What is electronic throttle control? PH Explains
Discover why cable-actuated throttles were ditched in favour of drive-by-wire systems
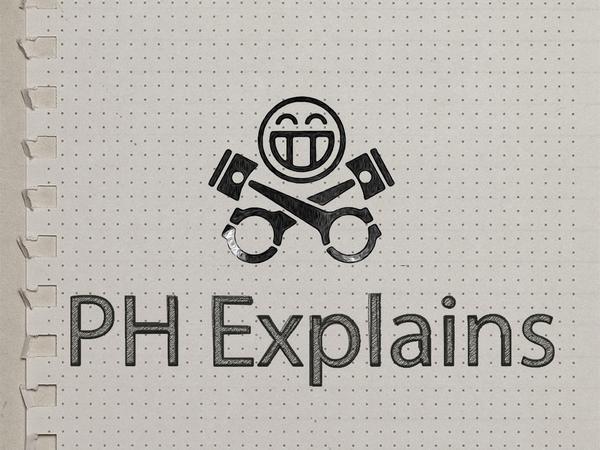
Electronic throttle control is a drive-by-wire system that replaces a conventional cable-actuated throttle body with an electronic set-up.
In a conventional throttle configuration, such as that found in an older car, a cable would run from the pedal to the throttle body. In an ETC-equipped car, the driver's inputs are instead monitored by a sensor on the pedal assembly and relayed to an electric motor that actuates the throttle plate.
The primary advantage of such a system is that the car can automatically regulate the engine speed, by reducing the throttle opening, without any driver input. This permits a wide range of safety and comfort-related capabilities, including cruise control and traction control, in a neat and easily packaged assembly.
Using a 'throttle-by-wire' system also has other benefits, including removing the need for convoluted cable assemblies - which can wear and bind over time, causing driveability and safety issues.
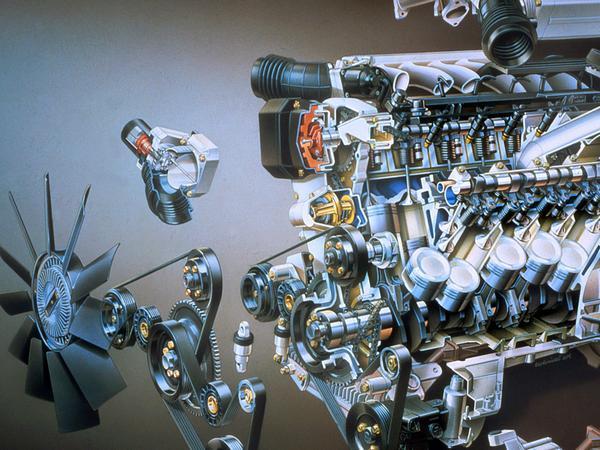
How do electronic throttle controls work?
In a conventional cable-actuated set-up, a cable runs from the pedal in the footwell to the throttle body. When the driver steps on the pedal, the cable transmits the motion of the pedal to the throttle blade within the throttle body, opening the throttle. When the driver lifts off, springs pull the throttle closed again.
An electronic throttle system removes the cable from the equation. Instead, a sensor on the accelerator pedal assembly monitors the position of the pedal. When the driver accelerates, the sensor transmits data regarding the pedal position to the car's electronic control unit. After processing the data from several other inputs, the ECU will then generate suitable signals which are sent to an electronically controlled throttle body.
This, instead of being opened by the motion of a cable, features a form of electronic actuation - typically a servomotor or stepper motor - which is continuously monitored and positioned by the ECU.
When a change in the throttle opening is required, appropriate signals will be sent from the ECU to the electric motor in the throttle body. The motor will then reposition the throttle blade to suit, increasing or decreasing airflow into the engine as required. An integral spring can help the throttle blade return to the idle position but, in any case, one will be present to ensure the throttle closes if there is a problem with the control system.
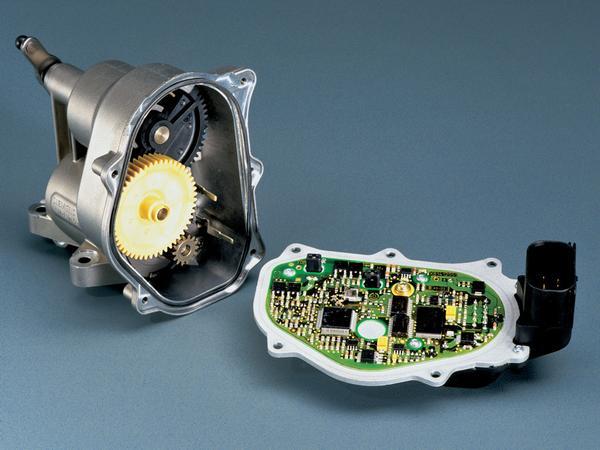
Are there any advantages or disadvantages to this throttle-by-wire approach?
Prior to the adoption of electronically controlled throttles, systems existed that allowed the car to override the driver's input. Bosch, for example, developed an 'Anti-skid Regulation' unit that enabled traction control in cars with cable throttle assemblies.
However, these set-ups were often complicated and bulky. Electronically controlled throttles, on the other hand, are far lighter and more compact, making them easier to package. They are also far more flexible in terms of what they can achieve.
The relationship between the motion of the pedal and the throttle opening can also be changed on the fly to suit the conditions or driving mode using ETC set-ups; a sport mode could grant very quick and substantial throttle openings when the driver tips in on the accelerator pedal - resulting in an artificially lively, punchy-feeling engine and experience.
Alternatively, the engine's response could be very gently and gradually metered out over the entire length of travel of the accelerator. This kind of response is ideal for urban driving or in snowy conditions, as it reduces the chance of wheelspin or jerky acceleration.
Electronically controlled throttles can also be used to regulate the engine's idle speed without any additional hardware, helping keep cost and complexity down - although many do retain standalone idle air control systems.
There are otherwise no disadvantages to using an electronically controlled throttle, provided it is calibrated well, as these configurations allow for lightning-quick changes of throttle position when commanded by either the ECU or driver themselves.
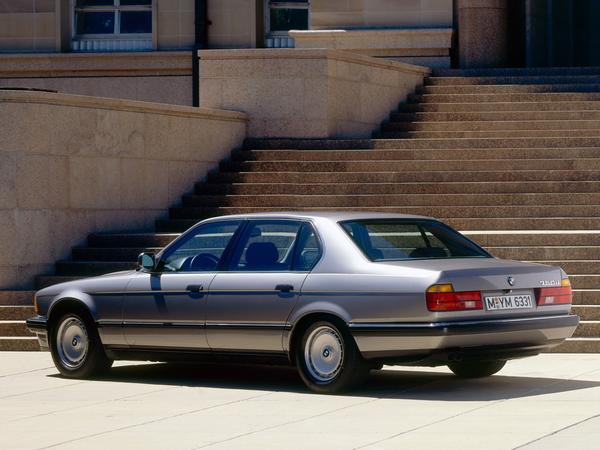
A brief history of electronically operated throttles
Electronically actuated throttle bodies were reportedly first prototyped by Bosch in the 1980s for use in motorsports applications. They were easier to package, requiring no convoluted cable routing, and permitted a wide range of additional features without needing any extra hardware. For example, a team could easily instate traction control without needing a bulky motor assembly to actuate the existing cabled throttle set-up.
BMW then adopted a development of Bosch's electronically controlled throttle bodies for its new V12-engined 7 Series flagship, which was unveiled in 1987. Doing so allowed BMW to equip the luxury saloon with the likes of cruise control, traction control and a speed limiter without resorting to an overly complicated cable and servomotor-equipped set-up.
The company's 5.0-litre 'M70' V12, which initially went into the 750i and 750iL, used twin Bosch Motronic engine management systems and a pair of electronically controlled Bosch throttle bodies. BMW's own 'Elektronische Motorleistungsregelung' - electronic power regulation system - monitored all the required inputs, such as accelerator pedal position and wheel slip, and would then send signals to the throttle bodies to open them to the optimum position.
Other manufacturers, such as General Motors, soon followed suit. As costs fell and the demand for improved safety systems and creature comforts continued to rise, electronically controlled throttle systems quickly became commonplace - with their applications ranging from basic city cars through to the likes of the Ferrari 458 Speciale and beyond.
Okay, throttle cables can bind or even break (I've had one throttle return spring snap in 40 years of driving) but I think it's pretty rare. I'm all for keeping things simple mechanically but that's not the way the world's been going for many years now. My current car has an intermittent problem with its electronic throttle and various steps have been taken to try and address the problem (cleaning out the throttle body, replacing the throttle pedal sensor, etc) but nothing has ever 'restored' it to feeling direct and connected to my right foot and giving me that instant and direct control all my cable throttle cars have done.
Okay, throttle cables can bind or even break (I've had one throttle return spring snap in 40 years of driving) but I think it's pretty rare. I'm all for keeping things simple mechanically but that's not the way the world's been going for many years now. My current car has an intermittent problem with its electronic throttle and various steps have been taken to try and address the problem (cleaning out the throttle body, replacing the throttle pedal sensor, etc) but nothing has ever 'restored' it to feeling direct and connected to my right foot and giving me that instant and direct control all my cable throttle cars have done.
Part of the issue with bad press of DBW is that some manufacturers engineered lag in to the systems to aid fuel economy and more prevalently mask over poor driveline rigidity, backlash, wind up. It is much cheaper to add lag to a DBW than it is to engineer a clutch, DMF, gearbox, prop shaft, diff and all the associated compliant mounts which doesn't shunt and judder.
I drive a E30 M3 and a E90 330. Although the E30M3 has a sharper response, it is on individual throttle bodies, the E90 is not far behind.
I am considering going to DBW for the E30M3 as it gives some advantages, such as limiting throttle opening at low rpm to stop bogging down. In doing so, I don't believe I will lose the response.
Or a cable can run from the pedal to position sensors on the throttle body. An electronic throttle doesn't necessarily mean that there's no throttle cable.
[/pedant mode]
What you're feeling is the "sporty" map so beloved of many DBW installations, which provide a greater % throttle response to the equivalent pedal movement. There's a difference between 'lag' and 'rate of response', IYSWIM.
I agree that a good DBW system isn't a problem...it's just a shame that, as noted, many mfrs don't care about a good DBW installation, they just use it to mask over engineering shortcuts elsewhere.
With ETC able to give control of the air path to the engine controller, the driver demand is now actually a torque demand, which is looked up from various maps that have all sort of input parameters. The EMS is then free to determine how to best set the engines controlling parameters (throttle position, ignition timing, boost pressure, cam timing, EGR, etc etc etc) to deliver exactly that requested torque. This means that the car drives the same hot and cold, high and low, and on a range of different fuels, and means the system can abstract away parasitic torque demands (Air conditioning, alternator) and prioritise external demands as well (Transmission, stability control etc) For the first time, the engine became part of the "Powertrain" rather than just being a dumb provider of motive force.
Fundamentally, an ETC system is no slower than a cable system, and can be faster (motorsport systems can get the throttle plate fully open BEFORE the drivers foot has hit the floor!), but in road applications, emissions, driveability and protection algorithms take precedence. (The move to gasoline direct injection has helped modern engines back to a faster response as they don't have to compensate or eliminate the inlet manifold fuel puddle mass issue that is so degrading of transient emissions control)
Oh...and whilst in the right application it's good, in the wrong one it's a f'n disgrace - VW preventing BGOL (even in their sporting cars), for example, and having some sort of signal damper which makes blipping the throttle very difficult to finesse, even when separating braking and rev-matching. This "we know best" attitude (please also see BMW and their early pedal-maps) really doesn't help the case of DBW.
In theory you're probably correct...but it appears that engineers can't help but tinker around with DBW systems, removing the potential advantage.
In theory you're probably correct...but it appears that engineers can't help but tinker around with DBW systems, removing the potential advantage.
In theory you're probably correct...but it appears that engineers can't help but tinker around with DBW systems, removing the potential advantage.
A cable operated carb could have response improved by adjusting the timing and volume of the accelerator pump - with the downside of poor respoinse at slow speed/demand.
In theory you're probably correct...but it appears that engineers can't help but tinker around with DBW systems, removing the potential advantage.

Agreed. Hence my comment about the potential of DBW vs the reality.
Manufacturers (well, Porsche and Lotus probably excepted in the sub-£100k market) don't make cars like the DC2 anymore...and even the two named probably don't dare trust their customers as much as mfrs used to have to. The proliferation of electronic systems tends to mean there's another layer of cotton wool and/or nannying in the way now.
(Just like NVH engineers - baby/bathwater territory for a keen driver, as the messages are more and more muted in modern cars unless you go the whole hog and get e.g. a GT3 or a Lotus), which in terms of driver interface undoes a lot of the recent advances in chassis stiffness and damping technology.)
Eldar - DC2 was EFI, not carbs. And the timeliness of the response was anywhere from <1,500rpm through to >8,500rpm...although below 4,000 you had to be rather patient as the power was being summoned from another country!



It's not just throttles; everything from the Windows start button to the Home button on an iPhone has a noticeable delay these days (gone on - try it!). Thankfully though, nobody really minds with those as they're only there to do a dull job, like cars are to most people. I'm guessing that's why cars have this delay, because manufacturers don't think it matters, just like Apple or Microsoft don't think it matters. I guess it doesn't matter to most users of cars, smartphones or computers. If you go to gaming forums though, you can find that gamers hate wireless mice due to the delay they have, which most of us don't even notice. To a keen driver like me, it really matters in a car too.
I find this such a major problem that it's completely ruined my enjoyment of most modern cars, which is a great shame. I've owned two DBW cars with throttle lag and tried to get round the problem with aftermarket fixes (none of which did anything other than empty my wallet). I've also tried to own an older car with a cable actuated throttle as a daily, but in the end it was just too expensive to keep on the road. Track cars have been ok, my Lotus 2-Eleven for example had utterly amazing throttle response from its DBW system. My current track car, like many racing cars, has a cable despite being a 2008 model. My solution for daily drivers has sadly been to buy diesels, which, for BMW at least, have instant initial response and I'm happy. Yes, they have an annoying turbo lag, found in other situations, but that doesn't bother me anywhere near as much because it doesn't affect cornering. Yeah, sure, I have to drive a diesel, but I guess it's the lesser of two evils.
Gassing Station | General Gassing | Top of Page | What's New | My Stuff