Vini – the Powerflex V8 Mini
Discussion
Hopefully this is of some interest.
It is not the usual story of an engine swap.
Vini, the V8 Mini.
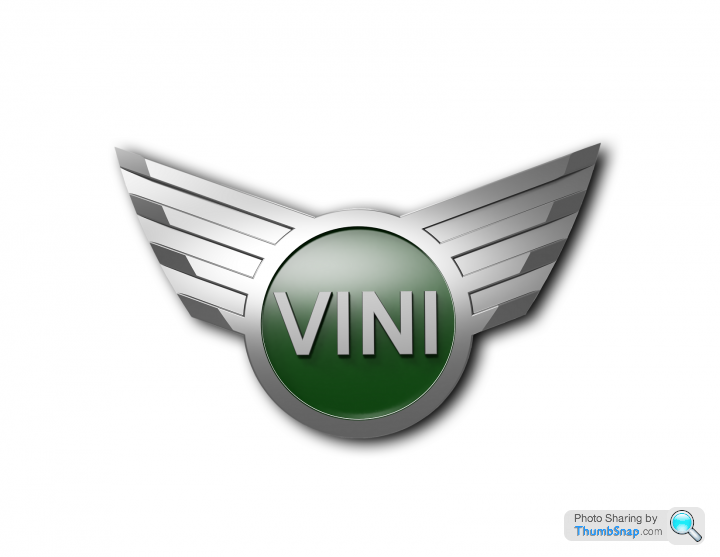
My company is Powerflex and we get to test and drive a variety of cars.
I’ve restored my Citroen SM, own a Citroen DS and an Alfa SZ. I love all three mainly for their engineering bravery (stupidity?) Some of the older readers might even remember where I started which was Power Engineering.
The background to this is that I have had a 968 Clubsport trackcar forever. I’ve done a fair bit of racing and was starting to feel that as lovely as the 968 is, I wanted something, well, a bit more scary.
More of a challenge to my limited track skills.
The first time I drove a Mini was in The Birkett at Silverstone and loved it. What a great package.
That got me thinking. Let’s build a fast Mini.
We sponsor the Mini Challenge so spoke to Antony (runs the championship) about the race cars and how far they could be tuned and improved without the burden of regulations. The advice was that 300bhp was feasible but not sensible for lots of track driving.
Later that year I was at The ‘ring and thinking of some of the world’s great engines. The S54 BMW M3 has always been regarded highly. But I didn’t want an M3.
The Mini I raced had been built by www.edmotorsport.co.uk who is a distributor for Powerflex. I’d also bought and raced a BMW Compact that they had built and was super impressed with the build quality and attention to detail.
EDM were building and racing a number of Minis at the time for different series so I thought now was the time to approach them for further discussions.
I’d assumed that asking for their thoughts on fitting an S54 engine into a Mini would be a very short conversation. The phone line would go dead, that would be that and I would simply forget it and buy a fast Porsche.
However I had not banked on their enthusiasm for mad projects and Eliot’s ability in all things engineering. I got the impression he wanted something more challenging in business than building saloon race cars.
Straight away he thought it was an excellent idea. We didn’t think too many steps ahead and didn’t try to analyse all of the potential pitfalls of something so radical.
They happened to have an S54 engine in stock so now we needed a car.
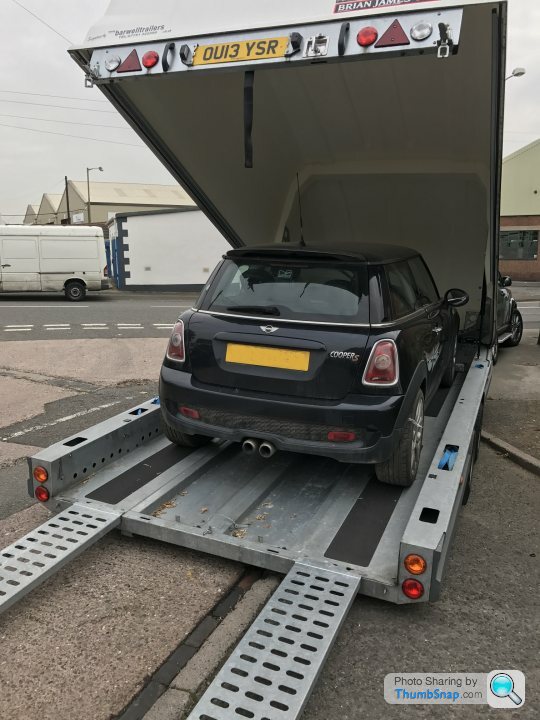


Step one was to strip the front down so that we could look at a bare engine bay and see the structure of the car.
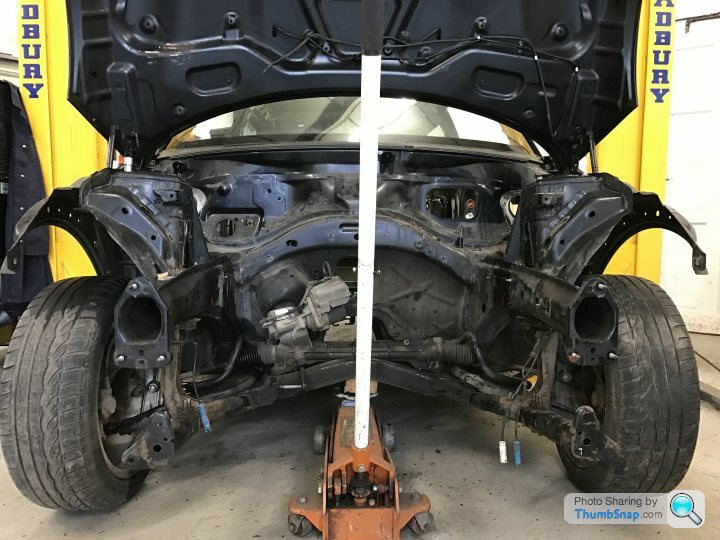
With this done, the engine was craned into place and it didn’t look unrealistic. It was long though.
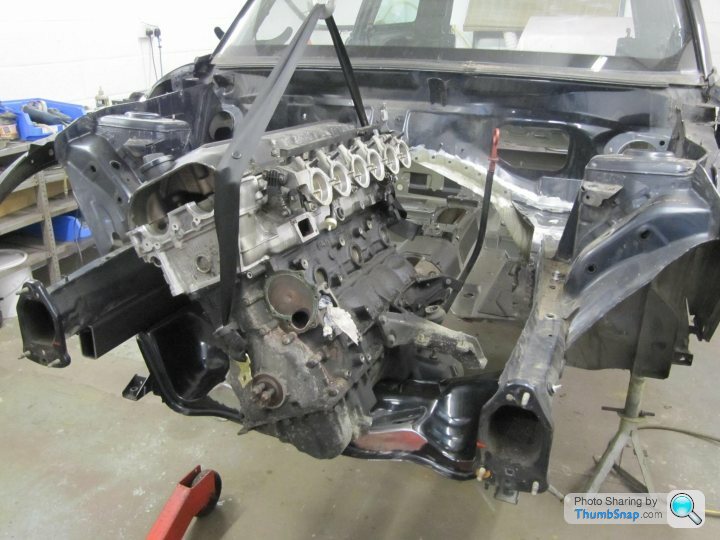
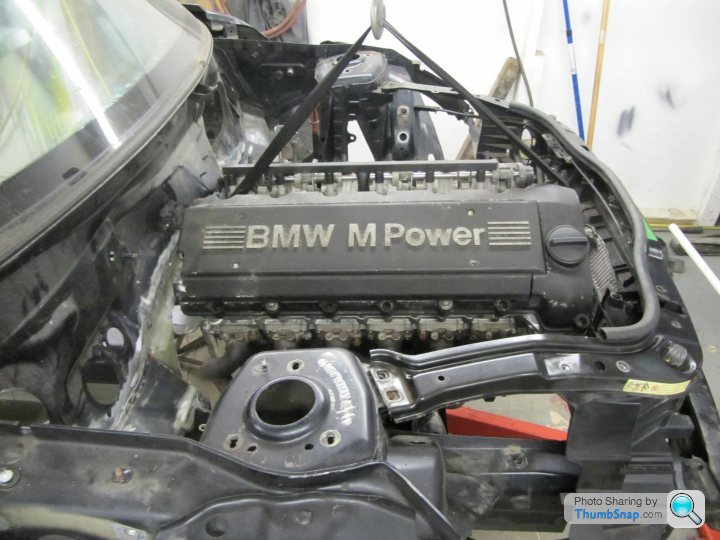
About this time, I was talking with Iain Litchfield and mentioned the project.
He said “why are you messing about with an iron block six banger when you could have an all alloy V8 which is smaller, lighter and makes 100bhp more? I have an engine you can borrow. See if that will fit?”
And so, you can see in only a few short weeks, mission creep has set in big time.
This was at the start of 2017.
It was always going to be a long project for reasons that will become obvious if you will permit me to tell the story.
Rather than sharing this from the start at the time, I thought it would be better to write about it as the car is nearing completion.
You will then see the immense detail that has gone in to building something really very special.
It is not the usual story of an engine swap.
Vini, the V8 Mini.
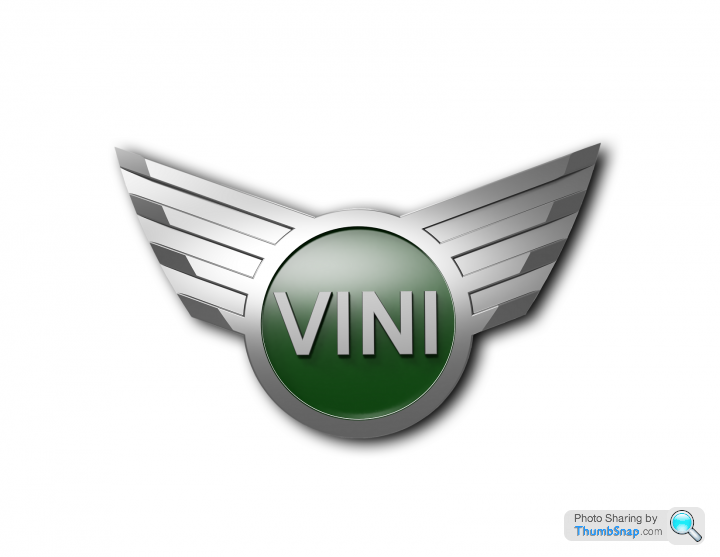
My company is Powerflex and we get to test and drive a variety of cars.
I’ve restored my Citroen SM, own a Citroen DS and an Alfa SZ. I love all three mainly for their engineering bravery (stupidity?) Some of the older readers might even remember where I started which was Power Engineering.
The background to this is that I have had a 968 Clubsport trackcar forever. I’ve done a fair bit of racing and was starting to feel that as lovely as the 968 is, I wanted something, well, a bit more scary.
More of a challenge to my limited track skills.
The first time I drove a Mini was in The Birkett at Silverstone and loved it. What a great package.
That got me thinking. Let’s build a fast Mini.
We sponsor the Mini Challenge so spoke to Antony (runs the championship) about the race cars and how far they could be tuned and improved without the burden of regulations. The advice was that 300bhp was feasible but not sensible for lots of track driving.
Later that year I was at The ‘ring and thinking of some of the world’s great engines. The S54 BMW M3 has always been regarded highly. But I didn’t want an M3.
The Mini I raced had been built by www.edmotorsport.co.uk who is a distributor for Powerflex. I’d also bought and raced a BMW Compact that they had built and was super impressed with the build quality and attention to detail.
EDM were building and racing a number of Minis at the time for different series so I thought now was the time to approach them for further discussions.
I’d assumed that asking for their thoughts on fitting an S54 engine into a Mini would be a very short conversation. The phone line would go dead, that would be that and I would simply forget it and buy a fast Porsche.
However I had not banked on their enthusiasm for mad projects and Eliot’s ability in all things engineering. I got the impression he wanted something more challenging in business than building saloon race cars.
Straight away he thought it was an excellent idea. We didn’t think too many steps ahead and didn’t try to analyse all of the potential pitfalls of something so radical.
They happened to have an S54 engine in stock so now we needed a car.
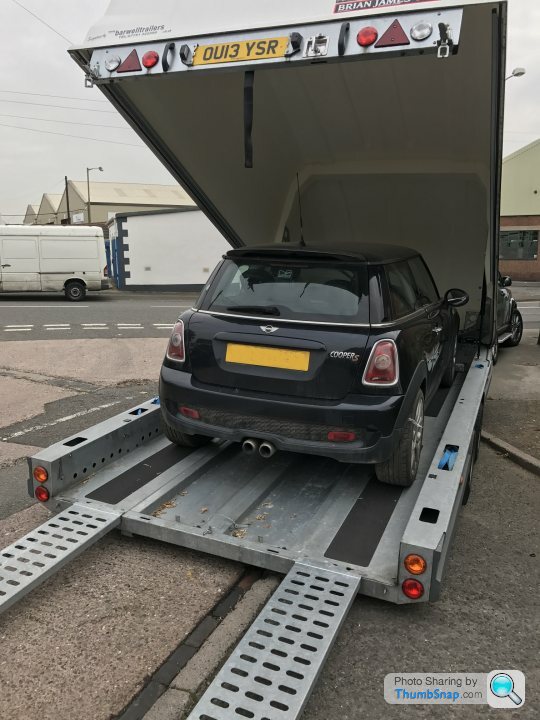


Step one was to strip the front down so that we could look at a bare engine bay and see the structure of the car.
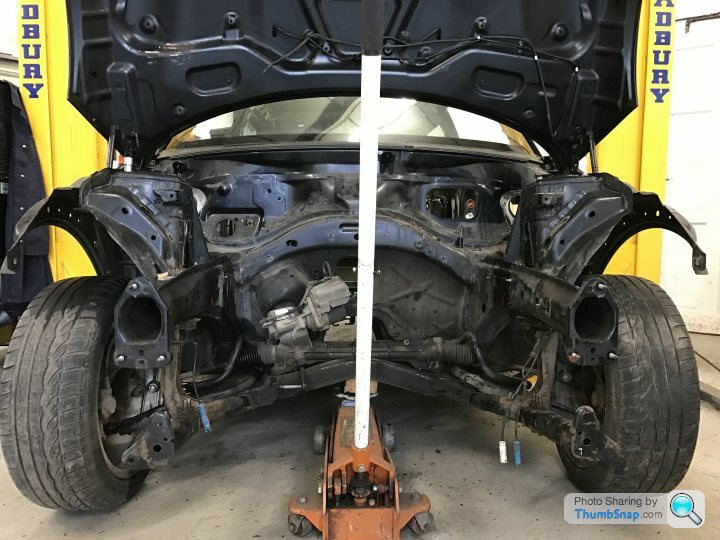
With this done, the engine was craned into place and it didn’t look unrealistic. It was long though.
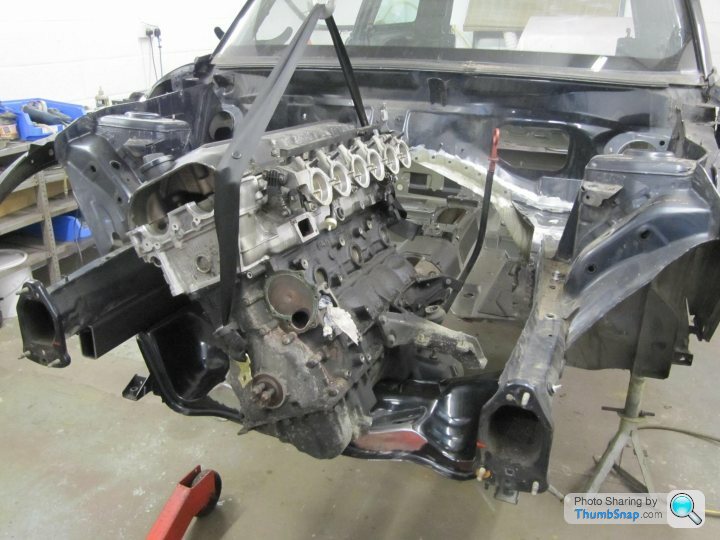
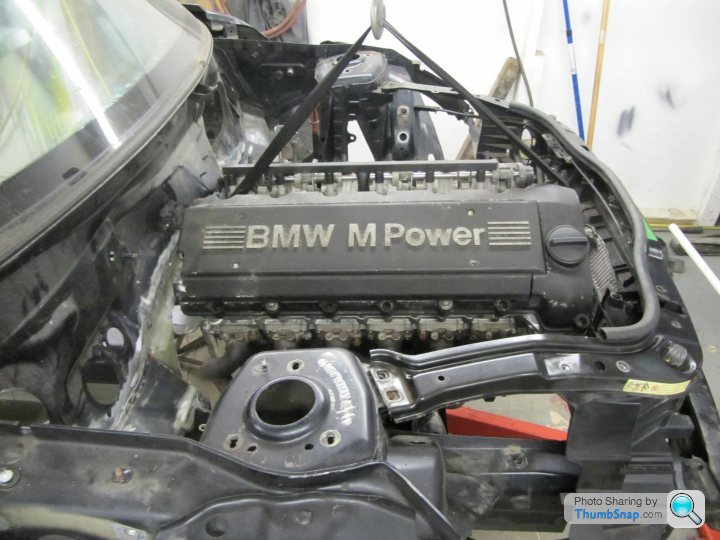
About this time, I was talking with Iain Litchfield and mentioned the project.
He said “why are you messing about with an iron block six banger when you could have an all alloy V8 which is smaller, lighter and makes 100bhp more? I have an engine you can borrow. See if that will fit?”
And so, you can see in only a few short weeks, mission creep has set in big time.
This was at the start of 2017.
It was always going to be a long project for reasons that will become obvious if you will permit me to tell the story.
Rather than sharing this from the start at the time, I thought it would be better to write about it as the car is nearing completion.
You will then see the immense detail that has gone in to building something really very special.
Edited by 96eight on Tuesday 3rd March 11:01
With the engine and grubby bits out of the way it was time to do some crude measurements and test fitting.
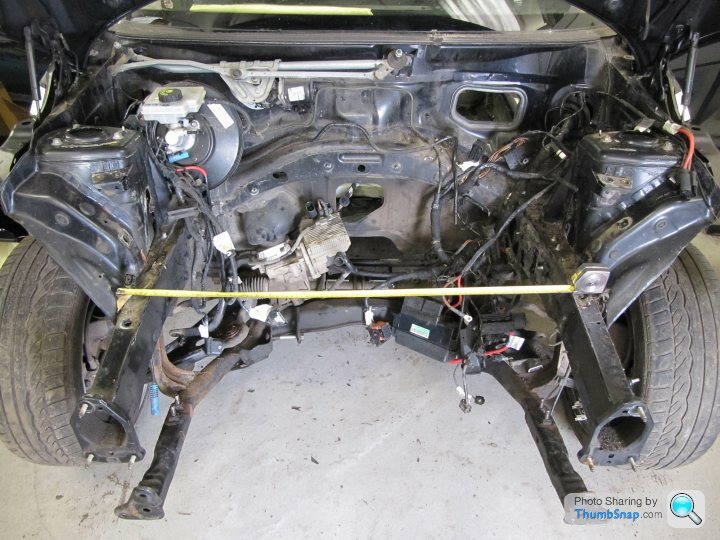
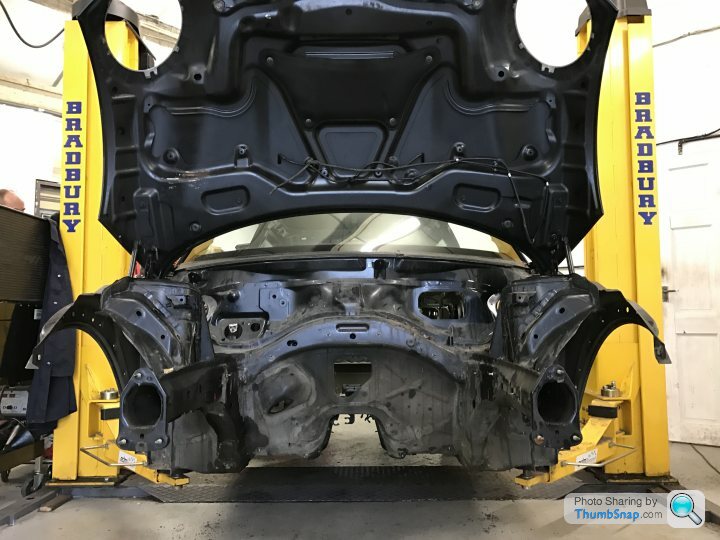
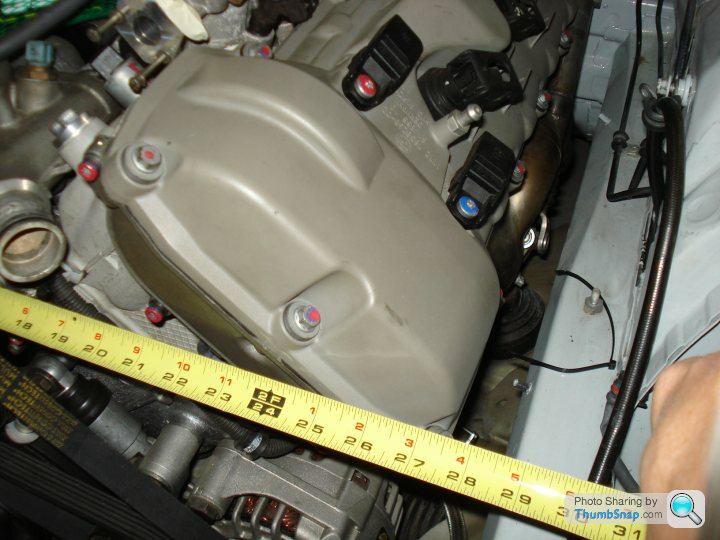
Still with no real thoughts of what we would do if it looked like fitting was a possibility.
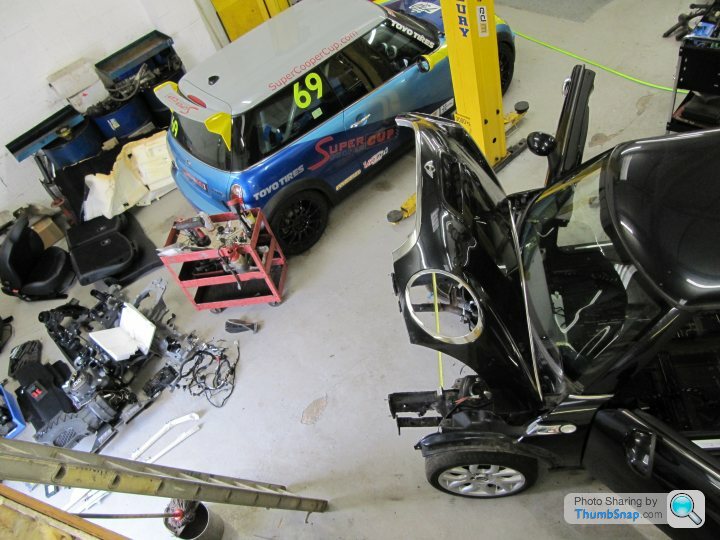
Whilst ideas as to the overall strategy for the build were still thin on the ground, EDM and I agreed very early on that we wanted the car to maintain a factory built appearance.
Not have the bumpers bolted where they touched and headlights mounted with fabricated angle iron.
If we were going to do this it had to represent Powerflex from a marketing perspective and be something that we would be proud to exhibit on track and at shows. It also was clear that EDM did not want something out there that wasn’t the best that it could possibly be.
Personally, the more time I spent with EDM discussing what might be possible, the more it became obvious that I’d chosen the right company with an attitude close to my company’s and a desire for quality.
The engine looked amazing in situ, even held in by an engine crane it looked like this part of the project was possible.
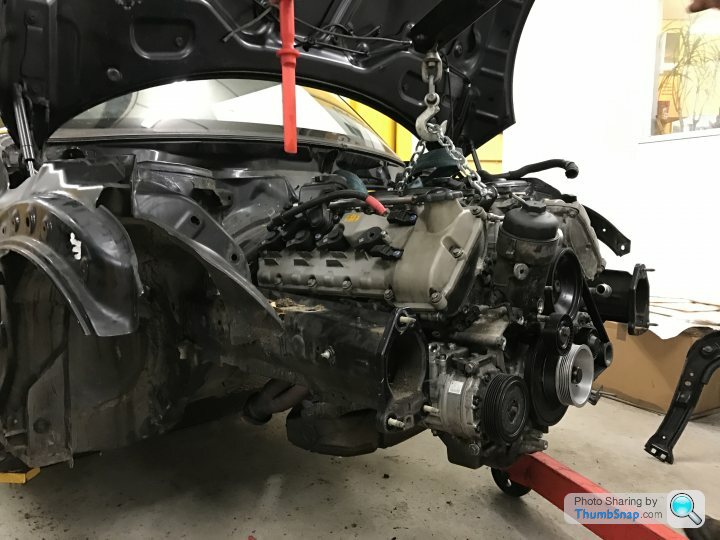
It would need to go a fair bit further back than this but width wise, it was game on.
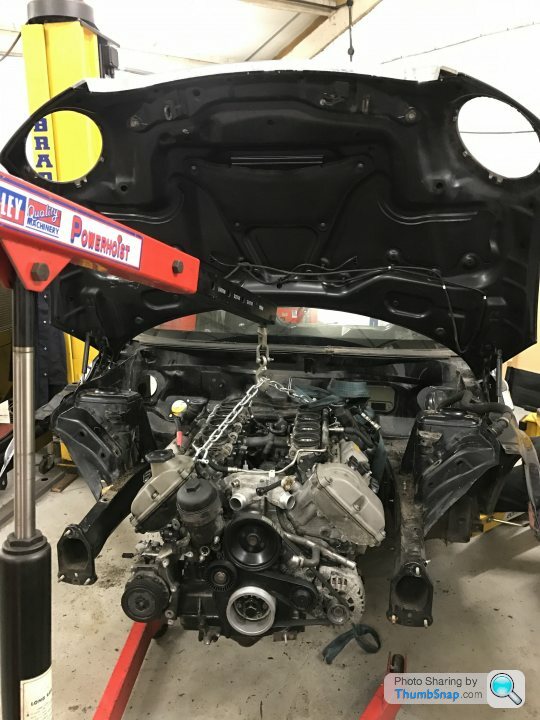
In fact a large amount of the standard front body parts were able to be test fitted around the engine. We even got the bonnet on.

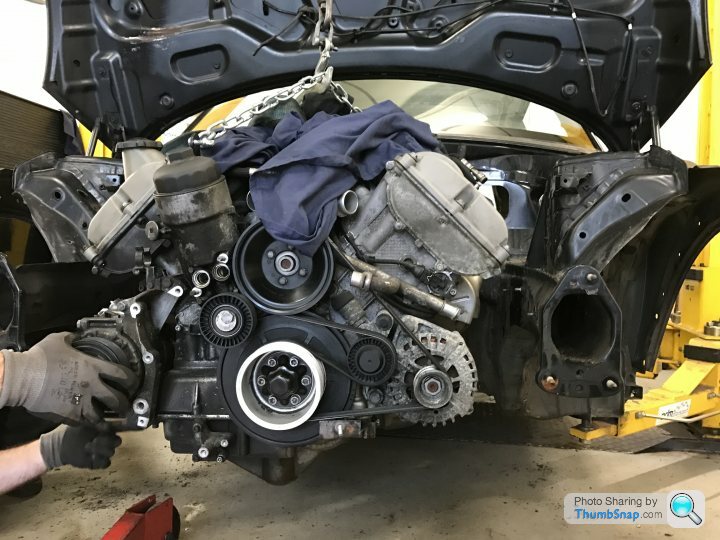
That was the GO/NOGO moment, as they say at NASA.
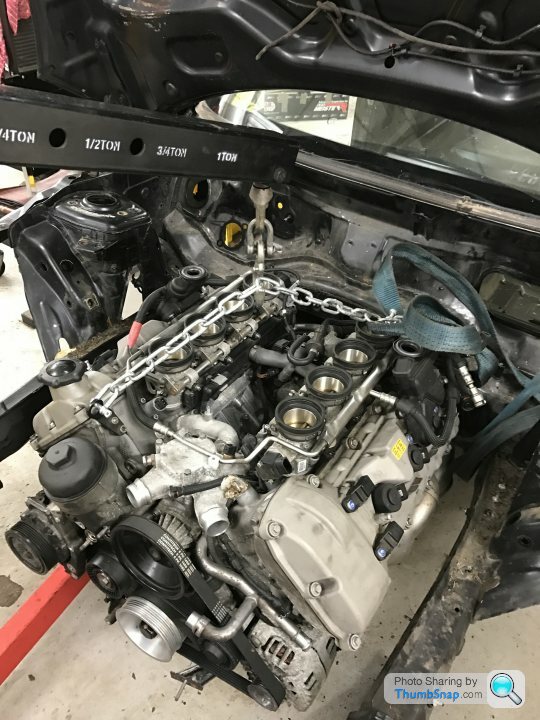
It was GO from me and GO from EDM.
Then the reality set in with little things like gearboxes and diffs and struts, and wishbones and steering racks and fuel tanks and hubs and roll cage and and and….. needing to be considered.
Still, they could wait! There was a shell to strip and as everyone knows taking things apart is the best bit.
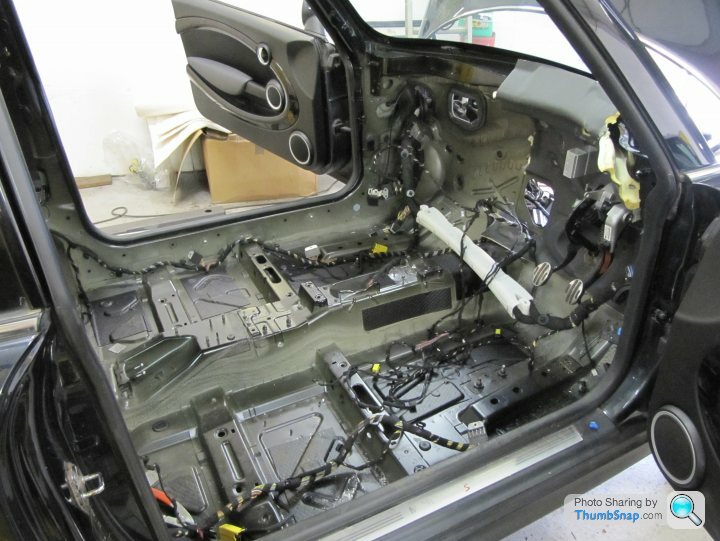
Amazing what the suspension does when you take some weight out.
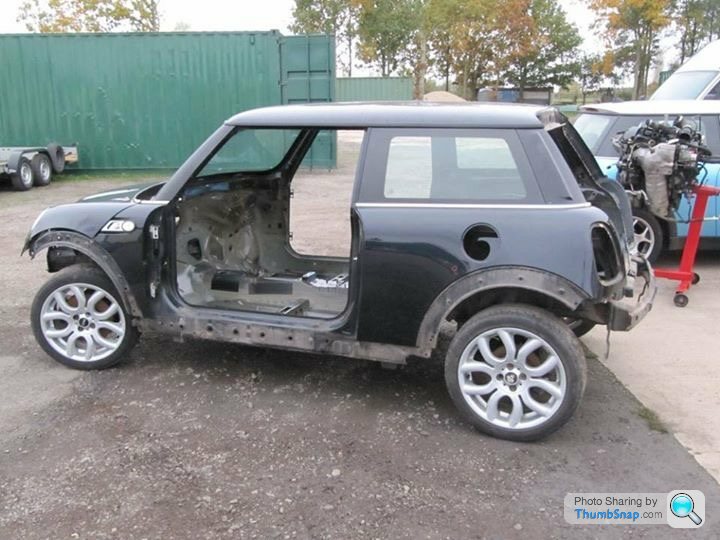
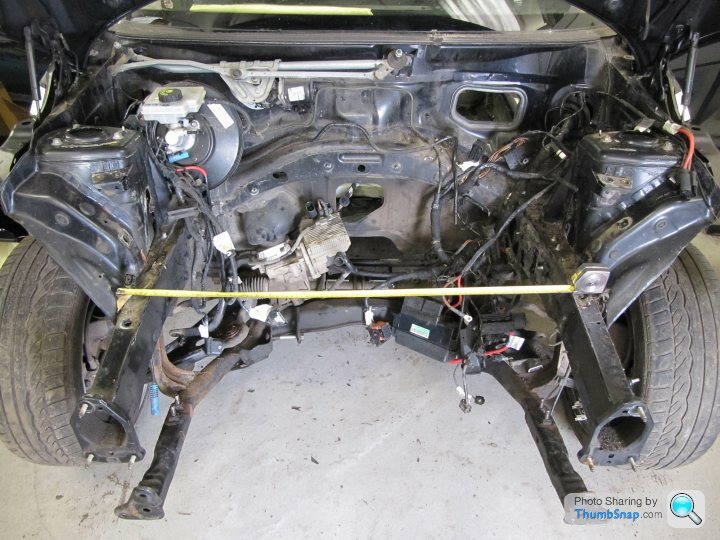
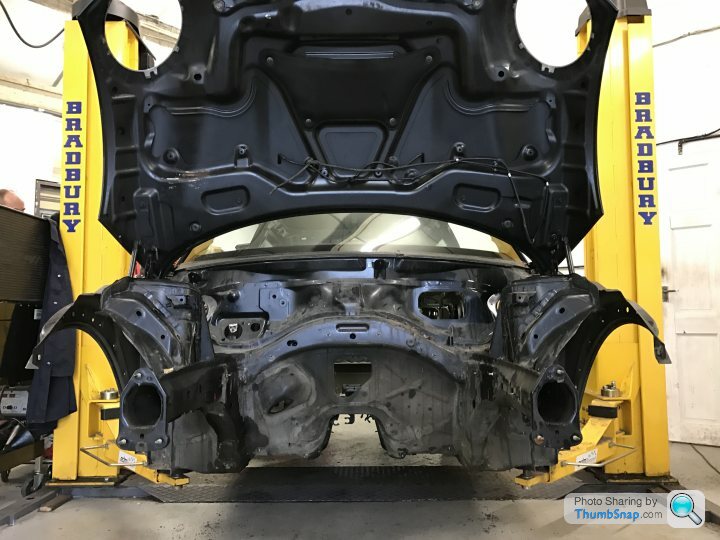
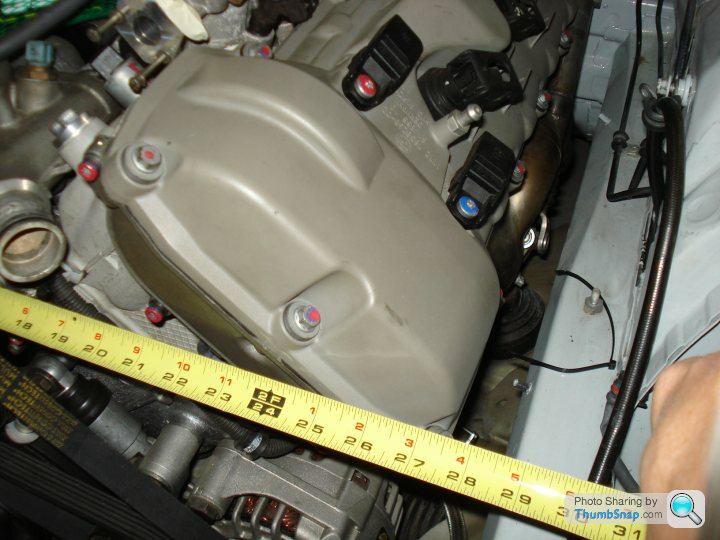
Still with no real thoughts of what we would do if it looked like fitting was a possibility.
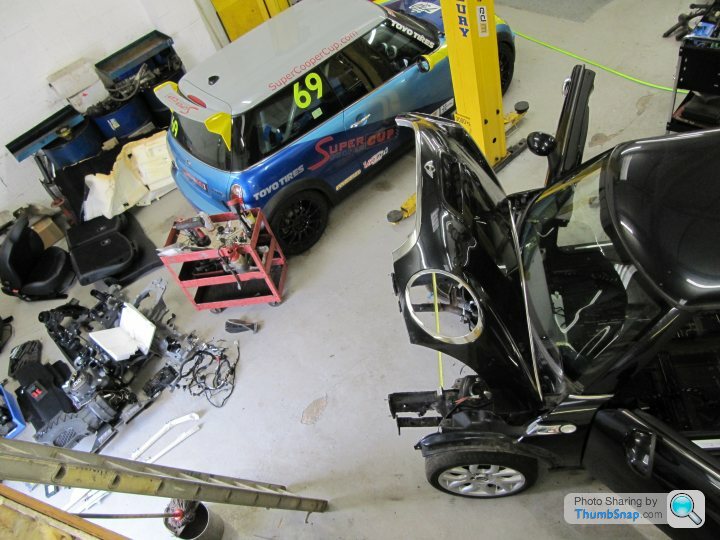
Whilst ideas as to the overall strategy for the build were still thin on the ground, EDM and I agreed very early on that we wanted the car to maintain a factory built appearance.
Not have the bumpers bolted where they touched and headlights mounted with fabricated angle iron.
If we were going to do this it had to represent Powerflex from a marketing perspective and be something that we would be proud to exhibit on track and at shows. It also was clear that EDM did not want something out there that wasn’t the best that it could possibly be.
Personally, the more time I spent with EDM discussing what might be possible, the more it became obvious that I’d chosen the right company with an attitude close to my company’s and a desire for quality.
The engine looked amazing in situ, even held in by an engine crane it looked like this part of the project was possible.
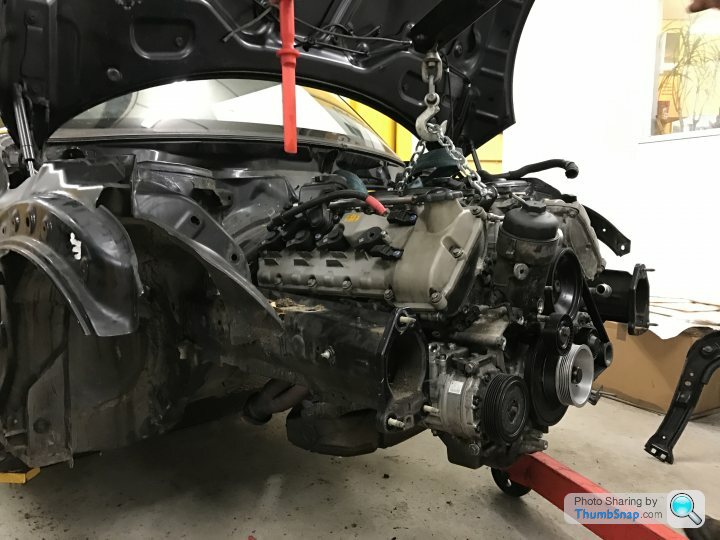
It would need to go a fair bit further back than this but width wise, it was game on.
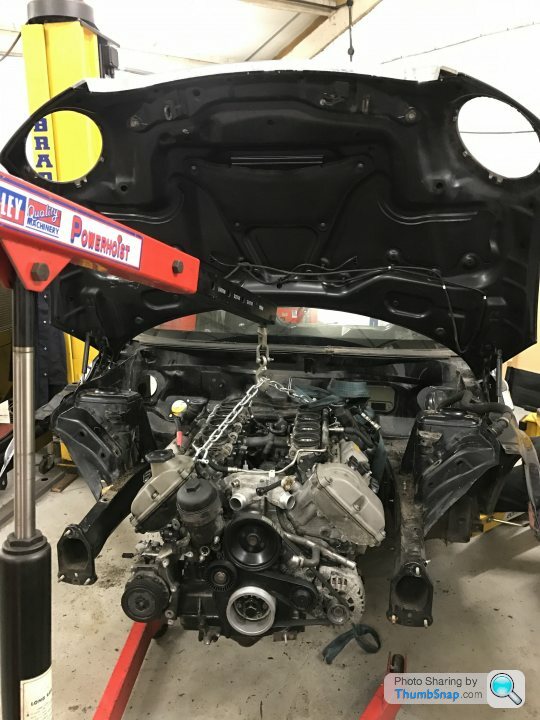
In fact a large amount of the standard front body parts were able to be test fitted around the engine. We even got the bonnet on.

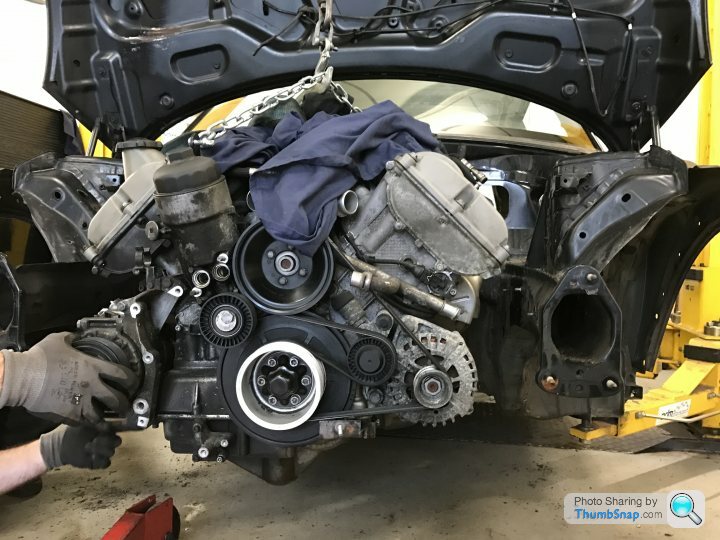
That was the GO/NOGO moment, as they say at NASA.
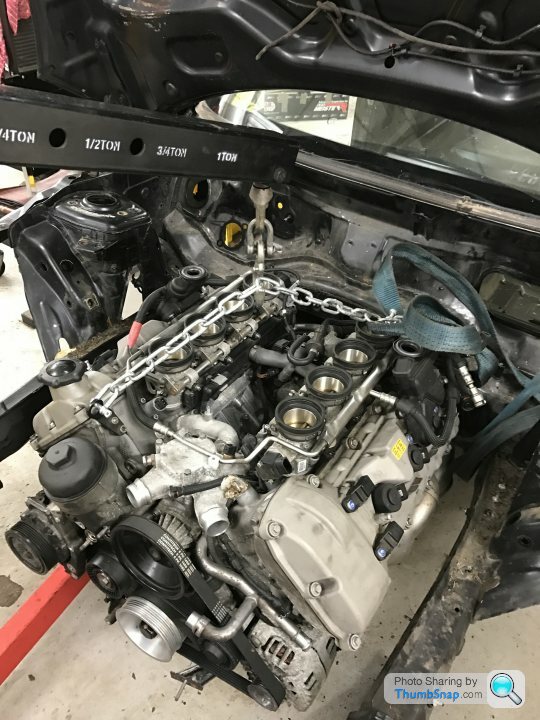
It was GO from me and GO from EDM.
Then the reality set in with little things like gearboxes and diffs and struts, and wishbones and steering racks and fuel tanks and hubs and roll cage and and and….. needing to be considered.
Still, they could wait! There was a shell to strip and as everyone knows taking things apart is the best bit.
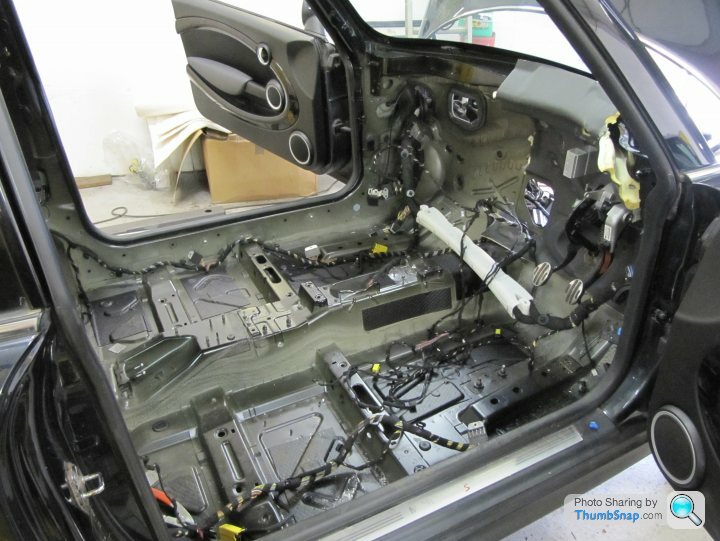
Amazing what the suspension does when you take some weight out.
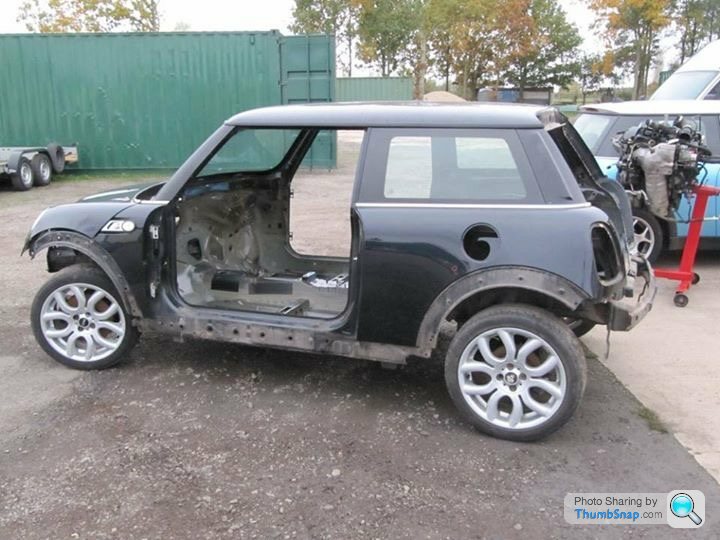
Apologies if this is a bit wordy at the beginning but I thought it was important to understand the thought processes and the problems in the early stages
There was nothing from the base car we needed to keep.
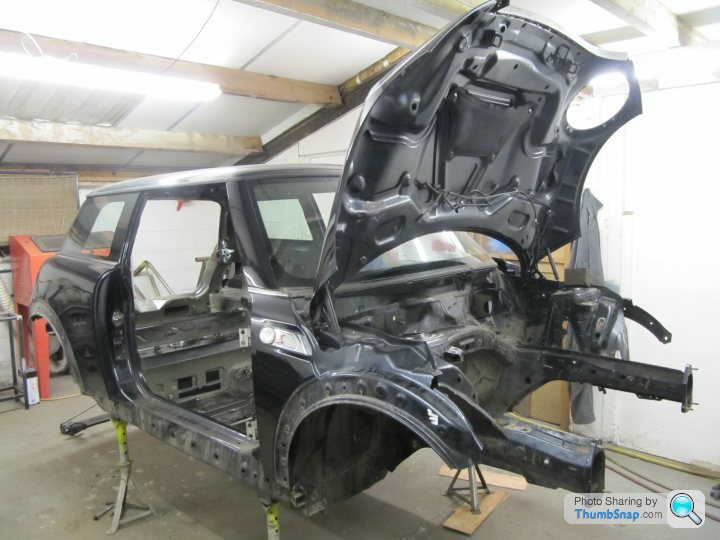
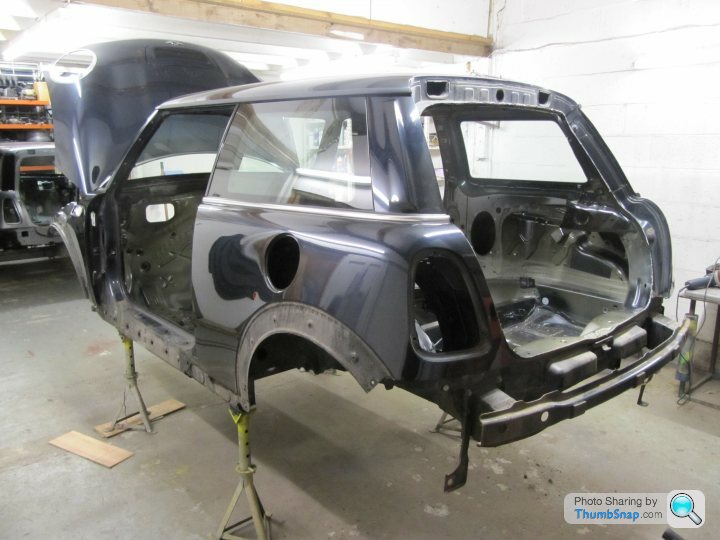
The wiring loom would be more difficult to modify than manufacture specially. The suspension, steering, hubs, wishbones all had to be discarded.
The glass was removed and kept but these were the only bits apart from the shell that we needed.
I now had to start giving some guidance to EDM as to the direction to go and what I wanted from the car.
They had to clearly understand my goals. And I had to invent some sharpish!
Many moons ago at Power Engineering we had a customer who wanted the ultimate EVO 6 track car. Money no object. A full race car suitable for trackdays.
It had everything possible.
At the time these were very rare and expensive and it was before the days of insane power figures.
So from a brand new road car we removed all trim, fitted a cage, and fitted all the bits needed for an impressive road legal trackday car. Some considerable time into the build, the customer started talking about the hifi he was going to have fitted when we had finished.
I realised we really had no clue what this chap wanted from the car and it became very difficult to finish, simply because we didn’t understand what he was trying to achieve.
I wanted EDM and I to be on the same wavelength so if decisions had to be made and I couldn’t be reached, Eliot would instinctively know what to do.
The car had to be road legal.
No bonnet bulges
No modified external panels
No big wheel arches
No crazy exhaust
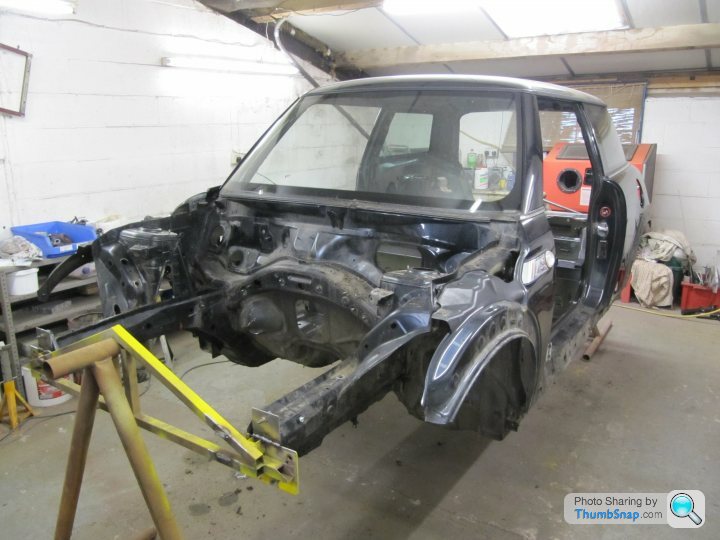
Powerflex is predominantly aftermarket and performance, with a fair percentage of our parts being fitted to race cars. It had to be something along those lines to reflect what my company does.
Road, Track, Performance and Race.
So I wanted the biggest possible juxtaposition between the inside of the car and the outside. The outside was to be subtle, stylish and to 95% of people seeing the car, standard.
The other 5% I want to be curious. “What is it? It’s not standard but what have they done?” On trackdays I would like to people to wonder why on earth a Mini is making that noise.
The inside, however would be touring car, but with two seats. As neat and beautifully put together as it is possible to be. This is where EDM excel. The quality of their prep is superb.
Oh and finally it had to be suitable to race. If there is a race series willing to take it then it had to have the cage, fuel system and all safety systems built so that it would be legal.
An awful lot of this was going to have to disappear.
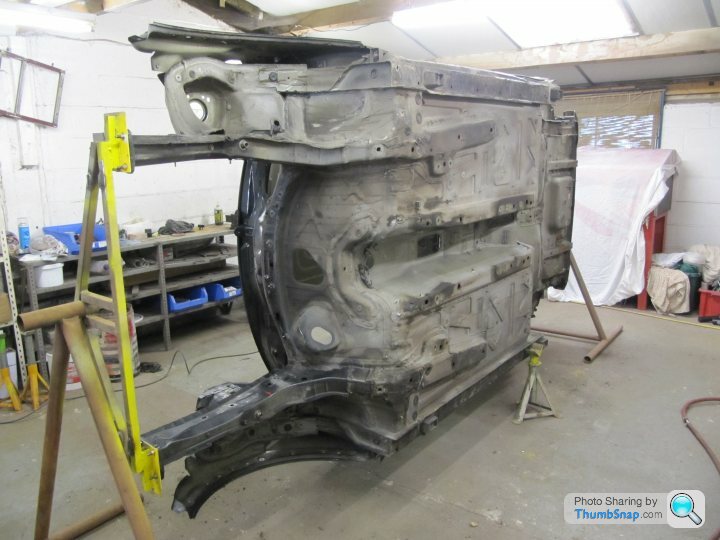
There was nothing from the base car we needed to keep.
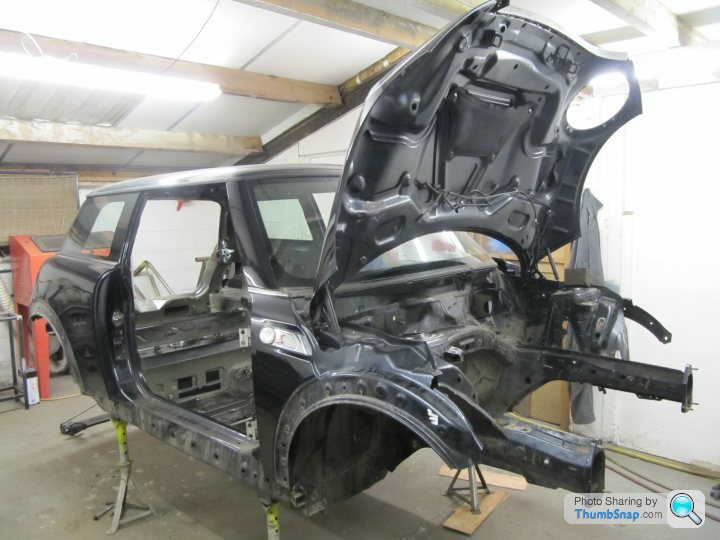
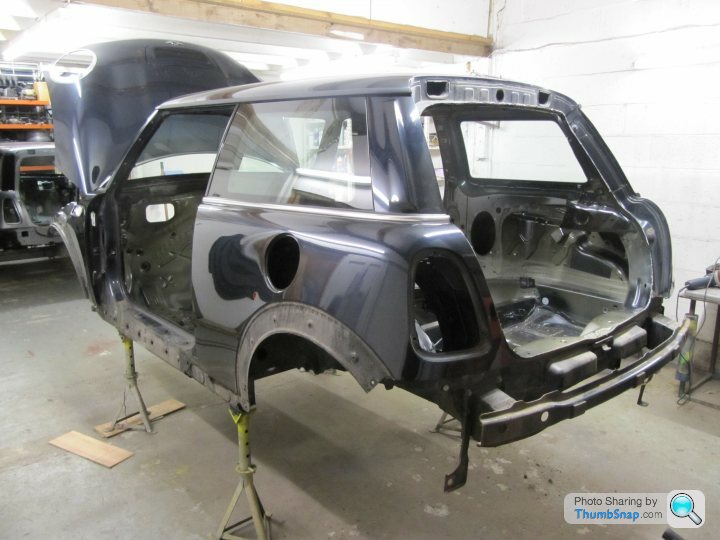
The wiring loom would be more difficult to modify than manufacture specially. The suspension, steering, hubs, wishbones all had to be discarded.
The glass was removed and kept but these were the only bits apart from the shell that we needed.
I now had to start giving some guidance to EDM as to the direction to go and what I wanted from the car.
They had to clearly understand my goals. And I had to invent some sharpish!
Many moons ago at Power Engineering we had a customer who wanted the ultimate EVO 6 track car. Money no object. A full race car suitable for trackdays.
It had everything possible.
At the time these were very rare and expensive and it was before the days of insane power figures.
So from a brand new road car we removed all trim, fitted a cage, and fitted all the bits needed for an impressive road legal trackday car. Some considerable time into the build, the customer started talking about the hifi he was going to have fitted when we had finished.
I realised we really had no clue what this chap wanted from the car and it became very difficult to finish, simply because we didn’t understand what he was trying to achieve.
I wanted EDM and I to be on the same wavelength so if decisions had to be made and I couldn’t be reached, Eliot would instinctively know what to do.
The car had to be road legal.
No bonnet bulges
No modified external panels
No big wheel arches
No crazy exhaust
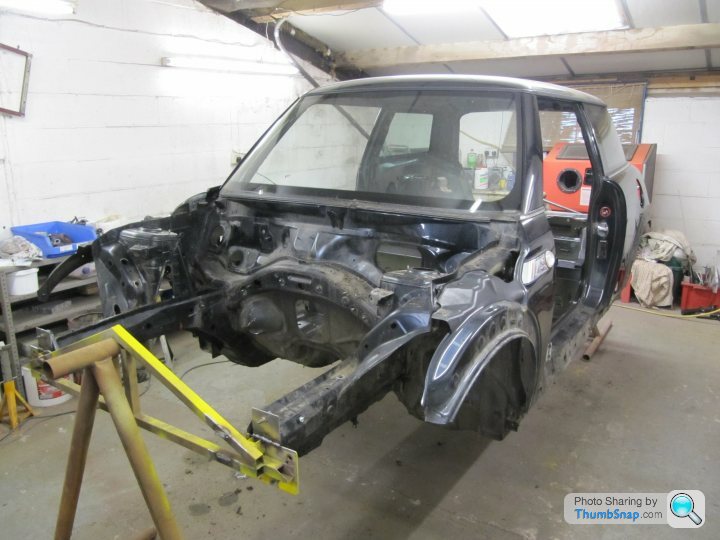
Powerflex is predominantly aftermarket and performance, with a fair percentage of our parts being fitted to race cars. It had to be something along those lines to reflect what my company does.
Road, Track, Performance and Race.
So I wanted the biggest possible juxtaposition between the inside of the car and the outside. The outside was to be subtle, stylish and to 95% of people seeing the car, standard.
The other 5% I want to be curious. “What is it? It’s not standard but what have they done?” On trackdays I would like to people to wonder why on earth a Mini is making that noise.
The inside, however would be touring car, but with two seats. As neat and beautifully put together as it is possible to be. This is where EDM excel. The quality of their prep is superb.
Oh and finally it had to be suitable to race. If there is a race series willing to take it then it had to have the cage, fuel system and all safety systems built so that it would be legal.
An awful lot of this was going to have to disappear.
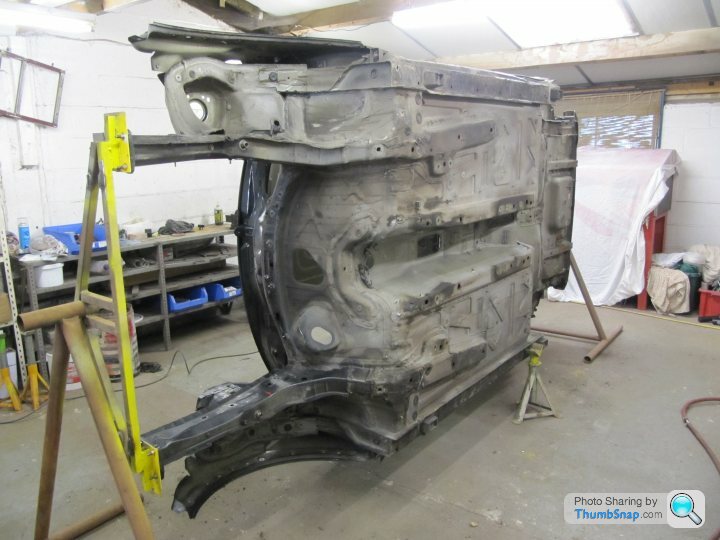
With a bare shell and a slightly less bare brief this is where the knowledge, experience and black magic of EDM came in.
I decided that, whilst driving, having both hands on the steering wheel for as long as possible would be a great idea.
Therefore we ruled out a sequential dog box with a lever change and opted to use the originalE92 M3 7 speed dual clutch box.
Advantages – Strong, available, and would be mappable with the ECU we had in mind.
The disadvantage was that it is heavy.
Great, that’s that bit sorted.
Plainly the Mini has no transmission tunnel so we knew that the front bulkhead would need significant attention, to say the least.
We have to get the engine back into the shell and low enough to clear the bonnet.
How do we go about getting this beasty in?
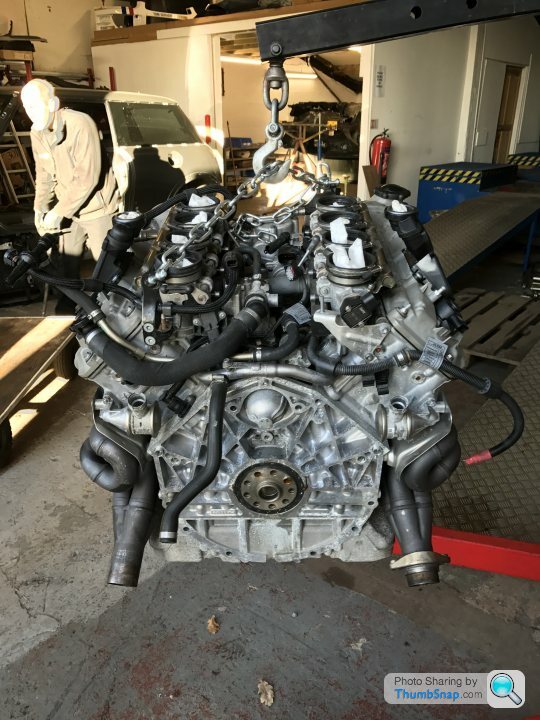
It is at this point that EDM had to stop, sit and think. Measure, guess, stop and think again.
Decisions made now as to engine position and angle would affect everything.
It is no exaggeration to say that a single mistake now could make the whole thing nonviable.
But that mistake might not become apparent for months to come.
The engine has a complex sump with a small clearance gap for the M3 steering rack.
We had to position the engine so that the sump would allow our steering rack to be in that gap.
The position of the rack controls the hub position, but the hub position is controlled by the wheel centre position and that cannot change.
The rack position dictates the wishbone and strut position. So all aspects of the front geometry are controlled by the engine position and height.
The engine angle controls the gearbox centre line, the propshaft and therefore diff position as well as impacting on the rear suspension.
Of course he had to take into consideration the exhaust system and ground clearance.
So it was now time for Eliot to get busy with the can opener.
A fair bit of this bulkead and floor was going to have to go to get the engine as far back as possible and positioned correctly to get the steering rack in place.
|
Well, it's in place ish
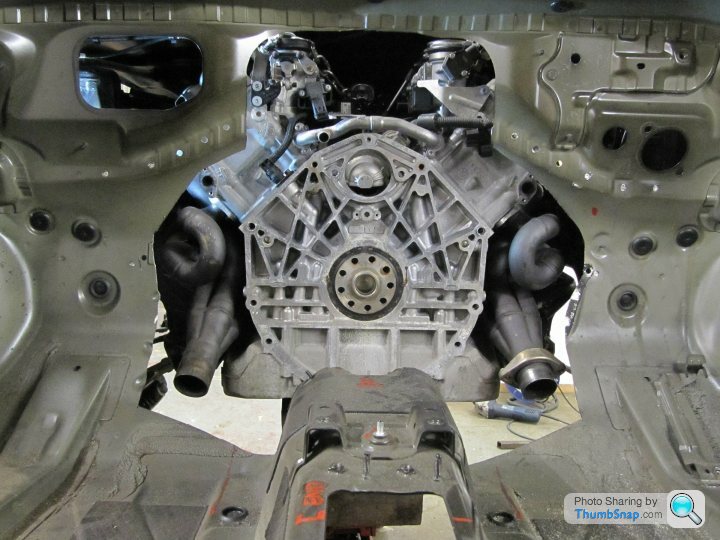
See how much further we've been able to get the engine. (when I say "we" I mean the Royal "we")
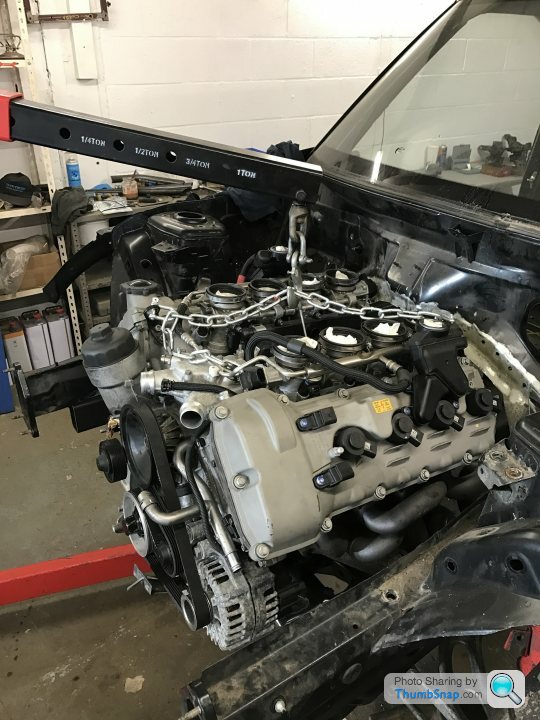
This is just the engine in situ against the bulkhead
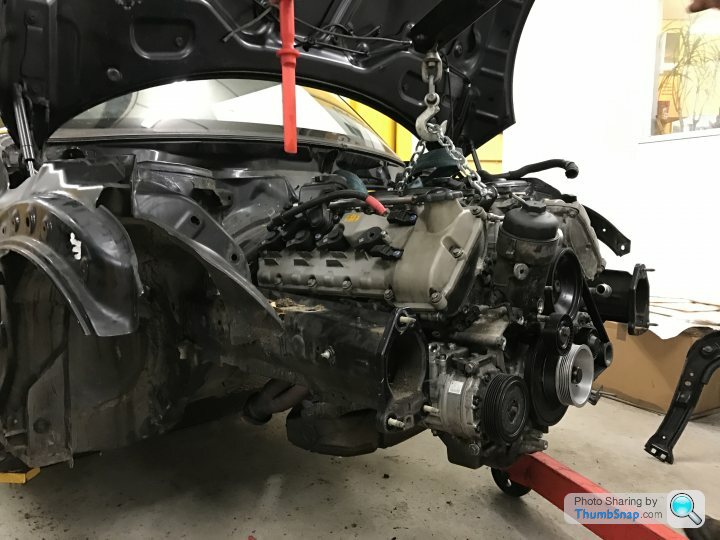
Now we are getting somewhere
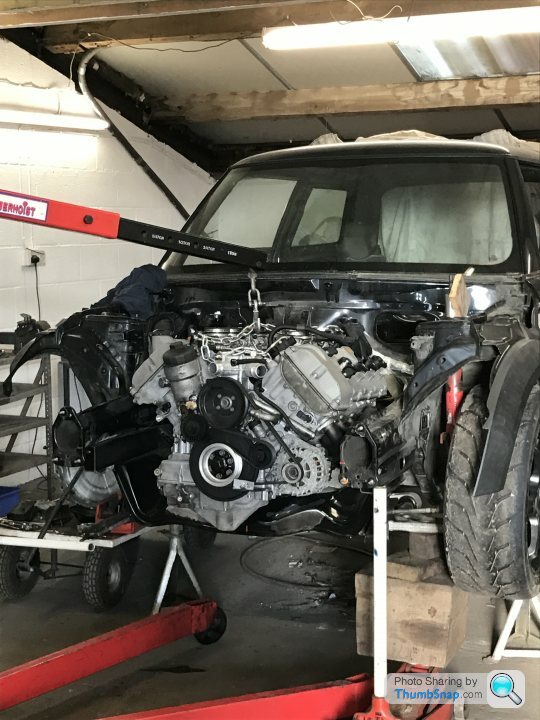
So much further back
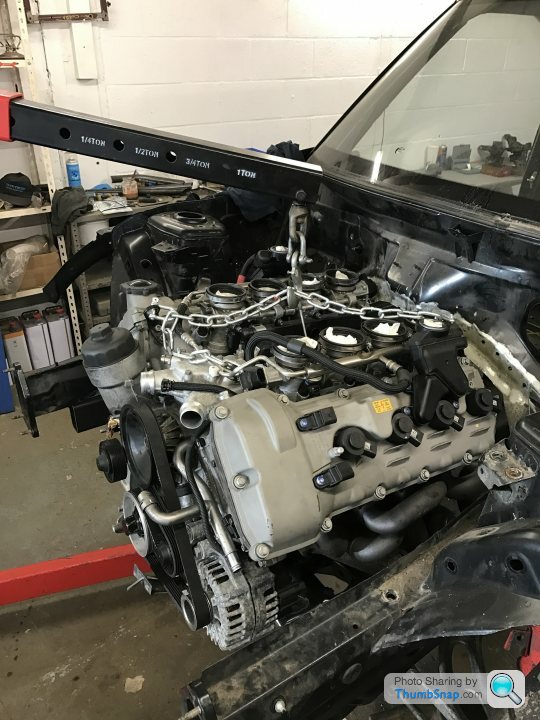
A fair bit of sheel strength gone already and we haven't started removing the floorpan yet
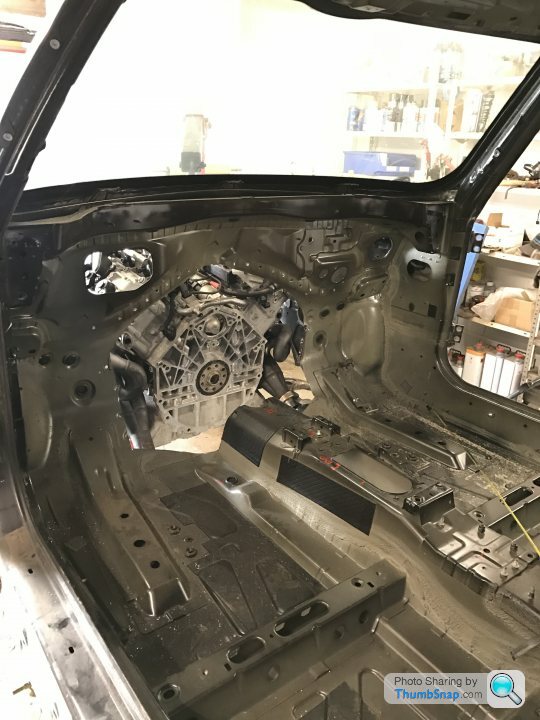
Very complex and efficient sump. We considered a dry sump system but we weren't convinced it would improve matter but it would add complication.
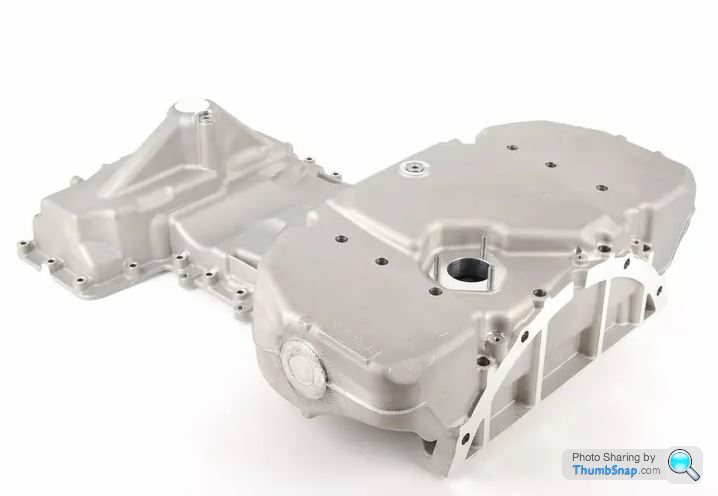
I decided that, whilst driving, having both hands on the steering wheel for as long as possible would be a great idea.
Therefore we ruled out a sequential dog box with a lever change and opted to use the originalE92 M3 7 speed dual clutch box.
Advantages – Strong, available, and would be mappable with the ECU we had in mind.
The disadvantage was that it is heavy.
Great, that’s that bit sorted.
Plainly the Mini has no transmission tunnel so we knew that the front bulkhead would need significant attention, to say the least.
We have to get the engine back into the shell and low enough to clear the bonnet.
How do we go about getting this beasty in?
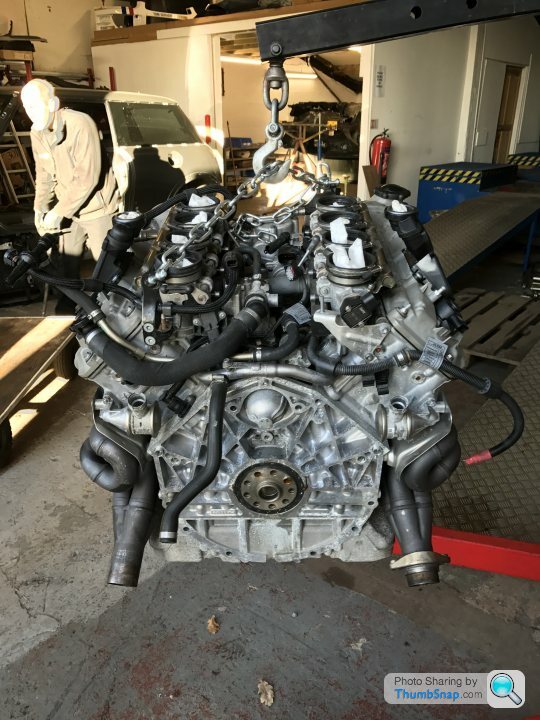
It is at this point that EDM had to stop, sit and think. Measure, guess, stop and think again.
Decisions made now as to engine position and angle would affect everything.
It is no exaggeration to say that a single mistake now could make the whole thing nonviable.
But that mistake might not become apparent for months to come.
The engine has a complex sump with a small clearance gap for the M3 steering rack.
We had to position the engine so that the sump would allow our steering rack to be in that gap.
The position of the rack controls the hub position, but the hub position is controlled by the wheel centre position and that cannot change.
The rack position dictates the wishbone and strut position. So all aspects of the front geometry are controlled by the engine position and height.
The engine angle controls the gearbox centre line, the propshaft and therefore diff position as well as impacting on the rear suspension.
Of course he had to take into consideration the exhaust system and ground clearance.
So it was now time for Eliot to get busy with the can opener.
A fair bit of this bulkead and floor was going to have to go to get the engine as far back as possible and positioned correctly to get the steering rack in place.
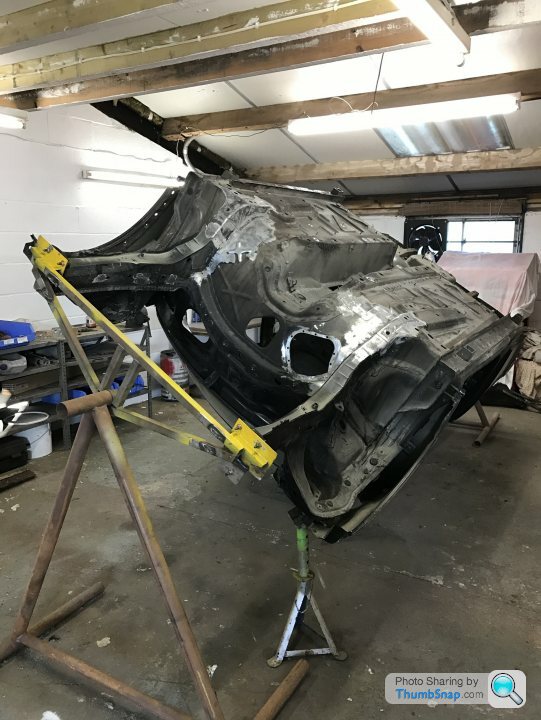
Well, it's in place ish
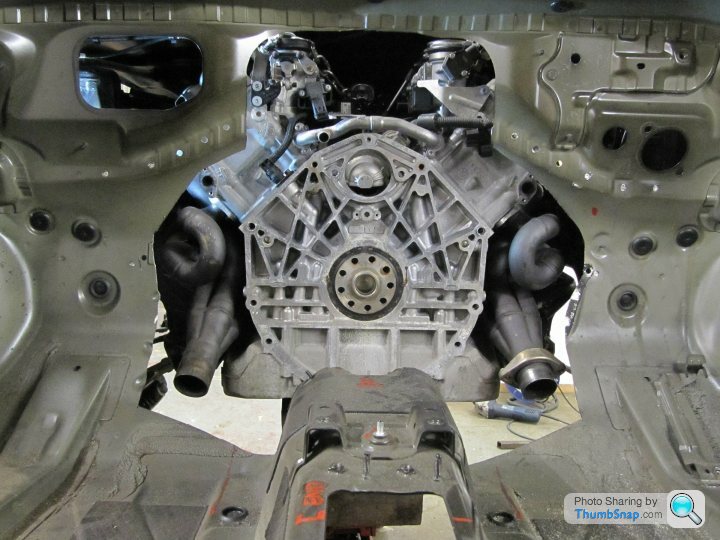
See how much further we've been able to get the engine. (when I say "we" I mean the Royal "we")
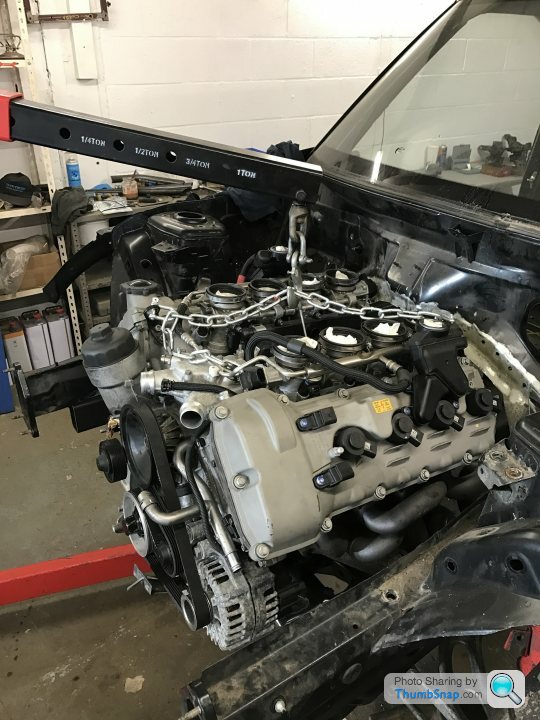
This is just the engine in situ against the bulkhead
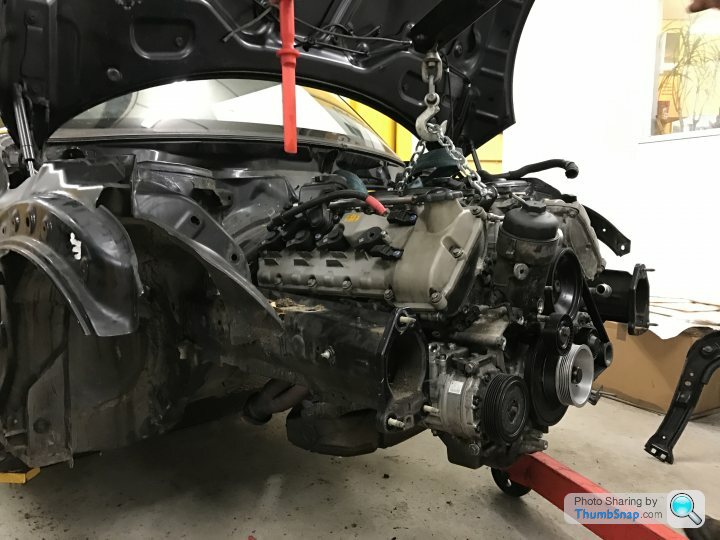
Now we are getting somewhere
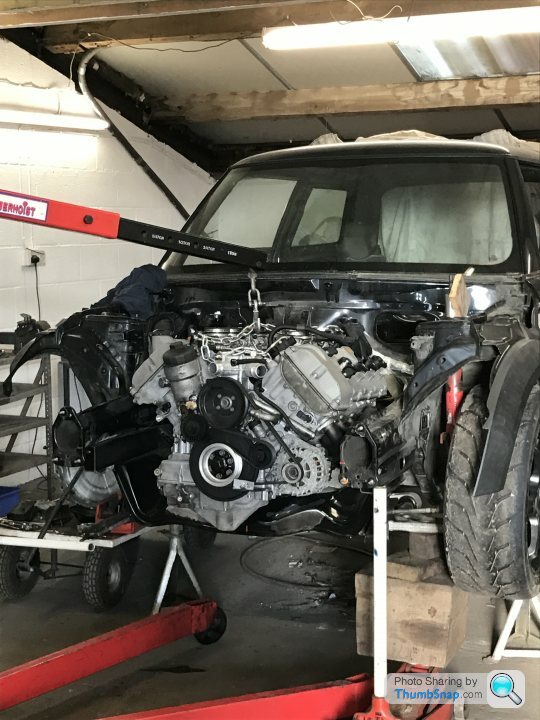
So much further back
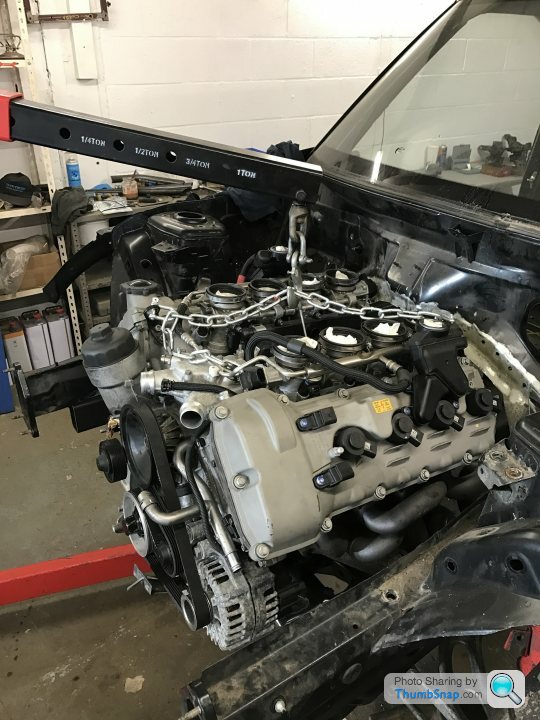
A fair bit of sheel strength gone already and we haven't started removing the floorpan yet
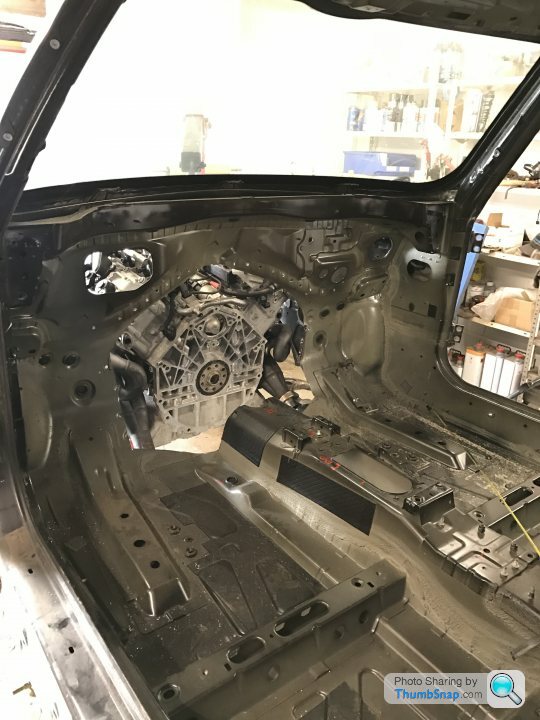
Very complex and efficient sump. We considered a dry sump system but we weren't convinced it would improve matter but it would add complication.
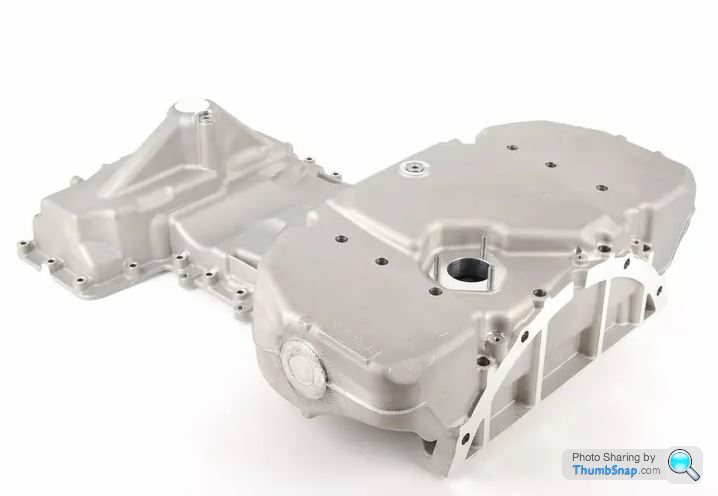
So to engine positioning.
Having described how critical the location of so many components are at this point, a lot of parts had now to be test fitted in a way that would allow some adjustment.
Trying to guess where the front subframe will go.
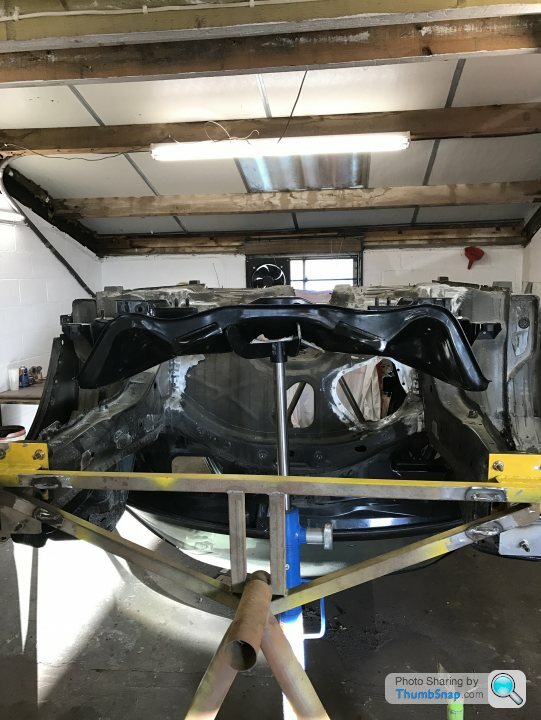
Box sections were tacked into place and the Impreza front subframe and steering rack mount secured in a way that the engine could be bolted in and moved around in all three directions.
Such a difficult thing to do with a heavy engine and things like the wheel position relying on the fit of everything else.
Engine mounted on heavily modified subframe
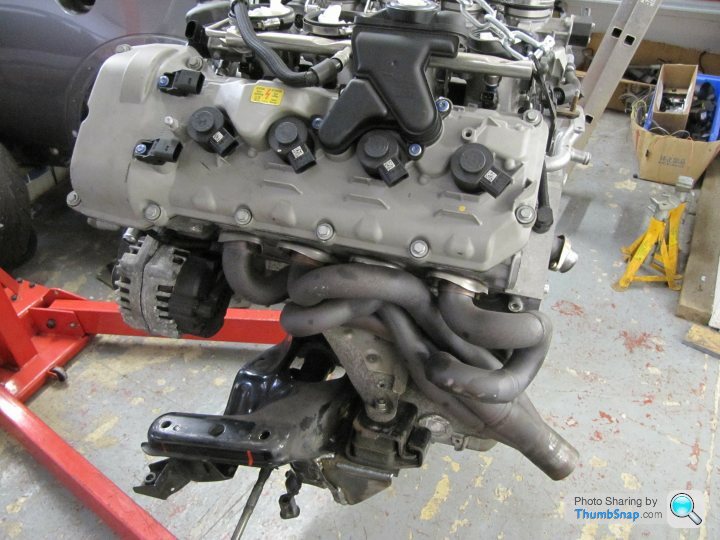
It isn’t easy to find the words to describe how hard this stage was for www.edmotorsport.co.uk
So starting from the wheel centre, the lower wishbone is fitted to the Subaru hub.
Wheel in place for positioning with subframe, rack and lower wishbone
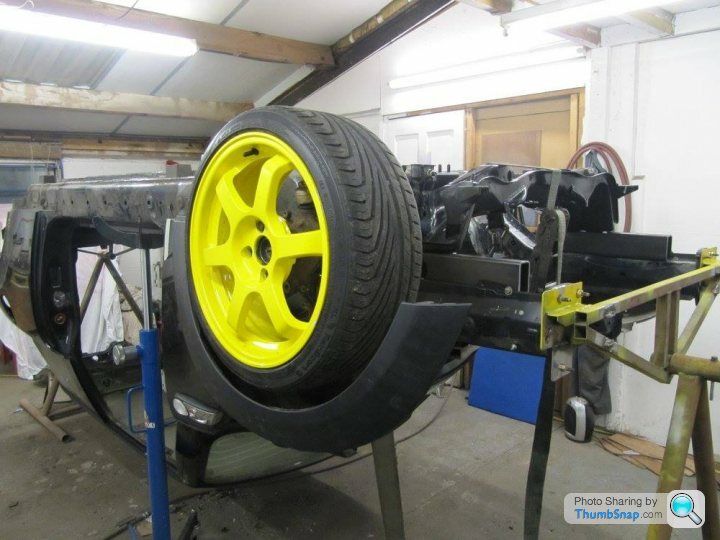
The inner wishbone joint is connected to the subframe and the steering rack is mounted on the subframe.
None of this is adjustable.
These were the fixed control points.
The subframe has to fit in the gap in the sump and the engine has to fit to the subframe.
The engine has to fit in the shell at a height and position to allow the gearbox to be aligned correctly and the drive line from the back of the gearbox has to point somewhere pretty close to where we hope the rear diff might fit.
Plus we need to get the twin exhausts at a height that does not limit ground clearance.
Subframe position reasonably fixed. (box sections will not stay. These are ugly, heavy and only partially fitted for strength)
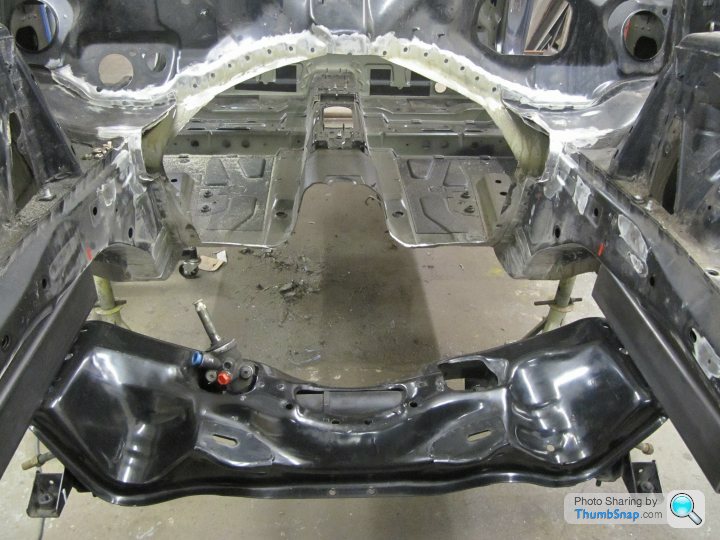
Having described how critical the location of so many components are at this point, a lot of parts had now to be test fitted in a way that would allow some adjustment.
Trying to guess where the front subframe will go.
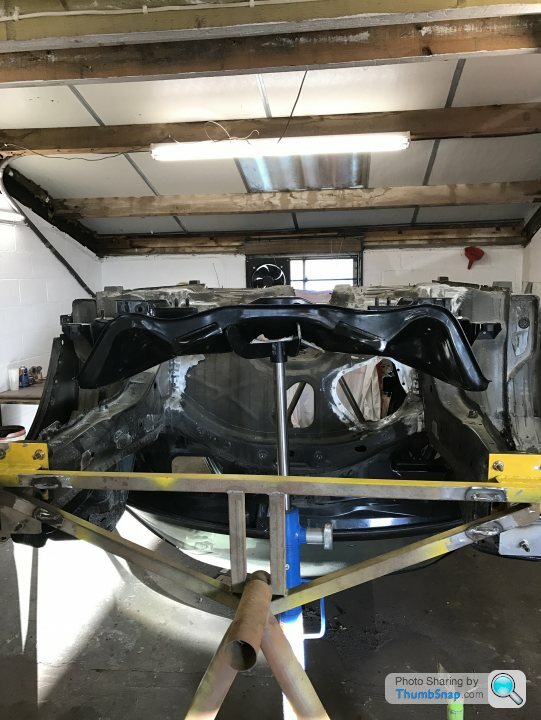
Box sections were tacked into place and the Impreza front subframe and steering rack mount secured in a way that the engine could be bolted in and moved around in all three directions.
Such a difficult thing to do with a heavy engine and things like the wheel position relying on the fit of everything else.
Engine mounted on heavily modified subframe
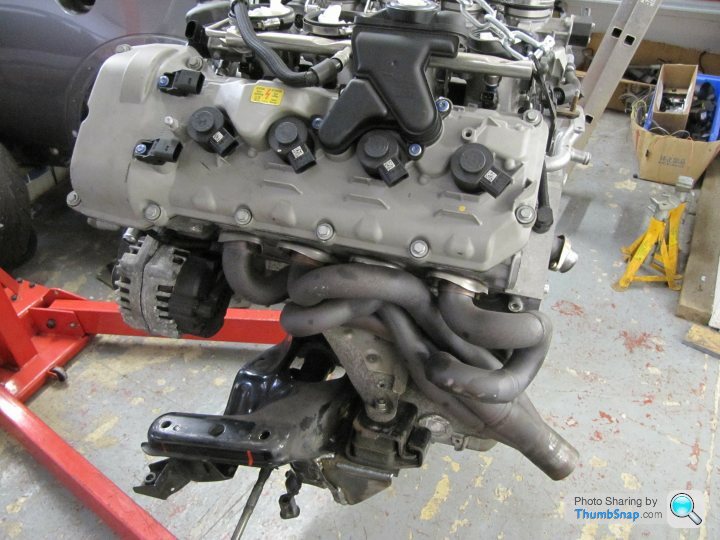
It isn’t easy to find the words to describe how hard this stage was for www.edmotorsport.co.uk
So starting from the wheel centre, the lower wishbone is fitted to the Subaru hub.
Wheel in place for positioning with subframe, rack and lower wishbone
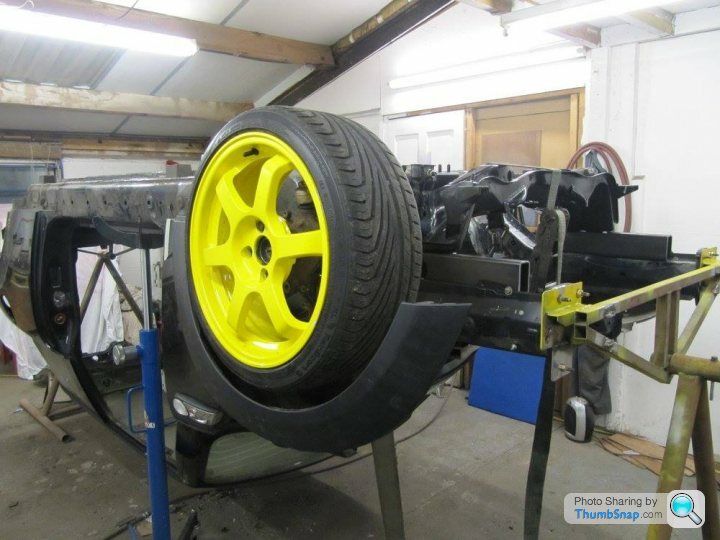
The inner wishbone joint is connected to the subframe and the steering rack is mounted on the subframe.
None of this is adjustable.
These were the fixed control points.
The subframe has to fit in the gap in the sump and the engine has to fit to the subframe.
The engine has to fit in the shell at a height and position to allow the gearbox to be aligned correctly and the drive line from the back of the gearbox has to point somewhere pretty close to where we hope the rear diff might fit.
Plus we need to get the twin exhausts at a height that does not limit ground clearance.
Subframe position reasonably fixed. (box sections will not stay. These are ugly, heavy and only partially fitted for strength)
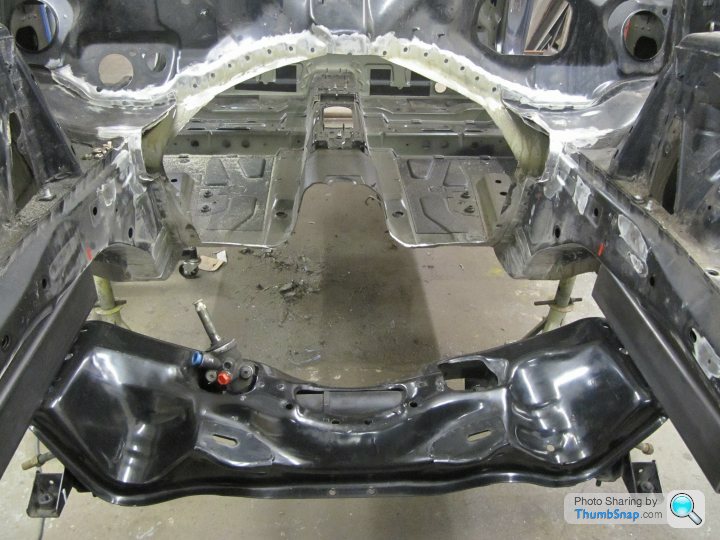
Megaflow said:
Sorry, unless I am being simple, I can't see an explanation for the Subaru suspension being used. There is a detail explanation of why you are fitting it now, to establish hard points and wheel positioning. I am curious why the Mini parts were consigned to the bin.
The Mini being front wheel drive has a completely different set of hard mounting points and the steering rack is mounted on the bulkhead so there was no way to use that. The front suspension struts were in the wrong place and the turrets needed to be moved so there was nothing from the Mini that was usable.It had to be completely changed and the Subaru front subframe turned out to be perfect, but there was still a load of metalwork to be changed to get the geometry correct with the struts we were developing.
Gassing Station | Readers' Cars | Top of Page | What's New | My Stuff