540HP NA 7L V12 3 seater
Discussion
klevenspielberg said:
Have you considered an F355 gearbox? They are transverse, not crazy money in the scheme of things, and would bring the complexity and lead time down a great deal I imagine. I don't know what sort of power they can handle or if the ratios are suitable for your application, but as you are looking into having custom gears machined anyway it might be worth a punt.
If you're at all thinking about commercialising the project, getting a 348/Mondial T (5 speed) 'box and a single V6 would probably not be a bad way to get an MVP. But hey, I'm a first time poster and not an engineer, so what do I know
Thanks for your comments, I really appreciate your post for 2 reasons;If you're at all thinking about commercialising the project, getting a 348/Mondial T (5 speed) 'box and a single V6 would probably not be a bad way to get an MVP. But hey, I'm a first time poster and not an engineer, so what do I know

1) I had not considered the F355 box, you are right they are not crazy money and look to be a very compact unit and closer investigation is warranted especially their torque capacity.
2) I was not aware of the MVP term (not my normal domain) and agree that simplicity is very desirable and increases the chances of getting it over the line. Design is an iterative process and I am happy to assess alternatives.
Edited by F1natic on Saturday 31st August 08:49
Caddyshack said:
Agreed, make it a long tail.
I think the reason why people are suggesting a stock engine is to remove an area of easy failure to the project...just getting the body panels, suspension and doors is challenge enough and we want it to succeed.
AMG v12 or supercharged v8 would be on my radar too.
Thanks for the suggestion - I am intending for this car to be road focused, and I have always been impressed by the compact nature of the road car. Used to study the one in Park Lane in detail and the longtails at Goodwood FOS. If the chassis development is successful over a long term (a few years of heavy use) then a NZ landspeed attempt (currently 220 mph) using a longtail might be a very sensible modification - just don't tell my wife. However the longtail would not be good for parking in the city! I think the reason why people are suggesting a stock engine is to remove an area of easy failure to the project...just getting the body panels, suspension and doors is challenge enough and we want it to succeed.
AMG v12 or supercharged v8 would be on my radar too.
My commute is curently about 80 minutes each way (with a very small gravel section, great fun) so the dual engine setup allows me to suspend 6 cylinders by locking out one clutch - this reduces heat load on the cooling system while sitting in slow traffic at the expense of a clutch release bearing life. The engines I am using have variable cylinder management so could even drop to 3 cylinders while trickling along, however the engine sounds like its running over a rumble strip in that mode which is too irritating. Also the original Mclaren F1 development was going to use a Honda engine, so I get satisfaction out of using them in my car.
Big engine torque and wide rear tires tend to blow clutches and transmissions - depending on your driving style of course. I am fairly set on the C6 setup becuse its so well developed at the 500+Hp rating - and thus I am very determined to try the transverse engine setup to suit it. The pinions and crown wheel are really stout items designed using the equations found in the Manual gearbox design book by Alec Stokes (ISBN 0 7506 0417 4). That was a few years of my life I won't be able to get back!
For the last 6 months during my morning commute into work I have been stopping at my local supermarket and collecting a couple of big packing boxes from the nightstack = free materials. I am intending to make a plug for the doors that is finally profiled by the router. I made a small test block by gluing sheets of corrogated cardboard together with PVA.
Using a 25mm diameter Kutzall ball spinning at insane rpm (https://kutzall.com/collections/sphere/ ... -1-4-shaft) I cut a test profile into the block. It looks workable, the body filler final skin of the plug should bond nicely to it - will cover the test piece this weekend.
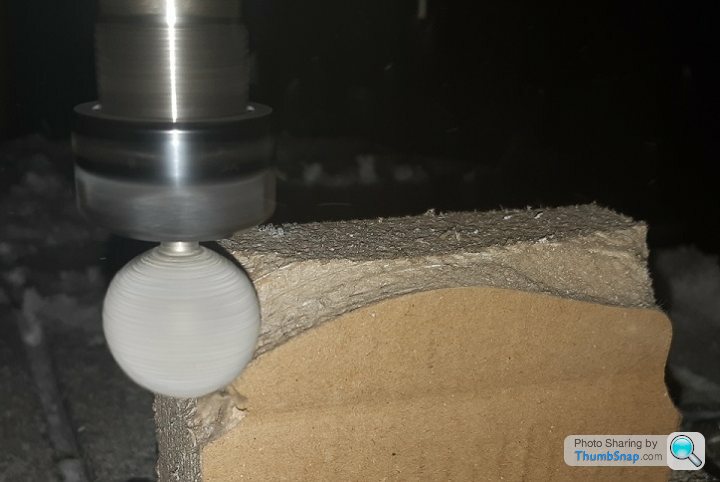
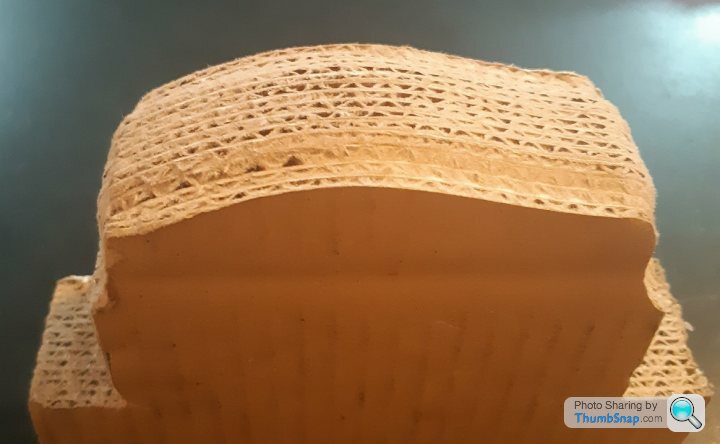
May not look like much, but it is proof of concept - I really don't want to machine big blocks of urethane or polystyrene foam.
Using a 25mm diameter Kutzall ball spinning at insane rpm (https://kutzall.com/collections/sphere/ ... -1-4-shaft) I cut a test profile into the block. It looks workable, the body filler final skin of the plug should bond nicely to it - will cover the test piece this weekend.
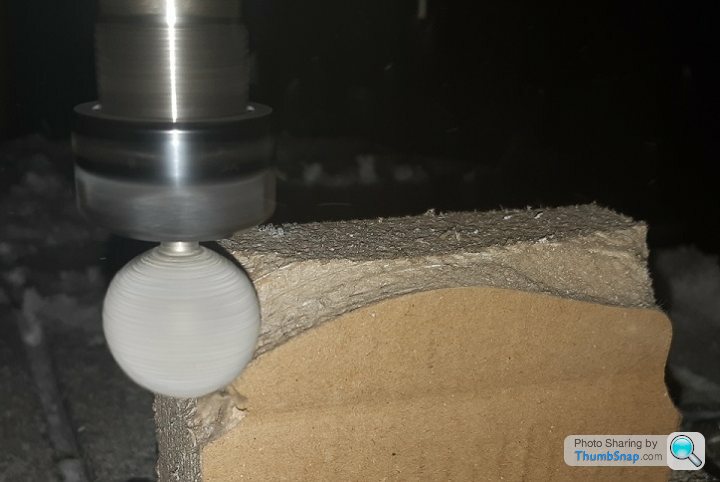
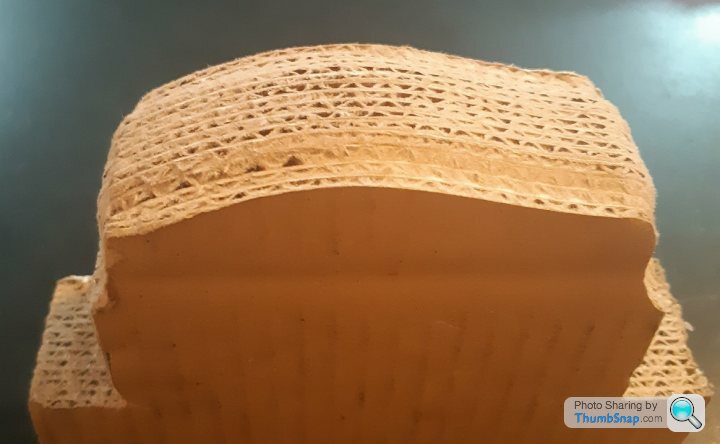
May not look like much, but it is proof of concept - I really don't want to machine big blocks of urethane or polystyrene foam.
F1natic said:
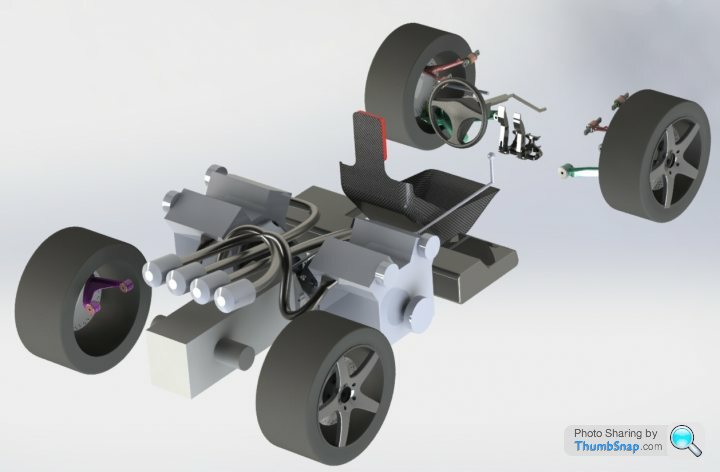
Not able to get much done this weekend due to work commitments - have layed out some of the interior ergonomics ahead of the full scale cabin mockup.
Got some 3D prints due off in a few hours.

Hi, good question. I was initially considering bolting both engines to a common output cog, but running one engine backwards messes with its cam tensioner. So to make as much of the setup factory stock they both spin anticlockwise looking at the flywheel. Since the drive runs through bevel gears and they oppose each other, they twist the transaxle input shaft clockwise as per the corvette installation.
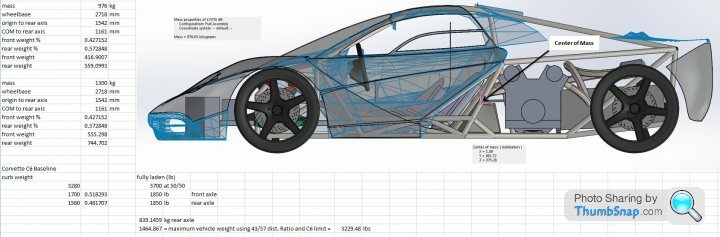
Been running multiple iterations of chassis tubing to match loads and positions - everything is slotting in nicely after 743 attempts. The rolling chassis gokart is looking to be around 976kg with no bodywork. Weight distribution is coming out around 43f/57r.
Edited by F1natic on Wednesday 11th September 12:45
F1natic said:
For the last 6 months during my morning commute into work I have been stopping at my local supermarket and collecting a couple of big packing boxes from the nightstack = free materials. I am intending to make a plug for the doors that is finally profiled by the router. I made a small test block by gluing sheets of corrogated cardboard together with PVA.
Using a 25mm diameter Kutzall ball spinning at insane rpm (https://kutzall.com/collections/sphere/ ... -1-4-shaft) I cut a test profile into the block. It looks workable, the body filler final skin of the plug should bond nicely to it - will cover the test piece this weekend.
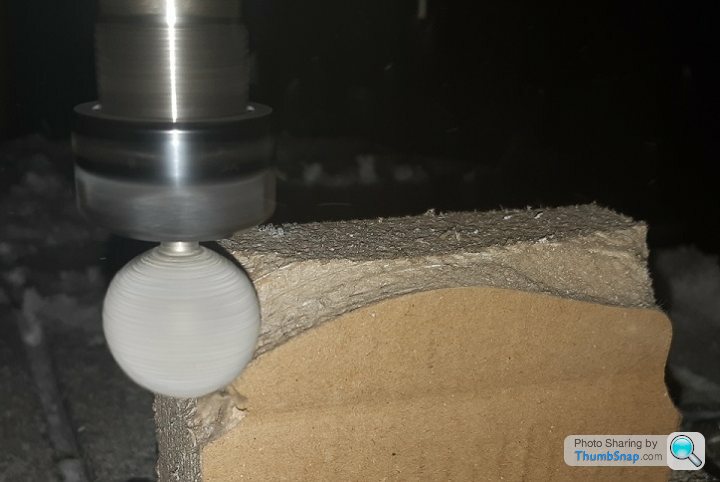
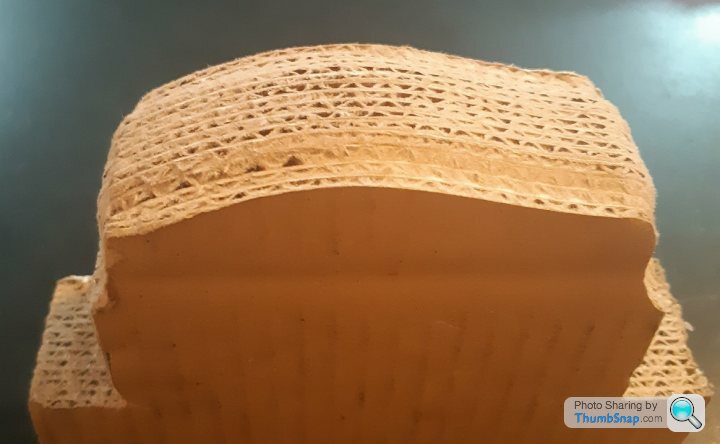
May not look like much, but it is proof of concept - I really don't want to machine big blocks of urethane or polystyrene foam.
Maybe you could think about bonding a layer of fibreglass tissue to the buck before you shape with filler, to provide a more solid base. The resin will soak into the cardboard and strengthen the outer few mm too.Using a 25mm diameter Kutzall ball spinning at insane rpm (https://kutzall.com/collections/sphere/ ... -1-4-shaft) I cut a test profile into the block. It looks workable, the body filler final skin of the plug should bond nicely to it - will cover the test piece this weekend.
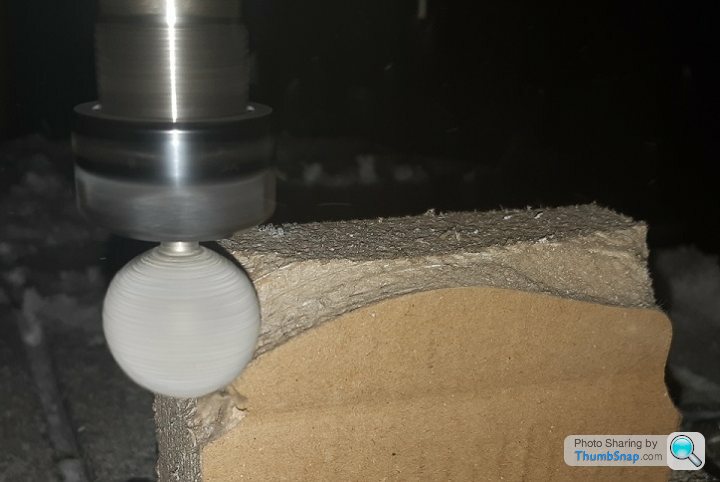
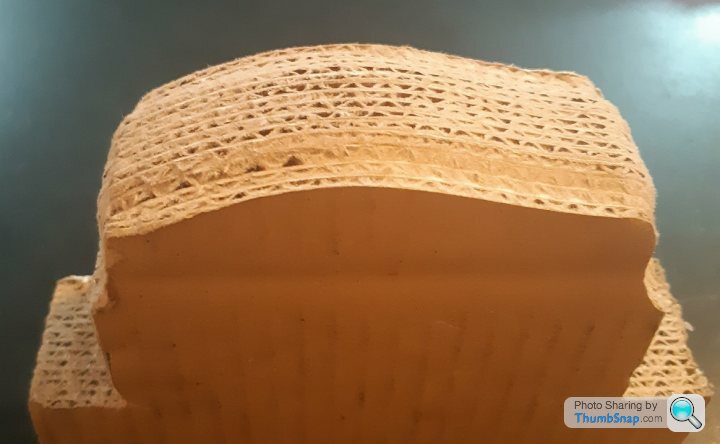
May not look like much, but it is proof of concept - I really don't want to machine big blocks of urethane or polystyrene foam.
Edited by Astacus on Wednesday 11th September 14:14
bern said:
Having said that! I'd have to put something like this on top of it and it's still a tribute to Bruce. Win, win!
What about when it rains??? No issue if you keep it pegged! Bruce and his team knew how to make them right, form follows function. I still can't make it through the McLaren film by Roger Donaldson with a dry eye. I grew up in NZ in the 70's with Canam toy cars - I think it seriously programmed my brain as to what a car should look like. For a road car application it needs better crash structures. Cheers!Astacus said:
Maybe you could think about bonding a layer of fibreglass tissue to the buck before you shape with filler, to provide a more solid base. The resin will soak into the cardboard and strengthen the outer few mm too.
Nice idea, thanks. I will give that a try on some of the half scale tooling block trials.Edited by F1natic on Wednesday 11th September 18:47
Following.
Im in the camp for ditch two engines. Really doesn't seem a good idea but happy to be proven wrong. I get the wanting a v12 thing but if that's the case get a v12. If youre dead set on a twin v6 setup maybe a twin VR6 may be a better alternative. Smaller packaging and sound great.
Just to add as well. I really want to see this work. Good luck and just know there are people counting on you now.
Im in the camp for ditch two engines. Really doesn't seem a good idea but happy to be proven wrong. I get the wanting a v12 thing but if that's the case get a v12. If youre dead set on a twin v6 setup maybe a twin VR6 may be a better alternative. Smaller packaging and sound great.
Just to add as well. I really want to see this work. Good luck and just know there are people counting on you now.
Edited by Michaelbailey on Thursday 19th September 15:22
https://www.roadandtrack.com/car-culture/car-desig...
By total chance I just found the article above - ironically it turns out that during the concept stage the Mclaren roadcar team had discussed using 2 x NSX V6 engines......
By total chance I just found the article above - ironically it turns out that during the concept stage the Mclaren roadcar team had discussed using 2 x NSX V6 engines......
F1natic said:
https://www.roadandtrack.com/car-culture/car-desig...
By total chance I just found the article above - ironically it turns out that during the concept stage the Mclaren roadcar team had discussed using 2 x NSX V6 engines......
Oh thanks for linking, will save that for a quiet evening. By total chance I just found the article above - ironically it turns out that during the concept stage the Mclaren roadcar team had discussed using 2 x NSX V6 engines......
What are your thoughts on predicted weight sans body? Happy or disappointed?
Ahem, unfortunately the weight keeps climbing - I have been adding a lot of extra tubes to the chassis. I have been watching Side Pole Crash Tests on you tube and am beefing up the passenger protection (no worries for the driver as they are so far from the crush zone).
I have a rear axle limit that I cannot exceed of 840 KG (fully laden Corvette is 3700lbs split 50/50 so certifier won't sign off if the vehicle axle load exceeds that). With the weight distribution of 43/57 that gives a total laden mass of 1473 kg. I am targeting 1300 but my certifier (www.fraser.co.nz) thinks that roadgoing body work will really push that target. While I do the chassis development the car will just be a exo spaceframe car much like the 3 balls track monster shown below - that will hopefully give me a chance to garner some assistance with carbon fibre panels.
Since the go kart is coming in at just under 1000kg, I have 300 kg of bodywork allowance - I am trying to be realistic as this is my first build (that's an oxymoron). Mclaren had a development budget of 8.5 million GBP, mine is a little lower so I will be happy if the wheels turn! I agree with Gordon Murray that weight to power is a critical factor - but for praticality I have to forego some of extremely low weight goals for "doable" & "affordable". I think on the performance to price factor it should be fairly well placed compared to other sportscars. Also as this is a development vehicle I don't see it ever being "finished" and therefore the final weight doesn't exist!
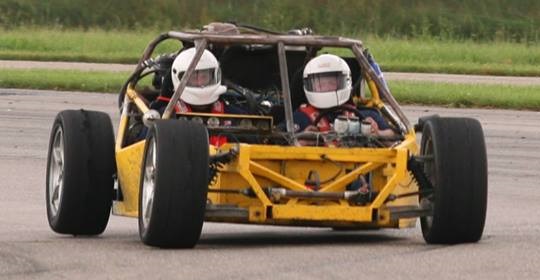
I have a rear axle limit that I cannot exceed of 840 KG (fully laden Corvette is 3700lbs split 50/50 so certifier won't sign off if the vehicle axle load exceeds that). With the weight distribution of 43/57 that gives a total laden mass of 1473 kg. I am targeting 1300 but my certifier (www.fraser.co.nz) thinks that roadgoing body work will really push that target. While I do the chassis development the car will just be a exo spaceframe car much like the 3 balls track monster shown below - that will hopefully give me a chance to garner some assistance with carbon fibre panels.
Since the go kart is coming in at just under 1000kg, I have 300 kg of bodywork allowance - I am trying to be realistic as this is my first build (that's an oxymoron). Mclaren had a development budget of 8.5 million GBP, mine is a little lower so I will be happy if the wheels turn! I agree with Gordon Murray that weight to power is a critical factor - but for praticality I have to forego some of extremely low weight goals for "doable" & "affordable". I think on the performance to price factor it should be fairly well placed compared to other sportscars. Also as this is a development vehicle I don't see it ever being "finished" and therefore the final weight doesn't exist!
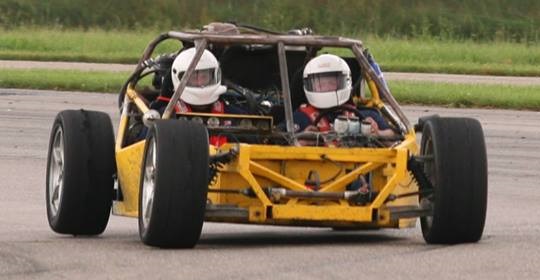
Edited by F1natic on Saturday 21st September 22:05
at 1300kg + 2 passengers at 86.5 kg each I am at the rear axle limit.
As an example of doing it the other way round - check out 6:33
https://www.youtube.com/watch?v=UfpQTAFoTU4
Hotrod lost 893 lbs (382 Kg) of bodywork on a C4 - that had air con and stereos and carpets etc.
As an example of doing it the other way round - check out 6:33
https://www.youtube.com/watch?v=UfpQTAFoTU4
Hotrod lost 893 lbs (382 Kg) of bodywork on a C4 - that had air con and stereos and carpets etc.
Gassing Station | Readers' Cars | Top of Page | What's New | My Stuff