Vini – the Powerflex V8 Mini
Discussion
So now to the rear.
Because EDM know as much about Impreza’s as they do Minis they felt that the rear subframe assembly from the 2005 Spec C Impreza would give us locations of some important geometry controlling suspension arms.
The rear carrier assembly has the diff and most of the suspension mounted on it.
So if they could attach that to the car in the correct place and locate the rear hub tie bars to the body then the diff would be good enough (and is available in lots of ratios as well as super strong motorsport versions) and a lot of the geometry would already be in place.
Of course the rear of the Mini shell is design to carry very little in the way of weight and being front wheel drive has no space for diffs and drive shafts but more importantly no room for rear suspensions struts.
An awful lot of the rear was going to need to be changed and mountings made in what was fresh air.
Rear tie bar mounting. This would late be tied into the rollcage
|
[url]
|
I can't begin to explain how difficult this location and positioning work is

Because EDM know as much about Impreza’s as they do Minis they felt that the rear subframe assembly from the 2005 Spec C Impreza would give us locations of some important geometry controlling suspension arms.
The rear carrier assembly has the diff and most of the suspension mounted on it.
So if they could attach that to the car in the correct place and locate the rear hub tie bars to the body then the diff would be good enough (and is available in lots of ratios as well as super strong motorsport versions) and a lot of the geometry would already be in place.
Of course the rear of the Mini shell is design to carry very little in the way of weight and being front wheel drive has no space for diffs and drive shafts but more importantly no room for rear suspensions struts.
An awful lot of the rear was going to need to be changed and mountings made in what was fresh air.
Rear tie bar mounting. This would late be tied into the rollcage

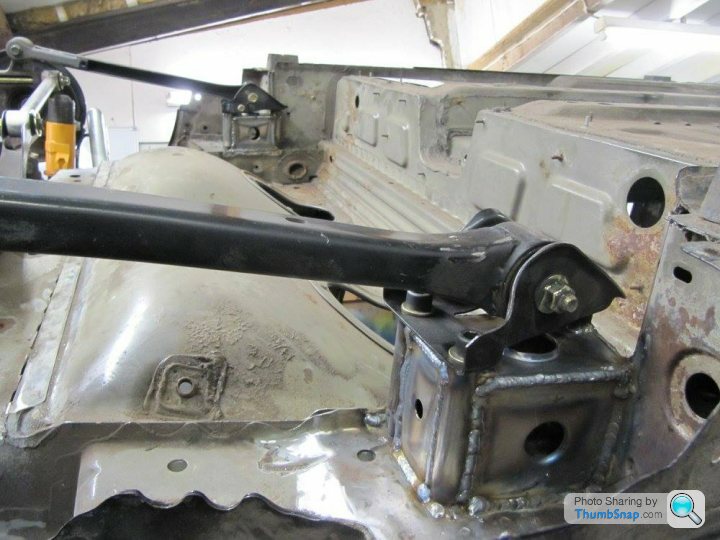

I can't begin to explain how difficult this location and positioning work is

This is where some serious CAD work was going to be required.
Cardboard Aided Design is skill possessed by the few and envied by the many.
The rear wheel arches needed room for struts and towers and had to be fabricated in the right position to get the rear geometry correct as well as allowing the shock length required for the amount of wheel travel we had designed in.


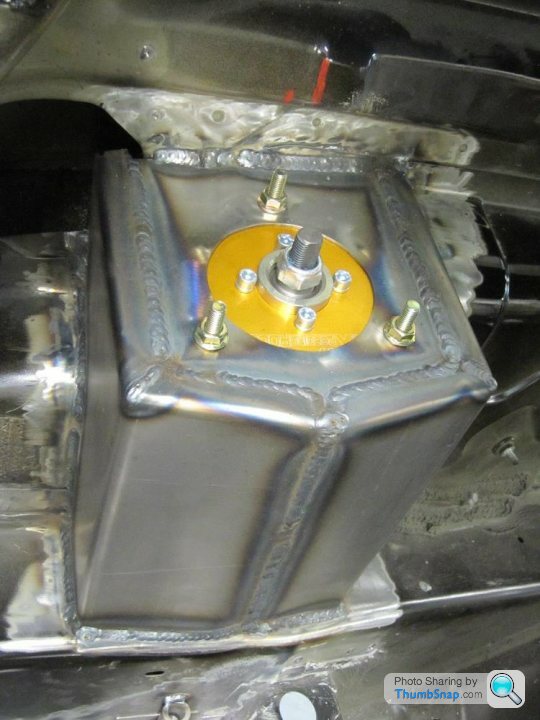
You can see the floor strengthening going in for the rear subframe below

These pictures are from a much later stage in the build, but give a clue as to the amount and quality of the work involved.
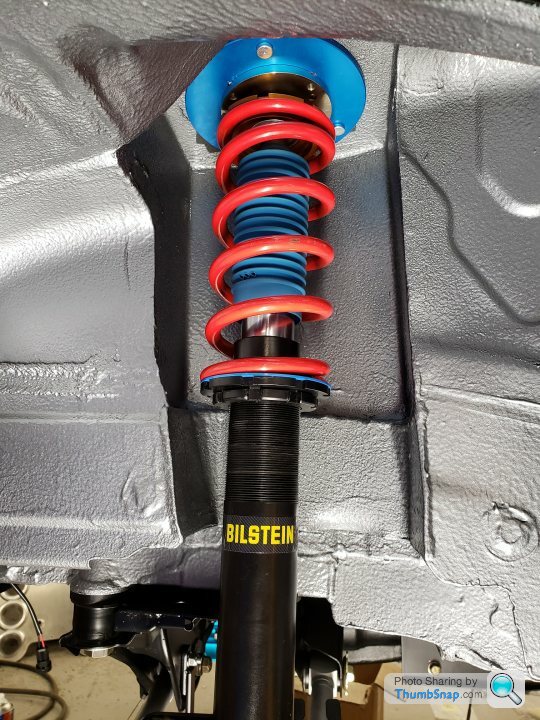
Bilstein built special double adjustable front and rear dampers for the project, of which more later.

Cardboard Aided Design is skill possessed by the few and envied by the many.
The rear wheel arches needed room for struts and towers and had to be fabricated in the right position to get the rear geometry correct as well as allowing the shock length required for the amount of wheel travel we had designed in.


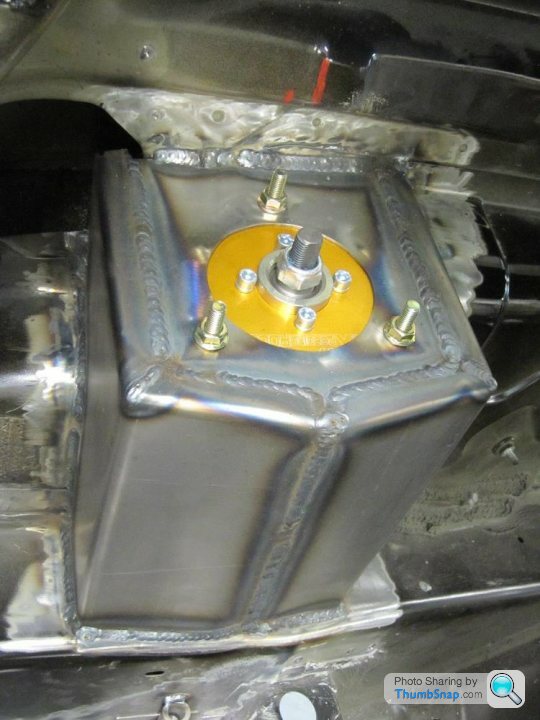
You can see the floor strengthening going in for the rear subframe below

These pictures are from a much later stage in the build, but give a clue as to the amount and quality of the work involved.
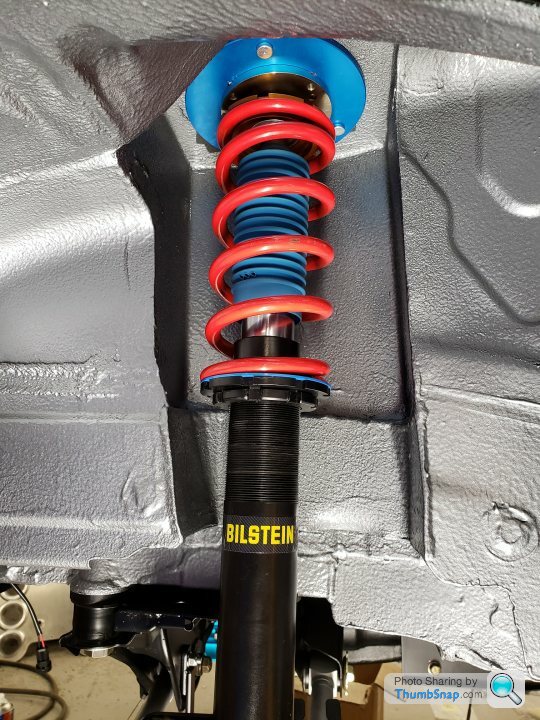
Bilstein built special double adjustable front and rear dampers for the project, of which more later.

Many thanks.
It is a big deal for www.powerflex.co.uk to have commissioned this, but as I say it has got out of control, but in a good way.
I started a trade association for the Performance Aftermarket a few years ago and am on the board of it.
www.paaa.eu.com
It has some prestigious members from the top end of manufacturers and distributors of performance parts in the UK.
We also have a membership section for workshops and tuners that derive their business from the performance aftermarket.
What this has meant is that I have been able to work with companies such as Eibach, Bilstein, Alcon, Cobra, Lifeline, Goodridge, Forge Motorsport, Milltek, ARP, ITG and many others.
They have all wanted to get involved in this project.
Absolutely not in a sponsorship way. I have insisted on paying for all parts supplied but what I have asked is that where we needed something special they pull out all the stops and make something really trick for us, knowing that it would be a showcase for them as well as Powerflex.
So there are a lot of very high quality really special parts on the car that would not normally be available for sale and would probably not be produced if this was not an industry collaboration.
All will be revealed!
It is a big deal for www.powerflex.co.uk to have commissioned this, but as I say it has got out of control, but in a good way.
I started a trade association for the Performance Aftermarket a few years ago and am on the board of it.
www.paaa.eu.com
It has some prestigious members from the top end of manufacturers and distributors of performance parts in the UK.
We also have a membership section for workshops and tuners that derive their business from the performance aftermarket.
What this has meant is that I have been able to work with companies such as Eibach, Bilstein, Alcon, Cobra, Lifeline, Goodridge, Forge Motorsport, Milltek, ARP, ITG and many others.
They have all wanted to get involved in this project.
Absolutely not in a sponsorship way. I have insisted on paying for all parts supplied but what I have asked is that where we needed something special they pull out all the stops and make something really trick for us, knowing that it would be a showcase for them as well as Powerflex.
So there are a lot of very high quality really special parts on the car that would not normally be available for sale and would probably not be produced if this was not an industry collaboration.
All will be revealed!
With front subframe position now fixed, strengthening of the front legs that would carry the weight (and more importantly the torque) of the engine had to be carried out.
These strengthening struts would become an integral part of the roll cage, ensure all loads and stresses are carried by the cage and not the bodyshell.
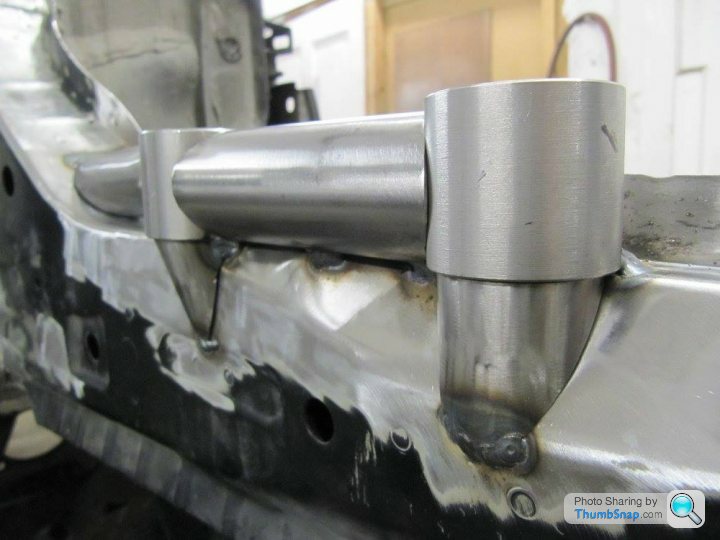
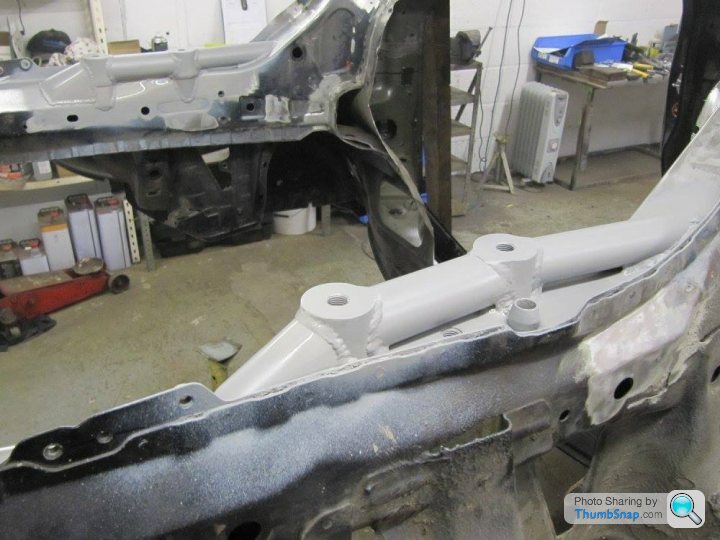
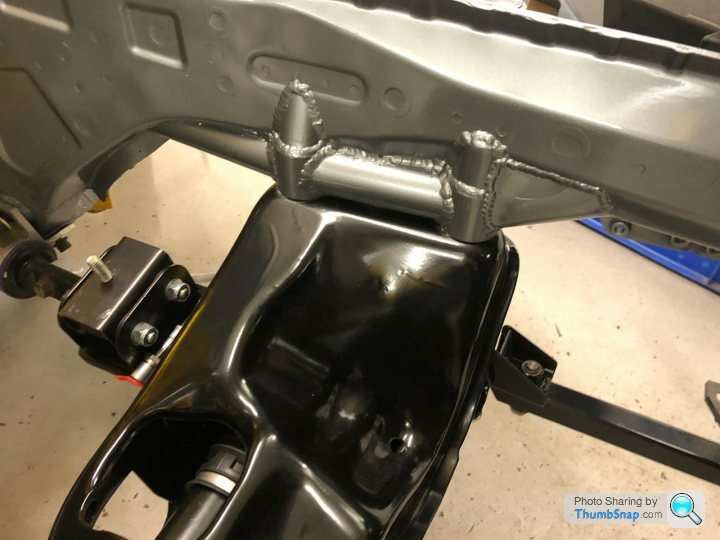
EDM will be glad when they can put the air hacksaw away and get the welder out!
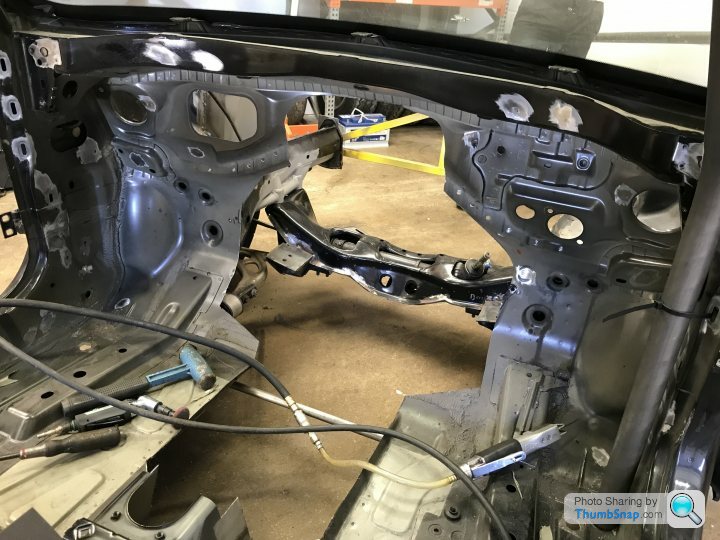
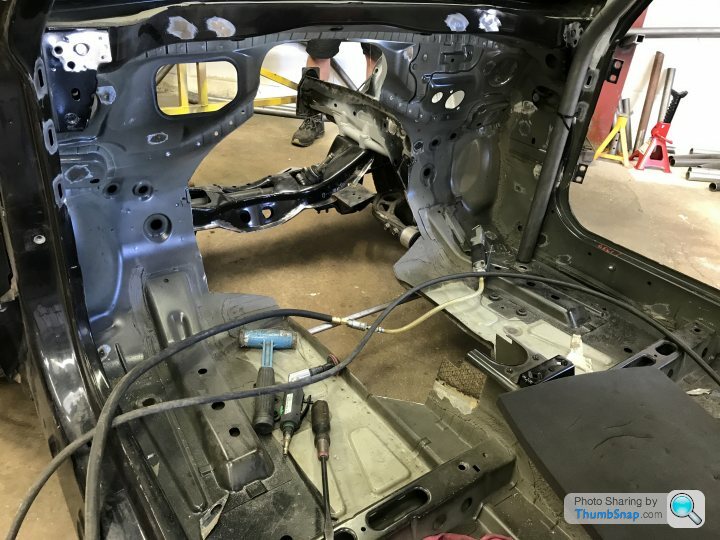
These strengthening struts would become an integral part of the roll cage, ensure all loads and stresses are carried by the cage and not the bodyshell.
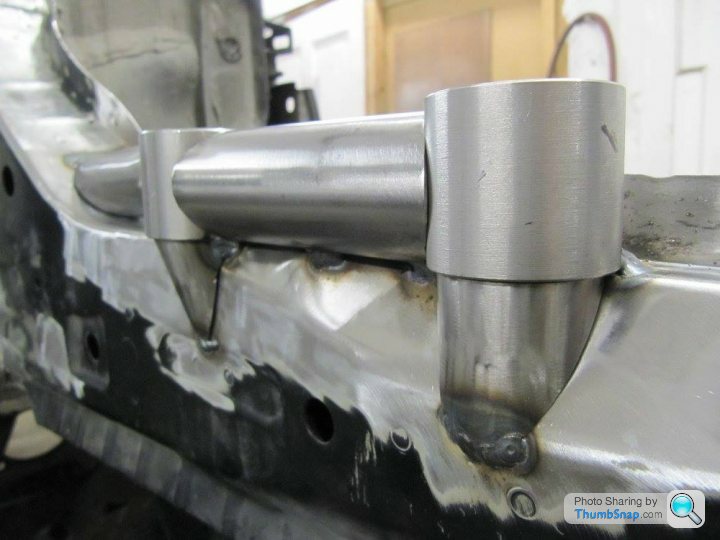
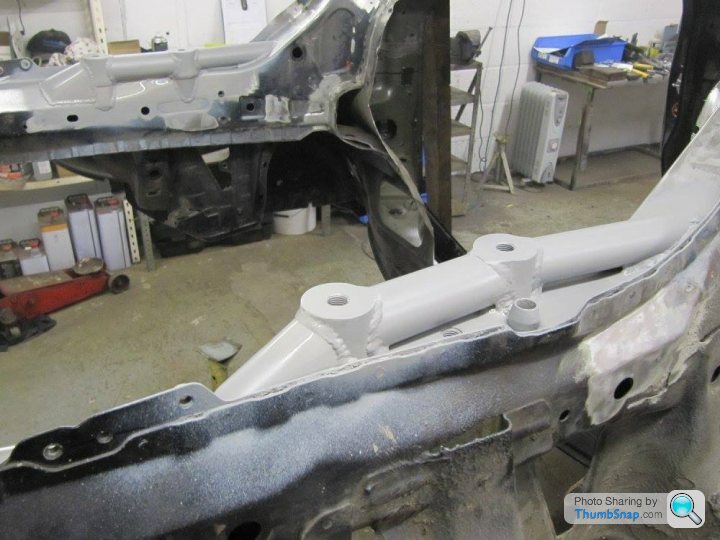
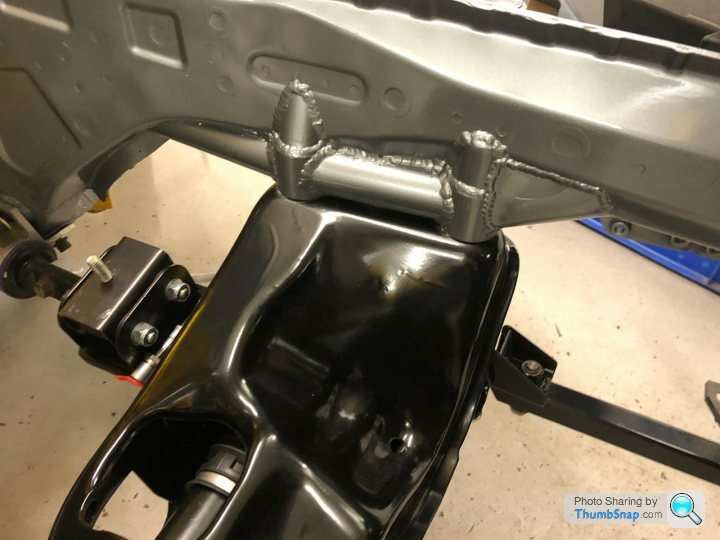
EDM will be glad when they can put the air hacksaw away and get the welder out!
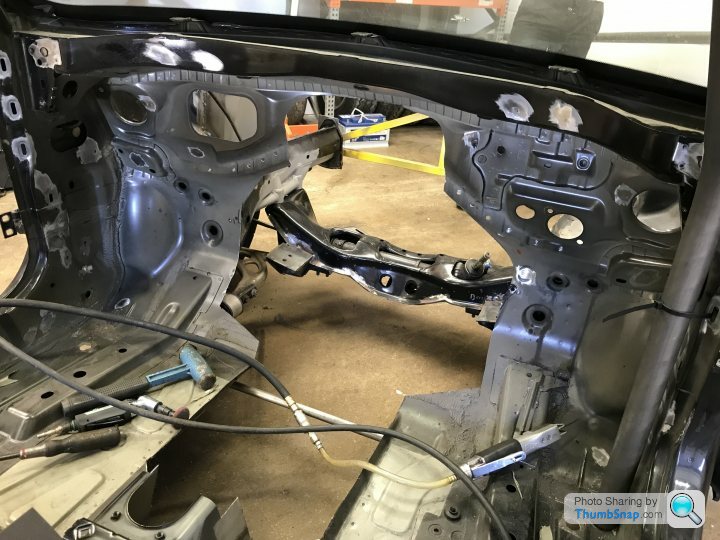
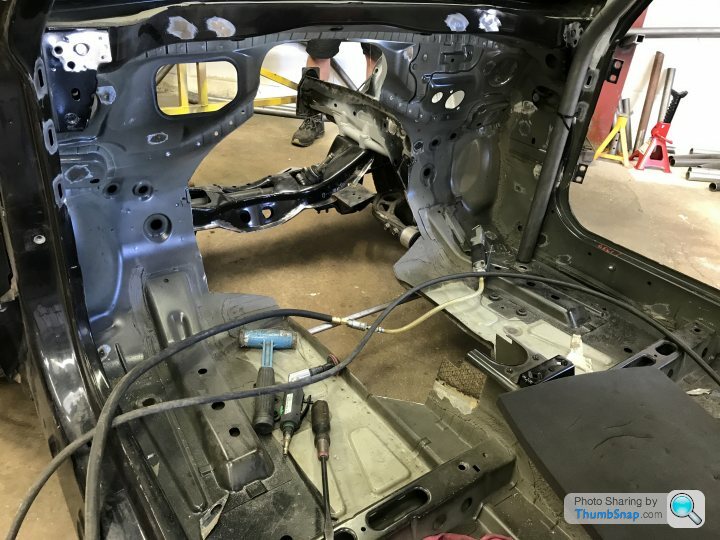
Back to CAD.
The front struts had to be repositioned to accommodate the revised geometry and the special dampers.
Because of what we do at Powerflex, I am an engineer but fabrication is black magic as far as I’m concerned.
This is making something that doesn’t exist and placing it in fresh air in exactly the right position.
But also taking into consideration all the other factors that might influence that component in a years time when final assembly shows up that it isn’t in the right place.
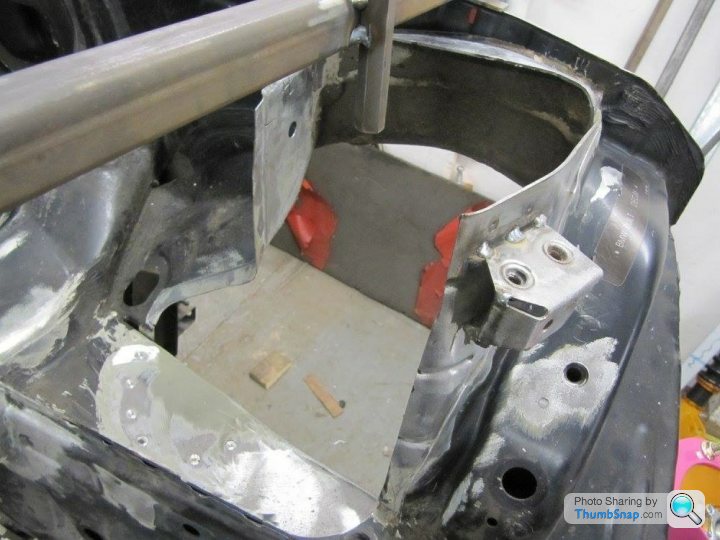
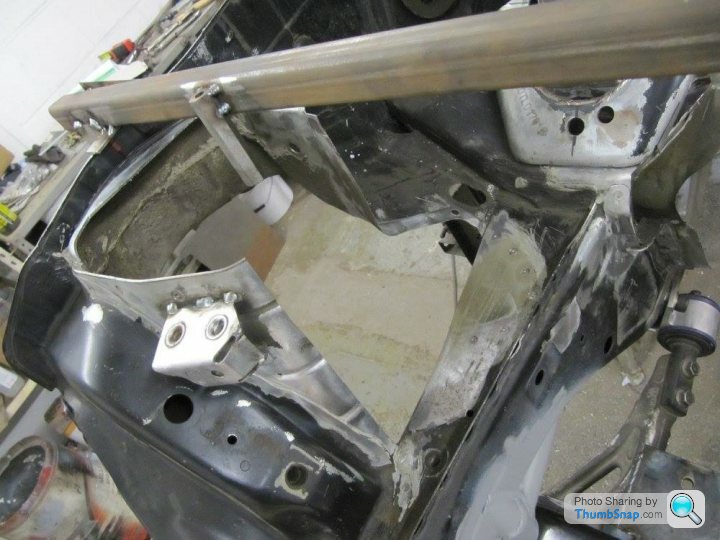
This position would control all of the front geometry and also the location of the entire front end of the car.


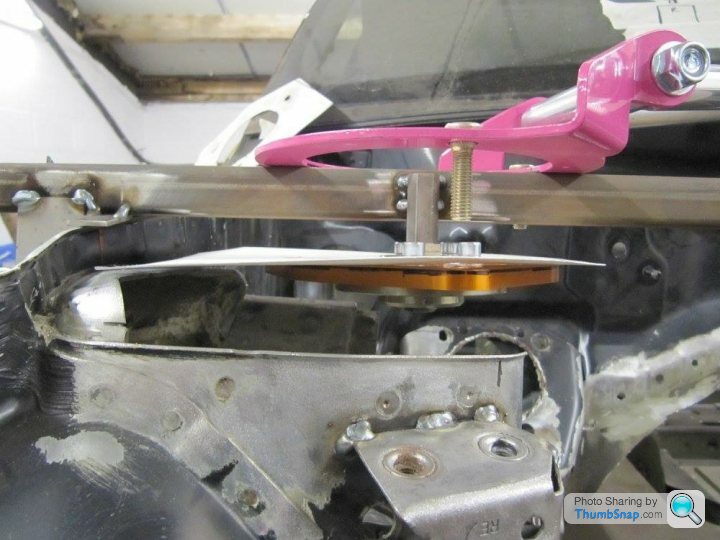
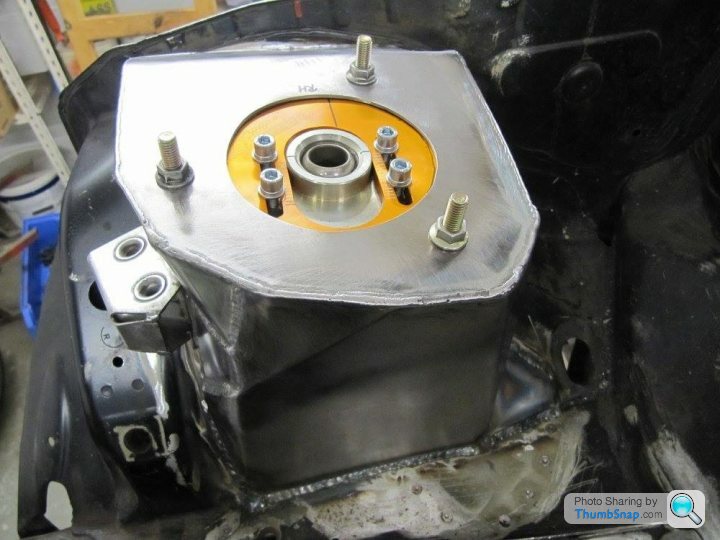
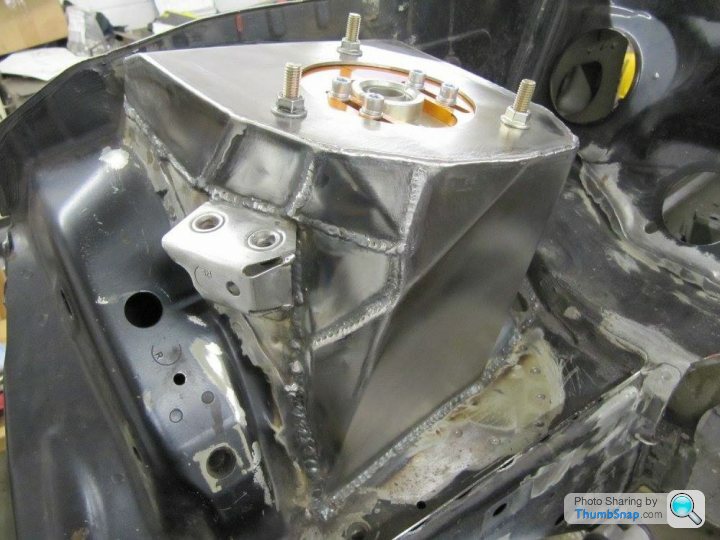
This upper panel positioning is the key to all of the front mounted components.
Radiators (Water, Oil, gearbox, power steering) (diff oil cooler will be mounted at the rear) and their associated mounts
Front panel which controls the light positions and therefore the bonnet
I didn't want bits of angle iron holding the lights and bumper on.
We must use all of the clever and beautifully make plastic mounts that BMW do so well to secure the original Mini parts
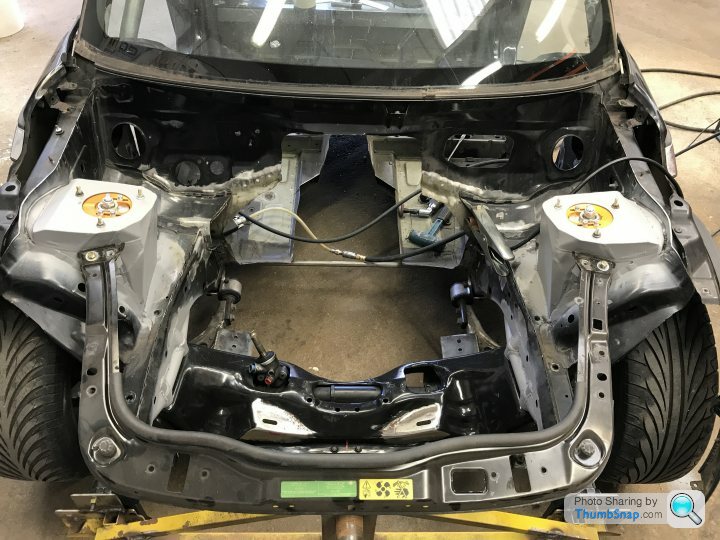
The front struts had to be repositioned to accommodate the revised geometry and the special dampers.
Because of what we do at Powerflex, I am an engineer but fabrication is black magic as far as I’m concerned.
This is making something that doesn’t exist and placing it in fresh air in exactly the right position.
But also taking into consideration all the other factors that might influence that component in a years time when final assembly shows up that it isn’t in the right place.
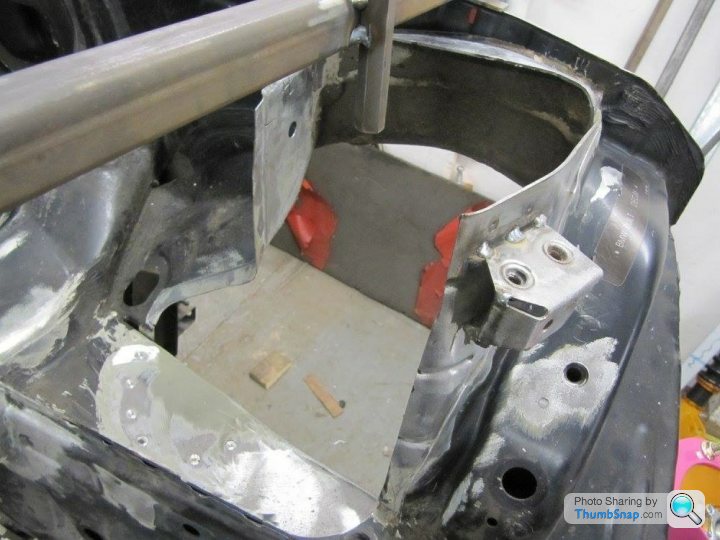
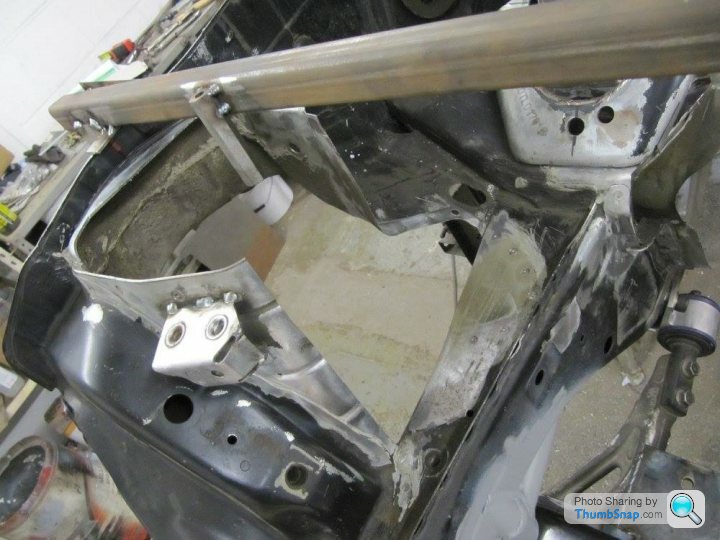
This position would control all of the front geometry and also the location of the entire front end of the car.


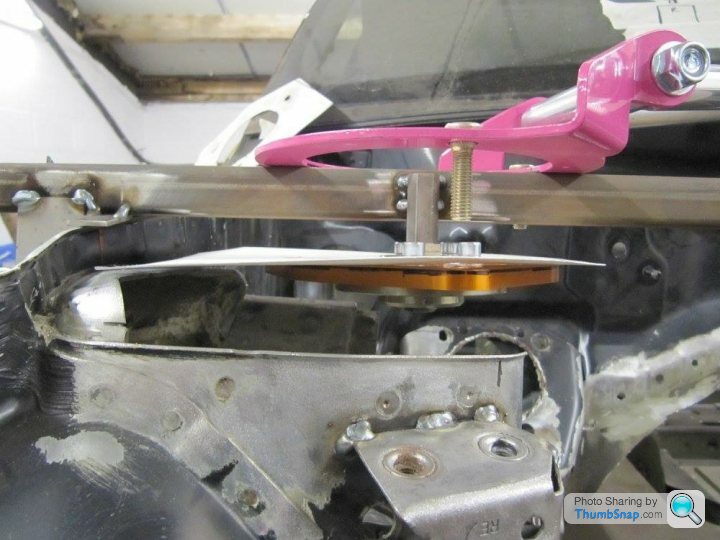
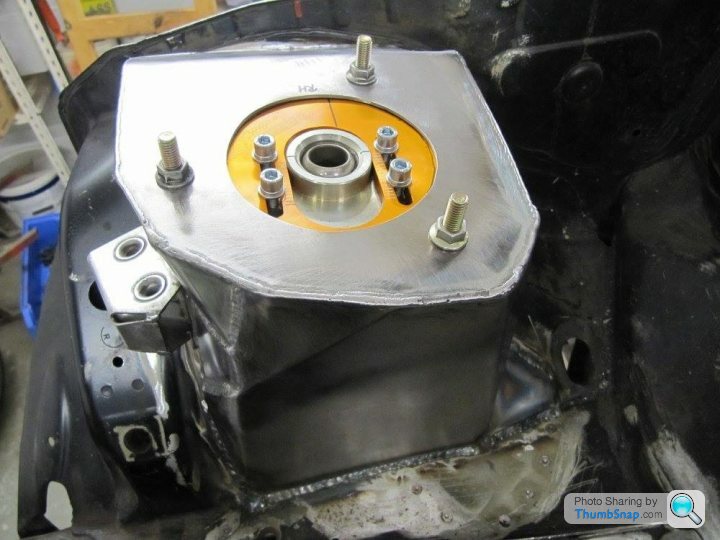
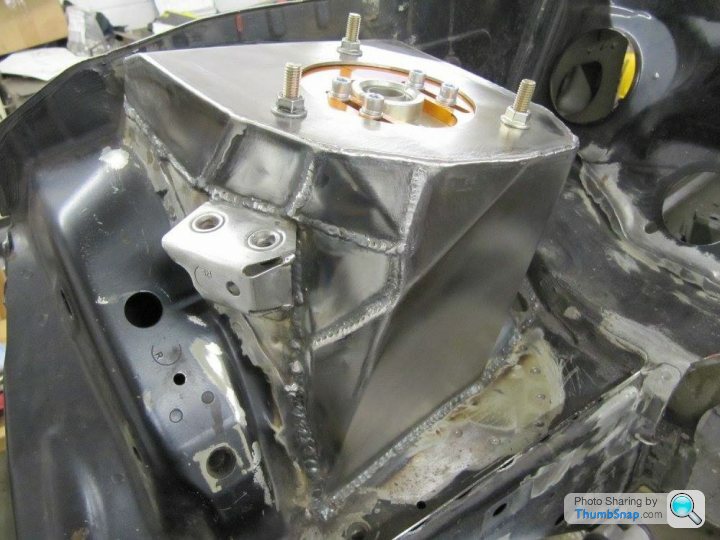
This upper panel positioning is the key to all of the front mounted components.
Radiators (Water, Oil, gearbox, power steering) (diff oil cooler will be mounted at the rear) and their associated mounts
Front panel which controls the light positions and therefore the bonnet
I didn't want bits of angle iron holding the lights and bumper on.
We must use all of the clever and beautifully make plastic mounts that BMW do so well to secure the original Mini parts
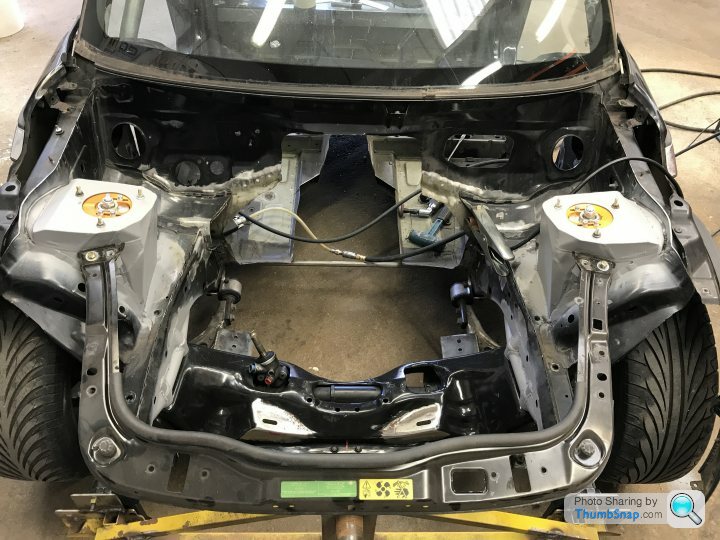
And so on to the cage
Given that Vini will be used on trackdays and by a number of the partners who have helped with special parts for their events, it had to be very safe.
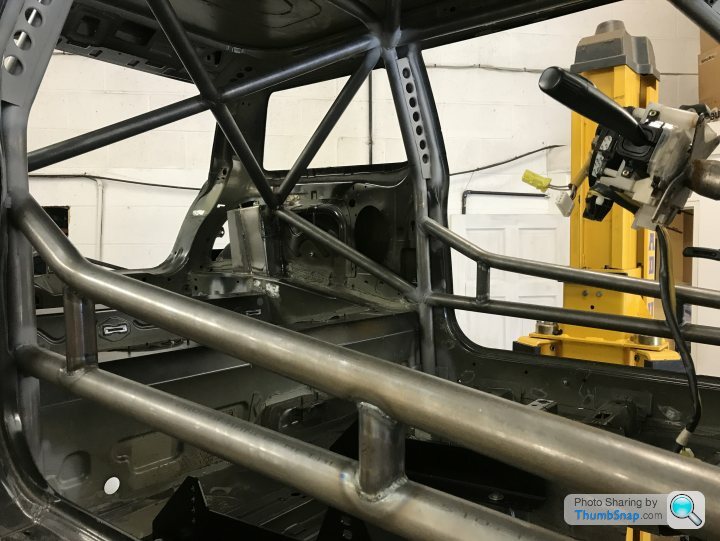
We don’t really know all of the things it is going to be doing so it needed to be built with a cage that would make it legal for racing also.
The cage had to also carry the loads so had to link the front and rear struts, front and rear subframe and provide strength to a massively altered body shell.
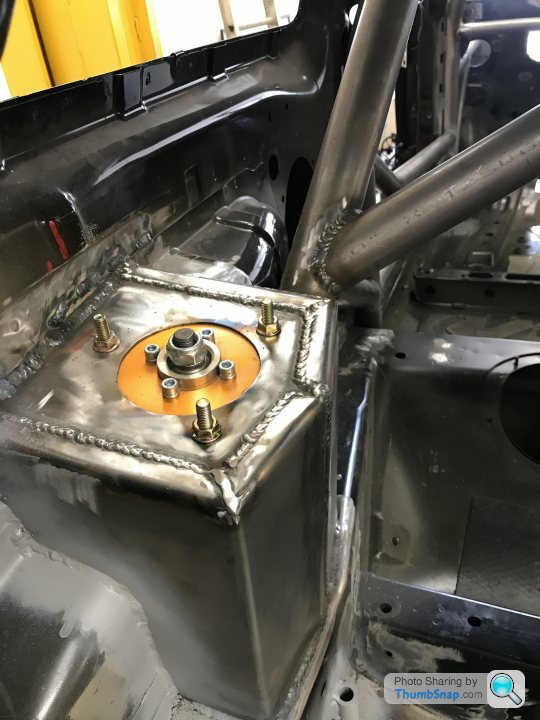
The engine will be stock but with a programmable ECU and custom exhaust and inlet, so it is going to be over the stock 414bhp by some way.
The shell had to be super strong
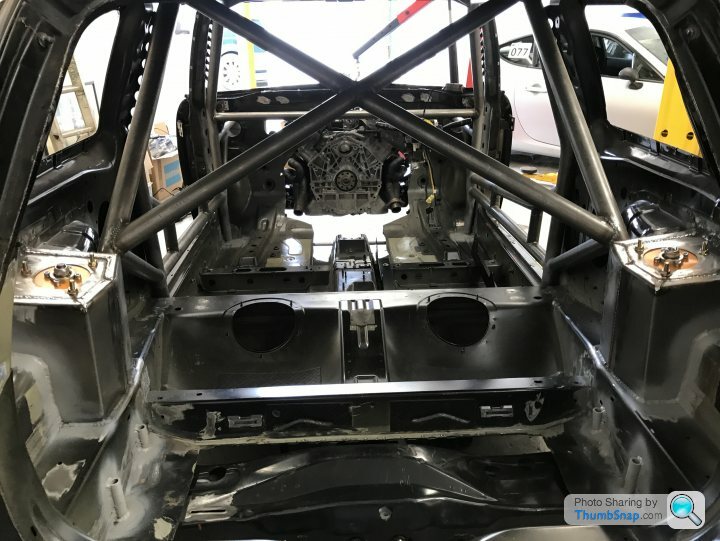
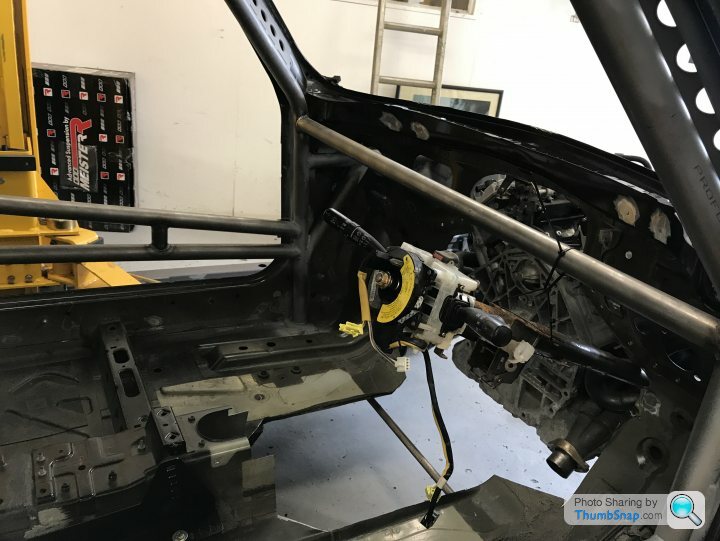
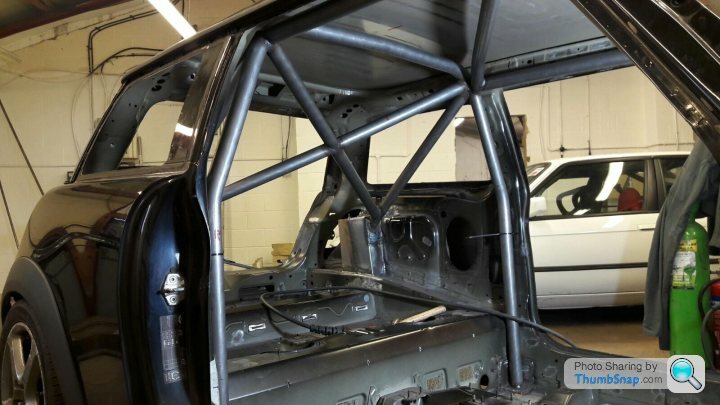
Linking the cage to the shell offers huge strength, safety and stiffness
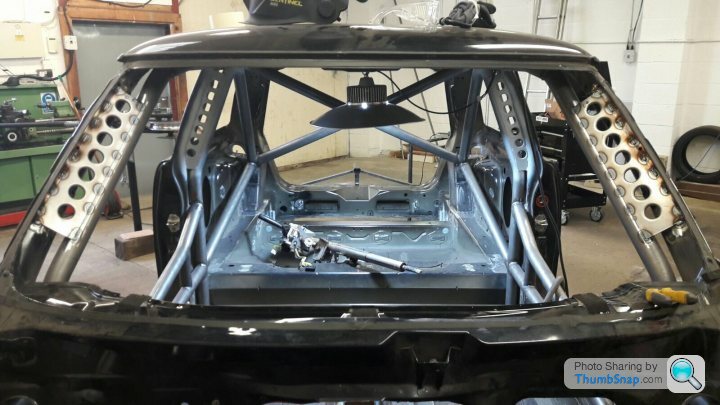
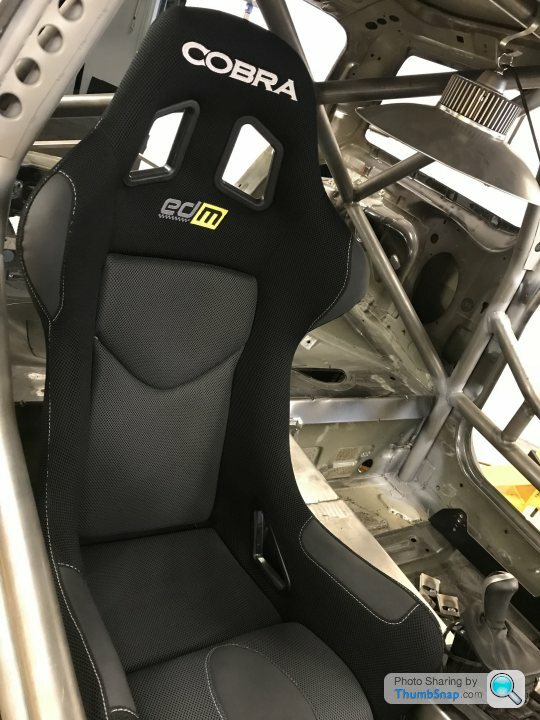
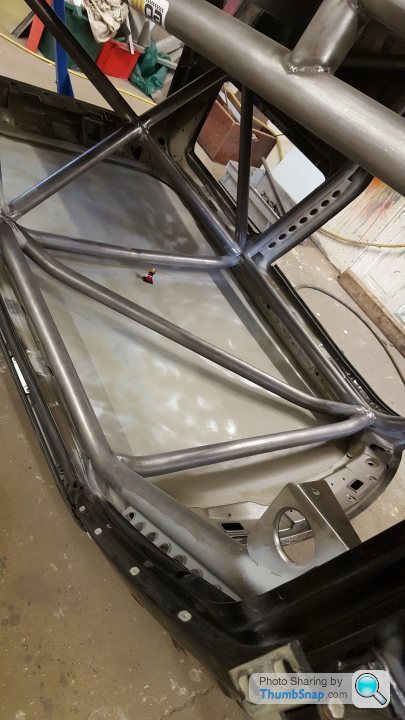
Given that Vini will be used on trackdays and by a number of the partners who have helped with special parts for their events, it had to be very safe.
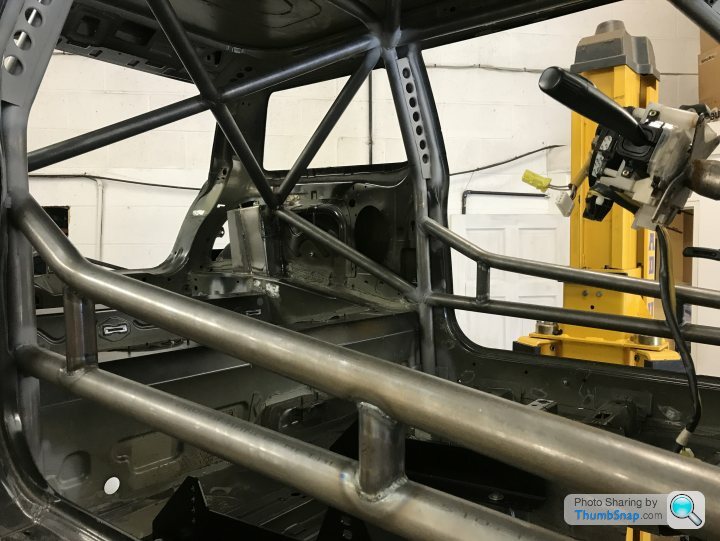
We don’t really know all of the things it is going to be doing so it needed to be built with a cage that would make it legal for racing also.
The cage had to also carry the loads so had to link the front and rear struts, front and rear subframe and provide strength to a massively altered body shell.
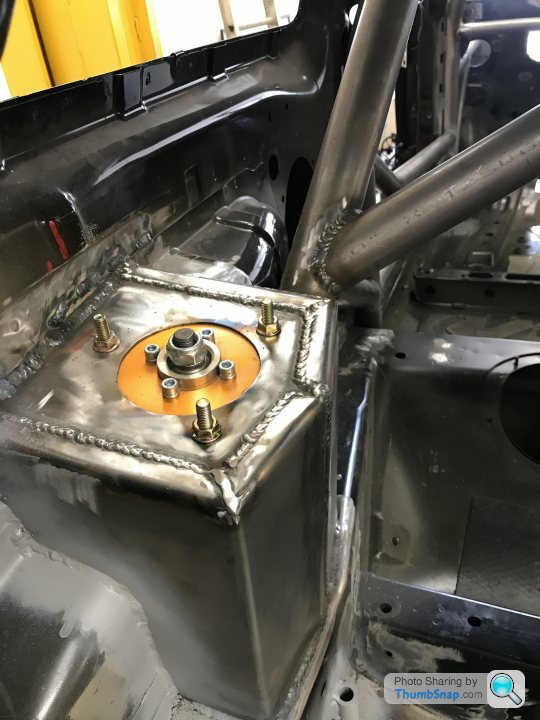
The engine will be stock but with a programmable ECU and custom exhaust and inlet, so it is going to be over the stock 414bhp by some way.
The shell had to be super strong
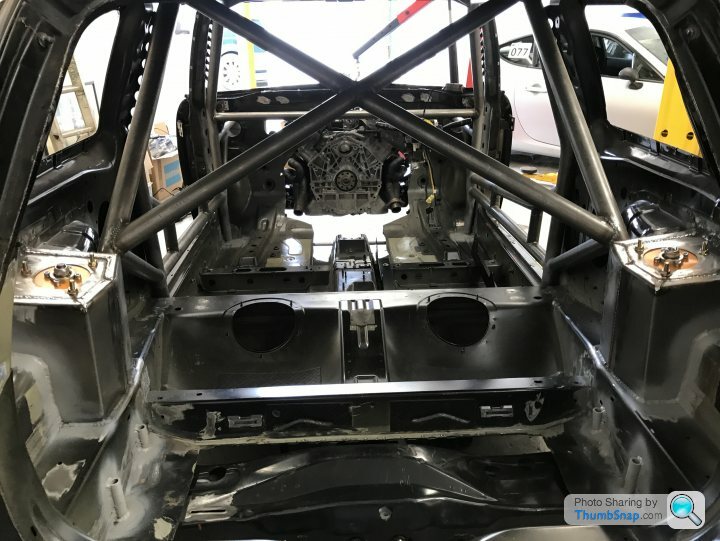
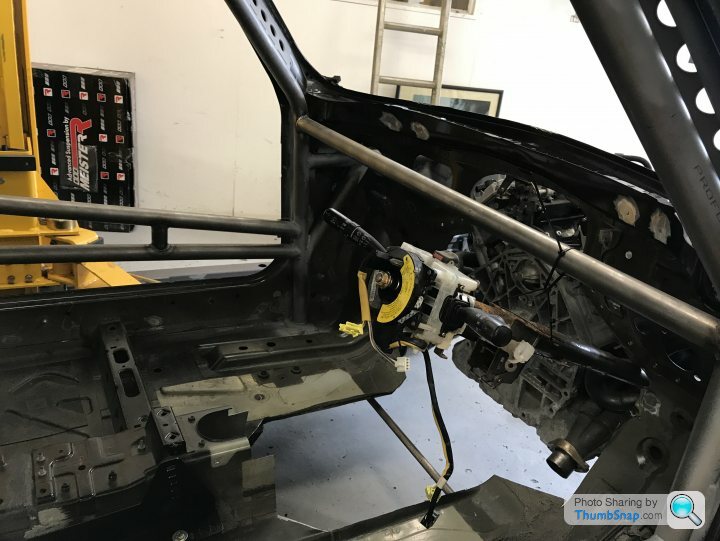
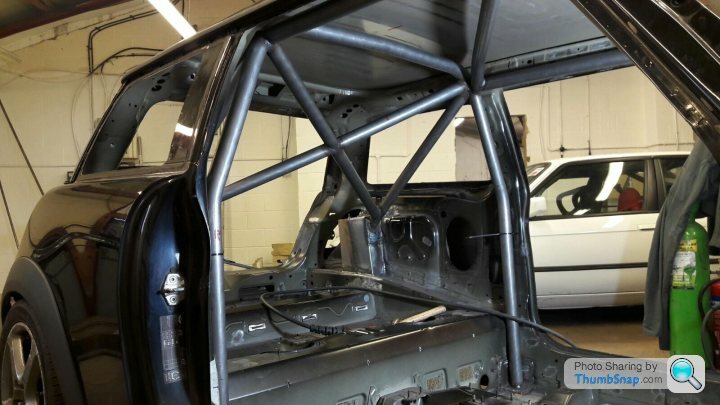
Linking the cage to the shell offers huge strength, safety and stiffness
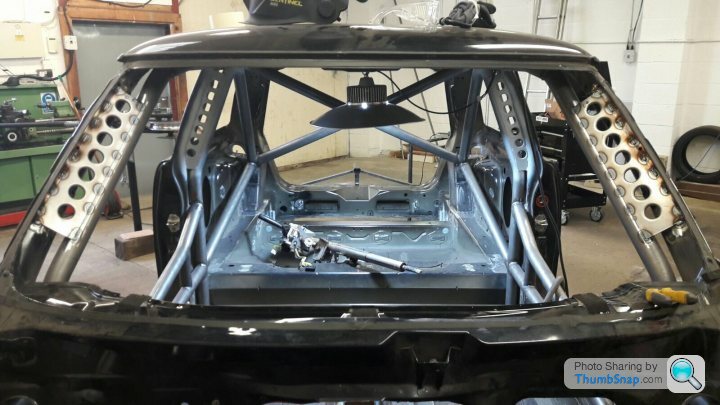
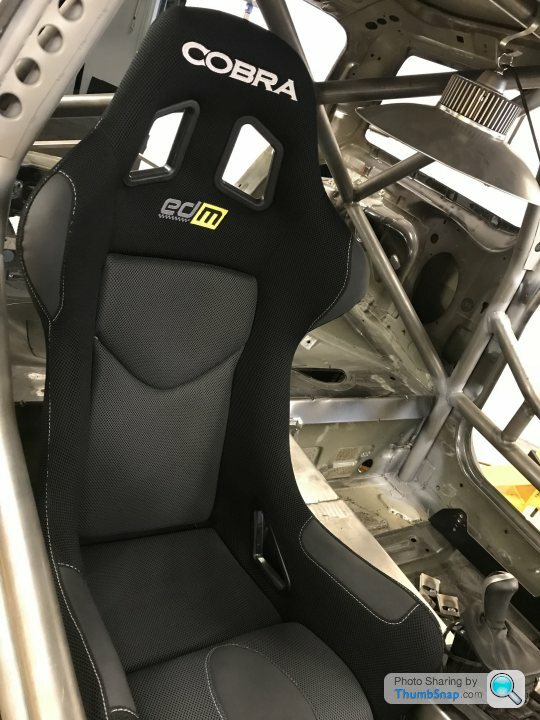
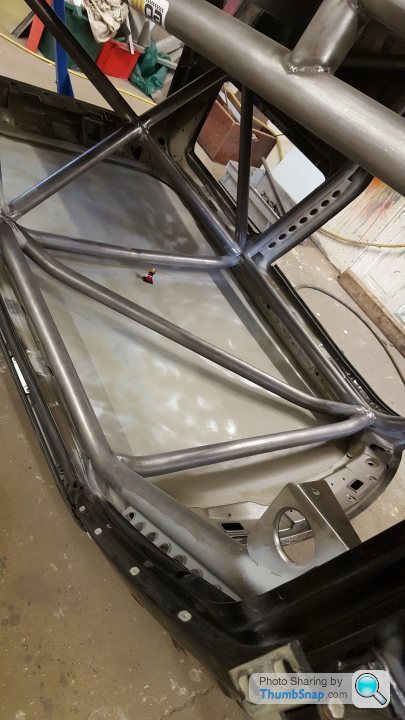
So with large chunks of the floorpan missing but the major components in place it was time to start putting some strength back in.

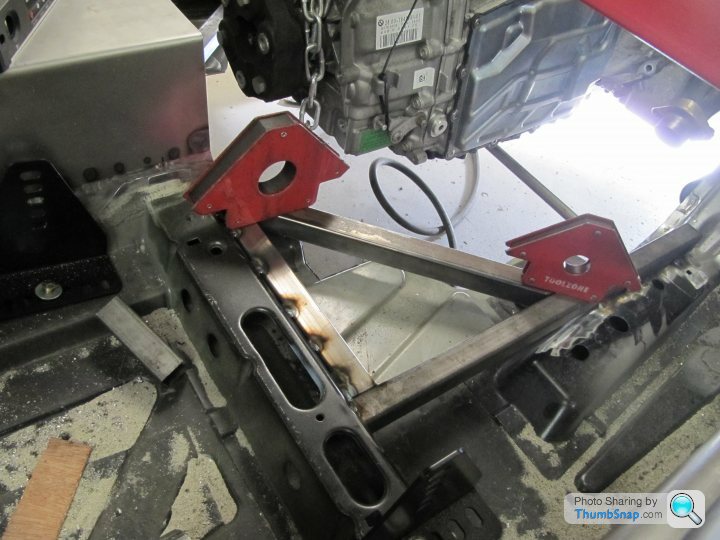
The majority of the floor was to be double skinned for strength and heat refection so these structural parts were going to be perfect to build an air gap.
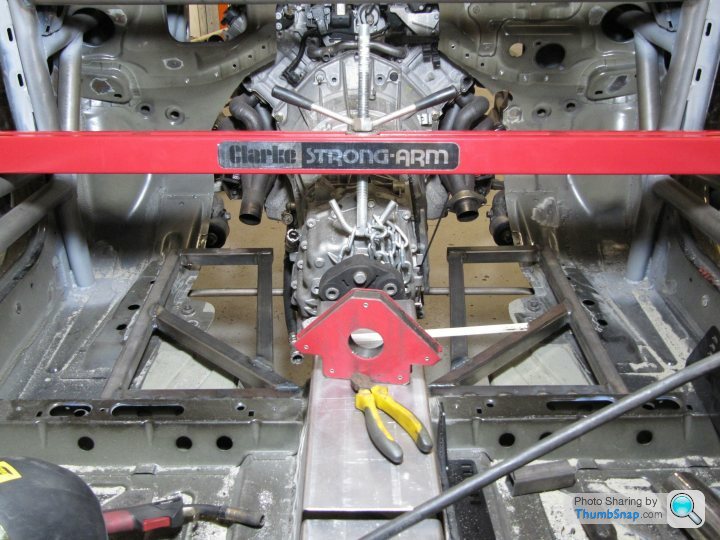
Looking from above through the windscreen aperture
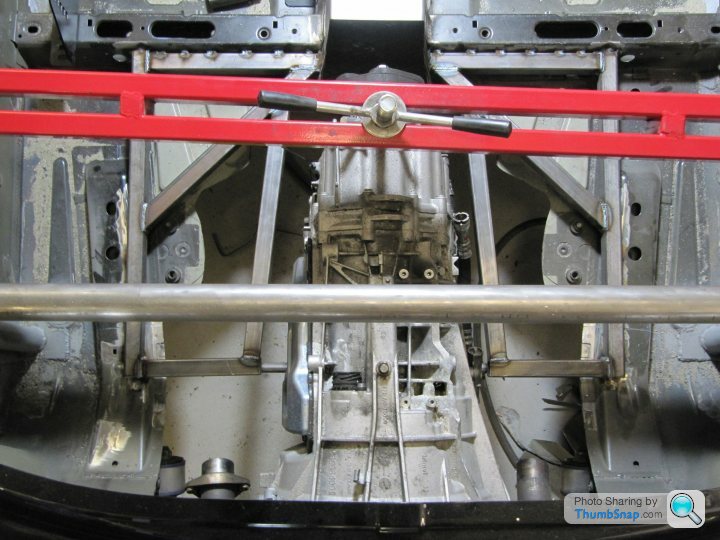

The exhausts are going to route close to the floor next to the gearbox on each side so heat management planning was a priority at this stage


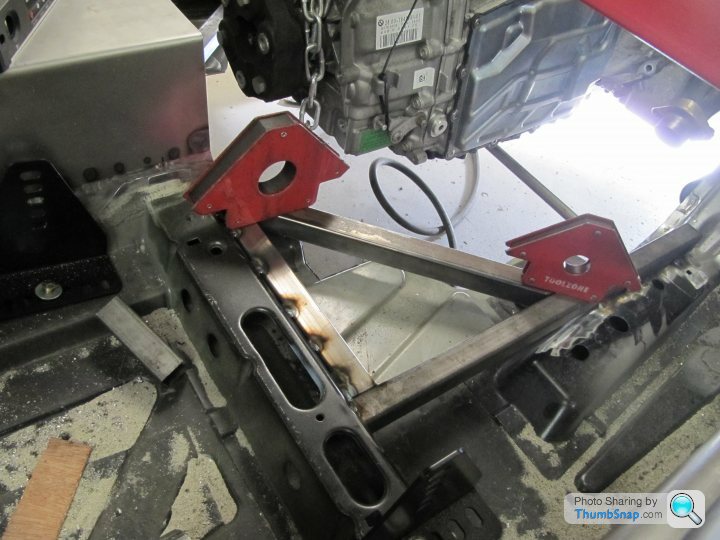
The majority of the floor was to be double skinned for strength and heat refection so these structural parts were going to be perfect to build an air gap.
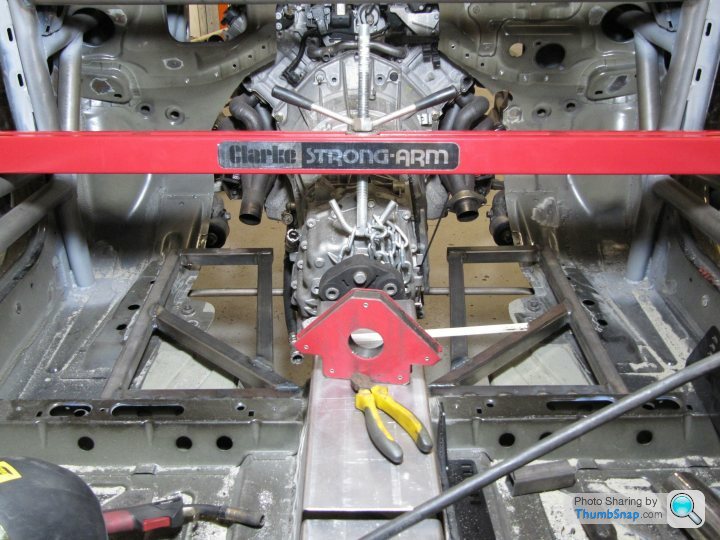
Looking from above through the windscreen aperture
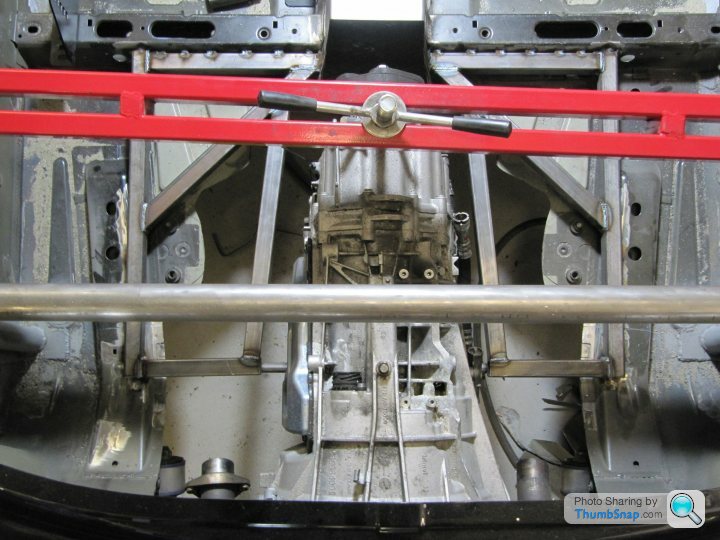

The exhausts are going to route close to the floor next to the gearbox on each side so heat management planning was a priority at this stage

Seeing his race car builds and the quality, detail and effort he goes to was the reason I chose Eliot to build it. I can't think of anyone who would have been brave and talented to do it.
There are many skilled people around but it is the thought he puts in to each piece that make him different I think.
There are many skilled people around but it is the thought he puts in to each piece that make him different I think.
On to the gearbox and propshaft covers.
Not really something that was ever needed in the front wheel drive Mini but a huge fabrication job looked to be made straightforward on the Powerflex Mini
by ED Motorsport
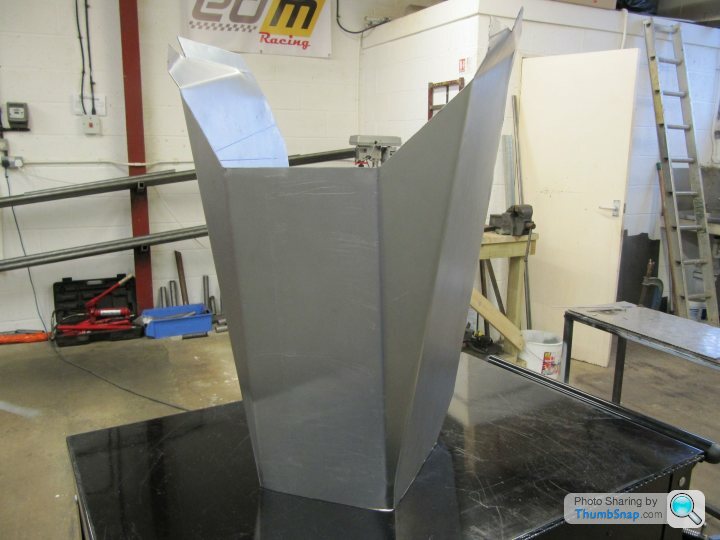
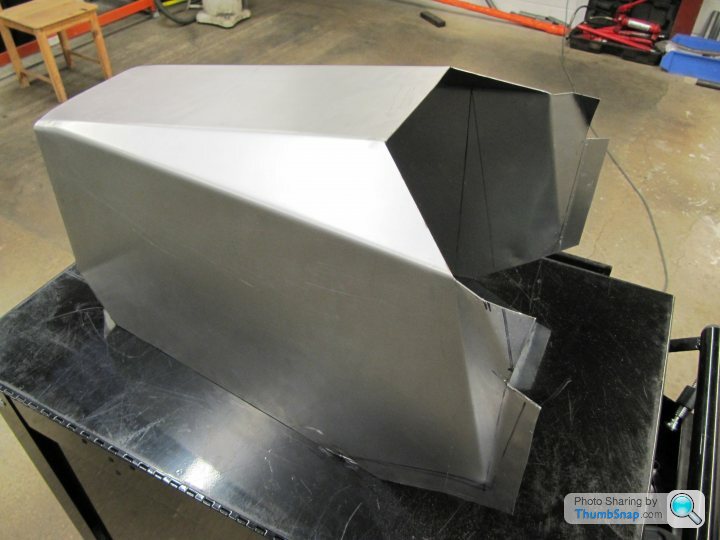
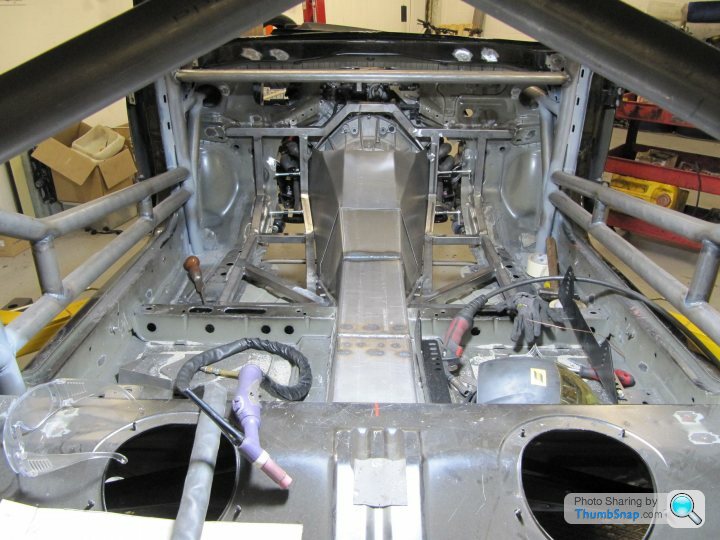
The floor is raised nearly 2 inches to gain ground clearance for the exhausts

The cage is looking quite extensive now. Strength being the requirement, both for safety but also shell stiffness
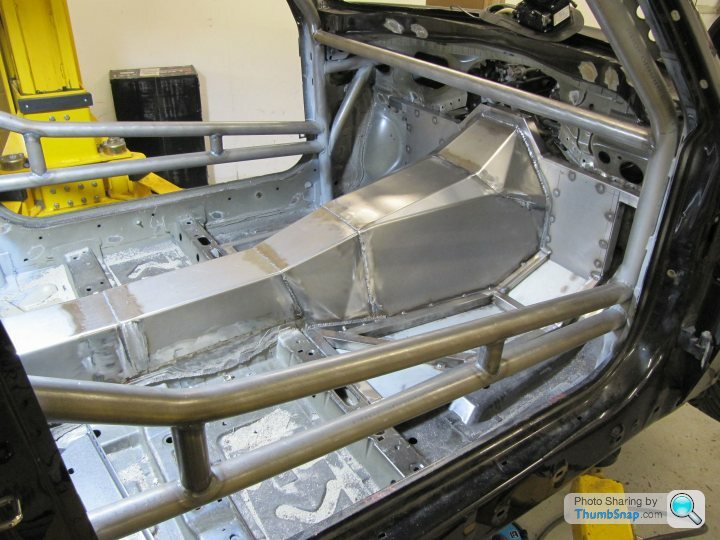
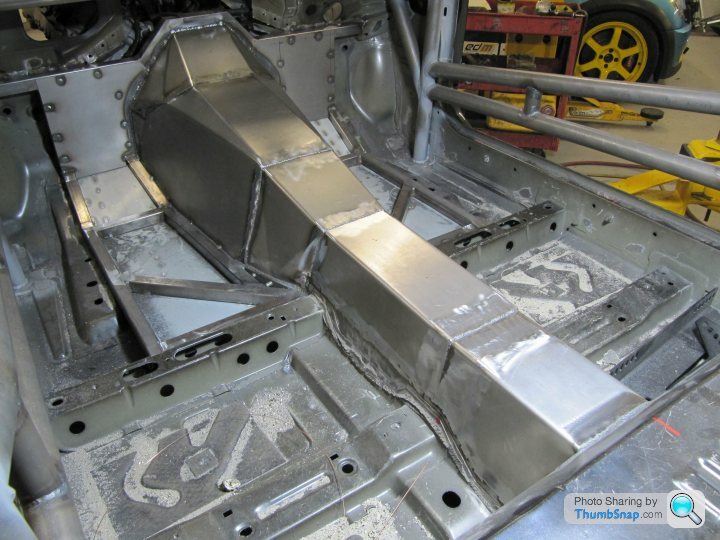
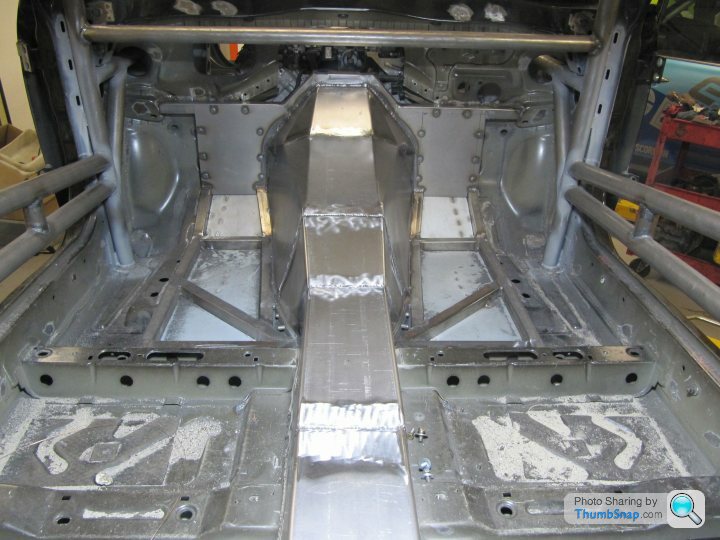
Not really something that was ever needed in the front wheel drive Mini but a huge fabrication job looked to be made straightforward on the Powerflex Mini
by ED Motorsport
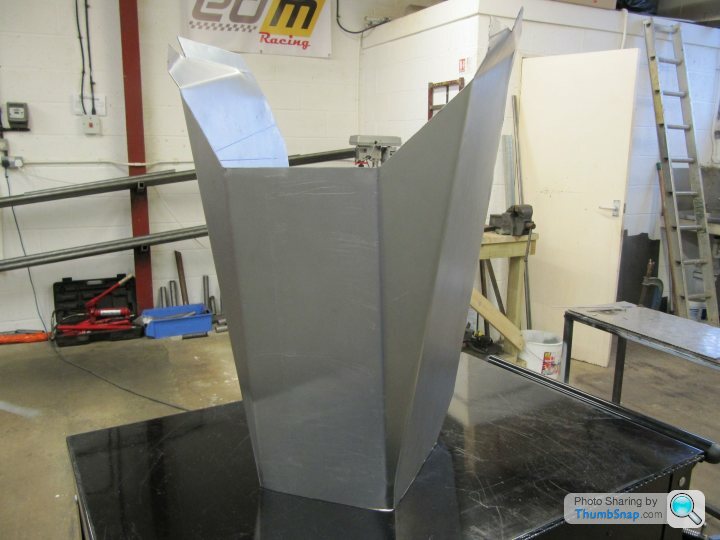
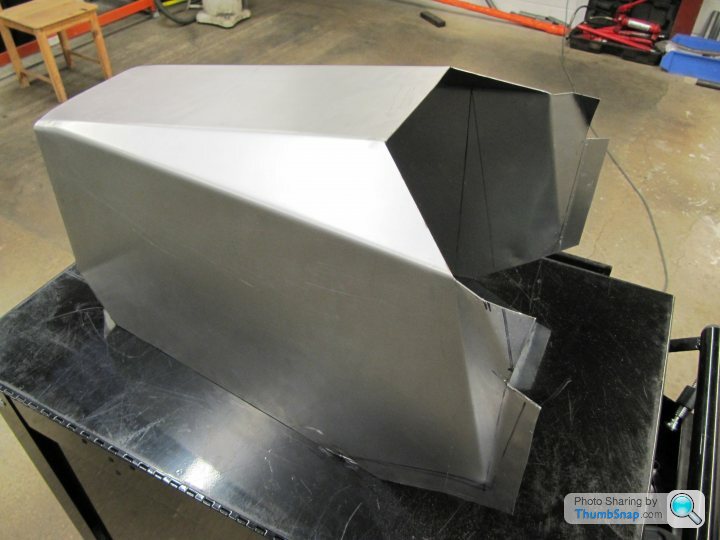
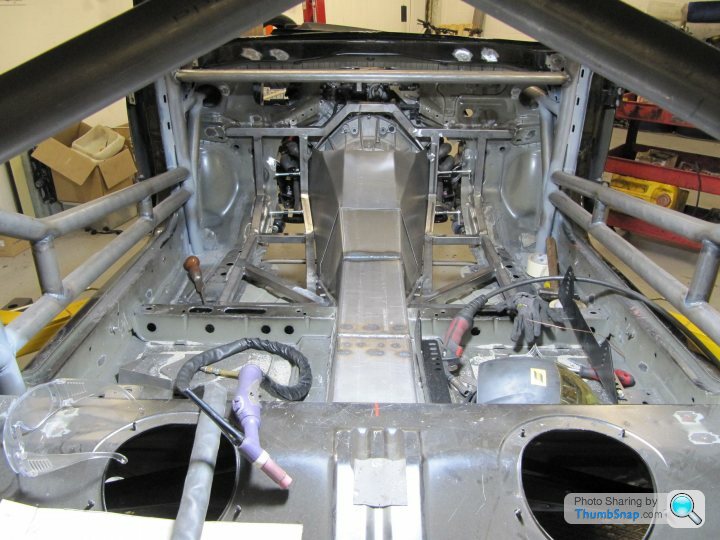
The floor is raised nearly 2 inches to gain ground clearance for the exhausts

The cage is looking quite extensive now. Strength being the requirement, both for safety but also shell stiffness
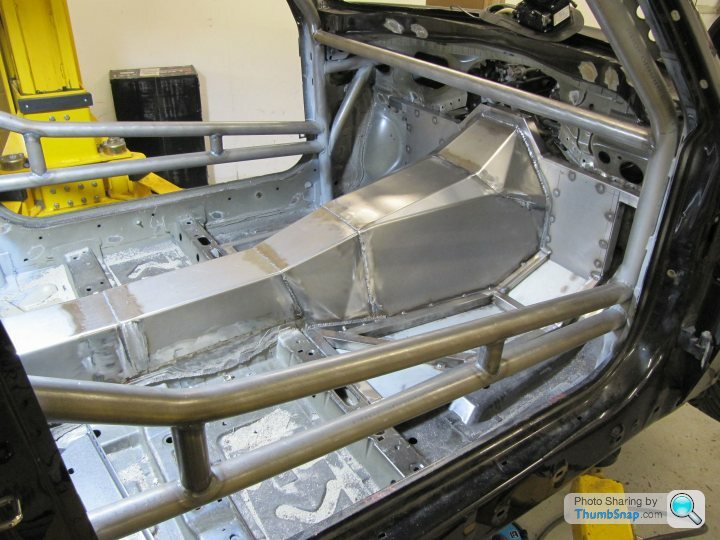
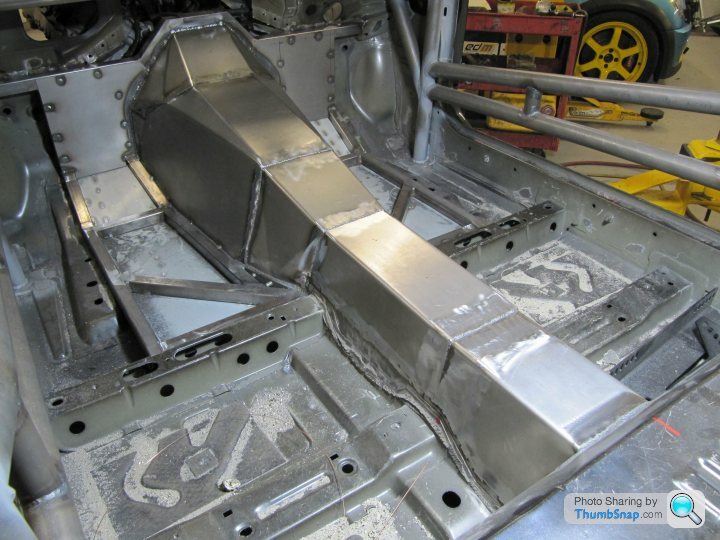
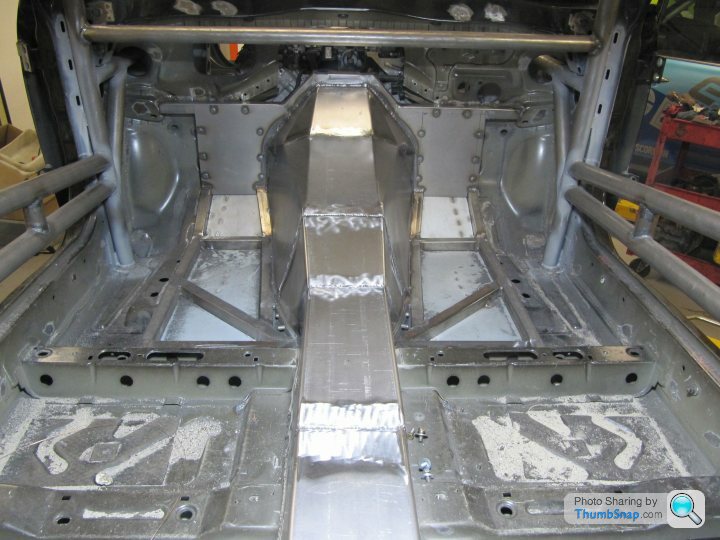
So, with the gearbox in, it needs a rear mount.
Sounds straightforward enough.
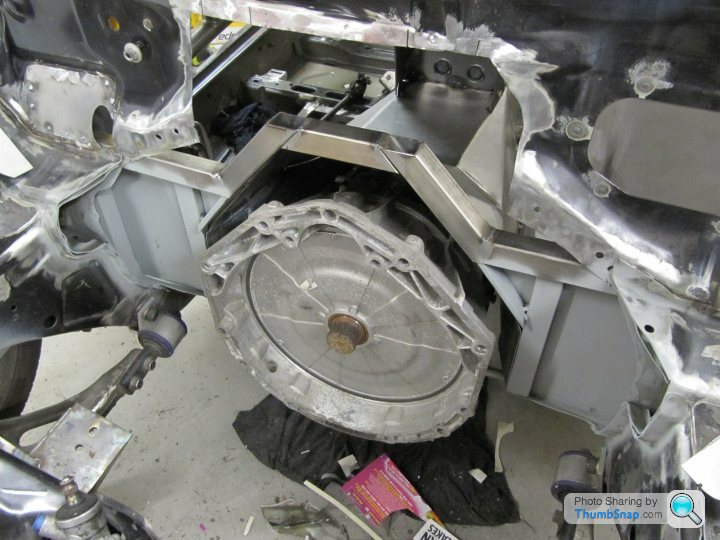
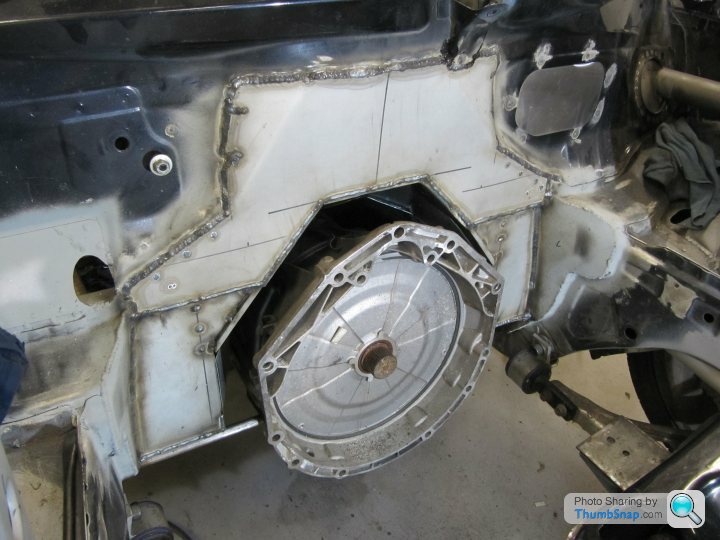
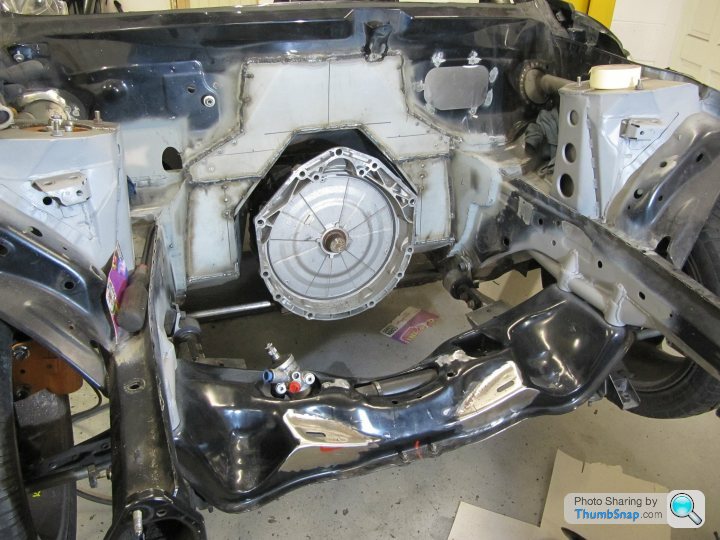

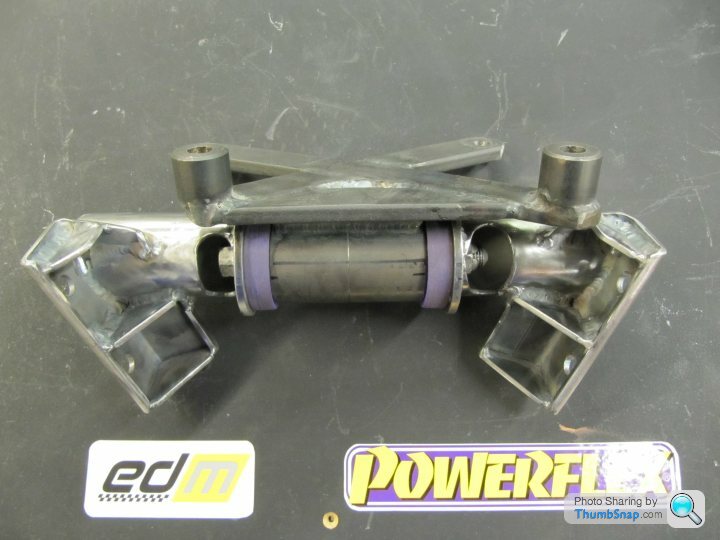
Even fabricating this rear gearbox mounting from a drawing would take an age but when you are having to position everything in fresh air and make something fit, I can't imagine the time and effort required.
The position of this and angle is dictated by the engine position and angle, this is dictated by the steering rack position which is critical due to the sump design, the steering rack position is dictated by the front subframe assembly which controls the front suspension geometry which is positioned in relation to the front wheel centres which are the only fixed points.
And all of this works because of decisions and measurements take months and months prior to fabricating this mount!
I am writing this as the commissioner of the car. Not the builder.
I'm an engineer and run an engineering/development business, Powerflex but I am in awe of the work that EDM and Eliot have put in and what they have achieved thus far.
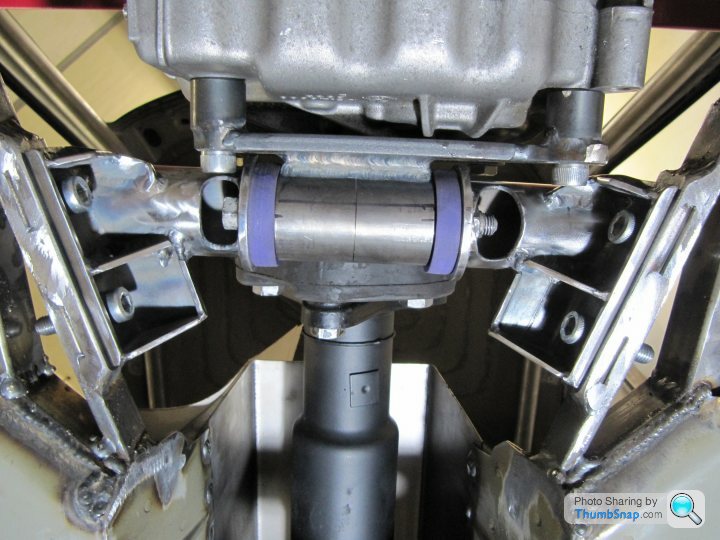
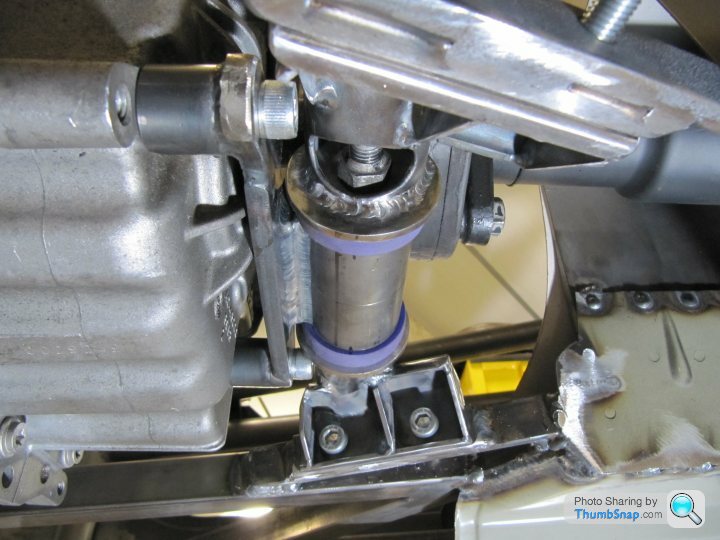
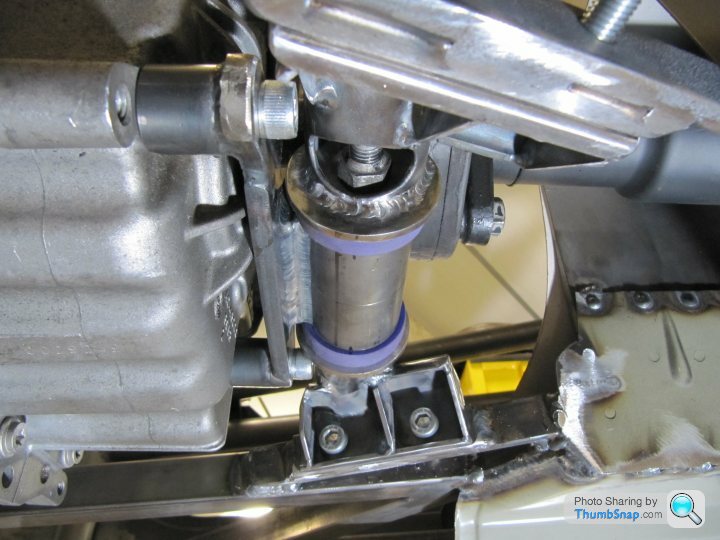
Sounds straightforward enough.
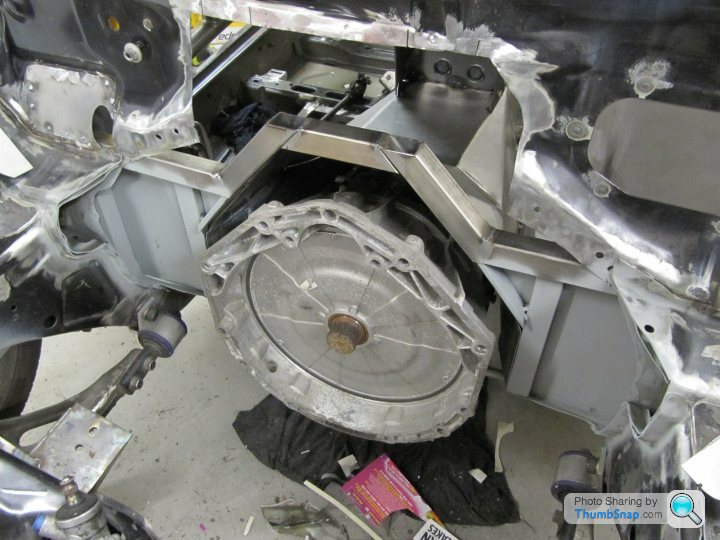
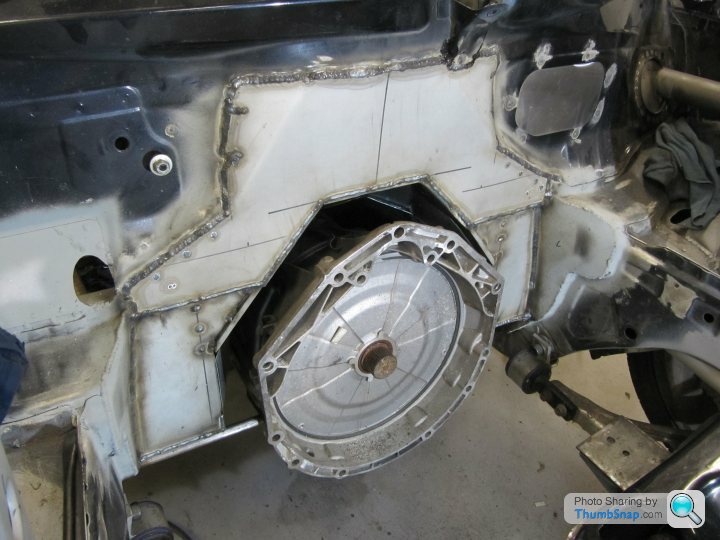
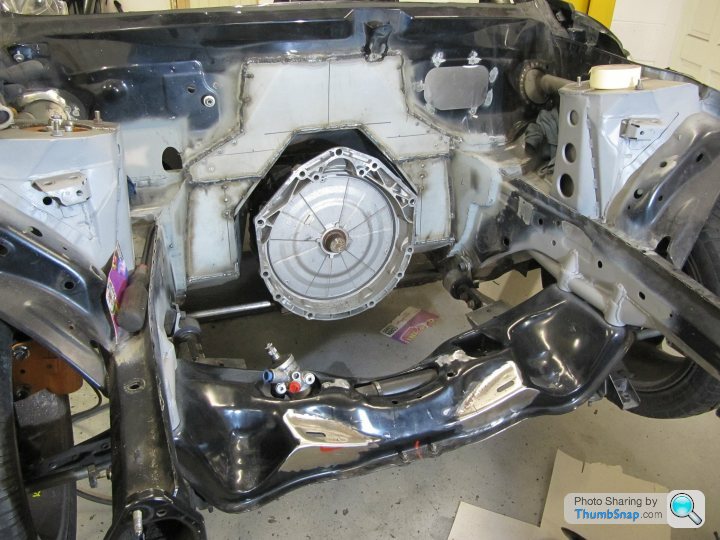

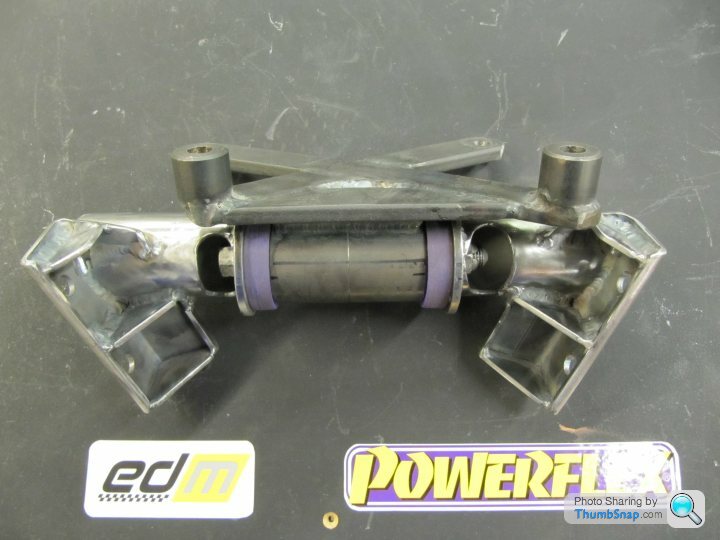
Even fabricating this rear gearbox mounting from a drawing would take an age but when you are having to position everything in fresh air and make something fit, I can't imagine the time and effort required.
The position of this and angle is dictated by the engine position and angle, this is dictated by the steering rack position which is critical due to the sump design, the steering rack position is dictated by the front subframe assembly which controls the front suspension geometry which is positioned in relation to the front wheel centres which are the only fixed points.
And all of this works because of decisions and measurements take months and months prior to fabricating this mount!
I am writing this as the commissioner of the car. Not the builder.
I'm an engineer and run an engineering/development business, Powerflex but I am in awe of the work that EDM and Eliot have put in and what they have achieved thus far.
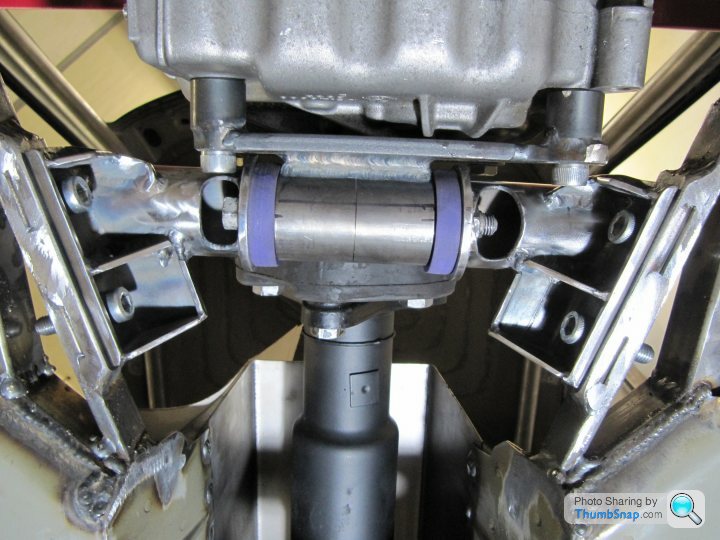
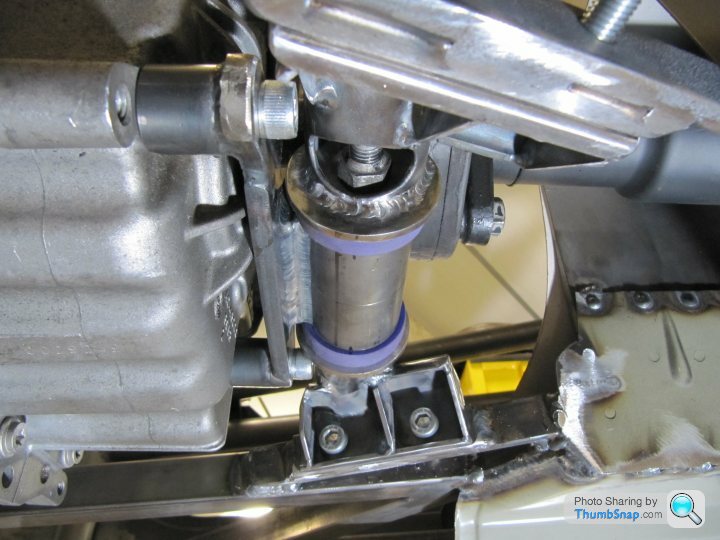
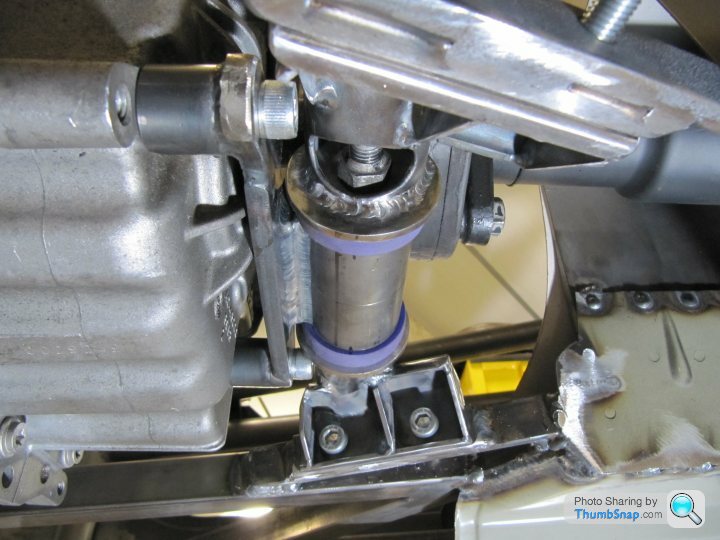
Now to the rear.
EDM decided to use the rear end from an Impreza, very early on.
It is an almost completely self contained subframe with correctly positioned suspension pick up points, great geometry, very strong wishbones, Powerflex bushes of course.
The diff chosen is the Impreza R180 Spec C with plated LSd and we have added a Cusco high capacity diff cover, thermostatically controlled Mocal pump and Setrab cooler with electric fan. The driveshafts have been specially built and are rated at 600bhp.
Obviously huge chassis mods to make everything fit and retain the correct geometry.
It also means we can use the very strong Impreza Spec C rear hubs which include sensors for the Bosch Motorsport M5 programmable ABS.



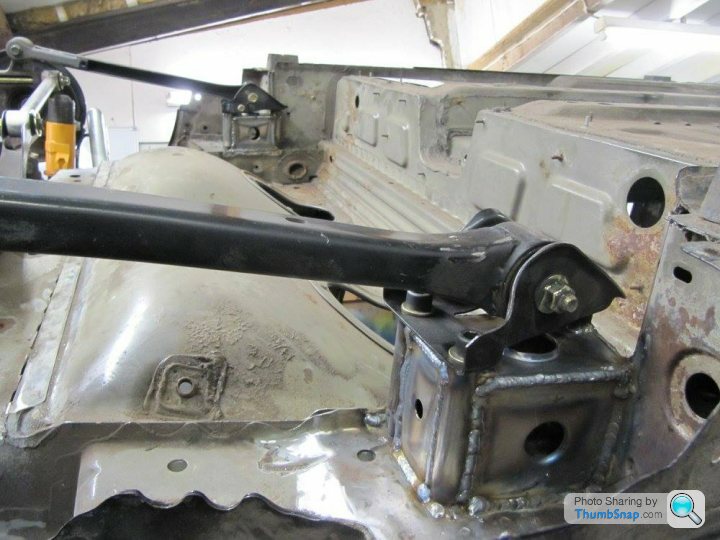
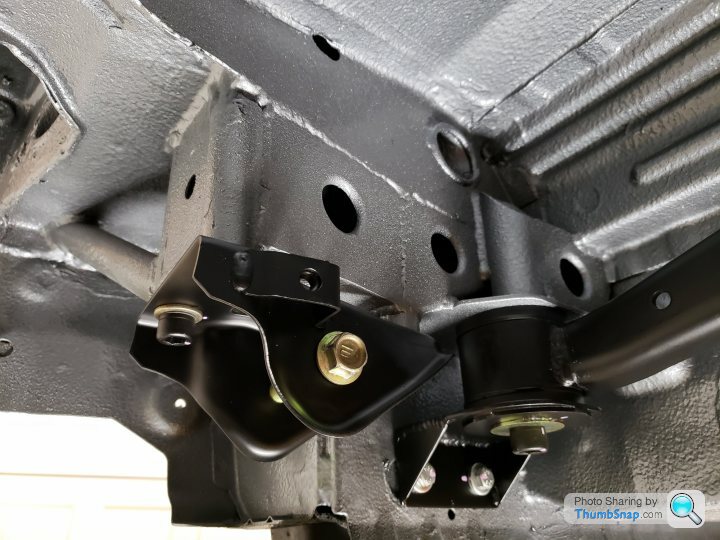
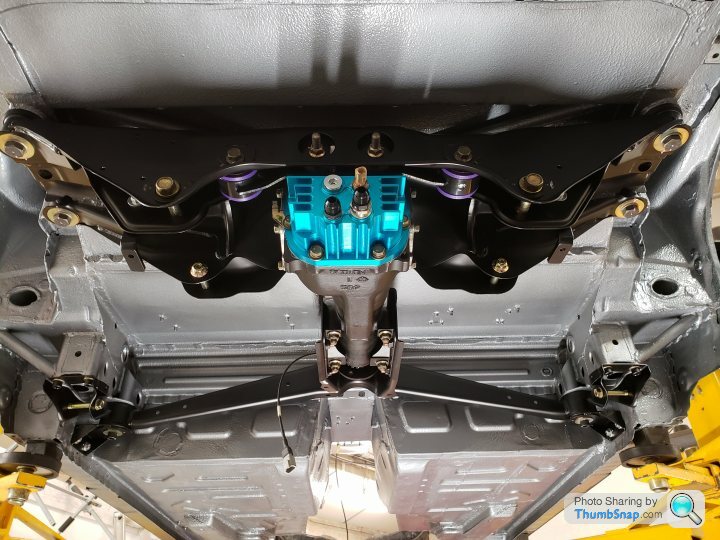
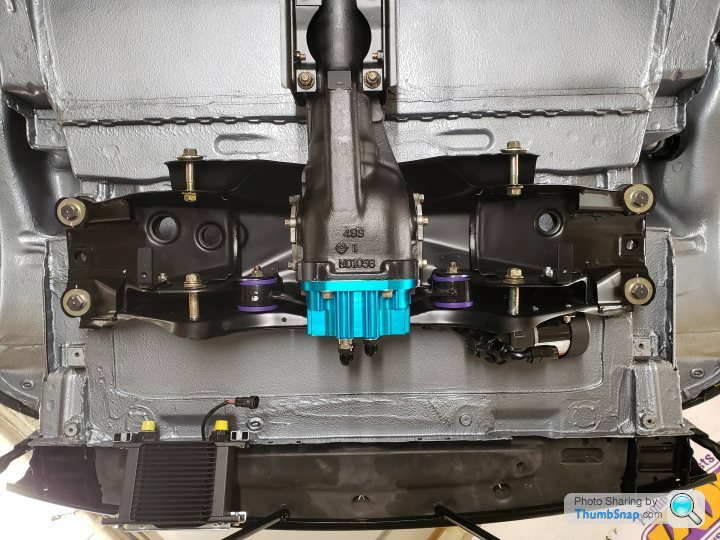
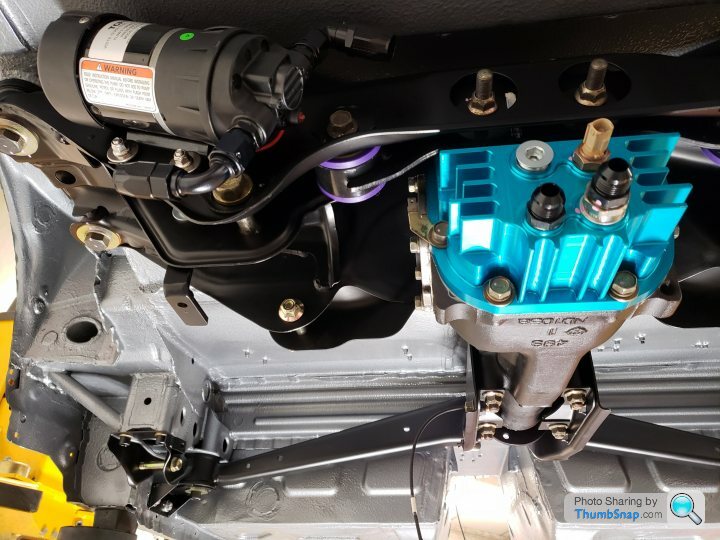
EDM decided to use the rear end from an Impreza, very early on.
It is an almost completely self contained subframe with correctly positioned suspension pick up points, great geometry, very strong wishbones, Powerflex bushes of course.
The diff chosen is the Impreza R180 Spec C with plated LSd and we have added a Cusco high capacity diff cover, thermostatically controlled Mocal pump and Setrab cooler with electric fan. The driveshafts have been specially built and are rated at 600bhp.
Obviously huge chassis mods to make everything fit and retain the correct geometry.
It also means we can use the very strong Impreza Spec C rear hubs which include sensors for the Bosch Motorsport M5 programmable ABS.



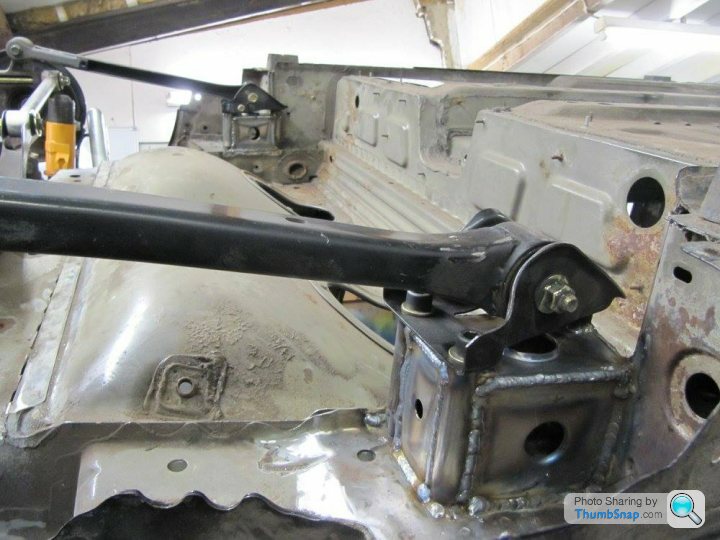
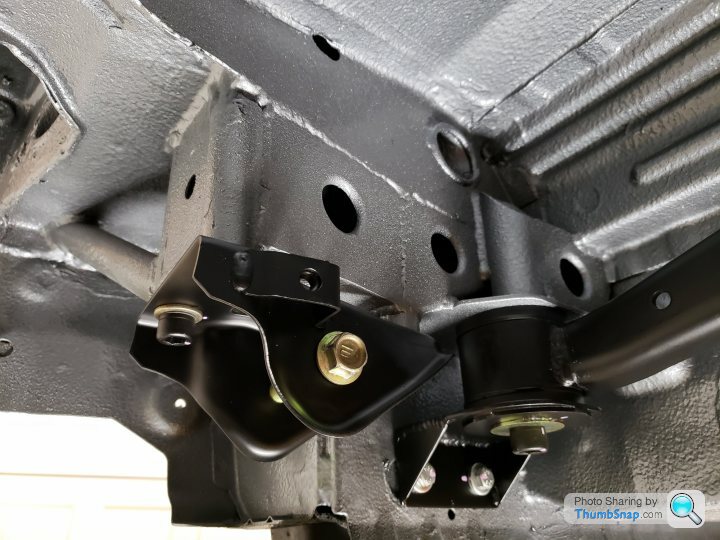
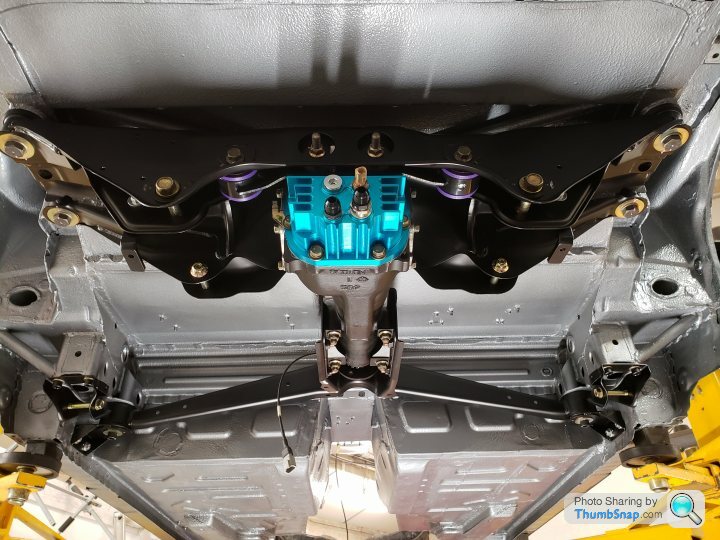
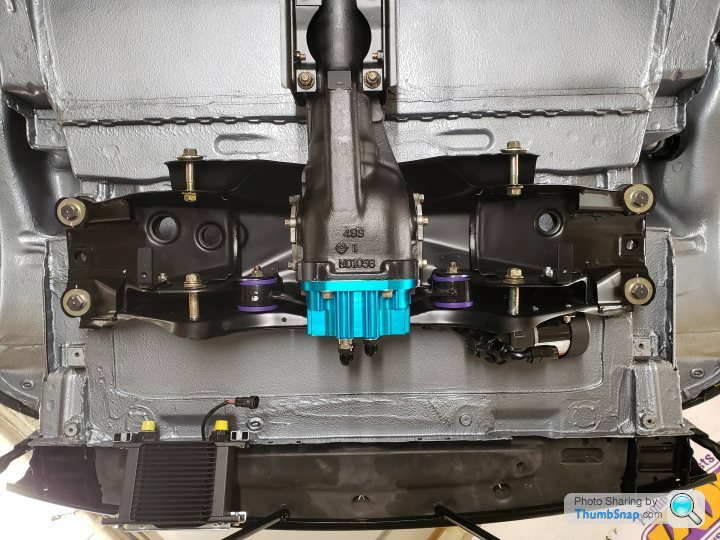
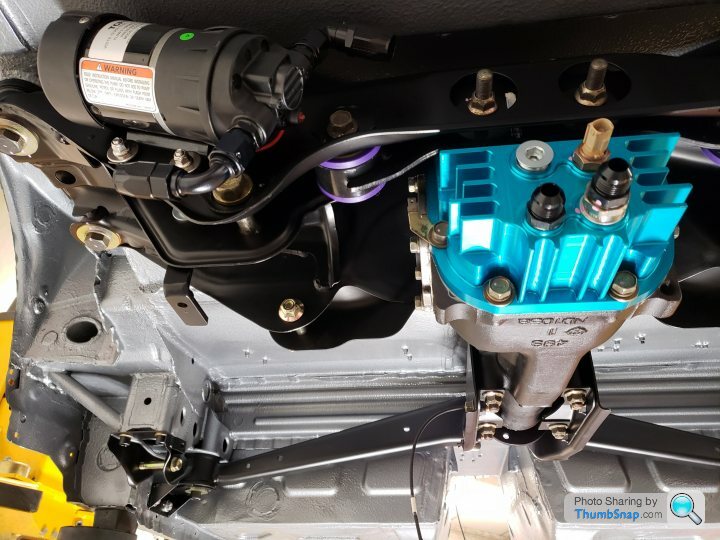
Given that the brief for Vini was that it is a promotional vehicle for Powerflex and should be road legal but also race legal, the safety aspects needed to be correct.
An FIA bag tank would be needed and housed within it's own container with sealing from the main people compartment.
Once again, after removing the floor at the back, EDM's CAD (Cardboard Aided Design) skills were needed.
ATL were incredibly helpful and fascinated by the project, which was a rear compliment considering the make the fuel tanks for the whole F1 grid.
The bag took some time to make, but typically of high end motorsport suppliers, it was delivered on exactly the day they promised and was perfect.
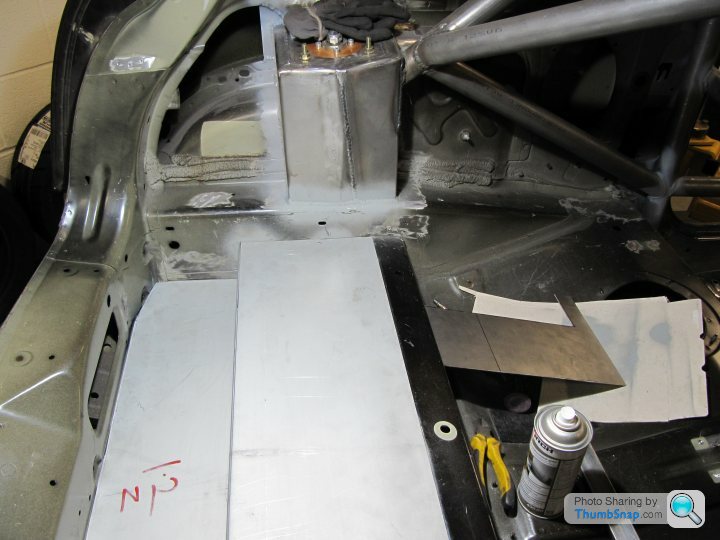
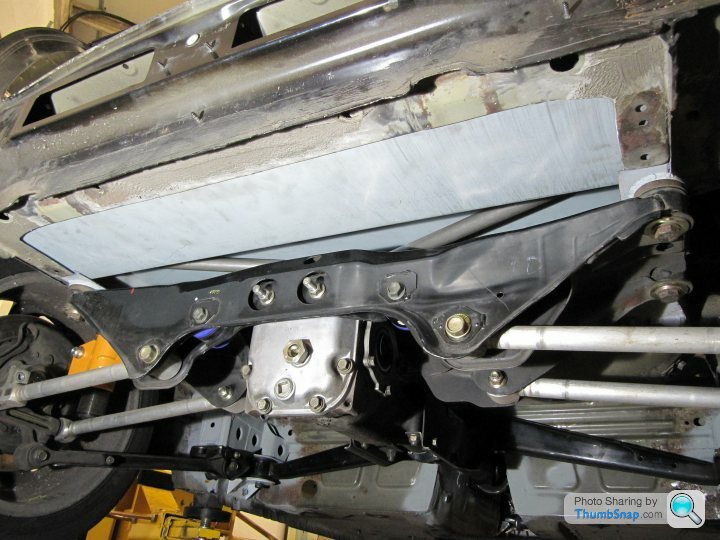
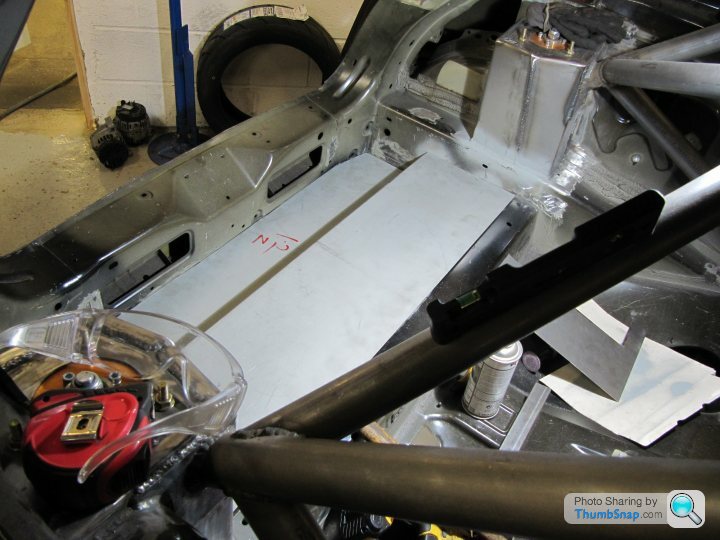
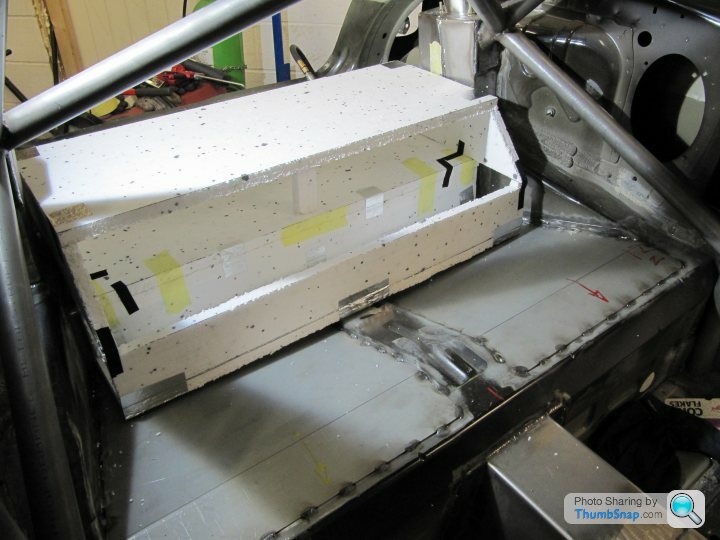

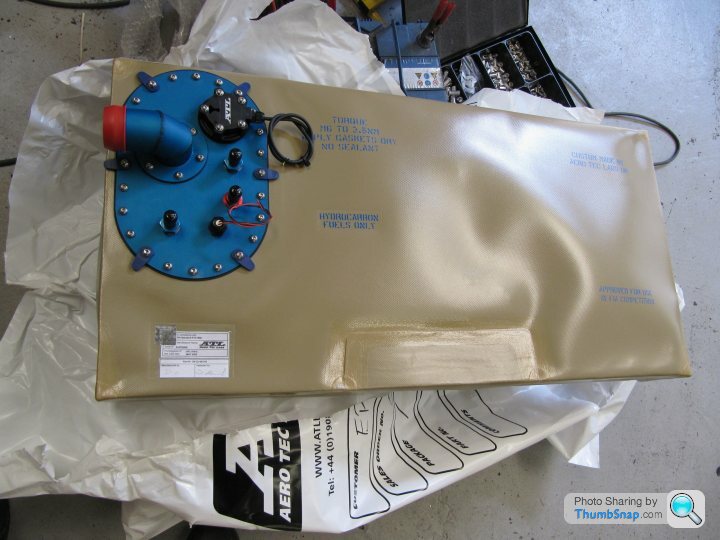
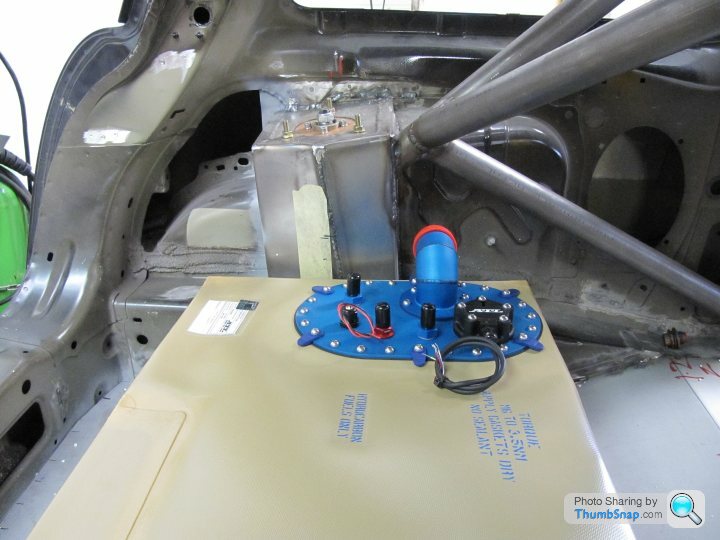

An FIA bag tank would be needed and housed within it's own container with sealing from the main people compartment.
Once again, after removing the floor at the back, EDM's CAD (Cardboard Aided Design) skills were needed.
ATL were incredibly helpful and fascinated by the project, which was a rear compliment considering the make the fuel tanks for the whole F1 grid.
The bag took some time to make, but typically of high end motorsport suppliers, it was delivered on exactly the day they promised and was perfect.
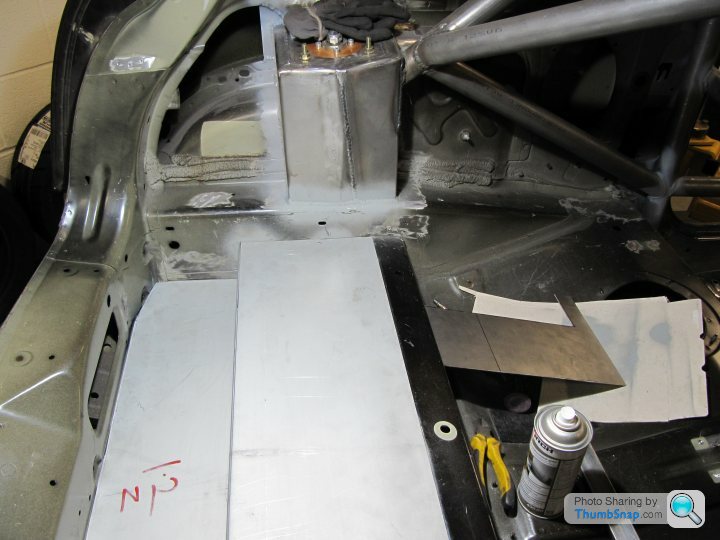
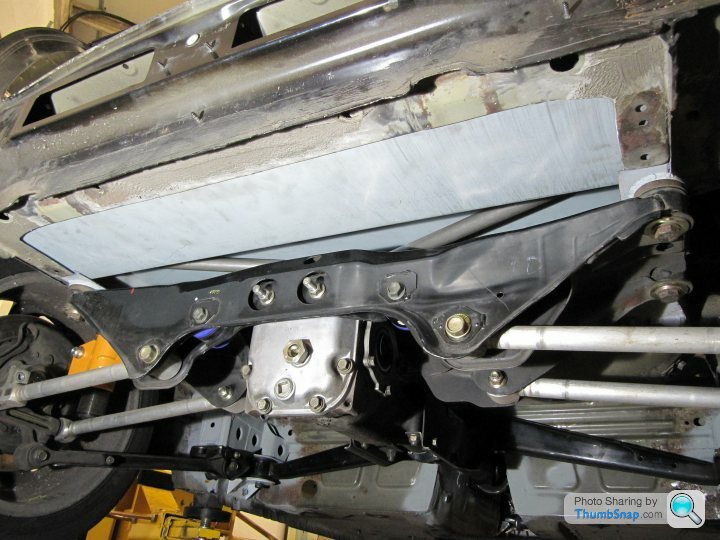
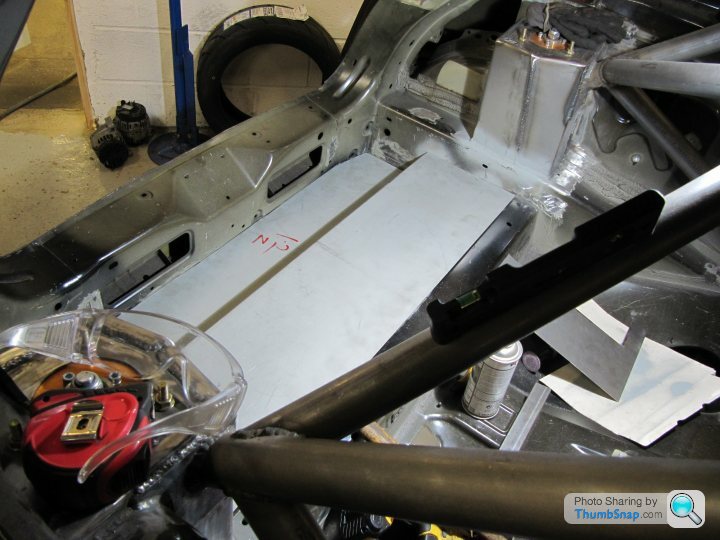
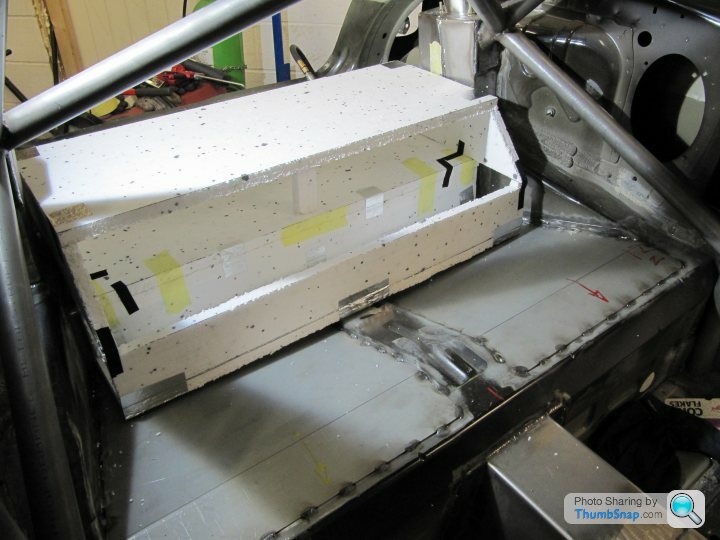

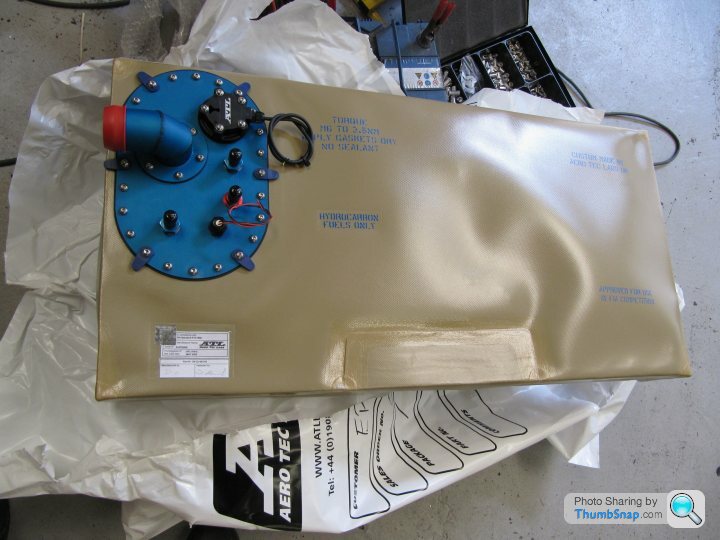
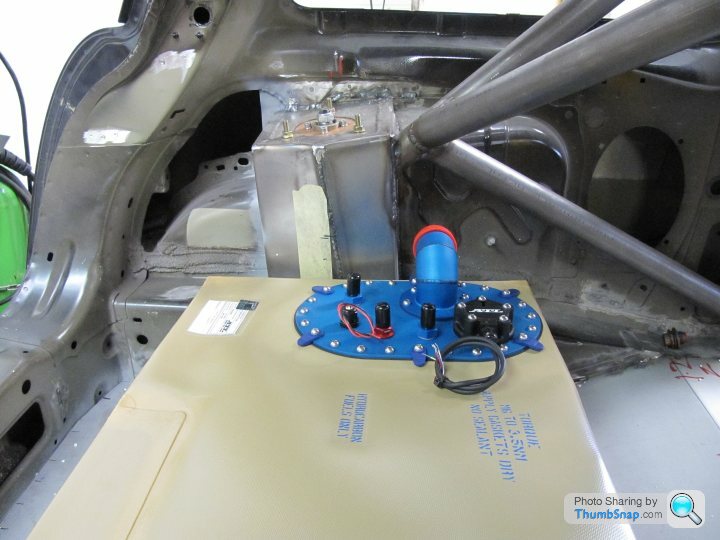

Gassing Station | Readers' Cars | Top of Page | What's New | My Stuff