Ideal Camshaft Lobe Centreline Angle
Discussion
Time for a heated debate as Mrs Merton used to say, if anyone remembers that programme.
There's been some discussion on the above topic recently. Most of what you see about it in print has been written by Mr Vizard and his own views on the matter can be read here.
http://www.stockcarracing.com/techarticles/scrp_06...
In essence he believes that the primary determinant of the ideal LCA for a performance cam is the cylinder size divided by the inlet valve diameter (CID/inch) and as that number gets bigger the LCA should decrease and vice versa. It culminates in this graph.
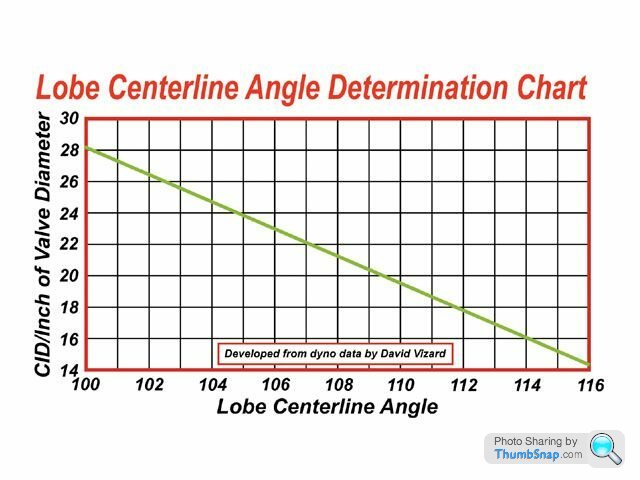
The equation of the line can be calculated as LCA = 132 - (16/14 x CID/inch)
So here's where we get into the heated debate. I submit that the cylinder size / valve size ratio has absolutely nothing to do with LCA, or at least very little and that the graph above is not a determinant of the ideal LCA. Fighting talk eh? Well I'll expound.
Firstly I should say that's it up to DV himself to say whether he claims that graph can be applied to engines other than the Chevy but it would be weird if only that specific engine had some sort of relationship that could be charted that no other engine followed. Anyway I'll assume it is indeed meant to be a universal panacea.
So how does it stack up in practice? There's a well known scientific method of finding out whether a relationship holds true which is to extrapolate that relationship to its extremes. I can't think of any common engine that has a bigger CID/inch than the maximum of 28 shown on the chart but there are lots that have a smaller number than 14, the minimum shown.
Let's start with the humble A series. A 1275cc MG Metro with 35.6mm inlets has a ratio of 14, right at the bottom of the range of values shown. According to the graph it should want an LCA of 116 degrees. Does it? Well there's a very good authority on the matter in the form of a book written by a certain Mr Vizard which states that nearly every Mini engine he ever tested required an LCA in the range 100 to 106 degrees for a performance cam. However the A series is a bit weird in terms of its siamese ports so lets stick with more conventional one port per cylinder engines.
The Peugeot TU 1360 8v engine has 39.3mm inlet valves. That gives it a ratio of 13.4 CID/inch which indicates an LCA of 116.7 degrees. Is that what it really wants? Not on your nelly. 106 to 108 degrees is more like it from the ones I've built as in fact we'll soon see the range 100 to 110 degrees applies to nearly every other engine.
Let's extrapolate further to 16v engines which have even smaller ratios of CID per inch of valve diameter.
The well known Vauxhall XE 16v has 500cc cylinders and 33mm inlet valves. A ratio of 11.7 CID/inch and an LCA of 118.6 degrees from the above equation. A friend dynoed a tuned one some time ago and spent a fair amount of effort on cam swings. He settled on 105 degrees inlet full lift and though I can't recall the exhaust figure it was somewhat similar and the LCA must also have been in that ballpark.
Let's go even further to motorbike engines. The 2005 Honda CBR600RR generates 102 bhp from only 0.6 litres, 170 bhp per litre. Pretty highly tuned in anyone's book. It has 150 cc cylinders and two 27.5mm inlet valves. A CID/inch ratio of a miniscule 4.2 and supposedly an ideal LCA of 127 degrees. What did Honda, who probably did a fair bit of testing, think it wanted. We can look at the specs.
http://www.aperaceparts.com/tech/05cbr600rr.html
The cam timing figures are given and we can calculate that the LCA is 104 degrees and the cams are installed with 3.5 degrees of cam advance. Same ballpark as every other engine as I've already stated.
So what's the message? You can plough through the specs of highly tuned engines ranging from small 4v ones to large 2v ones and in almost every case the ideal LCA stays somewhere around the 105 degree mark plus or minus 5 degrees. It's totally independent of cylinder size or cylinder volume per inch of valve diameter.
Over to you.
There's been some discussion on the above topic recently. Most of what you see about it in print has been written by Mr Vizard and his own views on the matter can be read here.
http://www.stockcarracing.com/techarticles/scrp_06...
In essence he believes that the primary determinant of the ideal LCA for a performance cam is the cylinder size divided by the inlet valve diameter (CID/inch) and as that number gets bigger the LCA should decrease and vice versa. It culminates in this graph.
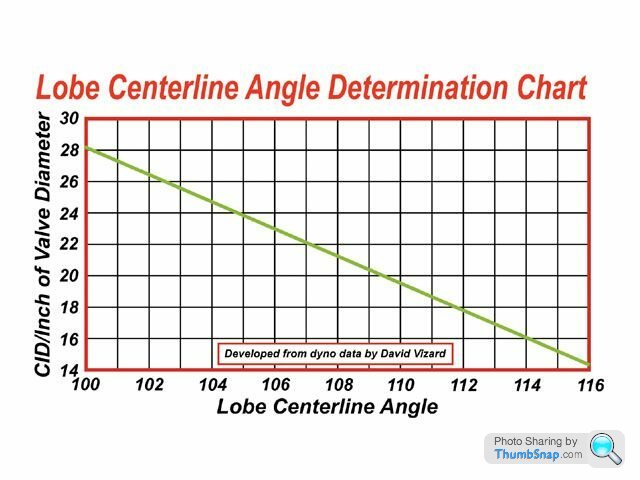
The equation of the line can be calculated as LCA = 132 - (16/14 x CID/inch)
So here's where we get into the heated debate. I submit that the cylinder size / valve size ratio has absolutely nothing to do with LCA, or at least very little and that the graph above is not a determinant of the ideal LCA. Fighting talk eh? Well I'll expound.
Firstly I should say that's it up to DV himself to say whether he claims that graph can be applied to engines other than the Chevy but it would be weird if only that specific engine had some sort of relationship that could be charted that no other engine followed. Anyway I'll assume it is indeed meant to be a universal panacea.
So how does it stack up in practice? There's a well known scientific method of finding out whether a relationship holds true which is to extrapolate that relationship to its extremes. I can't think of any common engine that has a bigger CID/inch than the maximum of 28 shown on the chart but there are lots that have a smaller number than 14, the minimum shown.
Let's start with the humble A series. A 1275cc MG Metro with 35.6mm inlets has a ratio of 14, right at the bottom of the range of values shown. According to the graph it should want an LCA of 116 degrees. Does it? Well there's a very good authority on the matter in the form of a book written by a certain Mr Vizard which states that nearly every Mini engine he ever tested required an LCA in the range 100 to 106 degrees for a performance cam. However the A series is a bit weird in terms of its siamese ports so lets stick with more conventional one port per cylinder engines.
The Peugeot TU 1360 8v engine has 39.3mm inlet valves. That gives it a ratio of 13.4 CID/inch which indicates an LCA of 116.7 degrees. Is that what it really wants? Not on your nelly. 106 to 108 degrees is more like it from the ones I've built as in fact we'll soon see the range 100 to 110 degrees applies to nearly every other engine.
Let's extrapolate further to 16v engines which have even smaller ratios of CID per inch of valve diameter.
The well known Vauxhall XE 16v has 500cc cylinders and 33mm inlet valves. A ratio of 11.7 CID/inch and an LCA of 118.6 degrees from the above equation. A friend dynoed a tuned one some time ago and spent a fair amount of effort on cam swings. He settled on 105 degrees inlet full lift and though I can't recall the exhaust figure it was somewhat similar and the LCA must also have been in that ballpark.
Let's go even further to motorbike engines. The 2005 Honda CBR600RR generates 102 bhp from only 0.6 litres, 170 bhp per litre. Pretty highly tuned in anyone's book. It has 150 cc cylinders and two 27.5mm inlet valves. A CID/inch ratio of a miniscule 4.2 and supposedly an ideal LCA of 127 degrees. What did Honda, who probably did a fair bit of testing, think it wanted. We can look at the specs.
http://www.aperaceparts.com/tech/05cbr600rr.html
The cam timing figures are given and we can calculate that the LCA is 104 degrees and the cams are installed with 3.5 degrees of cam advance. Same ballpark as every other engine as I've already stated.
So what's the message? You can plough through the specs of highly tuned engines ranging from small 4v ones to large 2v ones and in almost every case the ideal LCA stays somewhere around the 105 degree mark plus or minus 5 degrees. It's totally independent of cylinder size or cylinder volume per inch of valve diameter.
Over to you.
Rwdfords said:
I agree with a lot of what both DB and DV say about the optimum LSA to use
That LSA chart is engine specific,
There's a big problem with the theory though if that chart is really only applicable to Chevy engines. If so why? In any case there's really no such thing as "the" Chevy engine. When you factor in the vast range of bore/stroke ratios, cylinder head designs, valve sizes and inlet/exhaust ratios it's just as much a range of different engines as comparing engines from other manufacturers.That LSA chart is engine specific,
A theory that holds water should be universally applicable or at least have a cogent explanation of why it doesn't fit other cases. I suspect something much more complex than just CID/inch versus LCA is going on here.
I think part of the problem is the human tendency to try and fit data to ones pet theory or to ignore tests that don't pan out as being faulty in some way. I can almost guarantee that this whole deal is much more complex than just a straight line chart and if we had access to all the dyno tests it might become more obvious that some sort of curve is the true fit to the data.
It also makes little sense to me that the 104, 106 and 108 degree torque curves in the article I referenced are so close together and then there's a huge jump to the 110 degree one. I don't generally see that happening in other dyno tests.
Finally even with dyno data it's somewhat subjective actually choosing which is the optimum LCA. Again the 106 and 108 degree curves are almost identical so picking one over the other is not really an objective choice.
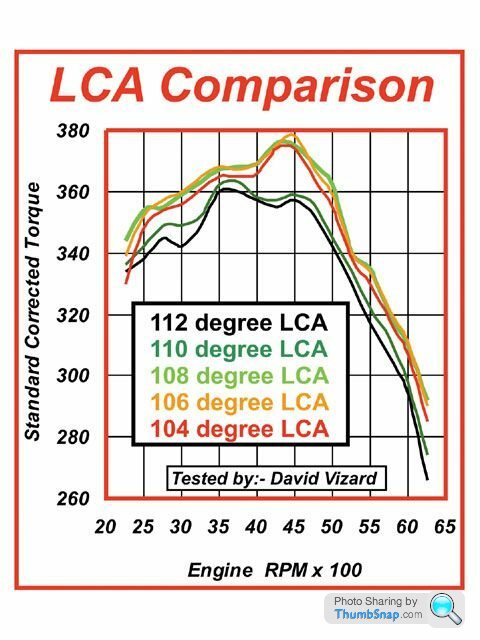
You could just as easily say the 106 degree curve is the optimum one. Usually a small change in LCA adds torque somewhere in the power band and takes it away somewhere else. It doesn't always give a nice clean best / worst situation with a clear winner.
So at the end of the day I can't agree that LCA is the most important factor in cam choice as DV says in various books and articles. Cam duration is far more important IMO and as long as you make sensible choices for LCA you can get right into the ballpark without undue testing.
If I had to pick a single LCA for an unknown engine I'd probably go with around 106 to 107 degrees. I used to use wider angles but I was probably over biased by the volume of literature on the Chevy engine. The famous Chevy tuner Bill Jenkins used to use 109 degrees in every engine he built, big, small, track or drag race. He stuck to it like it was some sort of magic number and I think I was too much influenced by this many years ago.
As DV states it's more important to not pick too wide an angle so even if the ideal was a couple of degrees more than 106/107 you wouldn't be losing much and there are not many engines that want much less than 106 so again you're unlikely to be far out.
Obviously some account has to be taken of CR and other factors but we don't all have the money and resources to test every possible cam so you have to make your best guess and live with it.
My personal opinion is that DV has become somewhat sucked into this issue trying to find a magic rule to quote to the extent that perhaps some objectivity has been lost. I'd like to see the vast amount of data he's no doubt accumulated and cast a fresh eye over it. I bet a pound to a penny I wouldn't fit the data to a chart in the same way or at least nothing as simple as a straight line.
Rwdfords said:
A 2.0 pinto with 44.45mm inlets would be 108* LSA going by the chart which is about optimum I think, and 110* LSA with 46mm inlets, also quite close to what is needed
Geometrically the 2 litre Pinto is almost identical to one half of a 350 Chevy and I'm not just talking about bore/stroke ratio here or indeed anything to do with valve sizes. I'm also not going to say exactly what I am talking about just yet.You can therefore bet with some certainty that it will want a similar LCA. IMO 110 would be far too wide for a long duration cam. I'd go with 107. That's very unlikely to be more than 1 degree out either way.
You need to stop thinking about valve size or CID/inch of valve diameter in relation to selecting an LCA. Trying to find such a relationship is a bit like going on a clitoris hunt. You might suspect one exists but your chances of finding it are very slim.
DVandrews said:
Interesting thread.. looking at the graph, can I assume that the curves are derived from a single camshaft which has the LCA moved around rather than a number of cams with the LCA and lobe separation tailored to suit. If that is the case, what was the lobe separation angle?, where is the notional 'nuetral' position of the cam WRT LCA?. The reason I ask is that moving the LCA on the inlet will have an affect on the exhaust LCA as well. It's one thing to determine the ideal LCA and cut a cam with correct LCA and lobe separation, but another altogether to simply swing an existing cam through an LCA arc as this will move both lobe centres. On twin cam engines there is scope for moving each cam independently to arrive at the optimum for each camshaft. On a single cam engine this needs to be determined before the cam is cut.
As an aside, on many 4 valve engines with long duration cams (275 degrees or above) a lobe centre of 102-104 on the inlet and 104-106 on the exhaust works very well.
Dave
DV and myself are using the term LCA to refer to what you are calling LSA i.e the angle between the inlet lobe peak position and the exhaust lobe peak position. The actual cam timing in terms of advance or retard is given by the inlet full lift position which you are referring to as the LCA.As an aside, on many 4 valve engines with long duration cams (275 degrees or above) a lobe centre of 102-104 on the inlet and 104-106 on the exhaust works very well.
Dave
Maybe both myself and DV should start using the term LSA to refer to what we have previously called LCA. If he will I will.
Workshop said:
Thanks David, it was really just a stab in the dark while I was having a coffee before I went to work. Really there was no sense trying to adapt CFM to the formula because I have no idea why it is multiplied by 16/14 and then 132 subtracted by it in the first place.
I afraid I assumed everyone would know how to generate the equation of a straight line graph but I suppose I do take maths for granted somewhat. It should be apparent that the LCA rises by 16 degrees as the CID/inch falls by 14 (from 28 to 14). The slope of the line is therefore -16/14 x CID/inch.It should also be clear that the line intersects the X axis at an LCA of 132. The LCA has risen from 100 to 116 as the CID/inch falls from 28 to 14 so a drop in CID/inch of another 14 to zero would add 16 more to the LCA. 116 + 16 = 132.
So the equation of the line is 132 - (16/14 x CID/inch).
So when CID/inch is zero then LCA must be 132 which it is. When CID/inch is 28 then LCA = 132 - (28 x 16/14) = 100 which again it is and similarly for any value in between or even either side of those.
However given we've established that LCA is not dependent on CID/inch in the first place it's sort of academic.
Rwdfords said:
6. Valve size, this has a direct effect on low lift flow which increases the overlap flow with a given camshaft as compared to the same engine with smaller valves
You have to be extraordinarily careful when making assumptions about how one thing affects another thing that some of the factors haven't been missed.If you increase valve size then you increase overlap flow but you also increase cylinder filling, which of course then requires more overlap flow to evacuate it and the factors cancel out.
Something I'll bet very few have ever realised is that you automatically change the ratio of low lift to high lift flow simply by changing valve size.
A 25mm diameter valve has an area of 25 x 25 x pi / 4 = 491 mm^2. The ratio of area to diameter is 19.6
Double the valve size to 50mm. The area is now 1963 mm^2 and the ratio of area to diameter is 39.3
So a small valve has more diameter (or circumference) for a given head area than a large one and with a cam of the same lift will have a different ratio of low lift to high lift flow. Swap one large valve for two small ones of the same total area and the effect multiplies. However if more low lift flow required a change in the LSA then small 4v engines would have radically different numbers than large 2v ones yet they don't. It all cancels out in the wash.
What the flow per cc does tell you is how much cam duration you need for a given state of tune.
A big factor that affects optimum LSA is the rod / stroke ratio and that is what I was referring to when I said the Pinto was geometrically similar to the 350 Chevy. That's the subject I'll get into in detail if I get time.
Edited by Pumaracing on Friday 27th January 00:15
I think most people who haven't studied engines in depth could be forgiven for assuming that the motion of the piston up and down the bore is somewhat symmetrical. That it sets off from TDC at a certain acceleration, reaches peak velocity half way down the bore and then slows down in a similar fashion to reach BDC.
Well nothing could be further from the truth. In a real engine due to the complex nature of the rod / crank geometry the piston accelerates away from TDC nearly twice as fast as it accelerates away from BDC. It reaches peak velocity in as little as 70 degrees from TDC and then spends the next 110 degrees slowing back down. This behaviour changes as the length of the conrod varies proportionate to the crank stroke. The longer the rod / stroke ratio the slower the piston accelerates away from TDC and the faster it approachs BDC. Only with an infinitely long conrod would the motion finally become symmetrical with peak velocity half way down the bore and the same acceleration at TDC and BDC.
The graph below shows how the acceleration changes as the rod/stroke ratio changes.
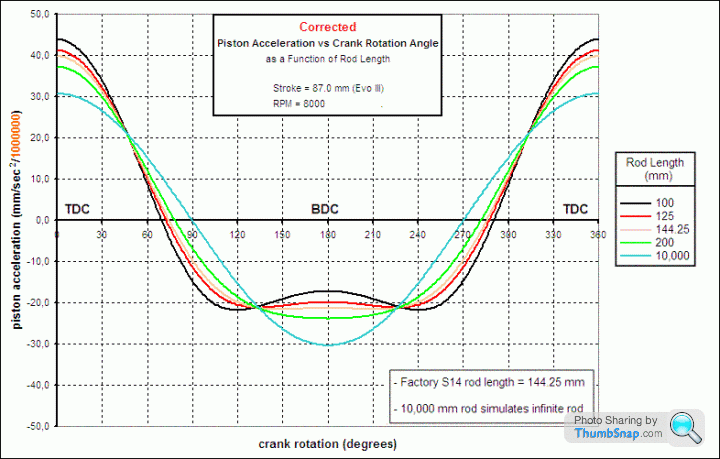
With ratios below about 1.6 the behaviour near BDC is quite bizarre and the acceleration curve is W shaped with two minima either side of BDC. Anyway that doesn't need to concern us for now.
What does need to be understood is that as the rod / stroke ratio increases the piston will always be slightly higher up the bore at any given crank angle away from TDC than it would be with a lower ratio.
Real world rod / stroke ratios range from a low of about 1.4 to a high of about 2.4 although there is no upper limit if the designer so chooses. Most production car engines have ratios in the range 1.55 to 2.0. The longest ratio in common use I know of is the old 2.9 litre straight 6 Jaguar XJ6 engine which has a ratio of 2.34. The 2.0 Pinto and 350 Chevy are both around 1.65, the 1275 A series is 1.8, the MGB even higher at 1.86 and very high rpm engines like the CBR600RR I mentioned previously tend to have ratios over 2 to minimise thrust forces against the bore and piston accelerations at TDC. The Honda actually has a ratio of 2.16.
The magnitude of the change in piston position when the rod ratio changes from the very low (1.4) to the comparitively high (2.20) is about 4 degrees of crankshaft movement.
So what effect does all this have on cam timing? Let's imagine we have an engine with a very low rod ratio, say 1.45, and we have optimised the cam events. Now we change the engine to have a very high rod ratio of say 2.20.
Assume our cam is the old faithful fast road profile from the 1950s that was always known as the 30/60 60/30 profile. This means it has a duration of 270 degrees, is timed straight up i.e. no advance or retard and has an LSA of 105 degrees.
Starting with the exhaust valve opening event. This occurs at 60 degrees BBDC which on the short rod engine represented a specific piston position a certain distance from BDC. However on the long rod engine the piston will be higher up the bore at the same crank angle. It will take another 4 crank degrees before it reaches the same distance away from BDC. So to compensate we need to open the exhaust valve 4 degrees LATER, at 56 degrees BBDC.
The inlet valve close shows a similar story. The piston position at 60 degrees ABDC will now occur at 56 degrees ABDC on the long rod engine so we need to close the inlet valve 4 degrees EARLIER.
We find the same story at the inlet valve opening and exhaust closing points. The inlet needs to open earlier and the exhaust close later.
So our 270 degree cam now becomes a 34/56 56/34 profile which means the LSA has narrowed to 101 degrees.
So there's our golden rule with rod / stroke ratios. The higher the ratio the smaller the LSA needs to be. As an approximation every 0.15 points change in ratio needs about 1 degree change in LSA. It's not an absolute and the effect varies somewhat with cam duration but that'll get you in the ballpark.
So taking our starting point as the Pinto engine with a 1.65 ratio and a theoretical 107 degree LSA then moving to the A series engine we'd theoretically need to narrow the LSA to 106 degrees. Moving further to the 2.16 ratio of the Honda CBR we'd need to knock another 2 degrees off to get to 104 degrees LSA. Now go back to my previous post and see what those engines actually had.
Now of course like anything engine related it's not quite as simple as that but that's enough complexity for now.
I suppose my closing views on LSA is it's not really such a big deal if you apply sensible rules. In fact I find that the cam offerings from most manufacturers do put you somewhere close to what you really need. For most people who don't have access to unlimited dyno time you'll never know how far out you were and comparing to other people's engines will simply lose any observable cam effects in the variations in head flow, induction and exhaust system differences etc.
I'm not saying the cam companies know everything, or even very much at all about how engines work, but over the decades what works and what doesn't has filtered down until you see a general consensus in most cam grinds. Stock road profiles have wider LSAs, say 110-112 degrees, to give good idle and low rpm manners. By the time durations have increased to fast road / rally profiles the LSA narrows down a bit by 3 degrees or so. Full race narrows even further usually. It might not be perfect but if your engine has a good head, the right CR and a decent quality build I've never found the cam to be the determinant of whether it'll win or not. I usually plump for a bit less duration than most people think they need and build an engine with stonking torque and easy driveability. If the driver can pedal that properly and the engine has one of my heads on it he'll win more often than not.
Well nothing could be further from the truth. In a real engine due to the complex nature of the rod / crank geometry the piston accelerates away from TDC nearly twice as fast as it accelerates away from BDC. It reaches peak velocity in as little as 70 degrees from TDC and then spends the next 110 degrees slowing back down. This behaviour changes as the length of the conrod varies proportionate to the crank stroke. The longer the rod / stroke ratio the slower the piston accelerates away from TDC and the faster it approachs BDC. Only with an infinitely long conrod would the motion finally become symmetrical with peak velocity half way down the bore and the same acceleration at TDC and BDC.
The graph below shows how the acceleration changes as the rod/stroke ratio changes.
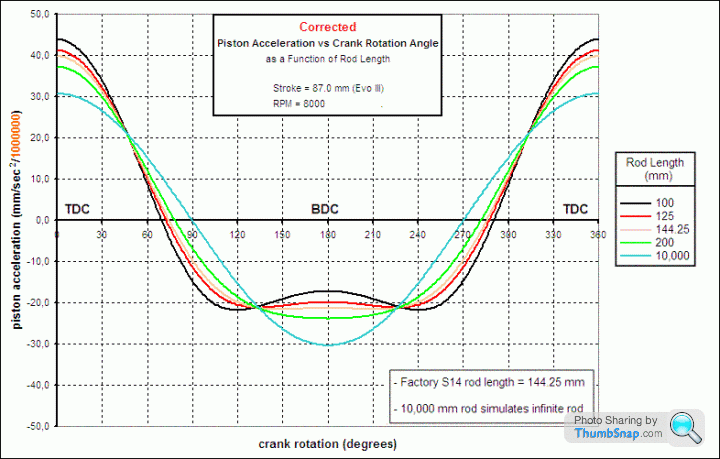
With ratios below about 1.6 the behaviour near BDC is quite bizarre and the acceleration curve is W shaped with two minima either side of BDC. Anyway that doesn't need to concern us for now.
What does need to be understood is that as the rod / stroke ratio increases the piston will always be slightly higher up the bore at any given crank angle away from TDC than it would be with a lower ratio.
Real world rod / stroke ratios range from a low of about 1.4 to a high of about 2.4 although there is no upper limit if the designer so chooses. Most production car engines have ratios in the range 1.55 to 2.0. The longest ratio in common use I know of is the old 2.9 litre straight 6 Jaguar XJ6 engine which has a ratio of 2.34. The 2.0 Pinto and 350 Chevy are both around 1.65, the 1275 A series is 1.8, the MGB even higher at 1.86 and very high rpm engines like the CBR600RR I mentioned previously tend to have ratios over 2 to minimise thrust forces against the bore and piston accelerations at TDC. The Honda actually has a ratio of 2.16.
The magnitude of the change in piston position when the rod ratio changes from the very low (1.4) to the comparitively high (2.20) is about 4 degrees of crankshaft movement.
So what effect does all this have on cam timing? Let's imagine we have an engine with a very low rod ratio, say 1.45, and we have optimised the cam events. Now we change the engine to have a very high rod ratio of say 2.20.
Assume our cam is the old faithful fast road profile from the 1950s that was always known as the 30/60 60/30 profile. This means it has a duration of 270 degrees, is timed straight up i.e. no advance or retard and has an LSA of 105 degrees.
Starting with the exhaust valve opening event. This occurs at 60 degrees BBDC which on the short rod engine represented a specific piston position a certain distance from BDC. However on the long rod engine the piston will be higher up the bore at the same crank angle. It will take another 4 crank degrees before it reaches the same distance away from BDC. So to compensate we need to open the exhaust valve 4 degrees LATER, at 56 degrees BBDC.
The inlet valve close shows a similar story. The piston position at 60 degrees ABDC will now occur at 56 degrees ABDC on the long rod engine so we need to close the inlet valve 4 degrees EARLIER.
We find the same story at the inlet valve opening and exhaust closing points. The inlet needs to open earlier and the exhaust close later.
So our 270 degree cam now becomes a 34/56 56/34 profile which means the LSA has narrowed to 101 degrees.
So there's our golden rule with rod / stroke ratios. The higher the ratio the smaller the LSA needs to be. As an approximation every 0.15 points change in ratio needs about 1 degree change in LSA. It's not an absolute and the effect varies somewhat with cam duration but that'll get you in the ballpark.
So taking our starting point as the Pinto engine with a 1.65 ratio and a theoretical 107 degree LSA then moving to the A series engine we'd theoretically need to narrow the LSA to 106 degrees. Moving further to the 2.16 ratio of the Honda CBR we'd need to knock another 2 degrees off to get to 104 degrees LSA. Now go back to my previous post and see what those engines actually had.
Now of course like anything engine related it's not quite as simple as that but that's enough complexity for now.
I suppose my closing views on LSA is it's not really such a big deal if you apply sensible rules. In fact I find that the cam offerings from most manufacturers do put you somewhere close to what you really need. For most people who don't have access to unlimited dyno time you'll never know how far out you were and comparing to other people's engines will simply lose any observable cam effects in the variations in head flow, induction and exhaust system differences etc.
I'm not saying the cam companies know everything, or even very much at all about how engines work, but over the decades what works and what doesn't has filtered down until you see a general consensus in most cam grinds. Stock road profiles have wider LSAs, say 110-112 degrees, to give good idle and low rpm manners. By the time durations have increased to fast road / rally profiles the LSA narrows down a bit by 3 degrees or so. Full race narrows even further usually. It might not be perfect but if your engine has a good head, the right CR and a decent quality build I've never found the cam to be the determinant of whether it'll win or not. I usually plump for a bit less duration than most people think they need and build an engine with stonking torque and easy driveability. If the driver can pedal that properly and the engine has one of my heads on it he'll win more often than not.
DVandrews said:
You could look at it that way if you look at open/close events and piston position only, hoewever, coinciding maximum lift with maximum draw on the cylinder would suggest moving in the opposite direction.
Then you'd first have to come up with a convincing argument why having maximum valve lift closer to peak piston speed makes any difference. In the average engine the piston reaches peak velocity at about 75 degrees ATDC. The inlet valve is not fully open until about 30 degrees later which is a long way apart. If matching those events was a big deal camshafts would be radically different.The piston generates a finite amount of depression as it sweeps from TDC to BDC. If the cylinder fills a bit worse at the start it will have a higher pressure differential over the inlet port later and flow more as the valve closes. If it fills well at the start it will flow less later. Swings and roundabouts tend to even all this out.
However at inlet valve close for example the valve wants to close at a certain cylinder pressure which balances the incoming charge momentum down the inlet port. Close too late and reverse flow will occur. That's determined by piston position which is in turn determined by rod / stroke ratio. Same applies to exhaust valve opening. You want to strike a balance between extracting energy from the burning charge and getting the exhaust gases out later. Piston position is key to all this.
At the end of the day you can posit any arguments you like but when Bill Jenkins went through all this on the dyno and race track in the 70s with the Chevy engine he found empirically that long rods wanted narrow LSAs and vice versa. I believe my argument explains this from simple first principles.
If you want to posit an argument that flies in the face of empirical testing it had better be a very good argument.
DVandrews said:
At this moment I am working on another engine where the rod ratio will be changing from 1.78 to 1.5 (a stroke increase) all other factors will remain the same. The cam timing was optimised on the dyno and gave the best curve at 106 ATDC, 108 BTDC. When the engine is converted I would normally advance the inlet cam by 2-3 degrees or so and retard the exhaust cam by a similar amount, this would bring the LSA in by around 2-3 degrees, normally this will give the best results.
I will ensure that when this engine is mapped I will first try widening the LSA to see what sort of result it gives.
What you are doing here is not quite the same situation as Jenkins was facing though. If you increase capacity but leave the head and cam alone then the engine will not rev so high, the powerband will shrink and the cam is now effectively a milder one than it was on the smaller engine. Jenkins was trying to get the most power out of every engine in every situation.I will ensure that when this engine is mapped I will first try widening the LSA to see what sort of result it gives.
For example in 354 cubic inch drag engines he used 290 degrees of inlet duration, in the 330 that dropped to 286 degrees and in the 302 to 282 degrees. His findings on LSA were in terms of what worked best after he'd reoptimised the state of tune for the different capacity. The more flow per cc the less cam duration is needed.
In fact he preferred smaller capacity bottom ends for drag use because they revved higher and gave more power. Track engines would not sustain such high rpm for extended periods though so he made the bottom ends bigger to bring the rpm down and increase reliability.
So it's quite possible you won't find the same solution on LSA if you leave cam duration alone as if you changed duration at the same time as the capacity.
Edited by Pumaracing on Saturday 28th January 07:49
Rwdfords said:
That LSA chart is engine specific,
Having found "How to Build Horsepower" on Google books..http://books.google.co.uk/books?id=OAw1GDB0kN0C&am...
it would seem no it isn't. According to the text on the page above and below it's meant to be applicable to any parallel valve 2v engine or indeed supposedly any 4v one with a modified head with good valve seats. Not sure why the modified head is necessary.
So given we've established it only works for the Chevy size engines it was based around anyway for which it generally predicts LSAs between 105 and 110 degrees as any other engine would want and goes haywire for anything smaller like the A series or a bike engine I think that's the last nail in the coffin for CID/inch of valve diameter and back to the drawing board for Mr V.
BTW, for anyone who thinks I'm having a right old pop at the Viz with no prior warning I emailed him all this privately two years ago when he first drew my attention to the graph, the CID/inch theory and the supposed magic number of 128 for predicting cam LSA. I said it didn't work then and I stick to that now.
So we're left with some critical thinking to do. If LSA does not respond to valve size per cc i.e. therefore also flow per cc what else apart from rod / stroke ratio does it respond to if anything? Are the dyno tests that show it changing a bit as engine capacity changes for a given head just white noise? If flow doesn't matter than surely rocker ratio doesn't either because that just alters overlap flow. How about CR? Is that a real influence?
Thinking hats on people.
I have a few ideas but I think it's time for a detailed response by DV first.
stevesingo said:
Just in case it may help you theorise this engine:
Bore+95mm
Inlet cam 272, 11.5 lift timed peak lift at 106
Exhuast cam 248 105mm lift timed 106
Inlet valve 38.5mm, Exhaust 32mm
Inlet port flow 264cfm@ 0.400" lift @ 28"
Inlet port flow 268cfm@ 0.450" lift @ 28"
Not sure what you're asking me if anything. The head flow is pretty grim for those valve sizes. Clearly it's a stock head with a discharge coefficient of only 0.5. If that could be raised to 0.6 there'd be a bunch of power to come. Well, 20% obviously or at least something close to that and that's before sticking some decent cams in it which would add another 10% or more. I've never met a 4v head I couldn't get up to a Cd of 0.6 or thereabouts.Bore+95mm
Inlet cam 272, 11.5 lift timed peak lift at 106
Exhuast cam 248 105mm lift timed 106
Inlet valve 38.5mm, Exhaust 32mm
Inlet port flow 264cfm@ 0.400" lift @ 28"
Inlet port flow 268cfm@ 0.450" lift @ 28"
I'd be looking at about 70 to 75 bhp per cylinder in road tune for something like that and 90 in race trim.
Workshop said:
Are you basing the LSA of 107 for a 1.65 rod ratio starting point on the best LSA you have found for the Pinto engine ?
Yes. For high duration cams anyway. The Sig Erson 134 grind was a cracking cam for road vehicles with 500 thou lift from 276 degrees on a 110 LSA but it wore out like buggery. Piper and Kent used to do a copy, probably still do but smaller LSAs work better on longer duration cams.Edited by Pumaracing on Saturday 28th January 08:35
David Vizard said:
AS usual Dave there is no fast answer to the wealth of comments you have thrown out there for, not just me but us all to contemplate. I have answers that will be seen to fit and explain some of the apparent anomalies you raise.
We are hoping you will raise these then so we can discuss the issue in more depth on here. I'm sure the readers will appreciate a more detailed understanding of LSAs and which engine factors really affect it. I have a vast amount of calculation and analysis on this subject but I'm not just going to put it all out there for no return unless we get into a mutual discussion of the topic.jmm25577 said:
Guys been reading with with great interest and finding the input invaluable. David I carried your aseries boook everywhere in my Mini days, a legendary piece of literature! Currently rebuilding my ff2000 pinto and thinking of trying to change the standard LCA of 113 degrees, I figured this could be altered by playing around with valve seat height, valve legnths and rockers although min valve lengthhas to be 110.55mm. Obviously there will be a trade off with lift in one direction or LCA in the other. I thought 110 LCA and sacrifice some lift? Other alternative is go to 115 to get max lift with min legnth valves? Compression is 9.9-1. Jim
I would maximise the lift and not worry about the LSA if you are forced to use a stock cam. Re your email I'm moving house at the moment and won't be set up again for probably some months but I'll notify when I'm taking orders again on the site.Very interesting. I didn't realise that pin offset actually changed the stroke even if only by an immaterial amount. However the change in crank angle for a given piston position is almost enough to merit factoring in to cam timing calculations.
But, please don't go too mad in future on the quantity of graphs. It's a lot for someone new coming to the topic to have to plough through to find the bits that actually relate to LSA.
But, please don't go too mad in future on the quantity of graphs. It's a lot for someone new coming to the topic to have to plough through to find the bits that actually relate to LSA.
Incorrigible said:
I'm finding this thread very interesting, however I'm having trouble understanding what's happening to the piston in this graph with a short rod just before BDC. The graph implies it starts accelerating upwards before BDC (and down again after)
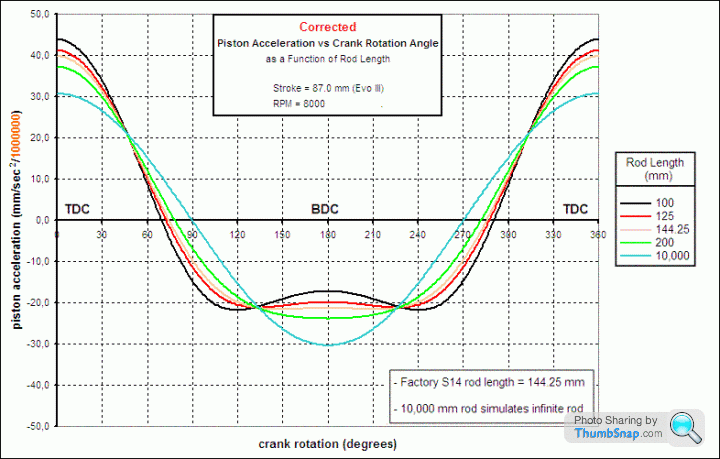
If someone could explain I would be gratefull
Prepares himself for "you thicky" comments
You thicky! Better?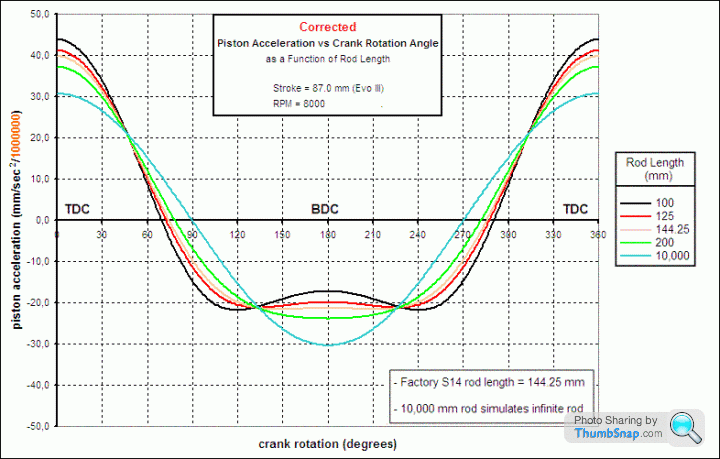
If someone could explain I would be gratefull
Prepares himself for "you thicky" comments
Anyhoo, it's actually very simple. Acceleration away from TDC is considered positive i.e. a value greater than zero. Acceleration towards TDC is considered negative i.e. a value less than zero. This is quite arbitrary and could be shown as the opposite of course.
The piston starts off from TDC with high positive acceleration which gradually reduces until the piston reaches maximum speed. Clearly when speed is at its maximum then acceleration is zero or speed would still be changing. This point occurs as the line crosses the X axis.
Now the piston starts slowing down as it approaches BDC. In car terms it would be braking so acceleration is negative with respect to TDC. Braking reaches its maximum intensity with a short rod some distance before BDC rather than exactly at it. Basically like lifting off the brakes just a bit before coming to a stop but the car is still slowing down constantly.
The second half of the curve is just the mirror image of the first. The piston accelerates away from BDC i.e. towards TDC so the value is still negative. Only acceleration away from TDC is positive. Speed reaches its maximum again where the curve crosses the X axis and then the piston slows down again. It's now like the car braking but in the direction away from BDC which is the same thing as accelerating away from TDC i.e. a positive value.
Imagine a car with the same number of reverse gears as forward ones sat on a straight test track. It accelerates off the line, reaches maximum speed, brakes to a stop and then the driver instantly slams it into reverse and starts off back up the track, reaches top speed again and then brakes to a halt back at the start line.
When the car is either accelerating away from the start line or braking towards it the value of the acceleration is positive.
When the car is either accelerating away from the finish line or braking towards it the value of the acceleration is negative.
DV, thank you for your detailed response to the issues raised in this thread. I'll get back on this once I've had time to compose a comprehensive reply with graphs and maths. Firstly though I'm not doubting your empirical results on Chevy engines and those with similar cylinder sizes albeit I don't have the data to study. However I'll reiterate my thoughts on why CID/inch doesn't affect LSA.
When we go from very large 2v cylinders (24 CID/inch of valve diameter) to very small 4v ones (4 CID/inch) the LSA stays essentially invariant. It's always in the region of 105 degrees plus or minus a few degrees. If we can change the CID/inch by a factor of 6 and the LSA doesn't alter much then we MUST conclude that the two are not related.
To fully answer all this we have to perform the scientific method of extrapolating to extremes. We must consider engine designs at opposite ends of the spectrum and then see if those in the middle fit any theory.
In considering all this I took three situations.
1) Taking a 2v engine and comparing it to a 4v engine with the same valve area per cc. i.e. one engine had a single large inlet valve of diameter X and the other had the same bore and stroke and two smaller inlet valves of diameter X / 1.414 (root 2). Both engines have similar peak flow but the 4v engine has 1.414 times the low lift flow. The LSA stayed constant.
2) Changing the bottom end capacity under a given cylinder head. The LSA stayed constant.
3) Increasing the cam duration radically in a given engine. The LSA stayed constant.
I'll work through the maths in due course.
If Chevy (or other V8) engines need different LSAs as the capacity varies then we need to find a real reason as the CID/inch variable doesn't fit the theory or the empirical results.
If you want a single factor to think about before I respond fully it's time. As engine rpm increases time to do anything decreases. Put a bigger bottom end under a given cylinder head and rpm at peak power decreases and time per cycle increases. The overlap triangle is not just a matter of flow area it's a matter of time for that flow to take place. That single factor cancels out most of the effects you believe make CID/inch a determinant in specifying LSA.
Once I've run through all the maths you'll see why time is the single biggest factor in determining ideal LSA and how it cancels out all the other factors and why LSA stays pretty much invariant.
When we go from very large 2v cylinders (24 CID/inch of valve diameter) to very small 4v ones (4 CID/inch) the LSA stays essentially invariant. It's always in the region of 105 degrees plus or minus a few degrees. If we can change the CID/inch by a factor of 6 and the LSA doesn't alter much then we MUST conclude that the two are not related.
To fully answer all this we have to perform the scientific method of extrapolating to extremes. We must consider engine designs at opposite ends of the spectrum and then see if those in the middle fit any theory.
In considering all this I took three situations.
1) Taking a 2v engine and comparing it to a 4v engine with the same valve area per cc. i.e. one engine had a single large inlet valve of diameter X and the other had the same bore and stroke and two smaller inlet valves of diameter X / 1.414 (root 2). Both engines have similar peak flow but the 4v engine has 1.414 times the low lift flow. The LSA stayed constant.
2) Changing the bottom end capacity under a given cylinder head. The LSA stayed constant.
3) Increasing the cam duration radically in a given engine. The LSA stayed constant.
I'll work through the maths in due course.
If Chevy (or other V8) engines need different LSAs as the capacity varies then we need to find a real reason as the CID/inch variable doesn't fit the theory or the empirical results.
If you want a single factor to think about before I respond fully it's time. As engine rpm increases time to do anything decreases. Put a bigger bottom end under a given cylinder head and rpm at peak power decreases and time per cycle increases. The overlap triangle is not just a matter of flow area it's a matter of time for that flow to take place. That single factor cancels out most of the effects you believe make CID/inch a determinant in specifying LSA.
Once I've run through all the maths you'll see why time is the single biggest factor in determining ideal LSA and how it cancels out all the other factors and why LSA stays pretty much invariant.
David Vizard said:
DB post.---- Taking a 2v engine and comparing it to a 4v engine with the same valve area per cc. i.e. one engine had a single large inlet valve of diameter X and the other had the same bore and stroke and two smaller inlet valves of diameter X / 1.414 (root 2). Both engines have similar peak flow but the 4v engine has 1.414 times the low lift flow. The LSA stayed constant.
Dave,
you have to look more at the valve circumference of the single vs the two intakes not the area as this does not figure into the overlap situation.
DV
You need to read what I wrote and think about it again.Dave,
you have to look more at the valve circumference of the single vs the two intakes not the area as this does not figure into the overlap situation.
DV
Gassing Station | Engines & Drivetrain | Top of Page | What's New | My Stuff