540HP NA 7L V12 3 seater
Discussion
I am pulling a 2006 Maserati Quattroporte Duoselect drivetrain apart at the moment, it has a bellhousing with internal power transfer like you need which then sends it on via a torque tube to the rear mounted gearbox/diff transaxle.
A pair of those bellhousing/internals and such a gearbox (they can be converted to manual rather than paddle) could be an alternative option for you. Very sturdy set up.
If you need any pics/dims let me know.
A pair of those bellhousing/internals and such a gearbox (they can be converted to manual rather than paddle) could be an alternative option for you. Very sturdy set up.
If you need any pics/dims let me know.
Edited by PAUL.S. on Monday 18th December 12:58
Using the OP's previous diagram, this bellhousing drive assembly could take power off each engines clutch and transfer it solidly to the central differential unit shown on that drawing, via the splined ends of each internal transfer shaft (shown removed from the bell housing below it), which normally mates to the torque tube on the Maserati. That car also uses a nice, small twin plate clutch which could be fitted to adapted Honda flywheels. Also has hydraulic actuation of the clutch which could be modulated if required.
Save a lot of engineering of those internal parts required of that bare cast bellhousing and only a simple adapter plate required to mate the Maserati version to the Honda blocks.
This one is now surplus to my requirements but yet to go on ebay
and I am sure I could find another as well to fit into a shipping box.
The Maserati rear transaxle is also very similar to the one shown, and is also available if needed.
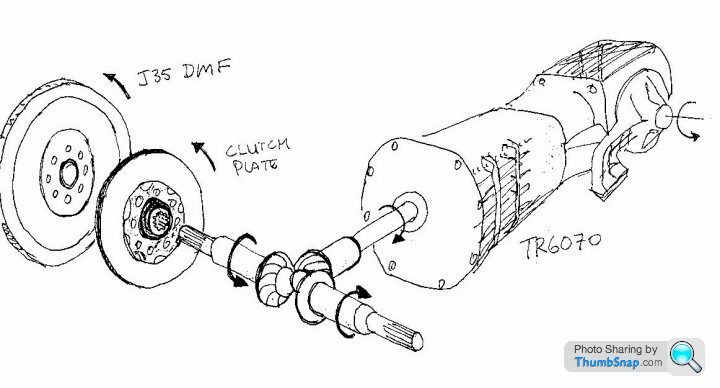
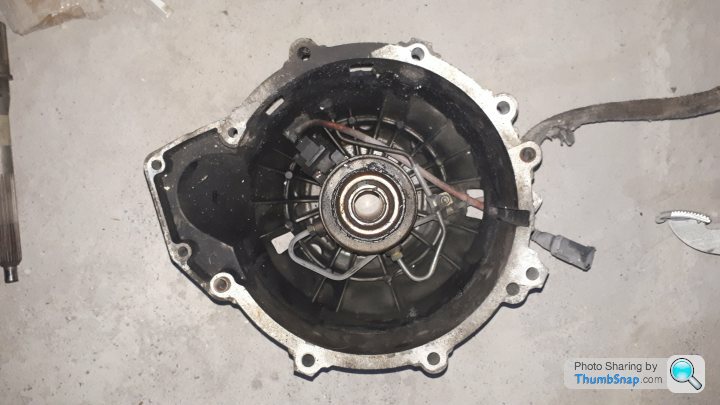
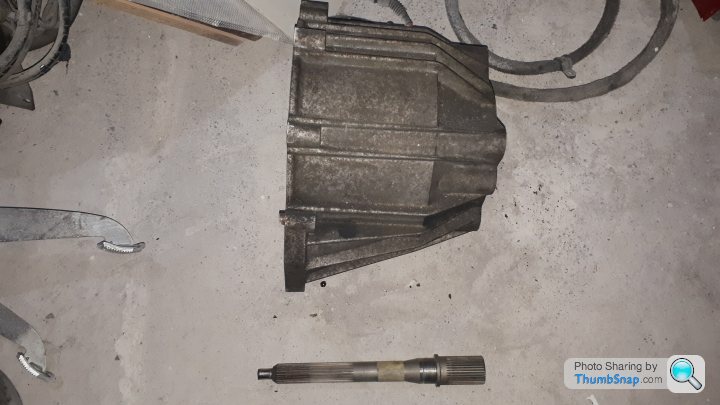
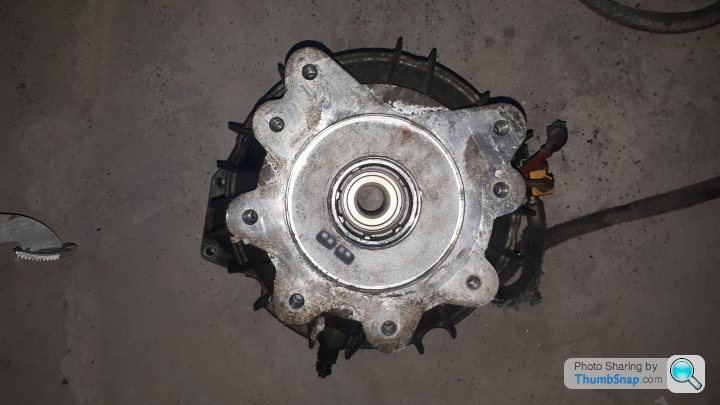
Save a lot of engineering of those internal parts required of that bare cast bellhousing and only a simple adapter plate required to mate the Maserati version to the Honda blocks.
This one is now surplus to my requirements but yet to go on ebay

The Maserati rear transaxle is also very similar to the one shown, and is also available if needed.
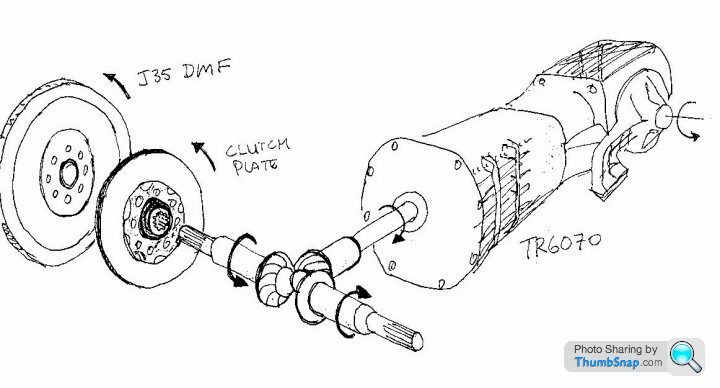
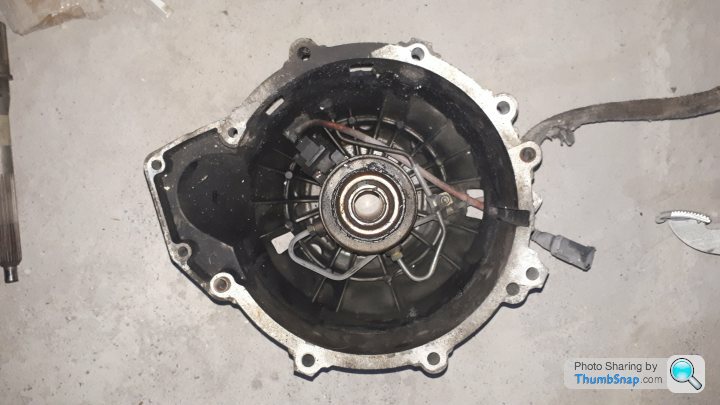
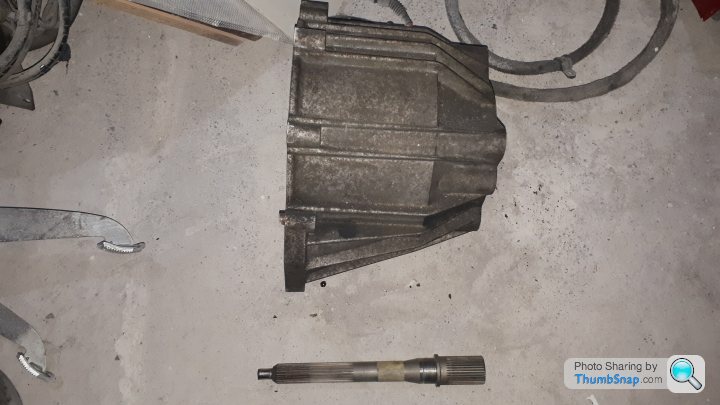
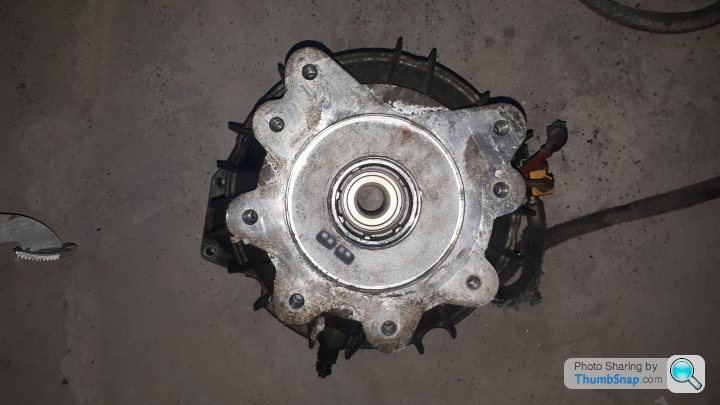
Edited by PAUL.S. on Wednesday 20th December 14:16
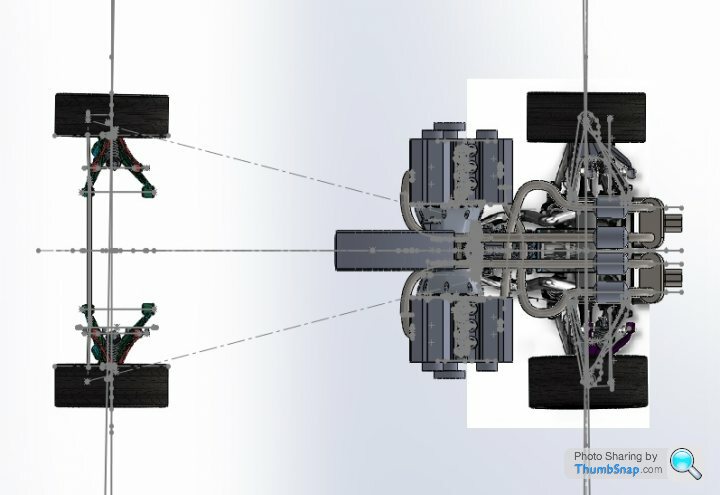
Hi Paul,
Thanks for your post, I greatly appreciate the info. Have spent a few days having a really deep think about this as a practical alternative method since it is equivalent to the layout I am using for the crownwheel. Off the shelf parts are always a preference when doing something as weird as this project, but there comes a point when all those standard parts have to be mated together with custom parts.
Due to the 344Nm torque on each pinion they need stout bearings for longevity and precise locating of meshing faces. Given the very tight physical width envelope I have painted myself into with the T-box I am fairly fixed on the pinion shafts and gears being integral units. For example the "diff head" is only 140mm wide.
I agree these parts have merit, and in a fresh sheet design could work well. I am not certain the twin engine concept is going to work out long term, which is why the chassis design is easily reconfigurable to a single twin turbo V6 or fully electric if necessary.
No problem, this possible solution only occurred to me when I saw your cast bellhousing and suddenly clicked that the one off this Maserati was a similar size and had nice big bearing holding that shaft into it. The cogs either side of your diff could also be directly splined onto the end of each shaft, narrowing the assembly, especially if you shortened that protrusion coming out of the back of the bellhousing.
The diff holder you cast could bolt directly to the ends of each bellhousing using the mountings already in place for the torque tube.
Not a sales pitch, but while it is here I can take any measures or any further pics you may need to see if it is an option for you.
Here is another already on ebay in the UK if you wanted a pair to be shipped to NZ you could have it delivered to me and I would then send them both on. You can have mine for £300 plus shipping
https://www.ebay.co.uk/itm/166107967962?hash=item2...
The diff holder you cast could bolt directly to the ends of each bellhousing using the mountings already in place for the torque tube.
Not a sales pitch, but while it is here I can take any measures or any further pics you may need to see if it is an option for you.
Here is another already on ebay in the UK if you wanted a pair to be shipped to NZ you could have it delivered to me and I would then send them both on. You can have mine for £300 plus shipping
https://www.ebay.co.uk/itm/166107967962?hash=item2...
Edited by PAUL.S. on Thursday 21st December 23:56
phalanxs said:
One thing I wonder about this build, is why did you choose to use two Honda clutches before the crownwheel, instead of say putting the crownwheel first and using a TR-6060 with its original cluch?
Cheers
At a guess, one reason is because a single clutch means the engines are permanently linked, even when cranking / starting - that plus the significantly increased rotational inertia at idle could be an issue.Cheers

/me waits for the OP to point out I'm posting b

phalanxs said:
One thing I wonder about this build, is why did you choose to use two Honda clutches before the crownwheel, instead of say putting the crownwheel first and using a TR-6060 with its original cluch?
Cheers
Packaging is an important reason, the 2 bellhousings nestle nicely into a space that accomodates the standard corvette input shaft, adding anything to the front of the transaxle kicks the trans back enormously, I do not want to go down the HTT Pléthore path.Cheers

2 clutches also allow me to isolate 1 engine completely, and make the car a little more commuting friendly.
AW111 said:
At a guess, one reason is because a single clutch means the engines are permanently linked, even when cranking / starting - that plus the significantly increased rotational inertia at idle could be an issue.
/me waits for the OP to point out I'm posting b
ks.
True on the permanent linking being something I intend to avoid. Crank harmonics can cause loads many times the rated average crank torque which could cause failures if cranks are bolted directly together or with downstream geartrain components. I have to tap the power off at a right angle so the main reason for doing it my oddball way with 2 DMF's initially is to isolate the gearset from the crank vibrations. A well designed one piece V12 crank resolves these fluctuations within itself, 2 independant motors don't. /me waits for the OP to point out I'm posting b

Rotational inertia at idle is not a factor, in fact it will help with moving off as car should be fairly stall proof given the 2 x heavy flywheels. Future track car development could use aluminium flywheels but my goals are road focused initially so using as many OEM parts as possible.
Progress on the build table has stalled temporarily but should get underway shortly. The donor V6 has been pulled (it sounded great with no pipes, need to upload that video to my you tube page). With drive shafts removed I could fully rev the engine safely with no load, the stock ECU and drive by wire throttle appear quite sluggish. Will compare with the test engine response when running speeduino/direct human controlled throttle plate, I get the feeling the factory ECU is muting the response quite strongly. Time will tell!
Edited by F1natic on Friday 12th January 05:53
F1natic said:
Great engines, can't argue with Horacio Pagani's choice, but my budget is a little more modest and therefore locally available Honda it is!
This surprises me somewhat. I'd happily believe that one of those old merc engines could be had for a couple of thousand, but equally I'd happily believe you if you told me any one of your custom made pieces (that bell housing or plenum casting for example) cost five thousand or more to design and make as a one off, and that whether an engine costs one thousand or five thousand would be little more than a rounding error in the overall project cost.Clearly my estimation of what stuff costs is a long way out.
Anyway, your work continues to astonish, bravo!
The project hiatus is drawing to a close and in preparation for some actual physical progress the full spaceframe was 3D printed at 1/6th scale to help visualise tubing assembly sequence. It was at this point that the potential leg trap was noticed.
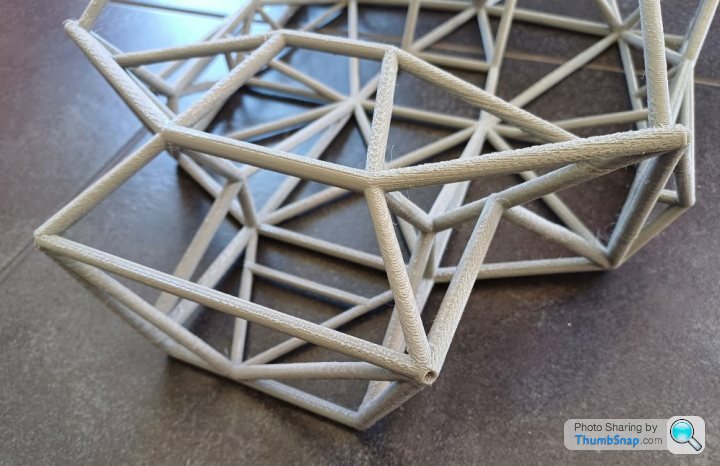
Rotating the structure around in ones hands gives more insight than a 2D screen view and the vulnerability of the footwell upper crosstube to buckling in a side impact was not obvious until it was printed out. The tubing I am using is typically used in sprint car chassis fabrication, the linked video is a superb demonstration of what happens to them in impacts; Ouch.
https://youtu.be/WOsoNGwDTcg?si=O9M8VdTXZlH9sHNi&a...
After some node repositioning the structure is now more resistant to sidecrush. Every accident is different and a nose shunt like Flemke's one is probably the most likely due to other road users not seeing the car, however in the case of a rollover/side impact/severe frontal crash the structure has to be well braced to work correctly. The aluminium nose tube structure is intended to absorb crash energy before it reaches the stiffer steel spaceframe. The aluminium radiator mounting frame will aid the crash structure (originally was going to incorporate a bumper bar but it is redundant) and the front suspension tearing off in the typical offside frontal crash should also not damage the drivers legs.
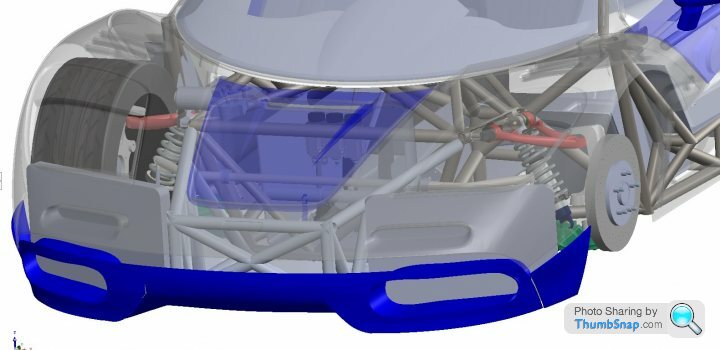
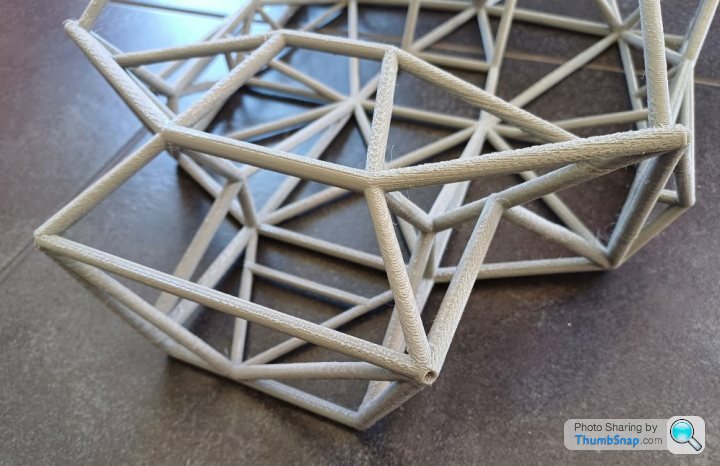
Rotating the structure around in ones hands gives more insight than a 2D screen view and the vulnerability of the footwell upper crosstube to buckling in a side impact was not obvious until it was printed out. The tubing I am using is typically used in sprint car chassis fabrication, the linked video is a superb demonstration of what happens to them in impacts; Ouch.
https://youtu.be/WOsoNGwDTcg?si=O9M8VdTXZlH9sHNi&a...
After some node repositioning the structure is now more resistant to sidecrush. Every accident is different and a nose shunt like Flemke's one is probably the most likely due to other road users not seeing the car, however in the case of a rollover/side impact/severe frontal crash the structure has to be well braced to work correctly. The aluminium nose tube structure is intended to absorb crash energy before it reaches the stiffer steel spaceframe. The aluminium radiator mounting frame will aid the crash structure (originally was going to incorporate a bumper bar but it is redundant) and the front suspension tearing off in the typical offside frontal crash should also not damage the drivers legs.
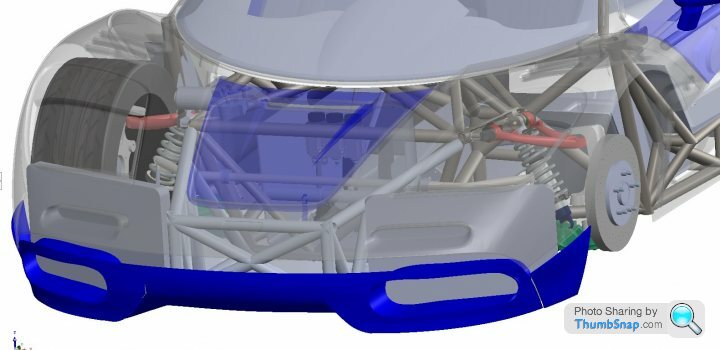
Had a bit of fun today cowtipping the donor shell using the old EK civic tow vehicle (which is nicknamed "the coackroach" because it refuses to die). Used an engine crane to lift the shell to just under the point of balance. Logs and old wheels make excellent packers.
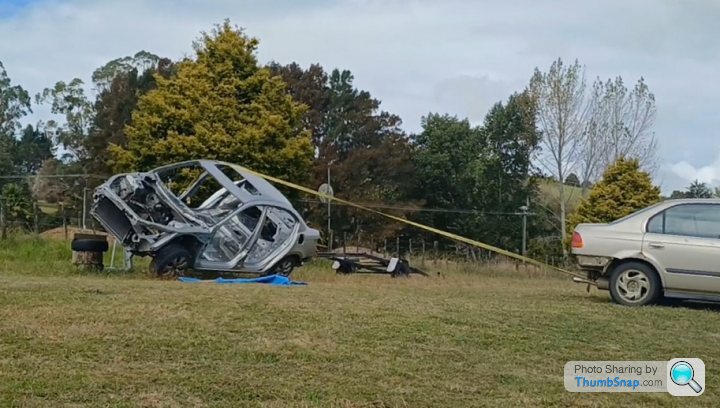
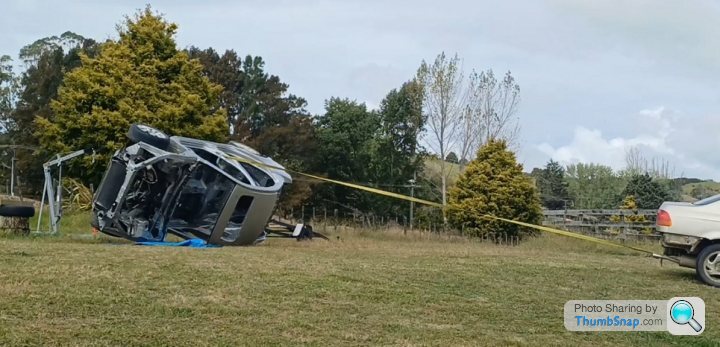
Have stripped out all the under gubbins shown here, which is a much easier task when everything is on it's side as the dirt doesn't fall in your face. The mufflers will most likely be used for the test mule, the evap system and heatshields will be incorporated in the final build and the subframes kept as spare parts for the daily driver.
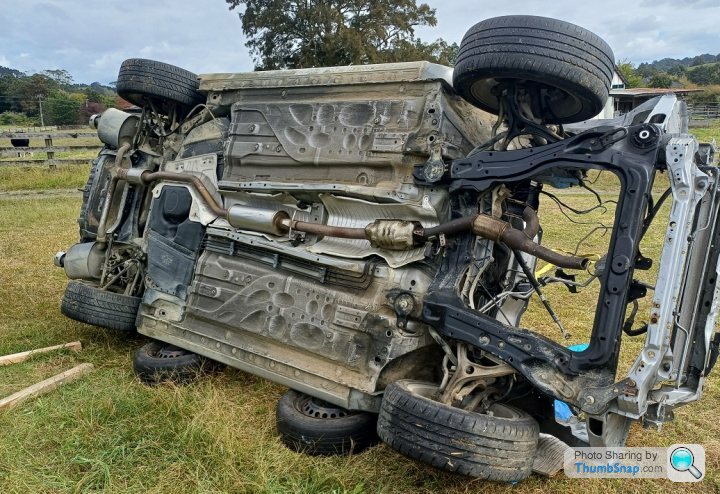
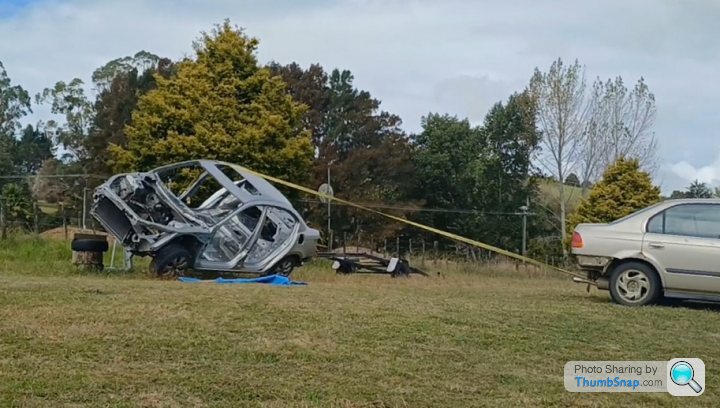
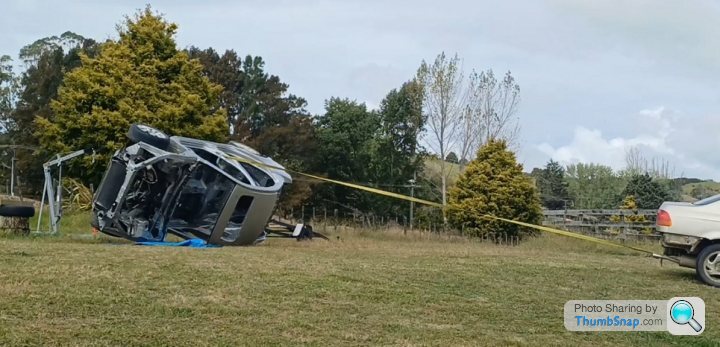
Have stripped out all the under gubbins shown here, which is a much easier task when everything is on it's side as the dirt doesn't fall in your face. The mufflers will most likely be used for the test mule, the evap system and heatshields will be incorporated in the final build and the subframes kept as spare parts for the daily driver.
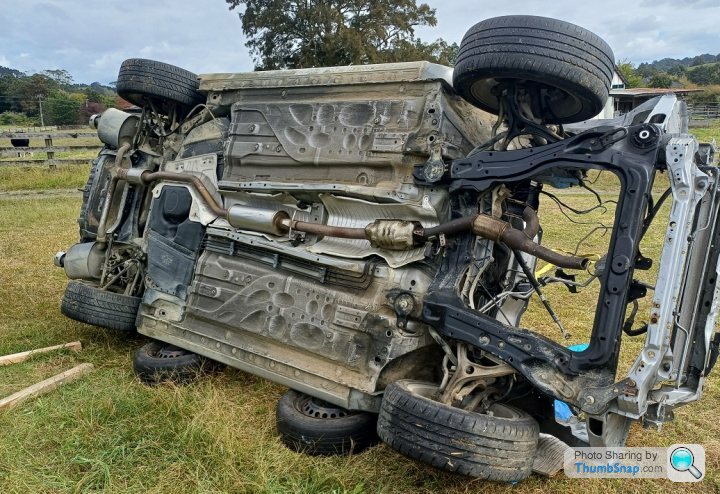
Edited by F1natic on Sunday 7th April 09:45
Gassing Station | Readers' Cars | Top of Page | What's New | My Stuff