How is engine torque "capped"
Discussion
I've noticed on the GTR particularly, that tuners will limit engine torque to a preset level. In this case, usually around 600ft/lb, likely due to the gearbox limitations. However, the engine can still make power, sometimes in excess of 800hp.
How is this achieved and more importantly, controlled? More precisely, how is the torque capped, but the power allowed to increase?
How is this achieved and more importantly, controlled? More precisely, how is the torque capped, but the power allowed to increase?
jimPH said:
I've noticed on the GTR particularly, that tuners will limit engine torque to a preset level. In this case, usually around 600ft/lb, likely due to the gearbox limitations. However, the engine can still make power, sometimes in excess of 800hp.
How is this achieved and more importantly, controlled? More precisely, how is the torque capped, but the power allowed to increase?
It's called tuning.How is this achieved and more importantly, controlled? More precisely, how is the torque capped, but the power allowed to increase?
Quite simple.
Play with boost, fuel, timing and voila. And IF they are actually making 800hp and less than 600lbft..clearly it would need to be at a fairly high rpm to be achievable
I'm not a design engineer in this field or whatever but...
Power is calculated as a function of torque X RPM.
If you can make the engine turn very fast, but with smaller power pulses, you can achieve higher power figures while keeping torque down.
Look at F1 cars and HGVs.
In some guises, they both make similar power figures, say 1000hp. But as the F1 engines are rotating at close to 15k RPM, their torque is lower.
HGVs on the other hand, have much lower revs but still achieve the same power. How? They have very large torque figures.
If you want big power but also want to keep the torque figures down, you must increase your engine's RPM.
Power is calculated as a function of torque X RPM.
If you can make the engine turn very fast, but with smaller power pulses, you can achieve higher power figures while keeping torque down.
Look at F1 cars and HGVs.
In some guises, they both make similar power figures, say 1000hp. But as the F1 engines are rotating at close to 15k RPM, their torque is lower.
HGVs on the other hand, have much lower revs but still achieve the same power. How? They have very large torque figures.
If you want big power but also want to keep the torque figures down, you must increase your engine's RPM.
When you fit a turbocharger and intake / exhaust system that has low losses at high engine speeds so that it can flow a lot of air (in order to make a lot of power, as air + fuel = power) then that system is capable of generating massive cylinder filling capability at lower engine speeds.
Typically, an un-controlled turbo charged engine could, if not limited by some means, make something like twice the boost pressure it makes at peak power speed at peak torque speed. In order to limit cylinder filling (and hence limit peak charge density and the resulting peak BMEP) we 'wastegate' the turbo charger to vent excess exhaust energy around the turbine, that in turn reduces boost pressure and hence charge density.
Tuners can use electronically controlled wastegates to set the characteristic shape of the boost pressure curve vs engine speed (within certain limits) so they might choose to limit boost pressure in the mid range (say 3krpm to 5krpm) and then set a higher pressure at peak power speed (say 7krpm) in order to hit a high peak power value
Typically, an un-controlled turbo charged engine could, if not limited by some means, make something like twice the boost pressure it makes at peak power speed at peak torque speed. In order to limit cylinder filling (and hence limit peak charge density and the resulting peak BMEP) we 'wastegate' the turbo charger to vent excess exhaust energy around the turbine, that in turn reduces boost pressure and hence charge density.
Tuners can use electronically controlled wastegates to set the characteristic shape of the boost pressure curve vs engine speed (within certain limits) so they might choose to limit boost pressure in the mid range (say 3krpm to 5krpm) and then set a higher pressure at peak power speed (say 7krpm) in order to hit a high peak power value
Thanks guys. I see that with the increase in revs a power increase is inevitable, so tuners are effectively tuning torque. The turbo efficiency will make power, understood.
My thoughts were by capping torque in some way, it would effectively strangle the engine, but if it remains constant then it will be multiplied by the revs. This clearly must be variable to maintain the flat curve across the rev range.
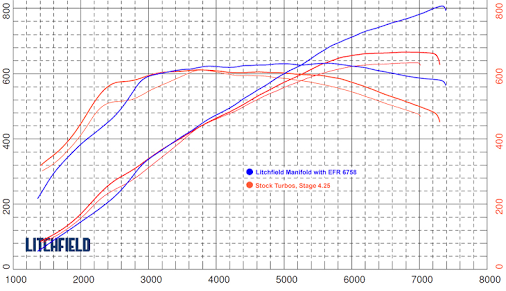
My thoughts were by capping torque in some way, it would effectively strangle the engine, but if it remains constant then it will be multiplied by the revs. This clearly must be variable to maintain the flat curve across the rev range.
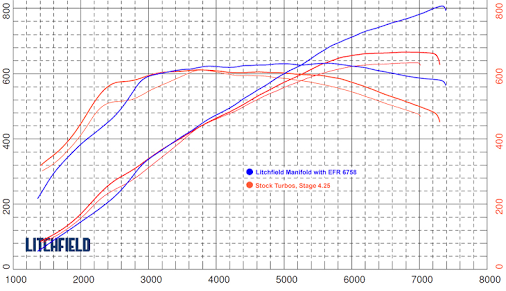
Torque is what generally breaks driveline components, not power, so it makes sense to limit torque, especially in the lower gears.
I have read that one reason manufacturers like auto boxes is that they don't have to engineer for the torque overloads that ham-fisted clutch abuse can cause.
I have read that one reason manufacturers like auto boxes is that they don't have to engineer for the torque overloads that ham-fisted clutch abuse can cause.
You map the engine to produce the torque curve within your required profile, assuming there is excess capacity to produce more than you wish at the rpm range.
With a turbo engine the torque curve is a function of the airflow the turbo can produce, if its efficient enough at low rpm to produce excess target torque, you can limit the amount of airflow it provides by limiting the turbine speed via the use of a wastegate.
On top of this, you also tune the ignition and fuelling to provide the control required. With modern ECU's there are many mapping points, which allows you to fine tune the base map, you then have the ability to use active controls that smooth out the rpm points between the mapped tables, plus you can also actively tune the transitions to make that smooth.
You can map all this per gear too, so if your particular car has a weak 4th gear, you can reduce peak torque for that gear but keep the torque higher for the others, which can handle the load.
You can also map this around situation, so for example you will limit the torque during a launch so you don't have too much wheel spin or load on the clutch and input shaft, but once up to speed you will allow peak torque.
On my own ECU I have 12 maps switchable from the driving seat, each map allows me to fine tune anything I want and then select that on the fly. During a sprint I will use the higher torque maps, when I use the car on the road I drop the peak mid range torque to reduce load on the drivetrain. My engine can produce 540lbft on the higher torque maps and just shy of 500BHP when allowed to, on the road i'll back it off to 450lbft but still have the same top end power. Doing that has allowed me to so far manage 113K miles on the stock drivetrain (bar a clutch upgrade) with zero failures, yet still win a sprint championship outright.
You can profile the engines to very small margins on the modern ECU's, mine even allows flat foot shifting so on upshifts I don't come off the throttle, as soon as the clutch is touched the ECU backs off the fuel and ignition to cut the torque, which unloads the gears, then when I come back off the clutch (this is a conventional H pattern synco box) the ECU ramps back in the ignition and fueling smoothly to bring the torque back in without shocking the transmition. Doing this keeps the turbo speed up between shifts (instead of dropping 60Krpm, it drops 10krpm) because air is still flowing through the engine, its just not producing any torque, so you get no turbo lag.
With a turbo engine the torque curve is a function of the airflow the turbo can produce, if its efficient enough at low rpm to produce excess target torque, you can limit the amount of airflow it provides by limiting the turbine speed via the use of a wastegate.
On top of this, you also tune the ignition and fuelling to provide the control required. With modern ECU's there are many mapping points, which allows you to fine tune the base map, you then have the ability to use active controls that smooth out the rpm points between the mapped tables, plus you can also actively tune the transitions to make that smooth.
You can map all this per gear too, so if your particular car has a weak 4th gear, you can reduce peak torque for that gear but keep the torque higher for the others, which can handle the load.
You can also map this around situation, so for example you will limit the torque during a launch so you don't have too much wheel spin or load on the clutch and input shaft, but once up to speed you will allow peak torque.
On my own ECU I have 12 maps switchable from the driving seat, each map allows me to fine tune anything I want and then select that on the fly. During a sprint I will use the higher torque maps, when I use the car on the road I drop the peak mid range torque to reduce load on the drivetrain. My engine can produce 540lbft on the higher torque maps and just shy of 500BHP when allowed to, on the road i'll back it off to 450lbft but still have the same top end power. Doing that has allowed me to so far manage 113K miles on the stock drivetrain (bar a clutch upgrade) with zero failures, yet still win a sprint championship outright.
You can profile the engines to very small margins on the modern ECU's, mine even allows flat foot shifting so on upshifts I don't come off the throttle, as soon as the clutch is touched the ECU backs off the fuel and ignition to cut the torque, which unloads the gears, then when I come back off the clutch (this is a conventional H pattern synco box) the ECU ramps back in the ignition and fueling smoothly to bring the torque back in without shocking the transmition. Doing this keeps the turbo speed up between shifts (instead of dropping 60Krpm, it drops 10krpm) because air is still flowing through the engine, its just not producing any torque, so you get no turbo lag.
Edited by anonymous-user on Sunday 13th August 15:12
jimPH said:
jsf, thankyou very much for taking the time to answer. A very informative post. I have a similar scenario in my current engine build where limiting torque output may be necessary.
So does wastegate speed alter the boost ramp?
no problem.So does wastegate speed alter the boost ramp?
The turbo wastegate is just a bypass valve, the exhaust gas exiting the engine goes into the turbo housing and then either passes through the turbine blades, driving that to drive the compressor via the turbo shaft, or it goes through the hole opened when the wastegate is opened up.
You use the size of the hole made by the wastegate to control how much exhaust gas doesn't drive the turbine.
Initially to gain maximum turbo spool and minimum lag, you want the turbine to be driven as hard as possible, so you start with the wastegate closed, that forces all the exhaust gases to drive the turbine. The problem with that is when you come to the point where the turbo starts to flow in its efficient range its easy for the airflow produced to overshoot your target before you can control the speed with the wastegate, so to manage the spikes in airflow this generates you have to build a wastegate control strategy that can catch the turbo as it ramps up whilst still gaining the best spool performance.
Once you are past that initial spool stage, its usually pretty easy to control the airflow, the talent in mapping is that initial spool control so you don't overboost beyond your safe targets whilst gaining best response.
You then control the turbine speed to provide peak engine performance, the mistake often made is people try and run the maximum boost the turbo will produce, but that's rarely the peak airflow point for the turbo or the engine, you just end up heating the charge air up and giving the intercooler too much to cope with, which drops power and puts the engine closer to its det point.
My own turbo could produce 2.2BAR easily, but I run it at 1.8BAR peak and by max engine rpm its down to 1.6BAR, because that's where the efficient turbine speed and airflow through the engine is. My turbo has a speed sensor on the compressor wheel and that is monitored by the ECU so it never overspeeds.
To do all this in practice you need a good closed loop control system, so you build your base map as close as possible, then switch on the active controls which fine tunes the wasetgate, with my own ECU I can have different wastegate targets for each gear, which you need as the engine load (and turbine response) is different depending on the gear you are in.
If you did that when cutting the torque during a gearshift, you would lose turbo speed, increasing lag time when back on throttle, it wouldn't reduce torque quickly enough to unload the gears either. You don't touch the wastegate at all in that scenario, just retard and cut ignition and fuelling, you keep the wastegate shut.
You can also have the situation where even with the wastegate fully open, the turbo is flowing too much air for the torque target, so you then control the torque via your ignition and fuel mapping.
You can also have the situation where even with the wastegate fully open, the turbo is flowing too much air for the torque target, so you then control the torque via your ignition and fuel mapping.
Edited by anonymous-user on Monday 14th August 13:57
jsf said:
If you did that when cutting the torque during a gearshift, you would lose turbo speed, increasing lag time when back on throttle, it wouldn't reduce torque quickly enough to unload the gears either. You don't touch the wastegate at all in that scenario, just retard and cut ignition and fuelling, you keep the wastegate shut.
You can also have the situation where even with the wastegate fully open, the turbo is flowing too much air for the torque target, so you then control the torque via your ignition and fuel mapping.
The throttle downstream of the compressor is used to modulate torque by the driver. Steady-state WOT torque limiting and torque modulation during gear changes are two separate things and are dealt with in very different ways.You can also have the situation where even with the wastegate fully open, the turbo is flowing too much air for the torque target, so you then control the torque via your ignition and fuel mapping.
Edited by jsf on Monday 14th August 13:57
Also, if your minimum boost line isn't set to less than the lowest maximum boost you need then you don't have a fuel and ignition mapping problem, you have a wastegate capsule setup problem. The ECU needs to have closed-loop control of boost pressure at all times otherwise it isn't a controller (obviously...)
Edited by AER on Tuesday 15th August 02:49
AER said:
The throttle downstream of the compressor is used to modulate torque by the driver. Steady-state WOT torque limiting and torque modulation during gear changes are two separate things and are dealt with in very different ways.
Also, if your minimum boost line isn't set to less than the lowest maximum boost you need then you don't have a fuel and ignition mapping problem, you have a wastegate capsule setup problem. The ECU needs to have closed-loop control of boost pressure at all times otherwise it isn't a controller (obviously...)
And if the driver doesn't modulate the torque, the ECU has to or you break something.Also, if your minimum boost line isn't set to less than the lowest maximum boost you need then you don't have a fuel and ignition mapping problem, you have a wastegate capsule setup problem. The ECU needs to have closed-loop control of boost pressure at all times otherwise it isn't a controller (obviously...)
Edited by AER on Tuesday 15th August 02:49
You are talking about ideals with regards to your second point, it is not that unusual on these big turbo installs that the waste gate cant limit the turbo enough on its own, so you have to use engine mapping of the other parameters to do so. That isn't required in a more balanced system where wastegate control will do enough as you sugest.
resurrecting this as i also would like some 'for dummies' explanation of how torque can be limited in certain gears, or otherwise how to tune for torque.
the 2.0 ecoboost is used in the elemental rp1 producing 332 lb/ft of torque. the same engine in the radical sr3 sl produces 340 lb/ft. both cars use hewland transaxles which are rated, according to hewland's website, at 240 lb/ft max.
my question is how both engines are able to exceed the gearbox torque limit, or rather how it is being managed so as not to kill the box? i have a hewland ftr transaxle and so understanding this would help the umpteenth iteration of deciding what engine to put in front of it.
the 2.0 ecoboost is used in the elemental rp1 producing 332 lb/ft of torque. the same engine in the radical sr3 sl produces 340 lb/ft. both cars use hewland transaxles which are rated, according to hewland's website, at 240 lb/ft max.
my question is how both engines are able to exceed the gearbox torque limit, or rather how it is being managed so as not to kill the box? i have a hewland ftr transaxle and so understanding this would help the umpteenth iteration of deciding what engine to put in front of it.
Gassing Station | Engines & Drivetrain | Top of Page | What's New | My Stuff