Aixam microcar - with a bike engine!
Discussion
This is actually an in-progress project but if retrospective (for a bit) build diaries are in fashion and you'll entertain my attempt at a bit of writing then ill happily share the build diary for this 
Rewind 18 months. Its my birthday, its late, and ive got some worryingly persuasive friends helping me browse ebay. Cars motorcycles and vehicles. Search term is 'project'. Many a vehicle was considered (im told) the selection process was logical and considered (unlikely) and justification of purchase absolutely watertight (ahahaha). Bidding ended at a 'nah we'll be fine i wont win it anyway' 32 pounds.
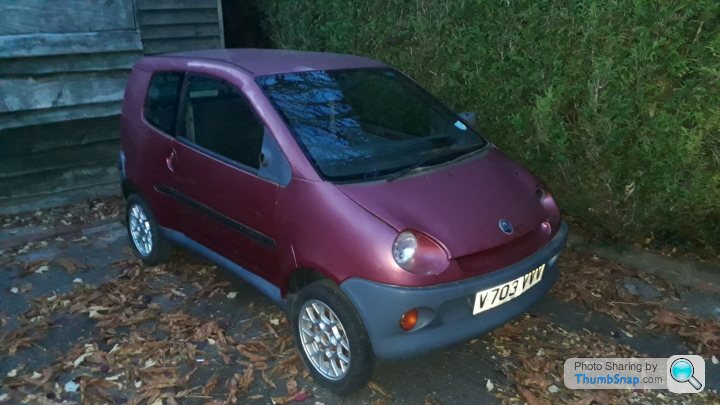
What the hell is it? I too found myself asking.
Its an aixam 500 microcar. All plastic body with steel subframes. They came with an air cooled 2 cylinder kubota diesel engine making (BRACE YOURSELVES) 5hp, and driving the front wheels via a CVT transmission with i think a centrifugal clutch. Kind of like a moped, except front wheel drive, and even more embarassing. 50mph top speed. 400kg and 145 width tyres. Now now ladies, form a queue.

Anyone recognise the van? :-)
It gets sillier. Once i'd arranged delivery 2 microcars turned up - If i'd read the listing i'd have known that was going to happen. One an almost rolling shell and one a not at all rolling shell full of parts. It turns out i was getting 'the parts to make a rolling shell' and not 'a rolling shell'. I'd have know this if i was capable of reading while bidding.
Bear in mind i said rolling shell. Not 'complete car'. Originally these cars came with the little kubota diesel engine that is in diggers/cement mixers/plant machinery. But these are worth money. I think whats happening with these cars is the guys are buying the wrecks, flogging the engine and chucking the rest of the car back on ebay. Which they have to do, because you cant weigh the car in (its plastic) and you cant take it down the tip (its a car). So it looks like im committed to this build, like it or not...
Some photos of my 'non-driveline' assembly....
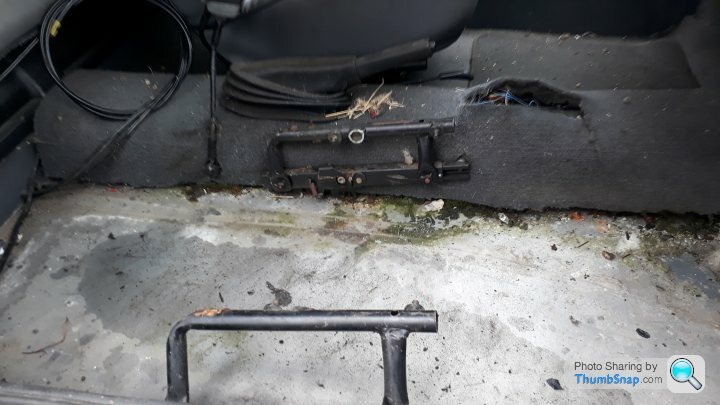
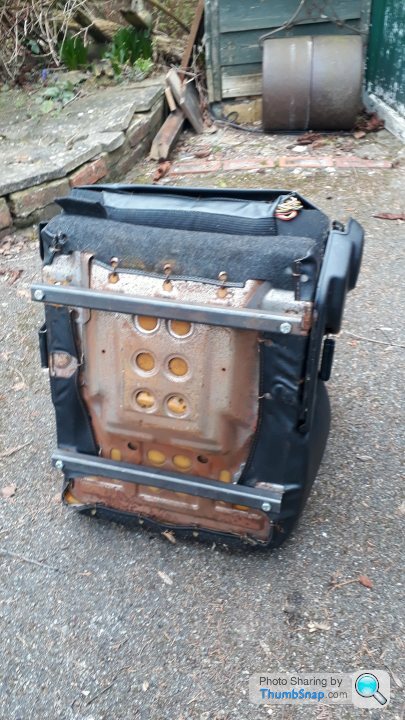
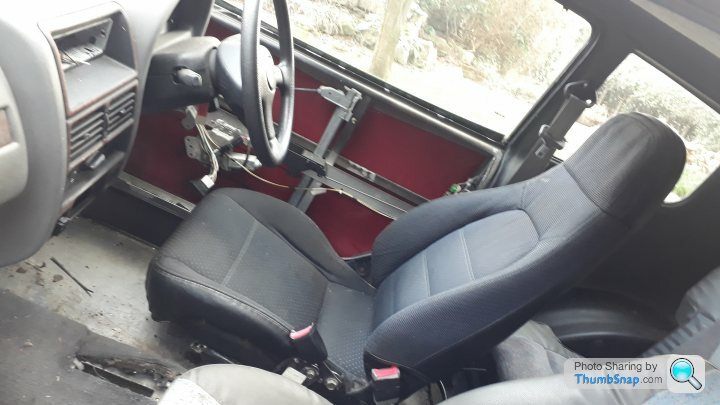
MX5 seat welded in
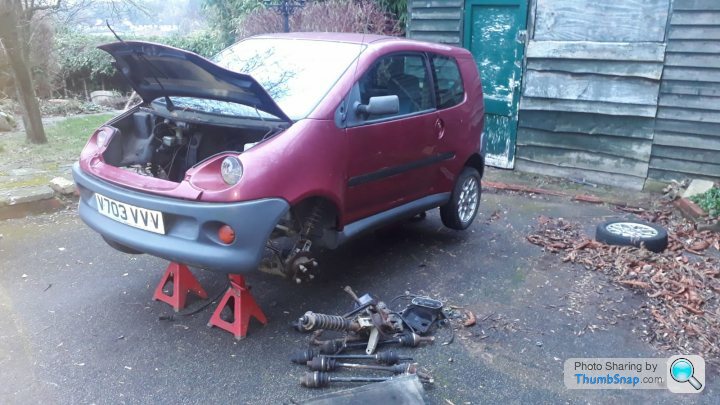
Mixing and matching suspension components
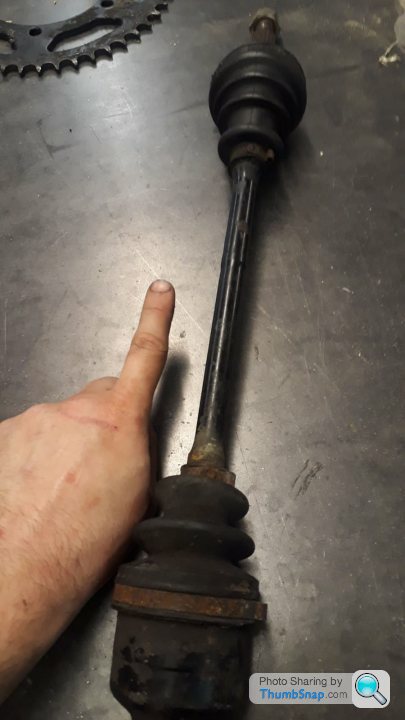
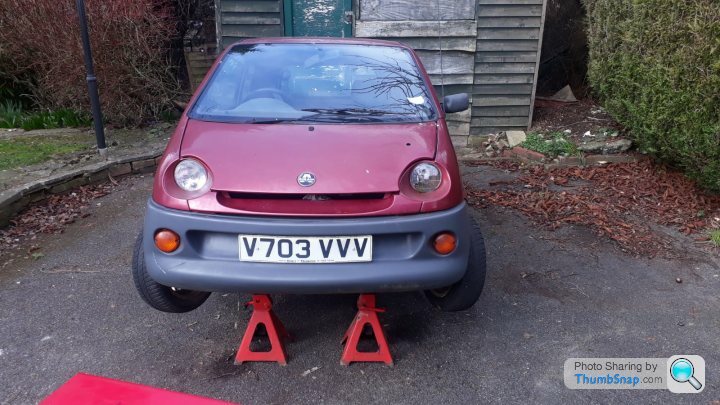
But mixing and matching only gets you so far. Not sure the alignment guys are adjusting that out...

Sorted the steering silliness by cutting and extending the track rods (i fully welded them later dont worry). Also the only driveshafts that fit were the longest ones... But at least i now have a truly rolling shell.
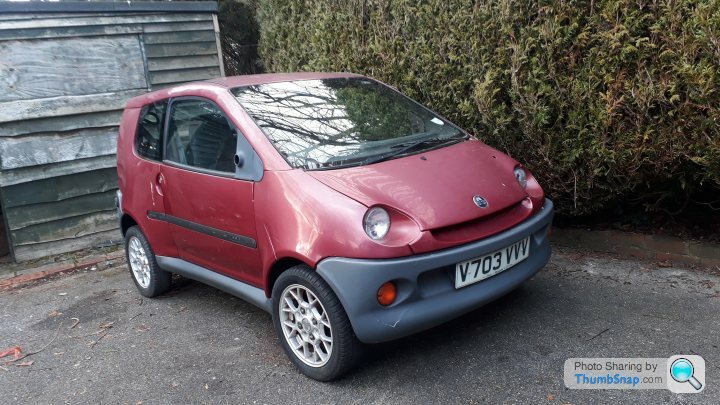
So by this point it was basically complete less its powerplant. Rolling shell with lights wipers interior brakes and electrics (and a drivers mirror) So all we need is an engine.... :-)

Rewind 18 months. Its my birthday, its late, and ive got some worryingly persuasive friends helping me browse ebay. Cars motorcycles and vehicles. Search term is 'project'. Many a vehicle was considered (im told) the selection process was logical and considered (unlikely) and justification of purchase absolutely watertight (ahahaha). Bidding ended at a 'nah we'll be fine i wont win it anyway' 32 pounds.
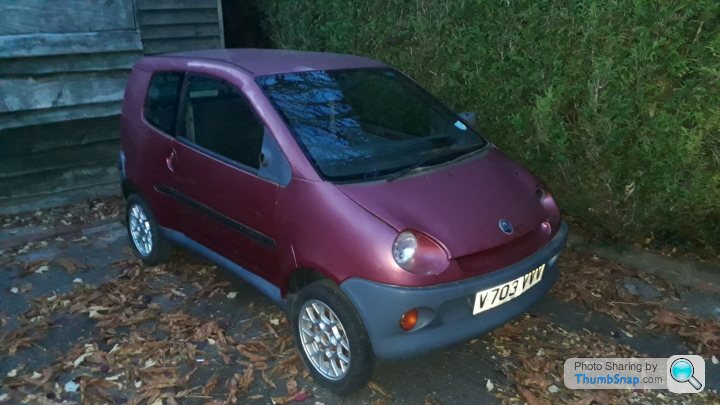
What the hell is it? I too found myself asking.
Its an aixam 500 microcar. All plastic body with steel subframes. They came with an air cooled 2 cylinder kubota diesel engine making (BRACE YOURSELVES) 5hp, and driving the front wheels via a CVT transmission with i think a centrifugal clutch. Kind of like a moped, except front wheel drive, and even more embarassing. 50mph top speed. 400kg and 145 width tyres. Now now ladies, form a queue.

Anyone recognise the van? :-)
It gets sillier. Once i'd arranged delivery 2 microcars turned up - If i'd read the listing i'd have known that was going to happen. One an almost rolling shell and one a not at all rolling shell full of parts. It turns out i was getting 'the parts to make a rolling shell' and not 'a rolling shell'. I'd have know this if i was capable of reading while bidding.
Bear in mind i said rolling shell. Not 'complete car'. Originally these cars came with the little kubota diesel engine that is in diggers/cement mixers/plant machinery. But these are worth money. I think whats happening with these cars is the guys are buying the wrecks, flogging the engine and chucking the rest of the car back on ebay. Which they have to do, because you cant weigh the car in (its plastic) and you cant take it down the tip (its a car). So it looks like im committed to this build, like it or not...
Some photos of my 'non-driveline' assembly....
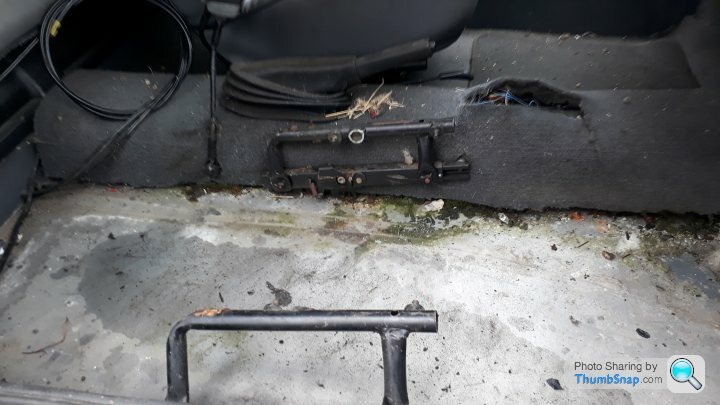
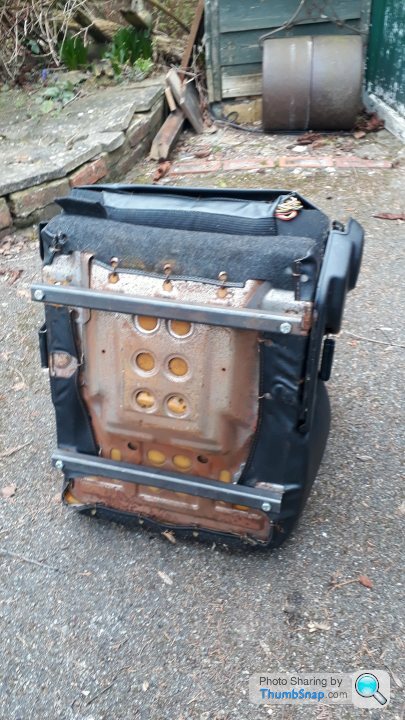
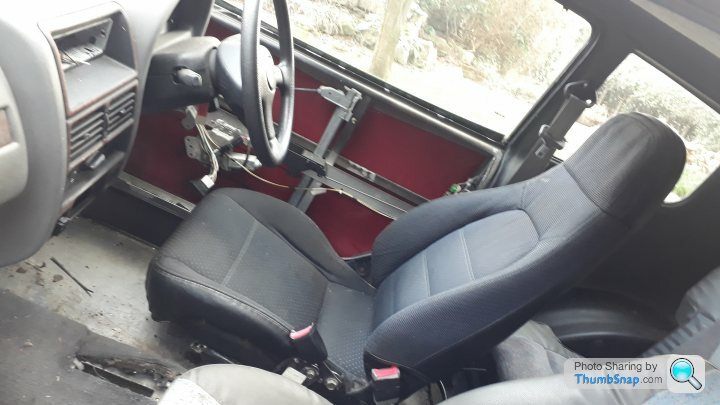
MX5 seat welded in
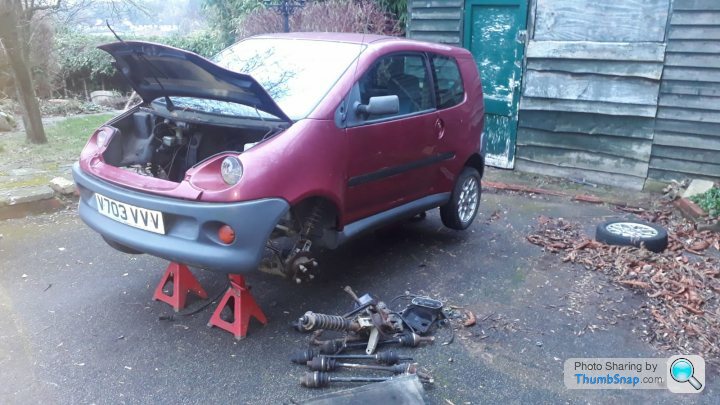
Mixing and matching suspension components
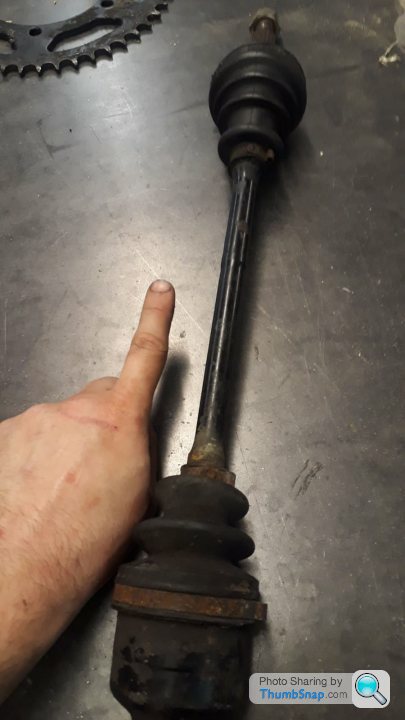
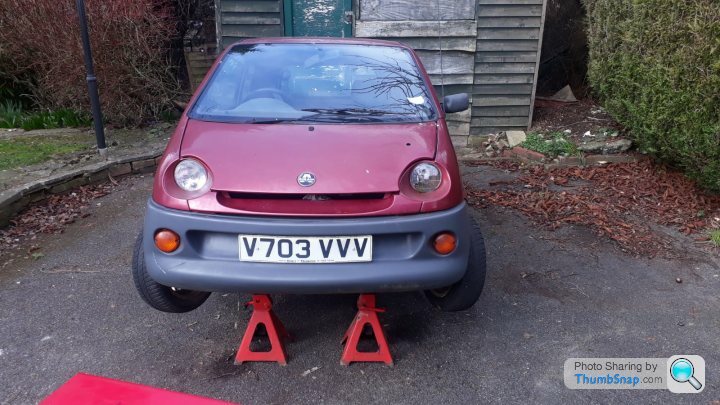
But mixing and matching only gets you so far. Not sure the alignment guys are adjusting that out...

Sorted the steering silliness by cutting and extending the track rods (i fully welded them later dont worry). Also the only driveshafts that fit were the longest ones... But at least i now have a truly rolling shell.
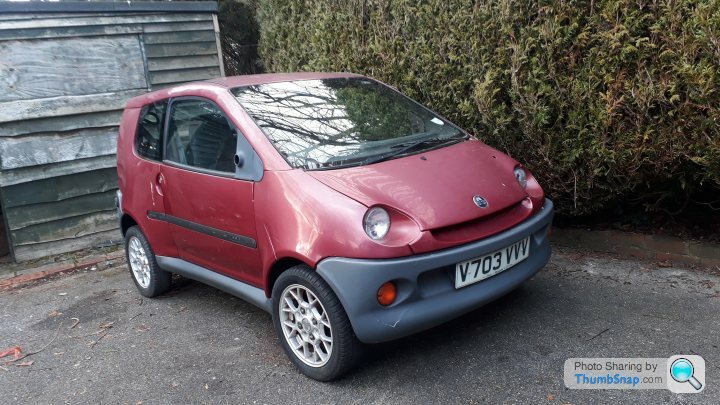
So by this point it was basically complete less its powerplant. Rolling shell with lights wipers interior brakes and electrics (and a drivers mirror) So all we need is an engine.... :-)
Edited by sparkybean on Wednesday 8th January 22:44
So obviously by the thread title the engine choice is a given but we did consider a few options:
Put the original engine back in - p
s offfffffff
Front drive hatchback engine and subframe in the back! - Too wide, dont want the wide arch silliness
Reliant rear axle and some longditudinal engine/box - Could do, but not really tempted by the rear suspension silliness or having the rear seat passengers changing gear for me
Electric motor! (seriously considered, always wanted to build an electric car, but im not made of money...)
A series - Feasable option.
Bike engine driving the front wheels - Chains/sprockets/bearings nightmare
We seriously considered the a-series. The temptation to plonk down a grand on the drivetrain from a mini or metro wasnt exactly nagging at me, despite the convienence - Weld the engine mounts to the steel front subframe, bodge 2 halves of driveshafts to the 2 others, and call it done. Tempting.
In the end though the bike engine plan won out for a pretty simple reason - despite having recently newfound access to a lathe and owning a mill (cough pillar drill on steroids) id not found a proper machining project to sink my teeth into yet - and i find stuff tends to get learned real quick if you throw yourself into the deep end with an objective. This was going to be a 'can i actually machine stuff' project. So....
Friends back round, get the beers in again, category motorcycles, cheapest first, buy it now only
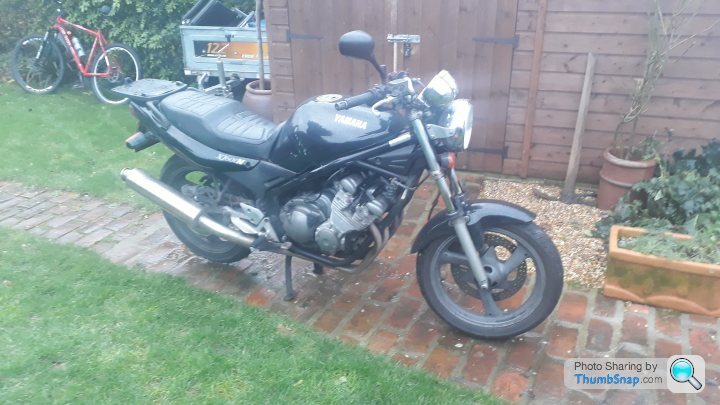
Yamaha 600 diversion - 70hp. This might be a classic motorcycle of absolute exquisite taste and class, or it could be an absolute eyesore that disgusts even the keenest yamaha fan. I have no idea, I know nothing of bikes. All i know is that it ran well when i bought it (apart from a bit of cam chain clatter, common problem apparently) and that 12krpm of sequentially shifted chain driven aluminium engine and gearbox silliness is what this plastic pile of excrement microcar really needs. I bought the whole bike for 300 quid. Perfect! Then spent the next month stripping and selling all the parts i didnt need - mainly to make some space, which paid for the bike, car, delivery of the car and the chocolates to buy off the neighbours' want to complain to someone. Score!
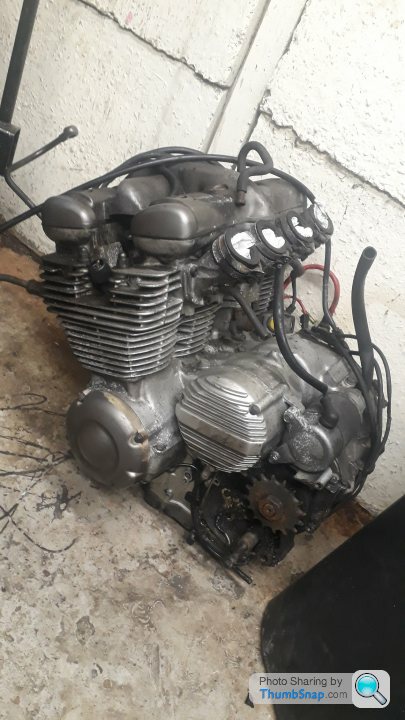
Now we just have to cram the 2 halves together....
Put the original engine back in - p

Front drive hatchback engine and subframe in the back! - Too wide, dont want the wide arch silliness
Reliant rear axle and some longditudinal engine/box - Could do, but not really tempted by the rear suspension silliness or having the rear seat passengers changing gear for me
Electric motor! (seriously considered, always wanted to build an electric car, but im not made of money...)
A series - Feasable option.
Bike engine driving the front wheels - Chains/sprockets/bearings nightmare
We seriously considered the a-series. The temptation to plonk down a grand on the drivetrain from a mini or metro wasnt exactly nagging at me, despite the convienence - Weld the engine mounts to the steel front subframe, bodge 2 halves of driveshafts to the 2 others, and call it done. Tempting.
In the end though the bike engine plan won out for a pretty simple reason - despite having recently newfound access to a lathe and owning a mill (cough pillar drill on steroids) id not found a proper machining project to sink my teeth into yet - and i find stuff tends to get learned real quick if you throw yourself into the deep end with an objective. This was going to be a 'can i actually machine stuff' project. So....
Friends back round, get the beers in again, category motorcycles, cheapest first, buy it now only
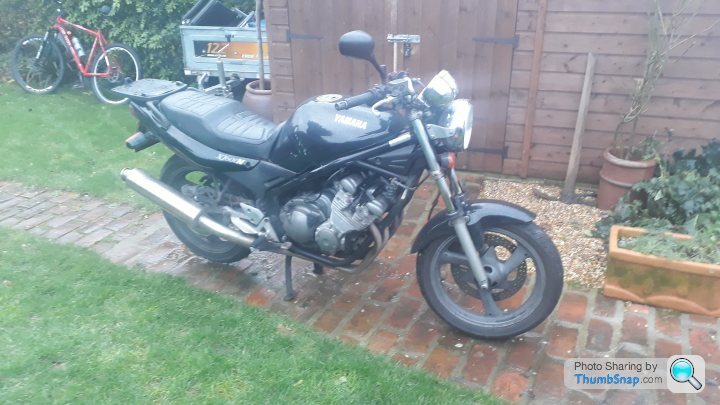
Yamaha 600 diversion - 70hp. This might be a classic motorcycle of absolute exquisite taste and class, or it could be an absolute eyesore that disgusts even the keenest yamaha fan. I have no idea, I know nothing of bikes. All i know is that it ran well when i bought it (apart from a bit of cam chain clatter, common problem apparently) and that 12krpm of sequentially shifted chain driven aluminium engine and gearbox silliness is what this plastic pile of excrement microcar really needs. I bought the whole bike for 300 quid. Perfect! Then spent the next month stripping and selling all the parts i didnt need - mainly to make some space, which paid for the bike, car, delivery of the car and the chocolates to buy off the neighbours' want to complain to someone. Score!
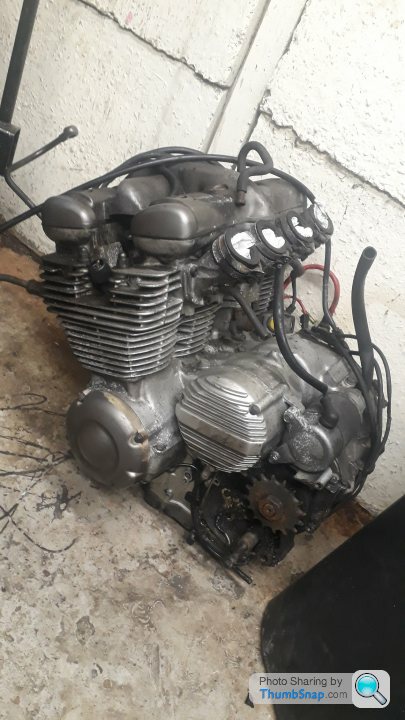
Now we just have to cram the 2 halves together....
Aha right. Thats what im hoping for, i think 5hp at 400kg going up to 70hp should be enough of a riot. 175hp/ton isnt slow, and the skinny tyres should make it silly enough to drive.
Of the 18 months or so of build thread timing, getting this far is half of it. Plans, thinking time, fair amount of head-in-hands 'what have i done why do i do this to myself' related self reflection, and general heel kicking fills in the time between actually working on the thing.
Machining photos coming...
Of the 18 months or so of build thread timing, getting this far is half of it. Plans, thinking time, fair amount of head-in-hands 'what have i done why do i do this to myself' related self reflection, and general heel kicking fills in the time between actually working on the thing.
Machining photos coming...
The yamaha is no great loss. Since buying it i learned it definitley falls into the 'not so exotic' category. It had a lot wrong with it and some review mag called it 'the vauxhall astra diesel' of the motorcycle world.
A litre bike would have been great but they all cost actual money!
A litre bike would have been great but they all cost actual money!
Shadow R1 said:
The oil sump will need some form of baffling.
Bikes lean when going round corners, cars don't.
Many engineering challenges to fitting any bike engine.
Your power figure is a tad on the high side, if it gives 50bhp your doing well.
Good luck with this and keep us updated.
I've seen between 50-80 on the xj, depending on spec. Wasnt sure, took a middle guess!Bikes lean when going round corners, cars don't.
Many engineering challenges to fitting any bike engine.
Your power figure is a tad on the high side, if it gives 50bhp your doing well.
Good luck with this and keep us updated.

Its oil cooled so i think i'll fit a pressure sensor on the cooler to keep an eye out for exaclty this. Anyway what's to say my car wont lean when cornering, have you seen how thin and tall this thing is! (yes i know it leans the wrong way lol)
So pretty much immediatley there are problems with the bike engine plan. The aixam engine bay is short and tall, whereas the bike engine is low and needs a lot of length for the chain to exit out the back of the gearbox (toward the rear wheel of the motorbike)
The chain can't come downward, as there is a lot of very important sump gearbox gear selector looking stuff in the way. Extending the sprocket outward from the engine (somehow) to clear the sump is an option - but after that the 2 driveshafts will need to be shortened to some comically short length in order to let the engine sit central in the bay. Im non-negotiably not having the engine off to one side.
A test fit with the crane confirmed this.

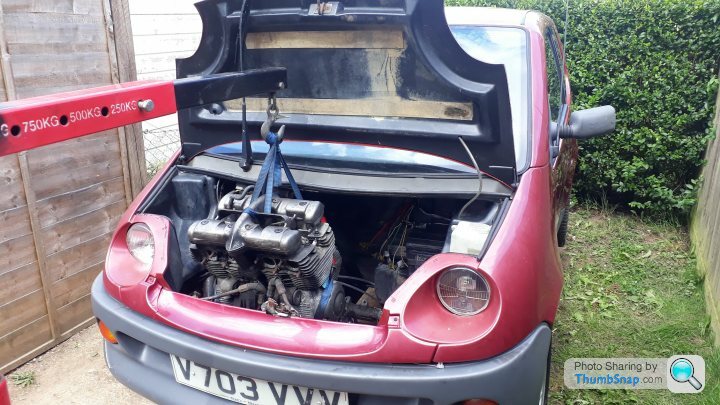
I mean it does 'fit' in the engine bay so thats a good start. But theres no way round the fact that an intermediate shaft is the best way to do things. Take the chain drive out the back of the engine to a sprocket on a driveshaft, across to another sprocket and down to between the 2 driveshafts of the car. See the finely cadded technical drawings...

By this point it was becoming abundantly clear that the exact placement of the engine was uncertain, until the lower driveshaft got sorted.
Reposting an earlier pic:

Without knowing where the sprocket was going to end up the engine's position would be uncertain. This car gets built from the bottom up.... So. Job 1 - make something that joins a sprocket to these 2 driveshafts. FIRE UP THE LATHE
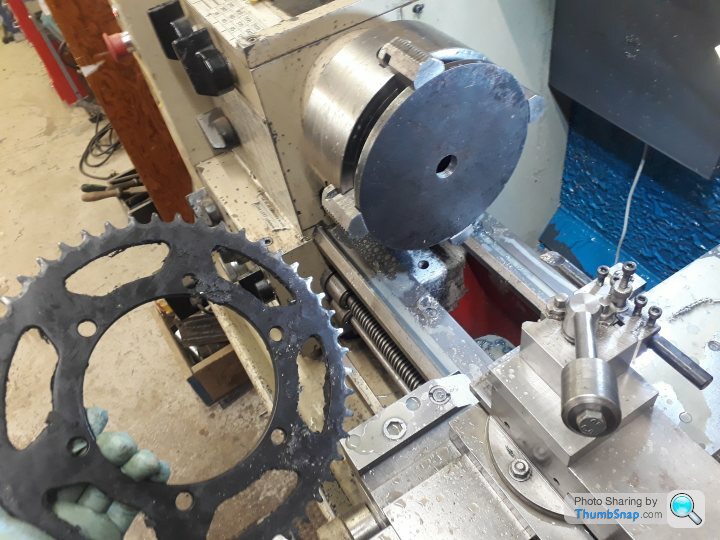
Yamaha back sprocket (yes, its worn out. I am cheap) Mild steel metal disc for a sprocket carrier

Turned a step in the sprocket carrier
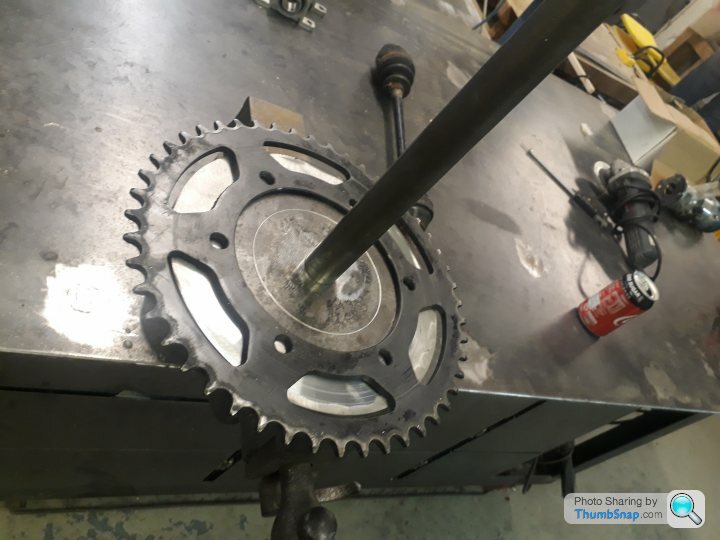
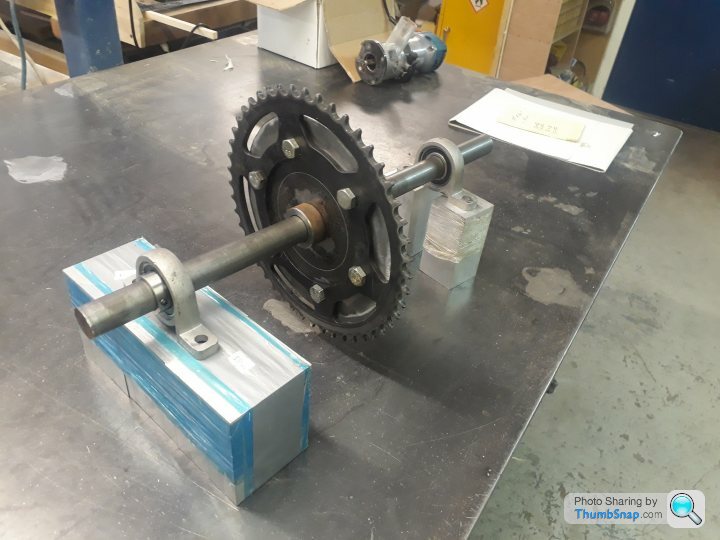
You ever buy something on ebay and not check the dimensions? I did that once and ended up with a comedy size universal tv remote for the elderly and blind. I also ended up with these puny bearings. Almost got laughed out the shop showing up with those...
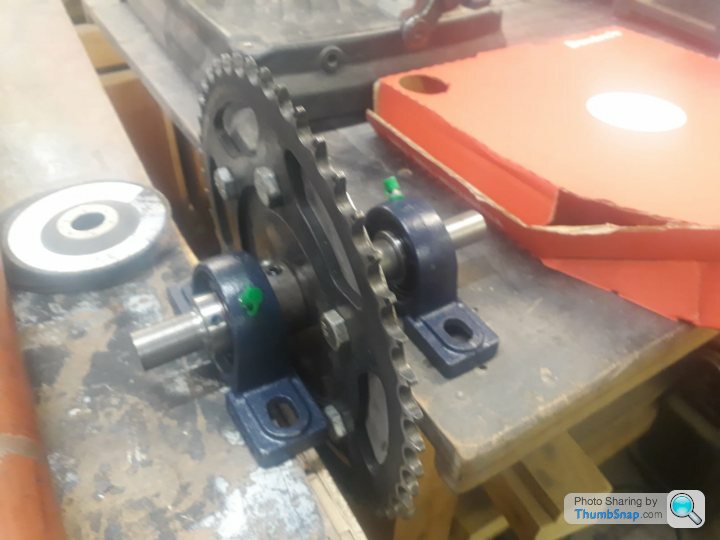

Better. Driveshaft shortened to length, proper pillow block bearings, all fits. Back home for a test fit....

Something like that - right? Use your imagination - a bit of steel box section, squirts with the mig gun, tada we have our main centre driveshaft sorted.
I can hear the comments about 'welded front diff?!' already...
The chain can't come downward, as there is a lot of very important sump gearbox gear selector looking stuff in the way. Extending the sprocket outward from the engine (somehow) to clear the sump is an option - but after that the 2 driveshafts will need to be shortened to some comically short length in order to let the engine sit central in the bay. Im non-negotiably not having the engine off to one side.
A test fit with the crane confirmed this.

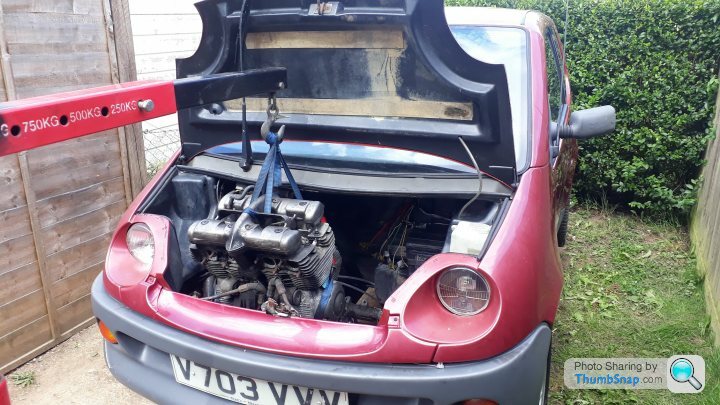
I mean it does 'fit' in the engine bay so thats a good start. But theres no way round the fact that an intermediate shaft is the best way to do things. Take the chain drive out the back of the engine to a sprocket on a driveshaft, across to another sprocket and down to between the 2 driveshafts of the car. See the finely cadded technical drawings...

By this point it was becoming abundantly clear that the exact placement of the engine was uncertain, until the lower driveshaft got sorted.
Reposting an earlier pic:

Without knowing where the sprocket was going to end up the engine's position would be uncertain. This car gets built from the bottom up.... So. Job 1 - make something that joins a sprocket to these 2 driveshafts. FIRE UP THE LATHE
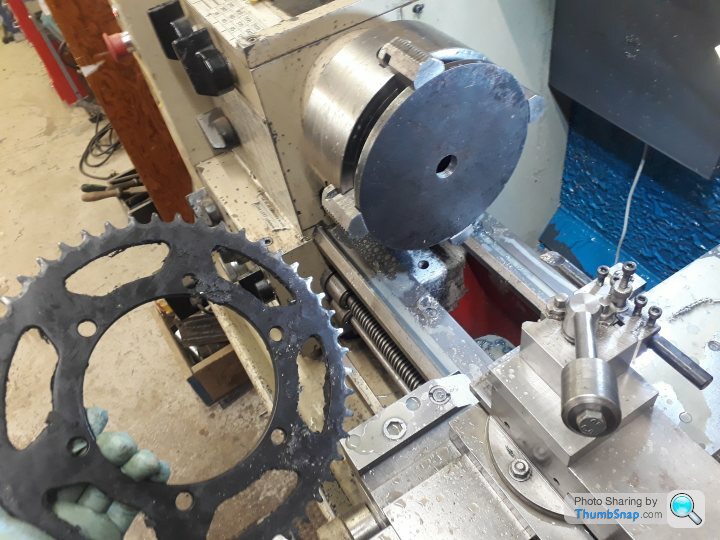
Yamaha back sprocket (yes, its worn out. I am cheap) Mild steel metal disc for a sprocket carrier

Turned a step in the sprocket carrier
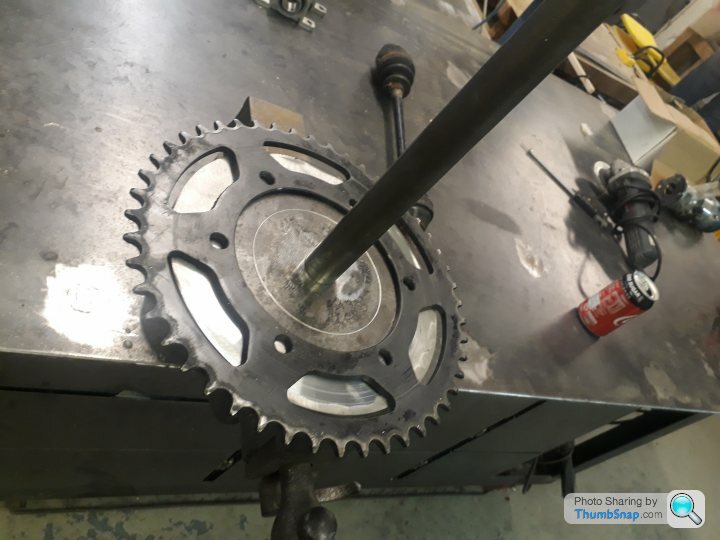
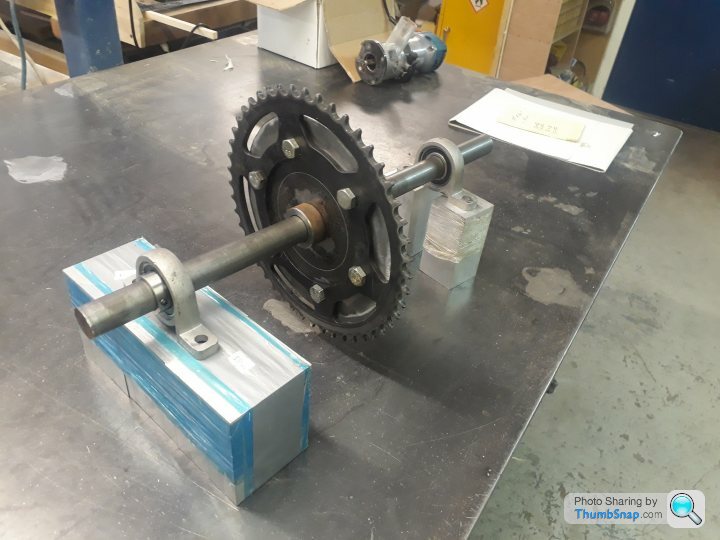
You ever buy something on ebay and not check the dimensions? I did that once and ended up with a comedy size universal tv remote for the elderly and blind. I also ended up with these puny bearings. Almost got laughed out the shop showing up with those...
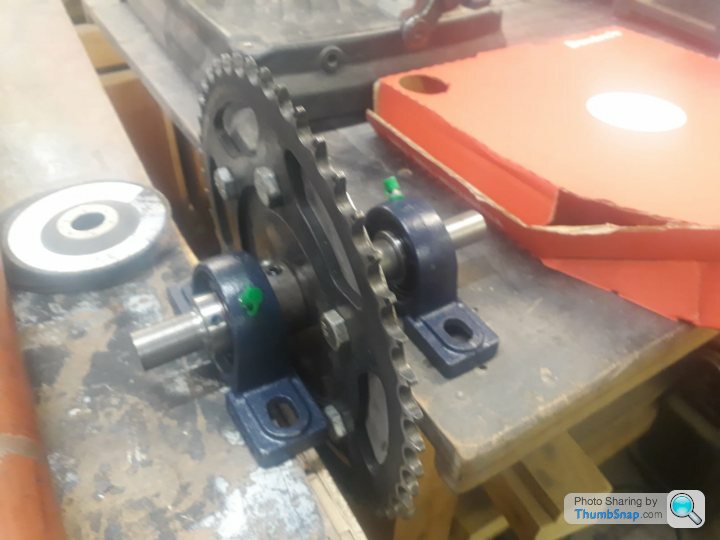

Better. Driveshaft shortened to length, proper pillow block bearings, all fits. Back home for a test fit....

Something like that - right? Use your imagination - a bit of steel box section, squirts with the mig gun, tada we have our main centre driveshaft sorted.
I can hear the comments about 'welded front diff?!' already...
Tyre Smoke said:
Now if it was rear wheel drive, it would pull a useful wheelie.
This is mad. I can't see that sprocket set up lasting more than five minutes.
Its about to get much worse, dont worry. Though i do agree that if it was rwd being able to wheelie would be useful, should i require.This is mad. I can't see that sprocket set up lasting more than five minutes.
Hark! Updates!
Finishing off the centre driveshaft was a f
king heap of f
king
What constantly surprises me with machining is how much time goes into setting up the part you are cutting in the mill, vs actually cutting the thing. Setup time on this part was 4 hours which included buying, modding and generally persuading into use a rotary table (that looks very homemade, thanks ebay). This was a couple of hundred quid - but i feel justified in not including this in the build cost because its a useful tool for loads of metalbashing jobs and ive always wanted one!

Im centering the shaft in the independent 4 jaw rotary table in this shot, in order to cut splines in the shaft. Except noone in their right mind would ever get and endmill near that diameter, the stickout is silly. Cutting a spline on this would be like trying to shorten a diving board with a pole mounted chainsaw. I had to build a steady, at exactly (no such thing in the metalbashing world) the same height as the rotary table centreline.

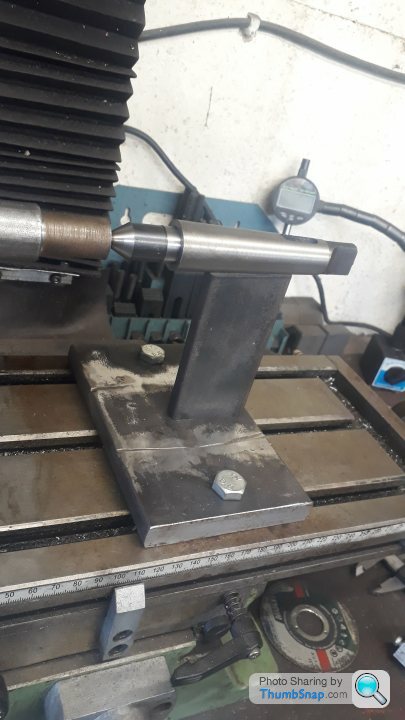
As i said - all in the setup.

To cut the splines i used this 45 degree tipped endmill. (which happens in this photo to have a chunk taken out of it, but luckily my camera forgot its reading glasses so you can't see that). The female spline in the inner CV joint seems to have a nearly 90deg V to the spline so this will do. Good enough for who its for.
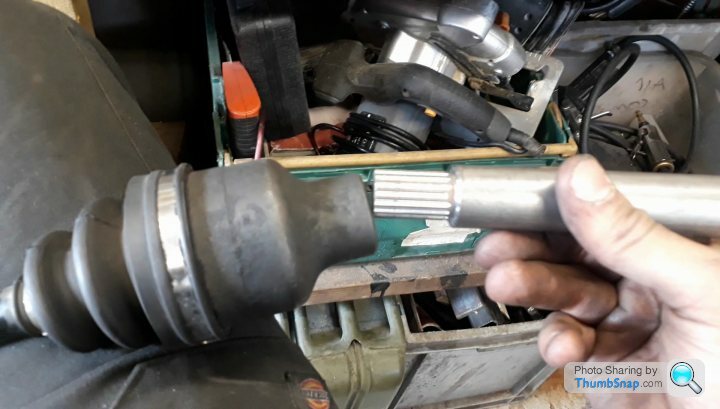
Horrendous i think you'll agree. I am not a machinist, i just pretend. To mill this i moved the bit down the shaft, back, and rotated the table 20 degrees (because 18 spline shaft). Took 2 rotations to get to depth.
To finish this off, i cut 2 keyways (180 deg apart) in the centreshaft and broached a couple of respective keyways through the sprocket carrier and shaft collars. Turn the mig to 11, dollop on the weld.

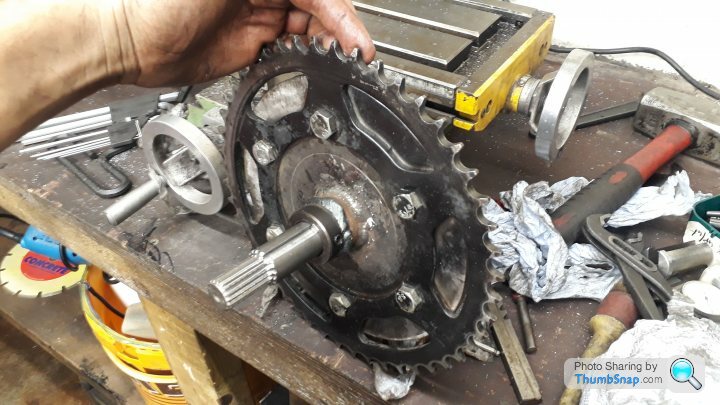

Fits! (unwelded unbroached continuity error, noone will notice promise)
Im somewhat concerned about the strength of the splines - this is just unhardened mild steel, without any of the clever flavourings that car manufactures spec for the material to improve strength/hardness/ductility/cost/sex appeal. But that said we are only dealing with a double digit hp and skinny decade old tyres. I think ill chance it.
I couldnt resist mocking the engine back up and seeing where that got us...
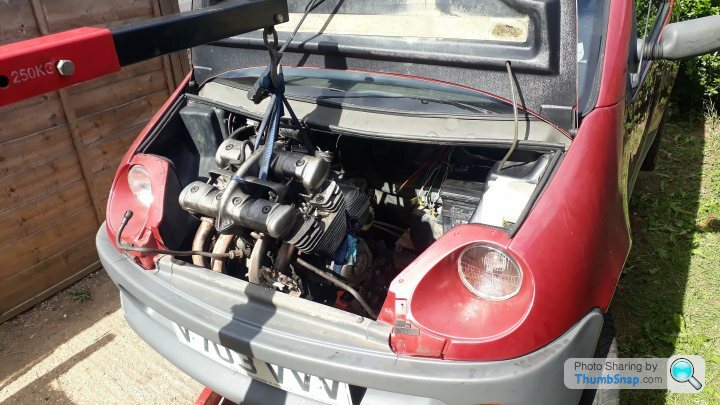

So far so good....




The exhaust fits (will need to be snaked through whatever structure i build to hold the drivetrain in) but the rest looks all a bit cosy. You can see the carbs arent going to fit - the scuttle is in the way. At this point the way i see it the options are either move the engine (to where?) or perhaps the intake manifold can be flipped over to bring the carbs to somewhere under the windscreen. This will probably wreck the intake flow path and i've no idea if these carbs are directional (its a bike, surely they can deal with a bit of fuel slosh in the bowls ect). To be considered another time.
Theres also this issue to ignore:
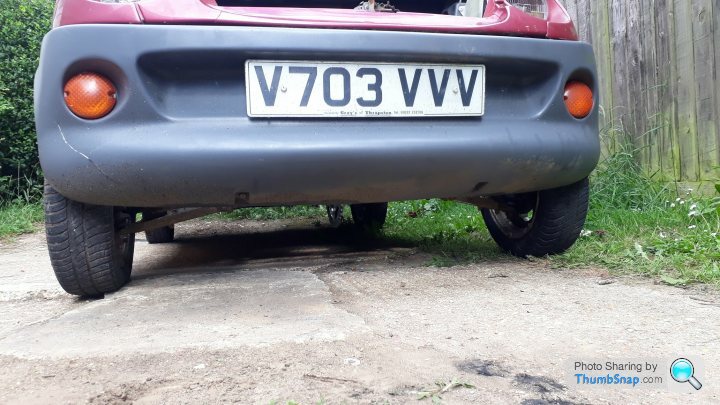
Update enough for now - more progress soon.
Finishing off the centre driveshaft was a f




Im centering the shaft in the independent 4 jaw rotary table in this shot, in order to cut splines in the shaft. Except noone in their right mind would ever get and endmill near that diameter, the stickout is silly. Cutting a spline on this would be like trying to shorten a diving board with a pole mounted chainsaw. I had to build a steady, at exactly (no such thing in the metalbashing world) the same height as the rotary table centreline.

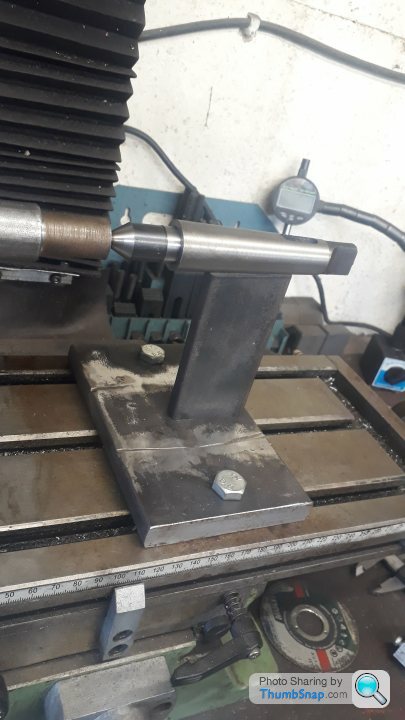
As i said - all in the setup.

To cut the splines i used this 45 degree tipped endmill. (which happens in this photo to have a chunk taken out of it, but luckily my camera forgot its reading glasses so you can't see that). The female spline in the inner CV joint seems to have a nearly 90deg V to the spline so this will do. Good enough for who its for.
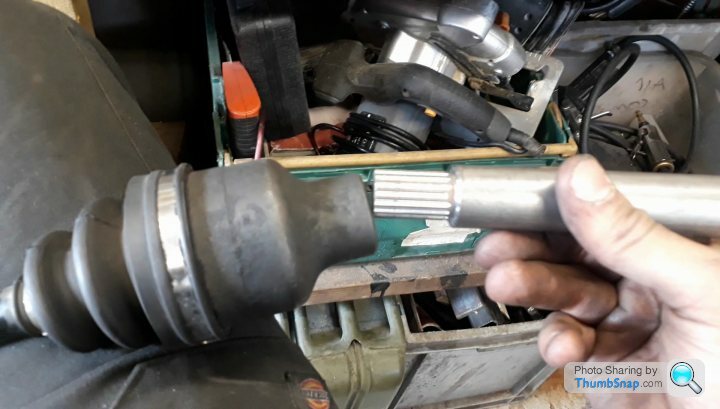
Horrendous i think you'll agree. I am not a machinist, i just pretend. To mill this i moved the bit down the shaft, back, and rotated the table 20 degrees (because 18 spline shaft). Took 2 rotations to get to depth.
To finish this off, i cut 2 keyways (180 deg apart) in the centreshaft and broached a couple of respective keyways through the sprocket carrier and shaft collars. Turn the mig to 11, dollop on the weld.

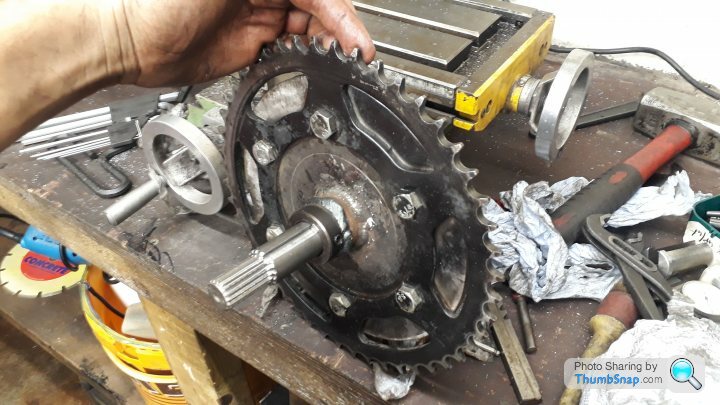

Fits! (unwelded unbroached continuity error, noone will notice promise)
Im somewhat concerned about the strength of the splines - this is just unhardened mild steel, without any of the clever flavourings that car manufactures spec for the material to improve strength/hardness/ductility/cost/sex appeal. But that said we are only dealing with a double digit hp and skinny decade old tyres. I think ill chance it.
I couldnt resist mocking the engine back up and seeing where that got us...
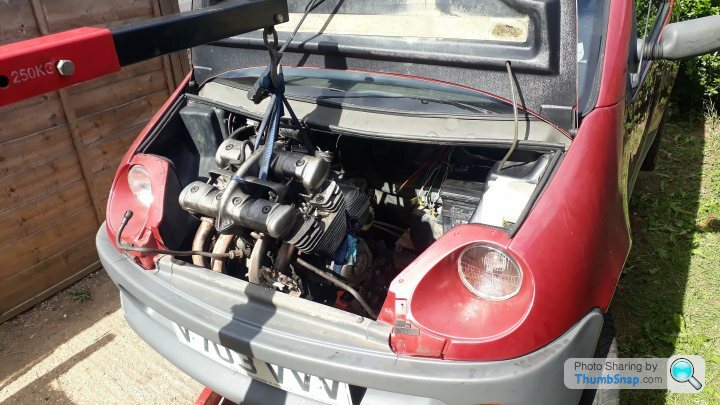

So far so good....




The exhaust fits (will need to be snaked through whatever structure i build to hold the drivetrain in) but the rest looks all a bit cosy. You can see the carbs arent going to fit - the scuttle is in the way. At this point the way i see it the options are either move the engine (to where?) or perhaps the intake manifold can be flipped over to bring the carbs to somewhere under the windscreen. This will probably wreck the intake flow path and i've no idea if these carbs are directional (its a bike, surely they can deal with a bit of fuel slosh in the bowls ect). To be considered another time.
Theres also this issue to ignore:
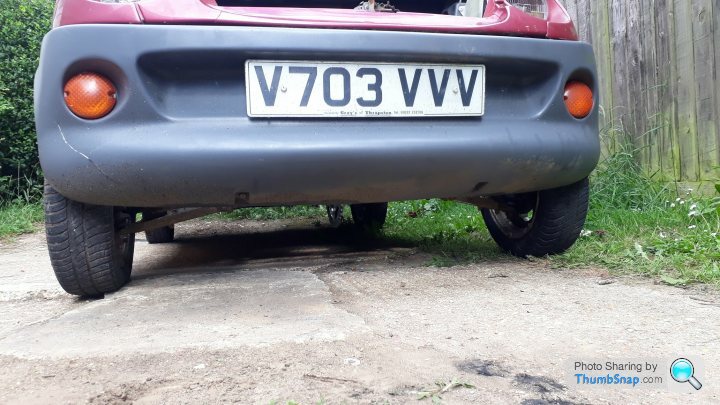
Update enough for now - more progress soon.
Edited by sparkybean on Saturday 18th January 20:08
eliot said:
So you don’t intend to fit a diff?
I think its a bit late for that! Honestly i didnt want the extra engineering effort or significant added cost of buying an off-the-shelf unit.http://racetrackdriving.com/tech/fwd-welded-diff/
TLDR: Power oversteer in a front wheel drive (if it doesn't roll first), says this man.
If you are expecting a build with a refined smooth tuned handling setup, then i think youre going to be dissapointed!
I did read that yes. I fully accept that slow speed manouvering will be horrible.
High speed manouvering will also be horrible, as well as medium speed manouvering.
In fact even in a straight line, without the manouvering, it will be horrible. Actually even stood still, not sat in it, not looking at it, it is horrible. No normal person in their right mind would ever want this. This is automotive build equivilant of a s
tpost and i am having a hilarious time of it.
This is not your airconditioned M5 (clearly)
Maybe i should start taking bets for 'distance until mechanical failure'
So far i have had;
Instantly
5 minutes
As soon as you turn away from dead ahead
Any raises? Can i get an hour out of it?
High speed manouvering will also be horrible, as well as medium speed manouvering.
In fact even in a straight line, without the manouvering, it will be horrible. Actually even stood still, not sat in it, not looking at it, it is horrible. No normal person in their right mind would ever want this. This is automotive build equivilant of a s

This is not your airconditioned M5 (clearly)
Maybe i should start taking bets for 'distance until mechanical failure'
So far i have had;
Instantly
5 minutes
As soon as you turn away from dead ahead
Any raises? Can i get an hour out of it?
Edited by sparkybean on Monday 13th January 10:19
Munter said:
Whatever happens. You are going to make sure we have video from multiple angles right? ??
Yes. There will be video :-) That way all the naysayers revelling in disgust get their fill when it blows up in some comically short amount of time.With a bit of luck i'll have photos of that lower driveshaft mounted on some box section by tomorrow, and then the games of turning an intermediate shaft, and making it fit, start.
Edited by sparkybean on Monday 13th January 10:15
Lets keep the ball rolling

I love box inch mild steel - its my go to construction material for most jobs. Some of those welds might even hold the crushing divvy torque. Bolting the bearings down is a job for later as the chain tensioning situation is yet to be decided. Also the further toward the back of the car i can mount the sprocket the lower i can sink the engine into the bay which is a priority in order to make room for the carbs.
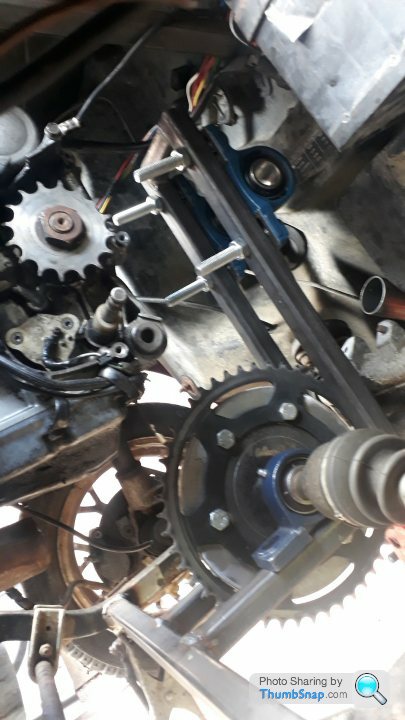
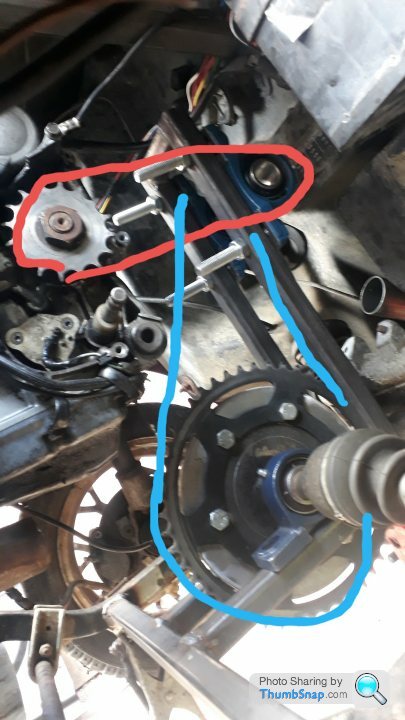
More box section to mount the upper bearings. Another quality artists impression so you can all visualise the horror that is this to-be drivetrain. This took way too long to do because i had to keep moving the engine in and out. In, check clearance, engine out, tweak setup, engine back in to check. Keep repeating this until standards drop below the quality of work being done, call it good enough.
Yes you can see an exhaust poking through there. While i had the welder out i thought id get that done. I used the original yamaha exhaust (kept everything i thought id need) so all i needed was some stainless straight and a handful of 90's (which i had the foresight to order a while back :-)
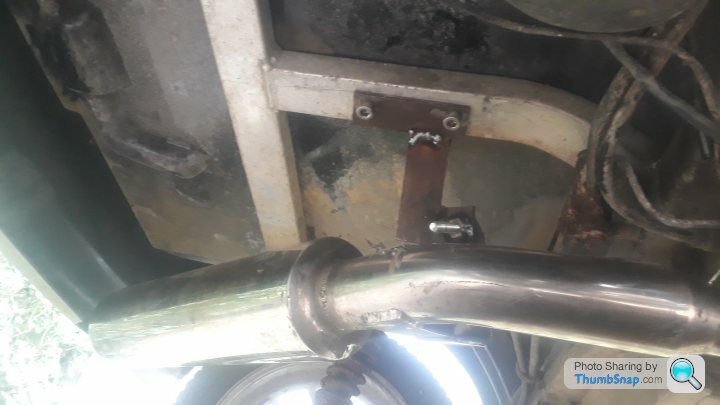
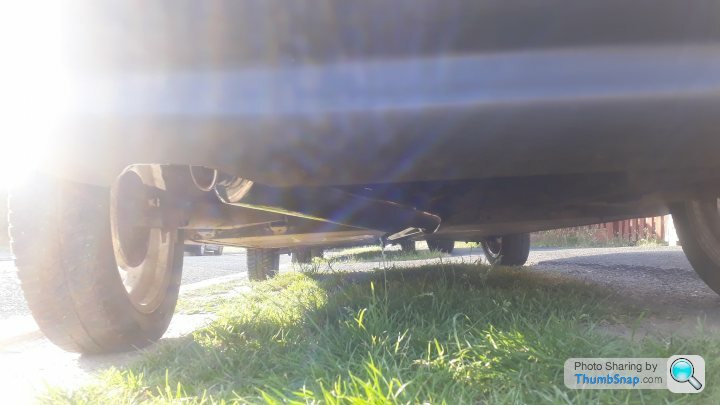
I think the standard of the exhaust system is in keeping with the rest of the build. I worry that the tip is going to melt the bumper but the good news is that problem is self rectifying.
Im pushing to get the engine bolted in, and im exhausted so thats all for now. Weathers miserable, and i need to go back to work and earn some money.

I love box inch mild steel - its my go to construction material for most jobs. Some of those welds might even hold the crushing divvy torque. Bolting the bearings down is a job for later as the chain tensioning situation is yet to be decided. Also the further toward the back of the car i can mount the sprocket the lower i can sink the engine into the bay which is a priority in order to make room for the carbs.
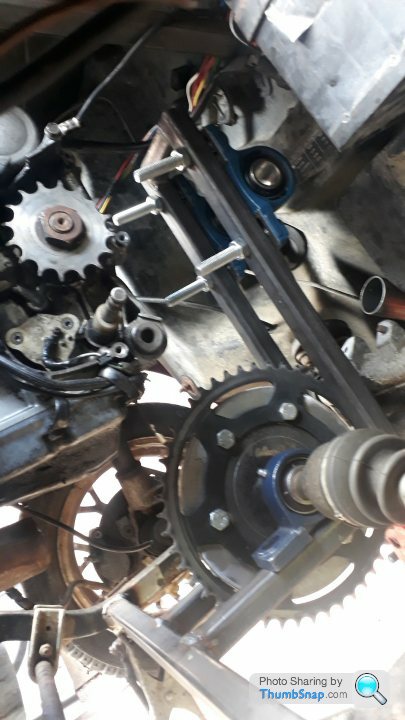
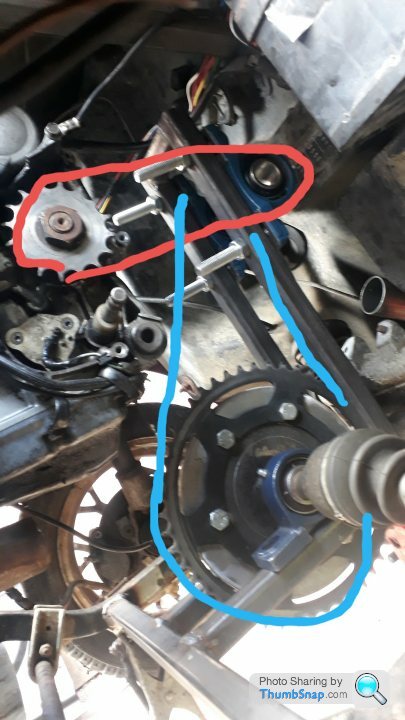
More box section to mount the upper bearings. Another quality artists impression so you can all visualise the horror that is this to-be drivetrain. This took way too long to do because i had to keep moving the engine in and out. In, check clearance, engine out, tweak setup, engine back in to check. Keep repeating this until standards drop below the quality of work being done, call it good enough.
Yes you can see an exhaust poking through there. While i had the welder out i thought id get that done. I used the original yamaha exhaust (kept everything i thought id need) so all i needed was some stainless straight and a handful of 90's (which i had the foresight to order a while back :-)
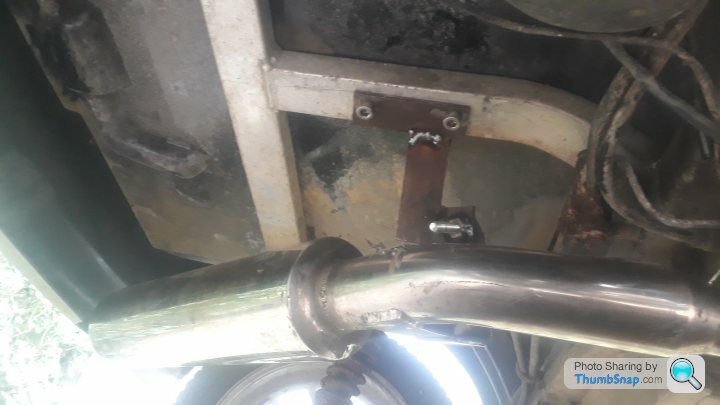
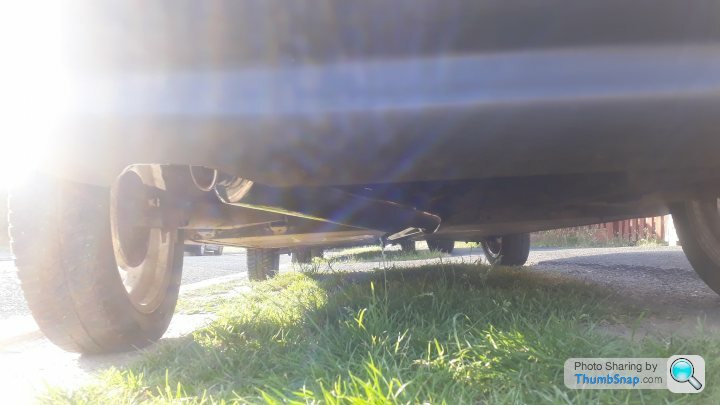
I think the standard of the exhaust system is in keeping with the rest of the build. I worry that the tip is going to melt the bumper but the good news is that problem is self rectifying.
Im pushing to get the engine bolted in, and im exhausted so thats all for now. Weathers miserable, and i need to go back to work and earn some money.
S2r said:
Well. this is quite mad (in a good way)
The red chain will take one hell of a battering - a friend did something similar many years ago when he mounted a stupidly wide rear tyre (like 300 wide) on his heavily modified bike. This had 2 front sprockets on a shaft set behind the engine so that he could get a chain to the rear sprocket. The smaller chain only lasted a couple of hundred miles before it blew itself to bits as a result of the small length coupled with 2 small sprockets, the inability to keep a reasonable tension and heat from the engine and/or generated from it moving round the sprockets. He ended up putting a smaller tyre back on...
Good luck
This is actually one of my main concerns. The intermediate shaft is pre-final drive so its RPM is quite high, which means it needs to be finely balanced and well aligned. Also the chain is short and the sprockets are small, meaning not only does each link bend a lot, but it does it often. Its also quite a small chain, not being your standard 530# or 010B chain, but the thinner 520#. Pitch is identical between the 2 grades but yamaha specced a light duty chain for their The red chain will take one hell of a battering - a friend did something similar many years ago when he mounted a stupidly wide rear tyre (like 300 wide) on his heavily modified bike. This had 2 front sprockets on a shaft set behind the engine so that he could get a chain to the rear sprocket. The smaller chain only lasted a couple of hundred miles before it blew itself to bits as a result of the small length coupled with 2 small sprockets, the inability to keep a reasonable tension and heat from the engine and/or generated from it moving round the sprockets. He ended up putting a smaller tyre back on...
Good luck

dukebox9reg said:
Slightly confused, just had a quick look on Google to see if anyone else has attempted anything on these and YouTube brings up one with the same reg....
Noooo dont spoil the first drive! Im only a couple of posts away from you guys being up to date. I'd secretly hoped i could get you all caught up to where it currently is progress wise and then drop my video attempt at an update/humor/first drive. The car is nowhere near done yet and there's so much driving/building/antics left in it that it would be criminal to not bring everyone along for the ride.Let me knock out a few more updates this weekend for you all and then ill put the video of where it currently stands progress wise. Then the updates are true and 'live' so to speak.
Edited by sparkybean on Saturday 18th January 15:13
Gassing Station | Readers' Cars | Top of Page | What's New | My Stuff