What is Dynamic Skip Fire? PH Explains
How continually activating and deactivating cylinders boosts economy without harming refinement
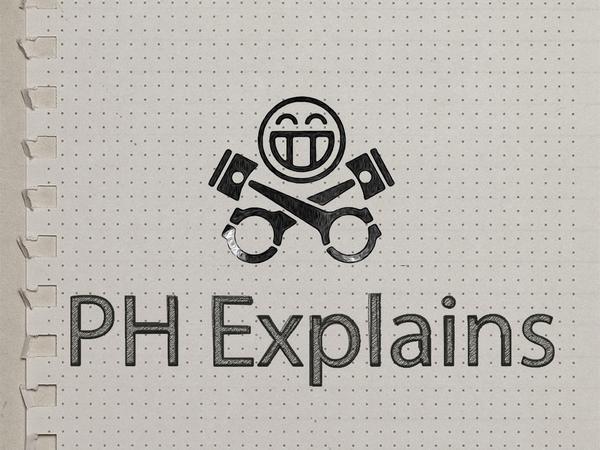
'Dynamic Skip Fire' is an advanced form of cylinder deactivation which offers improved refinement, flexibility and efficiency when compared to standard set-ups.
In conventional cylinder deactivation systems, the engine will alternate between fixed patterns of active cylinders in order to improve efficiency in light load conditions. These patterns will be decided by whichever combination of running cylinders results in the least vibration.
A Volkswagen four-cylinder engine equipped with 'Active Cylinder Technology', for example, will always shut down cylinders two and three. In certain situations, however, the efficiency of the engine could be boosted even further if it were to run on just the one cylinder - but doing so would induce prominent vibrations, reducing refinement.
DSF aims to permit such flexibility by firing the minimum number of cylinders per crankshaft revolution to maintain the desired torque output - and does so in an ever-shifting pattern that minimises engine vibration.
This form of dynamic 'variable displacement' was developed by Delphi Technologies and Tula Technology. Current users included General Motors, which has fitted it to the 5.3- and 6.2-litre versions of the 2019 model year Chevrolet Silverado. In GM's applications, the system is called 'Dynamic Fuel Management'.
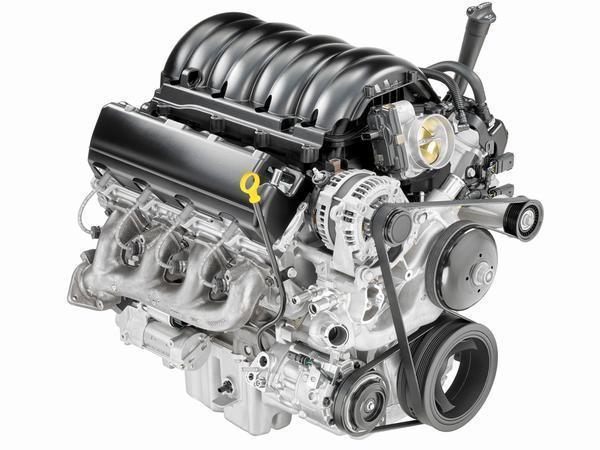
What are the advantages of dynamic skip fire?
In standard cylinder deactivation systems, cylinders will be shut off when the engine load drops to low levels - such as when cruising at a steady speed. This improves the efficiency of the cylinders that remain active, reducing the overall fuel consumption of the engine.
These set-ups typically have to shut down cylinders in specific patterns, however, in order to avoid excessive vibration. In a V6, one bank will shut down; in a V8, the inner pair of cylinders on one bank will be deactivated along with the outer pair on the other bank.
This means that the potential efficiency savings are limited by the number of cylinders that must remain active in order to avoid compromising refinement excessively; transitions between the cylinder firing modes can also be noticeable, further reducing comfort.
These set-ups are not flexible in their operation, either. A driver may require only a fraction more power but that additional demand may necessitate the entire deactivation system being disabled. This inefficiently brings all the cylinders online to meet the power demands of that moment.
DSF aims to counter these issues by instead deciding whether or not to fire each individual cylinder when the opportunity arises - and, as the name suggests, it can 'skip' the firing of cylinders which might cause vibration or noise-related issues.
Because it can choose whether or not to fire each cylinder, instead of shutting down just a fixed selection of cylinders, the system is far more flexible. The management system will look at the torque required, then decide how many cylinders need to fire in that revolution to maintain that output. It will then further pick a combination of firing cylinders that will avoid resonance issues, helping quell any excess vibration or noise-related problems.
If more torque is required, then additional cylinders can be unobtrusively and quickly phased in to meet the new demands - without having to resort to simply bringing every cylinder back online, as a conventional system would.
In a four-cylinder engine running at 3,000rpm, according to the manufacturer, a DSF system can alter the cylinder combinations up to 6,000 times a minute. This process of continually firing the most efficient number of cylinders in the best order helps DSF to deliver effectively the optimum engine displacement, while maintaining a suitable degree of refinement, at any given moment.
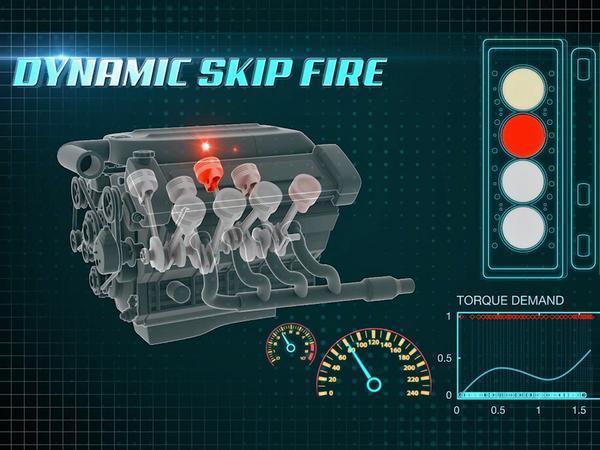
How does dynamic skip fire work?
An advanced management system runs the DSF system. It continuously monitors the driver's inputs to work out how much torque is required at any given moment, then decides how many and which cylinders need to fire in order to meet the demands while avoiding noise and vibration issues.
DSF controls the flow of air into and out of each cylinder using oil-controlled roller finger followers or tappets - as found in other cylinder deactivation systems - which effectively function as an on/off switch for each valve.
When a cylinder is not needed, the deactivation mechanism disconnects the valves from the action of the camshaft, keeping the valves closed. The air trapped inside functions as a spring, helping smooth the engine's action and conserving some energy, then when the cylinder is needed the valves begin opening again and firing recommences.
The cylinders that remain operational function at higher power and efficiency levels which - in conjunction with reduced throttling losses - helps cut fuel consumption and emissions.
There are other advantages to this approach, too, including improved catalytic converter performance. During deceleration, all the cylinders can be shut down - reducing pumping losses and preventing cool air being pumped through the catalytic converter. This helps avoid reducing its temperature excessively, which harms the performance of the converter.
Gassing Station | General Gassing | Top of Page | What's New | My Stuff