PH Origins: Direct fuel injection
How a pretty little two-stroke coupe pipped Mercedes-Benz's 300 SL to the direct-injection post
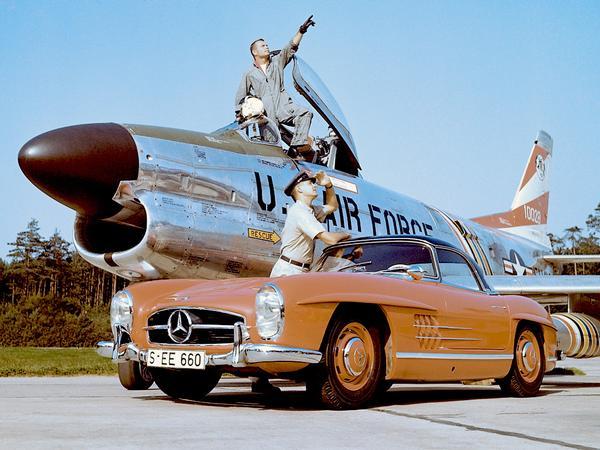
Search the web for 'direct fuel injection history' and two prominent results will often materialise: Leon Levavasseur and the Mercedes-Benz 300 SL. Their prevalence is understandable. Levavasseur is frequently credited as being the first to develop and design a direct fuel injection system for petrol-fuelled engines in 1902; the Mercedes-Benz, on the other hand, is often regarded as the first production car with direct injection - arriving on the market in 1954 with a Bosch-designed system.
While it's unquestionably the case that both Levavasseur and the fabled Merc are notable in many ways, neither of the above statements is correct - even though, in the case of Levavasseur, his 'direct injection' system is referred to in countless technical works.
In the early 1900s, as the Wright brothers clawed their way into the sky, Levavasseur - a skilled engineer - realised that there was a need for light, powerful engines that were better suited to aviation use. He consequently set about penning a series of new designs, the first of which was the remarkable 'Antoinette'.
This engine, the design of which was patented in 1903 and granted in late 1904, is claimed to be the world's first production V8 - a configuration that Levavasseur deemed would 'produce a torque as uniform as possible'. It had an aluminium crankcase and cylinder heads, cutting weight, water-cooled cylinders and a coil-based ignition system. This smooth-running V8 displaced 3.2 litres and, tuned to perfection, punched out some 80hp.
It wasn't immediately employed in an aircraft, however. Instead, Levavasseur and financial backer Jules Gastambide fitted Antoinette V8s into a series of highly competitive speedboats - proving their capabilities and reliability, before branching out into the rapidly expanding aviation industry.
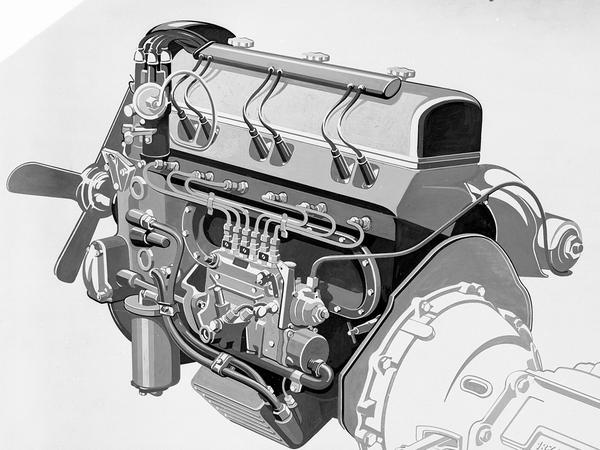
More to the point, this engine is often cited as featuring a mechanical 'direct injection' fuel system and, if you glance at pictures and the reports, it's easy to see why. Feeding such a complex multi-cylinder engine required either numerous carburettors or faith that the design of the intake manifold would roughly distribute the incoming air-fuel mixture evenly between the cylinders. This, besides not being ideal for optimising power output, could also cause reliability issues.
To work around this problem, Levavasseur designed a system that allowed for the 'grouping of various carburettors for feeding multi-cylinder engines', a concept which was later patented in 1906. This set-up featured an engine-driven fuel pump that supplied what was effectively a series of simple carburettors positioned above the intake valve of each cylinder.
These 'carburettors' - as they were described in the patent - consisted of a small fuel reservoir, kept topped up by the low-pressure pump, that fed a narrow metering port. Fuel would flow out of this port when the intake stroke commenced, mixing with the incoming air before entering the cylinder.
This indirect system, which the patent states relied on fuel being drawn out by 'engine suction', was crude but easily reconfigured to suit a variety of engine designs - which proved useful for Levavasseur, who later developed engines with up to 32 cylinders.
The general concept of injecting fuel directly into the combustion chamber had already been proven by this point, however - albeit not with petrol. Diesel engines had been relying on direct injection since the late 1800s; Rudolf Diesel's engines, from 1898 on, featured a fuel system that utilised compressed air to generate the required spray of diesel directly into the combustion chamber.
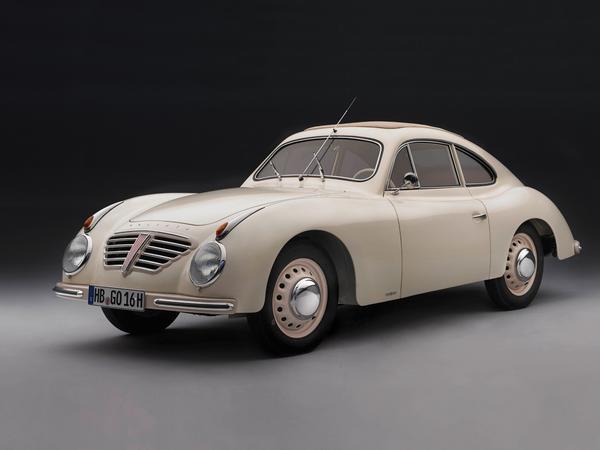
German engineering company Bosch, as diesels and petrol engines alike began being produced in vast numbers, took an interest in this burgeoning injection technology; one such tranche it was exploring, starting in 1912, was petrol injection. Improved fuel metering, after all, would offer several significant benefits - and, as Levavasseur had already demonstrated, a smartly designed system could easily be adapted to a range of powerplants.
Development was slow but, as aviation technology began to advance at an ever-increasing rate, demands upon fuelling systems grew. For example, in 1915, Junkers' J 1 monoplane weighed 1,080kg and was powered by a 120hp 9.5-litre Mercedes-Benz straight-six engine. Flat out, it could just exceed 100mph and - during testing - it is reported to have climbed to 3,000ft.
By 1937, an early production version of the company's new Ju 87 dive bomber took to the skies. Its maximum takeoff weight was ,3400kg, while its 661bhp, 19.7-litre Jumo inverted V12 could propel it to 200mph and a heady 26,500ft.
The capabilities and requirements of these modern aircraft caused problems for carburettors. When pilots pushed the nose of the aircraft down, the negative g-force that resulted would push the fuel in the carburettor's float chamber upwards. This would cause the float to sink, allowing fuel to flood the chamber.
This excess fuel would force its way into the engine, causing an overly rich mixture and a substantial drop in power output. This would be of a great disadvantage for a combat aircraft, which would be prone to high-g manoeuvres.
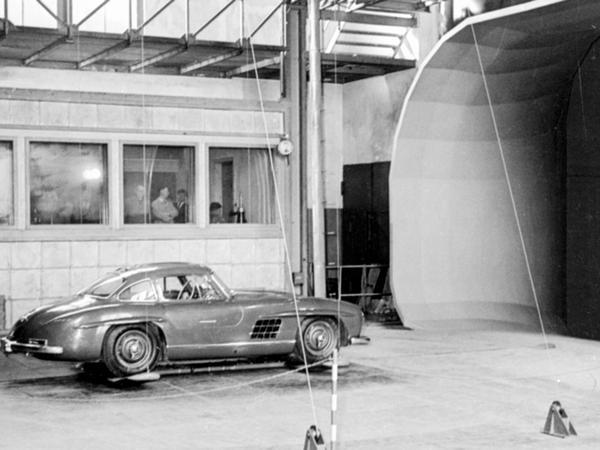
Carburettor icing was also an issue, causing reduced power and a potential loss of control - and, as boost pressures and fuel flow increased, catastrophic backfires through the intake manifold became more common.
To avoid these issues, Bosch developed a system - first used on the Daimler-Benz DB 601 in 1935 and in series production by February 1937 - that injected the fuel directly into the combustion chamber. This meant there was no air-fuel mixture that could explode in the intake, it prevented icing issues entirely and also solved the problem of negative-g fuelling. The direct-injected engines often also proved more efficient, powerful and responsive.
This gave the DB-equipped Messerschmitt Bf 109s a considerable edge, following the start of World War II, over early Merlin-powered Spitfires; German aviators knew that forcing a Spitfire to execute a nose-down manoeuvre would cause it to lose power, or make its pilot roll the aircraft in order to maintain positive g at the carburettor. This issue was significantly reduced later in the war by the introduction of 'Miss Shilling's orifice' - a flow restrictor, designed by engineer Beatrice 'Tilly' Shilling, which limited the effects of the rapidly changing g-forces on the Merlin's fuel system.
Other manufacturers had also been working on direct injection systems and, not long after, Jumo's own in-house direct-injected 210G engine took to the skies in March 1937. By 1939, the likes of BMW were using direct injection in conjunction with the world's first engine management system.
Bosch hadn't overlooked the automotive possibilities of its system, though; it reputedly got a compact DKW Meisterklasse saloon - with a two-stroke, two-cylinder engine - running using a direct-injection system by 1938. The war effort soon meant that all developmental and production resources were directed elsewhere, so testing of the automotive system ground to a halt - but aviation-focused direct injection continued to advance in leaps and bounds.
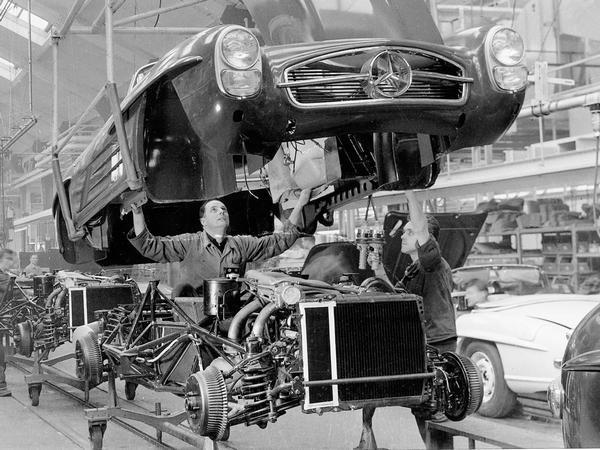
Following the war, Germany's economy necessitated efficient compact cars. One such car was the GP700, designed and produced by the Goliath motor company. The GP700, which was unveiled in 1950, was a two-stroke, front-wheel drive car with a transversely mounted engine - yes, like the Mini - and a range of body styles.
The 25hp 688cc engine wasn't particularly economical, though, so Goliath's development team approached Bosch to collaborate on a new fuel system that would boost efficiency and output. Bosch had soon designed a direct injection system, using its prior experience, which was suitable for mass production. Then, in April 1951, Goliath unveiled its direct-injected GP700 Sport at the first Frankfurt motor show.
The benefits were significant. Power rose by 10 per cent, compared to the previous carburetted engine, and fuel consumption decreased by 32 per cent. Only 27 of these elegant little coupes were built but Goliath forged ahead, making its injection system available on the saloon version - and later on its larger 845cc engines. Even 'The Autocar' deemed the injected Goliath an impressive feat, dubbing it 'one of the most economical cars in the world'.
Not long after, in 1954, Mercedes-Benz introduced the 300 SL in production form. It, like the Goliath, featured a Bosch-designed mechanical direct injection system - which was adopted in an effort to maximise the output and responsiveness of the Mercedes' 3.0-litre straight-six engine.
Direct injection was still some way from widespread use in the automotive marketplace, however. While research continued on the systems, it wasn't until the advent of modern electronic controls and injectors that a mass-produced, reliable and effective direct injection set-up became viable. Mitsubishi was first to the market with a modern system of this type, unveiling 'Gasoline Direct Injection' in 1996.
Many have since utilised electronically controlled direct injection but, due to the system's tendency to generate excessive particulate emissions, direct injection is sometimes blended with conventional port injection - allowing a happy balance between output, efficiency and emissions to be struck.
Gassing Station | General Gassing | Top of Page | What's New | My Stuff