BMW iX electrically excited motors
Discussion
Any thoughts on this, max_torque?
Seams a step backwards to old school synchronous motors with wound fields, presumably rotating so need brushes or rotating rectifier and a distinct rotor exciting stator (like aircraft alternators).
Peak field strengths presumably higher allowing higher torque for the initial get away. And greater flexibility for field weakening and optimising efficiency.
Most EVs use rare earth permanent magnets with a significant minority notably Tesla using induction machines.
Seams a step backwards to old school synchronous motors with wound fields, presumably rotating so need brushes or rotating rectifier and a distinct rotor exciting stator (like aircraft alternators).
Peak field strengths presumably higher allowing higher torque for the initial get away. And greater flexibility for field weakening and optimising efficiency.
Most EVs use rare earth permanent magnets with a significant minority notably Tesla using induction machines.
I don't have the knowledge to comment on the design itself - but I work across several brands in the automotive industry and BMW's motor design is apparently less reliant on expensive/rare materials and also, subsequently, cheaper. Hence why the i4 M50 has a second motor and way more power then it's little brother for a very modest premium - given that it comes with a lot of extra kit too.
I guess we have many years to wait to see whose EV motor designs are superior. We're ten years in now and it's not as if this section of the forum is full of EV drivers moaning about needing motor replacements.
I type this as an iPace driver - JLR developed their own motor and I find it hard to believe it's the most efficient or reliable design, because they're a chicken scratch outfit in the face of the global giants. The only problems reported to date however is that very brutal driving has lead to some cars needing to have the mounts replaced to stop 'clunking' when pulling away under full throttle. Or whatever we call a throttle in an EV..
I guess we have many years to wait to see whose EV motor designs are superior. We're ten years in now and it's not as if this section of the forum is full of EV drivers moaning about needing motor replacements.
I type this as an iPace driver - JLR developed their own motor and I find it hard to believe it's the most efficient or reliable design, because they're a chicken scratch outfit in the face of the global giants. The only problems reported to date however is that very brutal driving has lead to some cars needing to have the mounts replaced to stop 'clunking' when pulling away under full throttle. Or whatever we call a throttle in an EV..
granada203028 said:
Any thoughts on this, max_torque?
Seams a step backwards to old school synchronous motors with wound fields, presumably rotating so need brushes or rotating rectifier and a distinct rotor exciting stator (like aircraft alternators).
Peak field strengths presumably higher allowing higher torque for the initial get away. And greater flexibility for field weakening and optimising efficiency.
Most EVs use rare earth permanent magnets with a significant minority notably Tesla using induction machines.
The wound-rotor design is slightly less power dense than the currently prevalent PMSM designs, but ditching rare earths given historical supply chain instability seems sensible enough - even more so given the current global situation! Tier1 Mahle Powertrain are also touting a similar design currently.Seams a step backwards to old school synchronous motors with wound fields, presumably rotating so need brushes or rotating rectifier and a distinct rotor exciting stator (like aircraft alternators).
Peak field strengths presumably higher allowing higher torque for the initial get away. And greater flexibility for field weakening and optimising efficiency.
Most EVs use rare earth permanent magnets with a significant minority notably Tesla using induction machines.
For what it's worth, they're far from the first - Conti's tech in this area was in the first-gen Renault Zoes, so I'd imagine there'll be durability and manufacturing technique learning that BMW will have leveraged. Certainly it's currently more proven and mature than the switched reluctance tech from AEM that Bentley Motors have engaged in some research projects on.
BTW - Tesla are using PMSM as well as ASM these days. ASM are pretty useful in terms of wider efficiency spreads, even if their peak efficiency can't rival permanent magnets. Think that's one of the reasons that Audi shoved ASM tech into the e-tron I believe - more consistent efficiency across the operating range. They're big old buses which don't do well on rated/WLTP range, but actually don't disgrace themselves real-life autobahn range either.
An important thing in ASM or wound-rotor designs favour is the fact that the rotor isn't permanently-excited, so you can turn it off:
1. This really helps with in-cycle (and real life!) vehicle efficiency if you're dealing with a multi-motor setup, as at lighter road loads you can operate a single motor at a higher load/higher efficiency point and turn the other off - instead of operating two PMSMs at low load/low efficiency.
2. This also helps with the safety case for the vehicle - if you cut the power; the motors are off. They're safe and no hazardous voltages are present; even at high speeds . That's not the case with PMSM, so you start to need additional capability (HW components and SW) to deal with it. That adds cost and a token amount of size/weight, and takes more time to design and validate.
granada203028 said:
Any thoughts on this, max_torque?
The first thing to remember with electric motors is that really, they are ALL very efficient, no matter what architecture. The fundamental rules of our universe mean that conversion between E (electrostatic) and H (electromagnetic) fields can be done with very high efficiency..A typical electic machine is around 93 to 98% efficient, so really the real world consumption saving potential is pretty small, and in fact, it's better to spend the money on reducing the road load than on improving the already-very-good motor!
Going to a seperately exciting architecture is an interesting choice, but demonstrates that ultimate efficiency is really not required in pascar applications!
The negative points are really centered entirely on the physical considerations of getting current to the rotor windings, ie the brushes. However, an electric traction motor that is coupled to the wheels directly actually may not turn that many times in its life :
160,000 km is something like 700 Million revolutions, which over ten years equates to an average rotatonal speed of just 138 rpm!
A typical 12v alternator that we all are used too does far more turns, and sits in a much worse environment (unsealed underbonnet)
the advantages are signficant however:
1) Very "flat" efficiency curve, which whilst not as high at peak as for a PM machine, can maintain that medium efficiency across a wider speed range. This is especially true when we consider PM field weakening, which has a significant efficiency penalty. As you can effectively reduce the air gap magnetic field strength dynamically, you also can gain signifcantly lower iron losses at high motor speeds
2) A wider CPSR range means you can run a smaller machine at higher average speed, which is a cost saving
3) No PM material means lower cost and a more robust logistics chain
4) You could (not sure if BMW do this) run your machine at significantly elevated temperatures, because you have no PM's to cook and de-mag. Typical magnetic reach their Curie temperature at something above 200degC, whereas a laquered copper winding can run up to and over 300 degC if necessary. This means less derating and a potentially smaller cooling system (because you can reject the heat flux at a higher DeltaT
5) Failure mode safety case is much close to that of an induction machine, with no high voltage, high current or high torque excursions to worry about in the event of loss of field control in the field weakened zones
So, given that really, eMachine specific power density is already in-excess of what is absolutely necessary for a passenger car, grabing some of the other gains seems sensibly to me. What ever the real picture you can be sure however that BMW have done their homework on this one :-)
(worth noting that the entire purpose of the i3 and i8 programs was to capture real world user data on BEVs in the hands of actual customers. Every time I and other "i" users drive their car, it reports where and how and under what conditions we drove it back to HQ. That data is whatg BMW use to optimise the compromises on their latest cars)
BTW, for anyone wonder what on earth i am waffling on about. here is a picture of the BMW motor:

Those two small red wires feed DC current to the rotor windings, which spin around in the middle of the motor, and therefore need a pair of sliding carbon brushes, the little black squares with the flexible copper braided attached, to trasfer that current.
Those brushes are obviously wearing parts, unlike in a Permanent Magnet machine, where the rotor is free to spin on its bearings without such arrangements.
BTW, one option they haven't needed to us is to AC couple the rotor field supply across a AC transformer then rectify it locally, ie on the spinning rotor. This would remove the need for brushes, but add cost and slightly reduce efficiency. Clearly BMW are happy with the durability level they have with the existing standard method
ETA: because the rotor Field is DC and not a vector component (ie has no angular modulation) it's possible to use a non-segmented comutator, which is bascially a smooth copper ring, as seen in the that picture, unlike for a conventional brushed motor. That means no arcing or inductive HV spike and the brush can use it's full area at all times to carry the current. This means a very much longer life. In fact here, the picture shows pretty "short" brushes really, ie no issue with long term wear (longer brushes obviously have a longer life before they are worn down too much) The little stainless clock spring shown in the picture keeps the face of the brush pushed against the comutator surface

Those two small red wires feed DC current to the rotor windings, which spin around in the middle of the motor, and therefore need a pair of sliding carbon brushes, the little black squares with the flexible copper braided attached, to trasfer that current.
Those brushes are obviously wearing parts, unlike in a Permanent Magnet machine, where the rotor is free to spin on its bearings without such arrangements.
BTW, one option they haven't needed to us is to AC couple the rotor field supply across a AC transformer then rectify it locally, ie on the spinning rotor. This would remove the need for brushes, but add cost and slightly reduce efficiency. Clearly BMW are happy with the durability level they have with the existing standard method
ETA: because the rotor Field is DC and not a vector component (ie has no angular modulation) it's possible to use a non-segmented comutator, which is bascially a smooth copper ring, as seen in the that picture, unlike for a conventional brushed motor. That means no arcing or inductive HV spike and the brush can use it's full area at all times to carry the current. This means a very much longer life. In fact here, the picture shows pretty "short" brushes really, ie no issue with long term wear (longer brushes obviously have a longer life before they are worn down too much) The little stainless clock spring shown in the picture keeps the face of the brush pushed against the comutator surface
Edited by anonymous-user on Monday 14th March 11:23
Max_Torque said:
Those brushes are obviously wearing parts, unlike in a Permanent Magnet machine, where the rotor is free to spin on its bearings without such arrangements.
Forgive me as I’m not an expert in electric motors in any way, and all of my experience comes from racing electric R/C cars for a few decades, but won’t the comm require a skim at some point to retain maximum efficiency? Doesn’t that essentially make the commutator a consumable part also?It's more of a slip ring than a commutator - it's non-segmented as MT said. Hence wear should be a lot lower than segmented commutator.
The press release images appear to show that the brushes and slip ring are in a separate sealed chamber of the enclosure, which will not only keep carbon wear particles away from the rest of the machine - but could also aid serviceability.
The press release images appear to show that the brushes and slip ring are in a separate sealed chamber of the enclosure, which will not only keep carbon wear particles away from the rest of the machine - but could also aid serviceability.
As mentioned two factors make this very different to a conventional brushed motor
The old brushed motors most people are familiar with have permanent magnet stators and mechanically comutated electromagnetic rotors
ie they looked like this:
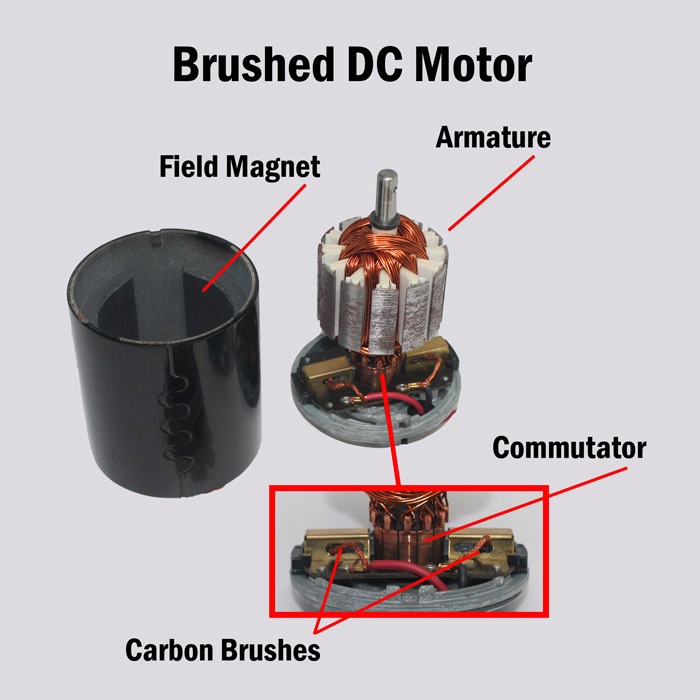
This meant pretty high brush wear because the full power of the motor had to go through those brushes, and because that power was constantly being "commutated" by those brushes, ie being stopped and started so as to be re-driected to the rotor segment that lined up with the magnets as they span past them. You can see the commutator segments in that picture and the indiuvidual rotor windings connected to them
Most brushed DC motors were built this way, fixed PM for stator and commutated rotor because retaining spining magnets is hard and expensive.
With a "electronically comutated stator" modern eMachine, the rotating magnetic field is created in the stator by solid state switches (mosfets or IGBT's) in the inverter, and the rotor electromagnetic field is a DC value. And because the rotor field does no work directly, the power you have to move across the spining slip rings is a very small percentage of the total motor power. That means your slip ring brushes carry far lower loading and don't have to constantly commutate that loading, and as a result their wear rates are much lower
The old brushed motors most people are familiar with have permanent magnet stators and mechanically comutated electromagnetic rotors
ie they looked like this:
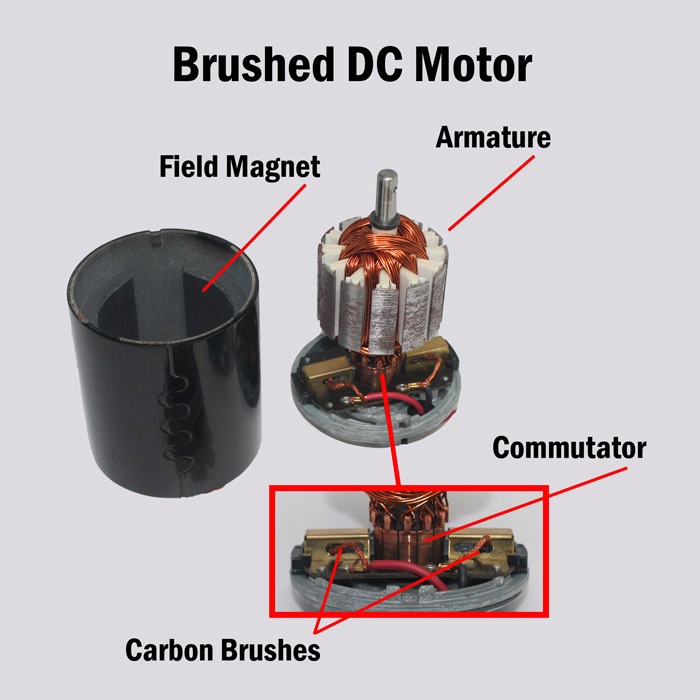
This meant pretty high brush wear because the full power of the motor had to go through those brushes, and because that power was constantly being "commutated" by those brushes, ie being stopped and started so as to be re-driected to the rotor segment that lined up with the magnets as they span past them. You can see the commutator segments in that picture and the indiuvidual rotor windings connected to them
Most brushed DC motors were built this way, fixed PM for stator and commutated rotor because retaining spining magnets is hard and expensive.
With a "electronically comutated stator" modern eMachine, the rotating magnetic field is created in the stator by solid state switches (mosfets or IGBT's) in the inverter, and the rotor electromagnetic field is a DC value. And because the rotor field does no work directly, the power you have to move across the spining slip rings is a very small percentage of the total motor power. That means your slip ring brushes carry far lower loading and don't have to constantly commutate that loading, and as a result their wear rates are much lower
Max_Torque said:
A typical electic machine is around 93 to 98% efficient, so really the real world consumption saving potential is pretty small, and in fact, it's better to spend the money on reducing the road load than on improving the already-very-good motor!
Going to a seperately exciting architecture is an interesting choice, but demonstrates that ultimate efficiency is really not required in pascar applications!
Maybe you covered it in the details that I possibly didn’t understand but is this actually true? My understanding is that peak efficiency is 90+% but that’s at a very optimal speed which doesn’t seem to be motorway speeds given how the consumption dramatically increases at higher speeds. Going to a seperately exciting architecture is an interesting choice, but demonstrates that ultimate efficiency is really not required in pascar applications!
Otherwise why are manufacturers talking at length about how their motors are the most efficient? Tesla certainly and BMW also. Unless it’s just marketing, there must be something to it and they must see unique value in developing their own motors.
Across a tightly-controlled legislative drivecycle fractional e-motor efficiency gains (or shifts in peak efficiency operating points) can have a tangible effect, especially as those drivecycles are often lower speeds, lower loads - where the e-motor may not be spending much time in its peak efficiency zones, so careful optimisation of this can bring real benefits.
However, in real conditions people tend to drive less smoothly and often at higher speeds - and it's here where the gap between motor A and motor B is much narrower. Hence the "noise" of real-life use cases has more of an effect on range/efficiency than the actual core motor technology. This is true for ICE powertrains too, but with EV their high efficiencies mean that other energy consumers (heating/aircon especially) become more dominant losses than before.
However, in real conditions people tend to drive less smoothly and often at higher speeds - and it's here where the gap between motor A and motor B is much narrower. Hence the "noise" of real-life use cases has more of an effect on range/efficiency than the actual core motor technology. This is true for ICE powertrains too, but with EV their high efficiencies mean that other energy consumers (heating/aircon especially) become more dominant losses than before.
Which sounds very reasonable as in reality everything seems to end up with a 200 mile range at motorway speeds no matter how amazingly efficient the new motors seem to be or how amazing the WLTP figures are. Back in the CO2 days there was obviously much tax benefit to be had from fudging the tests but who cares about unrealistic WLTP figures? I completely disregard them personally and look at real world tests.
Is it not possible to fix this with gearing, though? I guess this was Porsche's approach (which maybe had to do with top speed also) but they also end up with the usual 200 mile range so perhaps the answer is no.
Is it not possible to fix this with gearing, though? I guess this was Porsche's approach (which maybe had to do with top speed also) but they also end up with the usual 200 mile range so perhaps the answer is no.
Based on their powertrain design choices, I think a lot of the German EVs have autobahn performance and range as more significant priorities than outright WLTP range. You see this very much in the Porsche Taycan.
To drag things back on-topic, I suspect that the wound-rotor of the latest BMW EDUs might help them here too. There's no energy-sapping field weakening to worry about at higher motor speeds - so it should be a more efficient powertrain at motorway (or certainly autobahn!) speeds than the ubiquitous PMSM.
To drag things back on-topic, I suspect that the wound-rotor of the latest BMW EDUs might help them here too. There's no energy-sapping field weakening to worry about at higher motor speeds - so it should be a more efficient powertrain at motorway (or certainly autobahn!) speeds than the ubiquitous PMSM.
Edited by amstrange1 on Tuesday 15th March 11:11
It looks like it has solid rectangular conductors in the stator, unless that's just an outer sheath. This is obviously good for cross sectional area to reduce I2R, but potentially increases eddy current losses.
Can anyone give an insight into the typical fundamental/carrier frequencies seen in these motors and their associated controller, is there something about the motor architecture that allows for lower switching frequencies to be used?
Whilst on topic, what sort of lamination grade/thicknesses would they be using?
Can anyone give an insight into the typical fundamental/carrier frequencies seen in these motors and their associated controller, is there something about the motor architecture that allows for lower switching frequencies to be used?
Whilst on topic, what sort of lamination grade/thicknesses would they be using?
Edited by GT9 on Tuesday 15th March 13:17
Hairpin winding is often touted as a good way of maximising copper fill factor, and if you're doing welded/inserted hairpin (i.e. not continuous wound) then it's an easy manufacturing process with good control of where each wire sits in the stator slot. With standard round wire, you'll typically not get such a high fill factor and it's harder to manage the exact location of where each winding ends up - ergo more performance variation stator to stator. Tooling for hairpin is much pricier, but takt/process time is typically faster, hence higher volume stuff tending to be hairpin these days.
Typical switching frequency range for a silicon IGBT-based inverter 4-16kHz, depending on the switching devices (or 6-switch "power module") being used. Often dynamically changed across the operating range to maximise efficiency and minimise audible noise. SiC MOSFET based devices allow higher switching speeds, which can need careful management in the system design.
NO35 (0.35mm) to NO20 (0.20mm) lamination steel is the broad range used, usual price vs performance trade-offs at play.
Typical switching frequency range for a silicon IGBT-based inverter 4-16kHz, depending on the switching devices (or 6-switch "power module") being used. Often dynamically changed across the operating range to maximise efficiency and minimise audible noise. SiC MOSFET based devices allow higher switching speeds, which can need careful management in the system design.
NO35 (0.35mm) to NO20 (0.20mm) lamination steel is the broad range used, usual price vs performance trade-offs at play.
DMZ said:
Maybe you covered it in the details that I possibly didn’t understand but is this actually true? My understanding is that peak efficiency is 90+% but that’s at a very optimal speed which doesn’t seem to be motorway speeds given how the consumption dramatically increases at higher speeds.
Please don't confuse "efficiency" and "consumption" they are very much NOT the same thing at all.A mythical 100% efficient motor still consumes more energy at high vehicle average speeds because the road load (aero and rolling drag) is the dominant factor for an EV.
Max_Torque said:
Please don't confuse "efficiency" and "consumption" they are very much NOT the same thing at all.
Or rather powertrain (or motor) efficiency is not synonymous with vehicle efficiency. Frustrates me too, just because a vehicle consumes a lot (or is inefficient as a vehicle), does not necessarily mean the powertrain is inefficient.
Edited by amstrange1 on Wednesday 16th March 11:39
Very interesting thread. Particularly the observation that all electric motors are inherently efficient 'enough' to make it worthwhile to focus on other aspects. Most people that won't buy an EV today cite range (at their budget level) as an issue, and an extra 1-2% isn't going to swing anyone. Those yet to be convinced want 500 miles of range and instant charging before they'll become a willing punter I think!
I think it makes a lot of sense for the likes of BMW to instead chase more practical concerns such as materials cost saving, less rare materials that are potentially going to become supply problems too. Not least the fact that the motor unit costs less overall so is less of a cost down the line.
I personally would have no real concerns about the reliability of such designs either. These are sealed units and as such no additions such as dust or moisture will play their part in shortening the lifespan. What goes on in that sealed unit in terms of degradation is calculable and will have been tested to destruction. I'm sure there's already quite a few testbed EV motors out there that can claim a million miles of revolutions, moon and back etc etc. Frankly, if BMW can even deliver a motor that will reliably do 150k on average it's going to be just fine for virtually all customers, especially if it's relatively low cost to replace. I'm sure they can be confident their motor units will generally exceed that though..
I think it makes a lot of sense for the likes of BMW to instead chase more practical concerns such as materials cost saving, less rare materials that are potentially going to become supply problems too. Not least the fact that the motor unit costs less overall so is less of a cost down the line.
I personally would have no real concerns about the reliability of such designs either. These are sealed units and as such no additions such as dust or moisture will play their part in shortening the lifespan. What goes on in that sealed unit in terms of degradation is calculable and will have been tested to destruction. I'm sure there's already quite a few testbed EV motors out there that can claim a million miles of revolutions, moon and back etc etc. Frankly, if BMW can even deliver a motor that will reliably do 150k on average it's going to be just fine for virtually all customers, especially if it's relatively low cost to replace. I'm sure they can be confident their motor units will generally exceed that though..
I asked a very experienced power electronics design engineer about this. Here's what he said: (BTW, he was very complimentary about one of the posters!)
What BMW are doing is good. They are not brushes - they are slip rings that don't break current and therefore don't spark.They just wear, but these rings don't handle full power, in fact they only do a few percent of full power, so this is good. Permanent magnet materials mean chinese engagement due to rare earth supply, hence with the geopolitical situation BMW is being wise.
As an aside, he studied electric motor design in the 1980s and his professor had proven that a wound field is better on a large machine and permanent magnet is better on a small machine. He proved this by the relationship of magnet volume to machine horsepower. The crossover point depends on how good the magnets are and yes china has very good magnet rare earth materials.
What BMW are doing is good. They are not brushes - they are slip rings that don't break current and therefore don't spark.They just wear, but these rings don't handle full power, in fact they only do a few percent of full power, so this is good. Permanent magnet materials mean chinese engagement due to rare earth supply, hence with the geopolitical situation BMW is being wise.
As an aside, he studied electric motor design in the 1980s and his professor had proven that a wound field is better on a large machine and permanent magnet is better on a small machine. He proved this by the relationship of magnet volume to machine horsepower. The crossover point depends on how good the magnets are and yes china has very good magnet rare earth materials.
Gassing Station | EV and Alternative Fuels | Top of Page | What's New | My Stuff