540HP NA 7L V12 3 seater
Discussion
Appreciate the idea, might help if I find durability a problem with the simplest configuration. I had considered adding an ISG (integrated starter generator as per the T50) in the idler position, but since I am running belts for the dry sump and max rpm is only 7500 happy to use an off the shelf alternator and starter motor. The inspection panel is in the idler position and the crownwheel is also assembled through that aperture. Shimming the pinions and crownwheel so that tooth contact positions are correct is going to be a real exercise in patience. Trying to make the mule as low spec as practical for the first iteration so I can get the thing completed. Currently in a bit of a lull while I raise some funds for a clutch (which is a keystone for finishing the tbox design) and some tubing for the space frame. Should probably focus on starting the test engine in the downtime 
Have also come up with a workaround for the thing that bugs me most about the genuine F1, the headlight eyebrow panels. I have sourced a Mercedes SLK vario roof hydraulic motor to actuate the rear spoiler, so a couple of extra lines to power some actuators on the eyebrow panels will emulate the Nissan RCP92 front end styling, where the flaps can fully open to vent radiator air at low bumper to bumper speed, flush for low drag and cracked open slightly for an HDK effect. Will be quite smug if the idea works better than the original slot design of the clinic model.
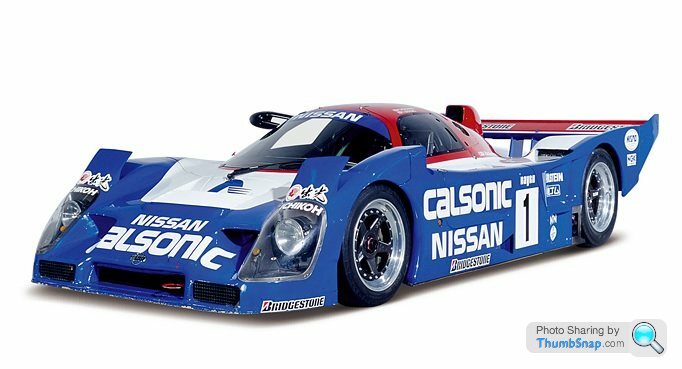
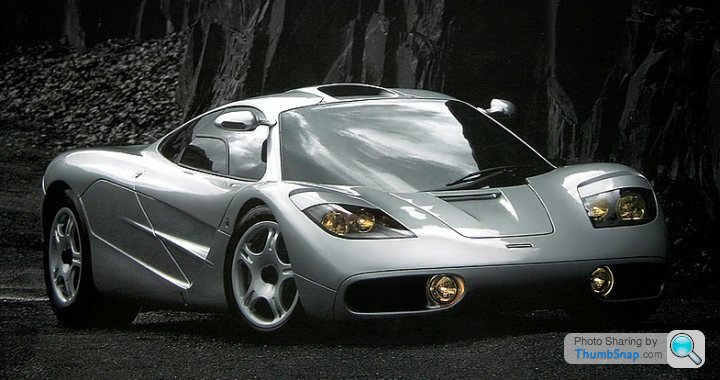

Have also come up with a workaround for the thing that bugs me most about the genuine F1, the headlight eyebrow panels. I have sourced a Mercedes SLK vario roof hydraulic motor to actuate the rear spoiler, so a couple of extra lines to power some actuators on the eyebrow panels will emulate the Nissan RCP92 front end styling, where the flaps can fully open to vent radiator air at low bumper to bumper speed, flush for low drag and cracked open slightly for an HDK effect. Will be quite smug if the idea works better than the original slot design of the clinic model.
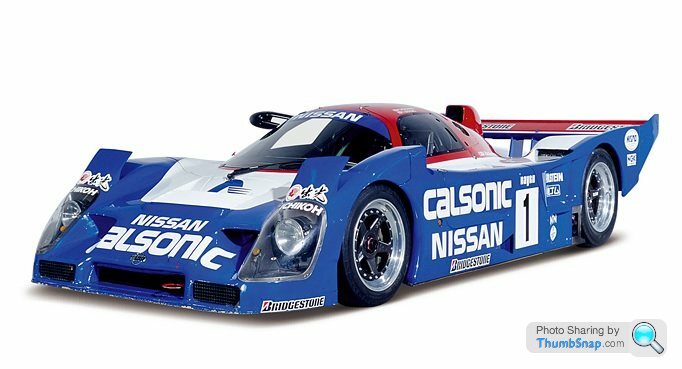
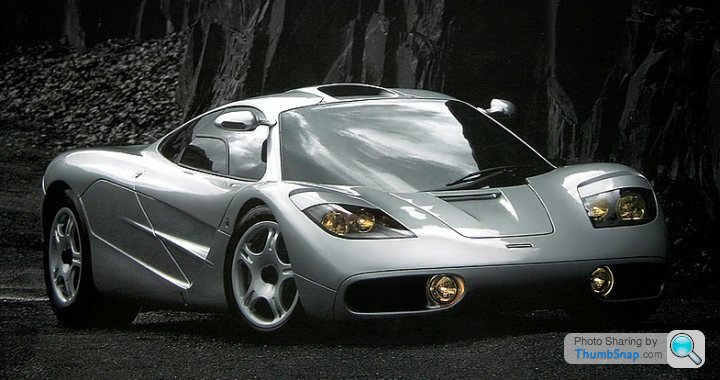
Edited by F1natic on Saturday 29th April 05:03
Good spotting Paul! I will ask the F40 Development guys if they have an old engine cover available for measuring, they are just down the road from me and quite supportive, even if it's just to discuss how they went about making theirs.
The Emira is an unexplored option, thanks to you I will look into it!
The Emira is an unexplored option, thanks to you I will look into it!
Bit of a detour, bought an old Singer 591 industrial sewing machine for $90, and a heavy duty conversion kit (bigger feed dogs, larger needles and speed reduction)

The roller presser foot is the most helpful upgrade, it allows multiple layers of leather to feed though. Still accelerates way to fast with my inexperienced hoof, but was considerably cheaper than the proper walking foot variety that are recommended for heavy materials. As the cabin will mostly be alcantara it should cope. Highly recommend Cechaflo youtube channel for hands on tutorials.
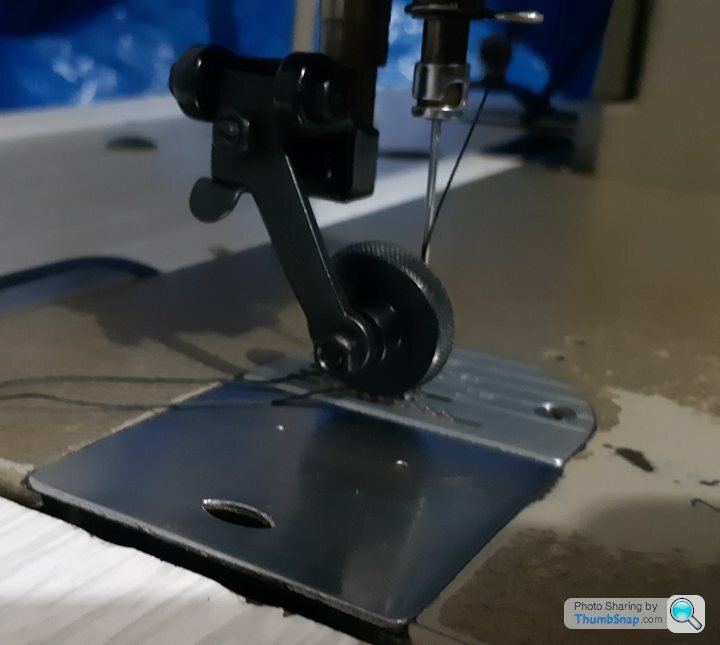
Turns out the estimate for weight of the OEM flywheel and clutch was close, a touch over 20 kgs each, which really hurts as there has to be 2 of them. Rice cracker diet has been implemented to help offset. Under-guessed the stack height with throwout bearing and have to move the engines out extra 50mm each, but luckily there are no clashes with the frame model. Confirming the OD of the ring gear enabled both engines to be dropped another 25mm without issue, which is beneficial. The transaxle is thus rotated nosedown a fraction more, don't expect any oil feed issues as the pump is at the lower front and the TR6070's are designed for high slosh use.


The roller presser foot is the most helpful upgrade, it allows multiple layers of leather to feed though. Still accelerates way to fast with my inexperienced hoof, but was considerably cheaper than the proper walking foot variety that are recommended for heavy materials. As the cabin will mostly be alcantara it should cope. Highly recommend Cechaflo youtube channel for hands on tutorials.
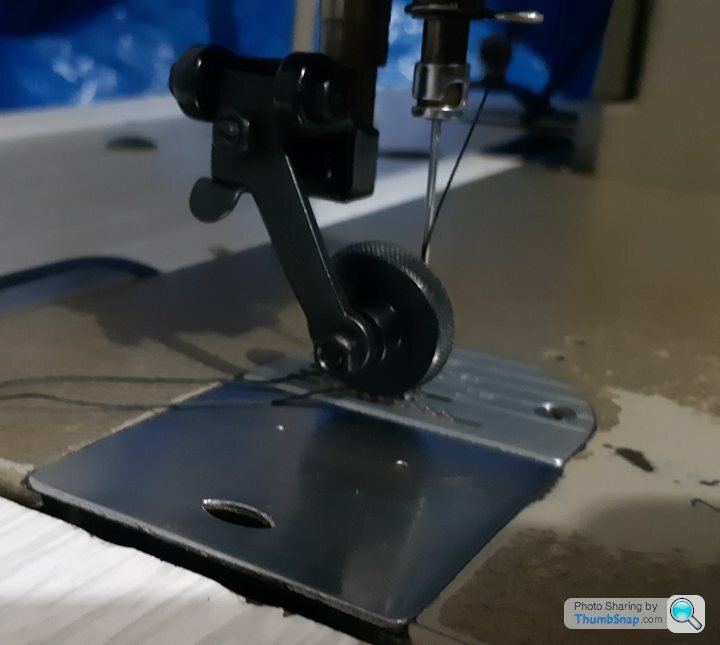
Turns out the estimate for weight of the OEM flywheel and clutch was close, a touch over 20 kgs each, which really hurts as there has to be 2 of them. Rice cracker diet has been implemented to help offset. Under-guessed the stack height with throwout bearing and have to move the engines out extra 50mm each, but luckily there are no clashes with the frame model. Confirming the OD of the ring gear enabled both engines to be dropped another 25mm without issue, which is beneficial. The transaxle is thus rotated nosedown a fraction more, don't expect any oil feed issues as the pump is at the lower front and the TR6070's are designed for high slosh use.

Edited by F1natic on Wednesday 17th May 11:38
Good tip I will have to remember when I get some of the material in to trial, thanks.
Lots of background things happening since the clutch locked things in place designwise, have printed out the first pinion housing pattern, pair of castings will follow on soon.
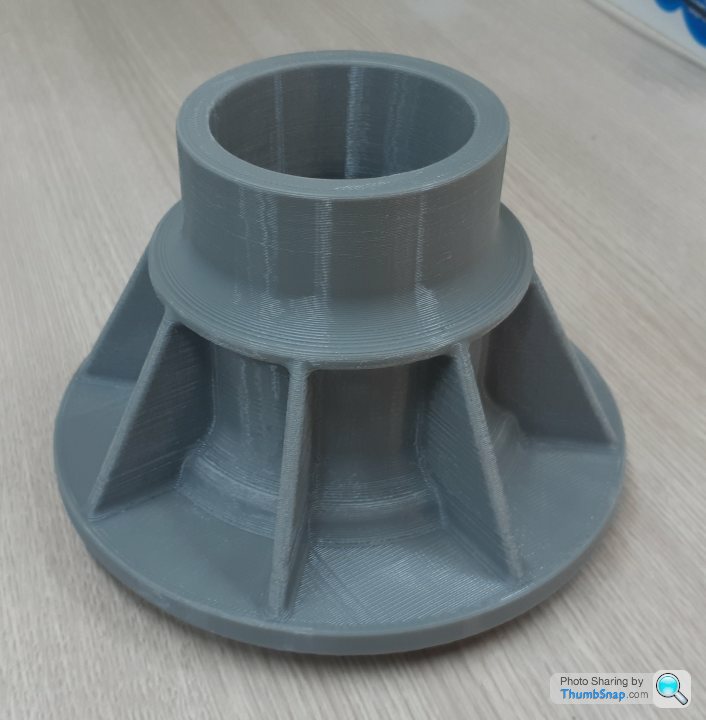
Bought a Melling M68 oil pump and measured on the CMM to confirm dimensions that will be machined into the billet dry sump housings. Once I have proven the parts work I will be happy to share the CAD files.

Lots of background things happening since the clutch locked things in place designwise, have printed out the first pinion housing pattern, pair of castings will follow on soon.
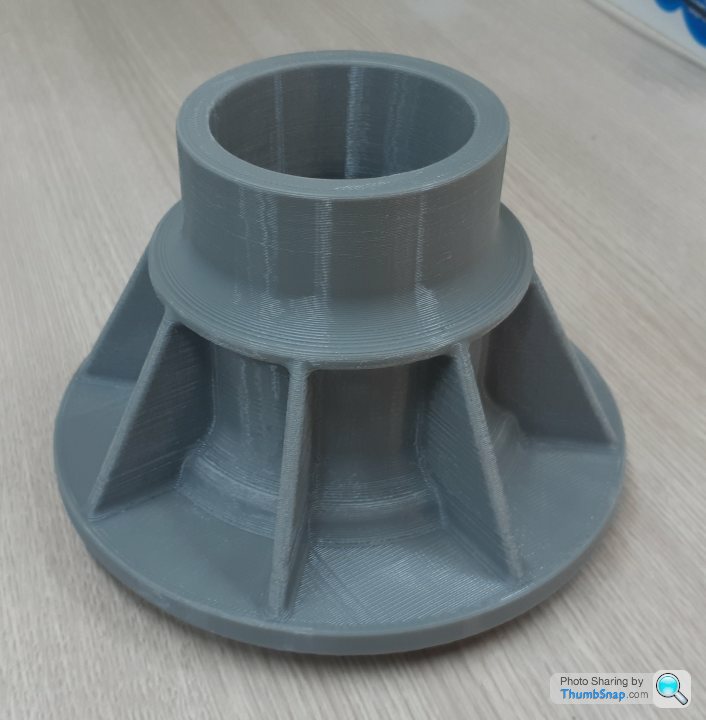
Bought a Melling M68 oil pump and measured on the CMM to confirm dimensions that will be machined into the billet dry sump housings. Once I have proven the parts work I will be happy to share the CAD files.

Basically boils down to living with the final results long term. The Honda V6 engines are understressed, compact and easily sourced. Could not find a suitable V12 locally to use or package. The corvette transaxle is a superb unit and underutilised in mid engine builds. The BMW V10 engine is a jewel and would be my "no limits" budget preference, but the twin engine method of attaining 7L of NA engine in a reasonable state of tune will be ample for a roadcar - IF reliability is achieved. Always have the fallback layout of a conventional twin turbo V6 layout if the Tbox doesn't work out. If I build a second one as a racecar then that convention would have to be followed, but for an experimental roadcar it's a more interesting engineering challenge for me to skin the cat in a different way.
Edited by F1natic on Thursday 29th June 23:25
RandomTask007 said:
^^ Understood. I'm just curious how important it would be to "sync" the engines together to avoid any harmonic issues. You're certainly welcome to tackle the problem any way you see fit. Def reminds me of the Cizeta V16T.
Harmonic issues between the 2 engines should be negated by the +/- 10 degrees of crank "slop" the springs and dampers in the OEM dual mass flywheel allow, and given the output load is between the 2 engines they do not directly "communicate" with each other. The biggest drawback is the exhaust note will be a mixed bag, unless I can get both ECU's to synchronize, then it will be indistinguishable from a "real V12" - but that can only occur when the clutch is disengaged. Brother D said:
Such a great thread!
Did you ever consider modifying an existing chassis for this project (like an Ultima or similar)? Or was this way too much of a unique of a project and just easier to build from scratch?
Thanks! No, I didn't want to modify an existing frame since my layout is so far from normal and the parts are so disparate that from scratch seemed the only logical way for me, however it is taking a lot longer than I hoped. Did you ever consider modifying an existing chassis for this project (like an Ultima or similar)? Or was this way too much of a unique of a project and just easier to build from scratch?
Penguinracer said:
Did you consider the Mercedes M120 or M275?
They can be picked up at reasonable cost outside of the NZ...but you'd need a helpful vendor who could make the freight costs feasible by finding space in an existing container load or with a vehicle on its way to Kiwiland.
Great engines, can't argue with Horacio Pagani's choice, but my budget is a little more modest and therefore locally available Honda it is! The J35 engines can live happily up to 7500rpm when the OEM ECU is removed, also the stock ECU blunts the engine response to make the standard Accord benign for general consumption. However a human controlled engine has quite a different character and with a bit of headwork they can breathe properly above stock RPM limits. This whole project is quite experimental so really only one way to find out.They can be picked up at reasonable cost outside of the NZ...but you'd need a helpful vendor who could make the freight costs feasible by finding space in an existing container load or with a vehicle on its way to Kiwiland.
This link is an interesting one, but I have not seen an update for a long time, was hoping to see this one finished;
https://www.drivelife.co.nz/2018/06/project-fz12-f...
Edited by F1natic on Wednesday 12th July 02:24 as I Spelled Horacio's name wrong! The shame.
Edited by F1natic on Wednesday 12th July 02:24
Have been refining the plenum chamber design and measured the volume of the standard J35 plenum and upper runners, which is 6.5 litres. What would life be without duct tape...
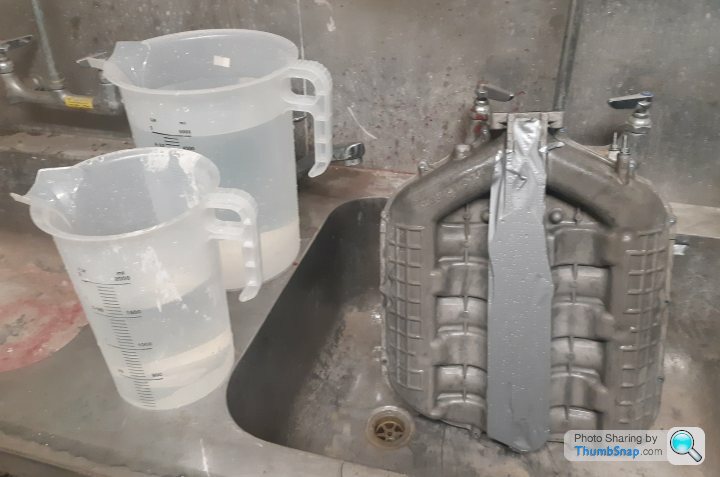
It will be fabricated aluminium runners and bellmouths bonded to a carbon fibre box - after all there has to be some bling visible through the engine covers.
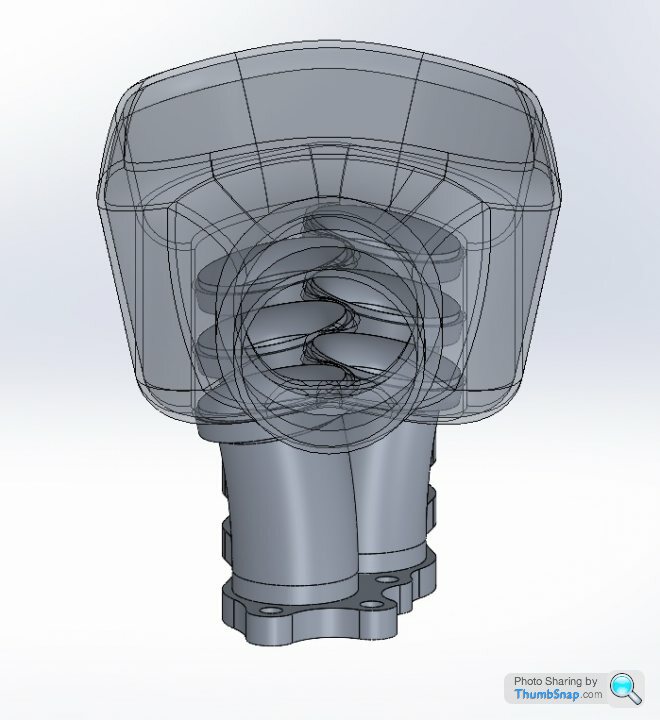
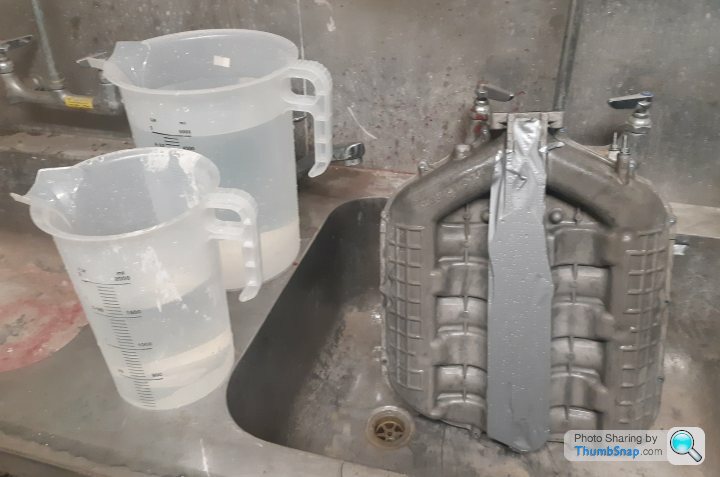
It will be fabricated aluminium runners and bellmouths bonded to a carbon fibre box - after all there has to be some bling visible through the engine covers.
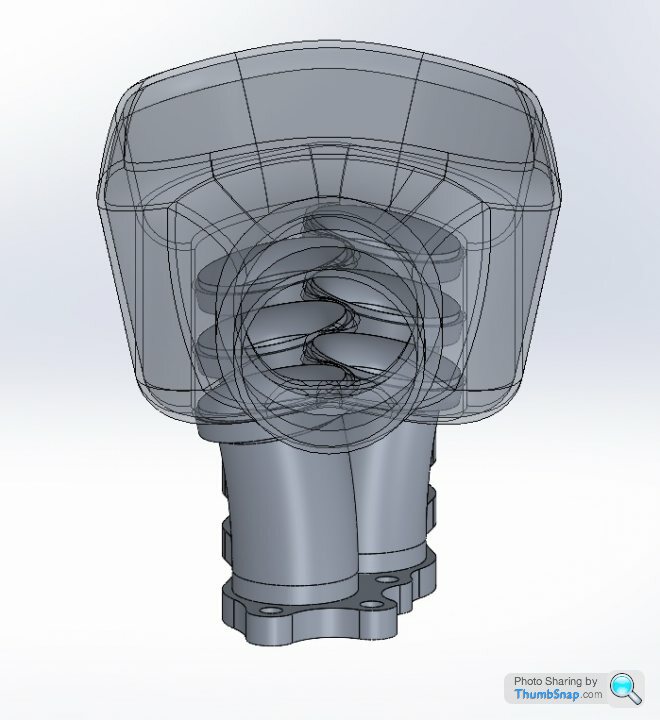
Edited by F1natic on Thursday 20th July 08:22
Thanks for the link Penguinracer.
Last week I picked up (chuckle) a NZ new 2008 Accord with 100,000 Kms on the clock from the salvage yard. Sad how a minor scrape down one side can write off a fully driveable car, but it was cheaper than a bare long block engine from the specialist Honda dismantler so a complete no brainer. It now has a new purpose as the project donor. It's great fun stripping cars down to uncover the clever high volume manufacturing tricks, plus now have lots of spares for my daily driver and most importantly all 12 cylinders!

Last week I picked up (chuckle) a NZ new 2008 Accord with 100,000 Kms on the clock from the salvage yard. Sad how a minor scrape down one side can write off a fully driveable car, but it was cheaper than a bare long block engine from the specialist Honda dismantler so a complete no brainer. It now has a new purpose as the project donor. It's great fun stripping cars down to uncover the clever high volume manufacturing tricks, plus now have lots of spares for my daily driver and most importantly all 12 cylinders!

Have cycled through another iteration of detail on the intake system, honing in on the final forms that will get fabricated. The intake air passes through a coarse mesh at the scoop entry to filter out the leaves and any other large road debris (birds, cephalopods, malicious discards etc.)
In extremes of cold or wet weather an air deflector is operated to close and block the air flow through the scoop and instead air is drawn from the top of the engine bay. The air deflector is the full scoop width, whereas the intake snorkel is only 2/3 the scoop width. Under normal conditions the air deflector is open and the bypassing air goes directly into the top of the rear cover to help cool engine bay temperatures.
The roof scoop is fixed to the chassis whereas the plenum and throttle body assemblies are fixed to the engines. To absorb the side to side engine rocking movement the standard Accord J35 rubber bellows have been reused. Not shown is the rear section of the airbox that is removable to allow access for servicing the 2 long rectangular K&N air filters that are inside the airbox.
For anyone wanting to make their own throttle body I can confirm that the butterfly shaft axis is co-incident with the throttle body bore.
Finally bought a pair of corrado wing mirrors to help finish of the door frame detailing.
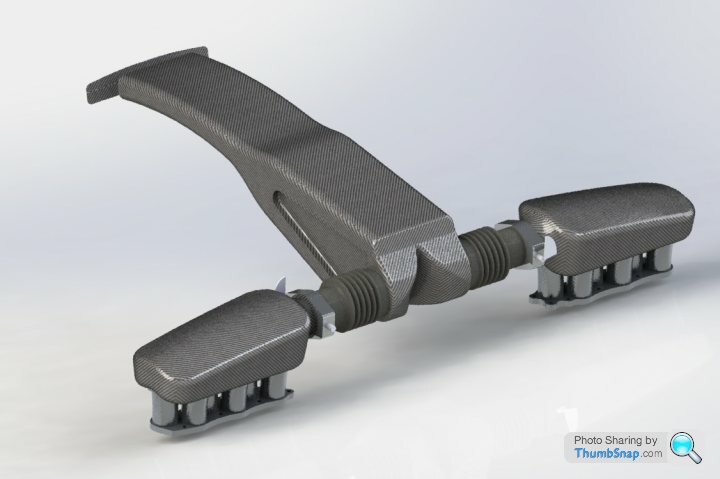
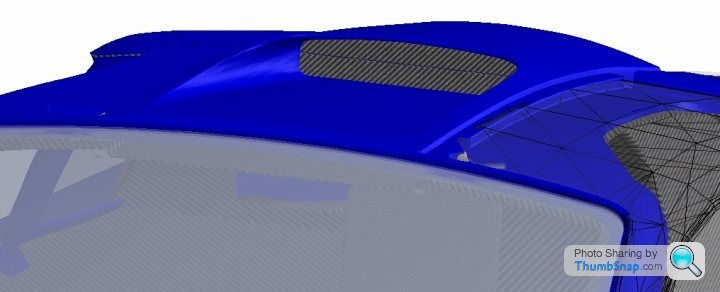
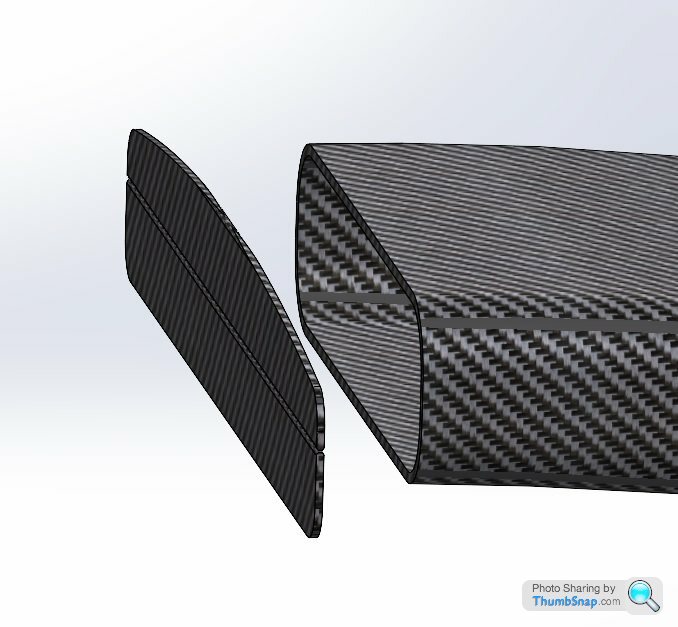
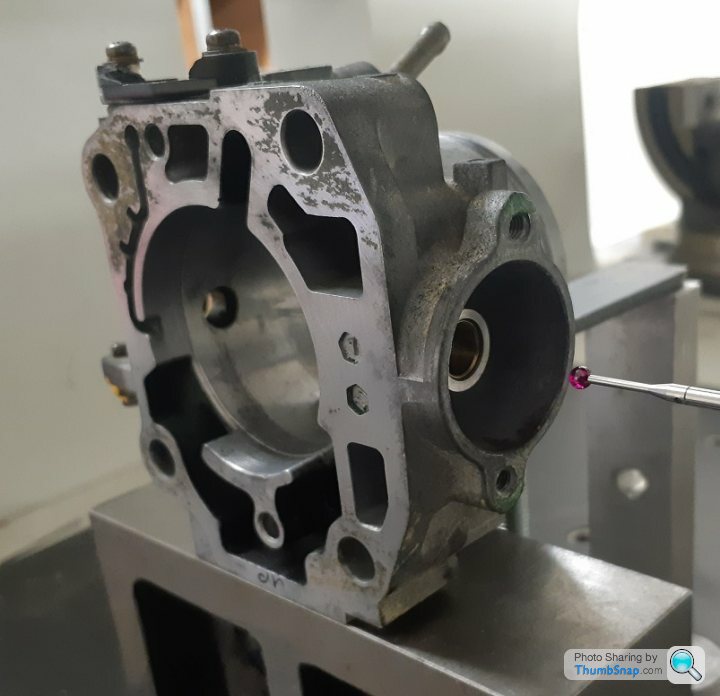

In extremes of cold or wet weather an air deflector is operated to close and block the air flow through the scoop and instead air is drawn from the top of the engine bay. The air deflector is the full scoop width, whereas the intake snorkel is only 2/3 the scoop width. Under normal conditions the air deflector is open and the bypassing air goes directly into the top of the rear cover to help cool engine bay temperatures.
The roof scoop is fixed to the chassis whereas the plenum and throttle body assemblies are fixed to the engines. To absorb the side to side engine rocking movement the standard Accord J35 rubber bellows have been reused. Not shown is the rear section of the airbox that is removable to allow access for servicing the 2 long rectangular K&N air filters that are inside the airbox.
For anyone wanting to make their own throttle body I can confirm that the butterfly shaft axis is co-incident with the throttle body bore.
Finally bought a pair of corrado wing mirrors to help finish of the door frame detailing.
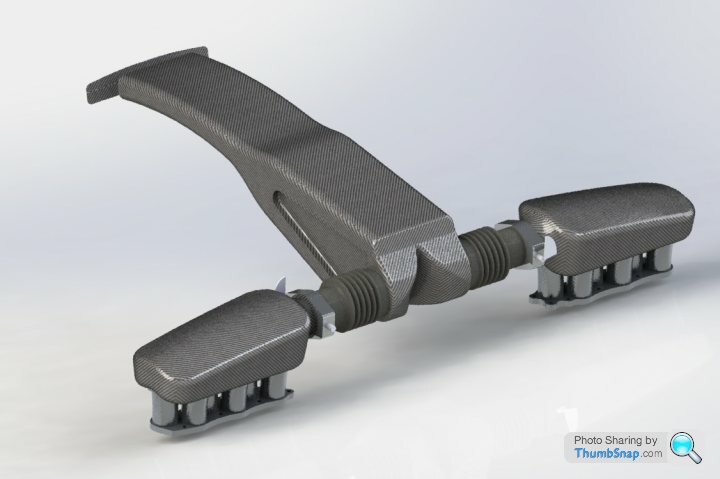
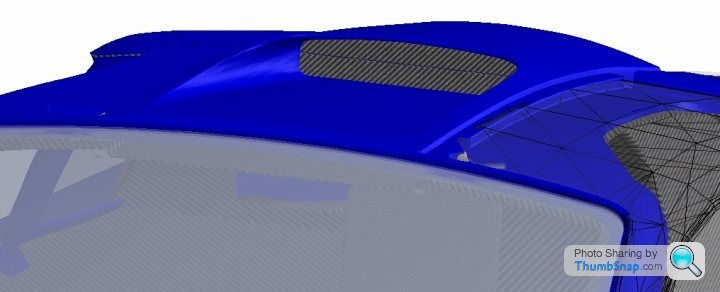
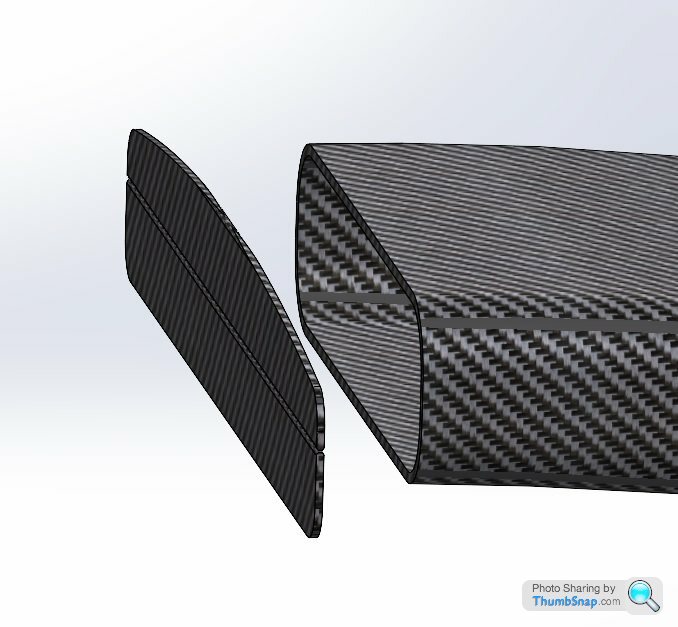
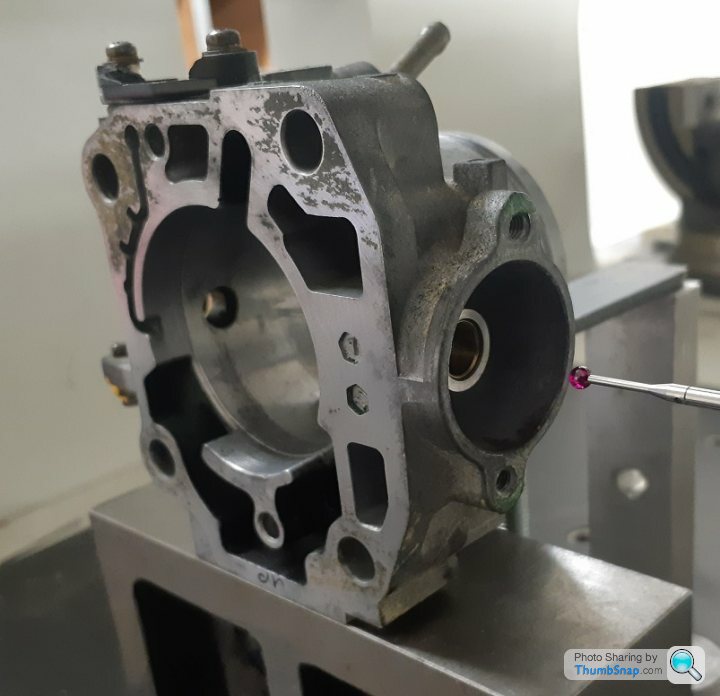

Edited to add wing mirror source
Edited by F1natic on Saturday 2nd September 11:03
Sorry, no idea how to successfully design a reliable water separator, trap and drain in a tight space. Perhaps an expired patent search? I remember reading that the airflow over the windscreen separates the air naturally due to the scoops position, but can't remember source of that info, might be in windtunnel section of DA.
I didn't want to spend time developing something that might let me down in the worst weather conditions so thought best solution is to avoid it altogether. Main concern is dealing with heavy deluges and icy conditions, which in both cases will require a gentle throttle and therefore engine performance will not suffer having the cold air intake shut off almost completely.
Nice article link, my vote is for the NSX.
I didn't want to spend time developing something that might let me down in the worst weather conditions so thought best solution is to avoid it altogether. Main concern is dealing with heavy deluges and icy conditions, which in both cases will require a gentle throttle and therefore engine performance will not suffer having the cold air intake shut off almost completely.
Nice article link, my vote is for the NSX.
Edited by F1natic on Tuesday 5th September 12:28
RandomTask007 said:
Bumping for an update. 
As an aside, those turn indicators came in and are perfect.
BTW, if you want, I have a -nice- model of an F1 LM; also have the 3D scan info from an actual F1 GTR (Dark gray). (Also have 3D scan info for the rear fascia).
Unfortunately my project has languished in the background as work/hobby balance is currently skewed in the wrong direction, although the door hinges are almost finalised for printing and casting. The timing of your offer to share a genuine GTR scan is absolutely perfect, especially if it has door detail. Very much appreciated, drop me a DM. 
As an aside, those turn indicators came in and are perfect.
BTW, if you want, I have a -nice- model of an F1 LM; also have the 3D scan info from an actual F1 GTR (Dark gray). (Also have 3D scan info for the rear fascia).
Have also been spending a bit of my spare time assessing subsurface modelling as a way of generating highly organic machinable surfaces, something I find difficult to control precisely in Solidworks - this video shows the technique I am working through;
https://www.youtube.com/watch?v=3rlMzsBWtPY
Congrats on collecting quite the array of genuine parts, it is really nice to have tactile objects to help drive the enthusiasm for your project.
Caddyshack said:
I think that would only work with pooled water, the engine would be sucking in the air and water before it had time to sit at the bottom. The odd thing is that cars can use water injection to cool them and I can’t see a lot of rain being an issue….obviously Gordon Murray thought it was and as such I would trust him more.
The F1 has 2 big conical air filters under the panel ahead of the plenum chamber, so depending on the air velocity profile water could coalesce and drain by gravity (out of any duckbills) before entering the plenum. Just like driving a convertible in the rain as long as you have forward movement a certain degree of filtering of heavy elements is achieved by the nature of the airstream over the scoop, plus a certain amount of water will be tolerated by a hot engine. However my problem is the massive steel rollover structure right where the filters would reside, so had to run the scoop through a smaller gap, with water separation at the front and filters nearer the rear. Some of the design is contingency planning, I probably won't end up building it unless it is actually required - the scoop deflector is probably one of them. The donor car was taken for it's last drive today, as I need the axles from it for my daily driver. After a proper warmup captured a range of ballpark datapoints for setting up the speeduino on the test engine, wideband O2 will be used to refine the fueling table.
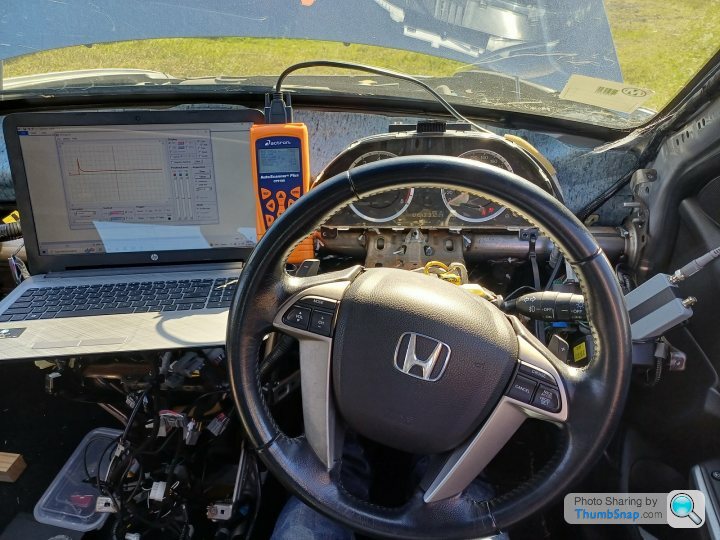
Sliced into the ignition signal wire to get a contact for the oscilloscope probe. Coil on plug dwell is 2.5ms at idle, around 3ms at higher loads.

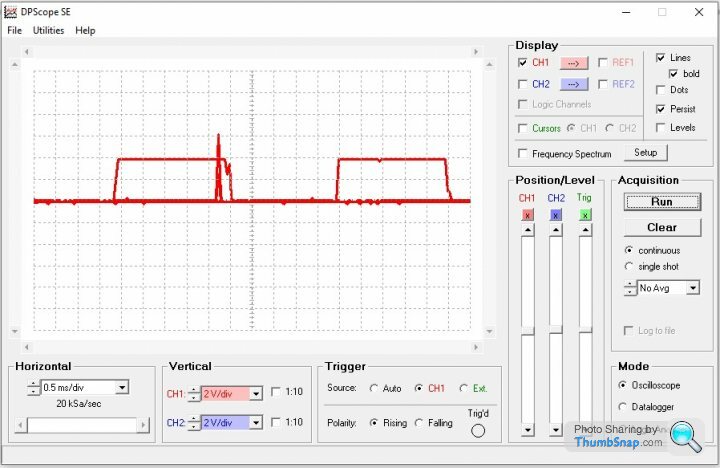
The ECU grounds the injector coil so intercepted the wiring on the injector coil ground side to analyse the injector pulsewidth across a range of engine loads. Car in drive and brakes fully on, holding throttle at the desired MAP values that the speeduino will use as the engine load axis. Transmission oil got very hot but as it's off the road now not an issue.
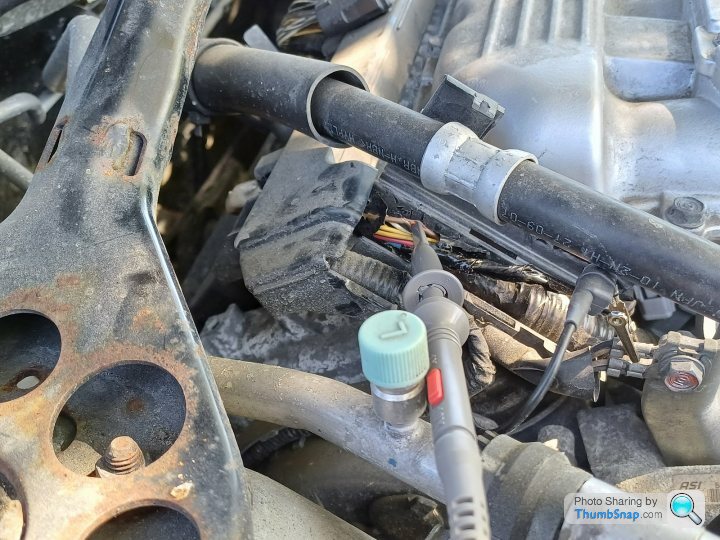
DPscope capture of full throttle injector pulsewidth - leads are set to 1:10 so voltage captured properly, however not sure they were correctly attenuated, but was really only interested in the pulsewidth anyway.
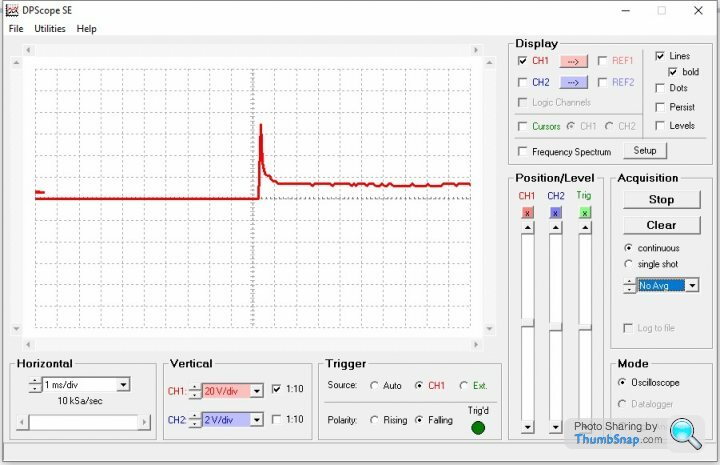
The laptop is running the DPscope software, works good enough for my budget/purposes. 16 quid plus shipping.
https://www.picaxestore.com/catalogsearch/result/?...
3D printed a housing and soldered leads to the 2 BNC connectors.
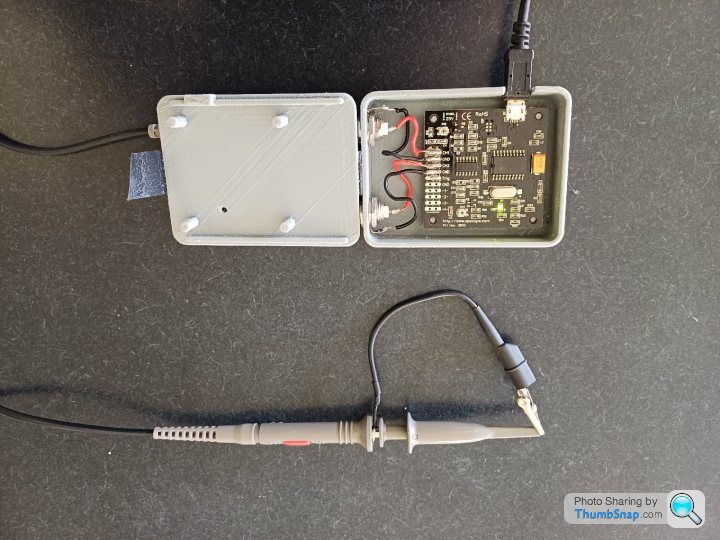
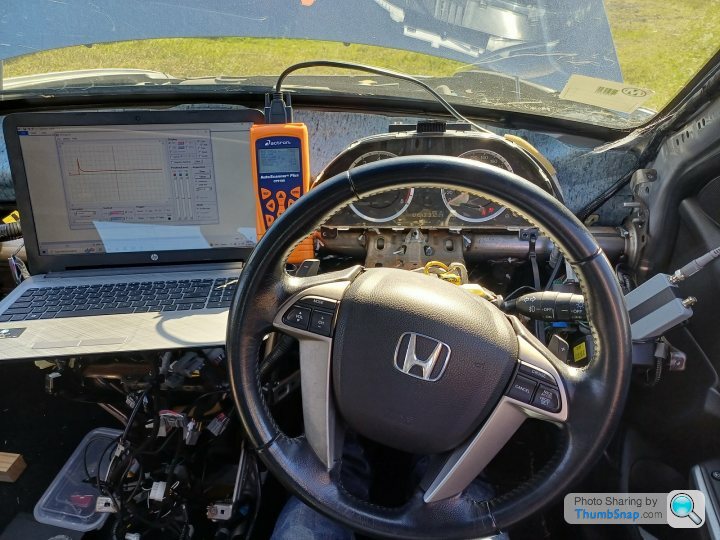
Sliced into the ignition signal wire to get a contact for the oscilloscope probe. Coil on plug dwell is 2.5ms at idle, around 3ms at higher loads.

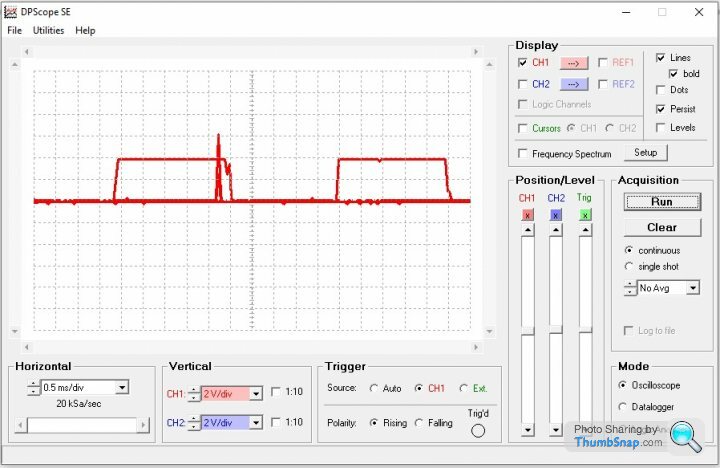
The ECU grounds the injector coil so intercepted the wiring on the injector coil ground side to analyse the injector pulsewidth across a range of engine loads. Car in drive and brakes fully on, holding throttle at the desired MAP values that the speeduino will use as the engine load axis. Transmission oil got very hot but as it's off the road now not an issue.
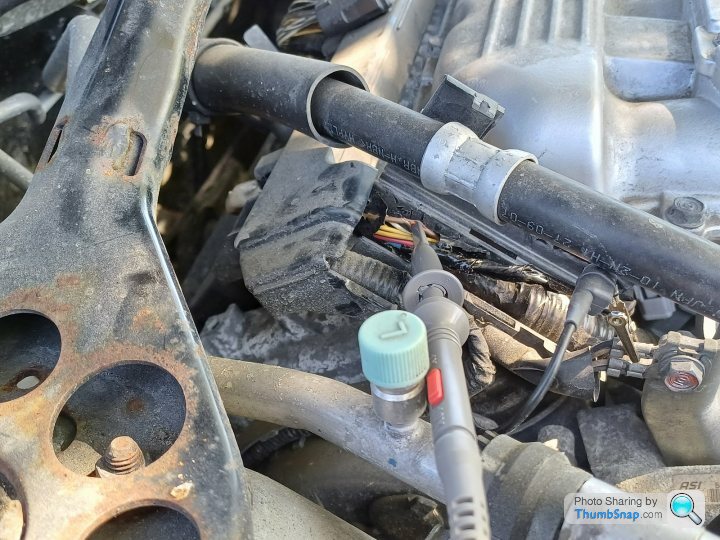
DPscope capture of full throttle injector pulsewidth - leads are set to 1:10 so voltage captured properly, however not sure they were correctly attenuated, but was really only interested in the pulsewidth anyway.
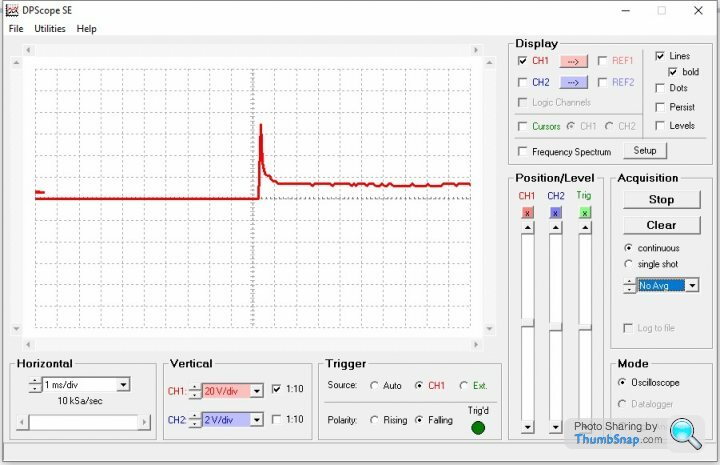
The laptop is running the DPscope software, works good enough for my budget/purposes. 16 quid plus shipping.
https://www.picaxestore.com/catalogsearch/result/?...
3D printed a housing and soldered leads to the 2 BNC connectors.
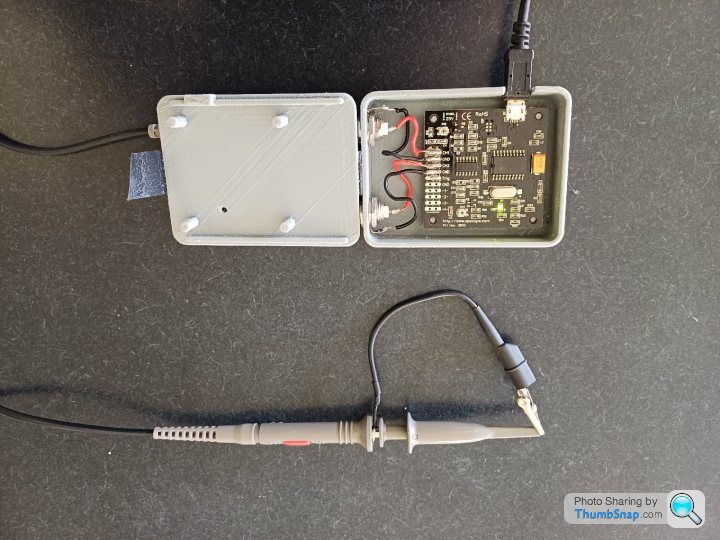
Edited by F1natic on Sunday 12th November 08:03
The original position does not suit the Mercedes SLK door latches being used for this build, however with a bit of "adapting" (using a grinder to remove the superfluous material from the OEM parts) and swapping around the installation can achieve something functionally very close.

The component on the left is a standard right hand door assembly, where the mechanism would be mounted inside the door. Dihedral doors typically have the latch mechanism in the body and the striker pin on the door, so in this case taking a cutdown LH mechanism (shown on the right) and rotating it so the striker approaches from the topside works - at least in the CAD assembly.

Countless hours have been spent trying to resolve the clearance around and mounting of the modified door latches to the frame, happy now with the solution that ties the passenger seat belt retractor mount into the door latch mounting plate and a major chassis node.
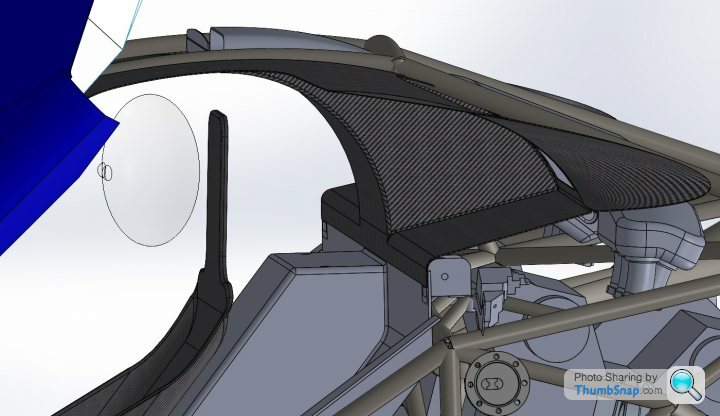

The component on the left is a standard right hand door assembly, where the mechanism would be mounted inside the door. Dihedral doors typically have the latch mechanism in the body and the striker pin on the door, so in this case taking a cutdown LH mechanism (shown on the right) and rotating it so the striker approaches from the topside works - at least in the CAD assembly.

Countless hours have been spent trying to resolve the clearance around and mounting of the modified door latches to the frame, happy now with the solution that ties the passenger seat belt retractor mount into the door latch mounting plate and a major chassis node.
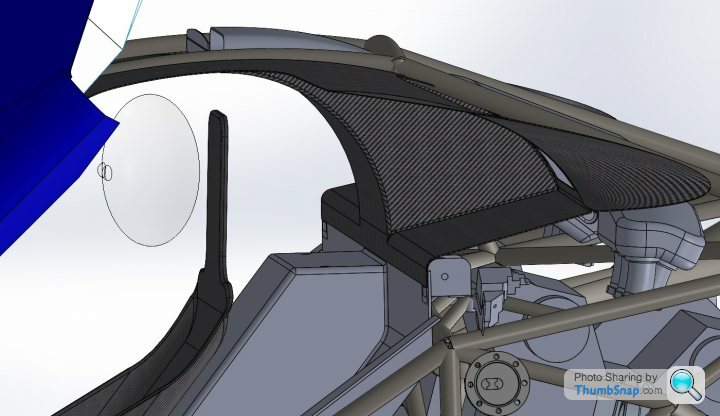
Edited by F1natic on Friday 24th November 23:21
Indeed "DA" is such a good source of photos from behind the scenes of the F1's creation. The chaps at IDAT did a great job too, although have never seen any photos of their work as I expect they were under confidentiality agreements. The whole process of taking the approved plug and reverse engineering the body panel tooling from it would have been a huge and highly skilled undertaking - modern scanning and CNC accessibility has likely replaced some of these skills? Would really like to hear how the process is currently done by someone involved in this aspect of the trade.
Next casting off the rank is a test bellhousing - hopefully for use on the secondary motor as no bosses or cutouts for the starter were detailed as I have run out of 2023. Will be cast in aluminium grade A356.
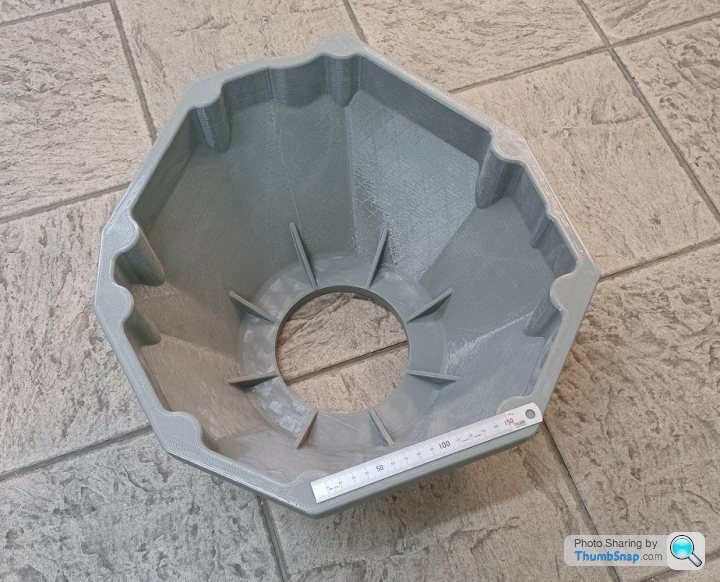

Next casting off the rank is a test bellhousing - hopefully for use on the secondary motor as no bosses or cutouts for the starter were detailed as I have run out of 2023. Will be cast in aluminium grade A356.
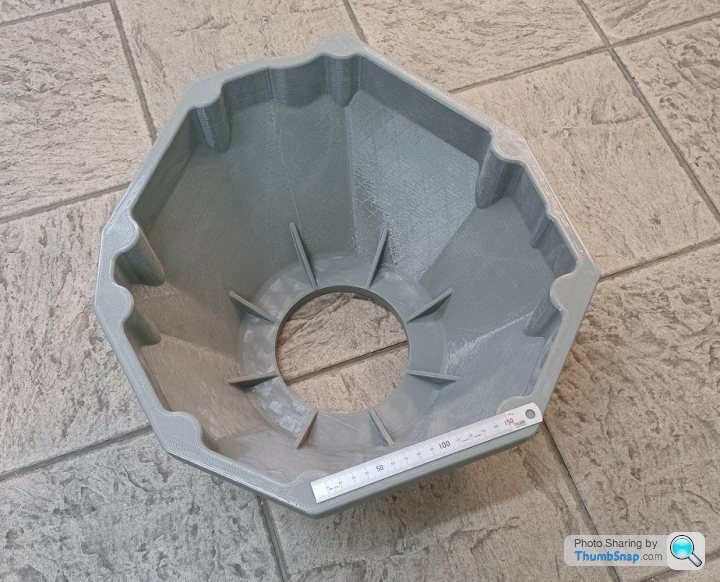

A while ago I 3D printed then cast in 4140 a small press tool for the intake tubes, finally got around to testing it. Worked out well as a cutting off guide in the bandsaw too. One dozen inlets took about an hour to make.

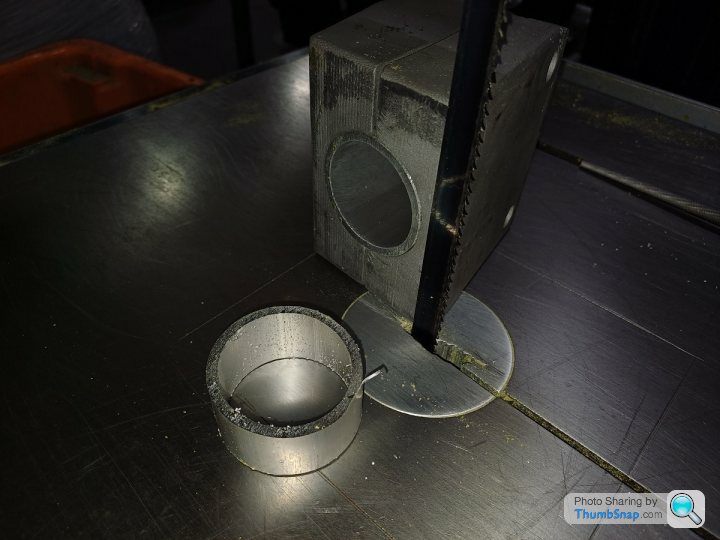
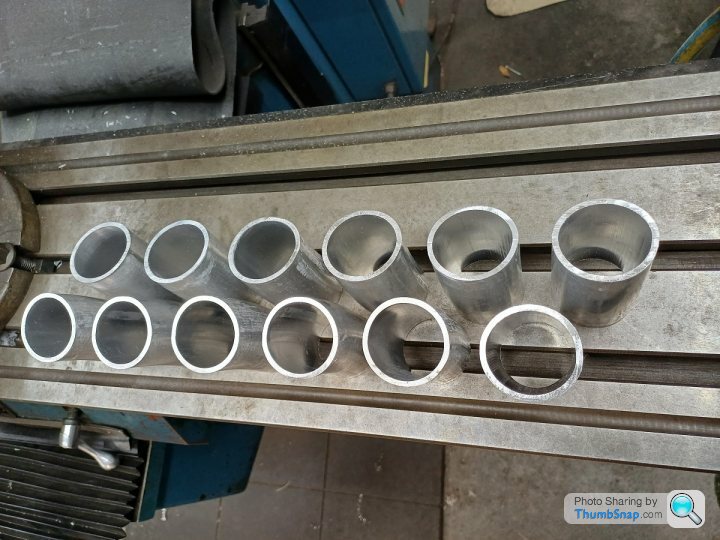
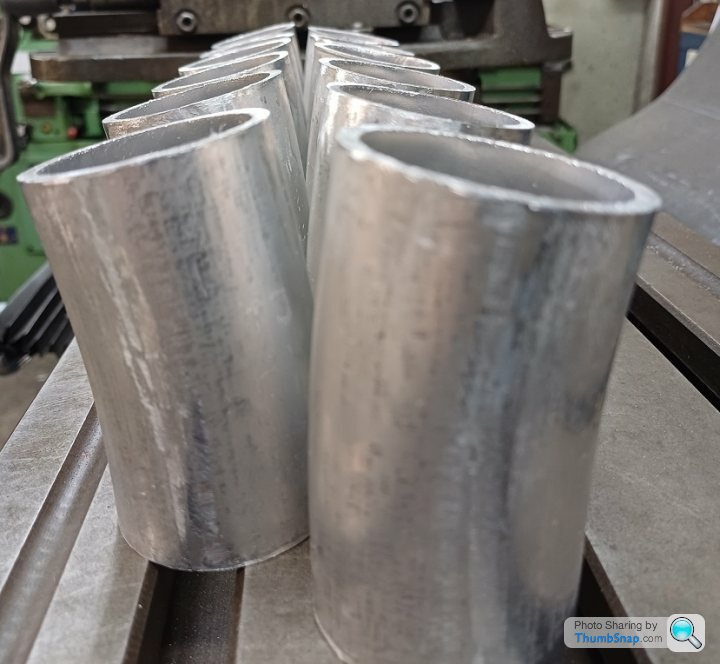
Will need to turn up some bellmouths and weld them to these tubes, then weld the tubes to the CNC'd lower plate which then bolts onto the standard honda lower intake manifold
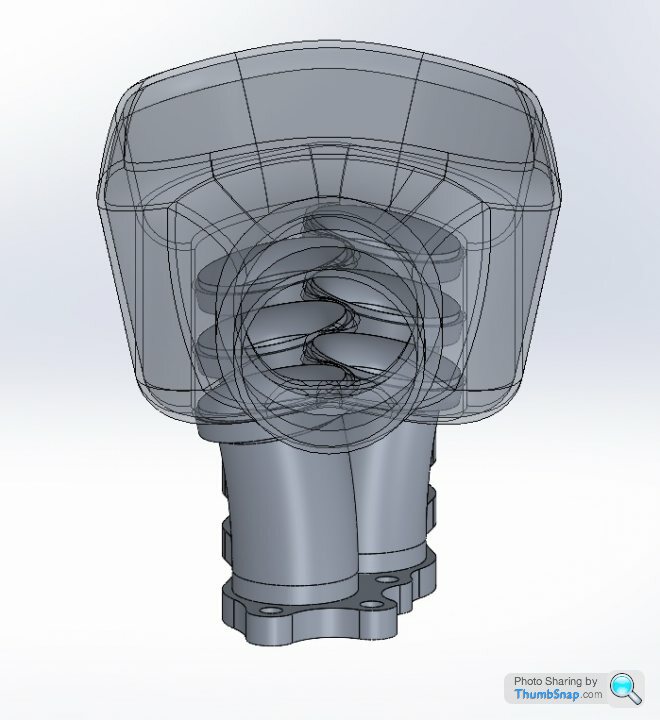

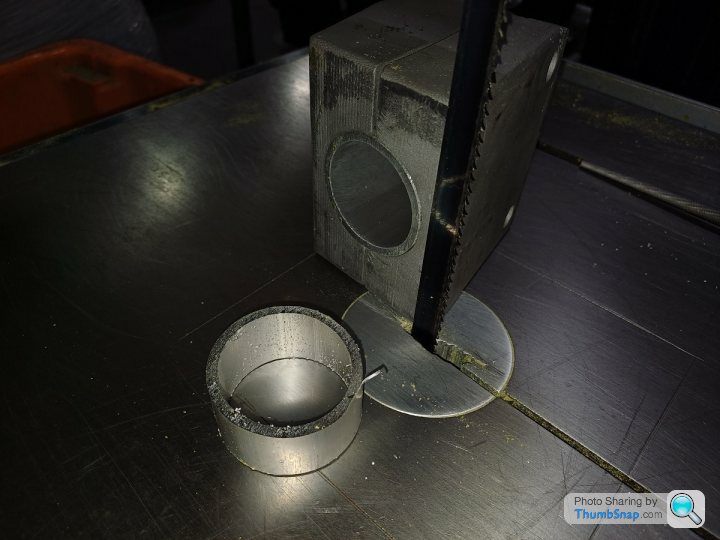
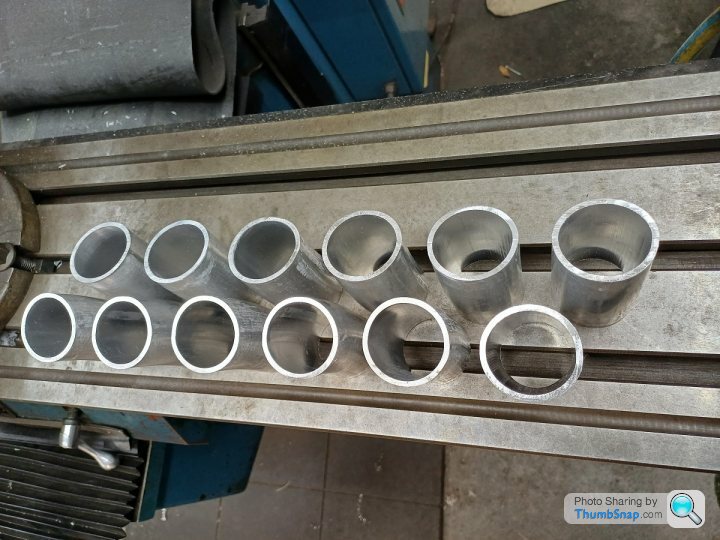
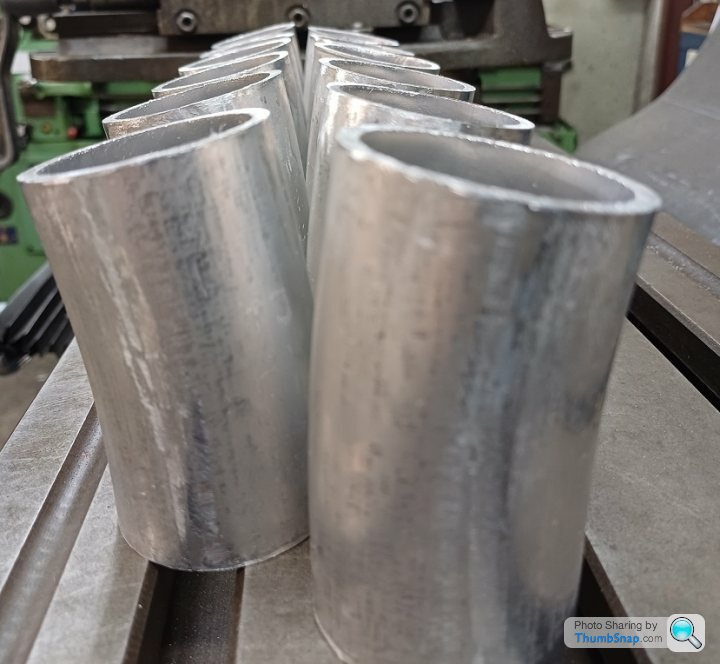
Will need to turn up some bellmouths and weld them to these tubes, then weld the tubes to the CNC'd lower plate which then bolts onto the standard honda lower intake manifold
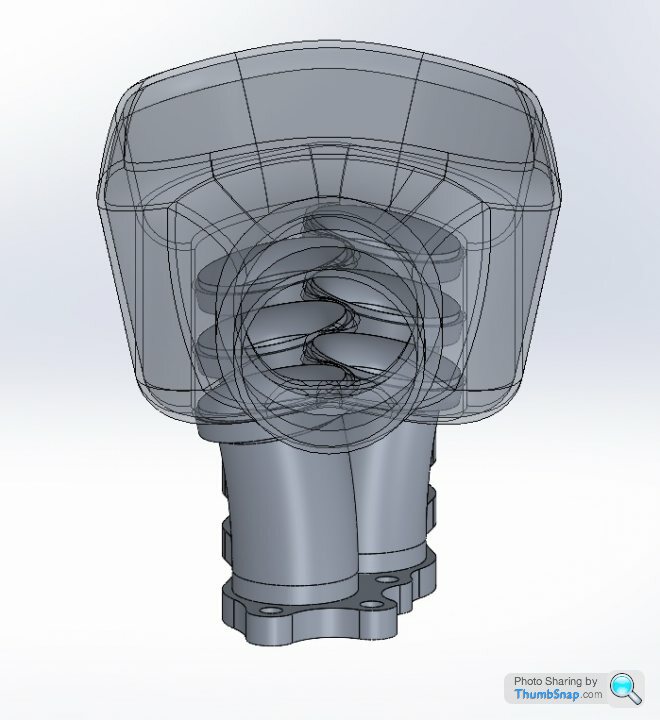
Bellhousing casting came out well for the first attempt;
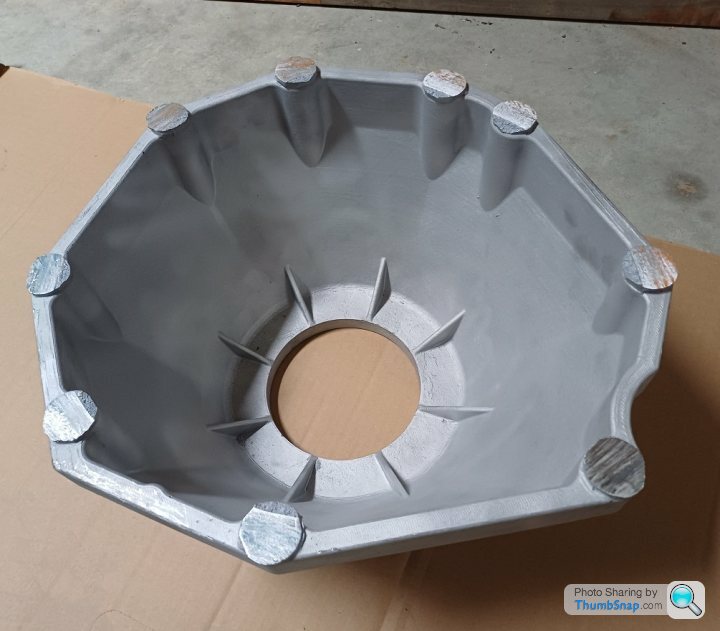
Fit looks good so will proceed to heat treat and machining in the new year - there was generous machining allowance included at each end.
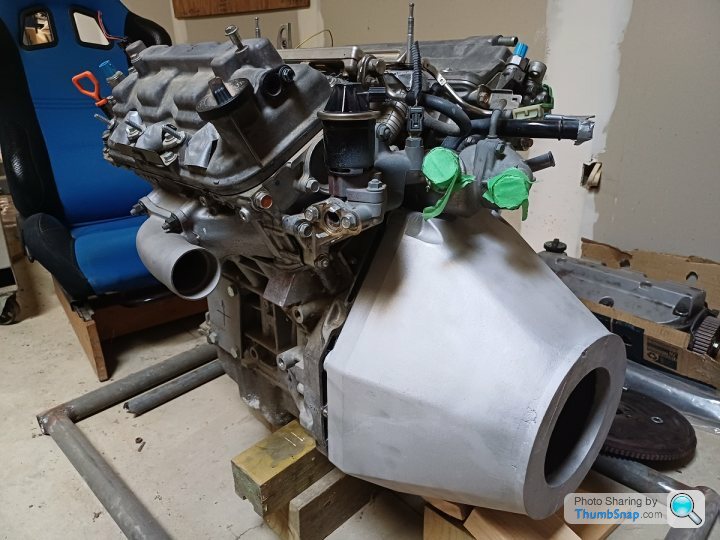
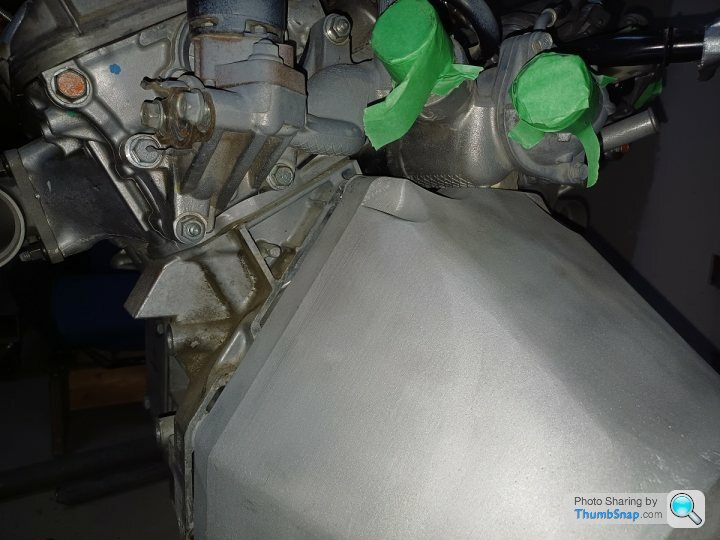
Also knocked off a small task of blocking off the auxiliary line in the corvette fuel pump with a small brass pin - now it needs a tank to be fitted into!


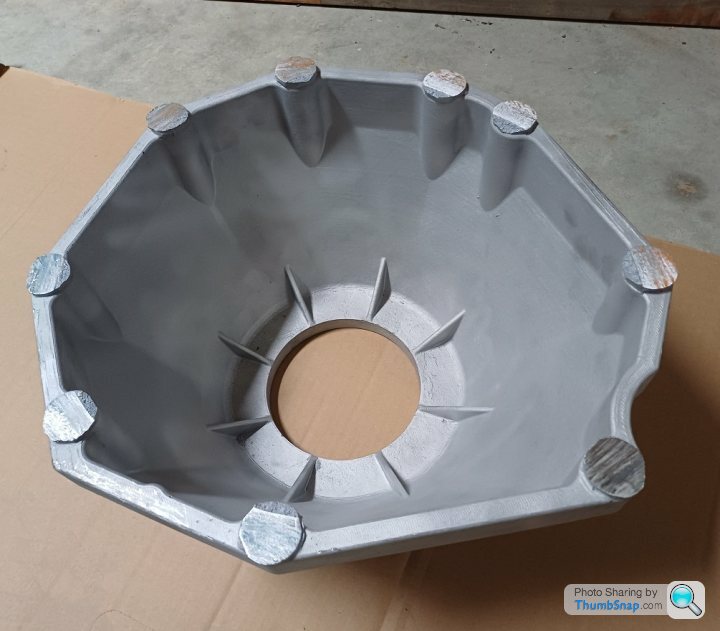
Fit looks good so will proceed to heat treat and machining in the new year - there was generous machining allowance included at each end.
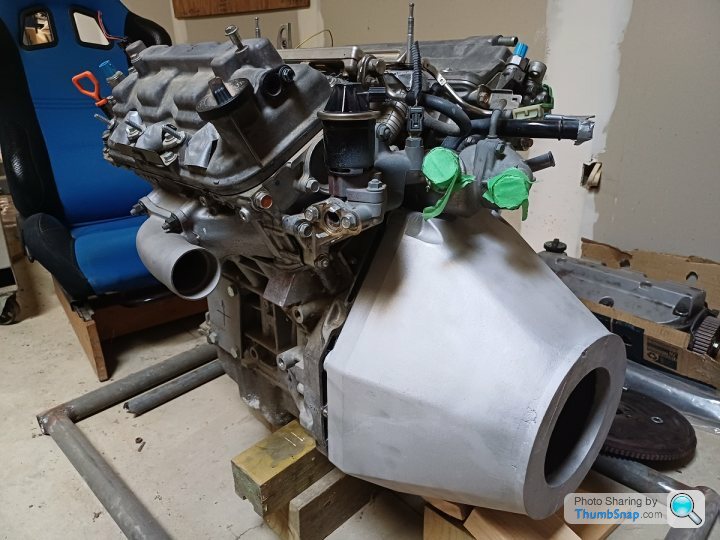
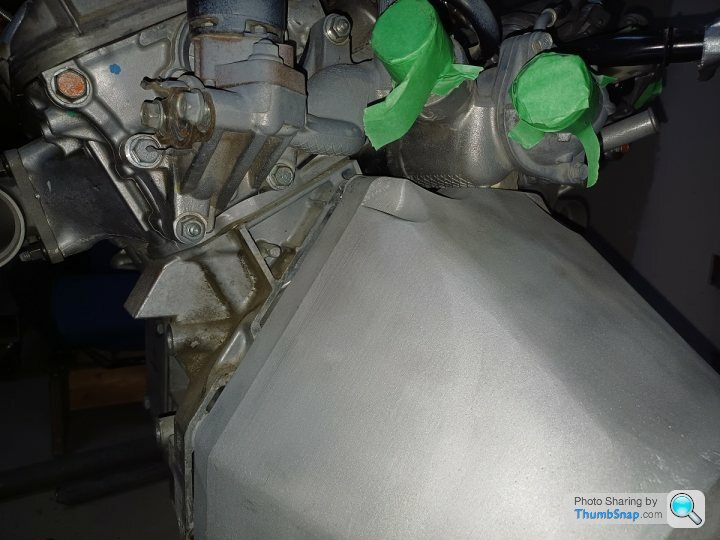
Also knocked off a small task of blocking off the auxiliary line in the corvette fuel pump with a small brass pin - now it needs a tank to be fitted into!


Edited by F1natic on Monday 18th December 06:57
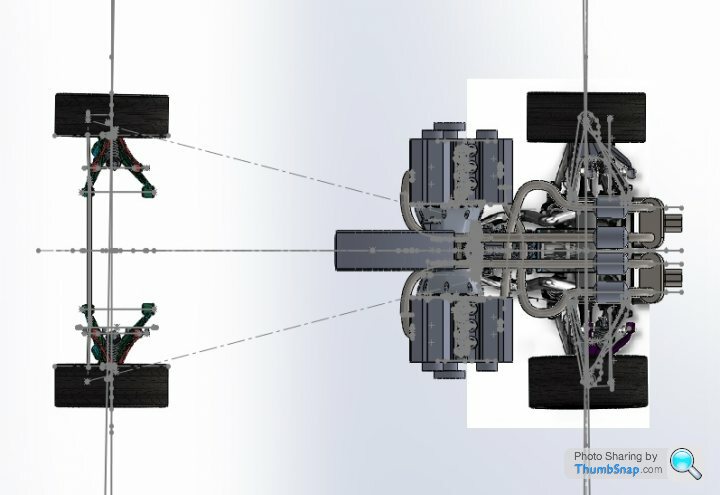
Hi Paul,
Thanks for your post, I greatly appreciate the info. Have spent a few days having a really deep think about this as a practical alternative method since it is equivalent to the layout I am using for the crownwheel. Off the shelf parts are always a preference when doing something as weird as this project, but there comes a point when all those standard parts have to be mated together with custom parts.
Due to the 344Nm torque on each pinion they need stout bearings for longevity and precise locating of meshing faces. Given the very tight physical width envelope I have painted myself into with the T-box I am fairly fixed on the pinion shafts and gears being integral units. For example the "diff head" is only 140mm wide.
I agree these parts have merit, and in a fresh sheet design could work well. I am not certain the twin engine concept is going to work out long term, which is why the chassis design is easily reconfigurable to a single twin turbo V6 or fully electric if necessary.
Gassing Station | Readers' Cars | Top of Page | What's New | My Stuff