Another body off thread.
Discussion
Penelope Stopit said:
Nothing wrong with knocking the bodges as long as also giving out praise for a job well done
Where have all the knockers gone?
That could be the name of a record
Jobs looking good, hope you're still enjoying the task
Well here's one!! Where have all the knockers gone?
That could be the name of a record
Jobs looking good, hope you're still enjoying the task
Why are we needing to praise a professional welder who has had to be called back to correct shoddy work. And even then his welds are serviceable now but nothing remarkable.
Here's one of my DIY efforts which are no worse than his, but I wouldn't be shouting about them, nor expect any praise.
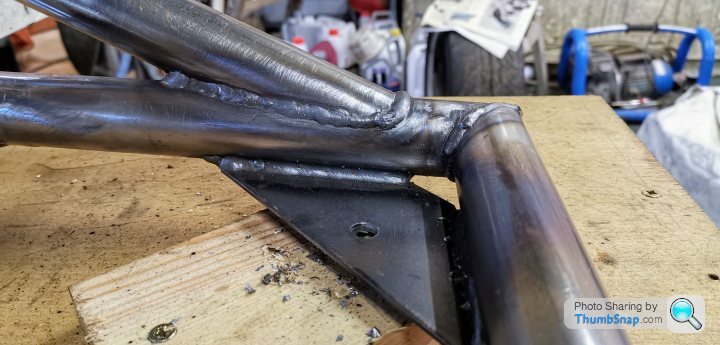
Dougal.
The point of this thread is to show others what the job entails.
Based on your observations I had a 3rd party and very knowledgable chap look over the chassis and mentioned some welds were not pretty but none were dangerous or not doing the job.
Anyway it’s behind me now.
Are you happy your welds are strong and good.
Based on your observations I had a 3rd party and very knowledgable chap look over the chassis and mentioned some welds were not pretty but none were dangerous or not doing the job.
Anyway it’s behind me now.
Are you happy your welds are strong and good.
Edited by Classic Chim on Tuesday 4th February 15:03
magpies said:
Sorry to go back to welding but.....
has any-one seen a failed weld on a chassis
I mean where it has allowed the chassis joint(s) to part or being the source of point of corrosion ?
would be good to know and re-inforce (pun intended) the need for well laid down welds
Yes, on a clubman race car chassis rather than a TVR chassis. Much thinner tube and it had fatigued next to the weld and cracked immediately next to it, the heat build up during the weld can weaken the tube, in an ideal world they're brazed, much less heat and distortion.has any-one seen a failed weld on a chassis
I mean where it has allowed the chassis joint(s) to part or being the source of point of corrosion ?
would be good to know and re-inforce (pun intended) the need for well laid down welds
Looking great Alun, keep up the good work. I've just finished stripping my chassis, now to make the jig before cutting all the rotten bits off.
The areas being replaced are very low stress and it's doubtful that even the poorest weld would not hold, however that's no excuse for poor welds. In stressed areas around engine, gearbox, differential and suspension, a poor weld would undoubtedly crack. TVR's welding is all to a high quality, imho, so failure of this type would be highly unlikely.
Dougal.
Dougal.
[quote=Classic Chim
Are you happy your welds are strong and good.
[/quote]
Yes, I am. And not just based on hope, but on hard evidence. Test pieces were run first for the various joints to ensure sufficient penetration. Those settings and technique were repeated on the job. This is the only way to ensure that you are not just producing a pretty weld, but with little penetration, which lacks strength. You can see from these test pieces how the weld goes right through the materials.

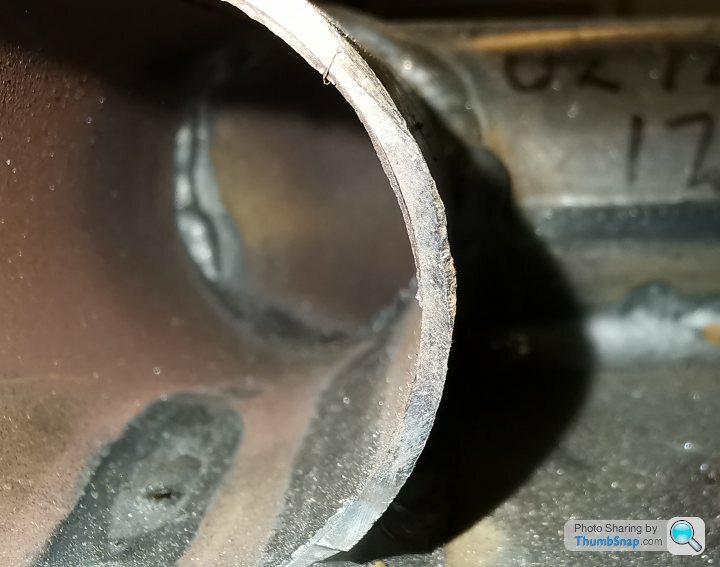

Are you happy your welds are strong and good.
Edited by Classic Chim on Tuesday 4th February 15:03
[/quote]
Yes, I am. And not just based on hope, but on hard evidence. Test pieces were run first for the various joints to ensure sufficient penetration. Those settings and technique were repeated on the job. This is the only way to ensure that you are not just producing a pretty weld, but with little penetration, which lacks strength. You can see from these test pieces how the weld goes right through the materials.

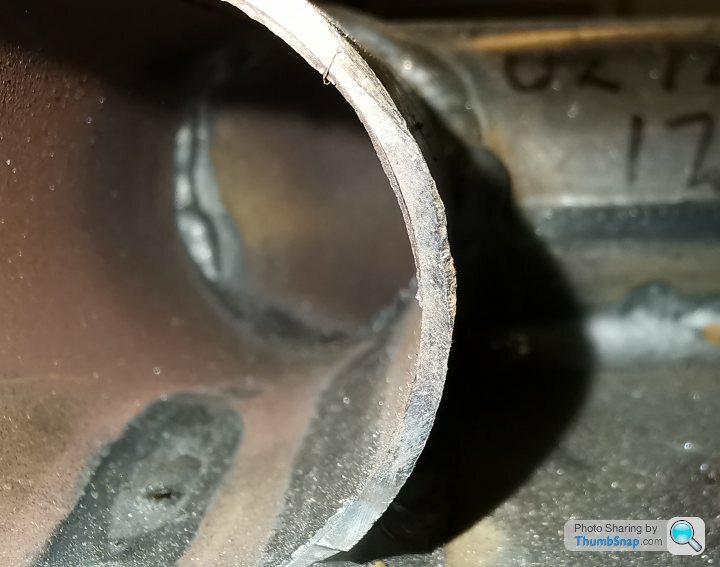

Very good. As said, one of the main sure fire ways to test penetration.
Cracks just beside the weld in the 'heat affected zone' is a common failure mode but seems unlikely on a TVR from my limited exposure. Same for westfields where the only real documented issues with chassis failure is cracking (haz) of the 'lightweight' chassis's which used even thinner than normal tube, and around the diff mount's, typically on high power cars used with sticky rubber.
Daniel
Cracks just beside the weld in the 'heat affected zone' is a common failure mode but seems unlikely on a TVR from my limited exposure. Same for westfields where the only real documented issues with chassis failure is cracking (haz) of the 'lightweight' chassis's which used even thinner than normal tube, and around the diff mount's, typically on high power cars used with sticky rubber.
Daniel
Dougal9887 said:
Well here's one!!
Why are we needing to praise a professional welder who has had to be called back to correct shoddy work. And even then his welds are serviceable now but nothing remarkable.
Here's one of my DIY efforts which are no worse than his, but I wouldn't be shouting about them, nor expect any praise.
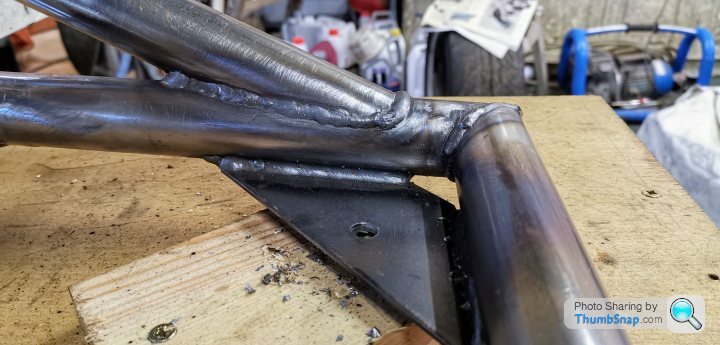
Dougal.
Wire speed needed turning down a tad Why are we needing to praise a professional welder who has had to be called back to correct shoddy work. And even then his welds are serviceable now but nothing remarkable.
Here's one of my DIY efforts which are no worse than his, but I wouldn't be shouting about them, nor expect any praise.
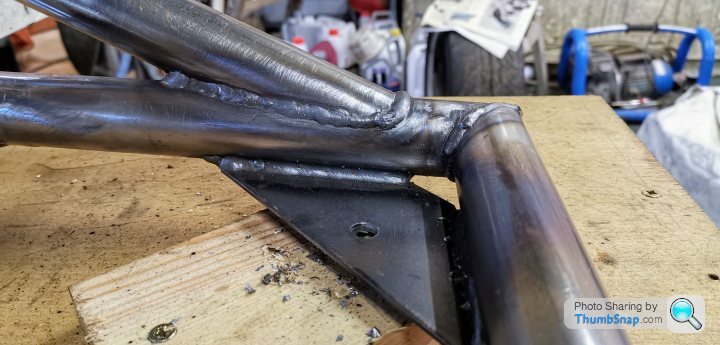
Dougal.



Zener said:
ire speed needed turning down a tad
but .............. I would give big a thumbs up to that welding job
no dips or voids either
from what I have witnessed TVR factory chassis welds were very good IMO certainly pro quality
Yes I agree, some of the weld beads were a bit high. What I found was that I needed the wire speed as I got into the tight angled joint. I should have used a lower speed around the front, then upped it to do the tight section and fillet plates. This is the sort of experience you get if you do these day in, day-out. Still, satisfied overall. 


Apologies to Dave for all this welding stuff!
I'll maybe start a new thread with some more detail on the metalwork and welding details in case anyone is interested in doing this themselves. In my opinion a worthwhile endeavour because unless you use one of the specialists or a fabricator accustomed to working with thin wall tube structures, the results you get may not be what you hoped for.
Dougal.
Peanut Gallery said:
Looking good! - Hope you did not mind me asking about that "crack" that you clarified was not a crack!
Looks like you will have a nice solid car soon!
Not at all. Looks like you will have a nice solid car soon!
What you were seeing is a weld ground back slightly for a better look, this gives the impression of a crack.
You are looking at photo’s, it’s very easy to see something that’s not there but thanks for the heads up.
I’ve since told them to leave the welds alone.
The car will be sand blasted so no need to dress them up to much and they will look more o/e this way imho.
I’ve had a loss of four weeks or more because I have a crappy back. This then has a knock on effect for me personally as now it’s less crappy I need to concentrate on other work which is why I’ve not been near the car.
Hopefully a week or so’s gap appears soon so I’ll have chance to get on with it.
It’s not a change of plans more logistics.
From painting in the past I’m mindful of how long paint takes to cure properly, especially these modern 2 pack paints from what I’ve read.
I want to leave it to cure for as long as it takes or half the work is pointless if your tightening bolts over it and tearing it apart.
Good use of lube and grease will be my main goal doing that but cured paint helps.
I’ve been pondering that for awhile and there’s no getting away from the fact I want the paint to harden. I don’t care how long it takes.
Classic Chim said:
From painting in the past I’m mindful of how long paint takes to cure properly, especially these modern 2 pack paints from what I’ve read. I want to leave it to cure for as long as it takes or half the work is pointless if your tightening bolts over it and tearing it apart. Good use of lube and grease will be my main goal doing that but cured paint helps. I’ve been pondering that for awhile and there’s no getting away from the fact I want the paint to harden. I don’t care how long it takes.
Be careful not to over thin your mix Alun, don't thin beyond 10% or it'll take forever to cure!I went with the special 'Winter Grade' from Jotun to counter slow cure times because, errrr.... its winter right now

Based on a minimum ambient application temp of 7 degrees C the basic rules are...
1. Make your mix in a higher temp environment, mixing at 20 degrees really helps get the reaction started
2. At 7*c wait a minimum of 12 hours before re-coating
3. Waiting 24 hours between coats is better
4. Wait an absolute minimum of 24 hours before putting the painted surface into service
5. Five days curing time before putting the painted surface into service is far better
6. All two component epoxy paints can only be considered fully cured after 3 months
The above is for the 'Winter Grade' I chose, a regular grade epoxy mastic applied below 10*c will likely take days to cure... if at all!
Gassing Station | Chimaera | Top of Page | What's New | My Stuff