What is an electric supercharger? PH Explains
If you need to improve a turbocharged engine's power delivery, an electric supercharger might just do the trick
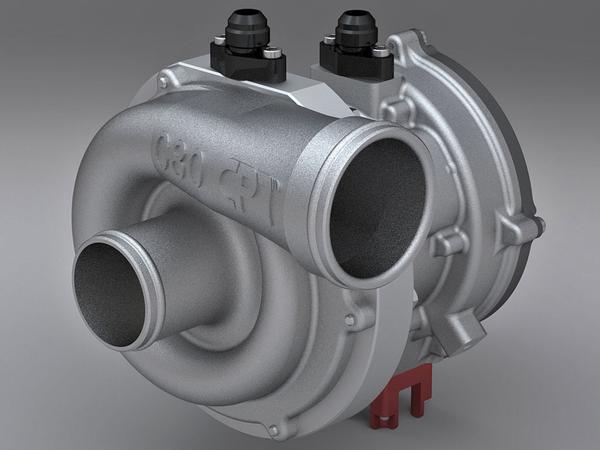
How does an electric supercharger work?
Electric superchargers function like conventional superchargers, in that they are designed to pump air into an engine. This increases the density of air in the engine's intake, meaning more oxygen is present in each cylinder after the intake stroke. This, among other things, allows more fuel to be burned and more power to be produced.
Electric superchargers, however, have so far primarily been used to improve the response of turbocharged engines by combatting turbocharger lag. This has been achieved by using compact set-ups that generate a small amount of boost almost immediately, helping get the car moving and more exhaust gas flowing - which helps spool the turbocharger, or turbochargers, quickening the engine's responses.
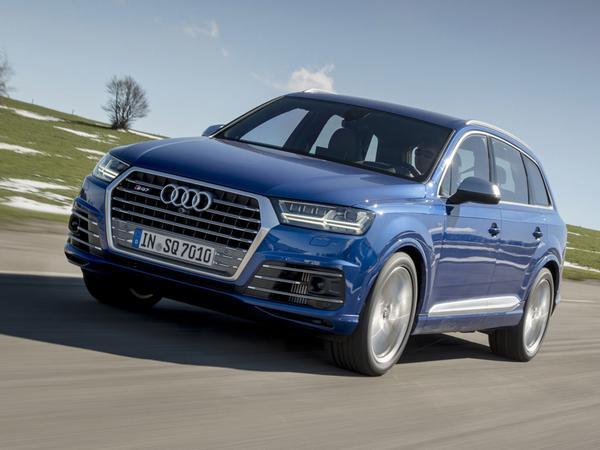
How do they differ from conventional superchargers?
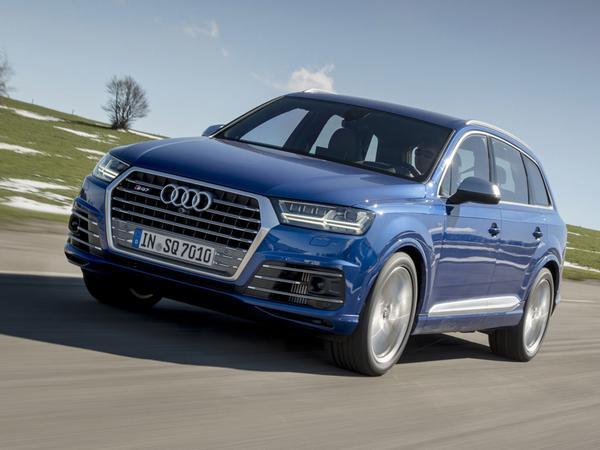
A conventional supercharger is driven by mechanical means. In most automotive applications, the supercharger is typically driven by the engine via a belt. Older superchargers may feature shaft or gear-drive set-ups, while some racing applications feature a standalone powerplant - a gas turbine, for example - to power the supercharger.
An electric supercharger, on the other hand, is driven by a powerful electric motor. This allows the supercharger to be shut down entirely, or spun up in fractions of a second when required, as well as permitting its output to be varied to best suit the engine load and conditions.
A mechanical supercharger, unless fitted with a multi-speed gearbox, is otherwise restricted by the speed of the engine that is driving it. Similarly, unless a clutch is fitted, a mechanical supercharger will consume energy and reduce efficiency when not needed.
Electric supercharger set-ups are complicated, however. Besides requiring dedicated control systems and additional intake piping, they require heavy-duty power supplies that can keep up with their high demands.
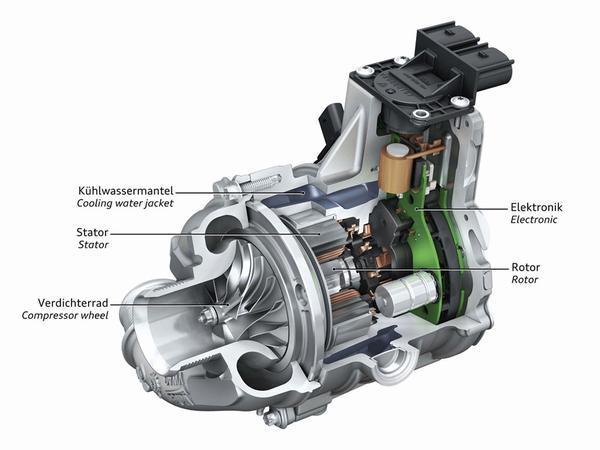
Common types of electric supercharger
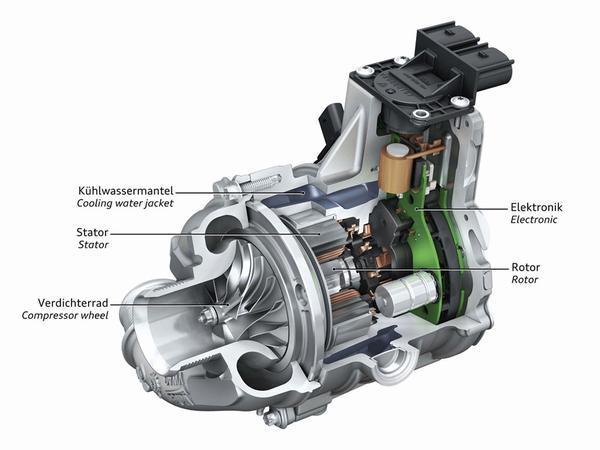
Electrically driven centrifugal superchargers: These resemble a turbocharger at a glance but, instead of an exhaust-driven turbine, they have a compact and powerful electric motor assembly driving the compressor wheel. This is the type used in the Audi SQ7 and, so far, it appears to be the preferable design.
Electrically driven Roots-style superchargers: Many early efforts involved converting conventional engine-driven Roots blowers to electric superchargers. They were often heavy, complicated and inefficient, and their appeal was limited as a result. That said, electrically assisted units - which retain an engine-driven pulley - have been developed. These offer improved response, reduced losses and other useful features. Some compact units have also been developed for fuel cells, where a compressor is needed to pump air through the fuel cell stack.
Are these the same as electric turbochargers?
Turbochargers, by their nature, are driven by exhaust gases - so a compressor that is driven by mechanical or electrical means cannot be anything other than a type of supercharger.
Consequently, the term 'electric turbocharger' is incorrect. It is routinely the case that the method of forced induction being referred to is actually an electrically driven centrifugal supercharger which can resemble a turbocharger.
That said, electrically assisted turbochargers do exist. These feature an inbuilt electric motor that can be used to spool the turbocharger, or to recover energy to improve efficiency.
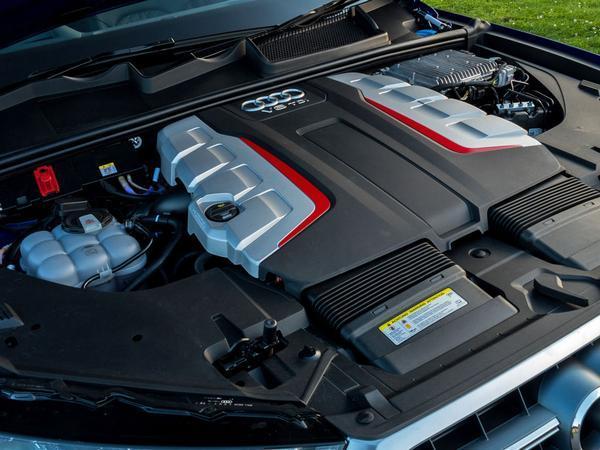
Recent examples of electric supercharging
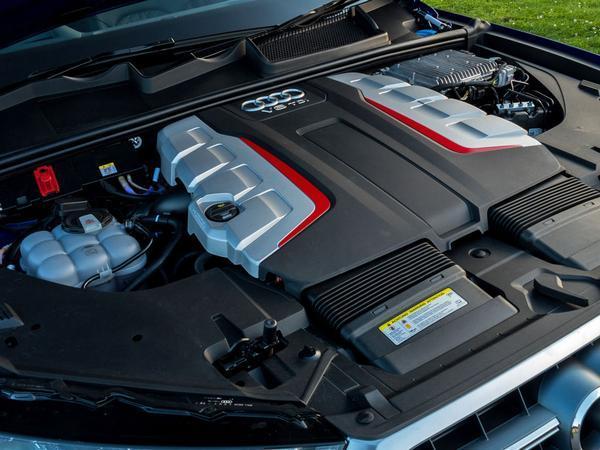
Audi's SQ7 was the first production car to feature an electrically powered compressor. The small compressor unit, which operates from idle to around 1,500rpm, helps get the SQ7 off the line and gets the turbocharging system up to speed quicker. The same system is used in the Bentley Bentayga.
Several other companies, including specialists Federal-Mogul Controlled Power and Aeristech, have also developed electric superchargers for commercial applications - the aim being to supply 'on-demand' supercharging that can reduce fuel consumption and emissions while improving performance.
[/quote]
Go on then, what exactly does this look like?
It fires air through the impeller right?
It fires air through the impeller right?
Two seconds on Google found this:
https://jalopnik.com/this-is-the-difference-betwee...
Looks like an electric motor is placed between the turbine (hot side) and the compressor (cold side) to get the compressor spinning before the exhaust pressure is high enough to spin the turbine in order to reduce turbo lag.
Didn't Magnetti Marelli have a Turbo proposal that used a motor connected to the turbine shaft that could in effect spool up the turbo when exhaust gas pressure was low? Was one of the first MGU-H concepts when F1 went Hybrid wasn't it?
RE: supercharger clutches, I remember we were once looking at a large engine charger and clutching it to increase off boost efficiency. It took someone pointing out that at full load, you're basically clutching a Ford Fiesta engine in and out, such is the power demand, to make the management realise it would never package.
Two seconds on Google found this:
https://jalopnik.com/this-is-the-difference-betwee...
Looks like an electric motor is placed between the turbine (hot side) and the compressor (cold side) to get the compressor spinning before the exhaust pressure is high enough to spin the turbine in order to reduce turbo lag.
An electric supercharger may in a "dual-charged" system assist a conventional turbocharger by "firing compressed air" into the compressor..
I'm just not confident the article is really clear.
I believe that all turbo-hybrid era F1 engines and the late Porsche 919 use the electrically assisted turbocharger format.
The motor/generator doesn't always have to be located between compressor and turbine and I believe one of Merc's advantages was locating their motor outside.
Also due to packaging I think all teams mount the turbocharger within the v of the engine, adding to heat issues.
An electric supercharger may in a "dual-charged" system assist a conventional turbocharger by "firing compressed air" into the compressor..
I'm just not confident the article is really clear.
Which aims to reduce lag using air injection, but I wouldn't exactly class it as an electric supercharger as far as the context of the article goes.
https://jalopnik.com/volvos-powerpulse-technology-...
Max, did the rally guys use the that tank as a surge tank, holding pre throttle air at the same pressure as WOT? That way when the throttle opened you have a tank full of pre pressurised air at operating pressure ready to go. Guess this only works as the rally guys could use anti lag to keep the turbo producing boost even with the throttle closed..
Max, did the rally guys use the that tank as a surge tank, holding pre throttle air at the same pressure as WOT? That way when the throttle opened you have a tank full of pre pressurised air at operating pressure ready to go. Guess this only works as the rally guys could use anti lag to keep the turbo producing boost even with the throttle closed..
The FIA introduced a 34mm inlet restrictor in front of the turbo charger to limit the maximum amount of air that can be sucked into the engine irrespective of boost pressure (once the flow becomes choked (supersonic, well, nearly, transonic in reality) no more air can pass, so engine power is limited. Clever engineers immediately saw however that the restrictor would only be choked when the throttle was pressed (more than about 50%) and a rally car, on slippery surface spends quite a bit of time off-throttle when braking etc. So, a series of one way valves was introduced, and the antilag system wound up to "11" and everytime the driver came off the throttle, the turbo would keep blowing, but rather than going into the engine, it would be sent into that tank, filling it up with high pressure air.
Then when the throttle was re-opened after a corner for example, the engine could, transiently, have a LOT more air and make, for a few seconds a LOT more power! In rallies, corners come thick and fast, average speeds are (relatively) low, so that extra power made a significant different.
Technically, it wasn't against the rules at the time, as ALL the air did indeed come into the system through the mandated restrictor (unlike Toyota's famous restrictor bypass cheat which WAS blatantly illegal)
However, concerned about the cars getting even faster, and some (legitimate) safety concerns around pressurised tanks in crash situations, the FIA introduced a "max inlet volume" rule, which limits the total system volume between the turbo charger exit and the engine inlet valves. That effectively mean't you couldn't install a tank of any sensible volume, and made the system obsolete. At Prodrive, we went on to introduce what looked to be a small, but similar tank into the intake system, but that actually relied on adiabatic expansion to further cool the charger air and increase the engines knock limit.
I have seen the funny pristine intake on the Subarus. Did it make much difference?
I have seen the funny pristine intake on the Subarus. Did it make much difference?
The adiabatic expansion system is fundamentally a change in approach. Up to that point, all intake systems were designed to be "Low loss" ie engine manifold pressure should be as close to turbo charger outlet pressure as possible. However, on a restricted ' air limited' engine, there is no way of getting more air into the engine. If you want more power you need to increase engine efficiency i.e. 1) lose less work to friction and 2) burn that air an generate a higher BMEP.
Point 1) means downspeeding, making peak power at a lower engine speed (once you've fitted ever other super trick low friction component you can), but downspeeding brings a lower knock limit, as there is less dynamic charge motion, lower flame front velocities, and more time for detonation to initiate before the charge has been burnt, forcing ignition retard and reducing power again. So the question becomes, how do you recover the knock margin?
Well, one answer is to somehow get a colder intake charge, but as intercoolers are deltaT driven devices it gets harder and harder to get to ambient temp the closer you get to that temp. But, a WRC turbochargers boost efficiency opens up another option! If "making boost" costs less power than returned by colder charge temps, can you use more boost to get a colder intake? Most people, who understand that compressing something makes it hot will be thinking at this point "huh? how does that work" but there is a very useful trick available (used for years in aeronautics btw).
What we do is we introduce a "lossy" pressure restriction down stream of the intercooler. Because it does not have a good pressure recovery, we need to jack up compressor outlet pressure to get back to the same manifold pressure. Normally, that would loose power, but, with careful design, the expansion after that loss can be made to tend towards an adiabatic one, ie one that cannot pull heat from it's environment. (when you compress air, it gets hot, when you expand it, it gets cold). Therefore the air expanding through that restrictor has to pull heat from somewhere, and the only place is itself. In effect, insulated from the rest of the world, it expands and cools itself (a similar technique is used in air conditioning systems with phase shift working fluids to an even greater effect)
So why would you do this? The compressor makes more boost, the air outlet from it is hotter, but that heat is lost again when the air is re-expanded through the lossy restrictor? Whats the point? Well, what you gain is the bit in the middle, if the air is hotter exiting the compressor, then it has a higher deltaT to ambient, and now you intercooling system CAN get rid of more of that heat (because it is operating at a higher average temperature above ambient) so when you then expand the air after the intercooler, the adiabatic expansion results in an air temp BELOW ambient! Hurrah!
With a wrc engine, which running 3bar(gauge) at low rpm is incredibly knock limited, the increased knock margin from the colder charge air releases more power than the extra power consumed by the (very efficient at high pressure ratios) turbo working harder. A net increase in flywheel power is the result.
Gassing Station | General Gassing | Top of Page | What's New | My Stuff