Building a Shoffice/Garden Room - value engineering it
Discussion
Given COVID, and warnings from my company that we may expect to be WAH well into next year, and having lost my office to the new baby, I’m considering building a combined 6x3.5 office / shed (two separate entrances most likely.
Construction would be timber frame, EDPM roof, windows in standard sizes (hoping to reduce cost)
I’d rather not spend the GDP of a small nation, so I’m trying to work out how to value engineer it, having done a rough calc and ended up with a cost of £2.7k just for wood and a bit of insulation last night (and it was very rough!). I’ve also looked at a garden room SIP kit which is about £3.7k but only would need cladding/roof membrane, a basic base and glazing (and has the speed advantage!)
So looking for advice from those who’ve tackled such a project, about where you can make accommodations to reduce cost. Some thoughts from me:
- Recommendations online seem to say 100mm celotex in the floor. Wow is this stuff expensive even from seconds and co. Could I use 100mm of EPS and suck up the insulation loss (how much difference would it make anyway, our 1930s semi not having any insulation in the timber suspended floor!)
- rockwool the walls instead of celotex again, using 4x2 walls so 100mm rockwool rolls would work
- celotex the ceiling only (probably doing cold roof due to 2.5m permitted development height limit, have seen someone online doing it so they have the celotex hard up against the roof deck, leaving the void under which seems reasonable if unorthadox, given this is a harden room
- foundation plinths from blocks with a light 500-600mm concrete foundation under. Set the spans up to enable 4x3 joists in floor to reduce costs
- buy second hand glazing on eBay. Works well when stick building as I can adjust the frame to accommodate what I can get. Not so good for SIPS
- Clad it in black corrugated steel ( seems lots of modern buildings doing this and if I detail it well it’s relatively good looking), significantly less £sqm than hardieplank, etc. Could also featherboard but would need to fire treat it
- use the structural floor covering as the final floor finish, painted or varnished (can always be changed later)
Any other obvious things I’m missing which could bring the cost down?
Construction would be timber frame, EDPM roof, windows in standard sizes (hoping to reduce cost)
I’d rather not spend the GDP of a small nation, so I’m trying to work out how to value engineer it, having done a rough calc and ended up with a cost of £2.7k just for wood and a bit of insulation last night (and it was very rough!). I’ve also looked at a garden room SIP kit which is about £3.7k but only would need cladding/roof membrane, a basic base and glazing (and has the speed advantage!)
So looking for advice from those who’ve tackled such a project, about where you can make accommodations to reduce cost. Some thoughts from me:
- Recommendations online seem to say 100mm celotex in the floor. Wow is this stuff expensive even from seconds and co. Could I use 100mm of EPS and suck up the insulation loss (how much difference would it make anyway, our 1930s semi not having any insulation in the timber suspended floor!)
- rockwool the walls instead of celotex again, using 4x2 walls so 100mm rockwool rolls would work
- celotex the ceiling only (probably doing cold roof due to 2.5m permitted development height limit, have seen someone online doing it so they have the celotex hard up against the roof deck, leaving the void under which seems reasonable if unorthadox, given this is a harden room
- foundation plinths from blocks with a light 500-600mm concrete foundation under. Set the spans up to enable 4x3 joists in floor to reduce costs
- buy second hand glazing on eBay. Works well when stick building as I can adjust the frame to accommodate what I can get. Not so good for SIPS
- Clad it in black corrugated steel ( seems lots of modern buildings doing this and if I detail it well it’s relatively good looking), significantly less £sqm than hardieplank, etc. Could also featherboard but would need to fire treat it
- use the structural floor covering as the final floor finish, painted or varnished (can always be changed later)
Any other obvious things I’m missing which could bring the cost down?
Equus said:
Every building is a compromise.
You have come up with a detailed specification and justification for it that you are clearly happy with (which is fine). I have a feeling that this would be one of those classic threads where you simply argue away anyone who suggests alternatives, because your mind is already set.
The one observation I will offer is that black metal cladding on a thermally lightweight timber frame building is as good a recipe as you'll find for death by heatstroke.
I know better than to argue with you Equus, although I'm pleased you think my spec at least some sense (given I've never specified a timber frame boiling before!).You have come up with a detailed specification and justification for it that you are clearly happy with (which is fine). I have a feeling that this would be one of those classic threads where you simply argue away anyone who suggests alternatives, because your mind is already set.
The one observation I will offer is that black metal cladding on a thermally lightweight timber frame building is as good a recipe as you'll find for death by heatstroke.
Hadn't considered the heat problem with the cladding; intuitively you think it would vent given it'd be battened off, but thats just not realistic is it. Might have to have a think about that one then, or find another solution (e.g. fire proofing some wood). Funnily enough when I was in New Zealand a couple of months ago my dad and I remarked about how they loved to paint their wooden frames houses dark colours, we figured perhaps it didn't have the heating effect we thought it would.
RE insulation, point noted from various posters, I wasn't aware rockwool was only 1/3rd the performance, I thought it was better than that tbh, that would only be 30mm, which wouldn't be enough. Does anyone know if EPS is worthwhile considering? 100mm full fill EPS I think would be equivalent to 50mm Celotex but a bit cheaper (although possibly not worth it).
One thing I'm finding hard is to work out the practical difference; I guess adhering to building regs or thereabouts you know you'll end up with a habital quality building, just got a nagging feeling it might be a little OTT and I could trim here and there, its just working out which bits don't matter so much, e.g. is the heat loss through the floor less than the heat loss through the roof, therefore bias towards more insulation there and make compromises in the floor.
Thanks all for the inputs, it helps.
Tin Hat said:
I would avoid EPDM roofs, we stopped installing them about 3 years ago, they are problematic. Kemperol is relatively inexpensive and significantly more reliable.
I have built our room with the deck directly over 100mm celotex, using foil back plasterboard beneath the joists as a token vapour barrier. I personally think that the cold/warm roof dilemma is not the drama that it could be in a garden room environment, as opposed to a living space that may have bathrooms and kitchens where significant moisture is generated.
I would definitely use celotex in the walls.
Cement board can be very effective for cladding, it is highly stable and durable and can often react well to being painted, requiring little long term maintenance.
Buy timber from a reputable timber merchant, if you use general Building goods suppliers, you’ll find 20% is unusable due to twist or warp.
Are you able to give a bit more detail on the roof makeup you're talking about? Not 100% sure I understand the makeup you're talking about?I have built our room with the deck directly over 100mm celotex, using foil back plasterboard beneath the joists as a token vapour barrier. I personally think that the cold/warm roof dilemma is not the drama that it could be in a garden room environment, as opposed to a living space that may have bathrooms and kitchens where significant moisture is generated.
I would definitely use celotex in the walls.
Cement board can be very effective for cladding, it is highly stable and durable and can often react well to being painted, requiring little long term maintenance.
Buy timber from a reputable timber merchant, if you use general Building goods suppliers, you’ll find 20% is unusable due to twist or warp.
Will look into the alternative roof products, and the cement board.
Tin Hat said:
Assuming that you are aware of cold/warm roofs and their differing ways of dealing with condensation, you may recognise that you either ventilate ( which increases the thickness of the roof ) or you need to (strictly speaking) develop an airtight box with vapour control layers. My suggestion avoids obsessing about the integrity of the VC layer, the internet would have you believe that this will lead to catastrophe
Yeah, was that a cold roof construction? There is someone on youtube who does a hybrid where he does cold roof but with the PIR hard up against the deck, and then Vapour Barrier layer across the joists. Isn't strictly compliant as he doesn't then ventilate the eaves, but works on the assumption that there isn't a lot of ways for vapour to get in-between, and as you say, it is a garden room, so how far do you go in engineering it?Am considering wall mounted all in one AC as I can install that myself vs a split where I need an engineer.
So, from what people have said, considering:
1) putting 100mm of EPS in the floor vs PIR etc
2) Reconsidering cladding options (could have a go at through coloured rendering I suppose!)
alfabeat said:
I've worked from a garden out building for getting on for 8 years. It is a chalet style with c50mm thick walls. No insulation. There is rock wool in the roof. No insulation in the floor.
It's fine in the summer with the doors and windows open (once the sun hits in the afternoon) and for winter I have a cheap wood burner from Machine & Mart, which gets it toasty warm in minutes and then I'm down to a t-shirt pretty quickly.
Suppose what I'm saying is, if you can have a woodburner, then is all this insulation necessary? I do have an endless supply of free wood though.
I have never felt the need to up the insulation levels.
I don't have an endless supply of free wood, and I'm in a built up area. Worth considering a fire but I suspect the sunk cost is probably quite high before payback, if at all when you are buying wood in.It's fine in the summer with the doors and windows open (once the sun hits in the afternoon) and for winter I have a cheap wood burner from Machine & Mart, which gets it toasty warm in minutes and then I'm down to a t-shirt pretty quickly.
Suppose what I'm saying is, if you can have a woodburner, then is all this insulation necessary? I do have an endless supply of free wood though.
I have never felt the need to up the insulation levels.
I'm actually, to be honest, more worried about thermal gain in the summer than I am heating int he winter, I think. The location would be in full sun from midday through till 7pm, so it is going to get a fair amount of sun (hence Equus point about cladding colours being a worry!)
Harry Flashman said:
Interesting debate in terms of insulation. I understand the roof being the most important bit - the importance of loft insulation is pretty indicative here. I have always lived in houses with uninsulated walls, but putting stuff into ceilings has been very effective.
My lean-to garage, all wood, no insulation, gets very cold in winter and very hot in summer. I have to take that as the best indicator for how a similarly constructed building would behave in the garden.
I think if/when we do it, there will be insulation everywhere to keep heat in in winter, a roof velux (with blind) to vent hot air, doors and windows on more than one side of the building in order to allow airflow, and most likely an aircon unit for both heating and cooling.
Not really a budget build, but if the room will get serious use, I suspect worth it. Still way cheaper than doing an extension, and probably slightly value additive to the house if using man maths.
We have a study already, but would quite like another workspace, and a small gym.
I was going to say don’t you live in a 6 bed pile with only the three of you! But like me you do love a good project My lean-to garage, all wood, no insulation, gets very cold in winter and very hot in summer. I have to take that as the best indicator for how a similarly constructed building would behave in the garden.
I think if/when we do it, there will be insulation everywhere to keep heat in in winter, a roof velux (with blind) to vent hot air, doors and windows on more than one side of the building in order to allow airflow, and most likely an aircon unit for both heating and cooling.
Not really a budget build, but if the room will get serious use, I suspect worth it. Still way cheaper than doing an extension, and probably slightly value additive to the house if using man maths.
We have a study already, but would quite like another workspace, and a small gym.

I agree using as much insulation as possible is good, but it is a hard call to know where you could shave a bit of cost off and not really notice (or the payback period is many many years). For example diminishing returns on loft insulation - I think I’ve read the first 100mm saves you the oft quoted £100+ a year, the extra 170mm to make a compliant 270mm total is like £20.
It’s occurred to me that as my plan is to split the place in two, with one half a shed / workshop type space, I could insulate that bit with EPS, and insulate the internal wall similarly, again to reduce the cost as the EPS is so much cheaper. Worth thinking about. Although detailing the wall to ensure two different spaces would be a challenge without bridging the insulation badly.
Milsey said:
Ours is approximately 6.5m x 3m, 1/3 is going to be storage and 2/3 garden room. You can feel it is warm, even with a 6 foot wide opening for the doors that are due to go in. We planned to be able to use this space all year round so may have to install a small heater for the colder months, warmer months we will have plenty of ventilation with two opening windows and french doors at the front. I estimate the total for insulation and foil tape etc to be around £350.
If you want a full sized sheet of 50mm PIR I have one left over going cheap!
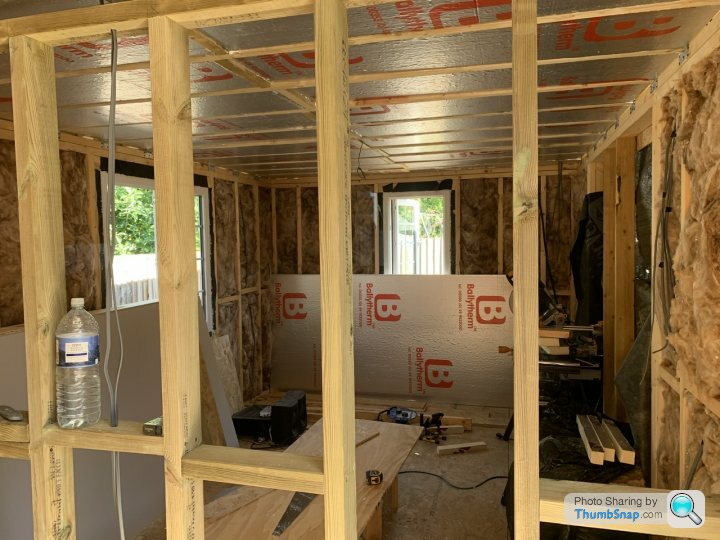
Ah can you come build mine? If you want a full sized sheet of 50mm PIR I have one left over going cheap!
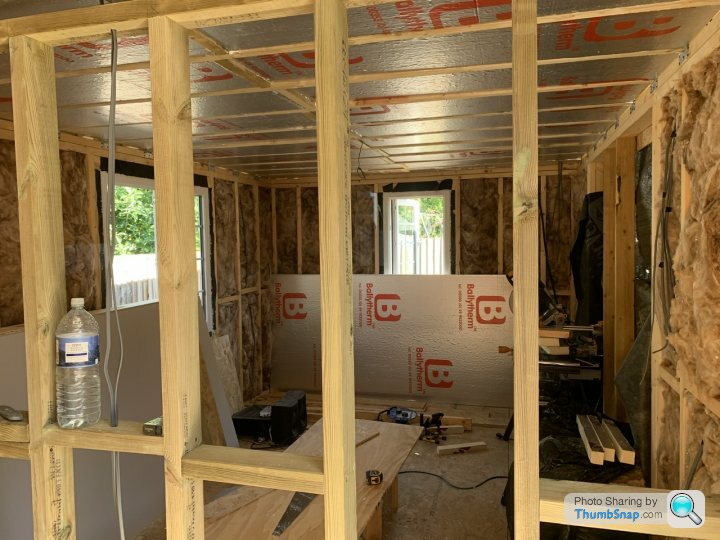

So you went for rockwool in the walls? Any particular reason?
@ Harry - Congrats, we've got a now 8 month old who is the reason I need a new office as she stole mine (rude) as we don't live in a 6 bed (but I do now have a british racing green painted dining room, which is partially your fault

I've been watching williams video's on YouTube extensively; I think he makes some really sensible accommodations to it being a garden room (lets be practical, is it a 100 year building? probably not). And can't argue with the look of the product at the end. His piling system is also clever.
Gassing Station | Homes, Gardens and DIY | Top of Page | What's New | My Stuff