Jaguar xjc 4.2
Discussion
Zippee said:
Been really enjoyable reading this so far, I just wish I had the skill to do what you are doing 
Have a great Christmas and looking forward to more investments in the new year. Do you have a rough time for completion yet?
The idea is to have a running car back from the body shop, then once back in my garage I can then finish off all the interior in my own time. It could be complete by next autumn but I’m in no hurry. 
Have a great Christmas and looking forward to more investments in the new year. Do you have a rough time for completion yet?


Nothing exciting but I’ve been having a go at re-plating the original nuts,bolts and washers.
Picture above shows the front upper wishbone inner mounts with freshly zinc plated original fixings.
Once I get the axles re-assembled the bolt heads and nuts will get a dab of clean grease or clear waxoyl to keep everything looking new as long as possible

Just sitting at the breakfast bar and rebuilding one of the petrol caps.
Surprising how many parts put these together.

Chrome is original, not perfect but I think is ok

New rubber seal, I’ve replated in zinc anything that is steel, springs, washers, the split roll pins that act as hinges. The cast aluminium body has just been shot blast with a fine glass grit.
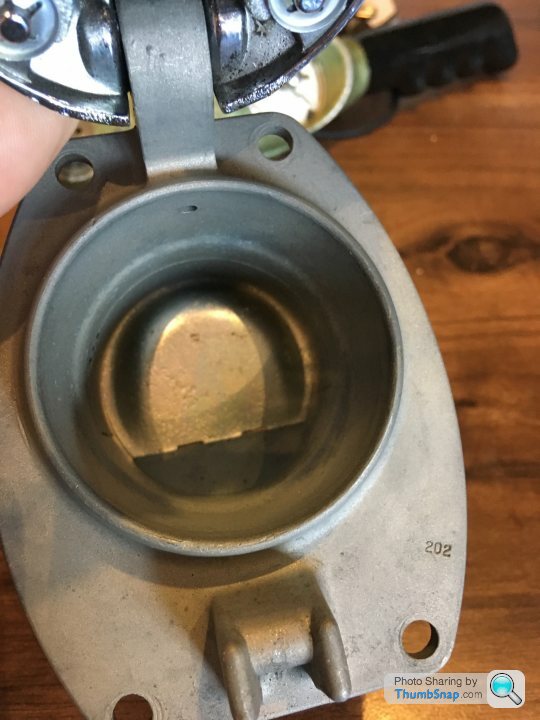
That bottom sprung hinged flap you can see where the corrosion had started to eat into the surface. That’s been replated as well.

Hopefully all good for another 40 years
Surprising how many parts put these together.

Chrome is original, not perfect but I think is ok

New rubber seal, I’ve replated in zinc anything that is steel, springs, washers, the split roll pins that act as hinges. The cast aluminium body has just been shot blast with a fine glass grit.
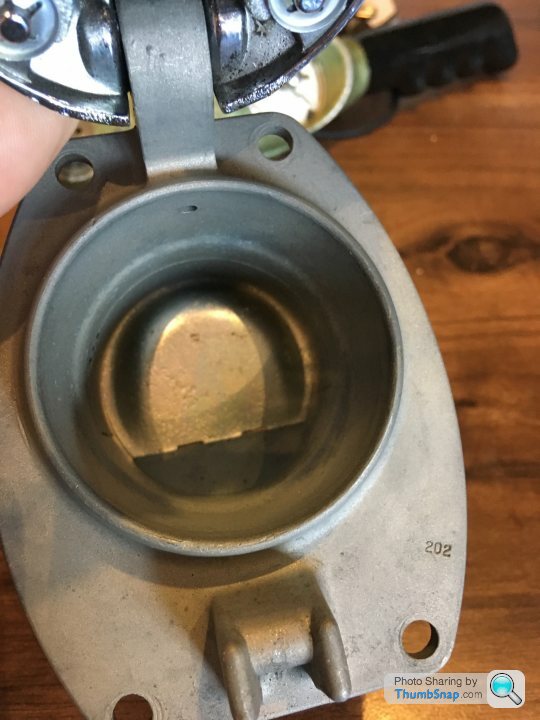
That bottom sprung hinged flap you can see where the corrosion had started to eat into the surface. That’s been replated as well.

Hopefully all good for another 40 years

The original front under bumper grill I re-assembled today also.
It’s made from stainless steel other than the bolts holding it all together which had obviously rusted and oozed orange over the slats making it all look like a cheap item. I don’t have any before pictures unfortunately but it looked like junk initially.
When apart I noticed the slats were not chrome plated but stainless so thought I’ll give it a bit of tlc. The original rusted steel securing bolts I could have replated but they would only rust again sitting inside plastic spacers. So I made the bolts from stainless steel m5 stud cut to length with stainless dome nuts on the top thread locked into place and used stainless nyloc nuts on the bottom to nip up and hold everything secure.
The bottom larger slat has a thicker pressed steel reinforcement fitted which also showed a lot of corrosion. I had that hot dip galvanised so won’t have any rust issues there.
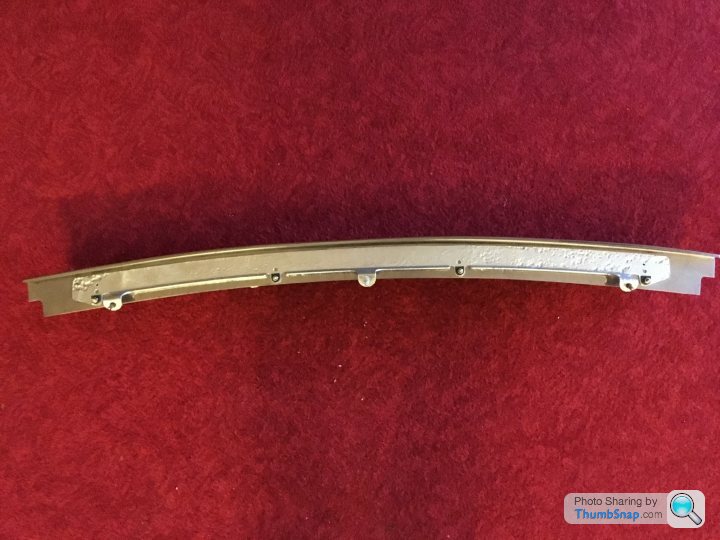
Above picture shows the hot dipped galvanised reinforcement plate. Below is the way round when fitted to the car


Just trying to show the shine. Not immaculate but very good for a used part. The top slat has a couple of brackets to pop rivet back on. I’ve re-plated those but not fitted yet. Picture of brackets below.

It’s made from stainless steel other than the bolts holding it all together which had obviously rusted and oozed orange over the slats making it all look like a cheap item. I don’t have any before pictures unfortunately but it looked like junk initially.
When apart I noticed the slats were not chrome plated but stainless so thought I’ll give it a bit of tlc. The original rusted steel securing bolts I could have replated but they would only rust again sitting inside plastic spacers. So I made the bolts from stainless steel m5 stud cut to length with stainless dome nuts on the top thread locked into place and used stainless nyloc nuts on the bottom to nip up and hold everything secure.
The bottom larger slat has a thicker pressed steel reinforcement fitted which also showed a lot of corrosion. I had that hot dip galvanised so won’t have any rust issues there.
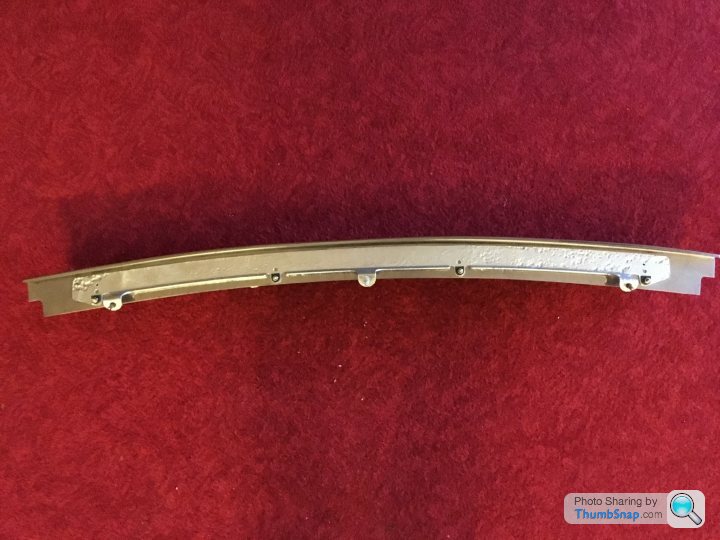
Above picture shows the hot dipped galvanised reinforcement plate. Below is the way round when fitted to the car


Just trying to show the shine. Not immaculate but very good for a used part. The top slat has a couple of brackets to pop rivet back on. I’ve re-plated those but not fitted yet. Picture of brackets below.

So I bought replacement bushes for the suspension components and went with super pro. Nothing untoward until I opened the front crossmember mount packet. To fit the upgrade Bush you need to use the existing Bush outer shell and the original crush tube. The crush tube simply slides out the original Bush but the shell obviously has a lump of rubber and metal bonded inside it.
Nothing is ever simple just lucky I still have the equipment at work to do this properly. Pictures below show the stages.

To get the grotty middle out I used a oxyacetylene torch to heat up the outer shell and burn off the adhesive used to bond the rubber into the shell. It didn’t need to glow red, but hot enough to see small flames as the glue burnt off. Whilst still hot I had a suitably sized steel bar to push out the centre via a hydraulic manual press. The middles came out fairly easily but still left a gooey mess inside the shell.
Below shows the inside of the shell cleaned up. I spun them up in a lathe and used 80 grit emery to remove the lumps then a 120 grit to finish.

Nothing is ever simple just lucky I still have the equipment at work to do this properly. Pictures below show the stages.

To get the grotty middle out I used a oxyacetylene torch to heat up the outer shell and burn off the adhesive used to bond the rubber into the shell. It didn’t need to glow red, but hot enough to see small flames as the glue burnt off. Whilst still hot I had a suitably sized steel bar to push out the centre via a hydraulic manual press. The middles came out fairly easily but still left a gooey mess inside the shell.
Below shows the inside of the shell cleaned up. I spun them up in a lathe and used 80 grit emery to remove the lumps then a 120 grit to finish.

Edited by RobXjcoupe on Friday 17th January 23:21

Above shows the outer shells shotblast before I zinc plated them.
Below shows the shells zinc plated together with the original crush tubes
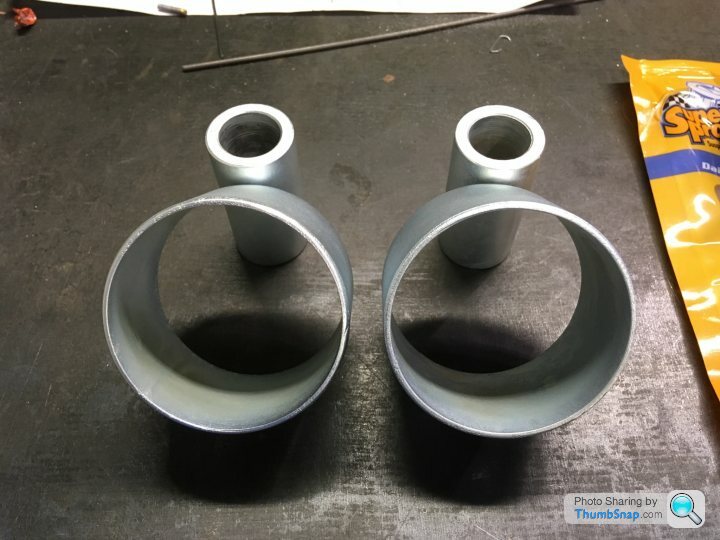

Then last thing was to press the new bushes into the refurbed outer shells. Again back on the hydraulic press so I can push these on nice and square.
Pictures below show finished item. Bit of grief considering the cost of the new poly Bush. Done now though


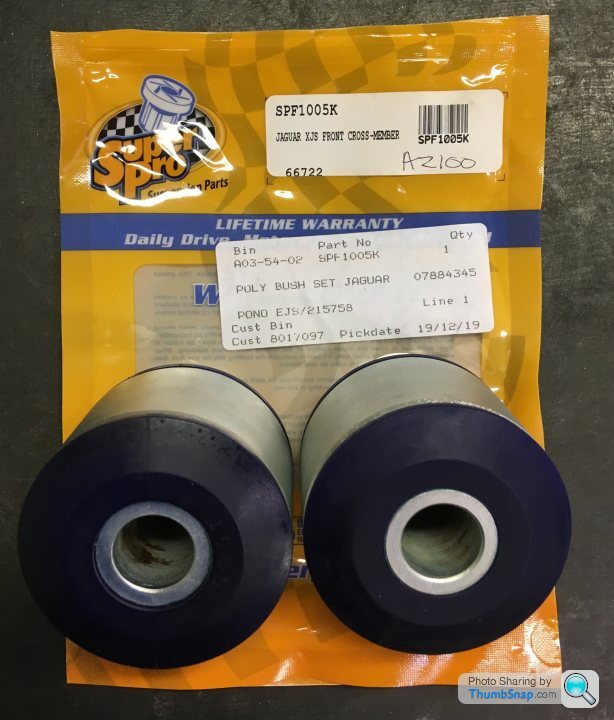
Having all the right tools makes life a lot simpler, but Mrs Bobbers is never going to be happy with me spending £000's on equipment to use once in a while and I'm not allowed to do homers where I work, they won't allow us to even bring in our own materials and do stuff in our own time!!!
Amazing skills evidenced here.
I some ways it would seem that your Jag was 'over engineered' ( ie the fuel filler cap!), so it must take a lot longer to overhaul the parts etc. But when the car is finished it will be so much more satisfying I would guess.
A very good read and so informative.
I have recently moved into a flat so do not have any sort of garage to 'mess around' in.
I really miss that but I am so envious ( in a nice way !) of folk who can fabricate and design parts.
Good luck on the job front, something car related would seem to be ideal, going by this thread !
I some ways it would seem that your Jag was 'over engineered' ( ie the fuel filler cap!), so it must take a lot longer to overhaul the parts etc. But when the car is finished it will be so much more satisfying I would guess.
A very good read and so informative.
I have recently moved into a flat so do not have any sort of garage to 'mess around' in.
I really miss that but I am so envious ( in a nice way !) of folk who can fabricate and design parts.
Good luck on the job front, something car related would seem to be ideal, going by this thread !
Bobberoo99 said:
Having all the right tools makes life a lot simpler, but Mrs Bobbers is never going to be happy with me spending £000's on equipment to use once in a while and I'm not allowed to do homers where I work, they won't allow us to even bring in our own materials and do stuff in our own time!!!
Well that sucks! I’ve worked as a Ford toolmaker for 30 years and as long as the Ford work was completed a homer has never been an issue. We had one lad working permanently on a jig borer who used to machine the cast iron mini cylinder heads so as hardened valve seats could be fitted, we had an electrostatic paint application for the old steel wheels and with a modified hanger bracket axle castings, freshly shot blast wire wheels would go around on a nightshift looking brand new again with a black finish.Supervisors, and managers never had an issue with using the facilities, just nothing big on a day shift.
Toolmakers used to fix all sorts of things for themselves, colleagues and management. Part of our DNA lol

Paul S4 said:
Amazing skills evidenced here.
I some ways it would seem that your Jag was 'over engineered' ( ie the fuel filler cap!), so it must take a lot longer to overhaul the parts etc. But when the car is finished it will be so much more satisfying I would guess.
A very good read and so informative.
I have recently moved into a flat so do not have any sort of garage to 'mess around' in.
I really miss that but I am so envious ( in a nice way !) of folk who can fabricate and design parts.
Good luck on the job front, something car related would seem to be ideal, going by this thread !
Thank you for your words. I must admit the mass of parts that need a refurbish is mind boggling but it will benefit the end result as I will know the exact condition of everything. I am on a budget of sorts, hence I’ve been doing a lot myself so as any cash goes into the body and eventually the interior. I some ways it would seem that your Jag was 'over engineered' ( ie the fuel filler cap!), so it must take a lot longer to overhaul the parts etc. But when the car is finished it will be so much more satisfying I would guess.
A very good read and so informative.
I have recently moved into a flat so do not have any sort of garage to 'mess around' in.
I really miss that but I am so envious ( in a nice way !) of folk who can fabricate and design parts.
Good luck on the job front, something car related would seem to be ideal, going by this thread !
I enjoy pottering with things, i find it relaxing obviously it helps using my work toolroom making and repairing bits and pieces. I post the pictures and words to try and show any future Jag owner how relatively easy it is to do certain things.
New job wise, here in South Wales, Tesco pay more per hour stacking shelves than being a body panel and interior fit quality inspector at the new Aston Martin st Athan facility. No toolmaker jobs at all. Not sure really if engineering will be my future job
Ordered a set of eibach springs, a set of -40mm for the front (same spec as the old Leda springs that were fitted just one had snapped hence new ones). Rear springs are also eibach but just -15mm, just couldn’t find any uprated shorter springs so I’m going to make new spring collars to fit my new rear shocks which reduces the fitted spring compression by 20mm so in effect the weight of the car will then lower by another 20mm but in case it’s too low I’ll also make some rear spring spacers to get the body sitting correctly. I couldn’t afford the extra money on adjustable height rear spring platformed shocks so doing it my way 

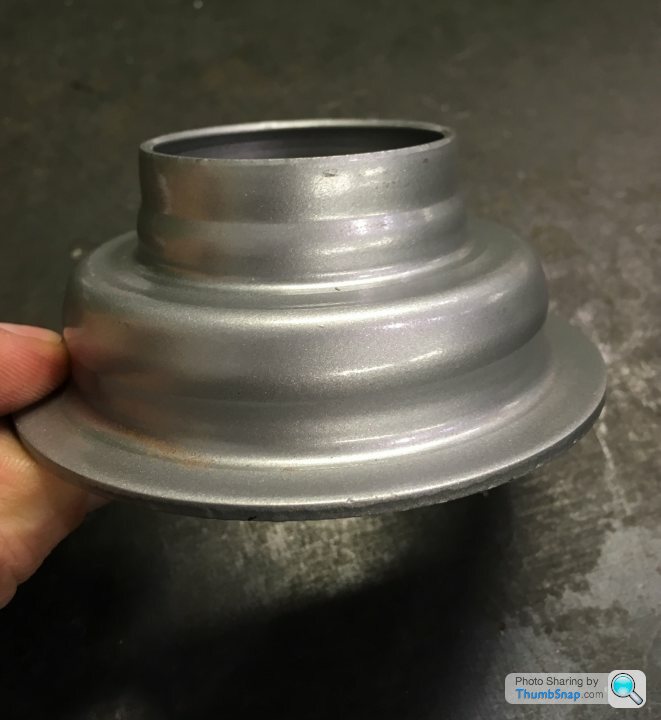
Above and below shows the original lower spring platform for my rear shock absorber.
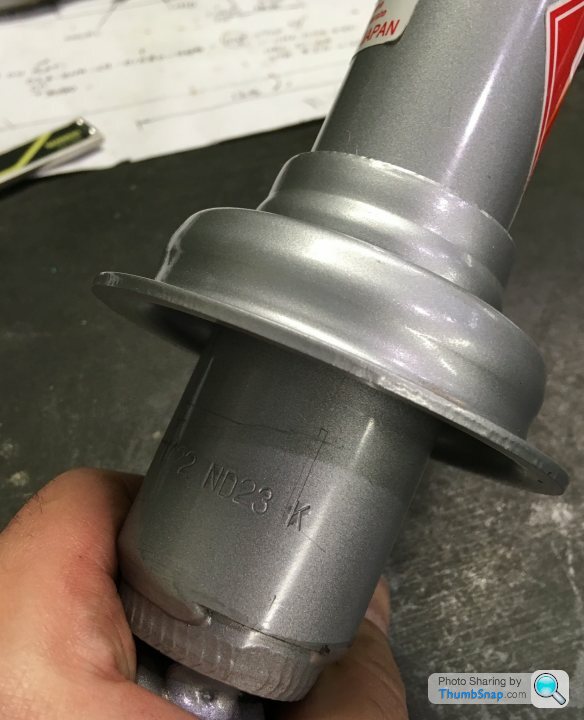
Even with the -15mm springs I just bought I still need to compress the spring another 50mm to fit on the shock. So if I lower the spring platform the spring will require the weight of the car to make up the extra compression and hence lower the back end nicely.
So to lower the spring platform I first removed the part that locates on the small shoulder on the damper so as to make a new top hat to fit within but with the platform lower down the damper body.
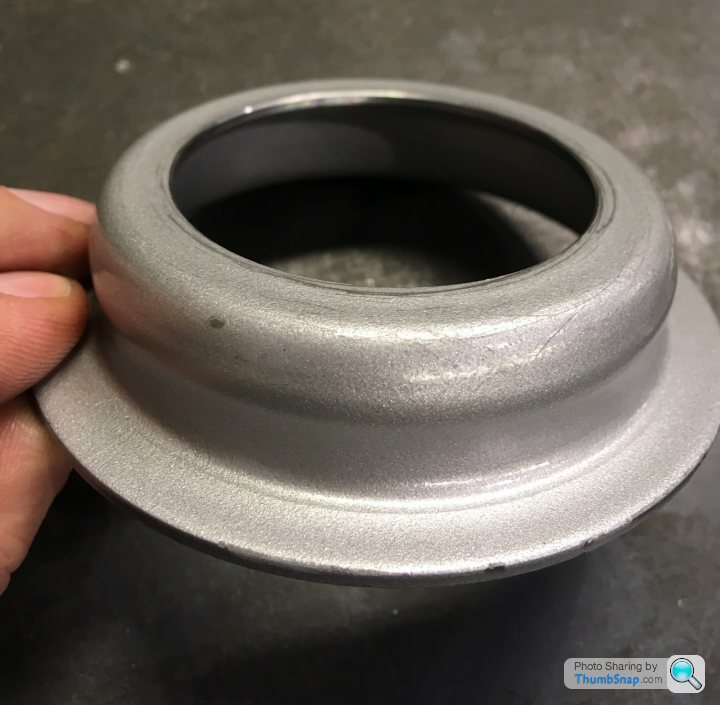


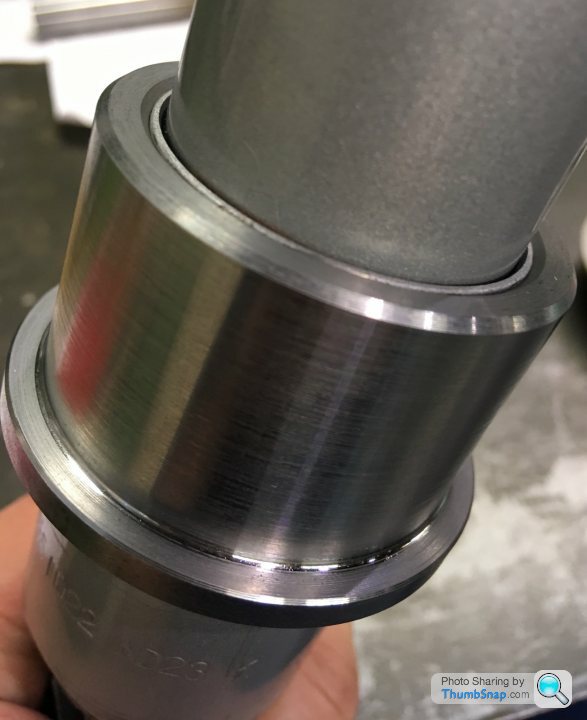
So above shows first top hat made and fitting nicely onto damper body.
The outside diameter of the top hat body is roughly 0.1mm bigger than the sized hole I made in the original spring platform so I can press the two parts together without needing to weld. The force of the spring will always keep the two parts firmly together also.

Below shows the modified spring platform fitted onto the damper body

Started to assemble the front suspension and noticed a couple of parts I hadn’t zinc plated before painting. Bit of a pain but might as well do things properly so they were stripped back to bare metal again and this morning went into my little zinc plating tank. Below shows the parts zinc plated and masked up for paint again.
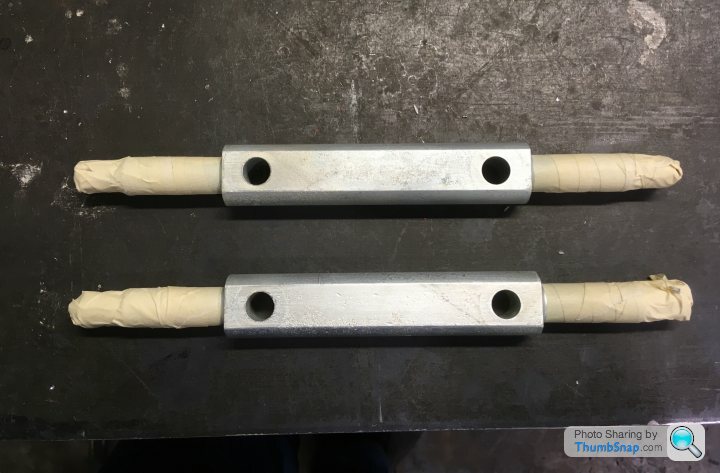
So this time the screw threads and the bush bearing diameter are protected properly against corrosion (the masked areas) with a black finish on the middle area.
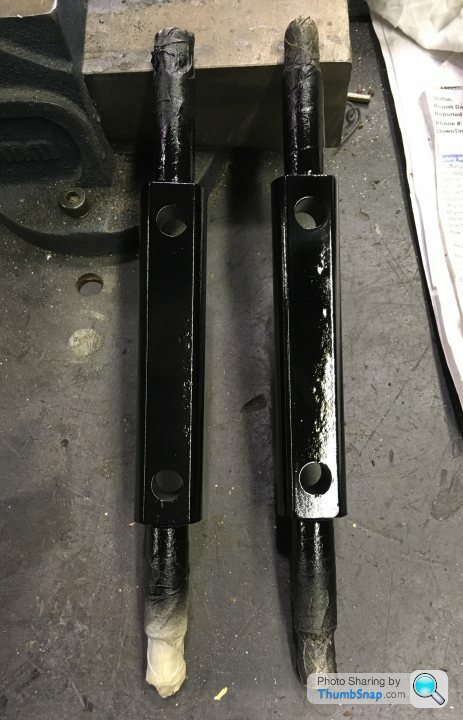

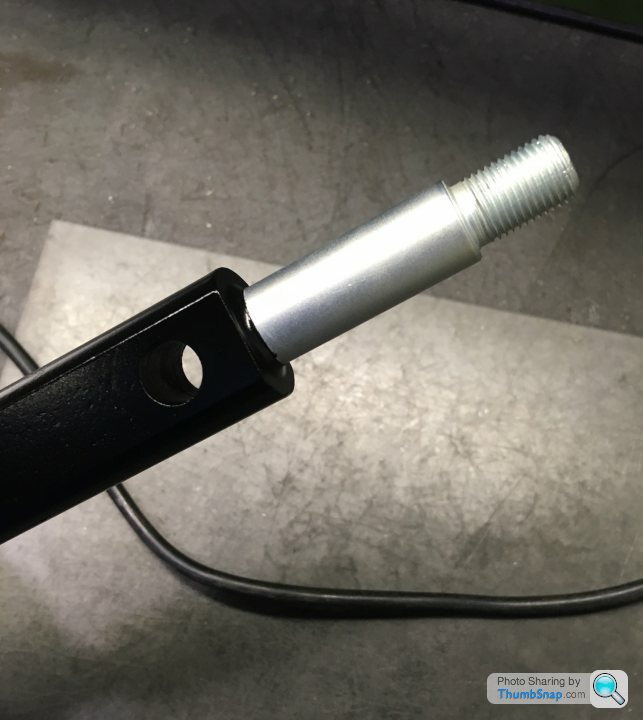
A better finish I think and once assembled a blob of wax or grease on the protruding screw thread will keep it bright for longer
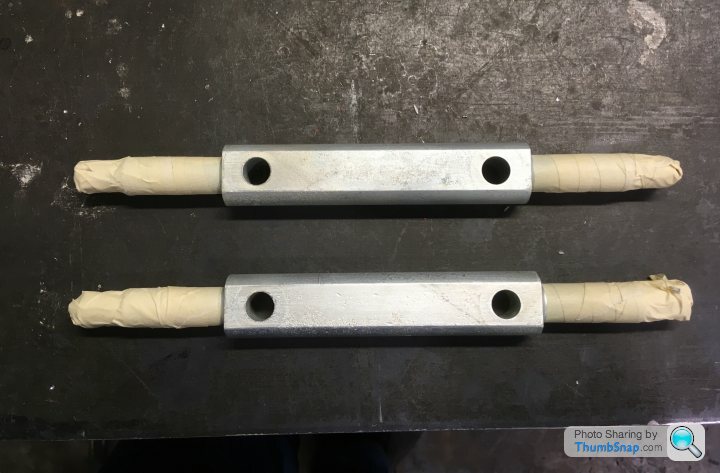
So this time the screw threads and the bush bearing diameter are protected properly against corrosion (the masked areas) with a black finish on the middle area.
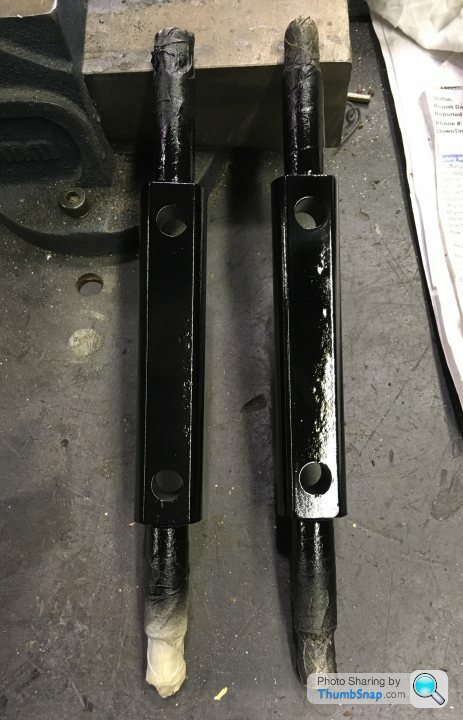

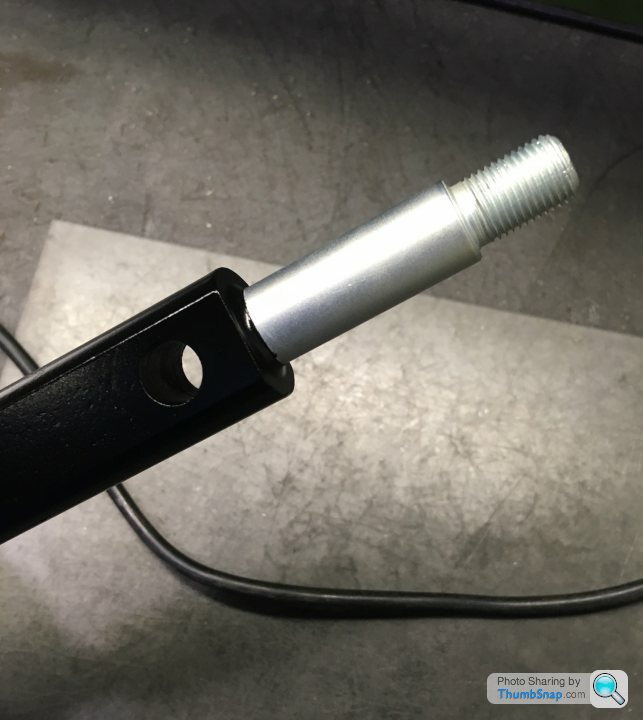
A better finish I think and once assembled a blob of wax or grease on the protruding screw thread will keep it bright for longer

Gassing Station | Readers' Cars | Top of Page | What's New | My Stuff