BMW Fuel Pump Controller (Helbako EKPM2(3))
Discussion
shoehorn said:
Max_Torque said:
It would be interesting to see inside the EKPM2 version
I have a couple of working EKPM2`s would you like one opened with photos?Or are you getting more intimate,Id be happy to pop one in the post.
A couple of thoughts if you are doing a DIY:
Use an aluminium core board for the power circuit(s) - gives the option of conduction cooling to whatever you mount it to as the mounting tabs can be part of the board and you can use it as the baseplate. Then stick the microcontroller etc. on a bit of FR4 and then stack the two with some standoff pins, with the connector mounted between the two boards; connector could be fixed on either of the boards, putting it on the FR4 one involves fewer interconnects. Should make the whole thing a lot simpler and less need for fancy multilayer PCBs with all those cooling vias. Also makes the thing generally more compact.
Don't bother with a case. For the cost of the unit you aren't going to bother with rework if it fails, assuming you do a bit of test and burn-in first I would just pot the thing into a solid block with the connector at one end and the aluminium core board partially exposed as a 'backplate'. Apart from needing to knock up a simple mould the effort is minimal and the result very robust. I have done this recently, the downside has been that things can't be fixed without stripping the potting compound but having done the numbers the units just aren't worth the cost of fixing as building a complete new one is cheaper than handling a simple repair would be.
Use an aluminium core board for the power circuit(s) - gives the option of conduction cooling to whatever you mount it to as the mounting tabs can be part of the board and you can use it as the baseplate. Then stick the microcontroller etc. on a bit of FR4 and then stack the two with some standoff pins, with the connector mounted between the two boards; connector could be fixed on either of the boards, putting it on the FR4 one involves fewer interconnects. Should make the whole thing a lot simpler and less need for fancy multilayer PCBs with all those cooling vias. Also makes the thing generally more compact.
Don't bother with a case. For the cost of the unit you aren't going to bother with rework if it fails, assuming you do a bit of test and burn-in first I would just pot the thing into a solid block with the connector at one end and the aluminium core board partially exposed as a 'backplate'. Apart from needing to knock up a simple mould the effort is minimal and the result very robust. I have done this recently, the downside has been that things can't be fixed without stripping the potting compound but having done the numbers the units just aren't worth the cost of fixing as building a complete new one is cheaper than handling a simple repair would be.
It's not really worth the cost of going to an IMS pcb for this sort of thing in my experience. Better to spend the money on slightly better FETS with a lower RDS(on) to reduce conduction losses!
(were only talking about a handful of Watts here, and IMS is still a costly thing to do at low volumes (because it limits the places you can go to get the pcbs manufactured/assembled ime)
(I've used IMS for a ~4kW 12v 3phase controller in a sub 100cm2 package before ;-)
(were only talking about a handful of Watts here, and IMS is still a costly thing to do at low volumes (because it limits the places you can go to get the pcbs manufactured/assembled ime)
(I've used IMS for a ~4kW 12v 3phase controller in a sub 100cm2 package before ;-)
shoehorn said:
Here you go Max,sorry they are not a bit sharper.
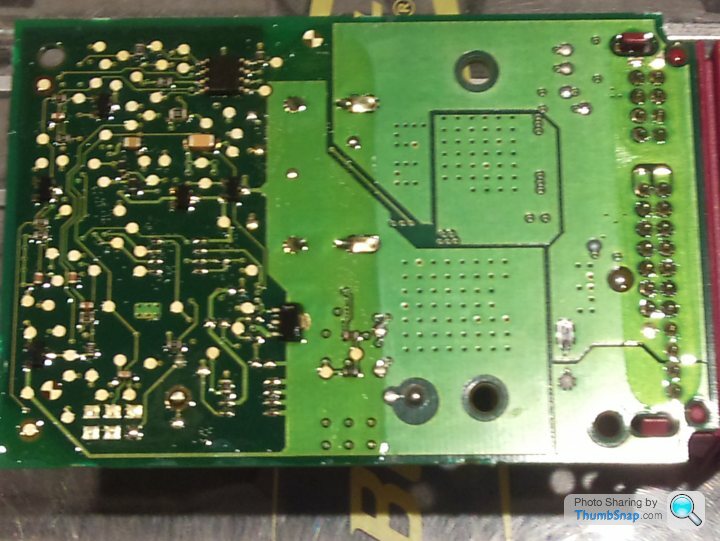
..
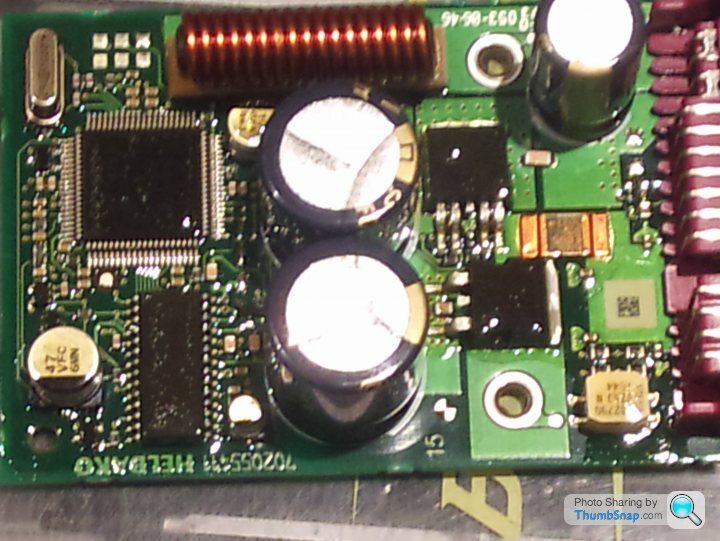
As I said if that whets your appetite and further investigation is required then I`d be happy to send this unit to you,good luck.
Yup, that ones completely different! Looks a lot more "old school" with large wound inductor, single big electrolytic filter cap and two smoothing caps, and what looks to be an output bridge made from descretes! It does have CAN on board too however.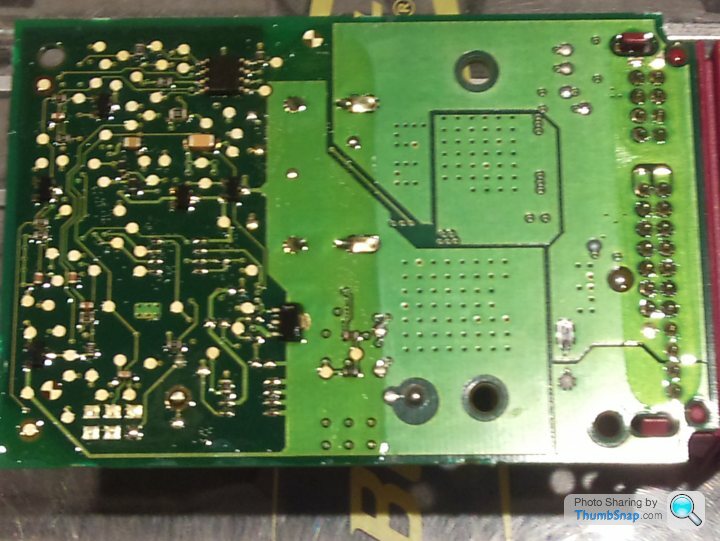
..
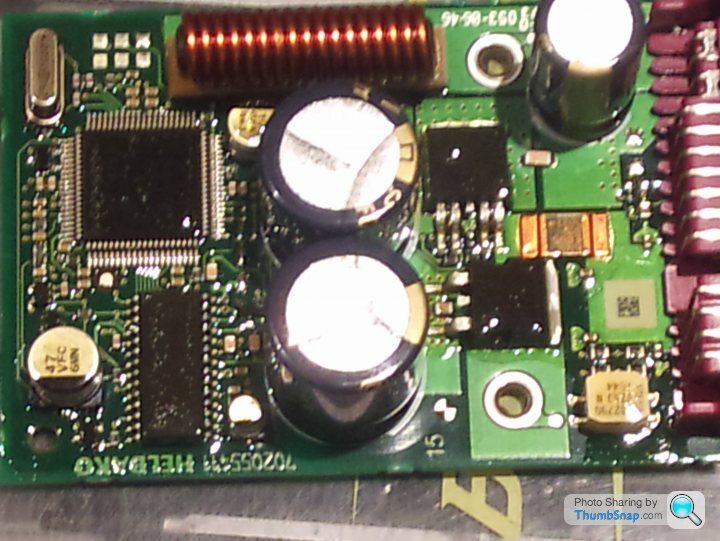
As I said if that whets your appetite and further investigation is required then I`d be happy to send this unit to you,good luck.
I hooked one of these BMW fuel pump modules to a CANbus and found the last byte on id 0x0AA turns the pump output off and on and if no data is sent the pump runs regardless. I'm pretty sure this last byte (or two) is engine rpm.
Two messages are also transmitted from the module which you can see in the screenshot, I'm assuming its diagnostic info but I'll need to do some testing with the output fully loaded to find out.
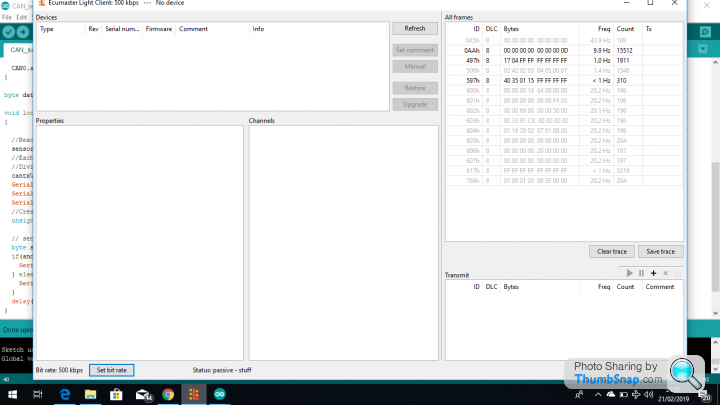
Two messages are also transmitted from the module which you can see in the screenshot, I'm assuming its diagnostic info but I'll need to do some testing with the output fully loaded to find out.
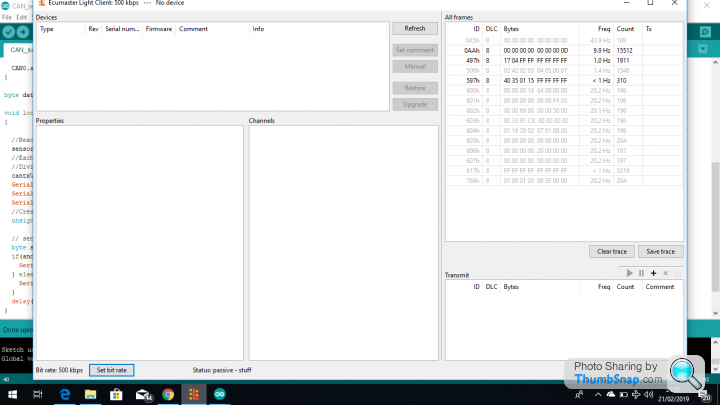
Gassing Station | Engines & Drivetrain | Top of Page | What's New | My Stuff