Revell Visible V8 Engine Rebuild/Upgrade
Discussion
This is another model I built a very long time ago (probably Christmas ‘78 or ‘79). It was quite complicated for an 8 year old, and I never finished it. I managed to assemble the crankshaft, pistons and cylinder heads, but the main issue was the camshaft was badly warped, and I couldn’t straighten it. Looking back, it never really had a chance of fitting, never mind working. Despite this, I was fascinated by the model, and I never threw it out. I re-discovered it the other day during a major clear out. I found another partially built one on EBay, which I got for £12.80 (unbuilt kits go for £70+). The newer versions go for much less, but aren’t motorised and don’t have the spark plug lights. This is what remains of mine:
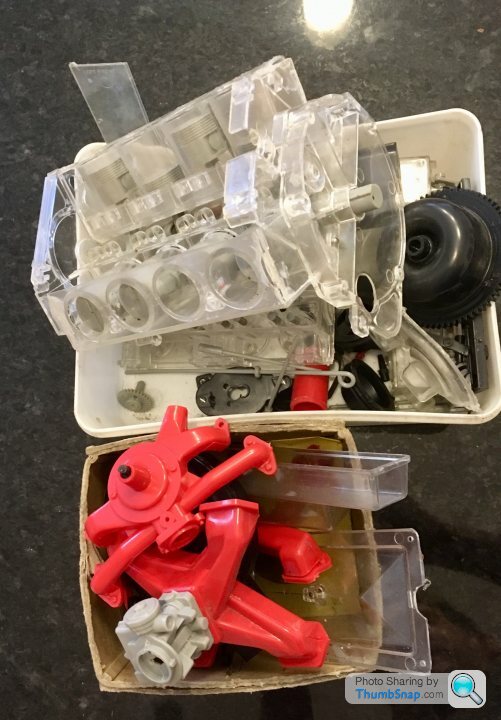
The plan is to make one good one out of the two, using my original parts wherever I can. I’m also going to make some refinements to make it look better and run more smoothly.
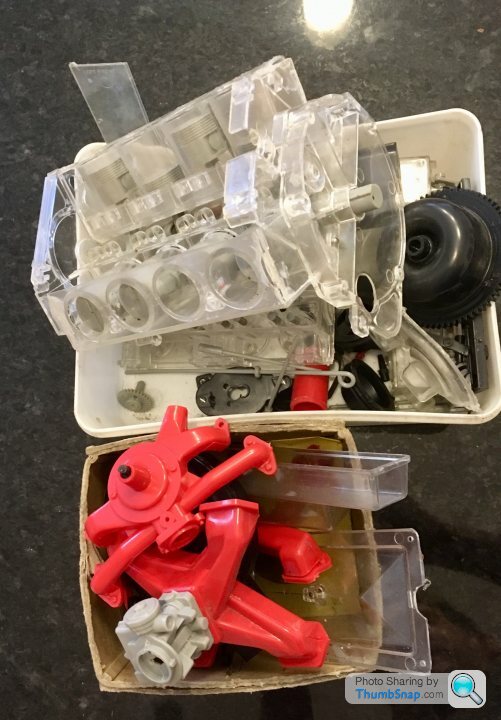
The plan is to make one good one out of the two, using my original parts wherever I can. I’m also going to make some refinements to make it look better and run more smoothly.
Still waiting for the EBay one to arrive, so I stripped mine and washed all the lubricant off the moving parts. Luckily, after 40 years the glue has gone brittle, meaning that it was easy to disassemble without much damage. Some of the transparent parts are ok, but the majority are scrap, so I’m really hoping the new one is sound:
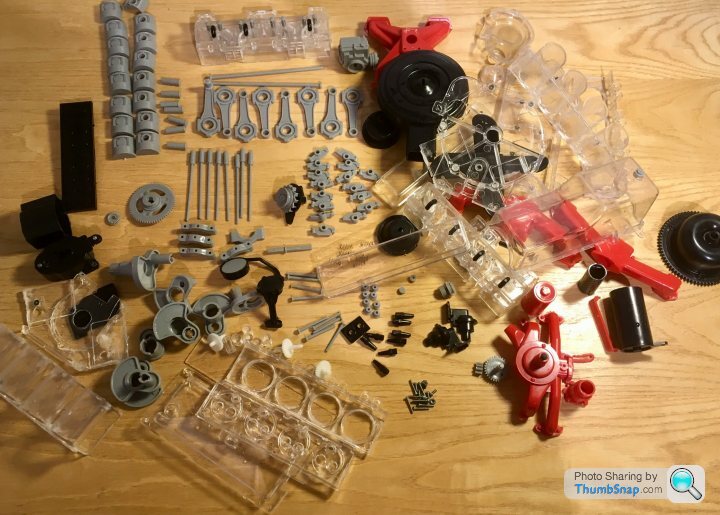
I’m going to need a very small dc geared motor - By some miracle the kit gearbox components survived, but assembling them into the casing and spinning by hand results in a terrible noise. I assumed from YouTube clips it was the mechanics of the engine itself, but it’s actually the drive gearbox.
I’m wondering if something from Lego might work.
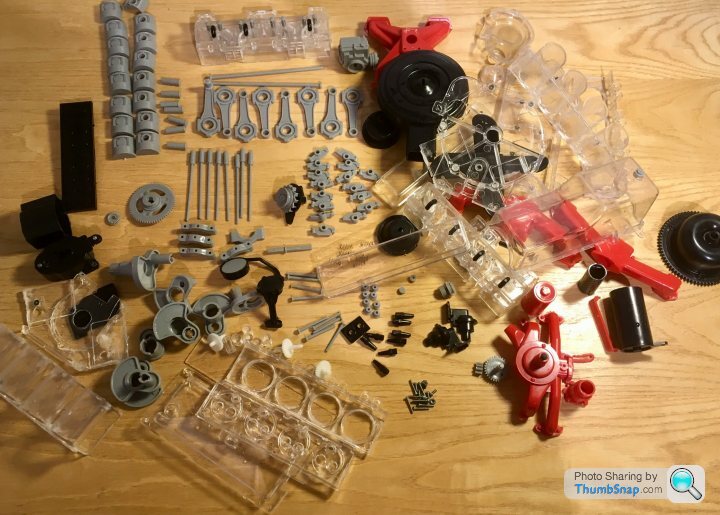
I’m going to need a very small dc geared motor - By some miracle the kit gearbox components survived, but assembling them into the casing and spinning by hand results in a terrible noise. I assumed from YouTube clips it was the mechanics of the engine itself, but it’s actually the drive gearbox.
I’m wondering if something from Lego might work.
Turn7 said:
In for updates....
fully expecting a full ally block n pistons......
No, I’ll leave anything major for my steam engine build! I want to keep this one in the spirit of what it is - a fairly rough and ready working model rather than an exercise is precision. It would be nice to refine some parts though to make it operate more smoothly.fully expecting a full ally block n pistons......

CanAm said:
dr_gn said:
.........I want to keep this one in the spirit of what it is - a fairly rough and ready working model rather than an exercise is precision..........
Hands up anyone who believes this! 
I’ll replace the plastic rocker shafts with steel - easy.
Might replace the cam followers with machined Teflon, and make them a decent fit in their guides - easy.
I could also make Teflon inserts for the valve guides - easy depending on how thin the walls would need to be.
I thought about applying aluminium bare metal foil to the main bearing surfaces - easy.
Finally, replace the fragile distributor drive bevel gears with metal - could be easy, could be a disaster.
tr7v8 said:
dr_gn said:
I’m going to need a very small dc geared motor - By some miracle the kit gearbox components survived, but assembling them into the casing and spinning by hand results in a terrible noise. I assumed from YouTube clips it was the mechanics of the engine itself, but it’s actually the drive gearbox.
I’m wondering if something from Lego might work.
Best bet would be either MFA or one of the model suppliers like component shop or RobobirdsI’m wondering if something from Lego might work.
EBay engine arrived:
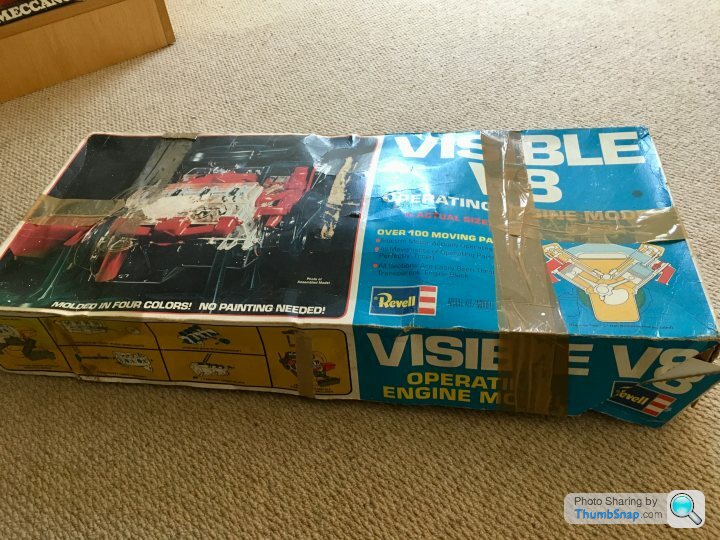
It got a bit mashed in the post, but all the missing bits on mine are there, apart from one distributor rivet:
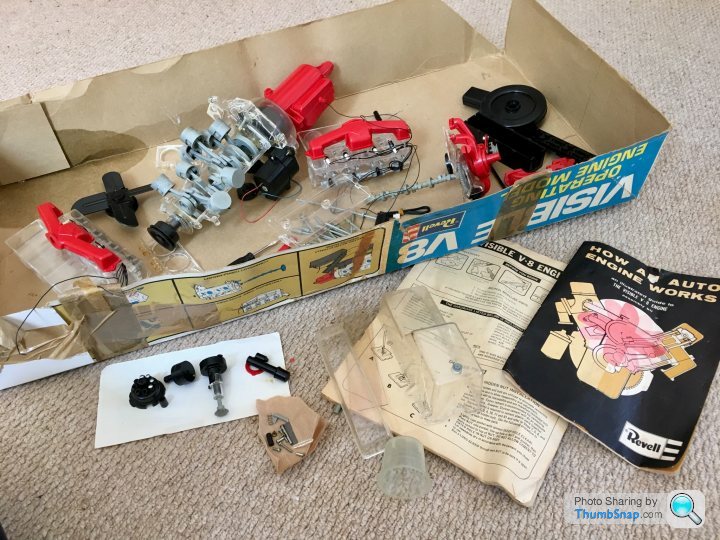
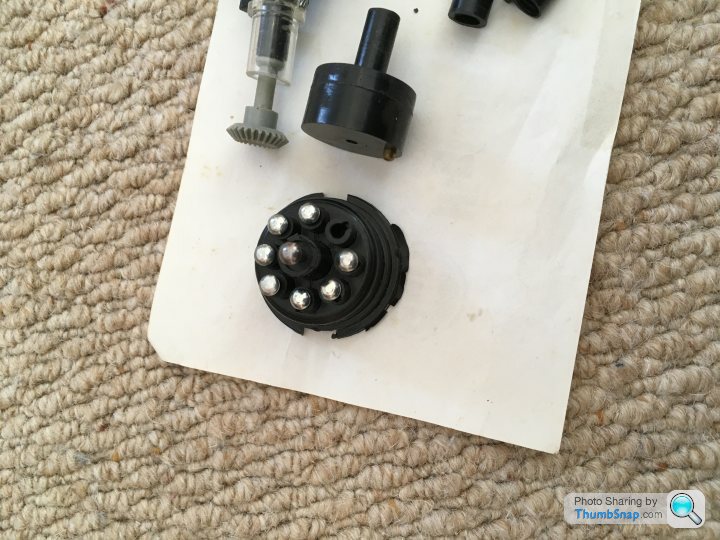
The camshaft is there - not warped, but the end with the gear was snapped where the previous owner tried to glue it after a breakage:
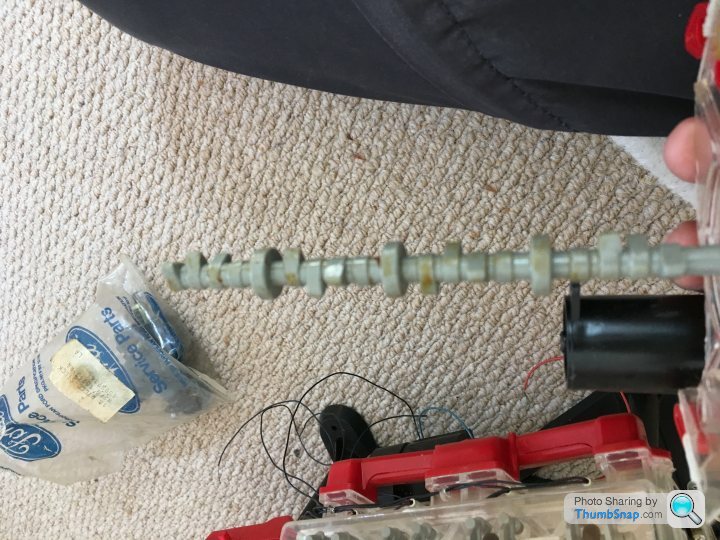
Looks like they got about as far as I did with mine, then had an issue with the camshaft and gave up (like me!). I don’t think it’s ever been run.
The original cam bevel is hopeless, but a Lego one might work:
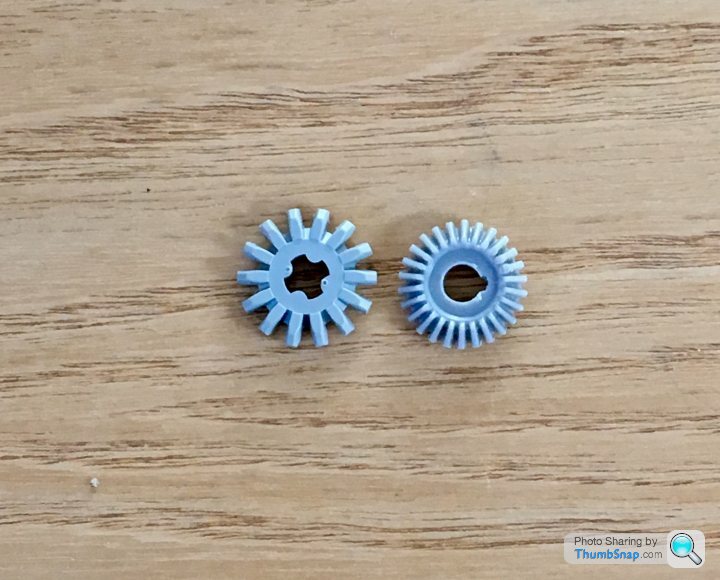
The clear plastic is brittle, but I think I can make one good block out of the best bits from both kits:

Also nice to have the original instructions:
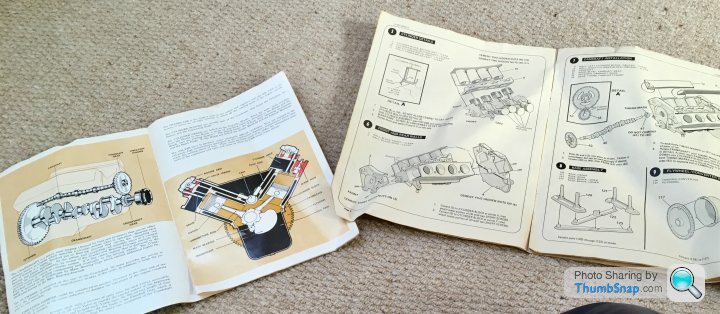
The original 8 bulbs work too:
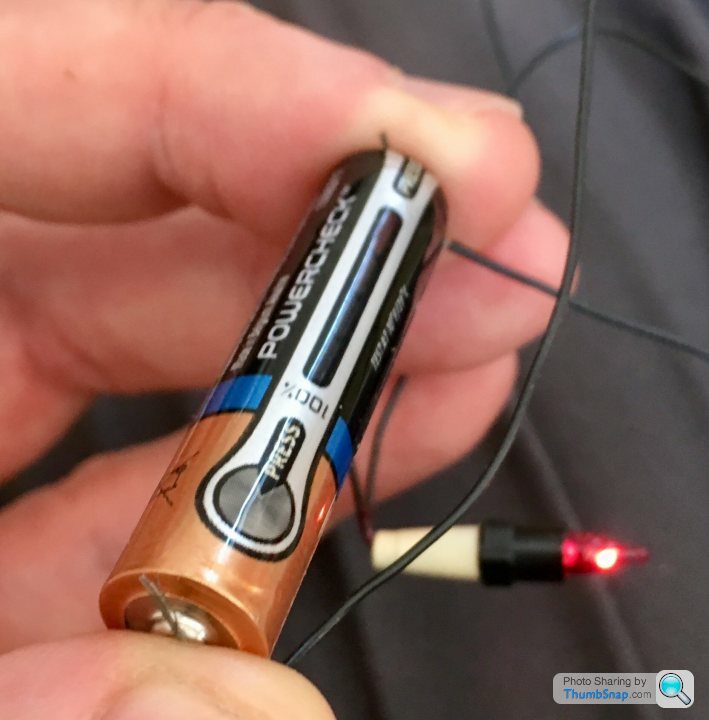
Now to clean up the clear bits...
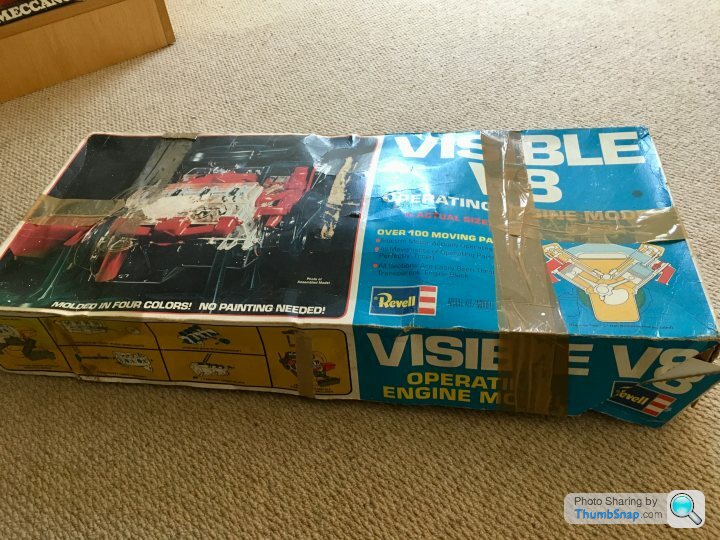
It got a bit mashed in the post, but all the missing bits on mine are there, apart from one distributor rivet:
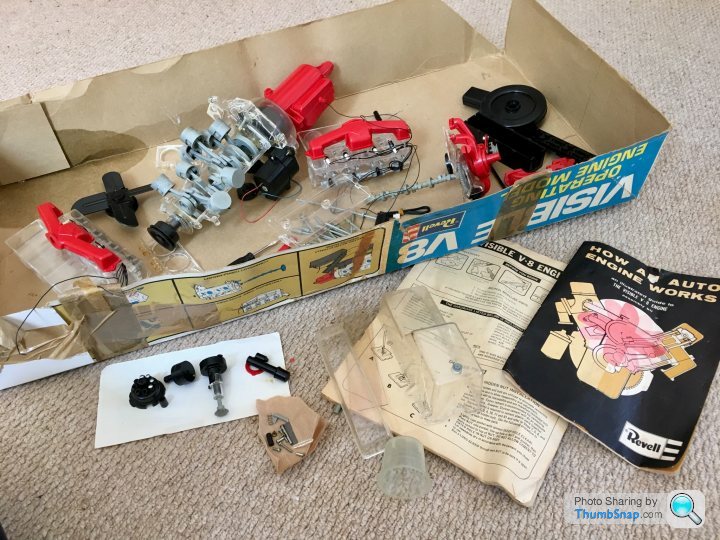
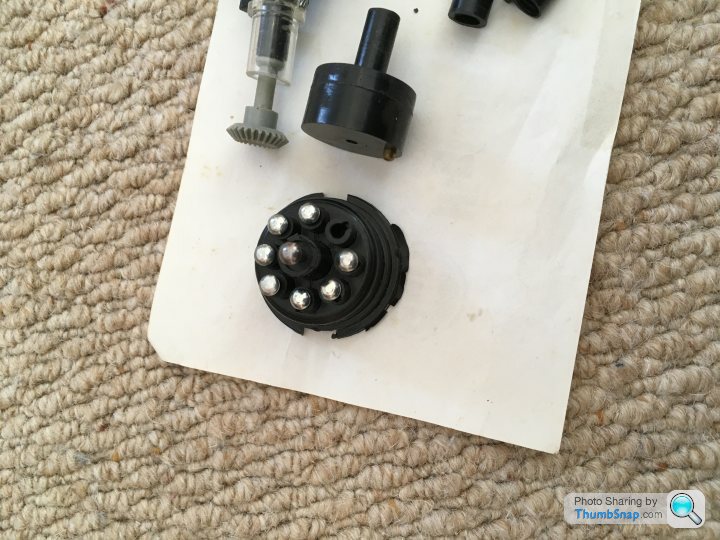
The camshaft is there - not warped, but the end with the gear was snapped where the previous owner tried to glue it after a breakage:
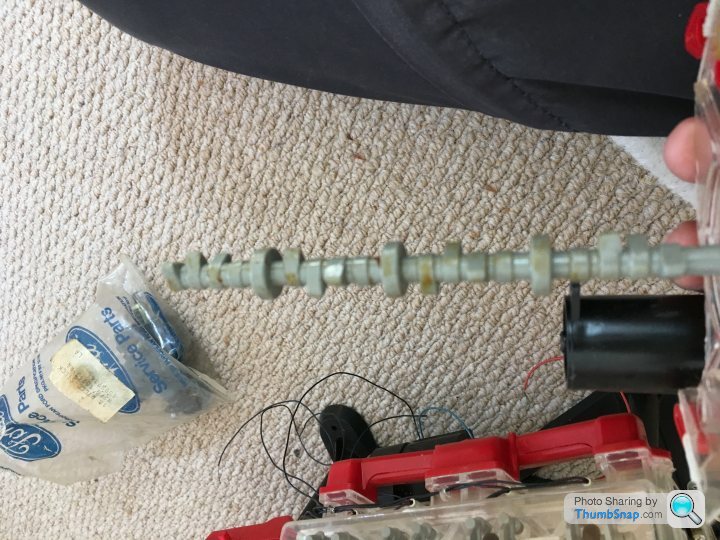
Looks like they got about as far as I did with mine, then had an issue with the camshaft and gave up (like me!). I don’t think it’s ever been run.
The original cam bevel is hopeless, but a Lego one might work:
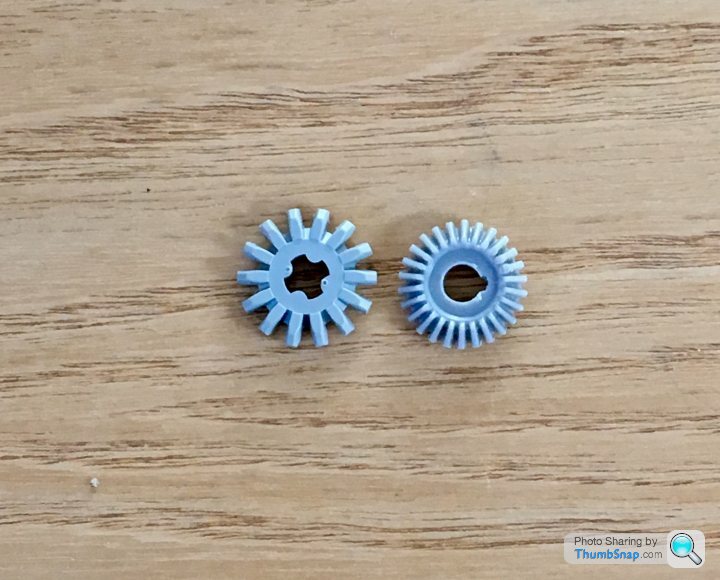
The clear plastic is brittle, but I think I can make one good block out of the best bits from both kits:

Also nice to have the original instructions:
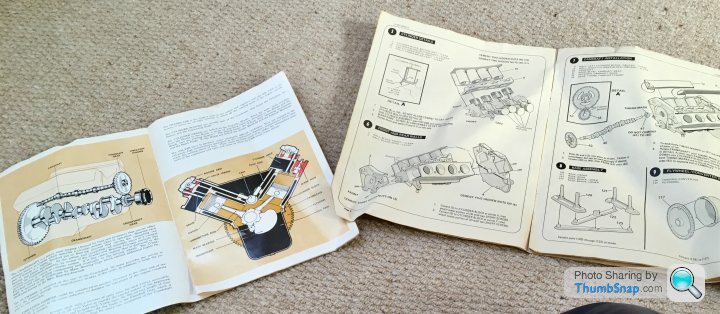
The original 8 bulbs work too:
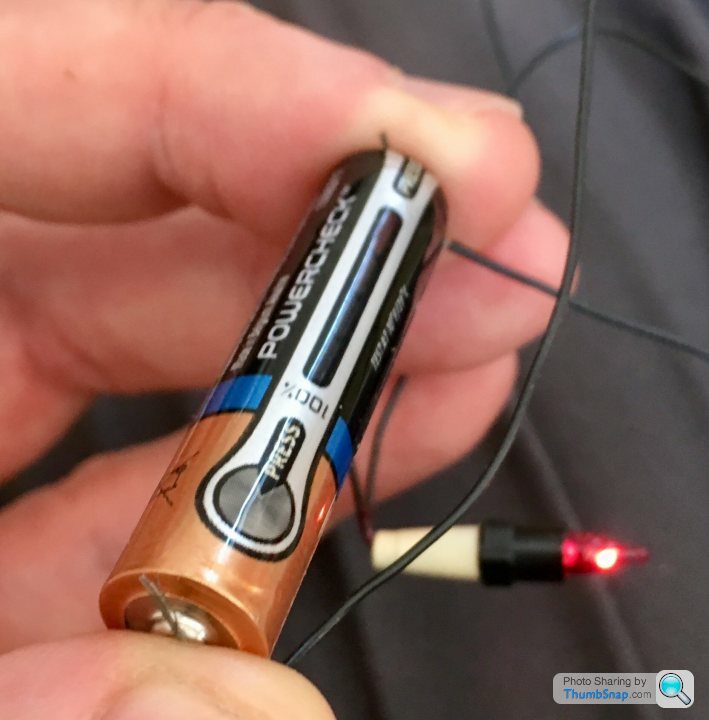
Now to clean up the clear bits...
I decided to split the con-rod bearings using a razor saw:
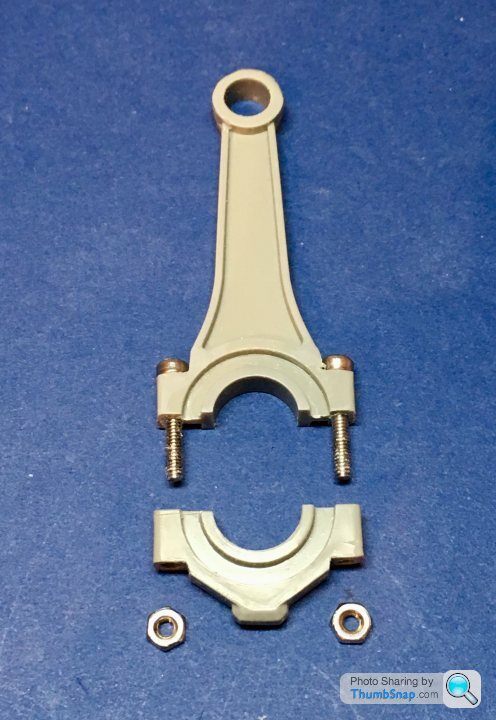
As well as looking a bit more realistic, it means I can assemble the crankshaft into the block and get it running smoothly without the pistons.
The standard kit has you assembling the crankshaft webs and pins with the eight one-piece con-rods, and eight pistons, and then building the cylinder block parts around it (there isn’t enough clearance for any other way). It means aligning and glueing many different parts simultaneously, which isn’t easy.
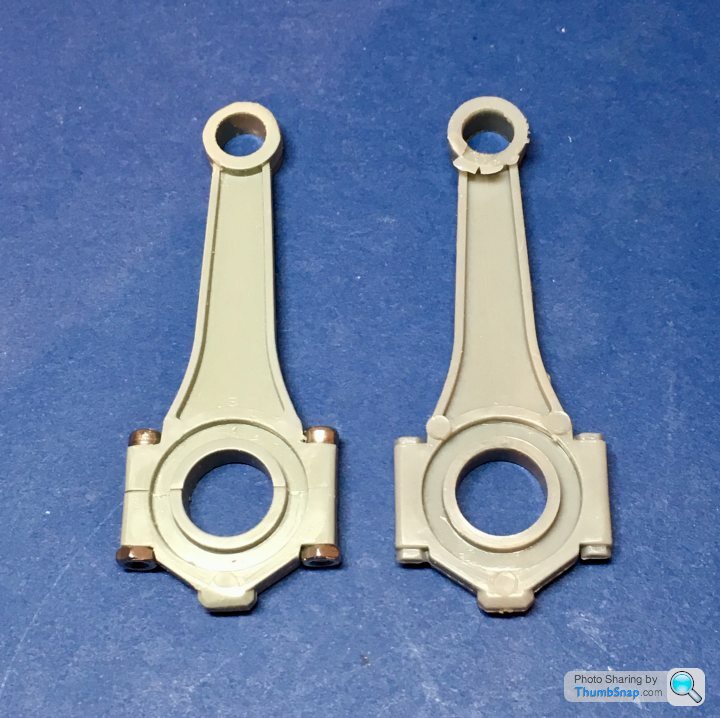
The other advantage is that although the bearing hole is not circular anymore due to the saw cut, it actually makes it a better fit on the crank pins - as moulded, they are a very sloppy fit.
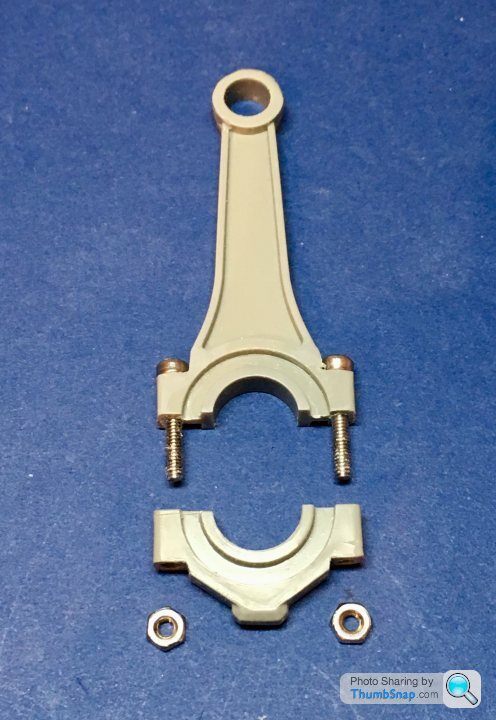
As well as looking a bit more realistic, it means I can assemble the crankshaft into the block and get it running smoothly without the pistons.
The standard kit has you assembling the crankshaft webs and pins with the eight one-piece con-rods, and eight pistons, and then building the cylinder block parts around it (there isn’t enough clearance for any other way). It means aligning and glueing many different parts simultaneously, which isn’t easy.
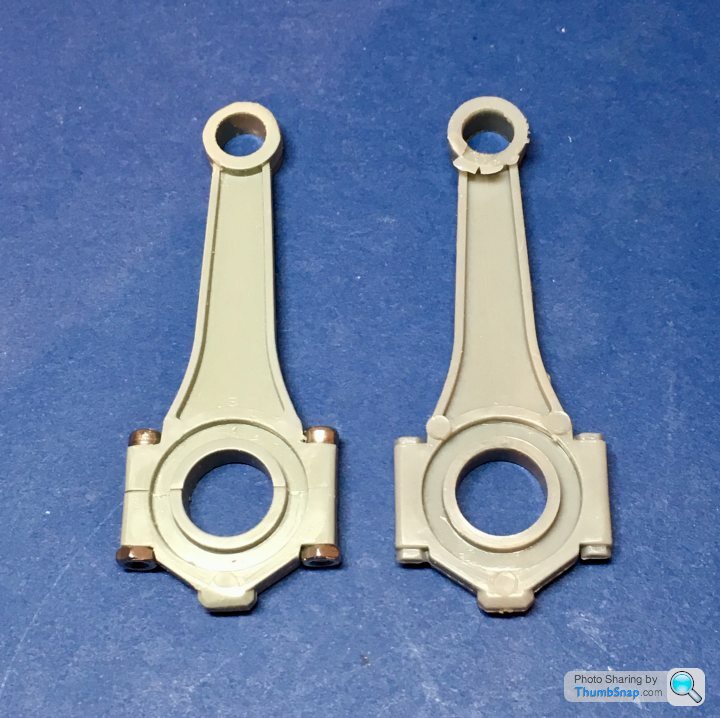
The other advantage is that although the bearing hole is not circular anymore due to the saw cut, it actually makes it a better fit on the crank pins - as moulded, they are a very sloppy fit.
anonymous said:
[redacted]
Yes, I built a few real engines in my time, and I did want to replicate the 'real' method. Unfortunately, I'd have to remove a significant amount of plastic to allow a standard nut to turn freely on the bottom of the bearing housing.I could give it a go with a spare rod and see how it looks. I would definitely have to glue the bolts into the rod because there's not enough access on top to hold it easily.
Machined some new cam followers out of PVC to get rid of the slop from the originals, and to stop them snapping over the cam and making a knocking noise. Also machined the first two aluminium pushrods. I’m going to put threaded adjusters in the rockers so that I can take any free-play out of the system and hopefully make everything smoother:
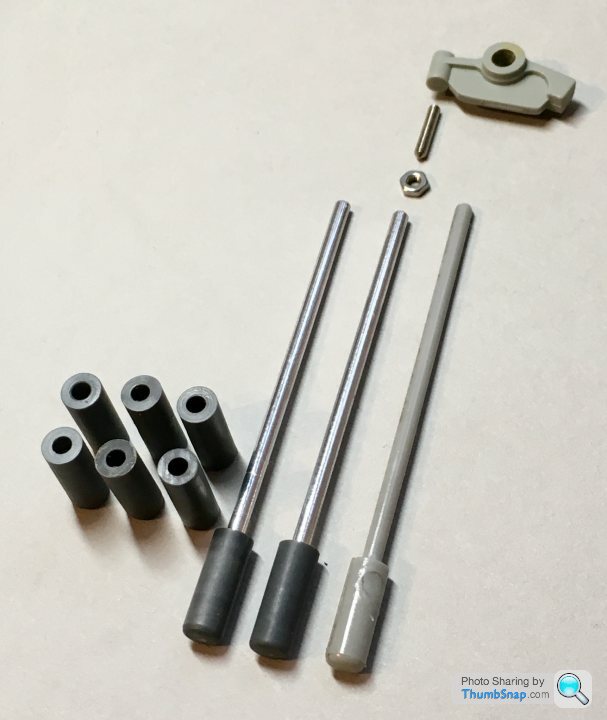
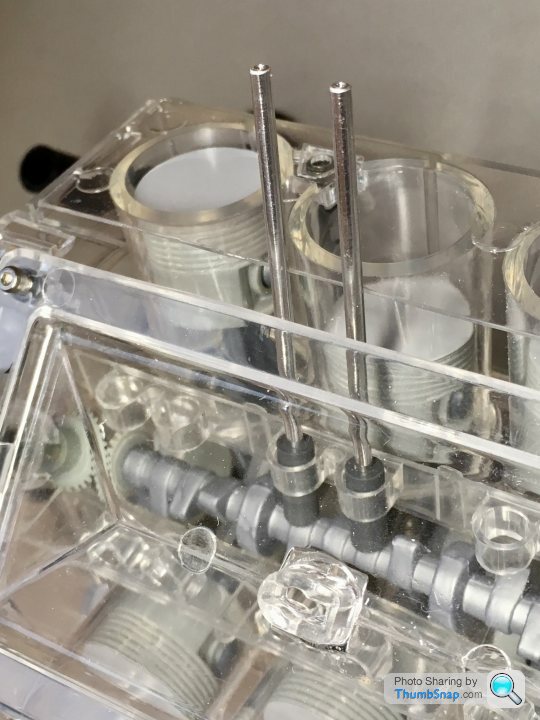
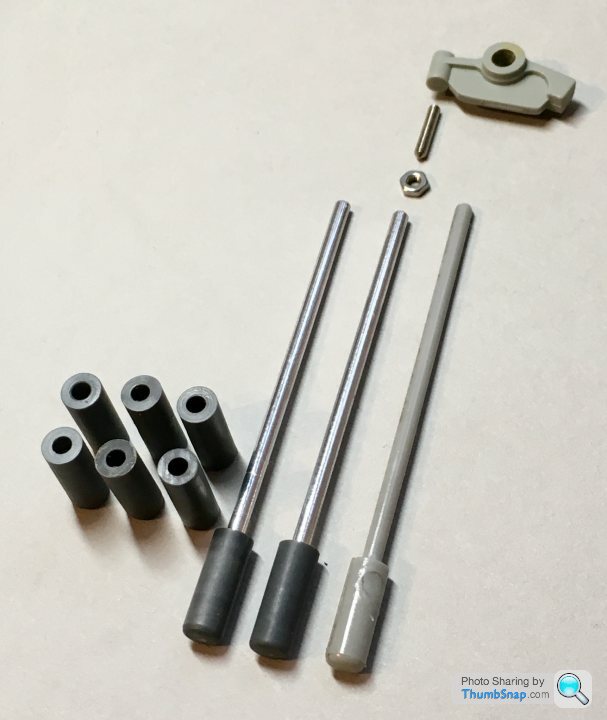
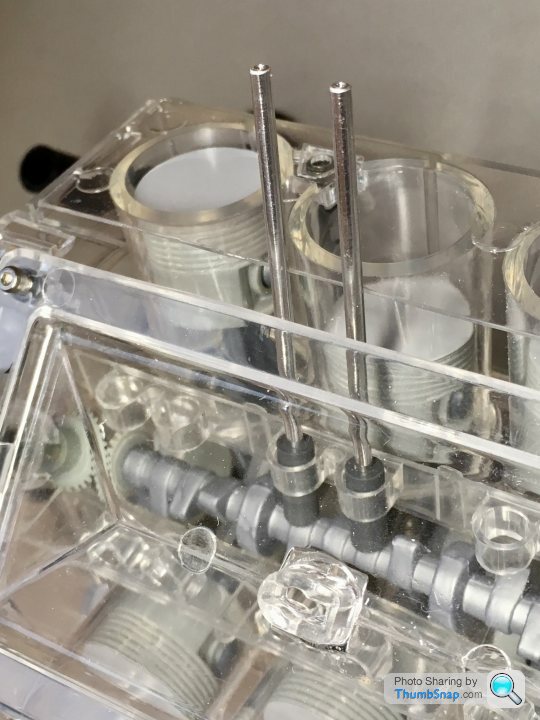
I got bored with this one I'm afraid - there is a lot of noise from the cam/cam follower interaction due to slop between the followers and guides. The followers really need to be metal, and run in tubular guides. I was going to turn some up, and press them into the existing plastic mouldings, but I got into model engineering a steam engine, and that took up a lot of time. This should be no issue, but its a matter of time...
Ennisdavis said:
Even with the better fitting lifters, there are no cam bearings so the cam flops around and jambs the lifters. Any fixes here?
That shouldn't be much of a problem if the cam is straight.The valve springs are weak, and even if they deflected the cam excessively, this should be limited by the clear plastic semi-circular cut-outs underneath the middle cam "bearing" bosses.
Of course, if the tappet guides aren't a good fit, and they begin to jam, this will cause much more bending load on the cam.
I might have another look at the guides tomorrow. Now I've got some experience of accurate lathe turning I might be able to come up with something.
Must admit I lost interest in this after embarking on ‘proper’ model engineering last year. The tolerances and compromises in producing a 1960’s era injection-moulded working engine add up to a not particularly great model.
Anyway, it needs finishing, so:
Made some clear plastic inserts for the cam followers. These are a better fit on the newly turned followers, and more importantly, give a longer sliding contact area. This reduces the jamming effect of the originals. I machined them to a top-hat section, and they’re PVA’d in place:
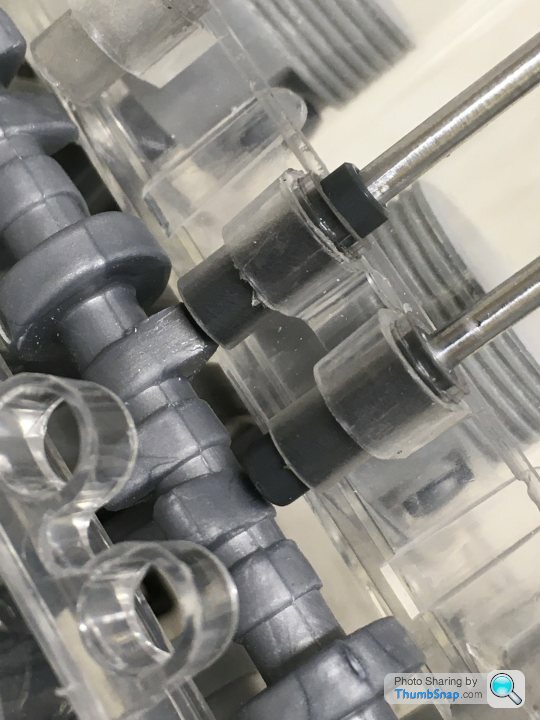
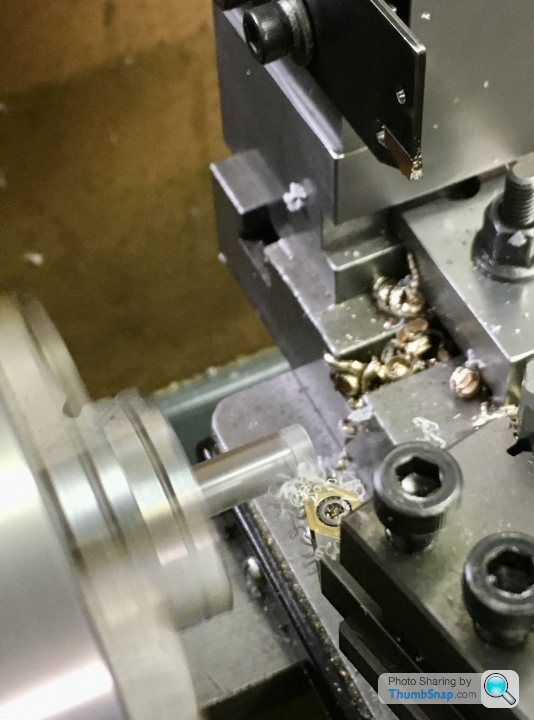
I’d wanted to use tappet adjusters on the rockers, like on a real pushrod engine, but the alignmemts were too far off. I still needed some way of taking up the rattly free play in the system though, so opted to drill the aluminium pushrods and install domed head screws:
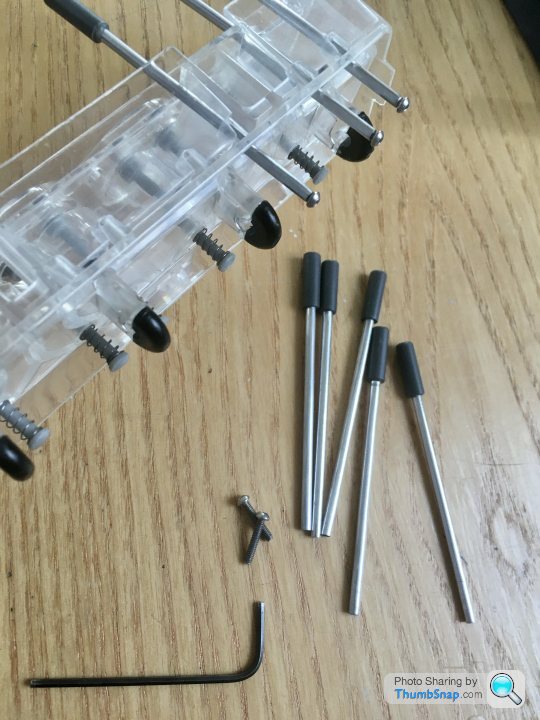
These allow everything to be closed up after assembly.
I used some knitting needles off EBay for the rocker shafts. They’re anodised and give a nice smooth action for the rockers without lubrication. The ends were drilled and tapped for retaining screws and washers:
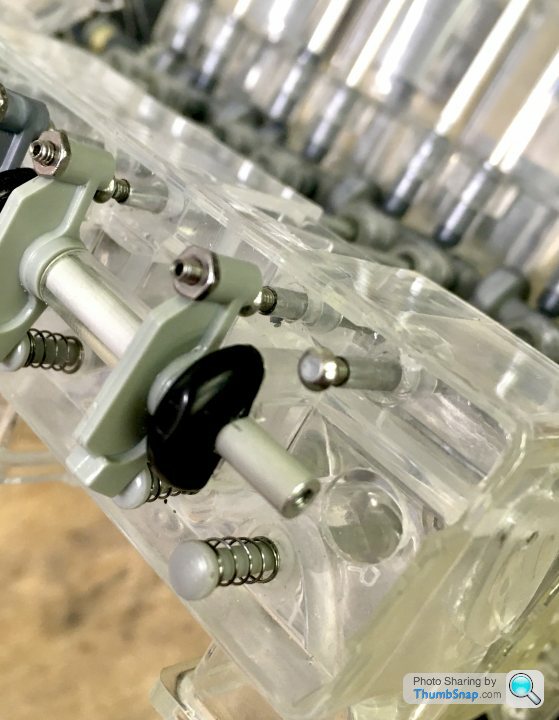
Also visible are the dummy tappet adjusters and lock-nuts. I was reluctant to add these, but the rockers assembly is the most visible part of the model when operating, and it needed a bit more visual interest.
I also found the two original cylinder head retaining screws per side weren’t enough. The heads would tilt under the action of the valves. I added three more by drilling the heads to the inside of the V:
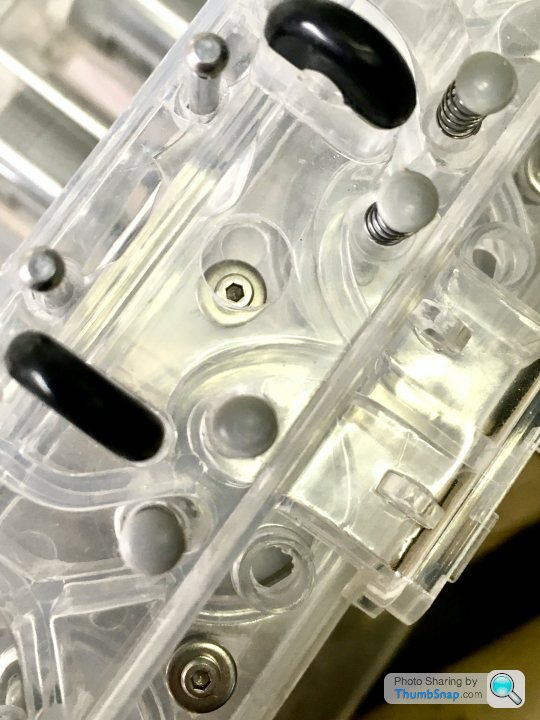
Like all other simulated bolt heads, I replaced the sump fasteners with real screws, and made a brass sump plug:
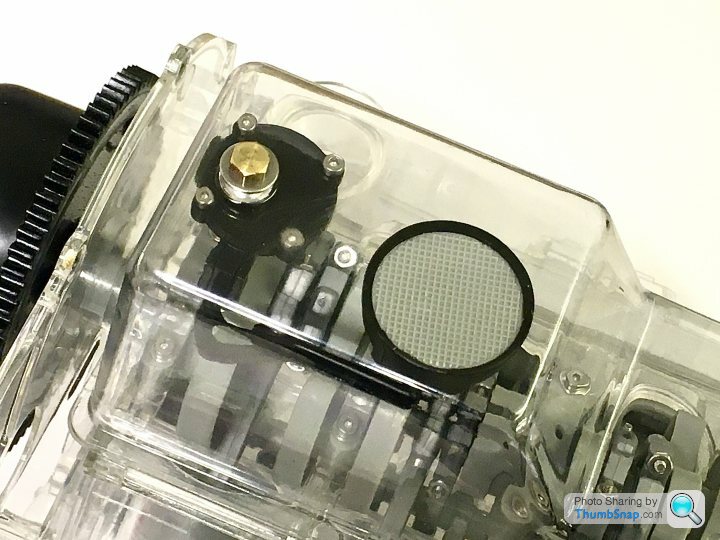
The weakest point of the model is the distributor bevel gear drive. I’m still refining this, using improved location for the gears, and using a lightly sprung-loaded meshing method. It works, but I’m unsure how long it will keep the correct timing. More of that some other time.
Current progress:
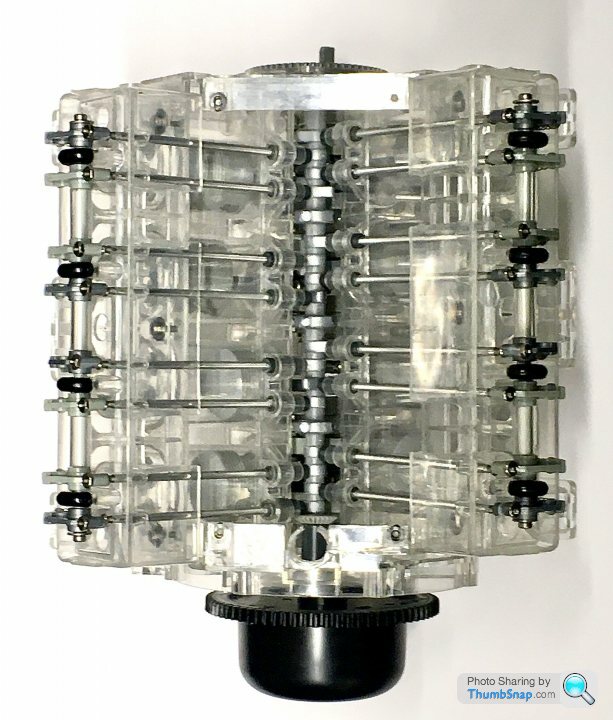
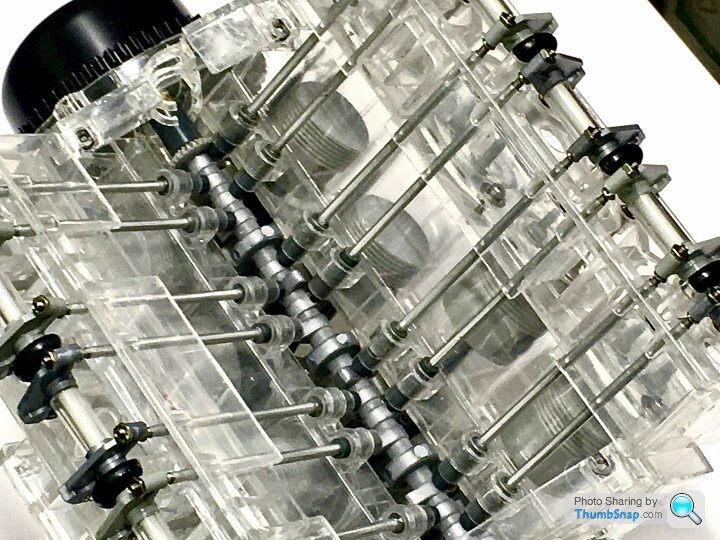
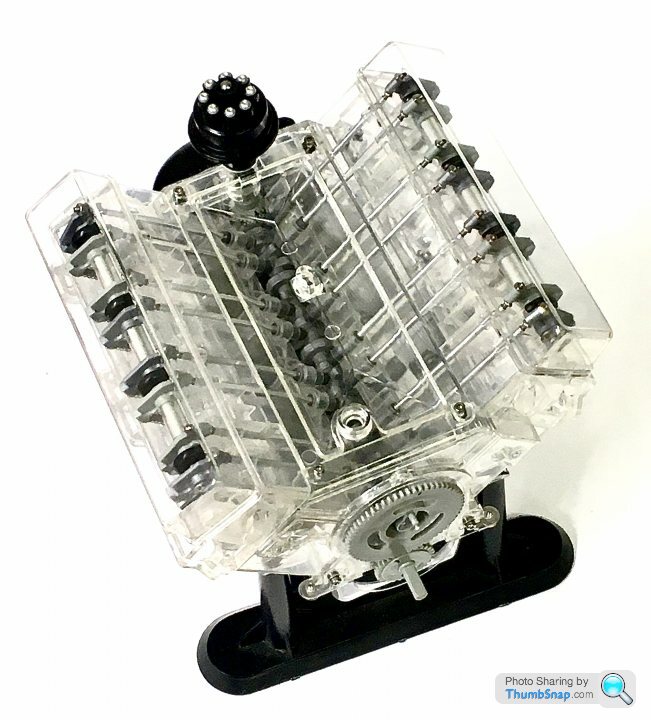
Still a long way to go.
Anyway, it needs finishing, so:
Made some clear plastic inserts for the cam followers. These are a better fit on the newly turned followers, and more importantly, give a longer sliding contact area. This reduces the jamming effect of the originals. I machined them to a top-hat section, and they’re PVA’d in place:
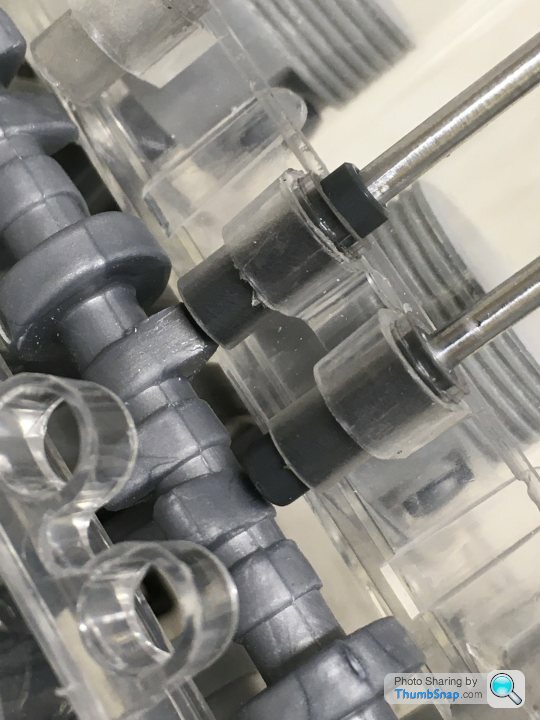
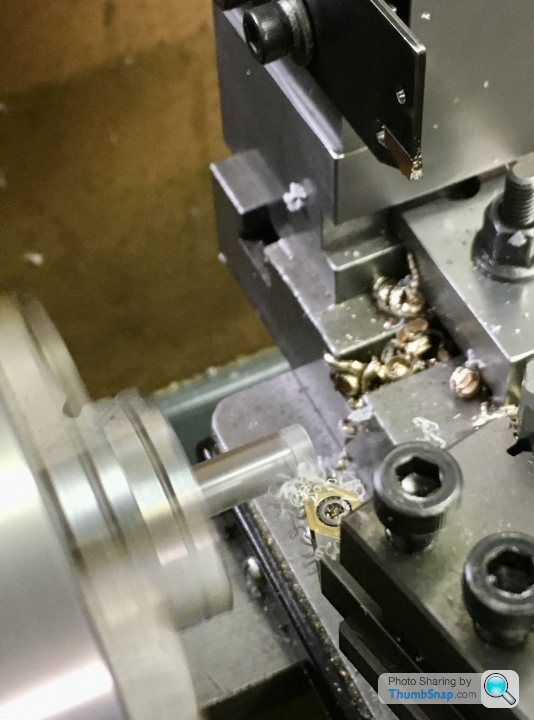
I’d wanted to use tappet adjusters on the rockers, like on a real pushrod engine, but the alignmemts were too far off. I still needed some way of taking up the rattly free play in the system though, so opted to drill the aluminium pushrods and install domed head screws:
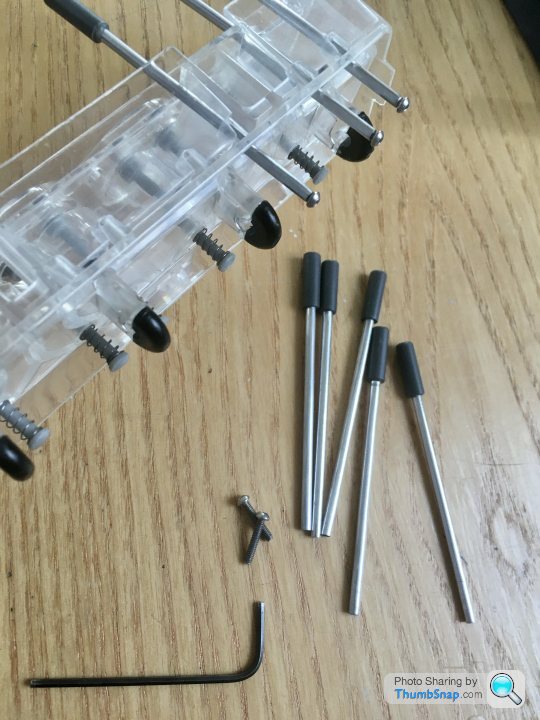
These allow everything to be closed up after assembly.
I used some knitting needles off EBay for the rocker shafts. They’re anodised and give a nice smooth action for the rockers without lubrication. The ends were drilled and tapped for retaining screws and washers:
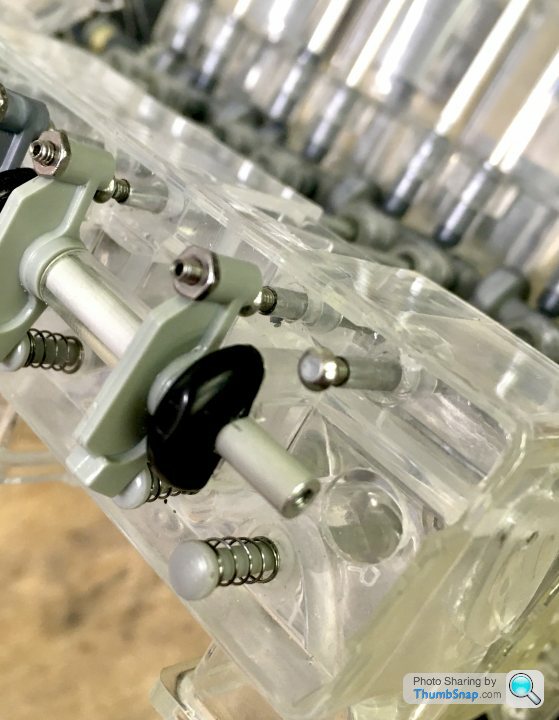
Also visible are the dummy tappet adjusters and lock-nuts. I was reluctant to add these, but the rockers assembly is the most visible part of the model when operating, and it needed a bit more visual interest.
I also found the two original cylinder head retaining screws per side weren’t enough. The heads would tilt under the action of the valves. I added three more by drilling the heads to the inside of the V:
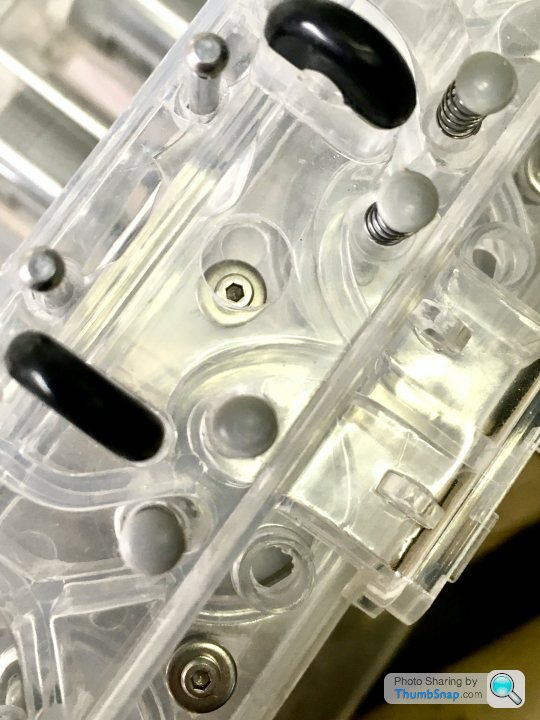
Like all other simulated bolt heads, I replaced the sump fasteners with real screws, and made a brass sump plug:
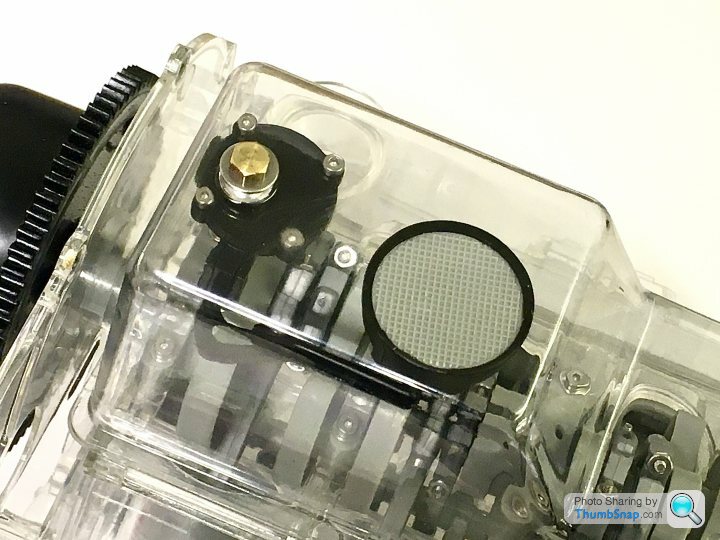
The weakest point of the model is the distributor bevel gear drive. I’m still refining this, using improved location for the gears, and using a lightly sprung-loaded meshing method. It works, but I’m unsure how long it will keep the correct timing. More of that some other time.
Current progress:
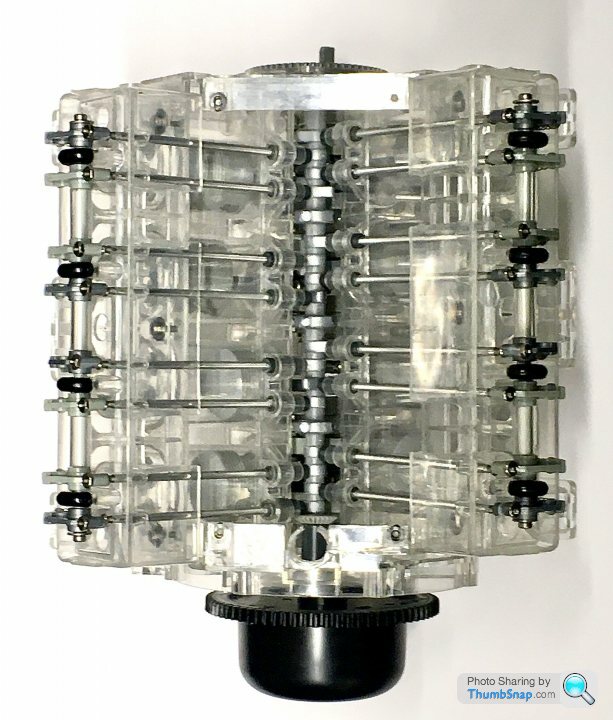
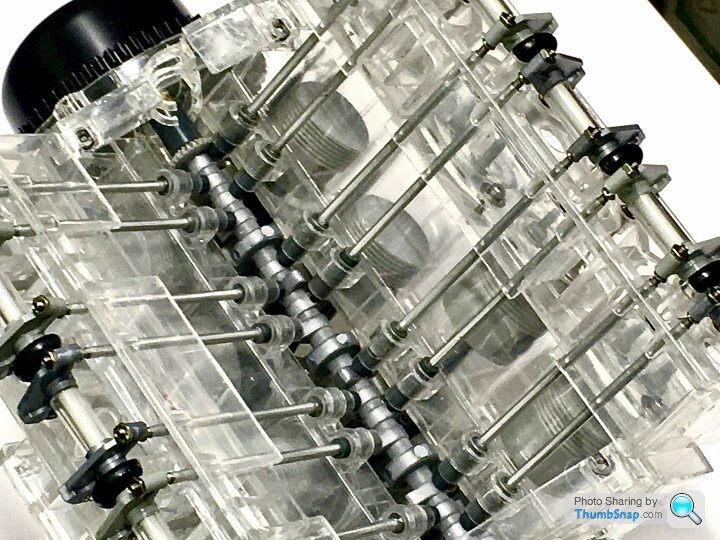
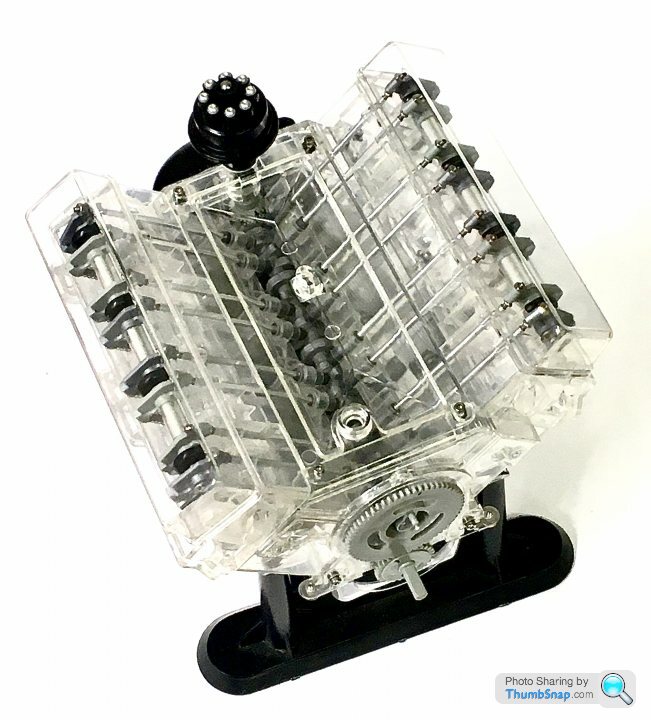
Still a long way to go.
GliderRider said:
If you're still looking for a geared motor, Proops do this 6 volt, 22rpm one for a fiver.
Proops 6 Volt, 22 rpm motor
As someone mentioned earlier, MFA Como Drills Ltd do a build your own gearbox with a variety of ratios:
MFA Como Drills multi ratio gearbox
Yes, still need a motor. 22rpm is a bit slow. Current thinking is to go from 0-60rpm.Proops 6 Volt, 22 rpm motor
As someone mentioned earlier, MFA Como Drills Ltd do a build your own gearbox with a variety of ratios:
MFA Como Drills multi ratio gearbox
I think the MFA gearbox might be a bit bulky and noisy. I really want to fit it in the gearbox, and drive the crankshaft with a co-axial coupling.
Thanks.
Gassing Station | Scale Models | Top of Page | What's New | My Stuff