BMW 330CI E46 Build thread
Discussion
Hello mate,
Did you ever make the m50 intake manifold adapter to use the m54 throttle body?
Is it possible to sell me one or possibly provide me the design files so that I can have it printed please?
My car has been sitting for so long because I need an adapter for the manifold and I haven't seen one that works.
If you can, please help. Thanks mate.
Did you ever make the m50 intake manifold adapter to use the m54 throttle body?
Is it possible to sell me one or possibly provide me the design files so that I can have it printed please?
My car has been sitting for so long because I need an adapter for the manifold and I haven't seen one that works.
If you can, please help. Thanks mate.
Sf_Manta said:
Looks great with the build so far.
Did you get the block vapour blasted? or just gave it a good scrub? Have heard if you get aluminum items vapour blasted it seals the surface and gives a better surface finish for paint.
The engine block was scrubbed with degreaser before sending it to the machine shop. Once they had finished the machine work they run it through what is basically a large dishwasher/parts washer to ensure it is fully clean, it does a great job of removing all of the oil stains and residue ready for painting, the vapour blasting looks fantastic though for items which are not getting painted.Did you get the block vapour blasted? or just gave it a good scrub? Have heard if you get aluminum items vapour blasted it seals the surface and gives a better surface finish for paint.
garbajkolektor said:
Hello mate,
Did you ever make the m50 intake manifold adapter to use the m54 throttle body?
Is it possible to sell me one or possibly provide me the design files so that I can have it printed please?
My car has been sitting for so long because I need an adapter for the manifold and I haven't seen one that works.
If you can, please help. Thanks mate.
Yes. I had a 3D Printed prototype and then moved to a laser cut aluminium version found below. This has been on the car for months now without issues.Did you ever make the m50 intake manifold adapter to use the m54 throttle body?
Is it possible to sell me one or possibly provide me the design files so that I can have it printed please?
My car has been sitting for so long because I need an adapter for the manifold and I haven't seen one that works.
If you can, please help. Thanks mate.
I can get these laser cut should you require one. Drop me a Private message if you want to discuss.

Engine building continues. I was waiting for the mains bolts to arrive so I was able to start to put the crank in and assemble the bottom end.
While doing this I checked the bearing clearances on the mains and the big end bearings. all of these were right in the middle of the factory tolerances.

Another expensive but worthwhile purchase for this engine build turned up. Set of custom ARP studs and nuts which are loner than the M50 kit ARP sell giving full thread engagement in the block. Decided to go down this route rather than spending the money have timeserts fitted to the block.
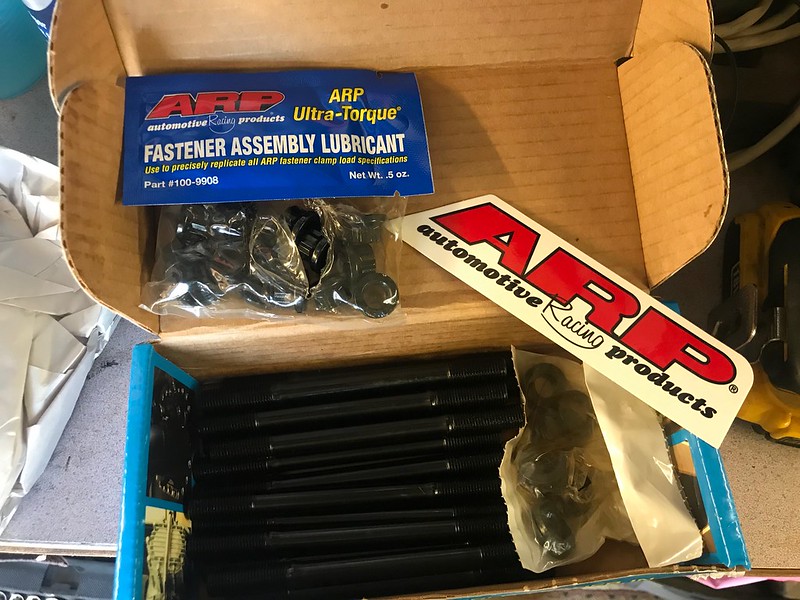
ARP head studs fitted into the block

The new ported head fitted to the block and torqued down. What a stressful job that was getting the head torqued down, still worrying about pulling the threads out of the block but with the longer engagement on these ARP's and only pulling on the threads in the block rather than turning at the same time the head is torqued down and ready to go

Dropped the cam trays, lifters and cams into the head and torqued down the cams

Before I could go any further with finishing off the engine building there was some other jobs which needed tackling first. One being the sump. I was seeing oil pressure as low at 8psi under braking and it was dipping in some corners. No wonder as the sump has zero baffling it. I started by drilling out the little tray that is in there from factory

I drew up some ideas for some basic baffle plates go so inside the sump to stop the sloshing of the oil under braking and cornering, these were cut from card using a laser cutter from the CAD drawing

Test fit in the sump, highlighted a few areas which needed adjustment

Finally made the final version from 2mm aluminium, ready for welding into the sump tomorrow.

Also been busy on the lathe, I looked at the coolant system I'm running and by removing the heater matrix It has become apparent that I have introduced a coolant loop which isn't required now I dont run a heater matrix so wanted a nice soluation to save running the pipes along the block while they're not needed. Aluminium plug made with grooves for orings

Added a plate to the top of it so I can be bolted into place so it doesn't come out of the block due to coolant pressure

While I was waiting on parts I thought I would spend a few hours in the evening this week getting the car ready for removing the engine.

A few hours later it was ready to lift out, found it was nice and easy to bring the engine and gearbox out of the front of the engine back by lowering it down with the subframe and gearbox mount in position

Removed the gearbox to find someone had already fitted a single mass flywheel. I thought someone had but couldn't find proof of it in the service history.
This will be going back in with the new engine

I dropped the sump off as I want to use the oil pump from this engine as it has the uprated oil pump kit in it from Vac Motorsport. I dropped the sump off to find this...

The bolt has also managed to unwind it self half a turn. Luckily due to the design of the bolt not being able to unwind it's self fully due to it hitting the sump this prevents the gear from falling off the shaft and completely losing oil pressure. However what the gear has done is be moving backwards and forwards on the shaft causing it to wear and damage the gear. Luckily the shaft is hardened and the shaft can be reused without issue

I took the oil pump with the Vac Motorsport shaft in it to work with me with a spare gear I had on the shelf and machined the centre of the gear to match the keys on the Vac shaft.
the Vac motorsport kit comes with an ARP left hand bolt which is pre drilled so when this is built up I will be wire locking this from both sides to try and maintain the balance of the shafts.
Amazing the issues that the harmonics of this cranks shaft cause.

Just because I've taken some decent photographs of the porting on the head here's the comparison.
Standard inlet side

Ported inlet side
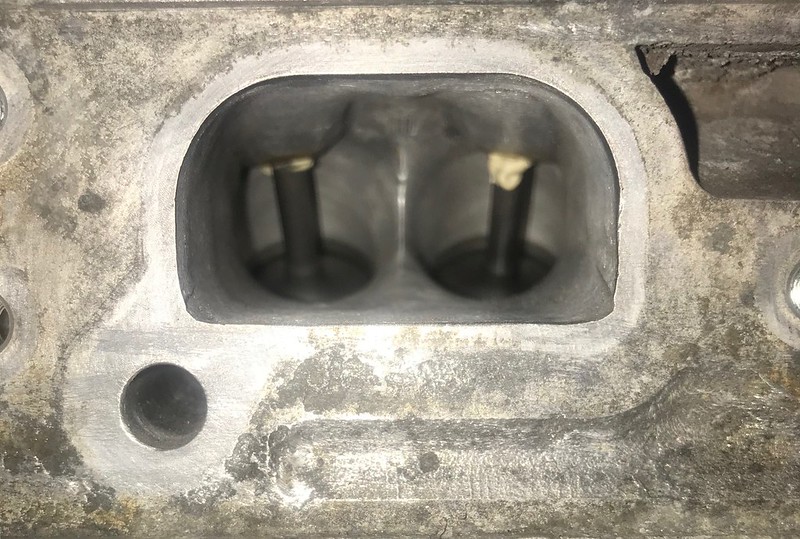
Standard exhaust side

Ported exhaust side (to match the S50 exhaust i'm running)

Engine building continues this weekend, I will be cracking on with wiring in the engine bay as well as finishing off the last jobs on the engine when the sump is back from welding I can finish off the timing of the engine and finish it off.
While doing this I checked the bearing clearances on the mains and the big end bearings. all of these were right in the middle of the factory tolerances.

Another expensive but worthwhile purchase for this engine build turned up. Set of custom ARP studs and nuts which are loner than the M50 kit ARP sell giving full thread engagement in the block. Decided to go down this route rather than spending the money have timeserts fitted to the block.
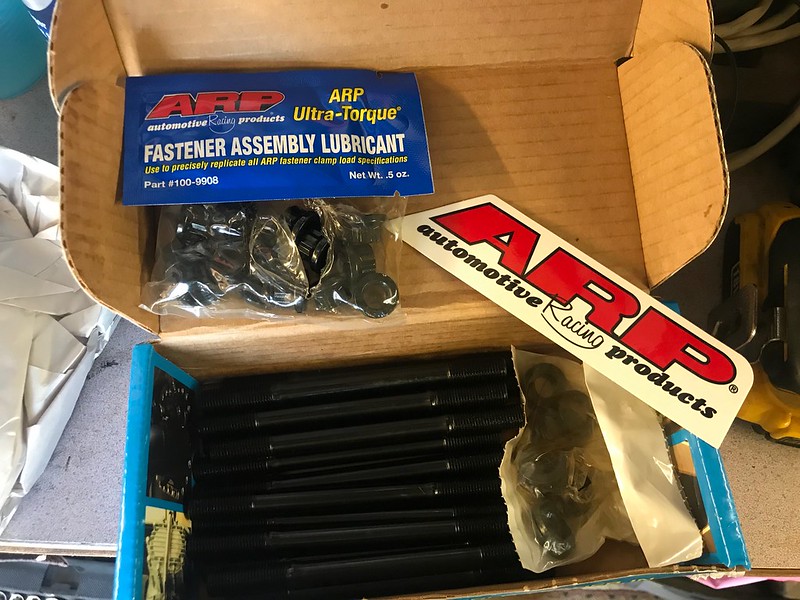
ARP head studs fitted into the block

The new ported head fitted to the block and torqued down. What a stressful job that was getting the head torqued down, still worrying about pulling the threads out of the block but with the longer engagement on these ARP's and only pulling on the threads in the block rather than turning at the same time the head is torqued down and ready to go

Dropped the cam trays, lifters and cams into the head and torqued down the cams

Before I could go any further with finishing off the engine building there was some other jobs which needed tackling first. One being the sump. I was seeing oil pressure as low at 8psi under braking and it was dipping in some corners. No wonder as the sump has zero baffling it. I started by drilling out the little tray that is in there from factory

I drew up some ideas for some basic baffle plates go so inside the sump to stop the sloshing of the oil under braking and cornering, these were cut from card using a laser cutter from the CAD drawing

Test fit in the sump, highlighted a few areas which needed adjustment

Finally made the final version from 2mm aluminium, ready for welding into the sump tomorrow.

Also been busy on the lathe, I looked at the coolant system I'm running and by removing the heater matrix It has become apparent that I have introduced a coolant loop which isn't required now I dont run a heater matrix so wanted a nice soluation to save running the pipes along the block while they're not needed. Aluminium plug made with grooves for orings

Added a plate to the top of it so I can be bolted into place so it doesn't come out of the block due to coolant pressure

While I was waiting on parts I thought I would spend a few hours in the evening this week getting the car ready for removing the engine.

A few hours later it was ready to lift out, found it was nice and easy to bring the engine and gearbox out of the front of the engine back by lowering it down with the subframe and gearbox mount in position

Removed the gearbox to find someone had already fitted a single mass flywheel. I thought someone had but couldn't find proof of it in the service history.
This will be going back in with the new engine

I dropped the sump off as I want to use the oil pump from this engine as it has the uprated oil pump kit in it from Vac Motorsport. I dropped the sump off to find this...

The bolt has also managed to unwind it self half a turn. Luckily due to the design of the bolt not being able to unwind it's self fully due to it hitting the sump this prevents the gear from falling off the shaft and completely losing oil pressure. However what the gear has done is be moving backwards and forwards on the shaft causing it to wear and damage the gear. Luckily the shaft is hardened and the shaft can be reused without issue

I took the oil pump with the Vac Motorsport shaft in it to work with me with a spare gear I had on the shelf and machined the centre of the gear to match the keys on the Vac shaft.
the Vac motorsport kit comes with an ARP left hand bolt which is pre drilled so when this is built up I will be wire locking this from both sides to try and maintain the balance of the shafts.
Amazing the issues that the harmonics of this cranks shaft cause.

Just because I've taken some decent photographs of the porting on the head here's the comparison.
Standard inlet side

Ported inlet side
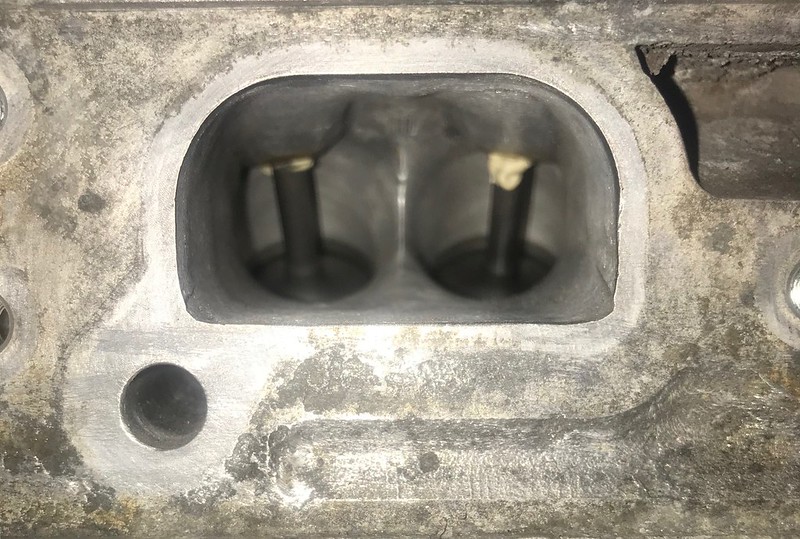
Standard exhaust side

Ported exhaust side (to match the S50 exhaust i'm running)

Engine building continues this weekend, I will be cracking on with wiring in the engine bay as well as finishing off the last jobs on the engine when the sump is back from welding I can finish off the timing of the engine and finish it off.
Weekend was here again which gave me a few hours each day to get on with the engine build.
First job before starting to think about putting the engine in was to get the engine bay cleaned and a few jobs in their tidied up. A good jet wash and degreaser with a scrubbing brush brought off the 17 years of dirt.
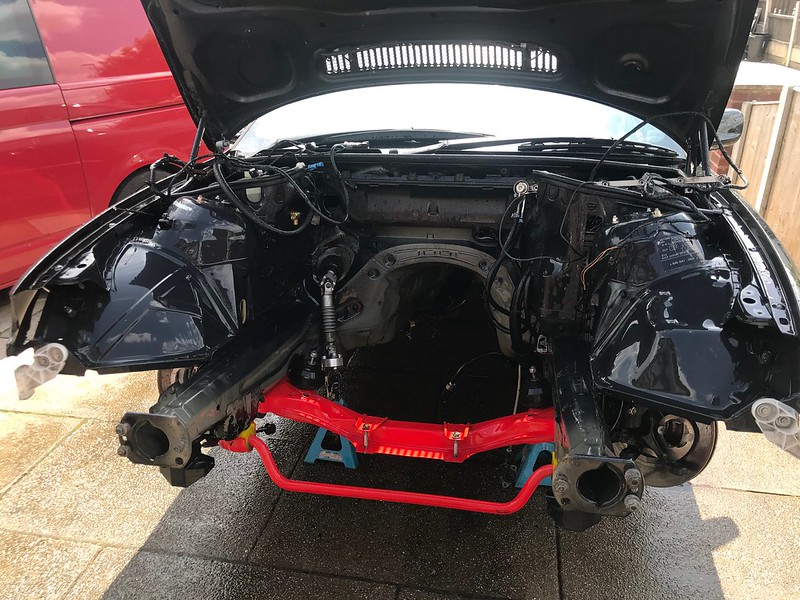
When I did the ABS delete on the car I ran copper wires around the engine bay. This was fine for the function but the appearance of the bent copper line wasn't really in fitting with the rest of the car so decided to get some braided lines made up for the engine bay. Cant really see them unless you point them out which is good really.

I have stripped back some of the wiring loom just to tidy it up and remove some of the excess plugs and the silly plastic box that is part of the BMW loom on these which is unsightly and doesn't fit with the inlet manifold I am using. Retaped up some sections of the loom to removing some of the plastic outer covering.

Baffled sump arrived back from welding. Nicely done, the rivets I put in to hold it together have been replaced with weld now and the 3 different plates have been stitched welded together before welding into the sump with a few small welds.

Finished off the timing of the engine and got the Vanos assembly bolted into postion. Ended up doing this a couple of times making sure the timing was perfect. It was a good job I bought the full kit fo the M54 dual vanos as without it you wouldn't be able to time up these with both cams being variable

Spark plugs, new rocker cover gasket and it was torqued down in the place. Actually starting to look like an engine now.

Once the engine could be lifted into the air again, it's a little awkward with this engine as you need the flywheel on to be able to time up the engine so can't leave it on the engine stand. I have gone back through the bottom end and fitted my ARP Rod bolts as well as the oil pump from my original engine. This time with the replacement oil pump gear and the ARP bolt in the Vac Motorsport shaft wire locked to prevent it from coming undone again in the future.

One finished M54B30 ready to go back into the car. Quite a lot of the parts, sensors and pipes onto the engine while it is nicely accessible on the garage floor.

With the M50 Inlet placed on it.

Other jobs I've been working on at the same time is having 1/8th NPT Stainless bosses fitted to the exhaust to be able to fit a Thermocouple. Will add EGT's to the data logger purely for reference. Might as well put them in there while the exhaust and engine is out and accessible.

After months and months of emails back and forward and data sent to Tilton it turns out that Tilton have admitted there is a major manufacturing fault with a large quantity of their proportioning valves. To the point when they bench tested some to send to me they weren't able to send a replacement that actually did what the technical documentation says it should. This is something they're going to be looking into post Covid 19. But for the moment I've got a refund on the valve I purchased in Feb and replaced it with a Willwood valve. When the car is running again I will be collecting some data from these valve and will share it and compare it too,

Mounted the gearbox onto the engine with the S50 (E36 M3) manifolds into the position on the engine. Continued to use the adaptor plates which I manufacture for this conversion as they space the manifolds off the black by 10mm which means they clear the engine webbing and the bell housing.
This photo gives a good view of the exhaust manifold set up into a 2.5" single v band.

Swung the engine and gearbox into the engine bay and mounted it in position.

Started to build up the engine bay around it. I've made a few changes to the oil cooler set up. I've flipped it upside down and mounted it higher up in the kidney grills so it's directly in the air flow rather than being slightly hidden behind the bumper

Spent the day putting the engine bay back together. Nice to take my time with it and tidy up and clean things as it goes back together. It was also time to try the first start on it too. Filled all the usual fluids with oil, water and power steering before leaving the injectors unplugged and cracking the engine over for 30 seconds to get some oil flowing around the engine.
Time for the first start. Engine fired into life after a couple of cracks. Let it build oil pressure for 15 seconds or so then turned it off to check for leaks and top up the fluids.
Ran it again for a further minute afterwards, not enough to get any temp into anything and nothing about 1000rpm for the moment but enough to get the engine full of oil and look for any leaks. So far it seems to be ok, sounds similar to the old engine, will run it again this week when I have the laptop handy and can get the engine for fault codes and the likes and look at the engine data on INPA/ISTA.
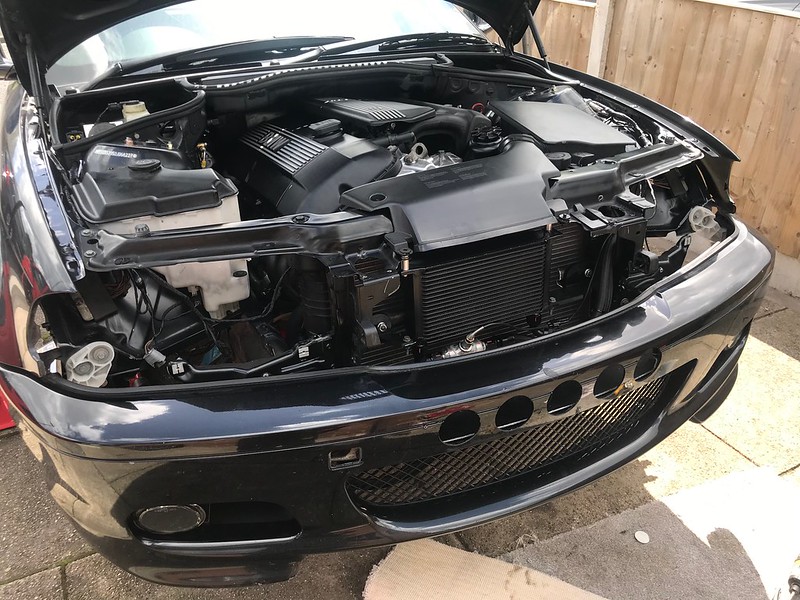
Got another 4 weeks till the car is booked in for running in on the dyno but it gives me time now to check everything over and work through a small list of other jobs on the car. Still feeling pretty apprehensive about the new engine but today was a big step in the right direction. Will hopefully feel more confident with it when it's up and running on the dyno and making some power hopefully.
First job before starting to think about putting the engine in was to get the engine bay cleaned and a few jobs in their tidied up. A good jet wash and degreaser with a scrubbing brush brought off the 17 years of dirt.
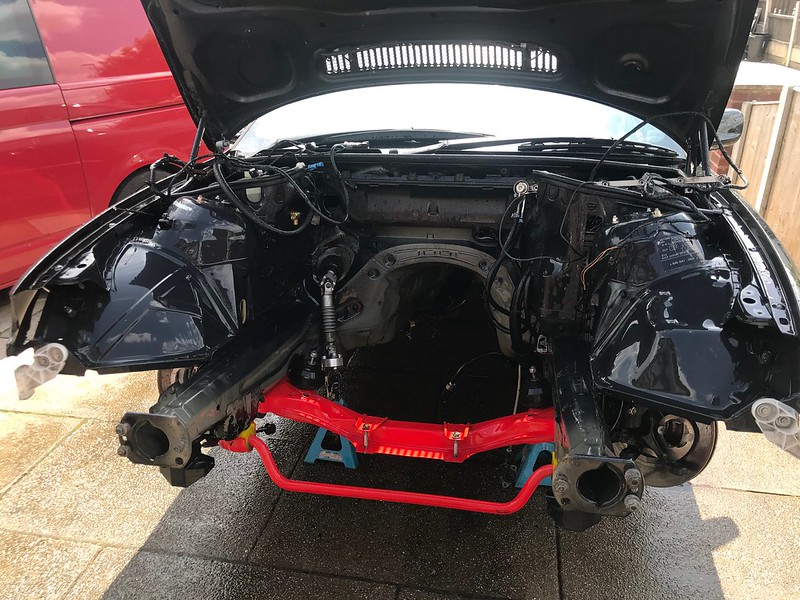
When I did the ABS delete on the car I ran copper wires around the engine bay. This was fine for the function but the appearance of the bent copper line wasn't really in fitting with the rest of the car so decided to get some braided lines made up for the engine bay. Cant really see them unless you point them out which is good really.

I have stripped back some of the wiring loom just to tidy it up and remove some of the excess plugs and the silly plastic box that is part of the BMW loom on these which is unsightly and doesn't fit with the inlet manifold I am using. Retaped up some sections of the loom to removing some of the plastic outer covering.

Baffled sump arrived back from welding. Nicely done, the rivets I put in to hold it together have been replaced with weld now and the 3 different plates have been stitched welded together before welding into the sump with a few small welds.

Finished off the timing of the engine and got the Vanos assembly bolted into postion. Ended up doing this a couple of times making sure the timing was perfect. It was a good job I bought the full kit fo the M54 dual vanos as without it you wouldn't be able to time up these with both cams being variable

Spark plugs, new rocker cover gasket and it was torqued down in the place. Actually starting to look like an engine now.

Once the engine could be lifted into the air again, it's a little awkward with this engine as you need the flywheel on to be able to time up the engine so can't leave it on the engine stand. I have gone back through the bottom end and fitted my ARP Rod bolts as well as the oil pump from my original engine. This time with the replacement oil pump gear and the ARP bolt in the Vac Motorsport shaft wire locked to prevent it from coming undone again in the future.

One finished M54B30 ready to go back into the car. Quite a lot of the parts, sensors and pipes onto the engine while it is nicely accessible on the garage floor.

With the M50 Inlet placed on it.

Other jobs I've been working on at the same time is having 1/8th NPT Stainless bosses fitted to the exhaust to be able to fit a Thermocouple. Will add EGT's to the data logger purely for reference. Might as well put them in there while the exhaust and engine is out and accessible.

After months and months of emails back and forward and data sent to Tilton it turns out that Tilton have admitted there is a major manufacturing fault with a large quantity of their proportioning valves. To the point when they bench tested some to send to me they weren't able to send a replacement that actually did what the technical documentation says it should. This is something they're going to be looking into post Covid 19. But for the moment I've got a refund on the valve I purchased in Feb and replaced it with a Willwood valve. When the car is running again I will be collecting some data from these valve and will share it and compare it too,

Mounted the gearbox onto the engine with the S50 (E36 M3) manifolds into the position on the engine. Continued to use the adaptor plates which I manufacture for this conversion as they space the manifolds off the black by 10mm which means they clear the engine webbing and the bell housing.
This photo gives a good view of the exhaust manifold set up into a 2.5" single v band.

Swung the engine and gearbox into the engine bay and mounted it in position.

Started to build up the engine bay around it. I've made a few changes to the oil cooler set up. I've flipped it upside down and mounted it higher up in the kidney grills so it's directly in the air flow rather than being slightly hidden behind the bumper

Spent the day putting the engine bay back together. Nice to take my time with it and tidy up and clean things as it goes back together. It was also time to try the first start on it too. Filled all the usual fluids with oil, water and power steering before leaving the injectors unplugged and cracking the engine over for 30 seconds to get some oil flowing around the engine.
Time for the first start. Engine fired into life after a couple of cracks. Let it build oil pressure for 15 seconds or so then turned it off to check for leaks and top up the fluids.
Ran it again for a further minute afterwards, not enough to get any temp into anything and nothing about 1000rpm for the moment but enough to get the engine full of oil and look for any leaks. So far it seems to be ok, sounds similar to the old engine, will run it again this week when I have the laptop handy and can get the engine for fault codes and the likes and look at the engine data on INPA/ISTA.
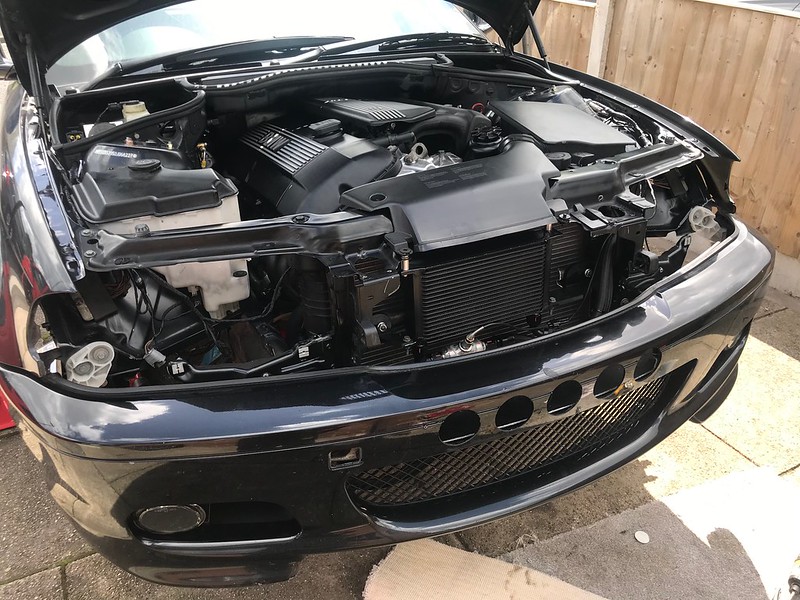
Got another 4 weeks till the car is booked in for running in on the dyno but it gives me time now to check everything over and work through a small list of other jobs on the car. Still feeling pretty apprehensive about the new engine but today was a big step in the right direction. Will hopefully feel more confident with it when it's up and running on the dyno and making some power hopefully.
It's been a month since the last update with not a lot going on until yesterday so I've been saving the update till today.
As usual there is always some 3D printing on the go. This time it's some mounts to hold an air dam under the radiator to close off the large 50 mm gap under there to keep the air going through the radiator rather than under it, and some small mounts to go under the brake line springs on the front to ensure they're solidly located using the factory brake line clips in the chassis mounts.

Test fitted the splitter after giving it a freshen up with a quick sand and a fresh coat of 2k gloss black paint.

When I had the front of the car removed to swap the engine I noticed how rusty and old the bonnet mechanism was starting to go. While it was removed to remove the front slam panel it wasn't going back on so finally time to get the aero catches fitted.
Measure twice and cut once, marking out on masking tape on the bonnet to ensure they're fitted in the right position

Done and dusted. Something I've wanted to have fitted on the car for ages but always let it on the to do list due to cutting holes in the bonnet

Fired up the engine for the first time about 2/3 weeks ago, did the usual checking for leaks, not running the car for more than a few minutes ready for running in on the dyno but when doing some checks, I come across the old fuel pressure issue which has always been an ongoing issue with this car since I removed the standard rail and filter set up for the swirl pot and a M52 rail with an uprated pump.
A few months ago I posted that I had fixed the issue as I had diagnosed it as being a faulted regulator by swapping the rail for a M50 rail, turns out that wasn't to be the case, when running the car I noticed that the fuel pressure was between 62-67psi whenit should be at 51psi (3.5bar)
After a few hours diagnostics with plumbing the mechanical gauge into various points in the system and finally going back to the standard in tank pump we found that the pump was too large for the standard regulator in the standard fuel rail.
Looking back at it's pretty obvious especially when looking at this:
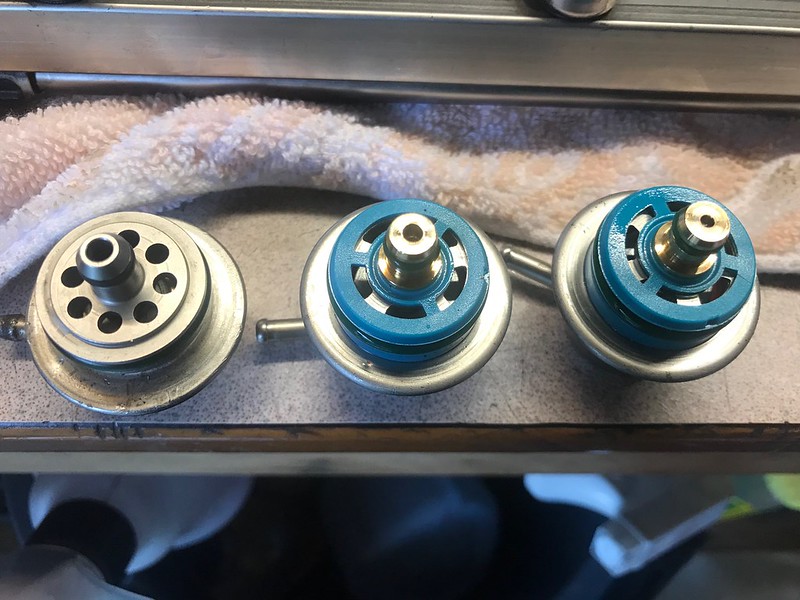
Left is random regulator from a US Spec M50, you can see the bleed off hole in the middle of the regulator is much larger.
The middle regulator is a M52 regulator I have drilled out to give the regulator more flow on the return.
The righ regulator is a stnadard M52 regulator prior to being drilled.
Along with drilling out the regulator I have also changed the fuel pump for a smaller Bosch replacement fuel pump.
With that fitted with the drilled out regulator the fuel pressure is perfectly stable 51psi. Finally!

Monday 21st July - Running in day for the car.
Loaded the car on the trailer and towed it over the EFI Tuning to get Chris to do the running in of the Engine, I would make any changes needed the to map and do some power runs towards the end to see what power it was making.

Strapped the car down on the dyno and Chris set off going through his running in process taking the car through a range of mixed loads and vacuum on the engine. Towards the end of this with more and more load it was becoming apparent that the car was running a little on the lean side at higher loads. We took a break from the running in and I added fuel to various points of the map were required.

The car went on then to do a few full load runs to the original 6800rpm limit and everything was looking really good something like this.
Really happy with how the car revs through the higher rev range and just holds the 260bhp flat to the 6800rpm limit.
The engine and exhaust note has really changes now and sounds a lot more free at higher revs.
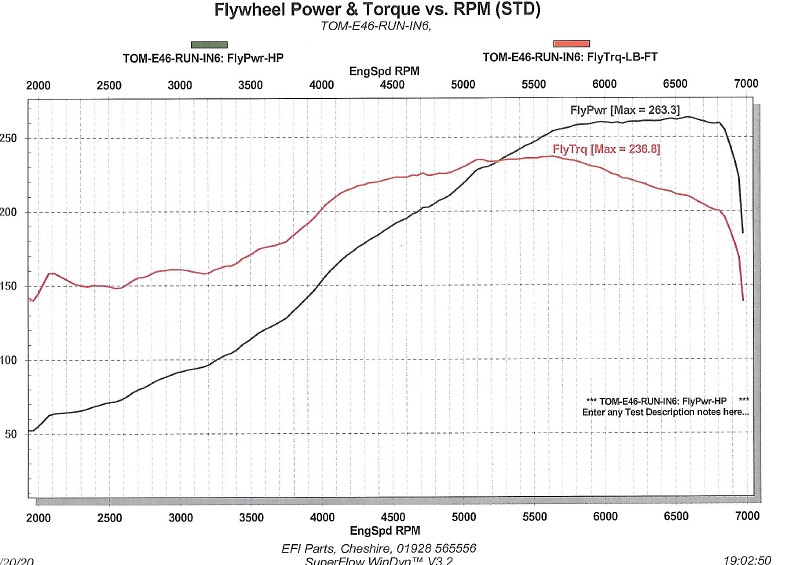
After this we did a few more power runs with a little bit of timing remove around the 5500 rpm area and found a slight increase in torque. We thought there was a little bit of timing pulled in the area so removed a few degrees and lifted the limiter to 7000 rpm and it maintained the 260bhp to 7000rpm.
Absolutely made up with how this engine project had turned out. One thing to consider when looking the the dyno graph is the car is purely a track car and the low down torque below 3500 was never used on circuit. I looked a log of Oulton Park from March this year and I never dropped below 4000rpm with my current final drive which was at Shell in 3rd gear. Will be looking at adding a Super Damper to the engine though in the not too distant future due to how rev happy this new engine is going to be.
There is still plenty of work which could be done with the map to find more mid range as we spent the time with the fueling I didn't get the opportunity to swing the cam timing to see what additional power could be found, there's always something else for another day!
For now I've got some modifications planned for the data logger. Finish off some of the jobs and give it a good clean ready for Snetterton on the 18th Aug and Cadwell on the 27th Aug
As usual there is always some 3D printing on the go. This time it's some mounts to hold an air dam under the radiator to close off the large 50 mm gap under there to keep the air going through the radiator rather than under it, and some small mounts to go under the brake line springs on the front to ensure they're solidly located using the factory brake line clips in the chassis mounts.

Test fitted the splitter after giving it a freshen up with a quick sand and a fresh coat of 2k gloss black paint.

When I had the front of the car removed to swap the engine I noticed how rusty and old the bonnet mechanism was starting to go. While it was removed to remove the front slam panel it wasn't going back on so finally time to get the aero catches fitted.
Measure twice and cut once, marking out on masking tape on the bonnet to ensure they're fitted in the right position

Done and dusted. Something I've wanted to have fitted on the car for ages but always let it on the to do list due to cutting holes in the bonnet

Fired up the engine for the first time about 2/3 weeks ago, did the usual checking for leaks, not running the car for more than a few minutes ready for running in on the dyno but when doing some checks, I come across the old fuel pressure issue which has always been an ongoing issue with this car since I removed the standard rail and filter set up for the swirl pot and a M52 rail with an uprated pump.
A few months ago I posted that I had fixed the issue as I had diagnosed it as being a faulted regulator by swapping the rail for a M50 rail, turns out that wasn't to be the case, when running the car I noticed that the fuel pressure was between 62-67psi whenit should be at 51psi (3.5bar)
After a few hours diagnostics with plumbing the mechanical gauge into various points in the system and finally going back to the standard in tank pump we found that the pump was too large for the standard regulator in the standard fuel rail.
Looking back at it's pretty obvious especially when looking at this:
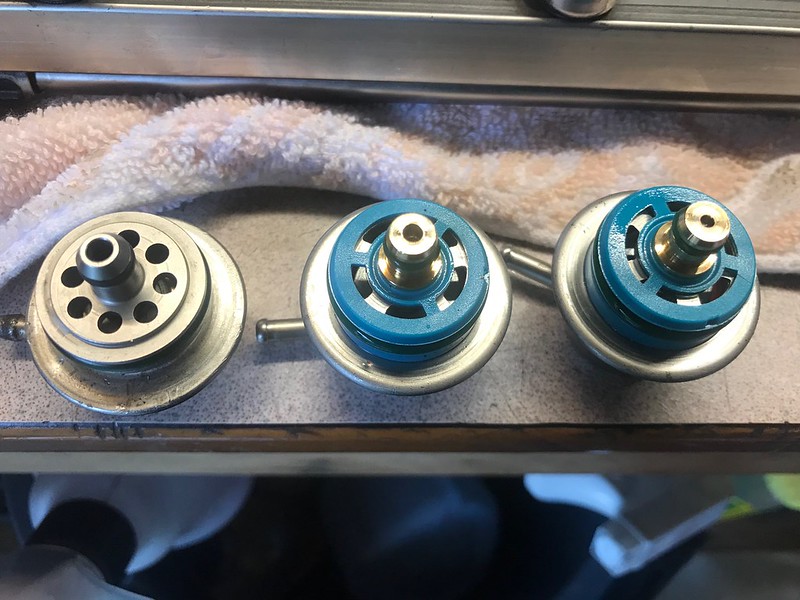
Left is random regulator from a US Spec M50, you can see the bleed off hole in the middle of the regulator is much larger.
The middle regulator is a M52 regulator I have drilled out to give the regulator more flow on the return.
The righ regulator is a stnadard M52 regulator prior to being drilled.
Along with drilling out the regulator I have also changed the fuel pump for a smaller Bosch replacement fuel pump.
With that fitted with the drilled out regulator the fuel pressure is perfectly stable 51psi. Finally!

Monday 21st July - Running in day for the car.
Loaded the car on the trailer and towed it over the EFI Tuning to get Chris to do the running in of the Engine, I would make any changes needed the to map and do some power runs towards the end to see what power it was making.

Strapped the car down on the dyno and Chris set off going through his running in process taking the car through a range of mixed loads and vacuum on the engine. Towards the end of this with more and more load it was becoming apparent that the car was running a little on the lean side at higher loads. We took a break from the running in and I added fuel to various points of the map were required.

The car went on then to do a few full load runs to the original 6800rpm limit and everything was looking really good something like this.
Really happy with how the car revs through the higher rev range and just holds the 260bhp flat to the 6800rpm limit.
The engine and exhaust note has really changes now and sounds a lot more free at higher revs.
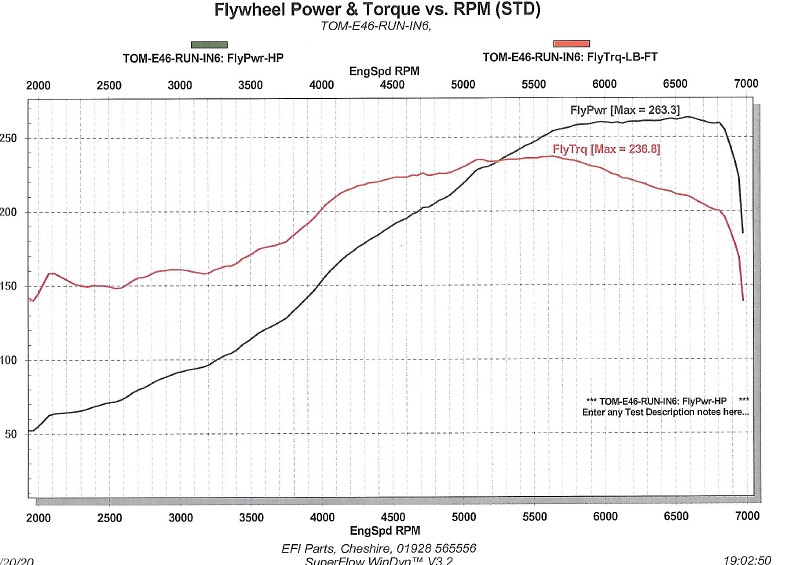
After this we did a few more power runs with a little bit of timing remove around the 5500 rpm area and found a slight increase in torque. We thought there was a little bit of timing pulled in the area so removed a few degrees and lifted the limiter to 7000 rpm and it maintained the 260bhp to 7000rpm.
Absolutely made up with how this engine project had turned out. One thing to consider when looking the the dyno graph is the car is purely a track car and the low down torque below 3500 was never used on circuit. I looked a log of Oulton Park from March this year and I never dropped below 4000rpm with my current final drive which was at Shell in 3rd gear. Will be looking at adding a Super Damper to the engine though in the not too distant future due to how rev happy this new engine is going to be.
There is still plenty of work which could be done with the map to find more mid range as we spent the time with the fueling I didn't get the opportunity to swing the cam timing to see what additional power could be found, there's always something else for another day!
For now I've got some modifications planned for the data logger. Finish off some of the jobs and give it a good clean ready for Snetterton on the 18th Aug and Cadwell on the 27th Aug
Edited by tombate911 on Tuesday 21st July 23:29
eezeh said:
Coming along nicely I think!
One observation, shouldn't the aero catches be fitted turned 180 degrees so that if for whatever reason the latch isn't engaged air can't get under one of the catches and flip it open?
This is something I had a debate about on one of the Track groups on facebook which have a big BMW following. I was using the argument you present. I was going to go down that route myself with the bonnet catches rotated 180 degrees to how I've put them but it brought the body of the catch too far forward into the curvature of the bonnet into the triple skinned section. I could have done them 90 degrees as you say but i'm fully aware of it so will be something I always check before going out on track anyway. Seems to be the common thing that all e46's seems to have them mounted the same way that I have done.One observation, shouldn't the aero catches be fitted turned 180 degrees so that if for whatever reason the latch isn't engaged air can't get under one of the catches and flip it open?
TheDukeGTi said:
I really like the process you've taken with this. Seems like a really well sorted car with improvements across the board. I bet it's a blast to drive.
Thanks! No doubt it will continue to progress after it gets some use towards the end of the year. Another month brings another update, this time with some interesting developments after the Covid restrictions are lifting.
Brakes
We'll start with a brake update. I mentioned in the last post that I had returned the faulty Tilton valve after a refund after they finally admitted it was a problem and they didn't have an answer for it.

When the car had be ran in on the dyno I could then spend some time messing with it on the drive and leave it idling without worrying about damaging the new engine, I managed to extract a couple of brake presses from the logger in 3 positions on the Willwood valve. Should note the 3 level locations where random and not equally spaced.
The graph shows the effects on the line pressure in the front and rear circuits. Happy to actually see the valve working correctly and giving me a range of adjustment.

For reference the faulty Tilton product data.

Carrying on with the logging theme, a friend of mine has developed this board which he will be selling shortly after some testing on the car. it's a 10 channel analogue to CANBUS board. I have now integrated this into the wiring of the car so that it takes in:
Front brake pressure
Rear brake pressure
Fuel rail pressure
Swirl pot pressure
Diff temp.
This information then is taken from the BMW Canbus network by the logger as well as the LCD screen. Great little board which has tidied up some of the wiring meaning that the analogue sensors no longer need to go to the logger and are terminated under the dash now.

More detail on the logger later.
Revisiting the dyno plot
So the car produced the following at EFI after running in the new engine. On the face of it the figures look good...

However after getting home from the dyno, spending an hour or two thinking and looking at the dyno, I went out to the car, had a look at the error codes and the live data in inpa and my suspicion was true. Exhaust cam sensor fault and the vanos stuck in it's default position, this happens to be where the cams sit above 6000rpm perfect for making peak power but not for mid range torque. Long and short of it is peak power will remain the same but the engine is producing a lot more mid range torque than on the print out with the vanos working correctly. Will try and get back on the dyno at some point to get a proper look at what the engine is capable of making torque wise. All sorted with swapping the sensor over to the known good one from my old engine.
After the running in session I dropped the oil and replaced it with some better quality shell oil for the new engine, and the car was ready for it's first day out on circuit with it's new engine.

Snetterton
I had originally planned to get the car ready for a Cadwell Park double header track day in August but after having one of the days cancelled due to racing I used the credit to book onto Snetterton. Long 4 hour drive for me to get to Snetterton so we travelled down the day before and stayed in a hotel 15 minutes from the circuit.
E46 unloaded off the trailer ready to go out for sighting laps, I had it noise tested first thing and it's louder again, this time 102db static. It appears that the silencers are getting more and more blown out as it gets louder every day. Something I will probably have to address in the near future.

Spent the first session taking it a little easier than usual. Getting used to driving the car again, keeping a close eye on the engine temps, oil pressure and fuel pressure. I kept the ear plugs out for the first few sessions so I could listen to the car and get a feel for it after being rebuilt.
I had nothing to worry about, the car was running flawlessly. Only thing I had to do was set the tyres pressures at the end of the 1st and 2nd sessions.
Quick check of the logs from the data logger shows a couple of things, first of all the new Canbus board logging the sensors was working perfectly.

Since messing with the fuel system 12 months ago fitting the return rail and swirl pot I have been plagued with issues with low fuel pressure, too much fuel pressure flow, running out of fuel on track with a 1/3 of a tank in the wrong side of the tank.
But finally I feel like I've got somewhere with this. Perfectly solid 53-55psi fuel pressure at idle and on track, especially at Snetterton with some fast corners, the new smaller pump and swirl pot working perfectly.
Swirl pot pressure drops to 0 during full load when the engine is consuming the max amount of fuel and in a couple of corners where the in tank pump isn't able to pick up fuel, which was the main reason for fitting the swirl pot.
Coolant and oil temps maxing at around 100-103 degrees. Water temp is a little warmer than i'd like so i'm going to experiment with a couple of ideas at Cadwell Park next week.
Logging brake pressures in the front and rear circuit gave a good indication of how the proportioning valve was working. On circuit it I moved it around a little, locking up the fronts, then locking up the rear and dialing in a nice balanced point were the car felt great under braking. Something I've been chasing for years with this car, finally felt like the brakes have clicked and I was able to use them properly. I've got the RC6 front pads in with the RC5 rears now.
The line up of cars...
BMW E36 - ITB Stroker ~285bhp
BMW E46 - Schrick Cams, M50 inlet - 265bhp
Clio Mk1 - 182 Engine with 421 cams on ITB's - 215bhp


The track day went perfectly. Couldn't have asked for a better day on track to be honest. The car also ran flawlessly and the new engine has transformed the car. It's much more free revving the eager. Now it will happily shift at 6700rpm, previously peak power was at 5900 and it dropped off rapidly. The new engine with a shorter final drive I fitted for Oulton park is a perfect combination. Finally felt like everything came together perfectly and worked how it was designed to this week and it was really confidence inspiring to drive the car knowing the brakes were working correctly and all the niggles like the fuel pressure was working great, was nice to be able to monitor this on the LCD screen including all the engine temps, brake pressures and live brake bias %, fuel pressures etc.
All set and ready to go again at Cadwell Park next week with Track Obsession.
Couple of videos from the day...
Couple of afternoon laps.
https://youtu.be/RLrbVK-dtRQ
Being followed by Foxy in the BMW E36
https://youtu.be/qraFiEGHVio
Brakes
We'll start with a brake update. I mentioned in the last post that I had returned the faulty Tilton valve after a refund after they finally admitted it was a problem and they didn't have an answer for it.

When the car had be ran in on the dyno I could then spend some time messing with it on the drive and leave it idling without worrying about damaging the new engine, I managed to extract a couple of brake presses from the logger in 3 positions on the Willwood valve. Should note the 3 level locations where random and not equally spaced.
The graph shows the effects on the line pressure in the front and rear circuits. Happy to actually see the valve working correctly and giving me a range of adjustment.

For reference the faulty Tilton product data.

Carrying on with the logging theme, a friend of mine has developed this board which he will be selling shortly after some testing on the car. it's a 10 channel analogue to CANBUS board. I have now integrated this into the wiring of the car so that it takes in:
Front brake pressure
Rear brake pressure
Fuel rail pressure
Swirl pot pressure
Diff temp.
This information then is taken from the BMW Canbus network by the logger as well as the LCD screen. Great little board which has tidied up some of the wiring meaning that the analogue sensors no longer need to go to the logger and are terminated under the dash now.

More detail on the logger later.
Revisiting the dyno plot
So the car produced the following at EFI after running in the new engine. On the face of it the figures look good...

However after getting home from the dyno, spending an hour or two thinking and looking at the dyno, I went out to the car, had a look at the error codes and the live data in inpa and my suspicion was true. Exhaust cam sensor fault and the vanos stuck in it's default position, this happens to be where the cams sit above 6000rpm perfect for making peak power but not for mid range torque. Long and short of it is peak power will remain the same but the engine is producing a lot more mid range torque than on the print out with the vanos working correctly. Will try and get back on the dyno at some point to get a proper look at what the engine is capable of making torque wise. All sorted with swapping the sensor over to the known good one from my old engine.
After the running in session I dropped the oil and replaced it with some better quality shell oil for the new engine, and the car was ready for it's first day out on circuit with it's new engine.

Snetterton
I had originally planned to get the car ready for a Cadwell Park double header track day in August but after having one of the days cancelled due to racing I used the credit to book onto Snetterton. Long 4 hour drive for me to get to Snetterton so we travelled down the day before and stayed in a hotel 15 minutes from the circuit.
E46 unloaded off the trailer ready to go out for sighting laps, I had it noise tested first thing and it's louder again, this time 102db static. It appears that the silencers are getting more and more blown out as it gets louder every day. Something I will probably have to address in the near future.

Spent the first session taking it a little easier than usual. Getting used to driving the car again, keeping a close eye on the engine temps, oil pressure and fuel pressure. I kept the ear plugs out for the first few sessions so I could listen to the car and get a feel for it after being rebuilt.
I had nothing to worry about, the car was running flawlessly. Only thing I had to do was set the tyres pressures at the end of the 1st and 2nd sessions.
Quick check of the logs from the data logger shows a couple of things, first of all the new Canbus board logging the sensors was working perfectly.

Since messing with the fuel system 12 months ago fitting the return rail and swirl pot I have been plagued with issues with low fuel pressure, too much fuel pressure flow, running out of fuel on track with a 1/3 of a tank in the wrong side of the tank.
But finally I feel like I've got somewhere with this. Perfectly solid 53-55psi fuel pressure at idle and on track, especially at Snetterton with some fast corners, the new smaller pump and swirl pot working perfectly.
Swirl pot pressure drops to 0 during full load when the engine is consuming the max amount of fuel and in a couple of corners where the in tank pump isn't able to pick up fuel, which was the main reason for fitting the swirl pot.
Coolant and oil temps maxing at around 100-103 degrees. Water temp is a little warmer than i'd like so i'm going to experiment with a couple of ideas at Cadwell Park next week.
Logging brake pressures in the front and rear circuit gave a good indication of how the proportioning valve was working. On circuit it I moved it around a little, locking up the fronts, then locking up the rear and dialing in a nice balanced point were the car felt great under braking. Something I've been chasing for years with this car, finally felt like the brakes have clicked and I was able to use them properly. I've got the RC6 front pads in with the RC5 rears now.
The line up of cars...
BMW E36 - ITB Stroker ~285bhp
BMW E46 - Schrick Cams, M50 inlet - 265bhp
Clio Mk1 - 182 Engine with 421 cams on ITB's - 215bhp


The track day went perfectly. Couldn't have asked for a better day on track to be honest. The car also ran flawlessly and the new engine has transformed the car. It's much more free revving the eager. Now it will happily shift at 6700rpm, previously peak power was at 5900 and it dropped off rapidly. The new engine with a shorter final drive I fitted for Oulton park is a perfect combination. Finally felt like everything came together perfectly and worked how it was designed to this week and it was really confidence inspiring to drive the car knowing the brakes were working correctly and all the niggles like the fuel pressure was working great, was nice to be able to monitor this on the LCD screen including all the engine temps, brake pressures and live brake bias %, fuel pressures etc.
All set and ready to go again at Cadwell Park next week with Track Obsession.
Couple of videos from the day...
Couple of afternoon laps.
https://youtu.be/RLrbVK-dtRQ
Being followed by Foxy in the BMW E36
https://youtu.be/qraFiEGHVio
Edited by tombate911 on Saturday 22 August 22:00
clarkson22 said:
Excellent build mate , car sounds awesome 
Thank you! It sounds totally different with the new engine. Not quite sure if the camera picks that up though,
Here is a video from the BMW E36 Following me
https://youtu.be/3zeQ9qTUIdk

Sf_Manta said:
Does sound rather rooty on the exhaust , hopefully mine should sound similar when i get the new system put in with M3 / Eisenmann components 
Did notice though your car seems rather short geared? what's the final drive ratio and guessing you've still got the 5 speed in it.
Yeah I would imagine that a decent amount of the noise comes from the M3 S50 exhaust manifolds. 
Did notice though your car seems rather short geared? what's the final drive ratio and guessing you've still got the 5 speed in it.
Back in March I went to a 3.73 FD. It didn't really work with the old engine set up as I was changing gear at 6000rpm as the power fell of to rapidly above that. However with the new engine they really do work together. I much prefer using 3/4/5. The 3.38 was all 3/4 gears around my usual circuits with probably needing to drop to 2nd at the hair pin at Cadwell which I was never a fan of in that braking area.
Back to Cadwell Park on Thursday so will be interesting to see how I get on there with the shorter FD and Engine. Probably take a bit of adjusting to get used to. But the shorter FD has balanced out now with changing gears 700rpm later.
Cadwell Park Aug 2020
Another week another update, this time it's another track day in another corner of the country.
Interesting how many people read through this thread on a weekly basis then message me privately on social media or private message. Always interested to hear comments and developments. The more discussion the better, always good to hear what other people would do in similar situations.
Luckily the car was faultless at Snetterton the previous week so the car only needed a wash, some fuel and clean SD cards putting in the cameras and logger, with that done it was loaded back onto the trailer ready to head over to Cadwell Park with Track Obsession. As we always try to do we set off over to Louth the day before saying in a hotel 10 minutes from the circuit.
Cadwell was set to be a great day with a fantastic group of cars going from our track day friendship group.
BMW's - E46 330 - E36 ITB - E36 Turbo - E36 S54 - E36 328
Renault - Clio 197 - 182 - MK1 ITB
Along with a wide range of other friends from track days coming along with their cars was making for a great day.


The morning got off to a nice smooth start, it was great to hop back into the driving seat off the back of Snetterton, the car felt pretty good straight off the bat and only required a slight adjustment in suspension settings on the rear. I went back to the known good set up I ran at Cadwell last year.
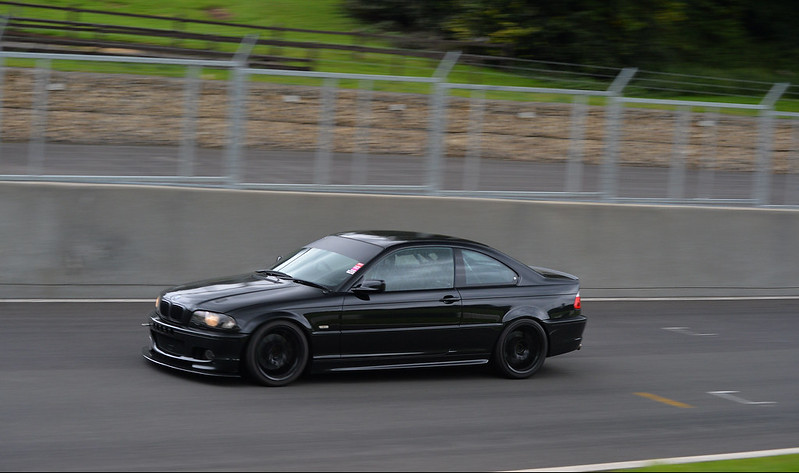

Spent the day lapping the car, very little disruption to time on circuit with only a couple of red flags through the day. I did however start to get a louder and louder grumbling noise from one of the wheel bearings which was getting louder and louder as the day went on. Between sessions I had the car on the axle stands and checked over all corners of the car and gave it a quick bolt check. Nothing was found and all wheels were solid, I put it down to a dry wheel bearing that was starting to wear out and monitored it as the day went on.
Had some fantastic sessions out on track with a number of different cars. Have a look at the end of the post for some videos.
If you wondered what it looks like in the rear view

Weighing
So at the beginning of 2019 I weighed the car at Oulton Park and it came in at 1300kg. During that summer the car went on a little diet when I changed the battery, wiring, heater matrix for a heater screen and repainted the car. I weighed the parts as they were removed and offset that against anything that was refitted or replaced but I wanted to have a proper note of what the car weighed, especially knowing that it had just made 265bhp on the new engine.
I took the car over to the weigh bridge and got it on there, really happy to find out it weighed in at 1250kg, pretty good weight for an E46 considering it still had glass all around and I haven't cut out any of the doors or boot... yet!.
BMW's post weighing

I managed a couple of good afternoon sessions and was finding a good flow on the circuit. Cadwell never fails to impress with the circuit layout and elevation changes.
However just before the end of the day around 4pm the grumbling noise from the wheel bearing turned into a loud crunch and clunking as the wheel went around, this happened at the end of the Park Straight, I turned into the corner and it didn't turn in with the usual precision so let the car run wide onto the grass and brought the car back to the pits.

It was easy to pin point the location of the grumbling now as the front wheel was wobbling ~30 side to side and top and bottom. That was the end of the day for me but really happy with how the car performed and the wheel bearing lasted through the day without causing disruption to the day or much lost time on circuit. Nice easy fit and we'll be out again.
Removed the wheel bearing and this is the state of the damage, one broken bearing race, multiple cracked ball bearings and the ball bearing cage in a number of pieces. This was a higher quality bearing from FAG as some of you may remember me having a number of bearing issues on the front left when I first built the car.

Data from a 25 minute session on track

-Good to see nice and solid coolant and oil temps hitting 105 and 97 degrees,
-Fuel pressure holding nice and solid at 3.5 bar, the little bit of pressure in the swirl pot drops slightly at high loads as the fuel is being consumed by the engine and the in tank pump is replacing the fuel in the pot. Fuel pressure at the rail is maintaining perfectly with only 15L of fuel in the main tank, previously the car has cut out completely at Cadwell with less than 20L in it. Proves that the swirl pot is the perfect solution.
-Diff temp is being logged in raw ADC readings from the Analog to Canbus board, the 245adc equates to 118 degrees for the diff oil. You can see the longer I stay out the hotter and hotter the diff gets. This is something I'm going to log on a couple of track days and may need to address, especially with planned changes.
Tyres
So since getting into track days back in probably 2015 I have always ran a Federal RSR and it's a great tyre that I've always said give great value for money in terms of grip vs wear vs cost. I have ran multiple sets of them on the Clio and the BMW. Over the past two years with the BMW I have stuck with them as I kept saying I would until I felt like I was driving towards the limit of the tyre. In the past it's been my driving which has held the car back. Obviously with more practise and smoother driving I could get more from the RSR's but I want to experiment with a better tyre choice so i'm going to look at my options and consider something with a bit more grip and a stiffer sidewall. At the moment I am leaning towards the Nankang AR1.
Videos
Cadwell Highlights
https://youtu.be/_NBAs_SDOEo
Cadwell Following MK1 Clio ITB and E36.
https://youtu.be/O2wrUtuPGR0
Laser Cutting
Had some more laser cut items made for M50 Manifold conversions for NA and Turbo
M54 throttle body adaptor for mounting on M50 Manifold

Porting adaptors between M50 manfiold ports and M54 head.

Another week another update, this time it's another track day in another corner of the country.
Interesting how many people read through this thread on a weekly basis then message me privately on social media or private message. Always interested to hear comments and developments. The more discussion the better, always good to hear what other people would do in similar situations.
Luckily the car was faultless at Snetterton the previous week so the car only needed a wash, some fuel and clean SD cards putting in the cameras and logger, with that done it was loaded back onto the trailer ready to head over to Cadwell Park with Track Obsession. As we always try to do we set off over to Louth the day before saying in a hotel 10 minutes from the circuit.
Cadwell was set to be a great day with a fantastic group of cars going from our track day friendship group.
BMW's - E46 330 - E36 ITB - E36 Turbo - E36 S54 - E36 328
Renault - Clio 197 - 182 - MK1 ITB
Along with a wide range of other friends from track days coming along with their cars was making for a great day.


The morning got off to a nice smooth start, it was great to hop back into the driving seat off the back of Snetterton, the car felt pretty good straight off the bat and only required a slight adjustment in suspension settings on the rear. I went back to the known good set up I ran at Cadwell last year.
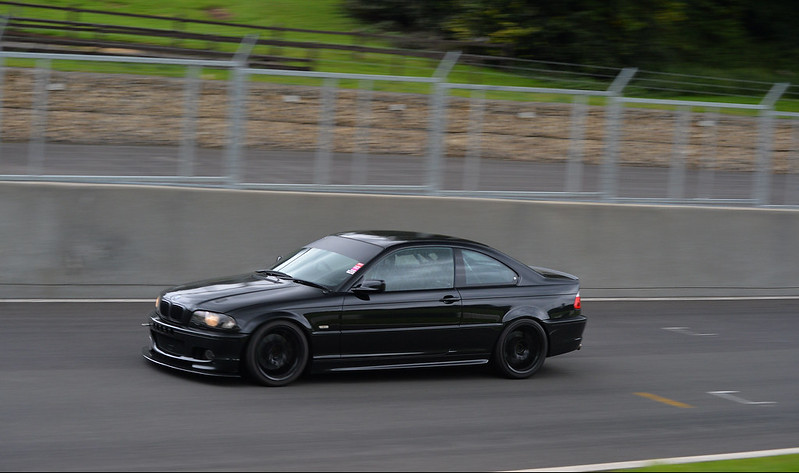

Spent the day lapping the car, very little disruption to time on circuit with only a couple of red flags through the day. I did however start to get a louder and louder grumbling noise from one of the wheel bearings which was getting louder and louder as the day went on. Between sessions I had the car on the axle stands and checked over all corners of the car and gave it a quick bolt check. Nothing was found and all wheels were solid, I put it down to a dry wheel bearing that was starting to wear out and monitored it as the day went on.
Had some fantastic sessions out on track with a number of different cars. Have a look at the end of the post for some videos.
If you wondered what it looks like in the rear view

Weighing
So at the beginning of 2019 I weighed the car at Oulton Park and it came in at 1300kg. During that summer the car went on a little diet when I changed the battery, wiring, heater matrix for a heater screen and repainted the car. I weighed the parts as they were removed and offset that against anything that was refitted or replaced but I wanted to have a proper note of what the car weighed, especially knowing that it had just made 265bhp on the new engine.
I took the car over to the weigh bridge and got it on there, really happy to find out it weighed in at 1250kg, pretty good weight for an E46 considering it still had glass all around and I haven't cut out any of the doors or boot... yet!.
BMW's post weighing

I managed a couple of good afternoon sessions and was finding a good flow on the circuit. Cadwell never fails to impress with the circuit layout and elevation changes.
However just before the end of the day around 4pm the grumbling noise from the wheel bearing turned into a loud crunch and clunking as the wheel went around, this happened at the end of the Park Straight, I turned into the corner and it didn't turn in with the usual precision so let the car run wide onto the grass and brought the car back to the pits.

It was easy to pin point the location of the grumbling now as the front wheel was wobbling ~30 side to side and top and bottom. That was the end of the day for me but really happy with how the car performed and the wheel bearing lasted through the day without causing disruption to the day or much lost time on circuit. Nice easy fit and we'll be out again.
Removed the wheel bearing and this is the state of the damage, one broken bearing race, multiple cracked ball bearings and the ball bearing cage in a number of pieces. This was a higher quality bearing from FAG as some of you may remember me having a number of bearing issues on the front left when I first built the car.

Data from a 25 minute session on track

-Good to see nice and solid coolant and oil temps hitting 105 and 97 degrees,
-Fuel pressure holding nice and solid at 3.5 bar, the little bit of pressure in the swirl pot drops slightly at high loads as the fuel is being consumed by the engine and the in tank pump is replacing the fuel in the pot. Fuel pressure at the rail is maintaining perfectly with only 15L of fuel in the main tank, previously the car has cut out completely at Cadwell with less than 20L in it. Proves that the swirl pot is the perfect solution.
-Diff temp is being logged in raw ADC readings from the Analog to Canbus board, the 245adc equates to 118 degrees for the diff oil. You can see the longer I stay out the hotter and hotter the diff gets. This is something I'm going to log on a couple of track days and may need to address, especially with planned changes.
Tyres
So since getting into track days back in probably 2015 I have always ran a Federal RSR and it's a great tyre that I've always said give great value for money in terms of grip vs wear vs cost. I have ran multiple sets of them on the Clio and the BMW. Over the past two years with the BMW I have stuck with them as I kept saying I would until I felt like I was driving towards the limit of the tyre. In the past it's been my driving which has held the car back. Obviously with more practise and smoother driving I could get more from the RSR's but I want to experiment with a better tyre choice so i'm going to look at my options and consider something with a bit more grip and a stiffer sidewall. At the moment I am leaning towards the Nankang AR1.
Videos
Cadwell Highlights
https://youtu.be/_NBAs_SDOEo
Cadwell Following MK1 Clio ITB and E36.
https://youtu.be/O2wrUtuPGR0
Laser Cutting
Had some more laser cut items made for M50 Manifold conversions for NA and Turbo
M54 throttle body adaptor for mounting on M50 Manifold

Porting adaptors between M50 manfiold ports and M54 head.

Edited by tombate911 on Sunday 30th August 21:16
After such a busy period of track days in the summer, attending Anglesey to help friends run their cars, taking the BMW down to Snetterton for it's first run out with the new engine and then following closely the trip over the Cadwell Park, I've not touched the car for a month until this weekend. Sometimes it's nice to have a little break away from things and pick it up again.
In the time I wasn't working on the car I had been thinking about the tyre options more closely.
I've been backwards and forwards with tyre options, sticking with the RSR's was one consideration but I wanted to try something with more grip from a higher level tyre after doing passenger laps at Snetterton and Cadwell in similar cars with much better tyres with the likes of the AR1's and DZ03's.
Second hand slicks were another options which seems really cost effective but finding the tyres in a size that I can fit under the E46 arches wasn't easiest as I wanted to move to a tyre that I can get easily. I didn't want to move to a slick and then 6 months later not be able to get the same tyres. Also some of the 245 width tyres I was looking at were from series which aren't running anymore so basically old stock with probably old dates on.
The final choice was to move to a AR1 or similar, I run a bit of a silly wheel really which is an 18" 9J fitted with 255/35/18, not the cheapest size of tyres, running 17" would be slightly cheaper but requires a second set of wheels as my other set are a staggered 18".I have considered buying another set of a Team Dynamics in 17 to be able to run 17" tyres as they're slightly cheaper in the same width. The other options to the AR1's are the DZ03's which are a lot more expensive in the 255/35/18 so I opted for what seemed to be the best option for me which is Nankang AR1 in a 255/35/18, admittedly they are £200 a corner. but they're brand new tyres which obviously haven't been abused or left on the shelf in someones unit for years after being used for a testing session on a race weekend in 2017.
In my opinion with tyres being your only contact with the tarmac it's better not to cut corners as it'll only ruin future track days, I've always tried to do everything to the best of my ability when building this car so the trend continues.

Got the tyres fitted to the rims on Sunday and did a test fit as the AR1's are a slightly different profile. Front clearance is about the same the RSR, I will thrown in a couple of 2mm spacers in the track day box just in case there are any issues on the front
The rear was a little different as the profile is a little squarer, I had to get the arch roller out and pull the rears out a further 3-4mm so the tyre could tuck under the arch under compression. The RSR's used to catch ever so slightly under some compressions but only enough to catch the writing on the tyres so this was a job that needed addressing anyway.

Final job on the list for the weekend was to fix the super charger noise from the engine bay which started at Cadwell Park. On the track day I identified it as the inlet gasket between the adaptor plate and the head. This is a gasket I laser cut at work when I first fitted the M50 inlet manifold, since then it has been reused, on and off many times, not something I would ever do with a critical gasket but I've reused this one a few too many times. Laser cut a new one in work last week from some gasket material I had left over in the garage and replaced. So much easier removing the M50 inlet. Only tool 30mins to do the swap and have the car built back up and running again.

Short and sweet update. There may be a few more things I'll have a look at before the next track days
26th October at Anglesey
21st November at Oulton Park.
In the time I wasn't working on the car I had been thinking about the tyre options more closely.
I've been backwards and forwards with tyre options, sticking with the RSR's was one consideration but I wanted to try something with more grip from a higher level tyre after doing passenger laps at Snetterton and Cadwell in similar cars with much better tyres with the likes of the AR1's and DZ03's.
Second hand slicks were another options which seems really cost effective but finding the tyres in a size that I can fit under the E46 arches wasn't easiest as I wanted to move to a tyre that I can get easily. I didn't want to move to a slick and then 6 months later not be able to get the same tyres. Also some of the 245 width tyres I was looking at were from series which aren't running anymore so basically old stock with probably old dates on.
The final choice was to move to a AR1 or similar, I run a bit of a silly wheel really which is an 18" 9J fitted with 255/35/18, not the cheapest size of tyres, running 17" would be slightly cheaper but requires a second set of wheels as my other set are a staggered 18".I have considered buying another set of a Team Dynamics in 17 to be able to run 17" tyres as they're slightly cheaper in the same width. The other options to the AR1's are the DZ03's which are a lot more expensive in the 255/35/18 so I opted for what seemed to be the best option for me which is Nankang AR1 in a 255/35/18, admittedly they are £200 a corner. but they're brand new tyres which obviously haven't been abused or left on the shelf in someones unit for years after being used for a testing session on a race weekend in 2017.
In my opinion with tyres being your only contact with the tarmac it's better not to cut corners as it'll only ruin future track days, I've always tried to do everything to the best of my ability when building this car so the trend continues.

Got the tyres fitted to the rims on Sunday and did a test fit as the AR1's are a slightly different profile. Front clearance is about the same the RSR, I will thrown in a couple of 2mm spacers in the track day box just in case there are any issues on the front
The rear was a little different as the profile is a little squarer, I had to get the arch roller out and pull the rears out a further 3-4mm so the tyre could tuck under the arch under compression. The RSR's used to catch ever so slightly under some compressions but only enough to catch the writing on the tyres so this was a job that needed addressing anyway.

Final job on the list for the weekend was to fix the super charger noise from the engine bay which started at Cadwell Park. On the track day I identified it as the inlet gasket between the adaptor plate and the head. This is a gasket I laser cut at work when I first fitted the M50 inlet manifold, since then it has been reused, on and off many times, not something I would ever do with a critical gasket but I've reused this one a few too many times. Laser cut a new one in work last week from some gasket material I had left over in the garage and replaced. So much easier removing the M50 inlet. Only tool 30mins to do the swap and have the car built back up and running again.

Short and sweet update. There may be a few more things I'll have a look at before the next track days
26th October at Anglesey
21st November at Oulton Park.
Post lock down #2 Oulton Park
ECU Adjustments.
Idle control
Spent a little bit of the lock down learning more about the MS43 standard ECU despite the long term plan is to replace it with standalone. The main reason behind it was since fitting the new engine with bigger cams the way the idle was mapped to use the throttle body rather than the idle control valve which has been removed now the engine was not able to control it's own idle and was stuggling at 600rpm, I had tried to nudge the idle up with some timing but the throttle body wasn't opening enough at idle. After doing some research into how the idle duty cycle is calculated and looking what values were put into the idle contro maps when I deleted the ECU I was able to rescale a couple of them to get more throttle opening at a given idle control duty cycle and set the required idle to 1000rpm and it idles perfectly now at 1000rpm even with the headed screen on which turns out was perfect for the next track day.
Coolant temp
I also looked at how the coolant temps were controlled in the ECU and noticed there were two additional set points and thresholds in the ECU for the electronic thermostat control.
The first one being a minimum oil temp, the oil has to get to this minimum temperature before the electronic thermostat starts to target coolant temps set by a 3D map. This was orignally set to 105 degrees, Funnily enough the exact temperature the engine was holding steady for 5 back to back laps at Cadwell within a degree.
The second was a coolant set point used until the oil temp reached the set point below.
With this new knowledge I pulled the oil temp minimum to 95 degrees and set the coolant set point to 90 degrees.
Tested it at Oulton Park yesterday and look at the consistent oil and coolant temps. More track days especially in warmer temperatures will tell how stable it stays but it's an interesting find, something I had overlooked in the past.

To the Track Day
Track days under Covid restrictions are a bit different at the moment without the passengers and the group of friends it usually brings with it, this one as well was forecast a very wet start to the day but everyone was just happy to get out in their cars and get some miles in on track before the end of the year.


In the morning the track was very wet, the focus was trying to drive as smooth as possible and focus on putting together some consistent laps.
In these wet conditions the heated screen in the car was a fantastic addition. It was fitted last summer and I've rarely had a chance to use it, only on the odd cold morning but yesterday It was on while on circuit all morning keeping visibility perfectly clear, definitely a worthwhile upgrade.
https://youtu.be/nqiZXT8HR0A
After lunch I went out to find a dry line had appeared in the 20 minute prior to lunch and an hours sun on the track during lunch time had really made an effect to dry the circuit, I was straight back into the pits to get the new AR1's fitted to the car and clicked the dampers up a couple of clicks, still left it reasonably soft as some sections of the track were still wet and wanted to adjust to the new tyres. The first lap was a very slow with brand new tyres on which hadn't been scrubbed in, it started with spinning the rear wheels half the length of the exit from the pit lane but after a slow lap to get them scrubbed in and get a little bit of temperature into them it was great to be back out on a drying track with semi slick tyres on again. In a nut shell first impressions of the tyres are really good, feel really positive on turn in and they really do grip well even in the dryline/damp conditions. Look forward to getting used to them further next year on a dry circuit.
Here's a video from one of the afternoon sessions. Once again the new engine ran flawlessly and has totally changed the driving experience of the car. Combined with the shorter FD I fitted earlier in the year it works really well now were in March the 3.73 final drive was too short for the old engine.
https://youtu.be/7syOeHLKA5U
I do normally have more video footage but I was using this track day to experiment with in car cameras,which went really well during the morning session but during one of the afternoon sessions the camera turned it's self off 7 minutes into the sessions so I don't have as much dry running footage as usual.

To sum it all up it was fantastic day on circuit for a winter track day. The last two sessions of the day really made it worth while all the effort to get the car out on circuit in the middle of winter. I do have a short list of things to mess with over the winter period to make sure the car is ready for the start of next year, most of it just being small bits of maintenance, hopefully march will be the next time I get out on track again.
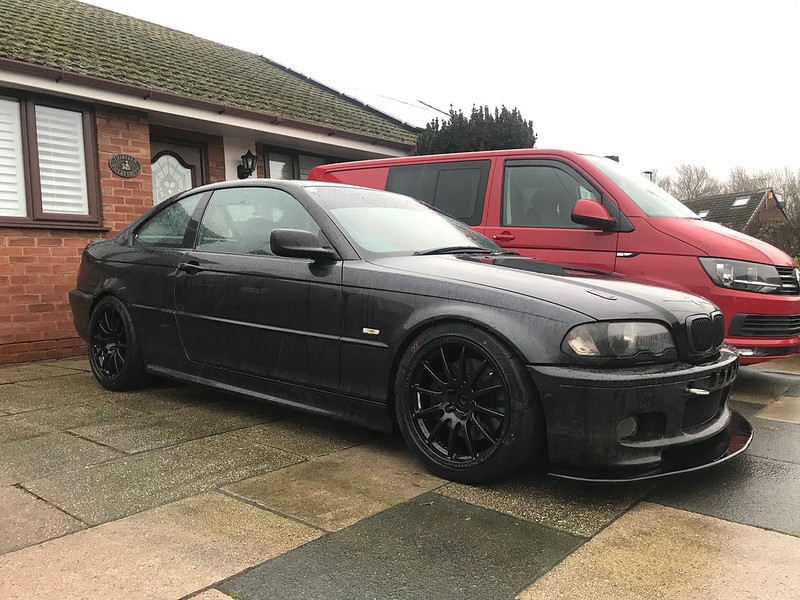
ECU Adjustments.
Idle control
Spent a little bit of the lock down learning more about the MS43 standard ECU despite the long term plan is to replace it with standalone. The main reason behind it was since fitting the new engine with bigger cams the way the idle was mapped to use the throttle body rather than the idle control valve which has been removed now the engine was not able to control it's own idle and was stuggling at 600rpm, I had tried to nudge the idle up with some timing but the throttle body wasn't opening enough at idle. After doing some research into how the idle duty cycle is calculated and looking what values were put into the idle contro maps when I deleted the ECU I was able to rescale a couple of them to get more throttle opening at a given idle control duty cycle and set the required idle to 1000rpm and it idles perfectly now at 1000rpm even with the headed screen on which turns out was perfect for the next track day.
Coolant temp
I also looked at how the coolant temps were controlled in the ECU and noticed there were two additional set points and thresholds in the ECU for the electronic thermostat control.
The first one being a minimum oil temp, the oil has to get to this minimum temperature before the electronic thermostat starts to target coolant temps set by a 3D map. This was orignally set to 105 degrees, Funnily enough the exact temperature the engine was holding steady for 5 back to back laps at Cadwell within a degree.
The second was a coolant set point used until the oil temp reached the set point below.
With this new knowledge I pulled the oil temp minimum to 95 degrees and set the coolant set point to 90 degrees.
Tested it at Oulton Park yesterday and look at the consistent oil and coolant temps. More track days especially in warmer temperatures will tell how stable it stays but it's an interesting find, something I had overlooked in the past.

To the Track Day
Track days under Covid restrictions are a bit different at the moment without the passengers and the group of friends it usually brings with it, this one as well was forecast a very wet start to the day but everyone was just happy to get out in their cars and get some miles in on track before the end of the year.


In the morning the track was very wet, the focus was trying to drive as smooth as possible and focus on putting together some consistent laps.
In these wet conditions the heated screen in the car was a fantastic addition. It was fitted last summer and I've rarely had a chance to use it, only on the odd cold morning but yesterday It was on while on circuit all morning keeping visibility perfectly clear, definitely a worthwhile upgrade.
https://youtu.be/nqiZXT8HR0A
After lunch I went out to find a dry line had appeared in the 20 minute prior to lunch and an hours sun on the track during lunch time had really made an effect to dry the circuit, I was straight back into the pits to get the new AR1's fitted to the car and clicked the dampers up a couple of clicks, still left it reasonably soft as some sections of the track were still wet and wanted to adjust to the new tyres. The first lap was a very slow with brand new tyres on which hadn't been scrubbed in, it started with spinning the rear wheels half the length of the exit from the pit lane but after a slow lap to get them scrubbed in and get a little bit of temperature into them it was great to be back out on a drying track with semi slick tyres on again. In a nut shell first impressions of the tyres are really good, feel really positive on turn in and they really do grip well even in the dryline/damp conditions. Look forward to getting used to them further next year on a dry circuit.
Here's a video from one of the afternoon sessions. Once again the new engine ran flawlessly and has totally changed the driving experience of the car. Combined with the shorter FD I fitted earlier in the year it works really well now were in March the 3.73 final drive was too short for the old engine.
https://youtu.be/7syOeHLKA5U
I do normally have more video footage but I was using this track day to experiment with in car cameras,which went really well during the morning session but during one of the afternoon sessions the camera turned it's self off 7 minutes into the sessions so I don't have as much dry running footage as usual.

To sum it all up it was fantastic day on circuit for a winter track day. The last two sessions of the day really made it worth while all the effort to get the car out on circuit in the middle of winter. I do have a short list of things to mess with over the winter period to make sure the car is ready for the start of next year, most of it just being small bits of maintenance, hopefully march will be the next time I get out on track again.
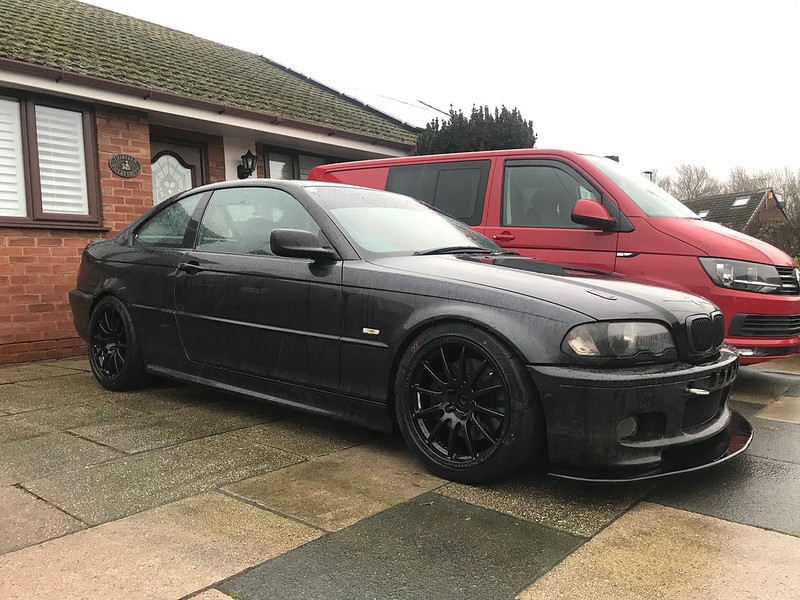
Gassing Station | Readers' Cars | Top of Page | What's New | My Stuff