Engine rebuild
Discussion
The briefest of brief updates.
The machine shop is still awaiting the bespoke cylinder liners from the USA. Once they’ve landed, the block can be bored and sleeved. I believe that’s all that’s left to do before the engine can be built back up again.
Meanwhile, Ricky has taken delivery of lots of shiny reciprocating bits, also from the States.
The CP Carrillo pistons, gudgeon pins and ring sets:

No, it’s not a V8. Some of those compartments are doubled up. As an aside, our Septic friends refer to gudgeon pins as “wrist pins”. How many of us have tried to explain how the linear motion of the piston is translated into the rotational motion of the crank by making our upheld fist the “piston”, our forearm the “connecting rod” and our elbow the “big end”. Lo and behold, your wrist suddenly becomes the “gudgeon pin”! Hence “wrist pin” I suppose?
The pistons are going to be MUCH lighter!
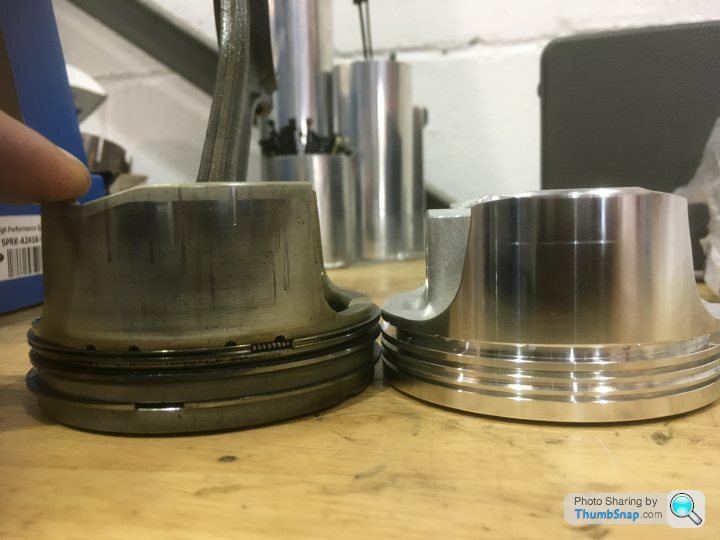
Note the scoring on the skirt of the old piston. Also note how much shorter, more narrow and hence lighter the skirt is on the new piston.
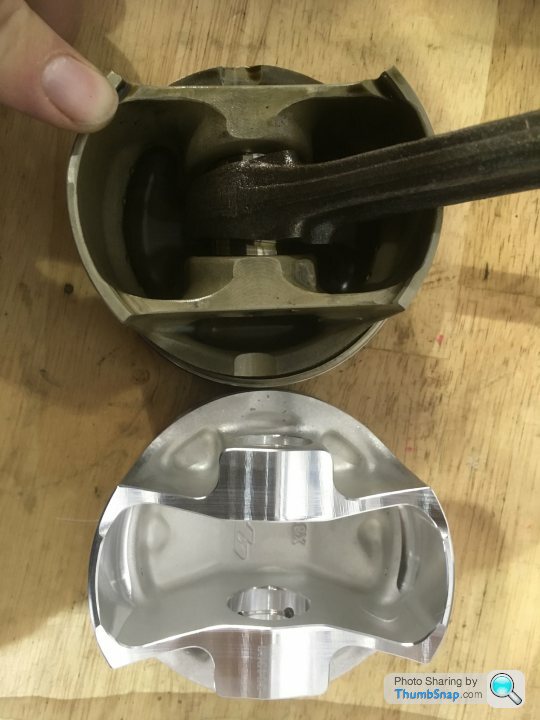
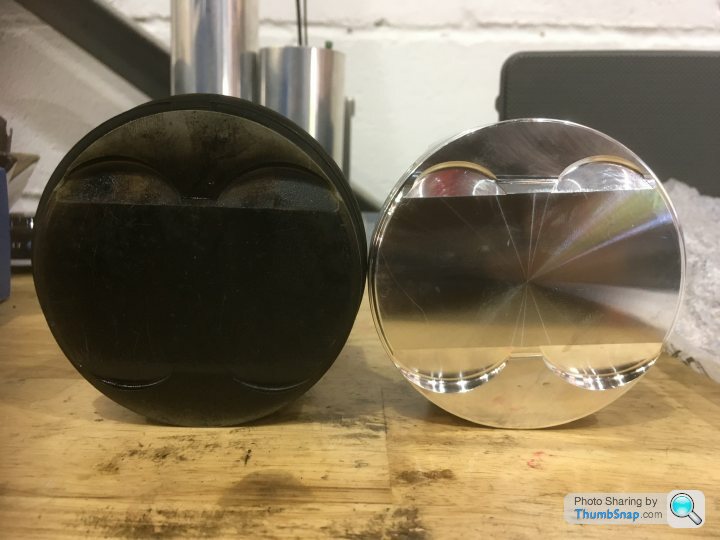
Finally, all of the valve train has also arrived from ‘Murica. Lots of small boxes containing inlet and exhaust valves, springs, top hats and collets. The heads are also with the machine shop, having already received new valve guides and seats, the latter being cut with reference to valves that Ricky already had in stock. For no better reason than I took photos of them, here are the valves, inlet then exhaust:


TTFN
The machine shop is still awaiting the bespoke cylinder liners from the USA. Once they’ve landed, the block can be bored and sleeved. I believe that’s all that’s left to do before the engine can be built back up again.
Meanwhile, Ricky has taken delivery of lots of shiny reciprocating bits, also from the States.
The CP Carrillo pistons, gudgeon pins and ring sets:

No, it’s not a V8. Some of those compartments are doubled up. As an aside, our Septic friends refer to gudgeon pins as “wrist pins”. How many of us have tried to explain how the linear motion of the piston is translated into the rotational motion of the crank by making our upheld fist the “piston”, our forearm the “connecting rod” and our elbow the “big end”. Lo and behold, your wrist suddenly becomes the “gudgeon pin”! Hence “wrist pin” I suppose?
The pistons are going to be MUCH lighter!
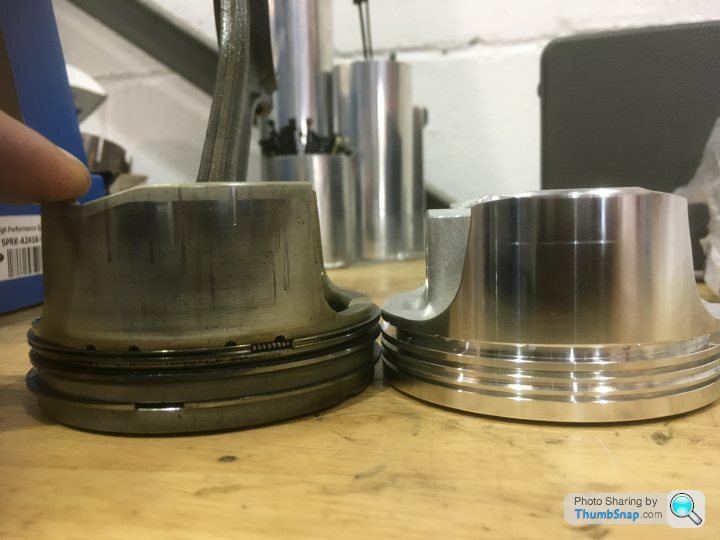
Note the scoring on the skirt of the old piston. Also note how much shorter, more narrow and hence lighter the skirt is on the new piston.
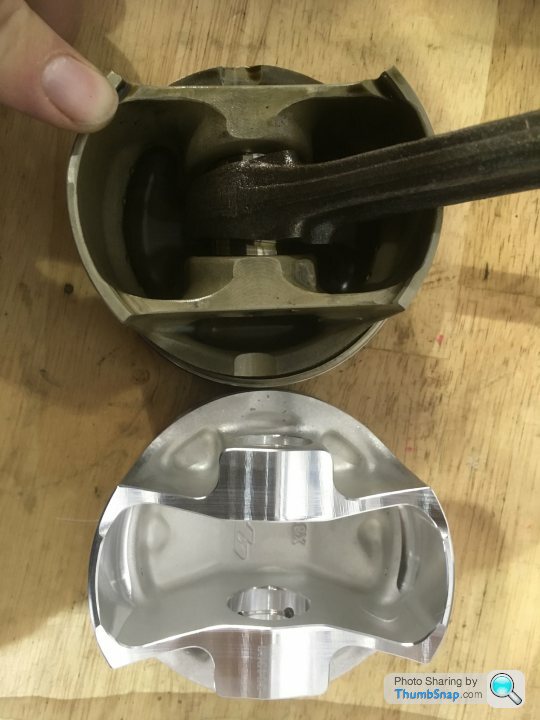
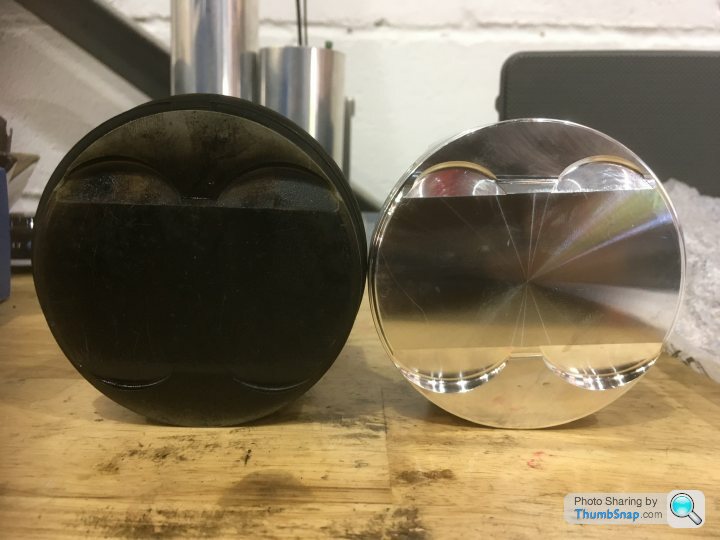
Finally, all of the valve train has also arrived from ‘Murica. Lots of small boxes containing inlet and exhaust valves, springs, top hats and collets. The heads are also with the machine shop, having already received new valve guides and seats, the latter being cut with reference to valves that Ricky already had in stock. For no better reason than I took photos of them, here are the valves, inlet then exhaust:


TTFN
Frustratingly stalled whilst we awaited the custom cylinder liners from the US. Apparently, they were busy building a wall or something?
Anyway, they arrived with the machinists a couple of weeks ago and they anticipated the block being finished this Monday just gone (yesterday!). I’m hoping to get over to Ricky’s in the next couple of days.
Thanks for your interest........and watch this space
Anyway, they arrived with the machinists a couple of weeks ago and they anticipated the block being finished this Monday just gone (yesterday!). I’m hoping to get over to Ricky’s in the next couple of days.
Thanks for your interest........and watch this space

Once again, thank you!
I made it over to Ricky’s this morning. Updates will follow soon enough, but sadly not immediately. The block and heads are with a specialist machine shop in Kent. They were awaiting the cylinder liners before they started. As of today, the scored block has been bored and eight of the liners machined into place. The old, worn valve guides have been pressed out and fitting the new ones shouldn’t take too long.
When they’re finished, Ricky will drive down to Kent to collect them in person so that he can inspect the work. Hopefully the build-up should then be pretty quick.
I’m also having one or two other things sorted whilst the car is off the road, but I’ll write about them as they happen........
I made it over to Ricky’s this morning. Updates will follow soon enough, but sadly not immediately. The block and heads are with a specialist machine shop in Kent. They were awaiting the cylinder liners before they started. As of today, the scored block has been bored and eight of the liners machined into place. The old, worn valve guides have been pressed out and fitting the new ones shouldn’t take too long.
When they’re finished, Ricky will drive down to Kent to collect them in person so that he can inspect the work. Hopefully the build-up should then be pretty quick.
I’m also having one or two other things sorted whilst the car is off the road, but I’ll write about them as they happen........
Did you ever have a dyno run of the car sort of anywhere close to the time it went in for this rebvuild?
I was just wondering if, once the refreshed unit is run in (what's the procedure for that then...?), if you would be inclined to get a dyno run done to see what sort of power the engine is making.
Anyway, sounding like things are progressing properly, if not as quickly as you probably like. But still, better to measure twice and cut once...
I, for the record, have read the whole thread from my desk in the place I work in Essex
Innit
I was just wondering if, once the refreshed unit is run in (what's the procedure for that then...?), if you would be inclined to get a dyno run done to see what sort of power the engine is making.
Anyway, sounding like things are progressing properly, if not as quickly as you probably like. But still, better to measure twice and cut once...
I, for the record, have read the whole thread from my desk in the place I work in Essex
Innit
I’m as impatient as anybody, but I want this done well and that means time and patience! Fingers crossed for some noticeable progress in the near future.
Although I was quite willing to thrash the engine on the road, I was always dubious about doing so on a dyno. It just seemed a sure-fire way of ensuring the catastrophic mechanical failure of an already worn engine. The thought did cross my mind of doing so to get “before” and “after” figures, but thought that that would REALLY be pushing my luck!
Ricky will use the car for a few days to bed the motor in and will be flashing the ECU with one of his custom maps. After an oil change it’ll be over to me. I’ll agree a regime with him, but I expect, as with any modern engine, it’ll be taking it steady, with no labouring for a couple of hundred miles, and then steadily upping the pace before another oil change at 1000 miles. But as ever, I’ll detail it here when I know more. Professional advice is always welcome!
And yes, it’ll be dyno’d when we’re satisfied that it’s well bedded-in.
Although I was quite willing to thrash the engine on the road, I was always dubious about doing so on a dyno. It just seemed a sure-fire way of ensuring the catastrophic mechanical failure of an already worn engine. The thought did cross my mind of doing so to get “before” and “after” figures, but thought that that would REALLY be pushing my luck!
Ricky will use the car for a few days to bed the motor in and will be flashing the ECU with one of his custom maps. After an oil change it’ll be over to me. I’ll agree a regime with him, but I expect, as with any modern engine, it’ll be taking it steady, with no labouring for a couple of hundred miles, and then steadily upping the pace before another oil change at 1000 miles. But as ever, I’ll detail it here when I know more. Professional advice is always welcome!
And yes, it’ll be dyno’d when we’re satisfied that it’s well bedded-in.
Standby........ standby........
The delay has been frustrating and I’ll endeavour to explain the “whys” and “wherefores” when I next post about the rebuild itself........
Which I’m pleased to report should be soon! The block and heads are finally ready for collection. It was machining the former that was causing the delay. I believe that they should be back in Ricky’s hands within the next day or two.
The delay has been frustrating and I’ll endeavour to explain the “whys” and “wherefores” when I next post about the rebuild itself........
Which I’m pleased to report should be soon! The block and heads are finally ready for collection. It was machining the former that was causing the delay. I believe that they should be back in Ricky’s hands within the next day or two.
Well…………
After a lengthy and unwelcome hiatus, it’s time to resume this thread!!
Hooray!!!
I shall remind you that I’m only a two finger typist. (Actually, lying abed in a hotel in Vienna, alarm set for 0450 BST, Sunday morning, iPad resting on my chest, strictly speaking I’m a two thumbs typist!) So forgive me if I keep the recaps to a minimum.
But you may recall that the time frame from initially asking for recommendations for a rebuild specialist, to buying a knackered Mk1 focus to get me by, to dropping the car off with Ricky, was short: three weeks?: a month? And I’ve been mindful throughout that Ricky, until recently a sole trader, has to maintain a steady income through bread-and-butter work: servicing: aftermarket exhausts: remaps......
Still.... I suspect that we both thought that I’d be back on the road with a rebuilt engine by early summer. Five months maybe?
The engine came out of my car in very short order and was stripped straight away. Ricky ordered all of the parts that he would need, many of them for bespoke manufacture stateside, whilst the block went away for specialist work at a third party contractor......
And somewhere along the line a b
k was dropped.
I want to make it quite clear that it wasn’t Ricky’s fault in the slightest. He’s been between a rock and a hard place for a few months. My block needed extensive machine work, and one false move would require the purchase of a new £5500 casting. Second hand, the 5.2s are available. But not the 5s.
So the work needed to be done by extremely competent people and they are few and far between. For this sort of work, Ricky sends his blocks and heads to the best. I know of them by reputation and if I name them, then you may well have heard of them too. But I’m not going to name names! Which is a pity as their work is superb.
Because somewhere along the line, their organisational skills were found lacking.
It was up to them to order the liners, from LA Sleeve in........ well, Santa Fe as it happens! And whilst the bespoke pistons and valve-train were manufactured and delivered from the States in about a month, the liners apparently took ten weeks!
And the work that should have taken one highly-skilled machinist a week to complete took...... another two-and-a-half months!
The trouble is that there are so few machine shops in the UK whom you would trust this work to. Many will tell you that they could do the work, but what’s their track record? Ricky has to rely on their work being spot-on every time, so you go with the best. And if they’ve forgotten to order the liners for one small job? Or if they sideline the work of one small, sole trader in favour of a bigger, more lucrative job, what do you do? Do you alienate the machine shop who you trust to get the job right?
So, over five months after he sent it off, Ricky received my block (and heads) back from the machinists.
And they’ve done a beautiful job!
Albeit a rather slow one....... But what could he do? This is work that HAS to be outsourced. And it HAS to go to the best. And they’ll survive quite happily without his custom, so you suck it up.
I understand that.
Doesn’t make it any less frustrating though!
Right! My thumbs are aching! And I need to sleep before another day of driving airliners around. Tomorrow, after tapas and Estrella in Barcelona (and if I can then be arsed!) I’ll write about that actual block work, complete with the “why’s” and “where fore’s”.
And some photos!!
After that comes an absolutely fascinating insight into con rods!! (No, really! It’s actually, genuinely fascinating!!! I was quite blown away by it. Trust me, it’ll be worth the wait........)
After a lengthy and unwelcome hiatus, it’s time to resume this thread!!
Hooray!!!
I shall remind you that I’m only a two finger typist. (Actually, lying abed in a hotel in Vienna, alarm set for 0450 BST, Sunday morning, iPad resting on my chest, strictly speaking I’m a two thumbs typist!) So forgive me if I keep the recaps to a minimum.
But you may recall that the time frame from initially asking for recommendations for a rebuild specialist, to buying a knackered Mk1 focus to get me by, to dropping the car off with Ricky, was short: three weeks?: a month? And I’ve been mindful throughout that Ricky, until recently a sole trader, has to maintain a steady income through bread-and-butter work: servicing: aftermarket exhausts: remaps......
Still.... I suspect that we both thought that I’d be back on the road with a rebuilt engine by early summer. Five months maybe?
The engine came out of my car in very short order and was stripped straight away. Ricky ordered all of the parts that he would need, many of them for bespoke manufacture stateside, whilst the block went away for specialist work at a third party contractor......
And somewhere along the line a b

I want to make it quite clear that it wasn’t Ricky’s fault in the slightest. He’s been between a rock and a hard place for a few months. My block needed extensive machine work, and one false move would require the purchase of a new £5500 casting. Second hand, the 5.2s are available. But not the 5s.
So the work needed to be done by extremely competent people and they are few and far between. For this sort of work, Ricky sends his blocks and heads to the best. I know of them by reputation and if I name them, then you may well have heard of them too. But I’m not going to name names! Which is a pity as their work is superb.
Because somewhere along the line, their organisational skills were found lacking.
It was up to them to order the liners, from LA Sleeve in........ well, Santa Fe as it happens! And whilst the bespoke pistons and valve-train were manufactured and delivered from the States in about a month, the liners apparently took ten weeks!
And the work that should have taken one highly-skilled machinist a week to complete took...... another two-and-a-half months!
The trouble is that there are so few machine shops in the UK whom you would trust this work to. Many will tell you that they could do the work, but what’s their track record? Ricky has to rely on their work being spot-on every time, so you go with the best. And if they’ve forgotten to order the liners for one small job? Or if they sideline the work of one small, sole trader in favour of a bigger, more lucrative job, what do you do? Do you alienate the machine shop who you trust to get the job right?
So, over five months after he sent it off, Ricky received my block (and heads) back from the machinists.
And they’ve done a beautiful job!
Albeit a rather slow one....... But what could he do? This is work that HAS to be outsourced. And it HAS to go to the best. And they’ll survive quite happily without his custom, so you suck it up.
I understand that.
Doesn’t make it any less frustrating though!
Right! My thumbs are aching! And I need to sleep before another day of driving airliners around. Tomorrow, after tapas and Estrella in Barcelona (and if I can then be arsed!) I’ll write about that actual block work, complete with the “why’s” and “where fore’s”.
And some photos!!
After that comes an absolutely fascinating insight into con rods!! (No, really! It’s actually, genuinely fascinating!!! I was quite blown away by it. Trust me, it’ll be worth the wait........)
Edited by 4321go on Saturday 10th August 21:18
So, onto the machining of the block.
You’ll recall that the bores were badly scored by the ceramic “sand” that had worked its way back up the header pipes from the cats:

As standard, the bores of the cast alloy blocks are plated with Nikasil, a nickel/ceramic coating that provides a hard finish for the piston rings to run against. Boring and re-plating/honing would result in oversize bores, and oversize pistons aren’t available. So the options were a new block, or a sleeved one. The latter would be a £2k saving and would result in a harder-wearing finish. There were no obvious advantages to having a new block for me, so we decided to machine the old one.
The steel liners came from L.A. Sleeve of Santa Fe, Ca. and are flanged. That is to say that for most of their length, they are a thin-walled steel tube, but towards the top, cylinder head-end, they are much thicker-walled. Therefore they are much more positively seated than a sleeve without a flange. The bores are rebored to the outside diameter of the sleeve, and then counter-bored to the diameter and depth of the flange, before the deck is skimmed flat. With the head torqued down the flange is pressed firmly into its seat. This isn’t my block, nor L.A. Sleeve liners, but I’m sure mine looked very similar:
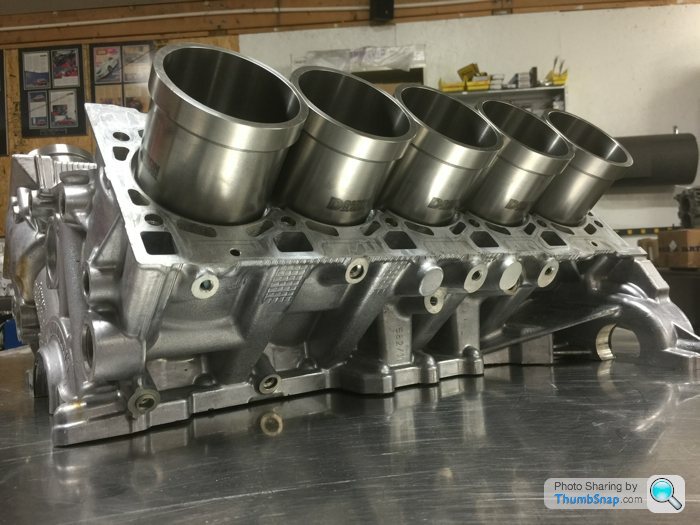
In the following pictures it appears that the bores have become Siamesed, and indeed they have, but only to the depth of the flange. Lower down, the alloy webs remain between the cylinders (and this IS my block):


Lower down in the bores, the liners have “windage” holes drilled through them, and this is a convenient time to show you one of the numerous differences between the 5.0 and 5.2 litre blocks. (Remember that the two V10 units (Lambo’s 5 and Audi’s 5.2) were developed separately from related, but different, 4 and 4.2 litre V8s.)
Here is an end shot of a (later) 5.2 litre block:

And my (earlier) 5.0 litre block
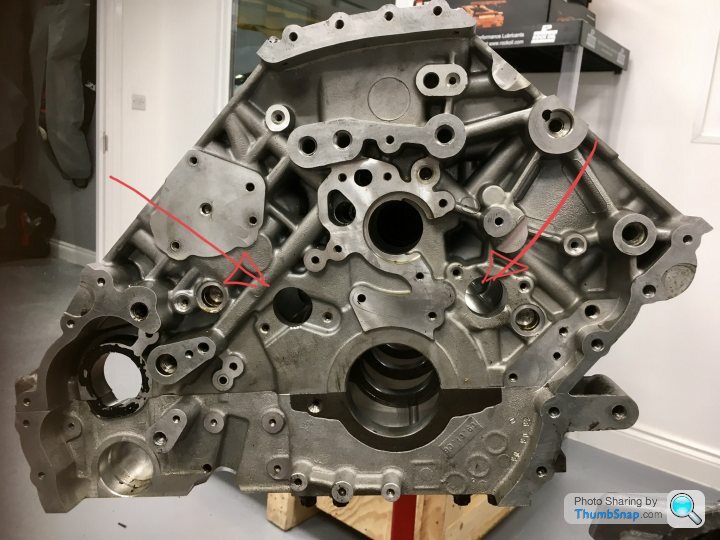
Note the two extra holes in the earlier block. These are the windage holes and pass through the lower end of each cylinder for the entire length of each bank. As the pistons thrash up and down, the air in the volumes below them is repeatedly being compressed and expanded. In the earlier engine, these pressure changes are alleviated and reduced by the air being allowed to pass from one bore to the next through the windage holes (in addition to it passing under the base of each bore). This extra alleviation of the pressure changes wasn’t needed in the later engines due to the increased efficiency of the oil scavenge pump fitted to the latter. Of much greater power (six chambers rather than three?) it can pump oil from the dry sump back to the oil tank at a much greater rate. Therefore the oil is less likely to become aerated in the short time that it spends under the thrashing pistons, and so there is less need to reduce the air pressure differences with the later oil pump.
Who knew? (Well, Ricky for one!)
Anyway, here is one of the windage holes in a cylinder sleeve, as seen down one of the bores of my block:
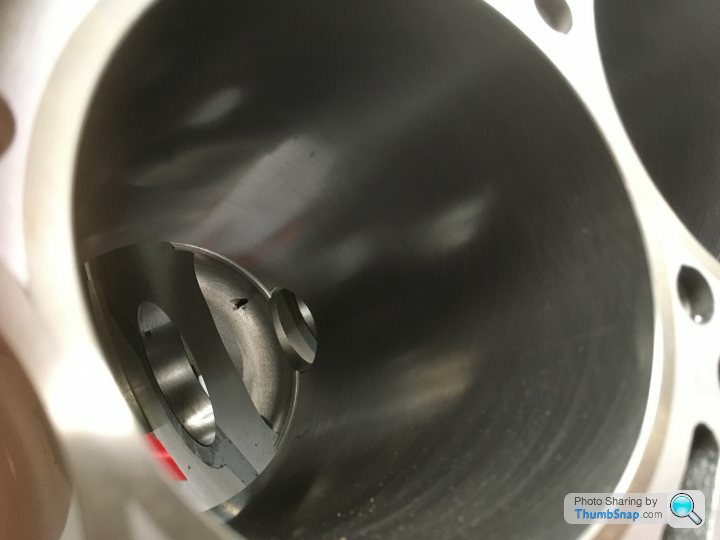
(I should add that all of the shots of my block were taken shortly after it arrived back from the machinist. Ricky had been measuring up for the crank shell sizes and then it was going into his parts cleaning tank for several hours. That should have shifted not only the swarf in the galleries, but the dead flies too!!)
With the sleeves machined into place, they then have to be honed to size and shape. And it was this process that led to the biggest delay in the machining process. Because, in all of the photos of my block above, the bore is the wrong shape!!
When you torque down the cylinder head onto the block, it distorts the block itself. (And indeed, how the block is distorted depends on whether the head is held down by studs or bolts, the former squashing the top of the block, the latter the bottom.) As you look at the photos above, the bores are not round! They will only become so again when the cylinder heads are torqued down onto them. Therefore, before the cylinder liners can be honed to size, the block has to be distorted in exactly the same way as if the heads were in place and torqued down.
This is achieved by the use of “Torque Plates”. These are THICK metal plates that are bolted down onto the block in exactly the same way as the cylinder heads are (either studs or bolts) and to the same torque, but with large holes in them allowing the honing tool to pass through them. The machinists “had” them, but couldn’t find them! Ricky has his own, but they were apparently too deep for the machine shop. So they had to make up a new set.......
Here’s a picture of a bore being honed (again, not my engine). The torque plate is a thick metal plate, but not as thick as the actual cylinder head casting. So here extension tubes have been machined to allow the actual head studs to be used. The honing tool is four abrasive pads held against the cylinder walls by spring pressure:

Next time......... Con rods!! (Trust me; it’s genuinely interesting!!)
You’ll recall that the bores were badly scored by the ceramic “sand” that had worked its way back up the header pipes from the cats:

As standard, the bores of the cast alloy blocks are plated with Nikasil, a nickel/ceramic coating that provides a hard finish for the piston rings to run against. Boring and re-plating/honing would result in oversize bores, and oversize pistons aren’t available. So the options were a new block, or a sleeved one. The latter would be a £2k saving and would result in a harder-wearing finish. There were no obvious advantages to having a new block for me, so we decided to machine the old one.
The steel liners came from L.A. Sleeve of Santa Fe, Ca. and are flanged. That is to say that for most of their length, they are a thin-walled steel tube, but towards the top, cylinder head-end, they are much thicker-walled. Therefore they are much more positively seated than a sleeve without a flange. The bores are rebored to the outside diameter of the sleeve, and then counter-bored to the diameter and depth of the flange, before the deck is skimmed flat. With the head torqued down the flange is pressed firmly into its seat. This isn’t my block, nor L.A. Sleeve liners, but I’m sure mine looked very similar:
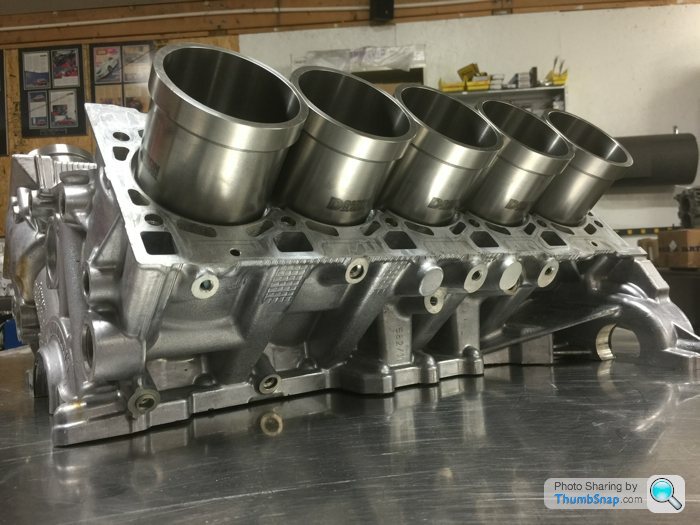
In the following pictures it appears that the bores have become Siamesed, and indeed they have, but only to the depth of the flange. Lower down, the alloy webs remain between the cylinders (and this IS my block):


Lower down in the bores, the liners have “windage” holes drilled through them, and this is a convenient time to show you one of the numerous differences between the 5.0 and 5.2 litre blocks. (Remember that the two V10 units (Lambo’s 5 and Audi’s 5.2) were developed separately from related, but different, 4 and 4.2 litre V8s.)
Here is an end shot of a (later) 5.2 litre block:

And my (earlier) 5.0 litre block
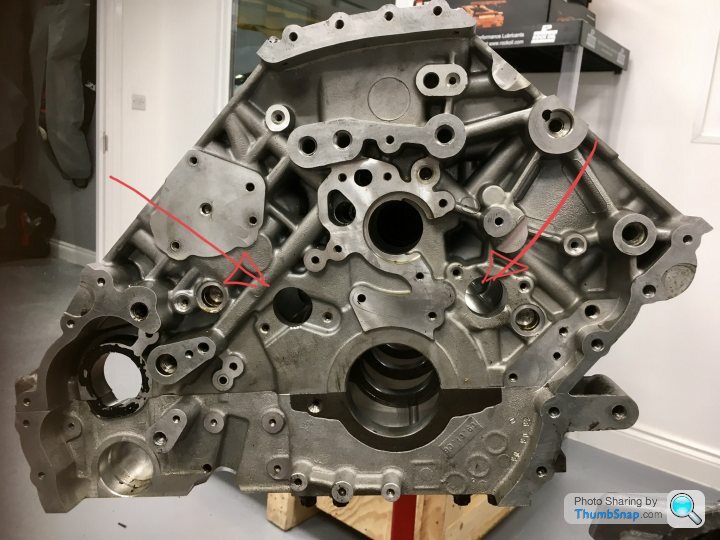
Note the two extra holes in the earlier block. These are the windage holes and pass through the lower end of each cylinder for the entire length of each bank. As the pistons thrash up and down, the air in the volumes below them is repeatedly being compressed and expanded. In the earlier engine, these pressure changes are alleviated and reduced by the air being allowed to pass from one bore to the next through the windage holes (in addition to it passing under the base of each bore). This extra alleviation of the pressure changes wasn’t needed in the later engines due to the increased efficiency of the oil scavenge pump fitted to the latter. Of much greater power (six chambers rather than three?) it can pump oil from the dry sump back to the oil tank at a much greater rate. Therefore the oil is less likely to become aerated in the short time that it spends under the thrashing pistons, and so there is less need to reduce the air pressure differences with the later oil pump.
Who knew? (Well, Ricky for one!)
Anyway, here is one of the windage holes in a cylinder sleeve, as seen down one of the bores of my block:
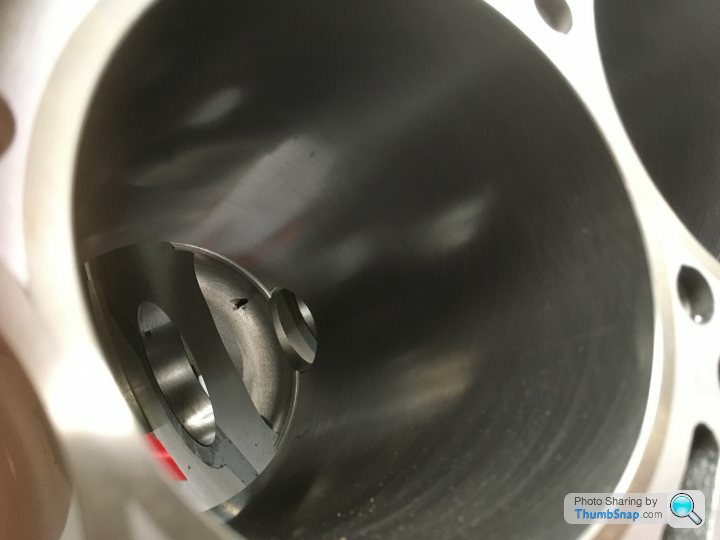
(I should add that all of the shots of my block were taken shortly after it arrived back from the machinist. Ricky had been measuring up for the crank shell sizes and then it was going into his parts cleaning tank for several hours. That should have shifted not only the swarf in the galleries, but the dead flies too!!)
With the sleeves machined into place, they then have to be honed to size and shape. And it was this process that led to the biggest delay in the machining process. Because, in all of the photos of my block above, the bore is the wrong shape!!
When you torque down the cylinder head onto the block, it distorts the block itself. (And indeed, how the block is distorted depends on whether the head is held down by studs or bolts, the former squashing the top of the block, the latter the bottom.) As you look at the photos above, the bores are not round! They will only become so again when the cylinder heads are torqued down onto them. Therefore, before the cylinder liners can be honed to size, the block has to be distorted in exactly the same way as if the heads were in place and torqued down.
This is achieved by the use of “Torque Plates”. These are THICK metal plates that are bolted down onto the block in exactly the same way as the cylinder heads are (either studs or bolts) and to the same torque, but with large holes in them allowing the honing tool to pass through them. The machinists “had” them, but couldn’t find them! Ricky has his own, but they were apparently too deep for the machine shop. So they had to make up a new set.......
Here’s a picture of a bore being honed (again, not my engine). The torque plate is a thick metal plate, but not as thick as the actual cylinder head casting. So here extension tubes have been machined to allow the actual head studs to be used. The honing tool is four abrasive pads held against the cylinder walls by spring pressure:

Next time......... Con rods!! (Trust me; it’s genuinely interesting!!)
Edited by 4321go on Sunday 11th August 21:44
Swampy1982 said:
....... however, a key detail is missing...
Hows the focus?
Unlike Italian exotica, which require almost constant, expensive fettling (and don’t believe those that say otherwise; if you USE these cars, they cost money!), the only failure in 8,000 miles has been a power-steering pump pressure switch; about £50.Hows the focus?
There are better examples out there. The suspension bushes are worn (it sometimes lurches a bit during cornering) and it could really do with a new cat. But you can pedal flat-out everywhere without fear of losing your license.
I worry that when the MoT is due in November, it won’t be economically viable to get it through. In which case I’ll scrap it and buy another as it’s been quite liberating to have a “normal” car, for trips to the “big” Tesco and the tip!!
yzr500 said:
Interesting but a few questions ,would the new piston clearance within the bores be different between Nikasil / iron sleeves ? also the new pistons would have the rings suitable for Nikasil not iron sleeves .
I’d have to ask Ricky for a definitive answer, but my own thoughts on it are that it goes the other way around. That is to say that the Nikasil process is designed to give the bores of an alloy block the same hardness and wear resistance as steel, and to interact with the spring steel of the rings accordingly, rather than the rings needing to be compatible with the Nikasil. As for the clearances, I’m pretty confident that they’d be honed to the same sizes as OEM; it’s the expanding rings that form the gas seal.Besides, we’re using the CP Carrillo aftermarket pistons and rings...... (remember, they’re probably better, certainly lighter and around £2800 rather than £14,000!).
Gassing Station | Supercar General | Top of Page | What's New | My Stuff