Facel Vega HK500. A childhood dream or a nightmare?
Discussion
B'stard Child said:
And so the slippery slope was found and down you slid 
Of course it's not intentional it just happened - it was an accident
Oh how true! The worst thing is I can't even claim it was an accident, as the emptying of my wallet (and all other sources of money) was premeditated 
Of course it's not intentional it just happened - it was an accident

Given B'stard Child's recent comments this post should be called 'The Slippery Slope' as, over the course of a couple of months the Facel went from something that could pass as almost complete back to a collection of bits. At the time I wasn't as concerned as perhaps I should have been! I just clung to the cost spread sheet Steve and I had discussed.
What could possibly go wrong?!
Actually, as someone who had funded other restorations I wasn't quite as naive as I'm making out. I knew costs would likely escalate and timescales lengthen. I also knew that once started there would be no going back; bailing out part way through would be a road to financial disaster.
Very soon we were back to this...
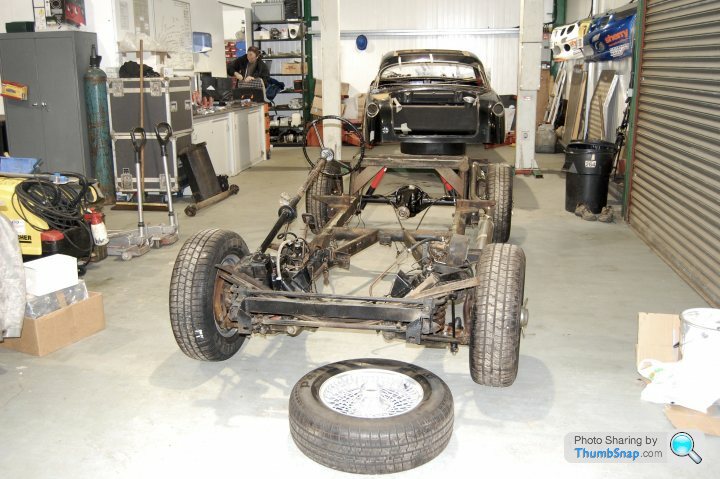
Steve captured the actual moment the body and chassis parted company.
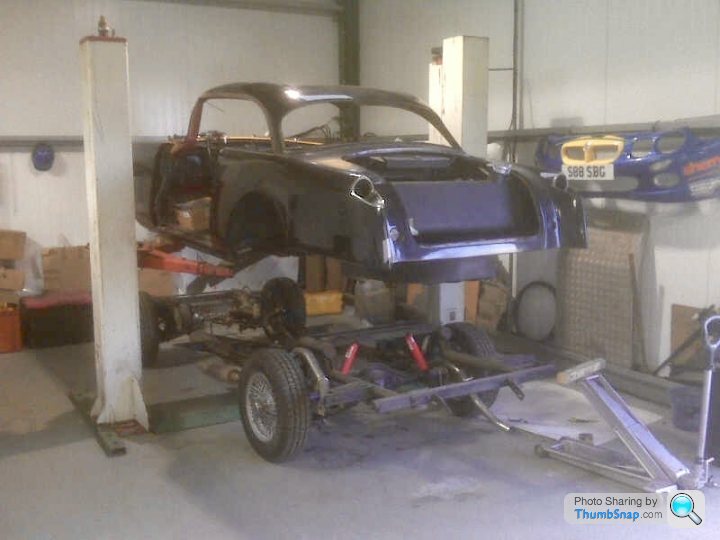
Taking the body off the chassis was a pivotal moment for a couple of reasons. Firstly, it would allow us to assess the real condition of the car (a bit of a risk) and secondly it would allow a more thorough restoration. If the answer to the first part wasn't as expected, the budget could be completely blown apart.
So what did we find?
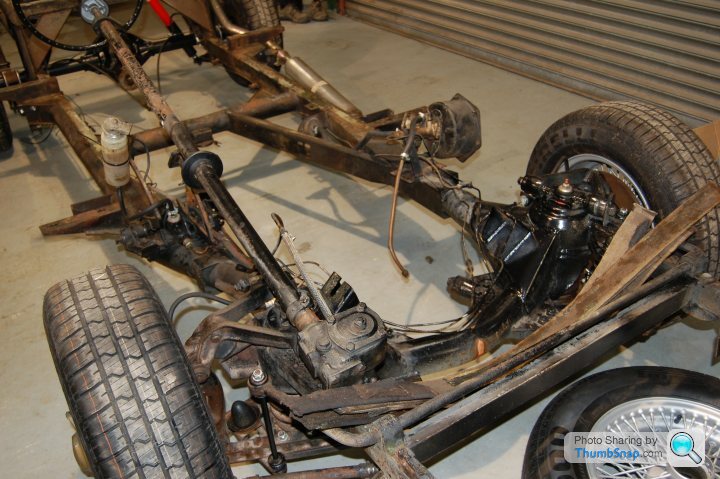
For those not familiar with the construction of the HK500, it is an amazing feat of engineering. The chassis appears to be massively over engineered, with chassis rails made from large diameter tubes and substantial cross members which are beefily braced. It would look at home as part of a ship or maybe a small bridge! The body is made from a patchwork of small panels stitched together to create a whole. For instance, the front wings form a single unit with the front panel and windscreen scuttle. Even though there is a separate chassis, the floor of the body is a welded steel structure that is reminiscent of monocoque construction. Given this 'belt and braces' approach, the amazing thing is how little rigidity the complete car possesses.
The chassis was in great condition and showed no evidence of collision damage, which was a relief. It still had the body number chalked on the cross member above the rear axle. Luckily that chalk number matched the body number in the factory records! As you would expect, the chassis had plenty of surface corrosion, but nothing serious. This is a testament to its sturdy construction as no real rust protection was applied by the factory, just a quick 'once over' with an underseal type product called 'Blaxon'. It was obvious from the areas that were completely bare that the quick waft of Blaxon was applied once the body was in place.
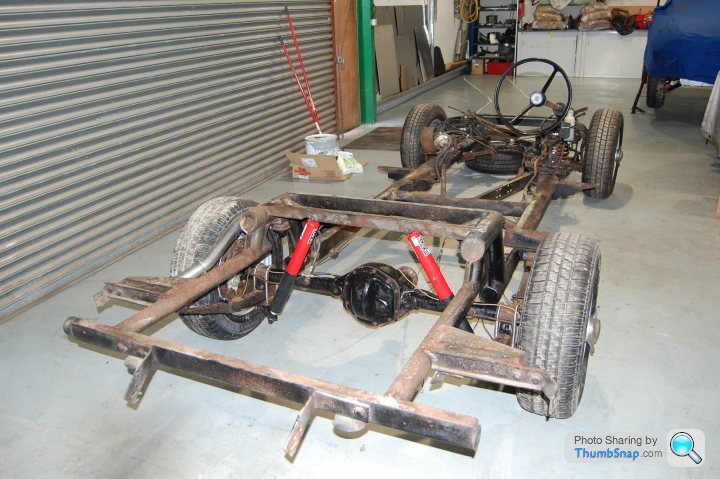
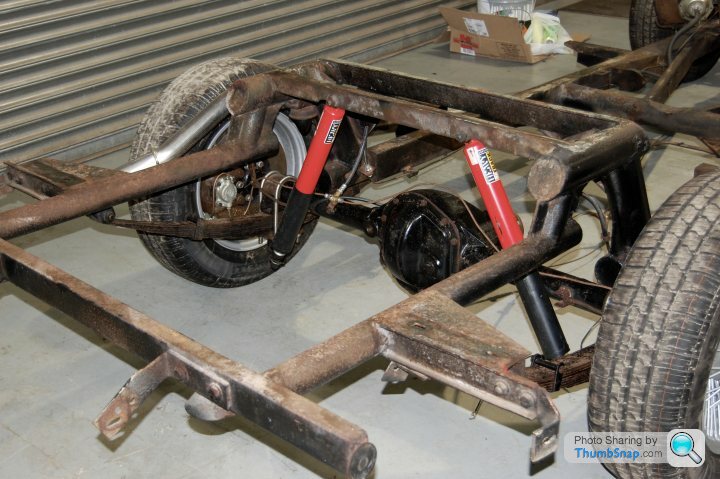
Here's the body number...not easy to read!

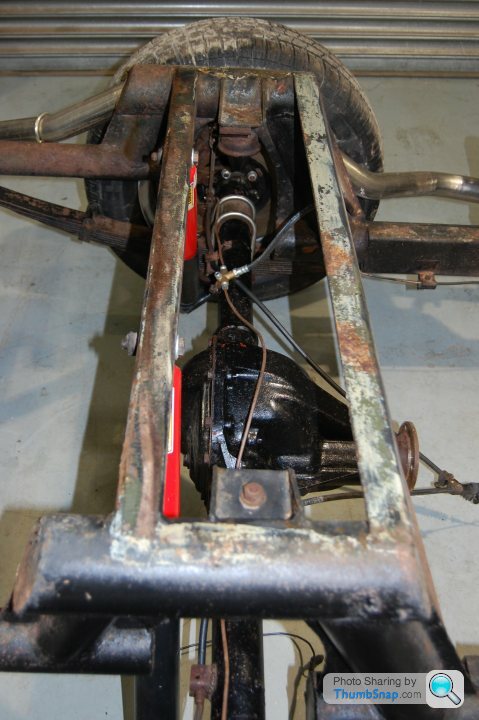
And the chassis number, much more clearly defined
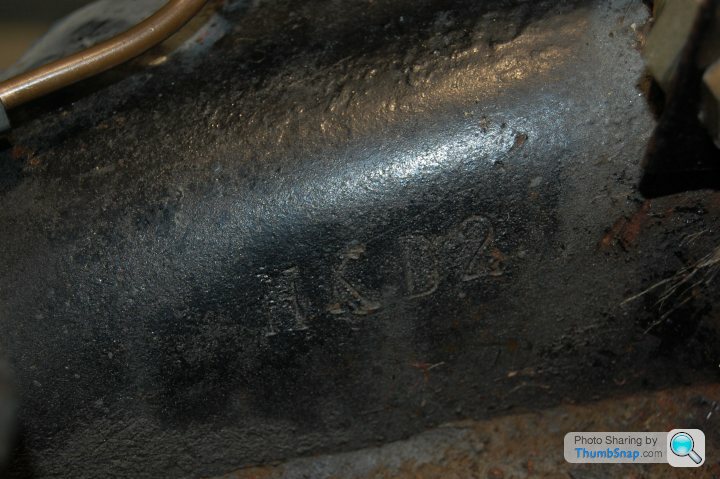
As mentioned before, taking the body off the chassis was likely to reveal a whole new list of jobs and necessitate the cleaning up of some areas hidden from view.

The body had benefitted from significant welding whilst in Geoff's hands, so was structually sound. However, some of the welding was a bit 'agricultural'.
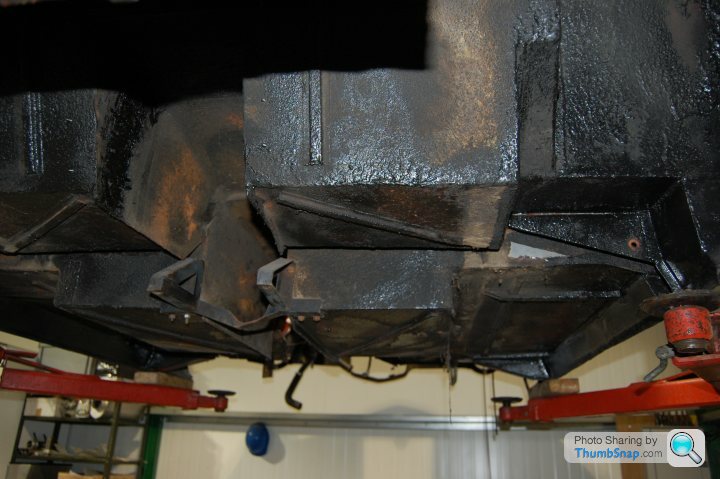
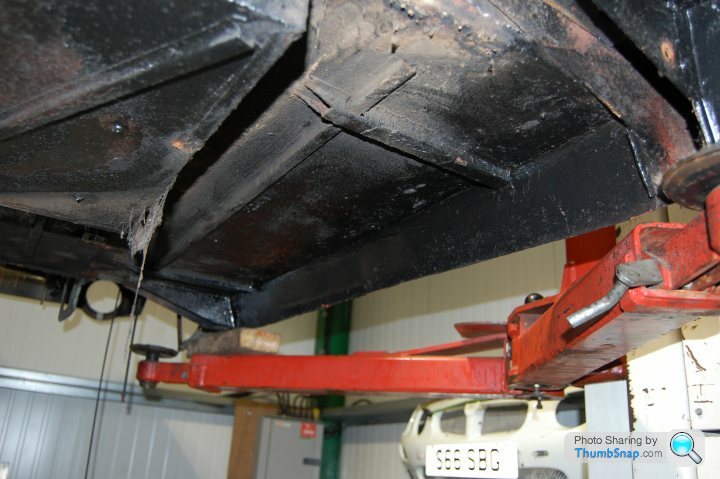
And some bits didn't appear to be welded at all...
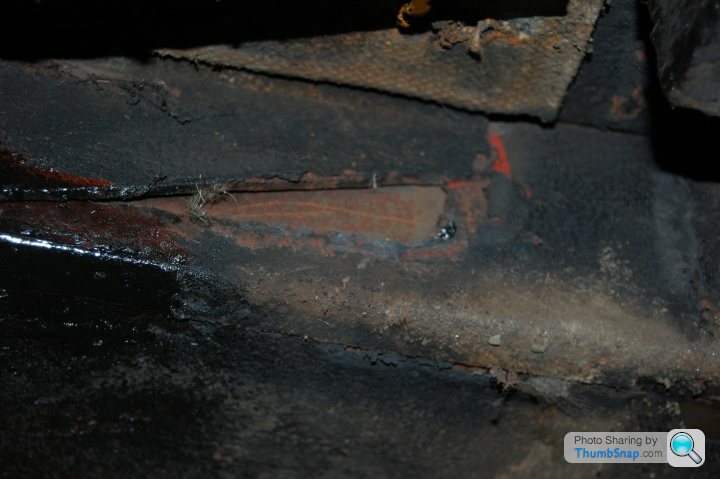
So the car was now back in pieces and we had the chance to compare what we had found with what we had included in our cost calculations. At this stage it didn't look too bad. There were a couple of areas that would require some welding, but that was about it.
What could possibly go wrong?!
Actually, as someone who had funded other restorations I wasn't quite as naive as I'm making out. I knew costs would likely escalate and timescales lengthen. I also knew that once started there would be no going back; bailing out part way through would be a road to financial disaster.
Very soon we were back to this...
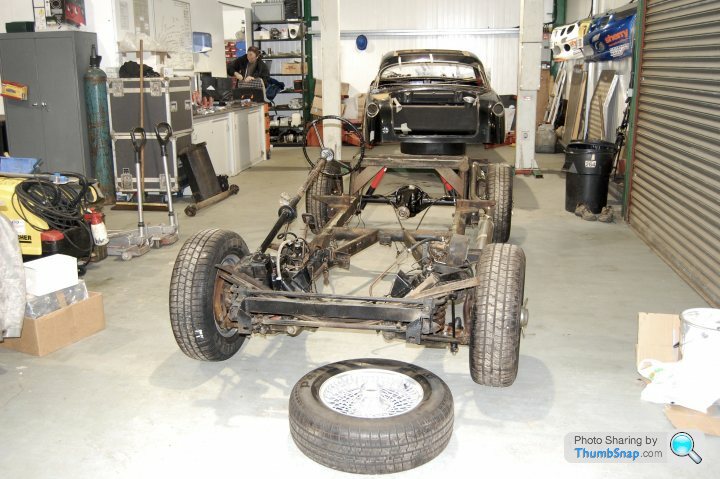
Steve captured the actual moment the body and chassis parted company.
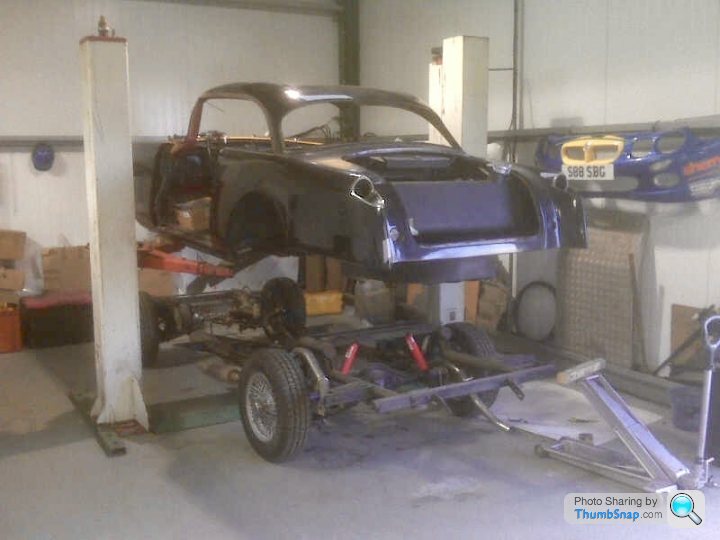
Taking the body off the chassis was a pivotal moment for a couple of reasons. Firstly, it would allow us to assess the real condition of the car (a bit of a risk) and secondly it would allow a more thorough restoration. If the answer to the first part wasn't as expected, the budget could be completely blown apart.
So what did we find?
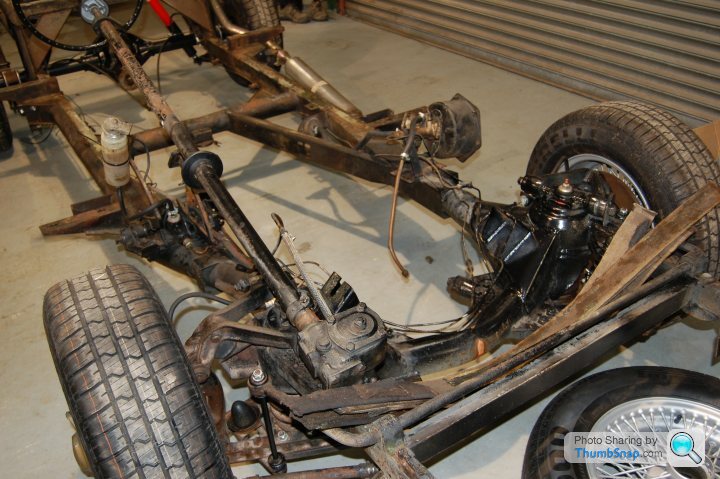
For those not familiar with the construction of the HK500, it is an amazing feat of engineering. The chassis appears to be massively over engineered, with chassis rails made from large diameter tubes and substantial cross members which are beefily braced. It would look at home as part of a ship or maybe a small bridge! The body is made from a patchwork of small panels stitched together to create a whole. For instance, the front wings form a single unit with the front panel and windscreen scuttle. Even though there is a separate chassis, the floor of the body is a welded steel structure that is reminiscent of monocoque construction. Given this 'belt and braces' approach, the amazing thing is how little rigidity the complete car possesses.
The chassis was in great condition and showed no evidence of collision damage, which was a relief. It still had the body number chalked on the cross member above the rear axle. Luckily that chalk number matched the body number in the factory records! As you would expect, the chassis had plenty of surface corrosion, but nothing serious. This is a testament to its sturdy construction as no real rust protection was applied by the factory, just a quick 'once over' with an underseal type product called 'Blaxon'. It was obvious from the areas that were completely bare that the quick waft of Blaxon was applied once the body was in place.
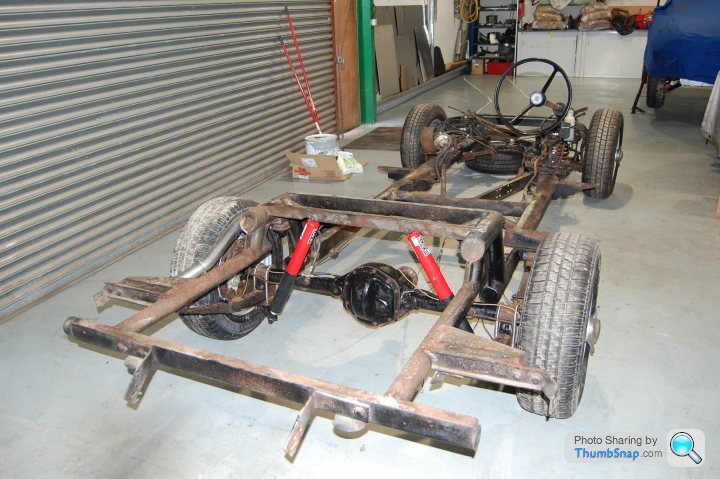
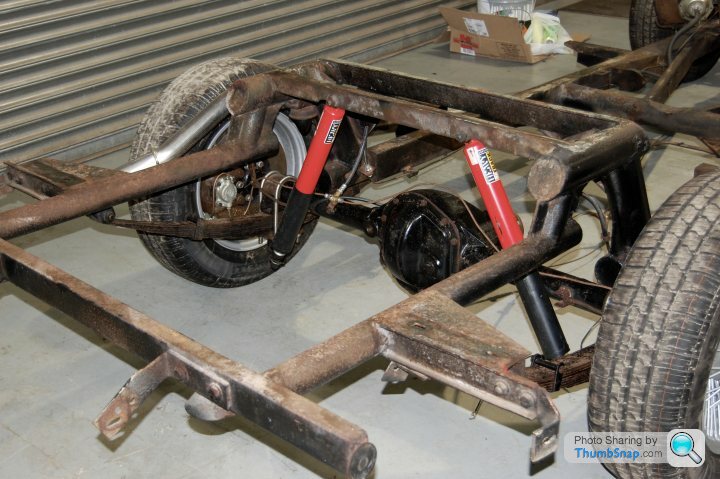
Here's the body number...not easy to read!

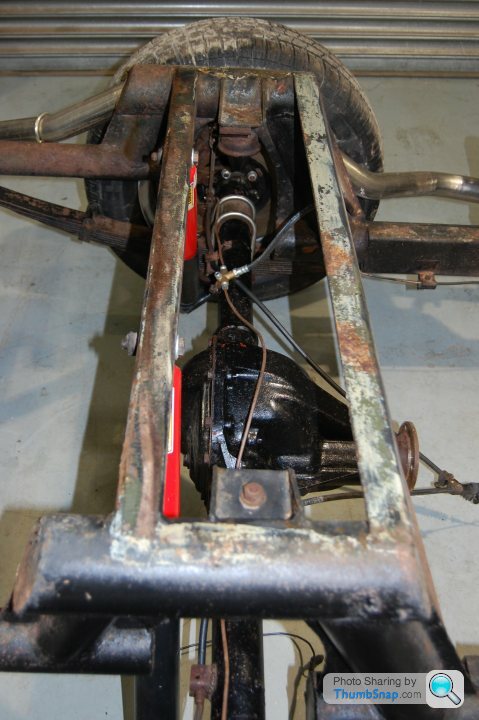
And the chassis number, much more clearly defined
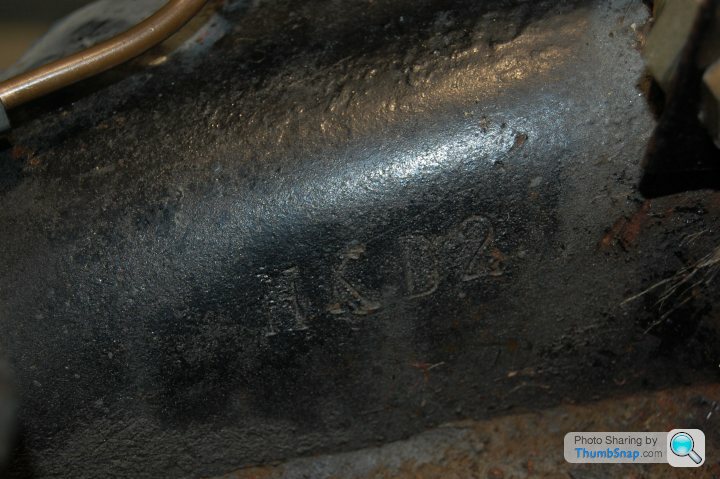
As mentioned before, taking the body off the chassis was likely to reveal a whole new list of jobs and necessitate the cleaning up of some areas hidden from view.

The body had benefitted from significant welding whilst in Geoff's hands, so was structually sound. However, some of the welding was a bit 'agricultural'.
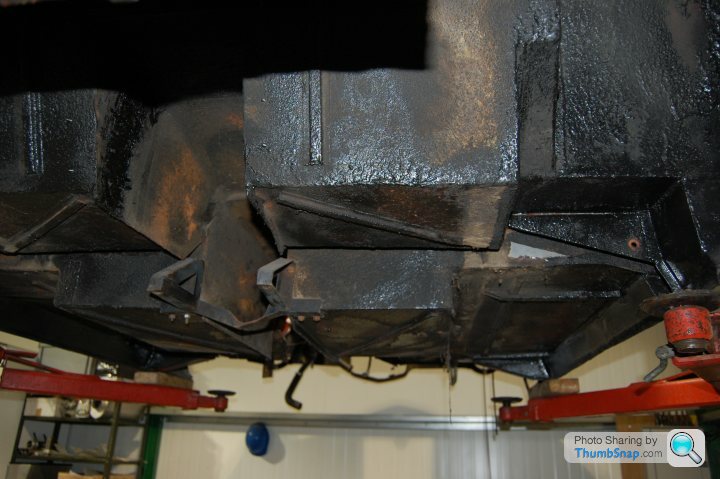
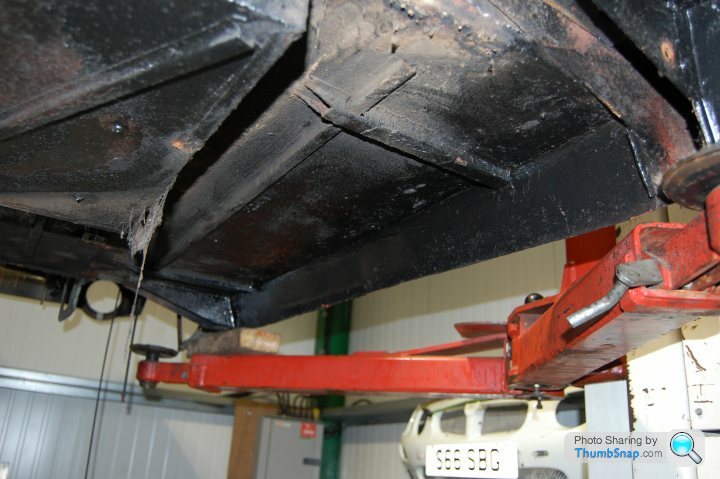
And some bits didn't appear to be welded at all...
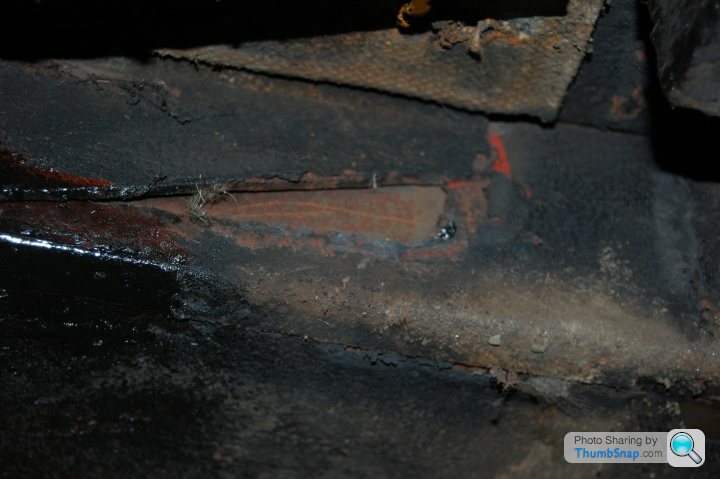
So the car was now back in pieces and we had the chance to compare what we had found with what we had included in our cost calculations. At this stage it didn't look too bad. There were a couple of areas that would require some welding, but that was about it.
Edited by theadman on Monday 21st November 22:18
I had a half term and Saturday job when I was about 15 so 1976 ish at Fulton motors in Maida vale they sold D atsuns one of my jobs was dewaxing New cars..bucket of paraffin and a sponge followed by turtle wax. In the compound was a v knackered face Vega in silver my memory tells me it had a push button autobox
I would take my smoke breaks in it ( as you did when a 70s teenager often wondered what became of it)
I would take my smoke breaks in it ( as you did when a 70s teenager often wondered what became of it)
Sorry for the lack of updates.
I've been visiting my daughter who lives in New Zealand. We haven't seen each other for over three years, thanks to Covid. Social media channels really help to bridge the distance, but it was only when we met at Auckland airport that I realised how much I had missed simply spending time together.
Cars might be a fascination and a consuming hobby, but the NZ trip really brought home that there are much more important things in life!
Anyway, if jet lag kicks in, the next installment might be at 3am tomorrow morning!
I've been visiting my daughter who lives in New Zealand. We haven't seen each other for over three years, thanks to Covid. Social media channels really help to bridge the distance, but it was only when we met at Auckland airport that I realised how much I had missed simply spending time together.
Cars might be a fascination and a consuming hobby, but the NZ trip really brought home that there are much more important things in life!
Anyway, if jet lag kicks in, the next installment might be at 3am tomorrow morning!

A brief recap for anyone not wanting to trawl the previous 7 pages.
In 1999 I bought the car thinking it would take six months to get back on the road.
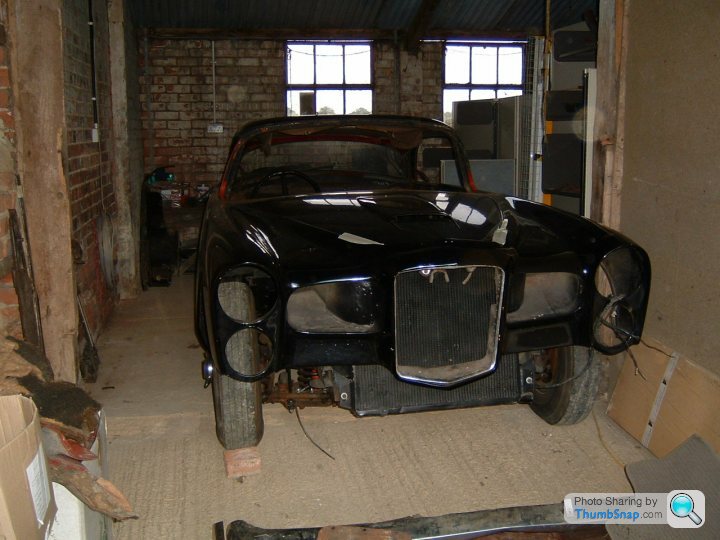
It took a bit longer...by 2007 it could move under its own steam, but was a long way from a visit to the MOT station.
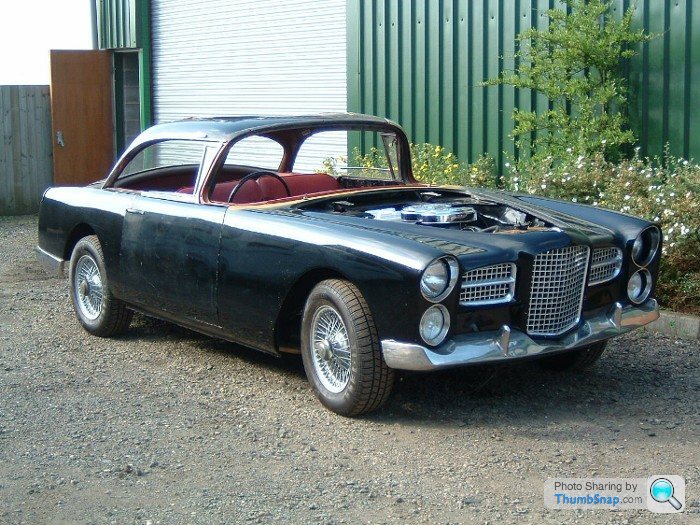
The next year it was back to this...
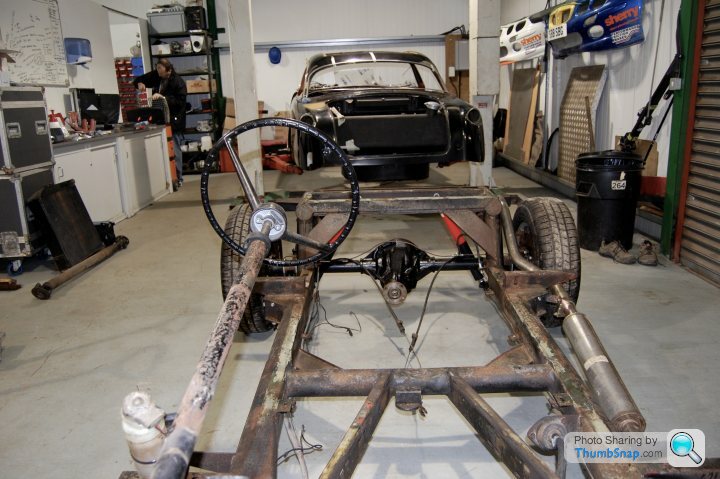
So...let's pick up the story here.
By the end of 2008 the chassis was beginning to resemble how it was when it left the factory in 1958, 50 years earlier. At that time it was given no real rust protection apart from a quick blow over with a product called 'Blaxon' that was an inferior version of the modern day 'Schultz' stone chip. It was clear that this had not been applied thoroughly as all the upper surfaces of the chassis were really patchy with areas of bare metal. Thank goodness the chassis sections are of a pretty heavy gauge because the body was insulated from the chassis by long pieces of webbing that could have been custom made to soak up and then trap moisture. You can see these lying across the chassis just behind the front crossmember in the photo below.
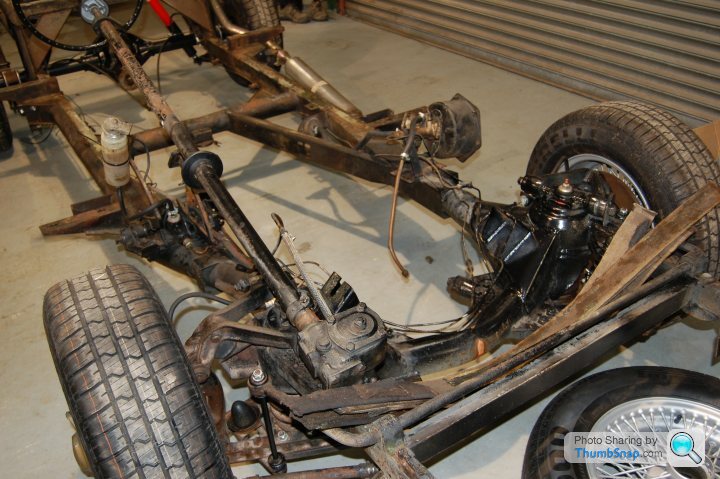
Having rebuilt the brakes at each corner early on in the restoration, it made sense to renew all the brake lines now they were completely exposed. Whilst the result is entirely functional, I was hoping for visual perfection as well and the wavy lines aren't really to the standard I was aiming for. However, I think they are fairly true to the factory original specification. They might now be out of sight, but they aren't out of mind!
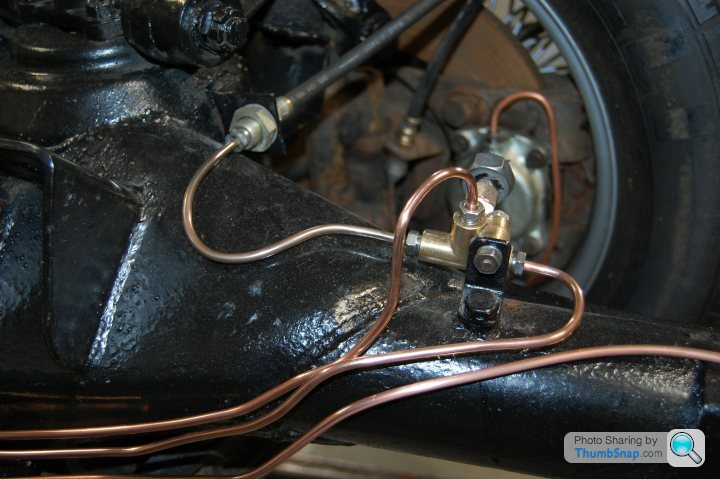
As you can see, the chassis wasn't completely stripped of all components as most of these had already been rebuilt in the intervening years and my plan wasn't for a completely concours car, as having had an E-Type rebuilt to that standard a few years earlier I ended up being afraid to use it. Therefore, it was agreed that the best finish we could achieve would be to hand paint the chassis with chassis enamel. This would protect it and vastly improve the under car appearance. Several coats were duly applied and the end result was pretty good.
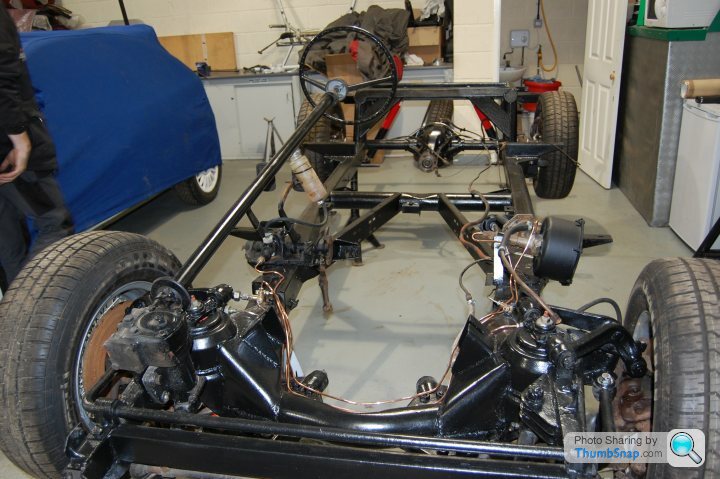
The factory chalk numbering was left, as it seemed a shame to paint over it.
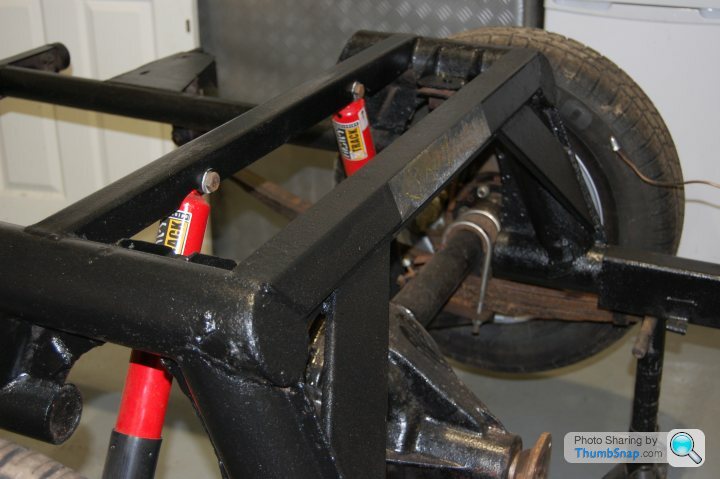
Sorting the chassis out and raising the bar in terms of the complete restoration led us to re-evaluate all other aspects of the project.
The body was always going to require a respray. It was suffering from head to toe micro-blistering and the paint was rubbish anyway. However, it was now becoming much more important to find someone willing to work to high standards without breaking the bank. This ruled out the top names as those I talked to were wanting upwards of £20,000 before they even saw the car. And this was over ten years ago!
All the work completed earlier in the restoration had been done by people who were known in their field, so the quality was good. I didn't feel the need to re-address any of the work so far.
The engine had been rebuilt according to the previous owner, so I wasn't expecting any issues on that front.
Whilst the seats and door cards had been retrimmed to a high standard, most of the rest of the interior trim was missing. As it would need to be remade anyway upping the game would have no impact in this area. The dashboard was now looking good, so there was no impact here either. One worry was actually keeping the retrimmed seats safe and in good condition until they were required.
That left the glass and the exterior trim. The condition of both could only be described as average, at best. The bigger challenge was the trim. Facel's principal business was the manufacture of stainless steel items for a range of industries. Given this expertise, it was only natural for them to make all the brightwork for their cars from stainless rather than chrome. Stainless is very hard and therefore difficult to refinish...it requires significant polishing to bring the shine back and any marks or scratches are hard to remove. After enquiring around a number of the chrome finishers and polishers I realised they wouldn't all be willing to take the Facel brightwork on as a project. But, if I attempted to bring the trim back to an acceptable level myself (which had been the original plan) I knew I was going to fall well short of the standard now required.
As the brightwork might prove to be one of the most difficult issues to solve, I set about researching this in 2009. By September, having talked to all the polishers and platers present at the Beaulieu Autojumble it became clear that the main contender was Derby Plating, with Castle Polishing and Plating the only real alternative. With all the brightwork clanking around in the back of my then current company car I set off to visit both of them in a single round trip. Derby Plating discounted themselves on two fronts; a real lack of enthusiasm for tackling stainless steel and price (which might have been a result of the former). Castle Polishing and Plating couldn't have been more different. 'Stainless steel...it's more difficult, but no problem, it's what we do.' The quoted price reflected that attitude as well, so I left everything with them and awaited their call.
A couple of months later the parts were ready for collection. Sadly, again I didn't think to take pictures as a before and after contrast would have been interesting. The difference was stark! Over the years the Facel had obviously been in a few tight squeezes and so the stainless strips that run above the sills were quite badly dented and scraped. Whilst not perfect, they now looked closer to factory fresh. This was the first trial fit simply to sort out the door alignment...
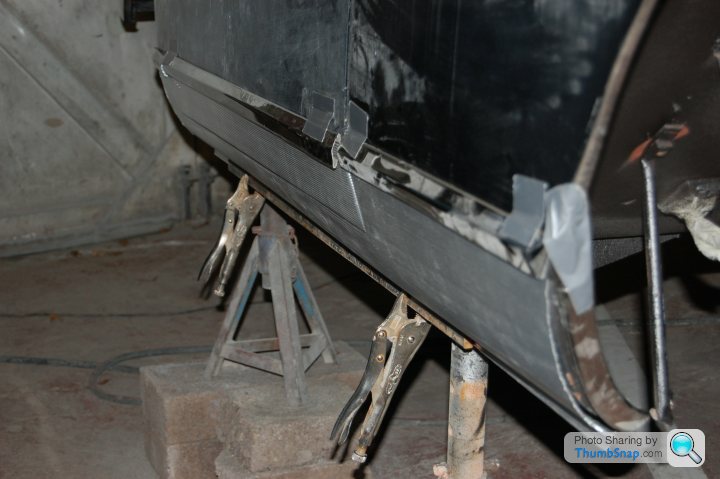
The car has a number of stainless finishers all the way round the tops and bottoms of the windows. On one side these had all been damaged by someone using a sandblaster close to the car sometime in the 1980s, so they were all pitted. This had all been polished out, but we later found that the polishing process had relieved the curves in the metal, making them really difficult to refit to the car.
In the meantime the hunt was on to find someone suitable to tackle the micro-blistering and repaint the car, but more on that next time.
In 1999 I bought the car thinking it would take six months to get back on the road.
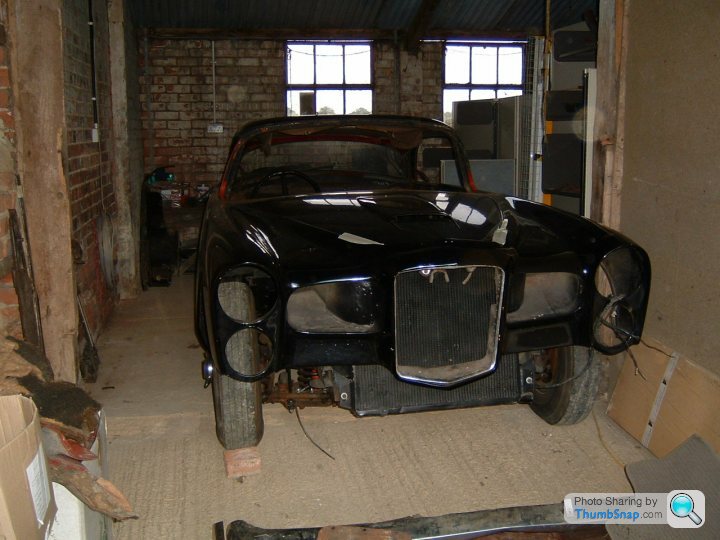
It took a bit longer...by 2007 it could move under its own steam, but was a long way from a visit to the MOT station.
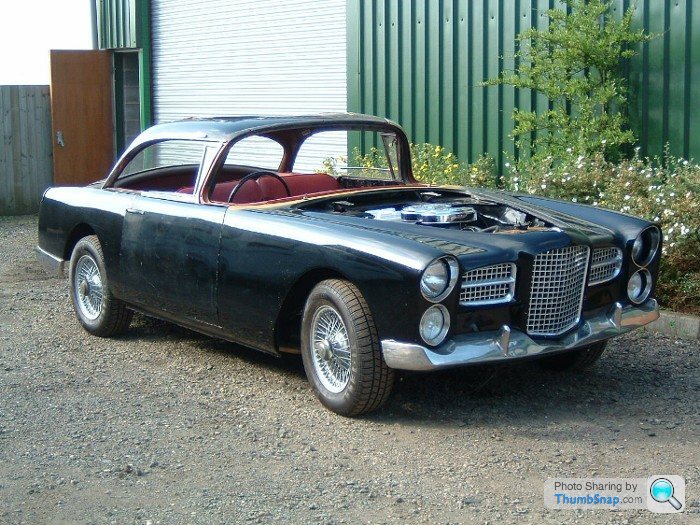
The next year it was back to this...
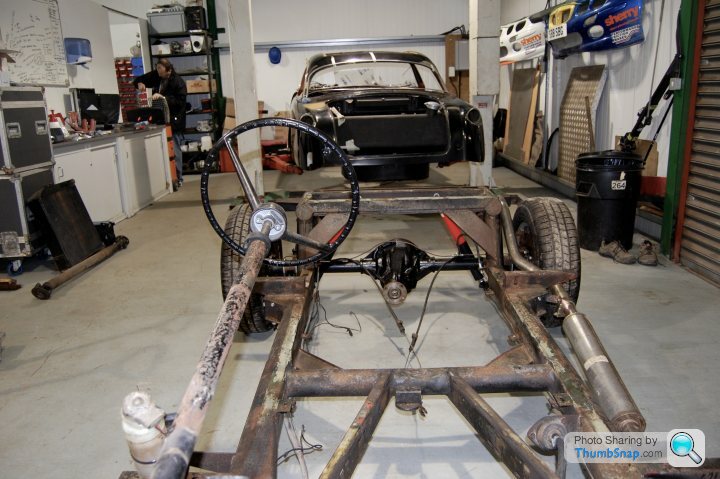
So...let's pick up the story here.
By the end of 2008 the chassis was beginning to resemble how it was when it left the factory in 1958, 50 years earlier. At that time it was given no real rust protection apart from a quick blow over with a product called 'Blaxon' that was an inferior version of the modern day 'Schultz' stone chip. It was clear that this had not been applied thoroughly as all the upper surfaces of the chassis were really patchy with areas of bare metal. Thank goodness the chassis sections are of a pretty heavy gauge because the body was insulated from the chassis by long pieces of webbing that could have been custom made to soak up and then trap moisture. You can see these lying across the chassis just behind the front crossmember in the photo below.
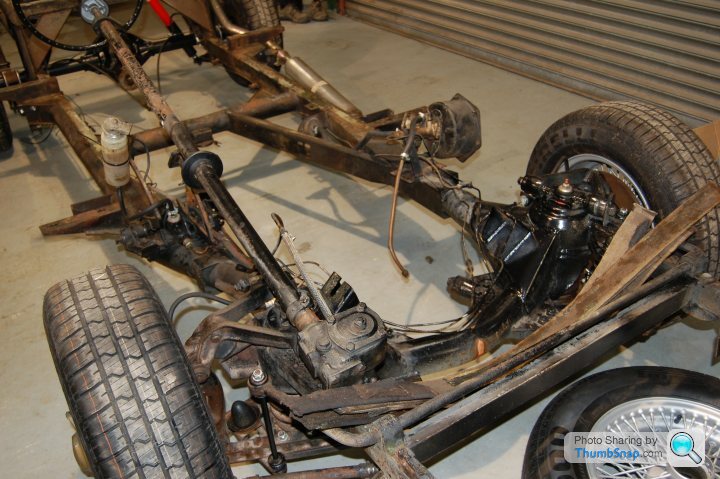
Having rebuilt the brakes at each corner early on in the restoration, it made sense to renew all the brake lines now they were completely exposed. Whilst the result is entirely functional, I was hoping for visual perfection as well and the wavy lines aren't really to the standard I was aiming for. However, I think they are fairly true to the factory original specification. They might now be out of sight, but they aren't out of mind!
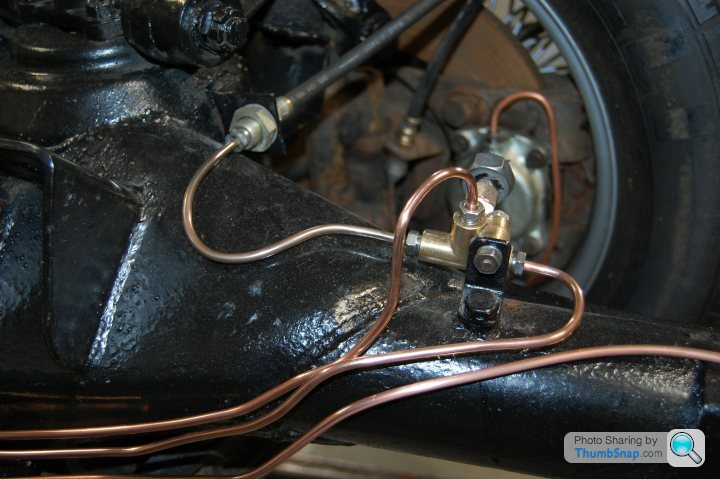
As you can see, the chassis wasn't completely stripped of all components as most of these had already been rebuilt in the intervening years and my plan wasn't for a completely concours car, as having had an E-Type rebuilt to that standard a few years earlier I ended up being afraid to use it. Therefore, it was agreed that the best finish we could achieve would be to hand paint the chassis with chassis enamel. This would protect it and vastly improve the under car appearance. Several coats were duly applied and the end result was pretty good.
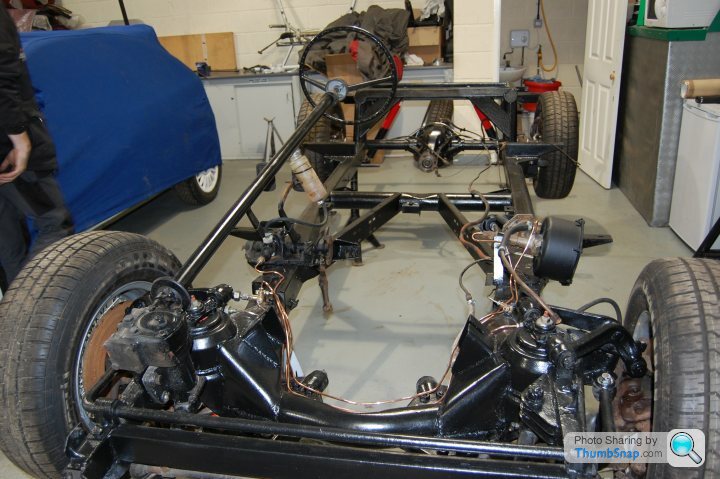
The factory chalk numbering was left, as it seemed a shame to paint over it.
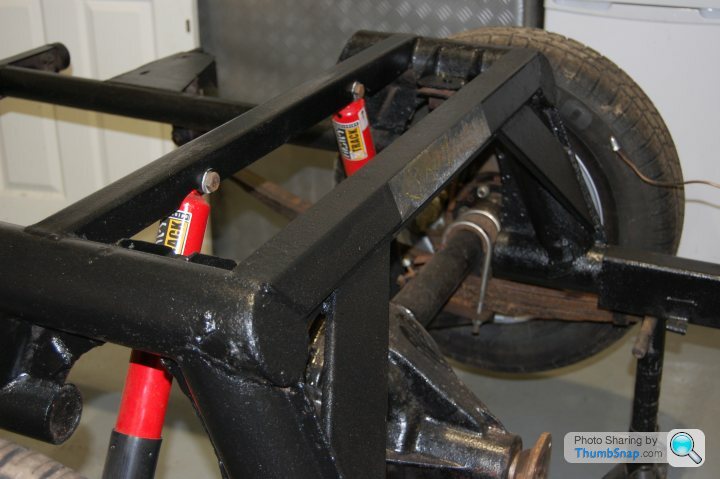
Sorting the chassis out and raising the bar in terms of the complete restoration led us to re-evaluate all other aspects of the project.
The body was always going to require a respray. It was suffering from head to toe micro-blistering and the paint was rubbish anyway. However, it was now becoming much more important to find someone willing to work to high standards without breaking the bank. This ruled out the top names as those I talked to were wanting upwards of £20,000 before they even saw the car. And this was over ten years ago!
All the work completed earlier in the restoration had been done by people who were known in their field, so the quality was good. I didn't feel the need to re-address any of the work so far.
The engine had been rebuilt according to the previous owner, so I wasn't expecting any issues on that front.
Whilst the seats and door cards had been retrimmed to a high standard, most of the rest of the interior trim was missing. As it would need to be remade anyway upping the game would have no impact in this area. The dashboard was now looking good, so there was no impact here either. One worry was actually keeping the retrimmed seats safe and in good condition until they were required.
That left the glass and the exterior trim. The condition of both could only be described as average, at best. The bigger challenge was the trim. Facel's principal business was the manufacture of stainless steel items for a range of industries. Given this expertise, it was only natural for them to make all the brightwork for their cars from stainless rather than chrome. Stainless is very hard and therefore difficult to refinish...it requires significant polishing to bring the shine back and any marks or scratches are hard to remove. After enquiring around a number of the chrome finishers and polishers I realised they wouldn't all be willing to take the Facel brightwork on as a project. But, if I attempted to bring the trim back to an acceptable level myself (which had been the original plan) I knew I was going to fall well short of the standard now required.
As the brightwork might prove to be one of the most difficult issues to solve, I set about researching this in 2009. By September, having talked to all the polishers and platers present at the Beaulieu Autojumble it became clear that the main contender was Derby Plating, with Castle Polishing and Plating the only real alternative. With all the brightwork clanking around in the back of my then current company car I set off to visit both of them in a single round trip. Derby Plating discounted themselves on two fronts; a real lack of enthusiasm for tackling stainless steel and price (which might have been a result of the former). Castle Polishing and Plating couldn't have been more different. 'Stainless steel...it's more difficult, but no problem, it's what we do.' The quoted price reflected that attitude as well, so I left everything with them and awaited their call.
A couple of months later the parts were ready for collection. Sadly, again I didn't think to take pictures as a before and after contrast would have been interesting. The difference was stark! Over the years the Facel had obviously been in a few tight squeezes and so the stainless strips that run above the sills were quite badly dented and scraped. Whilst not perfect, they now looked closer to factory fresh. This was the first trial fit simply to sort out the door alignment...
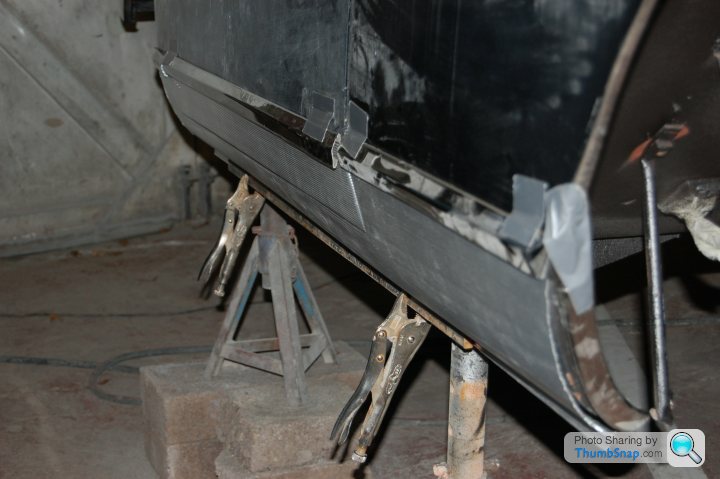
The car has a number of stainless finishers all the way round the tops and bottoms of the windows. On one side these had all been damaged by someone using a sandblaster close to the car sometime in the 1980s, so they were all pitted. This had all been polished out, but we later found that the polishing process had relieved the curves in the metal, making them really difficult to refit to the car.
In the meantime the hunt was on to find someone suitable to tackle the micro-blistering and repaint the car, but more on that next time.
theadman said:
Sorry for the lack of updates.
I've been visiting my daughter who lives in New Zealand. We haven't seen each other for over three years, thanks to Covid. Social media channels really help to bridge the distance, but it was only when we met at Auckland airport that I realised how much I had missed simply spending time together.
Cars might be a fascination and a consuming hobby, but the NZ trip really brought home that there are much more important things in life!
Anyway, if jet lag kicks in, the next installment might be at 3am tomorrow morning!
Fully understandable and no need to say sorry: I imagine she wants to know the updates before we do!! I've been visiting my daughter who lives in New Zealand. We haven't seen each other for over three years, thanks to Covid. Social media channels really help to bridge the distance, but it was only when we met at Auckland airport that I realised how much I had missed simply spending time together.
Cars might be a fascination and a consuming hobby, but the NZ trip really brought home that there are much more important things in life!
Anyway, if jet lag kicks in, the next installment might be at 3am tomorrow morning!


To take the kinks out of brake pipe use two lengths of four by two and roll the pipe back and forth, eventually you will have a perfectly straight piece of pipe. Then you can shape the line using sockets etc to give a nice radius. Result are pipes that look as if they were made in the factory.
Same applies to cables, a professional wireman gave me this advice, when you look at a harness made professionally you should be able to trace any wire inside without dismantling it as the wires will always run straight without crossing over.
The above made me think about brake pipes, there is nothing worse than brake lines that look like they were knitted and and are curved in all directions, rolling them takes out the kinks
Same applies to cables, a professional wireman gave me this advice, when you look at a harness made professionally you should be able to trace any wire inside without dismantling it as the wires will always run straight without crossing over.
The above made me think about brake pipes, there is nothing worse than brake lines that look like they were knitted and and are curved in all directions, rolling them takes out the kinks
Mercdriver, thanks for the tip about straight brake pipes. Some of the ones in the pictures were reworked later anyway, as I decided a dual circuit system would be a lot safer, given the car's performance potential, weight and virtually non existent handbrake. Having two wheels slowing you down would be a lot better than none in the event of a system failure!
Thanks for the most recent supportive comments.
Work on the car has started again, so, just maybe, the end is in sight? A photo from Tuesday...
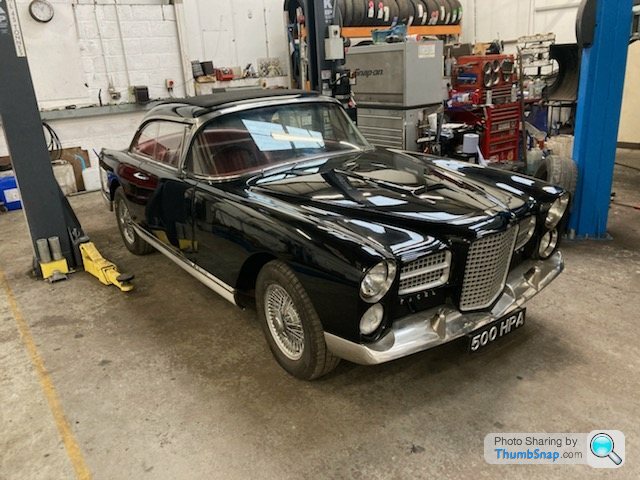
In the meantime, back to the story...
Having decided to 'do the job properly' and taken the car apart, the hunt was on for someone to complete the bodywork and then paint the car back in its original black.
John, the same friend who had put me on to the car originally back in 1999 had been following progress with interest. This was quite amazing, given that ten years had elapsed...he MUST have been interested!! John is pretty involved in the classic car scene, occasionally buying and selling cars and collecting 1950s Fords along the way. He and I had also judged the odd concours event together and also had connections through our respective jobs. John would often attend car events and it was at one such show that he came across a Capri that had had the most impressive respray in its original black. As you will probably know, spraying black is quite a challenge as it shows every blemish and imperfection. Both the preparation and the application need to be spot on for a pristine finish.
The Capri was so good that John approached the owner and started a conversation. It turned out that the owner's son had resprayed the car for him. John duly obtained contact details and then contacted me, saying he might have found the right person for the Facel.
A conversation with Gary and a trip down to Hayling Island where he was based was all it took for me to agree. Like many real diamonds, Gary's workshop didn't provide any clue to the quality of work being carried out. He was interested from the off. Much of his work was for insurance companies where quick turn around at an acceptable quality was the key to success. The idea of another car to showcase what he was actually capable of, where quality was the key and time was almost immaterial really appealed to him. He had done his father's Capri and a number of air cooled Volkswagens, but had never tried his hand at something more exotic. Everything he said filled me with confidence and so Steve built a jig for the body and sent it down to the south coast.
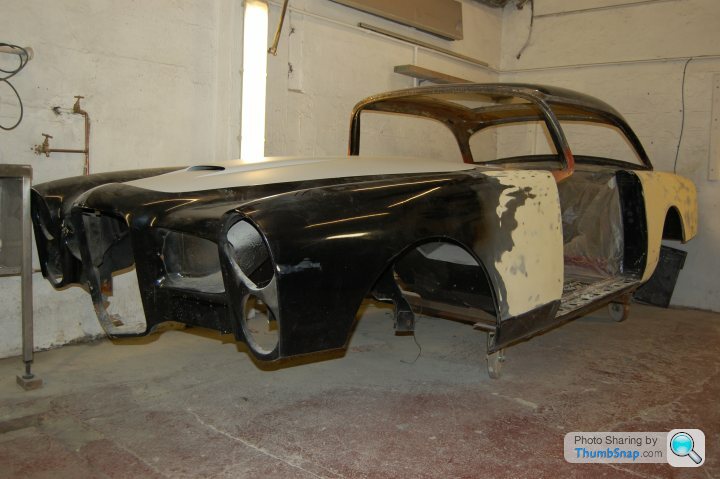
Gary and I debated whether to have the car dipped or not at some length. Back then, dipping was seen as the best way to go and as my car was more or less a bare shell it would have been very little effort to prepare the car.
The big factor in dipping's favour was that all the ugly secrets of the shell would be instantly revealed and Gary would then have a solid basis from which to start. I was quite in favour of going this route for several reasons. Firstly, it was obvious that the car's shape was attributable to a significant use of filler skim rather than the underlying metalwork. Secondly, the car had a bad case of 'measles' - it was badly microblistered on every part of the bodywork. This suggested that there was moisture under the paint and with the presence of all that filler I was concerned that the moisture might also be present between the metal and the skim coat. Dipping would instantly remove the filler and chase any moisture away.
To my surprise Gary wasn't keen. I didn't understand it...dipping was the new miracle cure for rust and new companies were springing up all over the place offering the service as an almost 'must do' in any restoration. Gary was worried that if the Facel was to be a 'keeper' the chemical process of dipping might cause problems in the future. He really was ahead of the game...I now know a number of people who had cars dipped as part of a rebuild that are now suffering consequencies years later as the acid leaches out of nooks and crannies to play havoc with shiny paint.
I'm not saying dipping is bad per se, but time has shown that the process lives or dies by the thoroughness of the neutralising process after dipping has taken place.
So, we didn't go down that route (and the paint is still fantastic ten years after application which is quite a result given the epic microblistering Gary had to cure).
Gary set about stripping the bodywork a panel at a time. The previous photo shows the progress, starting from the back of the car. All went well, with plenty of skim coming off the car down both sides. Most of the bottom 18 inches of the car had needed patching or repair panels. This work had been done by the previous owner at his bodyshop. By reworking what was there Gary managed to drastically reduce the reliance on building up the shape with filler.
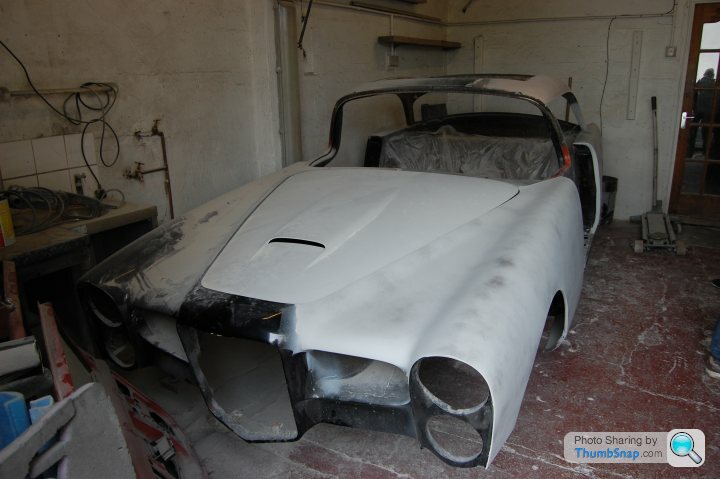
The main issue Gary came across was that the whole of the panel between the base of the windscreen and the trailing edge of the bonnet was riddled with rust that had just been filled over. Whilst this was not insurmountable it did cause a particular problem. Windscreen fitment is known to be a headache on the HK500, not helped by the dogleg 'A' pillars nor the lack of body rigidity. The rotten panel meant that Gary had to remake the whole length of the lip at the base of the windscreen. If the curvature was wrong, the windscreen wouldn't fit, or would crack once fitted. I spent many a sleepless night worrying about this as Gary had had little original metal in the way of a template to recreate this area.
The rest of the bodywork was pretty straightforward, but very time consuming. The whole front of the car was only approximately the same shape as when it left the factory. At least we had the original grilles and surrounds. As it was, these didn't fit very well at all. Gary had to spend time using the brightwork as his template and adjust the body to fit.
The roof was also a bit of a nightmare as Gary had to reshape it, again removing layers of skimmed filler.

During the reworking of the front of the car. You would never have guessed it was so far out, but offering up the bumpers gave the game away.
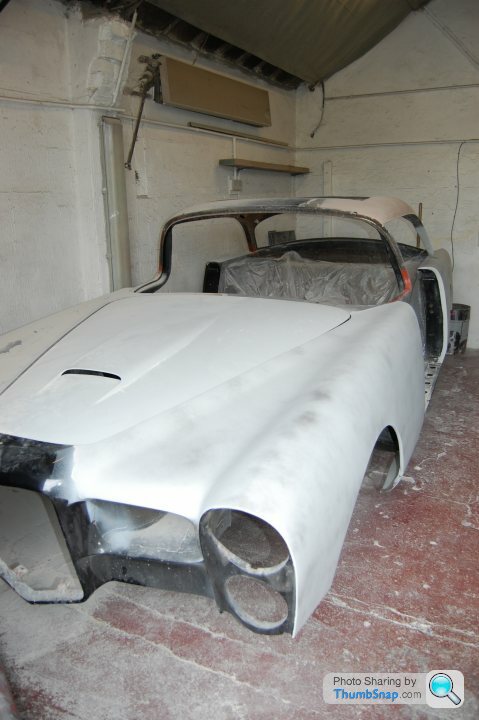
Reworking around the windscreen...the main area was the base of the screen, but the 'A' pillars required attention too.
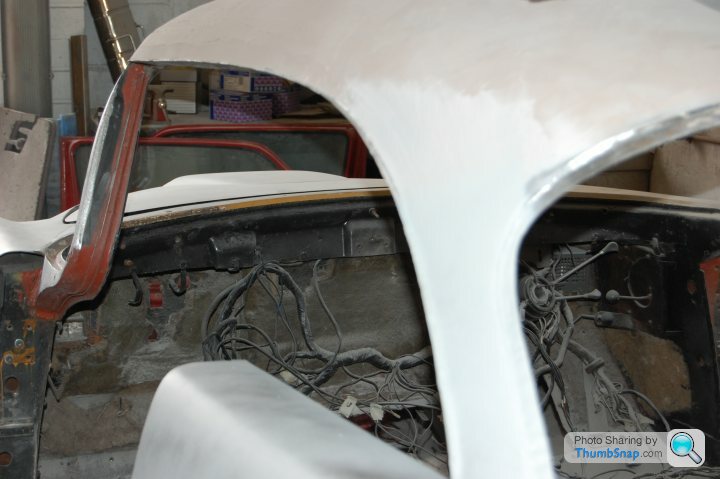
Finally, the car was ready for painting.
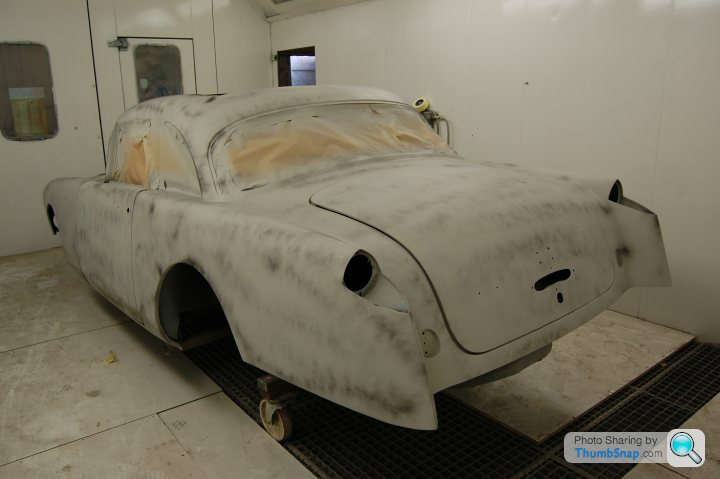
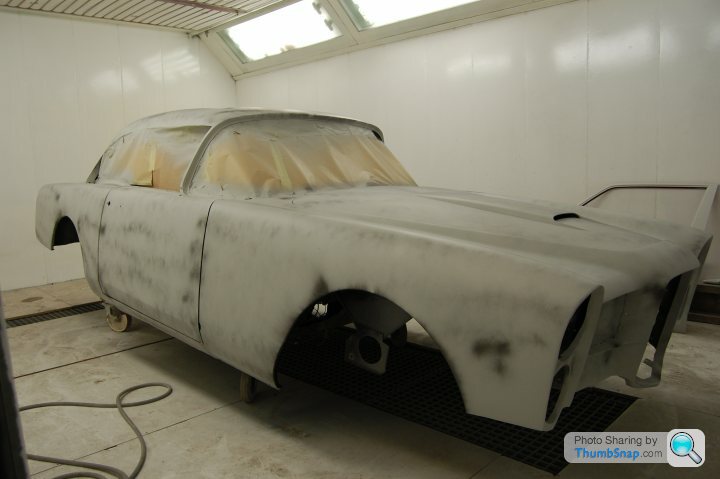
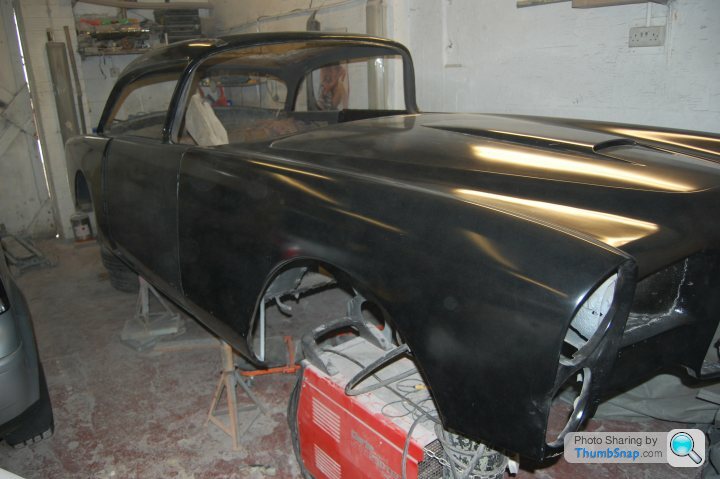
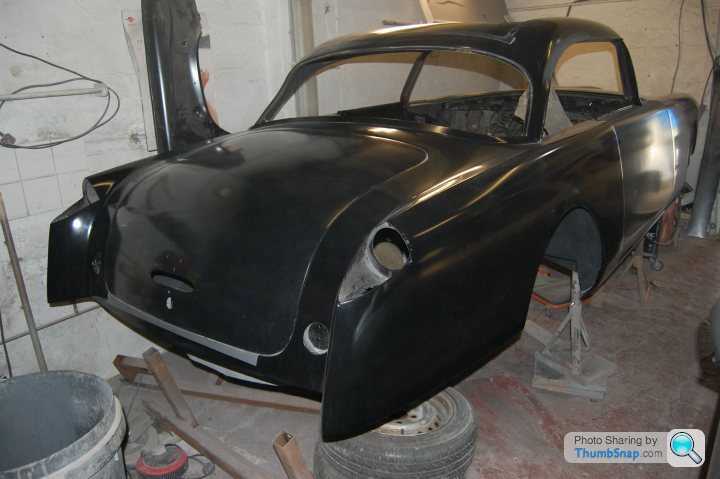
Before the final coats the side trims were cut to shape and trial fitted. This was another job where it had to be right first time as there was only just enough of the aluminium trim.
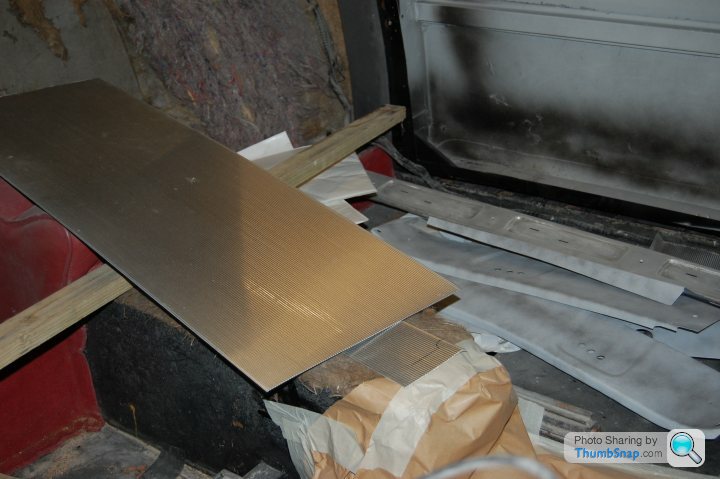
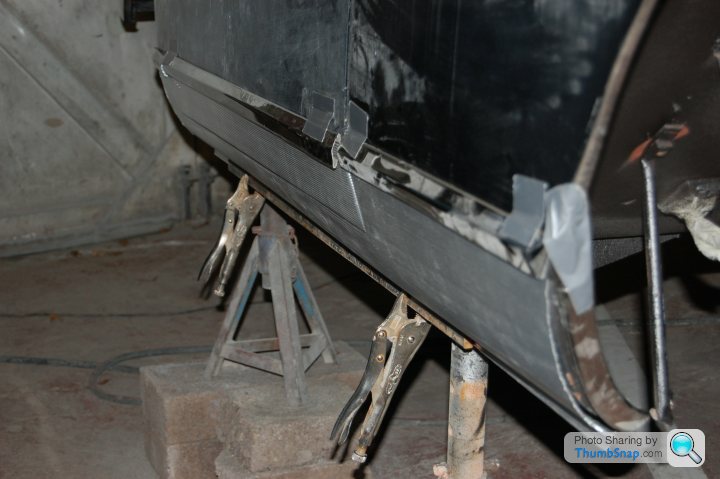
The front grilles and rear lights were also fitted to ensure there were no issues.
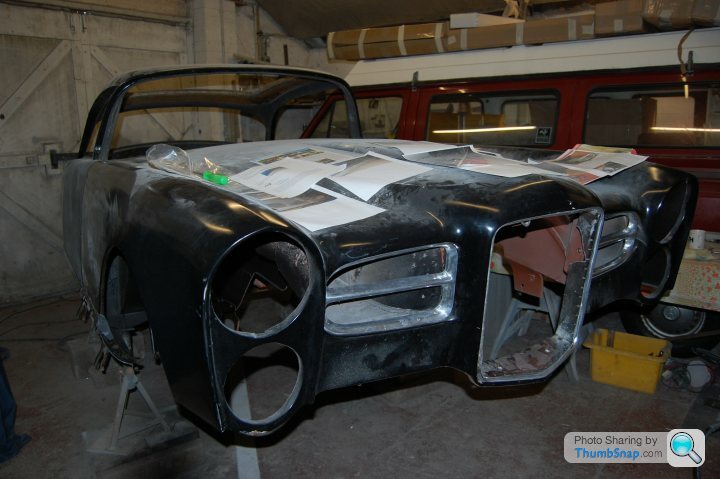
Gary surveys the work that has taken him over a year so far (between other jobs).

And then it was time for the final coats to be applied, rubbed down and polished. This was the point when I knew I had made the right decision to go with Gary...

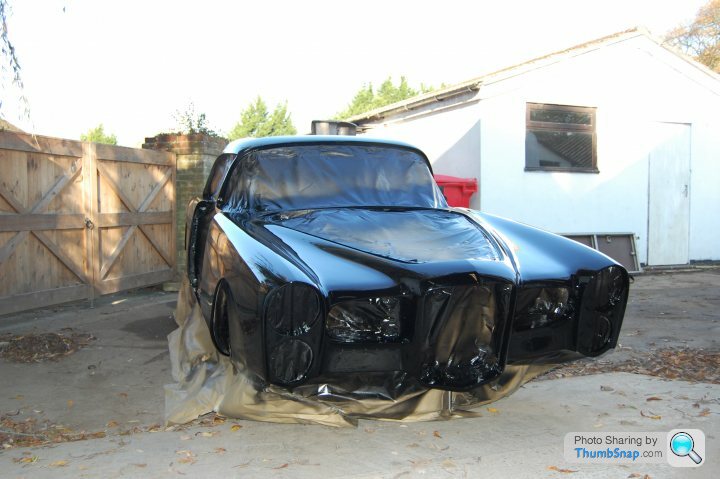
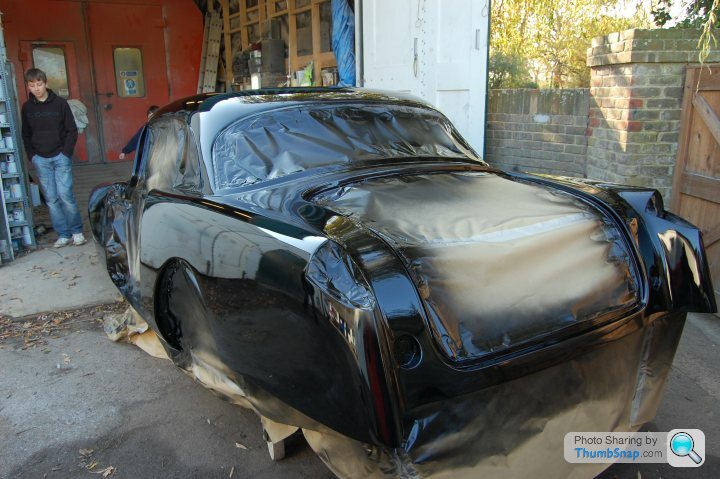
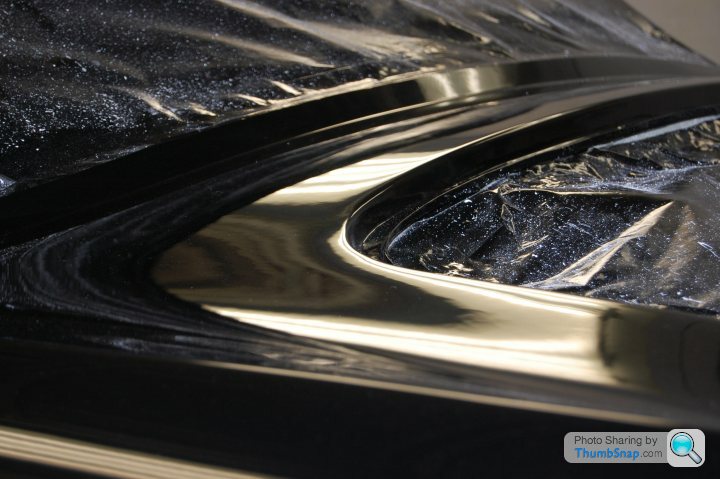
Finally, it was time to fit the front grilles and rear lights to check alignment...but they would have to come off the car again later.


So, finally the body and chassis were both brought back to the standard I was aiming for; excellent, but not necessarily concours. All that was required now was to put the car back together!
Work on the car has started again, so, just maybe, the end is in sight? A photo from Tuesday...
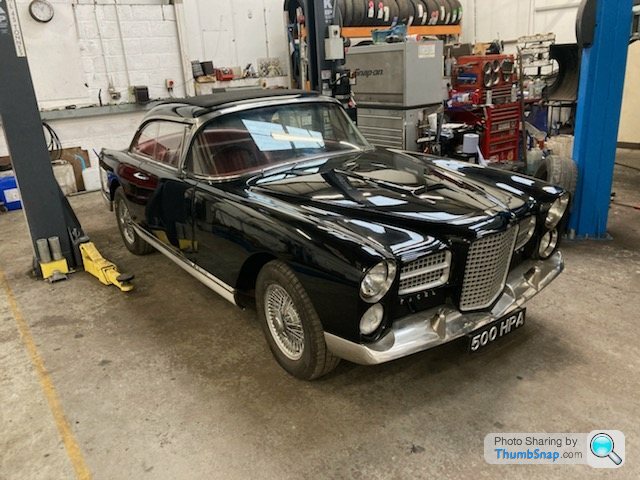
In the meantime, back to the story...
Having decided to 'do the job properly' and taken the car apart, the hunt was on for someone to complete the bodywork and then paint the car back in its original black.
John, the same friend who had put me on to the car originally back in 1999 had been following progress with interest. This was quite amazing, given that ten years had elapsed...he MUST have been interested!! John is pretty involved in the classic car scene, occasionally buying and selling cars and collecting 1950s Fords along the way. He and I had also judged the odd concours event together and also had connections through our respective jobs. John would often attend car events and it was at one such show that he came across a Capri that had had the most impressive respray in its original black. As you will probably know, spraying black is quite a challenge as it shows every blemish and imperfection. Both the preparation and the application need to be spot on for a pristine finish.
The Capri was so good that John approached the owner and started a conversation. It turned out that the owner's son had resprayed the car for him. John duly obtained contact details and then contacted me, saying he might have found the right person for the Facel.
A conversation with Gary and a trip down to Hayling Island where he was based was all it took for me to agree. Like many real diamonds, Gary's workshop didn't provide any clue to the quality of work being carried out. He was interested from the off. Much of his work was for insurance companies where quick turn around at an acceptable quality was the key to success. The idea of another car to showcase what he was actually capable of, where quality was the key and time was almost immaterial really appealed to him. He had done his father's Capri and a number of air cooled Volkswagens, but had never tried his hand at something more exotic. Everything he said filled me with confidence and so Steve built a jig for the body and sent it down to the south coast.
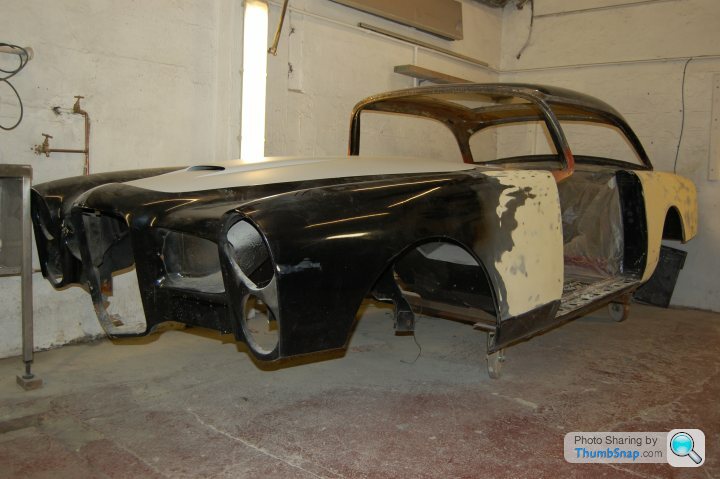
Gary and I debated whether to have the car dipped or not at some length. Back then, dipping was seen as the best way to go and as my car was more or less a bare shell it would have been very little effort to prepare the car.
The big factor in dipping's favour was that all the ugly secrets of the shell would be instantly revealed and Gary would then have a solid basis from which to start. I was quite in favour of going this route for several reasons. Firstly, it was obvious that the car's shape was attributable to a significant use of filler skim rather than the underlying metalwork. Secondly, the car had a bad case of 'measles' - it was badly microblistered on every part of the bodywork. This suggested that there was moisture under the paint and with the presence of all that filler I was concerned that the moisture might also be present between the metal and the skim coat. Dipping would instantly remove the filler and chase any moisture away.
To my surprise Gary wasn't keen. I didn't understand it...dipping was the new miracle cure for rust and new companies were springing up all over the place offering the service as an almost 'must do' in any restoration. Gary was worried that if the Facel was to be a 'keeper' the chemical process of dipping might cause problems in the future. He really was ahead of the game...I now know a number of people who had cars dipped as part of a rebuild that are now suffering consequencies years later as the acid leaches out of nooks and crannies to play havoc with shiny paint.
I'm not saying dipping is bad per se, but time has shown that the process lives or dies by the thoroughness of the neutralising process after dipping has taken place.
So, we didn't go down that route (and the paint is still fantastic ten years after application which is quite a result given the epic microblistering Gary had to cure).
Gary set about stripping the bodywork a panel at a time. The previous photo shows the progress, starting from the back of the car. All went well, with plenty of skim coming off the car down both sides. Most of the bottom 18 inches of the car had needed patching or repair panels. This work had been done by the previous owner at his bodyshop. By reworking what was there Gary managed to drastically reduce the reliance on building up the shape with filler.
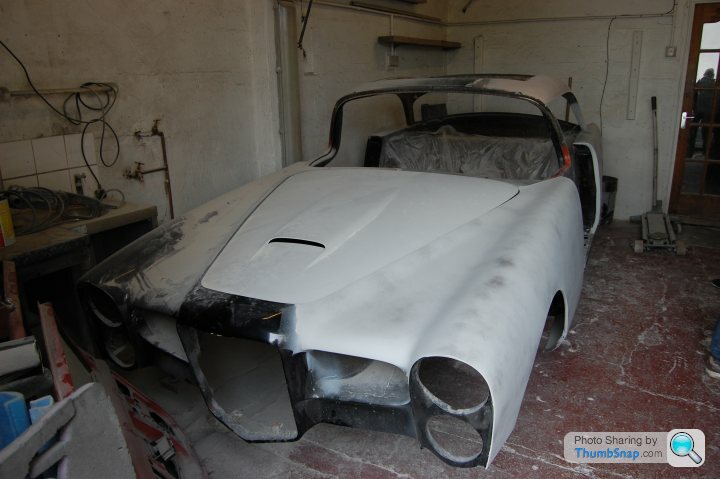
The main issue Gary came across was that the whole of the panel between the base of the windscreen and the trailing edge of the bonnet was riddled with rust that had just been filled over. Whilst this was not insurmountable it did cause a particular problem. Windscreen fitment is known to be a headache on the HK500, not helped by the dogleg 'A' pillars nor the lack of body rigidity. The rotten panel meant that Gary had to remake the whole length of the lip at the base of the windscreen. If the curvature was wrong, the windscreen wouldn't fit, or would crack once fitted. I spent many a sleepless night worrying about this as Gary had had little original metal in the way of a template to recreate this area.
The rest of the bodywork was pretty straightforward, but very time consuming. The whole front of the car was only approximately the same shape as when it left the factory. At least we had the original grilles and surrounds. As it was, these didn't fit very well at all. Gary had to spend time using the brightwork as his template and adjust the body to fit.
The roof was also a bit of a nightmare as Gary had to reshape it, again removing layers of skimmed filler.

During the reworking of the front of the car. You would never have guessed it was so far out, but offering up the bumpers gave the game away.
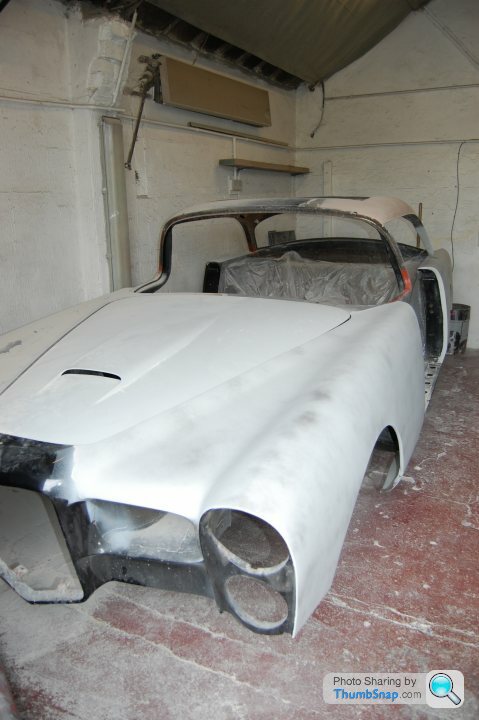
Reworking around the windscreen...the main area was the base of the screen, but the 'A' pillars required attention too.
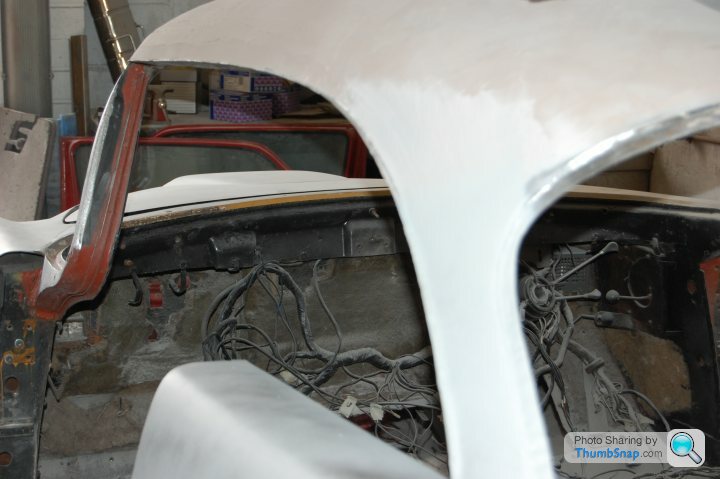
Finally, the car was ready for painting.
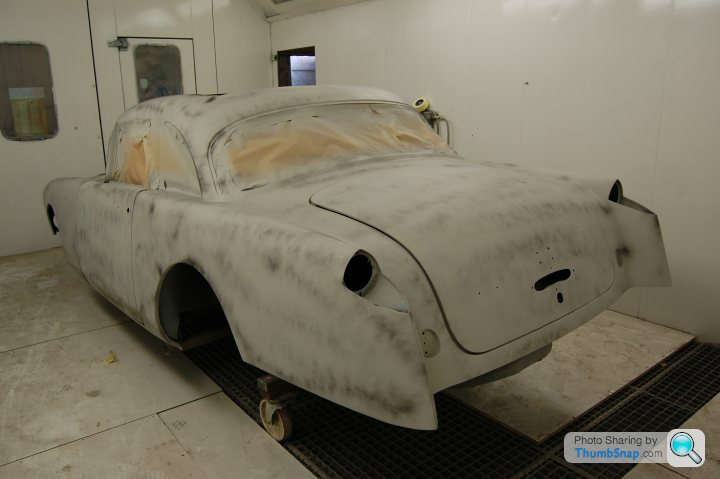
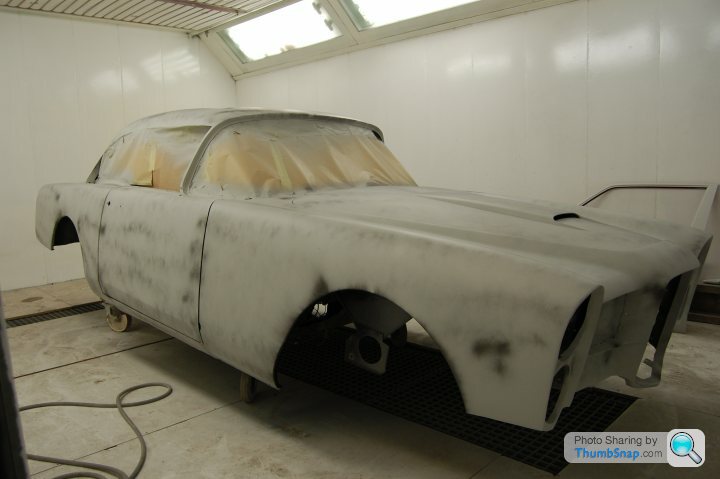
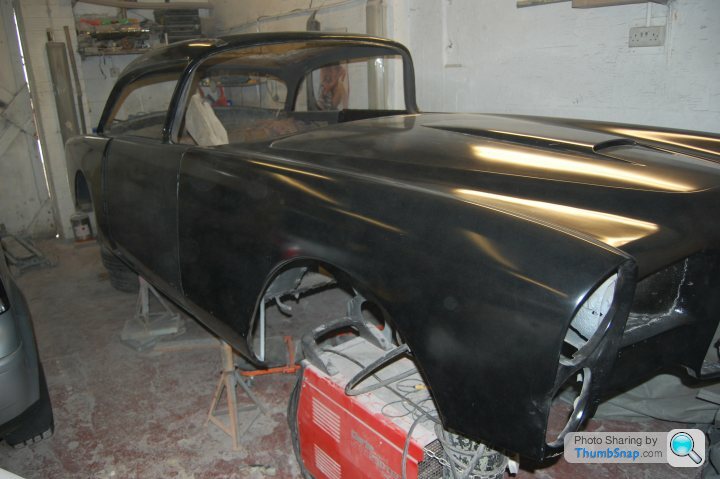
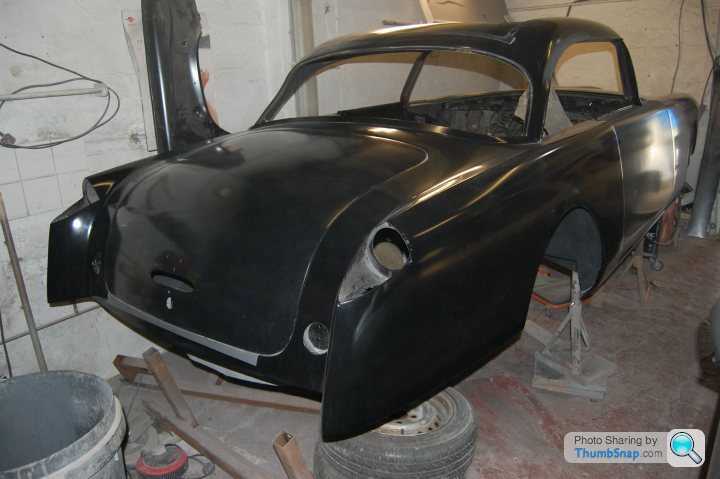
Before the final coats the side trims were cut to shape and trial fitted. This was another job where it had to be right first time as there was only just enough of the aluminium trim.
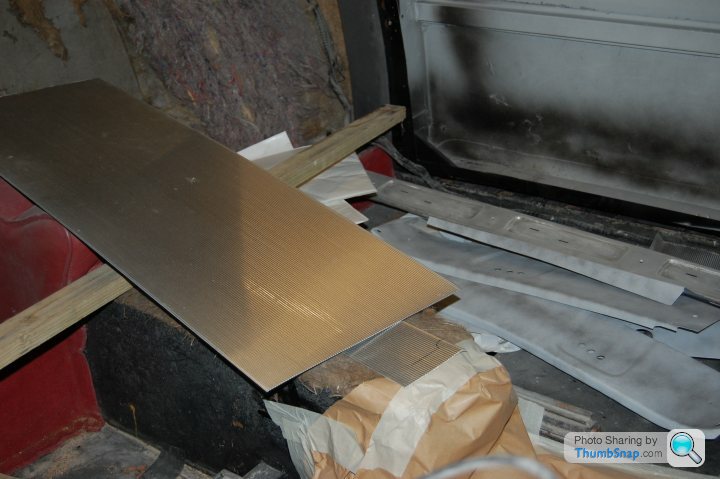
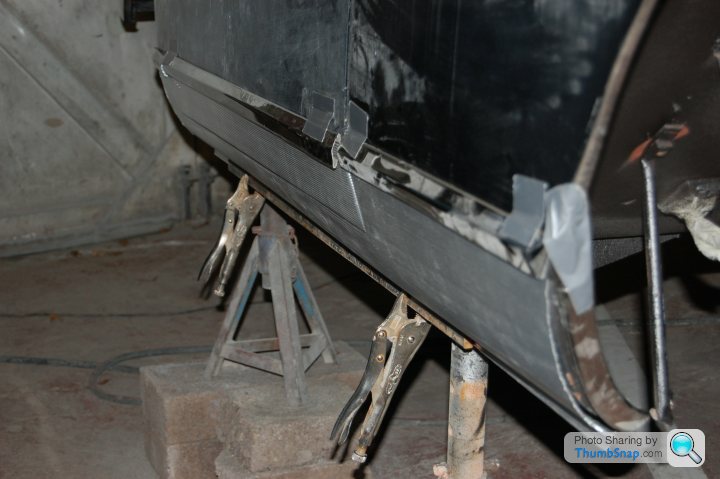
The front grilles and rear lights were also fitted to ensure there were no issues.
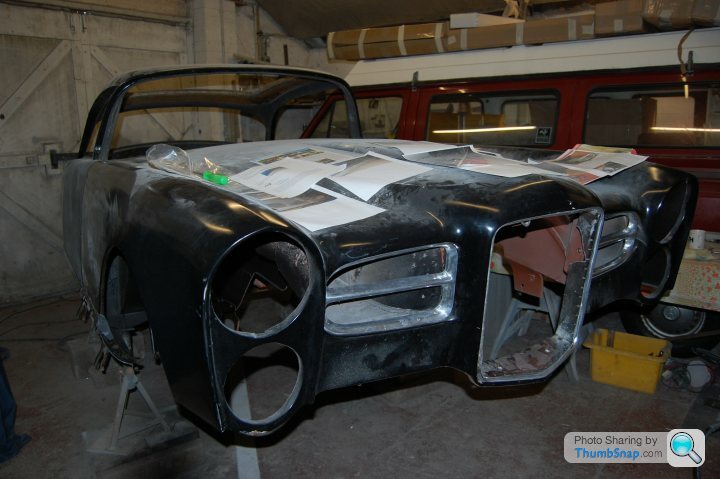
Gary surveys the work that has taken him over a year so far (between other jobs).

And then it was time for the final coats to be applied, rubbed down and polished. This was the point when I knew I had made the right decision to go with Gary...

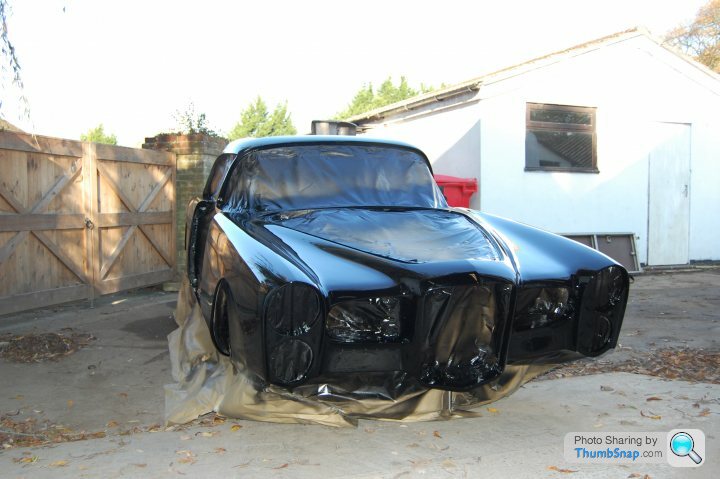
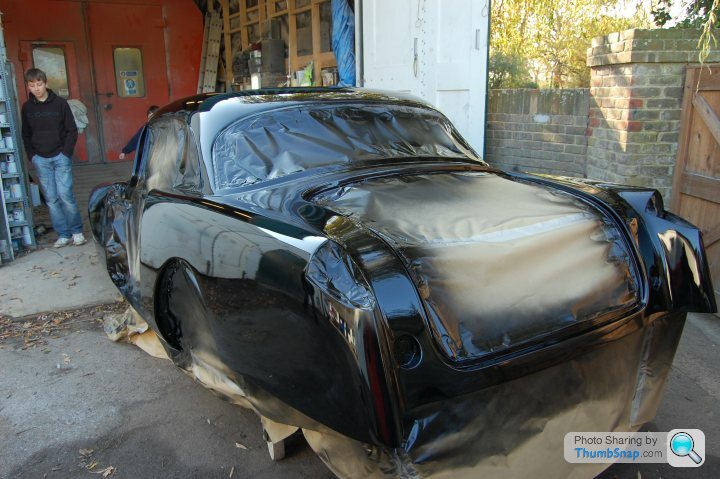
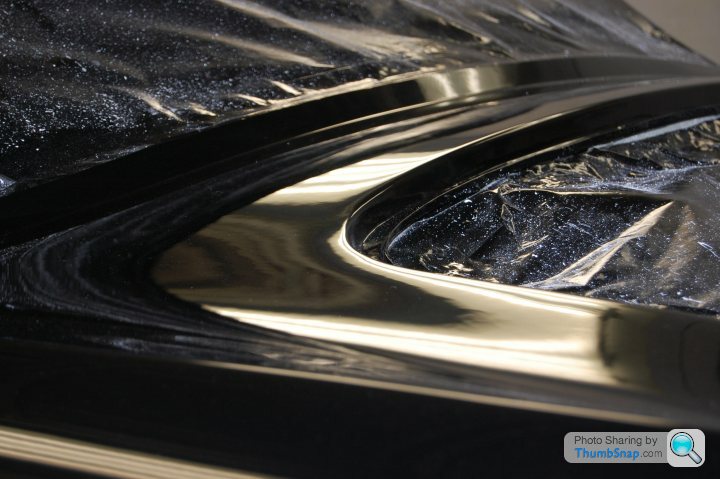
Finally, it was time to fit the front grilles and rear lights to check alignment...but they would have to come off the car again later.


So, finally the body and chassis were both brought back to the standard I was aiming for; excellent, but not necessarily concours. All that was required now was to put the car back together!
Williamp, at the risk of winning a parrot, it is pure black.
The interesting point though, is what black should it be as there are numerous shades. When I worked at Ford early in my career, the interior designers used to obsess about whether the hard plastics should be 'warm black' which was at the brown end of the spectrum or 'cool black' which was verging on dark grey.
Trying to find the exact shade as used by Facel in the late 1950s proved impossible. My first port of call was the French Facel forum on forum-auto (www.forum-auto.com) as this is the biggest online collective of Facel knowledge. No-one there seemed to know a RAL code for Facel black.
A bit more research revealed a possible reason why. The RAL colour standard used across Europe today dates from 1961, so 1950s paint shades would have been defined by the less precise codes devised in the 1940s. These were not commonly used outside Germany and the chances of a French company voluntarily adopting a German system at that point in time were probably nil.
So, without a precise code to nail down the colour, we looked at an area on the bulkhead, behind the dashboard that was probably the original paint. It was definitely at the warm end of the spectrum, so we searched the 1950s colour charts of Ford, Vauxhall and BMC to find a close match. In the end, we opted for Ford black from the period.
To obtain the best finish and to ensure the paint stood the test of time we used modern two pack rather than recreating the original cellulose.
So, a long answer to what might not have been a question at all!
The interesting point though, is what black should it be as there are numerous shades. When I worked at Ford early in my career, the interior designers used to obsess about whether the hard plastics should be 'warm black' which was at the brown end of the spectrum or 'cool black' which was verging on dark grey.
Trying to find the exact shade as used by Facel in the late 1950s proved impossible. My first port of call was the French Facel forum on forum-auto (www.forum-auto.com) as this is the biggest online collective of Facel knowledge. No-one there seemed to know a RAL code for Facel black.
A bit more research revealed a possible reason why. The RAL colour standard used across Europe today dates from 1961, so 1950s paint shades would have been defined by the less precise codes devised in the 1940s. These were not commonly used outside Germany and the chances of a French company voluntarily adopting a German system at that point in time were probably nil.
So, without a precise code to nail down the colour, we looked at an area on the bulkhead, behind the dashboard that was probably the original paint. It was definitely at the warm end of the spectrum, so we searched the 1950s colour charts of Ford, Vauxhall and BMC to find a close match. In the end, we opted for Ford black from the period.
To obtain the best finish and to ensure the paint stood the test of time we used modern two pack rather than recreating the original cellulose.
So, a long answer to what might not have been a question at all!
Gassing Station | Readers' Cars | Top of Page | What's New | My Stuff