Attempting to build the fastest road legal Elan in the world
Discussion
lukeharding said:
Excellent! Good to hear you're going with a smaller wheel, I think it'll suit it perfectly. Your car doesn't have the usual delicate aesthetic of a standard elan but I reckon it'll look spot on. Builds like this are definitely inspiring for everyone else to try and create something in their own garage, and for them to teach themselves some new skills.
Although there have been some external mods, I have tried to keep them to a minimum and retain the essence of the overall shape of the original. For example, I know that there is a vent on the bonnet, but no one has noticed that the bonnet height has been rasied around 50mm in order to clear the front of the engine without having to fit a power bulge. Took a lot of suble reshaping to achieve.rev-erend said:
This may beof interest.
http://www.specialsaloons.co.uk/elans/4582425904
https://www.flickr.com/photos/30098213@N05/6093845...
Built with no regard to aesthetics, function over form. The lines of the original body have been compromised, IMO, making the car look stuck together.http://www.specialsaloons.co.uk/elans/4582425904
https://www.flickr.com/photos/30098213@N05/6093845...
Mind you, beauty is in the eye of the beholder :-)
stevebroad said:
Although there have been some external mods, I have tried to keep them to a minimum and retain the essence of the overall shape of the original. For example, I know that there is a vent on the bonnet, but no one has noticed that the bonnet height has been rasied around 50mm in order to clear the front of the engine without having to fit a power bulge. Took a lot of suble reshaping to achieve.
Thats pretty impressive, a 50mm change isn't easy to hide! stevebroad said:
rev-erend said:
This may beof interest.
http://www.specialsaloons.co.uk/elans/4582425904
https://www.flickr.com/photos/30098213@N05/6093845...
Built with no regard to aesthetics, function over form. The lines of the original body have been compromised, IMO, making the car look stuck together.http://www.specialsaloons.co.uk/elans/4582425904
https://www.flickr.com/photos/30098213@N05/6093845...
Mind you, beauty is in the eye of the beholder :-)
Tweaked the passenger door so it fits the opening a litle better. Todo that I cut through the frame, twisted it, held it in place and carboned over the cuts. Looks naff at the moment but I will trim it up once cured.
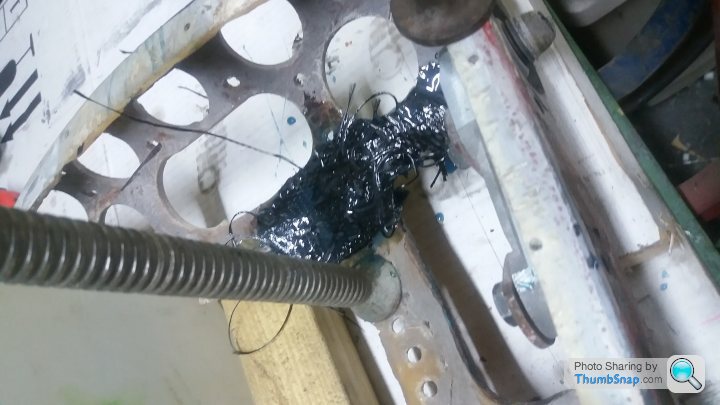
With regard to the driver's door, I have worked out how to secure the base of the lexan window and made a couple of aluminium moulds which are at present covered in carbon and cooking at 120deg C.
While that was going on I rumminated on how to fit the two parts of the door together. I think that I will butt join them with a 20mm carbon strip holding the two sections together. Watch this space :-)
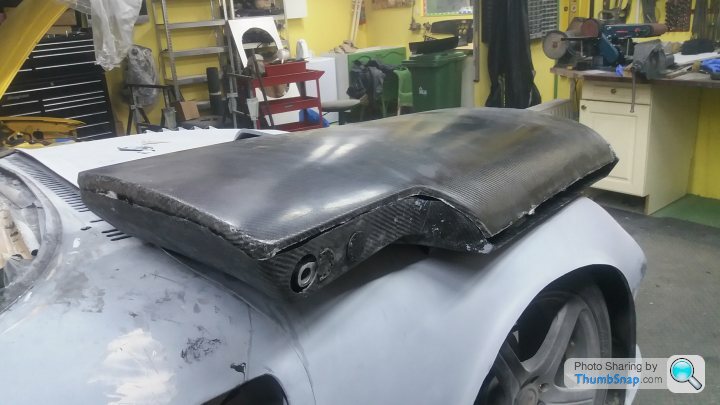
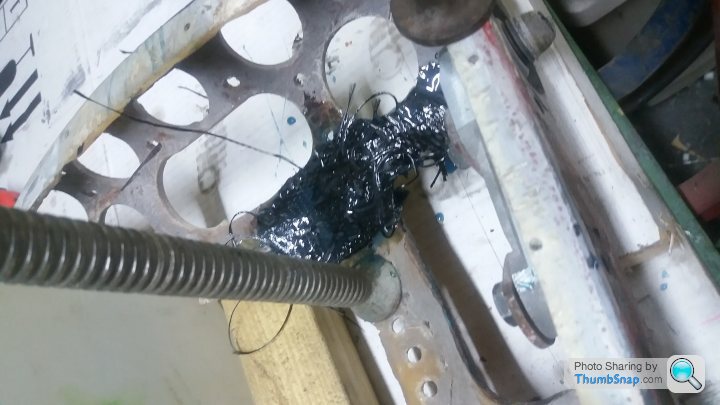
With regard to the driver's door, I have worked out how to secure the base of the lexan window and made a couple of aluminium moulds which are at present covered in carbon and cooking at 120deg C.
While that was going on I rumminated on how to fit the two parts of the door together. I think that I will butt join them with a 20mm carbon strip holding the two sections together. Watch this space :-)
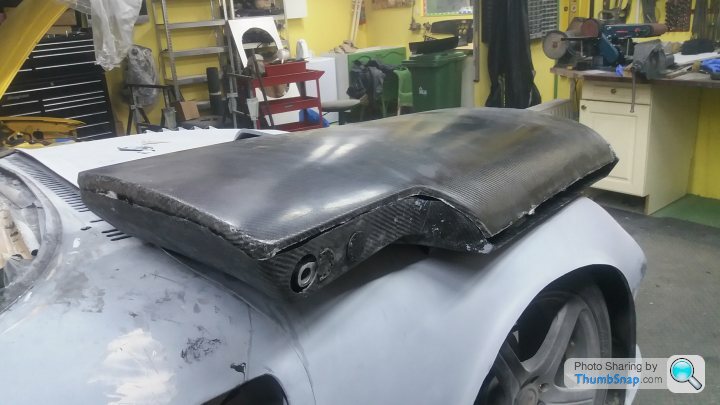
Edited by stevebroad on Wednesday 6th May 23:20
Edited by stevebroad on Tuesday 12th May 08:29
stevebroad said:
Watch this space :-)
I assure you, there are plenty of us who are watching intently! When you are cooking the panels in the oven do you have any weight applied to help with consolidation of the laminate or, due to the non structural nature of the parts, not need to? I have a fair few panels to make and had never even contemplated successfully making them without an autoclave, however you are clearly demonstrating that a cunning lad can work his way around any problem. Inspiration work, hope you don't mind if i rip off some of your ideas!
F1natic said:
I assure you, there are plenty of us who are watching intently!
When you are cooking the panels in the oven do you have any weight applied to help with consolidation of the laminate or, due to the non structural nature of the parts, not need to? I have a fair few panels to make and had never even contemplated successfully making them without an autoclave, however you are clearly demonstrating that a cunning lad can work his way around any problem. Inspiration work, hope you don't mind if i rip off some of your ideas!
When working with prepreg carbon, both heat and pressure (in the form of a vacuum) are prerequisites. When using carbon cloth and adding resin (like you would with traditional fibreglass) you don't use heat and the vacuum is optional, although advantageous as it will aid compaction and remove excess resin if done properly, inproving structural strength and appearance.When you are cooking the panels in the oven do you have any weight applied to help with consolidation of the laminate or, due to the non structural nature of the parts, not need to? I have a fair few panels to make and had never even contemplated successfully making them without an autoclave, however you are clearly demonstrating that a cunning lad can work his way around any problem. Inspiration work, hope you don't mind if i rip off some of your ideas!
Autoclaves are nothing more than an oven that can exert more than atmospheric pressure, not really required for custom automotive stuff. The only advantages of an autoclave are speed, consistency and repeatability, useful in the aerospace and construction industries. In fact, I have been helping (in a small way) a composite manufacturing company in developing techniques to use their autoclave prepregs in standard ovens, which has been interesting.
No problem, if I wanted to keep secrets putting them on here wouldn't be the best idea :-)
Edited by stevebroad on Tuesday 12th May 09:31
Great project ive read the whole thread, amazing the amount of stuff you’ve just made from scratch.
Out of interest what gearbox are you planning to use? Ive got a 2wd 550hp sapphire cosworth and looking into uprated gearbox options at the moment, leaning towards getting a quaife big tooth kit
Out of interest what gearbox are you planning to use? Ive got a 2wd 550hp sapphire cosworth and looking into uprated gearbox options at the moment, leaning towards getting a quaife big tooth kit
Finally started the job I have been thinking about for over a year and not been looking forward to tackling, door window frames. Made the second frame yesterday and started on the fitting process. I have no idea how I am going to secure it as it needs to be pretty rigid, so I am just going for it and will see how it pans out.
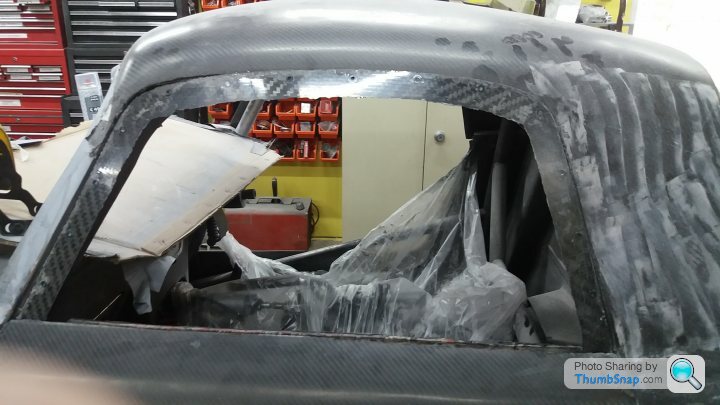

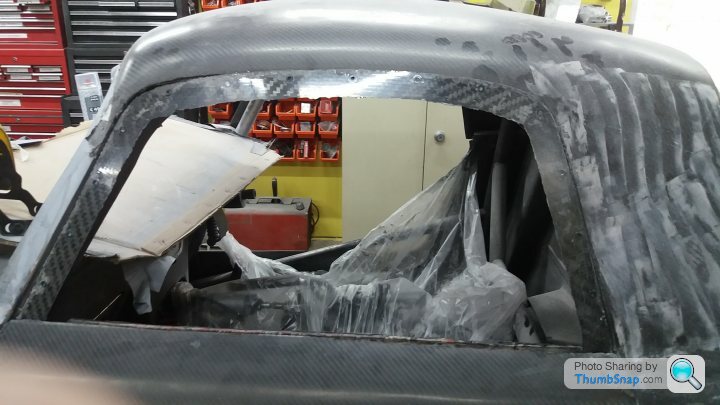

stevec33 said:
Great project ive read the whole thread, amazing the amount of stuff you’ve just made from scratch.
Out of interest what gearbox are you planning to use? Ive got a 2wd 550hp sapphire cosworth and looking into uprated gearbox options at the moment, leaning towards getting a quaife big tooth kit
Hi SteveOut of interest what gearbox are you planning to use? Ive got a 2wd 550hp sapphire cosworth and looking into uprated gearbox options at the moment, leaning towards getting a quaife big tooth kit
550 should get the Saph to shift :-) I owned a 475bhp Saph a few years ago and it was mental!
Gearbox is a 6 speed Elite sequential with pneumatic paddle shift. Would probably have used a Quaife but they wouldn't fit into my chassis.
Steve
Friday, as it was my son Alex's birthday and we had a gocart racing/bingo/trivial pursuit party, was the first lockdown day that I didn't work on the car! However, I have made quite a bit of progress over last few weeks and there is not a lot of bodywork left to do.
The roof and doors were the last big jobs (still have to make a rear diffuser but that can wait). Roof is on, passenger door is well on the way and the driver's door is in progress.
All that will be left after this will be details and I can then start the paint process as I have decided, finally, on the paint scheme.
The roof and doors were the last big jobs (still have to make a rear diffuser but that can wait). Roof is on, passenger door is well on the way and the driver's door is in progress.
All that will be left after this will be details and I can then start the paint process as I have decided, finally, on the paint scheme.
Gassing Station | Readers' Cars | Top of Page | What's New | My Stuff