540HP NA 7L V12 3 seater
Discussion
I am working on a homebuild project that I thought might interest some of you - but it is very unconventional so, like marmite, you are going to like it or hate it. But as I am only building it for myself and I like marmite.....
My ultimate car is the Mclaren F1 road car, I think it is the best packaging exercise carried out to date. However I doubt I will ever own a real one as the values are climbing a thousand times faster than my income. And then I got to thinking, would I really ever want to actually own a real one? They are beautifully styled, aerodynamic, have a superb powerplant and would be enormous fun to drive, but they are becoming so valuable that the enjoyment of them as a car is diminishing, and they are becoming a victim of their own success. As the recent Autocar Mclaren Ultimate series review stated only a handful of them are actually being used in anger, the rest are like jewels locked in a vault. A great pity but totally understandable.
So after more than 25 years of pondering and deliberating and realising that a real F1 is out of my reach I am embarking on a homebuild project that incorporates the ethos of the F1, and the title of the thread gives the highlights. I did not want to style my own car as that is a task very few homebuilders achieve with success, however I am quite comfortable designing a chassis and powerplant configuration that meets both my goals and the NZ LVVTA regulations to put this thing on the road.
My longstanding puzzle was how do you economically combine a large capacity V12 engine and manual transmission? Mclaren brilliantly devised a longitudinal V12 with a transverse gearbox to minimise length, however all the V12's I have seen available were not "bargains". Since I am going to drive this vehicle very hard the engine and gearbox maintenance costs have to be minimised, ideally using "off the shelf" components. The power and torque levels I am using are always challenging for midengined car builders as the transaxle options available are limited.
So we arrive at my solution, which is the marmite moment;
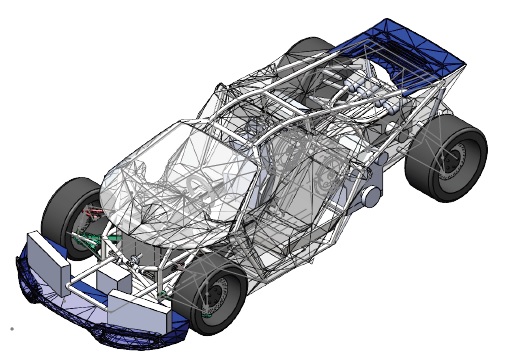
I have a pair of transversely mounted honda J35Z2 engines (stock 270hp and 344Nm of torque each), each with a standard dual mass clutch, that will drive a spiral bevel pinion that is in constant mesh with a common crownwheel at a 1:1 ratio. The crownwheel is coupled directly to the input shaft of a C6 Corvette transaxle (TR6060). I am using 2 ECU's as I can disconnect one motor while driving around on the other for improved economy - I like long road trips and the South Island has some beautiful roads but not many petrol stations.
Using this configuration I have some major benefits
- 3.5L V6 engines are reliable, cheap and plentiful - they are plug and play items
- TR6060 has a torque limit of 800Nm, wheelspin is most likely the torque limiter for this setup
- the weight is rear biased but not excessively, split as modelled is currently 43F/57R
- due to the space between the engines I have direct access to the standard corvette gearbox shift linkage - so direct "like a rifle bolt" shifts are easy to achieve
- I can also run the front bank exhausts through the same gap
Suspension and brakes are C6 corvette items, J55 brake option (Z51). Leaf springs are replaced by coilovers.
Spaceframe is all 4130 tubing, interior bulkheads and outer skin panels are composite material. Currently I am working on the surfacing models for the body panels, here is a snapshot of my progress to date - still a long way to go.
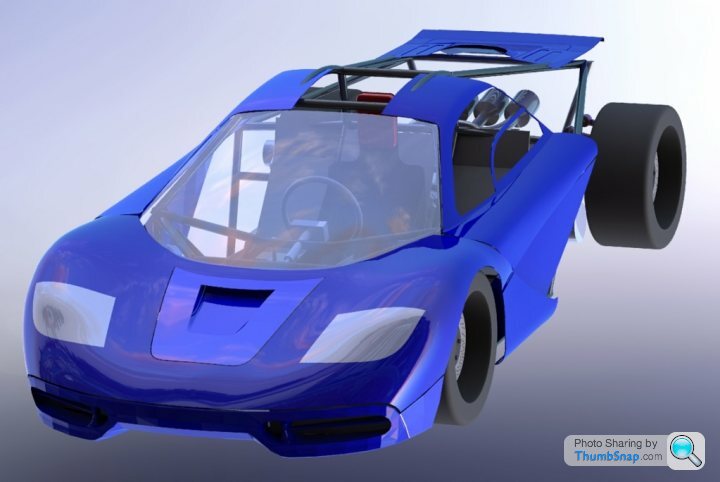
Target weight will be 1300Kg, mainly because this is the first car I have built from scratch so I am trying to be realistic. A full carbon composite chassis is not in my budget and is also harder to get road compliance with - but I will shave off weight wherever possible. Performance will still be good at that porky weight, however I can in the future change the cams and porting to get 350HP each, still natually aspirated. Turbo charging is also possible, the AR35TT uses the same block and heads and gives 550HP each, but 1100 is too much for the road. The gearbox life would most likely be shortened unacceptably at the level also. This is a daily driver & grand touring car, not a racecar and thus does not need bragging right HP numbers.
I think that suffices as an introduction, now for your comments...
My ultimate car is the Mclaren F1 road car, I think it is the best packaging exercise carried out to date. However I doubt I will ever own a real one as the values are climbing a thousand times faster than my income. And then I got to thinking, would I really ever want to actually own a real one? They are beautifully styled, aerodynamic, have a superb powerplant and would be enormous fun to drive, but they are becoming so valuable that the enjoyment of them as a car is diminishing, and they are becoming a victim of their own success. As the recent Autocar Mclaren Ultimate series review stated only a handful of them are actually being used in anger, the rest are like jewels locked in a vault. A great pity but totally understandable.
So after more than 25 years of pondering and deliberating and realising that a real F1 is out of my reach I am embarking on a homebuild project that incorporates the ethos of the F1, and the title of the thread gives the highlights. I did not want to style my own car as that is a task very few homebuilders achieve with success, however I am quite comfortable designing a chassis and powerplant configuration that meets both my goals and the NZ LVVTA regulations to put this thing on the road.
My longstanding puzzle was how do you economically combine a large capacity V12 engine and manual transmission? Mclaren brilliantly devised a longitudinal V12 with a transverse gearbox to minimise length, however all the V12's I have seen available were not "bargains". Since I am going to drive this vehicle very hard the engine and gearbox maintenance costs have to be minimised, ideally using "off the shelf" components. The power and torque levels I am using are always challenging for midengined car builders as the transaxle options available are limited.
So we arrive at my solution, which is the marmite moment;
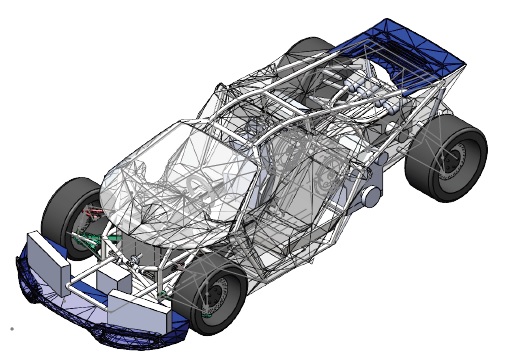
I have a pair of transversely mounted honda J35Z2 engines (stock 270hp and 344Nm of torque each), each with a standard dual mass clutch, that will drive a spiral bevel pinion that is in constant mesh with a common crownwheel at a 1:1 ratio. The crownwheel is coupled directly to the input shaft of a C6 Corvette transaxle (TR6060). I am using 2 ECU's as I can disconnect one motor while driving around on the other for improved economy - I like long road trips and the South Island has some beautiful roads but not many petrol stations.
Using this configuration I have some major benefits
- 3.5L V6 engines are reliable, cheap and plentiful - they are plug and play items
- TR6060 has a torque limit of 800Nm, wheelspin is most likely the torque limiter for this setup
- the weight is rear biased but not excessively, split as modelled is currently 43F/57R
- due to the space between the engines I have direct access to the standard corvette gearbox shift linkage - so direct "like a rifle bolt" shifts are easy to achieve
- I can also run the front bank exhausts through the same gap
Suspension and brakes are C6 corvette items, J55 brake option (Z51). Leaf springs are replaced by coilovers.
Spaceframe is all 4130 tubing, interior bulkheads and outer skin panels are composite material. Currently I am working on the surfacing models for the body panels, here is a snapshot of my progress to date - still a long way to go.
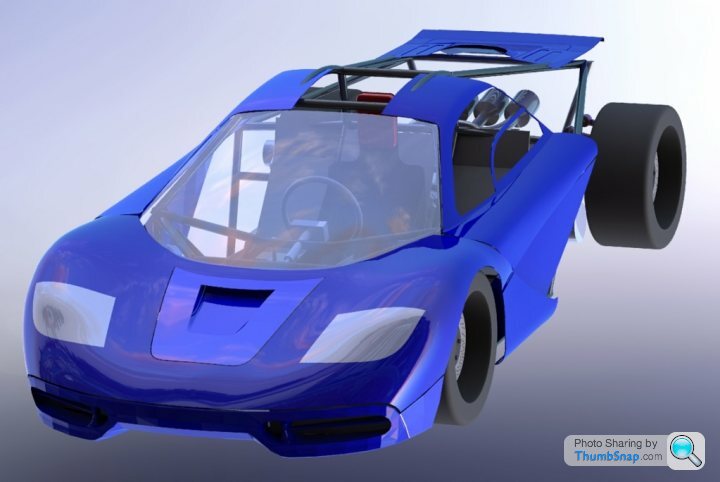
Target weight will be 1300Kg, mainly because this is the first car I have built from scratch so I am trying to be realistic. A full carbon composite chassis is not in my budget and is also harder to get road compliance with - but I will shave off weight wherever possible. Performance will still be good at that porky weight, however I can in the future change the cams and porting to get 350HP each, still natually aspirated. Turbo charging is also possible, the AR35TT uses the same block and heads and gives 550HP each, but 1100 is too much for the road. The gearbox life would most likely be shortened unacceptably at the level also. This is a daily driver & grand touring car, not a racecar and thus does not need bragging right HP numbers.
I think that suffices as an introduction, now for your comments...
Edited by F1natic on Saturday 18th July 08:03
Thanks guys, I assure you that this one will not be treated gently. Mad Mike Whiddett is based at the track (Hampton Downs) that I will be doing my initial reliability and system testing - so I can't imagine him resisting an offer to test it.
The crank harmonics between the engines is a real unknown, it is kind of experimental but like most things in engineering something similar has been done before - however in the link below they only achieved a 4000 Hp setup.
https://oldmachinepress.com/2017/04/20/ ... ft-engine/
In my setup both engines run completely independant of each other, and when 30 degrees out of synchronisation they may sound like a V12, however getting 2 ECU's to talk to each other and lag one to match the primary signal is uncharted territory. Would hate for it to sound like a poorly tuned V6, but it will be what it will be. I have also been told that clutches can walk so synch may be lost anyway, especially at higher horsepower levels. I love the sound of formula one engines on the rev limiter, like at Goodwood FOS. The roughness added a raw edge I quite liked the sound of. ECU's are Speeduino units designed in Australia by Josh Stewart - worth checking out if you like working with tunerstudio.
Currently I have the 2 factory standard V6's (1 still installed in my daily driver 2008 accord which I use to analyse the factory ECU parameters), all suspension control arms, spindles, rotors and calipers plus a porsche 911 steering rack, which is the only road car rack with a perpendicular pinion that i have found, however it is too short and needs to be lengthed to avoid bump steer with the C6 spindles. Currently have been given concept approval (4A) from LVVTA to complete the detail design drawings and submit for build permission (4B). Once that is done (next couple of months the way things are progressing) I can start cutting tubing, 3D printing my casting patterns (I have full access to an investment casting foundry with CMM, CNC mill and router, lathe etc) up to 120 Kg.
Got to clear a few things out of the rented workshop first. Build time for the rolling chassis is going to be a couple of years due to paycheck limits, and the body work will be a big stretch financially, but once I have the chassis sorted and proven then I can have plenty of fun while making the bodywork.
Glazing is currently my biggest hurdle, and using a windscreen from a genuine is out and nothing is even close as far as I have been able to tell so probably going to have to put a couple of sheets of flat glass on a CNC mould and drape it in a big kiln. A subcontractor I am talking with has successfully draped 40mm thick glass, I have a scale test run sheduled for early November.
The J35's have headifolds (more marmite anyone?) but that makes my fabrication job easier, pipes are same length front and back due and have to run through cats for compliance.
My testing plan is Thrash-Break-Fix-Repeat. The whole rear section will be on a subframe to allow easy removal for Tbox inspection and maintenance.
The crank harmonics between the engines is a real unknown, it is kind of experimental but like most things in engineering something similar has been done before - however in the link below they only achieved a 4000 Hp setup.
https://oldmachinepress.com/2017/04/20/ ... ft-engine/
In my setup both engines run completely independant of each other, and when 30 degrees out of synchronisation they may sound like a V12, however getting 2 ECU's to talk to each other and lag one to match the primary signal is uncharted territory. Would hate for it to sound like a poorly tuned V6, but it will be what it will be. I have also been told that clutches can walk so synch may be lost anyway, especially at higher horsepower levels. I love the sound of formula one engines on the rev limiter, like at Goodwood FOS. The roughness added a raw edge I quite liked the sound of. ECU's are Speeduino units designed in Australia by Josh Stewart - worth checking out if you like working with tunerstudio.
Currently I have the 2 factory standard V6's (1 still installed in my daily driver 2008 accord which I use to analyse the factory ECU parameters), all suspension control arms, spindles, rotors and calipers plus a porsche 911 steering rack, which is the only road car rack with a perpendicular pinion that i have found, however it is too short and needs to be lengthed to avoid bump steer with the C6 spindles. Currently have been given concept approval (4A) from LVVTA to complete the detail design drawings and submit for build permission (4B). Once that is done (next couple of months the way things are progressing) I can start cutting tubing, 3D printing my casting patterns (I have full access to an investment casting foundry with CMM, CNC mill and router, lathe etc) up to 120 Kg.
Got to clear a few things out of the rented workshop first. Build time for the rolling chassis is going to be a couple of years due to paycheck limits, and the body work will be a big stretch financially, but once I have the chassis sorted and proven then I can have plenty of fun while making the bodywork.
Glazing is currently my biggest hurdle, and using a windscreen from a genuine is out and nothing is even close as far as I have been able to tell so probably going to have to put a couple of sheets of flat glass on a CNC mould and drape it in a big kiln. A subcontractor I am talking with has successfully draped 40mm thick glass, I have a scale test run sheduled for early November.
The J35's have headifolds (more marmite anyone?) but that makes my fabrication job easier, pipes are same length front and back due and have to run through cats for compliance.
My testing plan is Thrash-Break-Fix-Repeat. The whole rear section will be on a subframe to allow easy removal for Tbox inspection and maintenance.
Edited by F1natic on Wednesday 21st August 14:02
Edited by F1natic on Wednesday 21st August 20:17
RelentlessForwardProgress said:
Have you got as far as door seals? Having spent hundreds on them for an E46 coupe and what with Singer spending >$100billion on theirs, i’d hate for details like that to scupper your plans. Masses of good luck to you, please keep us updated.
Thanks, and good question. I have a few options for extruded rubber seals suitable for a door system- www.pararubber.co.nz. -automotive clip on door seals. I may take a standard profile and cut most of the clip on section away and bond the remainder into a recess moulded into the door aperture. The F1 had a lot of thought gone into this critical detail, nothing worse than opening a dihedral door and dumping a bunch of water into the interior. NVH are another tricky matter and manufacturers spend millions lowering them (my LS400 is a superb example). Lots of sound deadening on the rear bulkhead and exhaust bandage over the exhausts should help.Edited by RelentlessForwardProgress on Wednesday 21st August 16:33
Oddly the doors are the first thing I am building on the test mule exterior, since i need to build an MDF seating buck to check my interior dimensions are comfortable before I committ them to steel. I am mocking up in full scale as much as possible since CAD is not always the most time effective solution. This buck will then be used as the mould for the carbon fiber interior. Plus in those gumption robbing phases of the build (we all have those) I will be able to sit in the buck and make car noises, which is actually important for positive visualisation and motivation. I might even hook up my PS3 and play GT6 in it, as I have setup the car parameters in the game and it is great fun to drive around the nurburgring virtually,.
Due to the unconventional nature of this build it is far easier to start with a clean slate and have all the critical parts in their final positions, then stitch everything together with tubing.
Edited by F1natic on Wednesday 21st August 18:51
Thanks for all the encouragement, I really appreciate the honest feedback - I have no ego in this and critical opinions are welcomed. It is impossible to see your own work subjectively, which is why I think most people should not style their own cars! Maybe if I had gone to the RCA....
I would probably style something like this - https://simpsons.fandom.com/wiki/The_Homer
Seriously though this car will be capable of EXTREMELY high speeds, the geartrain and suspension are the same part numbers as the C6 Z06 and have been validated up to 198mph (320kmh) with 505 HP (drag coefficient of 0.34 according to GM). The fastest I have ever driven is 125 mph for a short burst down the straight at the Nurburgring - I am talking about adding the UK speed limit on top of that. The high speed run at Nardo was done with under 600HP. It will not take much development to create 600-700HP from the twin engine setup - hence wanting to bring the center of mass as far forward as possible - the COP for the F1 is stable with a 40/60 weight split. With more power and the low drag coeffcient this cars potential is getting into very dangerous territory and instability caused by ineffective aerodynamic design could be fatal.
I would very much like to survive past the first trackday, so decided early on that piggybacking off aerodynamic development conducted in a proper windtunnel by boffins was not just a styling decision, but a safety one too. The shape is well proven in the wild (thanks to Dr Thomas Bscher) and stable at high speed, and produces downforce without external aerodynamic devices - I seriously don't think I could improve on that by guessing or using tufts of wool.
Another reason that reassures me is the fact that all the original patents are now in the public domain and can be used - which means we can all utilise the technology mclaren patented if desired - worth a look.
https://www.ipo.gov.uk/p-dl-notinforce.htm?filter=...
I think even Gordon Murray himself might have had to wait for the Mclaren patents to expire before publicising the T50??
I would probably style something like this - https://simpsons.fandom.com/wiki/The_Homer
Seriously though this car will be capable of EXTREMELY high speeds, the geartrain and suspension are the same part numbers as the C6 Z06 and have been validated up to 198mph (320kmh) with 505 HP (drag coefficient of 0.34 according to GM). The fastest I have ever driven is 125 mph for a short burst down the straight at the Nurburgring - I am talking about adding the UK speed limit on top of that. The high speed run at Nardo was done with under 600HP. It will not take much development to create 600-700HP from the twin engine setup - hence wanting to bring the center of mass as far forward as possible - the COP for the F1 is stable with a 40/60 weight split. With more power and the low drag coeffcient this cars potential is getting into very dangerous territory and instability caused by ineffective aerodynamic design could be fatal.
I would very much like to survive past the first trackday, so decided early on that piggybacking off aerodynamic development conducted in a proper windtunnel by boffins was not just a styling decision, but a safety one too. The shape is well proven in the wild (thanks to Dr Thomas Bscher) and stable at high speed, and produces downforce without external aerodynamic devices - I seriously don't think I could improve on that by guessing or using tufts of wool.
Another reason that reassures me is the fact that all the original patents are now in the public domain and can be used - which means we can all utilise the technology mclaren patented if desired - worth a look.
https://www.ipo.gov.uk/p-dl-notinforce.htm?filter=...
I think even Gordon Murray himself might have had to wait for the Mclaren patents to expire before publicising the T50??
Edited by F1natic on Thursday 22 August 11:28
Jbeale96 said:
One day, some time in the 2020s, you will have finished it, this thread will have hundreds of pages, will have inspired hundreds if not thousands of people and I will be able to say I was in it from the start.
What a truly incredible project.
I’ve called it now, don’t fail me OP!
Thanks mate, you just earned a drive in it when its done!What a truly incredible project.
I’ve called it now, don’t fail me OP!
chuntington101 said:
OP, if you are using the C6 gearbox and diff it might be worth looking at the Zr1 version. The tr6060 and diff are stronger than the stock c6 version.
you are absolutely right, the ZR1 is the ultimate box. After 2009 both the base Corvette and the Z06 used the TR6060 - designated as MM6 code, which is validated to 500 lb-ft of torque (around 680 NM). The TR6060 with the Z51 option features closer ratios and is designated as MZ6 - but is only validated to 430 lb-ft of torque. The ultra high performance ZR1 uses the TR6060 designated as the MH3, which is validated to 650 lb-ft of torque.However I am planning to use a low mileage box for initial testing and in 8 years of watching Ebay I have never seen a ZR1 box - they are rare. The MM6 is within my budget and pop up often at reasonable prices, much lower than a porsche G50.
Edited by F1natic on Saturday 24th August 19:46
3D print of nose at 1/10 scale has turned out good, surfacing is as desired. Wall thickness has to be exagerated otherwise the parts risk misprinting.
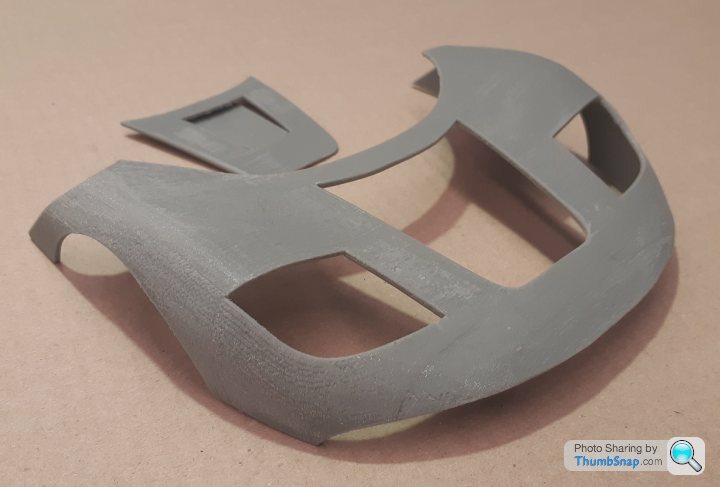
1/10 scale door skin.
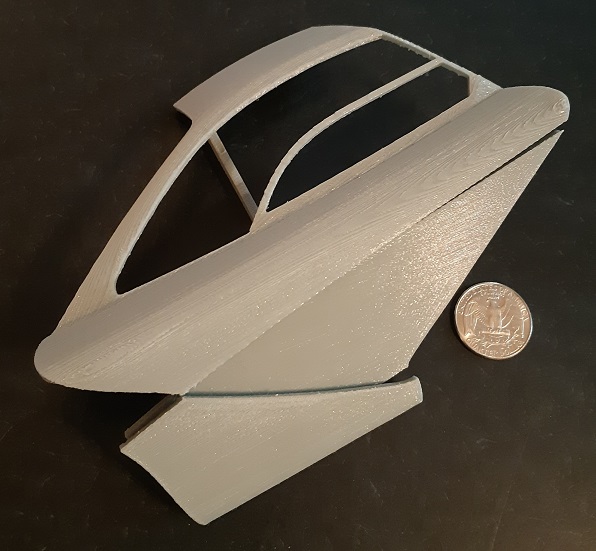
Going to focus on chassis detailing for the next couple of weeks - got some MDF today for the cabin mock up but my carpentry skills will get stretched.
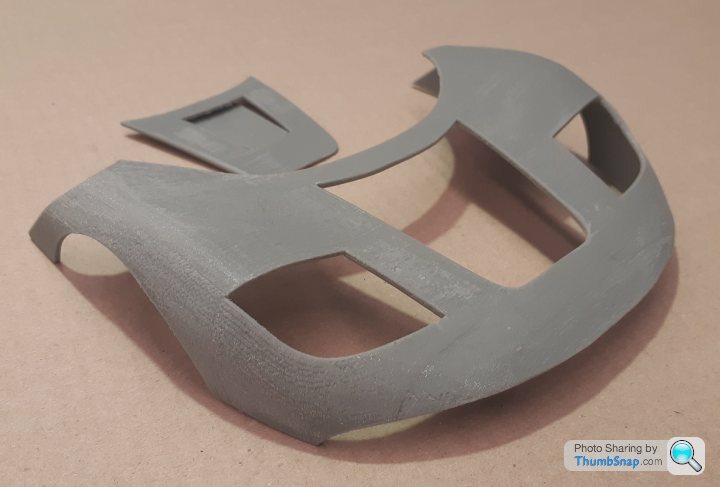
1/10 scale door skin.
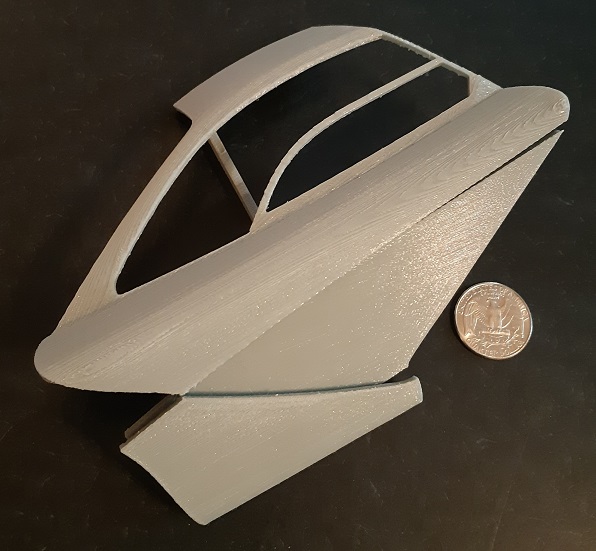
Going to focus on chassis detailing for the next couple of weeks - got some MDF today for the cabin mock up but my carpentry skills will get stretched.
Edited by F1natic on Sunday 25th August 09:56
RoverP6B said:
There is such a thing as an LS V12...
I don't know about you guys but USD$45K is out of my reality - crazy aussies. My plug and play V6's are currently NZD$850+ tax each = 520 GBP. The transmission and 3.42 ratio diff (rear carrier) can be bought NEW from GM for $USD 5,500 = 4,450 GBP - can't get a used porsche G50 for that as far as I have seen.
Low miles used C6 transaxles are averaging USD $3,850 = 3,135 GBP.
The Tbox is the key, and thats where I have my IP.
Because the whole rear section will drop out on a subframe I have a few options once the chassis is rolling;
1) a race spec setup - 2 dry sumped J37's
2) road car setup with the 2 stock J35's
3) fully electric for the near future when Tesla motor and battery packs are cheap enough secondhand
4) fallback position of a single V6 bolted direct onto the transaxle - twin turboed to get the power up (as per AR35TT setup) - if the Tbox is a failure
LaurasOtherHalf said:
Why do people keep suggesting traditional engines?
The OP has explained numerous times that in order to keep with the F1 datum points any such engine would need McLaren’s unique transverse gearbox.
Before saying “I’d fit a V...” come up with a unique gearbox to make it work
OP, did you find the answer to the cut outs above the headlights?
I reckon its because they don't like marmite! Or that we are all so used to seeing a certain setup that radical alternatives are viewed with great suspicion, and fair enough too, I've specifically put a weak link in the chain that will fail first - i.e. the dual mass flywheels are not reknowned for durability but if they take the beating and insulate my expensive custom made gears in the Tbox and also the ones in the transaxle then I am OK with that. Even Mclaren took a few attempts with some pretty experienced companies to get the transverse gear box sorted - I don't have their budget so my solution is really just a big lego set.The OP has explained numerous times that in order to keep with the F1 datum points any such engine would need McLaren’s unique transverse gearbox.
Before saying “I’d fit a V...” come up with a unique gearbox to make it work

OP, did you find the answer to the cut outs above the headlights?
One big benefit I see of splitting the full crankshaft power between the 2 engines is each clutch can be a lighter - a sport clutch will be all that is needed - I am intending to go through a few of them so ideally they should be cheap.
One benefit that I haven't discussed is the right angle drive in the Tbox allows me to set the engine crank centerline at an offset to the trans input axis - by using a hypoid gear set (like in a normal diff). The race version can therefore have a lower COG due to the drysumped engines being able to be dropped a few inches. The first powerplant will be road focused and used for testing the Tbox durability so engines will be stock initially.
I have not had a reply yet on the headlight eyebrow panels - refer my post in the epic Flemke Vol 5. I really don't see any reason for them to be there??
eliot said:
Well i wish you the best of luck sir, but i feel the engineering and available budget will see this become another rusty part-finished project on ebay in a couple of years.
Yes indeed, that's one of my fears too. Hence my strategy of multiple options on the powerplants. All the effort I put into the bodywork is independant of the powerplant. The twin v6 is an option nobody in industry would sanction, it adds too much weight and complexity to the package for little gain. But my budget dictates a few tradeoffs and unconventional options - I don't mind trying it because I have a foundry and machine shop to hand and I am OK with failure. The "only" unconventional parts are a 3 piece gear set and their housing and a custom steering rack - the rest of the chassis is fairly much off the shelf parts that just need a little cunning to bind together. The body work is of course a much bigger deal but that comes after I am out having fun on the track. Once the demonstrator is proven I think the rest will fall into place, people can be very supportive here in NZ once you are past the "dreamer" stage.
The driveable chassis will be very similar to one of my sources of inspiration;
https://youtu.be/6a1Gsjt92Do
Olivera said:
Extending the dimensions by a few cm here or there is infinitely easier than trying to engineer a twin engine setup 
I think it appropriate to make reference to the Artiplastzabrze effort - not a bad effort but even minor changes make a big difference to the aerodynamics, I am not sure I would attempt 200mph in one of those.
The supercars world is littered with failed attempts, a good example is https://en.m.wikipedia.org/wiki/HTT_Pléthore
They bolted a V8 onto the end of the same transaxle so resulting wheelbase forced bodywork to follow.
Classic styling has to follow the underpinnings, when form follows function you get a true design purpose, rather than a fashion statement.
klevenspielberg said:
Have you considered an F355 gearbox? They are transverse, not crazy money in the scheme of things, and would bring the complexity and lead time down a great deal I imagine. I don't know what sort of power they can handle or if the ratios are suitable for your application, but as you are looking into having custom gears machined anyway it might be worth a punt.
If you're at all thinking about commercialising the project, getting a 348/Mondial T (5 speed) 'box and a single V6 would probably not be a bad way to get an MVP. But hey, I'm a first time poster and not an engineer, so what do I know
Thanks for your comments, I really appreciate your post for 2 reasons;If you're at all thinking about commercialising the project, getting a 348/Mondial T (5 speed) 'box and a single V6 would probably not be a bad way to get an MVP. But hey, I'm a first time poster and not an engineer, so what do I know

1) I had not considered the F355 box, you are right they are not crazy money and look to be a very compact unit and closer investigation is warranted especially their torque capacity.
2) I was not aware of the MVP term (not my normal domain) and agree that simplicity is very desirable and increases the chances of getting it over the line. Design is an iterative process and I am happy to assess alternatives.
Edited by F1natic on Saturday 31st August 08:49
Caddyshack said:
Agreed, make it a long tail.
I think the reason why people are suggesting a stock engine is to remove an area of easy failure to the project...just getting the body panels, suspension and doors is challenge enough and we want it to succeed.
AMG v12 or supercharged v8 would be on my radar too.
Thanks for the suggestion - I am intending for this car to be road focused, and I have always been impressed by the compact nature of the road car. Used to study the one in Park Lane in detail and the longtails at Goodwood FOS. If the chassis development is successful over a long term (a few years of heavy use) then a NZ landspeed attempt (currently 220 mph) using a longtail might be a very sensible modification - just don't tell my wife. However the longtail would not be good for parking in the city! I think the reason why people are suggesting a stock engine is to remove an area of easy failure to the project...just getting the body panels, suspension and doors is challenge enough and we want it to succeed.
AMG v12 or supercharged v8 would be on my radar too.
My commute is curently about 80 minutes each way (with a very small gravel section, great fun) so the dual engine setup allows me to suspend 6 cylinders by locking out one clutch - this reduces heat load on the cooling system while sitting in slow traffic at the expense of a clutch release bearing life. The engines I am using have variable cylinder management so could even drop to 3 cylinders while trickling along, however the engine sounds like its running over a rumble strip in that mode which is too irritating. Also the original Mclaren F1 development was going to use a Honda engine, so I get satisfaction out of using them in my car.
Big engine torque and wide rear tires tend to blow clutches and transmissions - depending on your driving style of course. I am fairly set on the C6 setup becuse its so well developed at the 500+Hp rating - and thus I am very determined to try the transverse engine setup to suit it. The pinions and crown wheel are really stout items designed using the equations found in the Manual gearbox design book by Alec Stokes (ISBN 0 7506 0417 4). That was a few years of my life I won't be able to get back!
For the last 6 months during my morning commute into work I have been stopping at my local supermarket and collecting a couple of big packing boxes from the nightstack = free materials. I am intending to make a plug for the doors that is finally profiled by the router. I made a small test block by gluing sheets of corrogated cardboard together with PVA.
Using a 25mm diameter Kutzall ball spinning at insane rpm (https://kutzall.com/collections/sphere/ ... -1-4-shaft) I cut a test profile into the block. It looks workable, the body filler final skin of the plug should bond nicely to it - will cover the test piece this weekend.
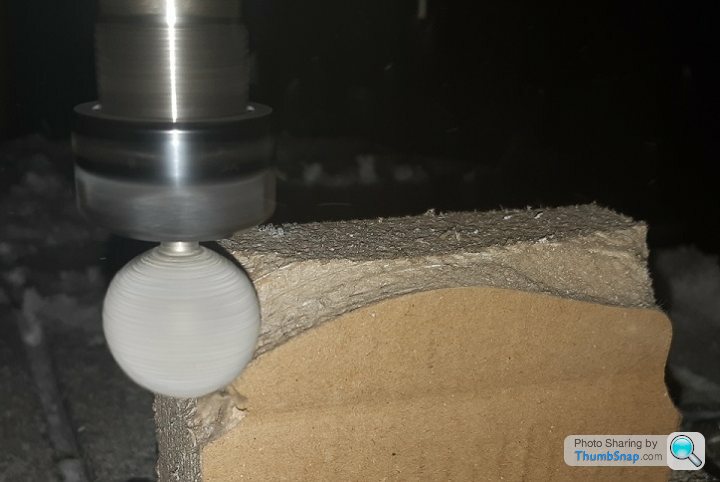
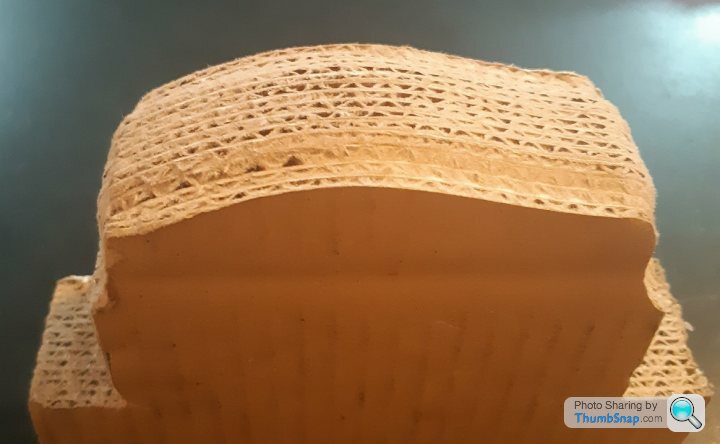
May not look like much, but it is proof of concept - I really don't want to machine big blocks of urethane or polystyrene foam.
Using a 25mm diameter Kutzall ball spinning at insane rpm (https://kutzall.com/collections/sphere/ ... -1-4-shaft) I cut a test profile into the block. It looks workable, the body filler final skin of the plug should bond nicely to it - will cover the test piece this weekend.
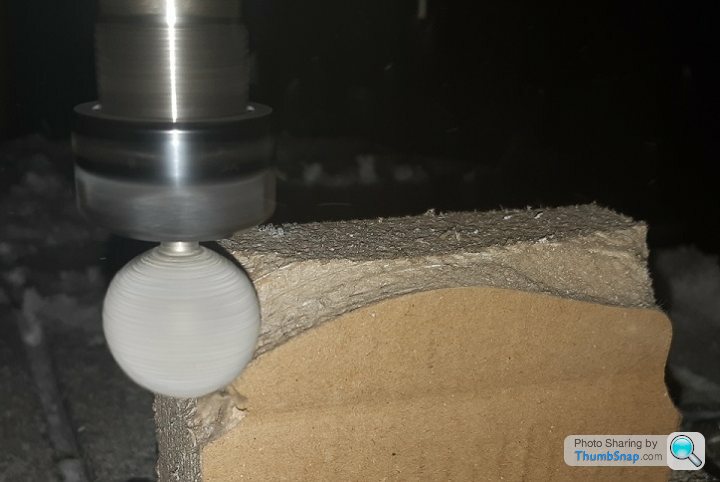
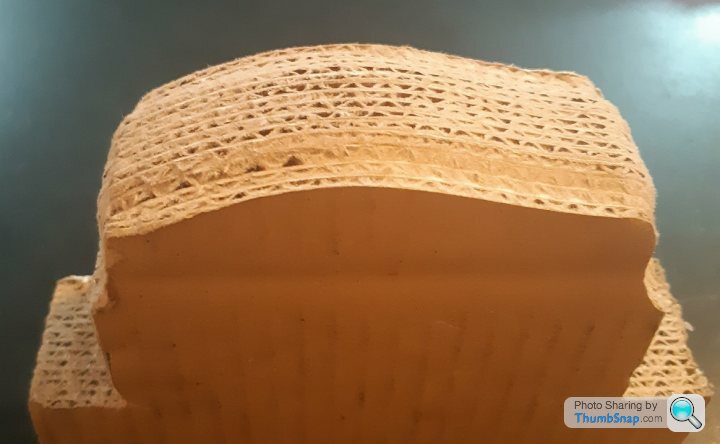
May not look like much, but it is proof of concept - I really don't want to machine big blocks of urethane or polystyrene foam.
Hi, good question. I was initially considering bolting both engines to a common output cog, but running one engine backwards messes with its cam tensioner. So to make as much of the setup factory stock they both spin anticlockwise looking at the flywheel. Since the drive runs through bevel gears and they oppose each other, they twist the transaxle input shaft clockwise as per the corvette installation.
Gassing Station | Readers' Cars | Top of Page | What's New | My Stuff