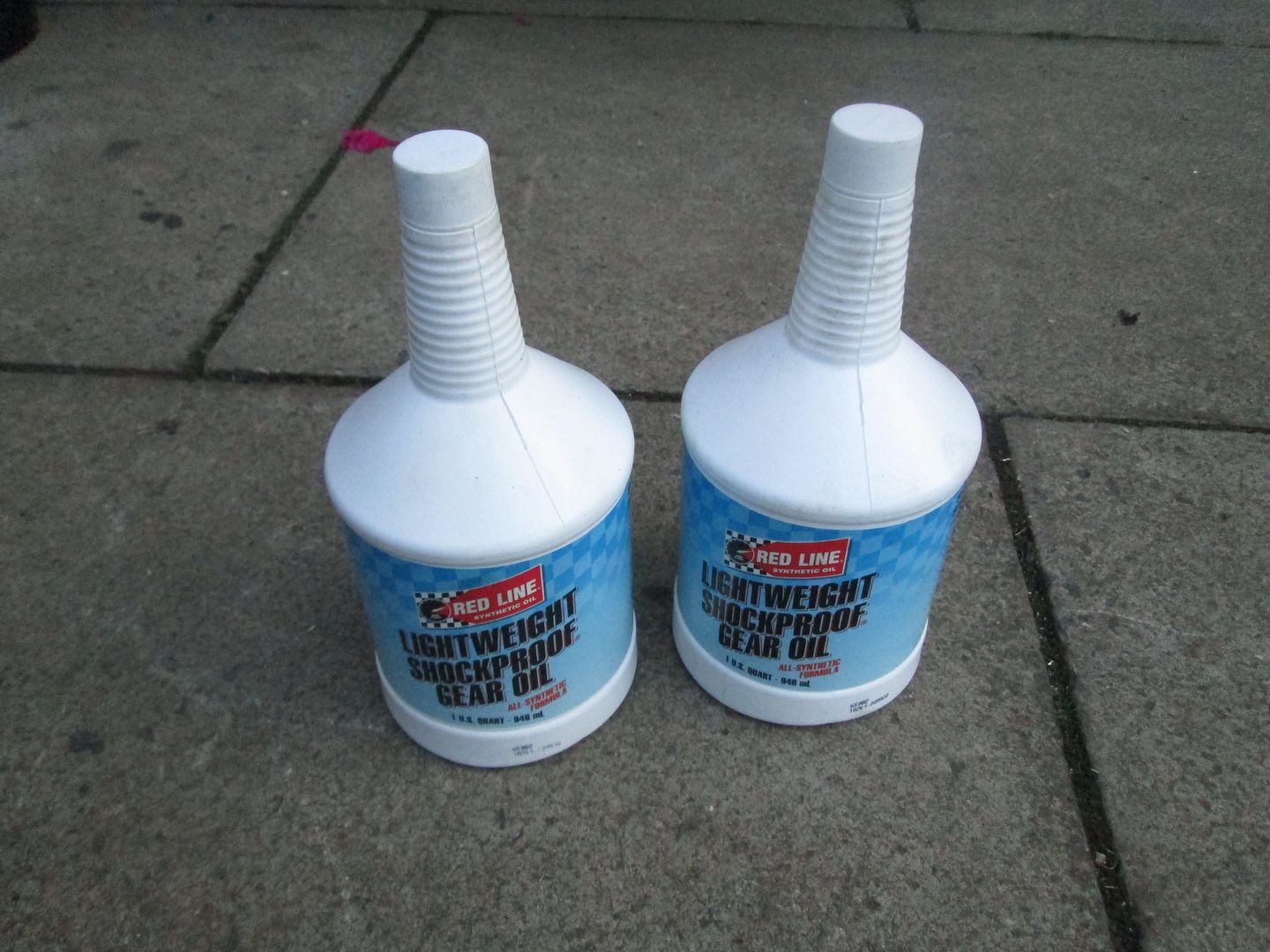
Luckily this seems to have had a great effect, as shifts are now 100x smoother and 90% of the noise has gone.
With the track day at Spa fast approaching I had a list of things that needed sorting, as I had been putting them off all year. With one of the requirements being a fire extinguisher, I debated for some time about what to do. Hand held would be sufficient, but you still have to unclip it, take the pin out and then use it, all whilst trying to get out of the car over the cage, etc. With having the cage, and getting out being the highest priority in case of fire I wanted something a bit more substantial.
I ended up opting for a plumbed in system, went with OMP over Lifeline but either would have sufficed. I also wanted to have the electrical system isolated, as if the fire was actually started by an electrical fault in the event of a crash the extinguisher would be useless. This ended up being a massive time consuming job. I already had most of the inlet system removed from the engine at the time as the loom was being trimmed - which gave good access to sort some bulkhead fittings for battery cables / extinguisher piping.
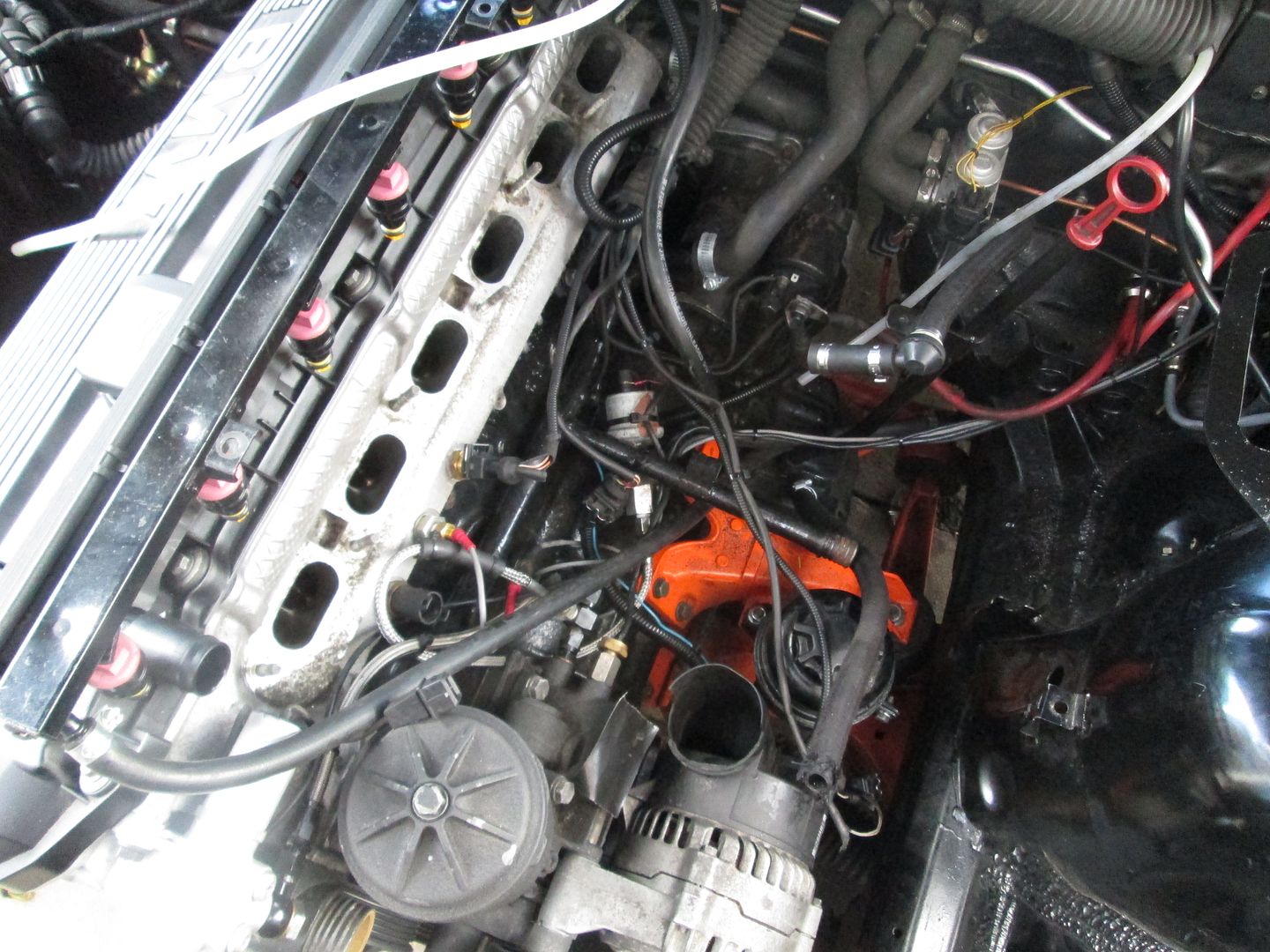
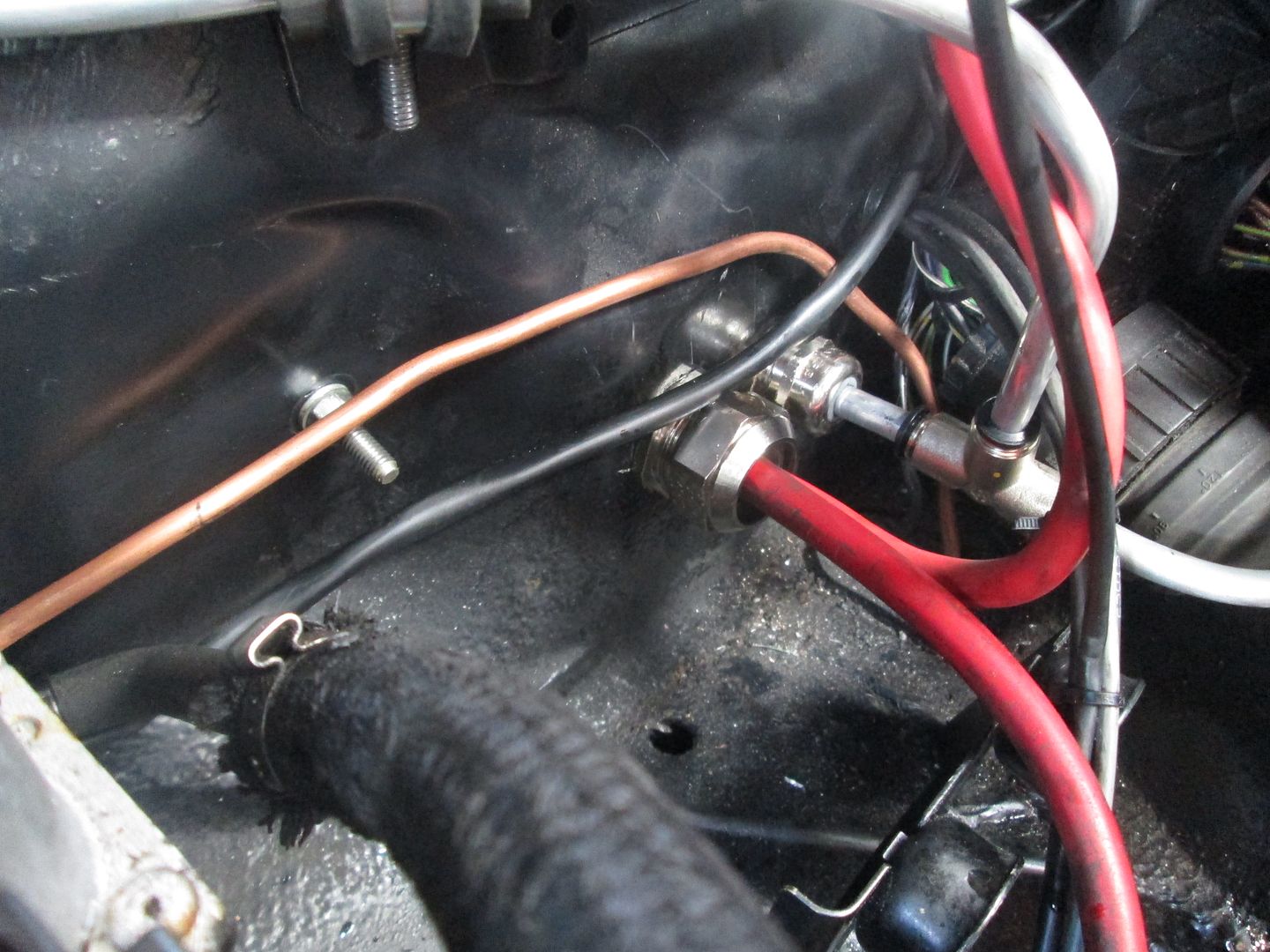
The next problem was mounting two pull cables on the outside, as the bonnet comes right up to the windscreen on the E36. I got a bit creative with the 'vents' in the top of the bonnet, and notched them out so the pull handles would go through. Mounting bracket was then made, and cables passed through to the inside via the scuttle panel using a grommet.
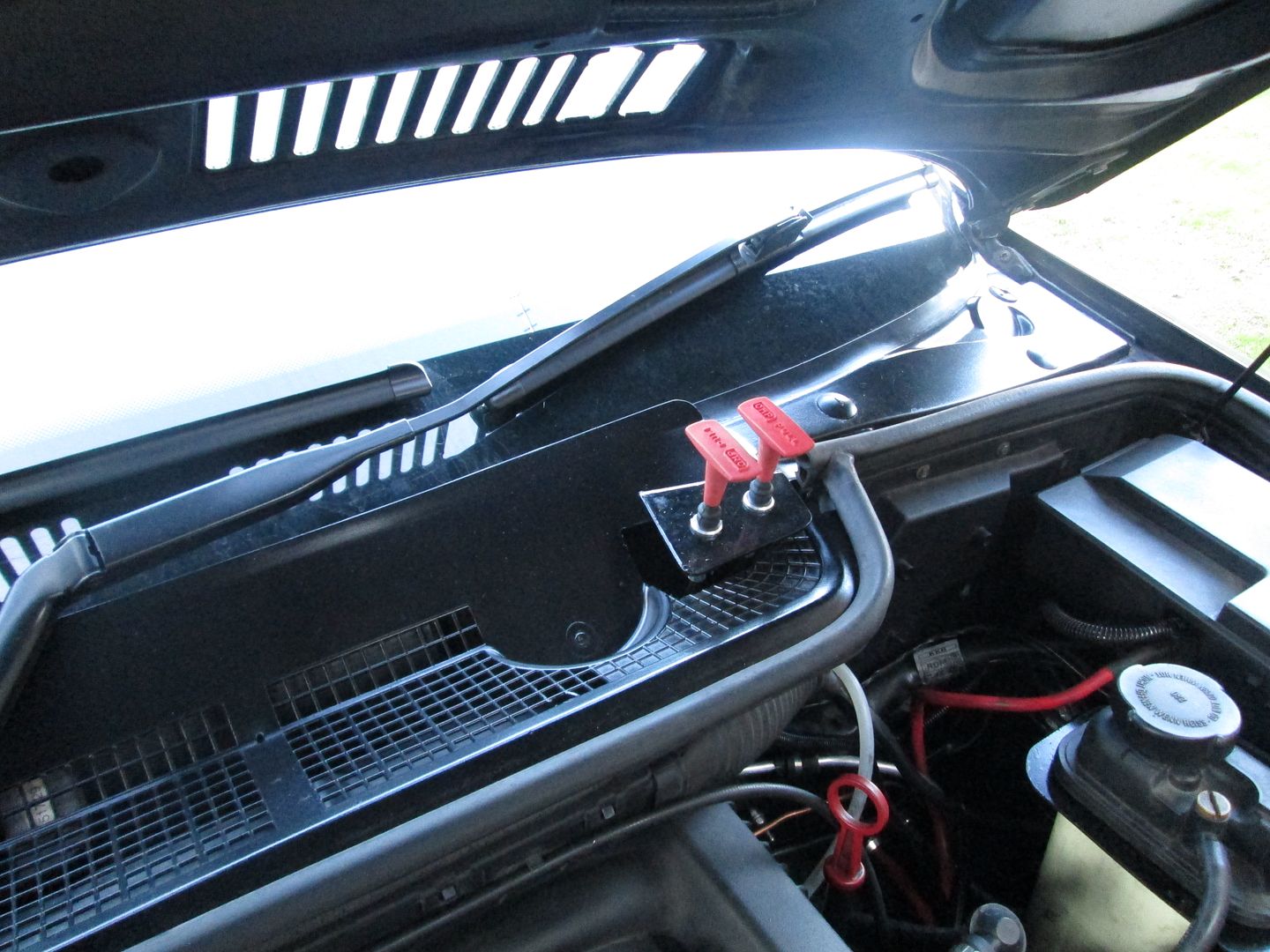
Two nozzles were put in the engine bay and piped up (exhaust and inlet side), you can just about see them on each suspension turret. The pipework runs round the back of the engine in the same mounts as the brake line. Two were also fitted inside, one in each footwell.
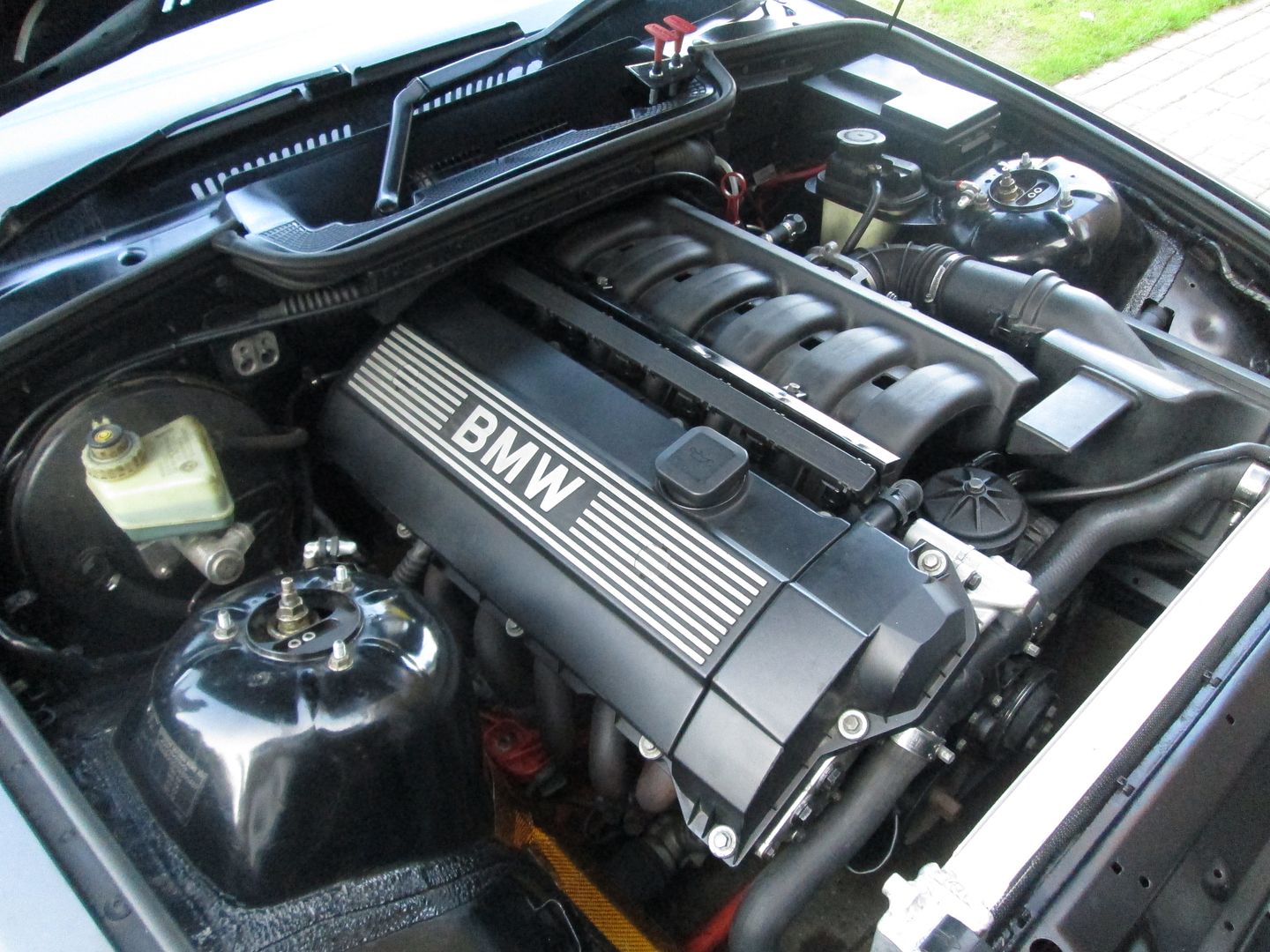
On another note, the whole exhaust side of the chassis, bulkhead and part of the tunnel have had reflective tape installed to try and keep some of the heat out of the cabin when on track. You can just about see some of this on the above picture.
The extinguisher bottle was mounted behind the passenger seat, and pipework ran down the passenger side of the tunnel.
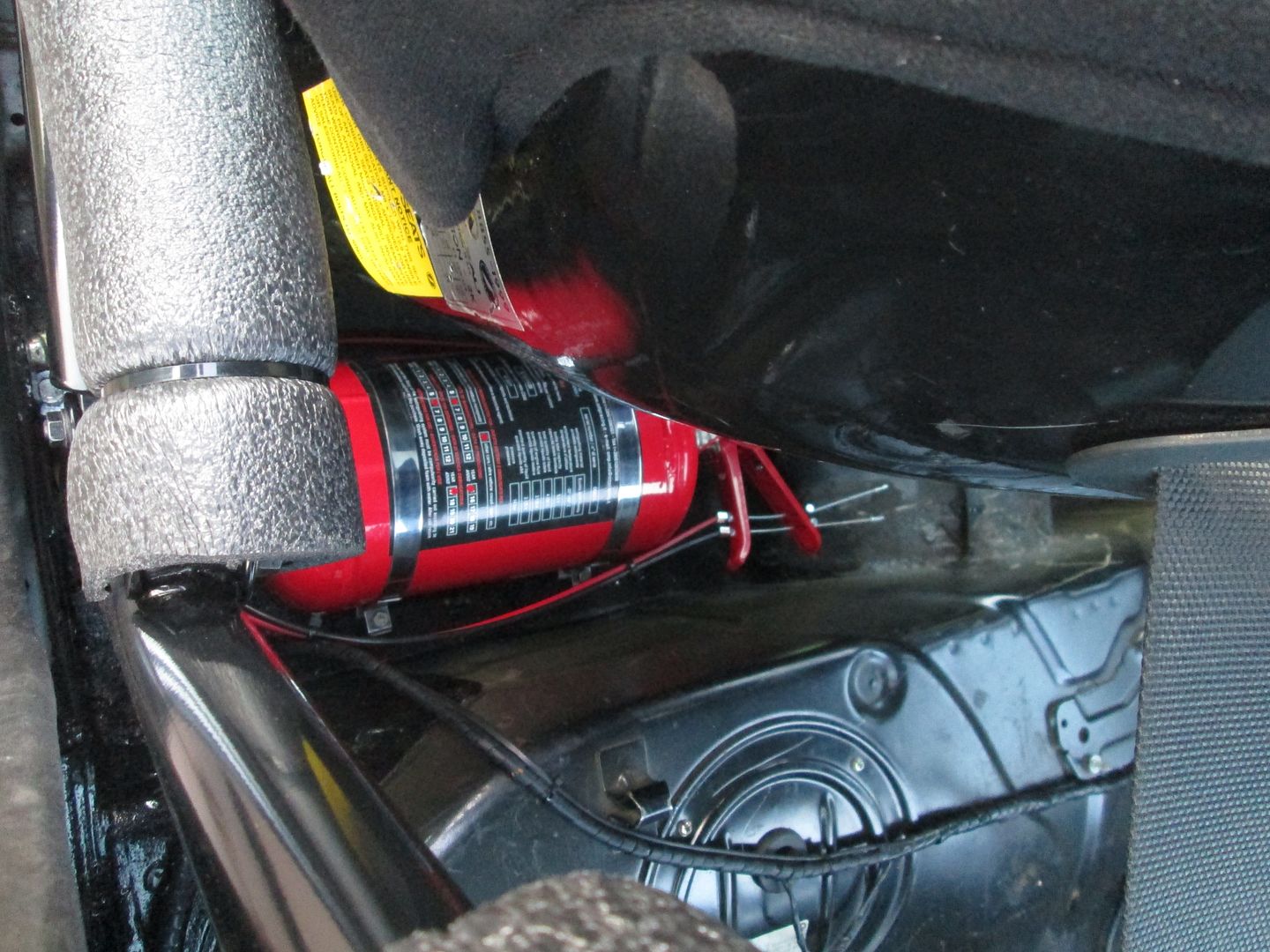
With that installed, I needed a pull handle inside to activate it if required. I also needed to mount the battery isolator, to which the exterior pull would connect. I had been meaning to move my gauges for some time, as the wideband used to be in the top centre vent, and the oil pressure/temperature in the middle of the clocks. I ditched the radio and made a panel to house them both on the dash, then mounted the isolator next to it. Swapped the clocks out and now I only have an aftermarket water temperature gauge in there.
At the same time, I replaced the standard OBC at the bottom of the centre console, which I had re-worked previously to use for the data logger. I now have a single switch for the data logger, so added some additional toggles for the radiator fan override, rear video camera power, etc. A bracket was made for the battery isolator pull cable and mounted to the dash - then a bracket was made for the extinguisher pull handle and that was mounted at the very bottom.

It all looks relatively simple, but making brackets, mounting things, is stupidly time consuming when doing a proper job of it. Obviously the extinguisher locking pin will remain in place when not out on a circuit.
Some other small jobs have also been done, like re-making the front brake ducts/mounts, moving charging points and adding new connectors to wiring, but never got any pictures of that. After a good month of messing about its pretty much ready for Spa, bar needing a quick clean.
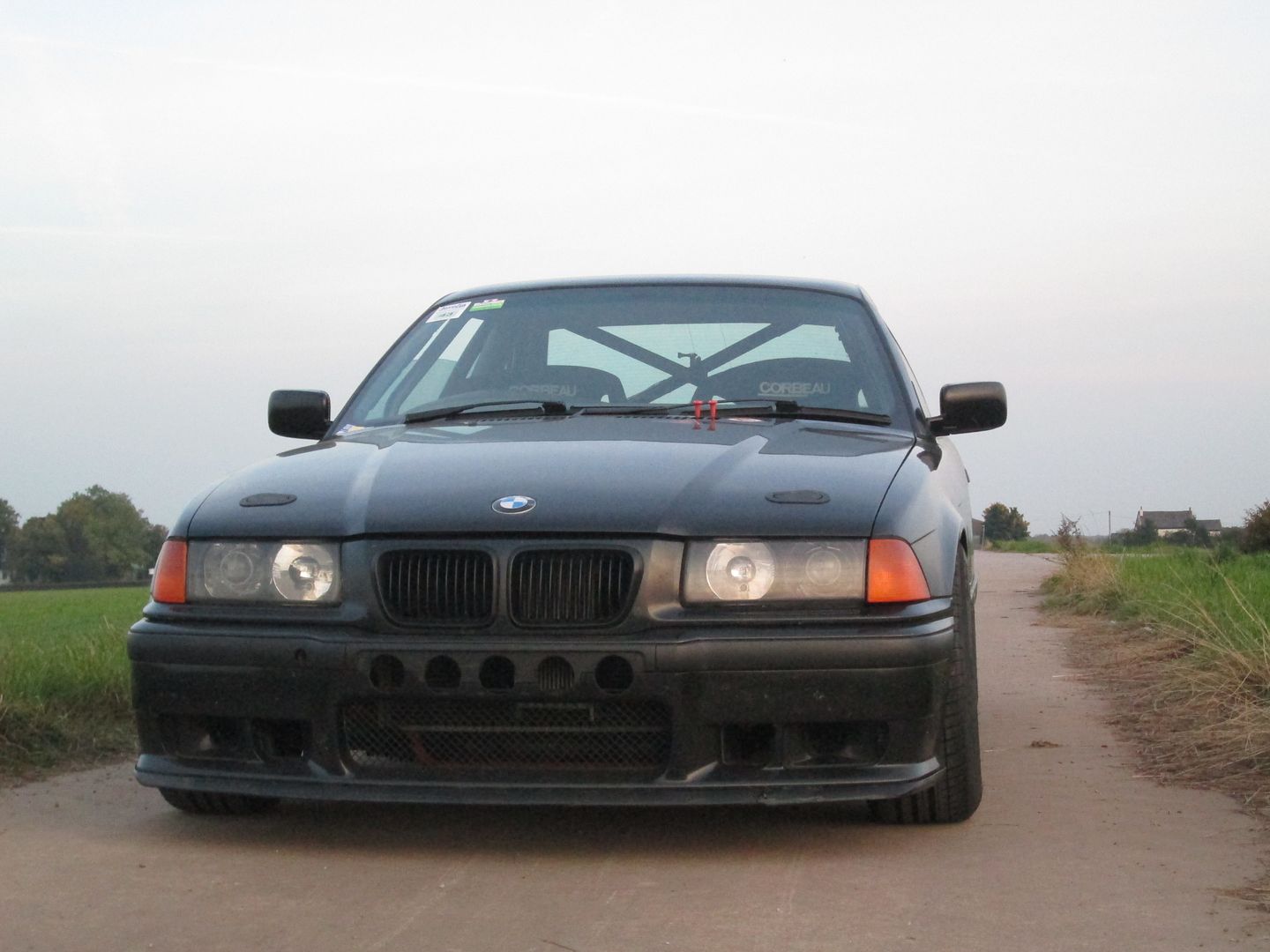
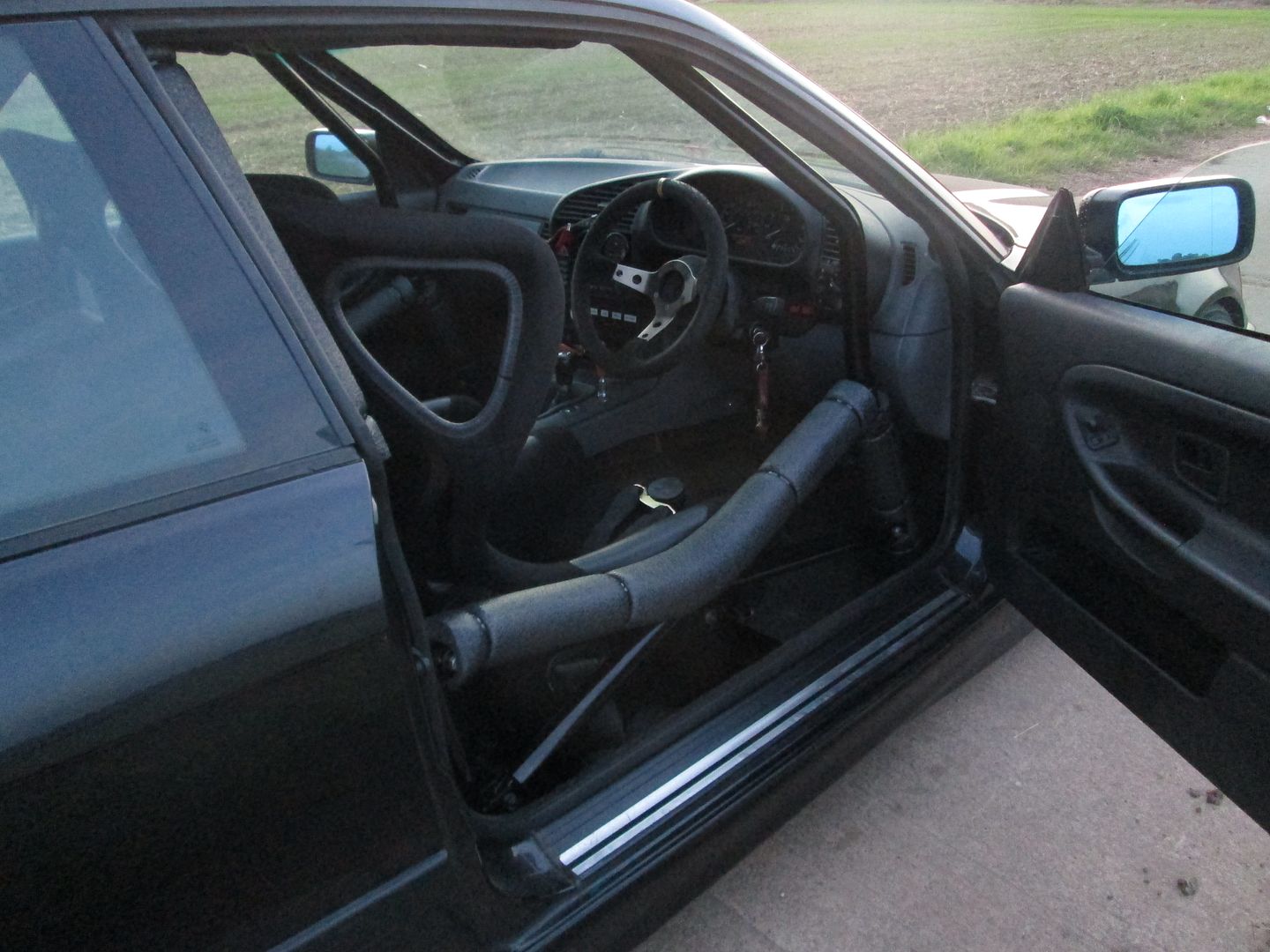
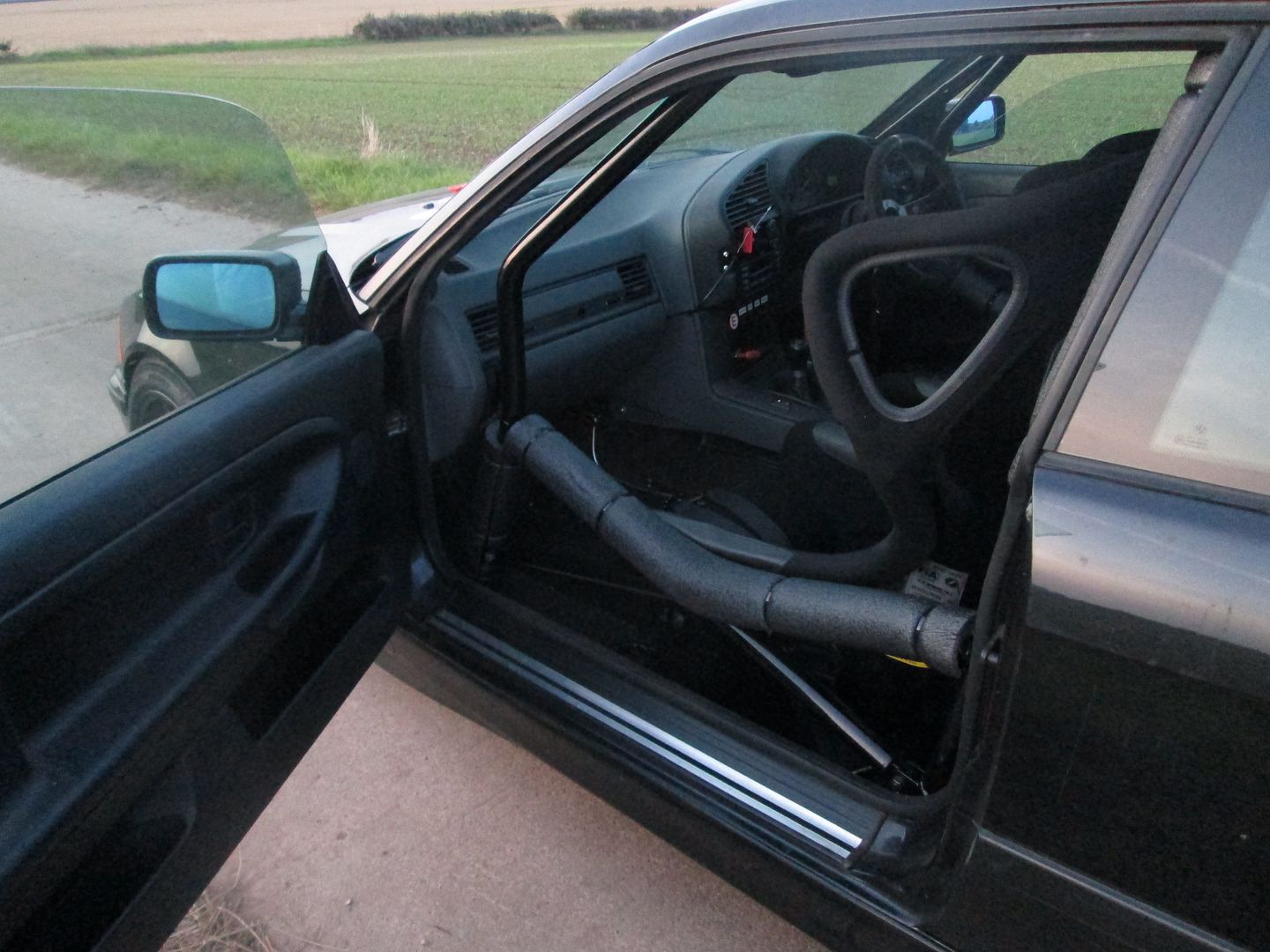
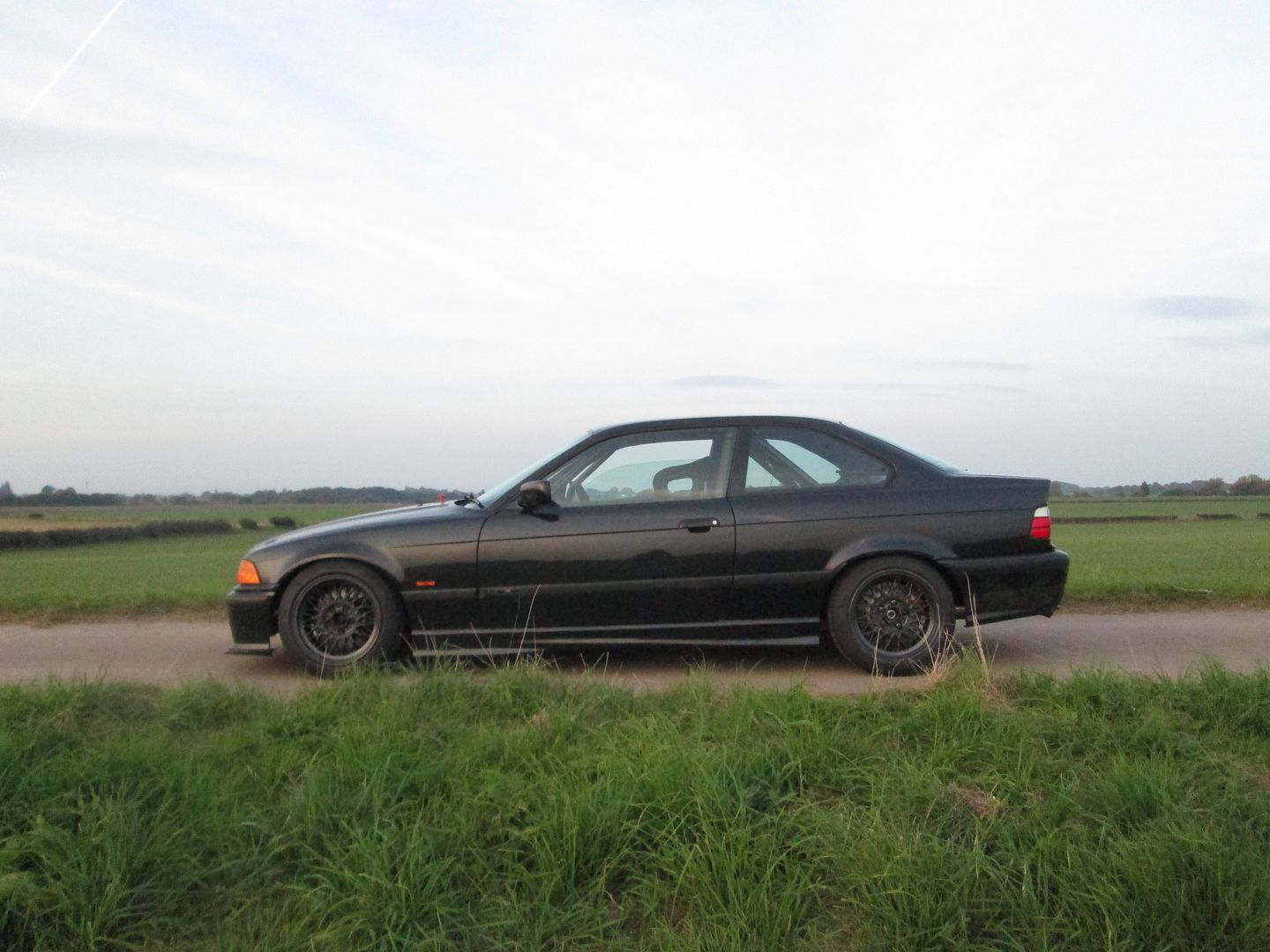
First up was 4 new Meyle ball joints in the trailing arms..
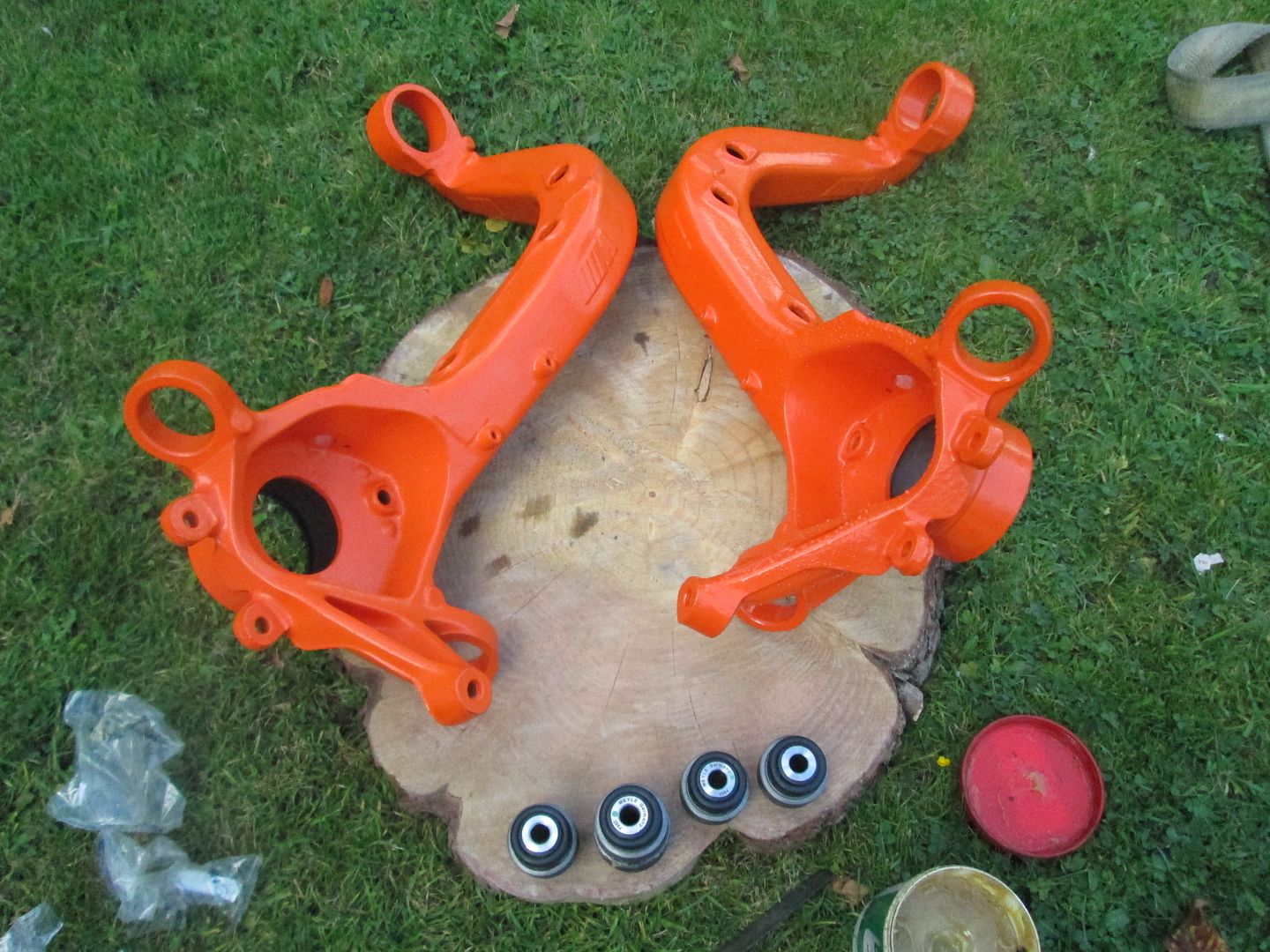
Then two new Meyle bearings. I also swapped my Powerflex Black Series trailing arm bushes to the new arms..
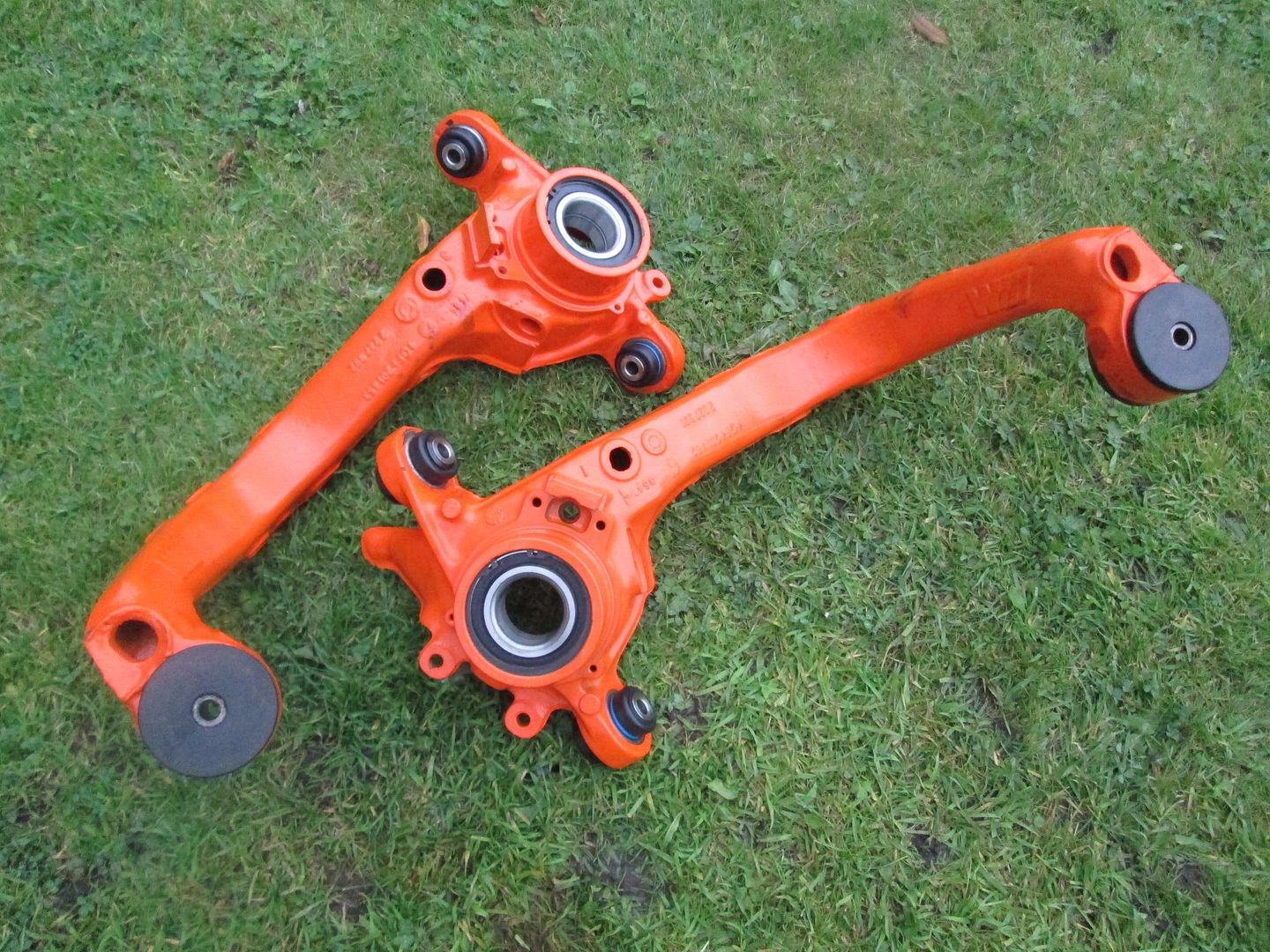
Stub axles were then pressed in and my studs swapped over, applied some Loctite 271 and torqued..
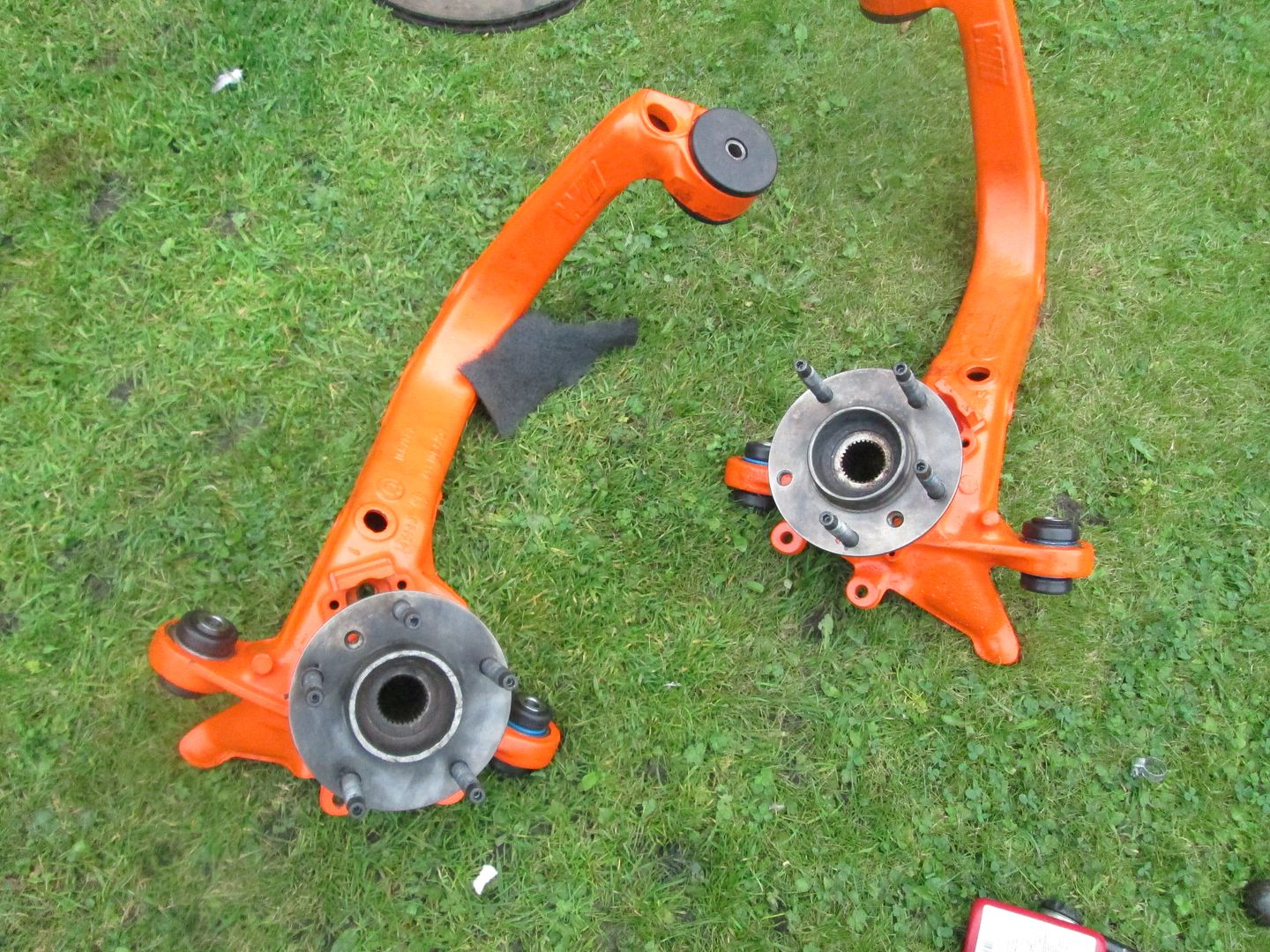
I stripped my adjustable camber arms down which were looking a bit well used (been on the car nearly 2 years). The standard rubber bushes were also showing signs of cracking, so they were stripped out.
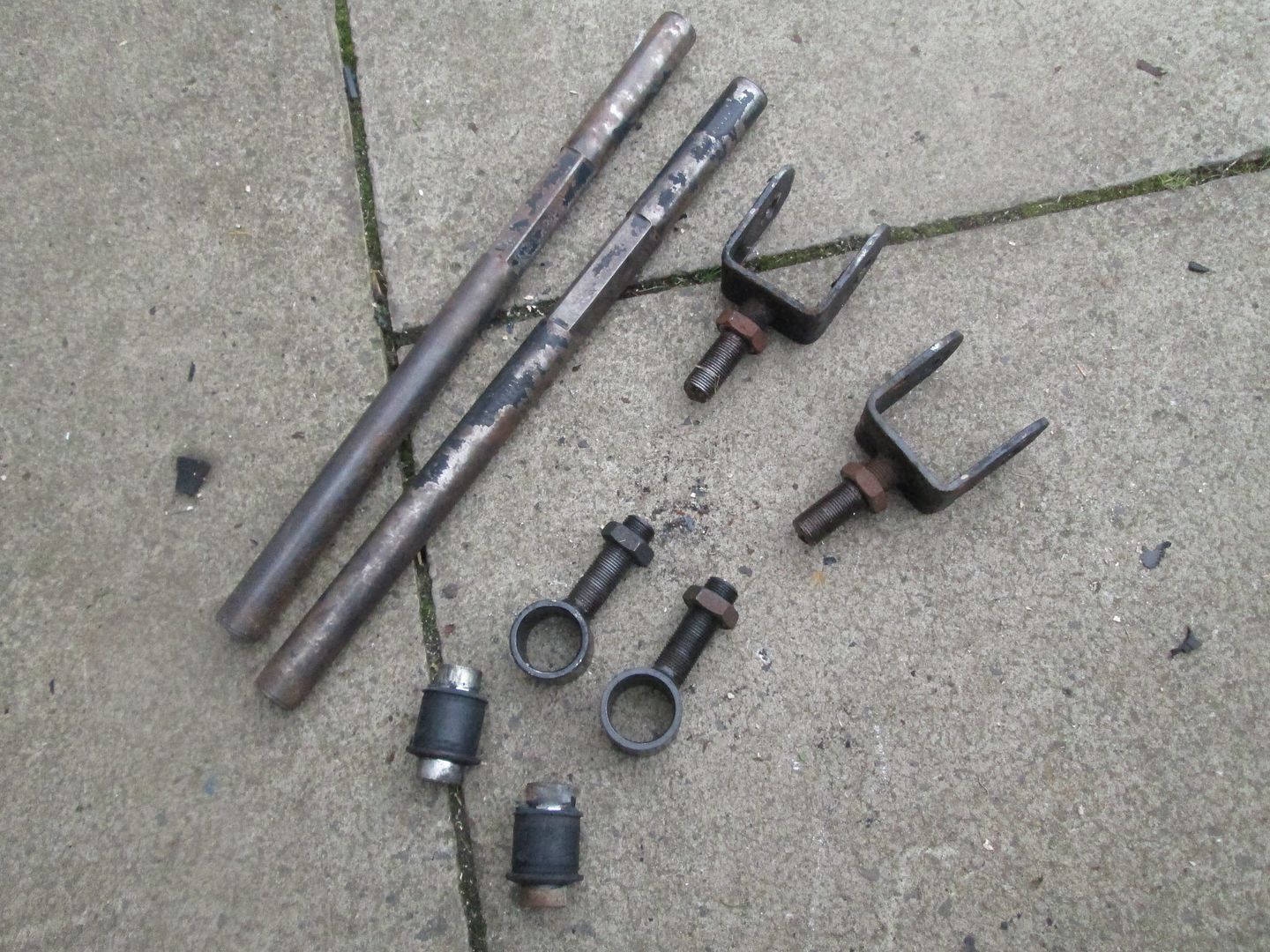
I managed to find some polybushes for the camber arms from a European supplier, as PowerFlex dont sell anything similar. They needed a bit of trimming to fit (outer diameter) as they are not meant for these exact camber arms - they work fine and fit well now..
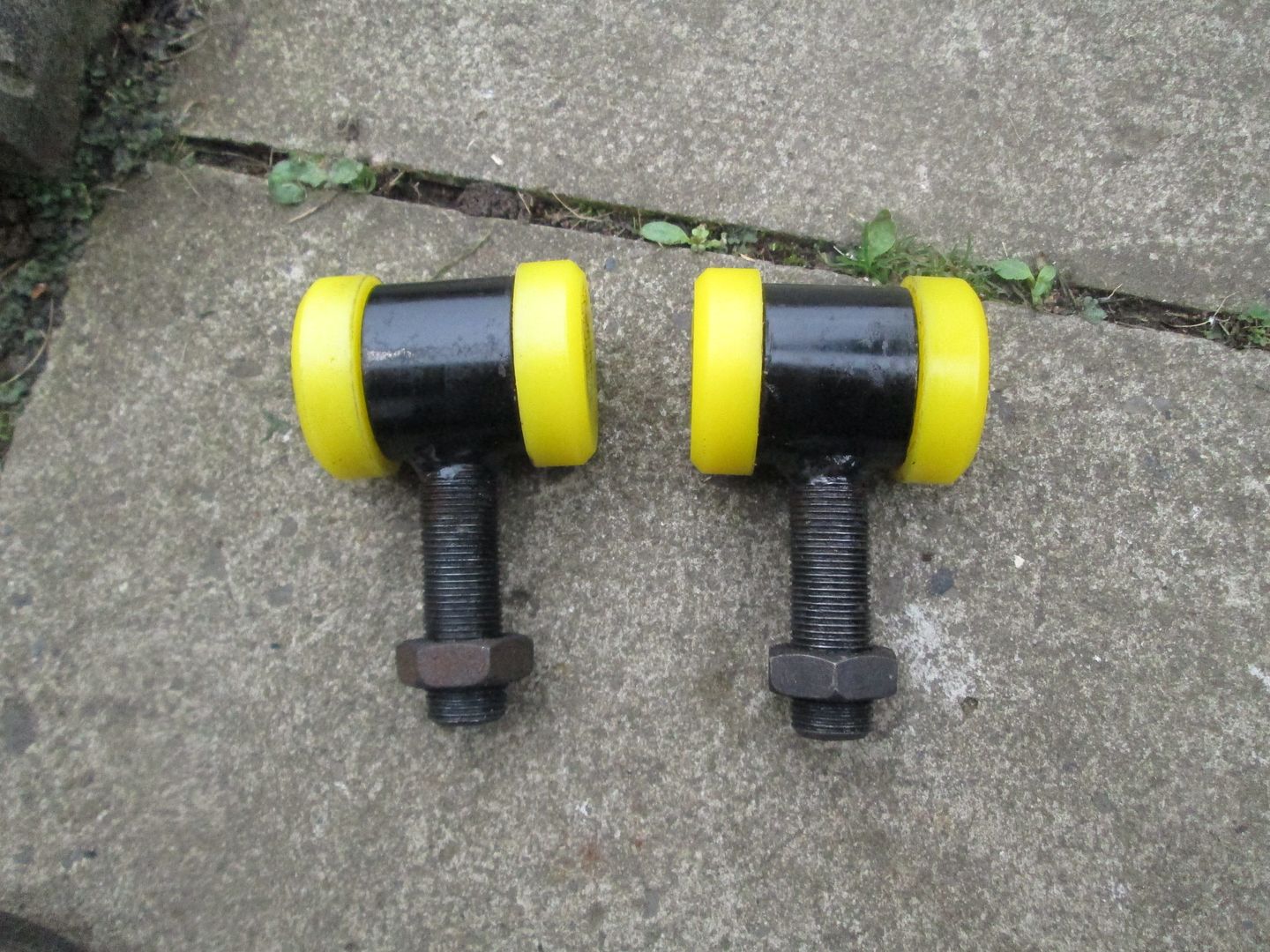
Then cleaned up, painted and assembled..
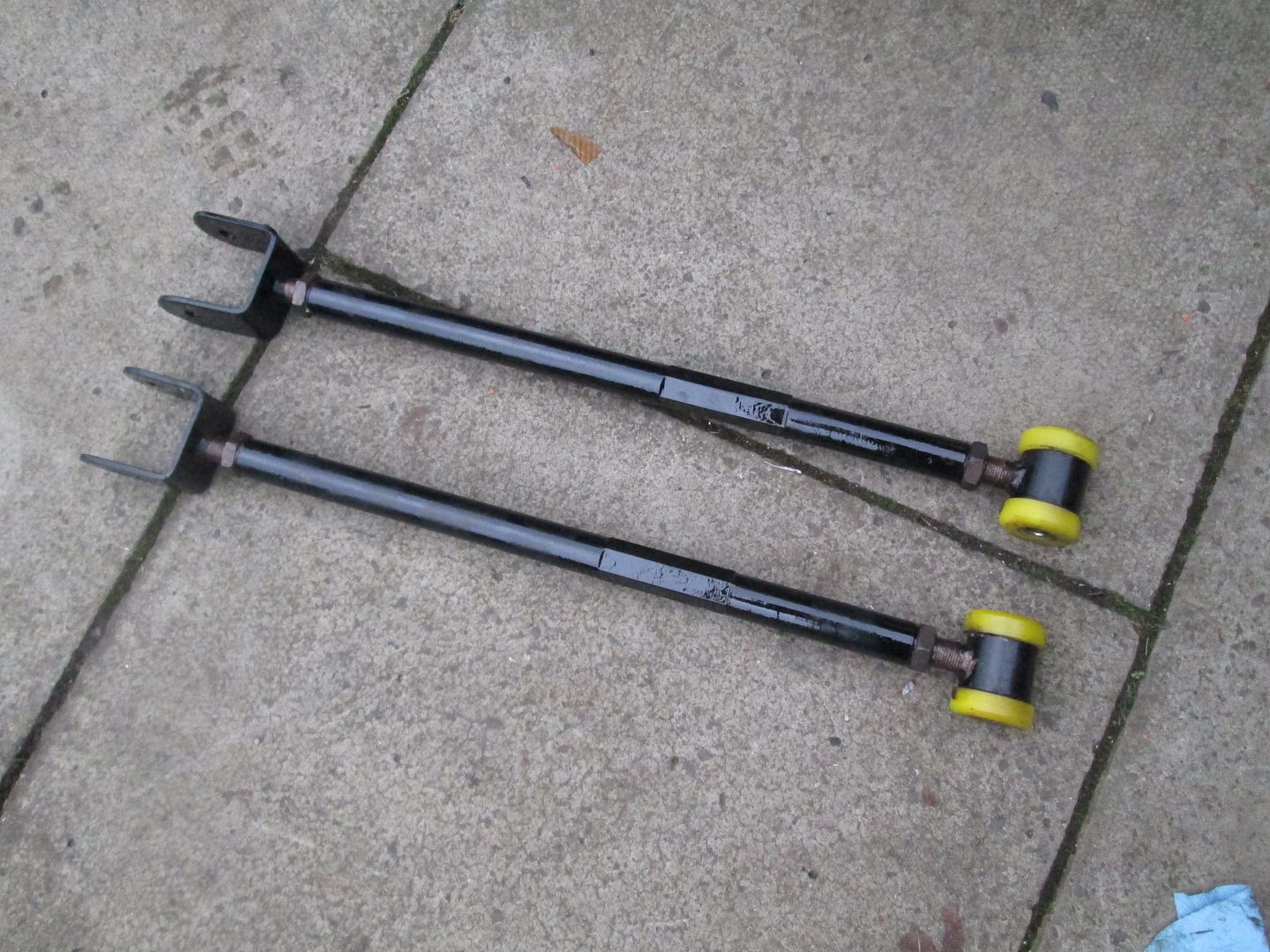
When the subframe was last built, I used a standard Lemforder bush on the upper inner control arm. The same supplier that stocks the above bush also have a polybush for this location, so it made sense to swap it also.
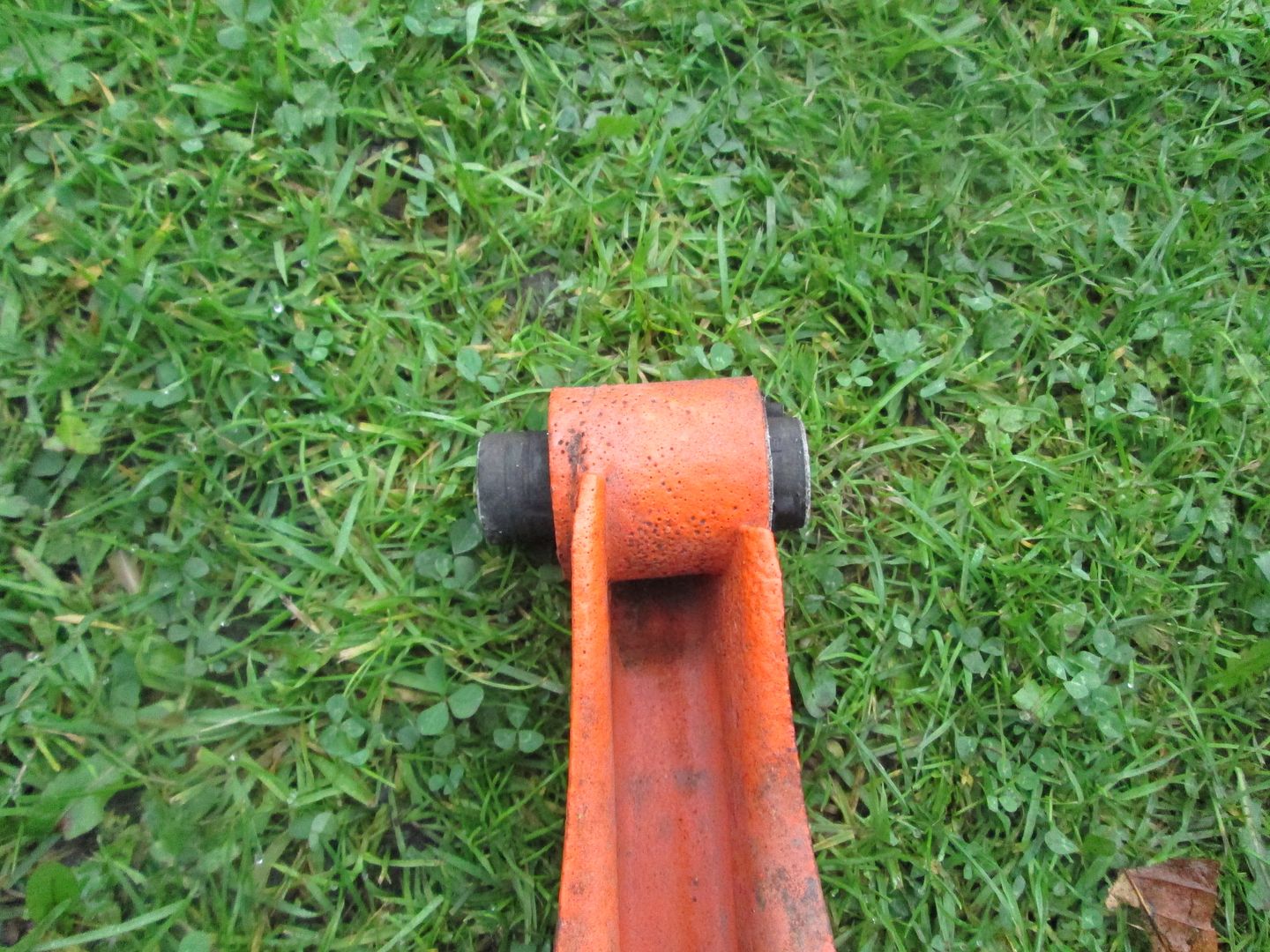
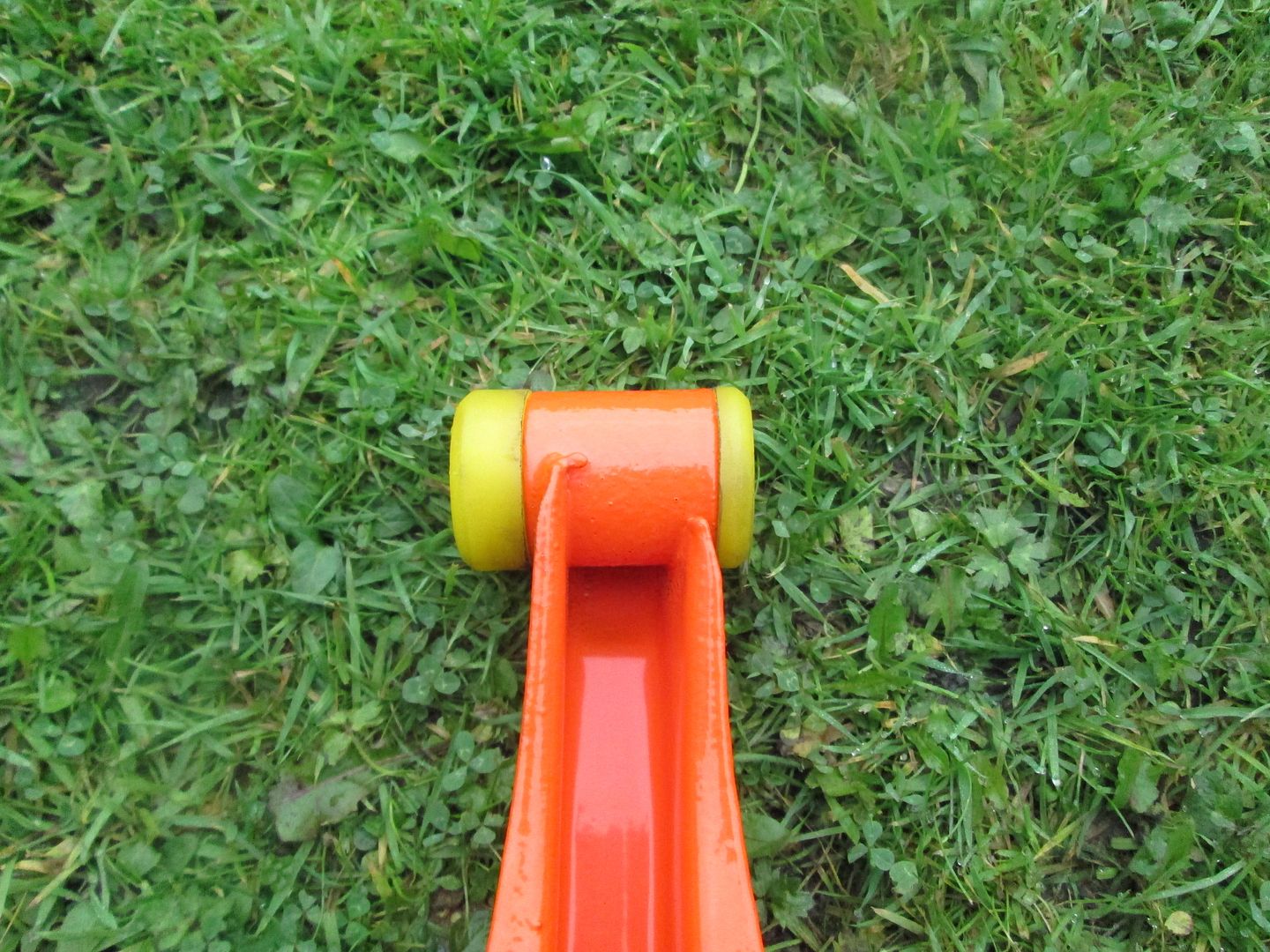

The above set of trailing and control arms were then bolted up to the car with the shock and spring, with new hardware. When the trailing arms were powder coated, the M3 3.2 rear calipers were also stripped and done. I then built them up with new seals and pistons.
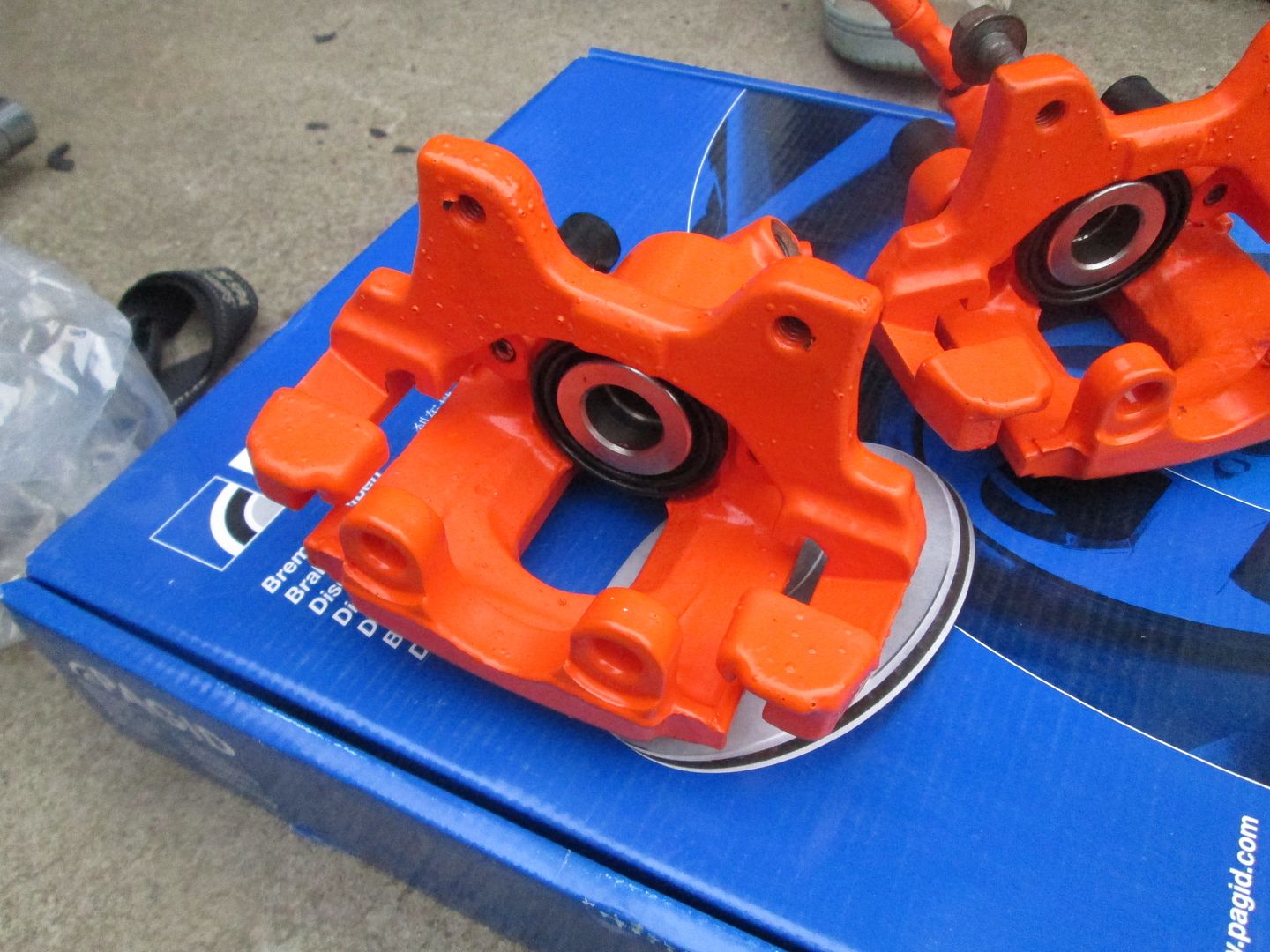
Got some CL RC5+ (to match the fronts), with new discs, and put them on the car..
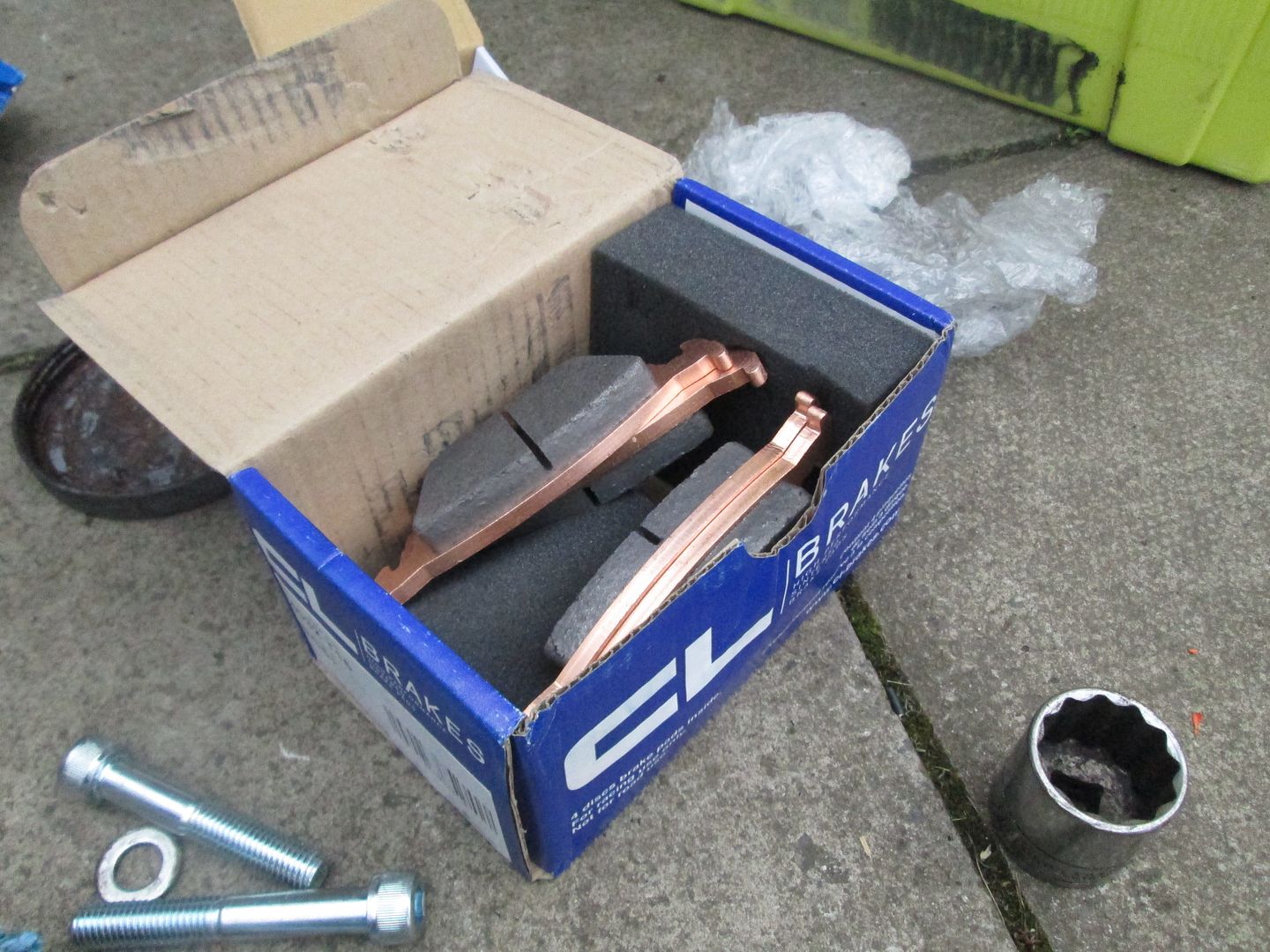
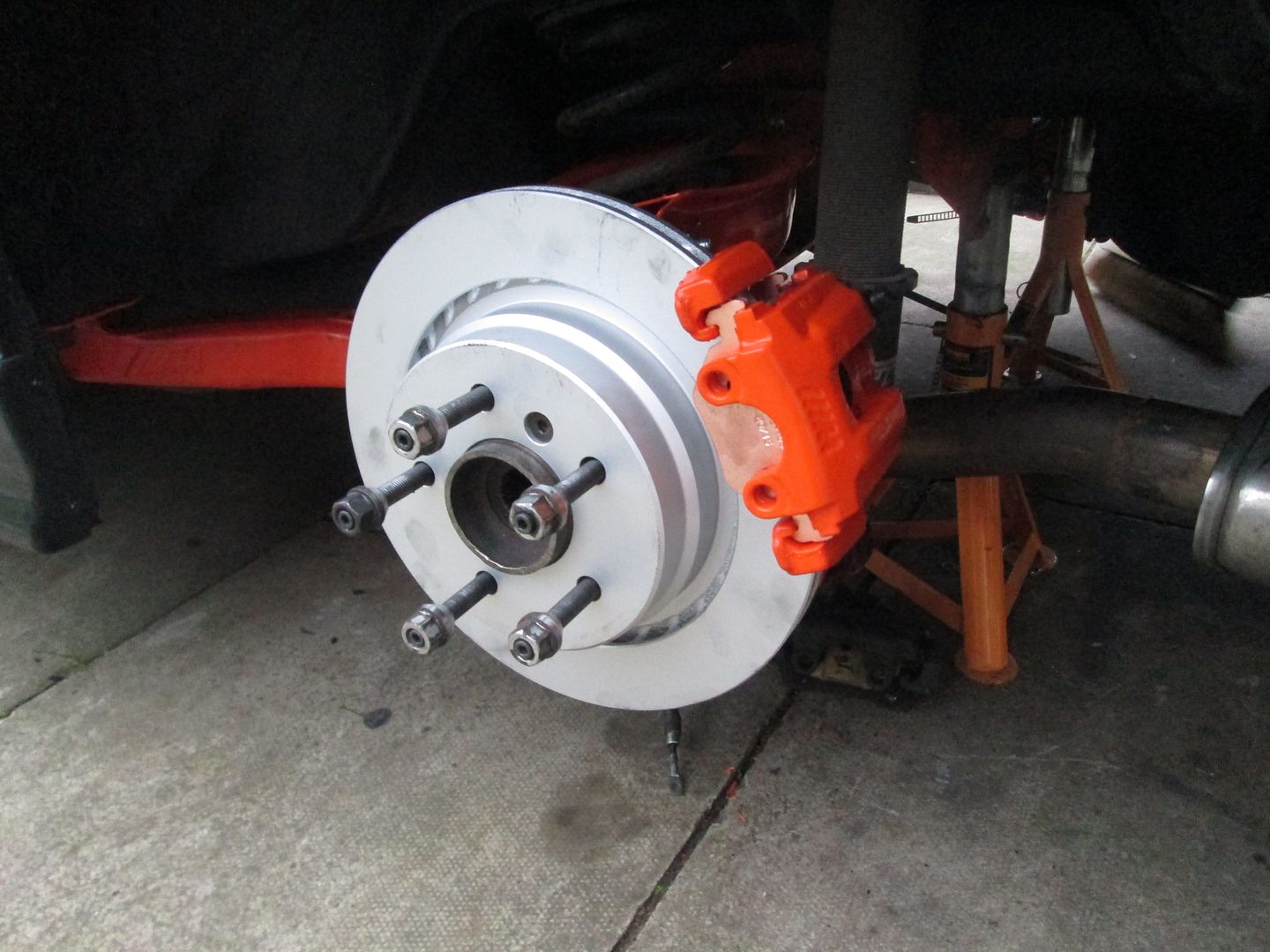
This has taken it from 276x19mm > 312x20mm.
There has been a massive amount of changes over the past month, with the above being just one. Days have been spent stripping l excess wiring out of the engine and interior looms, then rewrapping everything and generally tidying things up. This saved a good 4-5kg which I could not believe - there is so much rubbish in there. You always think these are going to be 'quick' jobs but they are so time consuming. The cooling fan has also been re-wired so the ECU controls the relay, rather than a radiator switch, and a manual override added.
With the rear end components replaced, I obviously needed to get the alignment done again. I decided to ditch the current 'normal' tyres I use for wet days (RainSport2) for a set of Michelin Pilot Sport 3's. Still using the Federal RS-R on my other set of wheels for dry days.
Once those were sorted, I had the alignment done. Previously, I ran:
Camber - 2.3deg Front, 1.8deg Rear
Toe - 0 Square Front, Total 20' Toe In Rear
I have now changed this, increased camber and a tad more rear toe:
Camber - 3.1deg Front, 2.4deg Rear
Toe - 0 Square Front, Total 30' Toe In Rear
The rear is now around the 'stock' M3 3.2 spec, alignment wise with camber and toe. I will have to see how it feels and go from there - the additional poly bushes on the rear arms are noticeably different.
Next up was a change in gearbox mounts - the standard ones do not last long and go soft over time. There are a number of companies selling poly mounts, but I wanted to avoid the 'bolt through the middle' style as no doubt it would just drastically increase noise and vibration. Quite a number of people use the RevShift mounts, which are made by a small company in the US. I ordered a pair and a couple of weeks later they dropped through the letterbox..
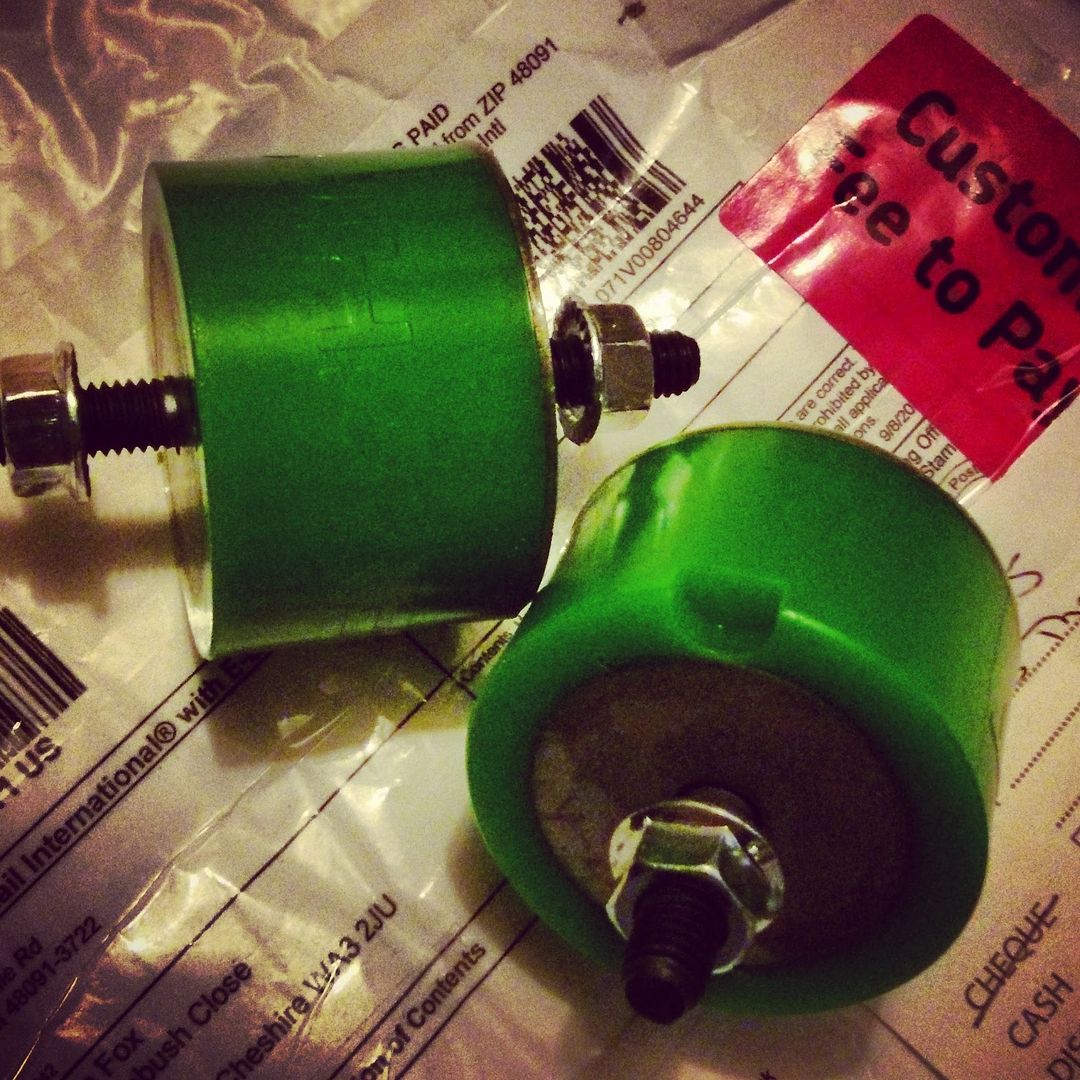
They were then fitted, and I also changed the gearbox oil at the same time. My gearbox has been noisy for some time, and the oil has already been changed (75w90) around 12 months ago. I suspected the level may have been low, or it just wasn't thick enough, even though its the recommended grade. Since using the single mass flywheel I have also had gearbox 'chatter/rattle' on idle, which goes once you are moving, but it was annoying. Many people have had success with mixing RedLine oils, but the two I needed are not really readily available. I went for the Lightweight Shockproof instead...

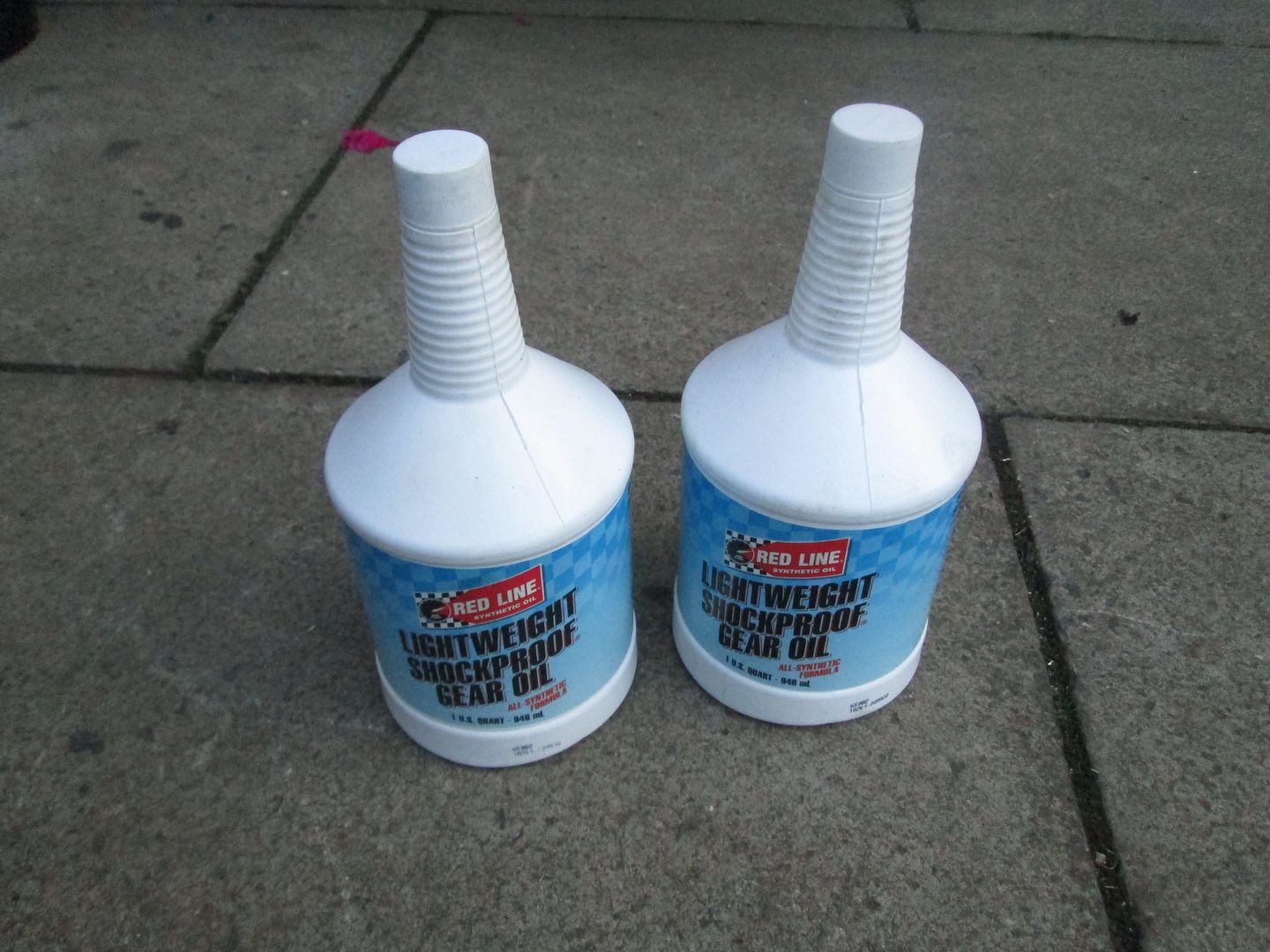
Luckily this seems to have had a great effect, as shifts are now 100x smoother and 90% of the noise has gone.
With the track day at Spa fast approaching I had a list of things that needed sorting, as I had been putting them off all year. With one of the requirements being a fire extinguisher, I debated for some time about what to do. Hand held would be sufficient, but you still have to unclip it, take the pin out and then use it, all whilst trying to get out of the car over the cage, etc. With having the cage, and getting out being the highest priority in case of fire I wanted something a bit more substantial.
I ended up opting for a plumbed in system, went with OMP over Lifeline but either would have sufficed. I also wanted to have the electrical system isolated, as if the fire was actually started by an electrical fault in the event of a crash the extinguisher would be useless. This ended up being a massive time consuming job. I already had most of the inlet system removed from the engine at the time as the loom was being trimmed - which gave good access to sort some bulkhead fittings for battery cables / extinguisher piping.
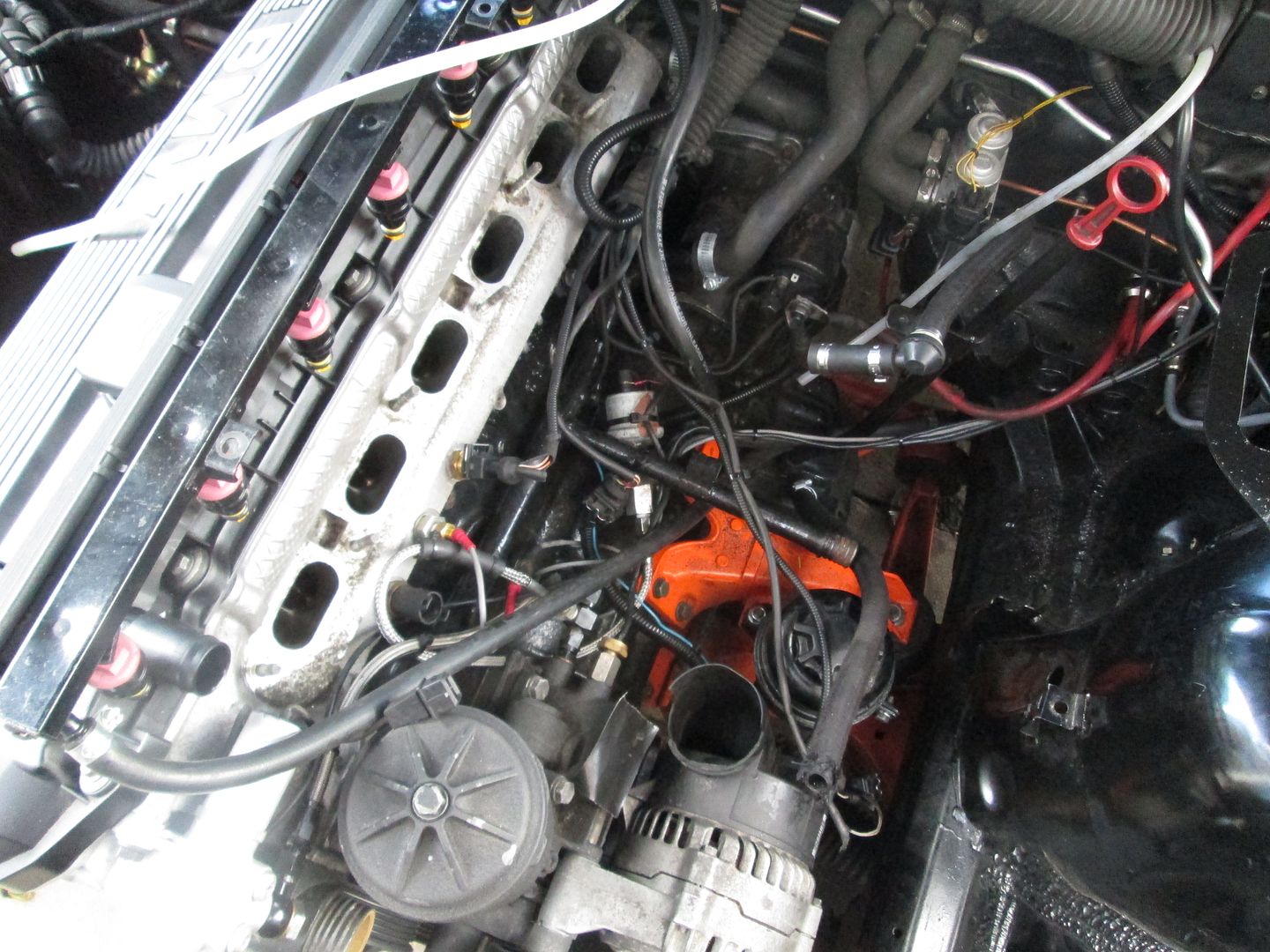
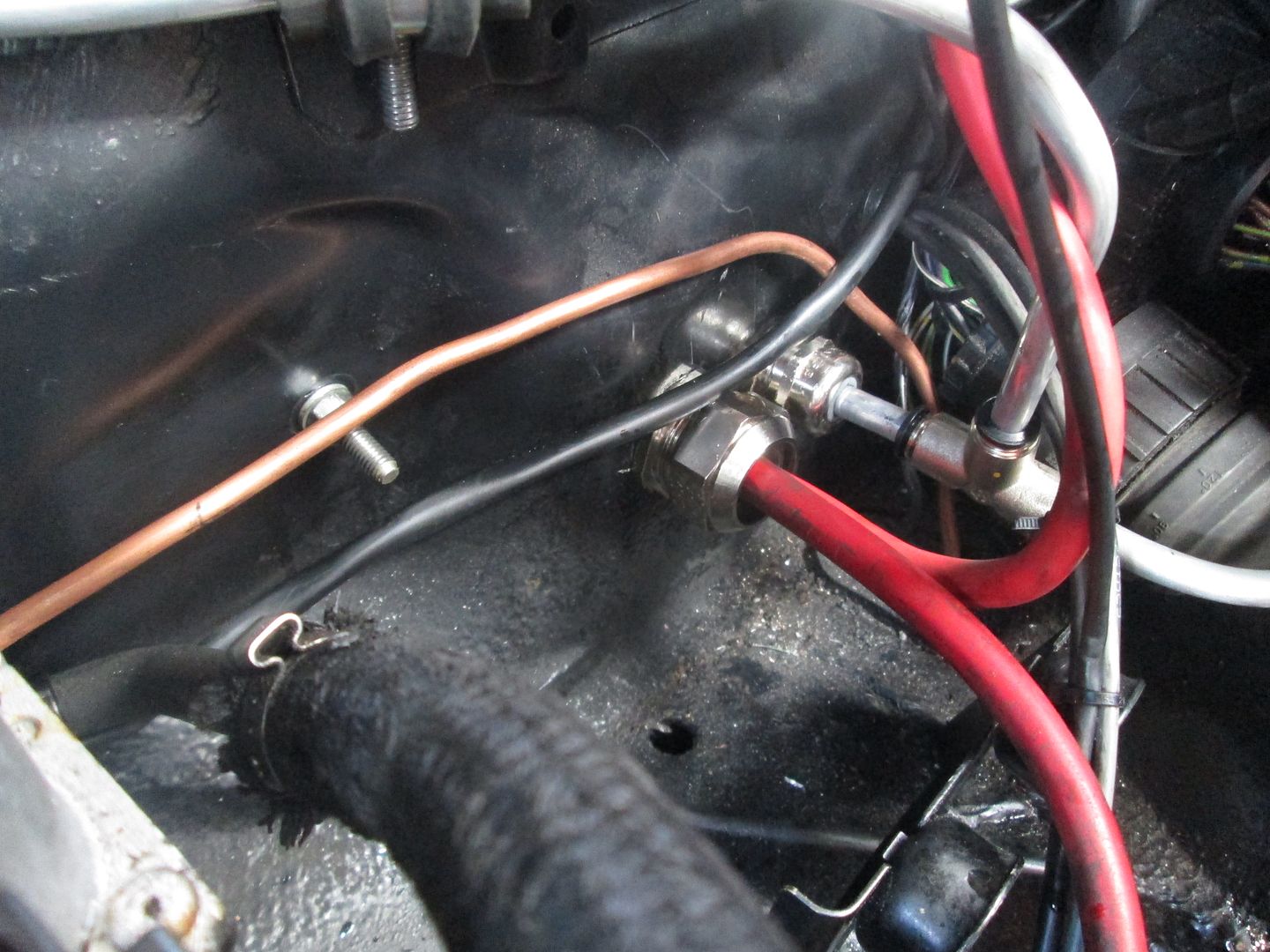
The next problem was mounting two pull cables on the outside, as the bonnet comes right up to the windscreen on the E36. I got a bit creative with the 'vents' in the top of the bonnet, and notched them out so the pull handles would go through. Mounting bracket was then made, and cables passed through to the inside via the scuttle panel using a grommet.
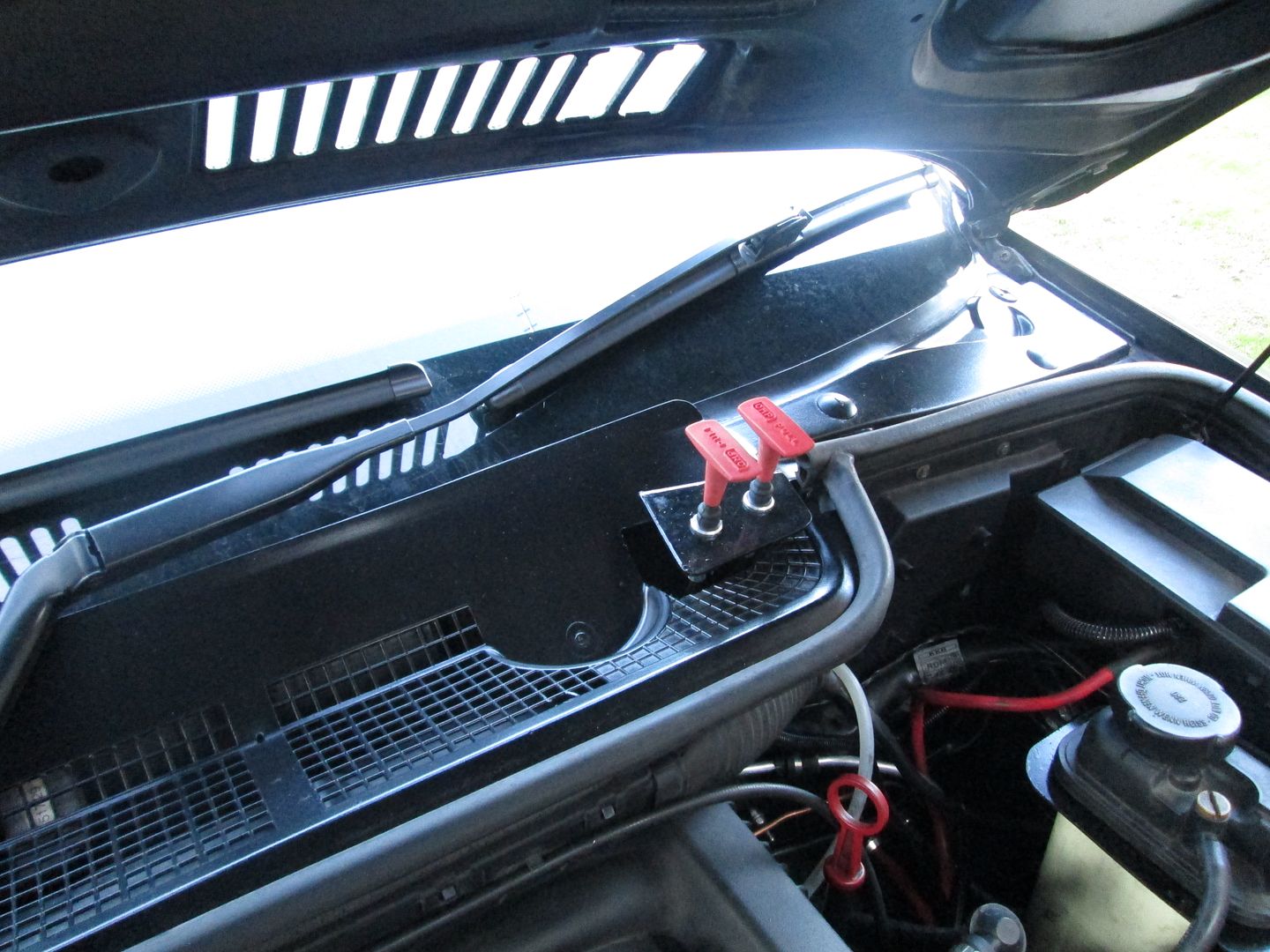
Two nozzles were put in the engine bay and piped up (exhaust and inlet side), you can just about see them on each suspension turret. The pipework runs round the back of the engine in the same mounts as the brake line. Two were also fitted inside, one in each footwell.
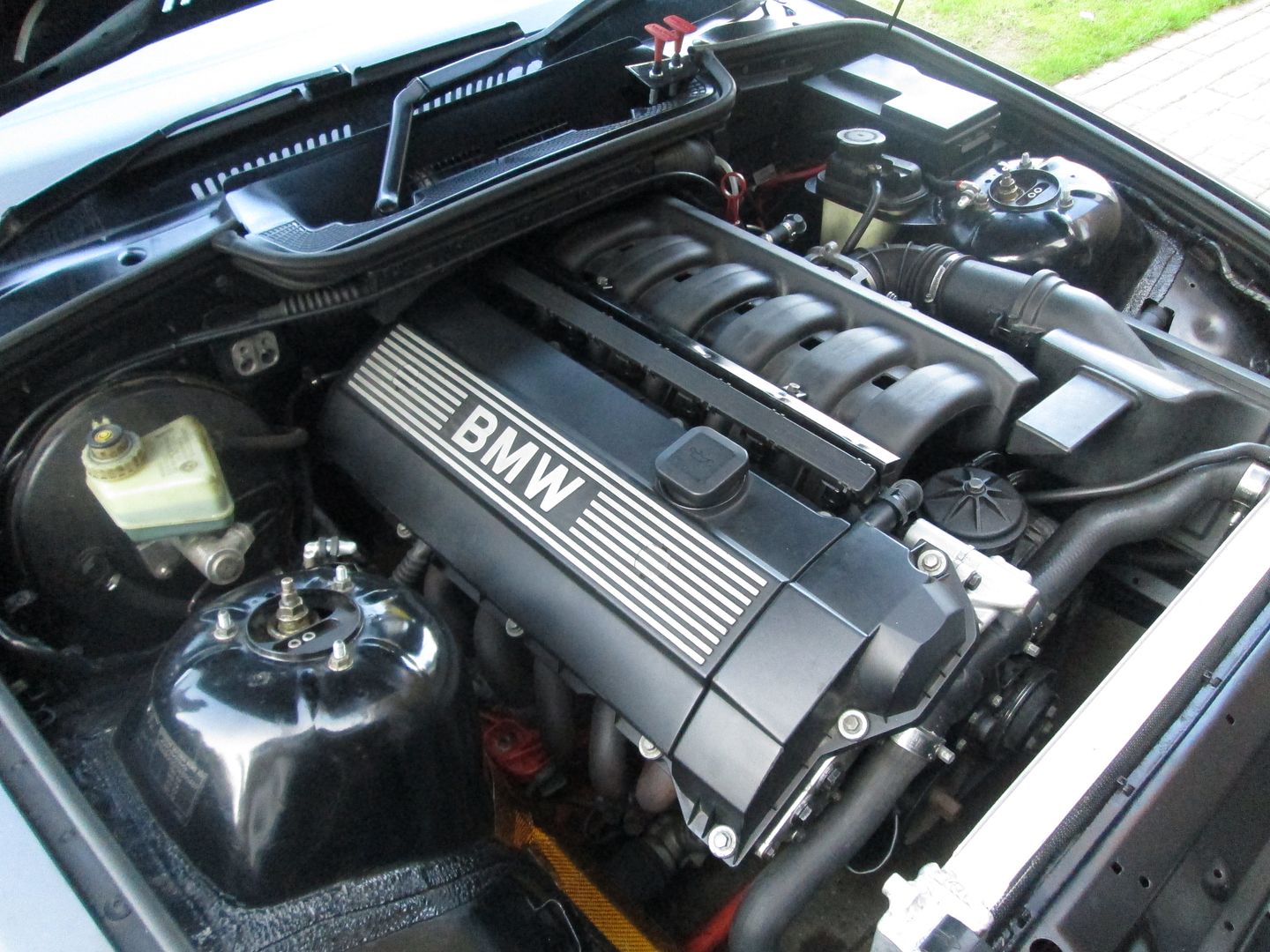
On another note, the whole exhaust side of the chassis, bulkhead and part of the tunnel have had reflective tape installed to try and keep some of the heat out of the cabin when on track. You can just about see some of this on the above picture.
The extinguisher bottle was mounted behind the passenger seat, and pipework ran down the passenger side of the tunnel.
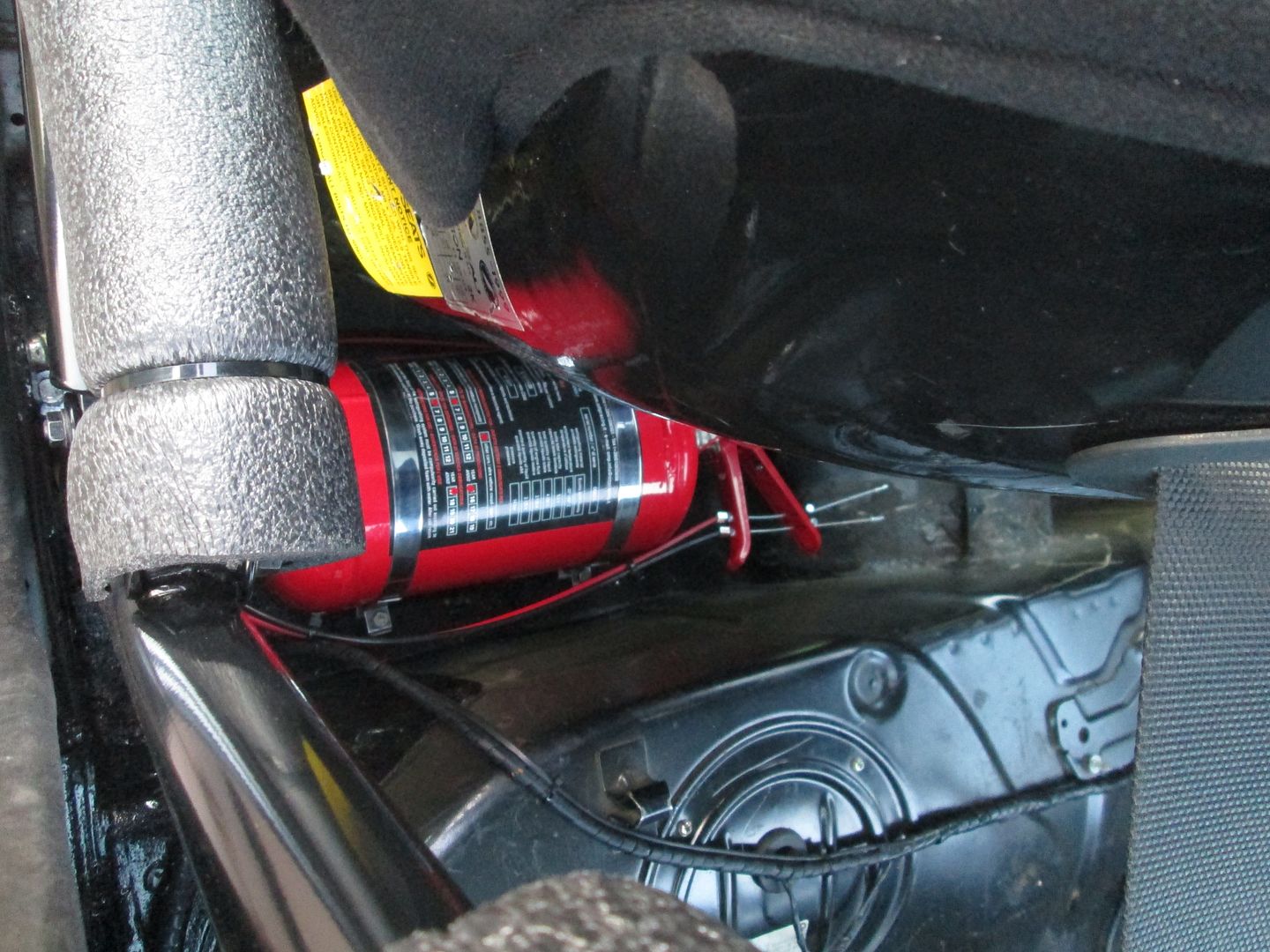
With that installed, I needed a pull handle inside to activate it if required. I also needed to mount the battery isolator, to which the exterior pull would connect. I had been meaning to move my gauges for some time, as the wideband used to be in the top centre vent, and the oil pressure/temperature in the middle of the clocks. I ditched the radio and made a panel to house them both on the dash, then mounted the isolator next to it. Swapped the clocks out and now I only have an aftermarket water temperature gauge in there.
At the same time, I replaced the standard OBC at the bottom of the centre console, which I had re-worked previously to use for the data logger. I now have a single switch for the data logger, so added some additional toggles for the radiator fan override, rear video camera power, etc. A bracket was made for the battery isolator pull cable and mounted to the dash - then a bracket was made for the extinguisher pull handle and that was mounted at the very bottom.

It all looks relatively simple, but making brackets, mounting things, is stupidly time consuming when doing a proper job of it. Obviously the extinguisher locking pin will remain in place when not out on a circuit.
Some other small jobs have also been done, like re-making the front brake ducts/mounts, moving charging points and adding new connectors to wiring, but never got any pictures of that. After a good month of messing about its pretty much ready for Spa, bar needing a quick clean.
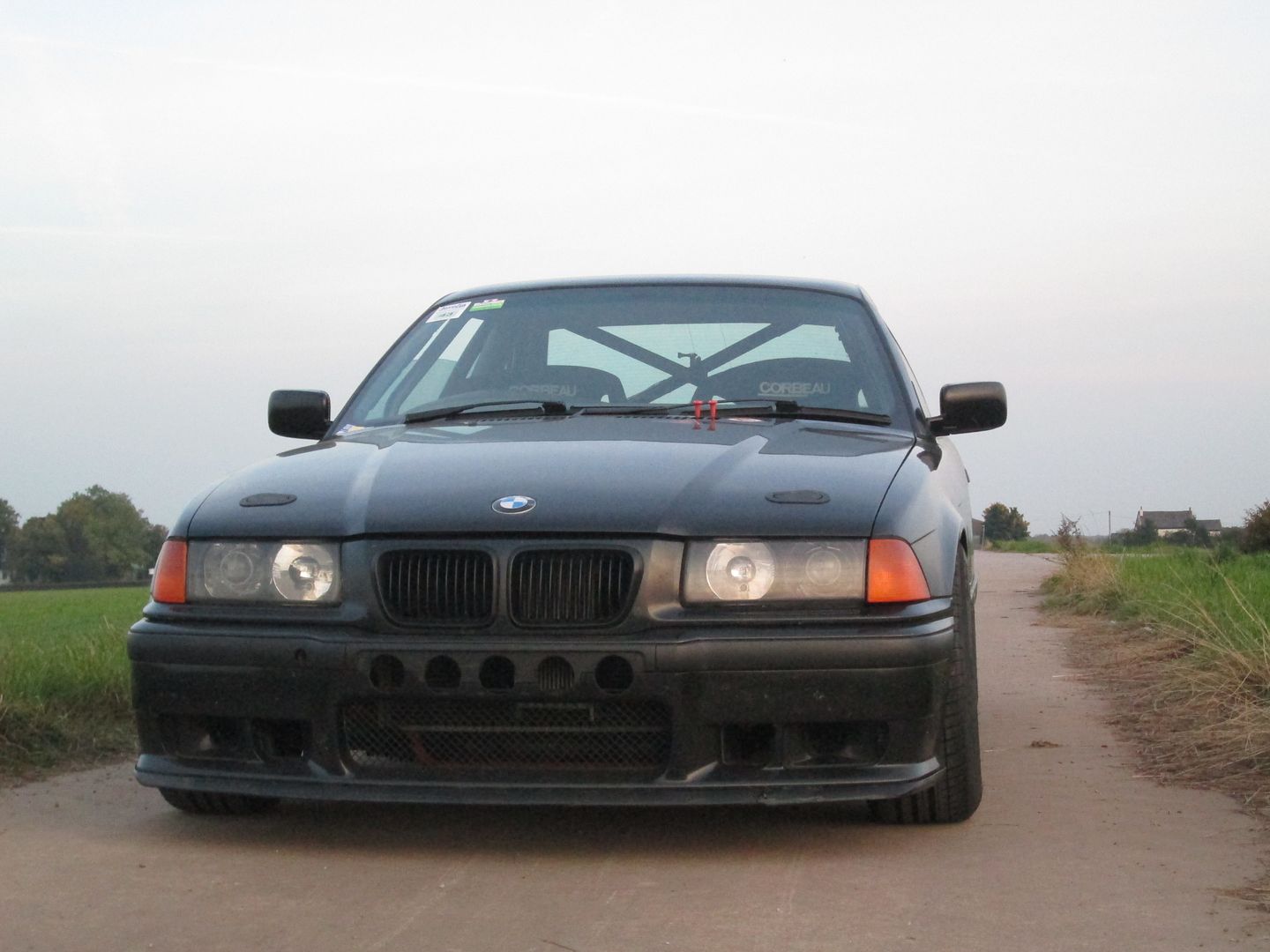
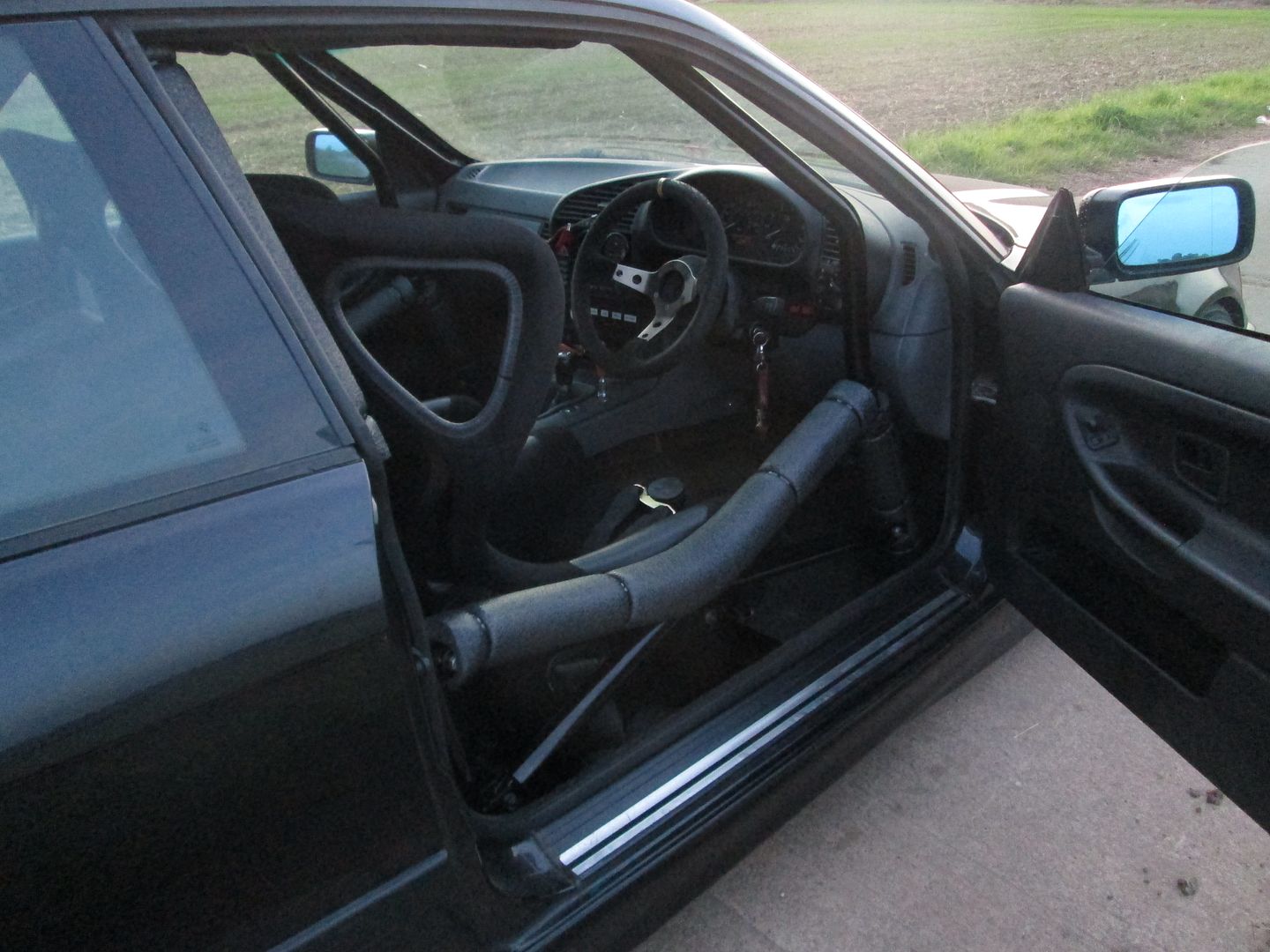
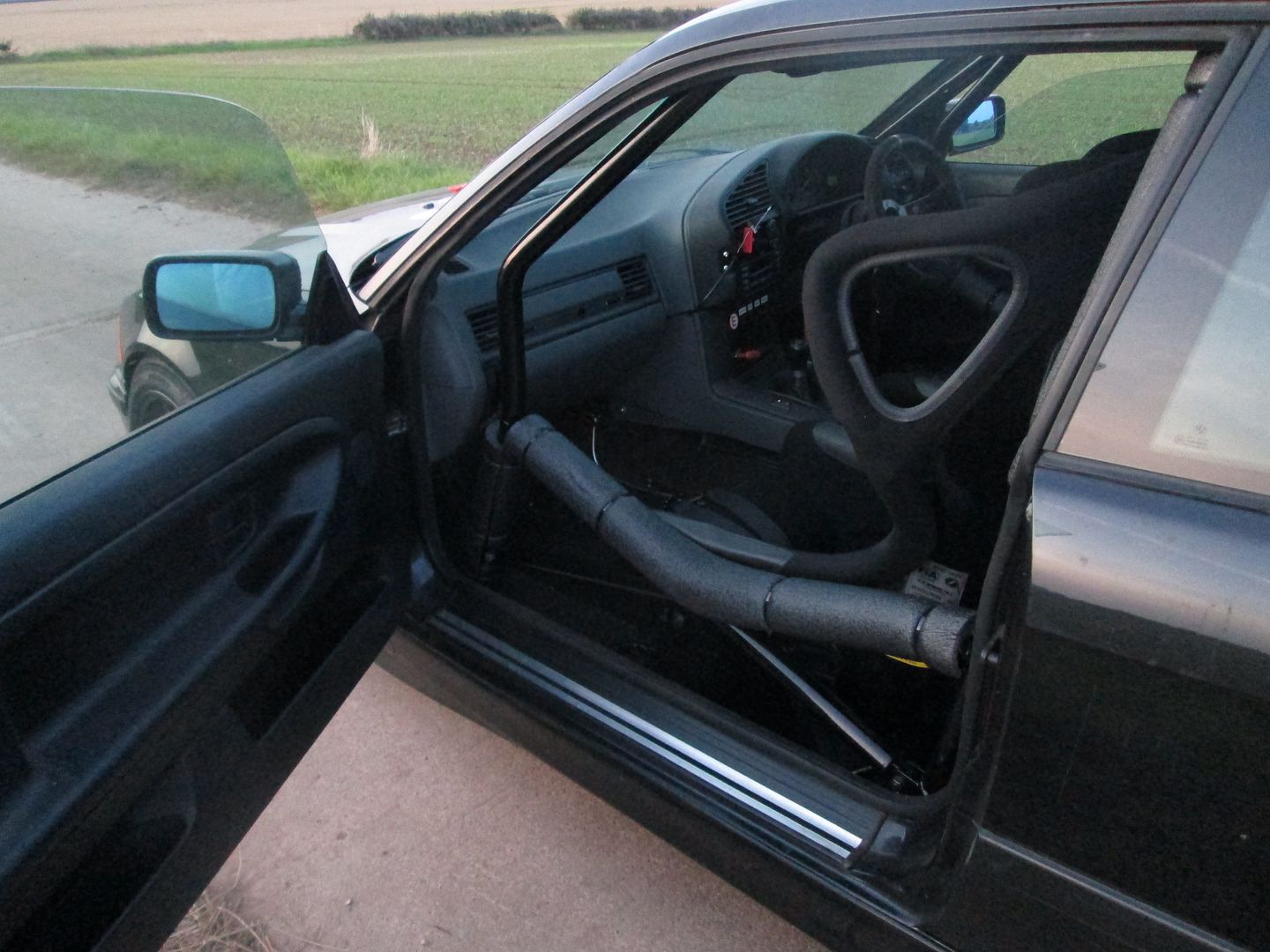
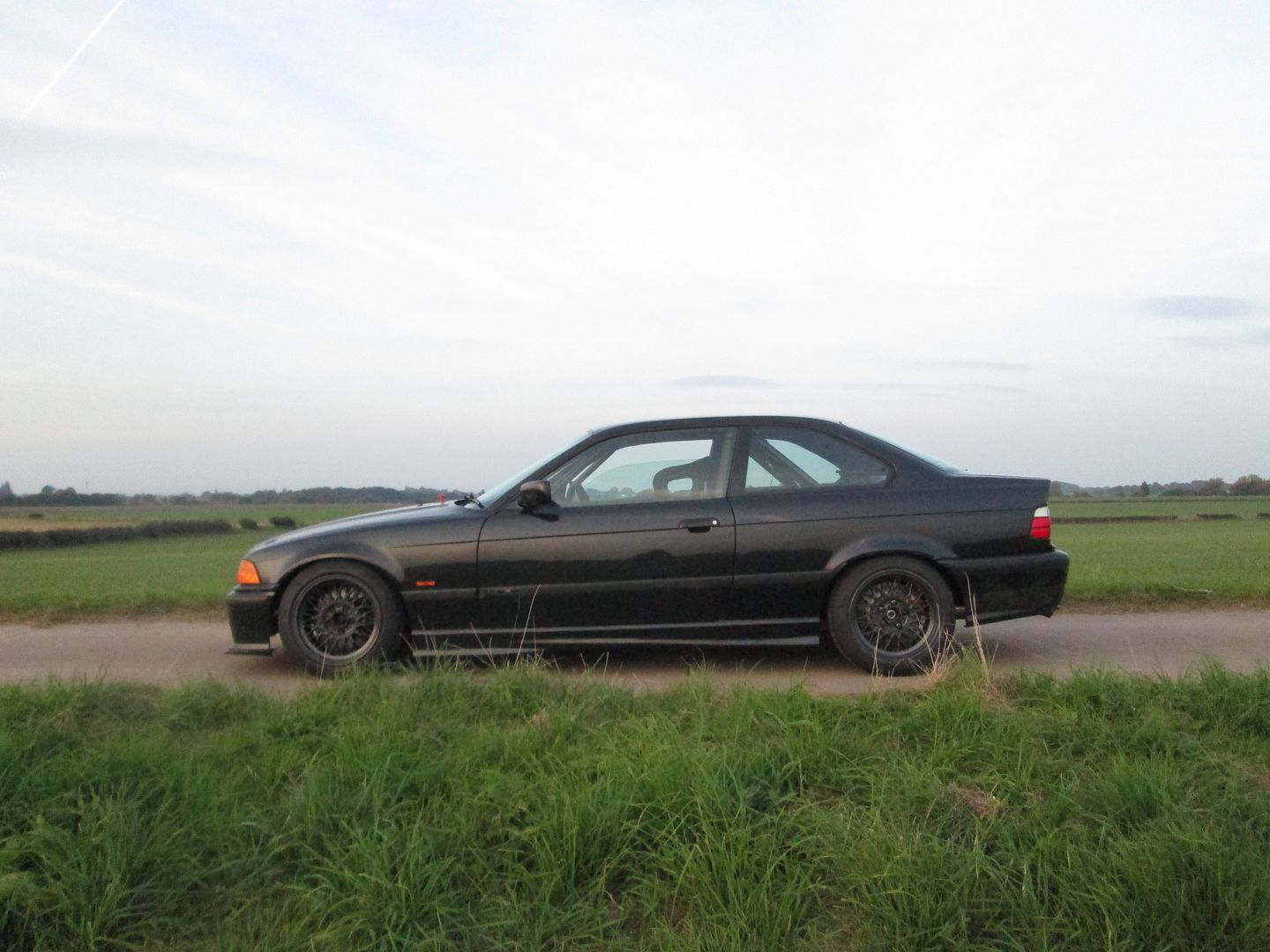
A couple of days before heading off for Spa I had the car out and noticed the wideband going off the scale at high RPM/wide open throttle. Panic set in and I thought there was an issue with either the map, fuel system or engine itself! I logged a bit of data and the wideband was bottoming out at 10.1...
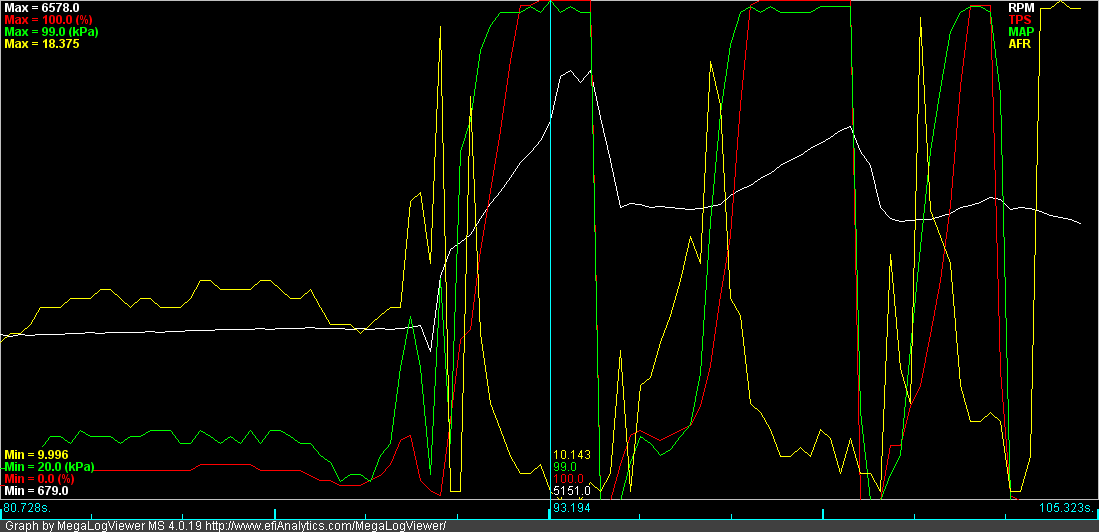
I initially checked the logs against some from the last track day at Cadwell, and everything seemed normal bar the wideband reading (trims, manifold pressure, etc). I swapped the fuel rail, fuel pressure regulator and checked over everything else in the dark after work but still the gauge was reading off the scale. I had disabled closed loop fuelling on the ECU at this point as I was confident the map was actually fine and it was possibly just the gauge/sensor playing up.
I spoke to Chris @ EFI-Parts who originally mapped it, explained the situation and he offered to run the car that very evening in his own time to double check the map and engine were fine as I was leaving the day after! We did a few power runs and instantly realised the wideband was completely broken, his own wideband reading was spot on and the car made the same power as it did when it was first mapped. Massive relief!

He keeps the wideband sensors in stock, so I got one from him and swapped it before getting on the ferry the following day. Old sensor:
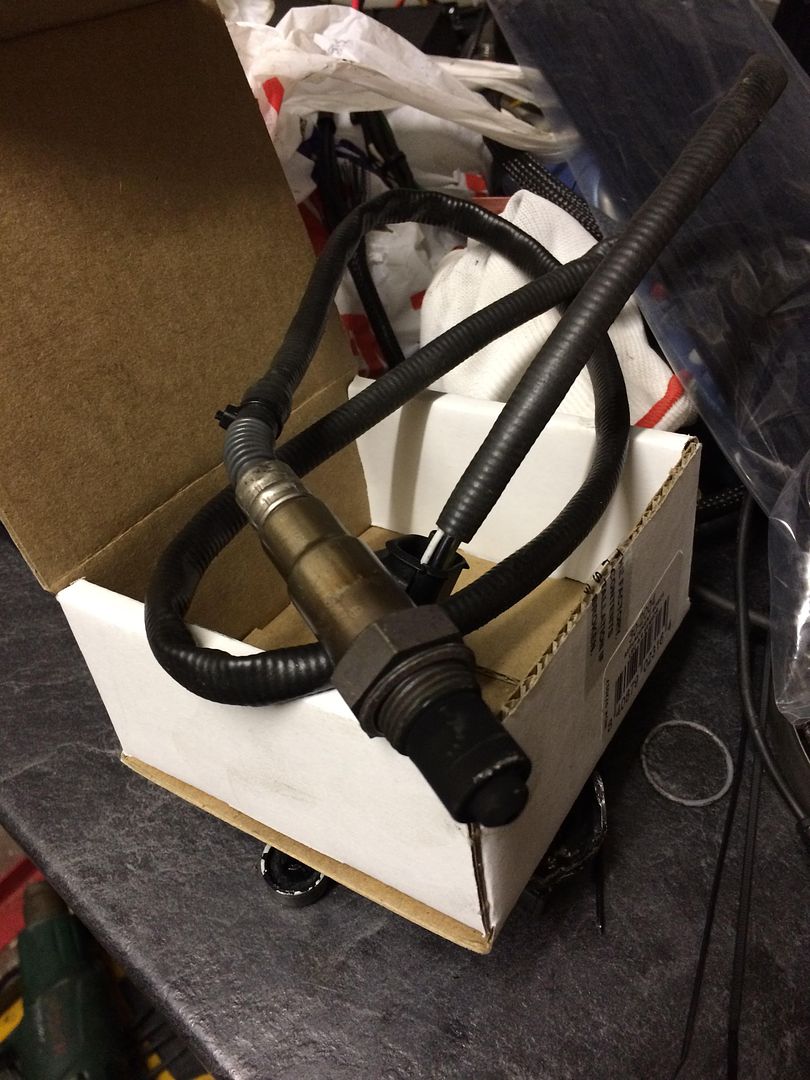
Loaded up the car and headed off to Hull to catch the overnight ferry - the forecast was changing by the hour and there had already been a covering of snow at Spa the previous day. Temperatures were around 2-3C, so we just had to hope for the best. I wasn't too concerned as I had the Pilot Sport 3's as an alternative tyre if the conditions were not up to the RS-Rs. We arrived in Stavelot late morning, 2C and raining. The forecast had improved for Friday, so we were hopeful.
The next day at the track, it was damp but the rain had stopped. I stuck on the Michelins all morning until a dry line started to appear just before lunch - in a way this was good as it gave an opportunity to learn the circuit at a slower pace. The car was issue free throughout the morning and the new alignment settings felt great, even in the damp.
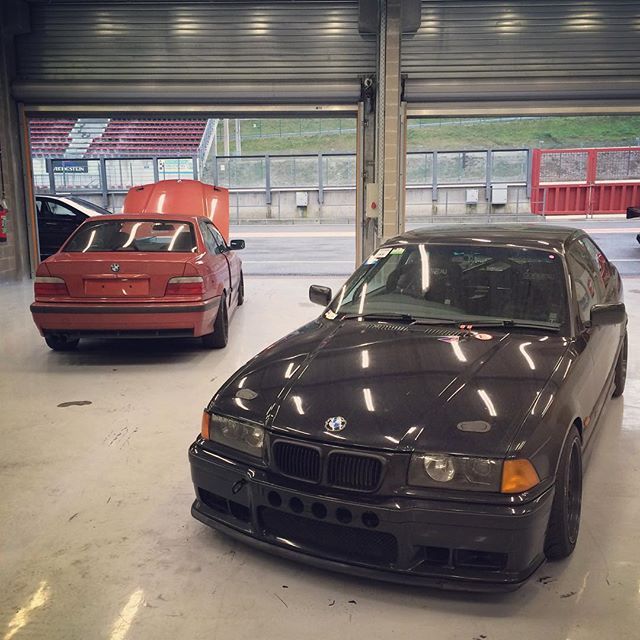
Swapped wheels to the Federals during lunch and spent most of the afternoon on track - covering just over 275 miles throughout the day.

https://www.youtube.com/watch?v=XYWqsVPLCd8
The car was spot on and drove fantastically in the dry, the rebuilt LSD gives far better traction from corners, and the new ratio seems to be a great match for the power band of the engine. Not to mention Spa itself, what a fantastic circuit. By far the best one I've driven so far, flows so much more than I ever expected.
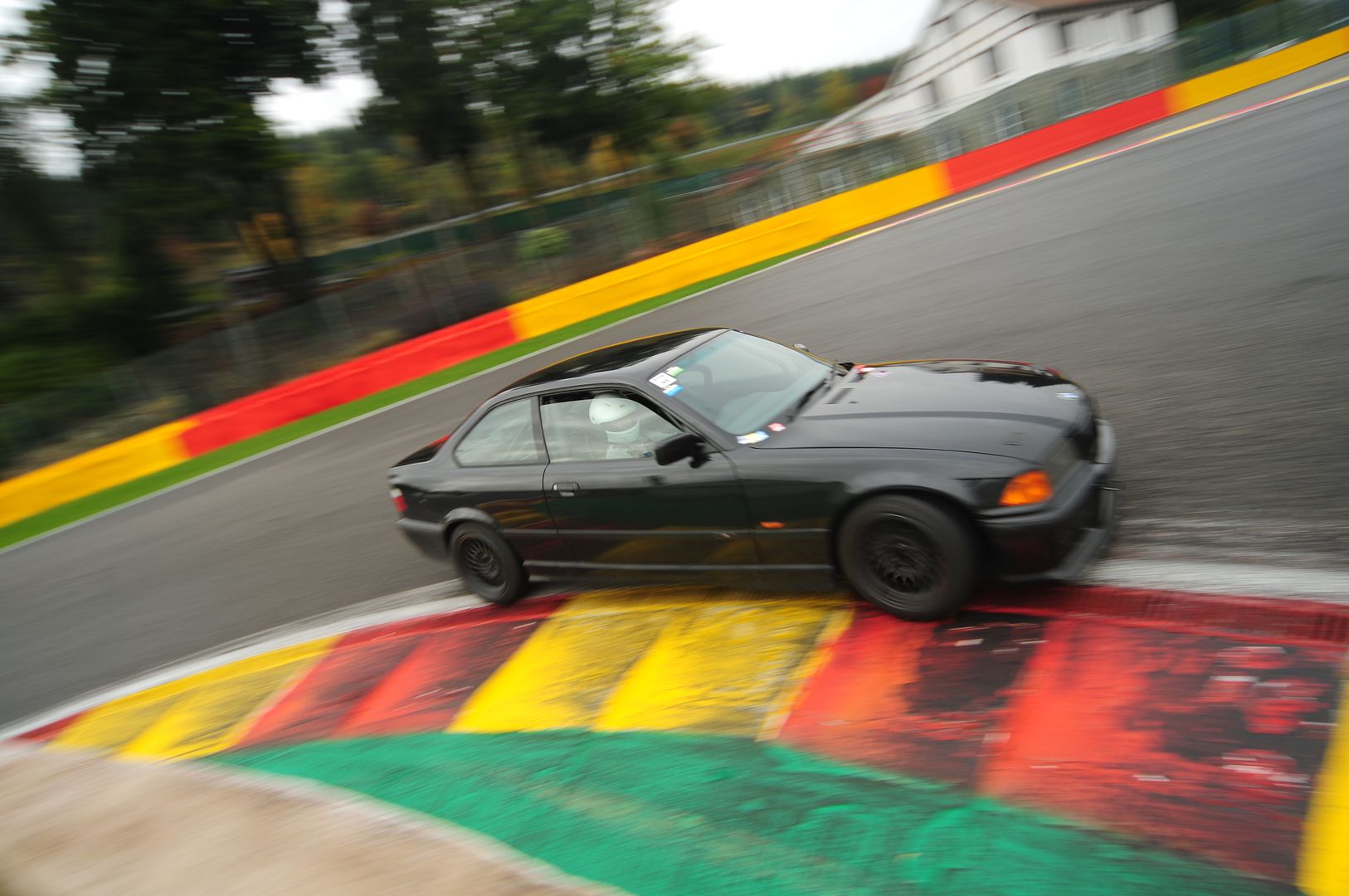
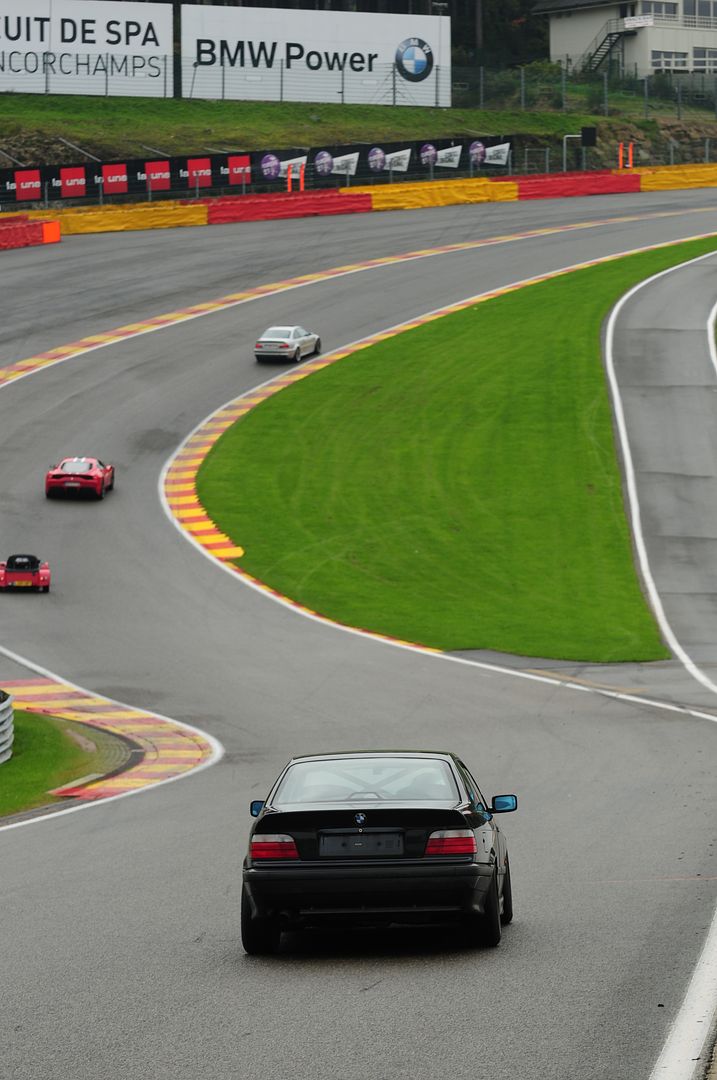
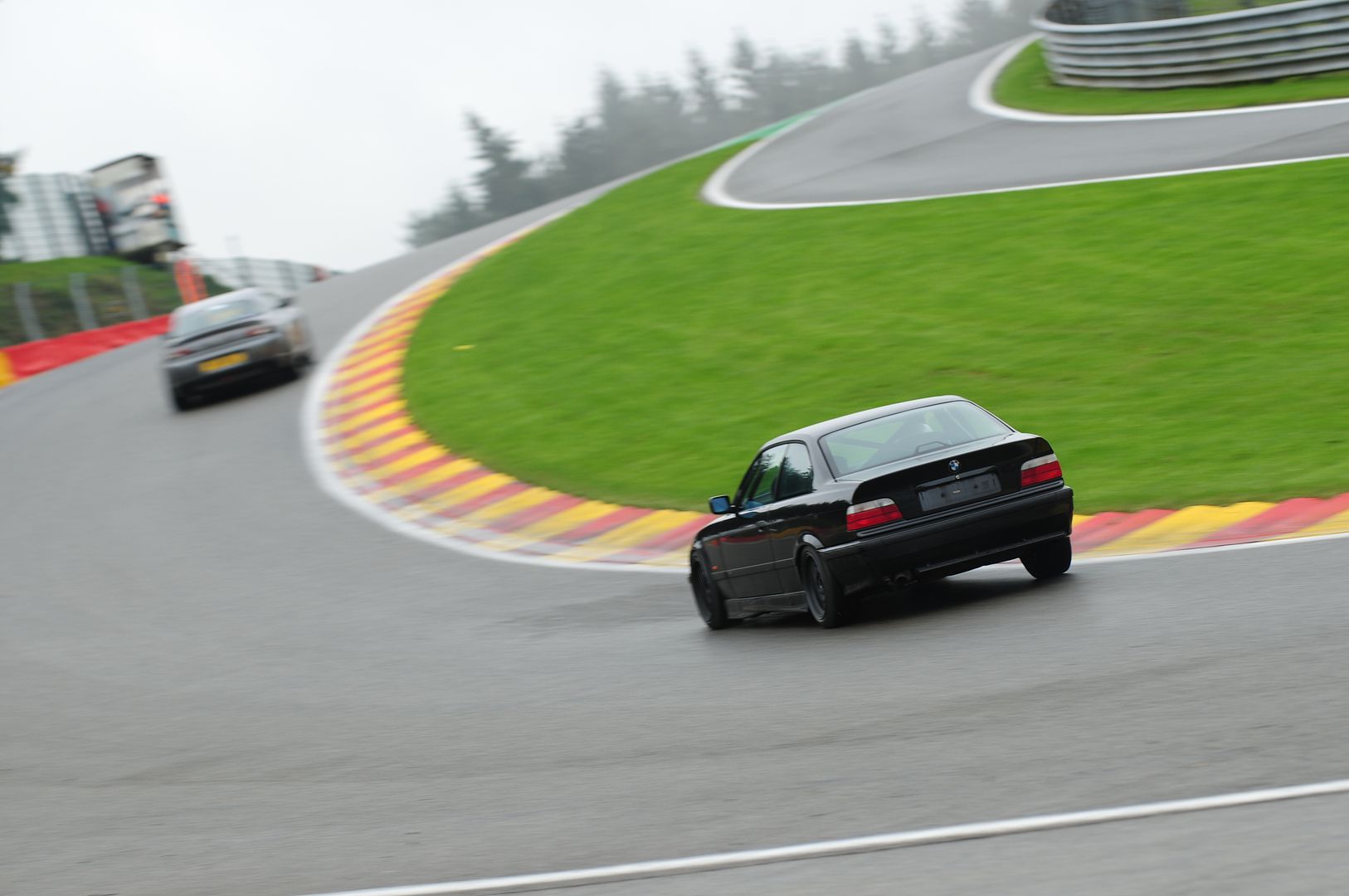
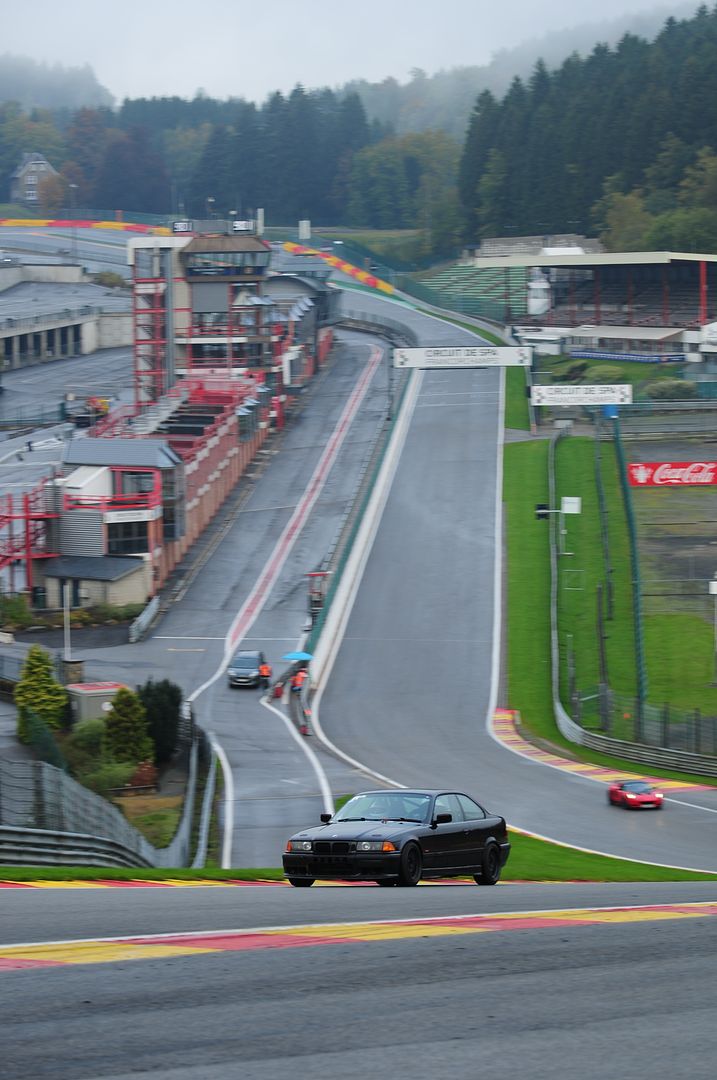
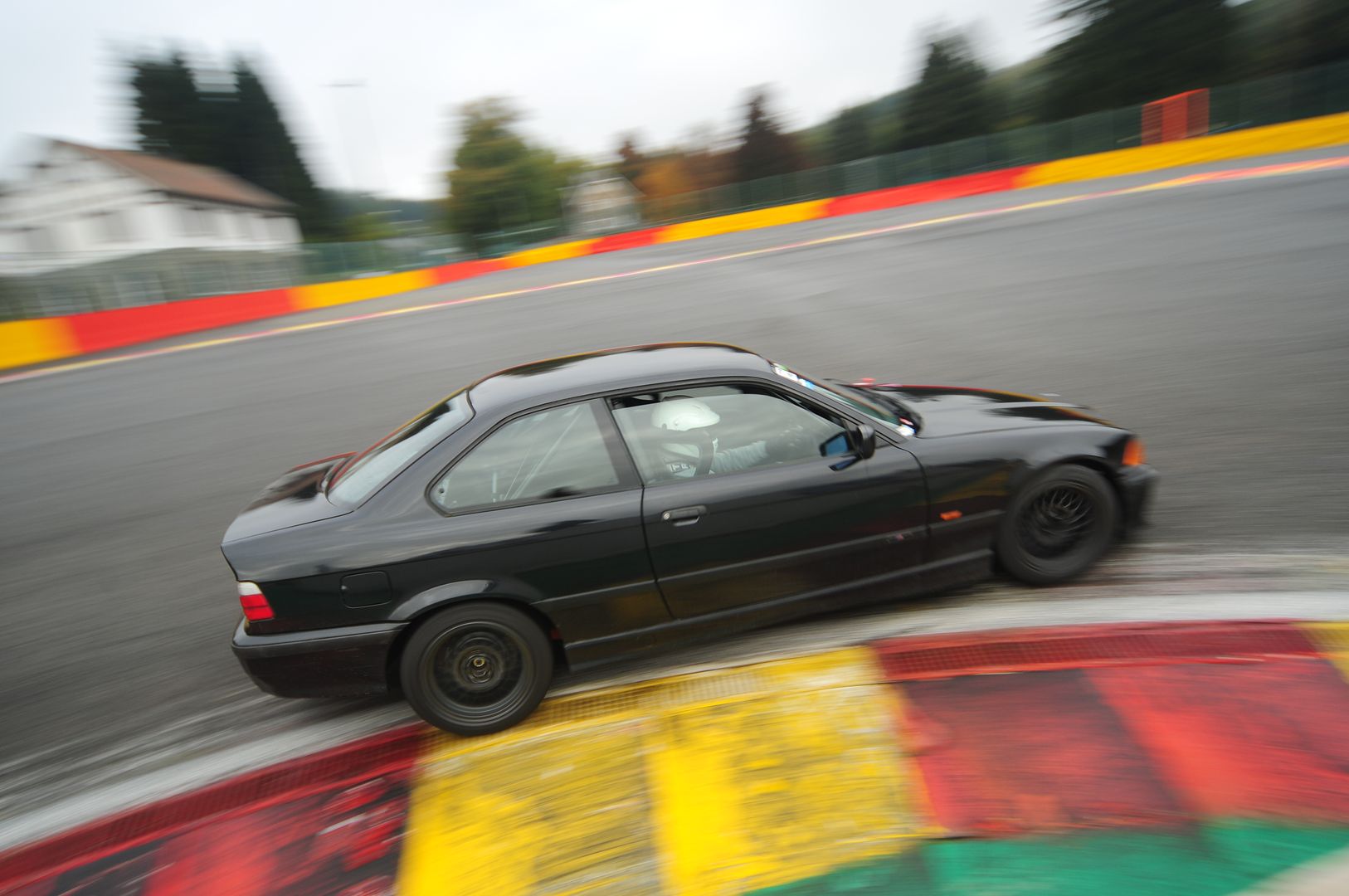
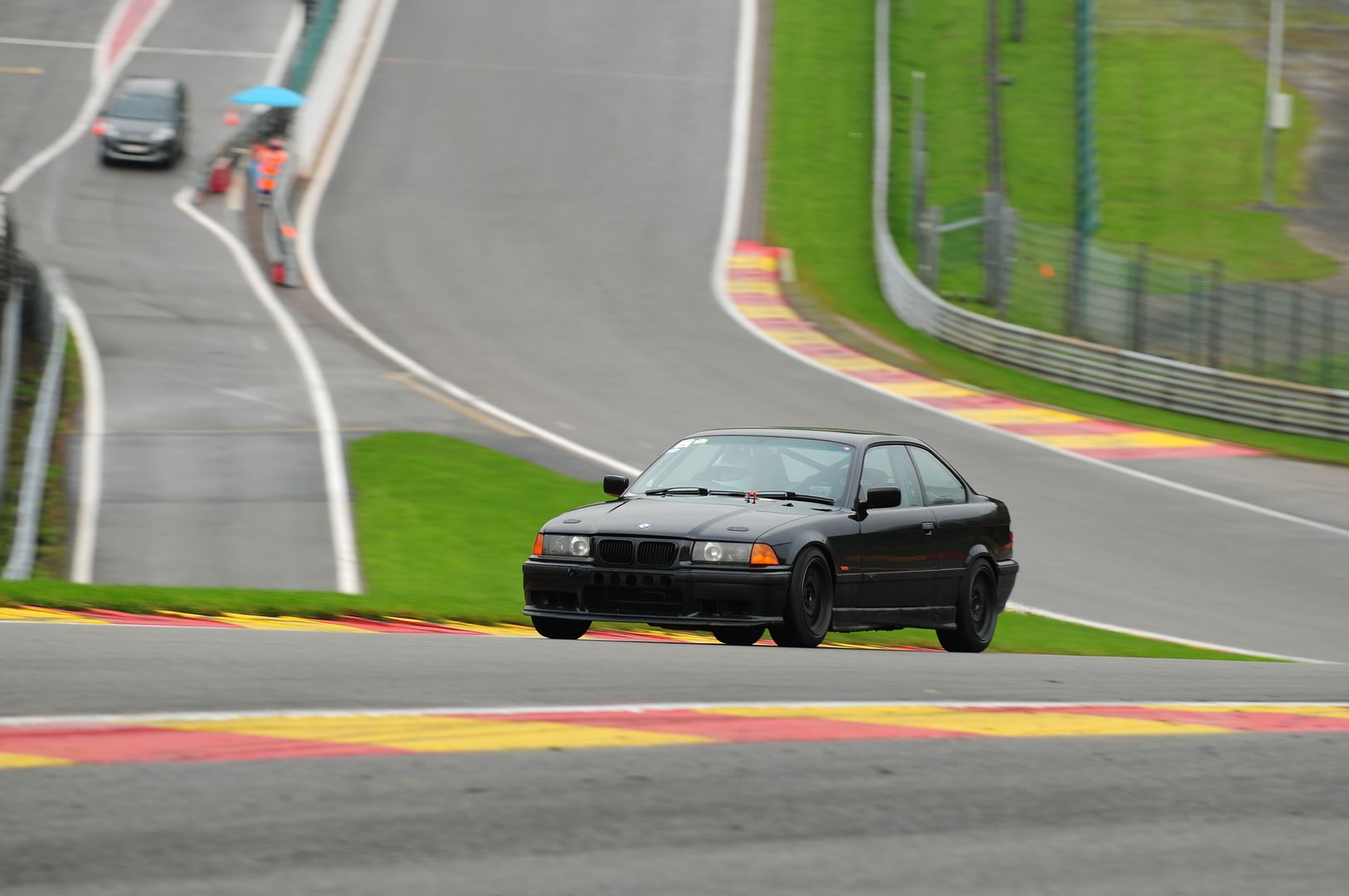
As the day went on the lap times dropped as I got used to the shorter gearing and available grip with the new alignment settings. 4th and 5th are now used most of the time compared to 3rd and 4th with the old ratio.
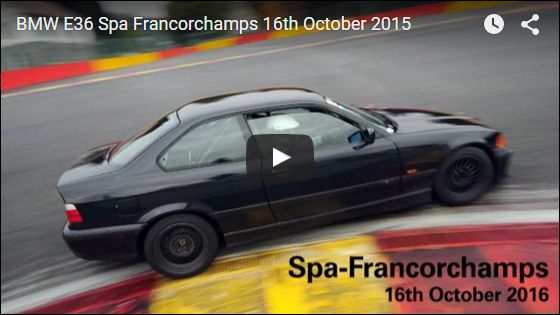
https://www.youtube.com/watch?v=HHuAj_4Z1ZA
Pleased to report the 'problem hub nut' is still locked in place and has not moved, which has made the rear end swap worthwhile! Just need to put some fuel in ready for Donington next week and take it from there!
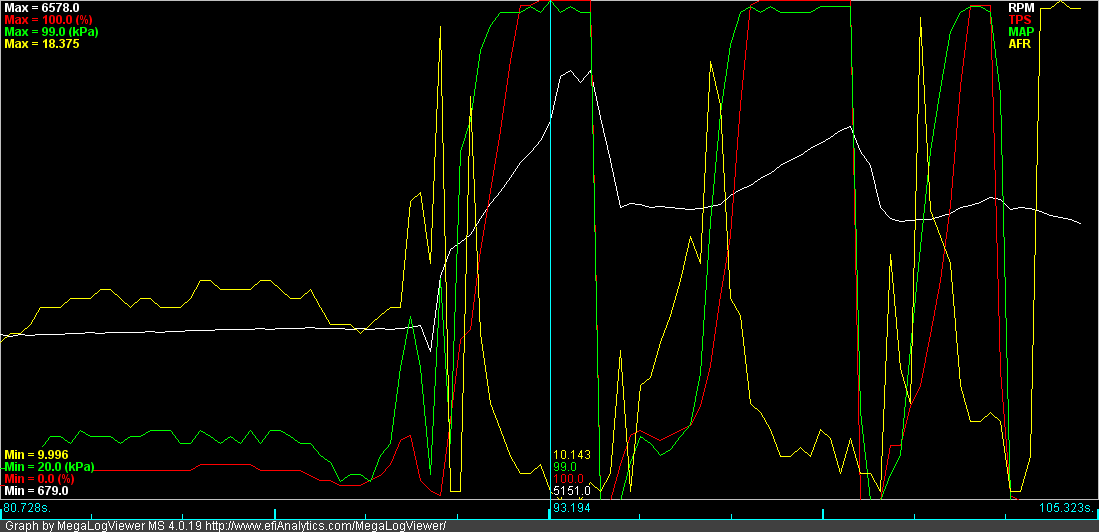
I initially checked the logs against some from the last track day at Cadwell, and everything seemed normal bar the wideband reading (trims, manifold pressure, etc). I swapped the fuel rail, fuel pressure regulator and checked over everything else in the dark after work but still the gauge was reading off the scale. I had disabled closed loop fuelling on the ECU at this point as I was confident the map was actually fine and it was possibly just the gauge/sensor playing up.
I spoke to Chris @ EFI-Parts who originally mapped it, explained the situation and he offered to run the car that very evening in his own time to double check the map and engine were fine as I was leaving the day after! We did a few power runs and instantly realised the wideband was completely broken, his own wideband reading was spot on and the car made the same power as it did when it was first mapped. Massive relief!

He keeps the wideband sensors in stock, so I got one from him and swapped it before getting on the ferry the following day. Old sensor:
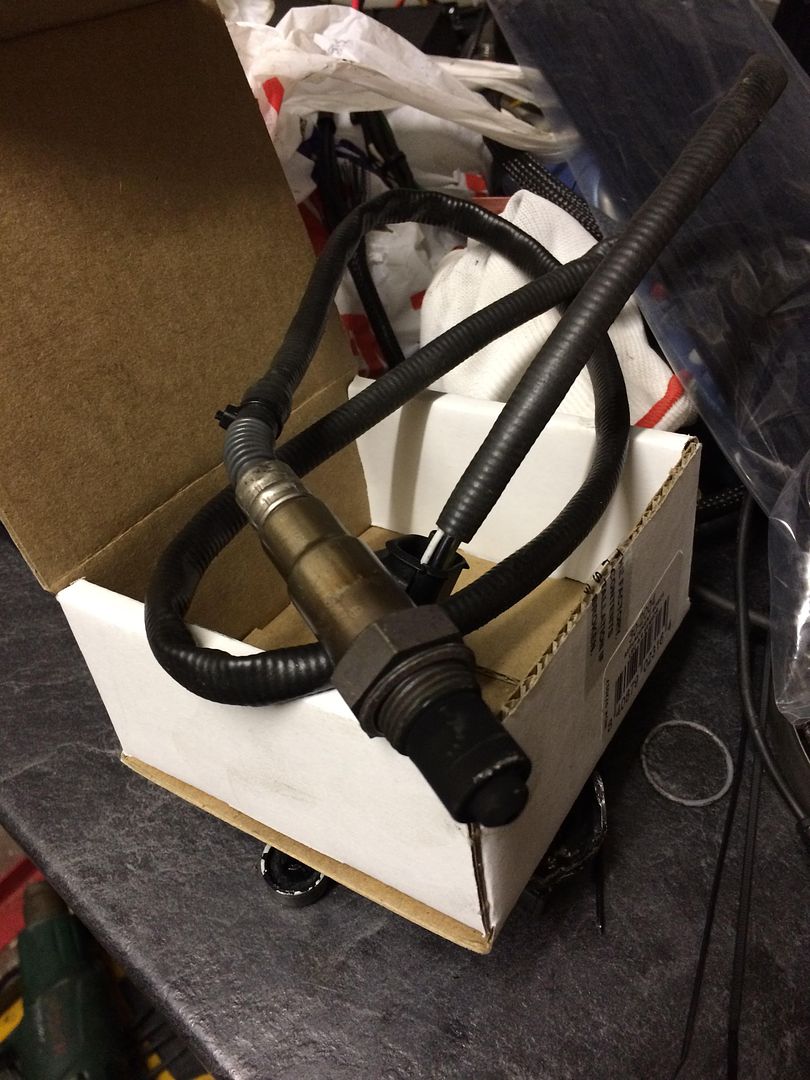
Loaded up the car and headed off to Hull to catch the overnight ferry - the forecast was changing by the hour and there had already been a covering of snow at Spa the previous day. Temperatures were around 2-3C, so we just had to hope for the best. I wasn't too concerned as I had the Pilot Sport 3's as an alternative tyre if the conditions were not up to the RS-Rs. We arrived in Stavelot late morning, 2C and raining. The forecast had improved for Friday, so we were hopeful.
The next day at the track, it was damp but the rain had stopped. I stuck on the Michelins all morning until a dry line started to appear just before lunch - in a way this was good as it gave an opportunity to learn the circuit at a slower pace. The car was issue free throughout the morning and the new alignment settings felt great, even in the damp.
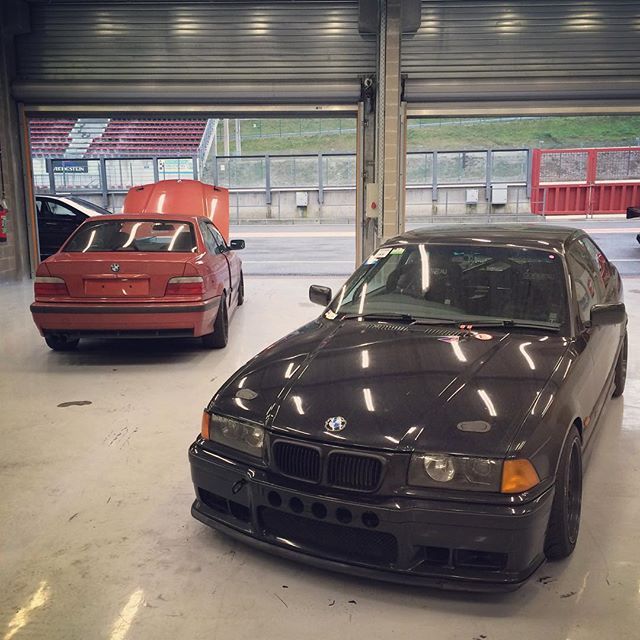
Swapped wheels to the Federals during lunch and spent most of the afternoon on track - covering just over 275 miles throughout the day.

https://www.youtube.com/watch?v=XYWqsVPLCd8
The car was spot on and drove fantastically in the dry, the rebuilt LSD gives far better traction from corners, and the new ratio seems to be a great match for the power band of the engine. Not to mention Spa itself, what a fantastic circuit. By far the best one I've driven so far, flows so much more than I ever expected.
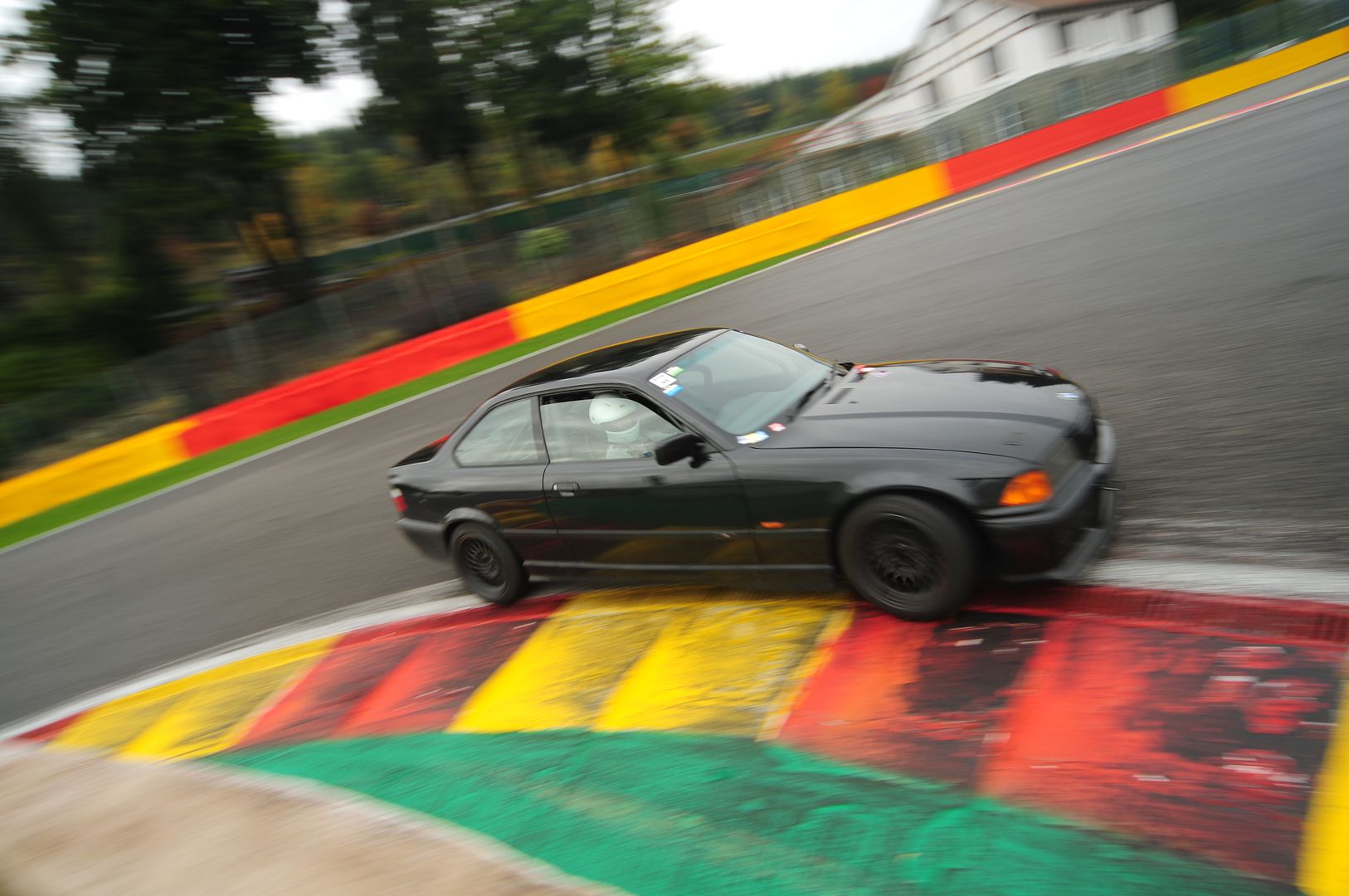
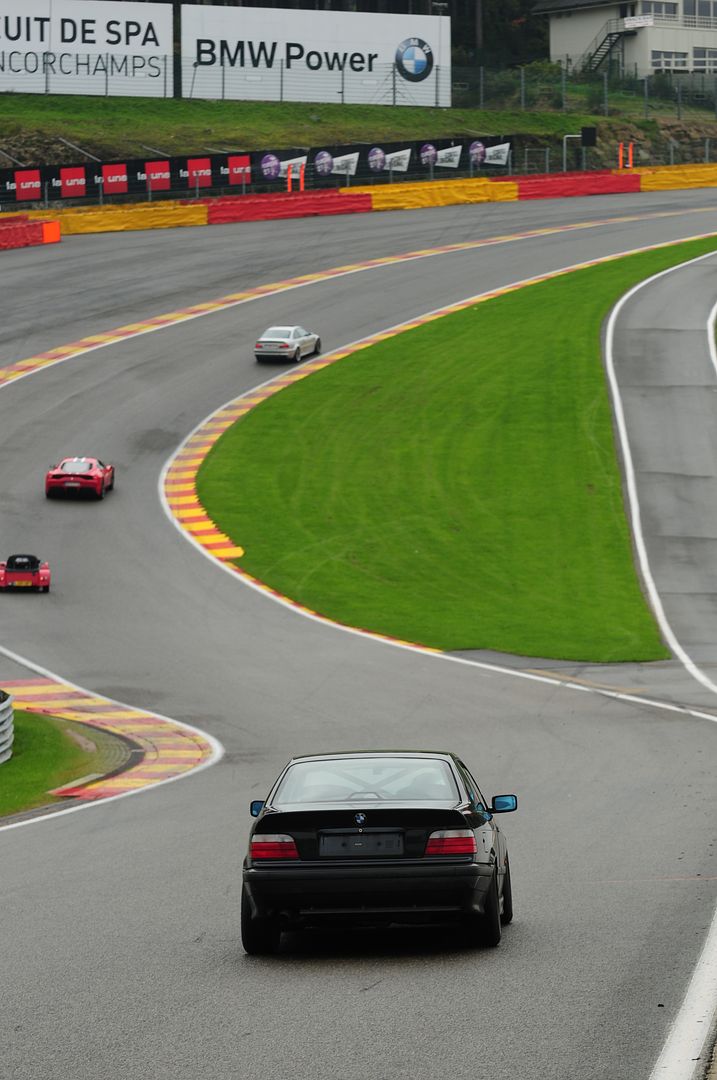
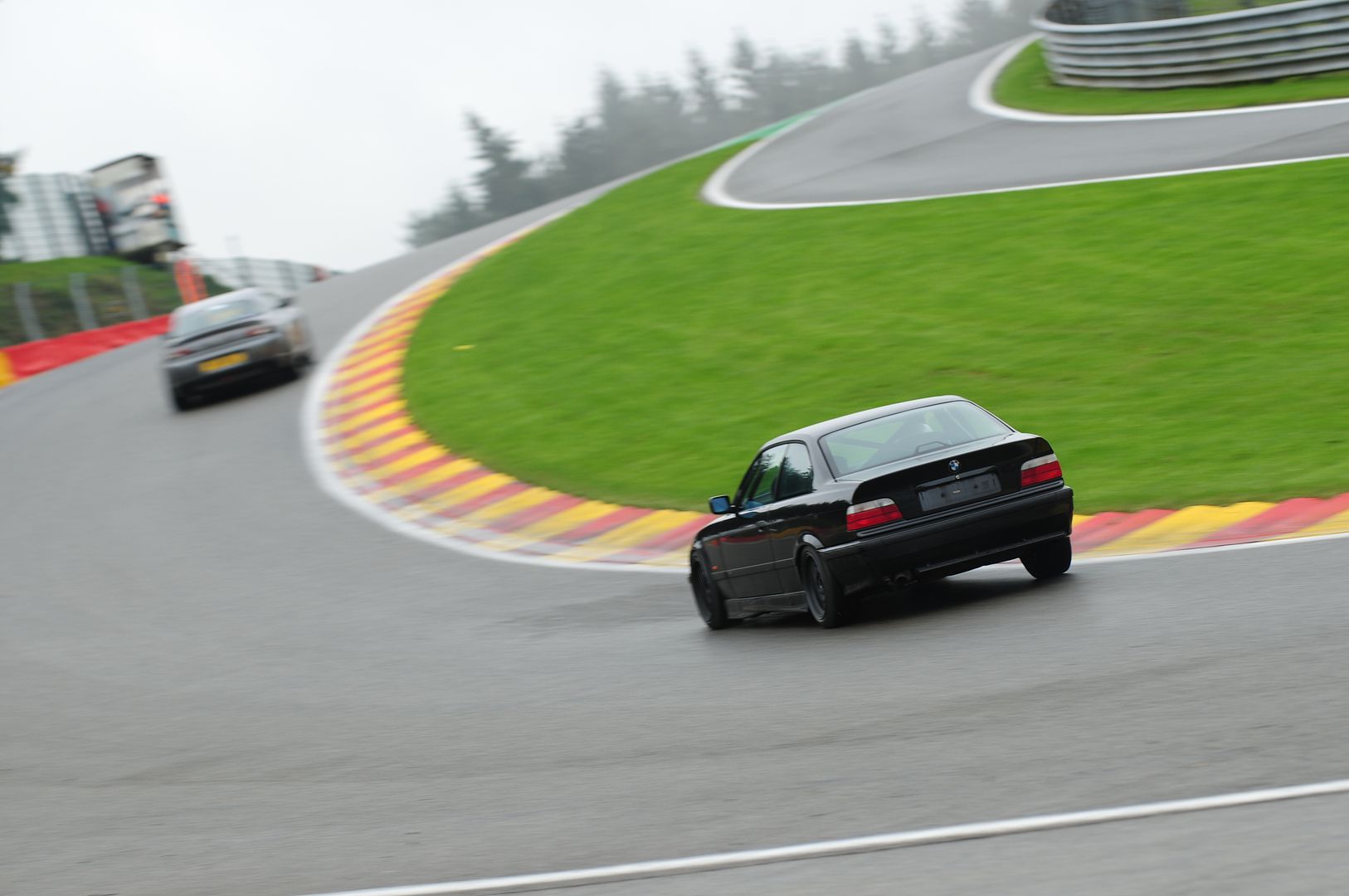
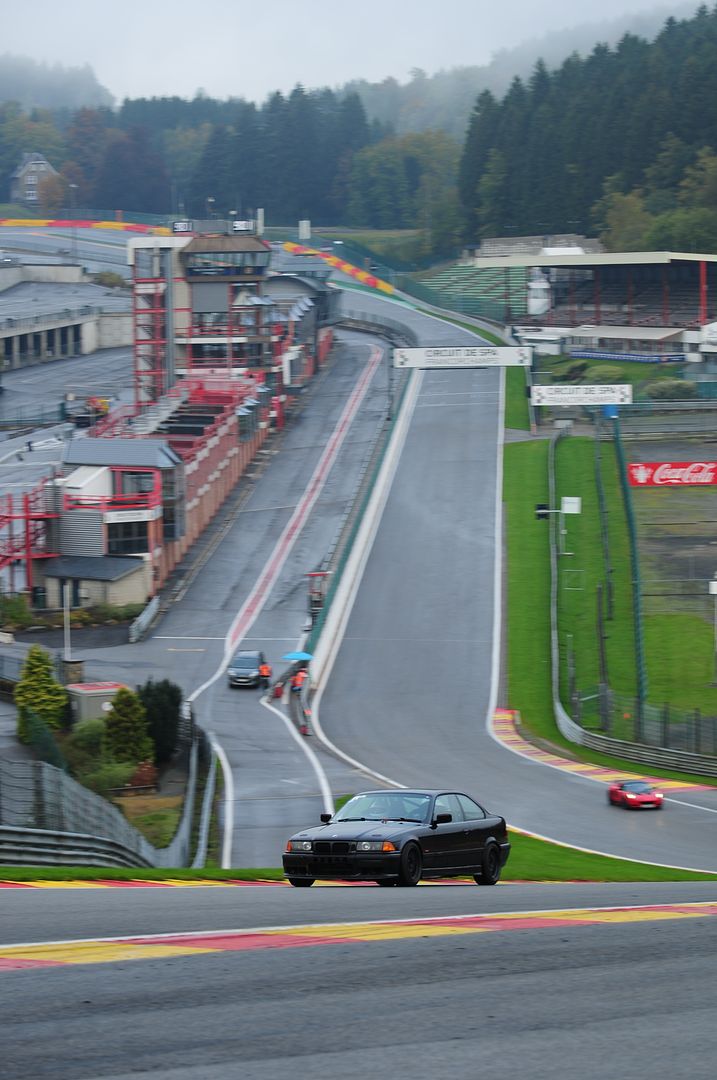
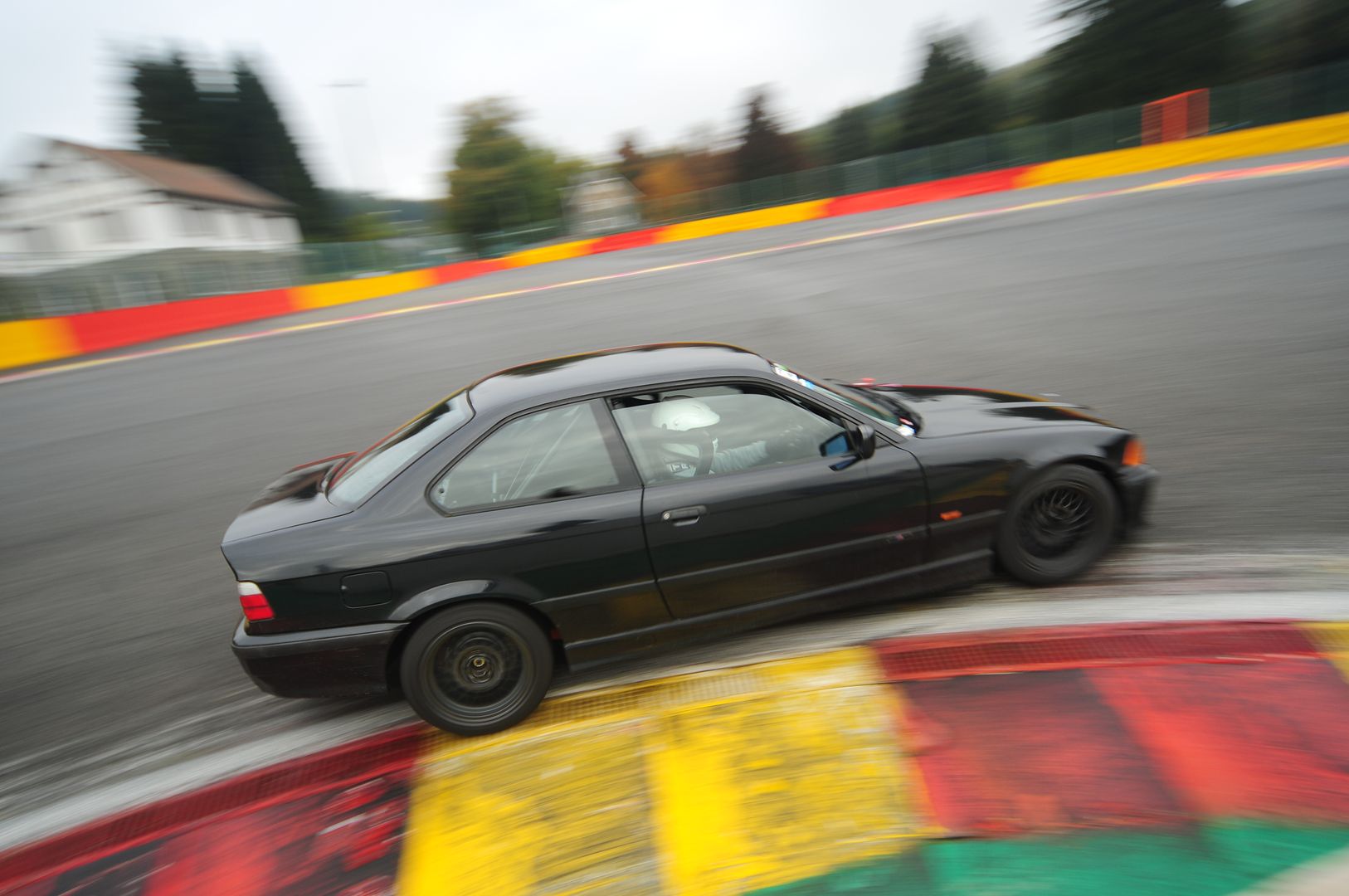
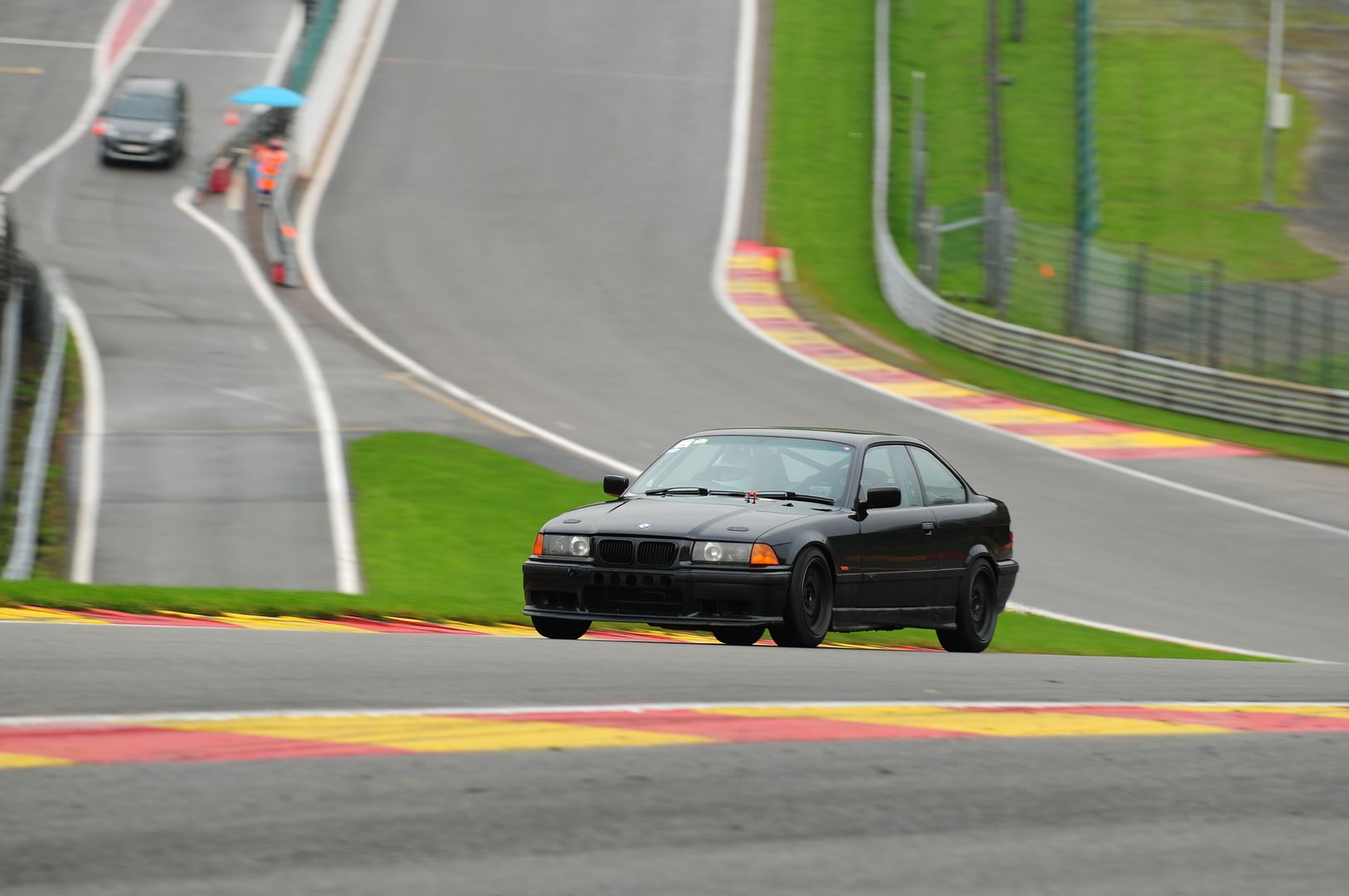
As the day went on the lap times dropped as I got used to the shorter gearing and available grip with the new alignment settings. 4th and 5th are now used most of the time compared to 3rd and 4th with the old ratio.
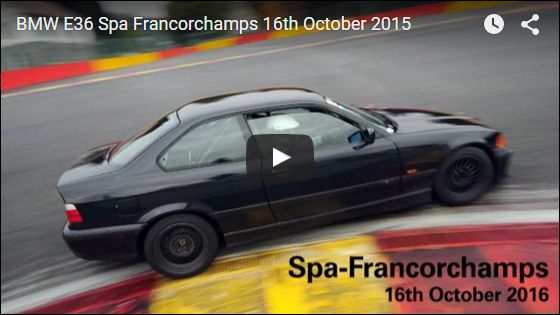
https://www.youtube.com/watch?v=HHuAj_4Z1ZA
Pleased to report the 'problem hub nut' is still locked in place and has not moved, which has made the rear end swap worthwhile! Just need to put some fuel in ready for Donington next week and take it from there!
Sorry, I didn't see your reply from earlier in the year. Its around 10.2:1, if not slightly less. The pistons were around 1.8-1.9mm below the deck, as most people experience (this was with the block being decked 4thou previously).
Quite a lot has changed since I last updated this thread - I'm just about finishing up another engine. Similar spec (M54) internals, M50 iron block, although more taken from the block to bump the CR slightly (with a bit of calculation on valve clearance), different camshafts and Jenvey ITBs. I will update the thread at some point
I may still have the Alu block, I can check tomorrow evening. Can't remember if I binned it.
Quite a lot has changed since I last updated this thread - I'm just about finishing up another engine. Similar spec (M54) internals, M50 iron block, although more taken from the block to bump the CR slightly (with a bit of calculation on valve clearance), different camshafts and Jenvey ITBs. I will update the thread at some point
I may still have the Alu block, I can check tomorrow evening. Can't remember if I binned it.
Great thread. What are your current tyre specs? The wheels are BBS 16' aren't they? Fancy selling a set?
I'm really impressed with the data logging which utilises a rasberry pie. Would you consider releasing the code you made to achieve this or a tutorial?
I'm really impressed with the data logging which utilises a rasberry pie. Would you consider releasing the code you made to achieve this or a tutorial?
Edited by Percent on Monday 22 August 14:24
Percent said:
Great thread. What are your current tyre specs? The wheels are BBS 16' aren't they? Fancy selling a set?
I'm really impressed with the data logging which utilises a rasberry pie. Would you consider releasing the code you made to achieve this or a tutorial?
I do somewhere, but I've not used it for a long time as since moving to standalone logging is much easier. If you still need it drop me a message. They are 16x8J BBS from E34/E38, I use a mix of 225/205s on them.I'm really impressed with the data logging which utilises a rasberry pie. Would you consider releasing the code you made to achieve this or a tutorial?
Edited by Percent on Monday 22 August 14:24
Its been a while since I updated this, nearly a year of outings and the car was great. Around September time it became apparent the black coupe shell was rotting from the inside out, along the sills. The outer sills had already been replaced once, but it was just not cost effective to repair again - that particular shell was past 200k miles. I ended up re-shelling it into a silver saloon, swapping everything.
Before that various other changes were made - got some Porsche 996 calipers to fit under the 16x8s with a bit of work, utilising the standard E36 M3 front disc (315mm x 28mm). Most who fit these move to E46 M3 discs, but that would mean a move to 17s.
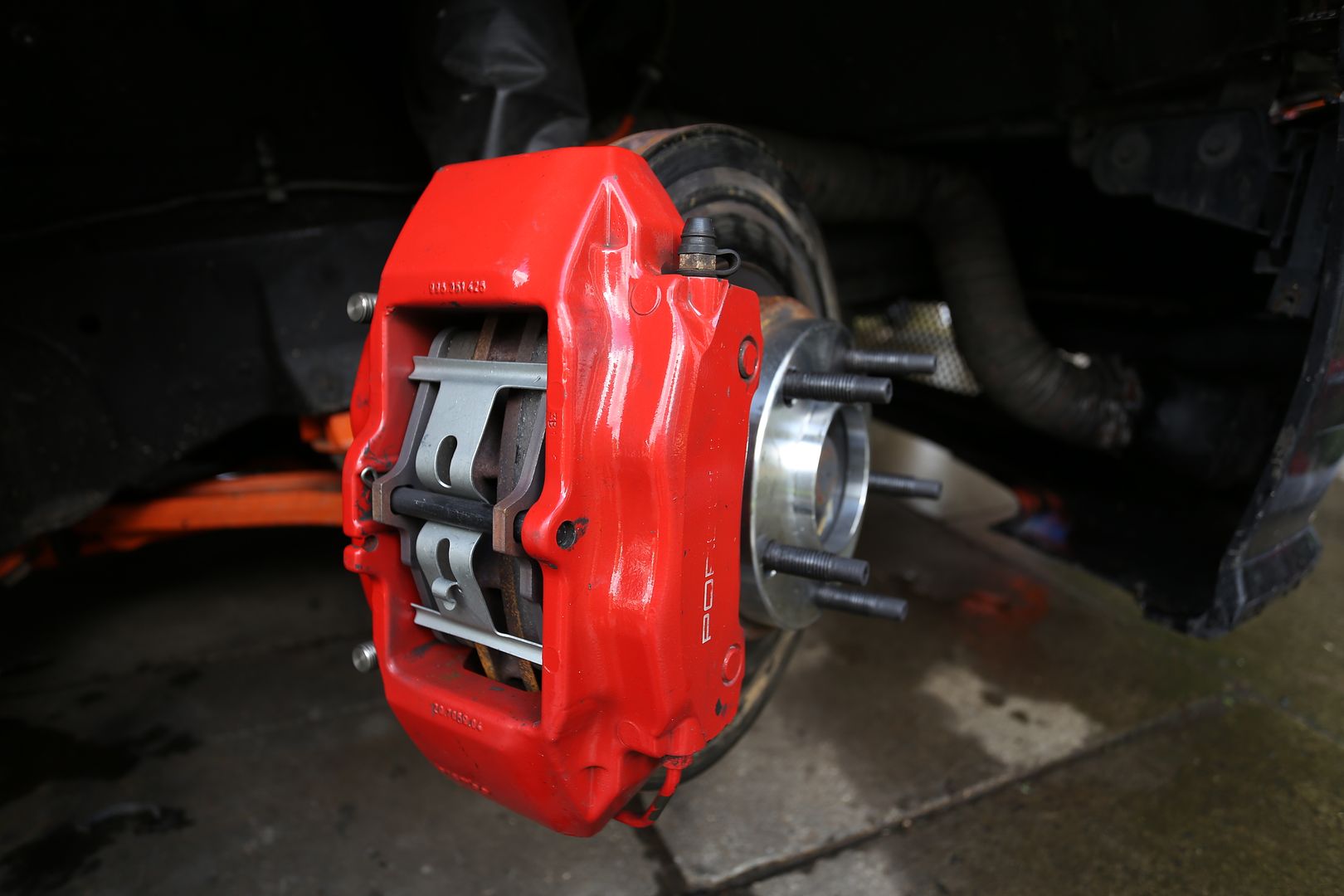
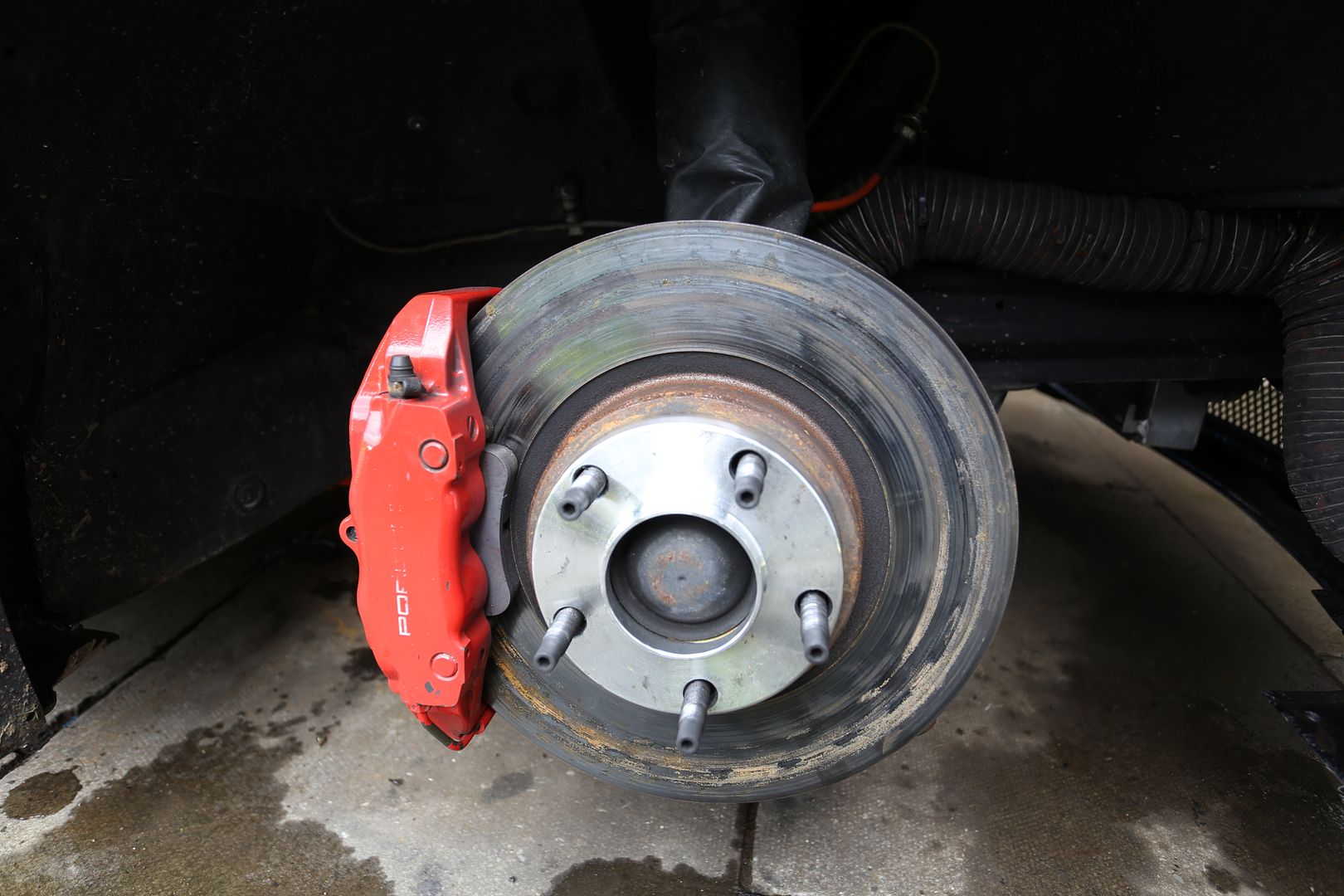
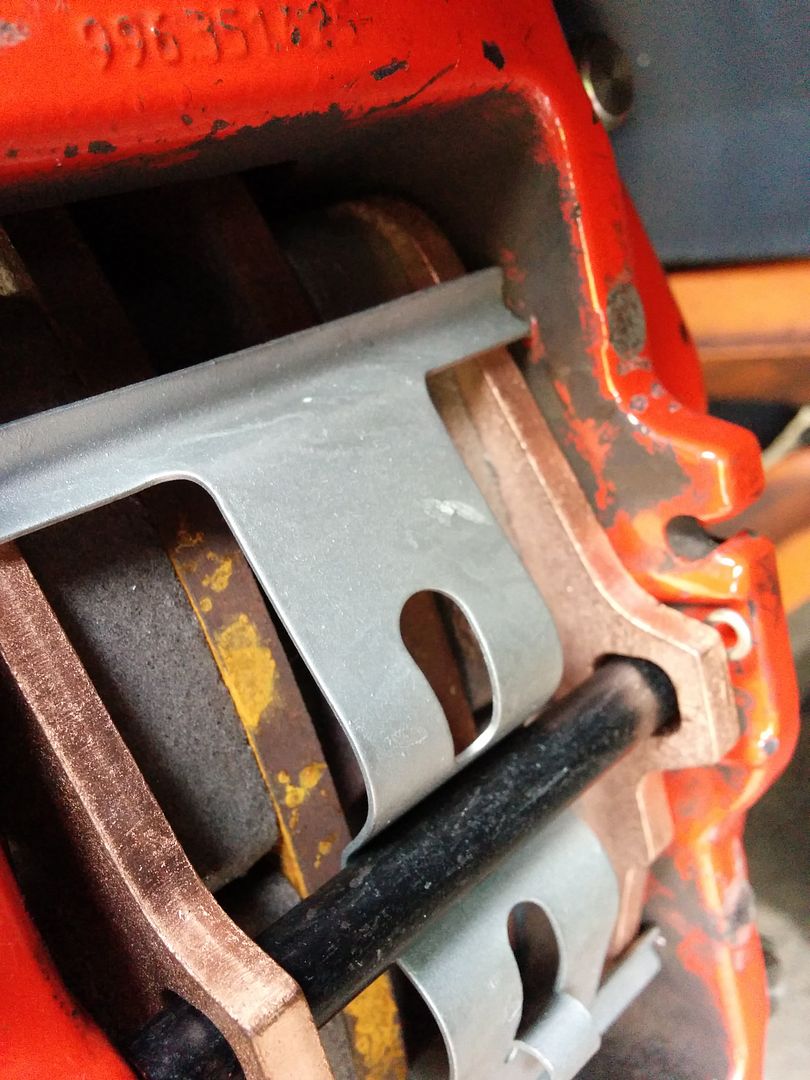
I also built a new engine, similar being an M50B30, slightly higher compression, cams, ITBs and various other bits. The other engine was still fine, and ended up going to a new home where it will still be used in anger.
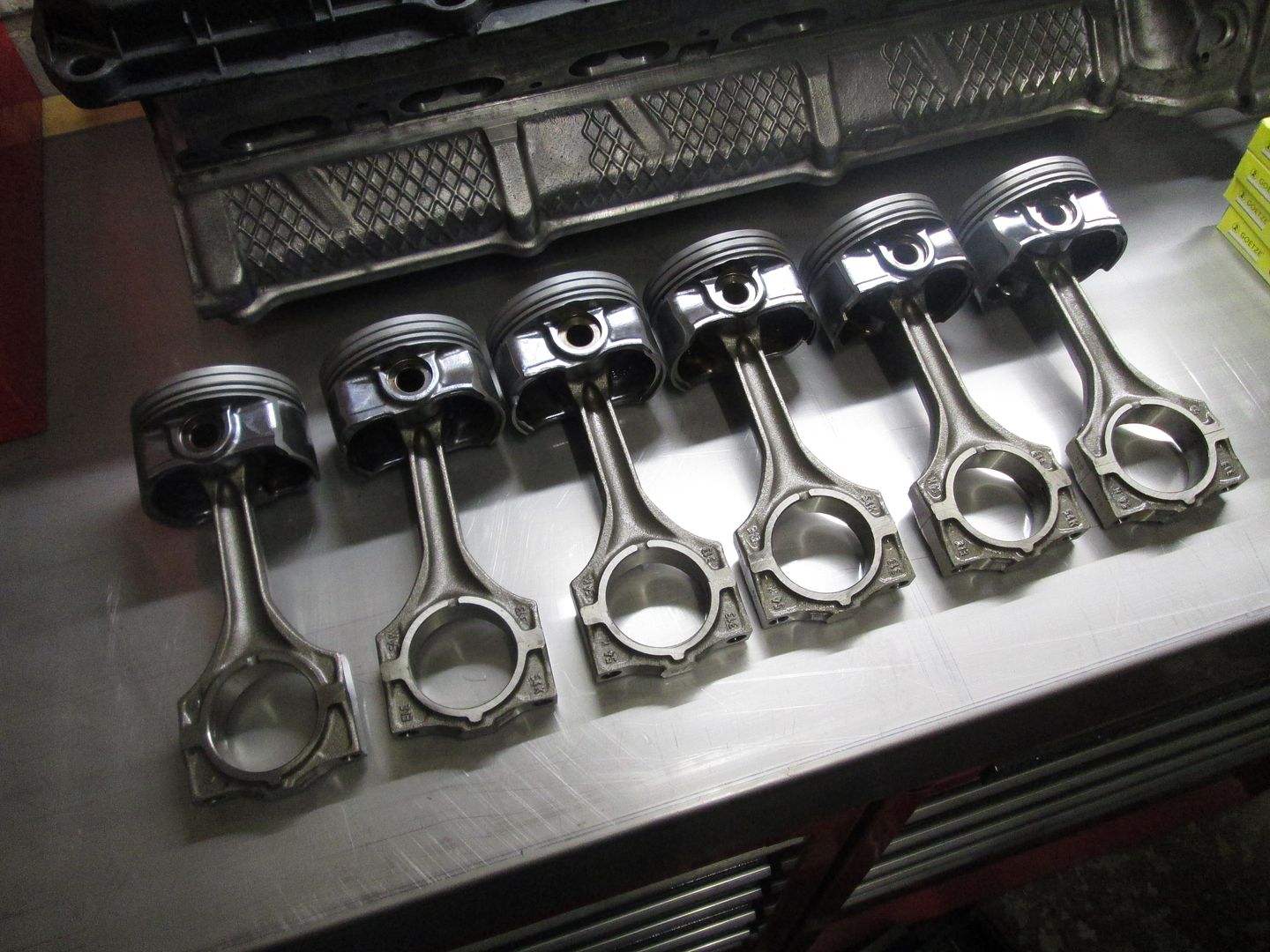
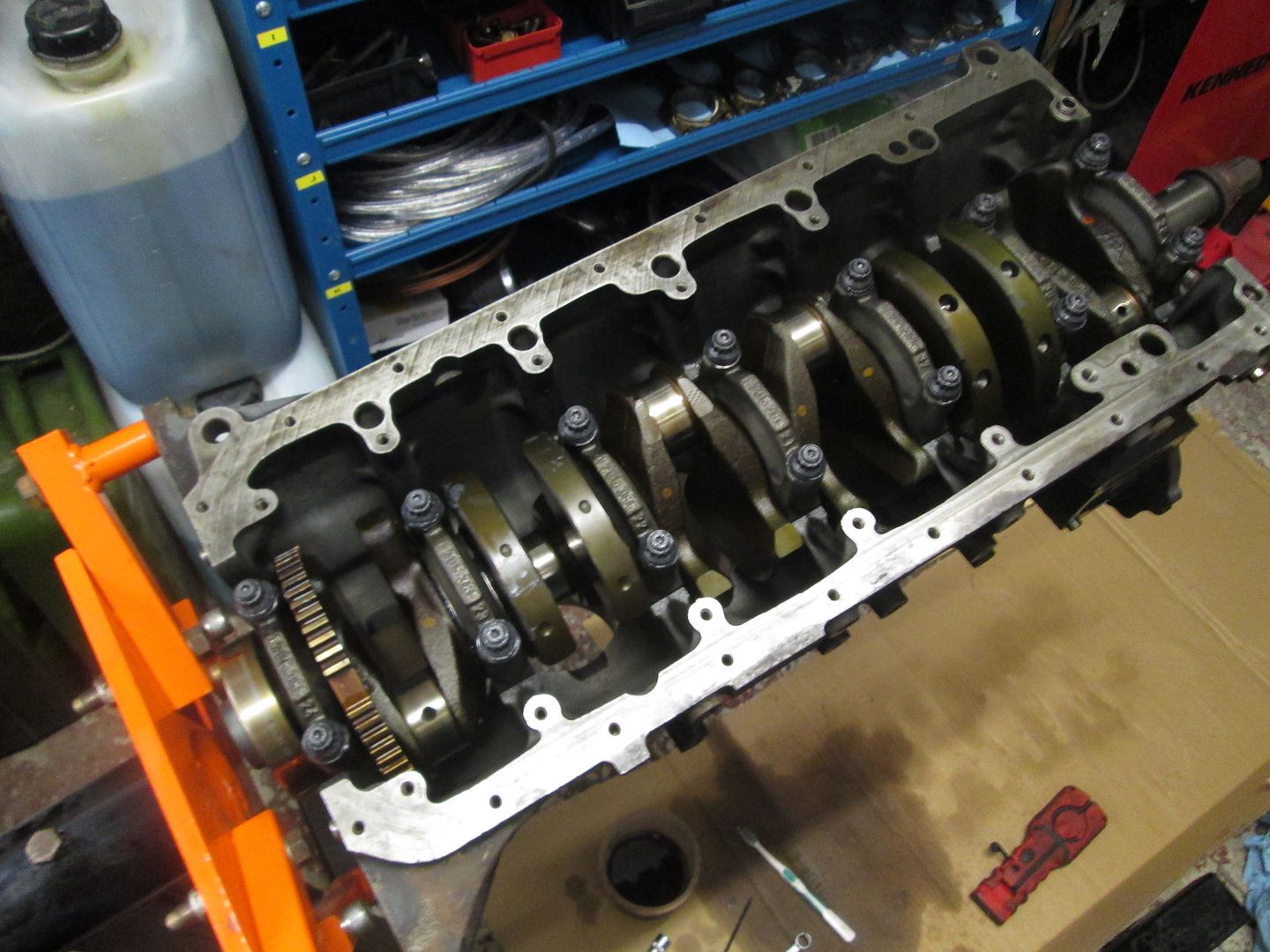
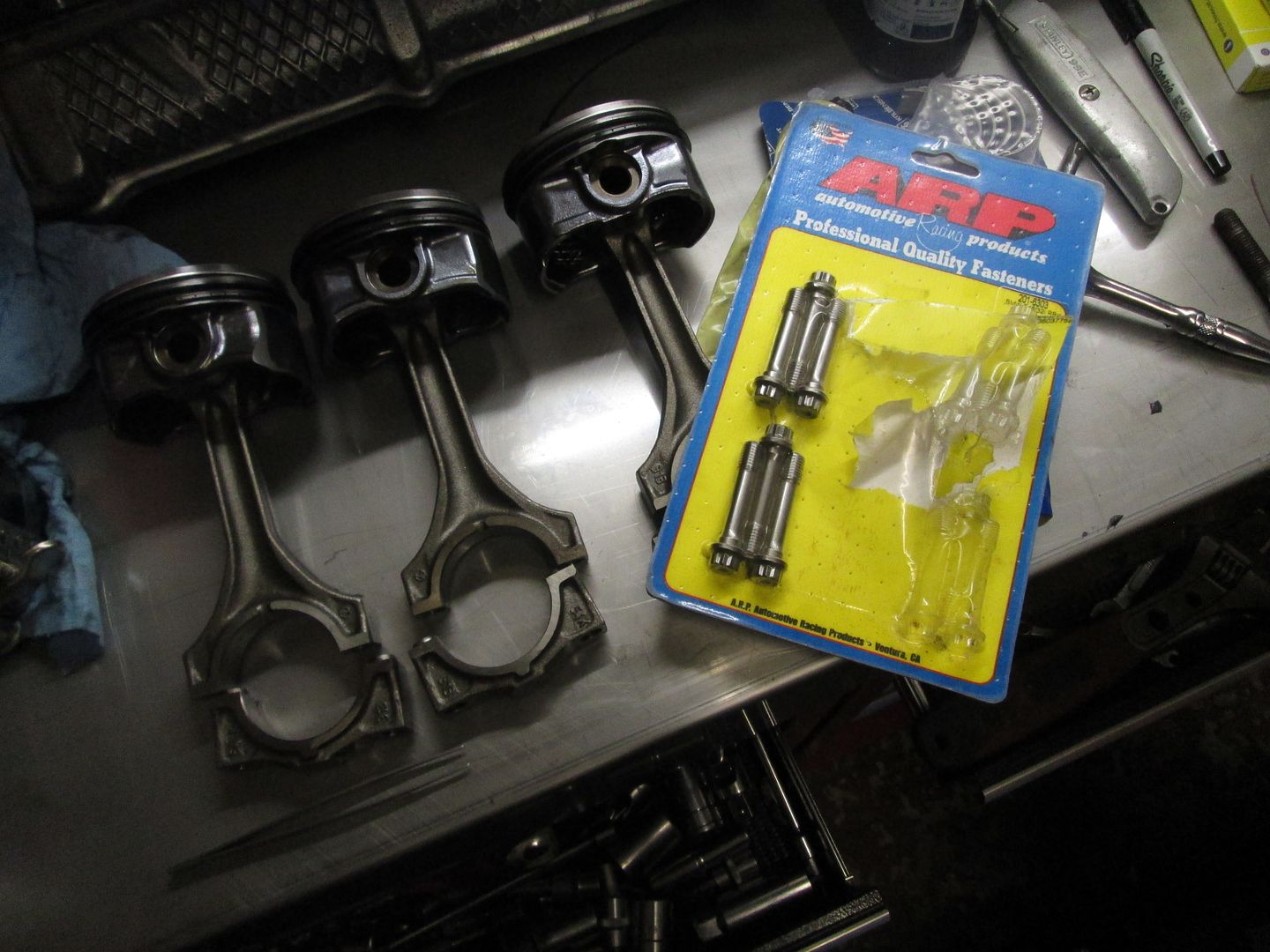
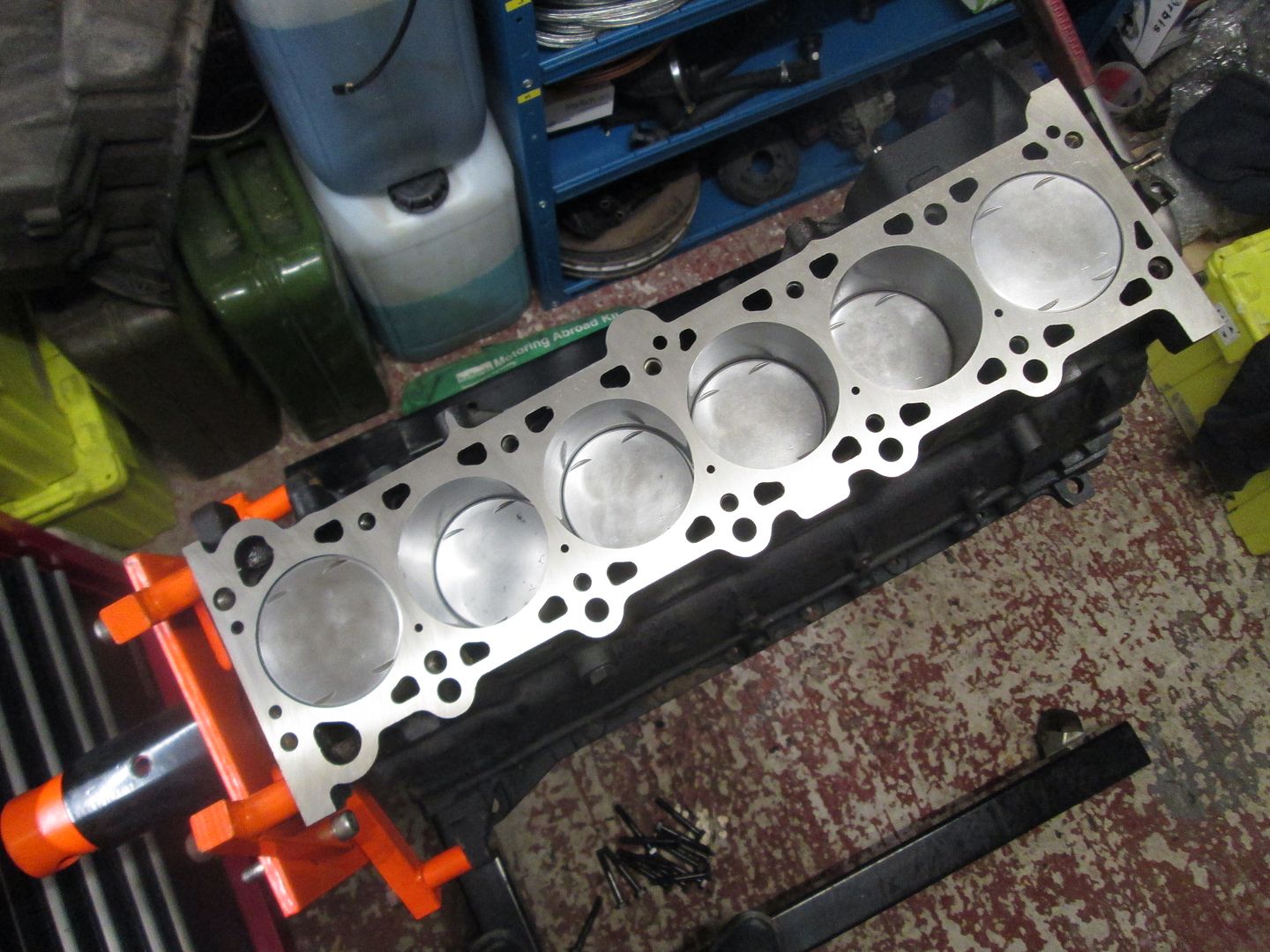
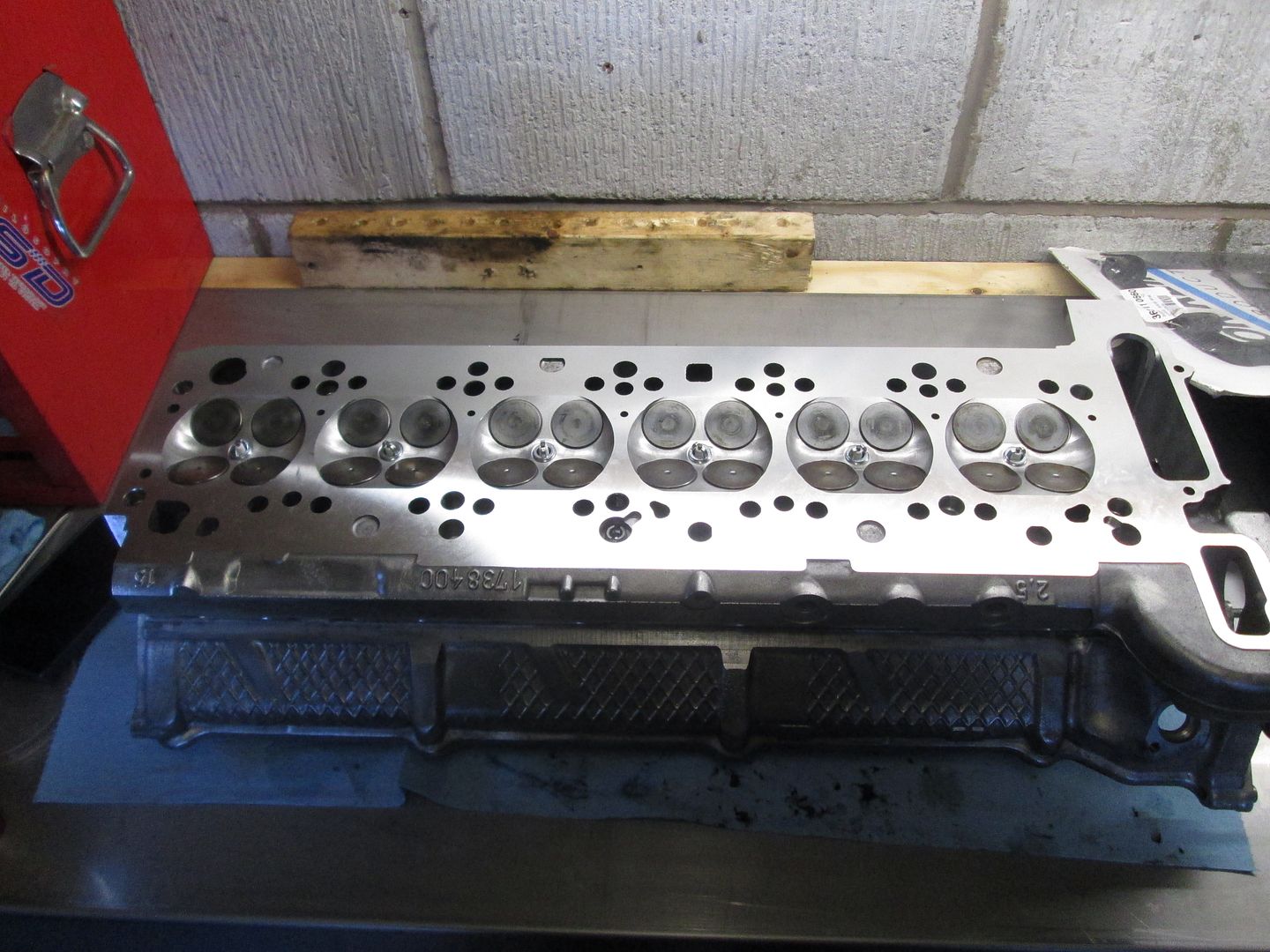
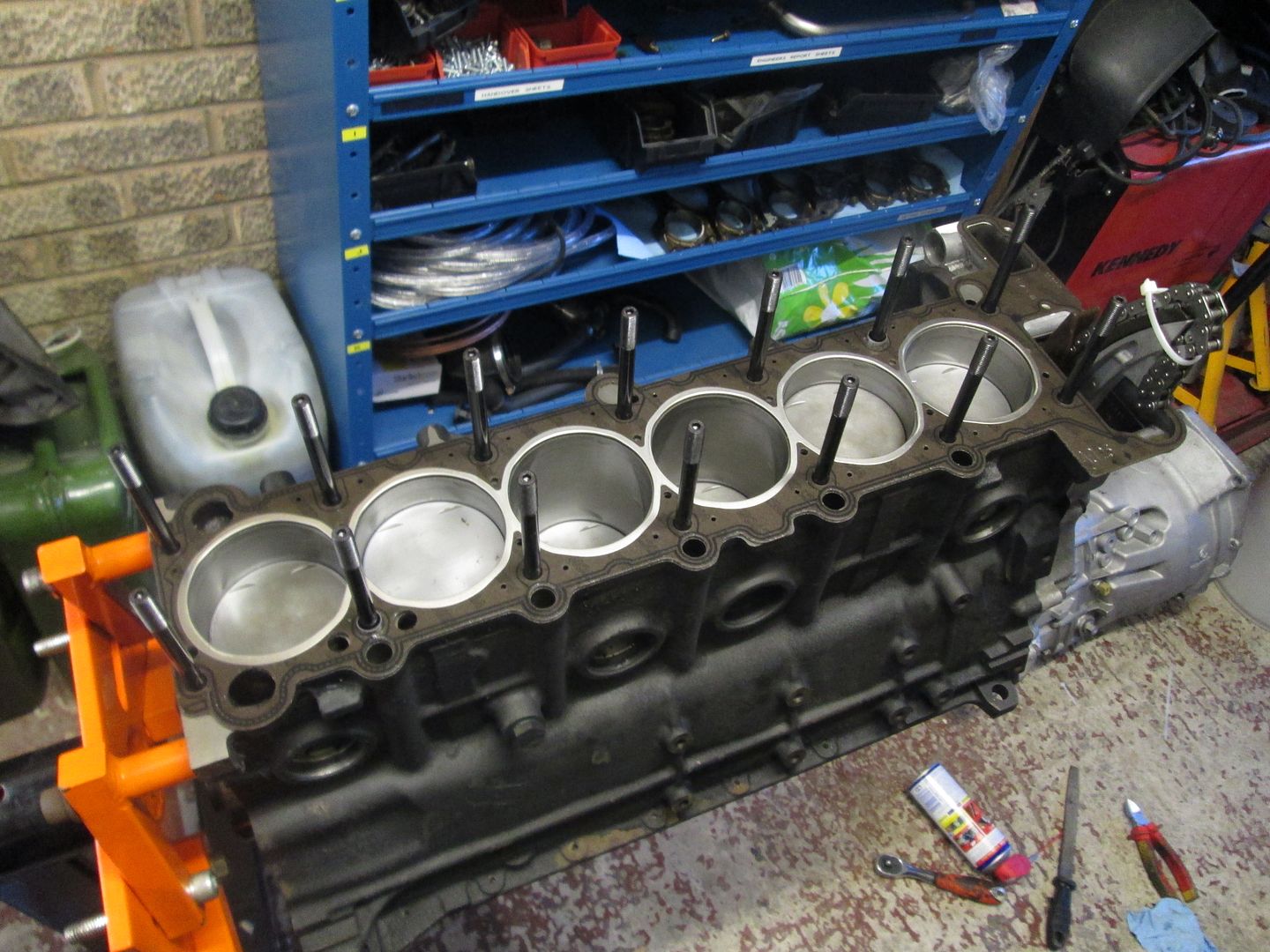
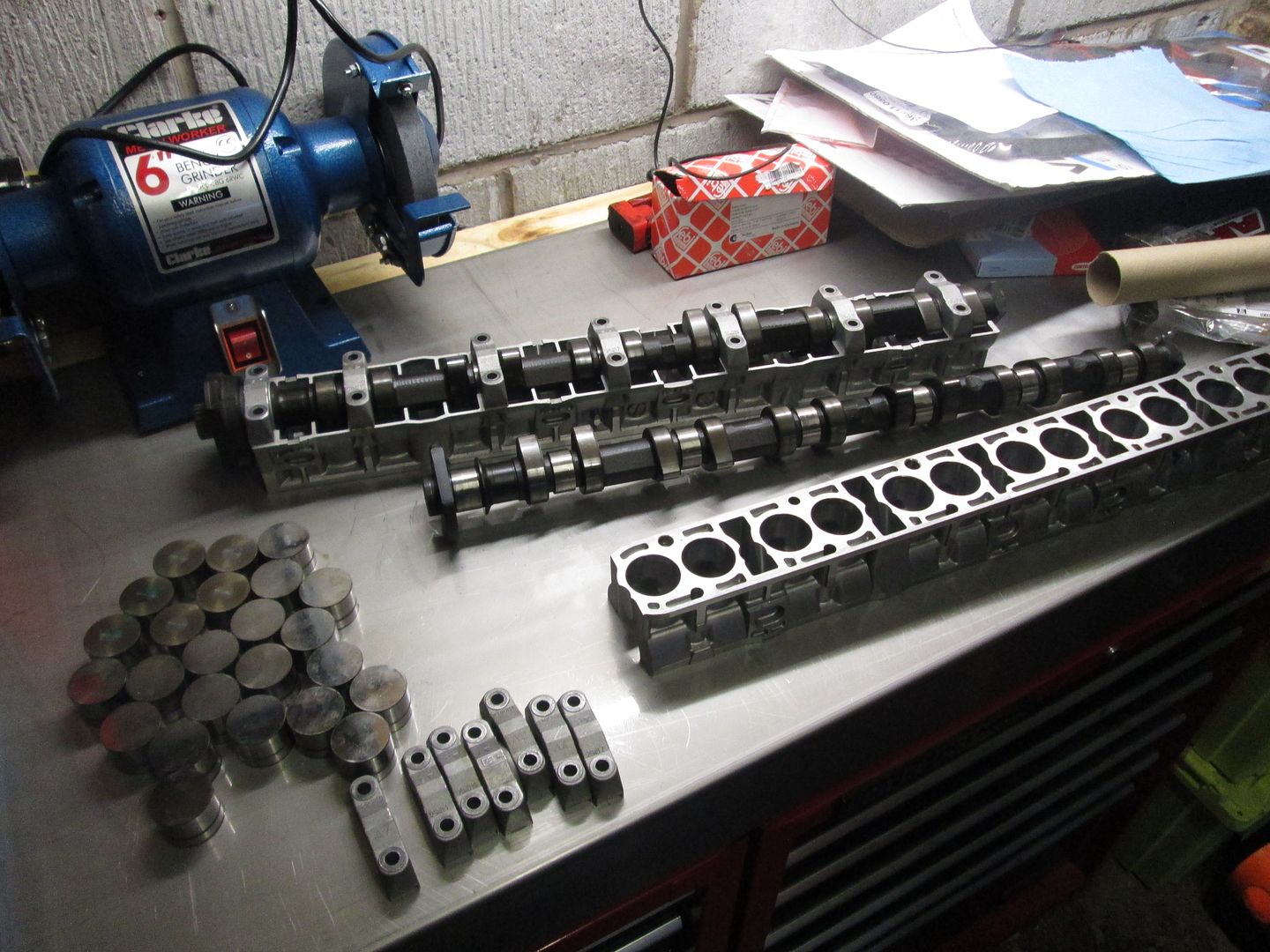
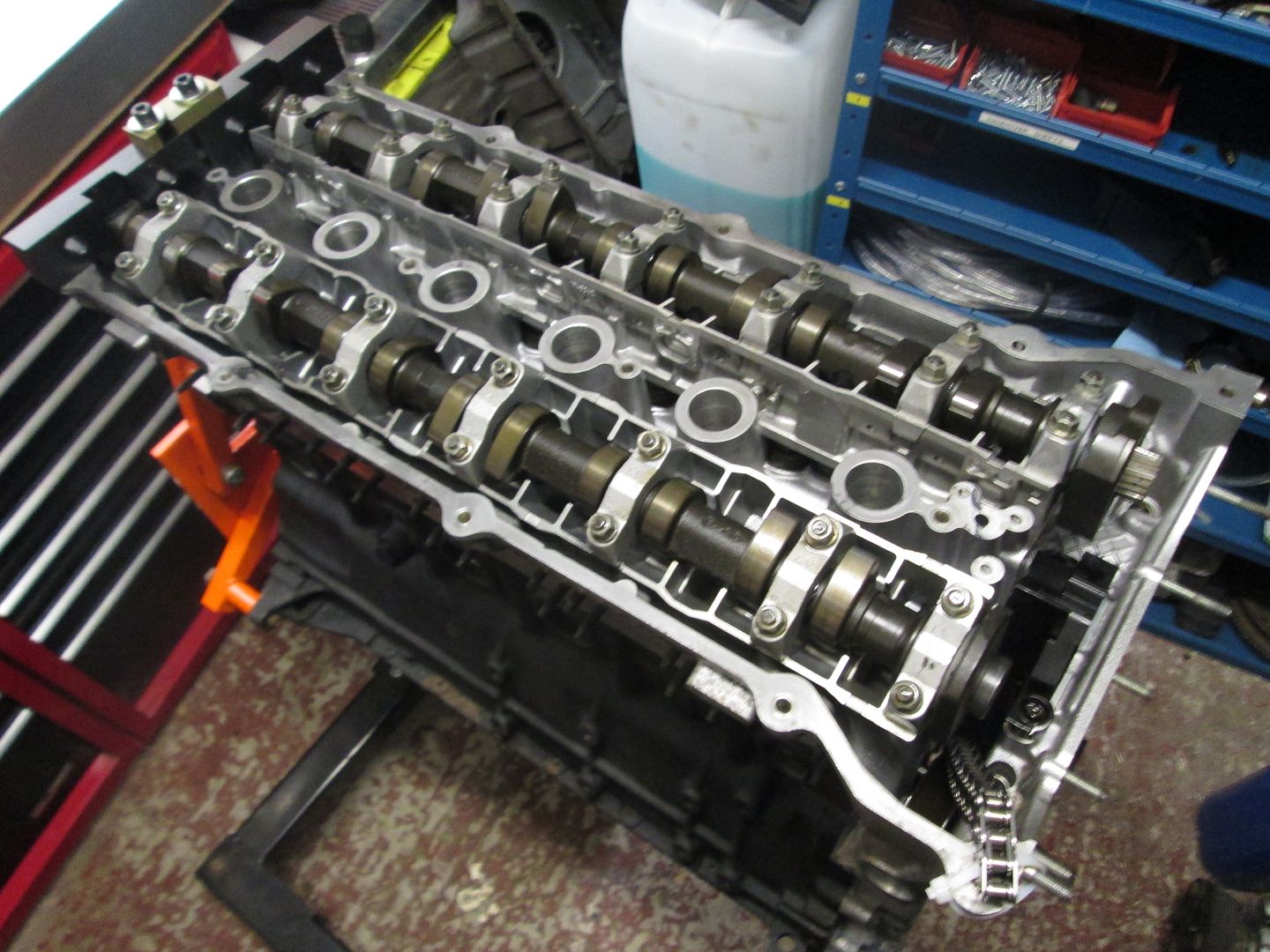
Engine then went into the car and everything else was bolted on. Various other jobs were done at the same time but I won't bore you with those..
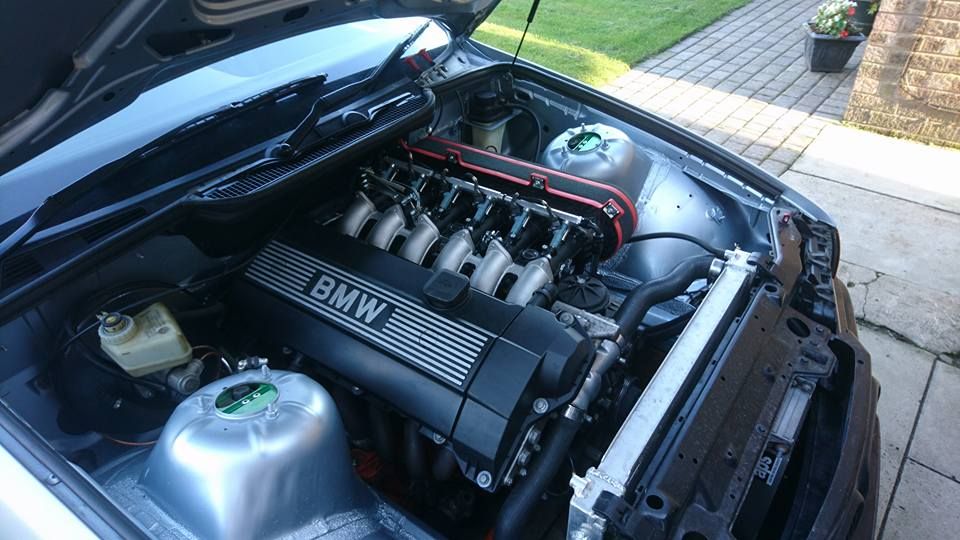
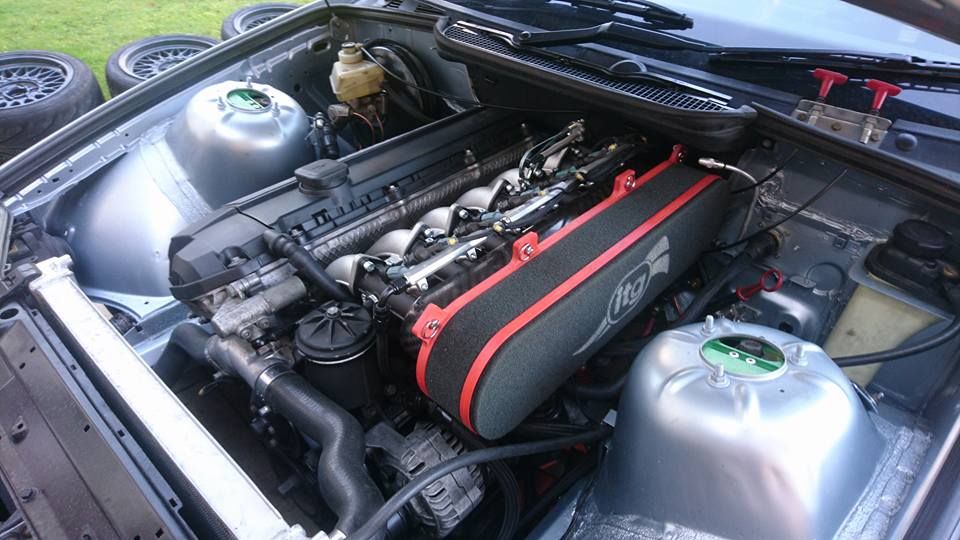

It then went for running in/mapping and finished up with 290hp @ 7200rpm / 265lbft @ 5000rpm. Power is still climbing at the limiter but I'm reluctant to spin the M54 bottom end past that just yet. A couple of days later I had the alignment done, then put it on the trailer and set off for a first outing.... Spa Francorchamps..
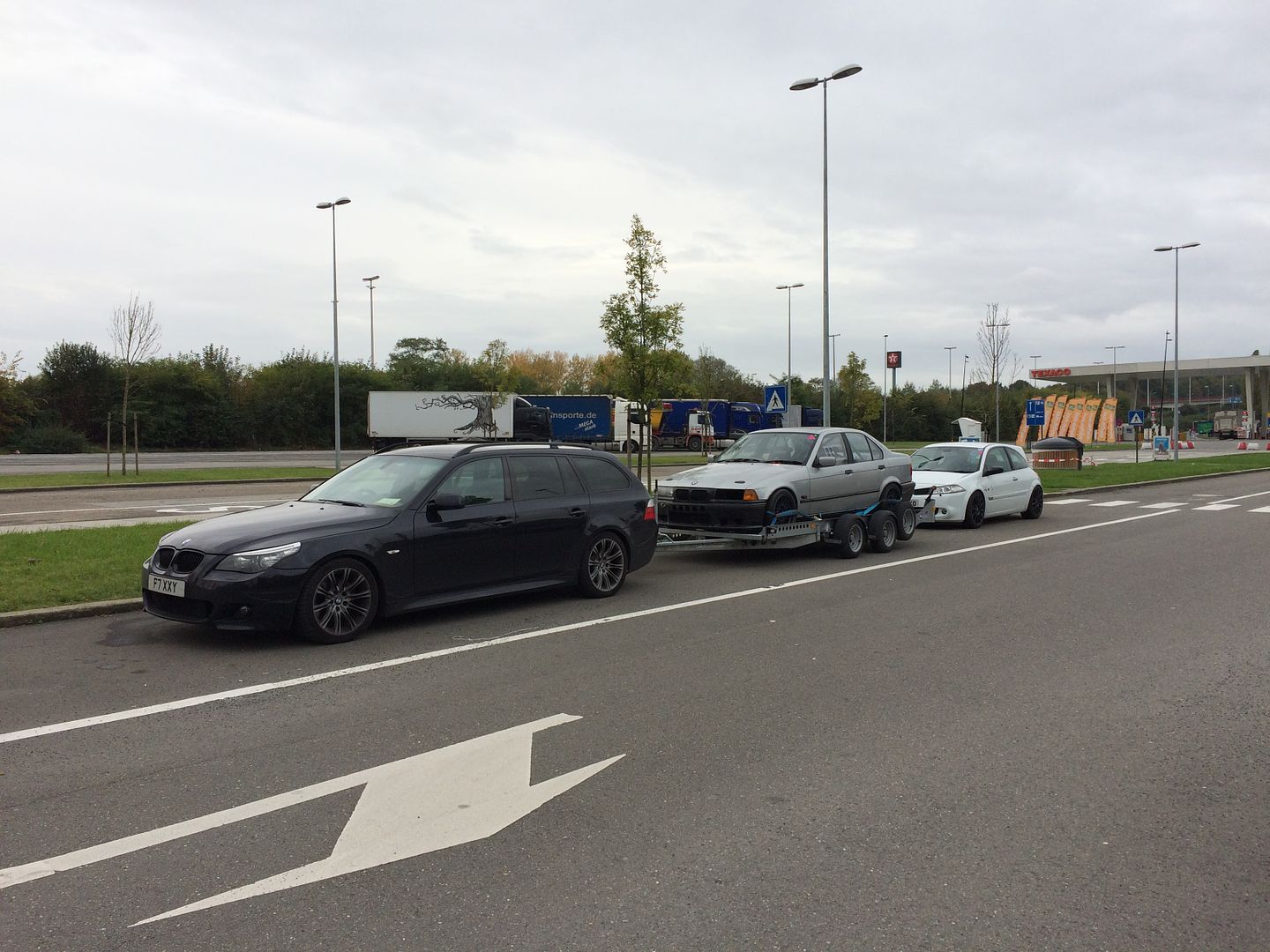
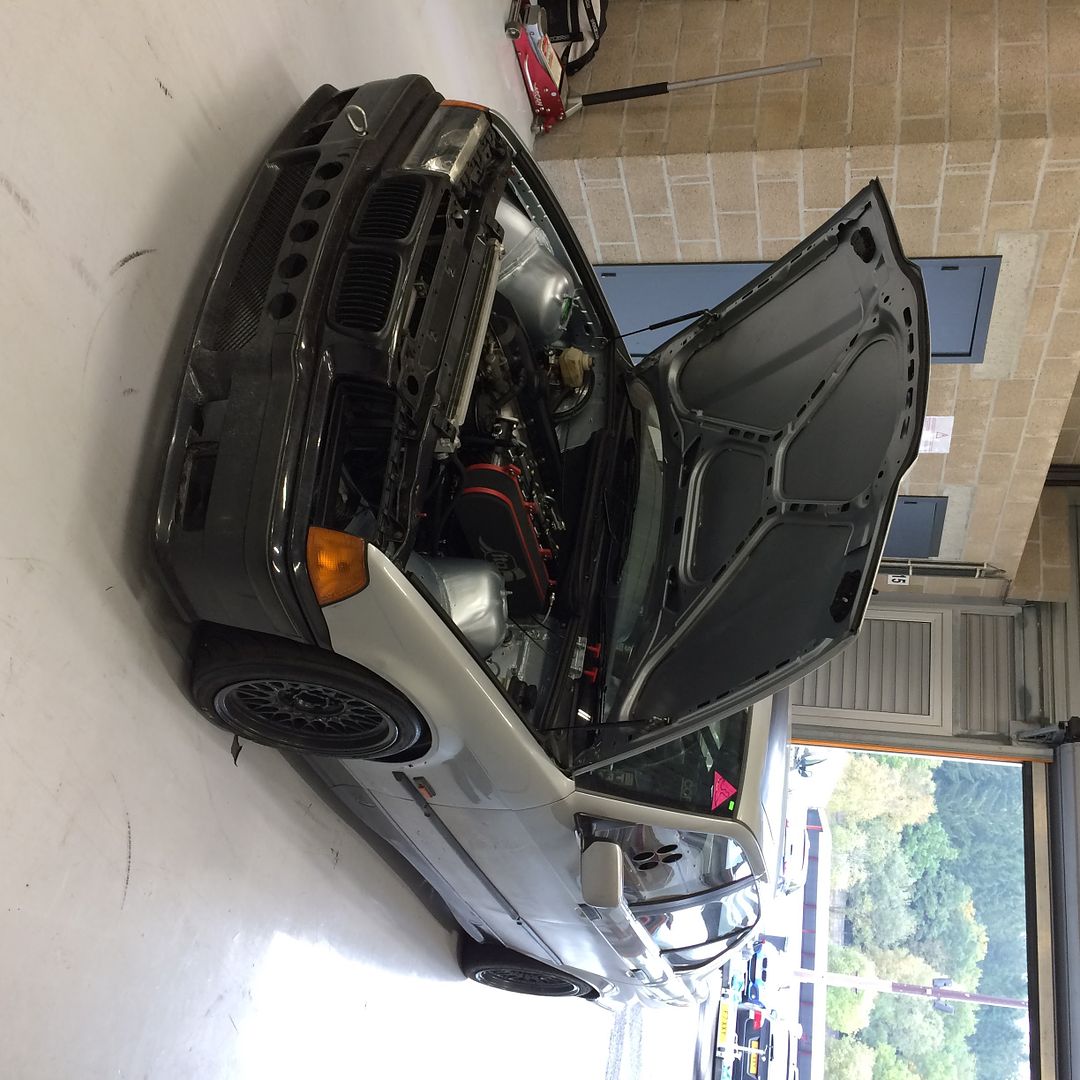
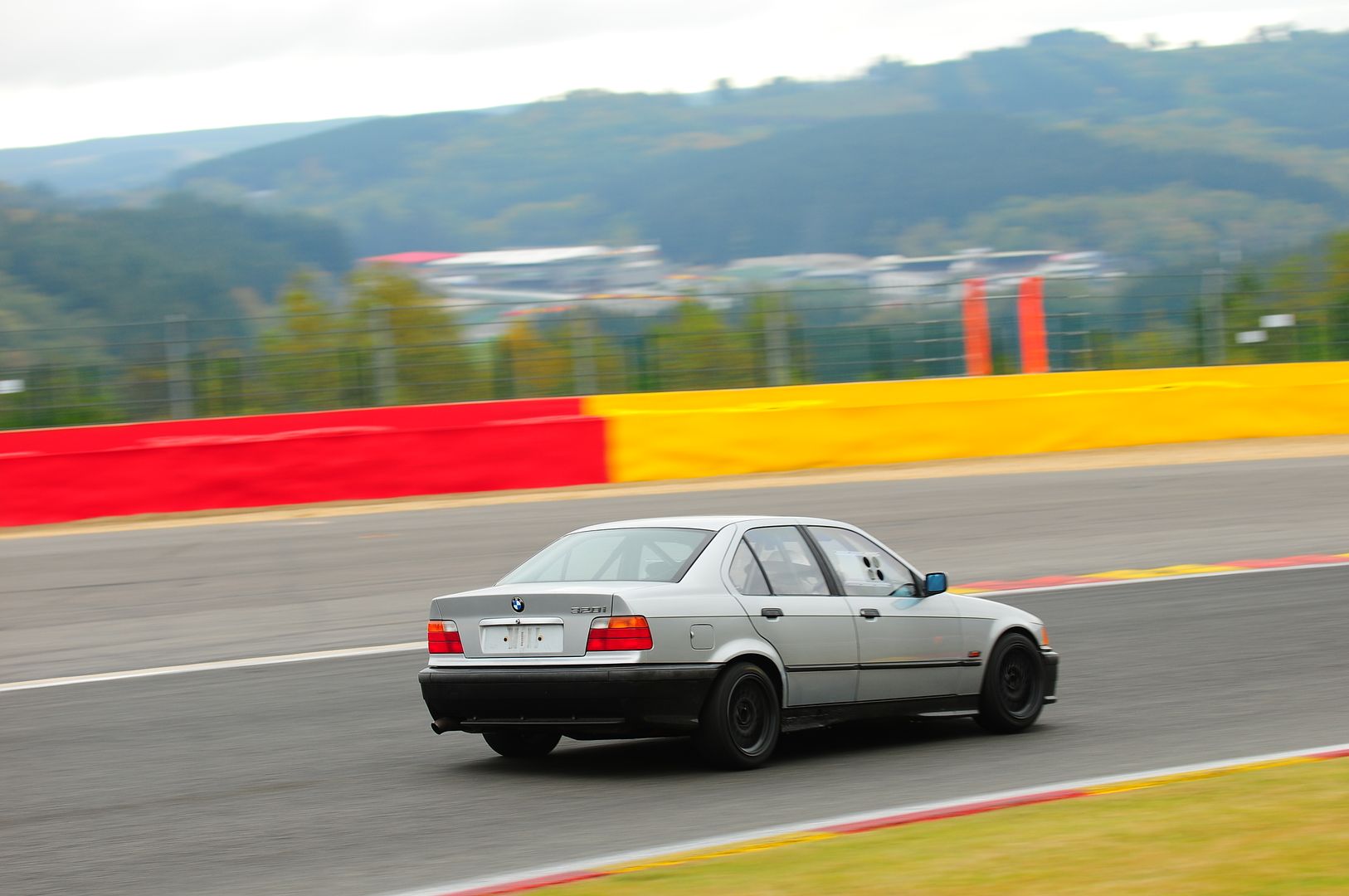
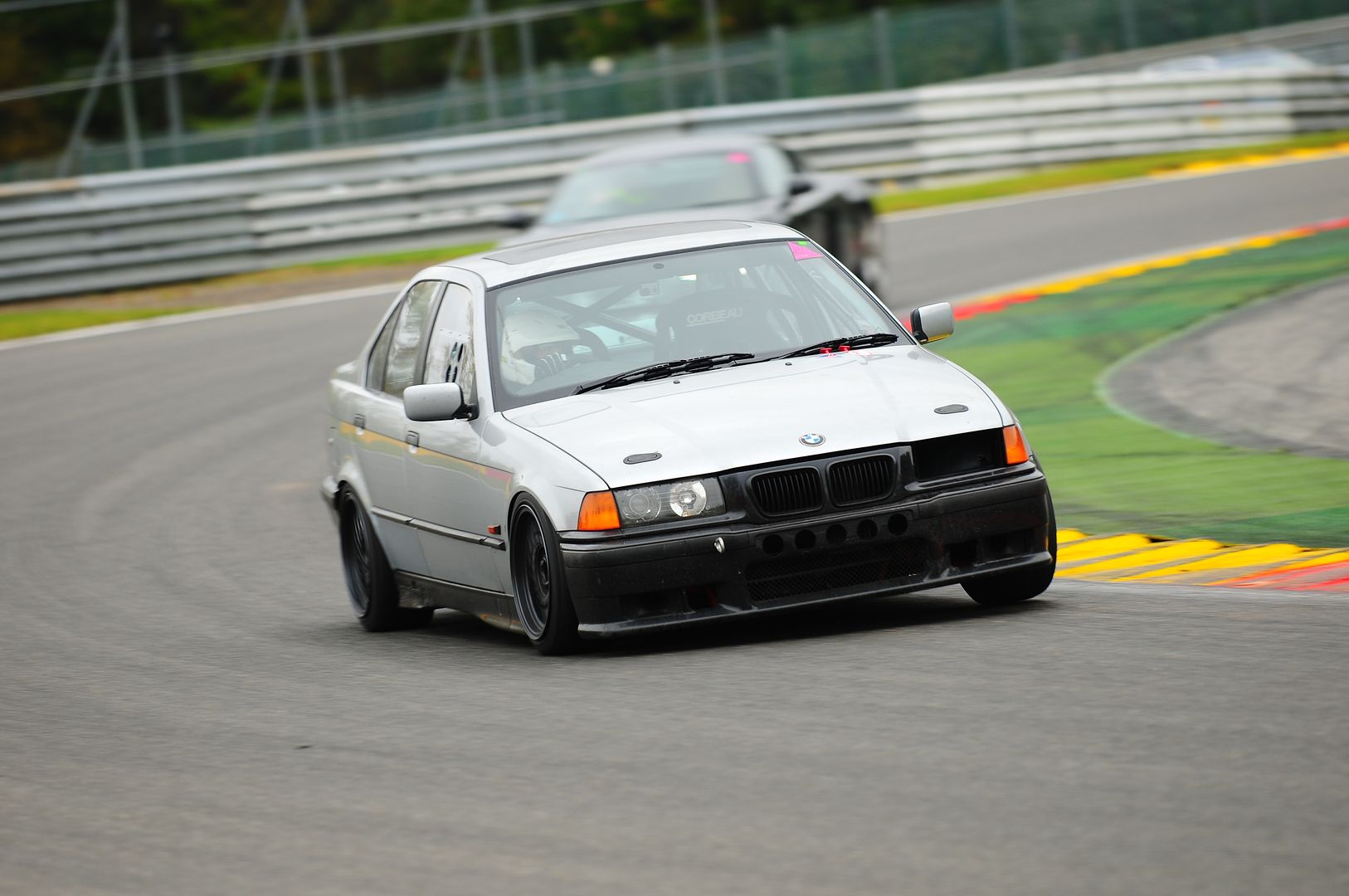
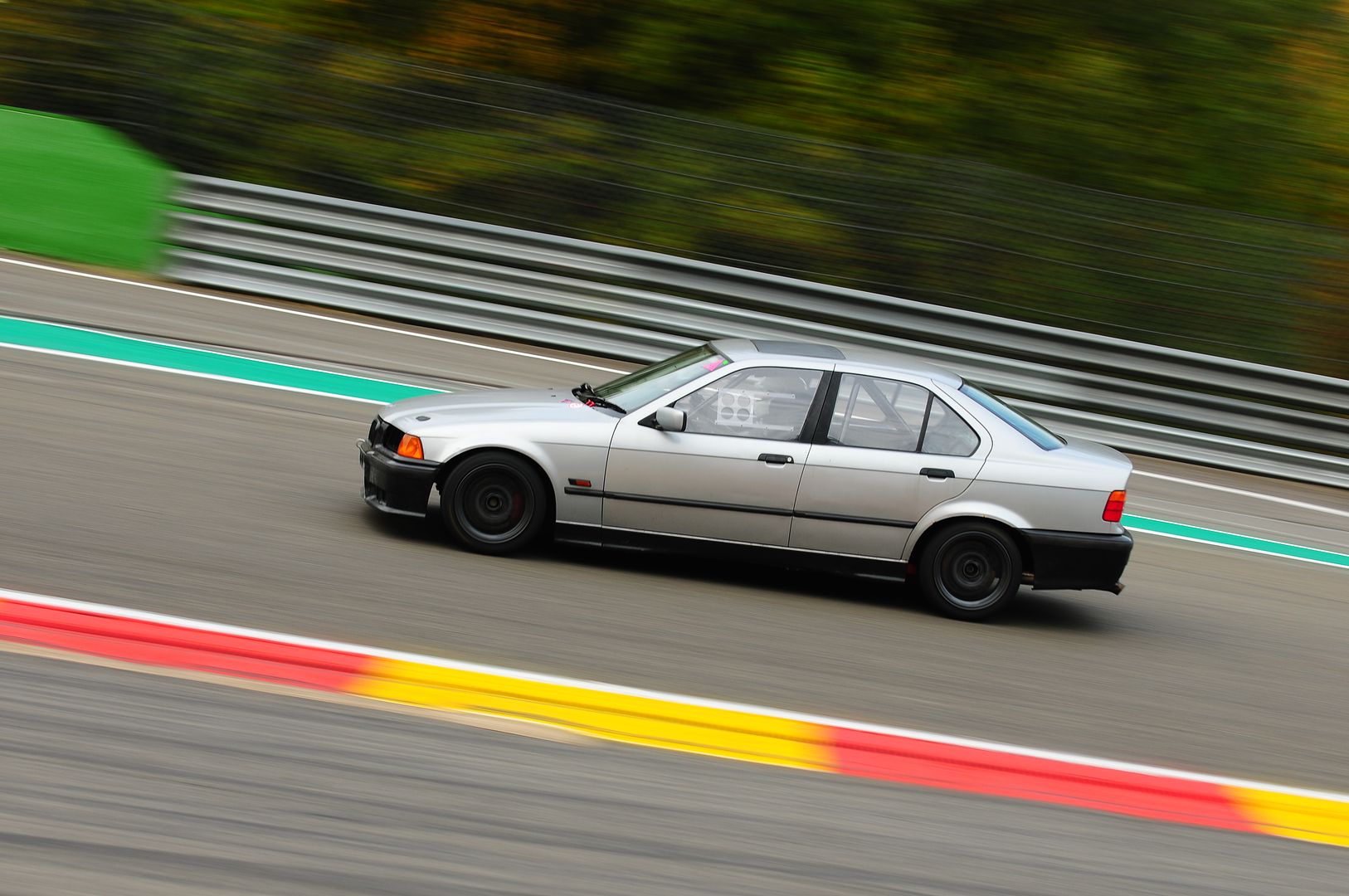
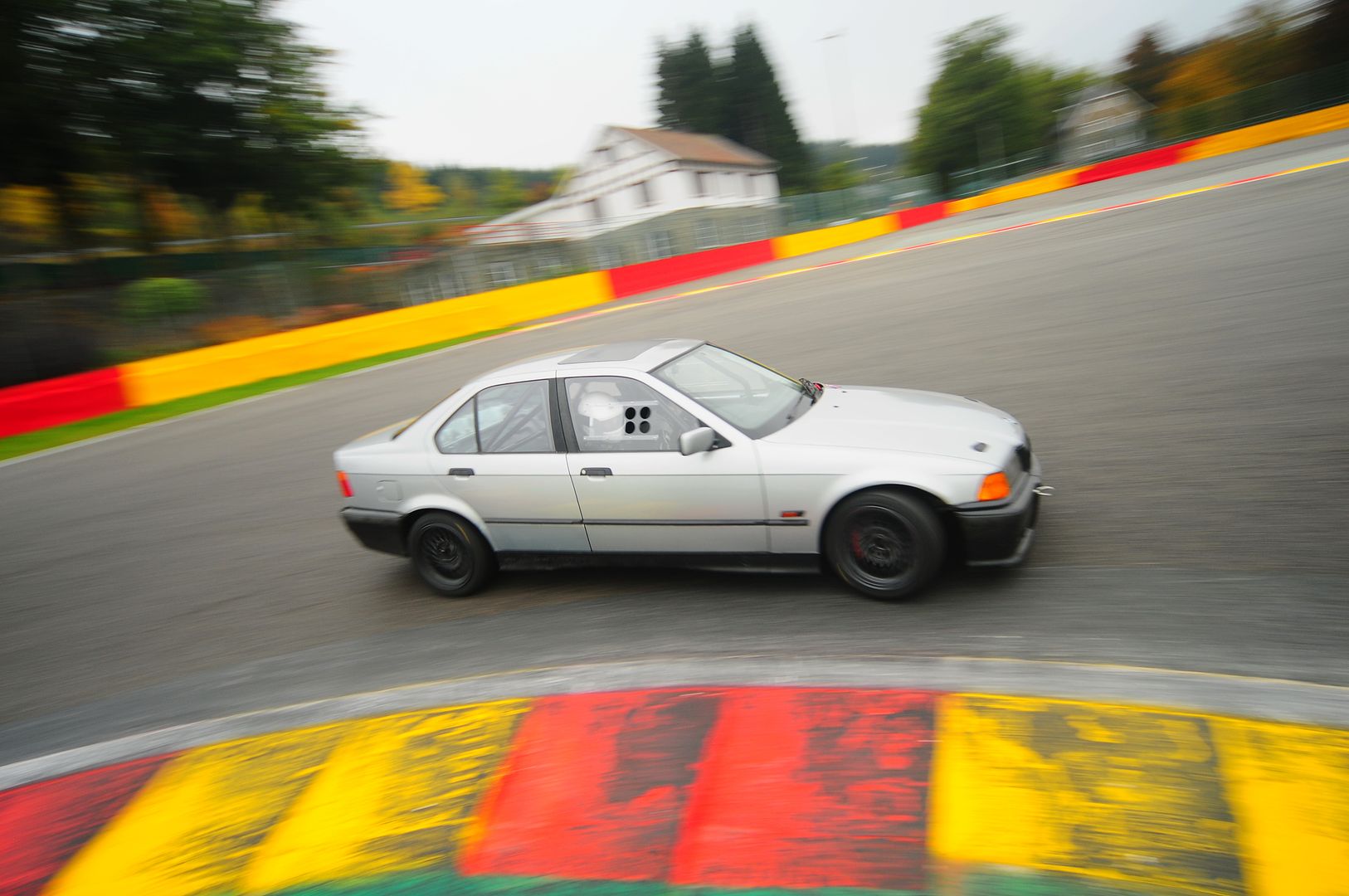
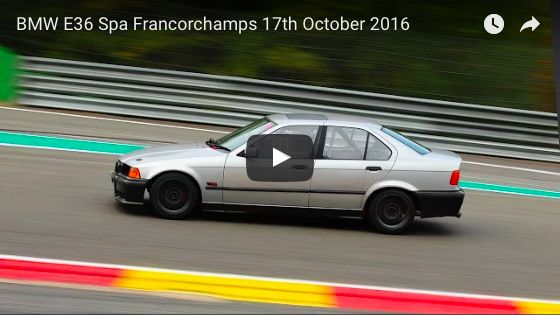
https://www.youtube.com/watch?v=XQAYLadOMKM
Fantastic circuit again as expected and no issues with the car. Taking it back out a couple more times this year and then see what needs attention.
Edited by f0xy on Sunday 30th October 09:41
That engine pulls like a train through the revs, have you got a shot of the dyno graph? be interesting to see the power delivery.
Also can you advise what your clutch / flywheel setup is? trying to find a decent replacement to the shoddy DMF setup on my E46 330i and looking for a SMF with a reasonable clutch for fast road use.
Also can you advise what your clutch / flywheel setup is? trying to find a decent replacement to the shoddy DMF setup on my E46 330i and looking for a SMF with a reasonable clutch for fast road use.
Sf_Manta said:
That engine pulls like a train through the revs, have you got a shot of the dyno graph? be interesting to see the power delivery.
Also can you advise what your clutch / flywheel setup is? trying to find a decent replacement to the shoddy DMF setup on my E46 330i and looking for a SMF with a reasonable clutch for fast road use.
Here is a comparison graph - M52B28 (original 328i engine), M50B30 v1 (with M50 inlet, etc), M50B30 v2 (with ITB etc)Also can you advise what your clutch / flywheel setup is? trying to find a decent replacement to the shoddy DMF setup on my E46 330i and looking for a SMF with a reasonable clutch for fast road use.
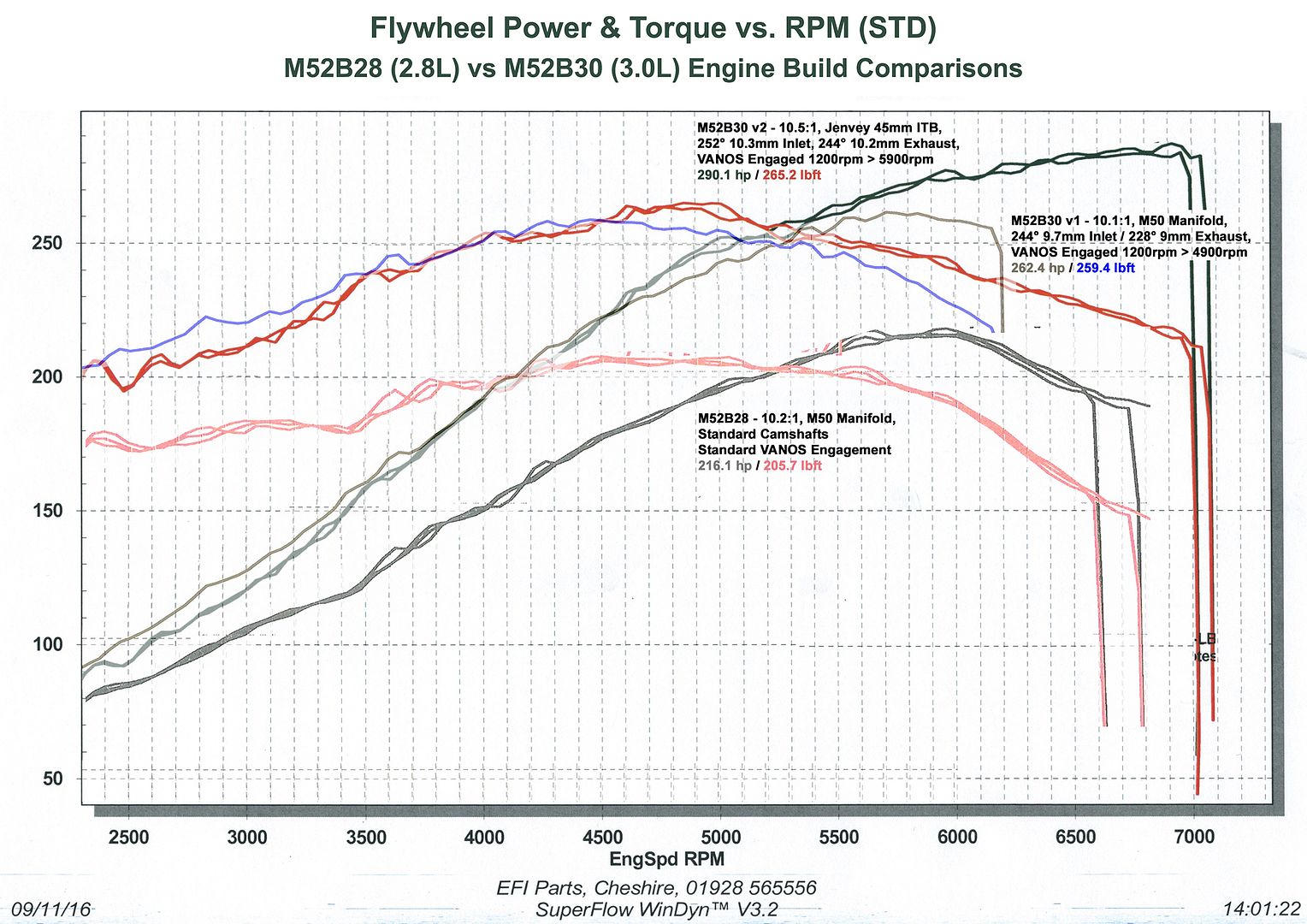
I'm still running the M20 flywheel + matching clutch setup (Sachs). The only difference is I run the uprated Sachs cover plate for that kit, the friction disc is still the E30 M20 item. When it was apart it was showing no signs of wear - I get people all the time asking me why does it not slip but I don't abuse it, clutch kick it or anything like that. I will carry on using it until I have an issue..... I use that with a 5spd ZF box (328i/M3), not sure if the E46 box is the same with regards to release bearing height though...
B'stard Child said:
nice work - was it just a good shell that came up or did you go hunting for a saloon rather than a coupe?
Luckily a friend was about to sell his 320i automatic saloon and it was solid underneath... he ended up donating it to me! Quite lucky in fact as I looked at 10-15 before then and they were all rotten on the sills, or had work before. I wasn't too bothered about what model the car was, as the whole thing has been rewired with the most minimal loom (9 fuses). essayer said:
Great thread! Out of interest, what were you using for the rpi graphs?
MegaLogViewer HD - https://www.efianalytics.com/MegaLogViewer/I still use it now, useful tool even if its just for viewing .csv log files
Gassing Station | Readers' Cars | Top of Page | What's New | My Stuff